Breeder Benchmarking Survey
Each year, Aviagen® Turkeys gathers results of performance from customer’s parent stock flocks to conduct an annual breeder depletion analysis. Over the past few months, customers contributing information to the survey have been provided with a detailed anonymous comparison of how the lifetime performance of their parent stock flocks compare to others. This provides an insight into breed potential and identifies opportunities for further management improvement.
Aviagen Turkeys also uses this information to produce accurate and realistic performance objectives, tailor support to help customers achieve the genetic potential and align the breeding programme goals to industry requirements.
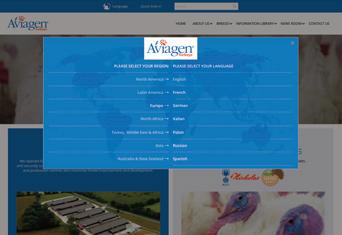
Summary results for the flocks depleting in Europe during 2021 are shown below. These results are presented as cumulative settable eggs to 24 weeks and include flocks from the majority of our customers. Average results include all results, even those that had problems, whilst the top quartile results are the 25% best performing flocks and demonstrates true breed potential.
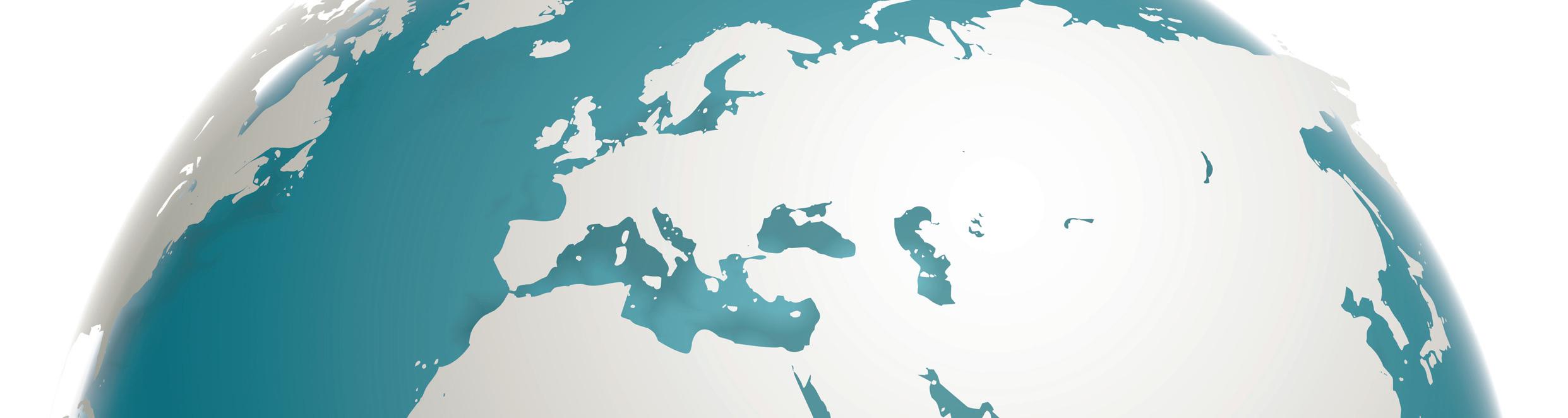
2021 was characterised by yet another performance improvement across a number of companies and average egg numbers were up by +1.1 eggs for the B.U.T. 6 and +2.4 eggs for the B.U.T. Premium compared to the 2020 results. Much of the improvement was at peak and immediate post-peak of production.
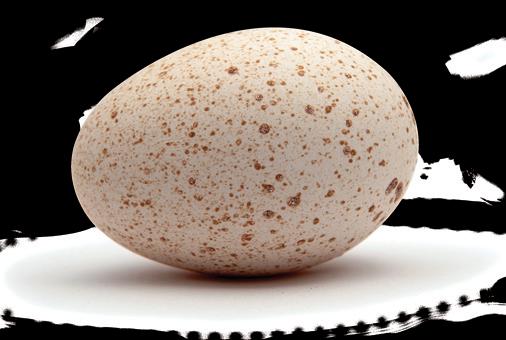
Improvements in performance can be attributed to a combination of factors: Genetic improvement arising from the breeding work on robustness and liveability; Improvements in management practices which have been tailored for the B.U.T. Premium and B.U.T. 6 and refined over many cycles; investments in breeder facilities to allow better expression of genetic potential; targeted technical support for customers with poorer performance. Climatic factors also cause some year to year variation. These results are more impressive considering the growing trend towards the use of automatic nests which reduces egg numbers slightly compared to manual nests. Updated performance objectives based on achieved top quartile field performance will be available shortly for the B.U.T. 6 and B.U.T. Premium.
are
to introduce
website, which you’ll

Industry-wide
B.U.T.
of B.U.T.
production
25% performance
performance objectives.
hen
the
to our
nd full of
news and industry-related
A Day in the Life of Luke Ramsay
ATL Management Specialist
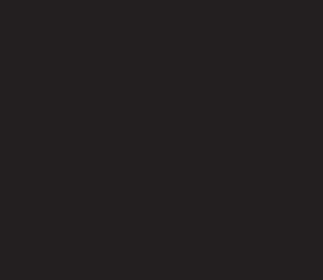

Luke joined Aviagen® Turkeys Ltd on 1st January 2019 as a Trainee Management Specialist. Throughout his first year with the company, he ran our commercial trials farm managing day-to-day tasks, carrying out weighing & assessments of the birds and was promoted to management specialist. He continues to give the site support on technical advice and help on weighing days and when the site needs setting up.

My role at ATL as a “Management Specialist”, involves working with customers across Europe to advise them on how to achieve the maximum performance from our birds focusing on day-to-day management. My intention is to create a solid understanding of our customers businesses to ensure that we can give the most suitable advice and get the best out of different production systems including training to help develop the local work forces. Below is how a typical day looks for me visiting a customer within Europe.
