Integrating Traditional Manufacturing with Advanced Technology
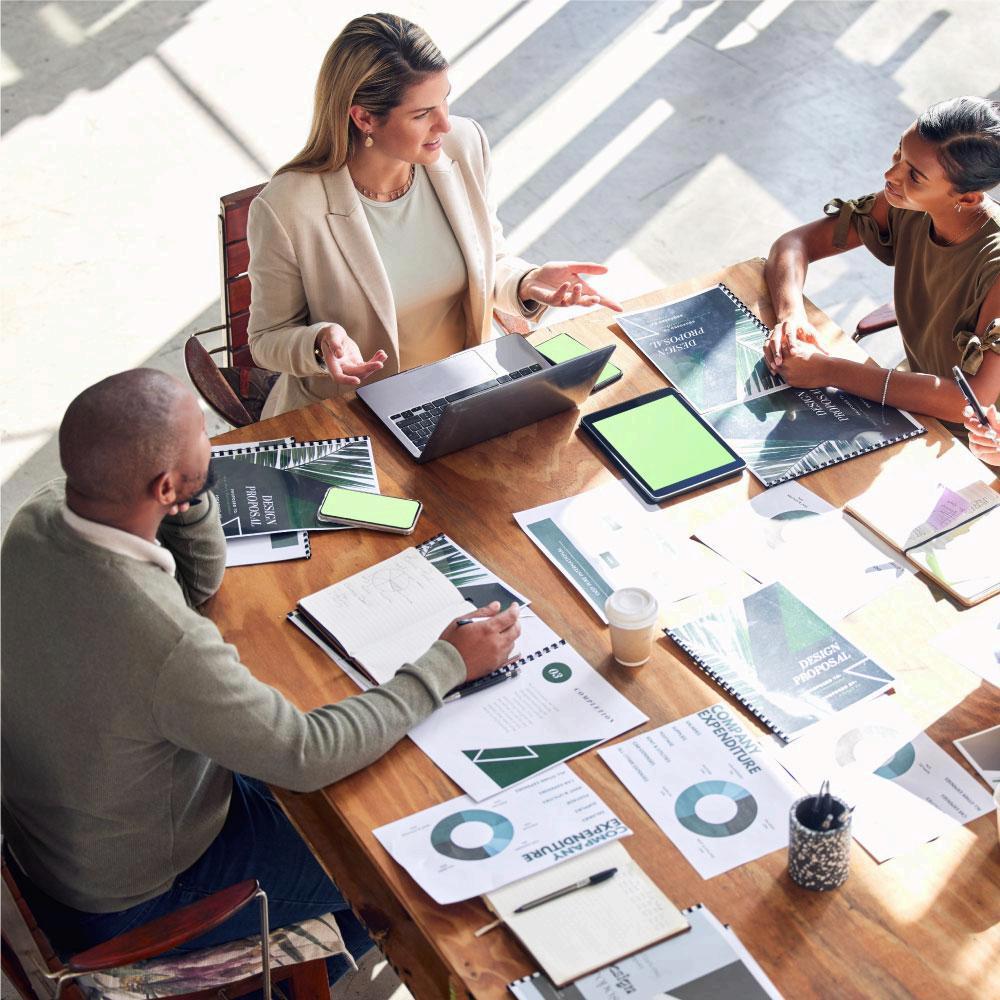
In today’s rapidly evolving industrial landscape, integrating traditional manufacturing methods with high-tech innovations has become increasingly essential Many manufacturing companies that once relied solely on old-school techniques are now incorporating advanced technologies to stay competitive and efficient.
Billy Wilson Howard Junior suggests that traditional manufacturing has always been valued for its reliability and craftsmanship. However, it often faces challenges such as slower production times and limited flexibility By introducing modern technologies like automation, artificial intelligence, and the Internet of Things (IoT), manufacturers can overcome these limitations. These technologies help streamline processes, reduce errors, and improve overall productivity.
The integration of high-tech innovation also enables manufacturers to collect and analyze data in real time This insight allows for better decision-making and predictive maintenance, ultimately reducing downtime and associated costs Moreover, technologies such as 3D printing and robotics enhance precision and enable more customized production runs, which were previously difficult to achieve with traditional methods alone
Bridging the gap between old-school manufacturing and modern technology requires a strategic approach Companies need to invest in training their workforce to work effectively alongside new tools and systems. It also involves updating legacy equipment and rethinking workflows to create a seamless blend of both worlds
Ultimately, this fusion leads to more intelligent factories that are more agile and responsive to market demands It preserves the quality and craftsmanship of traditional manufacturing while unlocking the benefits of digital transformation Manufacturers that successfully bridge this gap position themselves for long-term growth and innovation in an increasingly competitive environment