Muilte Contae Andun Mills 232 of County Down
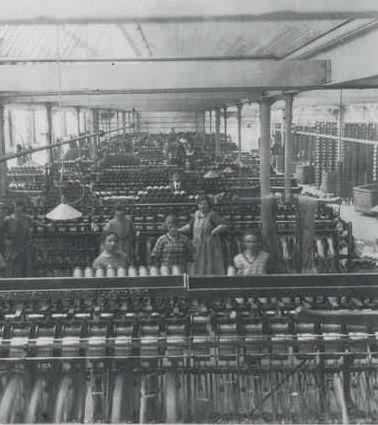

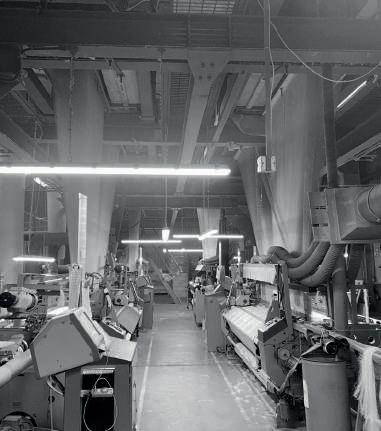
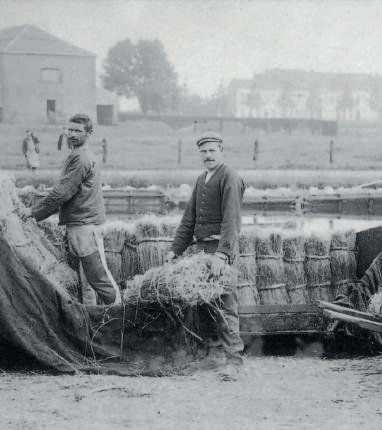
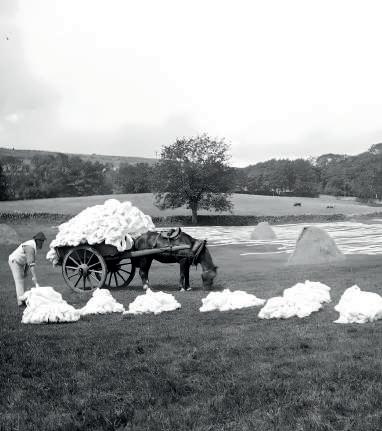
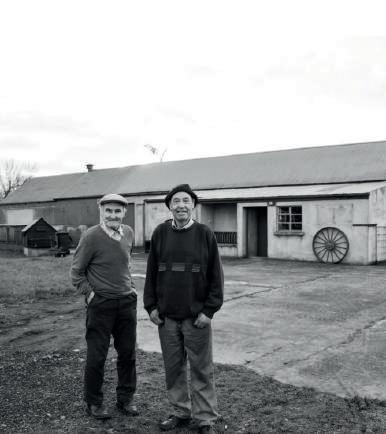
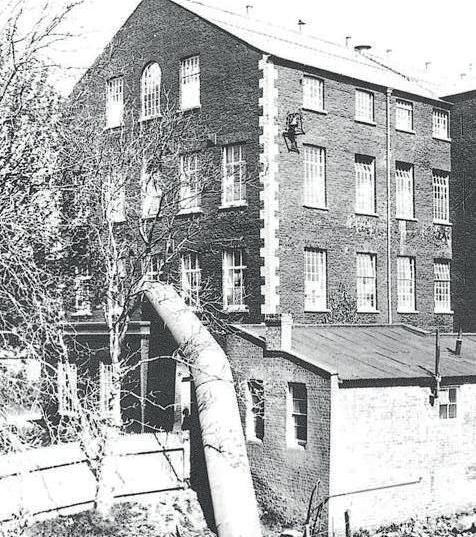
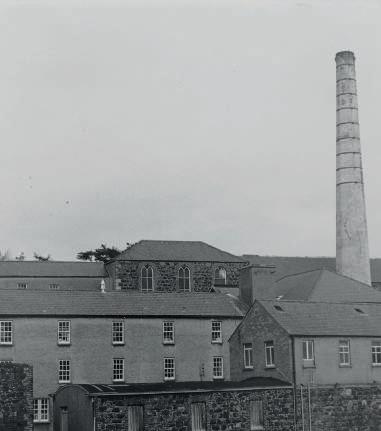
02–23
24–45
46–49
50–59
60–67 68–73
74–83
84– 91 92–105
Gilford
Banbridge
Loughbrickland
Newry
Blackskull
Waringstown
Dromore
Hillsborough
Lisburn
Rural Linen Towns
Anahilt
Dromara
Katesbridge
Milltown
Rathfriland
Mayobridge
Hilltown
Kilcoo
Rostrevor
Kilkeel
Downpatrick
Crossgar
Ballynahinch
Saintfield
Carryduff
Ballygowan
Comber
Newtownards
Dundonald
Bangor
Millisle
Kircubbin
To those who worked in the 232 Mills of County Down.
Dóibh siúd a bhí ag obair sa 232 Muilte Contae Andun.232 Mills of County Down showcases the various different mills involved in the linen industry in County Down. Thomas Ferguson in Banbridge is the last remaining linen mill out of the 232.
Documenting and paying homage to the industry in which so many people dedicated their lives to. Delving into the various different mills of bleaching, spinning, weaving, beetling and cultivating flax as a crop.
Through archival records, personal accounts, and historical anecdotes, interviews and photographs this book paints a vivid picture of the industry’s significance in shaping the region’s economy and culture. Each chapter sheds light on the various towns and cities involved in the processing of linen. This book is dedicated to preserving local heritage and ensuring that the mills of County Down are remembered.
Flax Mill — Herbert J Martin (Henry Uprichard)
Spinning Mill — Dunbar McMaster & Co
Weaving Factory — Cochranes Row, Dunbar McMaster & Co
Bleach Mill — Banford Bleach Works Company
Bleach Mill — Thornhill Bleach Mill
Bleach Mill — William Foster Uprichard Bleach Works
Bleach Mill — Messrs William Smyth and Co Ltd
Bleach, Spinning and Weaving Mill — Hazelbank Weaving Co
Beetling Mill — Haughton
Flax Mill — Herbert J Martin (Henry Uprichard)
Spinning Mill — Dunbar McMaster & Co
Weaving Factory — Cochranes Row, Dunbar McMaster & Co
Bleach Mill — Banford Bleach Works Company
Bleach Mill — Thornhill Bleach Mill
Bleach Mill — William Foster Uprichard Bleach Works
Bleach Mill — Messrs William Smyth and Co Ltd
Bleach, Spinning and Weaving Mill — Hazelbank Weaving Co
Beetling Mill — Haughton
The town of Gilford dates from about the middle of the 17th century when the Magill family, after whom it was called, acquired the land. The Magills were of Scottish origin. Early maps show the village of Gilford confined to what is now the Main Street. It had a tuck mill and a corn mill located in the vicinity of the present Presbyterian Church Hall. Houses were built around the crossing place or ford and on Castle Hill which was the main road leading from Lurgan to cross the river and proceed to Loughbrickland. In 1691, Sir John Magill (Johnston) grandson of Captain Magill granted by lease, for ever, to Thomas Purdy the tuck mill and corn mill of Gilford, with a large part of the present town and all that ground on which the present spinning mill now stands. Thus begins the 1st recorded history of milling in Gilford.
Having purchased these premises, the Purdys set about the processing of linen and by the end of the first quarter of the 18th century had extended their interests in the area. The will of Thomas Purdy, dated 21st August, 1728 states that he left the mills and lands to his sons, James and John after the interest of his widow ended. He further left to his son, James, the bleaching yard or green. The document also states that prior to 1691, the mills had been leased to a Hugh Ridley "Clothier" and John Thompson "Glover."
Up until the last quarter of the 18th century the Purdy family retained their interests in the linen industry. Imports and exports were facilitated by the vast enterprise, for those times, of cutting the Newry Canal which was opened in 1737 and finally completed to Lough Neagh in 1741 at an estimated cost of £896,000. It is roughly one and a half miles from Gilford to the Canal at Madden near Tandragee.
From 1775, however, the Purdy family began to dispose of their property in Gilford, mills included, and transfer their commercial interests to Newry. By a series of assignments up to 1792, the corn mill, tuck mill and lands became the property of a leading linen merchant – George Law. Being in the linen trade and with his family connections in the industry, he gave Gilford the stimulus that was to attract the attention of other enterprising entrepreneurs, who came into the district, purchased existing mills, developed machinery and increased output. Money was to be made in abundance and those engaged in the industry became very wealthy. In addition to the trade facilities afforded by the Newry Canal which served as the principal means of goods transport, there were the properties of the Bann water which were excellent for the whitening of the linen and, of course, the easily accessible water power.
During his years in Gilford, George Law extended his business interests by building a new beetling mill to the south of the present Gilford Castle. He also erected a new weir and widened the mill race to generate more power and thus increase production. When he died in 1802, his property became the subject of a law suit in Chancery between members of the Law family. Eventually the property was purchased by his nephew, Hugh. With the increased industrial development, there was the ever increasing need for labour and accommodation of a sort.
Sir James Johnston granted 46 leases for the building of houses on Castle Hill between 1807 and 1811. It is interesting to note that in each case there is a covenant that the or his assigns should within one year, "erect on the said granted premises one dwelling house, 40 feet in front and well dash, rough cast and whiten the same every two years and put sash windows in the said dwelling house." Unfortunately nothing now remains of this early development.
In 1835–1836 there opened a new era in the industrial history of the locality. About 1834, Hugh Dunbar, late of Huntly Glen, near Banbridge, where he carried on a linen thread and brown linen manufacturing business, conceived the idea of erecting flax spinning mills and linen thread manufacturing on a large scale in Gilford. To do so he obtained free farm grants from Hugh Law of the Corn Mill; from James Uprichard of lands at Banvale to construct a tail race and from WM McCreight lands on the opposite side of the river to the proposed mill. The original partnership was formed by Hugh Dunbar and WA Stewart of Edenderry, Banbridge and business commenced on 4th February, 1836, in premises in Mill Street. The dyeing houses were located at the rear of the present library. Having obtained the necessary lands and water rights, building of the large mill complex commenced in 1837. In 1837 Stewart died and Robert Thompson entered into a partnership with Dunbar to form Dunbar Dickson & Co. Thompson died in 1839, and having bought out his share, Dunbar now formed a partnership with John Walsh McMaster from Armagh. In the same year, James Dickson, elder son of Andrew Dickson of Glenconway, Co. Antrim, together with John McMaster became partners with Hugh Dunbar in his several trades of flax spinning and thread and linen manufacturing. The firm began to trade under Dunbar McMaster and Co. for flax spinning and linen thread and Dunbar Dickson and Co. for brown linen. Dunbar himself became the exclusive owner of the lands, mill buildings, workers' houses
At the beginning of this partnership, the mills at Gilford were substantial enough to permit the commencement of the business but for some time longer until 1843, part of the business, that of the manufacture of brown linen continued to be carried out at the Huntly Glen, Banbridge.
Completion of the Spinning Mills at Gilford took place in November 1841, and an extract from the Northern Whig of November 22, 1924, recalls the occasion, "19th November, 1841 was a great day in Gilford when one of the most splendid soirées ever held in this part of the country took place at the Works of Messrs. Dunbar, McMaster & Co. in the reading room and library belonging to the establishment. The proprietors, it seems, have just finished a large building for the manufacture of thread and this was appropriately fitted out and beautifully ornamented for the occasion. Upwards of 800 sat down to tea which was arranged in fine style under the able management of Mr. James Beck and company with a well selected committee.
After the company regaled themselves with a plentiful supply of good things of this life, dancing commenced and was kept up to a late hour. At occasional intervals lemonade was served with cakes and fruit. Several of the operators enlivened the company with song. A great many ladies and gentlemen from the surrounding neighbourhood and also from Belfast were present and seemed highly gratified with the proceedings of the evening. Mr. and the Misses Dunbar likewise honoured the soiree with their presence and appeared highly delighted especially Mr. Dunbar who, at all times, takes great interest in the welfare of his workers and spares no expense in making them comfortable. He has erected a hospital for the sick to the support of which he contributes very liberally. In fact, he has done everything which generosity and human feeling can suggest for the benefit of those employed at the Gilford works. Great credit is due to Mr. McMaster – one of his partners of the establishment. He used every exertion in his power to promote the comfort of the large assembly. The company retired at a reasonable hour, apparently highly delighted with the entertainment."
To accommodate the large number of workers encouraged to come to Gilford in search of employment mainly from Counties Monaghan, Fermanagh and Armagh, a huge house building project was begun. Altogether 180 houses were built in close proximity to the mill such were the numbers that came from the Keady district of Co. Armagh that Hill Street was known locally as "Keady Row." It was in this street that 2 houses were set aside and converted into a hospital for the sick of the town. From valuation field books many of these "two up, two down," type houses accommodated two families. It is not surprising that during the famine period, large numbers suffering from fever were accommodated in this well strategically erected hospital at the extreme north–east of the town. Though the records for the Banbridge Union Workhouse aren't complete it is known that a substantial number of people from the neighbouring townlands in the Lurgan Union died in the Lurgan Workhouse during the famine period. It was quite the task in supplying houses to accommodate the ever increasing population within the town of Gilford.
In a letter from an emigrant to his uncle, Mr. James Beck (mentioned in the report of the soiree), dated September 24th, 1848, from Dinsmore, Shilley Co. Cincinnati, he states:
"With great pleasure I received your letter dated 14th June, I received it the 10th July. It astonishes me to hear of the rapid improvement of Ireland; in my day there was no such factories as you are concerned in. And it also seems strange that Common work hands in that country get but £15 or £20 per annum and that Archabald and you get so large salaries.” It is certainly implied that the workers, despite the industrial advances, had poor wages, while management had comparable very much higher salaries.
In 1849, the following letter was circulated in the hope of establishing a market which would bring a degree of prosperity to Gilford and also attract business to the area.
