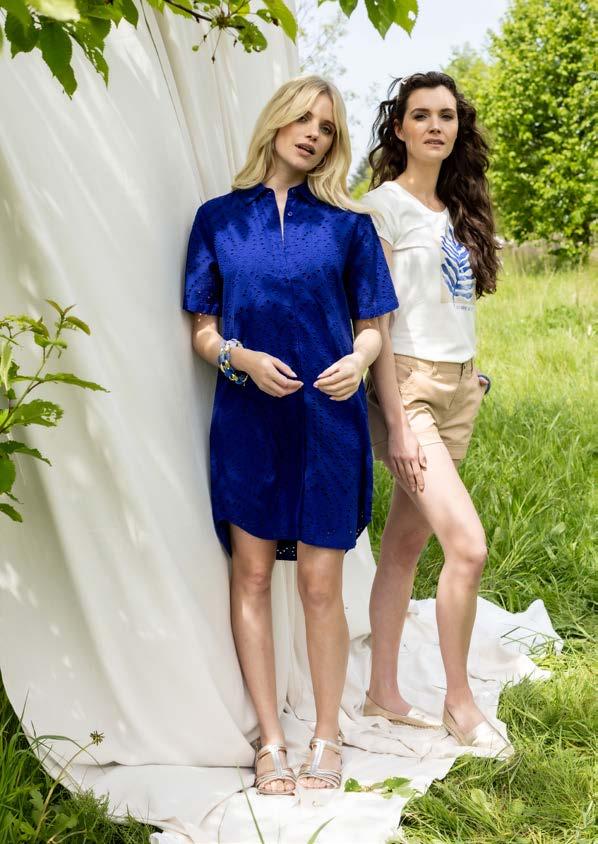
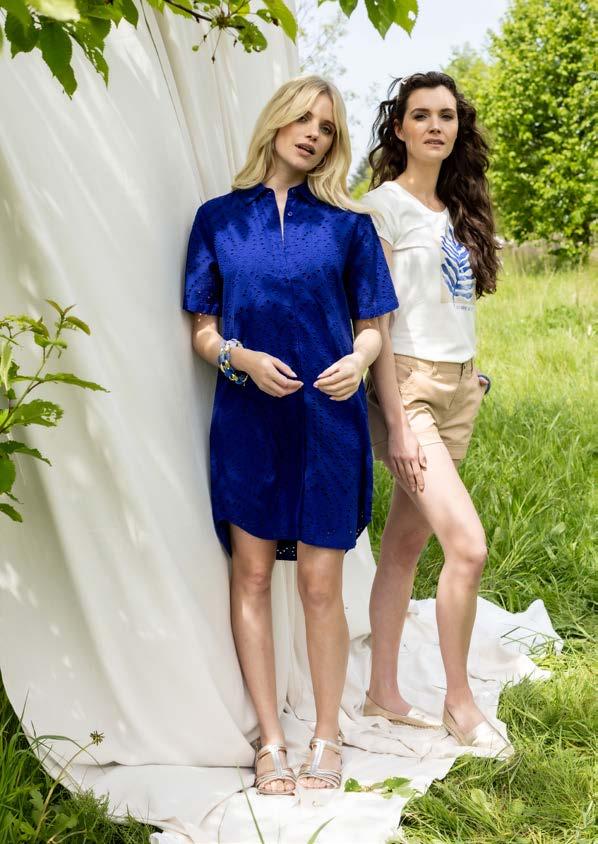
Sustainability
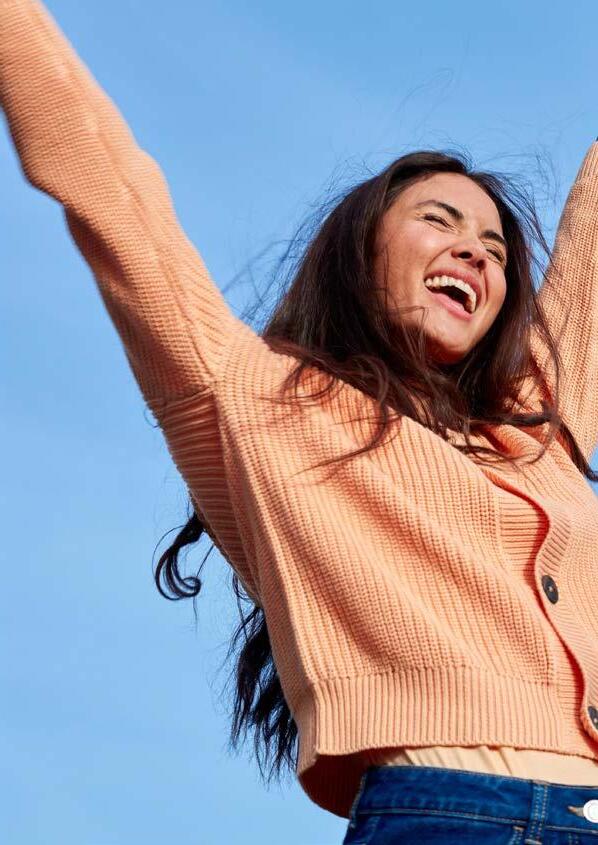
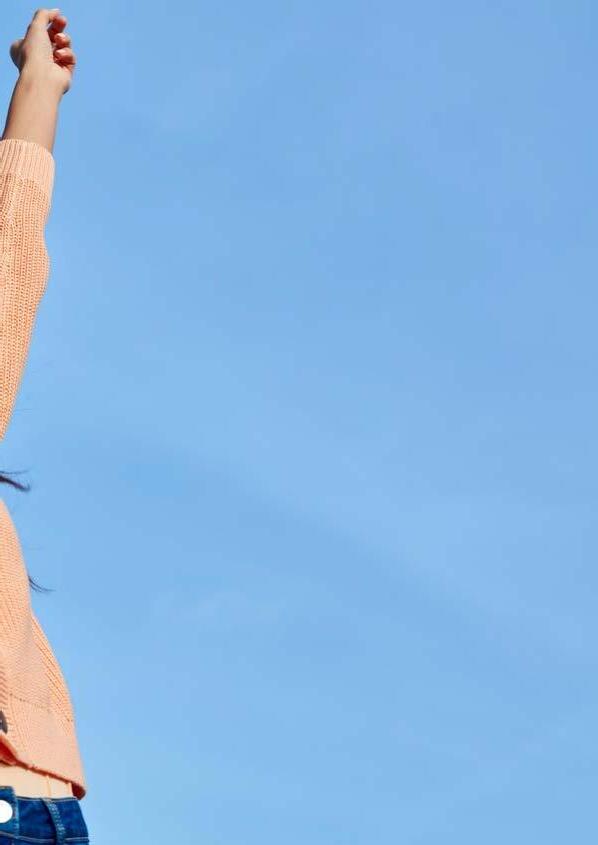
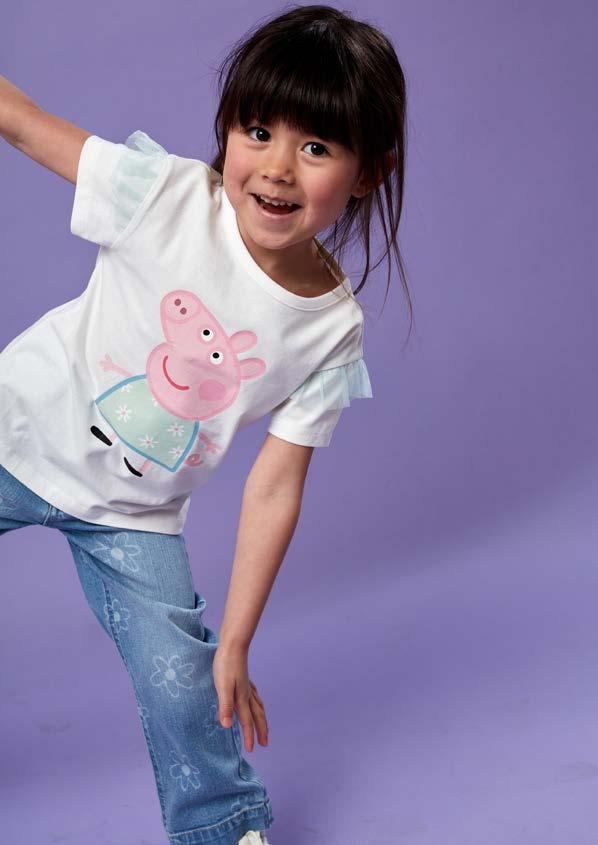
Welcome
Preface
Dear reader,
Bel&Bo is a family owned and run business. As a family we want to pass on the company to the generations to come. The transgenerational transfer from the 2nd to the 3rd generation has just taken place. My father, Michel Delfosse passed the torch to me and I am proud to be the new CEO of our wonderful company Bel&Bo. My biggest dream is to be able to pass on the company to the next generation to come.
