
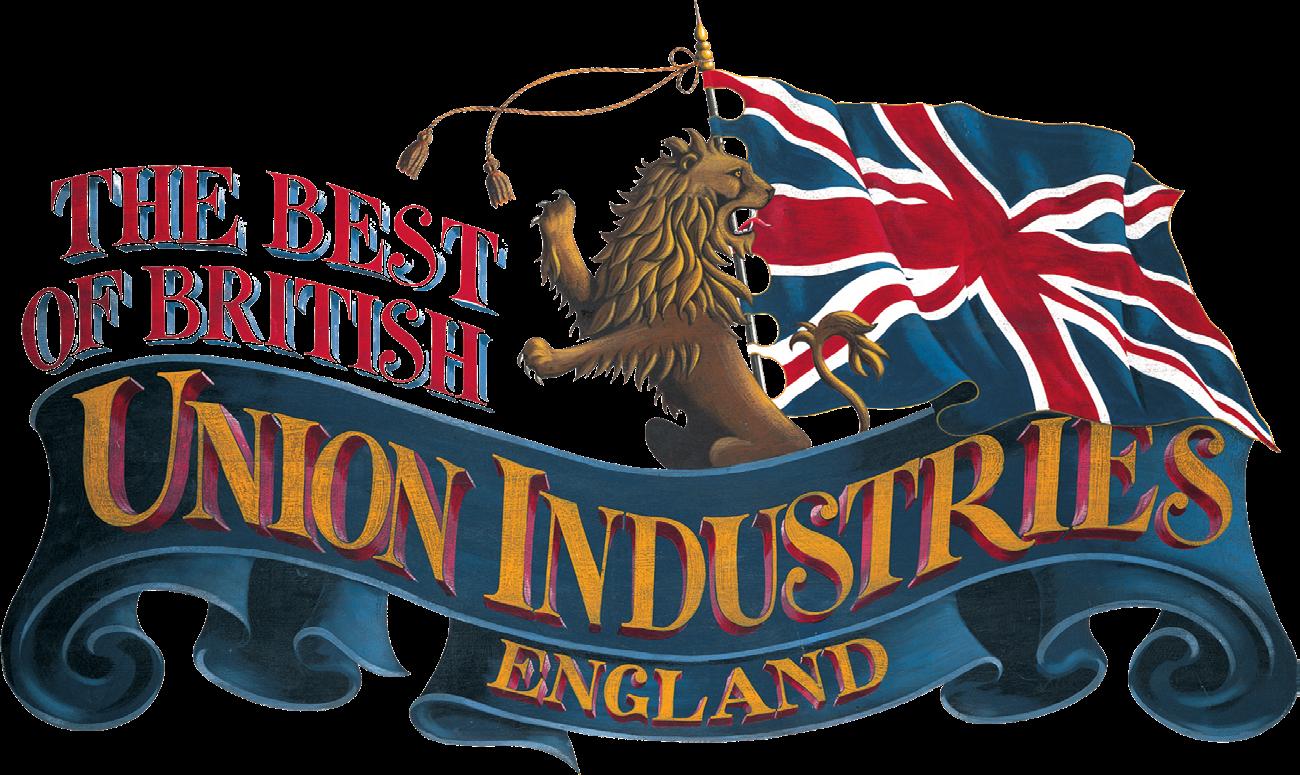
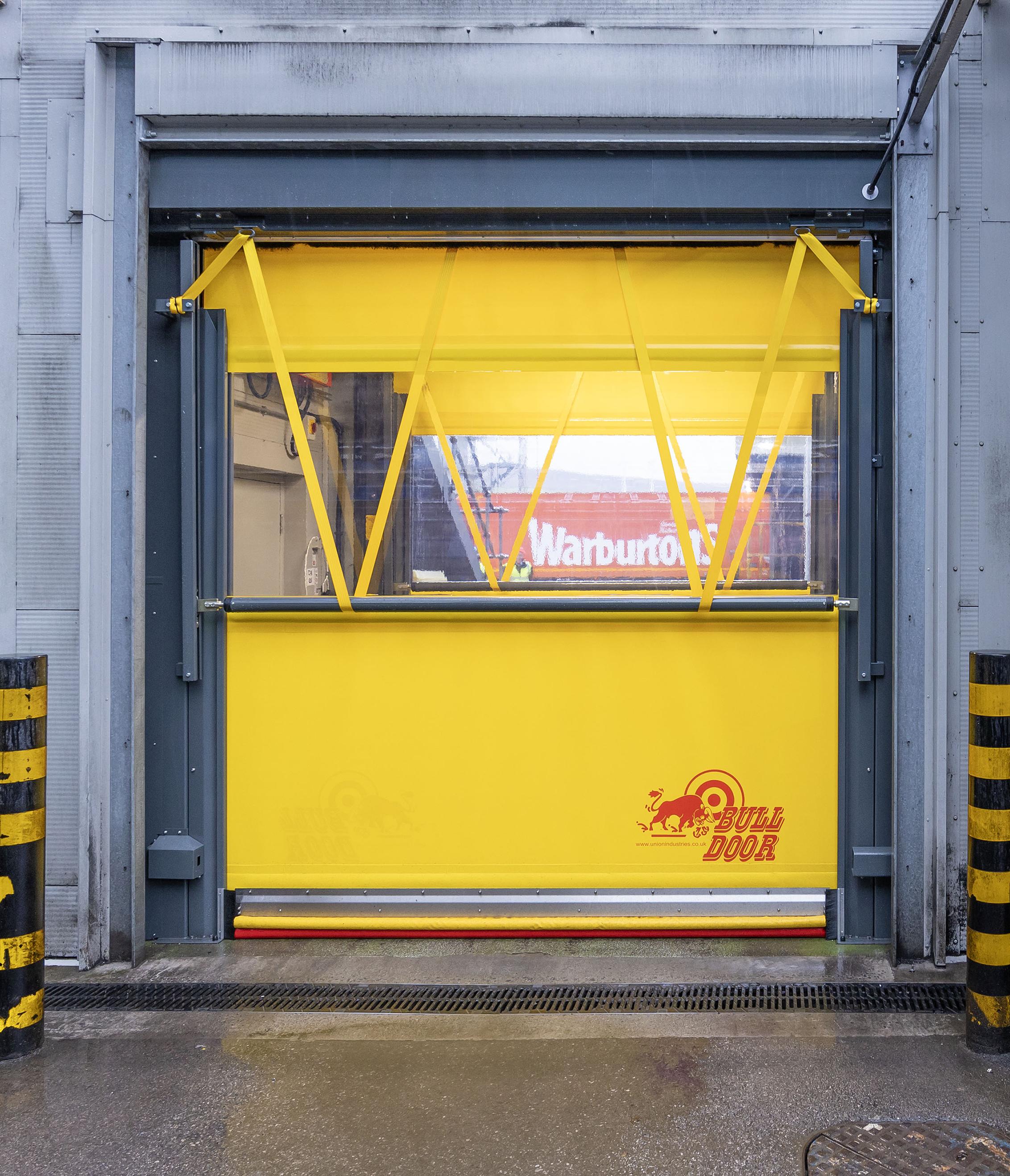
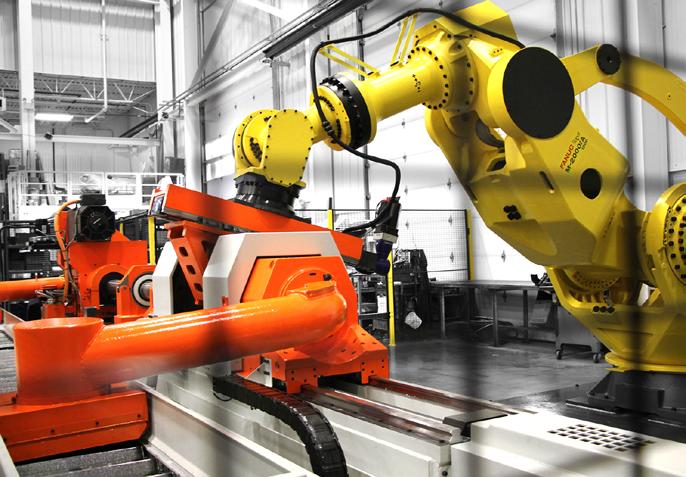
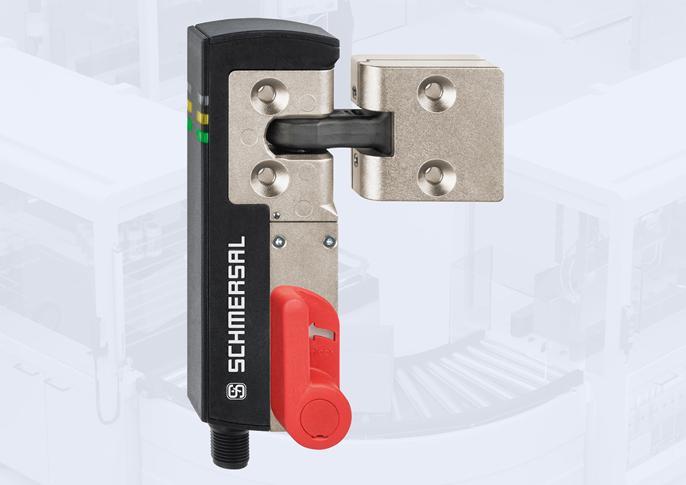
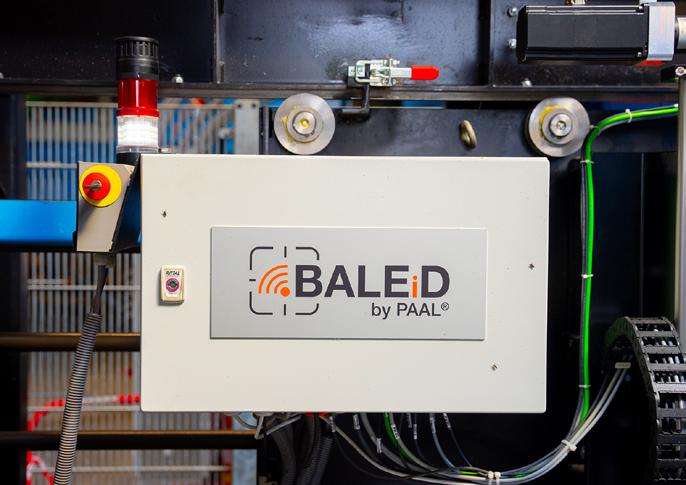
Third-party logistics (3PL) provider Kammac has been awarded both the Authorised Economic Operator (AEO) and the Fulfilment House Due Diligence Scheme (FHDDS) certifications, underscoring the company’s commitment to secure, efficient, and compliant supply chain services.
The AEO certification, endorsed by the World Customs Organisation (WCO), aims to improve international supply chain security and trade efficiency. Recognised in over 70 countries, certification holders work together to reduce customs restrictions and enhance cross-border trade operations.
As an AEO certified company, Kammac now benefits from prioritised customs procedures, enabling faster and more efficient import and export processes, including filings, inspections, and clearances.
“Achieving AEO status following HM Revenue and Custom’s (HMRC) rigorous six-month approval process marks a significant milestone for us,” said Leanne Lidell, Director of Compliance at Kammac. “The certification ensures simplified customs clearances and priority handling, meaning we can offer our customers more streamlined and reliable logistics services.”
In response to the needs of a longstanding global beverage client, Kammac initially attained AEO certification for its Wavertree site. Since then, all 15 Kammac sites have been included, further enhancing collaboration with global customers who require AEO status.
Kammac joins its sister companies within the Elanders Group in 2023 who also are AEO certified, providing a powerful network to existing and new clients.
“With our global footprint, our AEO certification facilitates seamless collaboration with fellow members, strengthening the service we can offer to clients,” said Leanne. “This certification bolsters logistics, particularly vital for UK-bound goods amidst the post-Brexit landscape.”
www.kammac.com
Reliable temperature measurement is a requirement for the success of many industrial processes. Berlin-based manufacturer Optris presents the Xi 640 infrared camera, a new member of its Compact Line, which enables reliable, affordable and non-contact temperature measurement in VGA resolution for mechanical engineering and the supplier industry.
With its Xi Compact Line, Optris combines the advantages of precise thermal imaging cameras with the benefits of infrared thermometers. The compact Xi 640 VGA infrared camera offers comprehensive, non-contact condition monitoring for industrial applications. With a high optical resolution of 640 x 480 pixels and a frame rate of 32Hz in the spectral range of 8-14µm, the VGA infrared camera can be used to monitor fast thermal processes at temperatures between -20°C and 900°C. Optris has equipped the Xi 640 with an “Auto spot finder” function, which can also be used
Well, apparently we’re on to something here!
