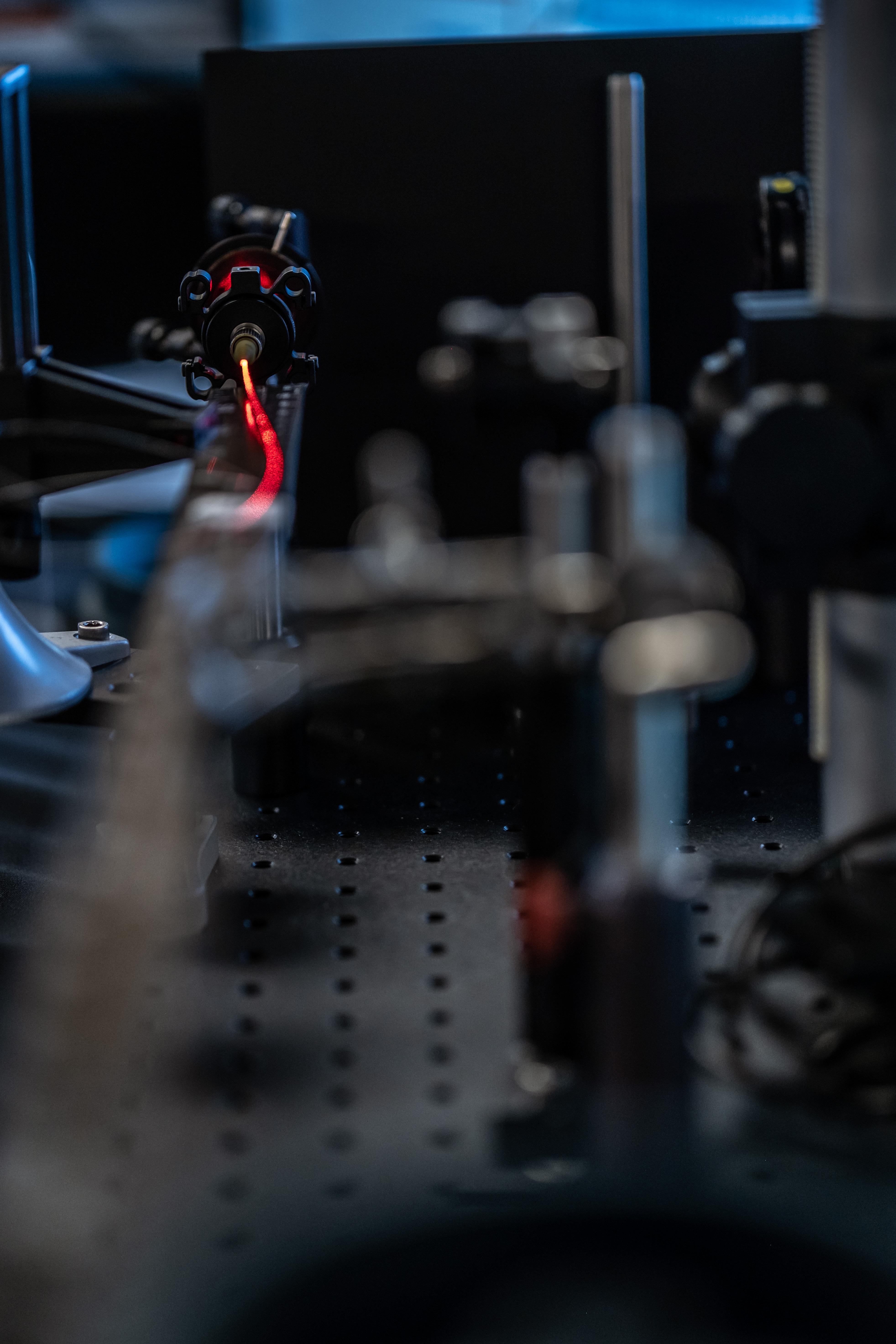
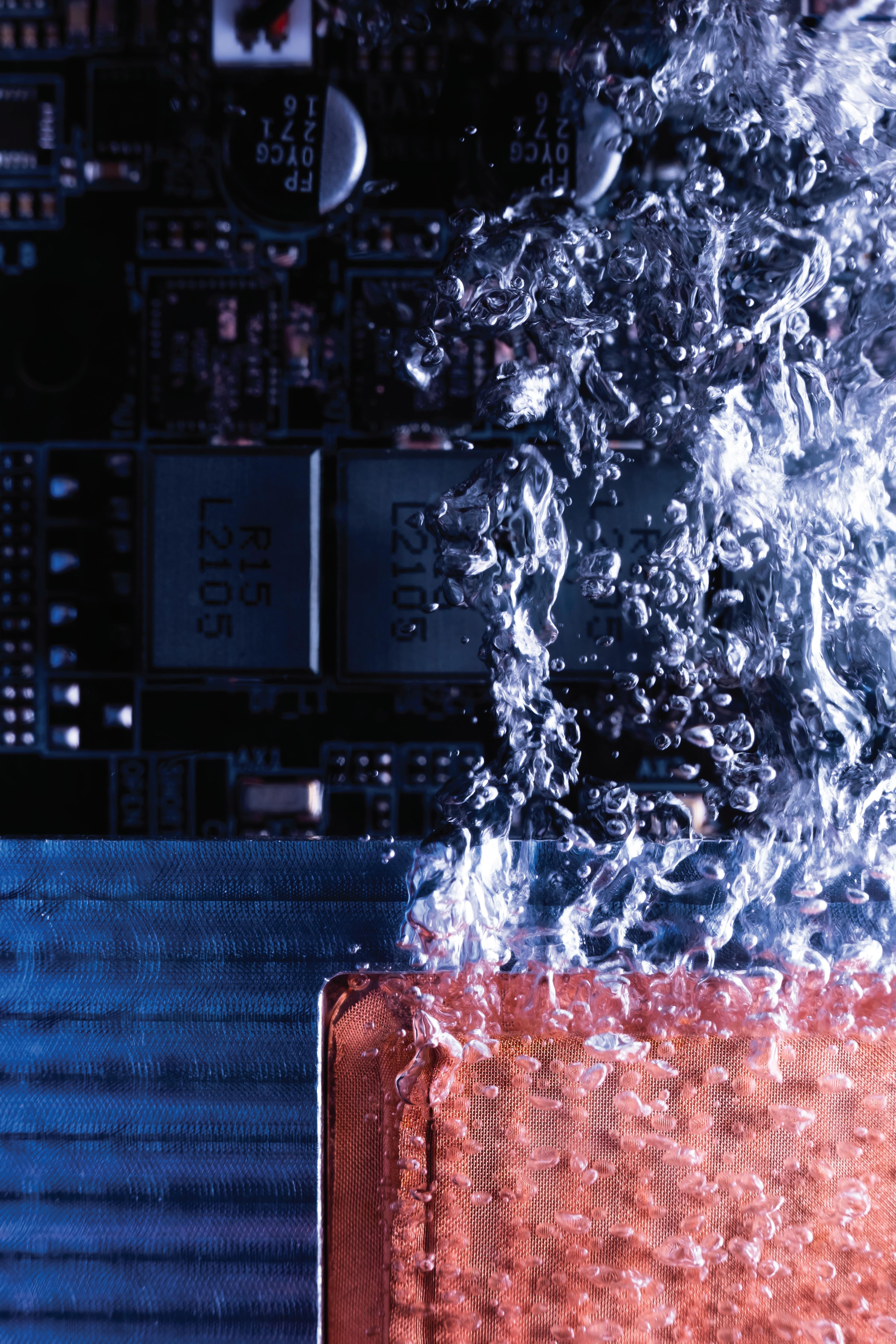

Teams display projects ranging from a crop-monitoring robot to a carpal tunnel treatment bracelet.
Craig M. Berge Design Day is a story of remarkable student success and all the ways engineers help people.
With 91 incredible capstone projects, 70 dedicated project sponsors, 125 seasoned industry judges, and $49,000 in prize money, I am so proud of this year’s Design Day.
As they looked toward professional careers, graduate studies and entrepreneurial endeavors, 470 seniors collaborated in labs and workshops on smart energy technology, medical devices and surgical tools, space systems and aircraft improvements. Their designs are a testament to the technical agility and creativity of our students and mentors.
Teams developed ways to 3D print entire structures using mine tailings and make ethylene from vodka production. They designed systems to test, reclaim and treat water, and plans for a plastics recycling plant. Students created crop-monitoring and basketball-playing robots; rocket launchers and lunar rovers; first-responder reconnaissance and ocean-monitoring drones. They refined a throw phone for crisis negotiations, designed a Coast Guard dispatch system, and prototyped an aesthetically inspired grab bar.
These feats of engineering show why the college’s graduates are highly sought after in industry and government.
Don’t be shy about asking questions as you take in the dazzling displays of ingenuity. Students are thrilled to tell you about these fantastic projects they’ve worked on throughout the academic year. There is a lot to see! If you miss anything, you can learn about the projects in the students’ presentation videos, which will be available online (b.link/DesignDay2024) following the awards ceremony.
Join us for the 4 p.m. Design Day Awards Ceremony, where standout seniors will collect 35-plus prizes in all, from the Fish Out of Water to the Most Outstanding Project.
Design Day and the Interdisciplinary Capstone Course are part of a lineup of competitions, maker fests, major-specific design classes, entrepreneurial and business mentorship, and industry and community projects in the Craig M. Berge Engineering Design Program. The program immerses undergraduates at all levels in real-world experiences that integrate design, manufacturing and commercialization.
We are especially grateful to the donors, program mentors, university and industry partners, sponsors, judges, faculty, staff and alumni who help make the design program and Design Day a highly successful enterprise.
I’d like to extend a special thank you to Nancy Berge and her family for their generosity, and to Larry Head, director of the Craig M. Berge Engineering Design Program, for his commitment to an unparalleled experiential learning program and design curriculum in higher education.
Bear Down, and support our Wildcat engineers!
David W. Hahn
Craig M. Berge Dean, College of Engineering
91
125+
19
$49,000
470
It’s exciting to see how brilliant engineering students are today. I have full confidence that the future is in good hands, and I will be proud to hand over the reins to the younger generations.”
MANNY MIERA, alum, CEO of PeakView Solutions, SPONSOR ADVISOR “
This award recognizes the project that embodies the best attributes of engineering design and the engineering profession. The winning project shall have an outstanding design approach and implementation, excellent system modeling and/or analysis that support the design, comprehensive system testing that verifies system requirements, and a superior presentation of results to Design Day judges. Team members of the winning project shall present themselves professionally and clearly demonstrate engineering knowledge of the design. The winning project shall clearly be the best project at Design Day.
While several designs may meet the judging criteria, this award is given to the design that does so the most effectively. The project that receives this award excels in many ways. The design is well thought out, and its implementation is of high quality. It accomplishes all key design requirements and is supported by rigorous analysis and testing. Its poster and presentation are professional and easy to understand.
Bly Family Award for INNOVATION IN ENERGY PRODUCTION, SUPPLY OR USE (1st prize - $2,000; 2nd prize - $1,000)
This award recognizes the best project related to sustainable, cost-effective and environmentally friendly energy production, distribution or use. Winning projects could focus on developing new energy sources, reducing energy costs, improving efficiency or reducing cost of energy distribution, adapting existing energy distribution methods to better integrate new energy sources, and increasing efficiency of energy use.
BAE Systems Award for BEST SYSTEM SOFTWARE DESIGN ($2,500)
Software has become an integral part of the operation, management and control of complex systems comprising mechanical, electrical and optical elements. This award recognizes the best use of software in a system design to enable task automation, object recognition, system robustness, data collection, or other impressive features that would be difficult to achieve without software. Teams will be judged on the reliability, robustness, maintainability, reusability, originality and testability of software embedded in their designs.
L3Harris Commercial Aviation Solutions Award for MOST ROBUST SYSTEMS ENGINEERING ($2,500)
The systems engineering perspective is based on systems thinking. When a system is considered as a combination of system elements, systems thinking acknowledges the primacy of the whole (system) and the primacy of the relation of the interrelationships of the system elements to the whole. This award goes to the team that most robustly addresses all aspects of the project from the systems perspective.
The French philosopher Voltaire is credited with the saying “Le mieux est l’ennemi du bien,” which means “the best is the enemy of the good.” Similarly, Leonardo da Vinci is credited with the saying “Simplicity is the ultimate sophistication.” This award recognizes the design team that best emulates these ideals and resists the temptation to overly complicate the design to yield a clean, simple, elegant, lowest-cost design that simply works well.
This award recognizes the most innovative use of optoelectronics and optomechanics in a design and is given to the team that demonstrates the most thorough approach to the design and engineering of its optical system. This award recognizes complete understandings of the optical design, system requirements, tolerance analysis, and optical component usage. Important criteria are integration of optics into the overall system, novel use of optical components, creative use of commercial off-the-shelf items, verification of optical components, meeting system requirements, use of standard optical design software, and manufacturability of optical design and components.
Rincon Research Award for BEST PRESENTATION ($1,500)
This award reflects the quality of the overall verbal and poster presentations. Verbal presentations should be well structured to describe efficiently the overall problem being solved and the specifics of how the team accomplished its design. Answers to questions should be direct and demonstrate mastery of the project. Presenters should speak in a clear and easily audible voice, making good eye contact with the judging pod. The poster board should be visually interesting and graphically well organized to tell a standalone story of the project.
School of Mining and Mineral Resources Lowell Award for INTERDISCIPLINARY SOLUTIONS FOR MINING ($1,500)
The Lowell Award recognizes the best interdisciplinary solution that supports the mining industry. Whether it is the improvements of optics and visibility for safety, reducing personnel exposure while working in the mine or mill, developing the next generation of high-altitude drones for mineral surveys, or a novel way of extracting minerals from space, this award requires the skills of all engineering disciplines. While expanding new frontiers in resource development, the winning team will demonstrate how it’s design solution will make quantifiable improvements to safety, the community, and the environment.
School of Mining and Mineral Resources Lundin Award for INNOVATION IN MINING ($1,500)
The Lundin Award recognizes design innovation in the safe and economical extraction of mineral commodities. Key focus areas for this reward include a written, well-documented mineral resource report, a well-developed mine plan, and an economic model to demonstrate the project’s viability. True innovation will illustrate the sustainability of the resource and its relationship with the environment and community. The written report and oral presentations for this project should demonstrate collaborations across the team members’ disciplines.
Innovation may include the novel use of existing components or the creation of entirely new components to meet customer requirements. The most innovative design will not only be a creative solution to a problem but also an effective solution that is well implemented. This award recognizes the team that has created or made use of components in the most innovative way, or demonstrated excellence in the implementation of innovative design in its project, or both.
W.L. Gore and Associates Award for LIFELONG INNOVATION ($1,250)
This award honors a student team that has demonstrated excellence and innovation in biomedical engineering design. It recognizes outside-the-box thinking that pushes boundaries and hands-on approaches to creative solutions. Projects are judged on the elegance and creativity of the technical solutions and their implementation. Teams should be able to communicate effectively their design, express how it will improve lives, describe the current environment or paradigm, and generally speak toward the economic reality of a possible implementation.
Mark Brazier Award for BEST BIOMEDICAL SYSTEM DESIGN ($1,000)
Biomedical engineering is a discipline that advances knowledge in engineering, biology and medicine, and improves human health through cross-disciplinary activities that integrate the engineering sciences with biomedical sciences and clinical practice. This award recognizes the team that has demonstrated excellence and innovation in biomedical engineering design. It recognizes outside-the-box thinking that pushes boundaries and hands-on approaches to creative solutions. Projects are judged on the elegance and creativity of the technical solutions and their implementation. Teams should be able to communicate effectively their design and the processes they use for creativity.
($1,000)
This award goes to the team that best considers the needs of the end user/client. Team members should demonstrate that they considered the end user’s needs throughout the design process. The team should have a list of end user concerns and show how they addressed them. Many times, a physical prototype is created to understand and study the fit, form and function of the device or system and usability testing is conducted with a sample group of end users to validate or improve the design. Teams are judged on the appropriateness of the prototyping used, how effectively prototyping is used to improve the design, and how well the needs of end users are considered. Prototypes can be made using rapid fabrication technology, traditional manufacturing, or can be hand built.
Successful implementation of any innovative design requires that all members of the design and production team communicate effectively. Design intent must be communicated from the design activity to the rest of the team using design documentation with a clear map for others to reproduce the design based on documentation only. The mechanical portion of the design is evaluated on the use of drawings with geometric dimensioning and tolerancing, solids models, illustrations and presentations that can be used to manufacture and inspect design hardware. Software and other systems are evaluated on the use of documentation that clearly and fully describes the system and illustrates the approach to testing.
This award recognizes the single-discipline design team that best demonstrates external team collaboration. Like real-world problems, senior design projects require skills from multiple sources, and students should learn the value of leveraging the strength of a diverse team as well as seeking out external guidance and support to succeed. These skills are foundational to a successful engineering career.
IEEE Tucson Section Award for BEST USE AND IMPLEMENTATION OF ENGINEERING STANDARDS ($1,000)
IEEE is the world’s largest technical professional organization dedicated to advancing technology for the benefit of humanity. IEEE and its members inspire a global community through its highly cited publications, conferences, technology standards, and professional and educational activities. IEEE is a leading developer of international standards that underpin many of today’s telecommunications, information technology, and power-generation products and services. This award recognizes the team that best shows the standards used in its project and how the use of those standards facilitated or improved it’s overall design and/or its performance outcome.
Mensch Foundation Award for BEST USE OF EMBEDDED INTELLIGENCE
($1,000)
The Mensch Prize for Best Use of Embedded Intelligence recognizes the engineering innovation team that best integrates embedded intelligence into a potential commercial product. Specifically, the award will be granted to a student team that has built a smart connected prototype that may have a commercial market. Embedded intelligence is characterized as the ability of a product to sense, process, communicate, and actuate (SPCA) based upon information gained from an understanding of both itself and others and for the benefit of many. Preference will be given to designs with SPCA capabilities that can demonstrably surpass human abilities to perform the same function.
($1,000)
This award recognizes the interdisciplinary team that creates the best video telling the project story. The video must capture the sponsor’s need, the process the team followed to develop the solutions, the final solution including test and evaluation, and how it meets the sponsor’s needs.
($1,000)
This award recognizes excellence in overall system design in a project that has an aerospace emphasis. Verbal presentations should be well structured to describe effectively the overall electronic system and the specifics of how the team implemented its design project. A key feature of the presentation must be representative data that demonstrate how the system was thoroughly tested. Answers to questions should be direct and demonstrate a high level of team competency about the details of the electronic system for the project. The presentation should demonstrate how all members have contributed to the project to exhibit core values of teamwork and professionalism.
This award recognizes excellence in overall mechanical system design in a project that has an aerospace emphasis. Verbal and written presentations should be well structured to describe effectively the overall system and the specifics of how the team implemented its design project. A key feature of the presentation must be representative data that demonstrate how requirements were analyzed, documented, designed against and tested. Answers to questions during the presentation should be direct and demonstrate a high level of team competency about the details of the mechanical system for the project. The presentation should demonstrate how all members have contributed to the project to exhibit core values of teamwork and professionalism.
Steve Larimore Award for PERSEVERANCE & RECOVERY ($1,000)
Issues and roadblocks always occur during the engineering design process. Although they cause panic and distress, they also represent great opportunities to learn and often lead to designs that would otherwise be impossible to conceive. This award recognizes a team’s ability to learn and to overcome issues or roadblocks encountered during the design process. The award is judged based on the ingenuity of solutions to problems caused by issues or roadblocks and the features in the final design that contribute to recovery from them.
for
This award celebrates pioneering projects that harness cutting-edge technologies to drive innovation in software development. This award will recognize a project that effectively integrates emerging technologies such as artificial intelligence, machine learning, DevOps (or DevSecOps), augmented reality or virtual reality (AR / VR) or other forms of automation and innovation into its software solution. Whether it’s revolutionizing user experiences, optimizing business processes, or pushing the boundaries of what’s possible in software engineering, this award highlights the transformative impact of embracing emerging technologies in the realm of software development.
($750)
This award goes to the team that best uses a physical prototype model to understand and study the fit, form and function of the device or system designed. Teams are judged on the appropriateness of the prototyping technology used, how effectively prototyping is used to improve design, and how effectively the use of prototyping is communicated. Prototypes can be made using rapid fabrication technology, traditional manufacturing, or can be hand built.
($750)
The Internet of Things is estimated to currently encompass over 15 billion devices and projected to double in the next six years. This award recognizes the team that best integrates modern IoT hardware, networking, data storage, and data analysis in a data acquisition and control system. Data acquisition should involve at least two sensors and a communication protocol while feedback and control should be provided by algorithms, analysis and actuators. Projects are judged on utilization of IoT devices and connectivity to provide simple, robust and efficient data acquisition and control to accomplish all or part of the project requirements.
The Fish Out of Water award congratulates students for successfully accomplishing a task that was not in their realm of expertise. The projects for senior design require skills from many disciplines, and students must sometimes learn a new subject or skill in an area outside of their major to help the team succeed. A student who not only learns this new subject or skill, but also uses it to effectively help the team thrive, shows dedication and initiative, traits that will continue to help in an engineering career.
($500)
This award recognizes the project that makes the best use of computer-based simulation or modeling. The simulation may be the project itself, or a design tool used to model the performance of the project design. Criteria for this award is based on scope of the simulation, the fidelity of the simulation compared to real-world performance, and the engineering judgment exercised in determining the complexity of the model.
Frank Broyles Award for BEST UAS DESIGN ($500)
This award recognizes the UAS project with the highest quality of design and construction that succeeded in, or made a good attempt to, achieve the sponsor objectives.