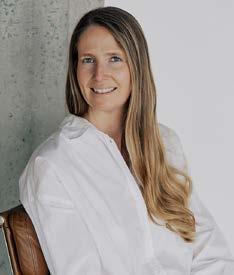
So sustainability is in our DNA: we think and act long term. We incorporate our family values such as respect, involvement, honesty, education, entrepreneurship and responsibility into the company. Other unwritten family rules such as who screams the loudest, gets the most food we prefer to keep outside the company walls.
We want every employee of Bel&Bo to be part of our big and loud family: be proud of their work and stimulate each other to be the best and happiest version of themselves. Team spirit and a pleasant, convivial atmosphere are extremely important, both at our headquarters and in our shops. We also want Bel&Bo to continue for many generations, so we need to look beyond and consider our responsibility for society and environment.
We embarked on a remarkable journey, and here are our achievements: We became the first Belgian retailer to join Fair Wear, won the CSR Award POM, ranked 2nd in the Great Place to Work 2022, became a Close The Loop ambassador, joined Amfori, signed the Transparency Pledge, endorsed the call for Due Diligence, and participated in the European SCIRT project.
We engage with different stakeholders to help us move forward: challenging but rewarding. Sometimes we take small pragmatical steps, sometimes we take a leap. The most important thing is that we keep moving forward together to a colorful and fair world.
We are grateful you have found your way to this social report. Let’s do this together!
About Bel&Bo
For 30 years, everyone has been finding their own style at Bel&Bo. And here within the Bel&Bo family, we couldn’t be more thrilled! From our roots in Deerlijk, West Flanders, our company quietly grew into the renowned fashion brand for all Belgians. Today, we’re a team of 600 colleagues, all passionate about fashion and keeping a close eye on trends. Each season, we bring you the most beautiful, timeless, everyday, and surprising collections. Comfortable in fabric, and even more so in price.
Come visit one of our 96 stores. Amidst the fleeting moments of everyday life, at Bel&Bo, you’ll find that special boutique experience. How about some authentic advice and occasional warm compliments? Together, we’ll discover the outfit that truly reflects you. So when you leave, you’ll have a renewed enthusiasm for the rest of the day. Wearing something new, you’ll be ready to take on the world!
Our year at a glance
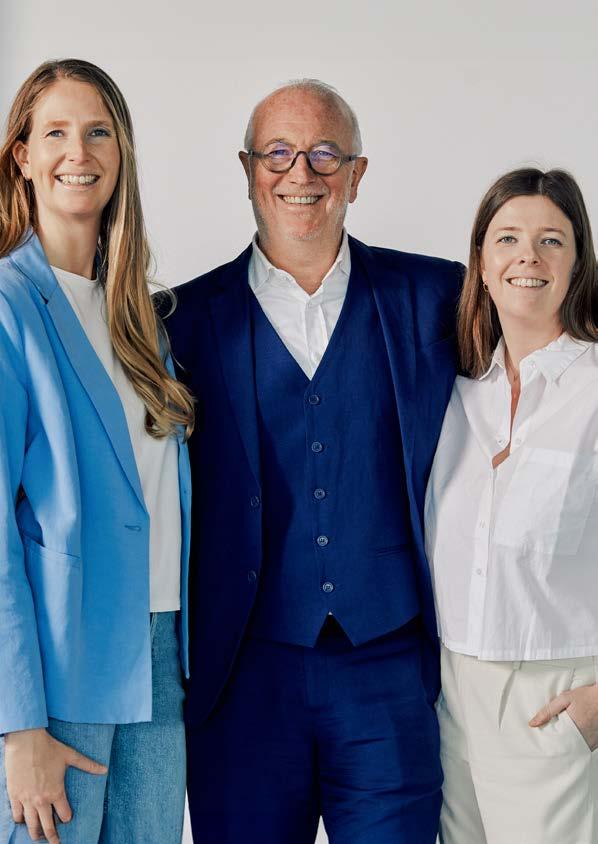
Family business
At Bel&Bo, we’re more than just a business – we’re a family. And like any family, we’re thinking about the future. Our dream? To pass on a fashion legacy that’s as welcoming as it is stylish, to our kids, grandkids, and beyond. Our clothes? They’re not just threads – they’re expressions of joy, confidence, and individuality. And we believe everyone should have access to that feeling, without breaking the bank.
But hey, looking good shouldn’t come at the expense of our planet, right? That’s why we’re all about finding ways to make a difference, from our sourcing practices to our eco-friendly designs. Because at Bel&Bo, we’re not just about outfits – we’re about spreading warmth, inside and out.
Our CSR strategy
Bel&Bo is organised based on 3 pilars: sourcing, sales and logistics. These 3 pilars are linked with each other through planning, marketing, transport and technical support. Everyday we work hard to make this circle run as smoothly as possible. With the support of our supporting departments (such as CSR, HR, IT and finance) this operating model is lifted to a higher and more sustainable level.
We have been on a sustainability journey for over a decade now, and along the way, we’ve learned that it takes more than just a dedicated CSR team - everyone needs to be on board.
How do we do this? We have dedicated project teams that span different departments for every important subject (Fair Wear team, CSRD team, GPTW team,...). Next to this, we upped the amount of CSR strategy meetings with top management from two times a year to four times a year. Lastly, our CSR manager has a weekly meeting with our CEO, so we can stay on top of new developments and make quick decisions.
SDGs
The Sustainable Development Goals (SDGs) are a universal call to action to end poverty, protect the planet, and ensure prosperity for all by 2030. These 17 interconnected goals address pressing global challenges such as poverty, inequality, climate change, environmental degradation, peace, and justice. From eradicating hunger to promoting gender equality and clean energy, the SDGs serve as a blueprint for a more sustainable and equitable world. At Bel&Bo we contribute by focussing on the following SDGs:
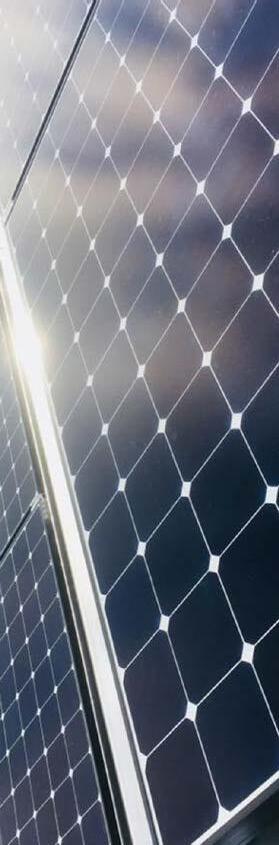

3:
SDG 3 is about health and well-being for everyone. At Bel&Bo we try our absolute best to keep our employees happy and healthy. By offering training sessions and workout classes we try to keep our employees’ minds and bodies healthy. Read more on page 15.