With the total PROFINET node count coming in at close to 60 million nodes by the end of 2022, it’s safe to say at this point in 2023 the grand total has surpassed 70 million – and therefore the venerable PROFIBUS. It’s no wonder then that there’s a large contingent of people enjoying the newly-built site focused solely on the PROFINET technology. And PI is here supporting them.
Backed by the experts, the PROFINET ecosystem forum is a great place to
start or continue your PROFINET journey. Moderated by the technologists that work with the protocol day-in & day-out, a fast and thorough response is assured.
Some topics that have organically appeared and are being discussed:
t “PROFINET as a software solution”
t “ASIC vs. FPGA”
t “Memory footprint”
t “PROFIdrive implementation” t “ETS Board”
t “PROFINET certification”
Learn more: https://forum.profinet.com
to measure the temperature of moving objects without having to readjust the camera.
Like the other models in the Xi family, which has now grown to six models, the Xi 640 uses a motorised focus for convenient focusing from a distance. The image processing is carried out using the free PIX Connect software with line scan function, which is also included. Important parameters are configured via a USB 2.0 interface; a USB-to-GigE converter is optional. The Xi 640 is supplied with a process interface cable and a USB cable. The thermal imaging camera can be used in ambient temperatures between 0°C and 50°C as standard. Optris offers a wide range of accessories for the camera, from the air purge unit and mounting bracket to the water cooled housing, which enables ambient temperatures of up to 250°C.
www.optris.com/en/ new-xi-640-infrared-camera
INDUSTRIES has launched a series of new ‘pull-down’ soap and paper towel dispensers, which represent the latest additions to its ‘Classic Behindthe-Mirror’ range.
The new units include a touch-free 2-litre soap dispenser and large capacity paper towel dispenser. They are designed to operate from behind a mirror or panel and are intended principally for incorporation into bespoke cabinets.
The distinctive ‘pull down’ feature of the new products supports easy replenishment; the new units feature lockable sliding cartridges. They drop down below the bottom of the cabinet, providing easy access to the soap and paper towel containers. Once refilled, they can be raised back and locked in place to protect the consumables from tampering.
In this respect, they differ from many other cabinet systems, which typically require the front-facing mirror to be opened outward like a door.
All the dispensers in the range are designed to be easy to install. They require an aperture to be cut into the cabinet’s base; the dispenser is then inserted and screwed into position. Detailed technical data and installation guides are available.
Supported by a 10 year warranty, all the products in the range have been designed by our team and are manufactured at our production facility in Lytham, Lancashire. Specification details for the new Behindthe-Mirror dispensers are available at NBS Source and bimobject.com
For more information, please visit: www.dudleyindustries.com
Boasting over four decades of experience and rooted in Sheffield’s rich steel heritage, Charles Day Steels is thrilled to introduce their latest cutting-edge machinery acquisition – a new sheet metal bender. This state-of-the-art machine is engineered to cater to a wide spectrum of bending requirements with unparalleled efficiency and quality; emphasising Charles Day Steels’ ongoing investment strategy and commitment to advancing their bending and sheet metal pressing services.
Charles Day Steels reinforces its position as a leader in the metal processing industry, catering to a diverse range of client needs with precision and flexibility.
Pfeiffer Vacuum supplies the necessary vacuum solutions from a single source.
Building on a foundation of excellence and innovation, Charles Day Steels’ latest in a long line of machine investments underscores their commitment to providing customers with cutting-edge solutions. This strategic move not only improves their in-house capabilities but also broadens the range of services available to their clientele. Boasting a tonnage of 320 tons and a bending length capacity of 4,300mm, this newest investment marks a significant upgrade over previous capabilities; allowing them to accommodate larger and thicker materials, and expand their service offerings to include more complex and demanding projects. With this investment,
Renowned for its unparalleled precision and flexibility, this machine investment is a gamechanger in the industry, equipped with dynamic crowning and Pressure-Reference technology to ensure the highest repetition accuracy and consistent quality across all projects. Its modular machine concept, coupled with a broad power spectrum, allows for the optimal configuration for specific sheet metal work, significantly enhancing production efficiency and flexibility.
For more information about Charles Day Steels and their services, or to inquire about how the Bystronic Xpert Pro 320/4300 Press Brake can benefit your next project, please click here to get in touch today.
Contact T 0114 242 0101 sales@lasercutting.co.uk www.lasercutting.co.uk
Magog Industries are long established UK designers, manufacturers and suppliers of processing, mixing and conveying screws and barrels. Based in Hertfordshire, the company operate across the UK, Ireland, Europe and beyond.
Magog now offer their latest range in coatings and materials, designed to enhance longer life and greater resistance in for increasingly demanding processing using recycled material.
“We constantly strive to offer solutions from optimal design to reduce wear to offering a wide range of surface technologies,” explained Michael Bate, General Manager. “We design everything in-house but also work closely with specialist partners to meet our customers’ specific processing and production requirements. Our three core competencies run through everything
we do: process experience, manufacturing expertise and engineering excellence.”
Enhanced coatings include: Thin Dense Chrome (TDC) to enhance wear with low friction and is FDA Approved for food process environments. Ceramic Seal coatings reduce porosity and increase plating/coating life 4 to 10 times longer in corrosive environments.
In addition, HVOF (High Velocity Oxygen Fuel) that is thermally sprayed applied provides a crack-free 98% density with hardness of 62 to 72 HRC. This scratchresistant tungsten carbide coating has gained much interest among plastics moulders. Magog also offer screws and barrels for processing aggressive material from through hardened D2 tool-steel to high-performance alloys such as Hastelloy (nickel-molybdenum) and Incoloy (nickel-iron-chromium).
Magog also specialise in refurbishment of pre-used parts which extends the life of screws and barrels by re-honing and partial re-line of barrel bores and hard welded re-build of screw flights in bi-metallic alloy as standard. This provides a cost-effective option and ensure lower operating cost.
T 01920 465201 enquiries@magog.co.uk www.magog.co.uk
Electric vehicles are a decisive factor in reducing CO2 emissions in road traffic. They store the energy required for propulsion in batteries and an electric motor converts it into motion. In contrast to combustion engines, no fossil fuels are required. If the batteries are charged with electricity from renewable energy sources, they even have a completely CO2-free energy balance. Today, lithiumion batteries are used almost exclusively as accumulators. Vacuum technology is indispensable for their production.
Tracer gas leak detection ensures quality The proper functioning, quality and safety of lithium-ion batteries, which are used as accumulators in impermeability to external influences such as moisture ingress. For this reason, leak detection systems are used in battery production to check the batteries.
One of the world’s leading battery manufacturers for the automotive industry is currently using test gas leak detection systems from Zeltwanger Leak testing & Automation GmbH, which are equipped with complete solutions from Pfeiffer Vacuum. The systems must meet stringent requirements. The decisive factors here are achieving the required cycle time and high reproducibility of the battery cell test.
Enabled by Pfeiffer Vacuum technology, even the smallest leaks can be quantified and localized with the help of Zeltwanger’s testing systems. This makes it possible to quickly eliminate leaks in a downstream production step.
Changes to geometries and improvements to production methods and processes can be initiated based on the results obtained. This leads to quality improvements, increases the yield and reduces manufacturing and testing costs.
T +49 6441 802 0
www.pfeiffer-vacuum.com
In this issue of Industry Update, we proudly recognise Union Industries in our Commitment to Excellence feature
As the UK’s leading design manufacturer and installer of bespoke industrial doors, Union Industries has set the standard with innovative products like the ICe-PIC, Ramdoor, Bulldoor, Matadoor, Picadoor, and the unique Eiger Freezer Door. These doors are essential in distribution centres, warehouses, factories, and storage facilities across the UK and Europe, enhancing logistics and minimising heat loss.
Union Industries caters to a broad spectrum of sectors, including recycling and waste management, manufacturing, logistics and warehousing, food production, chemical and pharmaceutical, temperature-controlled storage, and retail. Highprofile clients such as Tesco, Cummins, Co-op, BAE Systems, Ocado, Jaguar Land Rover, Warburtons, Weetabix, and DHL International rely on their exceptional products.
Founded in 1972 by Paul and Isobel Schofield as a tarpaulin maker and repairer, Union Industries has evolved significantly over the past 52 years. The Leeds-based company transitioned to an Employee Ownership Trust (EOT) in 2014, a move that has been pivotal in driving its success. This structure ensures employees have a vested interest in the company’s performance, fostering a culture of collaboration and shared responsibility.
We spoke with Andrew Lane, Managing Director at Union Industries, to uncover the secret behind their success. Lane attributes their achievements to the durability, efficiency, and low maintenance requirements of their products. “Our Bulldoor, for instance, is often regarded as the ‘reliable workhorse’ of rapid roll doors, performing over 1.4 million cycles per year and becoming a favourite across multiple sectors,” he said.
Union Industries prides itself on offering British-designed and made bespoke solutions, complemented by exceptional after-sales support. Features like the ‘Crash-Out’ facility and ‘Auto-Reset’ system reduce damage and ensure continuous operation even after impact, making their doors some of the most reliable in the industry. Their commitment to quality is evident in their exclusive Lifetime Warranty scheme, providing customers with unparalleled peace of mind.
Innovation remains a cornerstone of Union Industries’ success. Their VR software has revolutionised customer interaction, allowing clients to experience products in a 3D virtual environment and make informed purchasing decisions. Looking ahead, the company plans to expand its product line, including the new ICe-PIC Door for automation and conveyors in and out of cold stores.
Union Industries is also focused on increasing its market presence both domestically and internationally, continuously innovating in high-speed door technology, enhancing sustainability initiatives, and investing in employee development. With the
Lane highlights the company’s strong, familyoriented culture, with high staff retention and several employee owners who have been with Union for over 20 years. “Union is a great place to work,” he said. “We are always on the lookout for new talent. If you think you’ve got what it takes to join our Union family, keep an eye on the recruitment page on our website and drop us a line.”
Union Industries exemplifies excellence in industrial door solutions, consistently pushing the boundaries of innovation and customer satisfaction. Their commitment to quality, employee ownership, and forward-thinking strategies ensure they remain at the forefront of the industry.
T +44 (0)113 244 8393 enquiries@unionindustries.co.uk www.unionindustries.co.uk
UNISIG is an industry-leading American producer of deep hole drilling machines. The company supplies a large variety of customers from aerospace and automotive to energy, firearms, hydraulic cylinders, military, medical sectors, smaller bespoke companies and large original equipment manufacturers (OEM.)
With unparalleled installation capabilities across Europe, Asia and America, UNISIG has the expertise to provide advanced precision-driven machinery for all jobs, with its complete deep hole drilling solutions that range from machinery to tools and automation.
The drilling capabilities include: Gun drilling, BTA, counterboring/reaming, trepanning, pull boring, skiving and roller burnishing, bottom forming, bottle boring and much more. With a wide range of stock machinery lines for diverse manufacturing needs, UNISIG can also provide bespoke-engineered machinery across all applications.
The American heavyweight was established in 1981 and since that time, has built up to a pole position across the global industry with its renowned production of gun drilling and deep hole drilling machines. Entrust Manufacturing Technologies acquired UNISIG in 1995 and then moved the company to its purpose-built headquarters in Milwaukee, USA.
Their US Milwaukee facility was expanded by over 100,000ft2 in 2019 to keep up with increased
production capacity demand levels. The CNC grinding machine also supports greater production, alongside regular upgrading across the production facility. The dedicated design engineers at the UNISIG Tech Centre in Milwaukee are more than happy to build customised drilling machine orders, from prototypes to finished machines.
We spoke to Philipp Steimle, Sales and Service Manager for Europe, to ask more about company developments, “Due to ongoing supply issues, our company is expanding its own manufacturing department. The Kellenberger CNC grinding machine we have installed will allow us to finish all the drilling spindles in-house. We have also installed a laser-cutting machine, a CNC press brake and welding stations so that we can do all the guarding
and coolant reservoirs in-house to avoid delays in our machine building.”
“The UNE6 series for medical instrument drilling with its fully integrated automation is a game changer for the industry and is proving highly popular in the market. We have, and continue to invest in more inhouse production rather than external third parties to keep on top of our orders.”
UNISIG is a clear market leader with a commitment to excellence to all customers. From quick machinery and part shipping orders delivered around the world, to meticulous service and repair jobs (conducted on-site and remotely), all jobs are carried out by an expert installation team made up of UNISIG engineers.
