
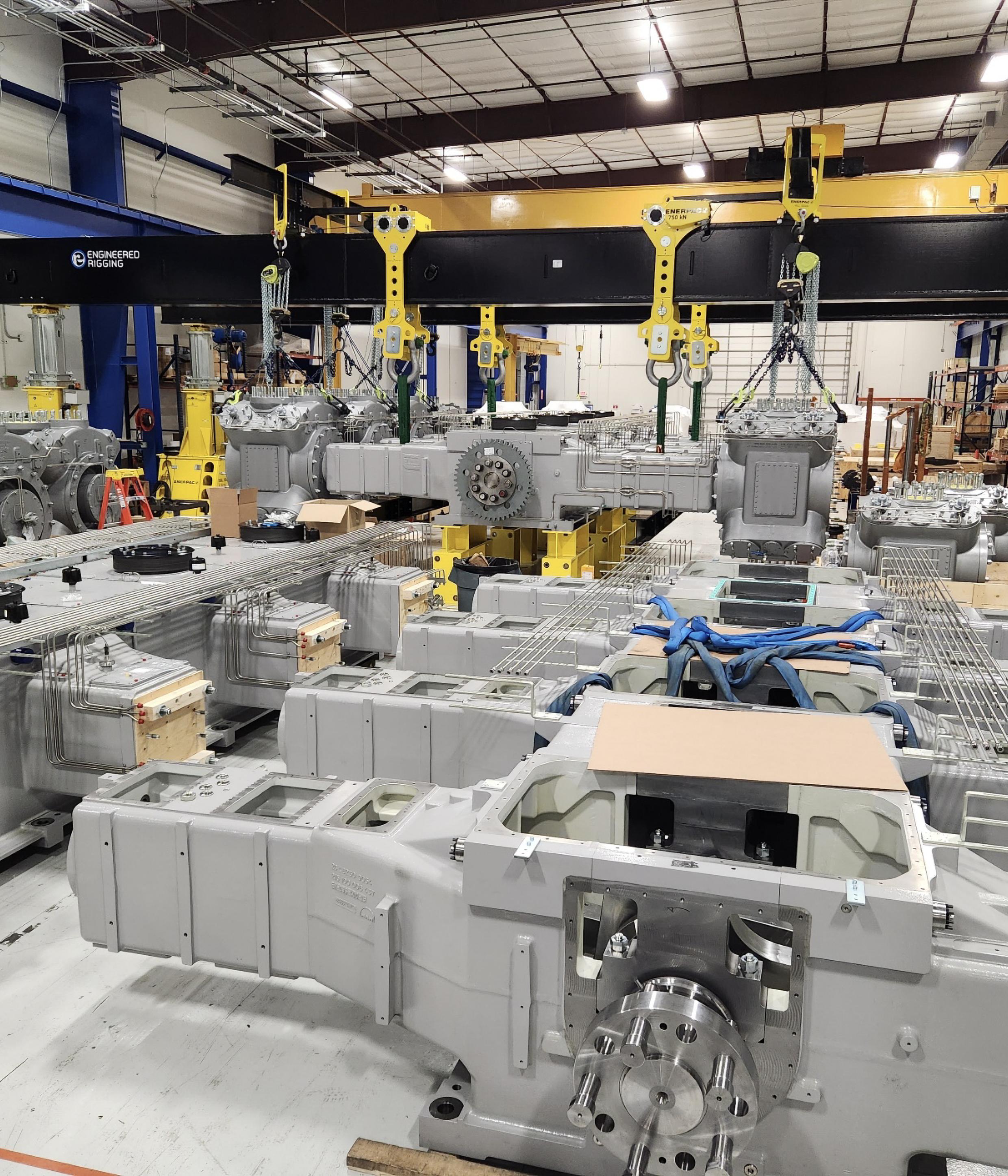


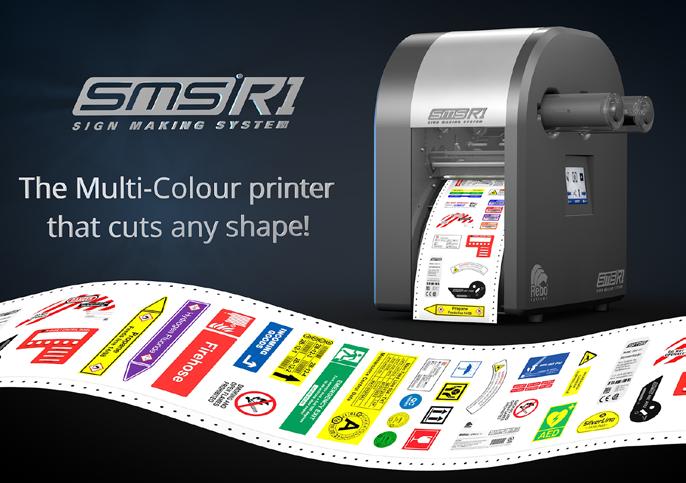
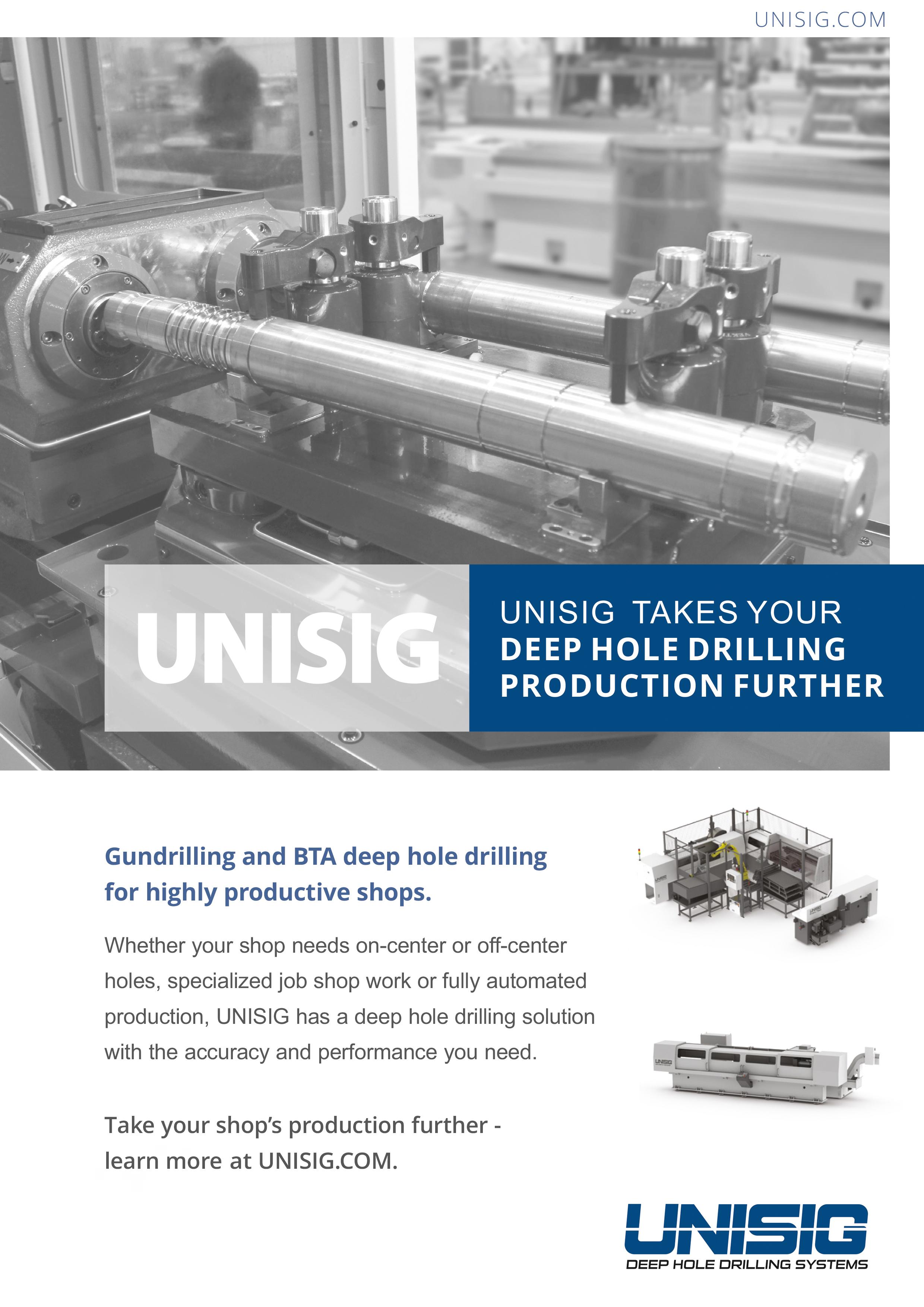
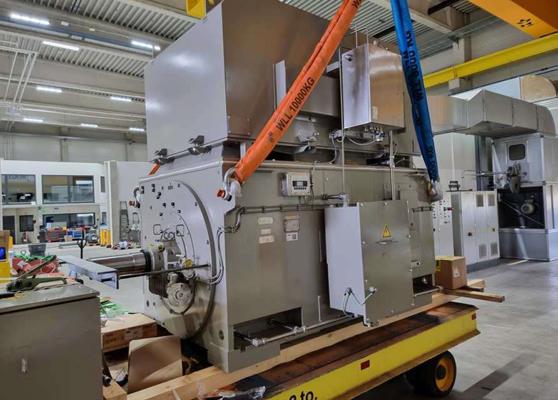
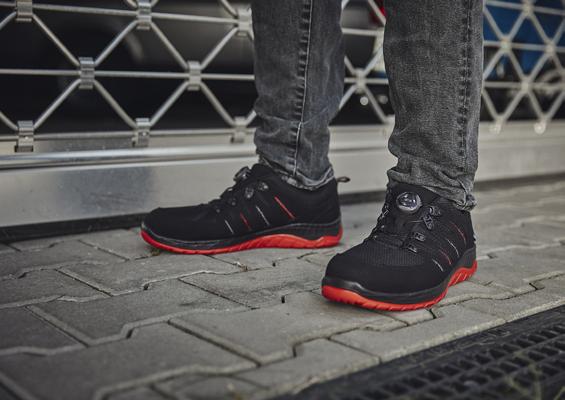
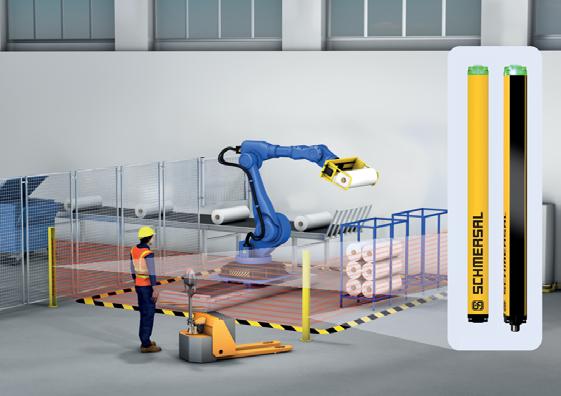
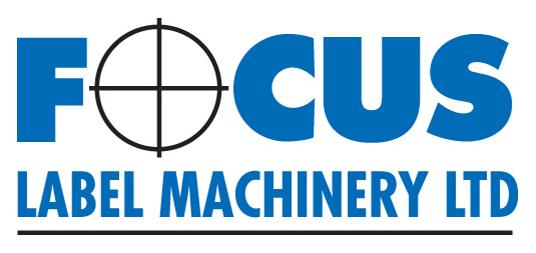
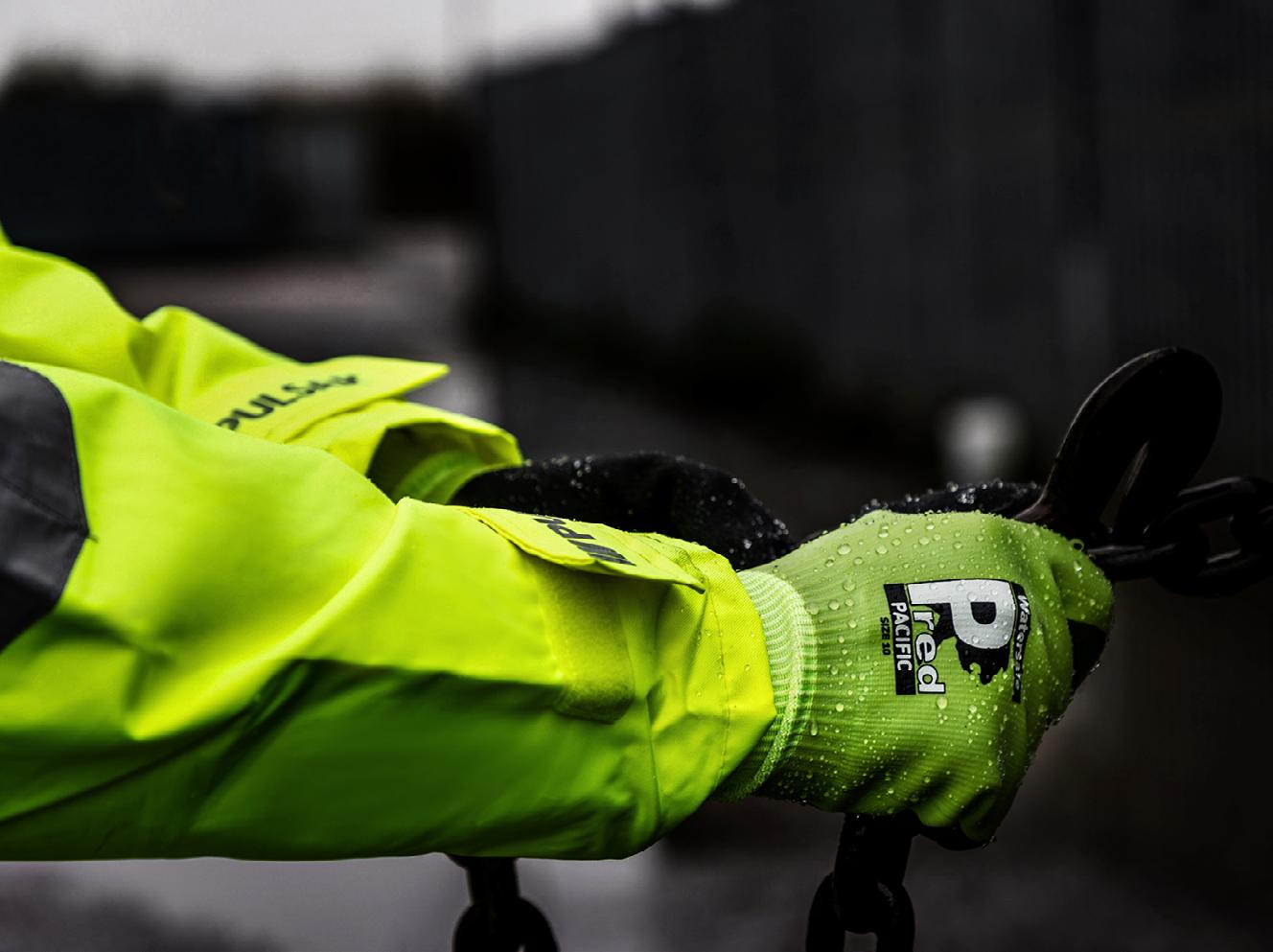
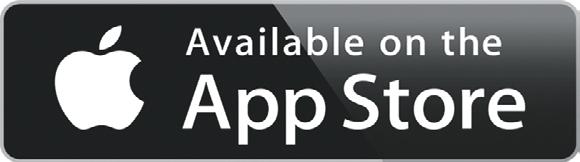
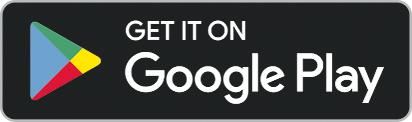
Established in 2023, Upman Laser UK has been committed to the creation and practical applications of fibre laser cutting and welding machines. With over 35 years of experience, the company provides innovative solutions to its clients’ needs and with quality, Upman can advise on the most effective equipment to be used for their customers varied projects.
Upman has three facets of corporate culture that lie at the heart of its business ethos. The Core Values embraces commitment, professionalism, integrity and innovation. The Upman Mission is to be known by every customer in the metalworking field and finally the Upman Vision which is to be the leading supplier in the laser processing industry.
Utilising the latest innovative technology, Upman looks at all parts of the welding process and how to make it more streamlined and effective for its customers. Maintaining high quality component parts increases an accurate and reliable result. For example, using a CypCut or HypCut operating system simplifies the complex CNC operations and
incorporates CAD, Nest and CAM modules into one unit. Essentially allowing everything from design to cutting to be completed with minimal effort.
The laser cutting head can be adjusted automatically for more precise focus making the process convenient, fast, and accurate. The head has a variety of choices which can differentiate for different laser needs such as welding, surface treatments and cutting.
The machine bed is constructed to strict guidelines to ensure
that reliability and durability are built in. To achieve this, each bed has heat annealing applied that alters the physical properties of the bed to increase its ductility and make the bed more malleable. The shot blasting occurs which is the propulsion of specific abrasive materials, fired at high velocity via a centrifugal wheel using kinetic energy to blast the abrasives.
The gantry used on all Upman machines, is constructed to Aerospace standard, and made from light-weight aluminium. As Aluminium has a resistance to corrosion and fatigue, it makes the components more durable for long-term use.
Two areas that Upman UK specialise in is Laser Cleaning Systems and Fiber Laser Welding. The Laser Cleaning System is an ecological positive process that removes substances such as oxides and paint rust without the use of industrial cleansers which can be time consuming and potentially hazardous, whilst sandblasting could damage the machine or the metal underneath while Laser cleaning is more cost-effective and reduces long-term maintenance. Fiber Laser Welding is a unique welding capability, which maximises penetration whilst using a minimal heat input. Coupled with auto single or double wire feed, the fibre welders are simple, effective, and easy to use.
For the future, Upman is taking a note of trends within the industry and whilst it is not legislation for laser safe enclosures to be installed as standard, Upman can offer bespoke solutions for specific requirements for a safe working environment. Within the Upman group, a number of live webinars and online tutorials are made available through the Academy Class, for the long-term education of the new generation of workers within this high-tech field,
Contact T 01482 420491 M 07743 989565 info@upmanlaser.co.uk www.laserweld.uk
Menzel Elektromotoren fills a gap in the market with its range of pressurised Ex p motors, configuring them from stock components in the shortest possible time.
Menzel recently built an Ex p compressor motor for an internationally active Austrian chemical company within three weeks. The squirrel cage motor from the MEBKSW series was modified in various ways to suit the application and sitespecific requirements.
The motor case was fitted with an air purge system that allows the motor to be flushed with an inert gas mixture before startup in order to remove potentially explosive atmospheres and to maintain