A typical day when visiting a customer
2.00 am – Alarm goes off after a shorter than preferred sleep. A quick coffee tops me up for the first few hours of the day, which will be spent in a busy airport. After getting all the luggage in the car, we are ready to set off to the airport.
4.00 am After an hour’s drive to Manchester airport, I make my way through check-in and security (which can be the most stressful part of the trip in recent times!), if I’m lucky and get through in good time I will be able to get a coffee and some breakfast at one of the cafes.
6.00 am Departure! I try to get on the earliest possible to flight to my destination which is normally around the 6am mark. This means I get almost a full day with the customers and maximise any time on farm.
8.30 am – After an hour and a half’s flight (8.30am destination time, 1 hour ahead of the UK), I have arrived and made my way out and to the car hire. Once familiarising myself with the cars controls and prepping to drive on the wrong side of the road… I set off towards the customer’s farm.
10.30 am – Seven and a half hours into my day and I’ve arrived at my first farm. We normally visit either one or two farms per day depending on the customer so bio-security is at the forefront of everything we do. On this occasion, we are visiting a breederrearing farm in the morning and a laying farm in the afternoon. Once we have showered into the farm, we commence into the houses where we find first week old poults just been let out of the rings. Overall the birds seem happy and everything else in order just a tweak of the ventilation settings to lower the CO2 levels and we are good to go.
12.30 pm – Dinner time! Thanks to Google translate, reading the menu is no longer a problem when travelling so you can order with confidence. I normally go for a soup or broth to start with, strawberry soup being a particular favourite so far! Followed by a salad with some kind of meat. That’s me fuelled up for a busy afternoon.