The recent addition of two new SSI Schaefer LOGIMAT® vertical lift modules (VLM) in the parts warehouse have further enhanced the alreadyexcellent customer service. The storage units hold up to 28 tons of spare parts each providing welcomed streamlined organisation and tracking. UNISIG operators can now effortlessly access parts inventory on the touchscreen and the VLM moves the correct tray forward, while a laser then selects the precise bin and location of the required part. This use of automated technology has optimised the inventory storage capacity and created a smoother, more accurate retrieval system.
UNISIG leads the way in expertly engineered, high-performance gundrilling. Another prime example of this is through the use of the Dual-Spindle gundrilling machine that comes with counter-rotation (UNE12-2-750-CR). This has impressive features that include the two spindles for advanced-precision gundrilling to 12mm in diameter and 750mm in depth, at 12,000rpm. And, with capabilities to produce over 2,000psi coolant pressure, with integrated chip collection system and a touchscreen control panel, the characteristic counter-rotation of cylindrical workpieces provides next-level hole straightness that you’ve never seen before.
Contact UNISIG to discuss how deep hole drilling equipment would support your business venture today: www.unisig.com
For over 40 years, we’ve helped our customers achieve success in deep hole drilling, providing them with the machines, automation and support they need to be competitive and profitable.
We have found that the initial energy we and our customers spend at the beginning of a quoting process pays off throughout the entire project, from inception to installation.
We take a systemised approach not only during this critical phase but also throughout the entire sales process. This ensures there are no surprises and that our customers know exactly what they can expect when starting discussions with UNISIG about their gundrilling and deep hole drilling needs.
This is our approach at UNISIG: 1) We listen to our customers, ask questions and understand what they need This may seem obvious, but often the temptation is there to just skip to a quote because we think we know what is needed after a brief discussion. Sometimes that is true, when the application is straightforward and familiar, or it is something we have a packaged solution for. We always try to make the quoting process quick and efficient, but there are times when the application deserves a more in-depth conversation. Our salespeople and engineers listen very carefully and often pick up on small details – a specific tolerance, material condition, process requirement or a future need for flexibility – that may change our recommendations.
2) We first identify a standard solution from our product line that can be applied at the lowest cost and shortest delivery possible At UNISIG, our product development mindset is to systemise solutions from our experience in many different industries, make them automation ready and embed application flexibility whenever possible. We invest millions of dollars annually in our product line and related spare parts, giving us a strong starting point for new applications. Our standard product line encompasses much more than machines, including standard automation, workholding, accessories and tooling that we can offer as part of the solution.
3) If a standard solution isn’t available, we consider a customised solution and we stand behind it
UNISIG is very good at building customised machines, and we do so often. Once we and our customers agree that a special solution is needed, we move forward with a great deal of confidence and experience.
We start by evaluating how we might approach the design using standard modules or proven concepts, thus eliminating long debug cycles and/or high costs. Then we use our mechanical and electrical engineering disciplines to virtually test the new machine before we build it.
4) If a commodity solution is readily available, we recommend that rather than upsell a machine the customer doesn’t need
We build machines that can gundrill or BTA drill deep holes that are impossible to drill on machining centres. Even if it may be possible to drill some deep holes on a CNC machining centre, our machines have the power, speed, dimensional accuracy, spindle density, coolant systems and process control that will improve productivity, tool life and reliability. Typically, though, when a customer comes to UNISIG with a specific part need, at that point they’ve most likely already struggled with a conventional machine and realised that a deephole drilling machine is obviously the way to go.
Please visit: www.unisig.com, email: info@unisig.de or contact us on: +49 (0)7125 9687590.
It couldn’t be more flexible: solenoid interlock now with new functions
The world’s smallest electronic solenoid interlock AZM40 now offers even more versatile application options with new accessories and new features. With dimensions of 119.5 x 40 x 20mm, it is particularly suitable for small safety gates or maintenance hatches and confined installation spaces. Despite its compact design, the AZM40 achieves a remarkable locking force of 2,000N.
With the new lockout tag, the AZM40 can now also be used for larger, accessible machines and systems. Service staff can attach a lock to the lockout tag when entering the danger zone. This means that the door of the safety guard cannot be closed, and unintentional start-up of the machine is prevented.
In addition, the new versions of the AZM40 solenoid interlock can be extended with an emergency exit or emergency release. Two different versions – with lever or push-button – are available. The lever is available both as an emergency exit and as an emergency release and can be mounted directly on the AZM40. The push button is also available as an escape release or emergency release. Its similarity to an emergency stop button makes it intuitive to operate. The emergency exit ensures that any trapped persons can free themselves from the machine area. The emergency release is used to ensure that the danger zone in a machine can be reached quickly in an emergency – eg. in the event
of a fire.
The new ‘inner values’ of the AZM include the
Another advantage is the long service life with now 500,000 switching cycles (actuator cycles) and 1,000,000 switching cycles (locking cycles).
addition of the high degree of protection IP69 and the temperature range of -20°C to +55°C, which open up additional application possibilities.
The bistable interlock principle of the AZM40 is also sustainable, with the advantage of permanently lower power consumption. Compared to monostable solenoid interlocks, more than 50% of the power consumption can be saved. A further advantage is the added safety: even in the event of a power failure, the safety door remains securely closed during hazardous run-on movements.
Thanks to the 180 degree angle flexibility, the actuator can approach the AZM40 continuously so that the interlock can also be used on flaps that do not close at a 90 degree angle or that open upwards at a 45 degree angle. The angle flexibility ensures that the interlock can be easily installed even in confined and difficult-to-access locations.
The AZM40 can be easily mounted on standard 40mm profiles with no overhang. For other profile system widths (20mm, 30mm, 45mm, 50mm and 60mm), a set of two universal mounting plates can be used for the AZM40 and actuator. This ensures quick and cost effective installation for a wide range of profile system widths.
Contact: Steve Watkins, Marketing & Business Development T 01684 571980 swatkins@schmersal.com www.schmersal.co.uk
The inspection of valves is an important part of the maintenance programme in industrial production and the effects of leaking valves are often underestimated. Around five to ten per cent of all valves in industrial plants leak. Undetected leaks caused by irregular or improper maintenance can have serious consequences, such as personal injury, but also costs due to loss of raw materials and unplanned production downtime, contamination and environmental pollution.
Explosion hazardous areas in industrial production often have harsh environmental conditions with high temperatures, corrosive chemicals, and abrasive particles. This can lead to damaged valves and thus to unplanned machine downtimes.
Thanks to regular in-house valve maintenance, companies only need to replace valves when they are defective; working valves are not replaced during standard inspections. Valve inspection can easily be carried out during the production process without having to test the functionality of the valves on an external test bench. This avoids production downtime and saves considerable time and money.
Valve Sense: The new generation of valve inspection for Ex-zones
As part of modern condition monitoring programmes, companies need easy-to-use, digital inspection tools to check their systems quickly and independently and to share data within the team or management. With Valve Sense for Ex-zones, i.safe MOBILE and their partner Senseven have transferred today’s digital capabilities to an intelligent valve leak detection system. The user-friendly kit simply connects acoustic emission sensors to i.safe MOBILE’s 5G industrial smartphone IS540.1 and transforms it into an intelligent, mobile valve inspection system via the Senseven software.
The software guides the user through the inspection process in a self-explanatory manner, records the sensor data and processes it. Algorithms and artificial intelligence help to analyse the data and provide immediate results on site. With
a Wi-Fi or network connection via a SIM card, all measurements are automatically synchronised with the proprietary Senseven back office, a Cloud-based platform that can be accessed from anywhere via mobile devices or a desktop, eliminating the need for data transfer via USB or card storage. The inspection data can then be utilised for further analysis and reporting and integrated into existing asset management systems.
Valve Sense requires neither training nor in-depth expertise to detect leaking valves of all types and sizes for water, gas, steam, air and viscous liquids. This allows companies to inspect their systems themselves regularly and without interruption of the process, detect leaks early and react immediately – without having to wait for the next maintenance cycle by external inspectors. They no longer depend on expert knowledge, can increase the efficiency of their processes, avoid additional costs and reduce the safety risk for employees.
www.isafe-mobile.com/en
Electrical heating systems have several safety features built in to prevent dangerous situations. High-limit sensors, or safety sensors, are one of the most important. Not only do they protect people, they help keep manufacturing lines running by limiting damage to equipment and product. In this article, Jeremy Ohse (pictured) at industrial heater, temperature sensor, and controller manufacturer, Watlow, explores best practice and considerations for high-limit safety sensors.
Understanding safety sensors
Thermal loops consist of a heater, temperature sensor, and heater controller. The controller has a temperature setpoint, receives a signal from the temperature sensor, and modulates power to the heater to maintain the temperature setpoint.
If there is a failure in the primary thermal control loop, the redundant safety sensor can tell the controller to reduce power to the heater or shut down the entire system. The most common failures are physically damaged sensors, worn out components, and pinched wires.
In an application away from industry, a hot tub uses a high-limit sensor to prevent the water from getting too hot. If the primary control loop fails, the heater will continue to heat the water. When the water temperature reaches a certain level, usually between 110 and 120°F, the highlimit sensor disables the heater to keep the water at a safe, enjoyable temperature.
To provide additional safety, when the high-limit sensor trips the system, users are ‘latched out’ until the system is inspected and reset by an operator, system designer, or
manufacturing engineer. Once the system is repaired and reset, it will operate normally again. In the hot tub example, the highlimit sensor will likely disable the pump in addition to the heater. A technician may need to inspect the hot tub and replace the primary sensor – or other defective parts – before resetting the system. This safety latch is often achieved in industrial systems through a programmable temperature controller and mechanical relay.
High limit applications
The high limit sensor in these scenarios are often thermistors, resistive temperature detectors (RTDs), or thermocouples (TCs). The best type of high-limit sensor is application dependent. The controller is often programmable so the user can adjust the primary control loop and the safety control loop temperature setpoints.
Location is essential
For the safest operation, the safety sensor should be attached directly to or immediately adjacent to the heat source. The farther the safety sensor is from the heat source, the more likely unwanted damage will occur when the safety control loop is engaged. For this reason, Watlow offers many heating products with sensors already embedded in the heaters.
Multiple high-limit sensors are used on large heating systems. A very large circulation heater may have several safety sensors to help identify failures in different sections of the heater. This approach allows operators to identify potential issues before they become a bigger problem.
Additional considerations
While the primary sensor and safety sensor are often two separate physical objects, they both plug into a single
heater controller. Just as there could be a failure in the sensor, there could be a failure inside the heater control. If the heater controller is agency certified (UL, CE, or ETL), it’s likely there are two independent micro-controllers inside the heater control box, one for the primary thermal loop and one for the safety loop. This second safety microcontroller is an important often forgot about distinction when selecting a heater controller. Look for the agency marking and inquire with the manufacturer if in doubt. Runaway thermal systems create risk of both fire and electrical shock.
Some systems involve a chemical reaction. Even after the heater is turned off, the chemical reaction may continue. If it becomes exothermic and continues to produce heat, shutting down the heaters will not stop the temperature from continuing to rise. In this example, the safety sensor could activate a fire suppression system.
A less accurate, lower cost method to provide safety could utilise a resettable thermostat or thermal fuse instead of a high-limit safety sensor. These devices are wired in series with the heater and create an open circuit when a manufacturer pre-defined temperature is exceeded. These alternatives can be good solutions in some applications, but nearly always have lower performance and are driven by cost.
Watlow integrates all types of thermal safety sensors into our heaters: TCs, RTDs, thermistors, thermostats, and thermal fuses.
High-limit safety sensors are a critical part of safe heating systems. By using the most suitable safety sensor and following best practices, your system will have the best opportunity to prevent unforeseen accidents and damages.
Watlow provides a range of industrial thermal sensors. Discover them at: www.watlow.com
The oil and gas industry is a crucial pillar of the global economy. However, this industry presents significant environmental and health challenges, including those related to noise. Monitoring and measuring noise in the oil and gas industry is essential to protect workers, local communities and the environment from the impacts of excessive noise exposure.
The sources of noise
Noise in oil and gas processing facilities can originate from various sources, such as compressors, pumps, turbines, generators, and more. The noise level and frequency depend on factors such as the type, size, speed and condition of equipment, the flow rate and pressure of the fluid or gas, and the distance and direction of the sound propagation.
The impact of noise
The noise that this work creates can have a negative impact on workers (and in turn your organisation), the environment and the community. For workers, exposure to high levels of noise can cause hearing loss, tinnitus, stress, sleep deprivation and other illnesses such as cardiovascular disease.
When it comes to the environment, noise can disturb wildlife, especially birds and marine life, and affect their behaviour, reproduction and migration habits and their survival. When considering the community, noise can also affect local residents causing them annoyance, but also sleep disturbance and interfering with their quality of life.
Managing noise
Managing noise in the oil and gas industry requires a systematic and proactive approach that involves identifying, measuring, assessing,
controlling, and monitoring noise sources and impacts.