a constant positive pressure during operation, thus preventing ingress of hazardous gases.
The motor was labeled II 3G Ex pzc IIB T3 Gc. Additional works included: conversion to cooling type IC 81W (water-cooled), mechanical adjustment from size 560 to size 630, repositioning the terminal boxes, preparation of the neutral box for the installation of current transformers, adjustment of the flanges for the slide bearings and installation of vibration sensors.
Menzel visited the customer’s plant even before the order was placed to discuss details and observe the installation situation and eventually also installed and commissioned the drive system.
In 2023, Menzel received the TÜV certification for the manufacture of squirrel cage motors in ignition protection type Ex p, pressurisation for Zone 1. The German motor builder can apply the manufacturing procedure to stock motors in a wide output range and is thus able to quickly and flexibly provide competitively priced Ex p motors featuring the product categories 2G and 3G.
www.menzel-motors.com/ pressurized-exp-motorszone1-operation
Wieland Electric presents the latest generation of highly efficient safety light grids and safety light curtains.
The importance of occupational safety grows in modern industrial and logistical environments as machines and systems become more complicated. Against this backdrop, Wieland Electric introduces its next generation of safety light curtains and safety light grids, which complement the existing array of optoelectronic protection devices and are distinguished by a high level of safety, flexibility, and use.
The new SLG4 series safety light grids were designed for applications requiring dependable access protection over wide areas on machines or in production sites. While withstanding temperatures as high as 70°C, the light grids may be put into action swiftly thanks to their simple software configuration and plug-and-play installation. Clearly visible LEDs also enable immediate on-site diagnostics, reducing downtimes.
Furthermore, the durable aluminium housing and protection rating IP65/67 in accordance with EN 60529 ensure that the optoelectronic protective devices perform reliably even in adverse environmental situations.
The SLC4 series safety light curtains are perfect for protecting fingers and hands in the machine's danger zone. When the machine is used frequently, they cut access times compared to physical guards, increasing production. Advanced functionalities like muting ensure safe material flow and contribute to cost-effective material supply and removal.
Cascading two devices enables vertical access and horizontal presence monitoring in a single system.
The SLC4 safety light curtains, like the SLG4 safety light grids, have a simple software-free configuration and the ability to do quick on-site diagnostics. This improves productivity and safety in industrial applications.
www.wieland.co.uk
The oxygen sensor MFOxy-Comp has been specially developed for use in composting plants. The materials used meet the high requirements of this field of application. The measurement method is based on a dynamic process at two zirconium dioxide slices, which form a hermetically sealed chamber. The entire measuring range is linear.
During operation the sensor system monitors its own function and reports in case of hardware and sensor malfunction.
The calibration is done without reference gas in atmospheric air. The output of the measurement values takes place via an analog (420mA) and a digital channel, the latter transmits the error messages.
The oxygen sensor MF-OxyComp is designed for the measuring range 0.1 to 25 vol% oxygen and equipped with an analog interface with 4-20mA and has a digital output as well.
sales@logidatatech.com www.logidatatech.com
Established in 1895 by Joseph Bierbaum, Kornbusch & Starting is a family run manufacturer now in its fourth generation of the Bierbaum family. Out of its headquarters based in Borken, North-Rhine Westphalia Germany, the company manufactures private labels for cloths, wipes, and sponges for international retail chains and drug stores in Europe, North Africa, South Korea and the USA.