1.30 pm – We are visiting a laying farm in the peak of their production, luckily this farm inseminates in the afternoon after the peak of eggs has been laid which, allows me to see all the processes the farm are using. I normally start with looking that the milkers and then following the same semen through the cycle to the inseminating of the females, giving a hand or showing different techniques to the staff. This allows me to get up close to the birds and understand how they are feeling and producing. The final thing to check is the egg collections and whether the flock has any floor layers. If they do, tell the staff how to deal with this and reduce it as much as possible.
4.00 pm – Before leaving for the hotel we will have a meeting with the farm manager and senior management team to discuss what we found during our visit and discuss any questions they may have.
5.00 pm – Farm visits have finished for the day so now we make our way to the hotel for the night. After check-in and a very quick bag drop off, we meet our customers in the reception area and head for dinner where we will talk turkeys for the rest of the evening.

Behind the scenes of our new adver tising campaign photo shoot

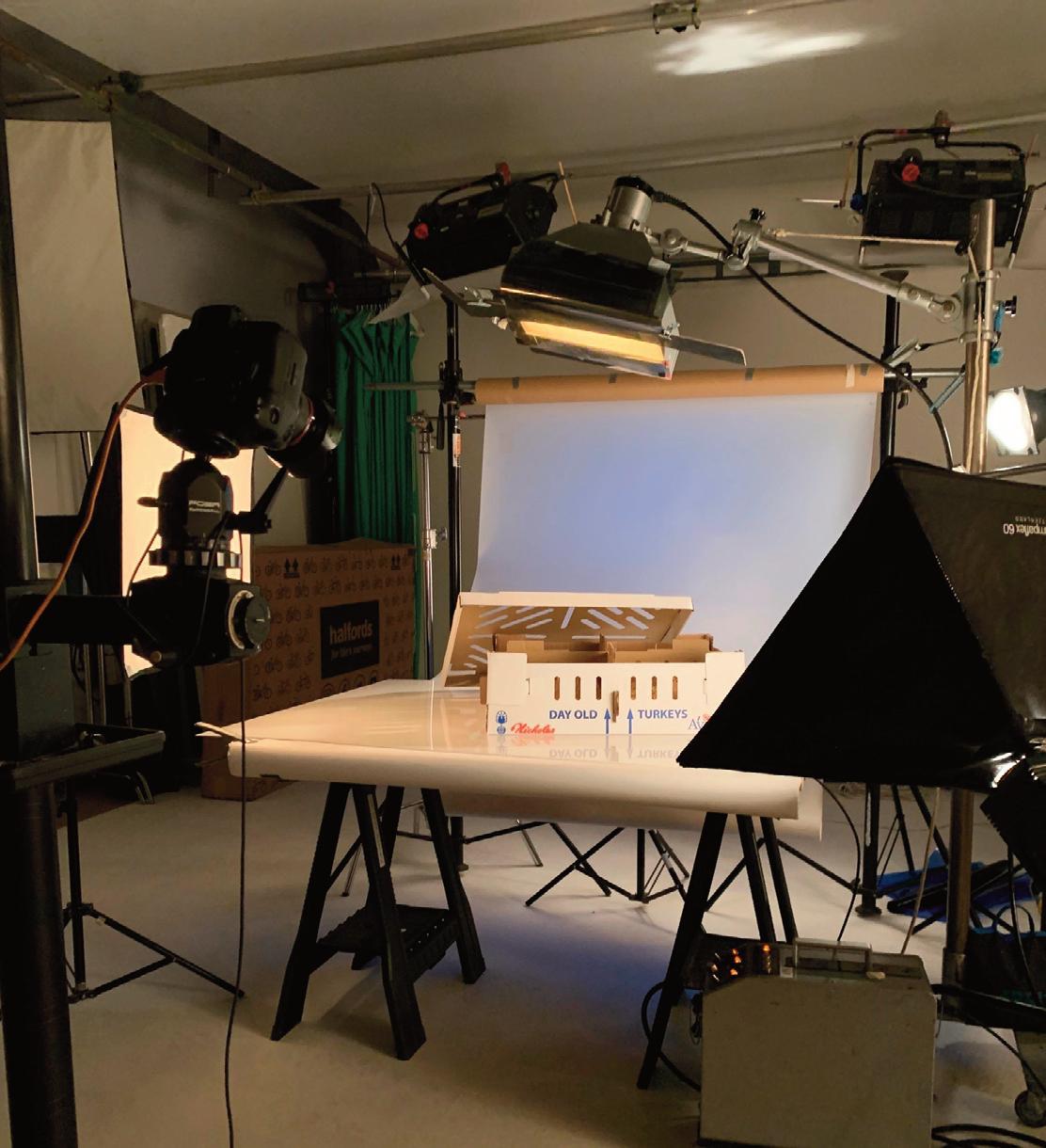
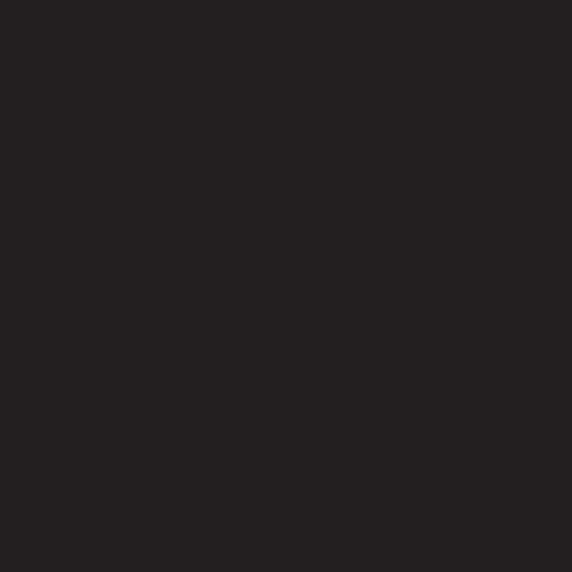
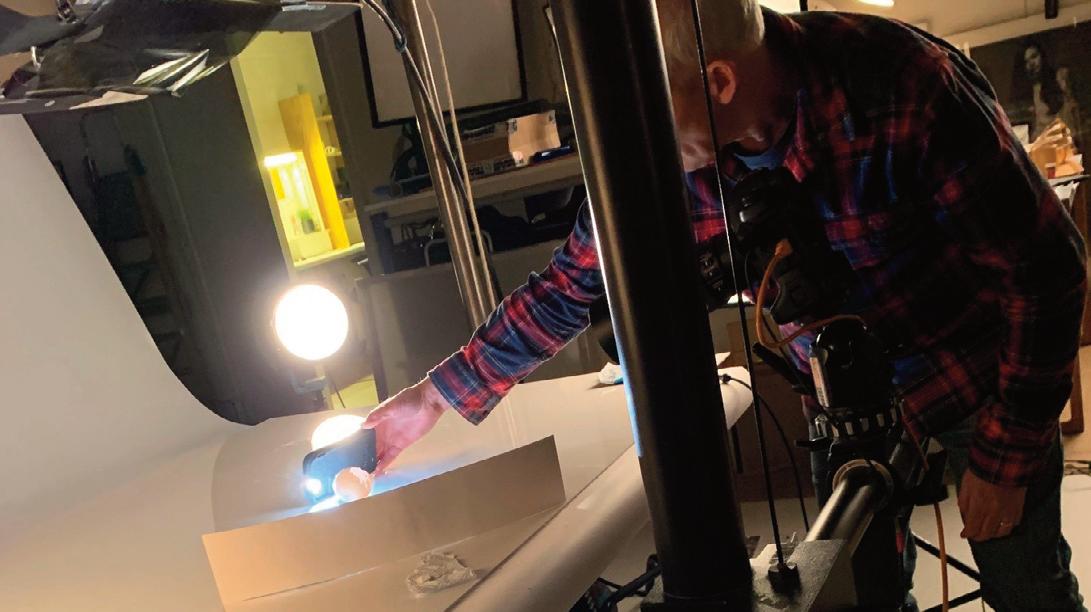
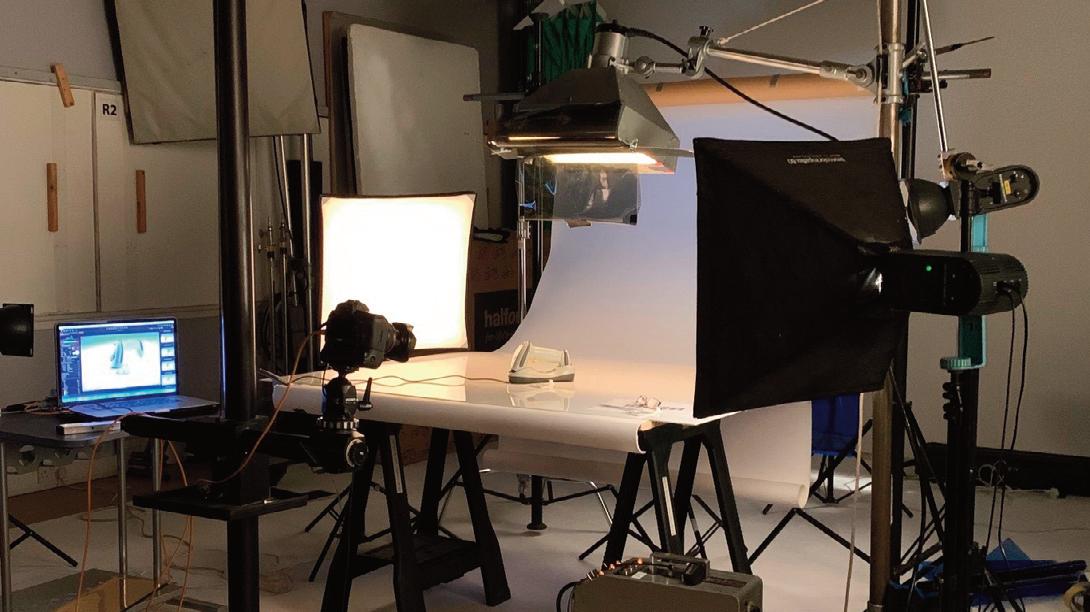
With a car boot full of wellington’s, hard hats, weighing scales and egg boxes it wouldn’t be unreasonable to think that we were heading to one of our farms for the day but today we had other uses for these items, today they were to be props for our photo shoot to create our new advertising campaign.

