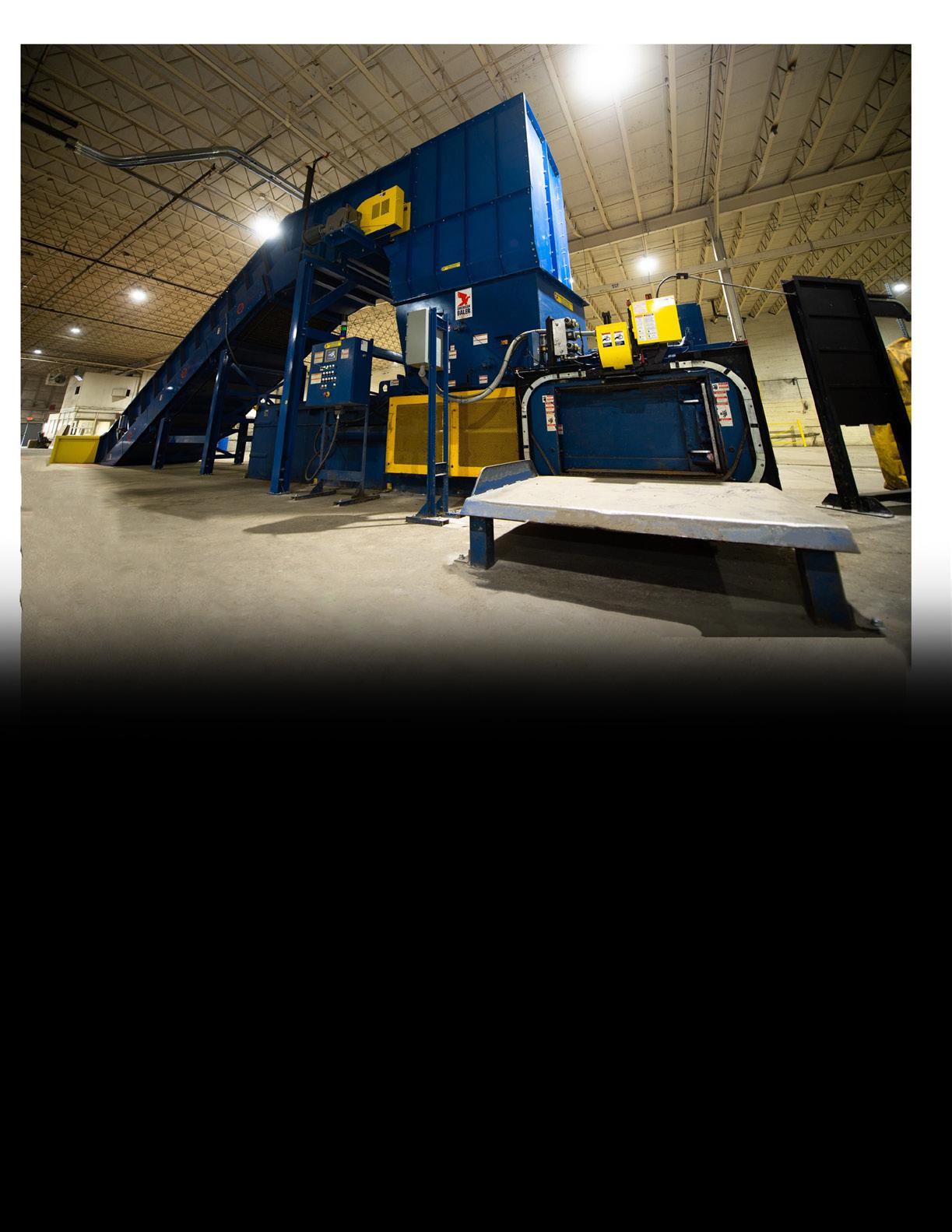
2 minute read
SPEED & P O WER
• PERFECT MIX OF PRESSURE (UP TO 4000 PSI) AND SPEED (UP TO 225 HP)
• HOPPER SIZED FOR THE LARGEST OF OCC AND TO MINIMIZE OVER FEEDING HIGH GRADES

• MANIFOLD BLOCK DESIGNED WITH REPLACEMENT CARTRIDGE VALVES THAT KEEP THE POWER UNIT COOLER AND QUIETER
• OPTIONAL STAMPER - TO MAXIMIZE RUNNING IN AUTOMATIC WITH BULKY GRADES
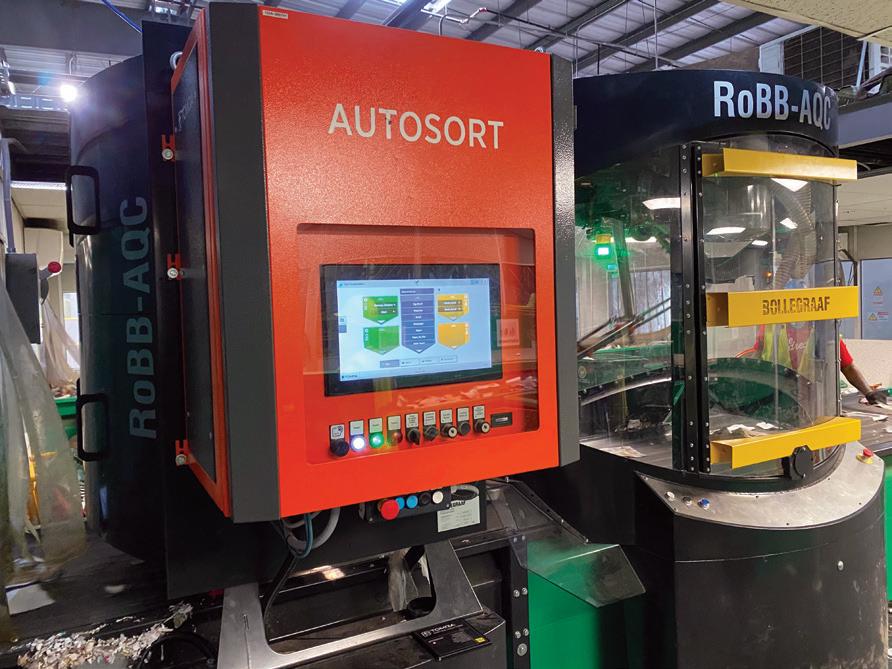
3. DO YOU HAVE A CONTAINER CLEANUP DEVICE?
An elliptical or ballistic separator (not unlike the elliptical trainer that you might see at your local gym) performs highly accurate separation of 2D and 3D materials. Paddles “walk” two-dimensional objects over the screen (items like film bags and light sheet paper). Items with rigidity (bottles, cans, 3D cardboard) bounce backwards. Also, the paddles have true two-inch holes in them to allow the last bit of glass fines to fall through. With minimal maintenance and no star changing required, the elliptical separator is ideal for the final cleanup or polishing of the container line.
If you plan to have a robot sorting on container quality control, make sure you are starting with a clean container fraction headed off to the container sorting line. If you aren’t, that robotic sorter is going to have a tough time wading through an inconsistent stream of waste items.
4. ARE YOUR CONVEYORS PROPERLY SEQUENCED?
Conveyor belts and sequencing play a large role in the success of any sorting device, including robotic sorters. Why? The goal, again, is to get the material to a single layer to give the robotic separation device a chance to succeed. There are some conveyor sequencing methods that can thin out material:
• Place two conveyors in succession and set them at different speeds.
• Use wider transfer conveyors directly prior to the robotic sorter.
• Use proper cleats on inclining conveyors that help space material and don’t clump it together.