Specialising as a private label manufacturer for the FMCG industry, as well as the professional sector, Kornbusch & Starting has innovated a vast range of products that have a strong emphasis on delivering sustainable solutions.
Combining traditional and modern manufacturing, the company has multiple production sites. Its fully integrated production for textile cleaning cloths made of viscose takes place in Borken, Germany. In Wald-Michelbach, its focus is on the production of household sponges using special processes, and includes all the processing stages from coating to fully automated final packaging. Finally, its fully integrated sponge production in the Czech Republic includes the complete processing of delivered sponge blocks through to fully automated final packaging. By using modern systems and automated processes, high quality and flexibility is guaranteed through all stages of the production line.
Thanks to modern production processes and a strong focus on quality and sustainability, its products are created to meet the highest standards, meeting
the needs of international and local retailers, professional cleaning suppliers, and distributors around the world.
Innovation and production quality has always been at the heart of the company. Named as the first manufacturer in Germany to switch from single-use plastic to paper banding together with its partner, Kornbusch & Starting not only respond to trends and changing market requirements, but also initiate trends, such as innovative sustainability and quality concepts – setting new market standards.
This innovation reflects the company’s strong commitment to environmentally friendly packaging solutions that have had a lasting impact on the industry. Sustainability has become one of the most integral parts to every business here in the UK, and this is an area that Kornbusch & Starting is looking to grow its customer base within. Therefore, in order to better service the UK market, the company is working to reduce the amount of plastic in its products.
By developing and implementing new materials and packaging solutions, the company strives to minimise its environmental footprint and promote more sustainable alternatives. The goal is to reduce environmental impact while maintaining the quality of its products.
Over the years, the company has remained committed to reducing CO2 emissions through targeted initiatives that drive continuous progress in sustainability.
By embracing innovative solutions such as plastic-free packaging and materials derived from natural raw sources, the company significantly minimises plastic consumption. In collaboration with its customers, it continues to develop sustainable packaging strategies, working toward
a plastic-free future.
As one of the leading private label providers in its segment, Kornbusch & Starting combine decades of experience with pioneering product development. One of its latest products to hit the UK market is ‘Drop Buddy’ – a private label thermoflex sponge with a texture which is firm in cold water and soft in hot water.
The Drop Buddy is more than just a sponge – it’s
a dependable cleaning companion designed for efficiency and precision. Its ergonomic shape ensures easy access to even the toughest corners, while AIpowered technology enhances its performance. Made in the EU, it seamlessly blends innovation and quality to deliver exceptional cleaning results.
Its complete adaptability means that it becomes hard in cold water and soft in warm water, making it the ideal sponge for any cleaning task. It is perfect for the kitchen or bathroom as it effortlessly removes stubborn dirt and limescale. What’s more, customers have harked at its versatility uses and have loved the additional extras that can also be included that feature a junior version, a magic eraser, or even custom printed designs.
Recently, Kornbusch & Starting revamped its website, introducing a fresh, modern look with a clearer brand identity. As part of its commitment to innovation it has upgraded its corporate design including updated site features such as a redesigned logo that represents the company’s evolution. The new appearance reflects Kornbusch & Starting’s commitment to clear, cohesive communication, showcasing both its values and future direction.
The reasoning behind some of the changes are explained here in this company statement, “The revised logo reflects our evolution and expanded product range. A special detail is the diamond – it is not only a modern design element, but also part of the logo of our parent company, the Bierbaum Unternehmensgruppe GmbH. In this way, we underline our affiliation and unity within the group.
“We want a uniform corporate identity that extends from the website to signatures and all communication. We also want a modern, highquality visual identity that reflects our self-image as an innovative private label partner.
“A relaunch is more than just a new design – it stands for progress, further development and a clear view of the future. We are looking forward to what is to come and for others to discover our new appearance!”
Kornbusch & Starting is trusted for its guaranteed standards, boasting certifications that are an essential part of its quality promise. In addition to specific certifications, including the OEKO-TEX Standard 100, Global Organic Textile Standard, Business Social Compliance Initiative, Forest Stewardship Council®, and IFS Broker, the company also operates according to recognised management systems such as ISO 9001 for quality management, ISO 14001 for environmental management, and ISO 50001 for energy management.
T +49 2861 94802
info@kornbusch.com www.kornbusch.com/en
The Health & Safety Event, held at Birmingham’s NEC from 8-10 April 2025, is the UK’s largest gathering of anyone responsible for running a safe and efficient workplace. With an extraordinary line-up of seminars, practical workshops, and exhibitors, it attracts thousands of workplace professionals from the industrial, commercial, and public sectors.
The Health and Safety Event is strategically colocated with 5 other events – The Fire Safety Event, The Security Event, The Workplace Event, National Cyber Security Show, Professional Security Officer Live – meaning you can access even more content, more products, and more exhibitors in new markets.
t Elevate your expertise and knowledge, while gaining CPD points through our expert-led content
programme.
t Stay up-to-date on regulatory changes and industry best practices essential to your role as a health and safety professional.
t Explore the latest products and solutions to improve health and safety standards.
t Network with the entire health and safety industry, with professionals from various industries and sectors.
Helping you navigate around the show and find PPE suppliers
Non-compliant and potentially unsafe PPE is a growing issue within our industry. Many products on the market are claiming to be CE approved but in reality, are not certified to the appropriate European standards and putting lives at risk.
In partnership with British Safety Industry Federation (BSIF), we introduce the Registered Safety Supplier
Trail. All suppliers of this trail are members of BSIF and have signed a binding declaration that the safety equipment and services they offer meet the appropriate standards, fully complies with the PPE regulations and is appropriately marked. Follow the trail and be assured that the PPE you are buying from is a Registered Safety Supplier.
The Health & Safety Event is partnering with Driving for Better Business, to deliver a unique feature for delegates in the form of our Driver Safety Zone. This zone will share vital information and resources with safety professionals who have responsibility for workrelated road risk.
Collaborating with a number of specialist partners, this zone will provide invaluable information and expert support to any safety professionals who are responsible for managing work-related road risk. We will be sharing expertise, leadership and best practice in the management of driver safety.
Contact www.healthandsafetyevent.com
At the Heatlh & Safety Event on Stand: 3/Q10, German manufacturer Elten will be presenting a wide range of safety shoes that are suitable for almost every area of application in industry and trade. In Birmingham, for example, models such as the ‘Antonio XXSG GTX Mid ESD S3S WR CI’ and the ‘Francesco XXSG black Mid ESD S3’ will be among the highlights on the Elten Stand: 3/Q10. Both models are equipped with a modern outsole called ‘Wellmaxx Safety-Grip’. Its coarse tread prevents slipping on wet surfaces. A negative profile at the ends of the sole also prevents tripping and twisting accidents.
The model ‘Antonio XXSG Mid GTX S3S WR CI’ is equipped with a modern outsole called ‘Wellmaxx Safety-Grip’ and the extremely hard-wearing ‘Extraguard’ upper material from Gore
The highlight: the sole is equipped with a core made of the high-tech material Infinergy® from BASF. This particle foam has extremely resilient properties and returns more than half of the energy expended back to the wearer. This is particularly important on hard indoor floors. It is easy on the joints, allows the feet to tire more slowly and thus helps to maintain concentration even at the end of the working
day. While the ‘Francesco’ is made of cowhide, the ‘Antonio’ is made of the extremely robust ‘Extraguard’ upper material from Gore-Tex. This upper material remains light even when wet and absorbs little to no moisture from the outside, even after prolonged use; it is 40% lighter than leather and yet very durable.
Elten also has tried and tested classics such as the ‘Maddox Boa® black-red’, which also comes from the ‘Wellmaxx’ series. The ‘Maddox’ is also a reliable partner thanks to its Boa® fastener. This allows the shoe to be closed with just one twist – no need for laces. Accidental loosening is therefore impossible. In addition, the clever wire lacing system means that the fit of the shoe can be optimally adjusted to the individual foot shape using a rotary knob.
Sophisticated foot protection concepts and technological innovations – these are the strengths of the German safety shoe developer and manufacturer Elten. The medium-sized family business is based in Uedem on the Lower Rhine and has been
manufacturing foot protection for over 115 years. Elten currently employs over 400 people and achieves an annual production of over 3 million pairs of shoes, which are sold throughout Europe. Users and their needs are always at the centre of the development of new models. These not only offer safe protection against injuries, but also fulfil the requirements of ergonomics, wearing comfort, keeping feet healthy and modern design.
Elten is one of the best-known brands in Germany –and not just in occupational safety. As a sponsor of Bundesliga football clubs Borussia Mönchengladbach and Union Berlin, among others, the family-run company from North Rhine-Westphalia stands for emotion, fun and team spirit.
https://elten.com/en
The UK’s leading specialist in the supply of products and services to tackle Hand-Arm-Vibration-Syndrome (HAVs)
HAVsHAVi is the UK’s leading specialist in providing solutions to help you comply with HSE guidelines for managing Hand Arm Vibration Syndrome. HAVi ACTIVIQ is a game changing new solution from HAVi Technologies. Coming from over 16 years of working with companies to help them comply with the vibration regulations, this solution enables you to make Better Decisions, Faster.
is a serious and debilitating condition, affecting over two million people in the UK alone. It develops when prolonged exposure to vibrations from power tools and machinery is transmitted to the hands and arms of workers.
HAVi products leverage cutting-edge technology and data-driven analytics to help mitigate these risks. Its Integrated Solution identifies both existing and emerging HAVs hazards within a business, empowering you to take proactive, corrective action to protect your workforce.
Featuring real-time alerts of exposure breeches, Intelligent Exception Reporting and a permanent record of both tool and operative performance, the HAVi Integrated Solution even has HSE Guidelines hardwired into its DNA.
Protect and safeguard your employees using HAVi’s latest technology – The HAVi Total Diagnostix platform, which is the beating heart of the Integrated Solution. Saving you time by eliminating all paper-based
systems, data collection is made easy and straightforward with a Bluetooth enabled Smart Watch worn by the operative, that alerts them to potential HAVs breeches.
Using cutting edge Cloud Based Analytics to identify and automatically alert for exceptions and trends, the HAVi Total Diagnostix platform keeps managers updated on their teams critical HAVs data, with clear and immediate state of current and emerging HAVs risks across the entire business.
Visit HAVi at the Health & Safety Event 2025 on Stand: 3/M80
Contact T 0115 932 7002 support@thehavi.com www.thehavi.com
At Boplan, we understand the importance of safety in the workplace. While prevention, training and signs are important, they do not prevent all accidents. That is why we offer a wide range of safety products that protect workers from specific risks in various work environments.
t Safety gates provide controlled access to specific areas.
t Safety barriers with handrails absorb the impact of vehicle collisions and force pedestrians to follow the walkway.
t Handrails provide an effective barrier between pedestrians and hazardous areas.
t Kick rails with handrails absorb impacts at ground level and keep pedestrians safe behind a barrier.
