
6 minute read
FROM THE EDITOR
Labour Shortages Call For A New Way Of Thinking
Even though automation is undoubtedly on the rise with the increased adoption of AI and similar technologies, the waste and recycling industry still fundamentally relies on human workers at its core. In recent years, though, these skilled workers have become increasingly hard to find and retain.
According to a white paper from the National Waste & Recycling Association (NWRA), this labour shortage can be attributed to a shrinking pool of younger applicants and an increasing number of retirements, paired with a growing shortage of workers with the required skills to drive and operate equipment. The paper also cites difficulty finding workers with commercial driver’s licenses to drive collection trucks as a large contributing factor. Due to a lack of drivers, many collection companies have cut back on their services by suspending yard waste collection and reducing the frequency of curbside recycling services – with some companies even pausing collection altogether.
All hope is not lost, though. SWANA’s most recent report Addressing the Labor Shortage in Solid Waste Collection Services suggests a number of solutions to combat the current shortage, such as urging employers to increase compensation for drivers and helpers to make these positions more attractive to potential applicants, as well as encouraging haulers to consider using automated collection trucks to reduce workforce helper demands.
Waste and recycling companies are also getting creative when it comes to attracting qualified candidates – and retaining current employees – by offering things such as daycare services in addition to flexible schedules, training opportunities, benefits, and bonuses. GFL, for example, implemented weekly bonuses for employees who attend work all week. Other companies are drawing on outside contractors, temporary hires, and staffing agencies to address labour shortages.
Within the next five years, the NWRA expects the solid waste collection industry to have 14,000 new jobs for collection drivers and helpers, and nearly 2,000 more for technicians and mechanics. According to the association, flooding an already tight market with more jobs than there are employees will worsen the situation.
As the recycling sector continues to navigate this difficult labour market, the adoption of new ways of thinking is vital to making substantive improvements. Later in this issue, we explore the different steps that still need to be taken to attract a new generation of people to the waste and recycling industry, like leveraging TikTok, Instagram, and other social media platforms to gain the awareness of younger demographics. Plus, with a new generation that’s proving to be highly passionate about sustainability, highlighting the environmental benefits of the industry can show younger generations that their sustainability passions can be transformed into a viable career. While it’s not an end-all solution, thinking outside the box is a vital next step in the push toward a thriving industry, and it’s one that is already in motion.
I can’t give enough credit to the SENNEBOGEN service team. They worked through all the ‘interesting’ challenges that came up along the way – there are no better guys out there. Being so new, there weren’t a lot of mechanics anywhere trained on this, but they and our dealer’s mechanics have been great about coming out and working alongside our mechanics.
Barge Terminal Manager, Huger, NC
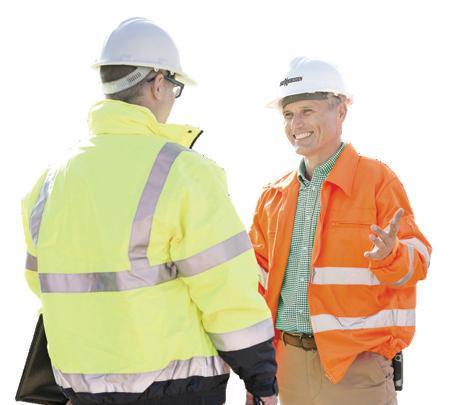
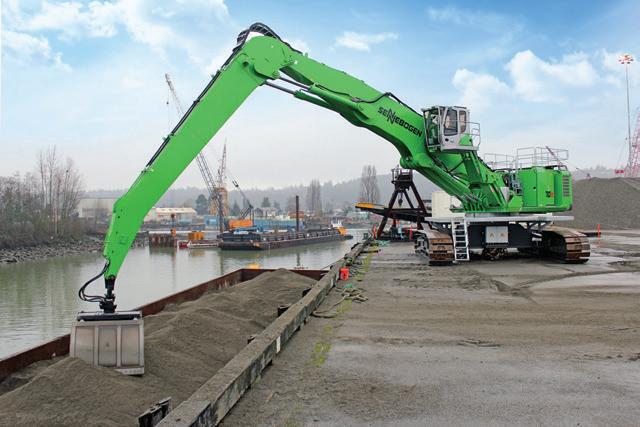
Read more about how our “Beyond the Machine” aftersale commitment ensures life-long support for SENNEBOGEN customers with the nation’s largest network of factory-trained technicians.