Sir, A meeting of the Inhabitants of Gilford, will be held in the National School, on Saturday next, the 3rd of March, at the hour of 2 o'clock, for the purpose of adopting a requisition calling upon the Seneschal of said Manor, to convene a public meeting of the Inhabitants of Gilford and its vicinity to take into consideration the priority of having a weekly market established. Your attendance is particularly requested, Franklin McCreight Secretary, Gilford.
It astonishes me to hear of the rapid improvement of Ireland
Sewing Machine Gazette January 1881
Advertisement for Dunbar McMaster & Co
Coincided with the American Civil War between
Dunbar, Dickson & Co. were extremely valuable and goods stamped with the said trade marks commanded a much higher price.
During the 1840s the firm provided schools under the National Board of Education. Sites for the Roman Catholic and Presbyterian Churches were presented by individual members of the firm. In the case of the Church of Ireland, Mr. John McMaster was a large subscriber to the actual cost of the building and the parsonage on the Stramore Road was erected at his own expense. Mr. Hugh Dunbar himself did not confine his generous liberality to the provision of Churches and schools. He concerned himself with the temporal welfare of his workers. It is recorded that he was a man of extraordinary generosity. He had a list of 400 poor people whom he served weekly at his own house with financial assistance. Having died suddenly in 1847, while dispensing his alms, the piece of money he was about to give was still found in his hand after death.
In 1858, McMaster purchased the Misses Anne and Jane Dunbar's share for £20,662 and the lands, buildings, etc. for £25,000, the latter to be held by him as his property, the partnership paying him for the use; each partner was to have a separate interest in proportion to the sum bought in by him and at the end of eight years any surviving partner might by a year's notice dissolve the partnership and be paid the value of the shares.
The great linen boom took place during these years which, in fact coincided with the American Civil War (1861–65). Grade reached the highest peak. Sales in the year ending 31st March, 1866, amounted to over £1,000,000. McMaster and the Dickson Brothers became very wealthy men and it was during this period that the latter built Elmfield and Gilford Castles.
Built, literally over the River Bann, the water of which is famous for it’s bleaching power.
However disagreements took place and on 1st April, 1866, McMaster served notice on his partners that the partnership was dissolved from henceforth, the trade of "Dunbar, Dickson and Co" would be carried on by him in partnership with WM Spotten and James Douglas of New York under the style of "WM Spotten and Co. successor to Dunbar, Dickson & Co."
A famous law suit followed with the petition filed by Benjamin Dickson on 6th April, 1866, stating said business was carried on as well at the Gilford premises as also at certain warehouses and premises at Belfast, Dublin, London, Manchester, Glasgow and New York and by agents, travellers and correspondents in almost all parts of the world…that the goodwill and trademark and name, 'Dunbar, McMaster and Co.' and 'Dunbar, Dickson & Co.' were extremely valuable and that the goods stamped with the said trade marks commanded a much higher price in all markets than other goods of the same description. That stock in trade at the last half–yearly estimate was upwards of £500,000.
This petition came before the Lord Chancellor of Ireland 24th–28th May, 1866. It was decided that John Walsh McMaster was absolutely entitled to the goodwill and trademarks of the partnership. However, the next year the Court of Appeal overruled this decision on 28th June 1867. McMaster carried it to the House of Commons which finally reaffirmed the decision of the Lord Chancellor. Bonfires raged in Gilford at the verdict, giving testimony that the workers supported the claims of McMaster.
Gilford MillsMcMaster continued to live in Dunbarton House overlooking the Mill and died in 1872 at the age of 53. He left 12 children. His eldest son, Hugh Dunbar McMaster being named after the founder of the Mill. Six other sons were mostly engaged in the linen trade at home and abroad with the exception of one son who became a clergyman and ministered to his flock in England. McMaster is buried in Tullylish Old Churchyard. By his will, he left all his land, etc., to the eldest son, with Dunbarton, House (after life interest to his widow), and various other legacies.
In spite of difficult conditions, Hugh Dunbar McMaster carried on a very successful flax spinning and thread manufacturing business. Huge sums of money were used to improve the layout of the works, the erection of new buildings and the installation of plant and machinery. A large reservoir near the works was erected for fire extinguishing and was connected with hydrants and hose in every part of the mills, so that a conflagration that occurred in 1869 when £40,000 worth of property was destroyed, was not likely to happen again. Towards the end of the century, the Gilford mill complex was reckoned to be unsurpassed in the whole of the British Isles in the completeness of its resources for all the processes of the industry.
The economic success story of this industry in Gilford was such that it was necessary and commercially profitable to open a mill in Greenwich, New York, in 1880. It was managed by Mr. John McMaster and was called Dunbarton Mills. Workers emigrated from Gilford to man the mill and an examination of the population figures for the period will reveal that the town showed a decrease of approximately 50%. This can be attributed, in part to the attraction of the new mill in America. A Grocer's advertisement of the time indicates that he has undertaken an emigration agency. No doubt to meet the demands of those who decided to leave and find "better conditions" elsewhere. It is interesting to read that in "Industries of Ireland" Published 1891, when referring to Gilford Mill it states, "To all these advantages, as regards water for bleaching and dyeing and motive power, must be added cheapness of "labour. . ." No wonder there was a steady demand for work elsewhere.
In 1886, the firm became a limited company and Mr. Hugh Dunbar McMaster conveyed the whole of his property, lands, mills, etc. under certain covenants. In 1901 he decided to join the great linen thread combine in which Barbours of Hilden were prominent. Up until his death in 1908, he took the place of his father in the industrial and social life of the area. He was survived by his wife, Florence, a daughter of Major General Saxton of England and it was to her homeland she returned after her husband's death.
A large lampstand was erected after his death to his memory. This stood in a prominent position in the Square, but with the development of the road and widening of the streets, it was removed only to be re–erected without its lanterns and now stands rather inconspicuously in the corner of the lawn in front of the library.
Gilford Mill has survived the passage of time and the depressing economic ills of the linen industry but its past glory will not be easily forgotten. The thread produced here was world famous and gained many eminent awards at international exhibitions at home and abroad including a prize medal for "great general excellence" at London 1862, 2 medal in Dublin 1865 for "superior quality," a medal for "superior excellence" at Philadelphia 1876 and a special gold medal at the Toronto Exhibition 1880. The "British Trade Journal" of 1890 states: "The success of the firm as manufacturers of yarn and thread must be attributed in no small degree to the exceptionally favourable position of their works. They are built, in part, literally over the River Bann, the water of which is famous for its bleaching power.
The extremely fine white and even yarn required in making lace which sells in London at fabulous prices is spun and bleached in this district and is largely produced by this firm. So well appreciated is the river that linen is sent long distances, even, from Belgium to be bleached on the banks of the Bann. The fine quality threads spun for certain lace and embroidery may be inferred from the fact that a length of thirty–six thousand yards weighed only one pound. Commercially, Messrs. Dunbar McMaster & Co. were known all over the world. The looms of Europe wove yarns spun in Gilford. Gilling twines were exported to the Adriatic and Mediterranean countries, twine for salmon–fishing to British Columbia, carpet threads, book binders' thread, extra strong threads for leather and thick cloths, and fine threads for the sewing machinist and lace–maker were exported to United States, South and Central America, Brazil, Australia and the rest of the British Colonies."
The loom’s of Europe wove yarns spun in Gilford.
Even as early in its history in 1849, on the occasion of Queen Victoria's visit at Belfast, "Dunbar McMaster & Co" and "Dunbar Dickson and Co." were chosen to exhibit for the Royal viewing. "The Northern Whig" Tuesday 14th, 1849, reports that "Dunbar, McMaster and Co." exhibited the following:
Specimens of foreign flax – Riga, Dutch, Flemish, French and Egyptian. Hackled flax both Irish and Foreign. Full series of tow, linen yarns and sewing thread."Dunbar, Dickson & Co." had the following on exhibition:
4 pieces 4–4 extra stout unbleached mill spun linen. 10 pieces 4–4 extra stout bleached linen for family use. 10 pieces 4–4 stout mill spun linen: 1 piece sheeting 117 inches wide. Brown damask linen made up for North and South America.
Today the firm still remains in business. It is now Dunbar, McMaster Ltd. No longer is it the thriving industry of former years. However, it has survived the recession in the linen trade and in doing so will be in an advantageous position to benefit if the industry should expand, as predicted. No longer does it echo to sounds of 1,500 workers as in its early days of existing but in the 1980’s the labour force of 150 produced flax yarn that was exported to Greece, Italy, Belgium etc. The remaining hope is that once again it may find its best quality flaxes used in the process being grown at home, instead of being imported from Courtrai in Belgium.
The remaining hope is that once again it may find its best quality flaxes used in the process being grown at home.
Once the largest industrial undertaking on the Upper Bann, production ceased at Dunbar McMaster’s mill in the 1980s and the site currently lies semi–derelict awaiting a new use.
The site currently lies semi–derelict awaiting a new use.
Gilford Mills2024
he worked
I worked at the bonding perm. cleaner there
Flax Mill — Eliza Heron and Robert MClements Scutch mill
Flax Mill — Mary McAneeny Flax Mill and Store
Flax Mill — George Crawford
Weaving Factory — Banbridge Weaving Co Ltd Office
Weaving Factory — Thomas Ferguson Damask Factory
Weaving Factory — Banbridge Weaving Comapny Ltd
Weaving Factory — Robert McClelland weaving
Weaving Factory — Smyth Weaving Company Ltd
Beetling Mill — Anthony Cowdy and sons Beetling Mill
Beetling Mill — Robert McClelland beetling mill
Beetling Mill — Uprichard and Lindsay Beetling Mill
Beetling Mill — Frederick Robert and Samuel McCaw Beetling mill
Bleach and Beetling Mill — William Smyth and Co Ltd Beetling Mill
Flax Mill — Eliza Heron and Robert MClements Scutch mill
Flax Mill — Mary McAneeny Flax Mill and Store
Flax Mill — George Crawford
Weaving Factory — Banbridge Weaving Co Ltd Office
Weaving Factory — Thomas Ferguson Damask Factory
Weaving Factory — Banbridge Weaving Comapny Ltd
Weaving Factory — Robert McClelland weaving
Weaving Factory — Smyth Weaving Company Ltd
Beetling Mill — Anthony Cowdy and sons Beetling Mill
Beetling Mill — Robert McClelland beetling mill
Beetling Mill — Uprichard and Lindsay Beetling Mill
Beetling Mill — Frederick Robert and Samuel McCaw Beetling mill
Bleach and Beetling Mill — William Smyth and Co Ltd Beetling Mill
Bleach Mill — Edenderry, Mill Mount
Bleach Mill — The Banbridge Bleaching Co
Bleach and Spinning Mill — Frederick Hayes and Co
The Company bears the name of the founder, Thomas Ferguson (27th April 1820- 24th February 1900), who was born in Clare, near the village of Waringstown in Co. Down, where his father John farmed. At that time the locality was a centre of Irish Linen hand weaving and this activity was commonly combined with farming. His father died in 1831, and he was orphaned, when his mother died in 1836. It is believed that the Rev. John Johnston (1786-1862) of Tullylish Presbyterian Church, became the guardian of Thomas, and his brother John. Thomas Ferguson’s guardian saw to the completion of his schooling and then arranged for him to be apprenticed to Brice Smyth (17961851) of Brookfield, Banbridge. This remarkable man, even though he was blind from smallpox as a child, was a very skilful hand loom weaver of fine linens, and a noted teacher of his trade. It was said Brice Smyth was also able to examine the brown webs as they were brought into his warehouse by the weavers, and in doing so he could have formed an accurate judgment as to whether, or not, the cloth had been correctly woven.
His apprenticeship completed, Thomas Ferguson left Brookfield sometime around 1845 and set up on his own as a hand loom weaver in Banbridge. It is believed he started business in a house in Church Square, in the town. In 1854, by then firmly established, he acquired a lease for 999 years of the site on which the Company operated for 137 years. The factory on this site was known as Edenderry Works.
In 1854, by then firmly established, he acquired a lease for 999 years of the site on which the Company operated for 137 years.
There he continued with his hand weaving business, until in 1866 he formed a partnership with his two brothers-in-law, James and Benjamin Dickson. Following the formation of this Company, Dickson, Ferguson & Co, the partners decided to build a new factory. Work was started in 1867 on the site which Thomas Ferguson had earlier purchase the lease, and the factory was equipped with steam powered looms with Jacquard machines for damask weaving.
In 1883 the two Dickson brothers retired from the business. The Company with its present title was incorporated in 1884 with Thomas and his sons, Howard and Norman, being the first directors with another son, Thomas S. as secretary. In later years three grandsons of the founder entered the Company while two great-grandsons and one great–great–grandson were all actively involved in the business. To find out more about the history of linen in Banbridge and Thomas Ferguson.
In December 1988 Thomas Ferguson & Co. Ltd. joined the Franklins Group. This was formed by another textile Company based in Banbridge Franklins International Ltd. Franklins is the premier badge, label and embroidery specialist in the UK and Ireland and was founded in 1835, in Coventry.
Franklins International Ltd supplies to youth organisations, commercial companies, charities, military, security and emergency services and manufacturers at local, national and international levels within the sports, industrial, fashion, career wear and promotional markets. In 1999 Franklins Group acquired Brownlow Textiles Ltd; currently known as Brownlow Linens. Brownlow is now a brand of Thomas Ferguson Co. Ltd.
In November, 2012 the John England brand came under the same ownership as Thomas Ferguson. John England (Banbridge) Ltd. is a designer and wholesaler of apparel and interior fabrics, and carries a wide range of unique off-the-shelf linens.
In January, 2015 John England (Banbridge) Ltd. joined Franklins Group. Now as a sister company of Thomas Ferguson both companies are working very closely together. John England exclusively sells fabrics by the metre and adds a wide choice of unique stock fabrics for the fashion and apparel, curtain, upholstery, theatrical linens, film productions, etc. to the range. It also designs unique fabrics along with our customers; to meet their specific requirements.
4th December 2023
Growing up, we thought there was for Irish linen.