Frank Broyles Award for ENGINEERING ETHICS ($500)
Increasingly businesses are adopting cultures that emphasize ethical conduct. This is driven in large part by the dollar value financial markets place on business reputation. Using questionable shortcuts to save cost or time are a practice that can have catastrophic consequences. Similarly, the marketplace can punish a business that ignores or inappropriately resolves conflicts. In addition, an individual might experience a significant conflict with other team members, or between the individual and sponsor or mentor. The award will be given to a team that identified and resolved, or did not resolve, an ethical issue faced during the design and creation of the project.
Lawrence Livermore National Laboratory Award for IMPACTFUL APPLICATION OF SCIENCE & TECHNOLOGY ($500)
This award recognizes the team that “thought big” and applied cutting-edge science and technology to make an impactful difference in the world – an enduring principle of LLNL.
AZ Technica MANUFACTURING READINESS Award ($500)
This award is given to the team that designs and builds a system that goes beyond meeting sponsor requirements and best considers usability and manufacturing readiness. Teams will be judged on manufacturing readiness of the design using the following considerations:
a) Design process considered alternative designs and selected the best choice that meets or exceeds all of the sponsor requirements and can be used immediately by the sponsor.
b) Design considered producibility, ease of assembly and cost.
c) Design showed consideration for reliability and maintainability issues while in the design/model/prototype phases as well as build phases.
d) Design considered user operation and included operator instructions.
e) Design technical data package was complete.
Dragoon Technology Award for MOST UNINTUITIVE DESIGN DRIVEN BY PHYSICS
($500)
Some designs are intuitive. But sometimes, application of basic physics results in a design that might – without an understanding of the underlying principles – be rejected or even laughed at. This award recognizes a design that only an engineer could love.
AZ Technica Award for SUSTAINABLE MANUFACTURING INNOVATION
($500)
This award is given to the team whose design incorporates the most innovative manufacturing method addressing reduced carbon emissions. Projects could include introducing a new technique for manufacturing or an innovative use of an existing technique that reduces the cost and improves the quality of a product while reducing carbon footprint.
Honeywell Award for TEAM LEADERSHIP
(two individuals at $250 each)
This award recognizes students who best exemplify teamwork skills, including the ability to work cooperatively with others to produce high-quality work, to take the initiative, to support and respect the opinions of fellow team members, to give and receive feedback, to demonstrate effective leadership, to keep their team focused, and to elevate the work of their fellow team members. Nominees for this award are selected by their teammates.
The student team is amazing, and we have seen the benefits of working with them both for advancing an engineering challenge but also to source future talent.”ABRAHAM JALBOUT, CEO of Auxilium Technology Group, SPONSOR ADVISOR
Integrated Grab Bar/Chair Rail System
Plastic Recycling, Carbon Capture and Disaster Relief Through Pyrolysis
Automation of Mirror Distortion Measurement Device
Modular Automatic Camera Focusing System
Mechanical Energy Storage System
Five Hole Probe for Three Dimensional Winds
Virtual SME Training, Critical Asset Control – Ambaflex
Remote System Tension Detection
Understanding the Normal Aging Brain So That the Puzzle of Alzheimer’s Can Be Solved
– Phase 2
Mine Conveyance Battery Charging System
Wearable Mechanical Device for the Wrist
PneumaBrace - A Wearable Electronic Carpal Tunnel Relief Brace
Treadplate Design Challenge
Chemotherapy Port App
Management Dashboard/Executive Information System
Medical-Grade Leak-Proof PCB Encasement – Flexible Material Technology
On-Instrument Slide Temperature Measurement
Rotating Detonation Engine Aerospike Nozzle Design Optimization
Rotating Detonation Engine Rocket Design and Launch
Residual Slide Volume Process Automation – Kimwipe Folder
Remote ID Drone Detection
Histopath Tissue Block Sorting Module
Aerospace DED Repair with Integrated Machining
Study and Design of Unpolarized Light Propagation in Polarization-Maintaining (PM) Fiber
Patient Safety
Perio-Dx – Bad Gums = Bad Kidneys + Bad Heart
Smart Energy Grid Simulation
Model Based Electrical Diagram and TID Generation
Vibroshear: A System for High-Throughput Drug Discovery of Agents Limiting Shear-Mediated Cell (Platelet) Activation
The Wired Room 2.0 – Automated Digital Sound, Image and Motion Analysis for Enhanced Medical Diagnostics From a Patient Encounter
BOTCOM – Satellite Communication System for Autonomous Aquatic Drones for Ocean Health
Wind Tunnel – Launch Vehicle Aerodynamic Testing
Basketball Shooting Robot Phase 2
Aerospace Radome Impingement Testing
Dispatch Console Audio Interface Design
Drone Detection and Tracking by Acoustic Signature (D2TAS)
Localized Temporarily Deployable Autonomous Navigation Network (LTDANN) (Joint UA/UMass Project)
Short Term Aerial Recognizance (STAR) - Phase 2
Repurposing Hemp/Cannabis Biomass: Fiber Extraction and Fractionation to Make Valuable
Biobased Raw Materials
Modular Biomedical Sensor Board for Education
CubeSat Centrifuge Terrarium
Large-Scale Lunar Prospecting Rover
Large-Scale Lunar Prospecting Rover Team II
AIAA Design/Build/Fly
Development of a Lightweight Structural Rechargeable Battery for Electric Aircraft
Development of a High-Altitude System to Generate a Global-Scale Dataset of Atmospheric Turbulence
Development of Solar Sail Spacecraft for Dynamic Maneuvering
Novel Cannula Design for Total Artificial Heart (TAH) Driver Unit
Wearable Robotics Fall Prevention Systems
F1 Drug Detector
WATER-SAFE - PFAS/Microplastic Water Detection System for Environmental and Human Health
Baseball Swing Rotation Trainer
Small Item Photographing Triage Robot (SIPhTR)
Advanced Rapid Manufacturing of Low-cost, Visually-Realistic Targets
Leach Pad Cover Wind Mitigation Proposal
Automated Material Sampling
Design and Testing of Apparatus for Weight Bearing 3D Ultrasound Shear-Wave Elastography of the Foot
Aquaponic Media Cleaning Device
Laser Diode Based Metrology Module
Deep Rock Geologic (Society of Mining Engineers Metallic Student Design Competition, 2023-2024)
San Xavier Mine West Portal Expansion
Phase 3 Pit Design
Mobile Alfalfa Drying System
Irrigation Canal Cleaning Tool
The Lunar Pioneers
Stormwater Mitigation Plan for Miami, AZ
Oxygen on the Lunar Surface Coal to Methanol
AZWA Student Design Competition
Dialy-ssist
Scale-Up of KinetiSol® in Pharmaceutical Manufacturing
Produced Water Reclamation Project
Carbon Capture for Algae Growth
of Beer
Brewery Upgrade Project
Electrocatalytic Conversion of Carbon Dioxide Emissions from Vodka Production
Synthetic Ivory, from Experiment to Experience
Uranium Project
Leave No Trace: Removing Trace Organic Contaminants (TOrCs) from Wastewater via Direct and Indirect Photolysis
What excited me the most was the chance to apply my education in optical engineering to a meaningful cause.”
Team 24001
supported by
Craig M. Berge Dean’s Fund
Create a fully operational negotiation system that can be deployed by the University of Arizona Police Department and FBI during a hostage or crisis situation to safely de-escalate danger.
When a person barricades in a closed location, with or without hostages, law enforcement professionals deploy a crisis negotiation team to de-escalate the situation. The team developed a “throw phone” to establish a secure, private, and reliable means of communication between negotiators and the person of interest.
The project includes two subsystems: the throw phone and the command unit. The team designed the throw phone with six video cameras and a video transmitter to transmit wide field-of-view video, a lavalier microphone to receive and transmit full-duplex audio via an iPhone 8, and a speaker to project audio. The phone’s case is durable to ensure that the individual in crisis won’t cause damage that would destroy the line of communication.
The command unit is designed to receive video using a 2.4 GHz and 5.6 GHz receiver and audio via a cellular receiver and SIM card. The throw phone and command unit are connected without the use of a commercial cellular network. The command unit can store hours of video and audio. A laptop screen displays information through a graphical user interface, which the operator also uses to call the throw phone, switch between video feeds, and record video and audio.
The team has produced a rugged, reliable wireless crisis negotiation solution that is ready for use.
Team 24003
PROJECT GOAL
Develop an algorithm to drastically enhance surgical monitoring by significantly reducing signal acquisition time while maintaining a high signal-to-noise ratio in testing of nerve pathways.
A somatosensory evoked potential (SEP) is electrical activity measured at the skin surface in response to nerve stimulation. SEPs can indicate problems with signal pathways in the central nervous system such as insults during spinal cord surgeries. However, current SEP monitoring provides delayed feedback, which increases the risk of critical neurological damage during surgery.
The team designed a software algorithm that enhances current SEP monitoring with efficient signal acquisition and analysis. This improves the signal-to-noise ratio (SNR) and provides faster feedback, enabling early intervention to prevent permanent nerve damage.
The algorithm has four blocks: 1) the data collection block processes raw signals and discards corrupted trials based on amplitude thresholds, 2) the model creation block develops an autoregressive model to accurately predict SEP signals, 3) the filtering block uses this model to filter out noise from relevant SEP signals in the recorded data, and 4) the display block calculates the SNR and displays the filtered data.
The system goal is to provide the surgeon with complete feedback within 20 seconds. The current state-of the-art for SEP monitoring is 3 minutes. The SNR will be improved by >= 20db, and tests will ensure the system has 90% sensitivity and 95% specificity. Ultimately, this will significantly reduce postoperative complications with more accurate, real-time feedback during surgeries.
TEAM MEMBERS
Preston Martin, Systems Engineering
Joshua Christian Reuter, Electrical & Computer Engineering
Richard Joseph Tracy, Mechanical Engineering
Daniel Zadorozhny, Electrical & Computer Engineering
Cade Douglas Seggewiss, Systems Engineering
Javid Sarkhosh, Industrial Engineering
COLLEGE MENTOR
Jeff Scott Wolske
SPONSOR ADVISOR
Joseph Berriman
TEAM MEMBERS
Arisha Fatema, Biomedical Engineering
Alana Marie Maluszczak, Biomedical Engineering
Ashley Moshkriz, Biomedical Engineering
Anuj Tripath, Electrical & Computer Engineering
Yeji Jeon, Systems Engineering
COLLEGE MENTOR
Don McDonald
SPONSOR ADVISORS
Charlie Berg Jeffrey Owen
TEAM MEMBERS
Omar Amanullah, Mechanical Engineering
Ryan Chen, Optical Sciences & Engineering
Nicholas Elijah Matthews, Biomedical Engineering
Yumou Wan, Electrical & Computer Engineering
Abhiman Gupta, Biomedical Engineering
Preston Joseph Leigh, Biomedical Engineering
COLLEGE MENTOR
Doug May
SPONSOR ADVISORS
Charlie Berg
Jeffrey Owen
TEAM MEMBERS
Brian Castellanos, Electrical & Computer Engineering
Mason Eves, Optical Sciences & Engineering
Lilian Naves, Mechanical Engineering
Cole Suddarth, Electrical & Computer Engineering
Logan Pawlowski, Optical Sciences & Engineering
Ross Margulis, Optical Sciences & Engineering
COLLEGE MENTOR
Mike Nofziger
SPONSOR ADVISORS
Ian Carr
Benjamin Cromey
Team 24004
Create an optical probe to measure blood flow in the anterior spinal artery.
Pressure on the spinal cord during fusion surgeries can lead to loss of spinal cord blood flow. The Spinal Blood Flow Monitor (SBFM) provides efficient and compact monitoring of anterior spinal artery blood flow. Current flow monitoring methods are slow, which can result in post-operative motor deficit or paralysis. Intra-operative monitoring using the SBFM can rapidly alert surgeons to blood flow decreases, improving post-surgical outcomes.
Laser doppler flowmetry (LDF) has shown great promise in measuring relative flow rates in confined spaces using affordably sourced components. The anterior spinal artery runs approximately 7 mm below the posterior spinal cord surface midline in the spinal canal.
Using a near-infrared laser allows light penetration of up to 10 mm and enables the fabrication of a less than 5 mm flexible assembly that can be sterilized with medical-grade ethylene oxide.
The SBFM uses a dual optical fiber probe that sends and receives near-infrared light that is scattered by red blood cells depending on their velocity. A photodiode converts received light into an electrical signal that an Arduino converts to a digital signal to send to a medical computer. There it is processed and displayed to give real-time blood flow measurements at the probe site. Multiple probes can be used in parallel at different levels of the spine to pinpoint the location of spinal pinching for more diagnostic utility.
Spectrally discriminate between a camouflaged object and the background the camouflage is designed to simulate.
Camouflage is an effective technology used to conceal personnel and equipment by mimicking the visible colors of the background environment. This project presents a novel imaging spectrometer that exploits spatial-spectral information from visible to near-infrared wavelengths to discriminate between camouflage and the background it was designed to simulate.
The team designed an operational and c alibrated imaging spectrometer to identify camouflaged personnel at distances of up to 500 yards. The operator uses a scanning system to sweep a narrow field of view across a scene. The system focuses the scanned scene onto an optical slit that is relayed and spectrally dispersed to a CMOS detector using an equilateral prism and spherical mirror. The system then combines multiple slit images into a three-dimensional hyper-spatial-spectral data cube, which it then processes to display a composite digital image and spectral graph on a graphical user interface (GUI). The system uses a clustering algorithm to discern pixels that deviate from the expected background spectra and visually flags those pixels as camouflage on the GUI, facilitating operator analysis and interaction. This project presents a unique system capable of detecting camouflaged objects and people.
Team 24006
PROJECT GOAL
supported by Craig M. Berge Dean’s Fund
Redesign a plane door’s latching and operating system for enhanced accessibility and safety specifically tailored for armless pilots.
Jessica Cox, the world’s first armless pilot, is building a foot-controlled airplane to overcome the accessibility limitations she faces with her current Ercoupe aircraft. She is modifying a Van’s RV-10, a larger and faster airplane that can accommodate her as she flies. Among these modifications is a safer and more convenient method for entering and exiting the plane’s fuselage. Team 24006 redesigned the door latching and operating mechanism to enable foot-controlled operation for opening, closing, and locking the door, ensuring its secure closure during flight, and provide a manual opening option in case of power failure.
The door opens and closes via a controlled winch-guided strut system in response to electronic commands from a key fob. To secure the door when closed, a lock system activates two electrically driven linear actuators linked to a rack and pinion assembly, extending them into the plane wall. This design provides an emergency opening option, with the winch featuring a readily accessible release mechanism that retracts the actuators to allow the door to open. Safety features include Arduino-controlled sensors that detect complete door closure, locking status, and any obstructions in the door’s path.
By combining innovative engineering solutions with a commitment to safety and accessibility, this project sets a new standard in inclusive aviation, empowering individuals like Jessica Cox to pursue their passion for flight without limitations.
Team 24007
PROJECT GOAL
Design and develop a compact animal treadmill to study gait under different gravitational forces, such as in space or athletic sand training.
Past researchers have encountered challenges in measuring animals’ gait kinematics and energy expenditure under different gravitation conditions. Previous methods used large amounts of material and did not incorporate controls for gait speed.
The team developed a means to study how ambulating on different surfaces (synthetic regolith to mimic space travel) and weights (the gravitational pulls of Mars, Earth, and the moon) affects a rodent’s gait. Understanding these conditions will allow for innovations in space exploration.
The system is made up of five subsystems: rodent treadmill, sand redistribution treadmill (SRT), harness, filter, and user interface. During operation, the SRT will deposit a fresh layer of synthetic regolith and evenly distribute it on the rodent treadmill. The rodent, secured using the harness, will ambulate on the rodent treadmill, and regolith will be filtered and recycled continuously. This system makes it possible to test the effect of rodent ambulation while simulating different gravitational pulls through a harness assembly.
TEAM MEMBERS
Sophie V Hunter, Electrical & Computer Engineering
Max Walker, Mechanical Engineering
Jack Weeks, Electrical & Computer Engineering
Brendan Andrew Williams, Aerospace Engineering, Mechanical Engineering
Alex Drey, Mechanical Engineering
Cory Bailey, Systems Engineering
COLLEGE MENTOR
Steve Larimore
SPONSOR ADVISOR
David Margolis
TEAM MEMBERS
Emma Boerner, Mechanical Engineering
Melanie Pimentel, Mechanical Engineering
Austin Russell, Biomedical Engineering
Remi Thomas Stauss, Biomedical Engineering
Alexis Nicole Henderson, Biomedical Engineering
COLLEGE MENTOR
Sardar R Mostofa
SPONSOR ADVISOR
David Margolis
TEAM MEMBERS
Landry Guerin, Mechanical Engineering
Dylan Krug, Electrical & Computer Engineering
Aidan James Peck, Mechanical Engineering
Osman Abdullah Syed, Electrical & Computer Engineering
Emilio Lorenzo Rodriguez, Biomedical Engineering
Aljouri Alhamdan, Industrial Engineering
COLLEGE MENTOR
Matt Christensen
SPONSOR ADVISOR
Abraham Jalbout
TEAM MEMBERS
Rebekah June Cutler, Mechanical Engineering
Gabe Eleazar Maldonado, Mechanical Engineering
Kory Pearson, Electrical and Computer Engineering
Ziyan Wei, Electrical & Computer Engineering
Daniel Folse, Software Engineering
Annalisa Minke, Biosystems Engineering
COLLEGE MENTOR
Matt Christensen
SPONSOR ADVISORS
Brian Little
Mark Siemens
Pedro Andrade Sanchez
Design a revolutionary 3D printer that uses mine tailings to build structures for various construction applications.
Current mining processes produce millions of tons of mine tailings each year. Mine tailings are byproducts that can cause several environmental issues and community hazards. The team designed a 3D printer that can print concrete structures using mine tailings. The 3D printer operates by taking commands in the G-code programming language based on the design of the model being printed. The printer is equipped with ethernet connectivity, augmenting its functionality and accessibility.
Duet Web Control is an online user interface that provides operators with an intuitive and userfriendly way to control the 3D printer. Duet3D, an advanced high-power controller, is used to synchronize and configure the movements of the 3D printer’s five stepper motors. The 3D printer features three axes (X, Y, and Z), with a single motor to control the Y axis, two motors for the X axis, and two motors for the Z axis. The Y and Z axes use ball screws for linear motion, whereas the X axis uses racks and pinions. Each axis is capable of 4 feet of travel, which can yield a printed structure of 4 feet by 4 feet by 4 feet.
Create a bio-inspired crop-monitoring robot that can autonomously determine the health of a field.
Agriculture is resource intensive; monitoring can make it more efficient. However, traditional monitoring techniques are either disruptive or very inefficient. This project seeks to address these challenges by employing an autonomous spider robot to use RGB-IR (RGB and infrared) camera and GPS data with existing plant health proxies to determine the health of a field.
Polyethylene terephthalate glycol 3D-printed plastic pieces and servo drivers allow the eight-legged robot to use a custom spider-inspired locomotion to walk 0.15 km per hour and rotate 360 degrees as needed. The robot is controlled by a microcomputer that uses a machine learning camera, GPS, and a nine degrees of freedom sensor to follow waypoints the use inputs through Google My Maps. The microcomputer instructs the robot to walk along the path set by the waypoints, avoiding obstacles the camera detects. The robot can operate in extreme heat conditions and in light rain for about one hour. As it walks, the robot passively collects RGB-IR data that it sends to a repository where it is processed. The user can then use the data to best manage the field.
Team 24010
PROJECT GOAL
Design and develop a system that functions safely as a traditional grab bar and illuminates the vicinity around it through with LED lights. These fundamental requirements are synthesized with a low-profile, sleek, and modular design, allowing implementation into nearly any environment.
A grab bar is a surface-mounted bar that provides assistance for people with limited mobility, such as seniors and those with disabilities. However, people are hesitant to install traditional grab bars in their homes or businesses, viewing them as unsightly. The team developed an integrated grab bar (IGB) with lighting that can be hidden in a chair rail. This innovative IGB is the product of the team’s expertise in multiple disciplines. The team put their energies toward drafting, creating schematics, building and conducting various analyses and tests to make the IGB a reality.
The result of these is a mechanical structure that can be mounted onto an existing wall. While deployed, the system can support the weight of a falling human and can be used as a guide support for traversing through a building. While not in use, the IGB can be folded up against the wall so it resembles an aesthetic chair rail until needed.
The IGB also features an electronic subsystem to control lighting elements. Material selection for this project was heavily driven by the goal of developing an eco-friendly product through the use of recyclable 3D-printed materials.
TEAM MEMBERS
Kurtis A Fiebelkorn, Mechanical Engineering
Jasiah Joseph, Electrical & Computer Engineering
Ani Melichar, Biomedical Engineering
Evelyn Preciado, Industrial Engineering
Ryan Alexander Malone, Mechanical Engineering
Isabellah Mayoral Ortega, Biomedical Engineering
COLLEGE MENTOR
Sardar R Mostofa
SPONSOR ADVISOR
Lisa Reeves
Team 24011
PROJECT GOAL
Design and construct a small-scale pyrolysis plant that safely converts municipal plastic waste into fuel.
Fuel scarcity creates additional hardships for those affected by a disaster. Additionally, plastic pollution, which causes great damage to the environment and human health – especially in underdeveloped areas – can be exacerbated during disasters. Chemical pyrolysis is a solution to both problems. Through pyrolysis, plastic waste can be used as fuel generation feedstock.
