ACW Cargo Handling Supplement is sponsored by
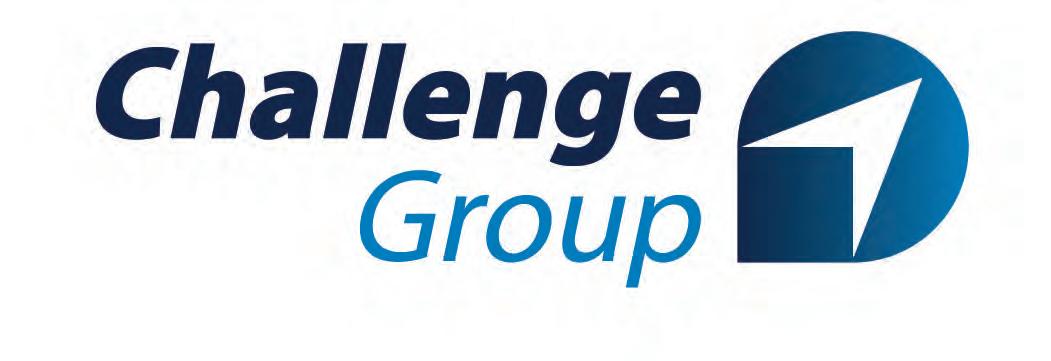
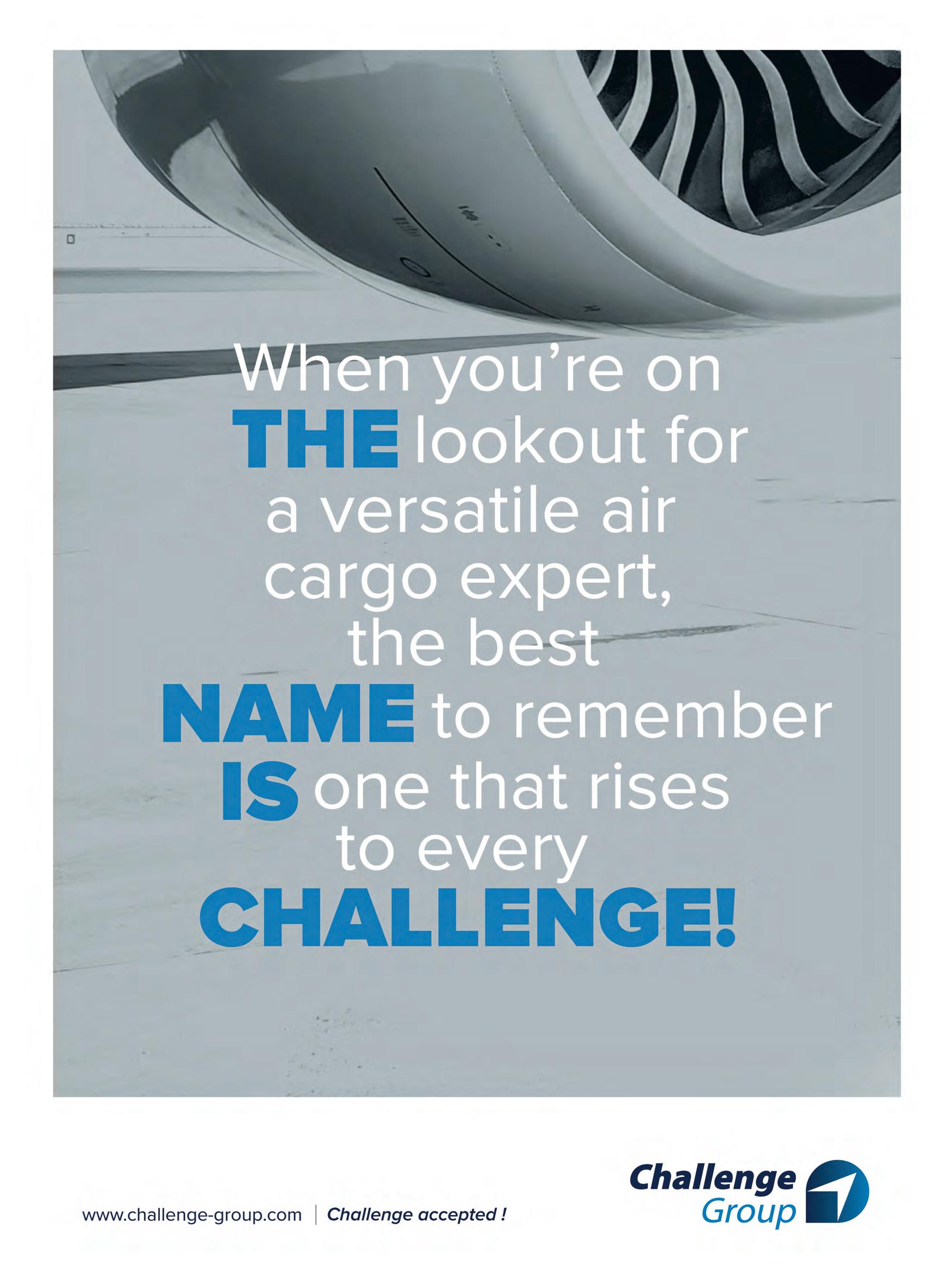

ACW Cargo Handling Supplement is sponsored by
The International Air Transport Association (IATA) considers safe and efficient ground operations as essential to airline operations. It pur sues a number of projects in this field with the assistance of ground handling partners. According to the association, cargo handling is performed at thousands of airports all over the world by hundreds of companies, big and small. IATA actively drives the development of ground handling operations standards, best-practice processes and procedures and promotes global consistency and harmonisation.
IATA describes cargo handling as the segment of the supply chain which processes goods landside in the cargo facility. From the deliv ery at the airport of origin until it is ready for loading on the plane, to the unloading at destination and handover to the consignee/freight forwarder, many steps are involved with cargo handling that must be closely followed to ensure shipments are delivered safely and securely.
Of course, cargo handling also happens away from the apron, away from the hustle and bustle of the airport. Indeed, Road Feeder Services (RFS) can operate hundreds of miles from the aircraft cargo door. Warehousing where airfreight is stored before or after flight is now likely to be miles from an airport on an industrial estate. And that warehousing is increasingly likely to be equipped with the latest AI and digital technology and automation for expected 21st century levels of service.