We are the double damask weavers in the world. very last
4th December 2023
Frederick William Hayes was born on 11th June, 1802, the third son of William Hayes of Millmount. William Hayes came as a young man to Banbridge, took over the old Reilly corn mill at Millmount, in the townland of Edenderry and started a bleachworks there.
In 1834, Frederick William Hayes acquired glebe land at the rear of Seapatrick Parish Church and built weaving sheds close to the River Bann. He also built Seapatrick House at that time, on the Banbridge side of his new weaving premises. Seapatrick House was built in the style of the great Linen Houses of the period, incorporating a gate lodge and driveway from Lurgan Road, with a lawn sweeping down to a riverside driveway fronted by pillared double gates at the bottom of Kiln Lane. His wife, Isabella Boyd, was the daughter of the owner of the Belfast Foundry, and they had four sons and one daughter at Seapatrick House.
In 1840, Frederick William Hayes ceased production of linen cloth and started linen yarn spinning and thread making in the premises. The weaving sheds were single storey and stone built with "Northlight" roofing. The "Northlight" roof was very popular at that time in the construction of factory premises. It consisted of a series of inverted V structures, which, when glazed on the short side, provided a maximum of natural light for the weaving operators below. In contrast, further buildings at Seapatrick Mills were in keeping with the traditional mill buildings of the period, strong, stone built edifices three or more storeys high. During those early years, Frederick William Hayes established a good manufacturing base for his products, which were given the name "Royal Irish Linen Threads". He died on 13th October, 1853, aged 51 years and was interned in Seapatrick Churchyard. His eldest son, William Hayes, succeeded him in running the mills.
William Hayes married his cousin, Martha Mary Law of Hazelbank House, Lawrencetown, in 1855 and took up residence in Seapatrick House. During his period of management with F.W. Hayes & Company, he successfully extended the premises. It was recorded at the time that the firm occupied 60 acres and employed 700 people. To meet the needs of an expanding workforce, William Hayes embarked on a programme of house building. Rows of workers' dwellings were built on the right-hand side of Kilpike Road, from the junction with Lurgan Road. He also built a short terrace of management houses fronting the Lurgan Road, opposite the churchyard. A corner shop was provided at this point, which was controlled by the company, to meet the needs of the workers and their families. The company also built a new schoolhouse of character design, in dark stone, opposite the entrance to the mills, for the education of the children of the employees.
Rows of workers’ dwellings were built on the right-hand side of Kilpike Road.
Trading warehouses were established in major English and Scottish cities during the period and a selling agency, H.B. Shaen & Company was arranged in New York. William Hayes had four sons and two daughters. He died on 12th July, 1876 and was interned in a new burial plot in Seapatrick Churchyard. Although still a minor, the eldest son, Frederick William Hayes II succeeded his father in running the firm. The management team was strengthened by the recruitment of Charles Hugh McCall as general mill manager. A few years later Samuel George Fenton, a Belfast man, joined the firm to assist with the overall running of the mills.
Trade fairs were held regularly in major cities during the latter years of the nineteenth century.
F.W. Hayes & Company won gold medals for the excellence of their linen threads at Dublin 1882, Cork 1883 and Belfast 1895. Before the days of aerial photography, the mill and factory owners employed professional artists to paint an "impression" of their manufacturing premises. These pictures were later colour printed on large advertising show cards, for distribution to trading warehouses and overseas agencies, as well as being used on printed packaging materials.
F.W. Hayes & Company won gold medals for the excellence of their linen threads at…
In the early years at Seapatrick Mills Irish flax was the standard raw material for the manufacture of linen yarns for thread making. This was readily available from scutching mills, through established flax markets held in the provincial towns. As the years of the 1800's progressed, foreign flax was steadily coming in. Russian flax, flax from the Baltic States and Belgian flax were becoming popular with the mill owners of Ulster. The flax grown around the Belgian town of Courtrai eventually became established as the superior flax for linen manufacture. But the spinning and thread making machinery changed little over the period. Machines used for preparing, spinning and twisting the linen yarns were highly engineered. Most of the machinery used for these operations was manufactured in the Province, the leading makers being, Jas. Reynolds & Co, Linfield Road, Jas. Mackie & Sons, Springfield Road, and Fairbairn, Lawson, Combe, Barbour, Limited, Albert Foundry, Belfast. These firms had developed on the success of the linen industry. The machinery used by F.W. Hayes & Company for the polishing, winding, copping, spooling, and balling of linen threads was usually purchased in the Manchester area, where a substantial cotton thread industry was being supplied. These machines could handle both linen and cotton threads.
Many manufacturing operations were being done by hand at Seapatrick Mills in the second half of the nineteenth century. The preparation of the flax fibre for later preparing and spinning operations being a good example. The natural flax was taken through a series of combing operations, called roughing and hackling. Rows of men in the flax lofts pulled "pieces" of flax through blocks of combing pins to entangle the fibre and remove the ancillary "tow" from the main fibre, called "line". After the turn of the century, large flax hackling machines were introduced at Seapatrick Mills to considerably improve the efficiency of these operations.
Further building of houses for the workers in the mills took place around 1890. An attractive red brick terrace of ten management houses (Milfort Terrace) was erected on Lurgan Road, opposite the entrance to Seapatrick Rectory. A red brick terrace of 14 workers' houses (Bannview Terrace) was built at the other end of the property, on the road to Lenaderg. Finally, eight semi-detached houses (Seapatrick Villas) were erected opposite St. Patrick's Chapel-of-ease (the "wee" Church). In 1895, Frederick William Hayes II with his wife Lily, left Seapatrick House and took up residence at "Clareen", Sydney Parade, Dublin. He died there on 2nd April, 1896, aged 37 years and was brought back to Seapatrick Churchyard for burial. The last member of the Hayes threadmaking family to reside in the Seapatrick district was John Law Hayes, a younger brother of Fredrick William Hayes II. John Law Hayes was not involved in managing the family firm, but lived, with church benevolence, at Seapatrick Rectory until he died, unmarried, on 7th March, 1934, aged 74 years.
As the years of the 1800’s progressed, foreign flax was steadily coming in.
The most profitable years for the firm were the years of the American Civil War, 1860–65.
Samuel George Fenton became the first managing director of the Private Limited Company of F.W. Hayes and moved into Seapatrick House with his wife, Lillie Jane. Their first daughter, Dorothy Caroline Fenton, was born there on 2nd October, 1896. A second daughter, Irene Lillie Fenton was also born there on 22nd June, 1899. He was to take F.W. Hayes & Co., Limited, into the amalgamation of thread manufacturing firms that became The Linen Thread Co., Limited, before the new century dawned.
It was once claimed by a leading linen thread manufacturer that the most profitable years for the firm were the years of the American Civil War, 1860-1865. This can be understood when consideration is given to the amount of linen thread required to manufacture huge quantities of military ordnance, for two opposing armies in civil conflict, on that vast continent. In those years, manufactured supplies required on the American mainland were still largely bought from the British homeland. The profitable years of the early 1860s placed some leading textile firms in a strong economic position, looking for manufacturing development. A very high import tax on linen thread, imposed by the United States Government at that time, made the establishment of American thread mills a very lucrative proposition.
F.W Hayes & Company amalgamated with The Linen Thread Company in 1899, as did Dunbar, McMaster & Company, with both their Gilford and New York Mills, in 1901. Other British linen thread manufacturers who joined at that time were : Ainsworth & Sons, Cleator Moor, Cumberland; Robert Stewart & Sons, Antrim Street, Lisburn; and Crawford Brothers, Beith, Ayrshire. More than 30 years later the Group purchased the thread manufacturing interests of Lindsay, Thompson & Co., Limited, Flax Street, Crumlin Road, Belfast.
It was primarily intended that the new company would market the product brands of the amalgamated mills. The identity of the mills, the future development of their prosperous personal traditions and immensely valuable local skills would be preserved. However, in a few years, amalgamation had prompted both rationalisation and standardisation in the subsidiary mills. Early in the 1900s, thread manufacturing ceased at the Gilford Mills of Dunbar, McMaster & Company. The product brands were retained but the production of the sole sewing threads and shoe yarns was transferred to Barbours Hilden Mills, while Seapatrick Mills undertook the manufacture of the linen sewing threads, bookbinders threads and carpet threads. This programme also took place in the mainland mills. Gilford Mills became a yarn spinning and bleaching unit, their purpose, to augment the yarn supplies of the other group mills and to market a range of linen yarns to weavers and other industrial uses at home and overseas.
With the influx of new production, extensive building was undertaken at Seapatrick Mills. A new office block was built close to the churchyard wall to house both management and administrative staff, a works canteen, beside the main gate; a flax machine room; rove store; bundling room and an impressive new thread mill. This housed the thread polishing department on the ground floor and the thread making-up department on the second floor. The building incorporated a flat roof with a parapet wall, to allow the addition of a third storey, should this be required at a later date. Unlike the original mill buildings of Frederick William Hayes, which were largely stone built, all the new buildings were in a very attractive red brick finish.
After the amalgamation, the head office of The Linen Thread Company was established at 52 Bothwell Street, in central Glasgow. This building also held the sales department and accounting section. F.W. Hayes & Company had established independent trading warehouses and selling agencies at home and overseas, from the middle of the 1800's These were run down under the central marketing plan of the new company. In the next few years, The Linen Thread Company established sales outlets in all corners of the world for the distribution of yarns, threads and nets manufactured by the amalgamated mills. These roughly took the form of company owned stock warehouses in the British Isles and English speaking countries overseas, registered selling companies in the European sector and contracted franchise agents in other foreign markets.
Seapatrick Mills had long specialised in the manufacture of linen jacquard harness cord. This was used in the weaving factories from 1870 for the manipulation of punched cards on a jacquard weaving loom, to produce intricate damask patterns in the cloth. Linen harness cord was of heavy construction, having had a double twisting operation. It was found that a new product could be produced on the technology of the harness cord and in the 1920s Hayes Twisted Flax Fishing Lines went on the market. They were particularly successful in Norway, South Africa and Australia in the years ahead.
Seapatrick Mills had long specialised in the manufacture of linen jacquard harness cord.
The success of the amalgamation was being felt at Seapatrick and the Hayes Company undertook a further building programme, to update their housing stock, in the years leading up to World War I. Land was acquired, from the church authorities, opposite the entrance to the mills and 28 semi-detached houses (Hayes Park) were built. The plans for the estate were prepared by William Larmour, the Banbridge architect, to an idea put forward by one of the Barbour ladies of Hilden. This involved the building of English style cottages in grey ornamental block, with high pitch roofs and dormer-type windows. The cottages were laid out with large gardens and planted with trees, shrubs and hedges, giving the appearance of a garden village. The estate was served by a winding driveway. Samuel George Fenton, who successfully directed F. W. Hayes & Company for over forty years, died on 5th September, 1936, and was interned in Dundonald Cemetery. John Doherty Barbour, of Lisburn, became the new managing director.
30th September, 1962.
In 1954, The Linen Thread Company sold seven of the U.S. mills controlled by "The Linen Thread Co Inc." to an American textile organisation and undertook a programme of diversification into engineering and electrical goods manufacture. The name of the company was changed to Lindustries Limited, to reflect the changing trend and The Linen Thread Company was reduced to the status of "Textile Division" in the new Group.
In 1957, the Finlayson, Bousfield Mills at Johnstone, Renfrewshire, were closed down. This reflected a declining world market for linen threads, against the new synthetic threads in nylon and "terylen”. Alexander W. Fleming left Seapatrick Mills to take-up the post of manufacturing director in the Textile Division of Lindustries Limited. He was replaced by John Francis Pim, who handled his responsibilities in F.W. Hayes & Company with a youthful enthusiasm. This extended to starting Seapatrick Mills Recreation Club, that excelled on the football field, and at some pleasant dances organised in the village school.
Early in the l960s the American consultancy firm, Kinsey & Company was commissioned by Lindustries Limited, to carry out a survey on the activities and efficiencies of the home mills. From their report a decision was taken to close Seapatrick Mill on 30th September, 1962. After a progressive rundown of production operations and the transfer of machinery and material stocks to Hilden Mill, the premises became vacant, thus ending 120 years of thread making at Seapatrick.
maybe half an hour or a quarter of an hour before time to start, and then that was the final one at eight o’clock.
You wouldn’t have been late, maybe a few minutes.
There would have been no remarks passed. You went in and got your work and started right away.
Flax Mill — Scarva, Samuel Chambers Flax Mill 1918
Flax Mill — Legananny, Silverford Cooperative Flax Society 1925
Flax Mill — Drumsallagh, Sarah Magaw Flax Mill 1927
Flax Mill — Greenan, James Little Flax Mill 1876
Flax Mill — SC Cupples Flax Mill 1902
Flax Mill — Drumnahare, John McClelland Flax mill 1833
Flax Mill — Falkiner B Small Flax Mill 1914
Flax Mill — Ballymacaratty Beg, Thomas Woods Flax Mills 1906
Flax Mill — Scarva, Samuel Chambers Flax Mill 1918
Flax Mill — Legananny, Silverford Cooperative Flax Society 1925
Flax Mill — Drumsallagh, Sarah Magaw Flax Mill 1927
Flax Mill — Greenan, James Little Flax Mill 1876
Flax Mill — SC Cupples Flax Mill 1902
Flax Mill — Drumnahare, John McClelland Flax mill 1833
Flax Mill — Falkiner B Small Flax Mill 1914
Flax Mill — Ballymacaratty Beg, Thomas Woods Flax Mills 1906
By 1927 all of the flax mills had shut down, as flax production swiftly moved abroad, with importation of flax increasing.