To do this effectively, it is recommended to conduct a noise survey that will help in determining the noise levels and frequencies at different locations and times, and compare them with the regulatory and occupational limits and guidelines. Additionally, implementing a noise management plan that outlines objectives, responsibilities, actions, resources and timelines is beneficial.
Any plans you put in place should prioritise eliminating or minimising noise at the source, followed by isolating or reducing noise along the path, and finally protecting or reducing noise at the receiver.
Can Cirrus Research help?
Not only can Cirrus Research experts talk you through the steps that you need to take to protect your workers, your business, the environment and local communities from the noise produced by your operation, they can also suggest the best instruments to help you do so.
Instruments recommended for monitoring noise in the oil & gas industry:
t The Quantum Outdoor Cloud-Based Monitor –Place this instrument around the boundary of your site and effortlessly investigate live and historical noise events anytime, anywhere. For an added cost, this instrument can also monitor ground vibration, weather and air quality.
t The Intrinsically Safe doseBadge – This wearable device has the advantage of carrying IS certification and is ideal for monitoring personal noise exposure in hazardous zones and explosive atmospheres.
t The Optimus+ Industrial – This sound level meter captures all essential noise level data simultaneously, allowing you to ensure your occupational noise surveys are comprehensive and robust.
Speak to our team by emailing: sales@ cirrusresearch.com or calling +44 (0)1723 891655, or by submitting a contact form on our website!
The Environmental Services & Solutions Expo (ESS Expo) 2024 is set to be the UK's premier environmental event, bringing together professionals from across the entire supply chain under one roof. Themes range across diverse sectors like waste management, recycling, energy, water, construction, manufacturing, policy-making, environmental consultancy, and so much more. Scheduled for 11-12 September 2024 at the NEC, Birmingham, the event offers a plethora of opportunities for attendees. Register for your free ticket to check out all of the below, and more:
1. Explore the co-located shows
ESS Expo 2024 encompasses five major environmental shows: Resource & Waste Management (RWM), Energy, Fuels & Decarbonisation (EFD), Water Resource Management (WRM), Contamination & Land Remediation (CLR), and Air Pollution Control (APC). Each show addresses critical aspects of environmental sustainability, offering a comprehensive view of the latest industry trends, technologies, and solutions. ESS Expo allows attendees to seamlessly explore a wide array of sectors and industries, all focused on addressing the most pressing environmental challenges of our time.
2. Attend expert-led conferences
ESS Expo features an expert-led conference programme that includes interactive speaker presentations, lively panel discussions, workshops, and Q&A sessions. Attendees will have the chance to learn from industry leaders and gain insights into the latest trends and innovations across the entire environmental spectrum. Current headliners include Chris Packham MBE (one of the UK’s leading wildlife presenters and conservationists) and Mike Gunton, an icon of wildlife broadcasting as BBC Studios' Creative Director and executive producer of record-breaking series, Planet Earth III. More huge names will be revealed soon (think global brands and Government officials, as well as industry focused seminars).
3. Network with industry leaders
Networking is the cornerstone of ESS Expo, with no shortage of options over the two days. With numerous opportunities to connect with peers, suppliers, and potential clients, attendees can engage in private meetings, AGMs, tutorials, member networking events, industry-specific forums, award presentations, breakfast briefings, and socials around the central bar, Inn on the Green, and ESS Live Stage. This is a prime chance for environmental leaders to build strong, lasting relationships and expand professional networks.
4. Check out all of the stages
ESS Expo boasts 17 Stages, 350 speakers, live bands, DJs, live demos and a whole lot more. Discover a diverse array of stages and themes at the show, each designed to bring you the latest insights and innovations across the environmental sector. From high-level government
discussions and cutting-edge technical sessions to interactive presentations and vibrant entertainment, the stages offer something for everyone. Attendees will benefit from a unique blend of learning, networking, and fun as they tackle the industry’s most pressing issues. Check out the full list here.
5. Witness live demonstrations
From spectacular displays of cutting-edge machinery, to live demonstrations of waste-processing equipment, refuse collection vehicles or street sweepers – the outdoor section of the show is a unique opportunity to see apparatus working in its intended environment, offering practical insights into their applications and benefits. It’s also a great excuse to step outside and enjoy some of the sunshine! Witness jaw-dropping displays that feature shredders, balers, material handlers, fire safety, dust suppression equipment and more – live in action. Discover the latest developments and innovations in municipal waste & refuse vehicles, and how they’ll benefit your operation, or see the latest fire protection and prevention solutions in action.
6. Be Inspired at the award schemes & initiatives
ESS Expo proudly features a variety of award schemes and initiatives that celebrate the achievements and contributions of outstanding individuals and organisations within the environmental sector. Women in Resource & Sustainability is dedicated to celebrating and exploring the contributions of women in the resource, recycling, and waste management sectors. It offers a fantastic opportunity for professionals within the industry to share experiences, challenges, and success stories, fostering a supportive community and encouraging greater inclusion and diversity in the sector. The 35 Under 35 Awards identifies the trailblazers in the environmental sector under the age of 35 who are striving for professional excellence, promoting industry innovation, and giving back to their company or community. The Environment 100 Recognition Scheme recognises our environmental leaders and sustainability champions, shining a light on the visionaries driving forward environmental sustainability in the UK. Check out what else is on here.
7. Engage in interactive workshops
Participate in hands-on workshops designed to provide practical skills and knowledge. These sessions are tailored to various expertise levels and offer a deeper understanding of specific environmental technologies and practices. Workshops and talks will cover a range of topics, offering practical insights and solutions for
everyday challenges in the environmental sector. Keep an eye out for the networking areas across the shows!
8. Meet world-class suppliers, discover world-class solutions
Discover products and services from some of the world's most influential brands and suppliers. This is an excellent chance to explore new solutions, compare products, and find the best fit for your organisation's needs, discover innovative products and services from over 600 environmental suppliers showcasing cutting-edge technologies and strategies in net-zero, decarbonisation, resource management, circular economy, water scarcity and management, biodiversity conservation, energy management, environmental emergency response, land management, emissions control, and more. Check out our full list of exhibitors here.
9. Further your contribution to sustainability
New for 2024, the ESS Green Ticket donates 100% of the proceeds to our partner environmental protection projects. These initiatives are carefully selected to ensure they have a meaningful impact, helping to offset the carbon emissions generated by the event. You will also be able to get a green ticket on site.
A Green Ticket Contribution:
t Supports vital environmental protection projects
t Contributes to the global effort to combat climate change
t Helps carbon balance the emissions associated with attending the event
Learn more about our environmental protection partner projects here.
10. Enjoy the outdoor space, live music, and social events
We know that walking around the show can be thirsty work. Which is why there’s ample opportunities to relax and enjoy a drink or two and unwind in-between meetings. Whether it’s checking out the ESS Central bar, sitting outside by the Inn on the Green, or soaking up the sun with some live music at Paignton on the Park or the ESS Live Stage, put your feet up for a minute and network in a more informal setting. The dedicated outdoor space features cold drinks, warm welcomes and is the perfect opportunity to take a break from the show and relax with customers, suppliers, or colleagues in a more relaxed setting. Check out what else is on here.
Whether you’re a visitor looking to gain insights into the latest environmental trends or an exhibitor aiming to showcase your innovations, ESS Expo 2024 promises a wealth of opportunities to engage, learn, and grow. Don't miss out on this unparalleled event in the environmental sector – secure your ticket today!
www.ess-expo.co.uk
We all agree the ‘cradle to grave’ material traceability is the goal that we should all be aspiring to, but bale identification has not been reliable and has depended on inefficient manual processes.
Let us introduce you to the new, patented BALEiD by PAAL system, which is set to revolutionise traceability within the industry.
Let us allow you to shake off the limitations of manual process and bring you an efficient closed loop patented system. It is now possible to generate, print and attach a label to each bale automatically and securely.
Our initial challenge was to devise the process that would automatically and securely attach the label to the bale. The patented PAAL applicator has achieved this and is linked to a label printer. With this set up it is possible to automatically generate, print and attach each label to a bale that shows whatever
relevant information that is contained within the baler control system.
We appreciate a huge amount of work and effort goes into producing a bale and now for the first time BALEiD by PAAL enables the complete picture to be captured in a convenient label. Not only will this system capture the fundamentals such as date/ time/ location and material type, it can also track each bale individually for shipments.
Let us open up a world of opportunities for your waste management system, by attaching a label (containing a unique RFID chip) to each bale you would be able to automatically record, monitor and control your bale output with valuable information, for example:
t Date and location where the bale is produced
t Precise weight of bale
t Purity of material
t Storage location and shipment onto truck
By implementing the BALEiD by PAAL you can eliminate the rejection of material (by the end processor) which is hugely costly and disruptive, any such risks are addressed prior to despatch.
The scanning of the RFID tags on the bales, the end processor receives, updates the RFID database. This results in the
provision of evidence for the recycler that the material has been processed in a certain way, giving the necessary ‘cradle to grave’ traceability.
Our priorities are changing, driving today’s standards and business practices. Closed loop recycling is at the heart of today’s circular economy demonstrating a strong commitment to sustainability. Adhering to environmental regulations is crucial, closed loop recycling helps businesses stay compliant with waste management and sustainability regulations.
Let us take you to the next stage of waste management efficiency, let us maximise your potential with BALEiD by PAAL.
Join us at RWM Show September 11th and 12th, Stand ME-A90 where we will be demonstrating BALEiD by PAAL.
www.kadantpaal.com
CPL/Puragen Activated Carbons has been a long-time supporter of the Environmental Services & Solutions Expo (ESS, incorporating RWM and EFD) and will again have a large stand at the show, which takes place at the NEC on 11-12 September 2024.
They again plan to display one of their eye-catching large Clean-Flo® mobile carbon filters on their Stand (EN-F50) and the company’s Head of Strategic Partnerships, David Reay, will be making a presentation on Day 1 of the event, on the EFD Technical Stage.
He will outline the various applications for activated carbon filtration relevant
to the sectors covered by the ESS expo, with a particular focus on PFAS-group ‘forever chemicals’ that can now be effectively removed and destroyed with CPL/ Puragen’s technical solutions. PFAS-group chemicals are a particular concern for the water industry, as well as society in general, and activated carbon is the best available technique for their efficient removal.
The presentation will also touch on developments in the purification of biogas and biomethane, as well as the recent energy-from-waste BREF that demands far lower emissions of mercury and dioxins from EfW facilities.
Come see us on Stand EN-F50. To contact CPL/Puragen in advance of the expo: T 01942 824240 info@activated-carbon.com www.activated-carbon.com
Impact Air Systems, the world’s leading air-based technology provider for the environmental, waste, recycling, and resource management industry, announces they are to exhibit their innovations at RWM in Birmingham, 11-12 September 2024 on Stand D224
“We are excited to formerly announce our latest innovations at these key industry events. Impact strives to be at the cutting edge of technology to offer solutions built for the industry. The promotion of resource recovery and the circular economy is a common theme across all our innovations this year with our Airlift and Zigzag Air Classifier (ZAC) solutions at the forefront, which enables waste operators to effectively recover materials such as flexible plastic packaging, glass, and aggregates, with a remarkably high success rate,” said Nick Ball, Impact’s Managing Director.
Impact Air Systems pride themselves on their British engineering roots along with innovative air system design applied to solutions to separate materials, which catapulted them into the recycling equipment market back in the early 1990s. Many years of working with industry professionals and listening to their issues with regards to separating waste to recover valuable materials, has resulted in Impact’s catalogue of impressive solutions which
add value while easing the pressure to produce quality material streams.
Impact’s solutions are in high demand by waste operators for their distinctive ability to separate material effectively & efficiently, while being engineered to an exceptionally high standard, providing minimal maintenance and downtime.
RWM is the perfect platform for Impact to showcase its range of solutions to the recycling market. For those who are seeking reliable equipment to improve their material quality, it is recommended that you take this opportunity to find out how Impact can make a difference for you.
Find out more at: www. impactairsystems.com or contact the team on +44 (0)116 244 8855 or email: sales@impactairsystems.com
There is a common misconception that all breather valves are rigorously tested to a certain standard before they are sold, but unfortunately, this is definitely not the case. Many breather valves on the market are not subject to stringent testing protocols, leading to significant safety and operational risks. When these untested and, more importantly, unsafe breather valves are procured, the end user unknowingly takes on many risks.
It is crucial to know the facts by conducting thorough due diligence from the initial purchase and throughout the entire lifecycle of the unit. First, ask yourself: Are your breather valves set correctly?