8:
We have been focussing on improving the working conditions at our suppliers for a long time. We do this by creating long lasting relationships with our suppliers where we collaborate and communicate as equals. This is a long-term job, where we try to do better year after year. Read more on page 18.

12:
We want to be a business that can last generations, and that starts with treating our planet with care and respect. We are increasing our usage of more sustainable materials, like organic cotton. Moreover, we’re passionate about empowering our customers to make sustainable choices. That’s why we offer convenient options like our take-back system, repair services, and a helpful care guide. Read more on page 36.
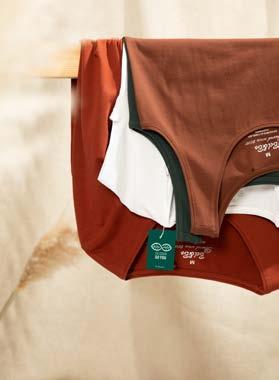

13:
To help fight climate change, we’re also exploring ways to be more sustainable closer to home. We buy green energy, have started mapping our CO2 footprint and invested in solar panels. We are constantly looking at ways to save more energy: lowering our heating temperature, investing in motion detectors and domotics systems. Read more on page 42.

17:
We cannot reach all these goals alone, which is why we have partnered up with several organizations such as Fair Wear, International Accord for Health and Safety in the Garment and Textile Industry and Amfori. Together we work on improving safe and fair working conditions and reducing our climate impact. Read more on page 19.
Sustainabilty timeline
2000-2007
First steps of social responsibility are taken. We draw up a first Code of Conduct and start carrying out independent audits with our largest suppliers via Bureau Veritas
2016
Bel&Bo has a study done by Ernst&Young: how to buy sustainably.
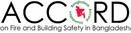
2018
Official admission to the Accord on Fire and Building Safety in Bangladesh. 2021

Bel&Bo joins the European SCIRT project 2023
In our last Brand Performance Check we were ranked as: “needs improvement”. We join the Fair Wear Academy pilot project to learn how we can improve.
2010
Our new name is launched: Bel&Bo
2016
We become a Fair Wear member and have our first Brand Performance Check. We score in the category “good”.
2021
We sign the Transparancy Pledge From now on we will publish on a regular basis a list naming all sites that manufacture our products (tier 1) 1 2 3 4 5 6 7 9 8
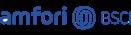
Bel&Bo becomes a member of Amfori. The Amfori Sustainability platform allows us to follow up on BSCI audits of our production partners.
2022
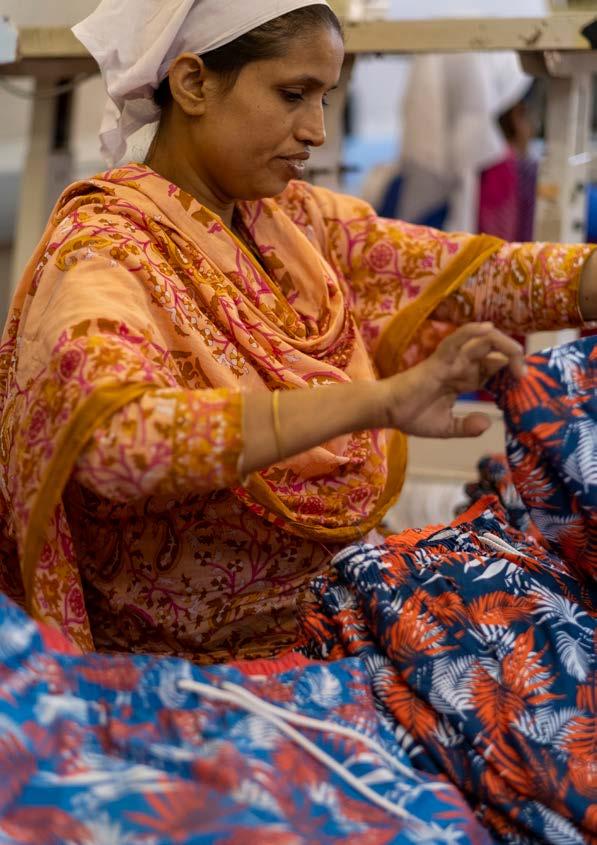
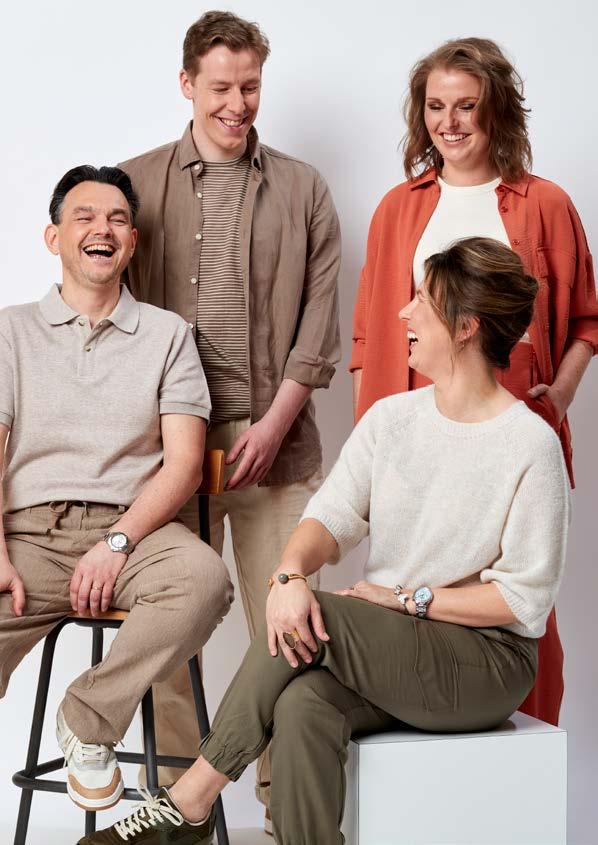
People
Own workforce
Management Employees
#650
Of which women:
#22
Of which women: 68%
59%
Great place to work
We are now second! on the prestigious Great Place To work list of large companies in Belgium. A Great Workplace is a working environment in which you trust the people you work for, you are proud of what you do and you enjoy being on the work floor. Through an anonymous questionnaire, our employees evaluate management, corporate culture and
whether the company creates an atmosphere of trust. Bel&Bo achieved a very high score in each of these areas. Despite the physical distance between the various employees, we succeed in creating a great sense of togetherness. By offering training sessions and workout classes, we try to keep our employees’ minds and bodies healthy.
Fair Wear
At Bel&Bo, social responsibility isn’t just a checkbox – it’s in our DNA. We’re a family business and we genuinely believe that the well-being of everyone connected to Bel&Bo, whether directly or indirectly, is absolutely vital. Joining forces with Fair Wear in 2014 wasn’t just a decision; it was a promise to uphold the highest social standards.
Our journey took a significant step in 2016 with our first Brand Performance Check, where we proudly achieved a commendable rating in the “Good” category. This positive momentum continued over the subsequent years, maintaining our standing until 2022.
What is Fair Wear?
