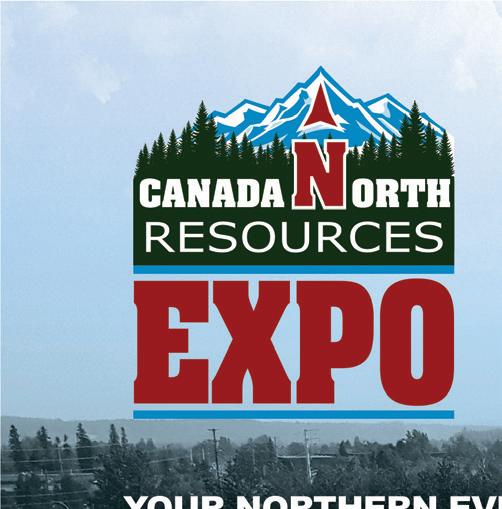
1 minute read
TURN INSIGHTS INTO PROFITS WITH AI VISION SYSTEMS
ACTIONABLE DATA PROVIDES OPERATORS WITH REAL-TIME INFORMATION TO IMPROVE OPERATIONS
The recycling industry’s role of recapturing and providing recycled content feedstocks is vital for a circular economy to succeed. Now more than ever, there is pressure to scale infrastructure and industrialize operations to boost material recovery and purity while maximizing asset capacities resulting in high-quality commodity supply to meet surging demand. Operators must understand the content of their inbound materials and have continuous visibility throughout their operation to ensure equipment and processes are producing high-quality outputs to meet the specifications of their customers.
One example of technology being utilized to provide insights that can be translated into profitability is BHS’ Max-AI Total VIS. This technology captures and analyzes live material composition data from multiple locations within a processing operation, providing operators with real-time, actionable information and alerts to adjust to changing conditions, enabling continuous improvement throughout their operations.
Other features of Max-AI Total VIS include measuring the content and composition of inbound materials and linking them with specific suppliers, while simultaneously verifying the purity of recovered materials and potential losses to residue. The system also measures process performance that can indicate upstream problems or areas for possible improvement.
The successful implementation and refinement of artificial intelligence (AI) vision systems combined with robotics led to the development of this technology. Total VIS is comprised of visual identification systems (VIS) at various chosen locations within a facility, simultaneously collecting, interpreting, recording, and presenting live data to the production staff, empowering operators to identify patterns, trends, and relationships between the system, material, and conditions. The system also provides continuous, live data streams from each independent Max-AI VIS location, as well as remote access for monitoring and reporting.

Each unit in the system is capable of accurately observing, recognizing, and relaying object detections in real time to a common location where the data is stored, interpreted, and presented in a dynamic user interface featuring customizable alert parameters, automated report creation, and raw data export for user-led studies. This structure allows users to readily observe and analyze system performance at any VIS location on a daily, weekly, or quarterly basis and quantify processing results.
With an artificial intelligence vision system, operators get actionable, real-time data that enables inbound material measurement, system performance improvement, higher commodity purity, and reduced commodity loss.
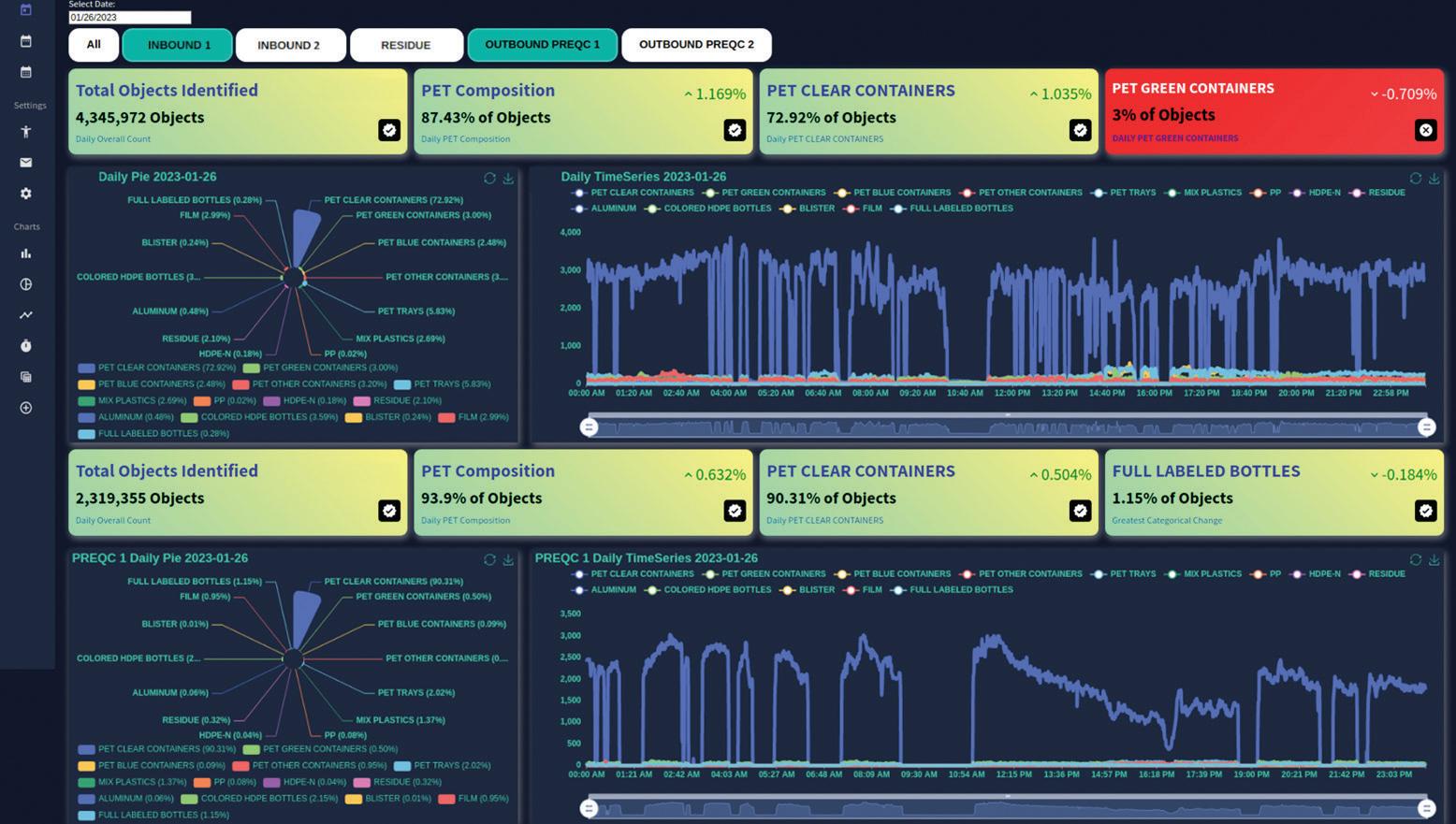
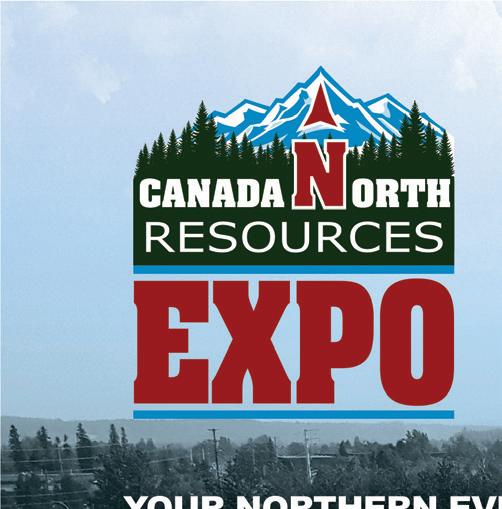