Boplan® develops and produces high-quality polymer safety solutions for industrial environments and sporting events. Our innovative and durable fall and impact protection is the reference in impact
absorption and protects people, vehicles, buildings and infrastructure worldwide in warehouses, production sites, logistics centres, cold storage facilities, (petro-) chemical sites, car parks and airports.
With over 25 years of experience, our comprehensive range of products includes safety barriers, handrails, bollards and column protectors. All solutions are designed to withstand extreme conditions and meet the strictest safety standards.
The DG250F: Unmatched strength and versatility
The new and improved Dock Gate sets a new standard in fall protection and impact resistance for loading areas. Designed with a tube-in-tube structure and robust base plates, it offers unparalleled protection against impacts up to 16kJ, both to the posts and the rails.
strongest polymer safety gate. With this Dock Gate, employees can work with confidence, knowing that their safety is guaranteed.
Visit us at The Health & Safety Event in Birmingham, 8-10 April 2025
The safety gate, made of highperformance polymer, features ergonomic handles and an assist mechanism for effortless manual operation. For even greater convenience, a motorised version is now available, making it easier than ever to secure loading docks or restricted areas. Compact, efficient, and easy to install, this dock gate is the world’s
Since 2001, Rapid has been a trusted global leader in workplace safety software, helping businesses protect their people, visitors, and contractors. Thousands of the world's most respected organisations rely on Rapid to streamline workplace health and safety, compliance, and risk management while driving operational efficiency.
Designed for the AI age, the Rapid One platform optimises health and safety processes, enhancing efficiency while ensuring compliance. With advanced AI-driven features, it delivers a seamless, end-to-end safety solution through its simple and award-winning SaaS subscription model, helping businesses stay ahead of evolving
safety regulations and industry demands.
Headquartered in Australia, Rapid has presence across the US, Asia, Europe and Africa. In June 2023, Rapid opened its UK office, based in West London, strengthening its presence in key sectors, including: Facilities Management, Manufacturing and Logistics, Property, Transportation, Building and Construction, and Healthcare. Global enterprises benefit from Rapid's AI-powered Computer Vision, which enhances safety by reducing risk, improving response times and preventing workplace accidents. By leveraging cutting-edge technology, automation, and real-time insights, Rapid empowers organisations to build a proactive safety management culture – ensuring safer, smarter, and more resilient workplaces worldwide.
Come and visit us on Stand: 3/D30.
Contact: Raymond Moussa T +31627975505
T +44 (0)1233 800557
rmoussa@rapidglobal.com https://rapidglobal.com/en-gb
‘Experts
Discover the new Dock Gate range and other innovative safety products at The Health & Safety Event 2025, Hall 3 Stand J40. For more information on our solutions, feel free to contact us ahead of the event or visit our stand during the exhibition.
T +44 (0)1902 824280 info@boplan.co.uk www.boplan.com
Hyde Park Environmental is back at The Health & Safety Event at the NEC in Birmingham from the 8th-10th April 2025. You’ll find them at Stand: 3/K60 & 3/H62
The Health & Safety Event is the leading expo for safe workplace solutions and innovations across the country and the team from Hyde Park Environmental will be on hand to discuss its vast range of spill control and containment products, including their own HUG absorbent range.
Established over 14 years ago, the company has locations in Antrim and Stafford and prides itself on creating a brighter future through environmental safety for industry at large.
With over 3,500 lines, the spillage experts offer solutions across environmental/waste management, hazardous material storage and handling, manual/material handling, PPE, slip and trip prevention and a unique brand of in-house absorbents called HUG.
In addition to a growing and innovative product range, the expert team offer free site surveys and consultation, appointed account managers for tailored service, on-site stock replenishment and same day dispatch for a quick turnaround.
To view the full range, please see the website below: https://hydepark-environmental. com
JSP will be showing the latest innovative, UKmanufactured safety products at The Health & Safety Event, 2025. Specialising in ‘above the neck’ PPE, JSP offer fully compatible sustainable safety solutions for today’s workplace.
JSP is the chosen brand for workers, offering tested, trusted, traceable PPE with full technical backup and support. Consistent testing and inspection ensure every product meets strict standards of quality. All JSP manufacturing sites run BSI-approved test laboratories, verifying performance for every batch. The BSI Kitemark™ licenses covering JSP PPE ranges are testament to this commitment to quality and continuous product testing.
New innovations on display include the popular new EVO® ALTA™ range of mountaineering-style
helmet offering all-round impact protection and the EVO®VISTA® range of next-generation safety helmets incorporating integrated retractable eye protection with up to A-rated impact resistance. Fully compatible EVOGuard® visors will also be on show, maximising compatibility and protection with a comprehensive selection for use with helmets and browguards.
Come and witness firsthand the great fit test performance of the Force®8 half mask and Force®10 Typhoon™ full face mask with award-winning PressToCheck filters and experience a face-fit test by one of the JSP fit2fit accredited team. Or try out the leading 4-in-1 Powered Air Purifying Respirator system – the JSP PowerCap® Infinity® where a fit test is not required.
Compatibility is key to protection – by choosing
OnStand: 3/E52 – ProtectHear, the leading provider of personal hearing protection, is marking its anniversary by unveiling their new, cutting-edge bone-conduction technology, seamlessly compatible with their market-leading earplugs.
With HSE’s CUFF highlighting the dangers of improper hearing protection, ProtectHear’s revolutionary earplugs have you covered.
ProtectHear solutions comply with CUFF in terms of hearing protection that is in ‘good condition’ as they last 5 years and are the most comfortable available, being uniquely moulded for every wearer. This means they are more likely to be worn and with a range of filters, ProtectHear can specify a protection level to suit your needs.
ProtectHear plugs can provide significant cost savings, over their 5 year lifespan of over £6K per 10 employees and are the more sustainable option, preventing a staggering 36,000 disposables from hitting landfill!
ProtectHear are so confident in their products they offer a no obligation 4 week free trial of their earplugs. Your workforce will get the correct level of protection and if required, communications options suited to your requirements.
Visit ProtectHear and discover how they are shaping the future of the noisy workplace with superior hearing protection solutions.
www.protecthear.co.uk
Grubs introduce its range of handcrafted Iberian leather boots featuring distinctive details for that luxury touch. Equipped with Grubs® legendary comfort technologies – makes them not only practical but also very stylish.
The boots are crafted using threepiece water-resistant full grain Iberian Leather on the upper and double-sided elasticated Gore on the side making them the ultimate work boot designed for everyday use.
The TEMPEST™ is an Australian style work boot made from tough oil stuffed Buffalo leather, with heavy duty twin elasticated side panels to allow easy pull on, kick off use. This rugged styled plain toed design makes it water resistant and gives a great relaxed workwear look – which looks as good with casual wear as it does with workwear.
Lined in new SUPERDRI™ mesh lining which wicks moisture away from the foot for all day comfort. Under foot the boot has a super-slip resistant COMMAND nitrile rubber outsole, resistant to oil, fertilisers and chemicals. The directly attached PU midsole adds all day comfort and durability to this classic, timeless style.
Grubs took the TEMPEST and added a hardwearing TPU scuffcap, backed up with a 200joule impact resistant CERAMIC safety toe, and added its DEFENDER™ anti-penetration nail proof insole and developed – the TORNADO – the Toughest most Rugged Leather Work Boot on the market today. All available in women’s UK 4 up to a men’s size 13. RRP £99.95.
Come see us on Stand: 3/G90. See the whole range at: www.grubsboot.com
JSP you can be rest assured that the Head, Eye, Face, Hearing and Respiratory products are certified compatible and designed to perform at the correct level when worn together.
Come and meet the team on Stand: 3/P40 at The Health & Safety Event, 2025, 8-10th April or visit: www.jspsafety.com
Multi-award-winning
CheckedSafe provides an end-to-end digital cloud solutions package to fleet management tailored to any industry.
Its brand-new app, GB Domestic Hours, features marketfirst technology and is designed solely for UK vehicle fleets. With a portfolio that already includes highly acclaimed compliance tools like Driver Licence Checks and Fleet Management Software, GB Domestic Hours enhances the lineup even further. This innovative solution empowers fleet managers to efficiently oversee fleets of any size fully digitally – eliminating the need for cumbersome paperwork.
What’s more, there's no need to store bulky boxes of reports, as everything is accessible in real-time. This allows for quick resolution of defects and issues, minimising downtime and lowering long-term costs through more efficient repair planning.
CheckedSafe has completely digitised the vehicle defect card by allowing drivers to carry out and report on their vehicle checks directly from their smartphone. It’s incredibly simple to use and features GPS tags, customised checks that enable users to create their own compliance checklist to suit their business needs, and what’s even better is that it can be accessed and used offline as all reports are automatically stored until the device has signal.
Visit CheckedSafe at the Health & Safety Event 2025 on Stand: 3/S52
T 01282 908429 info@checkedsafe.com www.checkedsafe.com
For nearly 30 years, Cardinus has been a leader in risk management, helping organisations create safer, healthier and more productive workplaces.
We provide end to end risk management solutions, combining software, eLearning, training, consultancy and physical interventions.
Our expertise also covers property risk, fleet safety, personal security, insurance risk, and health and safety consultancy.
Injury Prevention for Non-Office Workers
At this year’s Health & Safety Event, we’re showcasing FlashAI, the latest in injury prevention for
trusted by over 5 million people worldwide. Healthy Working is the ideal solution for home, office and hybrid working, which can reduce musculoskeletal risks by up to 80% in just two weeks.
To ensure the right fit, we offer a trial for up to 5% of your workforce, allowing you to gather initial risk data before full implementation.
Developed with 3motionAI, FlashAI is an AI-driven motion capture app that enhances workplace safety, reduces injuries and optimises human performance.
Designed for industrial and manual handling environments, it evaluates posture, pushing/pulling and repetitive activities. The real-time scoring system identifies risks, enabling targeted training and modifications.
Key features of FlashAI include:
t Posture evaluation and MSD risk identification t Skeletal hot zones for high-risk movement patterns t Instant ART, MAC, and RAPP assessments & reports t Task-specific risk scores with actionable
Just 1 Source & Supply will be exhibiting its diverse range of hand protection solutions at The Health & Safety Event at the NEC in Birmingham from the 8th10th April 2025. You’ll find us at Hall 3, Stand O12
Since our establishment in 2008, we have been servicing our Distribution Network with our ever-growing range of hand protection, which all started with the Predator by Ron Signature Collection. As an industry leader on welding gloves, we have used this presence and brand to develop a unique offering in a convoluted marketplace.
We don’t simply offer gloves and disappear; we are a long-standing partner with both Distributors and End
Users alike. Our range allows us to offer market leading advice on products in application at your site and then provide allencompassing support with a distributor who can match your requirements.