The project is a small-scale pyrolysis plant that safely converts common plastics like polyethylene, polypropylene, and polystyrene into a diesel-like liquid that can be used in place of conventional fuel. The high-temperature, oxygen-free reactor thermally decomposes shredded plastic waste into solid carbon char and heavy hydrocarbon vapor, which is fed into a heat exchanger and cooled until the heaviest hydrocarbons precipitate as a liquid. The plant then collects this liquid and flares the remaining gas to stabilize hazardous byproducts. Thermocouples monitor system temperature and pressure, which are displayed on a control panel to ensure safety and monitor reaction progress.
This prototype serves as a compelling proof of concept, showcasing the transformative potential of pyrolysis in mitigating plastic waste in the environment while simultaneously yielding a valuable end product. The plant’s portability and simplicity also enhance its ability to be deployed for humanitarian efforts that produce extensive plastic waste.
TEAM MEMBERS
Ben Hunt, Biosystems Engineering
Daniel Hutton, Chemical Engineering
Reina Kelley, Engineering Management
Gracie Reinholz, Biosystems Engineering
Jamie J Holmstrom, Chemical Engineering
Celeste R Cortez, Electrical & Computer Engineering
COLLEGE MENTOR
Doug May
SPONSOR ADVISORS
Manny Miera
Raphael Lepercq
TEAM MEMBERS
Francisco Navarro, Mechanical Engineering
Isaac Pimienta, Mechanical Engineering
Mina Yoo, Optical Sciences & Engineering
Kevin Garcia, Systems Engineering
Rob Purcell, Optical Sciences & Engineering
COLLEGE MENTOR
Mike Nofziger
SPONSOR ADVISOR
Nitin Patel
TEAM MEMBERS
Winona C Esher, Optical Sciences & Engineering
Isabel Parga, Systems Engineering
Alex Quenelle, Electrical & Computer Engineering
Noah Bucks, Systems Engineering
Connor Sturgeon, Mechanical Engineering
Ian Winski, Optical Sciences & Engineering
COLLEGE MENTOR
James Sweetman
SPONSOR ADVISOR
Patrick Hogan
Team 24012
PROJECT GOAL
Enhance an existing device that measures distortion in spherical mirrors by automating its use and providing an interface to create analytic reports based on past measurements.
The convex side-view mirrors on construction equipment are vital for safe vehicle operation. The extremely high demand for these mirrors makes their bulk production and testing crucial. This project developed an efficient, ergonomic, and quick testing system that measures mirror distortion while providing real-time analytics.
The design uses a test target consisting of concentric circles in the shape of a three-dimensional cone that sits above the mirror being tested. A Raspberry Pi with a touchscreen is connected to an Arduino Mega that controls four linear actuators. The actuators dynamically center the mirror along the X and Y axes to be co-aligned with the test target’s center. A machine vision camera at the top of the cone captures an image of the concentric circles reflected in the mirror, and a distortion measurement algorithm processes the image to determine if the mirror meets automobile mirror distortion standards.
The system collects, processes and stores data in an SQL database; displays a summary of the mirror’s distortion on the Raspberry Pi’s touchscreen; and updates stored measurements with date and time stamps. The graphical user interface allows easy measurement process control and generation of analytic reports for all mirror types measured within a certain time frame that are delivered to a provided email address.
Team 24013
Design and build an automated, modular system to accurately focus two aircraft cameras using optical, mechanical and electrical/software methods that can be easily repeated.
A correctly focused aircraft camera aids in safety and security and protects people and their property. A lens needs to be accurately adjusted when installed into a camera to provide the best resolution. A laser projected through a beam expander can be used to determine that the camera lens is properly focused based on how wide the laser spot appears on the camera.
This project will sample live video data and calculate laser spot size using software to convert pixels to a physical measurement. The system will then use a stepper motor and mechanical configuration to rotate the lens into focus.
This design uses a combination of a class 2 laser, beam expander, and a stepper configuration to rotate a lens into place. The software analyzes camera focus quality by converting sample images from the live video feed into a map of grayscale values that it uses to identify the laser beam. The software determines that the lens is focused when the laser spot is smallest. Once the system determines that the lens has been focused, the stepper will cease rotational movement.
Team 24014
PROJECT GOAL
Store electrical energy produced by renewable sources using a 4,000-foot-deep decommissioned mineshaft.
The largest mining companies have agreed to reach net zero Scope 1 and Scope 2 carbon emissions by 2050 by integrating renewable energy into their mining operations. However, it is crucial to address renewable energy intermittency. The project designed a gravity battery system used in a 4,000-foot mineshaft to achieve zero carbon mining. The team created both a demonstration model and a real-world design.
The demonstration model features a structural frame to support an Arduino-controlled hoisting mechanism powered by DC permanent magnet motors. The operator selects the charging mode on a graphical user interface, which tells the Arduino to begin spinning the motors. The motors then output torque to a gearbox connected to a cable drum that winds up the cable. The cable is run through a series of pulleys and connected to a set of weights. The weights increase the system’s gravitational potential energy until the operator stops charging or a limit switch is activated to halt the weight. When electricity is required, the operator will select the generating mode, causing the motors to disengage from the driver. The weights will then descend, causing the motors to produce electricity.
For the real-world design, the team focused on access points, site layout and hoisting configuration. The team also designed critical structural members and walkways and evaluated the design’s performance and economic feasibility using mathematical models.
Team 24015
Develop a probe that will measure relative wind, pitch, yaw, and speed, and electronically and mechanically integrate with a disposable host UAV.
This project improves data used for hurricane projection models and advances atmospheric science research. Current hurricane wind data collection is limited to manned aircraft flying high above storm systems as well as through upper layers. The probe’s data will be used to provide new lowaltitude wind data to supplement current hurricane models and research.
Engineering efforts involved aerodynamic testing and computational analysis and circuit board and software design. The five-hole probe integrates seamlessly with Dragoon’s Coriolis UAV platform, providing wind measurements while withstanding hurricane force winds. The probe itself is manufactured using stereolithography 3D printing and uses three off-the-shelf differential pressure sensors and a custom-printed circuit board and accompanying software. A 3D-printed enclosure integrates the probe into the host UAV’s wing and protects the instrumentation components from hurricane conditions. Using campus wind tunnel resources, the team characterized the probe to ensure accurate readings of pitch, yaw and wind speed. Additionally, the team conducted a repeatability study to verify accuracy across multiple probe heads.
TEAM MEMBERS
Matthew English, Electrical & Computer Engineering
Cecil Mrstik, Industrial Engineering
Ryan A Sunga, Mechanical Engineering
Jaime Jose Valencia, Electrical & Computer Engineering
Connor M Perkins, Engineering Management
Gavin Tampa, Mechanical Engineering
COLLEGE MENTOR
Pat Caldwell
SPONSOR ADVISOR
Michael Hemphill
TEAM MEMBERS
John B Franklin, Mechanical Engineering
Ashley Holt, Aerospace Engineering
Glenn Sears, Software Engineering
Carlton Martin Louie, Aerospace Engineering
Trevor Bailey, Electrical & Computer Engineering
COLLEGE MENTOR
Pat Caldwell
SPONSOR ADVISOR
Sean Culbertson
TEAM MEMBERS
Hamad Abdulla Alenezi, Mechanical Engineering
Faisal Almutairi, Industrial Engineering
Meera Shah, Systems Engineering
Yiran Xie, Optical Sciences & Engineering
Nina Mackey, Mechanical Engineering
Mishal Shahin Alquraini, Industrial Engineering
COLLEGE MENTOR
Michael Madjerec
SPONSOR ADVISOR
Joseph Mueller
TEAM MEMBERS
Tanner Curtis, Mechanical Engineering
Xuan Nguyen, Systems Engineering
Caleb Lane Pendleton, Mechanical Engineering
Adil Zeinulla, Industrial Engineering
Cole Hansen, Industrial Engineering
Paul Obrien Sylvester, Industrial Engineering
COLLEGE MENTOR
Matt Christensen
SPONSOR ADVISOR
Joseph Mueller
Team 24016
PROJECT GOAL
Create a virtual maintenance training program for Amazon’s Ambaflex spiral conveyance system.
The team worked to enhance the training of Amazon technicians for operating and maintaining the Ambaflex spiral conveyance and streamline the equipment troubleshooting process with remote assistance from subject matter experts (SMEs).
The design approach transformed current training from traditional methods such as YouTube tutorials and on-the-job training to an immersive and efficient virtual reality (VR) experience. This shift created a safer training environment, away from the bustling warehouse floor, ensuring a better use of time and resources by enabling practice without the downtime that waiting for equipment brings.
The project design expands the original scope of a project that began during the 2022-2023 school year. The expansion adds communication capabilities and provides training on different Amazon conveyance equipment. The system design integrates hands-free communication capabilities within the Meta Quest 3 headset, which allow technicians to directly interact with the SMEs while performing maintenance and troubleshooting.
This project represents a leap in industrial maintenance and training, leveraging mixed reality technology to create a more interactive, safe and efficient learning and troubleshooting environment.
Team 24017
PROJECT GOAL
Develop a remote tension measurement system that can monitor the tension of a conveyor belt, display the value in real time, and upload the data to a web-based platform.
Tension is a critical parameter for conveyor belts, impacting their performance and lifespan. Incorrect tension can lead to gradual conveyor belt deterioration, causing downtime and financial losses for distribution companies. Implementing an accurate tension measurement and recording system enables operators to follow trends of the belt’s status and condition, informing decisions on maintenance and repairs. This will help mitigate conveyor belt failures in distribution centers.
The system hardware consists of a modified tension bar, a load cell, an Arduino UNO Wi-Fi Rev2 board, and a 3D-printed housing. This integrated setup ensures precise tension measurement, includes a local digital display of the current tension value, and provides the ability to upload data to a web-based platform. The tension detection system allows the operator to monitor conveyor belt tension in real time and analyze historical tension data to inform maintenance planning.
Team 24018
PROJECT GOAL
Construct and install a specialized autonomous robot and tethered data transmission system to aid research focused on Alzheimer’s disease.
Researchers at the Evelyn F McKnight Brain Institute use the Instantaneous Cue Rotational (ICR) arena to study the normal brain aging of rats to advance Alzheimer’s research. The team developed an updated autonomous robot that dispenses food, tracks animal movements, and collects brain wave data as rats move on a circular track in the ICR arena.
This project redesigns an earlier autonomous robot with a wireless brain wave transmission system that grappled with operational reliability, time sync and system lag issues. The redesigned robot uses a new lightweight wired system to improve data collection while not burdening the rats. This wired system alleviates weight from the rats’ heads, ensuring frictionless movement during experiments while maintaining uninterrupted brain wave readings.
The new design also includes automatic feeding and waste cleanup capabilities and precise tracking via a camera system. Integrating advanced tracking capabilities along with the lightweight wired system ensures more precise movement data, facilitating enhanced synchronization with brain wave readings. This will offer researchers a more accurate understanding of the nuances in rat brain activity and aging processes and enhance precise data gathering with an emphasis on the functioning of the hippocampus and entorhinal cortex versus the aging brain.
Team 24019
PROJECT GOAL
Create a sustainable battery charging system for underground mining communication, ensuring continuous power during conveyance travel, thus improving efficiency and safety.
The Resolution Copper mine employs a battery-powered communication system within the No. 10 shaft auxiliary conveyance system. The existing system is powered by a 12V battery that needs daily replacement because its electrical capacity degrades during the operation of the conveyance as it ascends and descends the shaft.
The team has successfully developed a fully automated inductive battery charging system that integrates sensor alignment for precise activation. This system wirelessly induces power through electromagnetic fields, effectively recharging the conveyance system’s 12V battery. The result is a sustainable power source for on-site communication equipment that can withstand challenging and harsh mine conditions.
This solution uses sensor alignment and electromagnetic field technology to eliminate the need for daily manual battery replacements, thus reducing operational disruptions and associated maintenance costs. The implementation of this system enhances communication system reliability within the shaft and aligns with industry trends, promoting sustainability and increased energy efficiency.
TEAM MEMBERS
Max Duque, Optical Sciences & Engineering
Jason Freeman, Electrical & Computer Engineering
David Polk, Electrical & Computer Engineering
Ritik Makhija, Electrical & Computer Engineering
Guntaas Singh Chadha, Industrial Engineering
COLLEGE MENTOR
Don McDonald
SPONSOR ADVISOR
Don McDonald
TEAM MEMBERS
Yousef Aljuhairi, Electrical & Computer Engineering
Walker Anderson, Electrical & Computer Engineering
Trinity Brandt, Mechanical Engineering
Arthur Ferreira Eilers, Mechanical Engineering
Ethan Farris, Industrial Engineering
Mari Rocha, Industrial Engineering
COLLEGE MENTOR
Pat Caldwell
SPONSOR ADVISOR
Michael Hemphill
TEAM MEMBERS
Samuel Gonzalez, Mechanical Engineering
Jacob A Mondry, Mechanical Engineering
Valeria Maria Villarino, Biomedical Engineering
Thomas Zachariah Murickan, Biomedical Engineering
Brandon Bounds, Biomedical Engineering
COLLEGE MENTOR
Matt Christensen
SPONSOR ADVISORS
Zong-Ming Li
Trevour Greene
TEAM MEMBERS
Nawaf Z Almutairi, Electrical & Computer Engineering
Zack Amstutz, Biomedical Engineering
Michael Cesar-Torres, Electrical & Computer Engineering
Christian A Vanasco, Mechanical Engineering
Wakil Ur Rahman, Biomedical Engineering
Aydin Saucier, Biomedical Engineering
COLLEGE MENTOR
Pat Caldwell
SPONSOR ADVISORS
Zong-Ming Li
Trevour Greene
Team 24020
PROJECT GOAL
Create an ergonomic and accessible compressive, wearable mechanical wrist device that supports the treatment of carpal tunnel syndrome.
Carpal tunnel syndrome (CTS) results from compression of the median nerve within the carpal tunnel by the transverse carpal ligament (TCL). This disorder causes paresthesia and numbness in the median nerve distribution and can be permanent if left untreated. The device aims to relieve pain from CTS by applying specific compressive forces to the trapezium and pisiform carpal bones to induce an increase in carpal arch height through folding of the TCL, thus increasing the inner surface area to minimize compression of the nerve.
The design combines a mechanism containing a spring and a brace that uses a cord-tightening system. As the brace tightens around the wrist, the spring compresses and applies a specified force at each end of the wrist. This device is designed with industry-standard springs and conforms to current specifications regarding consumer orthotics, improving manufacturability. It is modeled to be compact for integration and aesthetic purposes.
Team 24021
PROJECT GOAL
Relieve pain from carpal tunnel syndrome through the use of a noninvasive, wearable, electronic device.
Carpal tunnel syndrome (CTS) affects numerous individuals, leading to pain and discomfort in the wrist that can hinder daily activities. Traditional treatments often involve surgery or constant medication, posing risks and inconveniences. This project introduces an electronic, wearable brace as an innovative and noninvasive solution for pain relief.
The design incorporates a flexible and comfortable hand brace equipped with a rubber bladder that expands pneumatically to apply pressure to the palmar side of the wrist. This decreases compression of the median nerve caused by CTS, which in turn relieves pain in the wrist. An onboard Arduino computer controls an air pump for inflation, a solenoid valve for air release, and a pressure sensor to ensure the force remains within a safe range.
The design also integrates a display to give the user information regarding treatment duration and force applied. The device is battery-powered and rechargeable, with the ability to provide treatment for at least the length of an average working day. The team created an ergonomic and comfortable device that users will find easy to use without hindering their daily activities.
Team 24022
PROJECT GOAL
Design a new treadplate pattern for Caterpillar that uses a computer numerical control (CNC) turret punch press manufacturing process.
A treadplate is a walking surface that has a pattern of protrusions for the purpose of increasing the coefficient of friction between a worker’s boots and the surface they are walking on. Using a CNC turret press to punch these protrusions will result in a more efficient and cost-effective solution to manufacture treadplates.
The team successfully designed and tested a protrusion pattern with optimal spacing that produced a high coefficient of friction for three specified environmental conditions: 1) dry, 2) muddy, and 3) oily. The team designed and built a custom test setup that used 3D-printed protrusion designs and spacings to determine a pattern and spacing that produced the maximum coefficient of friction. The test setup used rubber and various weights to simulate an equipment operator’s work boot and body weight across multiple treadplate protrusion designs.
The team selected the optimal pattern design based on test data and provided the design to Caterpillar’s treadplate manufacturer to have the pattern punched into steel using a CNC turret punch process. The team then tested the metal stamped pattern against the current pattern being used at Caterpillar in dry, muddy and oily conditions. The test results indicated that the new treadplate pattern design performed better than the current design and is more cost-efficient to produce using a state-ofthe-art CNC turret punch process.
TEAM MEMBERS
Abdullah Ahmad Almutairi, Industrial Engineering
Abdulaziz Alshayea, Industrial Engineering
Jackson Cobb, Mechanical Engineering
Nhattien Dinh, Mechanical Engineering
Stephen Philip Gonda, Engineering Management
Brian John Prieve, Mechanical Engineering
COLLEGE MENTOR
Michael Madjerec
SPONSOR ADVISOR
Lloyd Becker
Team 24023
PROJECT GOAL
Design and develop a smartphone application that remotely monitors vitals and symptoms among cancer patients receiving cytotoxic therapies to minimize medical emergencies.
Each year, more than 1 million people in the U.S. begin cancer treatment. Chemotherapy and immunotherapy are both systemic treatment types that respectively use cytotoxic drugs or cells to target tumor cells. In recent years, clinicians and patients have seen benefits to moving cancer treatment into patients’ homes. However, the risk of medical emergencies in this vulnerable population poses a severe limitation.
The team’s chemotherapy port app, CytoCheck, collects real-time quantitative data from wearable wireless heart rate and body temperature sensors. Additionally, CytoCheck uses regular wellness surveys to monitor qualitative symptoms such as pain, nausea, fatigue and skin irregularities. CytoCheck includes distinct patient and provider interfaces, and the patient can link their account to a provider to share and monitor data. The system flags biometric readings that fall beyond customized thresholds and alerts providers. The CytoCheck app analyzes, tabulates, and stores patient data, making the information human-readable on both user interfaces.
TEAM MEMBERS
Adrian Daniel Corey, Electrical & Computer Engineering
Oliver Beck Sjostrom, Electrical & Computer Engineering
Michael Villasana, Electrical & Computer Engineering
Lillian Wu, Biomedical Engineering
Catherine Calma, Biomedical Engineering
COLLEGE MENTOR
Sardar R Mostofa
SPONSOR ADVISOR
Chad Van Liere
TEAM MEMBERS
Gerardo Aguilar, Software Engineering
Joann Chang, Industrial Engineering
Kennedy Kolb, Engineering Management
Gerrick Rubalcava, Electrical & Computer Engineering
Ibraheem Sarwar, Engineering Management
Javier Refugio Cota, Software Engineering
COLLEGE MENTOR
Sardar R Mostofa
SPONSOR ADVISORS
Basavaraj Patil
Joshua Etchison
TEAM MEMBERS
Ethan August, Mechanical Engineering
Nooreen T Qureshi, Chemical Engineering
Hailey C Watts, Optical Sciences & Engineering
Ainsley Limesand, Systems Engineering
Bradley Scott Khanthaphixay, Biomedical Engineering
COLLEGE MENTOR
Sardar R Mostofa
SPONSOR ADVISORS
Krysta Kramer
Shannon Servoss
Dustin Charamut
Team 24024
PROJECT GOAL
Design and develop a user-friendly and adaptable dashboard system (CAT Hub) to improve the decision-making process for top-level executives at Caterpillar. This system will provide a complete overview of project status, potential risks and performance metrics.
The CAT Hub system’s main objective is to simplify project supervision and manage risks within Caterpillar’s operational structure. CAT Hub is a dynamic platform that uses advanced technologies and collects real-time data from different internal sources. The engineering team focused on incorporating Amazon Web Services to ensure the stability of the back-end system, Amazon DynamoDB for flexible storage of data, and Amazon ECS for effective orchestration of application containers.
The result is a robust executive management dashboard system that enables real-time monitoring and analysis of projects and includes features for identifying risks, tracking issues, and analyzing projects. With the introduction of this system, management can now use customized key performance indicators to assist in making well-informed decisions and planning strategically.
The team used careful planning and design of the system, repeated testing, and continuous incorporation of feedback to achieve the project’s objectives and develop this solution. The structure of the system allows for smooth integration with Caterpillar’s current databases, ensuring the consistency and dependability of data.
Team 24025
PROJECT GOAL
Design and prototype a medical-grade printed circuit board (PCB) encasement to mitigate safety hazards in tissue staining instruments, providing modular protection and reducing the risk to custom circuit boards.
Ventana Medical Systems, a Roche Company, develops automated tissue staining instruments to diagnose a variety of disease states using an array of technologies. Tissue staining instruments employ electromechanical devices, and as such, the staining reagents are in proximity to electronics. The team designed a PCB encasement meeting an ingress protection rating for light liquid spray and drips, along with an encasement constructed from a material compatible with the reagents used within the instruments.
The design uses two complementary halves to create a self-sealing housing that ensures a strong perimetric seal alongside compressive seals encompassing the wire egress locations to ensure that the custom circuit board remains operational. Additionally, the encasement is made of flexible silicone to ensure chemical compatibility of any reagents it would contact. The design’s omnidirectional liquid protection and chemically compatible material protects the electronics from risk of contamination and extends the lifetime and reliability of the custom circuit board and tissue staining instrument.