The day started well, the weighing scales were first to be photographed and they proved to be a bit tricky, the light caught everywhere on them casting shadows where we didn’t want to see shadows. Luckily, our photographer knew exactly how to position the props just right and we pushed on, a feather, a pair of old boots, a poult box and a test tube followed and by the end of the day we had all the images we needed to create our newest advertising campaign. We hope you like it!
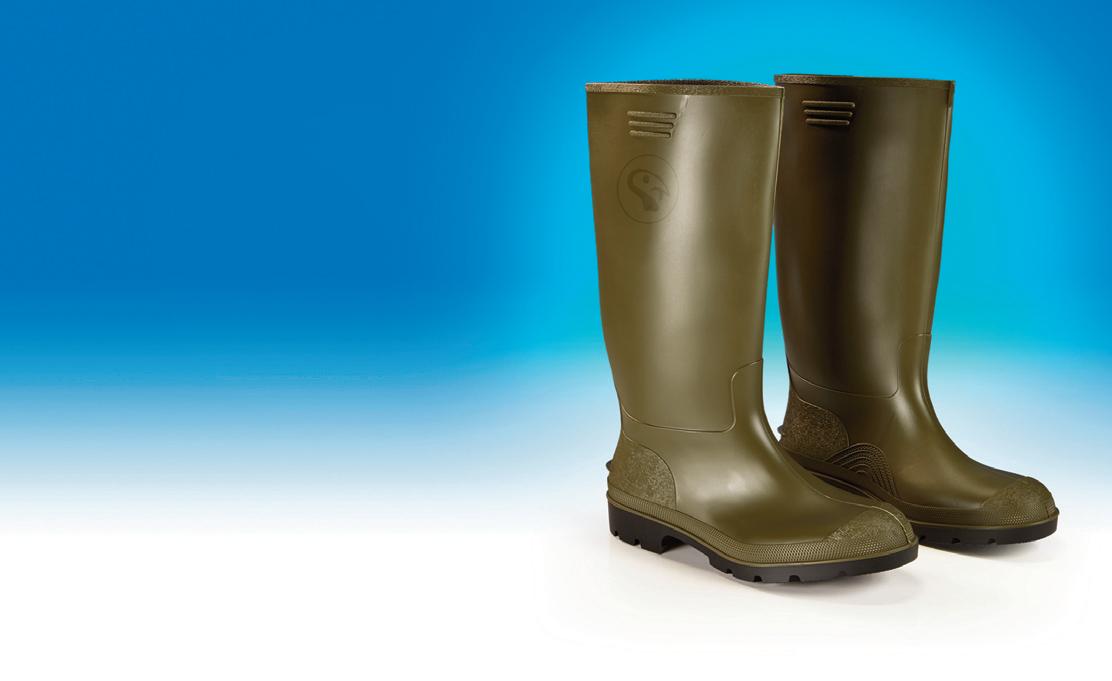
Nutritional Outlook
The turkey industry is going through the most turbulent period of raw material price increases resulting in feed prices being at their highest in the industries history. Cereal prices are reducing as harvest progresses, however wheat stocks are still likely to remain tight as the situation with Ukrainian grain exports still looks uncertain so there is a likelihood that wheat prices will remain firm. Despite US soybean yields and output set for record highs the soya market also appears firm.
In a situation where feed prices are escalating there is a strong case for evaluating the current feeding programme. It is important to remember that any significant reduction in the nutrient specification of the diet has the potential to negatively impact on flock performance and consequently output. Any change in the nutrient specification of the diet therefore needs to be carefully assessed and based on the best available evidence. Aviagen Turkeys Ltd have published information demonstrating the impact of altering the nutrient density of the diet on bird performance, information such as this needs to be referred to when considering such changes, this data can be used by the nutritionist to make informed decisions about the impact of any changes to diet nutrient specification levels.
Constraints are placed on raw materials when least cost formulating as this can have a significant impact on formulation costs. Constraints are placed on ingredients for different reasons, for example there may be a maximum constraint on soya-based materials as these contain anti-nutritional components which may be detrimental for bird health and performance. The inclusion rate of other materials may be restricted due to physical or milling constraints, for example excessive levels of maize may have a detrimental impact on pellet durability. The exact level such constraints are set at are almost always based on a subjective assessment along with an element of insurance or safety factor. Constraints may also be based on convention or whatever constraints have historically been in use. In a rising raw material cost base it is prudent to challenge existing constraints and capture any cost saving opportunities whilst maintaining the nutritional integrity of the diet.
Wheat is valued not just as an energy source but also aids in pellet quality in its ‘pellet binding’ properties, however when wheat prices escalate other cereals may be more cost effective, for example maize or sorghum. Neither of these cereals have the same ‘pellet binding’ effect of wheat however use of pellet binding agents, including a minimum quantity of wheat-based products, while also adapting feed processing techniques can overcome these issues.
The inclusion of alternative proteins to soya is also important to consider not just from an economic standpoint but also from a carbon emissions viewpoint. Although sunflower meal is currently in short supply peas, beans and rapeseed meal are suitable alternatives.
It is worth investigating what other materials are available in the feed mill which may currently be used in other species but not currently offered to turkey diets. Also, the feed mill purchaser may be aware of other materials available on the market which have previously not been considered for turkey diets.