Incorrect settings can lead to valve malfunction, causing potential overpressure or vacuum conditions that could compromise tank integrity. Are your breather valves performing safely? Regular testing ensures they function within safety parameters, preventing hazardous situations.
Do you know your breather valve leak rates, and is your media hazardous, flammable, costly or toxic? Understanding leak rates is vital for environmental, occupational health and safety compliance. Do they function as per intended design and specification, and do they meet the set point? This ensures that valves operate as required under specific conditions.
Has your breather valve been tested in accordance with API2000 Section 5.4? Compliance with this standard guarantees that valves meet industry requirements. Do you monitor your breather valves as part of your aging plant management plan? Regular monitoring can identify wear and tear before it leads to failures. Lastly, are you confident that all your breather valves maintain optimum efficiency and performance? Ensuring this can prevent costly downtime and environmental hazards.
The only irrefutable test method is using the Vent-Less test bench. This groundbreaking technology is revolutionising testing, ensuring that breather valves are tested prior to installation and during
the life term of the unit. The award-winning Vent-Less test bench aligns with the API2000 Section 5.4 test protocol, and the instantly generated certification stands up to regulatory scrutiny. The documented leak rate is also invaluable for LDAR, IED, and Regulation 61 reporting. These questions are critical for assessing your vulnerabilities and ensuring the safety and efficiency of your operations. Don't leave it to chance – make sure your breather valves are thoroughly tested and maintained using the Vent-Less test bench.
Come see us on Stand EN-J71. T +44 (0)1726 844707
info@assentech.co.uk www.assentech.co.uk
LogiDataTech’s dynamic MF-Oxy is an oxygen measurement system that can determine residual oxygen content in exhaust gas from combustion plants precisely and reliably. Therefore, with the use of a coupled controller, a plant operator can minimise the excess air specified for safety reasons, optimise combustion in the boiler and thus increase efficiency.
In this way it is possible to compensate for fluctuations in fuel quality for modern wood firing. Unlike Lambda probes, which measure the relative oxygen content, this robust measuring system determines the absolute content. For this reason, fluctuations in air
the measurement.
The system is calibrated electronically, without the need for reference gas or human intervention, in atmospheric air at the end of the furnace’s ventilation phase, thereby reducing maintenance work.
The measuring range is defined from 0.1-25Vol% oxygen. The system is offered with a temperature range of 0-250°C or 0-350°C, and a range of probe lenghts and two types of sinters.
www.logidatatech.com
Anua Clean Air UK Ltd stands at the forefront of air pollution control, specialising in the cutting-edge biological treatment of air and biogas. Our expertise shines through our patented Biofiltration and Bio Trickling technologies, designed for high performance and cost-effective emission abatement using innovative recovered media.
Our flagship technologies, Monashell® and CrumRubber , are sustainable marvels that incorporate reclaimed materials as key filtration components. These materials’ unique properties not only excel in capturing and treating pollutants but also deliver significant environmental benefits, including contributions to the circular economy and a reduced carbon footprint through minimal water and energy usage and zero consumables.
Jeddah, Laguna Lake in the Philippines, Coimbatore in India, and Sindos in Greece. Our CrumRubber™ technology has been successfully deployed in the Canary Islands, China, Oman, and the UK and Ireland. Exciting collaborations with Air Clean SRL and Air Clean USA are underway, bringing Dual Stage CrumRubber /Monashell® systems to Puglia, Southern Italy, and across Massachusetts, Connecticut, Maine, and Rhode Island in the US.
In recent years, alongside our parent company Anua Clean Air International Ltd and our Italian sister company Air Clean SRL, we’ve expanded our footprint across the UK, Ireland, and globally. Our international portfolio boasts impressive projects, such as the Dual Pass Monashell® installations in Riyadh,
Anua Clean Air UK also excels in maintaining the health and efficiency of existing odour control units. Our services include comprehensive equipment health checks, process upgrades, and media replacement services. Over the years, we’ve consistently provided these essential services to hundreds of biological air treatment installations worldwide, ensuring optimal performance and longevity.
Join us in our mission to purify the air and protect the environment with innovative, sustainable solutions. Contact us today: +44 (0)1450 420017 www.anuacleanair.co.uk
Bluewater, a world leader in innovative water purification and beverage solutions, is thrilled to announce the launch of its innovative solution for high-quality drinking water dispensers in the UK, the Bluewater Flow. Already a smash hit in the United States with over 14,000 installations, the Bluewater Flow sets a new standard across the UK and Ireland for dispensing on-demand pure, great-tasting water in offices, gyms, hospitals, and schools that is free from potential contaminants such as toxic PFAS chemicals or waterborne germs.
The self-sanitising, free-standing Bluewater Flow indoor refill stations are designed for simple installation & connect to any potable water line within a 100-foot range for easy replacement of existing water fountains, water coolers, and large jug dispensers. Users can enjoy chilled, fast-flowing water that undergoes a revitalising process including the infusion of electrolytes, increased alkalinity, oxygenation, and trace minerals, providing a great-tasting hydration experience.
Bluewater Flow 7 x Advanced Purification uses an existing water source and removes up to 99% of any impurities that can be found in typical tap water. The Bluewater Flow purified water system also improves the water by adding trace elements of essential minerals and electrolytes, and finally, finishes the water through a coconut carbon filter for a crisp, fresh, delicious taste.
The new Bluewater Flow refill stations for easy access to pure drinking water offer the following product highlights:
t Great-tasting, high-quality water free of lead, toxic chemicals like PFAS, and other contaminants
t Convenient small footprint
t Easy to install and maintain
t High capacity, rapid filtered water dispensing
t Serves both cold and hot water
t Sustainable, cost-efficient solution that reduces single-use plastic bottle waste and energy usage
t Foot pedal for no-touch dispensing
t Competitively priced with finance purchase or leasing packages available
Bluewater key account sales manager, Antonio Tedeschi, says the advanced filtration technology offered by the Bluewater Flow indoor station is a gamechanger in the drinking water dispenser industry.
Offering reliable and eco-friendly access to clean water, the Bluewater Flow is already a top seller in the United States with thousands installed at premium brands such as Red Bull, Apple, Marriott, Peloton, United Airlines, and Google as well as many state schools and other educational institutions.
“Our commitment to innovation and sustainability is exemplified by the Bluewater Flow station that delivers business customers the opportunity to provide healthier drinking water to customers and staff while reducing their environmental impact,” Antonio Tedeschi said.
M 07785 302694
david.noble@bluewatergroup.com www.mynewsdesk.com/bluewater www.bluewatergroup.com
The next-generation Ionpro system is a compact and portable solution that ensures the production of high-purity, bacteria-free water that meets the stringent standards set forth by pharmacopoeias worldwide. By providing a streamlined and efficient approach to purified water generation, Ionpro empowers pharmaceutical companies to navigate the intricate landscape of regulatory compliance needed to provide safe and effective medicines while optimising their operational processes.
As the pharmaceutical industry navigates an increasingly complex regulatory landscape, ensuring the compliance of purified water production on-site, has become paramount. Stringent standards set forth by pharmacopoeias worldwide demand unwavering adherence to purity and quality benchmarks, presenting significant challenges for small-scale production facilities, laboratories engaged in scale-up processes, and research and development institutes. These challenges stem from their limited space, resources and fluctuating water demands.
Implementing and maintaining compendial water systems that meet regulatory requirements can be resource-intensive and costly, particularly for facilities with limited budgets and personnel. One of the main hurdles is ensuring consistent water quality and microbial control, which can be difficult due to stagnant water, frequent start-stop cycles, and the complexities of designing and maintaining efficient piping and distribution systems within space constraints.
Additionally, validating and monitoring these systems to comply with evolving regulations can strain resources. Training and retaining personnel with the necessary expertise to operate and maintain compendial water systems is another challenge, especially in smaller organisations with
high staff turnover. Addressing these challenges requires careful planning, efficient water purification strategies tailored to specific needs, and effective resource allocation to ensure regulatory compliance and meet production demands.
The next-generation Ionpro™ solution Recognising these critical needs, Veolia Water Technologies has developed the next-generation Ionpro™ system, a comprehensive and innovative solution tailored to address the different requirements of compendial water compliance. Thanks to its new design, Ionpro offers enhanced management and control of consumption during production while retaining its compact and portable appearance.
t Ionpro is prefabricated and housed in a single cabinet. This compact system combines four technologies such as a softener, carbon filter, reverse osmosis (RO) technology and a pharmaceutically certified electrodeionisation
module (EDI). Thanks to its plug-and-play design, it can be connected directly to the main tap water supply on site, to produce high-purity, bacteriafree water.
t Ionpro is flexible due to its different models allowing the production of between 570 and 1000 l/h of high-purity water but also due to its eight options allowing, for example, the addition of a carbon dioxide (CO2) membrane deaerator.
t Ionpro features enhanced control with the addition of an emergency stop button, a new RO40 controller and a 7” HMI screen compatible with Veolia's Hubgrade digital solution. These new features have been developed to ensure better management of water consumption and enable the system’s energy consumption to be anticipated and controlled.
Hubgrade digital services meeting customer challenges in the water industry
Hubgrade is a digital solution combined with Veolia’s human expertise that ensures compliance, operational excellence and sustainability of the water treatment process in a convenient, secure and resilient way. The three innovative services of this data management solution:
t Evaluate and continuously follow the quality of the service and communicate with transparency.
t Measure and improve performance and guarantee a quality level of service.
t Accompany clients in their progress plans and remotely advise in the piloting of their facilities.
One product for several applications. Ionpro™ produces pure water that meets pharmacopoeia standards, making it suitable for other pharmaceutical applications such as laboratory use, for example. This level of purity is also of interest to other markets such as cosmetics or, more widely, the microelectronics industries.
www.veoliawatertechnologies.co.uk
We are a leading provider of pumps, power equipment, and fluid handling solutions to a wide range of industries throughout the UK and export markets. Our expertise extends to manufacturing and selling pressure washers, pumping systems, and component assemblies. With a deep understanding of our products and a network of industry experts, we can cater to the specific needs of our customers.
We are recognised as offering exceptional service, characterised by speed, accuracy, & flexibility. Our customers can count on us for support & assistance, allowing them to focus on serving their clients.
We value open communication and respect in all our interactions and strive to be helpful, personable, and friendly. We take responsibility for our actions and always follow through on our commitments.
With over 48 years in the industry, a dedicated team, and our own warehouse, production, and testing facilities, we are well-equipped to meet the demands of our partners and stock a wide range of quality products.
Located in Melton Mowbray, Leicestershire, in the heart of the East Midlands, we have good transport links and offer next-day delivery to most of the UK. Good access to East Midlands, Birmingham, and London Stansted international airports enables easy travelling for overseas visitors.
We pride ourselves on long-lasting relationships with our customers and suppliers built on trust and excellent service
t Customer Care & Sales team are ready to take your orders and help with enquiries.
t Technical experts to offer advice.
t Dedicated export sales advisor for European and international export matters.
t Dual Pumps has a proud tradition of long-serving staff.
t 99% of customers surveyed, rated our service as good or excellent.
t In a typical month, 99% of more than 2,400 calls are answered within a minute.
t More than 96% orders fill on active products over a typical monthly period.
Our experienced distribution team ensures you and your customer’s consignments are despatched securely and on time
Unrivalled stocks are ready for your choice of delivery. Optional plain cover delivery direct to your customer.
Our purchasing team liaises with suppliers daily, placing orders and negotiating the best possible prices
The warehouse team receives daily deliveries from suppliers and replenishment of stock is constant.
T +44 (0)1664 567226 info@dualpumps.co.uk www.dualpumps.co.uk
We’re excited to be launching a brand new GB Domestic Hours feature into our award-winning app...
Here at CheckedSafe, the UK’s leading provider of vehicle compliance and fleet management solutions, we are proud to be launching a new feature of our multi-awardwinning fleet management system: a new GB Domestic Hours tracking feature.
This latest addition to our Software-as-a-Service (SaaS) platform is designed to keep fleet operations within the legal boundaries of the Drivers’ Hours Legislation and the Working Time Directive.
While we’ve still got this feature under wraps for now, we’re expecting to launch this new venture at the end of July/early August…
So keep your eyes peeled for updates!
How we’re helping you comply with the Working Time Directive
In the UK, operators and drivers of goods vehicles, buses and coaches, are mandated by law to maintain precise records of working hours. This requirement, crucial for both safety and regulatory compliance, can often be cumbersome due to its paper-based tracking system.
Our new development simplifies this process by providing real-time alerts on any infringements, allowing for immediate corrective actions. This proactive approach ensures that drivers adhere to legislative requirements which govern the
hours drivers can operate and the necessary breaks, thereby reducing the risk of penalties and enhancing road safety.
