Innovating for the Future
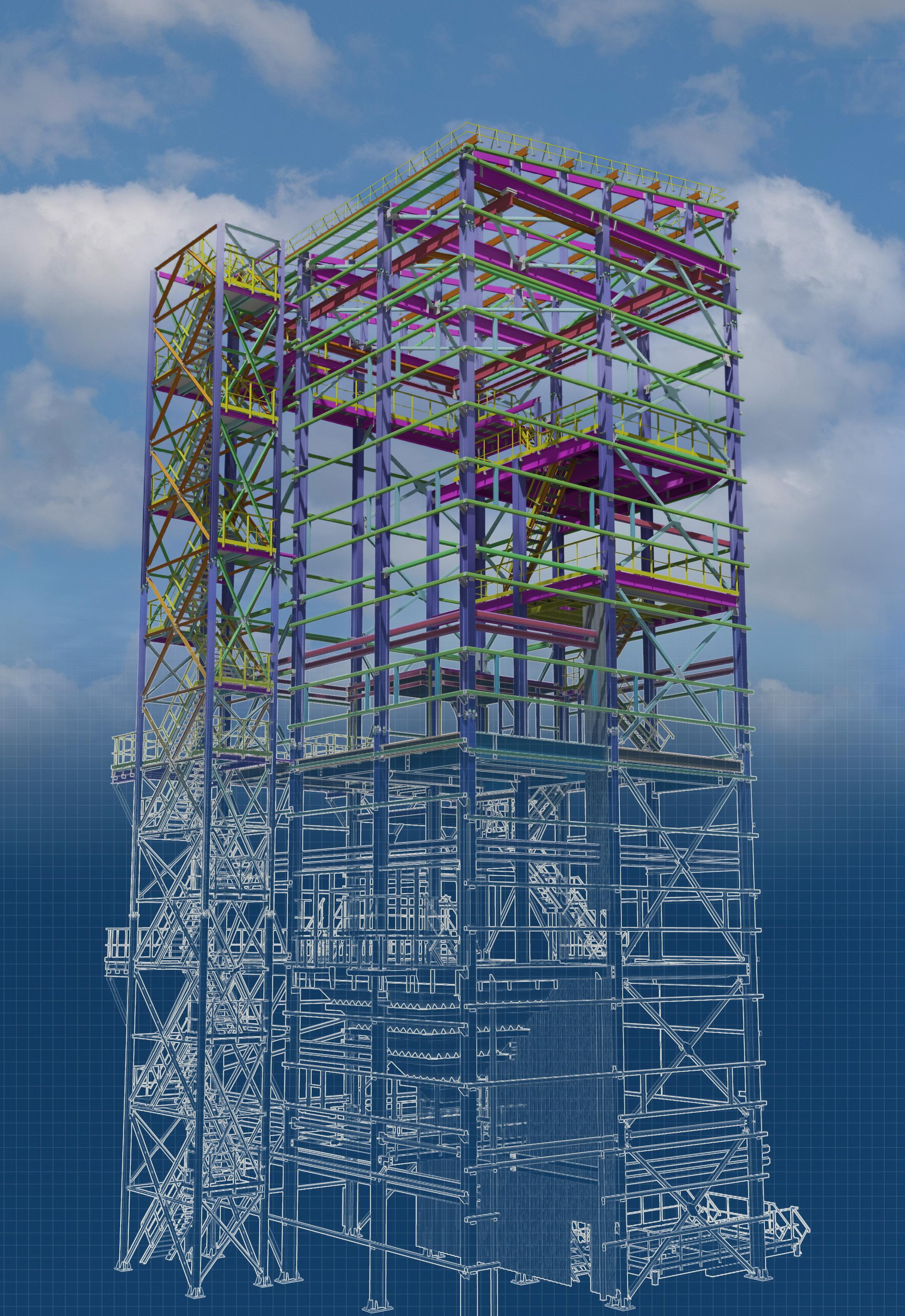

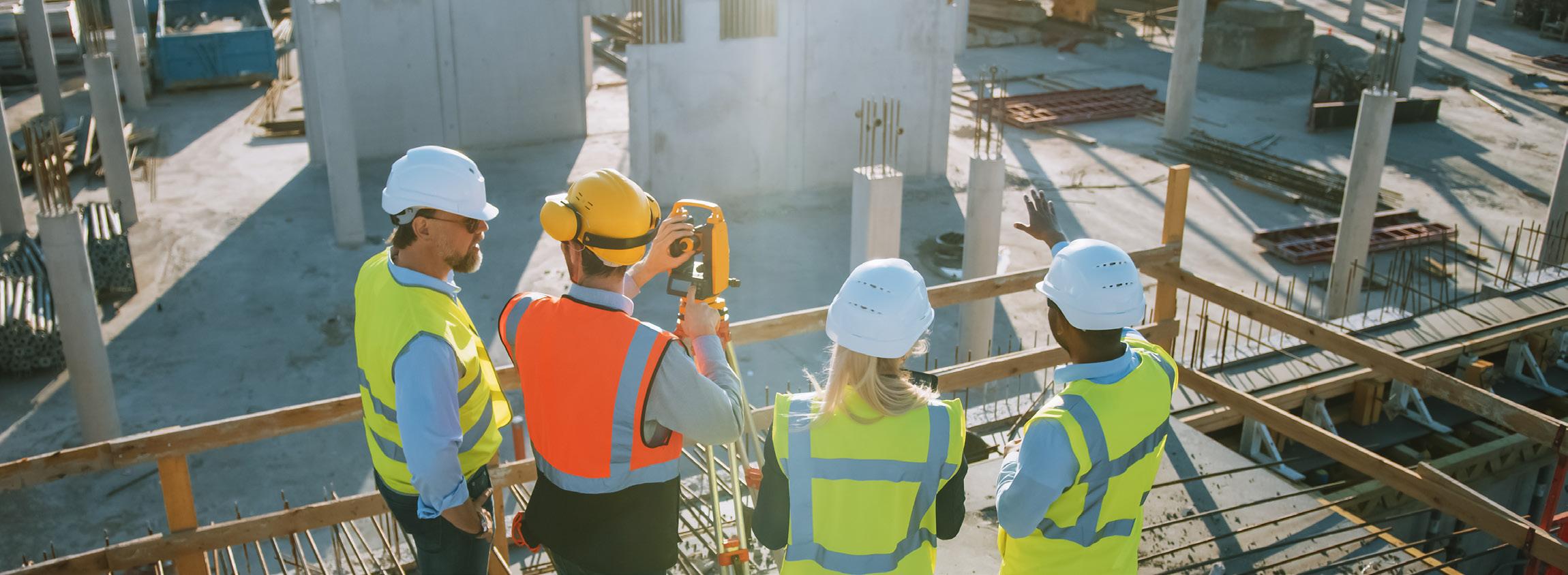
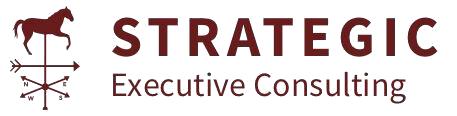
The construction industry has its challenges when it comes to workforce development. When we read projections of how many workers are needed to fulfill the amount of work that’s in the pipeline, one could easily see our industry’s future as dim. But let’s take a ‘glass-half-full’ optimistic look.
Our labor friends are fixtures at high school career fairs, and they have a presence at CTCs/Vo-Techs. As one carpenter representative told me, “There’s something different about high school students right now. They have a vision of where they want to go in life and put the work in to get there. This positive movement has been building the past few years, and I like the direction our young high school leaders are heading.” Obviously, not all high school students see construction as a destination, but the ones who do are excelling in the ACE Mentor Program and the Skills USA Competition that the CTCs host. What we lack in quantity, we make up for, and then some, in quality.
Moving up a level to higher education, the KCA saw firsthand how bright the future is when we launched the KCA Scholarship Program earlier this year. The young adults who applied for it were simply amazing. In our first offering, we ended with 30 applicants from six different institutions. The KCA Scholarship Committee tasked itself with shortlisting the finalists to the top three. However, determining only three was insurmountable since all 30 were impressive, so we selected the top six. As if the applications were not impressive enough, the committee was blown away by the six interviews. We were so amazed that we couldn’t pick just one winner. (The next issue will feature an article on our two winners.)
John Panzitta President, Keystone Contractors AssociationAt the young professional level, each of our job sites are populated with young minds that want to make a difference in the industry and the community. Seeing a void in the network of young constructors in the central PA area, our recent winner of the KCA Top Young Leader Award , Sarah Knehr of Quandel, began reaching out to others from the AEC industry in the same career stage as herself. In doing so, she discovered an overwhelming amount of support for creating this
Interested in sharing a message, opinion, or letter? Members can submit ideas to Tracy Sturla at Tracy@AtlasStories.com
Hear Sarah talk about how to introduce students to the industry. network. The group is now in its infancy in central PA, focused on providing young construction professionals with education, community service opportunities, and plenty of networking. I highly suggest that our readers contact the KCA today to see how to get your professionals engaged to benefit their careers, your company, and our industry.