Team 24026
PROJECT GOAL
Create a sensor capable of accurately measuring temperature across the surface of a glass slide for tissue staining instruments.
Roche Tissue Diagnostics develops automated tissue staining instruments to diagnose a variety of disease states; one such device is the BenchMark ULTRA. Tissue staining requires precise temperature control across the entire slide, so the BenchMark ULTRA uses a heater cap to heat a glass microscope slide. The On-Instrument Slide Temperature Measurement device will be used as a verification and validation tool to ensure accurate and uniform temperature across the glass slide while it is on the heater caps. This device consists of three main sub-assemblies: 1) the sensor board, 2) the sensor interface board, and 3) the graphical user interface (GUI).
The sensor board incorporates six surface-mount thermistors affixed to a printed circuit board (PCB). The design uses thermal epoxy to bond the thermistors to a glass slide to facilitate optimal heat transfer with high accuracy. The sensor board’s circuitry is safeguarded by thermal epoxy.
The sensor interface board, another PCB connected to the sensor board by a ribbon cable and housed in a water-resistant encasement, hosts all necessary components for extracting temperature data from the thermistors.
The GUI provides an interface with the sensor interface board to offer end users a visual representation of slide temperature.
TEAM MEMBERS
Essa Alqaoud, Mechanical Engineering
Chris James Curtis, Mechanical Engineering
Nestor Garcia, Electrical & Computer Engineering
Thomas Ziccarelli, Optical Sciences & Engineering
Anna Jiang, Biomedical Engineering
Ruby Hackenyos, Systems Engineering
COLLEGE MENTOR
Pat Caldwell
SPONSOR ADVISOR
Roger Guiel
Team 24027
PROJECT GOAL
Design and optimize an aerospike nozzle to be fitted on a rotating detonation engine to improve fuel efficiency.
Rotating detonation engines are a new type of engine that supersonically burns fuel and oxidizers to produce a greater fuel efficiency than a conventional combustion engine within a smaller space. Because of the annular detonation chamber used in these engines and the highly transient nature of the detonation front, conventional understanding of engine nozzle geometry cannot be readily applied to these new engines.
The project’s initial goal was to examine the behavior of a sponsor-provided engine with a conventional nozzle design. The team designed an aerospike nozzle using conventional equations to fit test engine parameters and tested the design in a variety of configurations for detonation stability and thrust.
The project included a thrust bearing to measure parameters that determined performance during testing. The team designed new parameterized nozzle components based on behavior seen in initial tests and a theoretical examination of the engine’s characteristics.
The team tested these new components for detonation stability and thrust in multiple configurations and compared them with conventional design components to provide insight into the effect of those parameters on engine performance. The new parameterized components showed an improvement in engine thrust output. A dual expansion aerospike design performed better than the conventional aerospike design while reducing the overall length of the nozzle.
TEAM MEMBERS
William Gee, Mechanical Engineering
Walter Rahmer, Optical Sciences & Engineering
Zackary Steinberg, Aerospace Engineering
Sydney Schmidt, Mechanical Engineering
Ryan Smith, Mechanical Engineering
COLLEGE MENTOR
Doug May
SPONSOR ADVISOR
James Villarreal
TEAM MEMBERS
Raul Beltran, Mechanical Engineering
Henry Chambers, Mechanical Engineering
Henry Overbeck, Mechanical Engineering
Kevin D Strout, Aerospace Engineering
Andrew James Lefcourt, Mechanical Engineering
Leah McAdams, Mechanical Engineering
COLLEGE MENTOR
Steve Larimore
SPONSOR ADVISOR
James Villarreal
TEAM MEMBERS
Abdelrahman Ahmed Abdelkhalek, Electrical & Computer Engineering
Abdelrahaman Alsharif, Biomedical Engineering
Ramiz Aminov, Mechanical Engineering
Derek Lee, Systems Engineering
Fawaz Ghannam, Mechanical Engineering
Paz Davila Valenzuela, Electrical & Computer Engineering
COLLEGE MENTOR
Sardar R Mostofa
SPONSOR ADVISOR
Keesha Everett
Team 24028
PROJECT GOAL
Design and build a rocket and ground support equipment that will launch the first rotating detonation engine in the United States.
Rotating detonation engines (RDEs) are the next frontier in rocket propulsion. RDEs generate thrust via a continuous revolving supersonic detonation wave, which enables a more efficient burn. This project launched the first RDE-powered rocket in the United States as well as the largest RDE in the world to date. RDE technology is in its infancy, but this flight demonstrates the technology’s feasibility and its ability to be integrated with traditional liquid rocket systems.
The rocket design uses propylene as a fuel and nitrous oxide as an oxidizer. The design stores fuel and oxidizer as pressurized liquids and feeds them to the engine using a blowdown system. The ground support system remotely fills the rocket and maintains optimal pressure, all while monitoring rocket conditions and providing critical safety and scrub functions. The ground support system externally actuates the rocket’s main valves simultaneously with engine ignition, and the rocket’s onboard flight computer deploys the parachute after reaching apogee. This rocket serves as a test platform that can be equipped with more advanced engines in the future.
Team 24029
PROJECT GOAL
Design and develop a fully integrated automated Kimwipe folding system.
Roche’s BenchMark ULTRA series instruments undergo comprehensive post-manufacturing testing. The instrument’s critical function is to dispense specific amounts of reagent onto a carousel of specimen slides. Testing uses pre-folded Kimwipes to measure the residual volume of dispensed reagents accurately. Test operators must manually fold hundreds of Kimwipes, which are used to wipe equipment and don’t leave lint residue. The manufacturing team at Roche needs a fast, reliable and safe system to produce folded Kimwipes to streamline the workflow.
The Kimwipe Folding System (KFS) aims to process hundreds of 8.2-inch by 4.4-inch Kimwipes into the required fold configuration autonomously. The design consists of a belt-driven intake that feeds Kimwipes into a wrapping mechanism to roll Kimwipes into a cylindrical tube. The KFS then uses a specially designed exiting module to flatten and perform a half fold to the Kimwipes and dispense them into a storage receptacle. To track each Kimwipe, the team implemented a multi-layered Kimwipe detection technique using infrared wavelengths. The system uses pre-programmed logic and custom libraries to achieve the required level of functionality.
Team 24030
PROJECT GOAL
Develop and demonstrate a remote module design that can broadcast commercial UAV information to any applicable receiver within its radius of operation.
Personal safety is essential to aircraft operations, so the Federal Aviation Administration (FAA) has developed new guidelines that require all commercial UAVs greater than 0.55 lbs to broadcast specific information, including location, velocity and identification. The team designed and demonstrated a simple hardware and software module to address these FAA-mandated requirements.
The design approach uses a combination of off-the-shelf hardware and basic circuit components to establish power and communication links within the system. The project team developed a printed circuit board to easily and effectively establish all the necessary electrical functions between the components and provide power to the system. The system uses a 3.7V lithium polymer battery to power the system and a charging circuit to recharge the battery between uses. The microchip and the GPS module operate concurrently to collect and transmit the specified FAA information. The GPS module continuously collects real-time location data and the embedded microchip processes the information for broadcast via Bluetooth. The system continuously operates at a minimum of once per second while the module is powered on.
TEAM MEMBERS
Evan Martin, Software Engineering
Jesus Saldana, Systems Engineering
Conor Ray Toole, Software Engineering
Nic J. Coyne, Electrical & Computer Engineering
Darius Carrozzo, Electrical & Computer Engineering
COLLEGE MENTOR
Michael Madjerec
SPONSOR ADVISOR
Mark Christianson
Team 24032
PROJECT GOAL
Enhance the efficiency of histopathology lab operations and, therefore, cancer diagnostics by designing and creating an automated tissue block sorting module.
This project introduces an innovative module that automates the orientation and storage of histopathology tissue blocks. Histopathology tissue blocks are patient biopsies embedded in wax and mounted in a specialized container and are an essential part of the pathology lab process. The process of orienting and storing histopathology tissue blocks is integral to diagnosing millions of new cancer cases annually in the United States but is time-consuming. Streamlining and automating this process would allow histopathology technicians to allocate more time to complex analytical tasks.
The histopathology tissue block sorting module uses a Raspberry Pi 4B to control an array of laser sensors and stepper motors and is guided by dual cameras for precise image analysis. This system ensures that tissue blocks, once inserted into the input bin, are autonomously oriented and prepared for storage by the parent module. The design incorporates custom 3D-printed components chosen for their ease of prototyping, precision and durability. The result is a seamless integration into existing lab workflows, providing a consistent and reliable output that increases the efficiency of histopathological analysis.
TEAM MEMBERS
Cassie Queddeng Borromeo, Mechanical Engineering
Jack Monrean, Mechanical Engineering
Grace Shah, Systems Engineering
Ananya Nigam, Biomedical Engineering
Sam DiMatteo, Biomedical Engineering
COLLEGE MENTOR
Steve Larimore
SPONSOR ADVISOR
Matt Mette
TEAM MEMBERS
Mariah Farmer, Materials Science & Engineering
John Hill, Mechanical Engineering
Patrick Pinder-Newton, Mechanical Engineering
Nav Attanayake, Engineering Management
Sophie Miller, Aerospace Engineering
Nick Joseph Gomez, Engineering Management
COLLEGE MENTOR
Steve Larimore
SPONSOR ADVISORS
Clay Sutter
Tania Ruiz Hermosillo
TEAM MEMBERS
Weijie Chen, Electrical & Computer Engineering/Optical Sciences & Engineering
Elijah Quiles, Optical Sciences & Engineering/Mathematics
Yihe Wang, Applied Physics/Optical Sciences & Engineering
Carolyn Hokin, Optical Sciences & Engineering
Bryce D Stickley, Electrical & Computer Engineering/Optical Sciences & Engineering/Mathematics
COLLEGE MENTOR
Mike Nofziger
SPONSOR ADVISORS
Tao Chen Ryan Knox
PROJECT GOAL
Evaluate the implementation of directed energy deposition (DED) integrated machining to repair aerospace components.
Integrating DED with machining presents an opportunity to streamline and reduce costs associated with aerospace component repair and overhaul processes. This project developed a comprehensive methodology, including material and cost evaluations, for using a Meltio M450 DED engine integrated with a Haas VF-2 computer numerical control (CNC) machine to repair a diffuser plate from a Honeywell 331 series auxiliary power unit. Adopting this innovative integrated machining process will yield significant sustainability and cost efficiency improvements over current methods.
The team acquired the diffuser plate’s geometry using a coordinate measuring machine and blue light scanner and generated G-code programming language for DED and CNC toolpaths using Mastercam and A+ software tools. The team then designed experiments that varied parameters such as dwell time, print speed and laser power during the printing process to optimize results.
The team performed Vickers hardness testing and grain size analysis to validate the printed component’s material properties and conducted a comprehensive cost analysis to determine the payback period associated with adopting this repair methodology compared to traditional approaches.
The team printed the required geometry onto the part and completed the experiment designs. This endeavor represents significant progress in using advanced manufacturing techniques to enhance aerospace component repair processes, paving the way for more sustainable and cost-effective solutions in the industry.
Team 24034
Investigate how unpolarized light propagates inside PM fiber through an all-fiber delivery system.
PM fiber is a common component in lithography machines and metrology tools. However, the physics of unpolarized light propagation in PM fiber is currently unknown. It takes effort to produce light of a particular polarization, thus better understanding of unpolarized light propagation in PM fiber may lead to refinements in the use of PM fiber. This project presents a theoretical overview of the physics of unpolarized light propagation in PM fiber backed by experimental results from an all-fiber setup.
The theoretical model shows that PM fiber preserves the unpolarized input state as quantified by the degree of polarization (DOP). PM fiber is represented as the product of three Mueller matrices: 1) a linear diattenuator, 2) a retarder, and 3) a variable partial depolarizer. The experimental setup consists of laser light depolarized via vibration within a single mode fiber. The setup then couples this light into the PM fiber and measures it at the PM fiber output with a polarimeter.
To characterize the Mueller matrix of the PM fiber, the team generated polarized light with a polarization controller, transmitted it through the fiber, and measured the output. The team then compared the DOP of the fiber-depolarized input light to the DOP at the output of the PM fiber. The team collected multiple measurements to ensure accurate and robust data for comparison to the theoretical model.
Team 24035
PROJECT GOAL
Design, build and test an additively manufactured compressor inlet guide vane with fluidic separation control.
Large wakes in airflow following the inlet guide vane of a turbofan engine compressor can interrupt flow into the engine compressor, impacting efficiency of the rotors downstream. This is more pronounced when the compressor inlet guide vane is at a high angle of attack, with increased wake turbulence near the trailing edge of the turbine profile. Ideally, the flow entering the compressor downstream of an inlet guide vane will have minimal flow separation and wake defects.
To decrease wake turbulence and increase efficiency, the team designed an additively manufactured airfoil to support flow injection. Injecting high pressure air over the inlet guide vane where separation normally occurs should reduce turbulence. The team used wind tunnel testing to measure the wake behind the airfoil.
The team also used finite element analysis and computational fluid dynamics simulations to guide the design process by predicting structural integrity, stress distribution, flow separation and performance. The team compared these results against verified experimental data to support design choices, optimize parameters and validate the final design.
The team manufactured the final design through metal fabrication using powder bed laser fusion 3D printing, which fuses layers of powdered 316 stainless steel with a laser, ensuring precision and structural integrity. The design will lead to improved engine efficiency and reduced maintenance costs due to rotor wear and tear.
Team 24036
Design an improved rowing tricycle that combines the benefits of a traditional rowing machine with outdoor mobility, enabling use in open-air environments similar to conventional cycling.
Stationary rowing machines are recognized for their effectiveness in improving cardiovascular endurance while providing a full-body workout. This project implements these inherent advantages and revolutionizes the traditional rowing machine by creating a piece of portable exercise equipment on wheels.
The Land Rower uses a combination of fitness rowing machine mechanics and tricycle design to generate controllable forward motion. The team also developed a new foldable aluminum frame to improve transportability and significantly reduce the system’s weight for user convenience. The team used finite element analysis to identify and reinforce high-stress areas of the new aluminum frame to ensure its structural integrity.
The redesigned drivetrain system allows users to put the trike into neutral and push themselves backward without the drivetrain binding, a feature not previously possible. The drivetrain is also easily accessible for ease of maintenance and assembly. Other improvements include sound level and quality, turning radius, cable management and overall usability.
TEAM MEMBERS
Eric Bhe, Aerospace Engineering
Sidney K Franklin, Mechanical Engineering
Marguerite Gilman, Aerospace Engineering
Megan Wildridge, Aerospace Engineering
Morgan Goz, Aerospace Engineering
COLLEGE MENTOR
Doug May
SPONSOR ADVISOR
Nick Nolcheff
TEAM MEMBERS
Isabel Bowling, Mechanical Engineering
Wyatt Crook Hackenyos, Systems Engineering
Maria Guadalupe Ramon, Mechanical Engineering
Gage Skelton, Industrial Engineering
Colter Henkhaus, Mechanical Engineering
Eryn Stich, Industrial Engineering
COLLEGE MENTOR
Matt Christensen
SPONSOR ADVISORS
Daniel O’Connor
Ben Blehm
TEAM MEMBERS
Fatmah Alhebaishi, Industrial Engineering
Ryan Grevsmuehl, Biomedical Engineering
Taylor Lansky, Biosystems Engineering
Monique Thomas, Biomedical Engineering
Derek Spaeth, Biomedical Engineering
COLLEGE MENTOR
Don McDonald
SPONSOR ADVISOR
Bijin Thajudeen
TEAM MEMBERS
Vanshraj Chawla, Electrical & Computer Engineering
Luke Dagnillo, Electrical & Computer Engineering
Angel Hernandez, Biomedical Engineering
Natalie Grace Jarrell, Biomedical Engineering
Venesa Romero, Biomedical Engineering
COLLEGE MENTOR
Don McDonald
SPONSOR ADVISOR
Bijin Thajudeen
Team 24037
PROJECT GOAL
Offer a noninvasive, at-home method of measuring phosphorus content in foods and fluids using sensing, machine learning and analysis.
One in seven U.S. adults is expected to develop chronic kidney disease. Patients with chronic kidney disease can experience threatening symptoms like bone fragility, muscle spasms and even death with excess consumption of phosphorous, an essential element found in a variety of foods. The team offers a point-of-care analytic system with a user-friendly mobile app consisting of image recognition and volume estimation of a variety of foods and fluids and a detection probe for estimating phosphorous content.
The design’s first component is a phosphorous detection probe and homogenizer housed in an enclosure resembling a small kitchen appliance. The probe directly measures the phosphorus content of a food sample blended with water.
The system’s second portion is an app that can recognize images of foods, compute the volume of food to be consumed, suggest serving sizes, and deliver an approximate phosphorous content of the food. This process depends on an evolving smart lookup table that continually updates itself as it collects data.
The app’s interface allows patients to measure phosphorous content and maintain daily and monthly graphical logs of phosphorous intake, offering dietary habit insights. The app also has telemetric capabilities that link to health care providers to enable proactive interventions and personalized treatment plans. The design’s estimated cost to users will be $350, with the app available as a free download.
Team 24038
PROJECT GOAL
Create a point-of-care device for screening using a microfluidic device and companion app to detect inflammation biomarkers in the gingival crevicular fluid (GCF) from the gum/ tooth interface.
Inflammation drives chronic kidney and heart disease; however, other than clinical blood tests, no rapid testing method exists to readily diagnose systemic inflammation. Several inflammation biomarkers are present in GCF excreted from the periodontal pocket, or gum/tooth interface. Thus, analyzing GCF could provide a noninvasive alternative to clinical blood tests.
The team created an easy-to-use at-home test kit, called the Perio-Dx Kit, to test for inflammatory biomarkers in GCF. The Perio-DX Kit design includes: 1) a paper-based vertical-flow immunoassay (VFA) and 2) a companion app for colorimetric detection of immunoassay results. The team designed the VFA in the shape of a square, with four wax-printed circles on the inside. Each circle contains immobilized antibodies to detect inflammatory biomarkers CRP, MMP-9 and IL-6.
The team designed the companion app to detect the presence of desired biomarkers and securely store information for the user. The app uses the mobile device’s camera and a color-detection algorithm to analyze and categorize colorimetric readouts from the VFA into high, medium or low intensities. The Perio-DX Kit provides for an easy-to-use, at-home testing system for early detection of inflammation.
Team 24039
PROJECT GOAL
Design a simulation of a smart energy grid system with interactive elements that produces a report analyzing Tucson Electric Power system efficiency and identifying major features or concerns.
Smart grids are electrical networks that use sensors and software to better match electrical supply and demand. This should be done autonomously while minimizing costs and maintaining electrical grid stability and reliability. Additionally, smart grid technologies can help manage the transition from nonrenewable to renewable energy sources, a matter of increasing urgency.
The design uses Simulink, a Matlab software environment, to represent a smart energy grid. The simulation file itself incorporates electrical grid aspects such as energy production, transmission and load balancing by using known models and algorithms. Along with the Simulink file, the system uses a combination of Matlab scripting, Matlab post-data processing, Python code, a JavaScriptbased server, and a graphical user interface (GUI) to maintain operability and flexibility.
Users will manipulate certain parameters and specifications within the simulation through the GUI, resulting in unique outputs for each set of parameters. Users can then analyze the data to further improve system efficiency and ensure that the energy grid is operating accurately as compared to real-life examples.
Team 24040
PROJECT GOAL
Develop a software tool named Junction Annotation & Network Utility System (JANUS) that will enable Northrop Grumman electrical engineers to create drawings, map drawings to tables within a technical interface diagram (TID), and replicate interconnections within a configuration file.
When designing electrical ground support equipment (EGSE) racks, electrical engineers typically create drawings and map those drawings to tables within a TID. Software engineers then replicate interconnections in the TID in a configuration file. However, this process can lead to inconsistencies that are often not found until later in the launch vehicle development process, which is undesirable.
The project optimizes communication between Northrop Grumman’s electrical and software engineers to streamline the design process for EGSE racks using our software, JANUS. The software tool automatically generates TID component tables, eliminating manual mapping and reducing inconsistencies and errors in launch vehicle development.
JANUS allows electrical engineers to upload diagrams, add component properties, and generate TID tables. Software engineers can view the TID in JANUS and request additional information, promoting efficiency and reducing errors in the design process. The project scope focuses on table generation and property clarification requests within the Visio-generated files. The tool successfully addresses and reduces the error-prone and tedious nature of the current process for both software and electrical engineers at Northrop Grumman, improving efficiency and reducing cost.
TEAM MEMBERS
Sebastian Govea, Systems Engineering
Adam Weida Hoffmeister, Software Engineering
Ian Johnson, Electrical and Computer Engineering
Gloria Romero, Electrical and Computer Engineering
Jamie Newhall, Engineering Management
Felipe Parra Polanco, Systems Engineering
COLLEGE MENTOR
James Sweetman
SPONSOR ADVISOR
Sabrina Huaraque
TEAM MEMBERS
Jesus Garcia, Electrical & Computer Engineering
Julia Rima, Electrical & Computer Engineering
Chase Craver, Engineering Management
Richardo Larez, Software Engineering
Rafael Pacheco, Electrical & Computer Engineering
COLLEGE MENTOR
Michael Madjerec
SPONSOR ADVISOR
Taylor Price
TEAM MEMBERS
Farah M Alqaraghuli, Chemical Engineering
JayCee Angel Miller, Biosystems Engineering
Ashley N Wheeler, Biomedical Engineering
Suleyman Omer, Biomedical Engineering
Paige Elisabeth Rudy, Biomedical Engineering
COLLEGE MENTOR
Don McDonald
SPONSOR ADVISOR
Marvin J Slepian
TEAM MEMBERS
Jaeden Carpenter, Electrical & Computer Engineering
Abiel Marquez, Electrical & Computer Engineering
Ameer Nessaee, Electrical & Computer Engineering
Marcus Vincent James Cathey, Biomedical Engineering
Max Farley, Biomedical Engineering
COLLEGE MENTOR
Don McDonald
SPONSOR ADVISOR
Marvin J Slepian
Team 24041
PROJECT GOAL
Develop a complete system to mechanically activate platelets to test the efficacy of agents that might limit shear-mediated platelet activation.