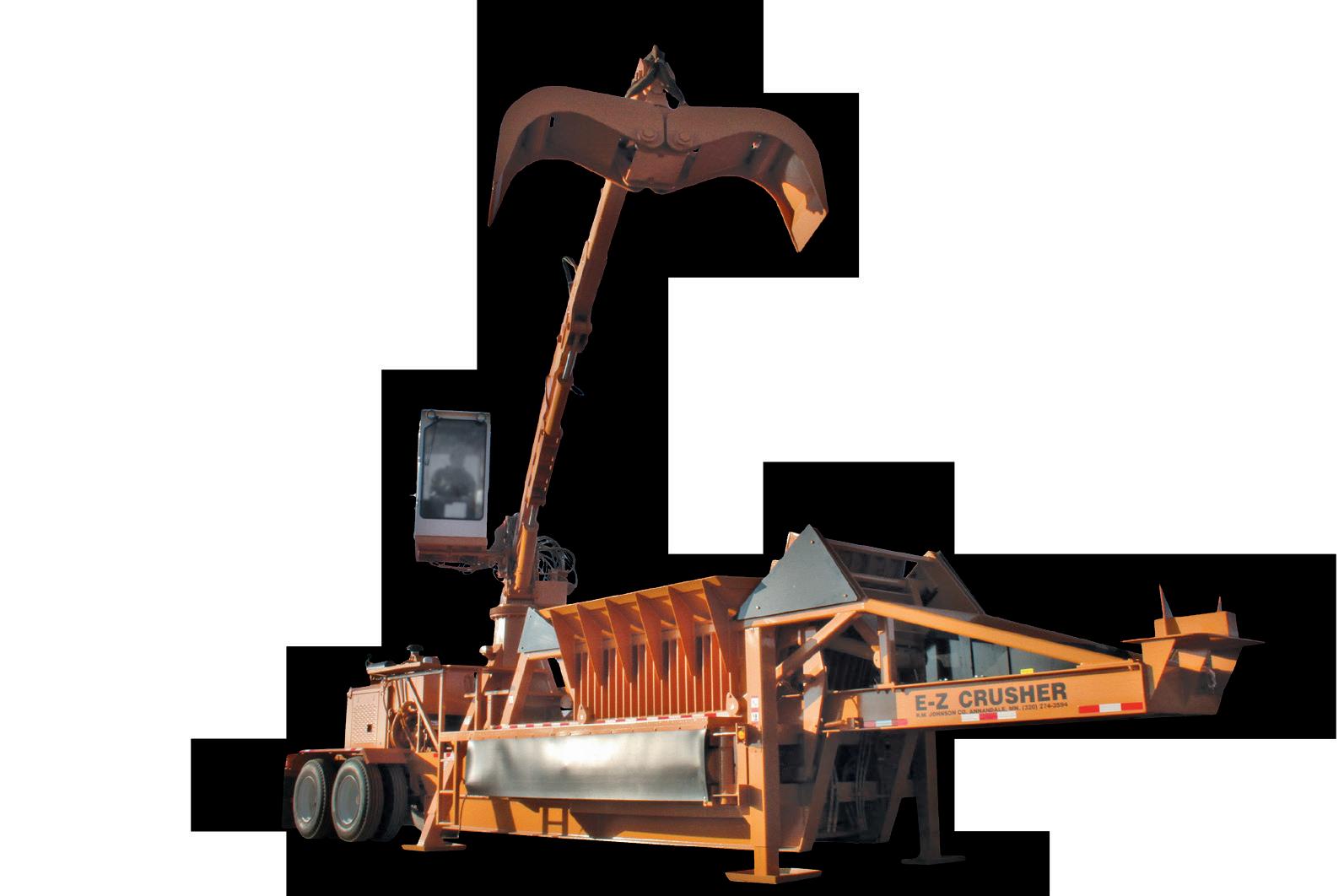
• Whenever possible, feed subsequent conveyors in line instead of at 90-degree angles.
If the material is piled up, the robotic sorting machine can’t see through the burden depth. If the robot can’t see it, it can’t sort it.
• Have all conveyors on variable speed drives to give maximum flexibility to properly sequence the conveyors. These are all small details, but they can be the difference between your robotic sorting solution performing at its best or its worst.