One example of this is that Kale Info Solutions (Kale), the US subsidi ary of Kale Logistics Solutions, has entered a partnership with Chicago Rockford International Airport (RFD), USA, to implement its Airport Cargo Community System (ACS). The system will reduce manual doc umentation and data entry time for cargo handlers at RFD, increasing process efficiency at the airport as well as reducing truck congestion and streamlining cargo flows.
As RFD has seen annual air cargo throughput triple over the last five years, with a 25% increase in volumes recorded just in 2021, the airport has increasingly become an important Midwest hub for e-commerce and international trade. This has been a factor in the investments that support the introduction of an efficient, transparent cargo IT platform to further streamline the digitisation and movement of cargo to keep up with the demands of our growing cargo operations in the future.
Cargo handlers are increasingly looking to receive real-time up dates on estimated cargo arrival times, while advance slot booking capabilities which enable trucking companies and ground handlers to co-ordinate landside freight movements, eliminate waiting times and enable efficient resource allocation, are increasingly important.
Airfreight industry observers are beginning to ponder whether better than expected air cargo data for August could auger a better-than-ex pected peak season. CLIVE Data Services, part of Xeneta, has been crunching the numbers as thinks the global air cargo market perfor mance data for August offered a glimmer of hope for volumes in the upcoming peak season as the decline in demand seen over the pre vious four months slowed, according to their latest weekly analysis.
The obvious point to make is that every kilo of airfreight flown, maindeck or belly, has to be handled. After -8% and -9% year-on-year
falls in demand in June and July 2022, August volumes were a more modest -5% adrift of the August 2021 level and -4% compared to the pre-pandemic 2019.