Our portfolio of Mercator Nitrile Products is a core part of our business and with various lengths, thicknesses and colours, we are confident we have the solution to align with your disposable needs. With wastewater treatment, solar panels and biofuel powering the manufacturing site, we know we are a leader in responsible sourcing for disposable products, something we are all passionate about at Just 1 Source.
As we continue to grow and learn as a business and supply partner, we have increased our focus on sustainability. We are on a journey to reduce single use plastic in our packaging, with over 50% now containing no plastic and all new products being sourced with alternative packaging materials, this will only improve. Our new Planetsafe range also includes products manufactured with rPET and Bamboo, providing various cut options and coatings. We would love the opportunity for you to get hands on with this range at our stand, or by reaching out to us through our website at: www.just1source.com
recommendations t AI-driven insights to enhance training and ergonomics
With real-time AI analytics, businesses can cut costs and save time on traditional risk assessments while improving accuracy and efficiency.
FlashAI seamlessly integrates with RiskAI, a centralised dashboard providing insights by task, employee and location, helping organisations make data-driven safety decisions.
For a limited time, you can access FlashAI for free to capture an initial risk profile at no cost. This allows you to experience its capabilities first-hand and understand how it can transform their approach to injury prevention.
Visit Stand: 3/T111 at the Health & Safety Event (8-10 April) to see how FlashAI can streamline risk assessments, improve worker safety, and boost productivity.
Can’t wait? Start using the app today by visiting our website.
T 0207 469 0200 info@cardinus.com www.cardinus.com
As part of our desire to be a market leader, we have now launched a range of products in Vend Ready Packaging, reducing the amount of time your team spend manually handling product and reducing your direct costs. This has been exceptionally well received within the market, and we are happy to provide samples of product to ensure they conform with your specific machines. With plans to grow this area, you can be confident that we will have a solution that works for you.
For more information, contact us on 01653 617718 or email: sales@just1source.com
Competency Cloud was created by the experienced team at Chipmunk Data, who witnessed firsthand the daily challenges construction and utility companies faced with workforce compliance. Spreadsheets, paper trails, and disconnected systems were causing headaches for businesses trying to manage their workforce certifications and training records.
Implementing robust health and safety protocols requires a proactive approach that encompasses thorough risk assessments, regular safety training, and meticulous record-keeping.
With Competency Cloud businesses can streamline the process of managing employee skills, certifications, and training requirements.
Our platform enables organisations to conduct comprehensive skill gap analyses, ensuring that their workforce possesses the necessary competencies to perform their duties safely and effectively.
Moreover, Competency Cloud's innovative Card Checkers feature simplifies the arduous task of verifying employee credentials, cross-referencing against multiple industry card
bodies to validate the accuracy of information and guarantee alignment with industry standards. This not only promotes efficiency but also allows companies to redirect valuable resources towards continuous growth and development.
We empower construction professionals with realtime access to employee profiles, competencies, and documentation through the Competency Cloud Mobile App.
Site Managers and H&S Professionals can effortlessly stay connected to their workforce, irrespective of location or time, while employees can complete assigned online training, eLearning, RAMS, Video Presentations, and Competency Assessment Questionnaires directly from their mobile devices.
Competency Cloud has revolutionised the way utilities
companies approach compliance, training, and workforce management.
Tailored specifically to address the unique challenges faced by the utilities sector, Competency Cloud offers a comprehensive solution that streamlines and simplifies the creation, management, and tracking of Utilities Authorisation Certificates.
By consolidating these processes into a unified platform, Competency Cloud empowers utilities companies to efficiently produce customised certificates, ensuring that their workforce meets and exceeds industry standards.
Come visit us on Stand: 3/P150 to explore further with our team.
Schedule a Demo: Transform Your Utility Compliance Management
Book a personalised demonstration to see how Competency Cloud can:
t Streamline your compliance processes
t Reduce administrative burden
t Enhance site safety
t Protect your business
www.competencycloud.co.uk
Withthe SMS-R1 – you can now produce technical labels in-house in all sizes and shapes –because equipment has curves and recesses – in highly durable materials and in any quantity you need – in minutes. For manufacturing, health and safety even part of product labelling can now be produced on-
demand, fully customised in shape, quantity and in colour.
Complete with all the necessary technical and safety pictograms, the SMS-R1 can ensure all your equipment meets current Health and Safety norms and has clear and concise operating information, maintenance information and service information.
Anything from a small component label up to highly visible labels with 95mm high text is possible from just one system.
Our large range of materials include high strength adhesives, high visibility, temperature resistant, chemical resistant & metalized polyesters – ideal for serial plates.
Keeping equipment clearly labelled avoids damage, accidents and reduces maintenance.
Seeing is believing. Rebo have distribution in the UK and in Europe.
Contact T +31 (0)35 601 6941 info@rebosystems.com www.rebosystems.com
Series SLC440COM/ SLG440COM: more flexible in use thanks to higher ranges and the enhanced functions of the SLC Assist app
Schmersal is set to launch new versions of its SLC440COM-H/ SLG440COM-H series safety light curtains and grids. With ranges of up to 30 metres (SLC440COM) and 60 metres (SLG440COM), they offer reliable hand and body protection and enable monitoring over greater distances with only minimal installation effort.
In addition, the safety light curtains and grids have a Bluetooth LE interface, which, with the ‘SLC Assist’ app developed by Schmersal, displays status notifications from devices and provides comprehensive diagnostic data. The new version of the ‘SLC Assist’ app now offers even greater functionality – as an example, the app can now also be used to calculate the required safety clearance to the danger area.
SLC440COM/SLG440COM series safety light curtains and grids secure danger areas and areas in applications such as presses, robot cells and palletising systems. Due to their increased ranges, the new versions of the SLC440COM/SLG440COM
can now also be used to reliably protect very large production systems, conveyors or the platforms of autonomous underground railways. With the help of deflecting mirrors, entire areas can also be secured and monitored with just one safety light curtain or grid. This solution reduces both the installation effort and the acquisition costs.
The Bluetooth interface and the app enable all status and diagnostic data regarding the operating
LogiDataTech supplies innovative gas measurement systems for directly determining gas concentration in a gas mixture. The explosion-proof MF420Ex-2.1 range measures the concentration of toxic or combustible gases and vapours in an explosive air mixture at an ambient temperature range of 0-50°C. They operate by utilising either a pellistor or a specific electrochemical sensor.
Calibration is a simple procedure and is carried out on-site using an alphanumeric display with the use of buttons, so the device does not need to be opened. The aluminium housing is suitable for wall mounting. The measured values are outputted via a linear current output (4-20mA) and the evaluation and further processing of the measured values are transmitted to
a device connected downstream by the user. The instruments comply with the current European ATEX standard and are approved for operation in zones 1 and 2.
LogiDataTech GmbH T +49 7221 97062-0 sales@LogiData.Tech www.LogiDataTech.com
status of the light grid/curtain to be called up on a smartphone or tablet in real time. The Schmersal app also offers extensive support for statutory testing and documentation, such as through an integrated operating hours counter and the capture of the switching frequency of the outputs.
The new version of the app now also includes a function for determining the safety clearance to the danger area in accordance with EN ISO 13855. Thanks to the intuitive user interface, all essential data can be easily captured and the calculated results retrieved. The app also suggests specific products from the Schmersal range: A single click takes the directly to the corresponding product in the Schmersal online catalogue.
The ‘SLC Assist’ app from Schmersal is available for Android and iOS devices.
Contact Steve Watkins, Marketing Manager, T 01684 571987 swatkins@schmersal.com www.schmersal.co.uk
Frankfurt Laser Company is proud to announce the launch of the 08BULT Diode Laser Components, a cutting-edge solution designed for diverse applications such as medical technologies and material processing. This innovative product offers unparalleled performance, precision, and reliability, making it an essential tool for professionals in advanced industries.
The 08BULT diode laser series features RealLight’s AW series multifunction laser modules with a fibredetachable configuration and single-emitter design. This compact module is equipped with an aiming beam, fibre detector, photodiode, and thermistor, ensuring ease of maintenance and consistent power stability.
Key Features:
Technical Highlights:
t Available wavelengths: 808nm and 980nm
t CW Output Power: 2W (808nm) and 3W (980nm)
t Fibre core diameter: 200μm with SMA905 connector
t Numerical aperture: 0.22
t Integrated thermistor for enhanced thermal control
The 08BULT diode laser is engineered to perform in diverse conditions, with an operating temperature range from 10°C to 30°C and robust tolerance for humidity. It boasts industry-leading spectral width and wavelength stability, ensuring precision in even the most sensitive applications.
Applications:
t Medical technologies, including advanced diagnostic tools
t Compact size for versatile integration
t Superior power stability for consistent performance
t Exceptional beam quality with various wavelengths available
t High reliability in demanding operational environments
t Easy-to-maintain design with fibredetachable configuration
t Material processing, delivering precision and efficiency for cutting, welding, and engraving tasks of/on plastic material
The latest diode laser components are available for order now. For more information or to request a consultation, please contact our sales team via the contact form at: www.frlaserco.com or contact our sales team via mail at: sales@frlaserco.com
The AccurioLabel 230 digital toner press from Konica Minolta is available in the UK, through Focus Label Machinery – an Accredited Industrial Print Partner of Konica Minolta. This cutting-edge technology also perfectly complements the Focus Reflex range of digital print finishing systems.
For digitally printed web, the Reflex 330 Digital Finishing System provides a fully comprehensive off-line finishing solution. The Reflex 330 re-register system is extremely accurate – even at speeds well over 100 metres per minute and includes the option for semi-rotary or full rotary converting for roll-to-roll or roll-to-sheet formats.
The versatile d-Flex digital hybrid press incorporates the latest HiQ 1,800dpi highspeed, full-colour Konica Minolta inkjet technology (CMYK + W), which has been cleverly integrated into the existing Reflex servo press with in-line UV or LED flexo print heads, die-cutting, slitting and rewinding. High quality variable images can be overprinted in perfect register with UV or LED flexo ink, then converted & rewound – in a single pass with speeds up to 60 metres per minute.
servo-driven flexo/digital combination press in the marketplace today.
The latest e-Flex twin servo flexo press with automated pre-register functions can be specified with multiple drying options, including UV, LED, infra-red and chill rollers. The dual servo system provides single touch set ups, with minimal waste for conventional printing and can be combined with a digital module for variable data, text & images.
The touchscreen HMI operator controls provide a fully programmable digital platform, plus storage of job details for future retrieval and are said to make the e-Flex, the most effective, affordable
The e-Flex incorporates top-loading print cylinders and quick-change print cartridges to reduce downtime and set-up wastage. A choice of ultraefficient interstation drying systems enables much higher press speeds. The short web-path allows for a compact design, while still maintaining good accessibility for the operator and plenty of space for optional equipment. A rail system is available for overhead press options, including delam/relam, rotary cold foil transfer, silk screen, turn-bar, and multi-layer re-register laminating.