However, the challenges brought about by the COVID-19 crisis in 2022 hindered our ability to effectively monitor and support our suppliers, leading to a temporary downgrade to the “Needs improvement” category.
Despite facing setbacks, we remained determined to progress. In 2023, we enthusiastically participated in the Fair Wear Academy pilot project to deepen our understanding of Human Rights Due Diligence (HRDD). This initiative provided us with valuable insights, and allowed us to skip one year of the Brand Performance Check as we worked to enhance our practices.
Fair Wear is a Multi Stakeholder Initiative (MSI) with 130 members. As an NGO, Fair Wear promotes good working conditions in the clothing industry. Fair Wear conducts an audit, the ‘Brand Performance Check’, of its members, to make sure they comply with Fair Wear standards. Bel&Bo has been a Fair Wear member since 2014.
Our BPC Scores
Fair wear code of labour practices
The eight social standards of the CoLP are based on internationally acknowledged standards such as the ILO convention for international labour rights and the United Nations’ Universal Declaration of Human Rights. These labour practices form the basis of our Code of Conduct and our monitoring and remediation processes.
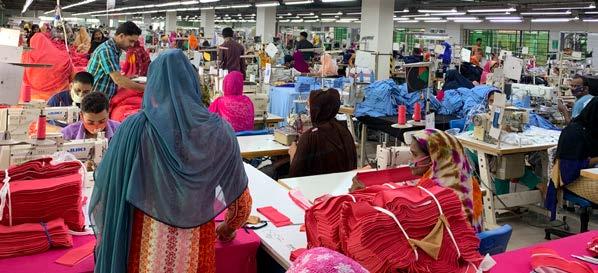
8. Legally binding employment
7. Safe and healthy working conditions
6. Reasonable hours of work
5. Payment of living wage
4. No child labour 3. No discrimination
Freedom of association 1. Employment is freely chosen
Human Rights Due Diligence (HRDD)
Communicate how impacts are adressed
Track implemenation and results
Principles for responsible business conduct
In 2023 we started on defining our HRDD (Human Rights Due Diligence) strategy. We created our new supplier Code of Conduct and new policies around Responsible Business Conduct, consolidation and unauthorized subcontracting. We conducted a first broad risk assessment of our operating countries and all our production partners. Afterwards we put new systems in place for the monitoring and remediation of our production partners. These new systems also include clear guidelines to track the progress of our efforts.
Right now our HRDD strategy is focused on our Tier 1 suppliers, meaning the suppliers that deliver us the finished products. We have started mapping subcontractors of our Tier 1 suppliers, but beyond that we have little to no information. This is a common problem in the fashion industry, which increases the risk of human rights in the factories further than Tier 1. In the coming years we will start mapping our supply chain further than Tier 1. 2 3 5 1 4 6
Identify & asses risks and negative impacts
Provide access to remedy
Preventing and reducing negative impacts
1. Principles for responsible business conduct
Executive Board
Sustainability team Topical experts
Policies
We have created several sustainability related policies, these policies form the basis of all our business decisions.
Sustainability team
The Executive Board, which includes all department heads and our CEO, is responsible for HRDD. The Executive Board is assisted by our sustainability team. This team consists out of our CEO, our buying manager, our CSR manager and someone from the finances team. They are responsible for the overall execution of our due diligence policies and procedures. They meet regularly and are supported by topical experts from our other departments.
Consolidation Policy Responsible Exit Policy
Responsible Sourcing Policy
Supplier Code of Conduct
Partners
To strengthen our HRDD process we work together with several partners. They help us with monitoring suppliers, assisting in remediation, collecting grievances,...
Amfori: We are a member of Amfori, which helps us monitor our supply chain and transforming insights into actions. Most of our supply chain has had BSCI audits.
Fair Wear: Fair Wear is a non-profit organization that works with brands, factories, trade unions, and NGOs to improve working conditions in the garment and textile industry. They focus on implementing codes of conduct and providing training to ensure fair labour practices and promote transparency throughout the supply chain.
Accord: The Accord on Fire and Building Safety in Bangladesh is a legally binding agreement between global brands, retailers, and trade unions to ensure safer working conditions in Bangladesh’s garment industry. It was established in response to the 2013 Rana Plaza building collapse and focuses on improving building and fire safety through inspections, remediation, and worker training programs.
2. Identify & assess risks and negative impacts
Transparency
At the heart of identifying social and environmental risks within our supply chain lies transparency. Our supply chains, going from raw material origins to the final product, weave through a complex web of stakeholders including farmers, producers, intermediaries, and distributors. Currently, we have insight into the primary manufacturers of our clothing, as well as their subcontractors.
In March 2022 we signed the Transparency pledge, we signed the transparency pledge to underscore our commitment to accountability and openness in our operations. By embracing transparency, we aim to build trust with our stakeholders and drive positive change within the industry.
Risk assessment
In 2023, we conducted our very first risk assessment. This process involved examining potential risks at both the country and production unit levels. Drawing insights from international studies, audits, and firsthand visits, we delved into the unique challenges posed by each country’s socio-political, economic, and environmental landscape. When it came to the risk assesments for each production unit, our focus was primarily on audit findings, ensuring operational processes met regulatory standards. In 2024 we will expand these risk assesments to also include product-specific risks and integrating insights from our country risk analyses.
Production unit risk scores
Green factories have few to no violations on their audit report. They are all compliant with legal wages and no serious violations in the Health & Safety department. These factories can still struggle with overtime hours, but they are not excessive.
Yellow factories mostly struggle with excessive overtime hours, smaller violations on health & safety and some don’t comply with legal regulations around insurances.
Orange factories have severe violations on health&safety, excessive overtime hours, and legal regulations around wages and insurances.
Red factories have too much violations, or are not in order with all documents like a recent audit report. We don’t place new orders with these factories as long as they have this risk score.
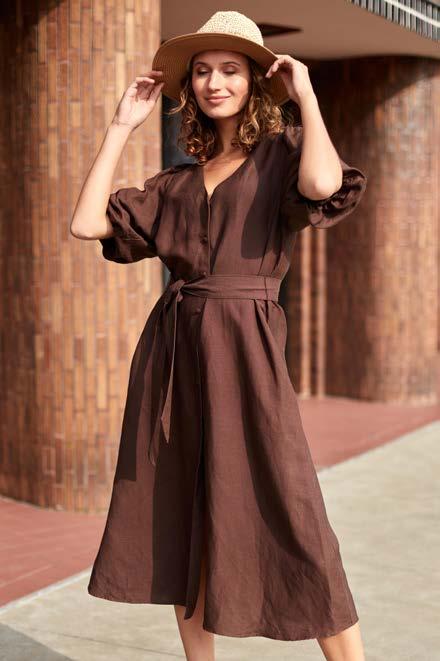
Country risks Bangladesh
Most of our basics are produced in Bangladesh. With our primary jeans supplier based there and a significant portion of our sweaters also crafted in Bangladesh, our partnerships thrive on quality and reliability. We visit our production partners in Bangladesh two times a year, to keep a good dialogue and conduct a check of the facilities.
24 Factories
38% Production Volume
7 years Avg. collaboration length
Monthly wage data for 2023
Legal minimum wage:
BDT 12.500 ~ EUR 105
Living wage*:
BDT 25.497 ~ EUR 214
*according to the Global Living Wage Coalition, 2023 data.
Country risks:
• Child labour
• Corruption
• Discrimination
• Excessive overtime
• Living wage
• Restricted freedom of association
• Structural, electrical and fire safety
India
India holds the title as our top supplier for Basic T-shirts and tops. Our collaboration with our Indian suppliers has spanned many years, forming a relationship built on trust and mutual respect. We visit our Indian partners at least once a year to check in with them and have a look at the factories.
