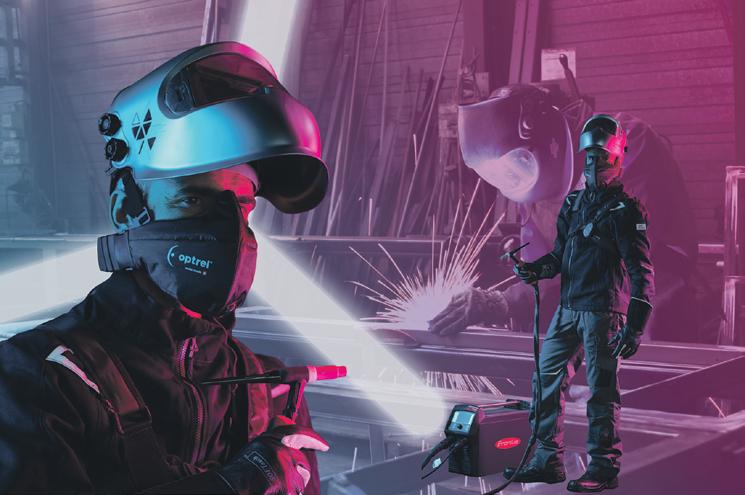
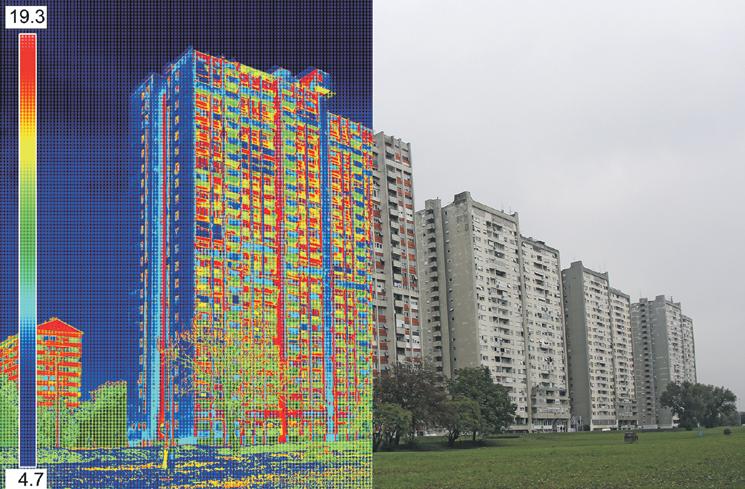

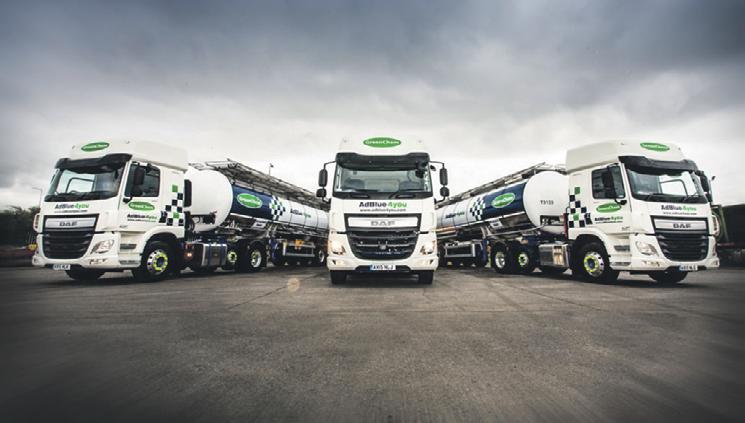

load cells are used
by calibration houses as calibration reference devices. Our highquality, yet competitively priced 3 and 6 axis load cells are used for many R&D, renewable energy and robotic applications.”
In terms of recent developments, Tony continued, “Being responsive to our customer’s needs and being able to offer a high-quality product with strong product knowledge at a competitive price with the best possible lead times is our number one priority. Last year we launched our range of G-Series Load Cells. The range comprises of miniature and small sensors for industrial applications, with capacities starting from just 4.5N Newton up to 200kN with metric threads. These are high-performance devices but aimed at more cost-conscious applications. This is a new market for us, but we have already had increasing interest. We also launched our brand-new e-commerce website on the 1st of April for the G-Series that showcases Interface load cells at competitive prices with all the convenience purchasing online offers,” stated Tony.
The new e-commerce website offers G-Series load cells on short lead times with next business day delivery for small quantities. Following its successful launch in 2021, it has become an increasingly popular product range for students, industrial engineers, OEMs and anyone requiring a small form force sensor offering accuracy, repeatability and Interface quality.
In the future, Interface is keen to continue its growth trajectory for 2022. Tony mentioned, “we are also working on new, wireless force and vibration sensors for remote monitoring in
systems such as luggage carousels. One more area we are pushing for growth is with XSensor’s pressure mapping systems, particularly in the Hi-speed systems designed for high-speed impact or crash testing and tire foot-print research. These systems are capable of capturing data up to 2,500
I
to the
As the company looks to continue strengthening its position with its customers in its more traditional markets of aerospace, automotive, motorsport, Universities and alternative energy research, it will be attending some expos over the next 12 months and be readily on hand to discuss any questions you may have about force, torque, pressure mapping or pressure, level & temperature measurement.
These expos include Instrumentation, Analysis & Testing Exhibition on the 16th of May 2023 at Silverstone Wing, Silverstone Race Circuit Manufacturing & Engineering at the NEC, Birmingham 7th & 8th June, Stand H48
Automotive Test Expo, Messe, Stuttgart, Germany 12th to 15th June and Advanced Engineering 1st & 2nd November 2023 Stand P172 also at the NEC, Birmingham.
Contact T 01344 776666 info@interface.uk.com www.interfaceforce.co.uk
TYDE is excited to announce the launch of their new range of Dudley ‘Victoria’ Outlet Valves.
Along with an improved version of the Dudley cable operated Victoria Valve, the all-new Mechanical Dual Flush Victoria Outlet Valve is now available to be ordered from TYDE’s production centre located in the heart of the Midlands.
The new Victoria Valves are both WRAS
Oliver Hydcovalves have announced the design and manufacture of three new valves for hydrogen transportation and refuelling. Using high performance polymer bearings and seals in partnership with DuPont™, valves have been qualification tested to 102,000 cycles of operation while maintaining a fugitive emissions leakage class of BH.
Another unique feature of the valves is their full-bore design. This avoids restrictive flow, which appears to be a common problem in many valves on the market. Nick Howard, Engineering Director at Oliver Hydcovalves stated; “By maximising the flow rate, it will deliver a more continuous and consistent flow of hydrogen medium. This will allow for hydrogen fuel to be dispensed and refilled onsite much more quickly, which will deliver dramatic time-saving benefits.”
As the world continues to move towards sustainable energy sources, hydrogen is emerging as the promising fuel option for vehicles and industrial transportation on land, sea, and air. The transporting and dispensing of hydrogen fuel in working environments such as fuel stations and onsite fuel storage facilities, require specialist valves that have been designed and engineered for continuous high cycle operative use and meet the requirements of ISO 19880-3.
When dispensing hydrogen fuel onsite, it generally requires a large area to be closed off while in progress, and can even involve a whole site closure, dependent on size of area. Therefore, the time it takes to dispense hydrogen fuel is crucial. Oliver’s full-bore valves deliver hydrogen much faster than other transportation valves that have a restrictive flow. This significantly reduces the downtime at a site, and in most cases, can be halved - minimising disruption to the forecourt and business operations.
Hydrogen fuel is stored and transported using pressurised tanks. Therefore, it's of paramount importance that valves can handle extreme pressures too. Since 1979, Oliver has been synonymous with valve safety and reliability, even relied upon by the world’s largest energy producers, suppliers, and end-users for its precision engineered solutions. As Oliver’s company mantra suggests ‘Reliability Under Pressure’, they’re well-positioned to provide the necessary assurances required.
This latest engineering achievement firmly places Oliver Hydcovalves at the forefront for hydrogen transportation valves. Built to the highest specifications using premium quality materials, and tested to the highest standards, it’s logical to see how Oliver’s claim to offer the best valve solution for hydrogen transportation and refuelling applications, certainly holds up.
Bore sizes include; 10mm, 14mm and 20mm. To learn more about hydrogen transportation and for guidance on hydrogen specifications, applications, qualifications and pricing, contact Oliver Hydcovalves on +44 (0) 1565 632636 or visit their website at: www.valves.co.uk
approved and can be serviced in under 5 minutes providing installers with a real time saving advantage. Both of these high-quality Outlet Valves are fitted with long life silicone seals and a choice of button mounting options.
The new Victoria Valves offer Water saving options with full and reduced flush options as standard. For maintenance or replacement, the robust but simple to use bayonet fixing enables the valve body to be quickly and simply removed from the cistern
making the Victoria Valve fast and simple to install and maintain.
The new Dudley Victoria Valves are excellent additions to TYDE’s extensive product range offering both quality and reliability and for peace of mind, the new Victoria Valves come with a 3 year warranty and can be ordered for next day dispatch. Order yours today!
For more information, email us at: info@tyde.co.uk or visit: www. thomasdudley.co.uk/tyde
now, Contractors, Fire Door Inspectors and Building Owners see the real benefit in using FireDNA
Post Grenfell, we saw an opportunity to introduce a new and innovative way of Monitoring Passive Fire Products in the built environment using the latest digital technologies.
FireDNA is cloud-based Software and a Mobile App that
FireDNA
of a mobile device.
FireDNA digitally links everyone in the chain of responsibility and creates a 'Golden Thread' of information across the full product lifecycle from cradle to grave.
There are many benefits in using FireDNA which has been designed and developed to allow;
Manufacturers:
To centrally deliver their certificates, production data, specification PDF’s, installation guidance and 3rd party certification to Main and Sub-Contractors.
Contractors & Installers:
Add installation statements, compliance / competency evidence and installation photos, which once inspected and approved, can be digitally signed-off, and handed over to their customers.
Fire Inspectors: Conduct audits and Inspections quickly and efficiently, which automatically output to detailed MS Word Doc Reports and Excel Spreadsheets. Again with photographs and detailed descriptions of passes, failures, or required remedial works.
Building Owners, Management Teams, FM's and TMO’s: Manage the compliance data and ongoing maintenance and remedial records, updates, and through their Dasboard can also assign onsite teams.