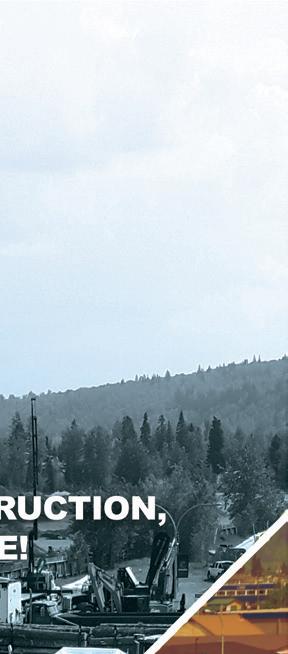



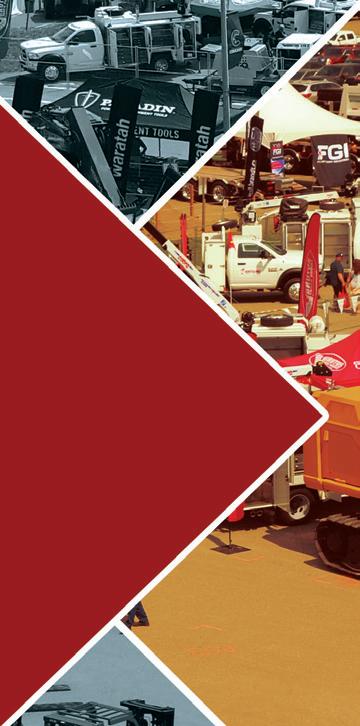
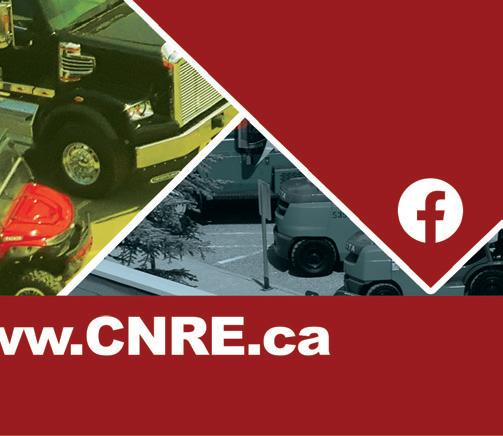
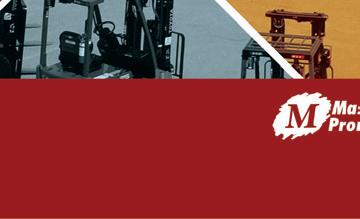