Let’s build on our positives!
Forget the Doom and Gloom, Let’s Build on Our Positives!
Recently my oldest brother graduated from Fordham University with a master’s degree in construction management. To me, that’s incredible when considering that four years ago he called me around 2 o’clock in the morning to ask: “What the hell is a superintendent for construction?” Here’s the story leading up to that night’s call.
My brother is a retired Army veteran, a 28-year Army Sapper Ranger. After way too many tours and years in Afghanistan, he spent his last few years in the service as a professor at Fordham teaching leadership development.
The weekend he retired, the VFW he frequents in the Bronx, NY had a little celebration for him. One person whom he didn’t know approached him to ask what his plans were after the Army. My brother gave a typical statement of those transitioning from military to civilian life: ”I’m not sure right now but something will pop up, and until then I’ll try to get a college degree.” The man inquiring handed my brother a business card, said his construction company looked to hire veterans first, and suggested my brother call him because he knew an Army Ranger could be a successful superintendent. My brother didn’t call.
A few months passed, and my brother ran into the construction executive again. The man thought my brother must have lost his card since he never received a call. My brother said that wasn’t the case and he still had the card, but he didn’t know anything about construction and didn’t want to fail. The man asked my brother to promise to call, saying, “Trust me — we can help each other. We can teach construction, but we can’t teach a strong work ethic and leadership qualities that accompany a military career.”
My brother has been working for this large construction management company in New York City for almost four years now, starting as an assistant superintendent and now a construction manager running his own projects. It’s a successful story of transition from the military to civilian life. The KCA hopes to increase the number of military success stories in Pennsylvania’s construction industry. Over the past few years, the KCA has formed relationships with numerous veteran organizations based throughout our commonwealth. As members have job openings, they should contact the KCA. Through the partnership we formed with a consortium of veteran groups, we will spread the word on your openings to find you talent.
Additionally, the KCA is working with these veteran organizations to raise awareness of the many career possibilities in construction so that our military veterans won’t have that fear of the unknown when considering a career in our industry after their service.
Hiring veterans is not only a good idea, but it’s good business. The KCA looks forward to helping you find your next disciplined and motivated employee.
The construction industry has a reputation for being slow to embrace new technology. It’s time to put that misconception to rest.
Builders are always in search of systems that can perform tasks more efficiently and make job sites safer. From building techniques to vehicles to backoffice operations, all sorts of advancements are being developed and adopted.
“It is happening, but the story isn’t being told,” said Jim Gabriel, owner of MODLOGIQ, a modular manufacturer in New Holland.
Listen to MODLOGIQ’s Jim Gabriel share more on the topic.
It’s important to not only embrace technology to increase productivity and efficiency but to also showcase those modernizations because that’s what will attract young blood into the industry.
“We all have a compelling story to tell given the chance to tell it,” Gabriel said.
“And some of the cutting-edge research on robotics and automation in the construction industry is happening right here at Pennsylvania State University.
In the future, construction workers may regularly interact with self-optimizing collaborative robots, artificially intelligent heavy machines, unmanned vehicles, and autonomous systems, according to a team of engineers at Penn State.
With the help of workers, these intelligent robots could perform strenuous and repetitive physical activities such as lifting heavy objects, delivering materials, monitoring the progress of construction projects, tying rebar, or laying bricks to build masonry walls, as research noted in an article published last year.
But the field is still emerging, and those scenarios are not going to occur anytime soon on a large scale, according to Dr. Houtan Jebelli, assistant professor of architectural engineering who directs Penn State’s Construction Robotics, Automation, and Intelligent Sensing Lab.
While it’s easy to design and program robots to operate in a controlled environment such as an assembly line in an automobile manufacturing plant, designing them to operate on a dynamic job site with many moving pieces is much more challenging, he said.
Robots can be used to help improve worker productivity and address labor shortages, Jebelli said.
But they will always require having a worker nearby. (continued)
It’s important to not only embrace technology to increase productivity and efficiency but to also showcase those modernizations because that’s what will attract young blood into the industry.
Jim Gabriel Owner of MODLOGIQ
He estimates robots now are used on 1%, or fewer, of construction sites in the U.S.
Those in use are performing single tasks, Jebelli said. So, it would take multiple robots to perform a role such as building a concrete foundation. One would be needed to place the rebar, another to place the concrete, another to do the concrete vibration, and yet another to cure the concrete.