Maintenance Teams: Access work schedules and update the ‘live status’ data once
remedial works are completed.
FireDNA helps to protect the public across all sectors: Residential, Commercial, Education, Healthcare, Retail and
Government, giving peace-of-mind to Tenants and Residents that the passive fire products in their buildings are compliant and safe.
FireDNA in addition:
t Facilitates the Golden Thread of information t Helps to enforce compliance ‘Regulation 38’, and supports the new British Standard for ‘Digital Information Management’ under BS 8644-1 2022
t Supports quarterly inspections of communal doors in residential buildings over 11m covered by Regulation 10
t Improves collaboration and communication between trades
t Creates time and cost savings (up to 70% on Fire Door Inspection & Reporting)
To find out more about how FireDNA can assist
or for more
and
www.fire-dna.com or call
In this issue of Industry Update, we are proud to announce Optrel AG as our PPE safety product manufacturer Company of the Month.
Optrel recently brought to the market a brand-new concept for welding and grinding applications. The Helix CLT, Quattro and 2.5 is the world’s first and only internal slide up welding helmet. Optrel welding helmets are synonymous with precision-driven Swiss quality and are reputed to be the best across the industry and packed innovation and unique technology. Welding often occurs in challenging situations or hard to reach areas. The Helix helmets offer state-of-
the-art panoramic field of vision, and is powered through a rechargeable battery system.
This full integrated hardhat hard hat product has a cuttingedge ergonomic design and IsoFit headgear with a total weight of only 695grams, Helix helmets can be worn for extended periods of time. Manual shade adjustment is no more with the industry only shadetronic technology, which automatically adjusts the shade to the correct level, meaning an end to eye strain, this addition to the Optrel range means they now have the perfect solution to any application that industry may require.
Optrel AG is a world-class manufacturer of active eye protection, powered air respirators, and supplied area products for the global PPE market.
Established in 1986, this Swiss-based Powerhouse was a pioneer in the first auto darkening filters (ADF) and has laid down the blueprint for Auto Darkening welding lenses that have come ever since. They have revolutionised the world of welding helmet protection twofold: by enhanced visibility and reduced risk of serious eye injuries from debris and sparks and indirect exposure to harmful UV/IR radiation from the welding process.
This family-run business, headed by Marco Koch, prides itself on not being a global mass-producer but instead, creating unique, enviable bespoke products. With full ISO 9001 and ISO 14001 quality accreditation, the innovative team offers quality assurance at every level of design innovation.
We caught up with Andy Knott: Sales Manager: United Kingdom, Ireland, Iceland, Australia and New Zealand to find out more,
“Everything that we produce is exclusively world-first: we really do push the boundaries of innovation and design.
Beyond welding helmets, we now support a broad spectrum of sectors from: construction, woodwork, medical, oil and gas, robotics and even sports: skiing and outdoor sports markets.
We recently branched out into the sports sector with auto darkening skiing goggles and sunglasses.
Our latest innovation is called "Swiss Air:" it is the world's first
and only powered air half mask that doesn't require a face-fit test.
This fully independent powered air half mask, is lightweight, shoulder mounted with a 14hr rechargeable USB battery. It is compatible with every face shape, even those for wear glasses or have beards. It meets full TH-3 classification and delivers constant filtered air to the user. Furthermore, it is waterproof and flameproof and fully compatible with all existing PPE. It was recently awarded full Network rail approval and has become a very popular choice within the construction sector.
We are delighted that this product won the 2021 International Red Dot Award for Design and Innovation.
It is the world's first and only fully carbon neutral powered air system, showing our continued commitment to sustainability in product design.”
The
TCT 3SIXTY is the UK's definitive and most influential 3D printing and additive manufacturing event. Registration is now open for the 2023 event taking place in June at the NEC in Birmingham.
In just a few months’ time market leading technology suppliers and large service companies will come together to attend the largest FREE additive manufacturing and 3D printing conference on the planet. Alongside raising awareness and adoption of additive manufacturing and 3D printing, the event is also designed to ensure that attendees develop a complete understanding of the potential of these amazing technologies that will in-turn utilise all stages of the design, engineering and manufacturing process.
This year you can expect to discover new solutions from over 200 technology providers as well as learn from the four stages of world class learning. The event is designed to help you to understand and choose the right applications and the right technology for your organisation. You’ll also have the opportunity to connect with key buyers including Jaguar Land Rover, GSK,
Samsung, Honda, Bespak, Delta Electronics, Unilever, BAE Systems and many more who will be on the lookout to evaluate and invest in 3D printing and additive manufacturing technology.
Some confirmed speakers include Toby Brown –Structural Engineer at JCB, Stefanie Briockwede –Managing Director, AM Division Deutsche Bahn, Professor Moataz Attallah from the University of Birmingham, and many more.
Join over 100 speakers, 5000 attendees and 200 exhibitors at TCT 3SIXTY 2023.
Book your tickets now.
www.tct3sixty.com
This was our second year exhibiting at TCT, with new dates and a shorter exhibition we were a bit unsure how it would affect attendance and opportunity for clients/suppliers to meet.
We had expanded to a new platform of FDM for our business coming from a Resin background and wanted to show that off at the show.
To our surprise the show was better than anticipated, we made more meaningful connections and key potential partnerships. Making the show more than worthwhile and booking next year whilst at the show and doubling our booth size. The attendees of the show were more experienced and focused than the previous year, and it was great to knowledge share with them.
We can clearly see the direction of the TCT show and the way it will be fundamental to the UK 3D additive manufacturing industries. For us this is the main show in our calendar.
EVO 3D is joining Evolution Sales and Marketing to provide a full technology solution for the additive manufacturing industry. EVO 3D is expanding with £250,000 of capital investment. Locations in Exeter and Huddersfield launch in January, creating new jobs and opportunities for innovation. Warehousing and logistics operations will move to a 4,000 sq ft unit in Exeter’s sustainability-focused SkyPark technology centre in January, 2022. Four new jobs are being created. EVO 3D’s new special projects team will also set up in Exeter. Martin Jewell, who founded J-Supplied 3D in 2018 will lead the team, continuing to pioneer innovations in additive manufacturing. Martin said: “The evolution of J-Supplied 3D into EVO 3D means we can focus on innovative additive manufacturing projects like our partnership with Plymouth University and OREC, as well as expanding further into high-value industries like aerospace and automotive.”
EVO 3D sales and marketing has moved to Huddersfield, where it shares space, resource, and experience with Evolution Sales and Marketing. Evolution Sales and Marketing provides a complete package of sales and marketing services in the UK and EMEA for global brands like Cougar Gaming (owned by HEC Group) and Patriot Memory (top 10 company for PC memory worldwide).EVO 3D, formerly J-Supplied 3D, provides end-to-end additive manufacturing solutions for industry, research, marketing, and hobby applications. Clients include the University of Cambridge and Adidas UK.
Contact T 0333 939 8184 Sales@evo3d.co.uk www.evo3d.co.uk
Central Scanning Ltd release a brand-new #HandsOnMetrology hand-held 3D Scanner.
31st January 2023, saw the global release of the Zeiss T-Scan Hawk 2, a lightweight 3D laser scanner designed and manufactured by Zeiss, who are renowned for high accuracy, and repeatable measuring equipment.
The new scanner, weighing less that 1Kg provides a highly portable 3D Scanner that is travel friendly and provides a user-friendly scanning experience working directly within the highly acclaimed Zeiss Quality Suite software. You can scan a highly detailed coin’s or ‘GO BIG’ with the new Satellite mode and scan a whole car.
Data collection, reverse engineering, inspection/ validation of a wide range of objects are where these types of 3D Scanners are used and being highly portable, this increases the applications where this technology can be deployed. Gone are the days when the item has to be bought to the ‘measuring room’. The T-Scan Hawk 2, 3D Scanner can be easily taken to the item, making the process much easier, hence the slogan ‘Take it, Make it’ which is frequently seen alongside the T-Scan Hawk 2.
For more information, see below or come and see us at the TCT 3SIXTY show - stand E39.
info@pro3dshop.com www.pro3dshop.com
Want to find out more about our products and services?
For further information and to see a demonstration, please come and see us at the TCT show on stand L17 WE 3D Scan, We 3D Print, We 3D Care... www.central-scanning.co.uk info@central-scanning.co.uk T 01527 558282
Incremental Engineering Ltd works with SMEs on their adoption of Additive Manufacturing within standard production. The company specialises in using and getting the most from HP MultiJet Fusion (MJF) to produce production components for OEMs and consumers.
In-house services: production Pa12 on HP MJF, full colour CB-PA12 on MJF580, DyeMansion dye and surfacing as well as AMT vapour smoothing / polishing.
Added value services: assembly, threaded inserts, paint, Cerakote (thin coat ceramic paint) and metal plating.
Incremental Engineering will be exhibiting some of the end use components and products that we produce in the UK for OEMs and consumers.
Jerry Sutton will be attending TCT for
Incremental Engineering Ltd and brings 25 years of machine design and build experience with him. He will be available for the duration of the event to discuss and advise on any ongoing projects.
Contact details: www.incrementalengineering.com contact@incrementalengineering.com
Upon gaining understanding of the specific needs, goals and desires of each client and their project, DCON Safety Consultants Limited is dedicated to implementing a design and construction management plan that will meet or exceed these requirements. And, DCON Safety Consultants Limited ensures that there is honesty, integrity, trust and professionalism underpinning every project. Moreover, the company’s services are centred on three delivery principles:
t Maximising Quality: The company implements proven health, safety and wellbeing strategies to help clients achieve high quality and cost-effective work commensurate with the design of their projects.
t Minimising Risk: The company effectively manages design and delivery risk on projects to match each client’s desired risk level profile.
t Managing Compliance: The company relies on its extensive background working on a wide variety of projects to assist clients in developing, monitoring and maintaining compliance performance.
This excellent service would not be possible without the leadership of Diarmuid Condon, a construction industry leader who brings unique perspectives to encourage, support and mentor the abilities of his colleagues. As a construction professional with a surveying background and experience spanning two decades, Diarmuid is emblematic of DCON Safety Consultants Limited’s commitment to providing outstanding services to clients. Diarmuid has contributed his invaluable expertise to over 400 projects over 20 years, with a client list including public sector departments, corporate owners, real estate developers, main contractors, design professionals and infrastructural bodies. With this incredible portfolio, Diarmuid is helping DCON Safety Consultants Limited to become a leader in health and safety consultancy across the construction industry.