T +44 (0)1949 836223 admin@focuslabel.com www.focuslabel.com
Tomorrow’s Warehouse, held at Coventry’s CBS Arena on 15 May 2025, is the go-to conference/ exhibition hybrid for logistics professionals to get to grips with modern warehousing.
Without the cost, hassle and planning required for a major exhibition, the show gives sponsors & exhibitors access to warehouse professionals in a relaxed atmosphere against the backdrop of a stimulating conference programme.
The programme shines a spotlight on unprecedented transformation in the warehouse, tracking trends and offering insights. This one-day,
free-to-attend conference also highlights a range of solutions that boost warehouse performance and flexibility.
We are determined that attendees will go back to their workplace with ideas, approaches, products, solutions and partners, all in mind, to action real improvements to their operations.
Attend Tomorrow’s Warehouse to gain practical, actionable insights that will help you make sure operations are a match for changing commercial realities.
Exhibit to access operations professionals who are seeking insights and solutions to boost their logistics processes in times of rapid and deep transformation.
Don’t miss this free-to attend conference tackling operational challenges in warehousing and logistics at a time of unprecedented transformation.
Contact https://tomorrowswarehouse.live
Third-party logistics (3PL) provider
Kammac has been awarded both the Authorised Economic Operator (AEO) and the Fulfilment House Due Diligence Scheme (FHDDS) certifications, underscoring the company’s commitment to secure, efficient, and compliant supply chain services.
The AEO certification, endorsed by the World Customs Organisation (WCO), aims to improve international supply chain security and trade efficiency. Recognised in over 70 countries, certification holders work together to reduce customs restrictions and enhance cross-border trade operations.
As an AEO certified company, Kammac now benefits from prioritised customs procedures, enabling faster and more efficient import and export processes, including filings, inspections, and clearances.
“Achieving AEO status following HM Revenue and Custom’s (HMRC) rigorous six month approval process marks a significant milestone for us,” said Leanne Lidell, Director of Compliance at Kammac.
“The certification ensures simplified customs clearances and priority handling, meaning we can offer our customers more streamlined and reliable logistics services.”
In response to the needs of a longstanding global beverage client, Kammac initially attained AEO certification for its Wavertree site. Since then, all 15 Kammac sites have been included, further enhancing collaboration with global customers who require AEO status.
Kammac joins its sister companies within the Elanders Group in 2023 who also are AEO certified, providing a powerful network to existing and new clients.
“With our global footprint, our AEO certification facilitates seamless collaboration with fellow members, strengthening the service we can offer to clients,” said Leanne. “This certification bolsters logistics, particularly vital for UK-bound goods amidst the post-Brexit landscape.”
www.kammac.com
Losyco, expert for intra-logistics on rails, introduces patented AllRounder wheelsets, an easy-to-install solution for taking heavy loads around corners on the floor-level LOXrail system. Two rollers mounted at an angle can be rotated in opposite directions in order to realise effortless 90° turns at junction points. This enables rail layouts with linking and crisscrossing lines without the need for additional, highmaintenance shunting equipment.
The time-saving and cost-efficient solution reduces the installation effort, even in halls with complex floor plans. Barriers like supporting pillars are simply avoided. The wheelset design ensures minimal friction due to the very small contact area between the rollers and the guide rail. Thereby, even loads weighing several tons can be easily moved across the rails and
around corners by hand.
The new solution is also useful for re-routing transport platforms back to the start of the line. Fitted with four wheelsets, the new AllRounder transport platforms for flexible manoeuvring carry payloads up to 10 tons on the LOXrail 25 system. LOSYCO will adapt them to customer requirements in terms of dimensions and track widths.
Contact: Tim Schneider T +49 521 945 643-0 info@losyco.com www.losyco.com
INFORM and AUTO1 Group have intensified their co-operation, with yard optimisation software now implemented in all production centres.
AUTO1 Group is a digital automotive platform for buying and selling used cars and following a pilot of INFORM’s vehicle Yard Management System (YMS) in 2022, the companies expanded the solution to a total of ten locations throughout Europe by the end of 2023.
The system supports AUTO1 Group by providing end-to-end transparency and more efficient processes in the parking areas of the production centres. In addition, in 2023 AUTO1 Group and INFORM turned their focus from the optimisation of parking areas to the optimisation of work flows within the production centres.
AUTO1 Group vice president logistics & production, Karol Niznik, says, “The YMS has helped to improve our processes, giving us transparency of all vehicles at our sites at all times. It is therefore only logical
to take the next step with INFORM. We expect similar improvements in the production centres by using the Workshop Optimisation System.”
The process of refurbishing used cars is particularly challenging as a high variety of different makes and models from different build years goes through the process. INFORM’s Workshop Optimisation Software is designed to help with that.
“The goal of the software is to automatically adjust the optimised schedule if any changes need to be made in the refurbishment process,” adds Hartmut Haubrich, director of vehicle logistics at INFORM.
For more information, visit: www.inform-software.com or call +49-2408-9456-0.
The Process & Chemical Engineering Show, running as part of the CHEMUK 2025 ‘Group of Events’, will return this 21st & 22nd May at the NEC in Birmingham, presenting hundreds of exhibitors and a full programme of expert speaker sessions over two packed days.
The Process & Chemical Engineering Show will showcase the latest technology and specialist services to attending process, plant, and control engineering professionals across the chemical, food & beverage, pharma, oil & gas, water & waste, and energy sectors.
Record numbers of NEW exhibitors confirmed 2025 will welcome over 60 brand new exhibitors for visitors to meet with including: 6ix Process Design, Abacus Valves, ABLE Instruments & Controls, Addison, ALBIN PUMP/LMI/Milton Roy Mixing, Ambic Equipment, Andritz, APIS MC, APMG Plastics, ARTECH ULTRASONIC SYSTEMS, AVA-Alms Valve Agency, AZO, Barriquand Heat Exchangers, Beckhoff Automation, Buckley Industrial, C&P Engineering, Chemviron Carbon, Co-ax Valves, Cognite AS, Dabico Airport Solutions, dataPARC, DESAL Supplies, DINNISSEN Process Technology, Elta Group, EPC Handelges, EUROTEC, Framatome, Friedheim International, G Bopp & Co, GMM Pfaudler, Hecht Technologies, Humberside Engineering Training Association, HYDAC, Hydrodif Products, Innomotics, Intertec-HESS, J1 Technologies, John Mayes Engineers, Johnson Valves, Kecol Pumping Systems, Knitwire, KROHNE, Meller, Merinox, OLG, Portobello Engineering, PR Electronics, R&G Fluid Power, Sampling Systems, Sandfield Penstok Solutions, Sigma-HSE, Simmatic Automation, SM Gauge Company, Spiroflow, Step on Safety, Stepart Plastics, Sulzer Pumps Wastewater,
Tantaline, Transworld Steel Enterprise, UK Extrusion, Visilume, VOOVIO Technologies, WEC (Leeds), Watlow, Ytron-Quadro Limited, and Zwick.
IChemE and IMechE to headline engineering speaker programme
The Process & Chemical Engineering Show speaker programme is an unmissable opportunity to hear from the heads of industry and academia as they discuss the challenges, opportunities, and innovation affecting the process engineering industries.
The IChemE and IMechE will be presenting a series of expert panel discussions, keynotes, and technical clinics at the show. Their respective membership teams will also be exhibiting, ready to meet with current and potential members and companies to see how they can support their personal and business development.
The full speaker programme will be released in March 2025. Please see the website for full details.
‘The Big Education Debate’ at CHEMUK
This feature session, running on Thursday 22nd May, will invite senior panel leaders from across academia and industry to discuss the UK’s educational framework and commitment to supporting its science skills and science base requirements. This critical debate comes in response to the recent pressures facing higher education chemistry departments across the UK.
Innovation Ecosystem at CHEMUK 2025
CHEMUK 2025 will present several of the UK’s primary innovation support organisations, giving startups and spinouts the opportunity to receive the support they need to continue their development journey towards full-scale commercialisation.
Participating partners include the Henry Royce Institute, Innovate UK Business Connect, CPI, Aston University, RSC Changemakers, Materials Innovation Factory, and the Biorenewables Development Centre.
Waste2Race: The sewage-powered car on track to make history Visitors this year will be able to see the hydrogen-
The engineering team behind the project from the University of Warwick will be at the show to meet with visitors and explain the technology creating green hydrogen from wastewater, powering the groundbreaking vehicle.
UK Government at CHEMUK Attendees will be invited to a full UK Government programme at CHEMUK. HSE and DEFRA will be providing industry briefings on Wednesday 21st May.
The UK Export Academy team will be exhibiting at the show, ready to meet with visitors that are looking to develop international trade opportunities. The academy team will also be running a one-hour panel session on Thursday 22nd May, outlining the international trade landscape.
Dates for the diary
The Process & Chemical Engineering Show at CHEMUK 2025 takes place on Wed 21st & Thu 22nd May 2025
Venue: NEC – National Exhibition Centre, Birmingham B40 1NT
Opening Times: Day 1: 9.30am – 5.00pm Day 2: 9.30am – 4.00pm
Register for your FREE entry badge at: www.chemicalukexpo.com
KSB, a global leader in engineering, employs over 16,000 dedicated professionals in development, production, sales, and service. Their shared passion for engineering excellence drives continuous innovation, rooted in robust research and development. The reliability of KSB’s pumps and valves is not only a testament to their exceptional dependability but also to the support of 190 service centres and over 3,500 maintenance staff worldwide. Operating under the KSB SupremeServ brand, these experts elevate service standards to new heights.
In the chemical industry, KSB stands out with solutions designed to handle high temperatures, aggressive, and flammable fluids, ensuring safety and reliability in the most demanding conditions. The product range includes seal-less pumps, high-pressure pumps, and various valves such as shut-off, control, & safety valves.
KSB’s industrial valves are synonymous with efficiency, reliability, and durability, tailored to meet specific application needs and ensure optimal performance. This commitment to innovation and
comprehensive service has solidified KSB’s reputation as a trusted industry partner.
We are thrilled to announce KSB’s participation in CHEMUK. Visit us at Stand C44 to explore our latest products and innovations. We look forward to engaging with industry professionals and showcasing our cutting-edge solutions.
Come see us on Stand C44. sales@ksb.com www.ksb.co.uk
Recontainers Ltd specialises in the buying, selling and cleaning of empty hazardous and non-hazardous chemical containers. Based in Lancashire, and established in 1991, the family-run business is exhibiting at CHEMUK 2025, after a successful event last year.
Recontainers Ltd buy and sell reconditioned IBCs (intermediate bulk containers) in different specifications (grade, pallet base, bottle colour, and whether the container is UN-certified or non-UN certificated). They also offer a IBC reconditioning (wash and return) service. This is also true of secondhand drums such a l-rings, and steel drums.