Country risks:
• Child labour
• Corruption
• Discrimination
• Excessive overtime
• Forced labour
• Living wage
• Restricted freedom of association
22 Factories
26% Production Volume
8 years Avg. collaboration length
Monthly wage data for 2023
Legal minimum wage: BDT 12.500 ~ EUR 105
Living wage*: BDT 25.497 ~ EUR 214
*according to the Global Living Wage Coalition, 2023 data.
China
Our production partners in China are responsible for a diverse array of categories, spanning from a wide selection of women’s pieces to the majority of our accessories and nightwear. We make sure to visit China once every two years, but China’s size makes it challenging to visit every factory ourselves. So, we rely on our agents to help and conduct checks in the factories.
72 Factories
20% Production Volume
7 years
Avg. collaboration length
Monthly wage data for 2023
Legal minimum wage:
CN¥ 2,360 ~ EUR 305.25
Living wage*:
CN¥ 2,719 ~ EUR 347
*according to the Global Living Wage Coalition, 2023 data.
Country risks:
• Corruption
• Excessive overtime
• Forced labour
• Insurance and social security
• Living wage
• Restricted freedom of association
Tunisia
Our production in Tunisia benefits from shorter lead times, ensuring quicker delivery to our markets. We have been collaborating with a trusted production partner there for over 10 years. This long-standing relationship guarantees consistency and reliability in our products.
4 Factories
3% Production Volume
8 years Avg. collaboration length
Monthly wage data for 2023
Legal minimum wage: TND 459 ~ EUR 136
Living wage*: TND 1002 ~ EUR 297
*according to the Global Living Wage Coalition, 2023 data.
Country risks:
• Corruption
• Child labour
• Restricted freedom of association
• Excessive overtime
Turkey
In Turkey, we specialize in producing embellished pullovers, adding a unique touch to our knitwear. The shorter lead times from our Turkish partners ensure timely deliveries. Additionally, we source high-quality yarns to create beautiful, durable knitwear.
Country risks:
• Child labour
• Corruption
• Forced lanour
• Precarious employment of refugees
• Restricted freedom of association
• Excessive overtime
Monthly wage data for 2023
Legal minimum wage: TRY 11402* ~ EUR 326
Living wage*: TRY 13087 ~ EUR 375
9 Factories 6% Production Volume
4 years Avg. collaboration length
*according to the Global Living Wage Coalition, 2023 data.
France
Our production in France excels in delivering short lead times for blouses, ensuring prompt availability. We source special fabrics in France that are unavailable in Bangladesh or India, adding unique qualities to our products.
9 Factories
4% Production Volume
3 years Avg. collaboration length
Country risks:
• Discrimination
• Precarious employment
Monthly wage data for 2023
Legal minimum wage: EUR 1747
3. Preventing and reducing negative impacts
We’re fully committed to ethical practices across our supply chain and operations. Acknowledging our responsibility, we’re dedicated to stopping, preventing, and alleviating any identified adverse impacts. Recognizing the necessity of collective action for complex global challenges, we prioritize strong partnerships with suppliers and collaborators.
Monitoring process
The Bel&Bo monitoring process starts when a new potential production partner is found. To be accepted as a new supplier for Bel&Bo, the following documents need to be submitted:
• Self-assesment questionnaire
• Recent audit report (except for low risk countries)
• Proof that the Workerinformation sheet has been posted inside the factory.
• Agree with our Code of Conduct
Only if these documents have been reviewed by the CSR department, a first order can be placed with the new factory. After this first monitoring stage, the factory risk assesment is executed. A new audit report is requested when the old one has expired, and all documents are renewed after 3 years.
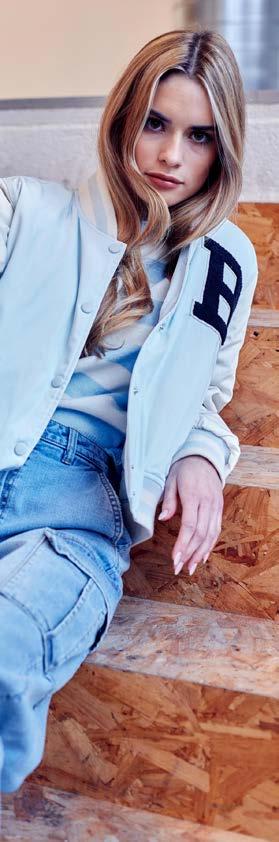
Remediation process
Our remediation process demonstrates our commitment to addressing social and environmental issues within our supply chain. With a commitment to accountability and transparency, we swiftly resolve any identified issues. Through close collaboration with our suppliers and partners, we foster sustainable solutions, ensuring ethical practices throughout our operations.
Since we have a pretty extensive supply chain, we have chosen to focus our remediation efforts on the 30 most important suppliers, that account for 75% of our total production volume. Based on the risk scores of each factory, a different action and/or prevention plan is shared with the factory.
Prevention plan
A prevention plan is put in place if we find violations on the audit report that could be prevented in the future. For example by finding the root cause of this violation, or by giving training to the workers on certain topics like health & safety. When there are instances of overtime found, we will always ask if Bel&Bo plays a part in the overtime and if we can help prevent this.
Action plan
An action plan is put into place to remediate findings of the audit report. For example when there is a missing fire exit sign, or there were missing safety needle guards on the knitting machines. We will ask the factory to solve these problems in a certain time period.
Equal partnership
Bel&Bo values equality in our partnerships with factories and strives to maintain open dialogue on all topics. However, with 150 production partners, our focus is primarily on our top 30. Among these, factories where we utilize over 10% of their capacity are designated as equal partnerships. We prioritize regular check-in meetings to discuss their feelings about our collaboration, our Fair Wear membership, and any feedback they may have.
With factories that are not labeled as equal partnerships, we still try our best to listen to requests and suggestions. We always let factories know if there is a chance our order quantity will change next season due to different circumstances.