Key to DCON Safety Consultants Limited’s services is working as a Project Supervisor for the Design Process and CDM Advisor in various sectors across the Irish construction market. No project is too simple or too complex for the company’s construction safety consultants, all of whom are construction professionals
with an average of 20 years’ experience in the built environment. The ability to maximise this knowledge and skillset means DCON Safety Consultants Limited can generate distinctive and innovative ideas from traditional PSDP service inputs and outputs.
Additionally, DCON Safety Consultants Limited offers planning compliance assurance services. The ability to strategically support a positive planning decision is exclusive to the company. Its Draft Construction Management Plans (DCMP) inform the overall planning, coordination and control of a project from the beginning of construction to completion. The DCMP also safeguards the obligation placed upon a client to produce a safe, functional and financially viable project.
DCON Safety Consultants Limited also provides its main contractor clients with intelligent, practical, and reasonable physical site safety advice to support compliance and good practice adherence. Behavioural safety outcomes inform how the company approaches each solution with the contractor and their supply chain, identifying opportunities for improvement.
To complement this, DCON Safety Consultants Limited can also help with clients’ health and safety strategy. Its holistic and integrated approach can help unlock substantial benefits for clients by providing a structured, objective and SMART framework for full optimisation through the creation of an environment that embraces health, safety and wellbeing.
This means DCON Safety Consultants Limited helps clients to
improve their health, safety and environmental performance; enhance staff satisfaction thanks to improved performance; improve risk management and corporate governance with a clear audit trail; gain confidence from long-term planning, better sustainability and performance; and improve overall corporate reputation, including greater staff satisfaction and a more efficient procurement and supply chain.
Finally, DCON Safety Consultants Limited can offer a safety expert witness service, which is headed by Diarmuid himself. He has extensively supported safetyrelated matters, and is a certified and competent safety professional who will work with clients to identify exactly what kind of safety expert is needed. Then, he will use an extensive network of contacts to recruit the right person to protect clients’ interests.
DCON Safety Consultants Limited’s fantastic service offering and proven track record of offering leading health and safety consultancy services makes the company a worthy winner of our Commitment to Excellence award. Such achievements are proof that DCON Safety Consultants Limited is well-placed to help ensure your safety, health and wellbeing and make your project possible.
If you are interested in finding out more information on DCON Safety Consultants Limited’s full range of excellent services, head to the website or get in touch directly using the contact details below.
T +353 (0)1 611 1556 diarmuid.condon@dconsafety.com www.dconsafety.com
The most detailed predictions yet about how future floods could affect local areas across the UK point to the urgent need for businesses to optimise their site drainage systems, says Lanes Group plc.
Scientists have created a future flood map that has identified flood hotspots likely to emerge as climate change accelerates, making weather more volatile, the BBC has reported.
The research, carried out by Bristol University and flood consultancy Fathom, reveals locations in England, Scotland and Wales that could be hardest hit by flooding over the coming years.
Lanes Group Development Director Richard Leigh said:
“More accurate modelling like this is going to be crucial as we move into an era where volatile weather patterns makes flooding more likely.
“The maps show how a business may be at risk of flooding, while another very close-by may escape the deluge. These predictive tools can help property owners and managers, both residential and commercial, plan their flood defences to prevent damage or minimise it.
“A business at the epicentre of a huge flood event is unlikely to escape being affected. But those on the margins, or where flooding is less intense, can do a lot to protect their premises by ensuring their site drainage systems are working effectively.”
The annual cost of flood damage across the UK currently, according to the Association of British Insurers, is £700m a year.
The researchers have found that annual damage figure
could increase by over 20% over the next century. They created their future flood map by simulating all types of flooding in the coming decades.
Information about terrain, river flow, rainfall patterns and sea level was fed into the model to create the most detailed picture currently possible about how homes and businesses will be affected.
Lanes, the UK’s largest independent wastewater and
drainage specialist, has developed a 6-step check list, which can form a critical element of a site drainage resilience review.
t Know your flood risks
Use all evidence, including this latest research and advice from the Local Flood Authority, to assess the local flood risk, bearing in mind that the level of risk can change over time, depending on factors such as the level of local development.
t Assess your drainage system
Have an accurate and up-to-date site drainage map. Every one of Lanes’ 22 depots can be commissioned to carry out a CCTV site drainage survey to establish the condition of drains and sewers across any premises.
t Carry out planned preventative maintenance (PPM)
In the long-term, preventing flooding is less costly than clearing up after it has occurred. Therefore, having a PPM schedule in place makes the best sense. System cleaning and flushing will reduce the risk of localised flooding disrupting business activities.
t Address site drainage problems
If site drainage problems, such as pooling of water and slow draining of toilets and sinks, are already apparent, deal with them now, and take steps to prevent assets being compromised, for example by wet wipes being flushed down toilets.
t Assess wider drainage issues
Off-site issues may increase flood risks, for example, if a local water course is blocked. Raising these issues with relevant authorities and property owners is an important step.
t Prepare an emergency plan Businesses must also be ready if the worst does happen. Ensuring a site flood response plan is built into business continuity planning is vital.
Having rapid access to a reputable drainage specialist, that has all the expertise and specialist vehicles to deal with flooding problems, could be the difference between an inconvenience and catastrophe.
www.lanesfordrains.co.uk
As much as we don’t want to admit it, modern temperature sensing systems are often the children of compromise. They are usually created after most of design work for the underlying equipment is complete, which means thermal systems must conform to the constraints of the underlying system. As a result, issues not at the forefront of a manufacturer’s mind may emerge. In this article, Jeremy Ohse, staff engineer at industrial heating technology manufacturer Watlow, explains how thermocouples can eliminate these compromises.
Sometimes, budget can limit a temperature sensing system’s potential and companies cannot always get the sensor or heater density they desire. It’s possible to save a lot of money by reducing the number of sensors, but this comes at a cost of losing a complete picture of the entire system.
Space also plays a role. Heaters and sensors take up space, and the wiring that connects them grows with each addition to the system. This ultimately requires more space, which may not be possible in all setups. Companies respond to this issue by wiring their heaters in series, reducing the wiring and space requirements. However, doing so risks removing the ability to fine-tune the system, which creates implications for effectiveness and efficiency.
The danger of these compromises is that they can impact daily operations in ways that are not always apparent at first glance, but rather living in a manufacturer’s blind spot. Companies might be running their heaters too much or too little, with product or quality implications without being aware.
Thermocouple heater (TCH) control
But what if we could live in a world where there is no need to compromise? Creative use of an older technology can make this possible.
Thermocouples are nothing new. Essentially, they consist of two dissimilar conductors forming an electrical junction. The setup is extremely sensitive to temperature changes, which can be measured by the change in voltage that flows through the thermocouple. Watlow is a manufacturer of temperature and process controllers, which has developed thermocouple heater (TCH) control that is significant due to its placement. When integrated into a heater’s power leads, it can provide temperature sensing without needing a discrete sensor.
Without a discrete sensor, there is little need for sensor wires to be run into the system, which saves on cost and space. Plus, they are mounted close or even within the heaters, providing precise measurements in specific locations to present the most complete view of a system’s performance.
How TCH fits into a thermal system
A new temperature sensor is only a small part of the change that is needed in industrial temperature sensing. More advances are necessary to take advantage of the TCH’s space-saving design and in-line temperature sensing capabilities.
For example, Watlow’s Adaptive Thermal Systems® (ATS™) is an edge-to-edge thermal management suite that include the TCH. While the harness that holds wiring for heaters and sensors is not always the first thing we think of when we think of innovation, the harness in ATS is worth highlighting. Featuring a standardized connector, the harness makes it easy to wire different heaters into the same system, and halves the number of connections required.
It’s important to stress that the right solution for an industrial temperature sensor system is never an “off-theshelf” solution. But the wrong custom solution can leave you with blind spots that create significant problems within the application. TCH and ATS enhance each other’s value when combined. As a result, this provides incredible value without breaking the bank and forcing companies to compromise on features that can lead to detrimental issues down the line. Further information is available at: www.watlow.com
There are documented safety issues around medium-voltage process heaters; now considered the popular alternative to gasfired heaters for larger application utilisation. Arc flash events are rare but carry potentially deadly consequences. The new usage of larger mediumvoltage process heaters in hydrocarbon processing have raised a few safety eyebrows.
Flash mitigation features are a key consideration to offset safety risks and prevent serious injuries.
The risks posed by arc flash Thankfully, arc flash events are rare: estimated at 3,500 globally every year but their capacity for serious injury, damage and death must never be underestimated.
The propensity for arc flash events increases when corrosive or conductive dust unexpectedly or negligently builds-up, causing a sudden short circuit. Other causes include pest infestations and even accidentally dropped industrial tools.
Equipment operating at higher voltages (above 600 volts) naturally carries more risk for potential arc flash, whereas those functioning at below 400 volts, will not cause large arch flash events.
Mitigating the risks of arc flash are an essential part of risk assessments, to protect workers and workplaces. Global concerns about carbon emissions, have led many companies to find practical solutions for decarbonisation, such as replacing gas-fired heaters with larger electrical heaters.
Furthermore, many applications are now assembling large
megawatt heaters, connected to multiple panels. This necessitates an engineered solution scenario: isolating the arc flash section and thereby isolating the faults from the main breaker/feeder, to avoid fire and fatalities.
Reducing the effects of an arc flash event
There are three essential strategies to negate the impact of potential arc flashes across industrial equipment:
1. Reduce the available fault current
2. Expand the distance from the potential source of an event
3. Decrease event duration (how long the arc primarily exists)
If money were not object, all three strategies would offer optimal safety but sadly, project costs can make this impractical to implement.
However, the third point has the largest impact on the total energy released and is the most effective way to reduce potential arc flash hazards.
In the debated safety dichotomy between arc-resistant cabinets and arc mitigation technologies: the mitigation technologies are generally considered more cost-effective and ultimately carry a higher safety return.
Therefore, implementing safety mitigation technologies into medium voltage process heater designs, is considered industrial best practice.
Fool proof Arc Flash Mitigation Technologies
Arc flash mitigation technologies work on the premise of reducing the energy of the event itself, by purposefully limiting its duration. This smart technology pre-empts the flash, simultaneously tripping the circuit in question, thus averting further damage. The technology either sensing the
current arc mitigation (current) or the optical arc mitigation (light).