Thrombosis and clotting complications are major risks associated with implantation of cardiovascular therapeutic devices (CTDs). Patients with CTDs are often prescribed drugs that target biochemical pathways associated with the activation of platelets, cells that are responsible for blood coagulation. However, studies conducted by the Slepian lab found that no particular drugs in clinical use can block platelet activation induced by shear forces imparted upon blood flowing through CTDs. This is because those drugs were not developed to target mechanical mechanisms such as fluid shear.
This project’s primary objective is to develop a complete system for high-throughput drug screening of agents that could limit shear-mediated platelet activation. The team developed a design consisting of a motor-driven system, controlled by an Arduino and associated electronics, to magnetically drive a six-point stir-plate with 16 wells per motor magnet fitted to a 96-well plate for platelet activation. The system will allow for the screening of new potential drugs to inhibit shearmediated platelet activation.
The design has a custom base containing the motor magnets and a specialized lid with the stir mechanisms, enabling efficient sample agitation. In addition to the activation of mechanical/ electrical/magnetic devices, the design uses a custom PC-based application that will load raw data exported from the plate reader, perform normalization calculations, plot the normalized data, fit a function and save results for further statistical analysis.
Team 24042
Create a smart room kit using cameras, microphones and a handheld digital stethoscope to extract quantitative biomarkers from a patient during a clinical encounter.
As clinical encounters between patients and physicians become increasingly shorter due to requirements of electronic health record data entry, important patient information such as voice, action and behavior is often lost and never recorded. Diagnoses and advancements of care are limited to brief in-person physician observation. The Wired Room 2.0 captures this lost information from the physician’s exam room.
The Wired Room 2.0 captures this lost information using cameras for motion analysis, microphones for audio analysis, and a handheld digital stethoscope for close patient audio examination. The system’s motion analysis measures joint angles of limbs and digits using Google MediaPipe. For the audio analysis, the system employs speaker diarization to extract a new class of digital biomarkers, such as spectral entropy and spectral flux, from the patient to drive future artificial intelligence implementation within the doctor’s office. The stethoscope analysis uses a deep neural network trained and tested on state-of-the-art data to detect lung sound abnormalities such as crackles and wheezes. The Wired Room 2.0 brings the most quintessential medical encounter into the digital age.
Team 24043
PROJECT GOAL
Communicate and control a drone swarm from a ground station anywhere on Earth using a satellite network.
Using large, manned vessels to explore the ocean is expensive. Autonomous boat drone swarms provide a scalable and more affordable alternative for gathering critical ocean health data. This project designed a satellite communication system that will enable an operator to communicate with swarms of autonomous boats from anywhere on Earth.
The design uses the Iridium satellite network with the Ground Control service provider to communicate between a software-only ground station and drones with embedded satellite transceivers. The team defined the communication protocol to handle data flow and mission flow between the two. The ground station has a graphical user interface allowing the user to monitor and send missions to the drones. The team built four ESP32-based land test drones, or land rovers, to test and demonstrate the communication system. The system has the ability to run missions and gather sensor data through a full mission demonstration with all the drones.
TEAM MEMBERS
Ryan Mackenzie Theodore, Systems Engineering
Kai Michael Ward, Electrical & Computer Engineering
Conner Alubowicz, Systems Engineering
Aeris El Asslouj, Electrical & Computer Engineering
Joanne Robson, Systems Engineering
Michelle Ruhl, Mechanical Engineering
COLLEGE MENTOR
James Sweetman
SPONSOR ADVISORS
Marvin J Slepian
Joellen L Russell
Team 24044
PROJECT GOAL
Design and implement a subscale, subsonic wind tunnel to test the aerodynamic properties of launch vehicle nose cone geometries.
Engineers use wind tunnels to test and refine the aerodynamic properties of objects, especially in aerospace and automotive applications. A subscale wind tunnel is more affordable, portable and user-friendly than larger versions.
The team designed and built a subscale wind tunnel with the goal of producing variable air speeds of up to Mach 0.5 in the test section. The team calculated the necessary dimensions of the nozzle, diffuser and test section of the subscale wind tunnel based on the size and volumetric flow rate of a commercial fan to ensure the design met its air speed goal.
Additionally, the team 3D-modeled the entire wind tunnel and ran a computational fluid dynamics simulation to further confirm calculations. The design included both a test object fixture, which allows for variable angles of attack, and a smoke generation system, which enables visualization of streamlines flowing over the test object.
The team conducted testing with common nose cone shapes to verify results. The user can control air speed and smoke trails during testing, and the design supplies live data of air speed and temperature inside the test section. The final product is a fully operational wind tunnel, with the ability to visualize airflow at airspeeds up to Mach 0.5 over prototype launch vehicle nose cones.
TEAM MEMBERS
Oscar Jonathan Lopez, Electrical & Computer Engineering
Konnor Benjamin Raskin, Mechanical Engineering
AJ Sandler, Aerospace Engineering
Savannah A Shah, Mechanical Engineering
Alex Kylie Daily, Electrical & Computer Engineering
COLLEGE MENTOR
Doug May
SPONSOR ADVISOR
Sierra Rose
TEAM MEMBERS
Saul Durazo Martinez, Electrical & Computer Engineering
Julia Christine Otto, Electrical & Computer Engineering
Katelyn Rees, Mechanical Engineering
David William Ruddell, Software Engineering
Eric Meyer, Systems Engineering
Caleb Cook, Optical Sciences and Engineering
COLLEGE MENTOR
Jeff Scott Wolske
SPONSOR ADVISOR
Luke Baer
TEAM MEMBERS
Christian Mba, Mechanical Engineering
Jeff Neidkowski, Materials Science and Engineering
Mark Studer, Mechanical Engineering
Asem Hisham Alkhawar, Aerospace Engineering
Justin Garrett, Mechanical Engineering
COLLEGE MENTOR
Jeff Scott Wolske
SPONSOR ADVISOR
Roger Esplin
Team 24045
PROJECT GOAL
Design and build a basketball shooting robot to compete in a free throw competition against an Arizona Wildcats basketball team player, aiming to inspire K–12 students to pursue careers in science, technology, engineering and math (STEM).
The team designed the Hoopster basketball shooting robot to repeatably score shots from the free throw line in head-to-head competition against basketball sharpshooters while being completely mobile and autonomous. To achieve this, the team performed analysis, multi-disciplined design and rapid prototyping to develop and deliver a robot that navigates the court, autonomously detects the hoop, calculates precise power and trajectory, and repeatably scores baskets.
Hoopster uses a camera, computer vision algorithms, and unique, computer-controlled motors to calculate and align launch and azimuth angles. Algorithms calculate the ball launch velocity, which is controlled by a spinning flywheel launching mechanism. An Xbox controller allows an operator to navigate Hoopster around the court. A touchscreen display facilitates user launch control, and a motorized ball “feeding” system ensures consistent shots. Results have shown a greater than 90% free throw shooting percentage.
Designed for demonstrations and competitions, Hoopster is intended to ignite STEM interest in K–12 students by competing against skilled basketball players and showcasing the cutting-edge technology and engineering processes needed to design and build the robot.
Team 24046
Develop a modular, configurable test apparatus to fire beads, representing foreign objects, at various speeds and angles against representative radome samples to assess damage caused by impingement.
Aerospace radomes protect expensive and sensitive guidance equipment on the nose of aircraft. The team designed and built a system and damage-scoring process to assess radome materials’ durability against foreign object impingement (FOI) caused by striking rain, hail, birds or insects during high-speed flight.
The design combines a shooting mechanism, controller, software, safe test chamber, and radome mount, and a procedure to assess FOI damage against radomes. The team used design concepts from paintball guns, high-pressure gas components, and polymeric beads to simulate raindrop impacts from low speeds up to nearly 2,000 mph. The team also designed safety protocols with electrical and mechanical interlocks to protect personnel during operation.
During testing, an operator enters a desired velocity into a program that calculates a corresponding pressure to charge the shooting mechanism up to 1,000 pounds per square inch. Upon firing, the bead impacts the radome at selectable angles and is safely captured in a test chamber made of recycled steel and polycarbonate, which allows visual observation and capture of bead impact as well as velocity measurement using a standard ballistic chronograph. The team has delivered a safe system and process to assess real physical damage to radomes caused by FOI at various impact speeds.
Team 24047
PROJECT GOAL
Modernize and streamline a legacy audio interface system used in United States Coast Guard dispatch centers.
Efficient communication is critical to the processes of the United States Coast Guard. For the Coast Guard, every second matters when lives are at risk, thus audio interfaces must be reliable and easy to use. Coast Guard dispatch centers currently use a system that requires multiple interfaces and is cumbersome to reset and use. Additionally, many of the components used in the legacy system are at end of life, making the system difficult to maintain.
The team designed an updated audio interface, called the Dispatch Console Audio Interface (DCAI), that combines existing interfaces and uses modern components to ensure maintainability. The design also streamlines features to provide ease of use, all while maintaining or exceeding the legacy system’s performance.
The DCAI system uses custom printed circuit boards; a primary digital audio processing microcontroller; and a secondary interface control microcontroller to enable individual audio channel control, analog-to-digital and digital-to-analog signal conversion, Windows 10/11 compatibility, and signal noise reduction. This results in an all-in-one interface that allows dispatchers to quickly and reliably manage high-quality audio levels throughout a dispatch center.
TEAM MEMBERS
Malcolm Hayes, Electrical & Computer Engineering
Daniel Hinojos, Electrical & Computer Engineering
Max Rigler, Electrical & Computer Engineering
Jimmy Bordner, Systems Engineering
Tim Haines, Electrical & Computer Engineering
COLLEGE MENTOR
James Sweetman
SPONSOR ADVISORS
Glen Abousleman
Jason Landoll
Team 24048
PROJECT GOAL
Develop a system that can detect and track multiple classes of drones using their specific acoustic signatures.
Many small drones equipped with cameras or dangerous payloads do not emit signals that are traceable by conventional means (radio frequency, satellite communication, etc.), meaning they often go undetected until they are within the effective threat perimeter. Such drones can have an immense and brutal impact on property, critical information, and human life, so they must be detected and traced by other means at an actionable distance before they become a threat. Identifying drones before they become significant threats will have immense global, economic, environmental and societal impact.
The team has designed a system for military and commercial use using a tetrahedral microphone array with parabolic dishes to amplify received sound. This array is wired to a system composed of four Raspberry Pi computers. One Raspberry Pi acts as the primary device, controlling the system, and the other three act as secondary devices that collect data to send to the primary Raspberry Pi.
The system preprocesses the signal and feeds it into a classification model to accurately detect the drone’s signature. If the model detects a signal, it prompts the primary device to aggregate all relevant audio recordings from the secondary devices to calculate signal time delays and power differences between each microphone. This data is then sent to the tracking portion of the software to calculate the azimuth, elevation and range of the drone and displays it on the interface for the user to view.
TEAM MEMBERS
Kevin J Barnett, Electrical & Computer Engineering
Jonas Max Frandsen, Mechanical Engineering
Jeffrey Gabriellini, Systems Engineering
Drew Andrew Halloran, Systems Engineering
Maddie Grossnicklaus, Aerospace Engineering
COLLEGE MENTOR
James Sweetman
SPONSOR ADVISOR
Brandon Pitts
TEAM MEMBERS
Joshua Owens, Software Engineering
Carter Philipp, Electrical & Computer Engineering
Eric Teitelbaum, Electrical & Computer Engineering
Kevin Aquino Santiago, Systems Engineering
Richard M Gin, Electrical & Computer Engineering
COLLEGE MENTOR
Doug May
SPONSOR ADVISORS
Jeremy Radtke
Rene Van Alstine
TEAM MEMBERS
Nathan Randall Julicher, Mechanical Engineering
Thomas Schwab, Software Engineering, Electrical & Computer Engineering
Maximo S Ybarra, Mechanical Engineering
Jason Li, Systems Engineering
Chuy Talavera, Mechanical Engineering
COLLEGE MENTOR
James Sweetman
SPONSOR ADVISOR
Jim Bakarich
Team 24049
PROJECT GOAL
Create a multi-transmitter nodal network to provide location information in the event of GPS satellite disruption.
Security forces, first responders and autonomous systems are increasingly reliant on GPS to reach their destinations and navigate and maneuver once they arrive. While useful, this reliance makes them vulnerable to disruptions in GPS. In collaboration with the University of Massachusetts Lowell, the team created the LTDANN to overcome this vulnerability using a self-contained system which provides location information to a receiver within a range of 15 km.
LTDANN can determine the location of a single receiver by measuring the received signal strength indicator (RSSI) values from four nodes. Information is sent to a device that displays connection strength of each node and calculates the location of the receiver relative to each node. The team verified functionality and accuracy of LTDANN in a 15 km by 15 km area.
In addition to this, the team worked toward implementing a time difference of arrival (TDOA) system in the future by creating software with algorithms to implement time difference calculations and simulated results. A feasibility study showed that messages could be timestamped within nanoseconds of being received and the team created a method for remotely synchronizing and maintaining clocks within 10 microseconds over a period of 25 minutes.
Team 24050
PROJECT GOAL
Develop the STAR system, a lightweight and cost-effective micro-UAV to help first responders carry out aerial intelligence, surveillance, and reconnaissance (ISR) operations.
The team created a compact, rapidly deployable, cost-effective, and real-time reconnaissance solution for first responders. Without effective solutions like this, first responders face reduced efficiency and substantial security concerns. While several drone systems currently available on the market include the necessary functionalities, they are often too expensive. Recognizing this limitation, the team specifically tailored a drone solution to the needs of first responders that was affordable without compromising quality.
The STAR drone design is compact and versatile, featuring a sleek carbon fiber housing, and is designed to be launched from a 40 mm launcher. The team created a custom pneumatic launcher from the ground up to validate this required launch method.
The drone operates within a range of 250 m, reaches an operational altitude of 50 to 100 m, and can fly for at least five minutes despite its compact size. This ensures extended operational capabilities for time-sensitive missions when air support or other ISR assets are not immediately available. It is equipped with a high-resolution camera capable of discerning whether an individual is armed, and seamlessly transmits this live video to a connected ground station. The STAR drone will provide extended capabilities to the operators and enhance their effectiveness in the field, ultimately leading to more successful mission outcomes and safer communities.
Team 24051
PROJECT GOAL
Design and build a transportable machine for separating fibers from cannabis/hemp stalks to facilitate the creation of valuable bio-based products.
Hemp/cannabis growers face environmental, legal and economic challenges related to plant disposal after harvest. This project aims to ease this burden for growers, while transforming hemp/cannabis waste material into valuable bio-based products. The team designed and constructed a grower-friendly machine capable of separating hemp/cannabis stalks into two components: the outer bast fiber and inner woody hurd. The machine performs a mechanical decortication process, stripping the bast from the hurd, using a series of rollers. The smooth rollers crush and break the hurd, while the toothed rollers perform a scutching process to separate the fiber. For easier collection, the bast and hurd are then sorted through an angled grate, enabling the smaller hurd pieces to pass through and the longer bast fibers to remain on top. Additionally, the team investigated creating a grower-friendly pre-treatment step called retting, which is crucial for softening hemp/cannabis stalks prior to decortication.
The team first prototyped this decorticator using 3D-printed parts to test roller resistance and crush force. The finished machine consists of a steel frame, protective paneling, two pairs of rollers, an electrical operator interface, a variable frequency drive for roller speed control, a motor, drive system, and the separation grate. Springs in the top rollers are adjustable to accommodate differing stalk sizes.
Team 24052
PROJECT GOAL
Develop an educational platform capable of measuring seven physiological signals, enabling students to gather and analyze data safely and efficiently.
In the realm of biomedical engineering education, practical experience measuring signals from living systems is paramount. Consequently, classrooms have a pressing need for laboratory equipment capable of safely recording common physiological signals. To ensure widespread adoption in educational settings, such equipment must be affordable, easily repairable in-house and adaptable for future expansion. While commercial systems exist, a unified approach leveraging third-party hardware, expandable functionality, and open-source software remains elusive. Without such a cohesive framework, integrating measurement modules into academic curricula remains challenging.
Introducing the Biomedical Sensor Board for Education, dubbed the MediBrick 2000. This innovative device includes sensors for temperature, impedance, pulse oximetry, electrocardiography and a digital stethoscope. Leveraging a system-on-a-chip microcontroller as its core powerhouse, each sensor wirelessly communicates with a receiver module and is powered by a battery for enhanced mobility. Wireless communication is particularly crucial for safety, notably when using skin electrodes for certain sensors. The receiver module interfaces with the student’s computer, where a user-friendly graphical user interface displays data from each sensor. Students gain the flexibility to select and collect data from their chosen sensor, facilitating a more enriching academic experience in biomedical engineering.
TEAM MEMBERS
Abdulaziz Alenezy, Industrial Engineering
Natalie D’Angelo, Biosystems Engineering
Khai B Nguyen, Chemical Engineering
Emil Roy Schaffner, Mechanical Engineering
Josh Millikan, Industrial Engineering
Travis Anthony Dagostino, Mechanical Engineering
COLLEGE MENTOR
Matt Christensen
SPONSOR ADVISOR
Andrew Omar Arias
TEAM MEMBERS
Daniel Fabricio Campana Moscoso, Electrical & Computer Engineering
Michael Chase Morrett, Biosystems Engineering
Alec Alec Newman, Mechanical Engineering
Carmella Ocaya, Biomedical Engineering
Muad Alsayar, Electrical & Computer Engineering
COLLEGE MENTOR
Steve Larimore
SPONSOR ADVISOR
Urs Utzinger
TEAM MEMBERS
Paul Shaheen Lynch, Aerospace Engineering
Hannah N Perez, Aerospace Engineering
Neo Stilson, Aerospace Engineering
Connor Zell, Aerospace Engineering
Jake Daniel Hathaway, Aerospace Engineering
COLLEGE MENTOR
Jekan Thangavelauthum
SPONSOR ADVISOR
Adrien Bouskela
TEAM MEMBERS
Kolob P Farnsworth, Aerospace Engineering
Bobby Ivan Heitzinger, Aerospace Engineering
Aidan C Keller, Aerospace Engineering
Ryan Marts, Aerospace Engineering
Divya Venkadesh, Aerospace Engineering
Zach Purdie, Aerospace Engineering
COLLEGE MENTOR
Jekan Thangavelauthum
SPONSOR ADVISOR
Adrien Bouskela
PROJECT GOAL
Operate a CubeSat terrarium in low Earth orbit while preserving the life of contained fungi for two weeks to gain insights into life support systems in space.
Human civilization faces several potential human-caused and natural catastrophes that threaten to wipe out Earth’s rich biodiversity. A proposed plan would safely store Earth’s specimens under cryogenic conditions on the moon. However, unfreezing and preparing the specimens for reintroduction to Earth will likely require a series of space-based terrariums located between Earth and the moon. The team proposed to accomplish this by conceptualizing, designing and building a prototype space-based terrarium inside a 3U Centrifuge CubeSat with a total mass of 4 kg and a total volume of 3,000 cm3 that will operate in low Earth orbit for one to two years.
The first test will use fungus. By meticulously selecting and integrating various instruments such as thermometers, hygrometers and barometric sensors, this project aims to create and maintain optimal conditions for fungal growth within the confined space of the CubeSat. Through real-time monitoring and data collection, the team will learn how fungi adapt to microgravity and the challenges of space. Ultimately, this endeavor serves to advance our knowledge of space biology, contibuting to the preservation of biodiversity and paving the way for future long-duration space missions.
Prototype a rover capable of exploring the lunar south pole environment using an active rocker-bogie mobility system to navigate the rugged lunar terrain and an arm-mounted spectroscope for prospecting.
NASA’s Artemis mission, which will return humans to the moon, includes ambitious plans to explore little-known regions of the moon for unique features and resources. Accomplishing this will require a fully instrumented rover platform to traverse the lunar south pole craters and analyze the surface.
The SYLVIA prototype is a scale model of the team’s detailed design submission to the NASA RAS-CAL competition. In addition to the chemical analysis technique of Raman spectrometry capabilities, the team gave SYLVIA a unique active mobility system. Unlike traditional passive systems used in other rocker-bogie rover designs, SYLVIA’s active suspension system will enable it to navigate the rocky, powdery, and steep terrain expected in the regolith conditions of the de Gerlache Crater at the lunar south pole.
SYLVIA also has the capability to independently perform in-situ geological science to support prospecting and communicate with Earth using NASA’s Deep Space Network. Where possible, the rover may cache obtained samples for pickup by a future sample return mission. It is capable of operating for at least 90 Earth days and can upload a detailed prospecting report that provides estimates of surface resource reserves.
Team 24057
Explore lunar south pole craters for high-priority resources using a rover that can perform independent prospecting without other planned lunar assets and communicate with NASA’s Deep Space Network.
NASA’s Artemis mission, which will return humans to the moon, includes ambitious plans to explore little-known regions of the moon for unique features and resources. Accomplishing this will require a fully instrumented rover platform to traverse the lunar south pole craters and analyze the surface.