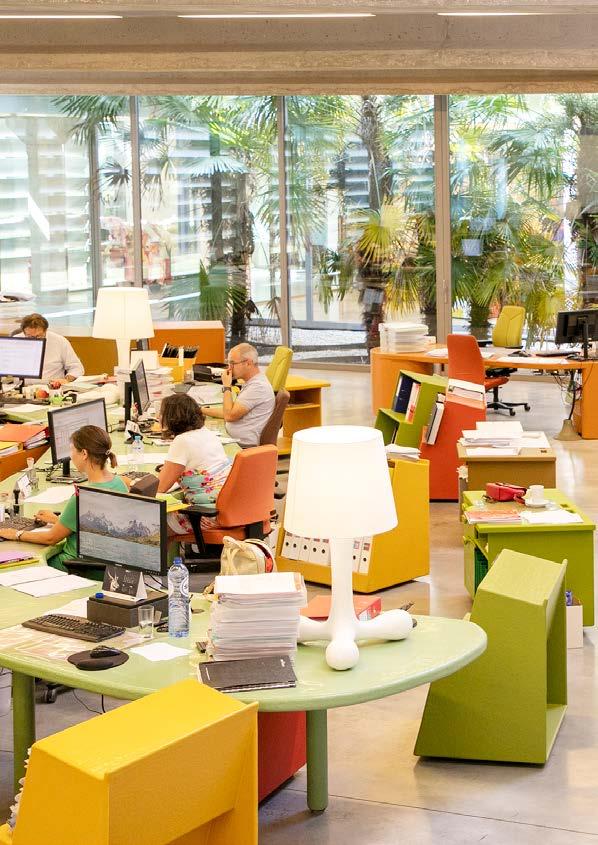
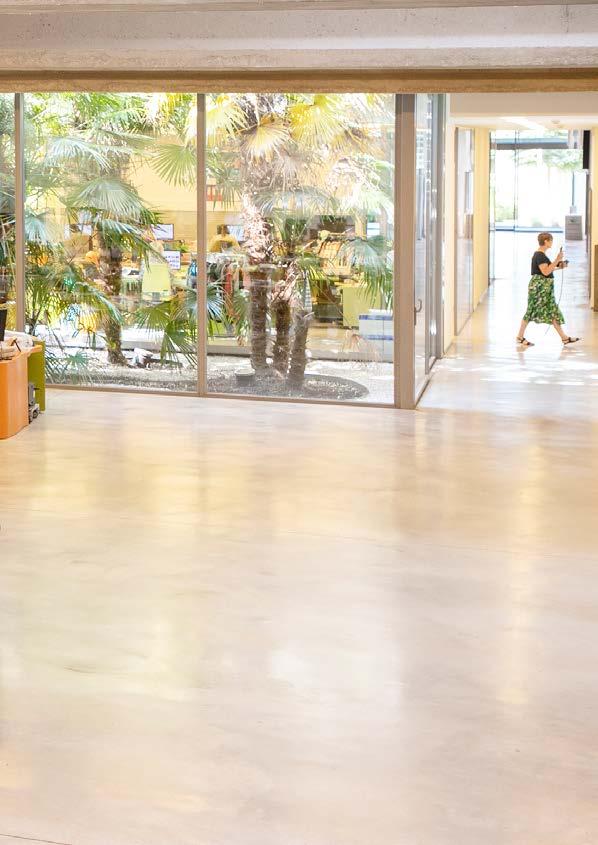
4 Track implementation and results
At Bel&Bo, our Supplier Code of Conduct serves as a cornerstone, outlining the essential standards we require our suppliers to adhere to regarding human and labor rights. We uphold these standards through a robust monitoring system, which includes regular third-party audits and on-site visits to verify compliance. Moreover, we have established comprehensive systems to continuously track the progress of our remediation efforts, ensuring that any identified issues are promptly addressed. Regular evaluations of all our suppliers allow us to maintain accountability and drive continuous improvement throughout our supply chain.
5. Communicate how impacts are adressed
As we navigate the process of due diligence, we view it as an ongoing learning experience, appreciating the importance of openly sharing our progress, challenges, and successes with our stakeholders. Our commitment extends to transparently communicating about our due diligence efforts and the practical implementation of our policies.
COMMUNICATION UPDATE
Policies
Social report
Annually on our website
Annually on our website
CONTENT
All our policies can be found on our website
Our social report provides a comprehensive insight into our sustainable business practices, offering detailed explanations of our internal operations and ethical conduct.
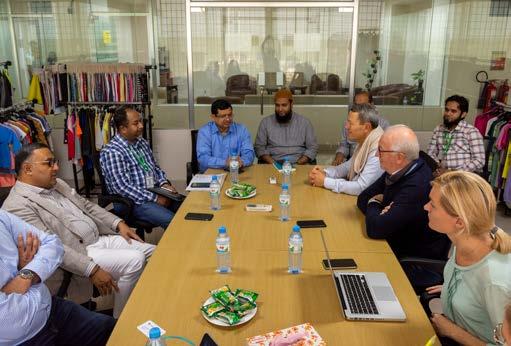
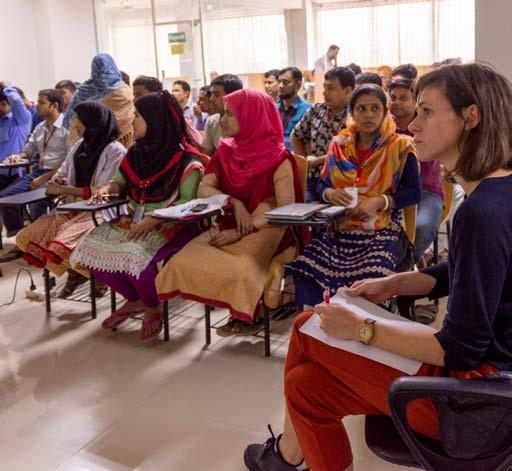
6. Provide access to remedy
Fair Wear grievance mechanism
The Fair Wear grievance mechanism begins with all suppliers displaying a Worker Info Sheet inside their factories, providing employees access to the Fair Wear helpline. Individuals or groups can then voice their concerns through this helpline. Fair Wear collaborates closely with all parties to investigate and resolve issues, fostering open communication throughout. This collaborative effort aims to uphold fairness and dignity in the garment industry.
Purchasing practices
The buying department is one of the biggest departments at Bel&Bo. They are responsible for negotiating the right price and decide where our order is placed. This means that they have a big impact on our sustainability efforts. This is why our buying department works closely together with the CSR department, and regular meetings are held. Our buyers have the flexibility to decide where to place orders, but they consider the risk assessment conducted by the CSR department. If they intend to place an order with a factory rated orange or red in terms of risk, they must first inform the CSR department and obtain their approval.
Twice a year, as each new season approaches, our sourcing strategy comes together. This detailed plan maps out order and delivery dates, order quantities, budgets, colors, and designs. It’s a joint effort, with input from every department, ensuring that we’re all in sync and ready to bring our vision to life. Transparent production planning, including shipment and delivery dates, is communicated with suppliers to keep them informed. Throughout production, updates are received to facilitate proactive responses to any delays.
To enhance clarity for suppliers, several manuals are provided to minimize confusion. These include a general supplier manual outlining instructions for delivery, labeling, and packaging. Additionally, there is a Quality Control manual offering guidance on sampling, quality control processes, and measurement tables. Standardized tech packs are utilized to ensure clear communication and avoid ambiguity.
At the close of each season, we gather for a meeting to explore potential action points for all our suppliers. We discuss various aspects including planning, design, communication, CSR, quality, and pricing. Suppliers with fewer action points will be prioritized. This ensures that we continue to foster strong partnerships built on mutual collaboration and shared goals for success.