Tomra Opens New Test Centre For Metals Sorting
TOMRA has celebrated the opening of a second test centre at its headquarters in Mülheim-Kärlich, Germany. TOMRA’s test centres give recyclers and plant operators the opportunity to test their materials on TOMRA’s sorting machines before making an investment.
TOMRA will use the second facility to develop innovations that can be extensively tested and optimized by specialized teams on site. The company conducts approximately 650 user and internal trials each year and anticipates the demand to grow.
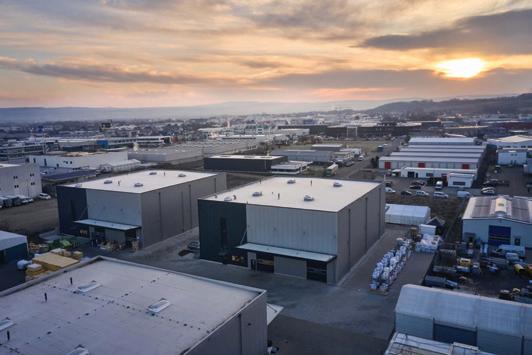
“Until recently, we’ve combined both metal and waste sorting machines in one area,” says Ralph Uepping, VP and head of technology at TOMRA Recycling Sorting. “Now, each test hall will be dedicated to one segment only. While waste sorting trials are done in the first established facility, the focus of the new facility is on metal sorting.”
TOMRA’s new X-TRACT, FINDER, and COMBISENSE, as well as a soon-to-be released machine for advanced aluminum sorting, have been installed in the new facility.
While the new facility allows the company to place a stronger emphasis on the metals segment, waste applications continue to play an equally important role. The original test centre started as a mobile test station in Andernach, Germany, before moving to Mülheim-Kärlich in 2009, and steadily grew in sophistication. It now offers 16,146 square feet (1,500 square metres) for waste sorting trials. Test possibilities include the recovery of recyclable polymers from mixed and source-separated waste streams, flake sorting, the separation of wood by material type, and more.
Deep learning technologies, a subset of AI, are also part of TOMRA’s product portfolio and can be tested in different sorting tasks. Available as a complementary solution to its core technologies, deep learning is a tool that helps improve sorting performance by detecting previously hard or impossible-to-detect materials.
CIRCULARISE JOINS AUDI’S END-OF-LIFE VEHICLE CIRCULAR ECONOMY PROJECT
Circularise has joined the MaterialLoop project initiated by Audi to move forward with its circular economy strategy and get valuable insights into how a circular economy can be put into practice.
Together with 14 other partners from the research, recycling, and supplier sectors, Circularise participated in the pilot project aimed to investigate the possibility of the reuse of post-consumer materials which are taken from vehicles at the end of their life cycle for the production of new cars.
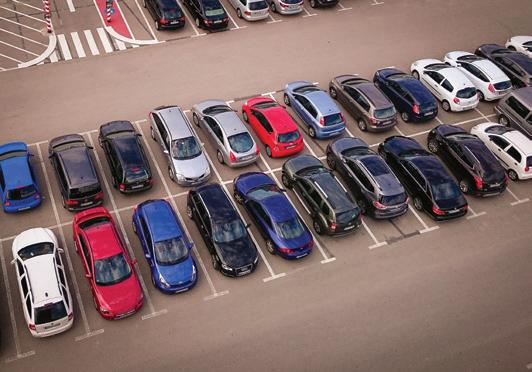
Back in October 2022, 100 vehicles, including former development cars, were dismantled as part of the MaterialLoop project. After disassembly, the car bodies were shredded and sorted into material groups comprising steel, aluminum, plastic, and glass. With the aim of testing the reuse of such materials in the production of new cars, Audi defined and piloted the further recycling process together with project partners from the recycling industry and Audi supply chain.
