
3 minute read
Tradex-Services GmbH
Name ›
Address/P.O. Box › Postal Code/City › State › Contact Person › Telephone › Email › Website › Social Media › Number of Employees › Founded (year) ›
Areas of Activity ›
toolcraft AG
Handelsstraße 1 91166 Georgensgmünd Bavaria Patrick Meyer +49-9172-6956-0 toolcraft@toolcraft.de www.toolcraft.de
F I QI
417 1989
| Medical technology | Semiconductors | Aerospace | Defence and security | Automotive, vehicle technology and motorsports | Optical industry
Member of toolcraft AG is a pioneer of future technologies, such as additive manufacturing and the construction of individual robot cells. As a provider of comprehensive solutions, toolcraft covers the entire process chain, from the initial idea to manufacturing, quality assurance, and testing in additive manufacturing, machining, injection moulding, and mould making. In the field of robotics, customised, fully programmed integration solutions are implemented. Building close working relationships with collaborative partners as well as universities, other institutions of higher education, and research centres is an important part of its corporate philosophy.
Future technology additive manufacturing meets classical machining
Additive manufacturing enables highly complex geometries with significantly reduced time and resources. Two years ago, the medium-sized company invested in a customised LMD system with powder nozzle from Trumpf with horizontal and vertical rotation axes. This enables “extreme high-speed laser metal deposition” (EHLA) – developed and patented by the Fraunhofer Institute for Laser Technology ILT.
The in-house measurement and testing laboratory provides precise answers for reliable component quality: from the inspection of materials on receipt and processrelated analyses such as density determination, structural analysis, and analysis of mechanical properties to the preparation of comprehensive reports.
The additively manufactured raw parts are refined into the complete functional component by machining processes. The machinery at toolcraft is always state-of-the-art. The use of multi-axis technology and angle heads is exemplary for its innovative strength. It is possible to machine almost any material. In addition, various furnaces, including a vacuum furnace, are available for heat treatment of the components. To significantly expand the machining process chain, toolcraft invested in a modern technical cleaning system at the end of 2020. With this, the finished components are finely cleaned and packaged according to customer
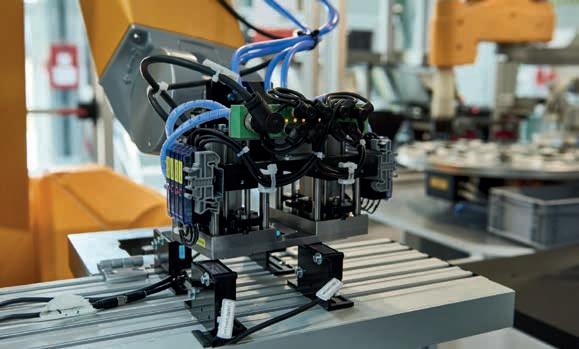
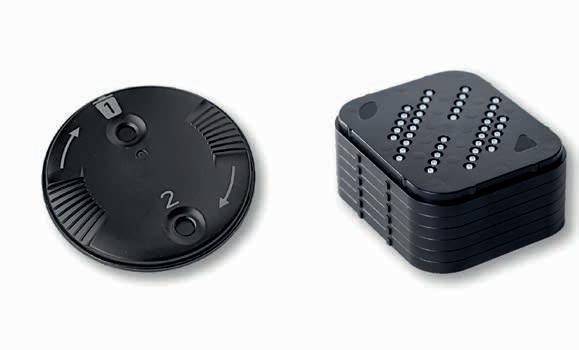
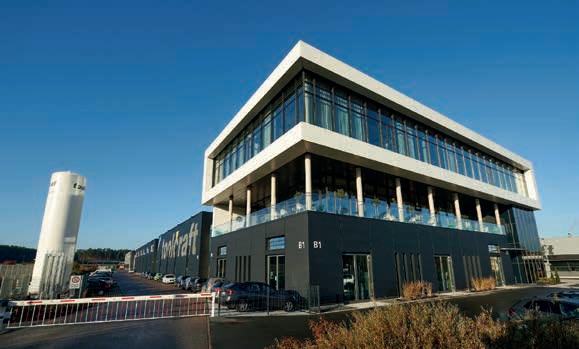
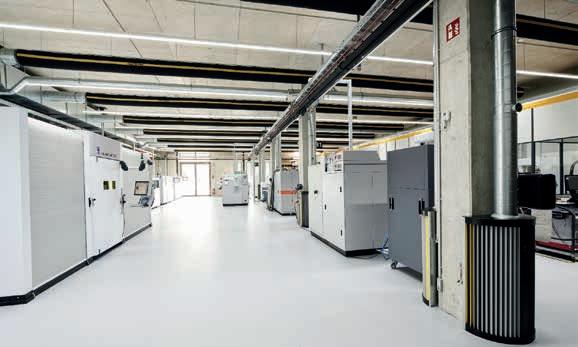
specifications, whereby absolute cleanliness can be guaranteed.
Expert knowledge of mould making, injection moulding, and robotics
toolcraft has developed a complete automated solution for the production and packaging of a cerumen filter protector for hearing aids. For this purpose, a mould to produce very small parts was designed and manufactured in the mould-making department. A micro-injection moulding system was combined with a robot to automate the entire process. Thanks to expert knowledge in process development as well as in camera and laser technology, toolcraft implemented component inspection using camera and laser micrometer technology as well as the lasering of the packaging components in the specified cycle time. Since then, the filter systems have been coming off the production line fully automatically have been coming off four production lines fully automatically.
Certified precision
toolcraft attaches great importance to the highest standards in the quality of its precision components. This is evidenced, among other things, by the certifications according to DIN EN ISO 9001, EN 9100 and DIN EN ISO 14001. Since 2014, the company has been certified according to DIN EN ISO 13485 for the manufacture and assembly of surgical tools and components for medical devices. In 2018, this was followed by certifications for additive manufacturing according to Nadcap and from TÜV SÜD.