Despite continuing transportation and supply chain chaos resulting from staff shortages in airports and airlines, global air cargo capacity in August recovered 7% from the same period last year, thanks to the surge of international summer travels in the northern hemisphere. It also continued to narrow its recovery back to the market capacity level seen in 2019, now just 9% away.
The air cargo market, however, remains chaotic and difficult to pre dict. Ongoing disruptions due to a lack of people resources, the war in Ukraine, industrial action, natural disasters, reports of record inven tory levels in the US, high inflation and more Covid-related lockdowns in cities in China – the ‘factory of the world’ for so many products – promise more air cargo market volatility over the rest of the year.
In order to improve air cargo ground handling operations, IATA has developed a Master Operating Plan which describes the key process es and sub-processes involved in transporting air cargo from shipper to consignee in a systematic and harmonised manner. It provides the air cargo supply chain with the first, industry-endorsed, standard de scription of the end-to-end process for transporting cargo by air.
The plan comprises 19 main processes and 78 sub-processes split into five categories of activities as follows: Origin forwarder; Origin carrier; Transport carrier; Destination carrier; and Destination forward er. The plan supports the primary objective for air cargo acceptance and handling is to ensure that consignments are ready for carriage in compliance with operator and IATA regulations, as well as with export and import rules of the countries through which the cargo will transit. In general, all items to be transported using commercial aircraft must pass through an acceptance process.
IATA’s Cargo Handling Manual (ICHM) is a publication of the most current recommended practices for airline stakeholders to follow. It gives all the required documentation in an accessible step-by-step format. It was developed by an IATA council named the IATA Cargo Handling Consultative Council founded in 2011 by the Cargo Advisory Council.
The IATA Cargo Handling Manual covers all working instructions door to door, from shipper to consignee, with a strong focus on air port to airport activities where cargo handlers and airlines operate, according to André Majeres, cargo mail & e-commerce operations manager at IATA.
The current issue contains 19 chapters in line with the plan. It in cludes the most up-to-date regulations regarding cargo handling and 10 appendices to expand on the subject.
If the air cargo handling sector has a motto, it has to be this: “If it flies, it has to be handled.” This supplement will look at some of the key play ers and how they go about, on a daily basis around the clock, safely and securely handling the cargo traffic the airlines move.
By involving all stakeholders, Swissport feels it can create a solu tion that will benefit all.
Dirk Goovaerts, head of Continental Europe, Middle East and Africa and Global Cargo Chair, speaks for the industry when he acknowl edges that the pandemic affected the whole aviation industry, including cargo services. However, it was the cargo segment that allowed the stakeholders to continue to operate – the delivery of goods, whether we talk about food supplies or vaccines or other re quired products – was a necessity and those had to be shipped fast and in a secure way.
He says: “The Covid pandemic has brought many changes to air freight shipping generally, and cargo handling specifically. Not least, the pandemic has further spurred the move towards greater digiti sation. Examples are Swissport’s Kiosks, ULD tracking and the Mobile Cargo Application. This new app has been rolled out in over one third of Swissport’s cargo centres, where it improves efficiency and captures milestones.
“Airport cargo communities have also always been important to Swissport, and their importance became all the clearer when ship ping high volumes of vaccines, amongst others through Swissport’s Pharma Centres. Swissport supports such communities in places such as Brussels, Frankfurt, Amsterdam Schiphol, Nairobi, and Jo hannesburg. These advances are changing our industry, and in that sense, it will not return to how it was in 2019.
“I am a great supporter of creating cargo communities – by involv ing all stakeholders we can create a solution that will benefit all. The exchange of know-how, experience and expertise allow us to be a leader in a constantly changing environment,” adds Goovaerts. In terms of bellyhold capacity, they change constantly due to vari ables, such as political conflicts and restrictions, safety restrictions or simply changing customer driven environment. Transatlantic capaci ty has increased and is almost at pre-COVID-19 level, whilst the cargo services between Europe and Asia are subject to some COVID-19 re strictions and higher cost due to the conflict in Ukraine.