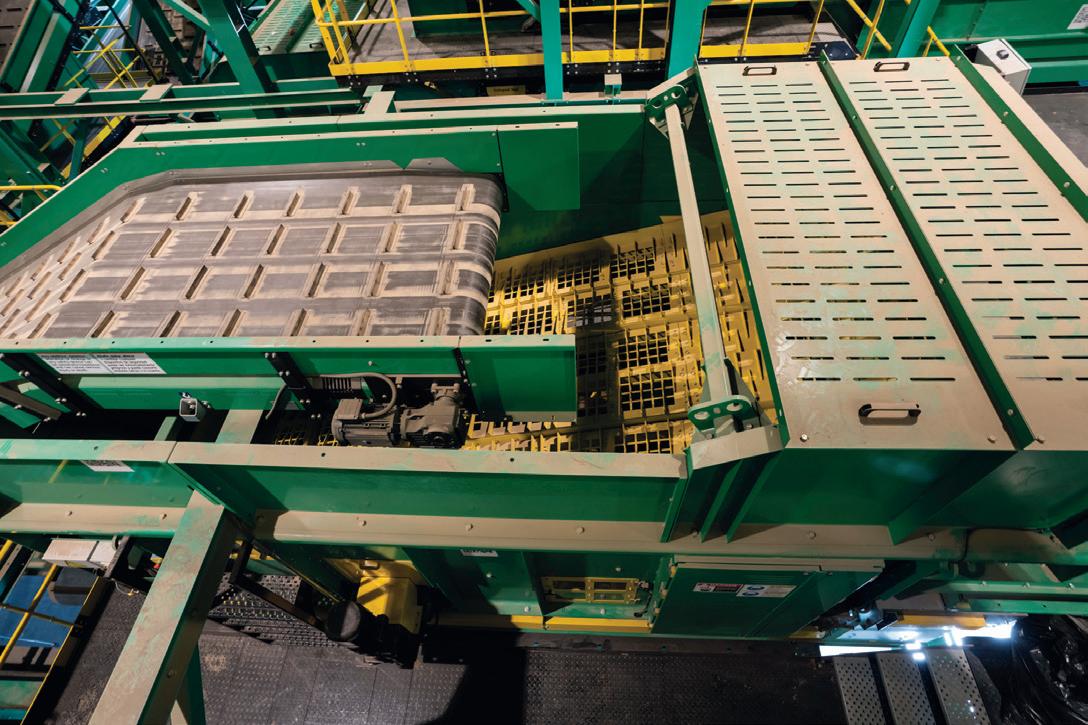
5. IS THE MATERIAL SPREAD OUT ACROSS THE WIDTH OF THE BELT?
If your system has the extra height needed, a vibratory feeder or a disc spreader could be the perfect tool to help spread the material across a wide belt for single-layer coverage to the robotic sorter. If you have a narrower incline conveyor dropping material onto a wider acceleration conveyor, this could be a problem. The material will not get spread across the full width of the acceleration conveyor and the robotic sorter may struggle with clumps of material. A vibratory feeder or disc spreader fans the material as it drops and provides even distribution across the full width of the acceleration conveyor.
The new model 4 E-Z log Baler is just what mid size scrap yards have been asking for! Priced right for any yard — small, mid size, or large!
Like the Model 3, the NEW Model 4 has no set up time and a very low cost to operate. The one man operations are all handled from the newly designed cab. With the 400º rotation crane and a reach of 27’ adding the continuous rotation grapple, it makes loading the larger chamber a breeze. Taking your loose scrap to a highly sought after shreddable log.