In the latter approach, the arc light is detected and a signal is sent to a protective relay, instantly tripping the breaker autonomously. This has the huge advantageous approach of detecting the arc at its infancy, thus rendering the duration to minimum levels, with the total energy produced dramatically downsized.
Current arc mitigation solutions
Current arc mitigation uses transducers to detect arcinducing current increases. However, if the transducers are incorrectly sized, they are incapable of proactively shutting down the system or clearing the event in a timely fashion.
The optical arc mitigation technology has the sizeable advantage of reducing clearing time and arc energy release by 50%, compared to current transducers.
Safety comes first
The Watlow® POWERSAFE system: designed for medium voltage process heaters, allows for sensors to be placed in the thermal controller, SCR node and/or single contactor node: all protected by a feeder/breaker.
An astonishing 12 heaters can collectively operate from a single feeder/breaker, whilst each individual heater is monitored by a hub/switching circuit node. In the event that the sensors detect an arc flash across any compartment: the feeder/braker will instantly close the line-up, thereby further minimising any arc damage. Further information is available at: www.watlow.com
Foremost Electronics the engineering-led Essex based importer and specialist distributor of electromechanical components, is a key source of supply for machine builders looking for rugged and reliable enclosures, human machine interfaces (HMI) and secure cable entry systems.
Channel partners for the German manufacturer nVent Schroff, Foremost can supply their range of cabinets, desktop enclosures, 19” cabinets, and sub racks. Their wide range of products include rugged, waterproof, modular and user configurable enclosures to suit many
industrial environments.
Just announced is the FIBOX NEO standalone enclosure featuring a modern design with a large viewing area reinforced against impact dust, snow and caustic substances. It is double insulated and has double walled base corners as well as integrated rain canopy.
Available from IDEC, Foremost can supply their wide range of machine safety products including the IDEC X-series E-stops with an exclusive “Safe Break Action” that turns the machine off if a failure occurs within
the E-stop itself. Other products include machine status LED indicator towers and the HT3P SAFETY COMMANDER™ which can convert a tablet computer into an industrial HMI with safety functions.
Comprehensive cable entry products available from icotek include water and dust proof and EMC shielding options as well as modular systems which can accommodate cables with connectors fitted.
For more information call +44 (0)1371 811171, email sales@4most.co.uk or visit www.4most.co.uk
As surgical instrument manufacturers pursue greater throughput while facing increased labor costs, automating the medical instrument manufacturing process has become a necessity. However, integrating automation into the gundrilling process for drilling deep holes in extremely precise surgical instruments in lights-out operation is a major engineering challenge requiring more than simply pairing a robot with a deep-hole drilling machine.
The right machine, tools and process must all come together to create small holes with extreme precision in difficult-tomachine materials such as titanium and surgical stainless steel. More importantly, the entire system must flow from a unified concept where the whole is greater than the sum of its parts.
To meet these challenges, UNISIG developed its UNE6-2i750-CR dual independent spindle gundrilling machine. The UNE6-2i is capable of gundrilling hole diameters ranging from 0.8 – 6 mm in part lengths measuring up to 30 inches with depth-to-diameter ratios from 20:1 to more than 100:1. The machine has a maximum combined drilling speed of 28,000 rpm and a 3,000 psi (207) bar programmable flow-based coolant system with dedicated pumps for each spindle to ensure precise coolant pressure control.
Automating hundreds of cycles of precision manufacturing, however, is not possible unless the overall operation is considered from the outset. Surgical instrument manufacturing is a sequential process: parts must be loaded into the machine in a particular way for specific operations that happen in a specific order.
Workpiece length, shape and configuration determine where it is gripped by the robot when loaded into a machine, moved from spindle to spindle for drilling, residual cutting fluid removed, and returned to the pallet. Where a part is gripped impacts where it is clamped for drilling to ensure accuracy. Every variable along the process chain must be considered and accounted for, and the calculus is detailed and complicated.
Then there are unique customer needs and requirements. The equipment and process must accommodate a variety of part families and hundreds of parts to increase runtime and efficiency. Operators must be able to change over part types and programming without calling in an automation specialist, and the entire process must be controlled from a central interface. Add to the mix that everything must be packaged in as small a footprint as possible, and the scope of the engineering challenge comes into focus.
UNISIG’s approach to solving these problems, however, results in targeted automation that enhances the existing benefits of gundrilling, ensuring a solid foundation for reliable processwide automation.
At its core, the automated UNE6-2i is a purpose-built machine with automation embedded in its design, not added as an afterthought. Flexibility and adaptability are maximized by a harmonious, interdependent mechanical, software and operational planning scheme.
To meet size constraints, a 6-axis robot was embedded in the machine with a pallet system on the backside of the machine, allowing easy operator access from the front to setup the machine without compromising ergonomics. The configuration enables quick setup changes between prototype and proving operations and full production runs.
The robot automatically repositions the workpiece from the front of the first spindle into the rear of the second spindle without operator input. The process of drilling a part from both ends in a single-piece flow is unique to UNISIG. Workpieces with enlarged features on one side are loaded from the rear of the collet, solving a common problem in gundrilling medical surgical instruments with full automation.
Control of the UNE6-2i and a computer are consolidated into the Human Machine Interface (HMI), a menu-driven touch screen system for easy, intuitive operation. Training and operator engagement with the system is significantly reduced due to user-friendly UNISIG controller menus and prompts. UNISIG’s comprehensive and integrated approach to automating medical part manufacturing is a vison that sets it apart in the industry. It’s more than drilling the impossible hole. It’s a commitment to understanding and to the research that drives continuous improvement and innovation for automated part production at its full potential.
Further information on all machines and the complete UNISIG machine program is available at: www.unisig.com or follow the company on LinkedIn and Twitter (@UNISIG). You will also meet us at the EMO 2023 show in Hannover, Germany, from 18.–23. September.
APlympton based precision engineering company pulled back from the brink of collapse just 5 years ago has recorded another strong year of growth. PTG Precision Engineers Limited were weeks away from going under and laying off all their employees when local Plymouth businessman, David Rowe, bought the business and transformed its future.
Rowe, owner of one of the largest engineering companies in the area, Applied Automation (UK) Ltd, felt strongly that losing PTG with its level of engineering knowledge and skills and with almost 40 years of trading was unthinkable. “As a machine builder I also knew they would be a great asset to my core engineering business and following the acquisition, which gave them financial stability, I appointed Mike Stevens, one of my senior managers at Applied Automation as their Managing Director. Since the acquisition in 2017, the company’s performance, despite the many challenges including covid and the increasing skills shortage within the industry, has been remarkable. PTG has truly risen like a phoenix from the ashes”, he said.
Under Mike Stevens guidance the company has retained IS09001 accreditation and is currently working towards ISO45001 (Health and Safety) and have significant knowledge, experience and the skills required to work in the nuclear sector along with the necessary inspection facility.
Over the past two years, PTG have invested in new machinery and are also able to offer specialist services which are in short supply in the South West of England, such as cylindrical grinding.
Mike Stevens is justly proud of the company’s customer retention rate, “It is exceptionally high and probably down to the fact that we really like to work closely with our customers. This ethos and working practice have helped us generate new business from some very prestigious customers, such as Leonardo Helicopters (previously Westland),” he said.
Stevens went on to explain that in his view probably the biggest current
challenge the industry and the company face is attracting young people to become precision engineers. “We work with local colleges and training companies and want to take on a couple of apprentices now. But, whilst many students consider a career in engineering, for some reason hands-on precision engineering seems to miss out”, he said. “For that reason, we’re now taking on people that are currently working in the engineering sector, such as setter operators for example, and we provide the upskilling and training to give them the skills and experience PTG will need in the future”.
With 2023 plans to expand their existing services in the Workholding, Nuclear and Aerospace sectors, where their expertise and experience makes them stand out from the crowd, the future is looking very positive for PTG.
www.ptgltd.co.uk
Mould making isn’t easy. There are many intricate challenges that include: highly complex geometry with 2D and 3D features, managing a wide range of part sizes, and short lead times on small quantities and new designs with no room for error. Compounding these challenges is the pressure to keep up
with the rapid pace of demand and technology.
But there’s a way to overcome those obstacles: Do better work with technology designed specifically for complex mould making.
Our USC-M series Milling and Drilling
Centres allow you to drill faster and mill better with a single machine and fewer setups. These Milling and Drilling Centres meet the challenges of milling and gundrilling all types of metals with either a single universal combination spindle or dedicated milling and drilling spindles. Utilising high performance spindles that provide exceptional rigidity
and power transmission, these machines deliver high-torque milling capability for aggressive metal removal and shorter cycle times. Additionally, 5-axis positioning enables mould manufacturers to tackle complex geometries with exacting precision in a single setup.
Many manufacturers claim to provide milling and drilling in a single machine, but the truth is those hybrid machines neither mill nor drill well enough to make a significant difference in either operation. In effect, one process is an afterthought of the other. Our USC-M series, however, was designed from the beginning to be a single machine with superior milling and drilling performance and accuracy. State-ofthe-art milling technology is embedded into a machine that has the power, thrust, speed and process monitoring competitors thought would be difficult to attain, or simply not possible.
In addition to superior quality and accuracy, the pay-off for single setup milling and drilling is efficiency and an improved bottom line. Mould makers cut delivery times to their customers with faster setups and production along with reduced overall labor costs. Once they move away from mould making operations with two machines, most of our customers find they can’t afford to manufacture without a USCM-series Milling and Drilling Centre.
The benefits of milling better and drilling faster with USC-M series machines do not stop at the spindle. There are intangible benefits as well. UNISIG USC-M series Milling and Drilling Centres allow mould manufacturers to approach their work differently and explore different approaches to mould making. With the entire manufacturing process streamlined, customers find their engineers and design teams enjoy more freedom and flexibility with the expanded capabilities. Finishing and assembly are faster because the design is more efficient, and manufacturers can do things effortlessly that were a struggle previously.
Ultimately, it’s about setting the bar high and keeping it there. UNISIG sets a standard looked up to by the competition. It’s a state-of-the-art mindset that takes mould finishing to a new level with a machine that allows you to mill better and drill faster.
www.unisig.com
The recent Government policy Powering Up Britain addresses the entwined objectives of increasing the nation’s energy resilience with achieving net zero by planning the decarbonization trajectory which will replace fossil fuels with cheaper, cleaner domestic sources of energy.