Notably, the new feature will be an extension of our existing fleet management platform but can also operate independently.
It offers a comprehensive dashboard built into their current app, that allows fleet managers to:
t Ensure full legal compliance with the Working Time Directive
t Eliminate the need for cumbersome paper records
t Manage driver fatigue and mandatory rest periods effectively
t Generate detailed reports on driver hours at the click of a button
However, innovation is nothing new for us here at CheckedSafe. This development to our SaaS platform follows last year’s advancements in providing driving licence checks
The future looks bright…
As we continue to expand our suite of compliance and management solutions, our team remain dedicated to their original mission of revolutionising the fleet management industry through technology, simplicity and innovation.
Co-founder and Director, Gary Hawthorne, comments, “Ultimately, what we’re doing is making the roads safer
places to be. Whether that’s by changing driver behaviour or ensuring fleet operators are compliant with legislation. We exist to make life safer and simpler.
“Our software is used by thousands of vehicles throughout the UK, and we’ve absolutely no intention of things slowing down. However, it doesn’t escape us that in order to stay at the forefront of fleet management technology, it’s important that we’re continually improving and innovating. This makes sure our clients are equipped with the best suite of tools to manage their fleets effectively.”
So, for fleets looking to modernise their operations and ensure stringent compliance with UK laws, here at CheckedSafe, we offer a comprehensive, robust app and portal that meets not only current needs but is constantly adapting to future challenges and regulations within the transportation sector.
Keep your eyes peeled for updates and register your interest at by emailing us at: info@checkedsafe.com
Alternatively, get in touch with us on 01282 937228 or drop us a message here if you have any questions!
In this issue of Industry Update, we are delighted to welcome CH Materials Ltd as our Passive Fire Protection Solution Company of the Month
CH Materials Ltd is a leading supplier of high-quality industry materials and products to the Passive Fire Protection sector, with premium products including: intumescent materials for manufacture of fire stopping devices, thermal protection tapes and accessories for fire rated doors, glazing and ducting applications.
Established in 2005, the Lancaster company became part of the svt group of companies in 2022, which supplies passive fire protection products for the construction, rail, air and marine transportation sectors. svt is also known as a heavyweight expert in battery safety, notably fire protection. With an upgraded office and warehouse space, the team at CH Materials have built up a large loyal customer base over the years across the UK.
CH Materials prides itself on offering rigorously tested products, built on meticulous product design and industry expertise, dating back years. The resident R&D team are well placed to offer expert advice on products through application, testing and product insulation and integrity characteristics. To prepare for certification, indicative fire tests can be conducted on doors, facades, glazing, partitions and more at the company’s test sites and customers can also request fully certified testing and final external accreditation.
This year’s Fire Safety Event was the perfect place to showcase the range of passive fire protection solutions and leading intumescent products, with the Flamro range proving to be one of the stars of the event.
The Flamro range of structural passive fire protection solutions have been perfected over a thirty-year period for a wide range of applications such as: cable and pipe penetration seals, linear joint seals, cable protection and ducting.
“We offer high quality fire protection products that meet high specifications and the bespoke needs of our customers. We work closely with our customers to improve and make their products the best they can be and with prospective customers to develop new and innovative products to add to their PFP portfolio.
“We are looking for partners with a knowledge of and passion for the passive fire protection market. The Flamro product range offers new and innovative solutions for penetration seals and cable protection. We believe building strong relationships with our clients is key to success in this area.
“svt are already one of mainland Europe’s major players in passive fire protection, the plans are to grow our ever-expanding portfolio of passive fire protection products into our existing and emerging markets.
“The depth of knowledge and expertise available through the wider svt Group is exceptional and, in our opinion, second to none. We are available to provide advice on a huge range of materials to help ensure you have the information available to develop your product range to offer innovative and competitive solutions,” outlined Corinn Sobczak, Technical Sales Manager.
See CH Materials at The Fire Safety Event 2025: 8-10 April 2025 – NEC Birmingham
To find out more about these leading passive fire protection solutions, see the details below: T 01524 406088 www.chmaterials.com
Access Platforms are indispensable for working at heights or hard-to-reach places, providing workers with a robust structure across many industrial sectors. Many essential services such as air conditioning units, pipes, and ductwork are often stored high in the roof and access platforms are key to installation and essential repairs/maintenance throughout the year. With health & safety in mind, the steady, well-fabricated structures give extra reassurance to workers, throughout the operation period.
Independent Access Sales (IAS) is a relatively new company but with decades of expertise behind it. Established in 2020 by Managing Director, Richard Martin, the Huntingdon-based company is set to take the country by storm.
IAS is a distributor of access platforms across the UK and Ireland and Richard brings more than 35 years of industry experience, from scaffolding, cradle platforms, erection, surveyor, to supervisor, “We are getting noticed now across the industry. We have won three awards in the last twelve months, including a Golden Award from Media2. We’ve been to numerous trade shows and generated a lot of interest.”
“We are excited to reveal that we have exclusively signed with SOCAGE, producer of globally-leading aerial platforms, to distribute their truck-mounted platforms, up to 100 metres. A truck-mounted platform is a mobile elevating platform, which can be attached to a roadlicenced chassis and is great when you require an access
platform to be adaptable, as it can be switched from site to site easily. We are looking forward to adding this to our growing portfolio and by the New Year, expect to be selling a wider range of Easylift Spider Platforms, SOCAGE
Truck Mounting Platforms and Leonardo HD by Bravi HD to new and existing customers across: facilities management, construction, heritage restoration to tree surgery and many more.”
The existing SOCAGE truck line has been flying off the shelves with customers already this year: the SOCAGE 20T carries loads up to 230kg and is a favoured mounted platform for working at height. The SOCAGE 21DJ works up to 20.3m and is a second popular choice for many applications.
For those working in facilities management or heritage restoration, the Easylift srl Piattaforme Aeree R360 provides a turret rotation of 360° for cleaning and delicate work in limited spaces. Designed to work at a height of 35.4m, it is also preferred by tree surgeons for all aspects of arboriculture. The R260 model works to a maximum height of 26m, with an outreach of 13.5m,
precision-designed for maintenance & installation jobs.
The Bravi Platform HD meanwhile is the default choice for tight spaces and doorways, offering a sturdier alternative to scaffolding or ladders.
IAS offers a full consultancy service for new customers, to source the perfect access platform and moving forward, offers six-monthly inspections, servicing and maintenance, meaning you can just get on with the job at hand.
“It is a real pleasure to hear repeat custom across many sectors. We take great pride in customer service, from our expert, technical know-how, to quick lead delivery times.”
“In the near future, we are hoping to begin talks with a dealership of little truck booms. These are ideal for a variety of one-day applications from street work, signage, windfarms to pest control. Look out for our Spring demo road tour round the UK! We look forward to meeting new and existing customers then.”
The company currently has an extensive range of used machinery for interested customers, including: JLG660SJ Articulated Boom, Aerial AL22 Truck Mounted, Multitel MJ201 Truck Mounted and Easylift R180 Spider Platform, please see this link for details: https://iasales.co.uk/used-machines
For more information, or to view the product range, please see the website below or ring Richard Martin: M 07483 246878 enquiries@iasales.co.uk service@iasales.co.uk www.iasales.co.uk
Union Industries, the leading manufacturer of bespoke high-speed industrial doors, has helped LoneStar Leeds Limited, a world-class provider of precision engineered components, sealing technologies and specialised coatings and plating reduce costs and improve efficiency through the triple installation of its Bulldoor.
Union Industries was first approached by LoneStar in 2023 and was subsequently tasked with providing solutions for site enhancement projects at its facilities, primarily on doorways frequently accessed by forklift trucks for deliveries and stock movement. The three Bulldoors were designated for deployment across LoneStar’s two sites in Leeds.
Headquartered in the West Midlands, UK, and employing more than 1,000 people across 13 sites, LoneStar Group has proven itself in global logistics.
It utilises a worldwide network of its own manufacturing and distribution operations, as well as primary supply sources, to supply and support customers in America, Europe, the Middle East, Central and South East Asia and Australia with precision engineered components.
The primary objective was to mitigate heat loss within the premises, thereby reducing energy expenditure and improving the company’s ECG performance. The existing roller shutters and sectional overhead security doors, characterised by slow operational
speeds, often remained open, resulting in substantial heat dissipation and increased energy consumption, especially during harsh weather conditions.
Union Industries developed tailored solutions for each opening, including reducing the opening size of a large doorway to curtail heat loss while maintaining optimal clear opening sizes to suit LoneStar’s requirements.
Additionally, it crafted a door to fit within tight spatial constraints without compromising operational functionality. Importantly, all three doors seamlessly integrated with existing security measures, ensuring comprehensive site security post working hours.
Like other doors in their range, Bulldoor also benefits from Union’s simple yet proven ‘Crash Out and AutoReset’ facility, in case of vehicle impact to the bottom
beam, thus ensuring minimal downtime and repair costs.
Rob Howe, Technical Sales Engineer at Union Industries, said, “We take pride in delivering tailored solutions that address our clients’ unique challenges. The successful installation of our Bulldoors at LoneStar underscores our commitment to innovation, efficiency, and customer satisfaction.”
Gemma Juniper, HR & HSE Manager at LoneStar Leeds, said, “The installation of Union’s doors was a pivotal step in our journey toward environmentally focused improvements across our company portfolio. The comprehensive heat loss payback report highlighted not only the potential cost savings but also the tangible benefits of enhanced energy efficiency.”
T +44 (0)113 244 8393 enquiries@unionindustries.co.uk www.unionindustries.co.uk
Union Industries, the UK’s leading manufacturer of bespoke industrial doors, has utilised virtual reality (VR) to help Leeds-based Met Fab Solutions maintain comfortable working conditions with the installation of a Bulldoor.
Union Industries has successfully deployed its innovative new VR software to assist Met Fab Solutions, a leading UK manufacturer of aluminium panels and aluminium pressings, specify and configure the correct door suited to its needs.
This innovative tool allows Union to immerse prospective clients in a 3D showroom where they can experience their high-speed door offerings and interact with the products in a virtual environment. The software, comprising a VR headset and handheld units representing the customer’s hands, showcases the extensive features, specifications and benefits of Union Industries’ products.
Met Fab’s powder coating facility contains an extraction unit which draws the temperature outside of the building
to keep the area cool during hotter periods. However, when windy, the extraction unit causes a wind-chill resulting in employee discomfort, hence the company’s need for a fast acting and reliable door.
The Bulldoor not only ensures the integrity of Met Fab’s facility but also significantly reduces the impact of adverse weather conditions. Operated conveniently via remote control, the door incorporates a ‘Crash-Out & AutoReset’ feature as a standard safety measure, minimising costs associated with door impacts.
Renowned for their reliability and efficiency, Union Industries’ doors, including the Bulldoor, have become the preferred choice for manufacturers dealing with heat loss and escalating energy prices. With a robust design requiring minimal maintenance, these doors can withstand constant high-volume operations, making them an ideal solution for industrial settings.
Rob Howe, Union Industries’ Technical Sales Engineer, said, “Once again, the Bulldoor is the first choice for those
in the manufacturing industry who aim to address heat loss and wind chill through open doorways.”
“The Bulldoor is one of our best-selling doors and has been developed by our own R&D team over the years to become the reliable workhorse that it is today. Its robust design ensures minimal maintenance and can withstand constant high-volume operations.”
“We are also thrilled with the success of our new virtual reality configuration tool. This software enables us to immerse prospective customers into our world, providing a first-hand experience of the advanced features and capabilities of our rapid roll doors.”
Steve Cockerham, managing director at Met Fab Solutions, said, “The collaboration with Union Industries has proven invaluable in addressing our specific needs.”
“In utilising the VR software, Union was able to demonstrate to us in detail how the Bulldoor was best placed to serve our specific needs and address the challenges we faced.”
“The Bulldoor has not only enhanced the integrity of our facility but has also significantly improved working conditions for our employees.”
Please see our video: www.youtube.com/watch?v=C_pZjPdKGwg&t=4s T +44 (0)113 244 8393 enquiries@unionindustries.co.uk https://unionindustries.co.uk
Got a driver that won’t consent to having their licence checked? Unsure how to tackle the situation? Here at CheckedSafe, we explore your options...
Do you have a driver that won’t consent to having their driving licence checked? Eager to get on the road without the necessary checks being done first?
Let’s take a look at what to do if you’re a fleet operator in these circumstances…
The importance of checking employee driving licences
As a fleet operator, you must check all of your driver’s licences at regular intervals. This means at the outset of employment before they are allowed to drive, and consistently after then – typically at least quarterly.
It is typically advised to take a risk-based approach to this process, which means drivers who have points on their licence should be checked more frequently.