Flax Mill — Carnmeen, James Henning Flax mill 1901
Flax Mill — Desert, John Edgar Flax Mill 1925
Flax Mill — Bessbrook Mills, 1973
Flax Mill — Castle Enigan, Andrew McMinn Flax Mill 1923
Flax Mill — Longhorne, Michael Torley Flax Mill 1921
Flax and Corn Mill — James McGaw Flax Mill 1874
Bleach Mill — Duncrue on the Halstead Co 1906
Weaving Factory — Thomas Gaffikin Weaving Factory 1925
Flax Mill — Carnmeen, James Henning Flax mill 1901
Flax Mill — Desert, John Edgar Flax Mill 1925
Flax Mill — Bessbrook Mills, 1973
Flax Mill — Castle Enigan, Andrew McMinn Flax Mill 1923
Flax Mill — Longhorne, Michael Torley Flax Mill 1921
Flax and Corn Mill — James McGaw Flax Mill 1874
Bleach Mill — Duncrue on the Halstead Co 1906
Weaving Factory — Thomas Gaffikin Weaving Factory 1925
Linen had been carried on at Bessbrook as early as 1760 by the Pollock family. The property was bought in 1845 by the Quaker Richardsons, whose connection with linen went back to 1654.
The first power flax-spinning mill in Ireland was in Bessbrook which subsequently became a substantial town with an estimated population in 1887 of 3,500.
To facilitate it the lake at nearby Camlough was enlarged (a fact already alluded to) and its water used to regulate the stream that supplied power to drive the mills for grinding corn, scutching flax and bleaching linens.
By the mid nineteenth century it was only in a few locations that the old irregular cluster of farm dwellings known as clachans, survive. Instead bogs had been drained, mountain slopes brought into cultivation and farmhouses built down laneways or sited at intervals along the new, straight main roads.
The clachans (e.g. at Clontygora, Cornamuchlagh, Ballynamadda, Lislea and Pollynagrasta) may have represented elements of the Pre-Plantation settlement pattern and in general they were located alongside the older roads which followed spring lines along the lower hill slopes: here farming communities could have benefited from rough pasture on the hills and cultivated land in the valley bottoms.
At one time, Bessbrook linen was among the finest in the world, and the linen mill provided most of the employment in the village. Tenement houses were constructed for the mill workers, many of which were of such good quality that they are still inhabited today. Each house also had an allotment garden for the growing of vegetables, and the area of the village where they were situated is still known as ‘The Gardens’, although the allotments themselves have been replaced by further housing. Most of the buildings in the village are constructed of granite, which is abundant locally.
In contrast, the large houses of the landlords set within wooded estates, parklands and gardens, represented the new features of the 19th century landscape. Examples are numerous but in our area we might name Heath Hall in Ballymacdermott townland, Killeavy Castle and Halls’ Narrow Water Castle.
Linen had been carried on at Bessbrook as early as 1760 by the Pollock family.
After a fire in 1839, the next carnation of the factory began in 1845 when the property was put on the market. Around this time the family which would leave a lasting impression on the mill and the community, the Richardson’s, were looking to expand their mill business and by 1846 the spinning mill was up and running.
In 1878 the company became known as The Bessbrook Spinning Co. Ltd, though the Richardsons were still firmly in control. In 1913 the company operated 20,000 spindles and 760 looms making it the seventh largest Irish spinning and weaving firm. The Spinning Company closed down in 1973 throwing most employees out of work. The Ulster Weaving Company carries on the linen business at Bessbrook until 1987 when it moved all production to its Belfast headquarters. The Craigmore viaduct on the Great Northern They can be seen in the background. Railways were important in linking customers and suppliers. A railway siding ran right into the works.
As with the rest of the Northern Ireland linen industry, at this time, the Bessbrook Spinning Company flourished over the next the 30-40 years, peaking around 1900.
In 1913 the company operated 20,000 spindles & 760 looms making it the seventh largest Irish spinning and weaving firm.
Peter Bradley writes of Bessbrook long ago. ‘I was born in Newry in 1917 but when I was very young the family moved to Hill Street (Quarry Road) Bessbrook. These houses together with Flynntown (Rock Row) were built to accommodate the labourers at the local quarry.
I started school in Bessbrook Convent School in 1921 and in 1923 transferred to St Malachy’s Boys School where I completed my school Leaving Certificate in 1931. On my fourteenth birthday I was recommended by Mr Campbell who was the chief cashier of Bessbrook Spinning Company, to take employment as junior clerk in the Mill’s wages department.
At that time there were 2500 people employed by the company and my job was to stamp and date insurance cards and to post any mail. On Wednesday mornings I accompanied the chief clerk in the company’s Rolls Royce to withdraw the wages for the entire workforce. Two policemen, the chief clerk and me went into the Belfast Banking Company in Hill Street, Newry and the amount required would be withdrawn in cash.
In order to make it easier to make up individual wages, it was my job also to have a list of any individual coins or notes needed – shillings, florins, half-crowns, ten-shilling notes, pound notes and five-pound notes. The odd ten-pound note was also withdrawn but only very rarely because nobody ever earned as much as that in those days. The average earnings then was about one pound ten shillings per week. On returning to the Mill the wages were made up by the chief clerk on Wednesday evenings. They were stored in the main strong-room safe and paid out to the employees on Thursday mornings by Mr Honeyford.
The average earnings then was about 1 pound 10 shillings per week
While I was working in the wages office I attended night school in Newry Technical College where I studied shorthand and accountancy up to final balance. I then studied English and Latin in Stapleton’s Academy for two further years. I had an ambition to go into engineering and I left the Mill to complete my three-year course in ‘precision engineering’ and ‘workshop practice’ at Chester College of Technology. I then was employed by Cammill & Laird in the engine-repair shop and I worked there during the Second World War.
I returned to Bessbrook where I met and married Kathleen Kelly from Dorsey, Cullyhanna. We settled in Flynntown where we reared nine children. I was employed for a number of years by BICC where I worked as a machine-fitter. In Bessbrook we always had a number of good neighbours both in Rock Row and Quarry Row but the houses had no bathroom or flush toilets or hot water supply. In the early Seventies the houses were demolished to make room for the present Fr Cullen Park, where we finally settled.
John Feehan recalls how the hundreds of workers would arrive at the mill each day - “I remember the war type lorries of covered canvas, where everyone sat in lines in the back...they came from everywhere..Newry, Whitecross, Belleek, and Darkley....”
John himself walked to the mill where many a time he had to run the last few yards in order to beat the factory horn - “ I ran down Park Lane to be in time to get my clocking in medal ... (A coin the size of a large penny which had the worker’s individual details on it)...if you weren’t in before five to eight you were docked an hour’s wages...”
As an eager 17 year old, John Feehan spent a year at the mill just before it closed in 1971. John’s working day began at 8am and finished at 6pm, with breaks of half an hour for lunch and 15 minutes in the morning and the afternoon.
John worked in the “card” office where his job involved sorting the stiff-paper cards which were a vital part of the loom system. Carefully punched holes in the cards guided the looms along a predefined path. This area is now the army officer’s accommodation block.
to be in on time to get my clocking in medal…John Feehan
if you weren’t in before five to eight you were docked an hour’s wages.
Flax Mill — Tullycarn, William Liddell and Co Ltd 1927
Flax Mill — Coolsallagh, Thomas Taylor Scutch Mill 1924
Bleach Mill — Coolsallagh, John Stacker Bleachworks 1924
Weaving Factory — Ravernett Weaving Company 1927
Flax Mill — Tullycarn, William Liddell and Co Ltd 1927
Flax Mill — Coolsallagh, Thomas Taylor Scutch Mill 1924
Bleach Mill — Coolsallagh, John Stacker Bleachworks 1924
Weaving Factory — Ravernett Weaving Company 1927
By 1964 one third of Northern Ireland’s mills had closed. In 1973 William Ewart & Sons and William Liddell & Co merged to become Ewart Liddell and were acquired as part of the Coats Viyella Group. In the 1980s Ewart Liddell underwent a major modernisation programme. During the 1980s and 1990s the company’s luxury linen products could be found in stores such as Harrods, House of Fraser, Marks & Spencer and Bloomingdales in the US. The company’s international clientele continued to expand in the sales of linen tableware to airlines, including British Airways, Concorde, Qantas, Continental Airlines and Air New Zealand Hospitality clients included Raffles Hotel, Singapore, The Mandarin Hotel, Hong Kong, and the Ritz Hotel, London. At the turn of the century Coats Viyella put Ewart Liddell up for sale. Irish fashion linen supplier Baird McNutt bought the company renaming the company Liddell Limited. In 2004 the company was acquired by Hilden Manufacturing Ltd. In 2008 Vision Support Services acquired Hilden and Liddell. The Ewart Liddell factory no longer exists however the rich design heritage of Damask linen design has been preserved in the photographic glass plates archive currently housed in the Belfast School of Art, Ulster University.
In 1973 William Ewart & Sons and William Liddell & Co merged to become Ewart Liddell.
The earliest recorded date of 1919 can be found on an image of a design for the Hans Crescent Hotel.
The William Liddell Collection is an archive of 1600 photographic glass plates that were discovered during the dismantling of the EwartLiddell weaving factory in Donacloney, County Down, Northern Ireland in 2007. On first viewing the faint monochromatic image on the glass plate’s look like ghosts from bygone days of refined domesticity. However it became clear that these traces of linen splendour are but a hint of the unique and extensive record of an era of craftsmanship in both the design and production of Irish linen hidden within the William Liddell Collection. The discovery of the photographic plates has provided a rare opportunity to uncover and celebrate the often-understated artistic, design and technical skills of the generations of individuals working in the design offices of the textile industries in Ireland. The photographic plate preceded film and was used to capture images on a light sensitive emulsion of silver salts that coated the glass plate. The use of glass plates for photography declined after the 1910s yet this method of photography appears to have been used to record design work produced in the Liddell design office throughout seven decades of the twentieth century. The earliest recorded date of 1919 can be found on an image of a design for the Hans Crescent Hotel. The latest date recorded is 1972 on a design for South African Railways. This documentary practice appears to have effectively ceased after the William Liddell Company’s merger with the William Ewart Company in 1973 to form Ewart Liddell. It is extraordinary that this form of photographic record was kept and perhaps more astonishing that the observation of everyday affairs of a textile manufacturing design office were the subjects of such an extensive and persistent documentary endeavour.
Flax Mill — McDowell Fitzsimons Scutch mill 1922
Flax and Corn Mill — Magheralana Flax Mill 1834
Bleach Mill and Retting Works — Ulster Retting Ltd 1920
Weaving Factory — James Pennington Weaving factory 1921
Weaving Factory — Tullyherron, Waringstown Weaving Co 1927
Weaving Factory — Robert Liddell, 1923
Flax Mill — McDowell Fitzsimons Scutch mill 1922
Flax and Corn Mill — Magheralana Flax Mill 1834
Bleach Mill and Retting Works — Ulster Retting Ltd 1920
Weaving Factory — James Pennington Weaving factory 1921
Weaving Factory — Tullyherron, Waringstown Weaving Co 1927
Weaving Factory — Robert Liddell, 1923
Waring introduced weaving techniques from Holland and Belgium to the weavers of Waringstown.
Waringstown owes its existence, name and unique contribution to the development of the Irish linen industry to William Waring, who built Waringstown House, around which the village developed. Waring, who was anxious to introduce a prosperous industry that would employ local people, was among the first in Ireland to see the potential of linen. While the Irish wool industry, seen as a rival by the English, was almost taxed out of existence, the Irish linen industry was granted tariff protection and actively encouraged. Waring's vision was continued by his son Samuel, who was greatly impressed by the linen finishing techniques he saw on his travels in Holland and Belgium. On his return in 1688 these techniques were introduced to the weavers of Waringstown and the village soon acquired a reputation for the highest quality cambric and damask cloths.
At that time almost every house had it’s weaving shop attached with two or three looms.
1910
Double Damask Weaver, Waringstown.
An essential prerequisite to the Jacquard weaving process was a series of punch cards onto which the pattern, already hand drawn by the designer, was transferred as a series of holes. It enabled a primitive form of automation in weaving. The weaver could out the cards through the ‘engine’ in sequence by means of foot treadles. This caused selected threads to be raised so the pattern indicated on the punch cards was woven into the cloth. The Jacquard process enabled a hand-loom weaver to work on damask at home on his own rather than as before with as many as 16 helpers.
Flax Mill — Drumbroneth, John Mulligan Flax mill 1920
Flax Mill — Lurganbane Flax Mill
Flax Mill — Ballyvicknacally, McConvilles Mill 2024
Flax Mill — Ballyvicknacally, David Mussen Flax Mill 1927
Flax Mill — Church Street, Murphy and Stevenson Scutch Mill 1924
Flax and Corn Mill — John Graham and Sons 1926
Weaving Factory — Murphy and Stevenson Ltd Weaving 1920
Weaving and Shirt Factory — Brewery Lane, Harrison Brothers 1867
Bleach and Beetling Mill — Ballymaganlis, William McMurray 1897
Beetling Mill — Whiteabbey Bleaching Co House Beetling Mill 1907
Bleach Mill — Drummiller
Flax Mill — Drumbroneth, John Mulligan Flax mill 1920
Flax Mill — Lurganbane Flax Mill
Flax Mill — Ballyvicknacally, McConvilles Mill 2024
Flax Mill — Ballyvicknacally, David Mussen Flax Mill 1927
Flax Mill — Church Street, Murphy and Stevenson Scutch Mill 1924
Flax and Corn Mill — John Graham and Sons 1926
Weaving Factory — Murphy and Stevenson Ltd Weaving 1920
Weaving and Shirt Factory — Brewery Lane, Harrison Brothers 1867
Bleach and Beetling Mill — Ballymaganlis, William McMurray 1897
Beetling Mill — Whiteabbey Bleaching Co House Beetling Mill 1907
Bleach Mill — Drummiller
been in my family for years. So it has.
McConville’s water powered Scutch Mill close to Dromore Co. Down provides a unique insight into the ancient craft of the scutcher who separated the fibre from the flax plant. Eugene McConville kindly showed us around his flax Mill on Tuesday. Eugene has a wealth of information about flax and the processes involved in harvesting flax and preparing it for sale into the Mills who turned it into yarn. He kindly donated samples of flax in various stages of the processes involved in scutching for our education programme. If you are interested in visiting the Mill tours can be booked by contacting McConville’s Mill.
1940 up to 50 people were employed locally
Felix McConville, the grandfather of the present owners, came to Dromore in 1870 from his birthplace in the townland between Annaclone and Rathfriland. He married a lady called Mussen, whose family had been involved in growing flax in the Dromore area for many years, and it was here that the McConville connection began.