Central to such reform is the multi-billion pound engineering services sector that provides active measures to deliver improved energy performance, productivity and wellbeing across the UK built environment. Actuate UK, the engineering services alliance, focuses on the whole-life carbon performance of buildings, and the successful integration of passive and active measures. We support continual grid decarbonisation.
People are now aware that new homes will differ significantly. Newly constructed buildings will adopt a “fabric first” approach at the design stage, maximising the performance of materials and components.
Such improvements are being supplemented by advancing technologies. Improved cabling and
faster fibre optics are increasing a range of building functionality. Smart heating and ventilation systems can assess the temperature and air quality of our homes and automatically adjust to the healthiest and most efficient setting. Lights can be switched on and off or adjust. Smart, fast electric vehicles’ (EVs) charging points in homes will be more common.
Battery energy storage will become a familiar domestic and commercial feature. Batteries capture and store energy from solar panels, which is then used to supplement or replace the energy drawn from the grid at times of high energy cost/demand and even sell electricity back to the UK grid.
The introduction of the Future Homes and Buildings
Standards in 2025 can make change on a larger scale; the Standard will include improved insulation standards, efficiencies of fixed building services and indoor air quality and will impact the way we design, construct and commission new buildings and retrofit our existing building stock. In addition, Government promises support for insulation of homes and replacement of gas boilers, as well as methods of carbon capture, utilization and storage (CCUS).
These measures are not about new buildings alone; 80% of our buildings today will still be in use in 2050. Decarbonising our existing stock is essential and requires retrofitting around 28 million homes.
Building services engineers will play a pivotal role
bridging the gap across products, installation and sustained practical energy performance. This is why we need a continuous supply of skilled engineering services professionals who are tuned in to the new technologies and can realise UK’s carbon reduction targets. Actuate UK’s Skills Group has been mapping the skills gaps and will be working with industry to lower barriers to necessary training so that businesses can deliver.
Delivering high skilled jobs for the future is part of a greater ambition for the growth of UK engineering services. Actuate UK agrees with the conclusions of Chris Skidmore’s review of net zero strategy that net zero transition will further increase UK economic growth.
Actuate UK will work with the new Department for Energy Security and Net Zero to ensure they listen to the professionals whose skills and experience can turn their vision and targets into a practical reality for everyone.
For more information, see below:
www.actuateuk.org.uk
ustainable technologies - including solar PV systems - are playing important roles in helping to produce low carbon and energy efficient buildings.
While investing in a solar PV system may seem like a straightforward decision for sustainability, you must consider the condition of your metal
roof. The ideal scenario is the lifespan of your roof aligns with the estimated 25 year life cycle of the PV system. If the roof has a shorter lifespan, it is recommended to replace or refurbish it prior to installing the PV panels, to avoid future complications.
The structural integrity of your roof must be considered when planning the
installation of a PV system, including the extra weight that the panels will bring. The average commercial solar panel weighs 22kg, meaning that for a 2,000m2 building, there will be an additional 22 tonnes of weight. The fixing method must also be taken into account, as a ballasted system, for example, will bring additional weight to anchor the array to the roof.
Replacing your roof is the best way to ensure that it is structurally sound for the extra weight from the PV system, but it is not the most sustainable option. The cost, complexity, and disruption of a new roof, along with the carbon footprint from the extraction and transportation of the new metal, must be taken into account. Repairs may be a cost saving option, but they do not resolve all roof issues and may end up being a waste of your time and money.
Refurbishing the roof by oversheeting, placing new metal sheets over the existing roof, is another option for you to consider. However, this will add significant weight to your roof, for example, the 2,000m2 roof will gain approximately an additional 30 tonnes.
With weight loading in mind, Sharmans offer two lightweight roof refurbishment systems:
t Delcote® - The Full Roof Coating
Backed by an industry leading 25 or 10 year product guarantee (Dual/Single Coat).
t Seamsil® - The Cut Edge Corrosion System
Backed by an industry leading 15 year product guarantee
These market leading metal roof coating systems refurbish the existing roof to extend its life cycle. They offer a lightweight refurbishment solution, only taking into account the additional weight of the PV system and its components when considering structural loading. If a structural survey determines that roof refurbishment is the best option, contact Sharmans for more information.
Contact T 01298 812371 info@hdsharman.co.uk www.hdsharman.co.uk
Interface Force is an internationally recognised brand and decades of experience have gone into making Interface manufactured load cells the benchmark for thousands of users around the world, and Interface Force Measurements was established in 1996 by Neil Johnstone.
Based in Crowthorn, Berkshire, Interface Force distributes to the whole of the UK & Ireland, but also overseas, especially into Turkey, Greece and the Middle East. The company is a primary distributor for Load Cells manufactured by Arizona-based Interface Inc., and it also supplies their Torque Transducers, associated electronics, multi-access Load Cells and the XSensor Pressure Mapping systems.
The global Interface Inc. is represented by a large network of distributors outside of the US, and they have requested products that are designed and manufactured in metric, with the precision and accuracy of all Interface products. These products are designed for an international buyer and user, and all specifications are in metric specs, a global standard for force measurement products.
Interface Force work mainly with aerospace, automotive, and motorsport companies, and Business Development Manager Tony Rokins told us, “We work closely with companies which are undertaking research into product development, and so this includes universities and also medical companies who need load cells for weighing saline bags – we have a very wide and varied client portfolio.”
In this crowded industry, Interface load cells and torque sensors have a hard-won reputation for reliable, accurate and repeatable test results. The range of pressure sensors and pressure mapping systems from industry leaders GP50 and XSensor back this reputation.
Tony continued, “With regards to force measurement, our load cells are preferred by aerospace companies because they are highly accurate, and the results are very repeatable. Also, the devices themselves are extremely reliable and so they are looked on very favourably by both automotive and aerospace manufacturers in particular.”
Interface Force is currently re-launching its XSensor High Speed Pressure Mapping System – the company offers a range of pressure mapping systems that can be applied to anything from impact testing to pressure
testing tires, runways, beds, seats and much more.
The XSensor system is the first system design to allow product designers and safety testing engineers to see, record and evaluate the distribution of force from highspeed impacts on safety equipment such as helmets and body armour.
The system is particularly popular with automotive and aerospace seating manufacturers as evaluating the performance of helmets and other protective equipment designed to prevent injury requires detailed understanding of the pressure distribution on the body surface during dynamic impacts. Xsensor’s high speed HS Impact system combined with the thin conformable sensors allows customers to accurately measure those pressures and evaluate how different design configurations affect pressure distribution on impact.
In addition to this, the system is also used by manufacturers of office seating, companies that develop seating for the home, and bed manufacturers.
In spite of its success in the industry, Interface Force is very much looking to future development. Tony informed us, “We are building new Applications which are based around renewable energy, and we are also developing Cloud-based, Wifi and Bluetooth data acquisitions by making our devices wireless. This would mean customers being able to collect data from anywhere in the world via an App.”
This ever-growing comprehensive range of indicators, signal amplifiers, data loggers and wireless transmitters has been designed to complement the extensive range of load cells, torque transducers and pressure sensors, and the range has developed to ensure that customers have access to the most accurate, up-to-date, and costeffective devices available.
Another new development is in the Airport environment, where Interface Force have begun to provide wireless monitoring of equipment on, for example, luggage carousels, and this product among many others have helped Interface Force to have a very successful past 12 months especially.
Interface Force’s product reliability is second to none and all of its product lines have to match this standard before ever being recommended to customers.
Interface is the world’s trusted leader in technology, design and manufacturing of force measurement solutions.
Its clients include a “who’s who” of so many industries, and the company’s engineers around the world are empowered to create highlevel tools and solutions that deliver consistent, highquality performance.
For more information: T +44 (0)1344 776666 info@interface.uk.com www.interfaceforce.co.uk
t The inner workings and functionality of vacuum gauges
t An introduction to all the relevant measurement principles
Pfeiffer Vacuum offers easy-to-understand videos that explain how to choose the right measurement principle
Asslar, Germany, 19. April 2023. To assist in choosing the right measurement principle, Pfeiffer Vacuum has made helpful explanatory videos that give a detailed insight into the inner workings and functionality of vacuum gauges. If the target vacuum is to be successfully measured and controlled, it is essential to select the right measurement gauge.
"Pressures and pressure curves must be maintained with precision if you wish to achieve optimal efficiency in production and the highest level of product quality. Our vacuum gauges are important quality indicators. Modern technology makes it possible to carry out total pressure measurements from atmospheric pressure through to ultra-high vacuum, covering all vacuum ranges precisely. We explain the relevant measurement principles in five videos: From capacitive through to piezo, Pirani, cold cathode and hot cathode measurement", explains Patrick Walther, Strategic Product Manager Instruments at Pfeiffer Vacuum.
Important questions are addressed in detail: "How exactly does physics apply in a vacuum gauge?" or "How can the properties of the gas be used to deduce the total pressure?"
The video on capacitive vacuum measurement shows how the diaphragm inside the gauge moves in relation to changes in the total pressure.
In the case of piezo-resistive vacuum measurement, viewers learn how the strain resistances in the diaphragm change depending on the pressure. The video on Pirani vacuum measurement explains how a thermal conductivity vacuum gauge works. It shows clearly how the transfer of heat through the vacuum inside the gauge is dependent on the total pressure. It also demonstrates how the heat transfer and thus the displayed pressure depend on the type of gas. The video on cold cathode vacuum measurement shows how gas molecules are ionized by high-voltage electricity to create a plasma. In the video on hot cathode vacuum measurement, you will see how a hot cathode transmitter works and how the gas molecules are ionized by electrons emitted from a hot heating filament.
www.group.pfeiffer-vacuum.com
The ML2540-Series laser modules deliver high output power up to 2W and are ideal for the use in industrial applications with harsh environmental conditions. The offered wavelengths range is from 405nm to 1060nm. Apart from round and line beam, other beam shapes like grids, circles or line and dot arrays are available. The line beam has a sharp rectangular shape with homogenous power distribution along the line. The housing is electrically
isolated and keeps the protection class IP65 (IP67 optional) conditions. TTL modulation up to 1MHz and analogue modulation up to 100kHz are optionally available. The power stability is <1% over 24 hours.