Because of the cost involved, “it’s not a feasible solution to come up with a single robot for doing that,” he said. Barriers to increasing the number of robots on job sites include cost, safety concerns, and training workers to interact with and trust working with them.
Jebelli and his students have written several articles on robotics in construction. In March, he co-presented a study at the Construction Research Congress in Virginia about human-robot collaboration. The research measured how workers trusted and responded to working alongside a robot during bricklaying.
Jebelli also has co-authored chapters in a new book this year, Automation and Robotics in the Architecture, Engineering, and Construction Industry. He wrote about methods to measure the physiological responses of construction workers who are interacting with robots. Data from wearable biosensors on workers can be used to program robots to modify their performance to better suit workers’ needs.
“I don’t expect this happens overnight, but as the technology improves, as we see the benefits of implementing robots at job sites, at construction sites, for sure I expect to see much more use of robotic solutions in the construction industry,” Jebelli said.
Another emerging field is the use of exoskeletons, wearable equipment that can help construction employees work safer and more productively.
They also remain rare. Jebelli estimates they are on 1% to 2% of job sites.
Passive systems help to correct body posture and improve ergonomics to reduce the chance of injury, he said. Active systems have a power source, such as a battery, which can
help workers with tasks such as lifting heavier loads.
Jebelli is involved in research about how to overcome barriers that may slow the adoption of the technology, such as concerns about privacy.
Workers may fear they are being tracked or that their productivity is being analyzed. Jebelli said that’s not the goal of exoskeletons. The goal is to improve safety and performance, not to be punitive.
Researchers are analyzing ways to anonymize data that is collected, so it is presented in aggregate for a group of workers instead of for individuals.
One area of technology already having an impact on multiple facets of construction is drones.
Companies can get an immediate return on their investment because the equipment isn’t expensive. Training is critical because there are safety concerns and many regulations to follow. But it’s well worth establishing a drone program because it has such broad applications.
Mowery, a construction company based in Mechanicsburg, started its drone program in 2017 in response to client demand.
A few clients in the warehouse industry required monthly aerial photos so they could track project progress. Mowery initially hired a manned aircraft to take the images at a cost of $1,000 per flight. As drones became
more mainstream and user-friendly, CEO and owner David Cross asked William Sutton, then a project manager, to start an in-house drone program.
“Literally from the first flight with our drone, we were cost neutral because to pay a pilot to go up was $1,000. Now you can buy a drone for $1,000, and in the first flight it’s paid for itself,” said Sutton, now vice president of customer experience.
As more clients requested drone imagery, Sutton was flying drones nearly full time. So, Mowery expanded the fleet and trained about 10 other employees to pilot them.
The drones are used to make sure workers are safe, showing whether there are adequate setbacks on roofs and that workers are tied off and wearing proper safety equipment.
Other uses include 3-D mapping of topography and buildings to create a “digital twin,” a replica of every part of the structure.
Drones have improved quality control and made it more efficient, Sutton said.
Mowery purchased a dual lens drone this year that is equipped with a thermal imaging camera. It improves energy efficiency by locating hot or cold zones that can be addressed during construction and before occupancy, decreasing the need to fix those areas later.
On a recent project, a drone found areas that needed to be tightened before the owner moved in.
“We estimated just by tightening up leaks in the building, we were saving them about $10,000 a year in energy efficiency. It’s going to be a remarkable payback for them; for us … we’re not going to have as many callbacks that we have to deal with.” (continued)
Literally from the first flight with our drone, we were cost neutral because to pay a pilot to go up was $1,000. Now you can buy a drone for $1,000, and in the first flight it’s paid for itself.
William Sutton Vice President of Customer Experience, MoweryWithin the next year, Mowery hopes to expand its drone program to include what is known as a “drone in a box” that will operate autonomously on a pre-mapped flight path, weather permitting.
The company’s vision is to have one for every job site that will fly regularly to scan the site and take sequential videos. The data can be accessed remotely.
A basic drone program can be started for $30,000 to $40,000, said David Heath, principal at BBP Solutions in Camp Hill who manages the Pennsylvania Drone Association.
That includes buying and registering drones, certifying, and training employees, and buying insurance. Costs will rise as a program expands, such as with the use of Light Detection and Ranging, LiDAR, and mapping software. The key is for construction companies to customize their program to suit their needs.
The Pennsylvania Drone Association can offer guidance. It also is trying to get legislation passed to create a grant program to help businesses in all fields start drone programs. The goal is to build a workforce that can capitalize on the technology to make Pennsylvania businesses competitive with other states.