The present mill was constructed around the turn of the century with the large mill wheel used to drive the machinery coming from nearby. The wheel, cast in Geoghegan’s foundry in Lenaderg, had previously been used to drive a beetling mill on the River Bann. Beetling, the final process in the production of linen, is the smoothing of the cloth by the action of hammers, made of ash planks, falling on the cloth at regular intervals.
The process to produce linen begins many months before however, and in its day was a labour intensive industry providing employment to many people in rural Ulster.
The flax, once harvested, is stored for around 14 months. After storage, it is taken out and ‘retted’ i.e. soaked in large pools for about nine days to help separate the fibres from the inner core. Once taken out and dried, it is crimped to make it more pliable, and then placed in the scutch machine.
On opening the sluice gates the water begins to flow bringing the large wheel into life. By a series of belts and cogs the main spindle, containing sets of spokes, begins to spin. The still hard flax is inserted by hand into the spinning spokes and the transformation occurs. The hard inner core, known as the shives, breaks off leaving the soft and pliable flax behind. The flax now has the same consistency as fine silken hair resulting from the scutching process. It then began its journey to market and in the early 1900’s there was a flax market in the town of Dromore but this was thought to have closed in the 1920’s so the flax was taken to Banbridge and Ballynahinch.
The main mode of transport would have been the horse and cart and in latter years the lorry, but there was a considerable amount of flax taken to Belfast on the old Newry to Belfast railway.
Felix McConville demonstrating the process of scutching.
Richard McConville, Eugene’s son, carried the business on from his brother and in the industry’s heyday, around 1940, up to 50 people were employed locally. The present owners still have the accounts books for wages, and the names of the mill workers read like a directory of the town. Characters such as Tommy Kernoghan, Fergy McGrath, Oliver Bickerstaff, James Dewart, Ned Fairley, Len Bostan to name but a few. Some of the workers, who were mere boys at the time, still live and work in the town.
The flax industry suffered however in the late 1950’s and 60’s with the increase in synthetic fibre production and the mill all but closed. There has been, in recent years, a resurgence of linen especially by it’s utilisation in the designs of Paul Costelloe and other Irish designers. This brought media attention to the small mill when the BBC programme, the Clothes Show, featured the present owners explaining the flax growing process.
The flax industry suffered however in the late 1950’s and 60’s with the increase in synthetic fibre production and the mill all but closed.
The Flax, now, it would blossom out into a wee
Flax Mill — Aghandunvarren, Phillip Jordan Flax Mill 1907
Flax, Corn and Saw Mill — Miller Marquis of Downshire 1834
Weaving Factory — Hillsborough Woolen Company 1860
Distillery and Weaving Mill — Hillsborough Linen Company 1919
Flax Mill — Aghandunvarren, Phillip Jordan Flax Mill 1907
Flax, Corn and Saw Mill — Miller Marquis of Downshire 1834
Weaving Factory — Hillsborough Woolen Company 1860
Distillery and Weaving Mill — Hillsborough Linen Company 1919
In 1876, a change was made in the factory production from woollens to linens
The Mill of Hillsborough Linen Company, Limited, was situated at a distance of about a mile, English, west of Hillsborough, and less than half a mile from the railway station. The buildings were, three storeys and two storeys high, they covered about two acres, and on 26 acres there are 52 workmen’s houses. Altogether, the premises consisted of about 140 statute acres, including the grazing farm. There was 318 looms, with the latest improvements. The manufactures included towellings, diapers and damasks. Yarns spun from Irish and Belgian flax were chiefly used. The products were sent to the markets of the United Kingdom and to the United States and Canada. An engine 135 horse-power, drove the machinery in summer. In winter a turbine wheel, equal to 70 horsed-power, was used as an auxiliary.
The buildings used were originally a distillery, that were operated by Mr. Hercules Bradshaw; a celebrated man of the turf. A short time after the demise of Mr. Bradshaw the distillery was acquired by a Limited Liability Company and changed into a woollen factory. A second limited liability company was formed while the concern was in full operation. It bought out the first company and continued to work until 1876, when a change was made from woollens to linens, the company re-organised and its name altered to the Hillsborough Linen Company, Limited. Some of the shareholders of the first company have stock in the present successful enterprise.
Mr J.J. Pimm of Lisburn, is managing director, and Mr. Arthur Pimm secretary. Mr Arthur Pimm resides at Culcavy Cottage, in handsomely planted grounds. About 300 people are employed in the factory, of this number more than half are females.
At the entrance to the factory there was a school under the National Board of Education. It was chiefly attended by children of the company’s operatives. The first storey of the school-house served as a reading and recreation room. It was established by the company for the workmen, who managed it by committee. For generations the mill provided the means of existence for a large proportion of the local population and this was often readily acknowledged.
Herbert Bell of Tullynore, Hillsborough, had his own recollections of many of these people and their work:
I went to work in Culcavy Factory in 1931/32. I was learning weaving. for a short period, then working at bleaching yarn, and later I was operating a cropping machine in the cloth office. The older person on the large machine was George Cunningham; he was reared at Chimney Hall, Lisburn Road. The cloth inspector was Waring McCleery from Moira, and he was married to a Uprichard.
I was learning weaving for a short period, then working at bleaching yarn, & later I was operating a cropping machine.
Annie McClenaghan nee Ball provides a lifetime recollection of work in a linen mills, starting with Hillsborough Linen Company. I started work in Hillsborough Linen Company as a Weaver at the age of 14. This was the main work place for most of the girls and women of the village and my mother introduced me into the intricacies of the trade. It was hard work and the youth of today would probably be horrified by the conditions under which we toiled, the noise, dirt and the cold.
This was the main work place for most of the girls and women of the village.
We put in a six day week, Monday to Friday 8am to 6pm and Saturday 8am to 12.30pm. More than welcome was the cup of tea we got at our loom at 10am. When 12.30pm arrived it was lunch break, but we had to be back at work at 1pm. For some it meant a `piece’ (sandwiches) consumed on the premises, but a few managed to run home for a quick bite. The weavers’ tools were a haddle hook (held in your mouth all day) and scissors (held in your hand all day). The women staved off the dirt by wearing an overall to save their clothes. If your loom stopped functioning the men would be called on to do the repairing or fixing, but as time meant money to the weaver the women sometimes became just as adept at the fixing and carried their own tools. I remember one method I was involved in was the supply of small cuttings of dry rabbit skin glued and put in the shuttle to stop the weft breaking. Another task was cleaning the looms every Friday. We were the producers of the best damask table cloths, tea towels and deck chair covers, the latter of which would cut the hands off you.
More than welcome was the cup of tea we got at our loom at 10am.
Flax and Spinning Mill — Largymore 1888
Flax, Spinning and Bleach Mill — Taghnabrick 1929
Weaving Factory — Lisnagarvey Linen Co 1927
Weaving Factory — Linenhall Street Weaving Factory 1911
Weaving Factory — The Back Lane Barracks 1929
Weaving Factory — James Ward Coulson Damask Factory, 1885
Weaving Factory — Lisburn Weaving Factory 1927
Weaving Factory — Jonathan Richardson Weaving Mill 1866
Weaving Mill — Milford Weaving and Finishing Co 1925
Spinning Mill — Island Spinning Co Limited Flax Spinning Mill
Spinning Mill — Robert Stewart and Sons Flax Spinning 1926
Spinning Mill — William Barbour and Sons Ltd 2006
Beetling Mill — Alex Martin Beetling Mill 1924
Flax and Spinning Mill — Largymore 1888
Flax, Spinning and Bleach Mill — Taghnabrick 1929
Weaving Factory — Lisnagarvey Linen Co 1927
Weaving Factory — Linenhall Street Weaving Factory 1911
Weaving Factory — The Back Lane Barracks 1929
Weaving Factory — James Ward Coulson Damask Factory, 1885
Weaving Factory — Lisburn Weaving Factory 1927
Weaving Factory — Jonathan Richardson Weaving Mill 1866
Weaving Mill — Milford Weaving and Finishing Co 1925
Spinning Mill — Island Spinning Co Limited Flax Spinning Mill
Spinning Mill — Robert Stewart and Sons Flax Spinning 1926
Spinning Mill — William Barbour and Sons Ltd 2006
Beetling Mill — Alex Martin Beetling Mill 1924
Beetling Mill — Jonathan Richardson Beetling Mills 1866
Beetling Mill — Taghnabrick 1870
Beetling Mill — Lisnagarvey Richardson Sons and Owden 1927
Bleach Mill — Richardson and Sons and Owden Bleaching Mill 1925
Bleach Mill — Richardson and Co Beetling and Bleach Mill 1879
Bleach Mill — Kilmakee Bleach Mill 1925
The site on which Lagan Valley Island was built once played a significant role in Lisburn’s industrial past. Previously the site for the Island Mill Spinning Company, famous for the production on linen through it, production at the mill came to an end in 1983. When this happened, Lisburn and Castlereagh City Council (then Lisburn Borough Council) purchased the site, and with funding assistance from the National Lottery to the Arts Council of Northern Ireland, regeneration of this site began.
The land was gifted to the people of the area by the Richardson family, leading linen bleachers and manufacturers in the area and descendants from a Quaker family who settled in Ireland at Lisburn in the early 1700s. The Richardsons owned three linen production plants in the area: The Island Spinning Co (now LCCC Headquarters) Millbrook Bleachworks (now housing) and The Glenmore Bleachworks one of the largest of its type in Ireland. The family lived at two large estates in the Lambeg area: Glenmore House (now apartments) and Aberdelgy (now a Golf Course).
The Richardsons owned three linen production plants in the area: The Island Spinning Co, Millbrook Bleachworks (now housing) and The Glenmore Bleachworks.
John Barbour moved from Scotland to Co. Down, Ireland in 1784 to establish a linen thread making business at the Plantation, Lisburn. At the same time his son, William, bought a derelict bleach green at Hilden and set up business. Later, the thread works were transferred to Hilden and as early as 1817 it was employing 122 workers.
In 1823 William Barbour bought a former bleach mill at Hilden and built a water-powered twisting mill. The Linen Thread Company was founded 1898 and it quickly became a large international company. In fact it became the largest linen thread mill in the world, giving Lisburn a richly deserved international reputation.
By 1914 it employed about 2,000 people and until recently some 300 workers were still employed there, with the work-force dropping to just 85 in recent years. Among the company's varied products were nets, which could be made into snares and fishing nets. The company built a model village for its workforce in Hilden, which consisted of 350 houses, two schools, a community hall, children's playground and village sports ground.
By 1890 the mill had 30,000 spindles 8000 twisting machines & used 200 tonnes of coal and 100 tonnes of flax per week.
By the end of the 19th century, William Barbour’s mill at Hilden was considered the largest linenthread manufacturer in the world. In 1898 the Irish, Scottish and American Barbour companies were merged into the Linen Thread Co, Ltd. When war broke out in 1914, around 2000 people were employed at the Hilden Mill and with their help the mill produced linen thread that was used to stitch war-time parachutes, uniforms, boots and knapsacks.
In 2006 the company annoucned it’s closure, the employees, some of whom have worked at the factory for over forty years, said they were 'disgusted' at the decision and felt let down by the company. The factory's senior shop steward, Jackie Ross, said the staff were devastated. Speaking after the start of the consultation process between staff and Coats Barbour, Mr Ross said: "They call it restructuring but it is a total closure. We were given a business plan to turn the company around in two years but we weren't even given that opportunity. This year we made a small profit and to our mind, if we had another year, we could have made this a very successful business.”
"We thought we had a promise two years ago about the future, but it wasn't worth the paper it was written on," said a very angry Mr Ross. "They are taking away the Barbour name," said Mr Ross. "They are taking away the heritage from the people of Lisburn. To them 85 is just a faceless number but they are not faceless to us. Those 85 workers are families, couples, brothers, sisters, fathers and sons. Workers at Barbour feel let down, disappointed and betrayed."
"We have, however, been compelled to restructure our business because of the industries we serve. The declining local market and the demand for lower costs from our customers makes it inevitable that we cannot continue to operate at Hilden and remain competitively serving our customer needs. We have to reshape our business to support our customers. We must meet their demands for quick, responsive supply whilst facing the challenges of a highly competitive global market. Doing nothing, in the face of these industry changes, is not an option."
It became the largest linen thread mill in the world, giving Lisburn a rich international reputation.
Lisburn Mills
They are taking away the
Barbour name.
We thought we had a promise two years ago about the future, but it wasn’t worth the paper it was written on.
of globalisation moves must be made to diversify the economy.
Particularly in areas where the textile industry has been so prevalent.
87 88 89 90
Flax Mill — Ballymurphy James Carlisle Flax Mill and stores 1918
Flax Mill — Cargygray Campbell Hook Flax Mill 1916
Flax Mill — Cluntagh Charles Rush House Flax Mill 1929
Flax Mill — Magheraconluce James McCormick Flax Mill 1929
Flax Mill — Growell
87 88 89 90
Flax Mill — Ballymurphy James Carlisle Flax Mill and stores 1918
Flax Mill — Cargygray Campbell Hook Flax Mill 1916
Flax Mill — Cluntagh Charles Rush House Flax Mill 1929
Flax Mill — Magheraconluce James McCormick Flax Mill 1929
Flax Mill — Growell
Cluntagh Charles Rush House Flax Mill 1929
“In this townland, on the river rising at Lough Aghery, there is one flax mill occupied by William Kearns it has a breast wheel 13 feet in diameter.”
1834 & 1929
In 1929 Magheraconluce and Cluntagh, the last two flax mills closed down.