Distillers dried grain and solubles (DDGS) is another protein source which can be cost effective, inclusion rates are limited to no more than 4% to 5% in diets due to the risk of mycotoxin contamination. Maize gluten meal is one of the highest protein
density cereal by products, consideration should be given to the low lysine content so the diet should be balanced accordingly. Maize gluten can be included up 5% to 7% in turkey feeds.
Processed animal proteins (PAPS) are used successfully in diets and now permitted for use in the EU under strict control measures, only feed for species for which the use of poultry PAPs is permitted can be produced on the same site and vice versa for pig PAPs. The number of feed mills that are 100% dedicated to pig feed or poultry feed is extremely low so, based on the current restrictions in use, it is unlikely PAPS will feature in turkey diets to a significant extent in the EU in the future.
A list of ingredients with suggested constraints are shown in the tables opposite.
Other less conventional protein sources such as insect meal and algae derived protein are considered viable alternatives to conventional protein sources however price and availability dictate these materials are used in more niche sectors such as specific aqua feeds and pet foods.
Lastly, additives such as enzymes increase the nutritional value of feed, this is particularly important in the current climate. It is important to liaise with suppliers to ensure their products are utilised to the maximum degree. Any new permitted technologies should be evaluated if demonstrated to be cost effective and safe to use.
Choice of turkey breed
Genetic selection results in strains becoming ever more feed efficient over time. The improvement in feed efficiency (FCR) of a 20kg B.U.T. 6 male birds has improved by 4 to 5 points in the past 3 years. The impact of this improvement in terms of feed usage per bird is significant, a 20kg bird will consume 0.8kg less over its lifetime. Based on current feed prices this reduction in feed intake equates to £0.28 per B.U.T. 6 male bird, all through genetic gain! It pays to consider what genetics are used in order to maximise the efficiency of today’s highly priced feed.
In summary:
1) Be cautious in reducing diet nutrient density with a view to saving feed cost, there may be consequences on flock performance.
2) Interrogate raw material constraints, capture cost saving opportunities while maintaining the nutritional integrity of the diet.
3) Consider alternative cereal sources and maintain feed physical quality.
4) Investigate alternative protein sources and if other materials are available in the mill or on the market.
5) Assess novel ingredients as some are becoming both nutritionally and commercially viable.
6) Optimise the use of feed additives to increase the nutrient contribution from feed materials.
7) Use the most efficient genetics to maximise the conversion of feed to live weight.
Water Quality
and management
Difficulties of Water Management
Poultry houses are ideal environments for growing microorganism: It is a warm environment; has relatively low flow rates of water through the lines at certain times of the production cycle particularly during early rear and at night facilitating sedimentation and colonisation; and provides substrates microbes can thrive on like probiotics, citric acid, vitamins, organic acids, and vaccines. A symbiotic relationship between bacteria, yeasts and moulds leads to the formation of a biofilm. The complexity of water supply systems makes effective cleaning and disinfection (C&D) challenging; and delivery systems can be old and poorly/incorrectly maintained. Furthermore the turkey growing cycle is long with lots of opportunities for waterlines to become contaminated.
Water is an essential nutrient for birds. Providing a clean water supply throughout production promotes bird health, welfare and performance, which is important irrespective of the production system used. Water disinfection during production is an integral part of a good flock management system. Controlling bacterial contamination and biofilm formation in the drinking system is key to reducing bird exposure to harmful organisms and lessening the risk to spread disease.
Hydrogen peroxide products can also be a very effective to sanitize your water system. Stabilised hydrogen peroxide works well on biofilms because it is a very good oxidizer and can break down the biofilm. In addition, it is non-corrosive to the drinker system and quite effective on bacteria, fungi and viruses. It can break down algae thoroughly enough to allow it to pass through nipple drinkers without causing the nipple to clog or stick.
As well as a continuous sanitizing of the water lines all bell-type drinkers must be washed with a disinfection solution at least three times per week. Wash thoroughly the bell and bowl with a brush or scrub pad. Wastewater should be poured into a bucket and removed from the house. Nipple drinkers should have a daily flush, which will keep water fresh and bacterial levels at a low level throughout the flock.
Measuring Water Line Sanitation
Daily Water Line Sanitation
Cleaning the water lines between flocks is only half the battle. Even with a thorough cleaning, if a significant number of bacteria, fungi or yeasts are still present, then the biofilm has the potential to return completely in 2-3 days. Therefore, the last step is to establish a daily water sanitation program. This will benefit both the birds and the water system. The three most common sanitation systems are chlorine dioxide, chlorine with acidification and hydrogen peroxide.
Chlorine dioxide is a strong sanitizer made up of sodium chlorite and inorganic acid. It is an unstable form of chlorine that rapidly breaks down into harmless water and salt. The conversion is achieved by mixing the chlorite solution with citric acid, transforming the chlorite to chlorine dioxide.

Chlorine with acidification is a system that kills organisms in the water using Hypochlorus acid (HOCI) and Hypochlorite ion (OCI). You must use two different medicators with using both chlorine and acidification: one to pump in the acid and then one to pump in the chlorine. You should never mix the products together in the same tank.