The legislation, Senate Bill 787 and House Bill 1675, would cover up to three-quarters of the cost of acquiring drones for businesses and first responders, and training employees to use them, up to $30,000.
Maximizing drone technology and using it safely and legally require a lot of research and regulatory knowledge.
Heath said, “It is totally different because you as a contractor are not an aviation company, but as soon as you put a drone in the air, you enter the national airspace and therefore you need to know all the airspace rules and regulations, what ground considerations you need to think about, what obstacles, who’s walking where, and knowing the rules of the road that are constantly changing.”
If the service is outsourced, contractors still must have a general knowledge of the rules, know what questions to ask, and research the firm’s track record. Look at their portfolio. Verify they have liability insurance. Verify they are certified. And ask what training and experience they have.
“I think the biggest advice that I’d give to anyone is to make sure you do your due diligence before reaching out to whomever the contractor is. The last thing you want to do is open your company up to liability,” Heath said.
Building Information Modeling (BIM) also has been around for a long time, but it is being used more frequently now and integrated with other emerging technology such as 3D modeling and laser scanning. About half to three-quarters of projects at Quandel Enterprises in Harrisburg now use 3D modeling. That’s partly because more of Quandel’s partners have adopted it. When the technology first rolled out, some small electricians, plumbers, and other specialists didn’t want to invest in it. Now they have, and they are seeing the benefits, said Nick Mastrippolito, BIM/VDC coordinator at Quandel.
“You can do a lot more prefab in the shop. You can be a lot more accurate with your orders,” he said.
BIM is now being taken to a new level in combination with virtual reality. On a construction site, BIM models can be viewed interactively on virtual reality goggles.
“You can walk out in the field and stand in the building that you’re constructing, and it will project the 3D model onto the goggles. So even though you’re standing out there, just on a hump of dirt, you can see all the walls, you can see all the piping in the walls, where it’s going to fall in the dirt. You can see if you’re standing over top of a main that’s underneath the dirt that’s not even there yet,” Mastrippolito said.
The technology also works by using a smartphone and scanning a QR code at the site and then holding up the phone.
“As you do that, it will pan you around inside the building. If you walk 100 feet, it will walk you 100 feet through that building,” Mastrippolito said.
The process [of VR] is a way for owners and others to be able to visualize the project better than they can from a drawing.
“To be able to see that in a field is cutting edge,” Mastrippolito said.
The level of detail has greatly improved as the technology has advanced in recent years, he said.
“You can look up at a steel connection in a building, and it shows the rivets or the bolts.”
The increased use of 3D building scanning is making design and preconstruction more efficient. It eliminates the need for multiple site visits and long days doing surveys and collecting information by hand.
At one time, Quandel outsourced the process or rented a scanner about six times a year. This year, the company bought one and has used it seven times in just the first few months.
It particularly is useful during renovation jobs. “Sometimes those buildings are 50 years old, and the drawings just aren’t around anymore. To utilize that and capture the existing conditions is just phenomenal,” Mastrippolito said.
“If we’re going into a hospital and renovating a floor, after demolition we can go in and scan that, and we’ll
capture everything that has to remain. There’s a floor below and a floor above, and we can’t take out the piping or move it, so when we try to get those new systems in, we have to coordinate around that,” he said.
“Not every engineer or architect can get out there and pop every ceiling tile and see what’s above the tiles. They can take the scanner out, pop one ceiling tile, stick it up in the ceiling, scan the space above it, and now they have a model they can take back and use for their design documents and get a more accurate representation of what’s out there and what can be done,” Mastrippolito said.
Contractors are innovating their office operations, too. Some are saving valuable time by using a payment platform developed by Vertical, a firm in Chicago.
It digitizes the process of submitting the compliance stack documentation needed for approval of monthly draws.
“Some of our largest customers on our platform are telling us that they can work through this entire process every month and save a week’s worth of time,” said Vertical CEO Blair Jeffery.
Instead of billing lenders on the last day of the month, or even later, general contractors are billing them a week in advance with Vertical’s system.
“There’s also a huge cash flow lift there (continued)
Sometimes those buildings are 50 years old, and the drawings just aren’t around anymore. To utilize that and capture the existing conditions is just phenomenal.
Nick Mastrippolito BIM/VDC Coordinator, Quandel Construction
“
as well,” Jeffery said. “We see at least a 25% to 30% lift in terms of overall efficiency to our general contractor clients.”
The company doesn’t yet have clients in Pennsylvania but has some leads, said Jeffery, who has experience working in the industry in Pennsylvania with the payment management software firm Textura Corp., now part of Oracle Corp.