Flax Mill — Tullindoney Flax Mill 1921
Flax Mill — Dromara Flax Mill 1926
Flax Mill — Crossgar, The Mill on the Rock 1969
Flax Mill — Rathfriland Road, William Dodds Mill 1911
Flax Mill — Aughnaskeagh, William John Corbett Flax mill 1914
Flax Mill — Tullinisky, William Heron Flax Mill 1970
Flax Mill — Carne Flax Mill 1836
Flax and Corn Mill — Kinallen, Earl of Clanwilliam Flax Mill 1928
Flax and Corn Mill — Kinallen, Johnston Flax mill 1914
Flax and Bleach Mill — Dromara, Bertie Dodds Mill 1926
Weaving Factory — John Thompson Weaving factory 1891
Flax Mill — Tullindoney Flax Mill 1921
Flax Mill — Dromara Flax Mill 1926
Flax Mill — Crossgar, The Mill on the Rock 1969
Flax Mill — Rathfriland Road, William Dodds Mill 1911
Flax Mill — Aughnaskeagh, William John Corbett Flax mill 1914
Flax Mill — Tullinisky, William Heron Flax Mill 1970
Flax Mill — Carne Flax Mill 1836
Flax and Corn Mill — Kinallen, Earl of Clanwilliam Flax Mill 1928
Flax and Corn Mill — Kinallen, Johnston Flax mill 1914
Flax and Bleach Mill — Dromara, Bertie Dodds Mill 1926
Weaving Factory — John Thompson Weaving factory 1891
1836–1918
They had 16 employees in their last year.
William John Corbett
David Johnston
S G Graham
James McIlroy
S J Walker
Sandy McVeigh
James Biggerstaff
Oliver Biggerstaff
Thomas Johnston
William Smartt
John McIlroy
William McLoughlin
Sandy Johnston
Mrs John Biggerstaff
Sadie Johnston
Minnie Graham
The flax industry has a long association with Dromara with the bleach green at Woodford dating back to before 1810 and there are linen trade connections to this site going back to 1758.
In the 19th century Dromara became the site of the highest bleach greens and scotch mill on the Lagan. The labour force was drawn chiefly from the surrounding area but some specialised labour came from as far away as Belgium.
When the war ended in 1945 demand for flax declined. Much cheaper man-made fibres were coming on the market with the result that many mills closed. Many local people still have memories of those days when the flax industry was a big part of their lives and remember the Belgians who came and lived and worked with them.
1868–1926
It was operated by the Fibre Corporation. At it’s peak it had between 80–90 workers.
Flax Mill — Shannaghan, James McMaster Flax Mill 1913
Flax Mill — Ardbrin, Annaclone Flax mill 1914
Flax Mill — Aughnacloy, John Wilson Flax Mill 1916
Flax Mill — Lisnasliggan, John McGiven Office and Mill 1867
Flax Mill — Cloghskelt, John Spiers Flax mill 1891
Flax Mill — Ballooleymore, Samuel Porter Flax Mill 1909
Flax Mill — Ballybrick, Alexander Mulligan Flax Mill 1888
Flax Mill — Shannaghan, James McMaster Flax Mill 1913
Flax Mill — Ardbrin, Annaclone Flax mill 1914
Flax Mill — Aughnacloy, John Wilson Flax Mill 1916
Flax Mill — Lisnasliggan, John McGiven Office and Mill 1867
Flax Mill — Cloghskelt, John Spiers Flax mill 1891
Flax Mill — Ballooleymore, Samuel Porter Flax Mill 1909
Flax Mill — Ballybrick, Alexander Mulligan Flax Mill 1888
But was restored to a full working capacity before officially closing in 1909.
In 1874 Ballooleymore Flax mill was officially listed as a Flax Mill. It went through a series of 5 different recorded owners with the last one James McCord. He owned it right up until it closed down in 1909. The flax mill was restored and reroofed after a major fire incident.
May 2007
Flax Mill — Glaskermore, Robert Corbett Flax Mill 1922
Flax Mill — Gransha, 1836
Flax Mill — Ballynaskeagh, Abraham Sinclair Flax mill 1892
Flax Mill — Longhorne, Michael Torley Flax Mill 1921
Flax Mill — Grallaghgreenan, Robert Swan Flax Mill 1892
Flax Mill — Tullyquilly, Mr Thomas Scott Flax Mill 1835
Flax Mill — Glaskermore, Robert Corbett Flax Mill 1922
Flax Mill — Gransha, 1836
Flax Mill — Ballynaskeagh, Abraham Sinclair Flax mill 1892
Flax Mill — Longhorne, Michael Torley Flax Mill 1921
Flax Mill — Grallaghgreenan, Robert Swan Flax Mill 1892
Flax Mill — Tullyquilly, Mr Thomas Scott Flax Mill 1835
Robert Corbet’s land with 2 flax mills recorded. 1870–1922
In 1870 it was worth £70
In 2024 this is £20,000
Flax Mill — Kiltarriff
Flax Mill — Drumlough, Alexander McCauley Flax mill
Flax Mill — Drumnascamph, David Davidson Flax and Saw Mill
Flax Mill — Lenish, Thomas Fitzpatrick Flax mill
Flax Mill — Ballynagappoge, 1969
Flax Mill — Ballyaughian, Essie Lindsay Flax mill 1916
Flax Mill — Kiltarriff
Flax Mill — Drumlough, Alexander McCauley Flax mill
Flax Mill — Drumnascamph, David Davidson Flax and Saw Mill
Flax Mill — Lenish, Thomas Fitzpatrick Flax mill
Flax Mill — Ballynagappoge, 1969
Flax Mill — Ballyaughian, Essie Lindsay Flax mill 1916
1864–1919
had over 30 workers when in full production.
The Mill lay idle during war years of 1925–1939 and briefly after the war, machinery sold for scrap.
Flax Mill — Bavan
Flax Mill — Cabragh
Flax Mill — John Edgar (James Weir) Flax Mill
Flax Mill — Saval More, James Glenny House, office and Flax Mill
Flax Mill — Bavan
Flax Mill — Cabragh
Flax Mill — John Edgar (James Weir) Flax Mill
Flax Mill — Saval More, James Glenny House, office and Flax Mill
1957 Children playing at Abandoned flax mill
1836–1924
Cabragh for scutching flax, diameter of wheel 13 feet breadth 2 feet, breast wheel, fall of water 14 feet.
Cabragh Flax Mill stayed in the Keenan family, until its closure in 1924.
Flax Mill — Cleomack — James Hall Scutch Mill
Flax Mill — Lisnamulligan
Flax and Beetling Mill — Ballyaughian
Flax Mill — Ballymaghery
Flax Mill — Ballynanny
Flax Mill — Cleomack — James Hall Scutch Mill
Flax Mill — Lisnamulligan
Flax and Beetling Mill — Ballyaughian
Flax Mill — Ballymaghery
Flax Mill — Ballynanny
The first site of the Linen Industry' in the Upper Bann Valley was at Hilltown in the Mourne country. A Scutch Mill and a Bleach Green on the banks of the fledgling, river Bann was run by a John O'Neill who was a descendant of the O'Neills of Clandeboye. He was a man of princely aspect, noble deportment, majestic stature and almost preternatural strength. He is buried in the old graveyard of Clonduff a few miles outside Hilltown.
The river Bann, with its source in the Deer's Meadow, flows through Hilltown, Ballymoney, Katesbridge, Banbridge, Gilford, Moyallon, Portadown and into Lough Neagh at the Bannfoot. Industry in its lower course virtually finishes at Portadown, though there was at one time a pottery at Robb's Ferry in the townland of Derrybroughas, some five miles north of Portadown.
The waters of Upper Bann were relatively soft and free of discolouration to a little beyond Moyallon. After this point it flowed through peat bogs near Portadown which imported a brown colour, not beneficial to a 'good white' in the bleaching of linen yarn or cloth.
In Memoirs 1836 note that Ballyaughian Flax Mill, “Belongs to David Lindsay, wooden machinery, situated on the River Bann in Ballyaughian townland; the breast wheel is 14 feet in diameter and 1 foot and 10 inches broad”
By 1872 it had expanded and a Beetling mill and office has also been installed. The next written record of Ballyaughian noted that it had 2 beetling engines and 8 scutching stocks.
In 1916 the mill was passed down to Essie Lindsay and it was last recorded in 1925, when it is expected it closed.
Remained in the Lindsay family throughout it’s life.
By 1872 Ballyaughian Flax Mill had expanded, adding a Beetling Mill and Office to the Mill.
1938–1946
During the war as many as 25 hands were employed constantly on night and day shifts.
Workers included William Johnston of Hiltown, the O’Hanlon & Hannelly Family.
Hugh Martin opened this mill in 1897, but did not use it as a working mill. In 1923 Mrs. Sarah Mussen of Ballymaghery near Hilltown and her husband George bought it soon after their marriage. Here they laboured for 30 years, until about 1920, when Mr. Mussen purchased the farm of Martin's of Bannvale, Hilltown which comprised a flax mill and corn mill.
When Mr and Mrs. Mussen and their young family came to Hilltown around 1920 they soon settled down and began to play an important part in the life of the local community. Mr. Mussen already knew something about the working of a corn mill and flax mill and under his able supervision business steadily increased. From miles around farmers brought their corn for grinding and throughout the season flax scutchers had steady employment. During the war (1938-1946) as many as 25 hands were employed constantly on night and day shift.
But all that has changed now too. As synthetic materials came on the market the demand for linen declined, the price of flax growing became uneconomic and rapidly faded out (though an effort is now being made to revive it). With the growing tendency for increased grazing , the cultivation of oats is only a fraction of what it was and in addition the ready made meals provided by many firms have made the grinding of corn less necessary than heretofore. So it is that the once humming machinery is now silent- but one never knows when the cycle will make its turn.
Probably best known of Mrs. Mussen’s family is her son George, who runs the home farm. He is a foundation member and secretary of the Mourne Sheep breeders’ Association Ltd and has also been appointed secretary of the recently formed Hilltown Farmer’s Attested Sales Ltd. Of the grandchildren, most prominent of course, is Willie’s son Kevin, who has captained the Co. Down Gaelic football to new heights of glory during the past few years.
The Mourne Observer on the 23rd May 1969 noted that it was Known as Mussen’s Mill. Originally water wheel driven later steam (turbine scutching) during the war, closed around 1950. Workers included William Johnston of Hilltown and the O’Hanlon and Hannelly sisters.
Mussens Mill is thought to have closed around
Flax Mill — Moyad 1836
Flax Mill — Moyad 1836
It is thought that their was a house with people living on the land from as early as 1770 due to the ruins.
Memoirs from1836 say, “Ballymoney is a new flax mill, in townland of Ballymoney, a good slated house built by John Burny. In 1835 it was noted to have a breast wheel, water wheel 16 feet diameter breadth 3 feet diameter of cog wheel 7 feet, water wheels and cog wheels cast iron. These memoirs also state, “Water was supplied by the Muddock river, which works 8 months in the year.”
In 1873 it was noted that there was a new owner, Hugh Byrne. Additionally it was noted that because of the bad supply of water, Byrne could no longer scutch his own flax because of the lack of facilities to first ret the flax. In 1884 Hugh Byrne sold Ballymoney Flax mill to Bernard Keely and it stayed with him until it was officially scored out as a flax mill in 1904.
1836–1904
Water was supplied by the Muddock river, which works 8 months in the year.
In 1873 it was noted that because of the bad supply of water, Byrne could no longer scutch his own flax.
Flax Mill — Ballymoney Roger Hall Scutch Mills 1883
Flax Mill — Newtown Margaret Turrettin Flax mill 1899
Flax Mill — Narrowater Roger Hall Flax Mill 1911
Flax Mill — Charles Sloan Scutch Mill 1929
Linen Mill — The Forestbrook Linen Co Beetling mill 1922
Bleach Mill — Kibrony Robert and John Martin Bleach Works 1916
Beetling Mill — Margaret Turrettin Two Beetling mills 1921
Flax Mill — Ballymoney Roger Hall Scutch Mills 1883
Flax Mill — Newtown Margaret Turrettin Flax mill 1899
Flax Mill — Narrowater Roger Hall Flax Mill 1911
Flax Mill — Charles Sloan Scutch Mill 1929
Linen Mill — The Forestbrook Linen Co Beetling mill 1922
Bleach Mill — Kibrony Robert and John Martin Bleach Works 1916
Beetling Mill — Margaret Turrettin Two Beetling mills 1921
1836–1916
The
Kilbroney is worked by David Lowry.
It has a wash mill and an extensive beetling mill of 3 storeys all in good repair. It works without interruption from the 1st of March to Christmas.
In 1916 it was scored out and replaced with offices.
David Lowry sold the property to the Martin brothers, by 1916 it had fallen into disrepair.
Flax Mill — Andrew Malmsley Flax mill 1922
Flax Mill — Ballymagart, Samuel Nicholson Scutch mill 1913
Flax Mill — Leitrim, James Quinn Mill 1887
Flax Mill — Ballymageogh, Charles Wilson Flax mill 1894
Flax Mill — Ballinran, Robert Wybrants Flax Mill 1897
Flax Mill — Carrigenagh, William Quinn Flax Mill 1918
Flax Mill — Tullyframe, Daniel Nichol Flax mill 1923
Flax and Bleach Mill — Aughnahoory, The Green 1834
Flax and Bleach Mill — James Walmsley Flax Mill 1915
Flax Mill — Andrew Malmsley Flax mill 1922
Flax Mill — Ballymagart, Samuel Nicholson Scutch mill 1913
Flax Mill — Leitrim, James Quinn Mill 1887
Flax Mill — Ballymageogh, Charles Wilson Flax mill 1894
Flax Mill — Ballinran, Robert Wybrants Flax Mill 1897
Flax Mill — Carrigenagh, William Quinn Flax Mill 1918
Flax Mill — Tullyframe, Daniel Nichol Flax mill 1923
Flax and Bleach Mill — Aughnahoory, The Green 1834
Flax and Bleach Mill — James Walmsley Flax Mill 1915
The old mill has been restored and it now used as holiday homes and for wedding venues.
In the late 1700s the Walmsley brothers from Preston in Lancashire arrived in Mourne to establish themselves as industry leaders in the milling of flax and corn. To this end they sought and were granted permission to build several mills in the Kilkeel area.