Swissport applied extensive measures to keep as much staff as possi ble during the pandemic. In the locations at which its cargo handling and volumes increased Swissport is actively looking for additional staff to provide excellent customer service to clients. It has launched a bespoke global recruitment campaign, which has shown great results.
“Our people drive our success, and constraints on the labour mar ket continue to pose challenges when finding suitable and sufficient staff. We set ourselves apart by embracing diversity and providing an inspiring and innovating workplace. Moreover, Swissport is fully committed to gender equality – not only did we join IATA’s 25by2025 initiative that aims at 25% women holding senior management po sitions, Swissport also released their internal target for having 40% female employees,” says Goovaerts.
Swissport handled 5.1 million tonnes of cargo last year, up by nearly
10% on 2019 and a hugely impressive 24.9% on 2020. Swissport is active at 287 airports worldwide and operates over 120 air cargo cen tres. This includes 16 IATA CEIV or otherwise certified Pharma Centres. Swissport’s total warehouse area globally exceeds 79 soccer fields.
Goovaerts says: “A continued focus on airport communities com bined with many initiatives in digitising our industry is something that we consider to be very positive. These improvements in efficien cy help us further analyse and develop our business, attract talent, and improve the services towards our customers.
“In my role as Global Cargo Chair I am in a privileged position of supervising all innovation and digitalisation projects aimed at the development of our cargo segment. We are pursuing several ground breaking projects that will benefit our staff by creating a technology and automation-driven environment; and our clients, by providing more efficient and tailored solutions,”
Swissport is trialling a range Speedcargo’s suite of products in Tel Aviv and Johannesburg. These are designed to help improve pro ductivity and maximise logistics efficiency. The Cargo Eye captures accurate dimensions and images of incoming cargo in real-time, and seamlessly integrates data into existing warehouse management systems, while the Cargo Mind is an AI-supported software solution that plans for optimal cargo space utilisation in seconds, while adher ing to regulations and business constraints.
“The airlines that took part in the trials provided a very positive feed back – the solutions maximise the efficiency the clients are looking for in this very competitive market. We are now finalising the trials and preparing for the rollout across other stations,” says Goovaerts. Specialist types of traffic
At over 120 cargo centres worldwide we specialise in many different types of cargo. While traditionally general cargo holds the largest share, Swissport facilities focus on e-commerce, oversize and out size cargo, pharmaceuticals, perishables, live animals and dangerous goods, spread all over the world.
“We are also pioneers in creating the perishable goods corridors: a farm to end customer supply chain which involves all stakeholders and that strictly conforms to the required handling procedures, pro longing the product’s shelf life and maximising the quality of cargo.
“We operate air cargo warehouses directly connected to the apron, where we often also provide ramp services, and second line facili ties. Several of these include highly complex and advanced material handling systems, such as in Frankfurt, which further optimises the handling process.
“Swissport has recently announced extensive new sustainability goals to support long-term development and success. These goals include the de-carbonisation of its operations, waste management and circularity, and diversity and inclusion among our people. As a global market leader, we want to set the benchmarks. In air cargo handling, Swissport plans to introduce mandatory waste-avoidance as part of its waste-management policy, to be rolled out at all of its120 air cargo centres by 2027,” adds Goovaerts.
“Our people drive our success, and constraints on the labour market continue to pose challenges when finding suitable and sufficient staff”
COVID-19 reminded the world, and our own industry, of the vital im portance of air cargo both in world trade and emergencies. That is the reflection of Wilson Kwong, chief executive of Hactl in Hong Kong.
During the pandemic, freight rates rose in response to an excess of demand over supply, but are now stabilising as capacity returns and demand cools. Air cargo is at all times an expensive commodity to pro duce, involving major capital investment and commitment, particularly by handlers and freighter operators.
“We must be careful not to repeat the mistakes of the past, by re turning to predatory pricing and so undervaluing our product. This will stifle the investment that has only recently started to happen through out wider areas of our industry, after decades of enforced neglect,” says Kwong.