Recontainers Ltd will return to Chem UK 2025 at the NEC Birmingham on Stand G120
Recontainers Ltd also has an online shop facility for trade or consumers (with bulk orders possible via request). Three of the best sellers include:
t Grade 1 Clear Reconditioned 1,000L IBC on Metal/Plastic Pallet (Non-UN)
t IBC Weatherproof Cover & UV protection 1,000L
t Grade 2 Clear Reconditioned 1,000L IBC on Metal/Plastic Pallet (Non-UN)
For more information, contact the team at Recontainers Ltd today: T 01706 211112 recontainersltd@aol.com www.recontainers.co.uk
BASA is the umbrella organisation for UK and Irish adhesives and sealants manufacturers and focuses on technical and legislative aspects and on promoting awareness of the industry and technology by providing guidance on technical and compliance issues to members via a library of documents on the website.
We are the voice of the adhesives and sealants industry and an information source for manufacturers and suppliers. We lobby on behalf of members and liaise with Government on legislation, keeping Members well informed of UK, EU and International proposals and initiatives.
With the growing concerns around the environment and using sustainable products and raw materials, BASA is dedicated to helping its members minimise harmful chemical usage and educate the public on the industry’s drive for safer products. BASA members work hard to formulate
innovative products that positively contribute to the sustainability agenda whilst maintaining performance and durability.
BASA will be available at CHEMUK and hopes to continue to reach more potential members, looking at ways to support its manufacturers post Brexit and help them to navigate potential new legislation and trade rules.
Come see us on Stand A140. Contact: Lorna Williams, Chief Executive Officer T +44 (0)330 223 3290 lorna@basa.uk.com www.basa.uk.com
Compression delivered H2 piston compressors in a phased order to Plug Power to support the construction of multiple new hydrogen liquefaction facilities
Making green hydrogen a readily available fuel relies on rapidly building production facilities. Companies like Plug Power are leading the way, creating an end-to-end green hydrogen ecosystem. In this environment, effectively delivering sufficient hydrogen relies on large reciprocating compressors, which is why Plug Power has partnered with Burckhardt Compression, a leading supplier of compression solutions for sustainable applications, to provide specialised equipment for new projects.
Green hydrogen is produced from water by splitting the hydrogen and oxygen molecules using electrolysis. This process is powered by renewable energy sources such as solar, wind or hydro, and when the resulting gas is utilised in a fuel cell system, the only emission is water. Consequently, green hydrogen promises to decarbonise industry, vehicles, and the way we produce fuel. There is a catch though – hydrogen is an incredibly light gas which makes it challenging to deliver it in required quantities to the consumer. Therefore, it must be compressed, or like in this case, even liquefied before transport to filling stations.
Big efficiency for large equipment Oliver Franz, Sales Manager H2 for Mobility &
Energy at Burckhardt Compression, explains the best approach, “To move large quantities of hydrogen efficiently, ring type compressors are a better choice than centrifugal. Our designs offer industry leading efficiency, which is an advantage especially in a renewable energy project where maximising production output versus power consumed is crucial.”
Considering this, Plug Power approached Burckhardt Compression to deliver a large quantity of H2 piston compressors in a phased order to support the construction of multiple new hydrogen liquefaction facilities. The first phase of compressors required the Burckhardt Compression team in the US to quickly grow its capacity.
“We have operated a facility in Waller, Texas, for eight years now, and assembling the piston compressors required for the project on-site meant we had to expand. Each compressor weighs more than 200,000 pounds (91 tons), which exceeded the capacity of our cranage. Beyond equipment upgrades, we also needed to bolster our team,” says Michael Ciambella, Compressor Engineering and Manufacturing Manager.
Increasing capacity and expertise
The expectations from Plug Power were high and Burckhardt Compression planned to exceed them. Ramping up assembly was dependent on the ability to move around a fully built compressor to enable assemblies to be executed in parallel. Burckhardt Compression invested in a hydraulic gantry crane system with a 1 million pound (450 ton) lifting capacity, which would allow the safe, slow movement of the compressors across the workshop. The company worked with experts to install and supervise all lifts during the project.
Burckhardt Compression was able to design a dry running piston compressor with a highly variable turndown arrangement to exactly meet customer needs
The investments paid dividends, as Michael confirms, “We were able to grow our assembly capacity at Waller
by 50%, which allowed us to effectively meet the first phase of compressors and any afterwards. The assembly turnaround time for each compressor was reduced from six weeks down to four, and sometimes we delivered even faster than that! We managed to complete the first phase three days ahead of schedule with zero safety incidents.”
Eleven new personnel joined the team too, including a consultant and a project lead with 20 years’ experience in compressor projects. As a global company, the US team also received training from a Burckhardt Compression expert from Switzerland, who joined the company for six weeks to ensure transfer of know-how for the assembly work. Components for the compressors would be manufactured in Switzerland and delivered to the team in the US.
Specifically designed for hydrogen Burckhardt Compression was able to design a dry running piston compressor with a highly variable turndown arrangement to exactly meet customer needs. This will allow operators to match the compressor’s performance to the process
requirements without any wasted energy.
Michael continues, “This is a dry design to ensure that no lubrication oil can contaminate the hydrogen and reduce fuel quality. With large diameter pistons for the first stage, there is a lot of heat from frictional forces, so the rider band must be able to withstand this and provide a long service life. We use proprietary polymer materials we have developed in-house. This enables over a year of operation before maintenance is required, which is unsurpassed in terms of uptime.”
The minimal weight pistons were designed with energy saving in mind, while still ensuring enough strength to compress the hydrogen. Compressor chambers are fitted with a fixed pocket, which can expand to increase internal space. Specially developed pressure packing further contributes to an extended service life. Ultimately, the design philosophy is to find the sweet spot in terms of gas temperature and required production output for the customer.
A monitoring solution from Burckhardt
Compression’s digital experts PROGNOST Systems is also included. A suite of sensors constantly delivers data regarding the performance of suction and discharge valves, bearing temperatures and rod drop. Consequently, operators can monitor equipment condition and predict any preventative maintenance measures steps needed, improving uptime.
As of Q1 2024, Burckhardt Compression has successfully delivered the first order and has more projects underway. Following the expansion of its team and facilities, this partnership has let Burckhardt Compression lead the way in hydrogen production.
A significant factor in the success of this partnership has been the readiness of Burckhardt Compression’s service and its flexibility to operate both within and outside the country, thanks to the extensive setup in the US. This ability instilled confidence in Plug Power to opt for the ‘new’ technical solution. Burckhardt Compression’s ability to provide reliable and efficient services, coupled with the commitment to customer satisfaction, has played a crucial role in the
successful implementation of these projects.
Michael adds, “We have 175 years of knowledge in compressors and over 50 years’ experience in hydrogen, so we can bring great expertise to a relatively young market. Our products support the entire hydrogen value chain, from production operations all the way to the forecourt. Burckhardt Compression even supports third-party compressors with modernisation solutions, tailored services and high-speed replicated parts. We are certain that the quality of our work speaks for itself, and that we can continue to support landmark renewable projects such as this.”
“Although the energy transition brings forth exciting opportunities, the challenges that it presents can be daunting to our customers. With a customer intimacy culture within Burckhardt Compression (US), Inc. we are committed to delivering the best business solutions for our partners such as Plug Power. Our successful completion of the first phase of units is an excellent testimony to Burckhardt Compression’s customer collaboration, product leadership, technical expertise and project capacity. We are super excited about our proven products and services supporting a sustainable energy future,” concludes Annie Savarimuthu, VP Systems Division, Burckhardt Compression (US) Inc.
Burckhardt Compression has released an exclusive timelapse video of the compressor lifting process at its facility, which can be viewed here: https://youtu.be/2JORdJLask8
info@burckhardtcompression.com www.burckhardtcompression.com www.plugpower.com
One of the technical highlights at ACHEMA 2024 was KSB Group’s new 3D-printed containment shroud for mag-drive pumps of the Magnochem type series. Named MagnoProtect, the component offers the same safety as a doublewalled containment shroud – without the latter’s disadvantages of heating up strongly and having high eddy current losses.
AtWhile providing comparable safety, the overall efficiencies of the new mag-drive designs clearly exceed those of canned motor pumps. Designed with a structure of channels, the new containment shroud offers a second, redundant, static safety barrier preventing leakage of the fluid handled.
A pressure transmitter monitors the vacuum generated, which is present during normal operation in the channels of the containment shroud. If the monitored pressure rises to atmospheric pressure, the outer containment shell is leaking. If the pressure rises above the ambient pressure, the
inner containment shell is damaged. The containment shroud design is characterised by high mechanical strength and good wear properties. It has been optimised to minimise heat losses and eddy currents.
Converting a standardised chemical pump with mechanical seal to a magnetic drive is easier and more cost-efficient than retrofitting it with a canned motor. The geometry and dimensions of the new containment shroud are integrated in the modular system of Magnochem, allowing metallic or ceramic containment shrouds to be replaced easily. This enables operators to upgrade older pump sets that are still in service without difficulty.
www.ksb.com/en-gb
Oliver Valvetek, innovation drives our commitment to advancing critical technologies. Over the past few years, we’ve increasingly focused our research and development efforts on creating solutions for Carbon Capture, Utilisation, and Storage (CCUS), a key component in the global drive toward reducing carbon emissions.
We are excited to share that we have developed two 3/8” subsea rotary gate valves, part of a group of prototypes heading to a customer for a pioneering carbon sequestration project in a subsea environment. This milestone showcases our dedication to pushing the boundaries of valve technology through advanced R&D.
Our subsea rotary gate valve is
specifically engineered for the demanding conditions of carbon sequestration projects. Its compact size ensures easy placement in constrained spaces, while its costeffectiveness makes it ideal for scalable solutions in large-scale CCUS applications. Additionally, it features the same proven metal-on-metal seal technology as our standard gate valves, delivering top performance even in the harshest subsea environments.
This advancement reflects Oliver Valvetek’s ongoing commitment to developing cutting-edge solutions that contribute to a more sustainable future.
For more information on Subsea valves, contact Oliver Valvetek on: +44 (0)1565 632636, email: sales@ valves.co.uk or visit: www.valves.co.uk
There is a common misconception that all breather valves are rigorously tested to a certain standard before they are sold, but unfortunately, this is definitely not the case. Many breather valves on the market are not subject to stringent testing protocols, leading to significant safety and operational risks. When these untested and, more importantly, unsafe breather valves are procured, the end user unknowingly takes on many risks.
It is crucial to know the facts by conducting thorough due diligence from the initial purchase and throughout the entire lifecycle of the unit. First, ask yourself: Are your breather valves set correctly?
Incorrect settings can lead to valve malfunction, causing potential overpressure or vacuum conditions that could compromise tank integrity. Are your breather valves performing safely? Regular testing ensures they function within safety parameters, preventing hazardous situations.
Do you know your breather valve leak rates, and is your media hazardous, flammable, costly or toxic? Understanding leak rates is vital for environmental, occupational health and safety compliance. Do they function as per intended design and specification, and do they meet the set point? This ensures that valves operate as required under specific conditions.