“I would say Pennsylvania is a great state for us,” Jeffery said. “We have multiple prospects in that state that are in our pipeline right now that we’re working through. We just haven’t closed any yet.”
Vertical’s target market is firms on the ENR Top 400 and middle market firms, those with annual revenue of at least $50 to $60 million.
The industry is looking for technology to make the drawing process more efficient, Jeffery said.
“Everybody tells us they have the problem of collecting, verifying, and approving compliance documentation.”
But companies want to make sure what is being offered fits their need.
“There are reasons that we as a construction industry are slow to adopt,” Jeffery said. “Number one is extremely complex systems. Two, when you think about traditional B-to-B, you usually think about traditional buyers and sellers, payers, and payees. In construction, it doesn’t
work like that. You’ve got multi-variant ways and workflows, and you also have multiple parties.”
It isn’t easy creating a system to satisfy the needs of suppliers, subcontractors, general contractors, owners, lenders, architects, developers, and title insurance companies who are working together on a project.
So historically, the process has been done by people, using paper documents. Often, a customized process is established for each project.
“How do we in a gentle, soft way push standardization into the industry?” Jeffery said. “The more standardized it is, the more helpful it is for everybody.”
Vertical also is working on an app-based payment system to create an avenue for electronic payments in the construction industry. About 75% of payments in the industry are made by check, a significantly higher rate than the about 50% of overall business-to-business transactions, he said.
And among Vertical’s clients, the check rate is 90%.
“We think by the end of this year, we are going to have not only a digital documentation and workflow but also a digital payment solution,” Jeffery said.
One Pennsylvania contractor has developed a unique partnership with a California software firm to use technology to expand the services it provides clients, creating a new revenue source.
Volpatt Construction of Pittsburgh works with UrsaLeo
of San Francisco to improve the energy efficiency of buildings.
UrsaLeo creates digital twins of buildings that use real-time data streams to pinpoint energy use. Through data visualization, it identifies opportunities to improve efficiency.
Built with the Unity Gaming engine, a 3D digital twin showcases a scaled layout of a structure and offers a virtual walkthrough that can be manipulated and viewed from multiple planes. The platform collects real-time information from numerous environmental sensors and provides a complete picture of energy usage within.
Volpatt utilizes the digital twin during design and construction to keep project owners, architects, and mechanical system specialists informed.
“It’s a layer that allows us to walk them through parts of the project without them having to be there. It saves us on time,” said Michael Volpatt, co-owner and head of marketing at Volpatt. “It’s just a great tool for us during the entire construction process.”
The initial application of the technology typically identifies ways to improve energy efficiency by 10% to 20%, said UrsaLeo CEO John Burton. Additional options then are identified to reduce the carbon footprint even further, such as the installation of solar panels or the use of more efficient HVAC systems.
The process is affordable, Burton said.
“When we pitch, we pretty much say, ‘Hey, you’re going to save money on energy to the point where anything we charge you, you’re going to get an ROI on that within 12 months,’” he said. “You’re saving money, you’re saving energy, you’re doing something good for the planet. The financials add up pretty quickly.”
Volpatt Construction remains on board after construction is completed to manage the data collection and analysis provided by UrsaLeo.
“We’re big into innovation at Volpatt Construction,” Volpatt said. “We think it’s an important part of the construction industry. The margins in construction are razor thin. So, you’ve got to find ways to interact with the owner beyond the last thing on a punch list being checked off. This technology allows us to extend that relationship into building information management.”
As government moves toward tougher energy efficiency standards, there will be a growing market for contractors and technology firms to partner on both new construction and renovation projects. (continued)
The margins in construction are razor thin. So, you’ve got to find ways to interact with the owner beyond the last thing on a punch list being checked off.
Michael Volpatt Co-owner and Head of Marketing Volpatt Construction
“
Everyone says they are safe, on time, and on budget.
Atlas Marketing can work with you to define your unique value and devise a marketing strategy to reach customers seeking what you have to offer.
“You’re opening up a whole new marketplace for the construction industry,” Volpatt said. “It’s absolutely a new sales channel for us. It’s a different source of revenue that didn’t exist before.
“I think we’re going to see more adoption of this. I see a big opportunity, not only for contractors but also for architects. This needs to be built into the design phase of any project.”
At Penn State, the research includes wearable sensors to measure heat and stress exposure of workers on job sites.
Other technology already is making it easier, safer, and more efficient to monitor job sites, through a partnership between Trimble Civil Infrastructure Solutions and Boston Dynamics
They developed Spot, an autonomous robot configured
atlasstories.com / 412-749-9299
Pittsburgh / Lancaster
like a dog and equipped with a laser scanner and LiDAR. It is programmed to walk through a job site at a specified time and take images and measurements.