For Hactl, COVID-19 inspired greater urgency in the digitisation and automation of processes.
“We changed our operational model to accommodate remote work ing for all admin staff, which necessitated abandoning all remaining paper processes and minimising physical meetings for instructions, ap provals and so on. We had been moving in this direction for some time, so these final changes were readily achievable,” says Kwong.
“Resilience in the face of potential significant staff absenteeism through illness, or enforced quarantines as an anti-contagion measure, also became a key issue. Effectively, we had to ensure that Hactl could continue its mission-critical services even when manpower levels were reduced. This led us to bring forward the creation of iHCC (Integrated Hactl Control Centre), which centralised all management functions and controls for the first time, enabling shift managers to monitor every aspect of our operation in real time, and make instant, well-informed decisions about resource deployment and optimization. iHCC was a
major support in 2021 when we suffered up to 40% reduction in ramp workforce through quarantine, yet successfully continued working with minimal impact on performance.”
These, and other measures such as a new digital ramp management processes, have fundamentally changed the way Hactl works and result ed in a more efficient and resilient Hactl operation for the future. These are steps that are necessary throughout the wider industry.
At present, Hong Kong airport has not returned to pre-pandemic pas senger flight levels and cargo capacity. The recovery is proceeding steadily, but it will still take some time to return to anything like the old scenario. Meanwhile, freighters, always important to Hactl, continue to provide a greater share of all capacity and represent a larger share of Hactl’s business.
Kwong says: “This picture varies around the world but, in Hong Kong, we expect this trend to continue long into the future, as any long-term shortfall in passenger bellyhold capacity must be replaced by freighters.”
Hactl is always hiring. During the pandemic, no staff were made re dundant although Hactl lost some through natural wastage, such as retirement. But recruitment for airport jobs in Hong Kong is challenging, because Hong Kong has almost full employment, and jobseekers can choose. They tend to favour work which is not based so far out of pop ulation centres, this does not entail unsocial hours and does not involve outside working in sometimes extreme weather. Increased automation will have to help Hactl solve this problem, as more efficient working and increased productivity are already doing.
In 2021, Hactl topped two million tonnes, some 18% ahead of preCOVID levels. That was exceptional, and so 2022 will not continue this trend, especially as consumer markets are dampened by cost-of-living
problems in developed markets. The market should stabilise and re turn to growth in later 2023.
Hactl’s entire handling business is based in Hong Kong, while its subsidiary Hacis operates an RFS network between nine locations on the Chinese mainland, where it has inland cargo depots.
In Hong Kong, Hactl was once the sole handler. There are now four cargo handling concessions on airport. Hactl has a 40% market share, serves over 100 carriers and 100 freight agents and is the largest in dependent operation: that is, as not a handling carrier.
Kwong is seeing more and more evidence of digitisation, following some of the initiatives Hactl spearheaded in recent years. This is es sential, as it will form the basis of the digital supply chains that will link separate service providers in a digital supply chain, enabling all in the “traditional” air cargo industry to collectively offer the efficiency, visibility and controls that e-commerce particularly demands, and which integrators offer as standard.
Kwong considers: “We currently use AI in our data systems, to detect and prevent any cyber attacks. Such security measures are essential when you move from an internal LAN (local area network) to a WAN (wide area network) model, as we have done.
“AI is also deployed in the management system for our giant Container Storage System; new algorithms developed in-house are enabling our system to make more sophisticated decisions about where to store the many different types and sizes of pallets and con tainers in our 3,500-ULD-capacity system. This has boosted capacity by around 10%, which is a valuable resource when you are handling cargo for often 100+ freighters daily.”
Hactl has highly-developed facilities for every conceivable cargo
type, including outsize cargo, aero engines, pharma, perishables and all kinds of live animals. It is accredited under all applicable industry standards and was the first terminal operator globally to achieve all IATA’s first three CEIV standards - Pharma, Perishables and Live.