Constructed in the early 1800s, with it’s first official recording being in 1866. The barn complex followed later to house a corn mill, kiln, granary and store houses to meet the growing demands of expansion in the linen industry. For well over one hundred years The Green was a thriving hub for local business and agriculture while the riverside paths and stepping stones provided the perfect spot for locals to enjoy a Sunday afternoon stroll. Sadly the mill stopped working in 1922 and the buildings and machinery fell into a state of disrepair until none of the original workings remained. The Green Holiday Cottages opened in 2020, after undergoing restoration of the mill.
In the late 1700s the Walmsley brothers from Preston, established themselves as industry leaders in the milling of both flax and corn.
It remained very profitable and stayed in the Walmsley family throughout its life as a mill.
Flax Mill — George Stockdale Flax Mill 1876
Flax Mill — James Campbell Flax Mill 1873
Flax Mill — Hugh Magilton Flax Mill 1889
Flax Mill — Ballybrannagh Upper 1838
Flax Mill — Robert Hanna Flax Mill 1907
Flax Mill — Rossconor Flax Mill 1925
Flax and Corn Mill — John Bailie Flax Mill 1837
Flax Mill — George Stockdale Flax Mill 1876
Flax Mill — James Campbell Flax Mill 1873
Flax Mill — Hugh Magilton Flax Mill 1889
Flax Mill — Ballybrannagh Upper 1838
Flax Mill — Robert Hanna Flax Mill 1907
Flax Mill — Rossconor Flax Mill 1925
Flax and Corn Mill — John Bailie Flax Mill 1837
1836–1925
In 1905 the Browns sold their flax mill to the Rosconor Cooperative Agricultural Society.
By 1925 all of the flax mills had shut down, Rossconor was the last working mill in Downpatrick. & it is thought it stayed open the longest because in 1905 Rossconor Cooperative agricultural society bought it over.
Flax Mill — Drumaghlis, John and Thomas McMillan Flax Mill 1924
Flax Mill — W.Hutton Flax Mill 1836
Flax Mill — Creevycarnonan, James Moffet Flax mill 1878
Flax Mill — Robert Morrison Flax Mill 1903
Flax and Corn Mill — Carnacally Mill 1920
Flax and Corn Mill — Lisara, Samuel King Flax Mill 1927
Flax and Corn Mill — Lisnamore, John Magee Flax Mill 1925*
Flax and Corn Mill — Listooder, John McRoberts Mill 1928
Flax Mill — Drumaghlis, John and Thomas McMillan Flax Mill 1924
Flax Mill — W.Hutton Flax Mill 1836
Flax Mill — Creevycarnonan, James Moffet Flax mill 1878
Flax Mill — Robert Morrison Flax Mill 1903
Flax and Corn Mill — Carnacally Mill 1920
Flax and Corn Mill — Lisara, Samuel King Flax Mill 1927
Flax and Corn Mill — Lisnamore, John Magee Flax Mill 1925*
Flax and Corn Mill — Listooder, John McRoberts Mill 1928
Memoirs from 1836 say, “In the townland of Lissara a corn mill belonging to Mr Galbraith; diameter of wheel 18 feet breadth 3 and a half feet fall of water 5 feet, breast wheel turned by the Annacloy River. Flax mill in same townland and same owner. Diameter of wheel 14 feet breadth 2 and a half feet, fall of water 4 and a half feet, breast wheel, there is a second flax mill adjoining, which is of the same dimension”
In 1892 the corn mill part of Lisara was said to be in a state of ruins, this continued to be the case until its closure in 1927.
In 1892 the Corn mill in Lisara was said to be in a state of ruins, this continued to be the case until its closure in 1927.
*Recorded in the Mourne Observer
Harry Drake
James Robinson
William John Adams
Tom Peter
Johnny McCann
Paddy Carvill
John Douglas
Jack Robinson
Paddy Quinn
John Quinn
Sandy Campbell
Eddie McVeigh
Sam McVeigh
Robert McVeigh
Charles McWilliams
Barney Carr
Barney Carlin
Dora McClements
Mrs Cleland
Mrs Parkinson
Nellie Simpson
Mrs Boyd
Aggie Carr
Maggie Cleland
Roseann Branney
Lizzie Ann Casement
1811–1895
Lisnamore Mills or Rockville Mills on the Annacloy River was an extensive mill complex on the Rocks Chapel Road 550m before Kilmore Bridge. Rockville was the accompanying house for the mills and is the long two-storey house that runs along the side of Rocks Chapel Road. The lane to the left of Rockville house took you down to the big mill on the riverbank.
Lisnamore Mills in the south-western corner of Lisnamore townland was probably built in the 18th century. The earliest record for the mills is from 1811 when it was called ‘Rock-Ville Mills’ and was advertised for letting by its proprietor Edward Humfrey. The advert referred to it as “The flour and bleach mills of Rock-Ville, with neat dwelling-house and offices in complete repair, a walled garden and orchard in full bearing, with about 25 acres of excellent land” (Belfast Commercial Chronicle, 19th Aug 1811). The bleach mill, was across the road from Rockville house, was built to make 5000 pieces of linen a year and there was also space for the workers to live.
Lisnamore Mills and the 30-acre estate was owned by Thomas and Anne Henry from 1841, but was rented out. Thomas died in 1866. When the mill's occupier died in 1847, the mill “in a fine grain country” was put up ‘for sale or let’ in May 1847, but wasn’t leased until May 1849 or soon after. Timber from the land was sold in April 1853, primarily for coaches.
From 1860 onwards, the complex was referred to as ‘Lisnamore Mills’ and the dwelling house remaining as ‘Rockville’. After the death of Thomas Henry (Lisnamore Mills owner), the mills were reslated in 1866 and the mill complex was restored to working order again in 1869. In 1869, the trustees of Thomas Henry leased it to John Jones Curran on a 90-year lease. However, Mr Curran's wife of nine years, Jane (nee Watson), died in 1869 and he remarried to Jane (nee Millar) in August 1872. She was the eldest daughter of William Millar of Crossgar and his wife Margaret. The new Curran couple emigrated to Toronto a few months later in 1873 along with John's five children.
“There had been three or four years of bad weather and no flax. John J had invested a lot in enlarging the mill. The big chimney was built at this time.”
Curran relative, 2010
John Curran’s 90-year lease was taken over by James McKenzie in 1876 for £300 and an annual rent of £60. From 1877, Robert H Taylor worked the mill. James McKenzie went into other business, and the mill complex was put up for sale in 1882 and again in 1887, but James McKenzie was a tenant there until 1891.
In 1889, the mills’ owners, namely the trustees of Thomas Henry, took James McKenzie to a rent tribunal for unpaid rent. However, James McKenzie won the case, partly because he’d spent £1,000 on the mills and dwelling house during his occupancy.
James McKenzie invested £1,000 on the mills and dwelling house, since 1877.
William Kennedy of Dunnanelly leased it from 1891. In October 1894, he was fined for “unjust weights” in what was now a flax mill, rather than a flour mill.
Six weeks later, the flax mill was accidentally destroyed by a fire and it became disused thereafter. The fire was discovered to have broken out in the flax mill shortly after 7pm on 22nd November 1894. “The men were at work at the time and managed to get out of the mill in safety. In a short time after the alarm the mill was in flames, and from the inflammable nature of the premises and content was impossible to stop the fire until everything had been consumed. The mill was filled with scutched and raw flax, the property of farmers in the immediate neighbourhood, who were depending upon the produce of this to meet the November rents now due, and the loss will be keenly felt by the majority of them. By the fire, which was still smouldering yesterday, a large number of hands have been thrown idle. None of the flax consumed was insured. It is stated that the fire was caused by the heating of driving shaft of the machinery.” (Northern Whig, 24th Nov 1894)
No work could be done in the mill anymore, resulting in a substantial loss of earnings. The landlord refused an abatement in rent and William ended up owing £120 (two years’ rent). Thus, he was evicted from the land in 1897 due to a “disagreement with the agent”, or in William’s words, “unpayment of excessive rent”.
In January 1900, the engine, boiler, and scrap iron from the mills were sold off, which annoyed William Kennedy as he had bought the equipment and hoped to still use it.
the 22nd of November 1894
7pm
The men were at work at the time of the fire managed to get out of the mill in safety.
The mill was in flames, due to the flammable nature of the premises it was impossible to stop the fire.
Everything had been consumed.
Flax Mill — Ballykine, John Owens Scutch Mill 1883
Flax Mill — Ballynahinch
Flax Mill — Ballymurphy, James Carlisle Flax Mill 1918
Flax Mill — Magheradrool, Gibsons Mill 1928
Flax Mill — Ballymacarn flax mill 1922
Flax Mill — Drumaconagher
Flax Mill — John McRoberts Corn and Flax Mill 1928
Corn and Flax Mill — Harris Mill or Mill Bridge
Bleach Mill — Drumnaconagher
Flax and Threshing Mill — Drumnaconagher
Flax Mill — Ballykine, John Owens Scutch Mill 1883
Flax Mill — Ballynahinch
Flax Mill — Ballymurphy, James Carlisle Flax Mill 1918
Flax Mill — Magheradrool, Gibsons Mill 1928
Flax Mill — Ballymacarn flax mill 1922
Flax Mill — Drumaconagher
Flax Mill — John McRoberts Corn and Flax Mill 1928
Corn and Flax Mill — Harris Mill or Mill Bridge
Bleach Mill — Drumnaconagher
Flax and Threshing Mill — Drumnaconagher
Memoirs of 1837 say, "Ballymacarn flax mill is a slated house in good order, the property of David Ker Esquire held by Francis McAuley. Built 1819 works 2 months in the year on average. Nature of water wheel breast, diameter of wheel 20 feet breadth 3 feet, diameter of cog is 10 feet double geared with wooden and metal machinery."
In 1870 John Marner bought the Flax Mill and it stayed in his family until it closed in 1922.
In 1837 the mill worked 2 months a year on average. Workers recorded are as follows:
The corn mill, the flax mill and the stable, are all shown on the OS map of 1834 and recorded in the valuation returns of 1836. All of these buildings were graded B+ to B- by the valuers, suggesting that they believed (or were informed) that most were at least twenty years old at that point. At this stage, the miller’s residence consisted of a long single-storey dwelling, which stood on the site of the present house; the valuers believed this to be the oldest building on the site, possibly dating from the early to mid 1700s.
In 1837 the present two-storey dwelling was built, with perhaps some of the fabric of the original house incorporated within the return. The twostorey barn to the south of the house was also added around this date, as was the storehouse to the north of the flax mill, the small cottage-like building and the projection to the north side of the corn mill. All of these are shown on the revised OS map of 1858.
In 1861 valuation, the house was graded ‘A’ with all of the other buildings ‘B’, suggesting that most of these were indeed the same structures listed in the 1836 valuation. The valuers also mention a ‘barn on loft’, a ‘flax mill on basement containing 3 stocks with rollers’, a ‘breast water wheel’ of 14ft with buckets of 4 ft, which worked ‘briskly 4 months in the year’, and ‘4 stocks and set of rollers’. As regards the corn mill, they state that there were ‘3 pair of stones shelling, grinding and hard corn and one stone for dressing pearl barley’ with a 18ft breast shot wheel with buckets 5ft, which also worked ‘4 months in the year’.
The Silcock family mentioned in both the 1836 and 1861 valuations are believed to have acquired Mary Brook some time around c.1790 to c.1800 from a family named Traill. The Traill connection with the area goes back to 1647, when James Traill, an officer in the Parliamentary army, was granted the townland of Drumnaconagher. His grandson, also named James, is believed to have been the first to actually settle within the townland, building a house there in 1721. Walter Harris, writing in his ‘Ancient and Present state of the County of Down’ in 1744 refers to this house, as ‘Marybrook, seated on a rising ground near a small lake…two miles south east of Ballynahinch. On the face of it, this reference appears puzzling, for the present Mary Brook does not appear to be sited on rising ground, nor is it near a small lake, and it is closer to 3 miles east of Ballynahinch, rather than SSE.
However, if we take into account that ground level to the north of the flax mill drops considerably (a drop which may have been more pronounced in the mid 1700s), then this could explain the ‘rising ground’, and the ‘small lake’ may simply be a reference to a mill pond or a flood plain relating to the nearby river.
At its height in the late 19th century, the Marybrook complex employed around 150, not only in corn and flax milling, but also in a small hemstitching factory, which was situated in a (now modernised) building along the main drive off Raleagh Road. The children of employees were taught in a small schoolhouse on the site. The hemstitching factory closed c.1900, with the flax mill ceasing production a few years later. The corn mill continued in full-time use until after WWI, with production coming to a halt by the 1930s. The Silcock family continued to reside at Mary Brook until the early 1950s, after which the site was abandoned and fell into decay. In the early 1970s it was acquired by Mr Lewis-Crosby, a senior figure within the National Trust, who restored the buildings and brought the corn mill back into use. The present owner acquired the complex in 1998.
Marybrook employed around 150 people in the late 19th Century
Flax and Corn Mill — Saintfield Co Milling Society Flax mill 1920
Flax and Corn Mill — Carrickmannan, Robert Dunville 1882
Flax and Corn Mill — Glassdrumman McBurney mills 1922
Flax and Corn Mill — Ravara 1834
Flax and Corn Mill — Saintfield Co Milling Society Flax mill 1920
Flax and Corn Mill — Carrickmannan, Robert Dunville 1882
Flax and Corn Mill — Glassdrumman McBurney mills 1922
Flax and Corn Mill — Ravara 1834
1834–1911
In 1905 the Flax Mill was used as concert hall.
1837–1922
By 1878 the Corn mill was not used, & the Flax mill burned down.
1922 the mill was roofless & was scored out as a mill.
Memoirs from 1837 state, That it was both a Corn and Flax mill situated in the townland of Glassdrummond, belongs to Alexander McBirnie, machinery principally wood. Diameter of the wheel 16 feet breadth 5 feet and a half. By 1878 it was noted that the Corn Mill had not produced anything for the last 3 or 4 years. The Flax mill is said to have been burned down shortly after this. But by 1892 the Mill was back up and running after the fire. Although it never housed a large workforce and also laid vacant for many years after then losing its roof in 1922.