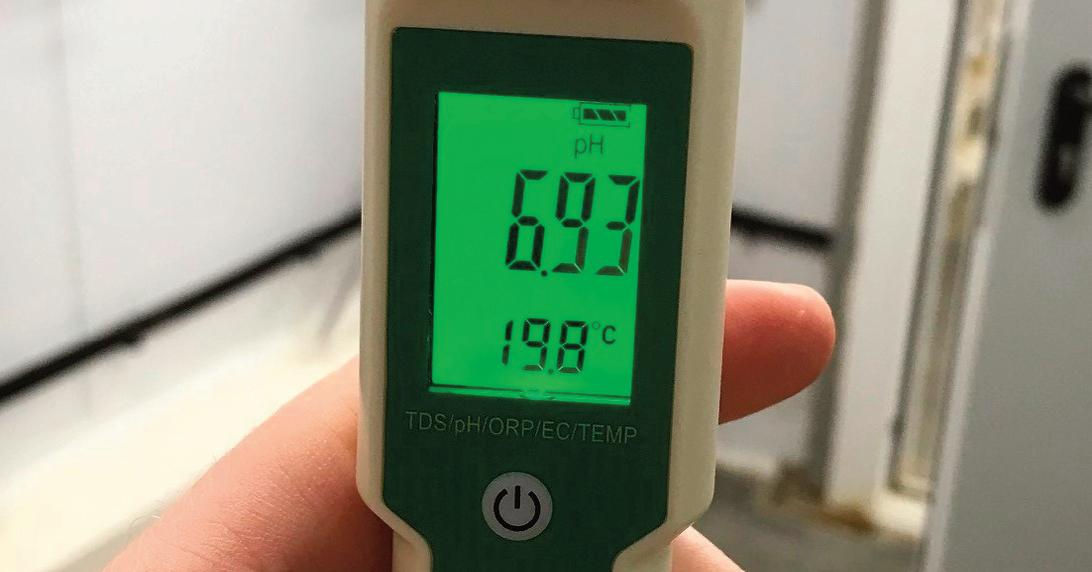
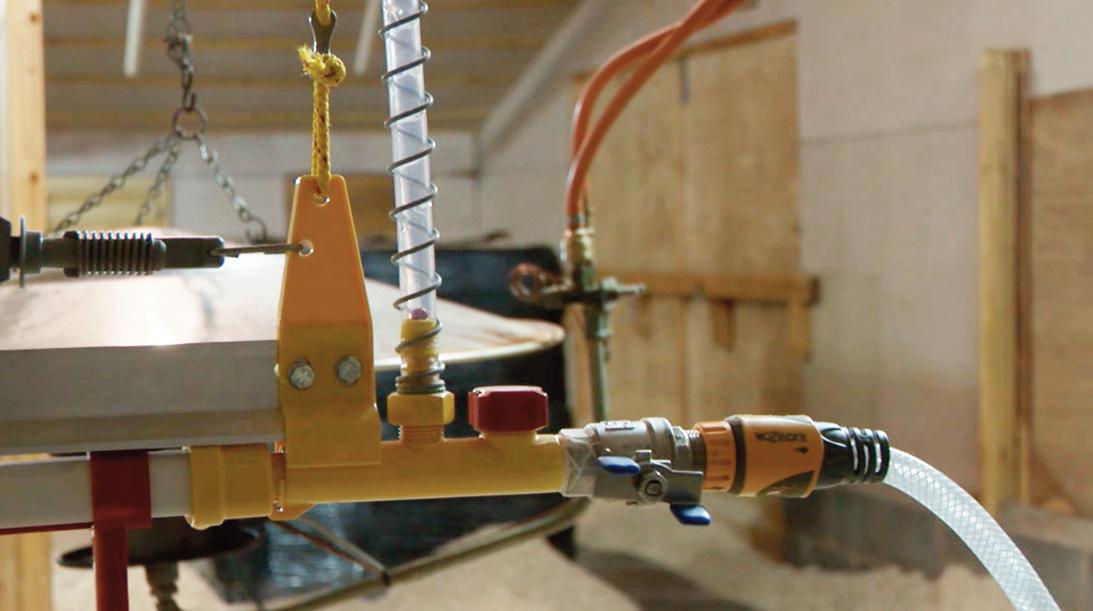
An important piece of information to know how effective the sanitisation program has been is the ORP value of the water; this can be done with a specific ORP reader, which are widely available. ORP stands for oxidation-reduction potential and it is a great way to find out if the water sanitation program is working. A strong oxidiser literally destroys viruses, bacteria and other organic material present leaving water microbiologically safe. An ORP value in the range of 650 and 700 millivolts indicates good quality water. A lower ORP value such as 250 millivolts indicates a heavy organic load that will most likely overwhelm a sanitizer’s ability to properly disinfect the water. The bottom line is utilise information on pH, ORP and chlorine level to determine if the sanitation program is effective and to also prevent equipment damage by the overuse of chemicals.
A couple of important points to note is that no sanitizers or any chemicals should be present in the water system when administering vaccines, medications or vitamins and do not mix different products in the same stock solution.
Step 1 – Choosing a sanitizer
Choose a sanitizing cleaner that can effectively dissolve any biofilm or slime in the system. Some of the best products for this job are concentrated hydrogen peroxide solutions. Prior to using any strong cleaners, make sure standpipes are working properly so air pressure build up in the lines will be released. Consult equipment suppliers before using products to prevent unnecessary damage.
Step 2 – Prepare the sanitizing solution
For the best results, use the products at the strongest concentration recommended on the label. Most medicators/ dosatrons will only allow concentrations between 0.8 and 1.6% of the original material. If you need to use higher concentrations, it is better to mix the stock solution in the large tank and then distribute it without using a medicator or Dosatron. For example, if a 3% solution is required, mix three volumes of the cleaner with 97 volumes of water for the final solution.
An excellent sanitizing solution can be made up by using a 35% hydrogen peroxide solution. Mix this as described for a 3% solution.
Once the water lines are filled with the cleaner, close the tap and leave the product in the lines for as long as the manufacturer recommends (over 24 hours if possible).
Flush cleaner for the water lines after the holding period. Water used to flush the lines should contain the level of sanitizer normally used in the drinking water for the birds. In the absence of a standard water sanitation program, add 113g of 5% bleach per 1 litre of stock solution and proportion this stock solution at the rate of 7.5g per litre of water. This will provide 3 5 ppm of chlorine in the rinse water.
After cleaning, sanitizing and flushing the system, the water supply should be fresh and chlorinated (3 5 ppm is the drinker furthest from the source). If using an ORP meter, the reading should be a minimum of 650.