The team’s design concept is a semi-autonomous rover platform capable of determining high-fidelity resource distribution over large areas with minimal human intervention. The semi-autonomous platform reduces the amount of human interaction during the task of making a resource map, which requires a high number of data points evenly and closely distributed throughout a large area. This rover can operate in the low light, low temperature, high-radiation environments associated with permanently shadowed craters in the lunar south pole region. The rover can detect both surface and subsurface resources such as oxygen, water, aluminum, iron, titanium, silica and platinum.
TEAM MEMBERS
Tala Alsaedi, Aerospace Engineering
Parrish Cole Halbert Ballenger, Aerospace Engineering, Mechanical Engineering
Jacob LaRue, Aerospace Engineering
Oliver Smith, Aerospace Engineering
Brady Tober, Aerospace Engineering
Eric DeWitt Hall, Aerospace Engineering
COLLEGE MENTOR
Jekan Thangavelauthum
SPONSOR ADVISOR
Adrien Bouskela
Team 24058
PROJECT GOAL
Following the spirit of the American Institute of Aeronautics and Astronautics (AIAA) Design/Build/Fly competition, develop and construct a stable aircraft with a large payload for transporting patients, medical equipment, or medications, that maximizes comfort and performance.
Safe and effective transportation is essential for successful medical missions. The team addressed this need by designing a medical transport aircraft. The development mentality focused on adapting the AIAA Design/Build/Fly rules for designing, building and testing an electric aircraft. The team’s design follows the spirit of the AIAA competition while prioritizing the project’s medical payload mission focus. The goal was to create a balanced design with good, demonstrated flight handling qualities and practical and affordable manufacturing requirements while providing high vehicle performance.
Within the AIAA rules, the team chose to prioritize ensuring the aircraft provided a stable and comfortable flight for any included passengers and pilots and the payload. A critical design requirement was minimizing the chances of the payload coming loose and potentially harming the passengers, pilots or patients. The team adapted the final product from the tandem wing aircraft design and optimized or changed aspects to produce an aircraft that meets the mission needs. The goal was to create an aircraft with real-world medical transportation applications in mind. The team prioritized achieving that goal over creating an aircraft which would maximize its AIAA competition points.
TEAM MEMBERS
Kessler Dante Foreste, Aerospace Engineering
Keegan Miller, Aerospace Engineering
Matthew Rorvig, Aerospace Engineering
Adam Nekolny, Aerospace Engineering
Jordan Robert Tichenor, Aerospace Engineering
COLLEGE MENTOR
Jekan Thangavelauthum
SPONSOR ADVISOR
Adrien Bouskela
TEAM MEMBERS
Andrew Nelson, Aerospace Engineering
Adrian Y Patron, Aerospace Engineering
Kathrine Kim Yuk Tham, Aerospace Engineering
Austin Miller, Aerospace Engineering
Jacob Ruhle, Aerospace Engineering
COLLEGE MENTOR
Sergey Shkarayev
SPONSOR ADVISOR
Dr. Vitaliy Yurkiv
TEAM MEMBERS
Jim Cronin, Aerospace Engineering
Jimmy Arlyn Hamilton, Aerospace Engineering
Kongo Lai, Aerospace Engineering, Optical Sciences & Engineering
Ryland Phipps, Aerospace Engineering
Tayvien Ahmaud Williams, Applied Physics
COLLEGE MENTOR
Sergey Shkarayev
SPONSOR ADVISOR
Adrien Bouskela
Team 24059
PROJECT GOAL
Research materials and design the necessary technology to implement a structural battery for an aircraft that does not compromise its mechanical properties or structural integrity and compare that design with two identical airframes: one powered by a standard battery and one powered by internal combustion.
The aviation industry has increased its focus on the research and development of electric aircraft with the goal of reducing the industry’s greenhouse gas emissions and operational costs. Electric aircraft represent a promising solution; they offer lower carbon footprints and reduced noise pollution compared to conventional fossil fuel-powered aircraft. A safe and effective electric aircraft would enable the conversion to renewable energy usage and simplified power sources.
However, there are several challenges relating to the energy requirements of modern aircraft and the limited energy storage and overall weight of batteries. These challenges currently prevent electric aircraft from being competitive against conventional internal combustion aircraft – such as piston, turboprop or turbine powered aircraft – in their respective roles.
In efforts to overcome and eventually eliminate these challenges, the team designed a structural battery that effectively combines the function and mass of the battery with some structural elements of an aircraft. Research suggests this will increase the electrical energy capacity of the entire aircraft. For this project, the team focused on developing a structural aircraft battery that is rechargeable and specifically designed for an electric aircraft.
Design and build a payload that can measure both horizontal and vertical winds to measure turbulence at high altitudes. The payload will also attempt a mission with the NASA High Altitude Student Payload (HASP) competition.
This project identified potential flight areas for UA dynamic soaring gliders. The team designed and built a payload mounted on a weather balloon. The payload can measure both horizontal and vertical winds to determine characteristics of turbulence spectra at high altitudes of up to around 100,000 feet.
The team designed the payload to meet the NASA HASP specifications. This 3 kg box includes tri-sonic anemometers, autopilot PX4, GPS, computers, and video and radio links. There are also multiple-hole Pitot probes mounted on a boom (stationary or retractable) some distance from the main payload cradle. The team launched the payload to an altitude of 100,000 feet to collect atmospheric data and conducted data interpretation in collaboration with Alex Kling at the Planetary Systems Branch of the NASA Ames Research Center.
NASA plans to release the call for proposals for the HASP 2024 flight season later in 2023. The team has submitted this design to NASA’s competition. If selected, the team will test its measurement payload there in addition to planned flight testing at the local airfield in Tucson.
Team 24061
PROJECT GOAL
Design a solar sail-equipped CubeSat for use in a novel propulsion application that uses stored kinetic energy to propel secondary payloads.
A solar sail spacecraft capable of dynamic maneuvering can be used to de-orbit hazardous small debris, such as defunct satellites and asteroids, in orbit around the Earth. The team designed and built a novel CubeSat that can accomplish these maneuvers by using solar flux on a solar sail deployed from the CubeSat to create a moment on the system. This increases the CubeSat’s stored kinetic energy by converting the momentum from photons into rotational velocity. The sail is connected to the CubeSat via an angle-adjustable deployment arm to maximize the angular acceleration due to the solar flux.
A secondary payload, initially stored inside the chief CubeSat for the team’s proof-of-concept mission, will be deployed on a secondary arm. This payload will be released into a new orbit, converting the stored rotational velocity into translational velocity. This concept has the potential to provide a reusable method for deorbiting space debris and redirecting small satellites into new orbits. In addition to the design of the CubeSat, the team modeled the dynamics of the system and built a ground prototype to showcase the CubeSat operations and controls.
Team 24062
PROJECT GOAL
Design a new cannula system, the interconnection between an artificial heart and pneumatic driver, with improved wear resistance to prevent premature failure.
Heart disease is the leading cause of death in the United States, affecting over 6.5 million Americans per year. SynCardia’s TAH system will reduce the number of deaths from this disease. TAH uses cannula made of PVC and a spiral wire reinforcement that connects the artificial heart with a pneumatic driver system to provide pressure in the system. Unfortunately, this canula develops full and partial cracks and plastic degradation after only 180 days of use.
The team collaborated with SynCardia engineers to design a better cannula for the TAH system. The new canula uses an alternative material with lower plastic degradation and a new pattern of reinforcement. The team also created prototypes with external supports that solved the issue of cannula cracking. These prototypes are compatible with SynCardia’s testing apparatus and meet FDA regulatory requirements.
To account for and mitigate the risks of this life-giving project, the team conducted failure mode and effects analysis and design of experiment testing. This thorough testing demonstrated the superior performance of this new design compared to the current cannula. Additionally, the team worked within SynCardia’s quality assurance and regulatory compliance frameworks to fully document the changes made to the cannula for eventual FDA regulatory approval and seamless integration into the TAH system.
TEAM MEMBERS
Jackson W Barger, Aerospace Engineering
Shae Aspen Henley, Aerospace Engineering
Christian Lane LeClaire, Aerospace Engineering
Alec William Maloney, Aerospace Engineering
Samantha A Stevens, Aerospace Engineering
COLLEGE MENTOR
Jekan Thangavelauthum
SPONSOR ADVISOR
Sergey Shkarayev
Adrien Bouskela
TEAM MEMBERS
Abby Little, Mechanical Engineering
Jesus Alberto Mota Jr., Biomedical Engineering
Erik Navarro, Mechanical Engineering
Lucas Young, Biomedical Engineering
Safiyah Abdessalam, Biomedical Engineering
Logan Radomsky, Biomedical Engineering
COLLEGE MENTOR
Pat Caldwell
SPONSOR ADVISOR
Duffy Elmer
TEAM MEMBERS
Raghad Alabagi, Electrical and Computer Engineering
Alan Guerra Davis, Mechanical Engineering
Mario Weiler, Software Engineering
Ezra Athar, Biomedical Engineering
Sierra Speranza, Electrical & Computer Engineering, Mathematics
COLLEGE MENTOR
Mike Nofziger
SPONSOR ADVISORS
Kavan Hazeli
Mehrdad Pourjam
TEAM MEMBERS
Michael Gnesda, Optical Sciences & Engineering
Caroline Elizabeth Kenyon, Biosystems Engineering
Jong Park, Mechanical Engineering
Alex Quintero, Mechanical Engineering
Justin Offolter, Optical Sciences & Engineering
Christian Ryan Sookoo, Industrial Engineering
COLLEGE MENTOR
Michael Madjerec
SPONSOR ADVISOR
Ryan Luu
Team 24063
PROJECT GOAL
Detect and prevent falls and minimize harm to a person using a walker by using stabilizing and steadying techniques integrated into the walker.
Falls are a leading cause of accidental deaths worldwide, especially among elderly people. Research shows that traditional walkers are a major risk factor in falls. The team developed an innovative walker design that will reduce this risk by increasing stability and preventing harm in case the user does fall. With the integration of a fall-prevention system within a smart walker, this project aims to mitigate falls and increase quality of life for the elderly.
The smart component of the walker consists of a strategically placed inertial measurement unit in the walker as well as force sensors in the handles to provide essential data for assisting in detecting falls. These sensor data are measured by an Arduino microcontroller. An algorithm in the microcontroller triggers the fall-prevention system if the sensor readings reach the fall-risk threshold. This fall-prevention system consists of two components: automatic solenoid brakes that quickly stop the walker to provide the user with steady support and stabilizers with servo motors and linear actuators that rapidly extend in the direction of the fall and prevent the walker from tipping over.
Team 24064
PROJECT GOAL
Redesign and enhance the “red head” component of the F1 Drug Detector from Lightsense Technology.
Lightsense Technology developed the F1 Drug Detector that is capable of safely detecting concentrations of 0.1% to 1.0% of methamphetamine and 100 to 900 micrograms of fentanyl in a sample using emission spectroscopy. Optical instruments housed within the “red head” component of the device make detection possible. The previous model of the red head required technicians to manually assemble the optical components, a tedious and time-consuming process that led to inaccurate angle orientations and made efficient manufacturing impossible.
To resolve these challenges, the team redesigned the red head component. The new red head prototype used 3D computer-aided design to produce a 50/50 clamshell from machined aluminum in contrast to the older single piece design. This improved design allows for straightforward and efficient optical component installation and cost-effective manufacturing processes. The new design also implements features that improve moisture and drop resistance.
From this prototype, the team created a mold for Lightsense Technology that will increase manufacturing throughput, resulting in improved product distribution of the F1 Drug Detector. In turn, this will increase the safety and health of their customers, emergency responders and members of government agencies.
Team 24065
KIDNEY ADVANCE PROJECT
PROJECT GOAL
Develop a low-cost method of microplastic and PFAS detection in drinking water.
Drinking water across the globe is plagued by microplastic and PFAS contaminants that, when consumed over time, can cause detrimental health effects including altered metabolism, reproductive and developmental defects, and increased risk of cancer. Many microplastic particles (MPP) are invisible to the naked eye, meaning they go undetected in drinking water. Current methods of MPP detection are time-consuming and require specialized laboratory training and expensive equipment. In the pursuit of accessible water quality testing, the team set out to make MPP and PFAS detection fast, inexpensive, and achievable for researchers and homeowners alike.
To do this, the team built a portable fluorescence microscopy system with high resolution; a 7-inch by 12-inch footprint; a cost of $2,640; and an estimated volume production cost under $1,200. Fluorescence microscopy enables the system to provide state-of-the-art detection through increased contrast. In combination with a filtering system, third-party PFAS analysis, and an advanced thresholding algorithm, the team was able to accurately detect the concentration and size distribution of MPP down to 10 microns as well as concentrations of 55 different PFAS types in a water sample.
TEAM MEMBERS
Dani Balicki, Optical Sciences & Engineering
Rachel Emily Nehrmeyer, Environmental Engineering
Togzhan Spatayeva, Biomedical Engineering
Ashley Tittelbaugh, Electrical & Computer Engineering
Evan Brorby, Optical Sciences & Engineering
Matthew Martinez, Biosystems Engineering
COLLEGE MENTOR
Don McDonald
SPONSOR ADVISORS
Marvin J Slepian
Bijin Thajudeen
Joellen L Russell
Team 24066
Develop a rotational trainer to teach a batter how to respond to high rotational loads and be able to transfer energy efficiently into a bat.
Evaluating batters and increasing their proficiency at the plate is a key factor of a baseball teams’ success. By measuring a batter’s response to rotationally accelerating and decelerating their bodies through an applied load, a professional hitting coach can examine and correct a batter’s ability to transfer energy from their body into a bat. This energy transfer is often evaluated with swing trainers and tee hitting. The team improved on this assessment method by designing and building a novel trainer for evaluating a batter and improving their success at the plate.
The trainer design uses an autonomous mechanical assembly consisting of a ClearPath servo motor driven by a ClearCore controller and helical gearbox with handle attachments to rotate user input loads through a 180-degree axis. The team built a portable base frame with wheels to support the mechanical assembly of the trainer so it can be used in either indoor facilities or outdoor ball parks. Users can change various operational modes and display results –reaction response, peak force, and speed – on a Generation 4 touch screen tablet mounted on a telescopic post. Coaches can run multiple trainer routines and evaluate the results to teach batters how to better transfer body energy through a swing.
TEAM MEMBERS
Marisela De la ossa, Mechanical Engineering
Aksh Patel, Mechanical Engineering
Ryan Rathbun, Software Engineering
Xander Anakin Rouille, Mechanical Engineering
Juan Ruben Cortez, Mechanical Engineering
Nabor A Rios, Electrical & Computer Engineering
COLLEGE MENTOR
Michael Madjerec
SPONSOR ADVISORS
Bobby Basham
Jeff Kensrud
TEAM MEMBERS
Faisal Ahmed, Mechanical Engineering
Rachel Ball, Mechanical Engineering
Julie Mason, Electrical & Computer Engineering
Shriniketh Sreevatsan, Optical Sciences & Engineering
Jaret Rickel, Electrical & Computer Engineering
COLLEGE MENTOR
Jeff Scott Wolske
SPONSOR ADVISOR
Matthias Whitney
TEAM MEMBERS
Don Ishikawa, Industrial Engineering
Nick Scott Muzzy, Mechanical Engineering
Aurora E Watson, Materials Science & Engineering
Ellie Dickinson, Engineering Management
Samuel Rogers, Optical Sciences & Engineering
COLLEGE MENTOR
Jeff Scott Wolske
SPONSOR ADVISOR
Eric Holder
Design and deliver a robot that autonomously sorts beads based on shape, size, color and optical character recognition.
Optical sorting is used in different industries such as recycling, manufacturing and shipping. The team’s project objective was to design and build a robot that can perform this task autonomously using bead sorting as a proxy for these industries. The target parameters were to have it fit within a compact form factor of less than 27 cubic feet and be able to sort with 90% accuracy.
The SIPhTR team used analysis, machine learning and rapid prototyping to design and produce a system that uses cameras, computer vision technology, imaging software, mechanical structures and simple motors to sort beads autonomously. Users select sorting criteria via an LCD display to enable flexible and categorization modes. Unlike traditional sorting methods that rely on external assistance, SIPhTR operates independently. SIPhTR’s operational autonomy isolates beads by a “conveyor belt and chute”-style isolator. A Raspberry Pi handles all image processing and applies the necessary computer vision algorithms. Motors enable a trap door and funnel to place beads into categorized bins. After thorough design and evaluation, the team produced the final version of SIPhTR, a fully autonomous and compact optical sorting system capable of sorting beads to greater than 90% accuracy.
Develop a manufacturing and assembly process, and a full-scale prototype, of a visually realistic military vehicle for training military intelligence analysts.
Exercise planners, instructors, and adversary modelers need dynamic and realistic adversary targets on their ranges for intelligence personnel to practice on. These must be low-cost and easy to update. The team developed an affordable, transportable and visually realistic, full-size prototype target and rapid manufacturing process to meet this need. An essential objective was to create an easily replicable manufacturing plan and process that can be repeated across a variety of military vehicles. Additional objectives included ease of assembly, weather resistance and the incorporation of key visual identification features.
The team’s final design is a modular, collapsible model consisting of an aluminum frame, vinyl tarp, and wooden turret. The team focused on using easily accessible materials, most of which were tested for weather resistance and structural durability. Generic tools were selected for ease of assembly and to minimize field personnel training. An interactive manufacturing sheet allows users to pick between a selection of vehicles and generate exactly the number of parts, materials and dimensions required to produce the desired target vehicle. As proof of concept, the team completed the design and assembly of a full-size HQ-7B vehicle that includes all key visual identification features.
Team 24069
PROJECT GOAL
Design and build a mechanized system to prevent wind from upending plastic covers used in copper leaching processes.
Copper is at the heart of the energy transition. Technologies critical to the energy transition such as electric vehicles, charging infrastructure, solar photovoltaics, wind power, and batteries all require much more copper than conventional fossil-based counterparts. Analysts forecast that copper supply must double by 2035 to support global decarbonization initiatives and objectives. However, bringing on new copper supply is challenging and may delay the energy transition.
Copper leaching is a mining technique that increases ore yields. This can be done by covering leach stockpiles with a thin plastic tarp to increase heat, but today’s manual covering process is labor-intensive, easily upended by wind, and potentially hazardous to employees.
To reduce these effects, the team designed and delivered a fully functional system to deploy a chain weight off of a reel during plastic cover installs. The mechanized design seamlessly integrates with a track-type bulldozer and uses integrated mechanical and electrical systems to automatically adjust the rate of chain deployment to match the plastic tarp deployment speed using a magnetic particle brake. Once deployed, the chain’s weight prevents wind from upending the cover. A hydraulic motor winds the chain link back onto the reel after use. The team’s tests show this is a safe, reliable, efficient system that prevents wind from upending the plastic tarps, improving safety and increasing mine yield by up to 10%.
Team 24070
PROJECT GOAL
Enhance safety, precision, and reliability in material sampling of finished products from mining hydrocyclones by implementing an automated sampling system.
Accurate and consistent sampling is crucial for process control and optimization, but traditional manual sampling methods are labor-intensive, and the hazardous nature of the environment poses safety risks to personnel. Taking into consideration the diversity of roles and form factors of mining hydrocyclones, the team designed and tested an automated sampling system for FLSmidth that is scalable, inexpensive, and easily serviceable.
The team’s Automated Material Sampling System (AMSS) incorporates a rack-and-pinion based sampling arm powered by an electric DC motor, a precise positioning sensor, and environmental shielding that is housed in a modular aluminum frame. It is designed to extract samples in a reliable and regulated manner. AMSS is lightweight and fully self-contained with its own power source, allowing operators to easily move it. By incorporating safety features such as fail-safe mechanisms and real-time system monitoring, AMSS mitigates risks associated with its operation and contributes to enhanced overall productivity and safety of operations in mining processing facilities.
In addition to building AMSS, the team provided recommendations to FLSmidth for adapting AMSS to a rail system so it could move to different locations in larger hydrocyclones. This will be designed and integrated in a future project.
TEAM MEMBERS
Raed Ahmed AlGhamdi, Industrial Engineering
George Edward Collias, Electrical & Computer Engineering
Daniel Kersey, Industrial Engineering
Eric Pelto, Mechanical Engineering
Cole David Wolfe, Mechanical Engineering
COLLEGE MENTOR
Jeff Scott Wolske
SPONSOR ADVISORS
Robert Crossman
Jared Sundberg
TEAM MEMBERS
Abdullah Ahmad, Industrial Engineering
Hudson H Coggins, Mechanical Engineering
Sam Kerns, Electrical & Computer Engineering
Tairzhan Kozhabergenov, Industrial Engineering
Aditya Krishna Kannan, Mechanical Engineering
Nick Hinrichs, Electrical and Computer Engineering
COLLEGE MENTOR
Michael Madjerec
SPONSOR ADVISORS
Kevin Soukup
Edward Monteverde
Francisco Yerena
TEAM MEMBERS
Nathan Kaku, Mechanical Engineering
Sebastian Magri, Optical Sciences & Engineering
Vaishnavi Narayanan, Electrical & Computer Engineering, Mathematics, Physiology & Medical Sciences, Psychology
Jesus A Siqueiros, Biomedical Engineering
Tom Thomas Murickan, Biomedical Engineering, Biochemistry
Susan Burrell, Biomedical Engineering, Mathematics
COLLEGE MENTOR
Mike Nofziger
SPONSOR ADVISORS
Dan Latt
Russell Witte
TEAM MEMBERS
Thomas Gentrup, Electrical & Computer Engineering
Jeff Horwitz, Biosystems Engineering
Colin Maroe, Mechanical Engineering
Lauren Vasquez, Biosystems Engineering
Minghao Zhang, Mechanical Engineering
Devin B Dafoe, Systems Engineering
Jeremy Ryan Sharp, Electrical & Computer Engineering
COLLEGE MENTOR
Steve Larimore
SPONSOR ADVISOR
Matthew S Recsetar
Team 24071
PROJECT GOAL
Build an ultrasonic imaging system to automatically measure the plantar arch structures of the human foot.