Flax Mill – Ballycowan, Moorecrofts Milltown 1837
Flax Mill – Ballydollaghan, John Hunters Flax Mill 1906
Flax Mill – Knockbreckan, Roger Hunter Flax Mill 1837
Flax Mill – Carryduff Russell Scotts Mill 1837
Flax Mill – Ballynavally, Susanna Gray Flax Mill 1921
Flax and Corn Mill – Mealough, John Hunters Mills 1913
Weaving Factory – Edenderry Weaving Company 1922
Beetling Mill – Ballynahatty 1837
Flax Mill – Ballycowan, Moorecrofts Milltown 1837
Flax Mill – Ballydollaghan, John Hunters Flax Mill 1906
Flax Mill – Knockbreckan, Roger Hunter Flax Mill 1837
Flax Mill – Carryduff Russell Scotts Mill 1837
Flax Mill – Ballynavally, Susanna Gray Flax Mill 1921
Flax and Corn Mill – Mealough, John Hunters Mills 1913
Weaving Factory – Edenderry Weaving Company 1922
Beetling Mill – Ballynahatty 1837
There had been a bleachworks on the site since the late 1700s which had later been turned into a flour mill. John Shaw Brown acquired the flour mill at Edenderry converting the premises to a weaving factory and making another large weaving shed.
The factory, known as the St. Ellen Works, developed from 1866 onwards into a successful enterprise, trading under the name of John Shaw Brown and Sons. The site which John Shaw acquired extended to 46 acres of rich pasture bounded by clusters of mature trees. The Russells had built their bleachworks on the low lying land close to the riverbank harnessing the water power in a mill dam and race. From 1866 onwards houses which formed the village were built on the level above the factory buildings in a cul-de-sac surrounded by an attractive landscape of hills and mature trees boarded by the river.
John Shaw Brown was educated for a career in one of the professions; but on the death of his uncle James Brown he took over the family linen manufacturing business, then at a very low ebb, though in 1834 the bleach green had been capable of producing 10,000 pieces of linen a year. He built a linen factory at Edenderry, five miles south of Belfast, which was one of the largest in the area; all the power looms and other machinery were made by the company’s own craftsmen.
He was able to return the business to profit in a remarkably short time, and entered into partnerships, first with a Mr Magee and later with a Mr Liddell; with the latter he opened a linen warehouse in Belfast. The business was in the name of Brown & Liddell till 1866, when the partnership was dissolved, and the firm of John S. Brown & Co. (later John S. Brown & Sons) established a large warehouse in Bedford St., where seventy people were employed to deal with huge orders from all over the world. The firm’s contracts to supply sheeting and damask for table and bed linen, to hotels, railway companies, and other concerns, were said to be the largest in the United Kingdom, and its trademark – a woven-in shamrock – was well known. Its products won prizes in many international exhibitions, and the company’s reputation was enhanced by the paternalistic care taken of employees in Edenderry, Lurgan, and Belfast.
My Granny worked there as a doffer her sister Beattie and brother Tommy were employed there too!
Flax Mill — Tullygarvan, William Nevin Wallace Flax Mill 1883
Flax Mill — Tullyhubbert, John Bennett Flax Mill 1906
Flax Mill — Edenslate, David McMordie Flax Mill1926
Corn and Flax Mill — Robert McKenzie Flax Mill 1930
Corn and Flax Mill — Ballyknockan Flax Mill 19230
Spinning Mill — Tullygarvan, William Valentine Mill 1880
Flax Mill — Tullygarvan, William Nevin Wallace Flax Mill 1883
Flax Mill — Tullyhubbert, John Bennett Flax Mill 1906
Flax Mill — Edenslate, David McMordie Flax Mill1926
Corn and Flax Mill — Robert McKenzie Flax Mill 1930
Corn and Flax Mill — Ballyknockan Flax Mill 19230
Spinning Mill — Tullygarvan, William Valentine Mill 1880
At this time Ballyknockan flax mill was situated in the townland of that name and belonged to David Orr. It was built in the year 1810. The wheel is of metal and a breast wheel. Its diameter is 13feet and its breadth 4feet and 1 inch. Ballyknockan flax mill adjoins the above, is situated in the same townland and also belongs to David Orr. The wheel was 15 feet diameter and 8 feet 8 inches in breadth. The last known owner of the working flax mill was Robert McKenzie in 1930.
1837–1928
Tullygarvan, formerly known as Tullygarvan Mills, Corn, holds a significant place in historical records, as noted in Griffiths map and OS Memoirs of 1837. Situated on the route from Ravara to Moneyreagh, it boasted a substantial breast wheel measuring 14 feet and 16 inches in diameter. Over the years, ownership changed hands, with James McGilton holding ownership in fee in 1877, followed by William Scott (William Nevin Wallace) in 1880, and later by John Davison Junior (also associated with William Nevin Wallace) in 1896 and 1912. By 1896, the mill underwent a transformation, with the conversion of an old corn store into a flax mill, equipped with six stocks and one roller. Noteworthy investments were made in scutching machinery and a new waterwheel. The mill continued its operations into the 20th century under the ownership of Harry Walker in 1928, though by then, its function had evolved to include a flax mill kiln. Intriguingly, by 1928, the mention of mills was struck out, indicating a transition in ownership, previously belonging to the Belfast Cooperative Society, marking the end of an era for Tullygarvan Mills.
Ballygowan Mills
The Spinning Mill closed in 1880.
The Flax and Corn Mill stayed open until 1928.
Flax Mill — Ballymagaughey, William Boyd Flax Mill 1925
Flax Mill — Ballywilliam, William Boyd Flax Mill 1899
Flax Mill — Ballymagaughey, John Millar Andrews Flax Mill 1922
Flax Mill — Ballyaltikilligan, Thomas Huxley Flax Mill 1921
Corn and Flax Mill — Isaac Andrews and Sons Flax Mill 1907
Corn and Flax Mill — Ballystockart, John Orr Flax Mill 1923
Spinning Mill — John Andrews and Co Flax Spinning mill
Bleach Mill — Thomas Andrews Bleach Works 1855
Bleach Mill — Comber Distillery Company Bleach works 1906
Flax Mill — Ballymagaughey, William Boyd Flax Mill 1925
Flax Mill — Ballywilliam, William Boyd Flax Mill 1899
Flax Mill — Ballymagaughey, John Millar Andrews Flax Mill 1922
Flax Mill — Ballyaltikilligan, Thomas Huxley Flax Mill 1921
Corn and Flax Mill — Isaac Andrews and Sons Flax Mill 1907
Corn and Flax Mill — Ballystockart, John Orr Flax Mill 1923
Spinning Mill — John Andrews and Co Flax Spinning mill
Bleach Mill — Thomas Andrews Bleach Works 1855
Bleach Mill — Comber Distillery Company Bleach works 1906
The earliest volume dates from May 1863 and records the initial construction of the mill. It gives details of every nut and bolt used in the building. Enclosed within the volume is a letter dated 28 May 1863 from James Combe & Co, Falls Foundry, Belfast to James Andrew, providing a quote for the estimated cost of building the mill: ‘We have made enquiries and we learn that the cost of a mill in the Belfast district on suitable foundations say 18 to 22 Bays long, 4 stories and attic would be about £450 per bay, 20 bays along £9,000. This indicates foundations - Ash car plinth, the foundation not exceeding 3 feet for walls and four feet deep for pillars, walls, columns, beams, arches, filing (no cross gutters in spinning room) roof with skylights, for attic, building 51 feet wide overall, first floor 14 feet, second 13 feet, third 12 feet 6 inches, fourth 12 feet 6 inches, attic for reeling, 4 feet at eaves, windows, staircase’. This early ledger also records the costs of material and labour throughout the construction of the spinning mill. Moreover, it gives details of the installation of the machinery into the building.
In 1910 they resumed recording the mill history, The correspondence reveals the changes within both the business and the flax industry at large. The letters depict the European dimension of the firm such as dealings with flax agents in Courtrai appointment of representatives in France, Germany and Austria and shipments of yarn to Russia, etc. The outbreak and impact of World War One is clearly documented in the letter book for that period. The above details their concerns about flax supplies, however, it would appear that they had large quantities in stock which saw them through the first 4 months of the conflict.
The letter books immediately after the war are revealing in their portrait of a company attempting to re-establish business with a war exhausted Europe and open up new markets. There are less local details, although a regular feature is the purchase of coal for the mill workers. The final letter books cover the period 1935-55. However, they are in effect yarn and flax order books.
Another nail in the coffin of the linen industry.
Mr Tom Andrews, the managing director of the family owned company, which has produced wet spun flax and linen yarn for the past 133 years, blamed a downturn in the demand for linen, an increase in the price of raw materials, and increased competition from the third world. ”This is a traditional industry where whole families have been employed by the company,” he said, “and it will have a devastating effect on the town.”
Mr Mills said the company suffered from a lack of investment, and he blamed the government for doing nothing to protect indigenous industry.
Flax Mill — Corporation South, Mill Street 1858
Flax Mill — Court Street Flax Mill 1858
Flax Mill — Ballyharry, Robert Crawford 1836
Flax Mill — Bootown, Robert Ferguson Steam Flax Mill 1892
Flax Mill — Ballyrogan
Flax Mill — Ballyalton, Robert Wightman Mill 1888
Flax Mill — Cunningburn, John Warden Flax Mill 1911
Weaving Factory — Ards Weaving Co Bleach Works 1930
Weaving Factory — Irish Tapestry Co weaving factory 1929
Weaving Factory — Wallace Street Weaving Factory 1880
Weaving Factory — Movilla Weaving Factory 1904
Weaving Factory — Great Francis Street Weaving Factory 1927
Spinning Mill — George Walker Flax and Hemp Spinning Mill 1930
Flax Mill — Corporation South, Mill Street 1858
Flax Mill — Court Street Flax Mill 1858
Flax Mill — Ballyharry, Robert Crawford 1836
Flax Mill — Bootown, Robert Ferguson Steam Flax Mill 1892
Flax Mill — Ballyrogan
Flax Mill — Ballyalton, Robert Wightman Mill 1888
Flax Mill — Cunningburn, John Warden Flax Mill 1911
Weaving Factory — Ards Weaving Co Bleach Works 1930
Weaving Factory — Irish Tapestry Co weaving factory 1929
Weaving Factory — Wallace Street Weaving Factory 1880
Weaving Factory — Movilla Weaving Factory 1904
Weaving Factory — Great Francis Street Weaving Factory 1927
Spinning Mill — George Walker Flax and Hemp Spinning Mill 1930
Bleach Mill — McCauseland and McNaughton Bleach Works 1881
Flax Mill — Ballymaglaff, David Kennedy and Son Flax Mill 1869
Flax Mill — Ballylisbredan, Belfast Cooperative Society Mill 1924
Flax Mill — Carrowreagh, Sir Daniel Dixon Flax Mill 1917
Flax Mill — Carrowreagh, Thomas Killips Flax Mill 1878
Flax Mill — Killarn 1832
Bleach and Corn Mill — Andrew Munce Mill 1884
Flax Mill — Ballymaglaff, David Kennedy and Son Flax Mill 1869
Flax Mill — Ballylisbredan, Belfast Cooperative Society Mill 1924
Flax Mill — Carrowreagh, Sir Daniel Dixon Flax Mill 1917
Flax Mill — Carrowreagh, Thomas Killips Flax Mill 1878
Flax Mill — Killarn 1832
Bleach and Corn Mill — Andrew Munce Mill 1884
1871–1924
John Galloway sold the mill to Belfast Cooperative Society in 1910.
Flax Mill — Ballyvarnet, Archibald Grey Flax Mill 1837
Flax Mill — Rathgill, William Bunn Flax Mill 1930
Flax Mill — Ballymaconnell, 1837
Flax Mill — Drumhirk, William McCammon Flax Mill 1836
Flax Mill — Portavoe, Annabella Boyd Flax Mill 1924
Flax Mill — Ballynoe/Kilnburn, G L Delachevois Flax Mill 1935
Flax Mill — Ballyvarnet, Archibald Grey Flax Mill 1837
Flax Mill — Rathgill, William Bunn Flax Mill 1930
Flax Mill — Ballymaconnell, 1837
Flax Mill — Drumhirk, William McCammon Flax Mill 1836
Flax Mill — Portavoe, Annabella Boyd Flax Mill 1924
Flax Mill — Ballynoe/Kilnburn, G L Delachevois Flax Mill 1935
Used as both a Store & Flax Mill from 1904.
Flax Mill — Ballynoe/Kilnburn, G L Delachevois Flax Mill 1935
Flax Mill — Craigboy, James McNay Flax Mill 1925
Flax Mill — Ballymacruise, James Fulton Flax Mill 1906
Flax Mill — Ballynoe/Kilnburn, G L Delachevois Flax Mill 1935
Flax Mill — Craigboy, James McNay Flax Mill 1925
Flax Mill — Ballymacruise, James Fulton Flax Mill 1906
Flax Mill — Ballywallon, Robert Birch Old Flax Mill 1920
Flax Mill — Black Abbey, Jessie Thompson Flax Mill 1914
Flax and Corn Mill — William James Walker Flax Mill 1917
Flax Mill and Threshing — Ballyherly, Benjamin Maxwell Mill 1876
Flax Mill — Ballywallon, Robert Birch Old Flax Mill 1920
Flax Mill — Black Abbey, Jessie Thompson Flax Mill 1914
Flax and Corn Mill — William James Walker Flax Mill 1917
Flax Mill and Threshing — Ballyherly, Benjamin Maxwell Mill 1876
Due to it’s geographical position, Kircubbin had very few mills, the ones that it did have were very small, family flax mills.
1820–1920
it stayed in the Birch Family for over 100 years.
There is contrasting amounts of information available about the mills of County Down. The major mills in the first half of the book have a lot of their history recorded as well as photographs from the time.
The rural mills have a lot more questions than answers. With different parts of their history not recorded physically, it is hard to piece together what really happened in their lifetime. If anyone has any information or first hand accounts of working or visiting any of the 232 mills of County Down, please do get in touch.