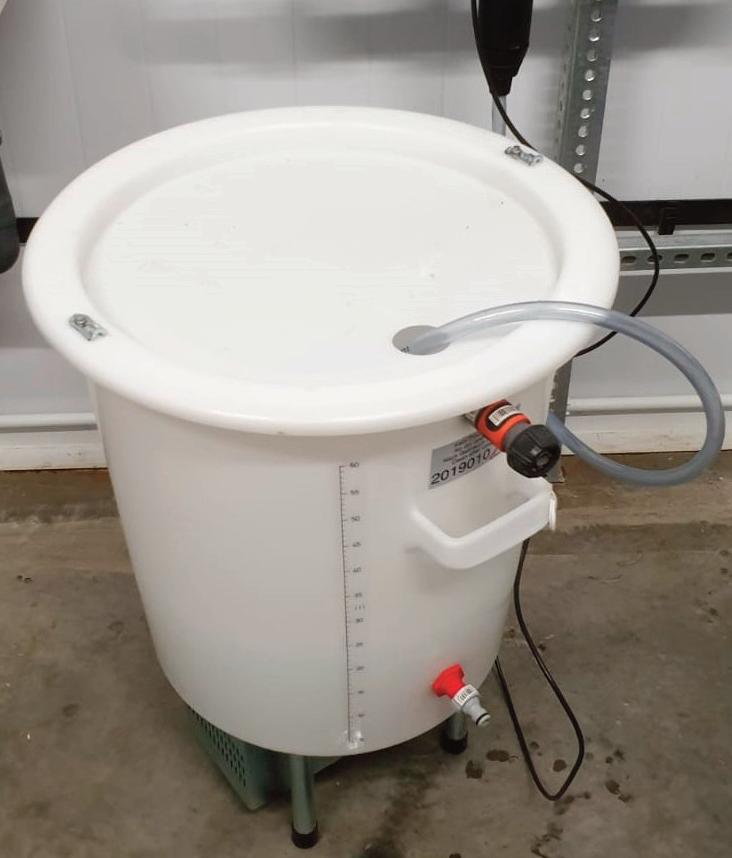
Lines that take water from a water well to the poultry houses should also be cleaned and sanitized between flocks. It is best not to flush these outside water lines through the water lines inside the buildings. Connect a water hose to the medicator tap to drain the outside lines.
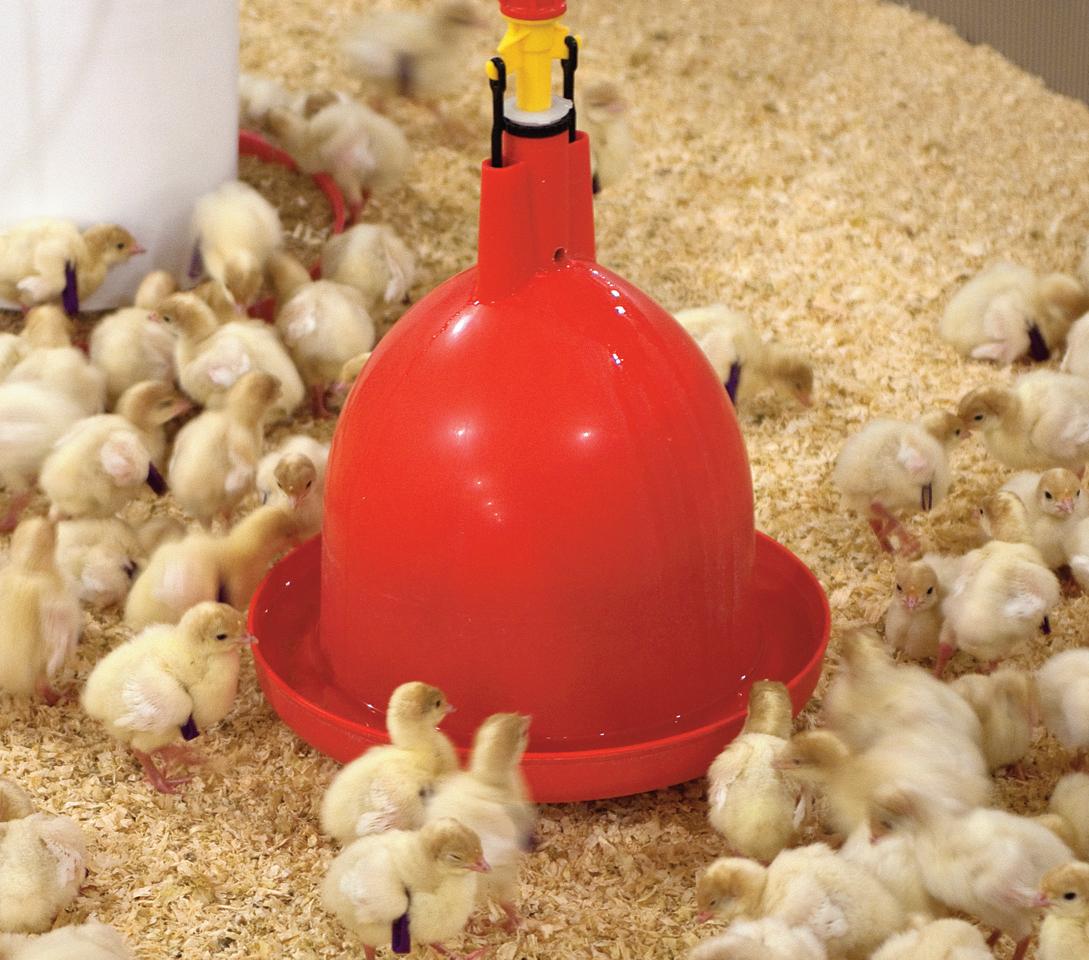
Step 4– Keep the system clean
Once the system has been sanitized, it is important to keep it clean. Develop a good daily water sanitation program for your birds. The ideal water line sanitation program should include injecting both sanitizer and an acid. It is important to note that this procedure requires two medicators or injectors since acids and bleach should never be mixed in the same stock solution.