Whatever your stance, your approach to the frequency of conducting driving licence checks must be established in a written policy. This provides full transparency to your team of drivers and also protects your business in the event of questions down the road.
What to do if a driver refuses licence checks
A driver refusing to have checks carried out on their licence poses a problem. Simply put, as an operator, if your drivers are on the road without a valid licence you may face:
t Prosecution and a legal sentence
t Action from the Traffic Commissioner
t Invalidated insurance
It is therefore essential that despite the difficulty of the situation, you do not allow a driver to drive on behalf of your business.
Step 1 – Speak to your driver and explain your legal obligations
The first step in tackling this would typically be to speak to your driver about the legal obligations you face. This would also be a good time to get out your written policy on the topic and explain the consequences of not adhering to the law. It is also advisable to ask them for their reasons for refusing.
Step 2 – Remind the driver they are subject to disciplinary action
If after that initial conversation, your driver still refuses to let you check their driver’s licence –it is time to remind them that must obey any reasonable and lawful management requests, or they will face disciplinary action.
Step 3 – If they still refuse, dismissal is likely
Finally, if they still refuse to participate in mandatory licence checks, you are within your rights as an employer to dismiss the driver (or refuse to work with them, if they are an agency driver). Legally, both ‘illegality’ and a lack of ‘capability’ are potentially fair reasons to dismiss someone during these circumstances.
How can CheckedSafe’s driving licencechecking software help?
At CheckedSafe, our licence-checking software revolutionises how you ensure your fleet drivers are both compliant and hold clean driving records. We use advanced Optical Character Recognition technology which boasts an accuracy rate of over 95% to efficiently verify driver licences remotely.
We make it easy for you to check for:
t Licence types – That your driver’s details are correct and whether or not they have the correct licence for their role (ie. full, copy,
HGV or professional)
t Driver offences – That all previous driver offences have been identified (ie. speeding, drunk driving)
t Points on licence – That the number of points stated on the driver’s licence is correct.
t Tachograph and CPC – The driver’s Tachograph Card and CPC expiry dates.
The benefits of our licence-checking software are as follows:
t Check the driving licences of your entire fleet remotely.
t Retain peace of mind that your business is compliant and safe.
t Create custom data points and personalised alerts.
t Make use of impressive Optical Character Recognition (OCR) technology.
t Easily identify drivers who are at risk within your fleet.
t Minimise the likelihood of you paying expensive fines.
t Stay informed of any new offences from drivers in your fleet.
t Manage your fleet from one streamlined.
t Use our innovative ‘pay-as-you-go’ service to check licences.
Remember, making sure every employee behind the wheel has a current & valid driving licence isn’t just a legal checkbox for you to tick – it is also a key part of managing your operations efficiently, effectively and safely.
If you’d like to learn more about our solution to managing your fleet and ensuring your business is compliant, please give us a call on 01282 908429 or email us at: info@checkedsafe.com
Michael Pasko explores the advantages of employing 420 chrome stainless steel coiled spring pins across diverse applications
Coiled Spring Pins are offered in light, standard and heavy duty to meet applicationspecific requirements
Spirol invented the Coiled Spring Pin in 1948 and they are used in companies developing automotive, medical, heavy equipment, military, aerospace, and consumer products. In applications requiring a combination of high strength, superior fatigue life, and corrosion resistance, 420 martensitic chrome stainless steel offer a host of technical benefits and provides an overall robust costeffective solution.
High strength
Spirol’s 420 stainless steel Coiled Spring Pins are hardened to values approximating their high carbon steel equivalents and share the same minimum rated shear strength. This process also develops desired spring properties and fatigue resistance.
Chrome stainless steel Coiled Pins also offer good corrosion protection against most common atmospheric and environmental conditions without the risk of rapid work hardening associated with 302/304 austenitic stainless steel. In most cases, companies may use 420 chrome stainless steel Coiled Spring Pins as drop-in replacements for high carbon steel pins assuming galvanic potential has been considered relative to the host material.
Corrosion resistance
When companies require corrosion resistant Spring Pins, there are two common options: carbon steel with a sacrificial protective plating or coating or
stainless steel alloys which are inherently corrosion resistant.
Platings and coatings provide excellent performance though they are consumed over time, whereas stainless steel provides a lifetime of protection providing free oxygen is available in the environment (free oxygen allows the fastener’s protective chromium oxide layer to reform if damaged). For plated and coated parts, once the plating or coating is depleted, the carbon steel is left unprotected and rapidly corrodes.
This graph shows how time impacts the corrosion resistance of coated steel compared with stainless steel
420 martensitic chrome stainless steel also provides good corrosion resistance in environments, including, but not limited to, normal atmosphere and humidity, steam, fresh water, alcohol, ammonia, alkalis, mild acids (eg. carbonic), petroleum products such as gasoline, oil, crude, and mild detergents and sterilising solutions.
While 302/304 austenitic stainless steel Coiled Pins provide excellent corrosion protection, this material is not an appropriate solution when the pin will be subject to dynamic loads, or where strength and fatigue resistance must equal or exceed that of high carbon steel. Alternatively, 420 martensitic chrome stainless steel provides an exceptional combination of strength and fatigue resistance – in addition to its inherent corrosion resistance.
420 chrome stainless steel also provides enhanced fatigue life, an important consideration given that Coiled Spring Pins often function as dynamic elements within many applications. A unique characteristic of Coiled Spring Pins is that their flexibility after installation protects host holes and assemblies by dampening vibration and shock loading.
For comparison, Coiled Pins of the same duty (ie. material thickness) produced from material of equal dimensions, were tested in the three standard materials: MBK – a standard duty, high carbon steel, plain finish; MCK – a standard duty, 420 chrome stainless steel, plain finish; and MDK – a standard duty, 300 series austenitic stainless steel, plain finish.
Resultant trend lines demonstrate 420 chrome stainless steels superiority in fatigue when tested at increasing percentages of assigned minimum double shear strength.
Summary
Coiled Spring Pins manufactured from 420 chrome stainless steel are an excellent material choice where high strength, moderate corrosion protection, and superior fatigue life are critical. Additional benefits to consider include cost/benefit relationship in performance applications, high-wear resistance, good tensile and creep strength at moderately elevated temperatures, oxidation and erosion resistance, improved component cleanliness as compared to high carbon steel, and reduced potential for mixed product & debris compared to plated and coated carbon steel product.
Michael Pasko is Applications Engineer at Spirol International.
www.spirol.com
Data for comparative purposes only – conditions in this test do not infer performance benchmarks in any application as varied load, host materials, hole size, and shear plane quality/ clearance will impact performance
The safe laser scanner UAM-05LP offers maximum vewrsatility for safe area monitoring
The Schmersal Group continues to expand its range of products for safe area monitoring: the company is now selling the UAM-05LP safety laser scanner from Japanese manufacturer Hokuyo in Europe, beginning with markets in Germany, France, Austria and Switzerland. The safety scanner is characterised by its extremely compact design and low weight, as well as its flexible integration options and high safety standards. This helps it to ensure maximum personal protection in logistics, manufacturing & the process industry.
Contactless protective devices, such as laser scanners, offer many benefits in the implementation of safety requirements. In contrast to guard fences and guard doors, there is no manual opening and closing requirement, and they do not impede materials transport. In addition, they also enable a clearer view of machinery and processes.
infrared beams to scan the environment and detect the entry of people and objects into the safety zone. This also allows the Hokuyo UAM to achieve a wide range: with a detection range of up to 270°, a safety clearance of up to
The UAM safety laser scanner handles presence control on stationary machinery and robot systems, with the UAM’s sensor utilising
5m and a warning detection area of 20m, the laser scanner can be used in various machinery safety applications.
The laser scanner can be easily configured for
Maintaining a safety shower is crucial for ensuring its optimal performance and effectiveness during emergency situations.
Here are several reasons why maintaining a safety shower is essential:
1) Reliable Emergency Response
Regular maintenance ensures that the safety shower is in proper working condition and ready to be used when needed.
By conducting routine inspections and maintenance activities such as testing water flow, checking water temperature, adjusting controls, and inspecting valves, any potential issues or malfunctions can be identified and addressed promptly, ensuring that the safety shower will function reliably during an emergency.
2) Employee Safety
The primary purpose of a safety shower is to provide immediate decontamination in case of exposure to hazardous substances. Regular maintenance helps ensure that the safety shower delivers the appropriate water flow rate, temperature, and coverage necessary for effective decontamination.
3) Compliance with Regulations
Safety showers are often subject to regulatory requirements and standards that specify their maintenance and inspection. By adhering to these regulations, organizations demonstrate their commitment to compliance and workplace safety.
4) Extended Lifespan
Proper maintenance and care can significantly extend the lifespan of a safety shower. By promptly addressing any
issues, replacing worn-out components, and conducting regular cleaning, you can prevent major breakdowns and costly repairs.
5) Reputation and Employee confidence
Demonstrating a commitment to maintaining safety showers indicates a strong safety culture within an organization. Regular maintenance instils employee confidence in the workplace safety measures and shows that their wellbeing is a top priority.
Conclusion
Maintaining a safety shower is essential for its reliable performance, employee safety, regulatory compliance, and overall operational readiness. Regular maintenance and inspections help identify and address any issues promptly, ensuring that the safety shower is always ready for use during emergencies.
For more information on service and maintenance, please contact Aqua Safety Showers on: +44 (0)1942 318096 or sales@aqua-safety.com
a wide range of uses and also has the ability to monitor two hazardous areas at the same time, eg. two adjacent robots. Each of the two safety zones switches its own OSSD output.
Furthermore, the safety laser scanner is also able to undertake access control as well as arm and hand protection for safety-critical areas in work zones, eg. as part of insertion and assembly workflows.
Another advantage of the Hokuyo laser scanner is its encoder input: with the help of encoders, the speed and direction of travel of automated guided vehicles (AGVs) are transferred to the laser scanner, so that the safety zones can be dynamically adjusted to stop the AGV in case of danger.
The Hokuyo UAM-05LP is suitable for use in machinery safety applications up to PL d, Cat. 3 in accordance with EN ISO 13849 and SIL 2 in accordance with IEC 61508.
Contact: Steve Watkins, Marketing Manager T 01684 571987 swatkins@schmersal.com www.schmersal.co.uk
ABB Robotics announced it is collaborating with UK-based tech start-up AUAR, to advance the use of robotic micro-factories to build affordable, sustainable low energy timber homes.
AUAR’s transformative approach to integrating robotic automation into the building process will tackle skills shortages, boost sustainability, and improve health and safety by deploying robots in a global network of local micro-factories. These micro-factories will construct energy-efficient, affordable buildings from sheet timber. AUAR reports today that it has completed a £2.6 million seed round led by deep-tech and AI fund Miles Ahead, alongside ABB Robotics & Automation Ventures and several other investors.
“The increasing capabilities of robots enabled by vision and AI, coupled with their inherent speed, flexibility and consistency, makes them the ideal solution for meeting the growing need for affordable, high quality, sustainable housing,” said Craig McDonnell, Managing Director Business Line Industries, ABB Robotics. “With 95%* of building firms in our recent market survey describing sustainability as ‘important’ or ‘very important’ to their businesses, and 38%* seeing robots as a
way of reducing waste, our collaboration with AUAR opens new possibilities for homebuilders to deliver affordable sustainable homes at scale.”
ABB is already heavily involved in helping construction companies automate their processes. ABB robots are widely used in a range of modular assembly and 3D printing building projects worldwide, as well as academic projects researching new ways to integrate robotic automation into construction.
The collaboration with AUAR follows the announcement by ABB working with German management consulting firm, Porsche Consulting, to develop innovative new practices in modular housing manufacture. go.abb/robotics
*ABB Robotics global market survey, 2023
The Water Fittings market for PE pipes is a very mature market in the UK and is well served by a few old established companies. Therefore, to succeed, a big new player needs to have superior products, a massive investment in stock on the ground, a total commitment to customer needs and success.
You can now buy Plas-fit UK products in almost every corner of the country, with our attentive operation backed up by our centrally located warehouse in Stoke-On-Trent, assuring reliable next-day delivery.
Abitumen tape wrap system from Winn & Coales (Denso) Ltd was utilised for the repair of damaged pipework at the new HS2 terminus at London Euston train station.
Following damage to the existing factory coating, corrosion had already begun to inflict damage upon the pipe and had propagated underneath the coating itself, causing it to delaminate. To eliminate further damage, the Denso™ Bitumen Tape Wrap System was applied to not only protect the pipe from the effects of further corrosion, but to provide a large degree of mechanical protection too.