Applications include, but are not limited to, roof tile alignment, railway conditions control, steel parts production, subsea robotics, traffic control, long distance pointer in defense applications. For more information, see below. www.frlaserco.com
IThere are estimated to be a staggering 20 million vehicles used
across the UK: that’s an estimated 700,000 company cars, 4.8
million trucks and HGVs and 14 million privately
for
cars (dubbed ‘grey fleet.’) Then, there are of course all the additional mopeds, motorbikes, taxis, minibuses, buses, coaches, emergency services and specialist vehicles, across regional villages, towns and cities every day. Driving for work can simply be a minefield, and that’s without the pedestrians, dogs, pot holes and road works, leaving even experienced, Highway Code-literate drivers feeling stressed and overworked.
‘Driver safety shouldn’t be a Lottery,’ warned Simon Turner in his monthly DFBB blog on the Safety & Health Practitioner website.
The Department of Transport has reported that an estimated 40,000 annual road casualties involved someone driving for work: resulting in a further stark statistic: one in 500 work drivers will be involved in a road injury collision, some fatal.
In 2007 The Department for Transport took action and Driving for Better Business was born: an awareness-raising campaign, aimed at helping those who manage work-related driver safety up and down the country. This free managementengagement programme shares industry good practice, through illustrated case studies along with the business benefits that those employers have also achieved from reduced maintenance costs to greater fuel efficiency. There’s also a sevenstep framework to help improve driver management processes.
“The role is to put the National-Highways funded Driving for Better Business programme in front of those responsible for managing driver safety: from Managing Directors, Fleet Managers, Safety Managers, Finance Managers, to HR managers.
We're looking to help them understand their legal responsibilities, the opportunities for improving business performance and efficiency, sharing case studies of good practice and resources that can help them improve their own management,” outlined Simon Turner: Campaign Manager at Driving for Better Business and Chairman of the Association for Road Risk Management (ARRM.)
There is a statutory legal duty placed on employers to manage driver safety, under the Health and Safety at Work Act 1974, and in the event of an serious
There are four main sections that cover these aspects: Section 2, Section 3, Section 7 and Section 37. Section 2 (duty of care to employees) states that the company’s business activities must never put their drivers at risk, from overworking, poor vehicle roadworthiness etc. Section 3 (duty of care to others), concerns risk to other road-users, such as: maintaining vehicle roadworthiness, to avert collisions and accidents. Any breaches of Section 2 and 3 can result in company fines and negative reputational damage, which have far-retching repercussions for the entire company.
Section 7 (employee responsibility): all employees need to adhere to safe working practices, which means, for instance, that drivers need to conduct regular vehicle safety checks and not drive while impaired or using a handheld phone. It also means managers mustn’t phone their employees while they’re driving if the policy says not mobile phone calls allowed.
Section 37 (Manager’s responsibility): senior-level managers need to ensure business activities are properly risk assessed and that includes driving activities, and make sure safe working policies and practices are put in place. Any breaches of Sections 7 and 37 can lead to fines, disqualification from being a director and even prison sentences.
Simon Turner is passionate about fleet driver safety and believes the Driving for Better Business programme can really help employers improve the way they manage driver safety, ending the ‘Lottery’ approach to work driving practices.
“We work diligently around the country: our audience is any company with staff that drive for work that strive for compliant best practice. Our programme is entirely free to access, with lots of free online tools and resources to help.
Our vision is a world, where those who use the roads for work do so safely, efficiently, and sustainably.
Furthermore, we want to improve safety and reduce risk for all those who drive or ride for work, by promoting good management practice and demonstrating the significant business benefits.”
By raising awareness of work-related driving risks from fatigue, vehicle roadworthiness to the dangers of drink and drug-driving; companies can allow clear guidelines to all employees and adhere to all Health & Safety at Work legislation.
By making concerted efforts to improve working practice and driver culture, a whole organisational culture shift can happen. This can then have knock-on
benefits such as: reducing insurance costs, increasing the company’s safety record and reputation, and reassure employees about vehicle roadworthiness.
The team at Driving for Better Business are making
In this issue of Industry Update, we are proud to announce ELKA Rainwear A/S as our waterproof textile manufacturer Company of the Month.
In this Anthropocene Age, we are increasingly seeing the daily global impact of climate change from flash floods to droughts. The UK generally follows temperate climate patterns; however, climate change brought the hottest UK summer on record last summer (over 40° c) and continued regional flash flooding across many areas. New research from The Met Office, using k-scale modelling and 100-year climate projections, show that extreme rain will be four times as frequent by 2080, compared to the 1980’s.
With the increased risk of extreme rain, it is imperative that all our key workers across industries such as agriculture, industrial fishing, off shore, construction to transport, have access to robust, durable waterproof workwear.
ELKA Rainwear A/S has been expertly manufacturing waterproof clothing since 1958. Originally founded by Ejnar Lauridsen in Karup, Denmark: the company name was formed from his first two initials (EL) and the first two letters of Karup (KA.) By 1979, the company was interested in a more international market outlook and the name changed to ELKA Rainwear A/S. With the headquarters firmly rooted in Sunds, Midtjylland: Denmark, this Danish company has expanded exponentially, with production plants in both Europe: Lithuania and East Asia: China.
“Our VISIBLE XTREME and WORKING XTREME stretchable range are perfect for protecting against wind and rain, whilst providing comfort and breathability and are all available in sizes XS- 5XL. The VISIBLE XTREME designs are EN ISO 20471-certified; embedded into the modern design is segmented reflective tape, providing health & safety compliance. The special precision-driven engineered weave allows
for longevity: bending and flex movements and the stretchable fabric is laminated with flexible PUmembrane for class 4/4 wind and rain protection,” explains Marc Palmer, UK Area Sales Manager.
The VISIBLE XTREME stretch waist trousers have taped seams, fully adjustable waist and Cordura® reinforcements on knee pockets, for comfort all day long. The VISIBLE XTREME stretch jacket has double storm flaps for even the most ferocious storms and handy hidden waterproofed pockets for ID and tablets/ notebooks, keeping you and your assets dry and safe.
The WORKING XTREME stretch three-layer jacket has an outer fabric, membrane and lining, all laminated into one ergonomic lighter jacket functionality.
The UK Sales team have been showcasing the stretch waterproof range at The Health & Safety Event from the 25-27 April at the NEC, Birmingham, explains Marc Palmer,
“Our cutting-edge, high-quality waterproof range is popular throughout the UK market and is placed in the mid-higher price bracket. We have a lot of repeat custom, and as we depart the world of fast fashion, companies are looking for more sustainability, durability and longevity options in workwear.
We are excited to be launching our new recycled polyester workwear range this Autumn, offering companies our stretchable high-visibility and non-high visibility range in a recycled material.”
Treston is not just a furniture manufacturer. We offer our customers comprehensive know-how and insights on how to make their workstations and workspaces as functional as possible.
Ergonomics is always taken into account when designing a workspace and because Treston products are modular, the workstation solutions we design are cost-effective and comply with the principles of the LEAN
philosophy. Our range of products with ESD protection and our expertise in ESD matters help our customers obtain safe and functional workspaces for the most demanding working conditions.
Our long history as a furniture manufacturer, more than 500,000 workstations delivered, and 15,000 customers globally are a guarantee that we know what we are doing.
In projects, our expert sales staff go through the customer’s needs, goals, current state, and processes. Based on the conversations, we then make design proposals for the spaces and furniture. Our design engineers can make the exact type of dimensional drawings that the customer needs.
Our retailers are also experts who can provide the services that you need flexibly and comprehensively. We also support our network of retailers through expert services.
At Treston, our wide selection of products and modular and adaptable workstation solutions ensures that our customers find furniture solutions to meet their individual needs cost-efficiently. Being a manufacturer enables us to flexibly create customised solutions.
Easy workspace design with the 3D Configurator
Designing an individual workstation is easy and quick with our 3D Configurator software, available at 3d.treston.com. The 3D Configurator guides you through the selection of all the necessary modules and accessories for your workstation.
When you have completed the design, you can send a request for a quote electronically, or save the drawing and supply list in PDF format on your own computer with a click of a button. We also offer an assembly service.
There is a comprehensive network of installation services that we use regularly at Treston, and we can also recommend, especially for use in larger projects, to speed up the implementation of changes to manufacturing facilities.
At Treston, our expert sales staff and network of retailers, our modular products, and our opportunity as a manufacturer with its own factory to form customised solutions, guarantee that we can create an efficient and functional workspace for our customers.
Do not hesitate to contact us if you are looking for a smart and functional solution for your working environment.
For more information, see below.
T +44 (0)1635 521521 salesuk@treston.com www.treston.com
With CHEMUK approaching, Industry Update took the opportunity to speak to PowTechnology CEO, Dave Oakes, who’s career in sensing, instrumentation and communications spans over 30 years.
Speaking with clear passion for the sector, Dave explained “The Industrial Internet of Things (IIoT) is well-documented as a network of interconnected sensors, instruments and other devices, facilitating data collection, exchange and analysis.
Whilst Covid highlighted the benefits of remote monitoring to many new industrial sectors, our experience has shown some reluctance to embrace the IIoT due to perceived entry costs and payback time.
PowTechnology counter these concerns with user-friendly, proven, affordable, modular hardware and software. We help customers lower operational costs, monitor the condition of essential kit to prevent breakdown, maximise resource, comply with legislation, introduce new revenue streams, improve service and differentiate themselves to win contracts.
PowTechnology was founded as Powelectrics, over thirty years ago, by Henry Powell. We began as a sensor distributor, supplying into factory automation and process control.
We have transformed into a respected, ISO 9001 and ISO 27001 accredited, end-to end IIOT solution provider, supplying proprietary, award-winning Metron hardware and MetronView software and interfacing with a wide range of third-party clouds and kit.
Still based in Tamworth, we recently renamed ourselves PowTechnology, which represents our capabilities better, whilst maintaining the heritage ‘POW’.
Over 100,000 IoT devices have been manufactured and supplied by PowTechnology. They deliver data on level, flow, temperature, pressure, vibration, humidity and more. Data… which creates knowledge… used for process improvement and strategic decision-making.
We’ve just had our best quarter and we’re on track for our best year. Fundamentally, this success is built on our genuine expertise and practical experience.
Our technology also benefits almost any business, including chemical, cryogas, pharmaceuticals, fuels, Adblue, waste,
recycling, agriculture, the environment, utilities, pumping, rail, construction and security. Our website bears testament to our wealth of sector and application knowledge, with over thirty case studies. They include household names and multinationals, such as GreenChem, United Utilities, Royal Mail, RSPB, Cemex, Fuchs Lubricants and Speedy.