Circularise provided all partners with the digital tool to trace the movement of all the materials from dismantling to recycling, and consequently reuse. The goal was to avoid downcycling and achieve the most sustainable end-of-life vehicle recycling practices possible.
“Sustainability in the automotive world requires a greater understanding of all the facets of material selection and production, design, engineering, supply chain, component manufacturing, finishing, and assembly,” says Mesbah Sabur, Circularise founder. “With digital product passports, we can support traceability and accounting of the materials, processes, and impacts at each step of the value chain. This makes it easier for automotive suppliers and OEMs to accurately measure the LCA and carbon footprint of vehicles, as well as make more informed decisions regarding the circular vehicle production.”
First Terex Recycling Systems Plant Installed
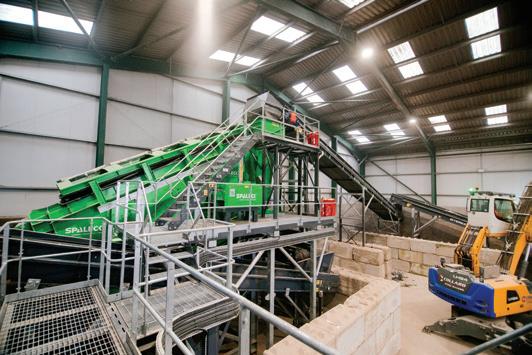
Collard Group has chosen a Terex Recycling Systems plant to increase the processing capacity of its site and recover cleaner products of higher value without adding to manual labour requirements. The plant, which is the first Terex Recycling Systems installation, was tailored to suit Collard Group’s site and the material which would be fed into it. Terex developed a process which incorporated advanced mechanical separation that would increase Collard Group’s processing capacity and recover products of a higher purity than what was previously achieved. The outcome is a plant that is processing skip waste – a mixture of commercial and industrial and C&D waste – to produce 0 to 10 millimetres fines, ferrous metals, clean 10 to 100 millimetres heavy fraction (inert), non-ferrous metals, wood, plastic, paper and card, and clean over 100-millimetre heavy fraction (inert) materials.
Plastics Market Trends
Trends are constantly evolving in response to changes in consumer preferences, technological advancements, and regulatory policies. Recycling experts at eFACTOR3 discuss trends to watch out for.
Turn to page 30 to read more.
HARRIS COMPLETES $5 MILLION EXPANSION AT GEORGIA MANUFACTURING FACILITY
Harris has completed a $5 million expansion and modernization of the company’s machining centre at its Cordele, Georgia, manufacturing complex.
The expansion and modernization of the existing 29,000 square feet added on an extra 14,000 square feet of production, training, and employee meeting space at the facility. The expanded capacity is home to CNC machining centres for turning, milling, drilling, and shaping. In total, the Harris Cordele campus is home to over 150 employees and nearly 200,000 square feet of total production space.
The Harris Cordele manufacturing complex is a 22-acre campus that encompasses facilities for fabricating, machining, cylinder manufacturing, and equipment assembly, in addition to parts, service, and administrative offices.
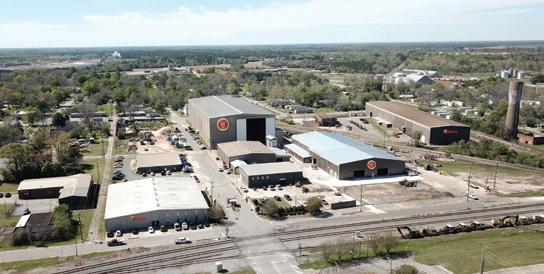