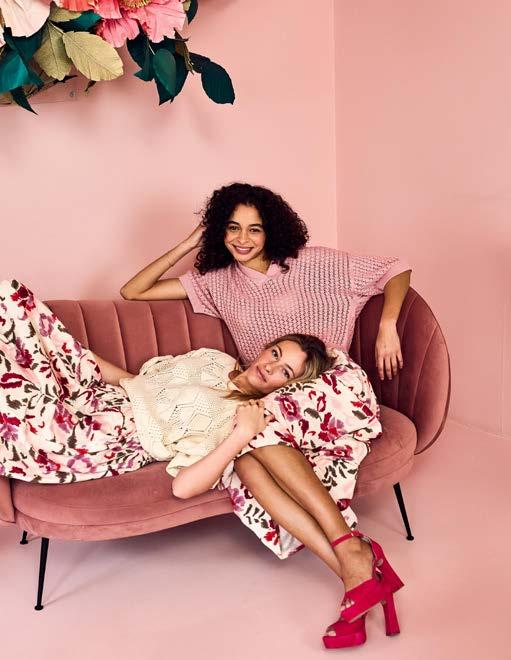
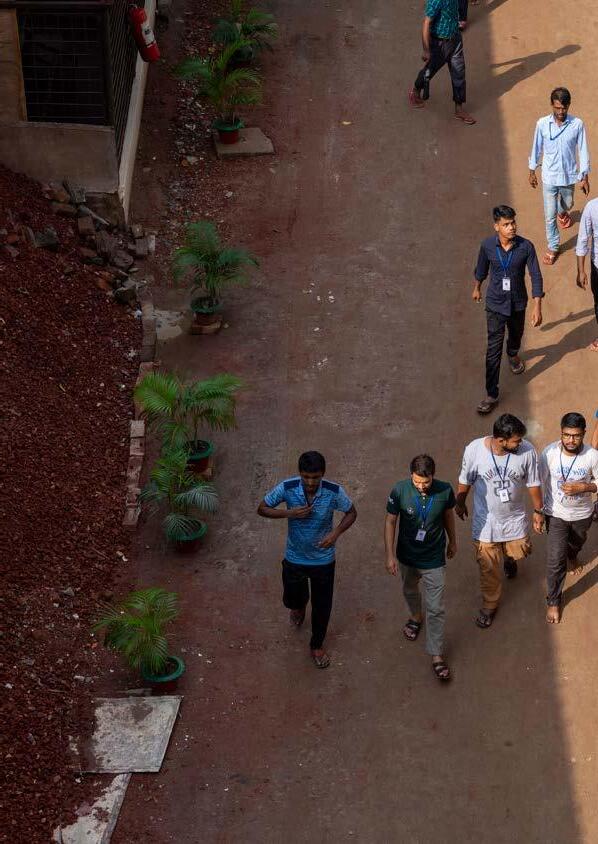
PLANET
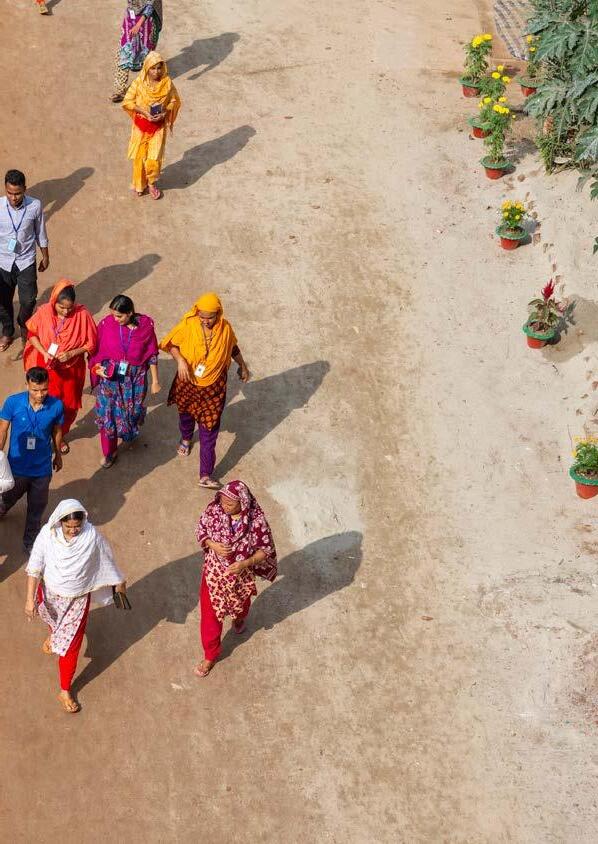
So Good, So You
The biggest C02 impact of the fashion industry today is in the production of yarns and fabrics. To alleviate this impact, we are increasingly opting for materials that are both more people- and environment-friendly.
Today, many of our materials are still conventional, but we are committed to increasing this step by step every year.
To help customers make fairer and more sustainable choices, we designate our smaller-footprint collection with the “So Good, So You” logo. This collection consists of at least 50% materials with a lower impact on people and/or the environment.
Materials included in our So Good, So You collection:
• Organic cotton
• Linen
• Lyocell/LenzingTMEcoveroTM
• Recycled materials (excluding polyester)
Circularity
Bel&Bo wants to help relieve the burden that fashion puts on the planet. Our strategy is to evolve towards circular fashion, so that waste no longer exists and fewer raw materials are needed for fashion.

In collaboration with “We Make Hope” (Wereldmissiehulp), we’ve established a take-back system. Our customers can drop off old clothing in our Bel&Back collection bins and earn points on their customer card as a reward. These points can be redeemed for our circular shopping bag or a discount. “We Make Hope” handles the collected clothing, sorting it accordingly. Wearable items are sold in their secondhand shops, while garments that are no longer usable are recycled into insulation padding, mattresses, or transformed into new fibers. We’re especially proud to offer our circular bag, crafted from recycled clothing collected through this initiative.
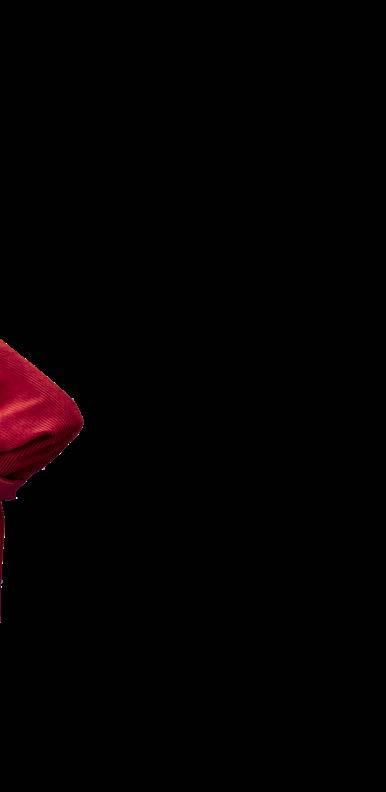
Usable clothing is sold in WMH seconhand shops
Sorting!
Shredding
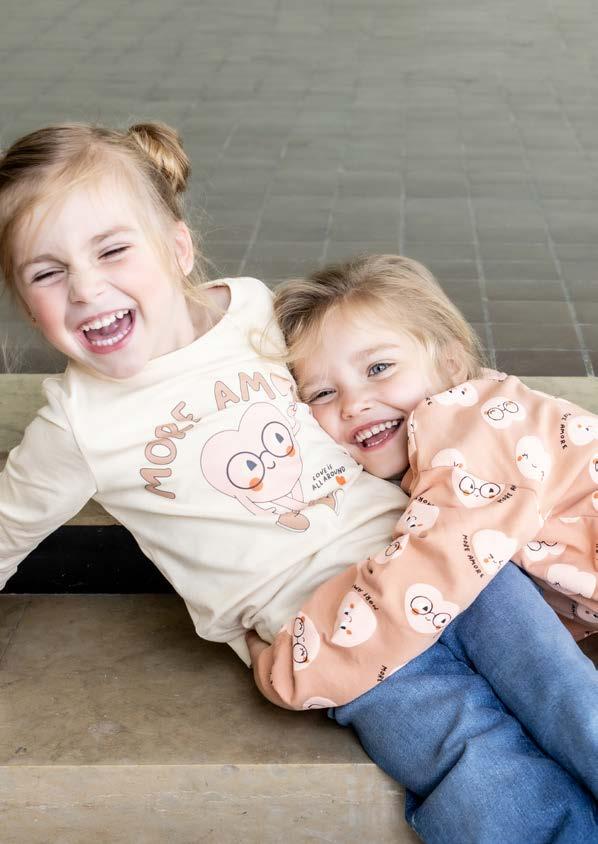
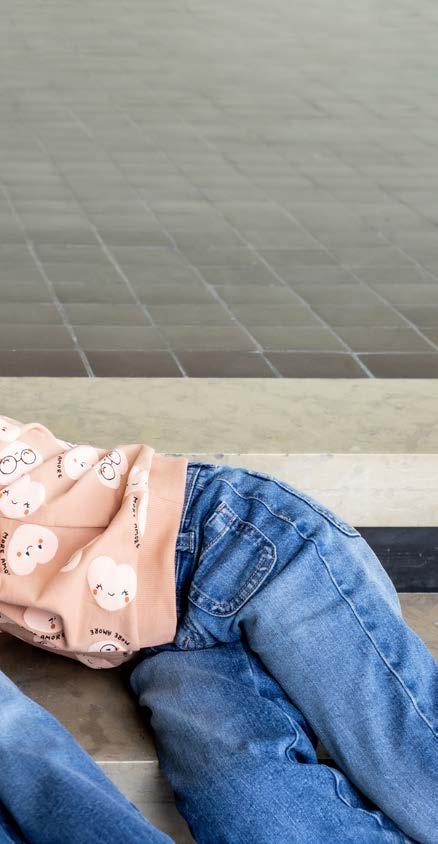
Zero waste fashion, SCIRT project
Less than 1% of textile waste is recycled into new fibres according to an Ellen MacArthur Foundation report published in 2017. This build up is not due to low consumer demand, but rather to a lack of knowledge regarding the technological, economic and environmental feasibility of recycling fibre mixtures. There is a need to align the quality and cost of recycling processes with the demands of textile companies and fashion brands. The SCIRT (System Circularity & Innovative Recycling of Textiles) project aims to develop a solution to accelerate the transition to a circular fashion economy. With the support of technical partners and research institutes, Bel&Bo will develop, prototype and produce a sweater using recycled fibres.