PowTechnology invest heavily in R&D, collaborating with academia to embrace cutting-edge technologies and enjoying the diverse skill set of an experienced, rapidly expanding internal Development Team
Our kit is designed as highly scalable, modular IIoT building blocks. This means we can often offer off-the-shelf, ‘plug n play’ solutions. Equally, our agility allows us to design bespoke solutions, with minimal development costs, creating proofs of concept within a few months, where others may take years.
I encourage you to examine the case studies on our web site.” As an example and with CHEMUK in mind:
GreenChem is one of Europe’s largest AdBlue® producers and distributors with thousands of contracted customers. In 2010 they needed a more reliable telemetry solution to measure tank levels and ensure customers did not run out of essential supplies.
PowTechnology’s lloT hardware reports level data to PowTechnology’s software, to assist a range of operational activities. A huge advantage is the ability to remotely configure units to accommodate over 40 tank designs.
“As one of Europe’s largest AdBlue® distributors, GreenChem rely upon efficient logistics. PowTechnology’s dependable and robust remote tank level monitoring solution supports that and
In the BC era (Before Collaboration), automation was the sole preserve of industrial giants with massive budgets. The emergence of collaborative robotic solutions, user friendly tools and intuitive software has changed all that. Nowadays, smart solutions are here to benefit businesses of any size.
Fast deployment at affordable price point
Ready to use out-of-the-box, collaborative application solutions greatly simplify the deployment process, allowing companies to deploy automation with a minimum of costly downtime and at a fraction of the cost of traditional automation deployments.
Competitive advantages for your business
The competitive advantage conferred by automation range from increased productivity and throughput to enhanced reliability and improved quality.
Collaborative application solutions hit that sweet spot between affordability, no-fuss usability, and flexible functionality that manufacturers demand.
your factory: https://onrobot.com/en/blog/ why-you-need-collaborative-automation
Find out how others got started with automation: https://onrobot.com/en/case-studies
Remove physical and financial pain out of palletising
out how we can help you automate your palletising processes: sales@onrobot.com
flexibility to define your system around your unique business needs, but with all the benefits of a single vendor:
t Faster deployment and easier changeovers
t Fits into existing layout and workflows
t Lowers total costs and speeds return on investment
t Future-proof for evolving business needs
t Fully tested, certified, and warrantied for reliability
Manual palletising is a labor intensive, repetitive and injury prone task which makes it an excellent candidate for collaborative automation. Despite this, many end of line palletising tasks are still
And with traditional palletising robotic solutions coming with a high price tag, when the capital outlay is considered alongside long deployment time, the number just don’t add up
Discover the cost-effective solution for quickly deploying your first automated palletising cell
The OnRobot Palletiser is here to take the physical processes with the combination of unprecedented affordability, performance and fast integration
Get in touch with one of our automation experts to find out what palletising configuration is right for your facility: sales@onrobot.com
Learn how to build a palletising application: https://learn.onrobot.com/en/ palletizing-what-expect?area=8
Find out how automation can help you. Get in touch with an automation expert to start the automation journey! –
Discover the OnRobot range of products and solutions, robot arm grippers and EOAT components: https:// onrobot.com/en/products-and-solutions
Read more about collaborative automation for
OnRobot Palletiser is available as a complete out-of-the-box system or as individual components to create a mixand-match solution that will work for your specific application needs.
Get in touch with one of our automation experts to find
Read more about complete OnRobot Palletiser solution: https://onrobot.com/en/solutions/ onrobot-palletizer
Discover other OnRobot solutions: https://onrobot. com/en/products-and-solutions?solutions
Collaborative palletising starts with your unique application needs
These days, workers are in short supply and product demand is high. Get ahead of your competition by automating you palletising processes.
Automating palletising provides fast return on investment even for smaller manufacturers and logistics organisations. It’s cost-effective, quick to deploy, and offers the flexibility needed for high-mix, low-volume environments and peaks in demand. You get better consistency and higher productivity without overtime or injuries.
Your business needs first
The OnRobot Palletiser is available as a complete or the individual components can be combined for your perfect mix-and-match solution. This gives you the
At this year’s PPMA show Soken Engineering, a recently acquired subsidiary of Jenton International, will launch an all-inclusive range of heat sealing packing systems for ‘on the go’ food businesses wanting to improve presentation, product lifespan and handle a varied range of lunch products on a single system!
Deli’s, garden centre cafes, hospitals and garage forecourts that hand-pack lunch items in takeaway cartons/boxes with press-on lids will compromise product presentation and lifespan due to air leaks which fast-track spoiling. As the UK’s demand for lunch products continues to broaden, Soken has responded with a 3-in-1 Heat-Sealing System which perfectly seals packs of sandwiches, wraps and salads with only the need for a tool change. Now artisan businesses only need to invest in a single
system to improve pack presentation, hygiene and preserve lunchtime foods by up-to three days, putting a stop to food waste and resulting loss of profit which is entirely preventable.
The 3-in-1 Soken range includes level 1 machines ideal for small cafes which want to seal a single pack at a time, level 2 machines – which seal up to 4 packs at the same time – ideal for caterers supplying mobile vans and local shops, as well as level 3 intermediate automated systems – which can output up to 48 packs per minute – perfect for medium sized businesses such as airline caterers or large garden centre chains.
All Soken equipment is manufactured in the UK and backed by a two-year return-to-base warranty. As all tooling and parts are designed and manufactured in-house, spares can be provided
within very short time scales. It also means that if a caterer has any unusual packaging requirements bespoke tooling can be developed as required. In addition, Soken can supply all necessary consumables such as sandwich packs, ready meal trays with lidding film and salad boxes. Plans are in the pipeline to develop packaging options which are plastic free.
Stephen Hawes, Soken Engineering sales manager said: “If sandwich boxes and salad packs are not sealed properly the shelf life of the food is compromised leading to waste and reduced profits. Our versatile easy to operate 3-in-1 ‘fresher for longer’ packaging systems give catering outlets the ability to sell a wide range of foods in tamper evident heat sealed packaging which extends shelf-life considerably. As a business we are always striving towards net zero so helping reduce food waste is a key priority.”
Schmersal at interpack 2023 – new safety and automation solutions for the packaging industry
Wuppertal, 5 April 2023. Packaging and process solutions for companies operating in food, beverages, pharmaceuticals and cosmetics will once again be the focal point of this year’s interpack. In Hall 18 / D15, the Schmersal Group will be presenting new products and innovative safety solutions that meet the central requirements of this industry: hygienic design and high plant availability.
New command device series for food-processing machinery
The H series from Schmersal will be showcased at interpack 2023 as a full range of command and signalling devices for hygiene-sensitive applications, particularly food processing. The new H range not only meets the requirements of the new standards for these applications and the ‘hygienic design’ construction principle but is fully modular as well. A total of 147 different devices are available, including 26 mushroom pushbuttons, 24 selector switches and four potentiometer-rotary switches.
New compact safety light barriers for the packaging and food-processing industries
Schmersal has developed the new SLB440 series safety light barriers for hygiene-sensitive applications in the packaging and food-processing industries. With a diameter of 62 mm and a height of 115 mm, the light barriers in the SLB series are extremely compact and achieve protection class IP69. The sealing caps on the SLB440 are made from stainless steel (V4A), while the transparent protective tube is made from robust polycarbonate (PC).
AZM300 solenoid interlock with a hygienic design
The AZM300 RFID solenoid interlock has also been designed according to hygienic design principles. The AZM300 with protection class IP69 is an innovative safety interlock that finds particular use in the food-processing and packaging industries. The AZM 300’s features include the patented operating principle with a rotating shaft and star handle. It allows the safety door to be held virtually without play when closed. An RFID sensor is used to identify the actuator reliably, thus providing three different code levels and, consequently, protection against tampering.
The smallest electronic solenoid interlock in the world: AZM40
With dimensions of 119.5 x 40 x 20 mm, the AZM40 is the smallest electronic solenoid interlock in the world. With these compact dimensions, the AZM40 is particularly suitable for installation on machinery equipped with small flaps or rotating/sliding doors. Due to extensive integrated monitoring functions, the AZM40 can be switched in series with all other electronic safety switchgear from Schmersal. This makes monitoring multiple safety doors in a single system much easier and more cost effective. The AZM40 is especially suited to use on packaging machinery and in complex packaging lines.
Visit Schmersal at interpack in Düsseldorf between 4 and 10 May 2023: stand D15, hall 18.
www.schmersal.co.uk
Dairy-Tech 2023 took place on the 1st February at Stoneleigh Park in Warwickshire and was a roaring success with new show features that had visitors excited and impressed.
Dairy-Tech provides a platform for suppliers to meet the needs of a modern dairy professional, as well as offering farmers support, information and advice to run sustainable and resilient dairy businesses. The show highlights and exposes the exciting industry of dairy and includes all the latest industry trends, innovations and updates that are relevant to a dairy business.
This year a brand-new Lameness Village helped farmers get to grips with managing lameness in their herd providing support, advice and helpful tools from industry experts. This idea came into fruition because of the increasing focus on the issue as part of the Government’s Animal Health and Welfare Pathway to which lameness is a main priority.
To support this, there were also lots of helpful resources available at the show to help farmers get to grips with the rollout of the Environment Land Management (ELM) scheme that included talks from a number of Data
representatives and even Farming Minister Mark Spencer.
The 2023 show also welcomed Prof Frank Mitloehner from the Department of Animal Science at UC Davis, USA, who discussed what a sustainable dairy system looks like, and his fellow US speaker Dr Matt Utt, Senior Dairy Product Analyst at Zoetis, who outlined how to hit the basics regarding dairy profitability.
For information on Dairy-Tech 2024, see below.
www.dairy-tech.uk
Waikato Milking Systems are excited to announce that the Farming Equipment and Technology Fund (FEFT) 2023 grants can be used to help farmers fund the costs of some of their automation technology and products.
As one of the world’s largest producers of rotary milking systems and world-leading smart technologies, Waikato Milking Systems have a range of milking technology and solutions that meet the FEFT criteria of improving productivity, environment and animal health and welfare.
At the recent Dairy-Tech 2023 event, Waikato Milking Systems CowTRAQ™ Collars were in high demand due to their groundbreaking technology and immediate availability. CowTRAQ™ Collars allow farmers to monitor the heat and health of every cow 24/7 to maximise their herd performance, and keep their farm efficiency on track.