Standard B-mode ultrasound imaging and shear wave elastography can be used to analyze physiological tissue to gain pertinent information such as tissue stiffness. Current applications focus on internal organs; however novel research has extended these imaging modalities to the plantar arch structures of the foot.
No standard method or device exists to perform these scans with consistency and ease, so the team created an innovative mechanical system to perform autonomous scans of the foot using existing ultrasound probes. The system performs a 2D scan of the plantar arch soft tissue utilizing linear mechanical stages. A technician can perform the scan while a patient is standing for an accurate assessment of tissue health, and the system contains weight sensors to provide biofeedback regarding uneven patient weight distribution.
The device accommodates shoe sizes from a women’s size 5 through a men’s size 13 and supports patients up to 400 lbs. To enhance accessibility for individuals with disabilities, the device is equipped with support rails and ADA-compliant steps, ensuring all patients can undergo scans safely and comfortably. After assessment, the system processes and formats the completed scan to create a 3D model of the stiffness of the arch-supporting ligaments for clinician analysis.
Team 24072
Design and deploy a device capable of autonomously cleaning Light Expanded Clay Aggregate (LECA) media for integration into aquaponic farming systems.
Aquaponics is a symbiotic cultivation method combining hydroponics and aquaculture that relies heavily on LECA as a growth medium for supporting plant root systems. However, the current manual process of cleaning LECA is labor-intensive and time-consuming, requiring nearly three days from start to finish.
In response to this challenge, the team designed and constructed the Aquaponics Media Cleaning System (AMCS) to automate the arduous task of separating LECA from unwanted materials such as roots and sediment. The AMCS is made of a suite of components including a root masticator, a primary tumbling chamber, a hydraulic washing system, and a conveyor belt mechanism for final sorting. Crucially, the entire cleaning process is orchestrated by an Arduino microcontroller, affording users the flexibility to customize process durations and sequences to suit their specific requirements.
Designed with the demands of greenhouse environments in mind, the AMCS prioritizes durability, user-friendliness, and safety. By seamlessly integrating with aquaponic farming systems, this innovative device promises to significantly reduce both the time and manual effort associated with LECA cleaning, thereby enhancing operational efficiency and productivity in aquaponic farming endeavors.
Team 24073
PROJECT GOAL
Generate water droplets at a set frequency and successfully detect their presence using laser light and opto-electronic components.
The team created the Laser Diode Based Metrology Module (LDBMM) to supplement an existing lithography system used by ASML that uses an extreme ultraviolet (EUV) laser to facilitate highprecision etching of semiconductor wafers. In one step in the process, a high-powered laser vaporizes droplets of molten tin. This project is a proof of concept of a system that can detect the precise moment a droplet of tin enters the system so that the high-power lithography laser can be triggered with high temporal accuracy. An accurate, low-latency system allows for increased tin droplet frequency, higher extreme untraviolet power, and the production of more wafers per hour.
The LDBMM is composed of a water droplet generator, visible laser diode, anamorphic prism pair and a silicon photodetector. A custom microfluidic dispenser introduces a droplet into the laser beam path between the prism pair and photodetector, and the photodetector senses the interruption in the optical signal. The system electronics and software log the exact moment of detection and relay this information to the user. The LDBMM is light enough to be portable and compact enough to sit on a test bench.
TEAM MEMBERS
Jordan Shea Cheema, Mechanical Engineering
Pablo Antonio De La Fuente, Mechanical Engineering
Emily Noethen, Optical Sciences & Engineering, Mathematics
Katie Twitchell, Optical Sciences & Engineering, Statistics & Data Science
Amie Celine Rott, Optical Sciences & Engineering, Mathematics
Amelia Miles, Systems Engineering, Aerospace Engineering, Military Science & Leadership
COLLEGE MENTOR
Mike Nofziger
SPONSOR ADVISOR
Erik Huerta
Team 24074
PROJECT GOAL
Propose and design a feasible mine design for a metallic mineral deposit based on real-world constraints provided by the Society of Mining Engineers Metallic Mine Design Competition.
The Deep Rock Geologic team competed in the Society of Mining Engineers Metallic Mine Design Competition for students majoring in mining-related engineering fields. This year’s competition involved completing an Order of Magnitude Study for the La Grande Lithium Project located in Northern Quebec, Canada. The project consisted of two phases spaced over the year.
In the project’s first phase, the team developed an economic plan for a mine and designed a mill to produce a 6% lithium concentrate. This was based on the idea of crafting an engineering solution to a problem posed by the company’s chief engineer. During the second phase of the project, the competition placed new economic constraints on the team and the team had to design a processing plant capable of producing high-grade lithium for direct shipment to battery manufacturers. This was presented as a proposed solution to company leadership. The team redesigned the mine with a higher cut-off grade, developed a new processing plant, and updated the project economics based on the Phase 2 study results.
The Society of Mining Engineers awarded the Deep Rock Geologic Team second place overall in the Metallic Mine Competition.
TEAM MEMBERS
Brynn M Brettell, Mining Engineering
Carter Brown, Mining Engineering
Matthew J Gray, Mining Engineering
John Kyle Stubblefield, Mining Engineering
Sundari Udall, Mining Engineering
COLLEGE MENTOR
Edward Clifton Wellman
SPONSOR ADVISOR
Edward Clifton Wellman
TEAM MEMBERS
Geoffrey Sven Gill, Mining Engineering
Seth Michael Kreinbrook, Mining Engineering
Jeremie Mat Mwaku, Mining Engineering
August Martinez Roquet, Mining Engineering
Grady Sherwood, Mining Engineering
COLLEGE MENTOR
Edward Clifton Wellman
SPONSOR ADVISOR
Gail Heath
James Werner
TEAM MEMBERS
Reyna E Clark, Mining Engineering
Esteban Guerrero Murrieta, Mining Engineering
Ethan Lathrem, Mining Engineering
Savannah M Stewart, Mining Engineering
Joseph A Welch, Mining Engineering
Shayne Elise Zadro, Mining Engineering
COLLEGE MENTOR
Edward Clifton Wellman
SPONSOR ADVISORS
Sunghee Lee
Curtis Wettstein
Team 24075
Use geophysics and geotechnical investigations to determine the most suitable location to place a new portal and subsequent decline at the University of Arizona’s San Xavier mine.
The San Xavier West Portal Expansion team was asked to determine a suitable location and design for a new portal expansion on the western side of the San Xavier mine site. To do so, the team performed a comprehensive geophysical investigation utilizing magnetometry. This yielded a plethora of geologic and structural interpretations regarding the 17-acre survey area. After considering geotechnics, cost, and safety, the team concluded that the new expansion should be located in the northeastern portion of the survey area: a location with consistent granodiorite exhibiting a strong magnetic susceptibility. A risk matrix helped confirm the exact location of the new portal based on a myriad of design considerations including portal dimension, rock support, cut geometry, waste placement and equipment selection. Ultimately, the team determined that a 20-foot by 20-foot arched portal was required to accommodate San Xavier’s future plans to acquire a 60-ton haul truck.
Project sponsors also indicated interest in connecting the west portal to the existing east portal at a straight, low grade for testing equipment at high speeds. To accommodate this, the planned grade will never exceed 15%, ensuring adequate operating conditions for the most extreme design requirements. With the team’s plan for the first 100 m of expansion, this project should provide the project sponsors with the appropriate resources to continue development in the area.
Team 24076
Provide Pinto Valley Mine with an open pit design to serve as Phase 3 while considering eliminating the pit’s East ramp, geotechnical constraints, and maximizing the mine’s net present value (NPV).
Capstone Mining asked the Phase 3 Pit Design project team to analyze its current long-range mining plan. The team identified potential designs and made recommendations to maximize the mine’s NPV, the primary measurement of the mine project’s value.
The team considered constraints attributed to the mine site’s geology. Lerch-Grossman cone calculations, the industry standard iterative phase-design process, determined the ultimate pit limit of the mine. Based off a specified starting point, the mineral deposit geometry, mining and processing costs, economic pit limits, and metal prices, the team was able to incorporate an economic analysis of the final pit design with an emphasis on maximizing the operation’s NPV.
The team completed a comparison of the economic limits within the geotechnical constraints and developed base pit shell designs. This included the roads and necessary adjustments based on the Lerch-Grossman cones. These designs and analyses were all performed with the mine design software MinePlan3D, provided by Hexagon. These designs were reviewed by the MGE Faculty and Capstone Mining to ensure design constraints were appropriately incorporated and to accommodate any potential design changes early in the process. The pushback shell was finalized following that review, and scheduling began shortly after.
The outcome of this phase design study is a mine plan, an economic model, and a written report documenting the mine design analysis.
Team 24077
Design a portable drying system equipped with a forced and heated air system that will decrease the total amount of drying time for alfalfa.
For many retail and wholesale applications, it is necessary to dry alfalfa after harvesting. An alfalfa dryer reduces the curing time required to process alfalfa, lessening the chances of loss due to rain, moisture, fire and spontaneous combustion. The more efficiently the alfalfa can be dried, the greater the potential revenue.
The team developed a concept for a mobile alfalfa drying system that can move to harvest locations and dry alfalfa at or near the point of harvest. The deliverable is an operational and patentable mobile alfalfa drying system suitable for commercial use that can be replicated and disseminated to a wide market.
The team’s concept reconciled the design parameters of previous fixed-site alfalfa drying systems with the constraints of an economically buildable portable drying system. The result was the Mobile Alfalfa Drying System. This device has an inlet for placing alfalfa inside the trailer and a cover consisting of a cap equipped with a tube system that functions as an inlet and outlet for heated air to dry the product within a short period of time. Based on the difference in temperature, volume, and moisture level, the team calculated that the design’s British thermal unit (a measure of heat content) and cubic foot per minute (airflow volume) meet the goals of efficiently drying alfalfa in the field.
Team 24078
Develop a hydraulic tool attachment to remove sediment buildup within a concrete-lined irrigation canal for the Bard Water District.
Continuous sediment buildup slows the water flow in the Bard Water District’s concrete-lined agricultural irrigation canals. Bard’s current method for removing this sediment, an improvised mechanical device to clear buildup, is inadequate. As a result, their concrete-lined irrigation canals operate at reduced efficiency and reliability and there is an increased danger of pathogen growth and distribution.
To address this problem, the team developed a new system for sediment removal that Bard Water District can use while the concrete-lined irrigation canals are at or below 60% capacity. The goal was to design, prototype, test and deliver a system compatible with current hardware that can clear sedimentary deposition buildup from the canals to the same or a greater degree than current methods while achieving improvements in cost, schedule and safety.
The design concept was to use pressurized water to force the sedimentary deposits in the canal’s direction of flow to a point at which they can be safely extracted from the canal. The system will be submerged in the canal and turn up sediment so it can move constantly with the flow in the canal. At the conclusion of the project, the team will transition control to the Bard, California, Water District with a technical data package and close out report including all intellectual property created through the project.
TEAM MEMBERS
Marcos Eduardo Andrade Meza, Biosystems Engineering
Joan Hernandez-Landey, Systems Engineering
Miguel Lua, Systems Engineering
Josue Nunez, Systems Engineering
Juleanna Rios-Monge, Industrial Engineering
COLLEGE MENTOR
Samuel Peffers
SPONSOR ADVISOR
Kenneth Bingham
TEAM MEMBERS
David Alejandro Brito Coronado, Systems Engineering
Jo Guler, Biosystems Engineering
Walter Loel Stoltz-McCormick, Systems Engineering
Nick Okada, Engineering Management
COLLEGE MENTOR
Samuel Peffers
SPONSOR ADVISOR
Nick Bahr
TEAM MEMBERS
Sam Hasbrouck Bevier, Aerospace Engineering
Zenith Prakash Kumar Mesa, Aerospace Engineering
Colby Thomas, Aerospace Engineering
COLLEGE MENTOR
Sergey Shkarayev
SPONSOR ADVISOR
Jekan Thangavelauthum
TEAM MEMBERS
Jaqueline Diaz, Environmental Engineering
Linda M Engelman, Environmental Engineering
Irbis J Martinez, Environmental Engineering
Danielle Marie Schroeder, Environmental Engineering
COLLEGE MENTOR
Adrianna Brush
SPONSOR ADVISOR
Lisa A Jones
Team 24079
Develop and validate a novel spring-loaded landing and launch system for a lunar lander model.
NASA’s Artemis program aims to return humans to the moon. One of the main challenges the Artemis astronauts will face is plume-surface interaction (PSI), which is dust kicked up by landing craft.
NASA created the Human Lander Challenge to encourage engineering students to develop and test innovative solutions to this problem.
The Lunar Pioneers team chose to address the risk of PSI in NASA’s competition by focusing on the landing and launch system because this is one of the primary times when a large amount of dust is kicked up. A spring-loaded landing and launch system will minimize PSI and allow for extended engine cutoff heights during landing. The team created and tested a prototype of this spring-loaded landing and launch system integrated into a model lander. This successful test demonstrated the structural feasibility of this mechanism and reliability in simulated lunar conditions.
The team’s prototype method for reducing PSI contributes to the advancement of lunar exploration technologies. Ultimately, this new method for launch and landing will support future human exploration missions to the moon and beyond.
Team 24080
Design an economical, nature-based stormwater management system to solve flooding and drainage issues in Miami, Arizona.
This project aims to address flooding and drainage problems faced by the people of Miami, Arizona, in accordance with the most recent United States stormwater management plans. A recent wildfire in the area exacerbated flooding issues by stripping greenery from the surrounding mountains, which caused more water flow into the town. In addition to increasing floods, a significant part of the population falls below the poverty line. This has restricted adequate access to the resources needed to address these flooding and drainage issues. These community attributes were the driving forces behind the team’s choice to select Miami as the focal point for the design of a stormwater drainage system that is highly effective, while keeping in mind the socioeconomic and physical landscape of the community.
The proposed stormwater design is based on the team’s comprehensive analysis of the town’s topography, soil composition and water flow contributing to flooding in Miami. To understand the broader implications of the design implementation, the team considered the town’s history and social dynamics when making the design. In addition to mitigating flooding, the project emphasizes the creation of recreational green spaces as part of the stormwater management strategy. The team delivered a sustainable solution that met the needs of the community while aligning with contemporary stormwater management principles.
Team 24081
PROJECT GOAL
Develop a process for harnessing the abundant oxygen resources present on the moon.
The moon’s surface holds a vast reservoir of oxygen within its regolith, the rocky surface composed of minerals and compounds such as ilmenite. However, this oxygen is not readily available in its gaseous form. Instead, it is chemically bound within the regolith. This presents an opportunity for application of chemical engineering tools and techniques. The team has proposed an innovative process using a hydrogen reduction reaction and electrolyzer that can efficiently extract oxygen from the regolith. The team created a process simulation of the proposed method that details sizing, flow rates, purity and composition of the oxygen extracted from the regolith. Additionally, the team used this simulation to estimate the cost, energy requirements, and production time of this process.
The results of this project will form the basis of a device that will ultimately produce usable oxygen stores for propellent and life support in various future space exploration missions.
TEAM MEMBERS
Tobi D Adigun, Chemical Engineering
Rachel Amland, Chemical Engineering
Julian Andrew Duff, Chemical Engineering
Gage Duncan, Chemical Engineering
COLLEGE MENTOR
Adrianna Brush
SPONSOR ADVISOR
Farhang Shadman
Team 24082
PROJECT GOAL
Design a preliminary system to convert coal into 5,000 metric tons of methanol per day.
The project aims to address the increasing demand for chemical feedstocks that have been prompted by rising crude oil prices. As crude oil becomes more expensive, countries with little to no access to this resource are trying to find better alternatives to use for fuels. Methanol is one potential alternative. It can be produced by processing coal, which is still relatively abundant, as the primary fuel source. The coal is burned to produce syngas, which can then be refined into methanol.
The team proposed to produce methanol from coal reserves in the United States, leveraging the country’s abundant coal resources. The objective was to design a system capable of converting coal into 5,000 metric tons of methanol per day while prioritizing cost-effectiveness and minimizing the environmental impact.
The key criteria for this project were maximizing methanol purity and ensuring economic competitiveness in the international marketplace. The team chose lignite coal for its low cost and reduced sulfur and nitrogen content, which lowers treatment and maintenance expenses. Oxygen supply at 99.5% purity was sourced from a nearby plant to drive this reaction.
TEAM MEMBERS
Alberto Borboa, Chemical Engineering
Mikalie Ann Caldwell, Chemical Engineering
Logan Patrick Johnson, Chemical Engineering
Emily Colette Lofgren, Chemical Engineering
COLLEGE MENTOR
Adrianna Brush
SPONSOR ADVISOR
Robert Siml
TEAM MEMBERS
Jonah Vincent Olson, Environmental Engineering
Isaac Walter Yilmaz Peters, Environmental Engineering
Citlali Ramirez, Environmental Engineering
Harrison Frederick Wood, Environmental Engineering
COLLEGE MENTOR
Adrianna Brush
SPONSOR ADVISOR
Adrianna Brush
TEAM MEMBERS
Jocelyn Sara Brooks, Chemical Engineering
Patrick Lee Dewsnup, Chemical Engineering
Evan Alexander Gruszka, Chemical Engineering
Denae Ynes Ytuarte, Chemical Engineering
COLLEGE MENTOR
Adrianna Brush
SPONSOR ADVISOR
Marvin J Slepian
Team 24083
PROJECT GOAL
Create a design proposal for the expansion of the Rainbow Valley Water Treatment Plant that will meet constituent removal levels for future elevated flows and provide plant redundancy.
The Arizona Water Association hosts a yearly student design competition that tasks students with an engineering analysis and design project related to a water treatment plant. Teams are challenged to create innovative and cost-effective methods to meet the competition design goals.
This year, the schools were asked to design a recommendation for expansion for the Rainbow Valley Water Reclamation Facility utilizing three wastewater treatment evaluations, including conventional activated sludge, membrane biological reactors (MBR), and an alternative technology.
The team analyzed these three options and determined the MBR to be the best option for solids treatment. In addition, the team’s design for expansion improves reliability and operational consistency. The team also determined a recommended timeline for construction, an estimate for operation and maintenance, and an opinion of probable construction cost.
Team 24084
PROJECT GOAL
Design and prove the viability of a water recycling system for spent dialysis fluid to reduce water consumption during treatment.
Hemodialysis is a medical treatment that artificially filters waste and excess fluid from the blood of patients with renal failure. It is a critical therapy that can keep people healthy for many years, but the process uses large volumes of water to create dialysate. This fluid is typically discarded after the patient receives treatment, meaning that the benefits of dialysis come with a large and expensive water footprint.
To address this issue, the team created Dialy-ssist, a recycling system for spent dialysate that returns clean water. The system is a multi-stage purification process that uses activated carbon, zirconium, DI resin, UV sterilization, and urease. Through this novel process, Dialy-ssist is capable of removing salts, uremic toxins and bacteria from the used dialysate. This allows the treated effluent to be safely reused as water in future dialysis sessions. In addition to minimizing the environmental impact of this medical treatment, Dialy-ssist has the potential to provide patients with increased mobility by reducing the amount of time they need to be connected to a water source during treatment.
PROJECT GOAL
Design and scale-up a pharmaceutical manufacturing process that involves KinetiSol® processing technology.
KinetiSol® processing is a fusion-based, solvent-free process that utilizes frictional and shear energies to rapidly transition crystalline drugs and polymers into an amorphous solid dispersion. It has been applied to many poorly soluble molecules and has proven to be a bioavailability enhancement solution at all levels of development. Currently, KinetiSol® is protected intellectual property and is only used on a small manufacturing and research-level scale.
The team’s goal was to upscale the pharmaceutical manufacturing process of KinetiSol® using abiraterone, a hormone therapy drug used to treat advanced prostate cancer (especially castrateresistant prostate cancer), as the model active pharmaceutical ingredient (API). For many cancer patients, abiraterone is the last line of defense, but it is hard to absorb. Currently, abiraterone is produced and sold as ZYTIGA by Janssen utilizing spray-drying to make a soluble amorphous solid dispersion. Making it bioavailable using KinetiSol® is game-changing. By reducing processing time and the need for chlorinated solvents, and enhancing the bioavailability, KinetiSol® offers a more efficient and affordable process.
The team produced a feasible manufacturing pathway using KinetiSol® to provide a comparable replacement and improvement to the spray-drying technique. This proved that abiraterone can be made more affordable for cancer patients through reduced manufacturing costs and times. This process can also be modeled and expanded to other compatible small molecule APIs.
Design a water treatment process that effectively and efficiently removes hydrocarbons and other contaminants from produced water, a common byproduct of oil well extraction.
Produced water is a prevalent liquid byproduct in various oil extraction processes. This consumption of water for extraction drains limited water resources and contaminates it in a way that is difficult to clean for reuse. This leads to water scarcity.
The Produced Water Reclamation Project’s goal was to create a method for decontaminating the produced water to make a new sustainable source of water to supplement other needs, such as agriculture and tourism.