If only one medicator or injector is available, then inject bleach (concentration of 5%) at a rate of 40g per litre of stock solution. Proportion at 7.5g per litre of drinking water.
The objective is to provide a clean source of drinking water with a continuous level of chlorine at 3 5 ppm at the end of the building furthest from the medicator.
Please note:
Always check dilution rates and follow manufacturers guidelines. Steps 1-3 Down time between flocks. Step 4 During the flock life cycle.
Step 3 – Clean the lines
It takes 30 38 litres of water to fill and clean 30.4m of 1.9cm water line. If the building is 152.4m long and has two water lines, you should make up a minimum of 380 litres of sanitizing solution. Water lines should be designed so that they can be opened to drain completely when the cleaning is done.
Open water lines and drain completely.
Begin pumping the cleaner through the water lines.
Watch the water as it leaves the drain line for signs of the product, such as foaming.
IT’S WHAT YOU DON’T SEE THAT SETS US APART
B.U.T. Premium
A B.U.T. Premium egg is the start of something special. It’s the beginning of a well-bred and developed poult that will deliver top-performing results aimed at enhancing your bottom line. And with high productive performance, exceptional welfare, enhanced liveability and improved FCR, B.U.T. Premium is your best choice for top profits. For more information about our entire range, visit www.aviagenturkeys.com Our top-performing birds deliver direct to your bottom line
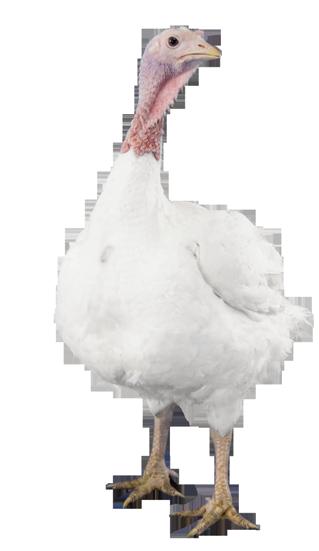
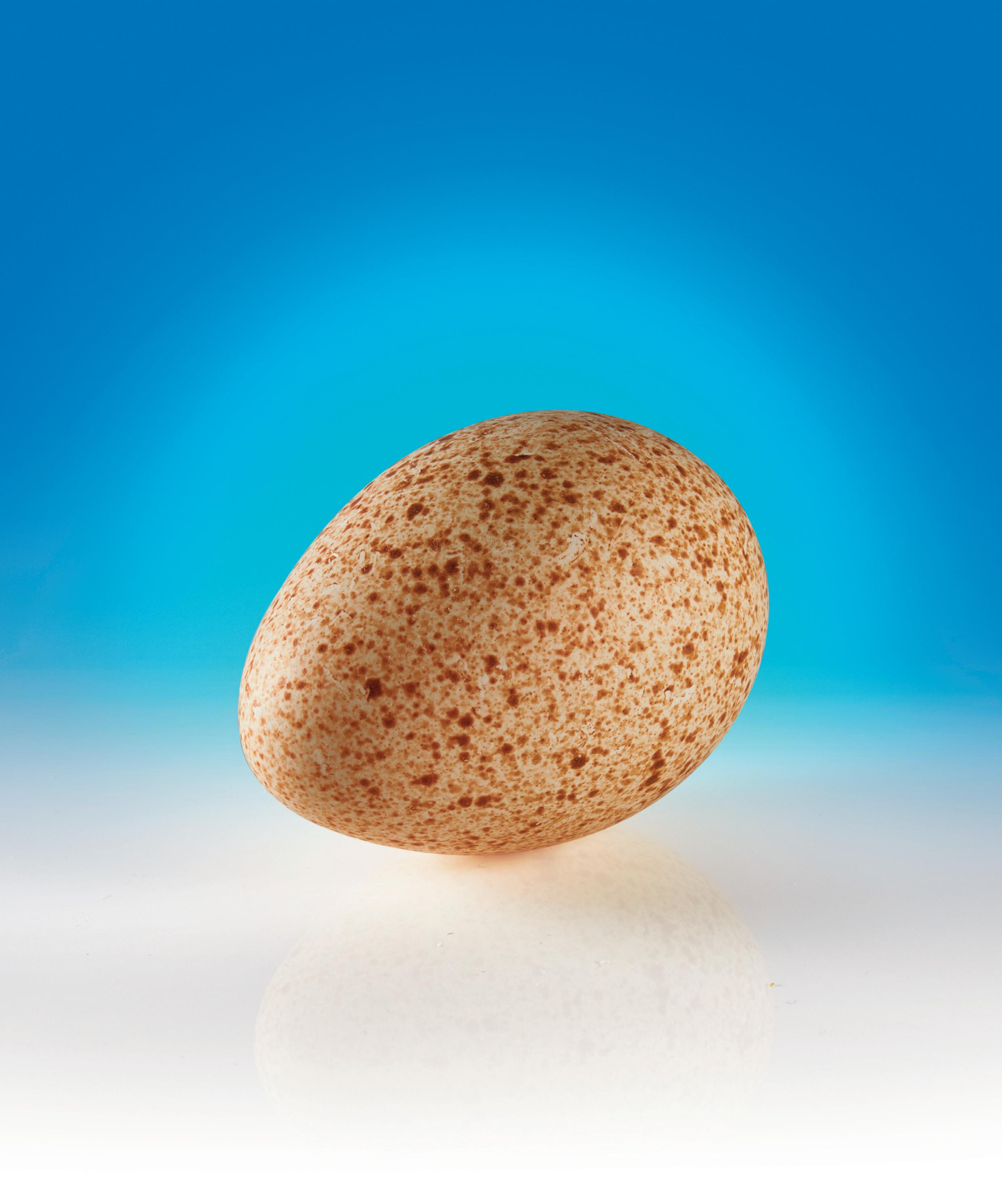