Meanwhile their range of automated Sort Gates have been designed to suit all farm requirements and budgets to ensure the accurate sorting of animals, and to enhance cow flow. Together, these two products will improve your productivity and keep your herd’s performance on track and sorted 24/7.
Go Low Carbon had a successful Dairy-Tech 2023, catching up with existing clients while also speaking to new contacts about how best to reduce their energy spend and carbon footprint.
From our base in North Cumbria, we’re specialists in supporting the UK’s busy agricultural sector, installing solar panels on dairy farms, poultry units and other integral farm structures. Not only that, but we have an incredible team of carbonconscious energy brokers who have a consistent track record of finding the best energy suppliers for agricultural businesses – a process that leads to substantial annual savings.
We stick to our core values throughout every installation that we undertake; be honest, communicate openly, educate as we develop a relationship, and provide overall value for money. Through experience and dedicated research, we’re proud to say that we understand needs and demands of the dairy industry. If you’d like to reduce your energy costs while also reducing your carbon footprint – we should chat.
“Working with Go Low Carbon was a great experience for us. They truly have your best interests at heart and the end result is saving us thousands on an annual basis.” - One happy agricultural customer. T
Continual innovation for dairy: how Wolfenden Concrete are helping farmers stay profitable and herds stay healthy
Wolfenden have more than 45 years’ experience working with dairy farmers, developing innovative products for housing, slurry management and herd welfare. Continual investment in R&D and in the latest design software makes Wolfenden supplier of choice for farms across the UK for newbuilds and for expansion or adaptation of existing infrastructure.
Wolfenden offer a complete suite of award-winning Supa products for farmers looking to address Net Zero with more efficient slurry systems, and for better herd health and wellbeing - all designed specifically for the dairy sector. Hybrid Supa Slats combine hardwearing yet soft rubber inserts with a non-slip concrete surface, helping to cut emissions and improve cow movement to reduce lameness. As the only mainland UK manufacturer of Hybrid Slats, Wolfenden are setting new standards of performance for animal welfare and slurry management. These complement other products in Wolfenden’s dairy range - Supa wide and Supa deep slurry channels; Supa strong diagonal slats, and Supa narrow slats for young stock.
The Waikato Milking Systems CowTRAQ™ Collars and Sort Gates both qualify for the FEFT 2023 grants, and are available immediately.
For more information call us on 0750 841 7698, or visit our website to read about our range of products. www.waikatomilking.com
Greencrop attended the Dairy Tech show again this year, on stand P40. We displayed one of our Dribble Bars which gathered great interest, particularly with the small claims grant available to customers. The show again was a great success, and we look forward to attending next year with our latest machines and offers.
Greencrop offer a range of dirty water and slurry spreading solutions; to spread slurry/waste/dirty
Wolfenden’s products are specified for projects large and small, right across the UK. Their innovation and vast experience helps dairy farmers achieve the productivity that is critical for sustainable and profitable farming.
Contact: T 01282 844213
info@wolfendenconcreteltd.co.uk
www.wolfendenconcreteltd.co.uk
water from livestock farms, washing plants and AD Plants.
With legislation to start in 2025 where slurry cannot be applied to the land above ground, slurry spreading will have to change to shallow injectors, Trailing Shoes or Dribble Bars.
Greencrop can supply a range of all the above equipment and a great budget range of dribble bars up to 9m spreading width able to mount on existing vacuum tankers from the back door without having to weld on any mounting brackets etc and can also be able to still use the splash plate if needed.
For more information, see below.
www.greencrop.co.uk
Avery successful day was had at Dairy Tech 2023, for Peacock Technology’s second visit to the show.
Based in the heart of Scotland, Peacock Technology provides engineering solutions for the Agri-tech and energy sectors. Combining years worth of experience in the dairy sector with the range of engineering history in other areas, allows Peacock Technology to confidently provide products to meet different farmers needs.
The IDS Teat – Post Spray System, is a compact robot used to spray cow’s teats post milking on rotary parlours. Built around a proven, robust industrial robot arm and a 3D vision system, it can reliably and consistently locate and apply a spray disinfectant to cow teats. Helping
to fight mastitis and most importantly improve cow welfare with accurate results every time.
The IDS i-QUBE is a sensor worn on the rear leg that reliably and accurately monitors each cows movement.
Automatically collecting detailed information on patterns of behaviour, algorithms analyse the data to provide accurate alerts and information.
Competitive, simple and affordable, we work with our clients to provide a tailored pricing package, while supplying regular servicing and support.
Visit us again in 2024, with our new developing technologies!
info@peacocktechnology.com www.peacocktechnology.com
Greenhill Systems was extremely active at this year’s Borderway UK Dairy Expo 2023 when over the two days the team offered their industry knowledge and advice as well as showcasing the Heatguard roof sheet alongside Vervaeke Agri calf pens and curtains.
Greenhill Systems is the largest supplier of Heatguard roof sheeting and associated products across UK and Ireland: mainly to the agricultural, equestrian and commercial construction sectors.
The Greenhill Heatguard sheet is a robust, triple wall polycarbonate sheet with a co-extruded UV layer, protecting the sheet and anything underneath by impeding 99% of detrimental UV rays.
The dual-function athermic pigment within the sheet restricts the heat from direct sunlight, whilst
simultaneously optimise natural light to pass into the building.
This results in a brighter building, enhancing the wellbeing and production rates of livestock, with the careful removal of hotspots, shadowing and overheating on hotter days. The resulting brightness reduces the cost of artificial lighting, leaving an energy cost windfall for owners.
The Greenhill Heatguard is generally used as a full-roof option but can alternatively be used with fibre cement sheeting and accessories, and is available in Big6 profile.
With its own farming division, the team at Greenhill Systems is expertly placed to provide consultation on the best use of Heatguard, to suit any specification. For further information please contact:
Paul … 07715005770 Ryan … 07734374160 info@greenhillsystems.co.uk www.greenhillsystems.co.uk
Oxi-Tech is a British start-up tech company, that has developed a system that creates an extremely powerful, yet environmentally friendly chemical-free disinfectant.
The technology achieves superior disinfection using only tap water, and low-voltage electricity.
The company’s “patented "Pulse Technology" is disrupting the chemical industry as it’s chemical-free system removes the majority of associated carbon involved with chemical production, manufacturing of plastic barrels, packaging/ labeling, and all the heavy road miles of transportation and delivery.
“It’s a step change in environmentally conscious disinfection, and we’ve already attracted the keen interest of some of the largest players in the industry” stated Oxi-Tech’s new CEO Paul Morris
In addition to the obvious environmental and operational efficiency benifits, the system saves significant amounts of energy currently wasted by chemical treatments and the excessive heating of water, used to control waterborne pathogens, such as legionella, and cryptosporidium.
Our Pulse Oxidation Technology can effectively replace chlorine, acids and other hazardous chemicals with a safe, pH neutral, and highly effective alternative, made only from the water in use, and site available, low voltage electricity.
Oxi-Tech’s first step into the market place was in Dairy parlour disinfection, where the results of their prototype located on just one farm in Norfolk were so successful, they gained the Excellence Award’s runner up position from the government’s Agri-Epi Centre programme. This initiative focused on those technologies that had the biggest environmental impact in farming in the UK, this led on to the system being recommended by DEFRA and included on the UK government ‘Farming Equipment and Technology Fund’ grant list, an accolade that stands as a powerful endorsement of the technology. This commendation should come as no surprise, given the powerful environmental and economic benefits of the technology.
www.oxitechsolutions.com
not only sanitise the surface but destroy the biofilm, giving you long lasting protection.
The dye and fragrance-free product was created and tested by UK & USA scientists, who have since carried out a series of tests for applications in a variety of environments. Currently, we use the disinfectant in animal sciences, human sciences, plant and crop sciences, air quality and manufacturing sciences.
The magic of our product is that it leaves no residue, meaning you can use the product around animals, in drinking water, on produce etc. and there’s no trace that the product was ever there. As we leave no residue, the bacteria is unable to build up a tolerance against the disinfectant, making it one of the best disinfectants on the market.
The product is easy to use and contains no phosphates, it's hydrated in water and once applied to the surface can be left to air dry, no rinse is required. You can order up to 1000L of product in a single box.
T 01225 983710
www.vsbiosciences.com
info@vsbiosciences.com
system
The Science
days. In winter,
outside
(whether ‘wet’ or ‘dry’) is brought inside and heated. As air heats it expands, but the actual moisture content of each molecule cannot change, and therefore the relative humidity falls.
It is widely acknowledged that maintaining relative humidity levels between 40-60% significantly improves human well-being and mechanical performance. Read more to find out how low humidity effects both human and mechanical production.
How does low humidity effect our wellbeing?
Low indoor relative humidity has a negative effect on human comfort. The adult human body is typically 60% water, so in a dry environment our bodies naturally lose moisture. Unlike temperature, low humidity is more difficult to detect.
Typical symptoms include:
t Dry and itchy skin
t Cracked lips
t Dry eyes (especially for those with contact lens)
t Sore throats
t Nosebleeds
t Headaches
In addition, low relative humidity dries our mucous membranes and inhibits our body’s natural defence against germs, viruses, and bacteria, making us much more vulnerable to catching common colds and flus. Maintaining relative humidity between 40-60% is scientifically proven to reduce the spread of airborne pollutants and viruses.
How does low humidity effect mechanical processes?
Moisture absorption also affects hygroscopic materials like wood and paper. The low humidity dries out these materials causing them to shrink, curl, crack or split. When these materials pass through machines, usually at high speeds, it causes paper jams and machine breakdowns. A list of common problems is listed below:
t Static electricity build-up and ESD
t Drying out of hygroscopic materials like wood and paper
t Paper jams and machine breakdowns
t Increased wastage
t Decreased productivity
The Solution There is a wide range of humidifiers and a variety of factors to consider in selecting the right humidifier for each building or application, such as energy use, water supply, cold water or steam, gas or electric, evaporative or spray, humidifier situation, control compatibility and maintenance needs. It is therefore important to seek advice from specialists who can provide guidance and design a bespoke
Humidity
applications
Contact T 01372 571200 info@humiditysolutions.co.uk www.humiditysolutions.co.uk
Our industry-leading customers around the world rely on UNISIG® deep hole drilling technologies for powerful, intuitive capabilities. We engineer our machines to handle a complete range of applications, and support them with our high level of expertise and service.
Standard Gundrilling Machines: Job Shops & Production Drilling