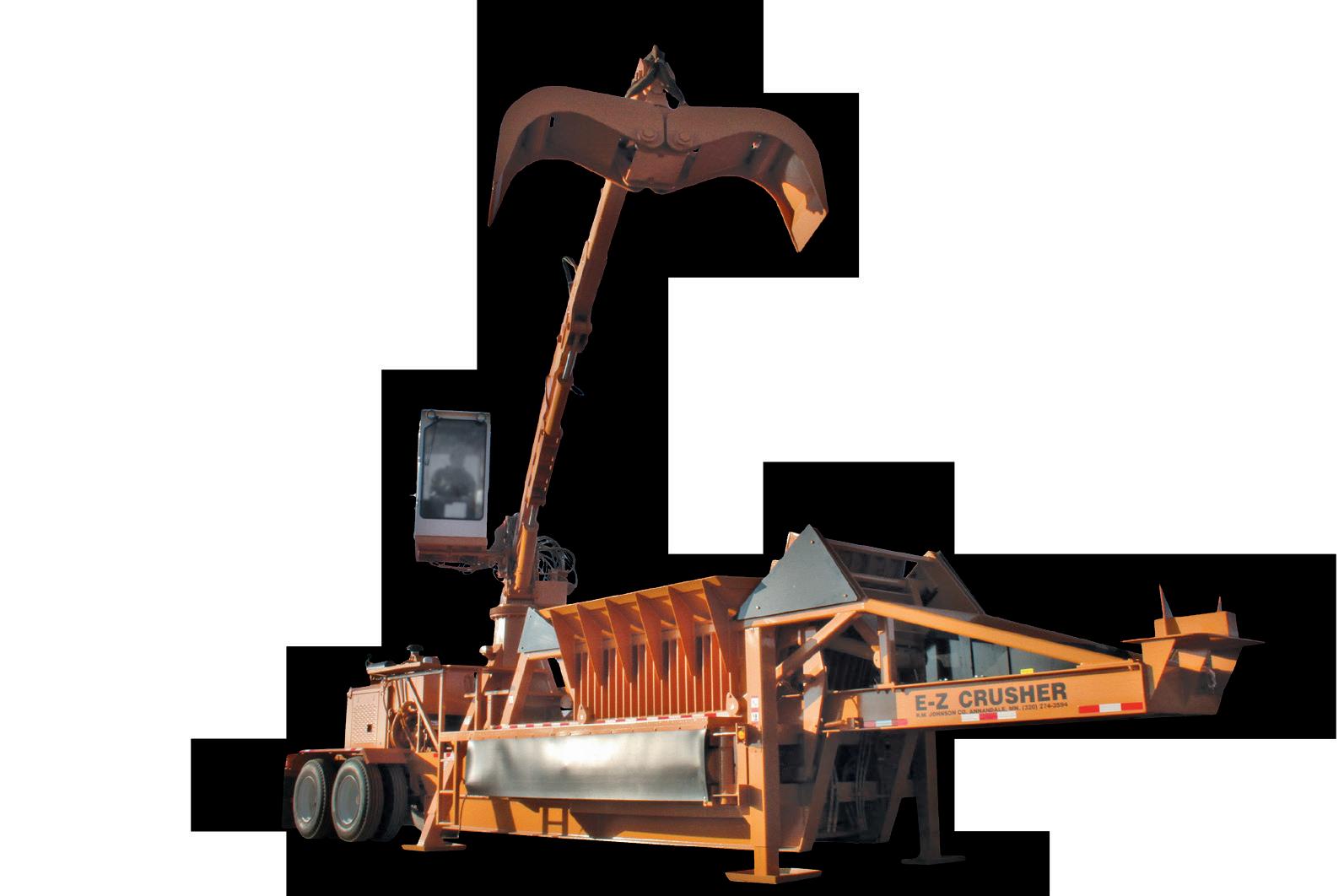
— Cycles in under 2 minutes!
— Produces up to 70 tons per day.
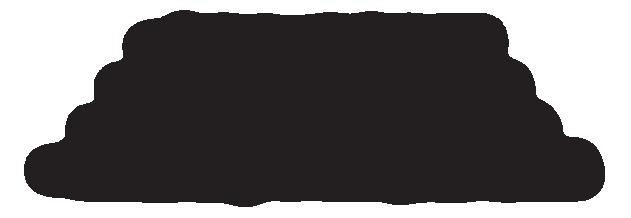
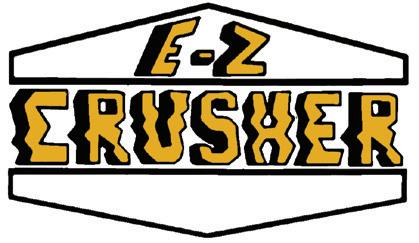
— Fully portable in the closed position.
— New seat design for more operator comfort.