The team proposed and designed a treatment process to eliminate the free oil, dissolved hydrocarbons, total dissolved solids, hydrogen sulfide, and total suspended solids from produced water. The overarching goal of this initiative was to address water scarcity in New Mexico by advocating for the treatment and utilization of produced water instead of the continuous use of valuable Colorado River water that could be better utilized for agricultural, municipal or industrial use.
TEAM MEMBERS
Porter J Bradley, Chemical Engineering
Emily Laura Hom, Chemical Engineering
Tamar Ozer, Chemical Engineering
Sam Scott Winegarden, Chemical Engineering
COLLEGE MENTOR
Adrianna Brush
SPONSOR ADVISOR
Thomas Olden
TEAM MEMBERS
Manuel Andres Amavizca, Chemical Engineering
Mike Brown, Environmental Engineering
Fabiana Murrieta Mercado, Environmental Engineering
COLLEGE MENTOR
Adrianna Brush
SPONSOR ADVISOR
Harry Patton
TEAM MEMBERS
Cassidy Ann Chang, Environmental Engineering
Tea Iwai, Environmental Engineering
Faith Siepker, Environmental Engineering
Lorinda Leigh Treadway, Environmental Engineering
COLLEGE MENTOR
Adrianna Brush
SPONSOR ADVISOR
Kimberly L Ogden
TEAM MEMBERS
Wenli Liu, Chemical Engineering
Edwin Machado, Chemical Engineering
Ahmed Wasif Mustakim, Chemical Engineering
Elijah Zachary Reveles, Chemical Engineering
COLLEGE MENTOR
Adrianna Brush
SPONSOR ADVISOR
Adrianna Brush
Team 24087
PROJECT GOAL
Design a carbon capture system using a new polymer mesh technology to reduce natural gas plant emissions and produces an algae feed product.
Greenhouse gases (GHGs) absorb heat and create a blanket in Earth’s atmosphere, resulting in increased global temperatures. Carbon dioxide is the main GHG that is emitted due to anthropogenic activity, and flue gas from natural gas power plants constitutes 35% of total emissions.
Carbon capture and storage methods refer to technology able to remove this carbon dioxide from the atmosphere and sequester it in plants, soil or water. Algae is one promising example that has the capacity to effectively sequester carbon dioxide. In addition to high carbon utilization and growth rates, algal biomass can be converted into useful products such as biofuel and animal feed supplements.
Lawrence Livermore National Laboratory has developed a polymer composite mesh that selectively adsorbs carbon dioxide from flue gas. The team performed a technoeconomic analysis of this mesh to determine the feasibility of using this method over the existing direct injection method of carbon capture. The analysis included a design of a polymer mesh composite capture system which contains algae ponds and harvesting equipment. The aim was to produce the most algae and capture the most carbon.
Team 24088
PROJECT GOAL
Create a process in which osmotic distillation is used to remove ethanol from beer to reach a goal of 2% ABV beer while maintaining its original taste and aroma.
The market for low-alcoholic beverages has seen a rise in demand over the past decade due to the introduction of new laws around driving under the influence of alcohol, increase in education and awareness of the significance and impact of a healthy lifestyle, and even religious reasons. More people are opting to drink low-alcoholic beverages instead of traditional alcoholic ones. Despite this demand, the low-alcoholic beverages industry still has a long way to go before it can manufacture a product with all the desirable qualities of a top-quality alcoholic beverage.
The biggest challenge in the dealcoholization process is maintaining the volatile organic aromatic compounds that give rise to the authentic flavor of the alcoholic beverage. These compounds are typically lost with change of temperature and pressure. In this project, the team used osmotic distillation, a membrane-based separation process capable of running at low pressures and ambient temperatures. This preserves the aromatic compounds in beer with the goal of creating a low alcoholic beverage with almost all the desirable qualities of a regular alcoholic beer. The team optimized the dealcoholization process to create a product that has most of the aromatic compounds with the lowest possible alcohol content. The team conducted taste and smell tests to determine what combination of aromatics and alcohol content is most popular among consumers.
Team 24089
PROJECT GOAL
Design processes to improve operational efficiencies and minimize waste produced by the pilot plant brewery located in the Forbes building and the microbrewery housed in the Student Union Memorial Center.
The brewing process produces many waste products. These include spent yeast, spent grain, carbon dioxide, and the water used for cooling. The team’s objective was to transform the spent grains and yeast into economically viable co-products, design and build a carbon dioxide capture and purification system for the carbon dioxide produced during the fermentation process, and construct a closed loop system for the cooling water using Forbes’ cooled water system.
By employing these processes, the team will help the nutritional sciences department align the brewing process more closely to the sustainability goals of the university and generate profit from waste products.
TEAM MEMBERS
Koseku Buzugbe, Chemical Engineering
Simon Nathanael Field, Chemical Engineering
Nik Gruber, Chemical Engineering
Lucas Pelger, Chemical Engineering
COLLEGE MENTOR
Adrianna Brush
SPONSOR ADVISOR
Gregory Ogden
Team 24090
PROJECT GOAL
Design and optimize an electrocatalytic process to sustainably convert carbon dioxide emissions from vodka production into ethylene.
The alcoholic beverage industry produces about 1.5 gross tonnage of carbon dioxide annually. This accounts for 4% of annual global carbon dioxide emissions. Vodka production plants produce carbon dioxide during the fermentation process and many of these plants simply purify the carbon dioxide in scrubbers before releasing it into the atmosphere. The team instead proposed an innovative and sustainable solution for these carbon dioxide emissions: introducing an electrocatalytic process designed to convert carbon dioxide emissions into ethylene, a valuable feedstock in the plastics industry.
The process begins by humidifying the scrubbed carbon dioxide before feeding it into a membrane electrode assembly electrolyzer. The electrolyzer uses electrocatalytic reactions to selectively reduce carbon dioxide into ethylene. This generates gas and liquid byproducts including ethanol, propanol, formic acid, hydrogen and carbon monoxide. These gases and liquids are then separated using a two-phase separator. Finally, two cryogenic distillation units in series purify the ethylene. While electrocatalytic reactions for carbon dioxide reduction are typically conducted on a laboratory scale, this innovative process offers an opportunity for vodka distilleries to significantly reduce their carbon dioxide emissions and expand the market of green ethylene.
TEAM MEMBERS
Laura Katherine Dunham, Chemical Engineering
Sophie Elizabeth Fuller, Chemical Engineering
Alexia Monae Penn, Chemical Engineering
Nick Katsuji Swenson, Chemical Engineering
COLLEGE MENTOR
Adrianna Brush
SPONSOR ADVISOR
Adrianna Brush
TEAM MEMBERS
Khoa Son Hoang, Chemical Engineering
Hannah Tran Ly, Chemical Engineering
Adrian S Martinez, Chemical Engineering
Peyton Nicole Mikula Meyer, Chemical Engineering
COLLEGE MENTOR
Adrianna Brush
SPONSOR ADVISOR
Caitlin Schnitzer
TEAM MEMBERS
Alex Allred, Chemical Engineering
Dylan William Clevenger, Chemical Engineering
Madison R Hoff, Chemical Engineering
Jordan Thomas, Chemical Engineering
COLLEGE MENTOR
Adrianna Brush
SPONSOR ADVISOR
Eric Loewen
Team 24091
PROJECT GOAL
Develop synthetic ivory using resin and calcium minerals that closely resemble the material characteristics of real ivory in an effort to reduce the global poaching of elephants and other animals.
Ivory is a hard, off-white material composed of dentin and made from the tusks of elephants and other animals such as walruses and warthogs. Around 100 of these animals are killed each day for their ivory. It is desired due to its beauty and rarity, and many people seek to possess it as a status symbol.
In an attempt to combat this practice, the team developed a synthetic ivory to provide a humane alternative. The main objective of this project is to explore different types of resins and calcium minerals and experimentally determine which components resemble the characteristics of real ivory such as hardness, density, tensile strength and color.
The secondary objective of this project is to design an upscaled batch process method to fabricate synthetic ivory and capture 2% of the current market. Possible applications include piano keys, chess sets, jewelry and a variety of decorative purposes.
PROJECT GOAL
Manage fissile material and byproducts by designing a single-reactor system to make uranium powder for fuel pellets and safety systems.
President Biden’s Executive Order 14057 directs the United States to use 100% carbon pollution-free electricity by 2035 and achieve net-zero emissions by 2050. To meet these goals, current nuclear energy production will need to double by 2050.
The Uranium Project studied chemistry to create a method for converting as much uranium hexafluoride (UF6) to uranium dioxide (UO2) as possible. The resulting UO2 powder will be used in nuclear fuel pellets. The process will also produce HF gaseous byproduct which will be safely collected and stored for resale.
The design was based on an existing patent using “flame” reactors. The technical challenge was to reduce the existing patented three-reactor system used for this process into a single reactor which can extract the desired solid product from a gas phase reaction. The process also had to conform to U.S. Department of Energy fuel purity requirements and recycle or safely store the byproducts. The team accomplished this in a mathematical model of the equilibrium that will “push” the reaction to the desired product.
Team 24093
PROJECT GOAL
Design and build a treatment process that uses solar light to maximize the removal of harmful TOrCs from wastewater effluent.
Wastewater treatment is an impressive process that can make contaminated water safe enough to drink or return to the waterways. Unfortunately, it is not perfect. Currently, treated wastewater effluent often contains low concentrations of many TOrCs. These chemical byproducts commonly come from disposed pharmaceuticals and can be dangerous. For example, some of these TOrCs display estrogenic activity, which research suggests is harmful to both human and aquatic health. Fortunately, TOrCs undergo direct and indirect photolysis and attenuate into less harmful byproducts when exposed to the UV radiation in sunlight.
The team created a lab-scale apparatus to recreate this process. The device contains a basin to expose wastewater to solar light and a UV disinfection reactor which runs when solar light is unavailable. The team took samples of the treated water to provide experimental data on TOrC degradation rates. A comparison between these data and predicted reaction kinetics yields information on the viability of the system for a scaled-up process. The final product is a functional lab apparatus and a data-driven costbenefit analysis that informs decision-making for future independent projects’ needs.
TEAM MEMBERS
Molly Katherine Cragin, Chemical Engineering
Hannah Sue McCollum, Chemical Engineering
Ellie Jean Mouer, Chemical Engineering
Avery Zai Zai Royer, Chemical Engineering
COLLEGE MENTOR
Adrianna Brush
SPONSOR ADVISOR
Avelino E Saez
Team 24094
PROJECT GOAL
Determine a way to make mealworms go through their lifecycle as efficiently as possible in order to produce a stable source of mealworms to produce fishmeal.
Tilapia farming has the potential to be an important source of profitable and sustainable protein for feeding the population. However, farmed tilapia are often fed corn or soybean meal. This is not the most sustainable method and can leave a lot to be desired in terms of fish quality.
The team sought to develop a sustainable method for producing mealworms as an eco-friendly fish feed source tailored to the tilapia’s dietary needs. The project’s objectives include identifying the optimal mealworm type and growth method, establishing a production process, and designing systems to make this process work for both small-scale farmers and larger producers. The team attempted to maximize production of the mealworms while minimizing their cost. Additionally, the ideal product will minimize the time required to go from mealworm to fishmeal. The resulting mealworm-based fishmeal will come in a variety of blends ranging from a 15% mealworm ratio to a 30% mealworm ratio. The end goal of this project is to capture around 15% of a specific state’s tilapia farming market with this mealworm-based fishmeal.
TEAM MEMBERS
Yousuf Al Balushi, Chemical Engineering
Abdulrahman Asaad Alakeel, Chemical Engineering
Bader AlShatti, Chemical Engineering
Omar Buresli, Chemical Engineering
Yaqoub Yousef Haidar, Chemical Engineering
COLLEGE MENTOR
Adrianna Brush
SPONSOR ADVISOR
Kimberly L Ogden
TEAM MEMBERS
Ebrahim A Abdulmalek, Chemical Engineering
Abdulwahab Khaled Altammar, Chemical Engineering
Connor Patrick McFarlane, Chemical Engineering
COLLEGE MENTOR
Adrianna Brush
SPONSOR ADVISOR
Fred Brinker
ANDREW LEFCOURT, student team leader for Nobel’s Rotating Detonation Engine Rocket Design and Launch “
Team 24095
Design a process that can recover more than 65% of the helium from natural gas and recover methane with a heating value of 950 British thermal units/standard cubic feet while maintaining a high percentage of purity and recovery for all products, including natural gas liquids (NGLs).
The team designed a process for recovering helium from natural gas that has two main units: an NGL extraction unit and a helium recovery unit. In the process, a de-ethanizer column recovers the NGL and uses the Union Carbide double-column cycle technology to recover crude helium and reject excess nitrogen.
The team optimized energy usage by adjusting the double-column operating pressures. The success of this project is based on the ability of the system to use the NGL product as a refrigerant in a refrigeration loop. This loop uses the strong refrigerant properties of hydrocarbons, such as propane, to transfer heat within the process.
The thought of being a part of something so revolutionary got me excited.”
Dear students,
Thank you to everyone who has participated in this wonderful event, the Craig M. Berge Design Day which bears our family name. My family and I are delighted to see and learn about your design projects. They are truly outstanding.
Much of my husband’s life and engineering career was all about designing. As a student, he built and designed his dragster. Later in life, as a mechanical engineer, he worked for a company that paid for his education. The company loaned him to the U.S. Navy to design the starter for a jet airplane named the Intruder. That plane is on aircraft carriers to this day. Knowing that the Navy is still using something he created is truly remarkable.
My husband would expect remarkable things from each of you, too. He would be so proud of your creativity and all you have accomplished.
In my husband’s memory, I am honored to support the Craig M. Berge Engineering Design Program and these student experiences that move you toward the next chapters in your lives and careers.
All the Best,
SYSTEM REQUIREMENTS
4 weeks
PRELIMINARY DESIGN
4 weeks
After students are assigned to projects, teams work with their sponsors to generate structured lists of system requirements and metrics for evaluating nal designs and prototypes.
Following approval of the Systems Requirements Memo, teams conduct research and brainstorm to produce preliminary or conceptual designs.
DETAILED DESIGN
6 weeks
WINTER BREAK
Based on feedback from sponsors and mentors at the Preliminary Design Review, teams modify their preliminary designs and create detailed manufacturable designs to create prototypes for Craig M. Berge Engineering Design Day.
SYSTEM REQUIREMENTS MEMO
In this structured document, against which all designs, tests and prototypes are gauged, students de ne requirements for completed projects in consultation with sponsors.
PRELIMINARY DESIGN REVIEW
In this formal review, sponsors and mentors critique conceptual designs –for which sponsor approval is required – challenge assumptions and help teams re ne their plans.
DESIGN CHANGES/ BEGIN BUILD
7 weeks
FINALIZE BUILD/ ACCEPTANCE TESTING
9 weeks
Following the Critical Design Review and approval of the Critical Design Report, teams begin purchasing parts and manufacturing custom components to produce their prototypes.
CRITICAL DESIGN REVIEW
At this milestone, sponsors and mentors ensure their teams are meeting all requirements and have feasible plans to manufacture and test prototypes within budget.
During the last phase of the program, teams collaborate closely with sponsors to assemble and test their prototypes. They also prepare their presentations and demonstrations for Craig M. Berge Design Day.
CRAIG M. BERGE DESIGN DAY
FINAL DESIGN PRESENTATION
In this formal exchange, sponsors and mentors provide project feedback as teams address any last-minute changes.
AEROSPACE ENGINEERING
ARCHITECTURAL ENGINEERING
BIOMEDICAL ENGINEERING
BIOSYSTEMS ENGINEERING
CHEMICAL ENGINEERING
CIVIL ENGINEERING
COMPUTER SCIENCE & ENGINEERING
ELECTRICAL & COMPUTER ENGINEERING
ENGINEERING MANAGEMENT
ENVIRONMENTAL ENGINEERING
INDUSTRIAL ENGINEERING
MATERIALS SCIENCE & ENGINEERING
MECHANICAL ENGINEERING
MINING ENGINEERING
OPTICAL SCIENCES & ENGINEERING
SOFTWARE ENGINEERING
SYSTEMS ENGINEERING
Capstone projects are the culmination of a year’s worth of work. Students have applied knowledge from the breadth of their undergraduate education, exercised out-of-the-box thinking and spent hundreds of hours producing the best solutions for their sponsors. We applaud your dedication and professionalism and congratulate you on your achievements.
Project mentors apply hundreds of years of collective engineering experience to guide students in the completion of their projects. They ensure the implementation of industry standards in the design process. Their expertise in devising solutions to challenging problems adds a critical dimension to students’ engineering knowledge. Thank you for your hard work, your commitment to excellence in engineering design and your role in the education of our students.
Sponsors provide students with real-world questions and allocate funds to the program. They designate technical staff and mentors to steer students through the intricacies and requirements of their projects. Sponsors are a big part of what makes the Craig M. Berge Engineering Design Program (which encompasses Interdisciplinary Capstone and other capstone courses) what it is today: one of the largest and best-quality programs of its kind in the nation. Thank you immensely for your continued support.
The external judges who participate in Craig M. Berge Design Day supply independent professional assessments of the quality of students’ work. They help maintain the accreditation of undergraduate University of Arizona Engineering degree programs by providing insight and suggestions for improving the Engineering Design Program. Thank you for volunteering your time and applying your knowledge to evaluate students’ capstone projects.
Dedicated professionals in the College of Engineering ensure the program’s smooth operation. They spend thousands of hours each year organizing events, communicating with sponsors, operating manufacturing areas, generating marketing materials and news, maintaining budgets and purchasing records, and performing a myriad of other tasks. Thank you all for your invaluable contributions and the excellence you bring to the program.
Ageless Lifestyle Home
Amazon
Ana Needham
Arizona Water Association (AZWA)
ASML US, Inc.
Auxilium Technology Group
AZ Technica
BAE Systems
Bard Water District
BD (Becton Dickinson)
Capstone Mining Corporation
Caterpillar Inc.
Chicago Cubs
Coherent
Dataforth Corporation
Dragoon Technology
Elbit Systems of America
FLSmidth Krebs
Fort Huachuca
Frank Broyles
Freeport McMoRan
General Dynamics Mission Systems
Henry & Suzanne Morgen
Honeywell Aerospace
IEEE
Kenneth Bingham
Kidney ADVANCE Project - NIH
L3Harris Commercial Aviation Solutions
Larry Head
Lawrence Livermore National Laboratory
Lightsense
Mark Brazier
McDonald/Watt Projects
Mensch Foundation
Microentities Worldwide
NASA
Neurovascular Research and Design
NexoTerra
Nobel
Northrop Grumman
Parker Meggitt
PeakView Solutions
Phoenix Analysis & Design Technologies
R3 Aerospace
Raytheon Technologies
RBC Sargent Aerospace & Defense
Resolution Copper
Rightfooted Foundation, supported by the
Craig M Berge Dean’s Community Fund
Rincon Research
Roche Tissue Diagnostics
San Xavier Mining Laboratory
Sharon ONeal
Simpson Family
Steve Larimore
SynCardia Systems
Technical Documentation Consultants of Arizona
The Bly Family
Tucson Electric Power
W.L. Gore And Associates
Arizona Center for Accelerated Biomedical Innovation (ACABI)
Craig M. Berge Dean David Hahn
UA College of Medicine
UA Department of Aerospace & Mechanical Engineering
UA Department of Biomedical Engineering
UA Department of Biosystems Engineering
UA Department of Chemical & Environmental Engineering
UA Department of Mining & Geological Engineering
UA Police Department/FBI, supported by the Craig M Berge Dean’s Community Fund
UA School of Mining & Mineral Resources
Adrianna Brush
Pat Caldwell
Matt Christensen
Steve Larimore
Michael Madjerec
Doug May
Don McDonald
Sardar R Mostofa
Mike Nofziger
Kimberly L Ogden
Samuel Peffers
Sergey Shkarayev
James Sweetman
Jekan Thangavelauthum
Edward Clifton Wellman
Jeff Wolske
Larry Head, Craig M Berge Engineering Design Program Director
Debbie Claggett, Engineering Design Capstone Coordinator
Cecilia Lopez, Business Manager
Ashley Barrientos, Purchasing Office
Alondra Gonzalez, Purchasing Office
Nataly Islas, Purchasing Office
Monica Palafox, Purchasing Office
Matthew Briggs, Design Faculty
Urs Utzinger, Design Faculty
Alexa Armstrong, Engineering Design Center
Miguel Barrera, Engineering Design Center
Cienna Charron, Engineering Design Center
Seven Gilbert, Engineering Design Center
Andrew McGill, Engineering Design Center
Angel Perez, Engineering Design Center
Samantha Perry, Engineering Design Center
Carolina Ferreira Silva, Engineering Design Center
Sierra Speranza, Engineering Design Center
Chuy Talavera, Engineering Design Center
Elias Thomas, Engineering Design Center
Gabe Vogt, Engineering Design Center
Megan Wildridge, Engineering Design Center
It’s great to see all the hard work and creativity the students are putting in. Their excitement and enthusiasm remind me of why I love engineering so much, and it inspires me in my job.”
MATT METTE, alum and Roche SPONSOR ADVISOR “
From startups to Fortune 500 companies, a varied group of sponsors benefits from this outstanding interdisciplinary academic program each year.
Try out potential employees
Explore new technologies
Move products to market
Support engineering education
Boost company profile on campus
Teams of four to six seniors, mentored by industry liaisons and University of Arizona Engineering faculty, spend an entire academic year taking your design projects – many of which become patented technologies and commercial projects – from start to finish.
View the 2024 Design Day project presentations at b.link/DesignDay2024
ICAP.ENGINEERING.ARIZONA.EDU