Hactl’s Superterminal1 base was opened in 1998 at an unprece dented cost of $1 billion, and has been regularly upgraded since. Key features are: 395,000 sq m floor area; 3,500 bay, multi-level Container Storage System, served by 40 fully-automated driverless ATVs; addi tional storage for 1,573 empty units; 10,000 bay automated stillage storage/retrieval system for loose cargo (Box Storage System); more than 466 pallet workstations; 313 truck docks; 2,100 staff; facilities for temperature-controlled cargo, livestock/bloodstock, perishables (30 dedicated truck docks), valuables (dedicated zone for handling nine armoured vehicles simultaneously), aero engines, outsize cargo and hazardous/radioactive cargo; more than 1,000 CCTV cameras through out; card-controlled access; personnel-free cargo storage zones; centralised control suite (iHCC) deploying cutting-edge technology to display operational status; and a design capacity of 3.5 million tonnes per annum.
Liège Airport-based Challenge Handling has a positive business atti tude that is putting it ahead of the curve. That is the thought of David Alexis, general manager of Challenge Handling.
It might be counter-intuitive, but David Alexis is quietly positive about how his company has come out of the pandemic. He says: “Ac tually, the pandemic accelerated our growing plans that were already underway. Our staff were seen as heroes as they were coming every day to meet the needs of the hospitals and the people in terms of PPE. We managed to keep our employees involved and motivated by making them realise that their job was essential to the world, the country, the region.
“During the pandemic, we had one of the lowest absenteeism rates of our history which demonstrates the commitment of our teams to work through the difficult conditions brought on by the pandem ic. We are always ahead of the curve in putting in place proper and strong measures to ensure the safety of our working environment. It was a team effort, with all workers and social partners, playing a key role as real partners in the development of our company.”
He is keen to point out that implementing a successful expan sion strategy involves finding and attracting the potential resources for fulfilling the mission and ensuring that activities are carried out seamlessly.
“We were 86 people at Liège Airport in January 2006, we stayed at an average of 150 until six years ago and we have now more than 500 full-time employees working in Liège.
“As a group consisting of seven different entities, our staff have op portunities for internal moves and this gives us a huge advantage in retaining our staff and keeping them motivated to learn new skills to develop themselves within the group.”
Alexis says: “We have a good mix of all the commodities. Seventy per cent of the cargo we handle is vertical cargoes involving live animals, dangerous goods, oversize, oil & gas, perishables and pharma com modities. When it comes to figures, we handle 7,000 horses per year; more than 1,000 tonnes of perishables per week, around 200 pharma shipments per month. Of particular note is that we carry oversized cargo on nearly all of our flights: centre-load-cross-load- 40 ft – 30 ft –overlaps are part of our daily core business and as such have become our specialty.
“As an example, we recently handled and loaded a rotor of 94 tonnes. We have one of the largest high lift loaders in Europe which can up lift up to 52 tonnes in one go. We are also specialised in dangerous
goods: we are indeed the sole handler in Belgium for the handling and storage of fissile material and the exclusive handler of electronic manufacturer RADAC in Liège Airport.”
The capacity of Challenge Handling in Liège is 425,000 tonnes. A strategic expansion plan before the pandemic has accelerated it. In December 2020, Challenge Handling opened its new, state-of-the-art second line warehouse facility of 10,500 sq m and in January 2022, it launched its second frontline warehouse of 12,000 sq m in the north apron of the airport.
“We have now two frontline facilities (one in the north and one in the south of Liège airport) and one second line facility (for import and forwarder handling) with a total area of 42,000 sq m. This enables us to offer our customers the biggest flexible handling platform in Liège,” he says.
There are further development plans such as building a stacker system of 400 ULDs, including temperature-controlled rooms, in the front-line north building. The south platform is already equipped with a stacker system of 300 ULDs and a second line facility has also a stor age caster deck capacity of 200 ULDs.
Alexis notes: “This will help us to handle half a million tonnes of cargo annually.”
For Liège, Challenge Handling is planning to extend its north frontline and warehouse by adding a stacker system. It also has plans to dupli cate the Liège model in foreign countries such as USA in the very near future. This will provide Challenge Handling with additional hubs to offer customers the same high handling standards in place in Liège.