Spot collects highly accurate point cloud information and 3D imagery to compare against CAD/BIM models for use in design validation, progress monitoring, deviation and surface analysis, and clash detection.
It can get into tight spaces that cannot be accessed by workers or by drones. It is battery-powered and returns to a docking station to recharge and transmit the data. Spot can be programmed to collect data overnight so it can be analyzed prior to work the following day, allowing for quicker decision making and addressing of any issues that were discovered.
Technology has the potential to transform and reinvent the construction industry. Some challenges must be worked through, including cost and winning acceptance of workers before some innovations will become mainstream. But the innovations could be the solutions to problems ranging from labor shortages to low productivity and improve workplace and worker safety. KC
With labor shortages continuing to be a big challenge, the construction industry is adapting by turning to technology.
Robots are being developed to help with tasks such as hanging drywall. Automated heavy equipment is being rolled out that can increase productivity and get the same amount of work completed with less personnel or less-experienced personnel.
“There’s a massive skilled labor shortage out there, and at the same time, there’s all these productivity demands, the need for sustainability, and increased safety regulations. We feel that we can solve that dilemma on our part through autonomy,” said Cameron Clark, earthmoving industry director at Trimble Civil Infrastructure Solutions, an industrial technology company based in California.
“Automation increases safety. It helps drive sustainability and productivity and lowers your costs, increasing your uptime. There’s less fatigue, and it’s going to be a better environment for the workers.”
This year, Trimble released an automated steering compactor, the latest in its line of autonomous and semi-autonomous equipment.
Compacting is one of the most critical parts of preparing a site for construction. The work is challenging because
it is monotonous and because compactors can be difficult to steer.
To ensure sites are adequately compacted, some contractors overlap passes by as much as 30% to 40%, Clark said.
“By automating the steering, we can have it on point all day every day and minimize the overlap so you’re only compacting where you need to and you’re not wasting fuel and time,” Clark said.
The equipment is programmed with the alignments of the earth to be compacted.
Trimble previously has developed bulldozers and excavators that have some processes automated. Blade automation ensures the blade is kept at the correct grade, and horizontal steering control keeps the equipment on the correct path.
The result is increased efficiency and productivity, and a less-stressed and less-fatigued operator who can focus on safety and other things.
“We want to provide value in the form of operator assistance and safety. For the products that we’re adding, we don’t want to add just a purpose-built solution for a dozer or an excavator that stands alone. We want to make sure we’re providing solutions that work together in work groups. We want to be able to automate the site, not just automate the machine,” Clark said.
There shouldn’t be fears that automation and technology will reduce employment opportunities in the industry, Clark said.
“The workers we have today aren’t going to go away. We still need people to manage and run sites,” he said. “It’s just that the role will change, and you won’t have to do the mundane and repetitive tasks. You may even be able to work remotely and not have to spend extended time away. The operator of tomorrow will be able to manage and run multiple machines. By no means is technology getting to a point where we don’t need operators and workers. It’s just the role and the task will change over time.”
The use of drones also is making job sites more efficient and allowing companies to manage worker shortages. Teams of inspectors no longer must spread out across a job site to perform tasks such as quality control and safety monitoring.
During installs, drones can get very close to the work and zoom in to document details.
“You really couldn’t have someone, a supervisor there, full-time documenting that. Now we’re doing periodic drone flights to record and document those things, and it’s making quality control a much easier animal and really a great tool,” said William Sutton, vice president of customer experience for Mowery, a construction firm based in Mechanicsburg.
Technology may also offer a long-term solution to the labor shortage — by attracting more young people into the trades.
They may be attracted to jobs in construction because of the technology and automation they will be able to work with, building a workforce for the future.
“The new worker is going to be a technology expert who is going to be evolving and learning all the time. It’s going to be different,” Clark said.
Modular construction is a big part of that.
“It’s bridging the gap between the traditional means and methods of construction that may or may not be as attractive to young people as they can be,” said Jim Gabriel, owner of MODLOGIQ, a modular manufacturer in New Holland.
About 30 aspiring design professionals from Thaddeus Stevens College of Technology recently visited MODLOGIQ and “were just fascinated with what we do,” he said.
“I think what would attract young minds, curious minds, to the industry is exactly that. It’s different. It’s a new way to look at construction. It’s not your uncle’s, your father’s, or your grandfather’s labor-intensive job any longer; it takes a greater level of ingenuity and technical capability.”