Winn & Coales (Denso) Ltd are leading manufacturers and suppliers of corrosion prevention and sealing systems. The bitumen tape wrap system supplied for the project was
comprised of a bitumen-based primer (Denso Primer D ), a heavy-duty PVC-backed bitumen tape (Densoclad 70™ Tape), and a protective outerwrap (Denso™ Glass Outerwrap). The protective outerwrap offers exceptional mechanical and impact strength for buried pipes exposed to aggressive backfill conditions. Once applied and fully cured, the whole system provides a long-term protective coating that is ready for immediate service.
T 020 8670 7511 mail@denso.net www.denso.net
Blocked rising mains often lead to considerable problems, and if there is no access to the rising main, this usually means increased effort.
What would it be like to have access to the rising main without manholes?
That’s exactly what happened last November, when we, at Plas-fit UK Ltd. had launched our highly respected top-quality range of WRAS approved fittings. Until recently sold successfully in Germany and the Netherlands, and now quickly building a great reputation in the UK amongst merchants and installers alike.
Have a look online plas-fit. co.uk at our range of highest quality products, or better still, pick up one of the Plas-fit UK fittings and see and feel the difference yourself. You’ll find us to be reliable & good people to do business with, so let’s talk.
T 01782 894912
office@plas-fit.co.uk www.plas-fit.co.uk
With the Quick-Pig system, you can do all this from the top of the ground.
t Inspect your wastewater pressure pipe without degassing the manhole and personal protective equipment – thanks to the launcher that is integrated into your pipe during normal day-to-day operations t Cleaning (pigging & flushing) t Camera inspection (from OD
140mm)
t Protection of employees from hazards in the manhole (health & safety) t and much more...
The Quick-Pig system is an established system in Germany & Switzerland.
The first trial is also underway in the UK and will also ensure greater safety in your rising main.
Because prevention is always better than having the problem in your line.
Contact person: Nico Hindriks, Area Sales Manager T +49 5921 8347-883
nico.hindriks@reinert-ritz.de www.quick-pig.com
The future of a printing industry forged by its past
It’s easy to take the printing industry for granted, so here’s something to consider. When we talk about the technological evolution of the human race, we tend to measure it in terms of the journey from one of two key moments: the start of the Industrial Revolution, and the invention of the Printing Press (in 1436 by Johannes Gutenberg, in case you were wondering).
Print has been changing the world ever since. And we imagine that ever since Johannes first worked out that a roomful of monks slaving over manuscripts probably wasn’t the fastest way to spread the word, people have been looking to the future of print.
Industry evolution was slow at first. It wasn’t until the late 19th Century that print took its next great leap, with the invention of lithography (or offset printing) which dramatically cut the cost, improved the quality and boosted the consistency of print.
Innovation accelerated rapidly over the following century. But where will it take us next?
On demand in demand
If we look at the shift in our client profile over the past few years, it’s safe to say that the most profound is in the growth of print on demand businesses.
Print on demand gives customers the print they need fast, but that inevitably places greater pressure on the print business and its suppliers to operate in an agile way. Hook everything up in a streamlined way, and on demand means the business needs to carry less stock, which means reduced need for storage, lower operating costs and less waste. Set up times are minimised. Short print runs become much easier to a) do and b) make profitable.
Better still, print on demand enables a print business to adapt its tactics quickly, which makes responding to a changing market much easier. Of all printing industry trends we can expect to shape the next few years, this is perhaps the one likely to have the biggest impact on business.
Intelligent application of AI It’s not news to announce that AI will play a growing
role in print. It’s set to play a growing role in everything. What is perhaps a little more refreshing is that, unlike in many industries, the predictions for AI in print are a little more realistic. Take AI’s role in the future of print industry production, for example.
The suggestion isn’t that AI will take over the world. But it will do things that make print companies more efficient, keep production humming, and remove some of the more laborious tasks.
AI has a big role to play in maintenance optimisation, for example, predicting maintenance needs so there’s less chance of a breakdown when you can least afford it. It’s likely to play a larger role in workflow automation, streamlining workflows in the most efficient way.
And AI has a big role to play in ensuring the quality and consistency of print projects – from clarity and sharpness to colour balancing – is on point.
A sustainable future
Not so long ago, the future of a print industry that relied on lots of natural resources and not very eco-friendly solvents didn’t feel particularly encouraging.
As the world shifted to digital and realised the full extent of the climate emergency, there was a worry that print would be left behind. Of course, that didn’t happen. One of the reasons for that is that print changed.
Now, when we look to the future, print industries can point to the increasing use of water-based inks, the reduction in solvents, the growth in recycled print materials and the way print equipment has changed to optimise energy use.
We’d argue that the world was always going to need physical print. But there’s no doubt that the ongoing efforts to create a more sustainable future is making the decision to use print a much easier one for carbon-conscious clients.
Making print more personal
It’s perhaps more of a data trend than a print one, but as marketing becomes more personal, with evermore granular use of data, so the outcome of
that is a shift to printing products featuring not just individual names, but which are personalised with images and text. It’s all part of using print to find new ways to engage in a deeper way with consumers.
Secure print
The future of printing technology is smart. Take security for example. With a digital signature or code printed onto your products and stored in blockchain, end users need only scan the code to verify authenticity.
Already in use in academia (for example, on exam papers), and product labelling, there’s much wider potential in tackling counterfeits.
Erasable ink
Why, in an article on the future of printing technology and processes, are we featuring tech that’s a good ten years old? Well, it’s because erasable print may have been around for a decade, but it’s remained on the fringes.
It certainly sounded like the stuff of spy movies. Print your document and, if you don’t like the results (or you need to hide the results from SPECTRE) run it through the printer again where a heat plate will wipe the ink, leaving you with an almost blank page.
To date, the issue has been that word ‘almost’. The ability to reuse paper up to five times has been somewhat offset by the fact that the erased print wasn’t always entirely invisible, which could lead to some fairly messy looking documents.
As tech improves, however, it’s still possible that erasable print may become part of the future of print, helping to cut waste and costs.
Talk to Soyang
How will the future of the printing industry directly impact you business’ future? To explore how the latest technology and materials could support you, talk to Soyang
Contact T +44 (0)161 765 3400 sales@soyang.co.uk https://soyang.co.uk
Soyang Europe has been working with Reconomy to offer customers access to environmentally focused and responsible waste management services.
International circular economy specialist Reconomy has revealed how its relationship with wide-format and superwide-format media manufacturer and distributor Soyang Europe is helping UK print service providers to improve their environmental credentials.
Reconomy combines technology and skills to enable businesses to better manage their resources, helping to reduce waste, optimise their supply chains, and contribute in a meaningful way towards the circular economy.
While this involves working directly with print companies, Reconomy is also partnered with several leading manufacturers and distributors, supporting their customers with textile waste management. One such partnership is with Soyang Europe, whereby printers using materials from Soyang Europe can responsibly dispose of their waste.
This partnership came about three years ago with the support of FESPA UK. Reconomy was working on various sustainability initiatives with FESPA, while Soyang Europe is a long-term member of the association.
The process works with Reconomy providing customers with a baler to prepare their textile waste. Soyang Europe then collects the bales when delivering new products to customers, with the waste taken to its facility in Altham in Lancashire ready for bulk collection and transportation to a recycling facility for processing.
“It was a perfect fit,” said Reconomy Director, Jon Hutton. “Soyang has always been proactive in wanting to offer their customers, and the wider industry, waste management solutions for their products.
“Sustainability is a hot topic for several reasons. Brands and consumers are looking down the supply chain for environmental credentials, so it’s therefore a driving factor in how to not only maintain and gain business, but how a printer positions themselves for the long term.”
Mark Mashiter, Managing Director at Soyang Europe, added, “It provides our customers with an outlet for their waste. This works well with local customers when we deliver orders to them; we can bring any textile bales back with us and store them in our yard until they are collected.”
Originally, Reconomy had sourced a solution for recycling PVC banner and polyester fabrics at a UK site, whereby waste was blended with other polymers to produce low grade products. While this process ended when more desirable material became available to the market, a recovery route was soon set up and, with the support of Wheeldon Brothers, waste could now be diverted from landfill to renewable energy.
Reconomy combines technology and skills to enable businesses to better manage their resources, helping to reduce waste, optimise their supply chains, and contribute towards the circular economy
However, recycling has since been reestablished and material is again being used in manufacturing processes. Coupled with its use for renewable energy, all of this is helping work towards a circular economy.
An additional benefit to the service is that Soyang Europe is willing to take other supplier’s waste textiles along with its own. This option is available to customers using their own transport within a set radius of Soyang Europe’s facility and when making deliveries.
“Soyang Europe wants to be part of the environmental solution and not the problem,” Jon said. “The take-back scheme provides a platform for printers to demonstrate their sustainability by providing customers with an outlet for their recycling waste.
“Several customers have engaged with Reconomy further and are now collecting their own clients’ end-of-campaign textiles, integrating this with the collection of their materials. All loads are tracked, and Certificates of Recycling can be issued once the material has been processed.”
The work does not stop here for Reconomy, with Jon saying the company will continue to work with Soyang Europe, FESPA UK and its wider membership base to provide more sustainable solutions to the UK industry.
“It’s our aim to continue to be a driving force in educating the industry on the importance of recycling and developing circular economies,” Jon said. “This, with the continued support of Soyang Europe, will ensure more customers take up this service.”
T +44 (0)161 765 3400 sales@soyang.co.uk https://soyang.co.uk
Here we discuss the rise in demand for personalisation, the subsequent rise of DTF technology, and some of the applications it can be used for
Personalisation has been one of the stand-out trends in the print industry for some time now, offering customers the opportunity to create unique pieces and put their own stamp on products.
While more demand is always welcome news for print businesses, it can create some headaches in terms of having the capacity to continue to create quality work, time after time. This is especially true when it comes to personalisation and the many different designs, fonts and colours that come with it.
With this in mind, how do you ensure that you can produce quality work in a quick and cost-effective manner? One method that has increased in popularity in recent years is direct-to-film, or DTF if you would rather, which transfers print onto a range of substrates using a heat press mechanism.
You only need to look at what some of the major manufacturers are doing in this sector to see how popular the technology is becoming. Take Mimaki for example; just last year, the company released its new Mimaki TxF300-75, a production DTF printer, which is built on the same stability & functionality of the TxF150-75, its first DTF printer that launched a few months prior.
But why is the Mimaki TxF300-75, and indeed its sister machine – with well over 300 sales to date – so popular with printing companies around the world, especially when it comes to personalised print? What is it about DTF machines that makes them such a solid choice for this type of work?
First and foremost, the TxF300-75 is an incredibly cost-effective way of producing all sorts of printed pieces, be them personalised or standard. The relatively low costs of film and inks will stand print companies in good stead if they are looking to make a go of personalised print, allowing them to maximise profit on each job.
There is also the fact that the TxF300-75 is capable of producing highly accurate
and quality work, repeatedly, thanks to a top print resolution of 1,440dpi. Other built-in features also help users to achieve high accuracy such as a degassed ink pack, which lowers the risk of poor ink ejection, as well as a Nozzle Check Unit and Nozzle Recovery System, both allowing for stable, uninterrupted print production.
Such is the attention to detail and ability to produce high-quality output that some print service providers are now using the Mimaki TxF300-75 to create custom designs that look like they have been embroidered. Of course, there will always be a place for old-fashioned embroidery in personalisation but being able to offer customers a similar end result, for a cheaper price, will only help to bring in more work.
polyester, and dark coloured fabrics – all in widths of up to 810mm.
DTF also typically offers a wider colour gamut than other types of printing. As such, you can offer customers a greater choice when it comes to colour for personalised work and open up more options for them. This is certainly the case with the TxF300-75, which offers users the very much sought-after white ink option. In addition, the machine features a built-in ink circulation system to prevent white ink clogging, thereby further enhancing ease of production.
It is also important to remember that it is not only the design that differs on personalised printed work. To maximise the reach of your services, you need to be offering a wide range of options to customers, rather than just a handful of personalised products. With the TxF300-75, the machine can handle all manner of fabric such as cotton, mixed fabric,
What is more, customers who run the TxF300-75 can also respond to rising customer demand for more sustainable printed work. The machine prints directly onto DTF film using Mimaki’s PHT50 pigment inks, which are ECOPASSPORT certified, validating their lower environmental impact and meeting the requirements for OEKO-TEX certification.
Of course, working with a quality printer can only get you so far; you also need reliable substrates to ensure success in personalised print. With this in mind, Soyang Europe will soon add a new DTF film to its range of solutions.
Available to purchase from early July, customers can combine this specialist film with the leading qualities of the Mimaki printer to produce high-quality personalised print for customers across a range of markets.
If you would like to learn more or see the technology in action, please email: hardware@soyang.co.uk