Reducing our footprint
In the fashion industry, the production process has the biggest carbon impact, while transport and packaging are responsible for only a small portion of the carbon emissions. However, we’re still trying our best to reduce our carbon emissions from these practices as much as possible.

Green Energy
The energy we purchase to power our head office, central warehouse and shops is 100% green and produced in Europe. At our head office, we have invested in solar panels, which provide 45% of our electricity consumption.
Energy conservation
Together with Powerpulse, we annually map our energy consumption and carbon footprint at headquarters, central warehouse and shops. This helps us see what efforts we can still make. In addition to investments such as solar panels, we have also implemented some energy saving measures, to help us reduce our energy consumption.
In our stores:
False ceilings and walls help minimize heating requirements, while motion detectors ensure lights only operate when needed. Additionally, installing on/off switches for lighting in specific areas can further conserve energy. A trial of a central control system for heating and air conditioning in stores is also implemented
In our office:
We follow market developments and see when we can invest in, among other things, a heat pump for our HQ and electrification of our vehicle fleet.
We use energy audits to see where we can save energy further.
Transport
In cooperation with Flanders Logistics, we have searched for the best route planning with the lowest possible fuel consumption. Thanks to this, we are already driving 30 000 km less per year. This corresponds to 8,000 litres of fuel and 750 driving hours.
Our online sales are shipped CO2-neutral through our partner DPD, and our flyers are also delivered CO2-neutral to mailboxes via BPost.
Packaging
Our clothing is never packaged individually. Most clothing is delivered on coat racks or packed in assortments. If we see during processing that garments are nonetheless packed individually, we pass this on to the purchasing department to take up with the supplier. The packaging of our web packages is made of recycled plastic. If, as a customer, you leave your packaging in the shop, we can have it recycled into new applications. Thanks to our plastic loop program, we avoid it becoming residual waste.
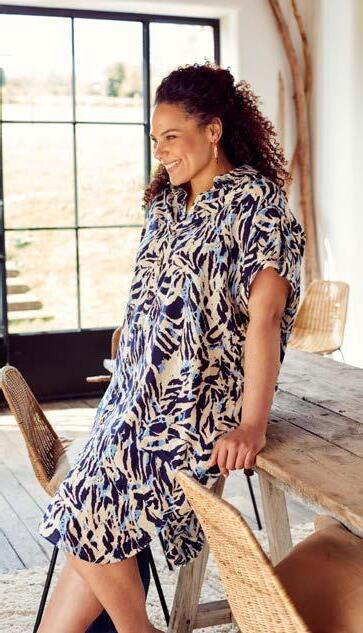
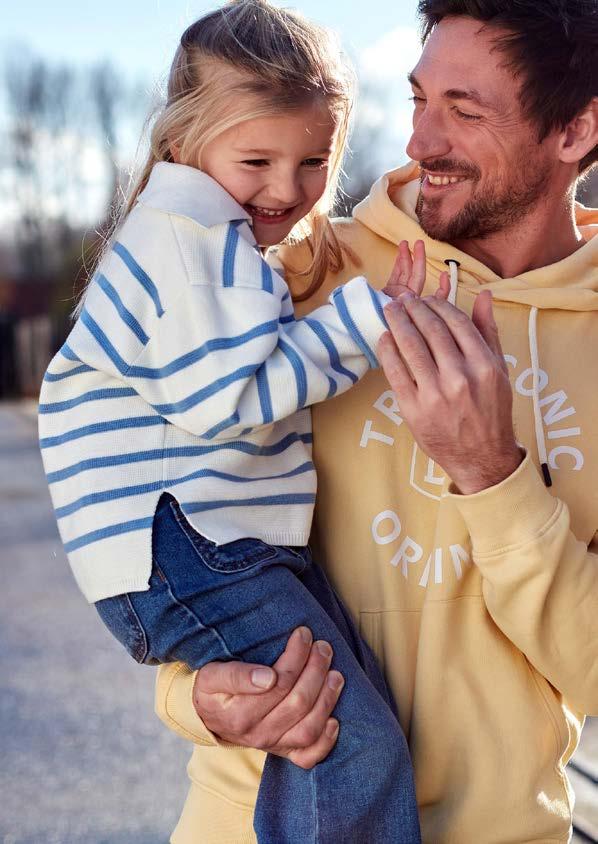
Together, we create change
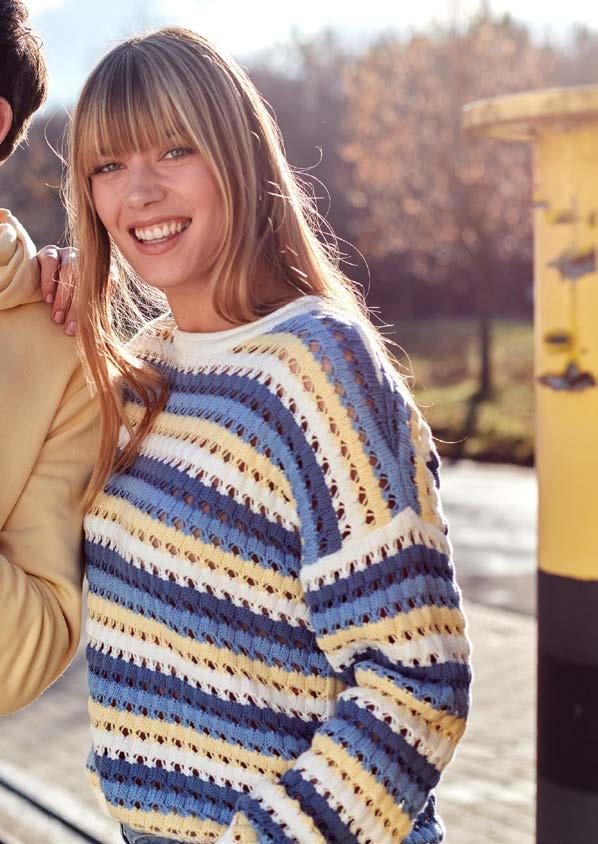