Challenge Handling is specialised in the daily handling of a huge variety of very special and complex cargo. It recently handled 7 B-747 charters featuring stage material from Ramstein’s band for their US tour, two full charters of five star jumping horses for the Longines Global Champions Tour event in New York, one rotor of 94 tonnes shipped to Turkey, philharmonic concert equipment to the US, one Ferrari F1 driven by Michael Schumacher….and “the list can go on”, says Alexis.
Challenge Group Airline activity represents 55% of total activity at Liège, 45% of its activity is generated by other business partners and the handler keeps increasing this percentage as it has a lot of capacity to offer, both in front and second line facilities.
Not only does the group offer handling, but also logistics solutions, such as trucking, via Challenge Logistics, aircraft capacity via Challenge Air Cargo and online aircraft maintenance via Challenge Technic.
Guillaume Crozier, senior vice president, UAE Cargo, dnata is seeing a recovery in handling activity as the world returns to some sense of nor malcy post-pandemic.
Crozier says: “We are actively recruiting to respond to the rebound in passengers, flights and the continuing strength of our cargo business. In recent years we have invested in our staff, in training to reskill and up skill our core workforce and be able to flexibly adapt our operations to a changing operating environment. As a result of our commitment to our staff over the past years, we are well placed to meet the staffing challeng es facing the industry.”
In the UAE, dnata provides cargo services at the two Dubai airports, Dubai International (DXB) and Dubai World Central (DWC). In the financial year 2021-22 teams handled more than 700,000 tonnes of cargo at the two Dubai airports – 3% more than in the financial year 2019-20.
There has been a massive growth in import general cargo volumes, including fashion accessories, electronics and fast moving consumer goods. Among the various categories of cargo, mail and courier have shown steady increases as compared to pre-pandemic volumes, indicat ing a rising trend with e-commerce shipments.
“There have been significant investments in digitalisation and inno vative technologies that enhance efficiencies across the industry,” says Crozier.
“We will continue our digital transformation journey to provide the best possible services to our customers through advanced solutions. We will launch a next-generation air cargo community platform which will take CALOGI, our existing community platform, to a whole new level.
“In addition to offering a highly integrated, cost-effective trading plat form, it will deliver a number of significant benefits for air cargo supply chain stakeholders, including general sales agents, airlines, ground han dlers, forwarders, road feeder services and third-party logistics providers. It will allow stakeholders to conduct business with their customers and interact with authorities on one platform, sharing information and set
tling payments using their CALOGi credit account.
“Customers will be able to integrate the platform into existing work flows through APIs and take advantage of all innovative functions while using their own system. The platform will also help customers simplify existing processes, without investing in multiple systems. Furthermore, it will enhance sustainability by promoting paperless and cashless trade through collaboration and automation.”
In addition, dnata will launch autonomous drones in its warehouses at DXB and DWC airports to digitise acceptance and warehouse inventory processes by monitoring shipments with 99.8% accuracy.
dnata’s partner’s innovative software enables the drones to map the environment, collect inventory data, count cases, measure temperature, and read barcodes using only their cameras, without the need for any additional active infrastructure. The drones are paired to a tablet device providing live inventory data. The collected data can be viewed directly on the tablet or the web, via a user-friendly application. The drones can operate at temperatures as low as -10 degrees Celsius degrees, enabling us to take advantage of the technology in our state-of-the-art cool chain facilities, too.
dnata already uses AI through various tools across its business and looks forward to further digitising its operations by the beginning of 2023 by launching the state-of-the-art ‘OneCargo’ Terminal Operator Solution developed by IBS.
OneCargo automates key business and operational functions, includ ing safety and quality monitoring, reporting and ULD management, with an integrated, cloud-based platform. AI-driven tools and analytics provide enhanced visibility on sales and business performance, allowing customers to match real-time demand with available capacity for maxi mum profitability. In addition, OneCargo eliminates all redundancies and manual check sheets, substantially improving operational efficiency.