Has your breather valve been tested in accordance with API2000 Section 5.4? Compliance with this standard guarantees that valves meet industry requirements. Do you monitor your breather valves as part of your aging plant management plan? Regular monitoring can identify wear and tear before it leads to failures. Lastly, are you confident that all your breather valves maintain optimum efficiency and performance? Ensuring this can prevent costly downtime and environmental hazards.
The only irrefutable test method is using the Vent-Less test bench. This groundbreaking technology is revolutionising testing, ensuring that breather valves are tested prior to installation and during
Hansford Sensors is a leading global manufacturer of industrial vibration monitoring equipment. We design, develop and manufacture a range of high-performance industrial accelerometers, vibration sensors, 4-20mA transmitters, cable assemblies, industrial enclosures and ancillary equipment. These products can be used in a wide range of industries including petrochemical, metal, paper & recycling.
Visit hansfordsensors.com, contact 0845 680 1957 or email sales@hansfordsensors.com
the life term of the unit. The award-winning Vent-Less test bench aligns with the API2000 Section 5.4 test protocol, and the instantly generated certification stands up to regulatory scrutiny. The documented leak rate is also invaluable for LDAR, IED, and Regulation 61 reporting. These questions are critical for assessing your vulnerabilities and ensuring the safety and efficiency of your operations. Don’t leave it to chance – make sure your breather valves are thoroughly tested and maintained using the Vent-Less test bench.
Contact T +44 (0)1726 844707
info@assentech.co.uk www.assentech.co.uk
Maintec is the longest standing exhibition for the predictive maintenance, reliability and asset management industry, and Chris Hansford, Managing Director of Hansford Sensors Ltd, has been attending the show for almost 40 years.
As a globally recognised leader in industrial vibration monitoring, Hansford Sensors designs & manufactures a broad range of high-performance equipment. Its offerings include accelerometers, vibration sensors, 4-20mA transmitters, cable assemblies, and industrial enclosures. At Maintec 2024, Hansford Sensors highlighted key products like its Accelerometer Power Supply Modules and Vibration Sensors, showcasing its commitment to delivering reliable solutions for industrial applications.
As well as Vibration Systems and Switches, Hansford Sensors also offer a range of accessories for vibration monitoring that include DIN rail mounted monitoring and protection modules, vibration switches and charge amplifiers.
Vibration monitoring products are crucial in industry because they help detect early signs of machinery malfunction, such as misalignment, imbalance, or bearing failures. Hansford Sensors systems are ideal to support various outputs like AC acceleration and velocity, ensuring versatility in usage. Its products are designed for robustness with IP ratings suitable for harsh environments, making them ideal for industries such as manufacturing, power, and mining.
What’s more, Hansford Sensors also provide an online calculator designed to simplify your vibration analysis. From an input of acceleration, velocity or displacement the Vibration Calculator converts the amplitude and frequency into a range of engineering units to optimise analytical performance.
For more information on all products, or to use the calculator, please see below: T 0845 680 1957 sales@hansfordsensors.com https://hansfordsensors.com
Set to open in October 2024, this location will be the new headquarters for Kärcher Hire
t The Chadderton site will also be the cleaning providers first Kärcher Owned Kärcher Operated centre in the North West and its largest regional centre in the UK, offering a range of best-in-class services for businesses in the region t The new site continues an exciting period of growth for the cleaning solutions provider
Kärcher UK, a leading provider of cleaning solutions, is thrilled to unveil it has selected Manchester for its newest and largest Kärcher centre, which will open in October 2024. Building on the established Manchesterbased Kärcher Hire business, the 18,122 square foot, two-acre site, will house a new Kärcher centre, as well as Kärcher Hire’s new headquarters.
Kärcher Hire rents an extensive range of the latest Kärcher equipment and has grown to become one of the largest cleaning equipment hire companies in the UK. Building on its reputation for providing customers with best in class, fast and reliable service throughout the UK, they have outgrown their current base in Droylsden, Manchester. Kärcher Hire is set to supercharge its operations, continuing to expand their client base across the UK.
The Kärcher centre will be run by centre Manager, Simon Barlow, and will include a superb showroom that businesses and consumers alike are welcome to visit to discuss their cleaning headaches. A major focus
will be servicing professional businesses needs across the North West, including Greater Manchester, Merseyside and Cheshire.
With a distinctly Mancunian feel, the centre is set to offer unparalleled services to local businesses. The centre will provide full sales, lease, hire, maintenance, service and repair solutions, training facilities, showrooms with a variety of different floor types, and meeting rooms for businesses needing to discuss their cleaning needs.
The Kärcher team is also happy to visit business premises to complete site surveys, conduct product demonstrations and provide training – all designed to support companies in finding the right solutions to increase their operating efficiency. With an unrivalled range of products available for purchase, lease and hire, the Kärcher team will provide the best solution offering the best fit for any business, commercially, practically and financially.
The announcement of the new Kärcher centre comes as the cleaning solutions provider continues to evolve and grow its offering, in the face of a business landscape in which cleaning and hygiene is more important than ever before.
Matthew Gellie, Head of Rental at Kärcher UK, commented, “Kärcher Hire has been working out of four depots across the UK for the last eight years, so we are thrilled to retain the dedicated staff from our Droylsden depot and to announce our headquarters in Chadderton. This expansion will undoubtedly supercharge our growth, doubling the size of our workshop and office space – giving us the ability to scale our operations.”
Simon Barlow, centre Manager of the Manchester Kärcher centre, added, “We can’t wait to assist businesses across the North West in finding the right tools for their cleaning requirements. Here at Kärcher we are armed with the expertise and an impressive range of products and are well equipped to support you in improving your operational efficiencies.”
The new site will be located at: Unit 4, Oldham Broadway Business Park, Chadderton OL9 9XA.
For more information, visit: www.kaercher.com/uk or email: enquiries.uk@karcher.com or call 01295 752082.
Jangro is a dynamic, forwardthinking company at the forefront of innovation in the cleaning and hygiene industry. As the largest network of independent janitorial distributors across the UK and Europe, Jangro delivers sustainable and high-quality solutions, all tailored to meet the diverse needs of facilities managers and cleaning professionals. Jangro’s extensive product portfolio – from catering to chemicals, paper to PPE – is designed to be practical, cost-effective, and easy to use, helping enhance hygiene and operational efficiency for businesses.
Built on long-term relationships with its distributors and customers, Jangro offers tailored solutions for a wide range of industries and sectors. From retail and hospitality venues to education hubs, healthcare facilities, and transportation sectors, Jangro’s customer-centric approach ensures exceptional service and value for its clients. Its local network provides a comprehensive and personalised service, combining regional knowledge with a commitment to large-scale operational excellence and efficiency. Every product is supported by various resources, including training programmes, safety data, and online tools designed to empower cleaning professionals.
Jangro wants to drive even further change in the industry when it comes to sustainability, as the company recently created its own sustainability scoring system, with the aim of getting set standards agreed upon and implemented across the sector.
Innovation is at the heart of Jangro. By leveraging advanced technologies like AI and IoT, Jangro enhances the customer experience and drives efficiencies. Its AI tools, like Carpet Care, help to streamline product selection and offer tailored solutions to improve hygiene standards. This commitment to pioneering solutions ensures that Jangro remains a trusted leader in the cleaning sector.
Jangro is a leader in sustainability, ensuring its products meet high environmental standards
without compromising performance, such as Planet Mark, ISO 14001 – Environmental Management System, and the EcoVadis Gold Medal, which puts Jangro in the top 5% of companies globally for sustainability excellence. Its NTRL range, for example, is a collection of eco-friendly cleaning solutions that are Vegan Society Accredited, free from harmful chemicals, biodegradable, and sustainably packaged. This range supports Jangro’s wider sustainability pledge, which incorporates responsible sourcing, reducing carbon emissions, and promoting a circular economy.
With a strong focus on safety, sustainability, and innovation, Jangro continues to set the benchmark for excellence in the cleaning and hygiene industry. Whether it’s through its ecofriendly offerings, industry-first Keep it Clean podcast, advanced technologies, or unparalleled customer support, Jangro remains committed to helping businesses thrive in a cleaner, greener, and safer world.
Come see us on Stand E55 at The Cleaning Show 2025. T 01204 795955 enquiries@jangrohq.net www.jangro.net
The energy- and resource-saving production of lacquers, paints and coatings is the focus of ystral’s trade fair appearance at ECS 2025. The European Coatings Show and Conference will take place in Nuremberg, Germany from 25 to 27 March.
The mixing and dispersing technology specialist, ystral projects, designs and manufactures mixing, dispersing and powder wetting machines as well as process systems, which are used worldwide in various industries. At ECS, ystral is focusing on the enormous efficiency gains that are possible in the production of lacquers, paints and coatings with innovative process technology. “We would like to enter discussions with manufacturers in these industries about how they can significantly reduce the energy and resource requirements of their processes – and how we can support them with our
technologies, our in-depth industry knowledge and our expertise, which has grown over decades,” says Dr Hans-Joachim Jacob, Senior Expert Process and Applications at ystral.
In Hall 4 (Booth no. 4-553) the company is presenting two technologies, the powder wetting and dispersing machine YSTRAL Conti-TDS and the YSTRAL Jetstream Mixer, which enable energy and process time savings of up to 90% compared to the agitators and dissolvers commonly used in the production of lacquers and paints.
30,000 times higher volume-specific power with the YSTRAL Conti-TDS
In the YSTRAL Conti-TDS, a vacuum and very high shear forces are concentrated in a very small volume. The vacuum separates the particles and then disperses them at a shear rate that is 1,000 times higher and with a volumespecific power that is 30,000 times higher compared to conventional technologies. “The result is significantly shorter process times, lower energy consumption and temperature rise, the highest quality and significant savings in costs, raw materials and space requirements,” says Jacob.
100% homogeneity with the YSTRAL Jetstream Mixer
YSTRAL Jetstream Mixers rely on a consistently vertical mixing principle and combine a turbulent micro-mixing zone in their mixing head with an almost turbulencefree vertical macro-mixing of the entire vessel contents. Unlike when a conventional agitator is used, the product is actually completely homogeneously mixed at the end of the mixing process – without unmixed zones, without sediments –and consistent results are achieved regardless of the batch size.
Further information
A white paper by ystral on the topic ‘Saving energy using more efficient process technology; 8 levers for more energy efficiency in the production of paints, varnishes, printing inks & coatings’ can be downloaded from: https://ystral.com/whitepaperenergy-paints-coatings An online seminar with Dr. Hans-Joachim
Jacob on the topic ‘The Magic of Making Paint –Innovations in Paint Production’ will take place on Tuesday 11 March 2025 in two identical sessions in English: at 9 am EST and at 4 pm EST. Registration for the online seminar is free of charge at: www. ystral.com/innovations-in-paint-production
Further information on ystral’s presence at the European Coatings Show 2025 can be found at: https://ystral.com/en/ecs-2025
For more information on ystral, contact the regional UK office (S3 Processes Limited) in Derbyshire: T 0845 5053530 info@s3process.co.uk www.s3process.co.uk https://ystral.com