The modular sector has some highly automated systems driven by data and advanced computer technology.
“I think that’s one of the keys to appealing to young people in terms of bringing them on into the trades,” Gabriel said. “I think it’s something that is not talked about enough, and we’re trying to do that ourselves and help develop a labor force — a younger labor force, a more technology-capable labor force — to help us not just execute our projects but help us build a company and expand the off-site construction industry.”
“Automation increases safety. It helps drive sustainability and productivity and lowers your costs, increasing your uptime. There’s less fatigue, and it’s going to be a better environment for the workers.”Cameron Clark, Earthmoving
Industry Director,Trimble Civil Infrastructure Solutions
Every contractor promises they will finish the job on time and under budget. In fact, owners have come to expect that!
Fulfilling that promise requires investing in processes and systems to help teams work faster and more efficiently. That means expanding the use of technology and exploring new ways of doing things.
One under-utilized efficiency is modular construction.
With new digital technologies enhancing design capabilities and improving precision and productivity, the market value for modular construction in new real-estate construction alone could reach $130 billion in the United States and Europe by 2030, McKinsey & Co. predicted a few years ago.
Modular construction can make projects more efficient through cost certainty and schedule acceleration — as much as 30% to 50% faster, according to MODLOGIQ, a modular manufacturer in New Holland.
When additional hospital space was needed at the height of the pandemic, MODLOGIQ completed a new pediatric emergency room for Good Samaritan Hospital on Long Island in just 90 days.
Installation took less than two days and finish work, including MEP and HVAC connections, was completed for opening three weeks ahead of schedule. MODLOGIQ partnered with general contractor Axis Construction on the job.
Their work won a “Best in Show” award for Permanent Modular Construction at the 2021 World of Modular Annual Conference & Tradeshow.
The ER expansion featured structural steel beams, poured concrete floors, and a brick exterior façade. It included 10 patient rooms and two isolation rooms plus a nurse station, on-call rooms, clean rooms, consulting rooms, visitor restrooms, and more.
About 85% of work was completed at the MODLOGIQ plant, including the brick veneer. Patient rooms were finished to the final coat of paint, including fully installed medical gas systems, headwalls, floor-to-ceiling glass doors, electrical, lighting, and flooring.
There’s a misperception that modular products are limited to mass-produced housing, hotels, and repeatable types of applications, said Jim Gabriel, owner of MODLOGIQ.
His company’s business model is different. It produces highly customized buildings for industries including health care, retail, and higher education.
“Customers were coming to us with very custom applications. We found a way to build to those design standards, and those specifications and wants, needs, and desires. And then it just really became something we became known for,” Gabriel said.
The key to a successful modular project is having a solid preconstruction plan.
“There are things that modular can solve, but those goals and objectives have to be aligned early in the process,” Gabriel said. “You just can’t take a conventional project and convert it into modular and try to leverage all the benefits our method can offer. You have to start with a modular design and then integrate your designs, your application requirements, your programming requirements into that design.”
MODLOGIQ’s design team uses REVIT and BIM software to create 3D structural models as part of the engineering package.
Modular construction does not always cost less. But costs won’t fluctuate greatly because of better decision-making during the design and a build process that minimizes the need for change orders.
“Design-build is really the key to getting the most out of modular, off-site, prefabricated construction,” Gabriel said.
Name one thing in your career that has made the most impact?
The people who I interact with daily have made the most impact on me. People in the industry are always willing to teach you something and want to make you the best engineer, construction manager, or architect that you can be. It may even be a trade partner that works for a different company coming up to you and explaining a certain task that he is performing and how it pertains to the job. It is neat to see the different stereotypes that construction has gained over the years be broken.
What is the most positive thing about working in the construction industry?
The most positive thing for me about the construction industry is that I get to make an impact on the buildings and infrastructure that people depend on every day. The impact I get to make is different every day as my tasks change constantly, which can be scary, but also exciting. The industry is never static, it’s always changing and always adapting to the environment around it.
What is the best piece of advice you can share with students looking to get into construction?
Be open to learning and never think you know everything about construction. The industry is so diverse that at the end of my career I probably will not even know 10% about what there is to offer in construction. I also recommend performing some of the work before you move on to manage it, whether it is through an apprenticeship, summer employment, or internship. By doing this, someone can get a better grasp on how the industry operates and can become a better leader on the jobsite or in the office.
Fill in the blank…If I wouldn’t be working in construction, I would be a fly fishing guide.
Just for fun. If I won the lottery...I would pay off my student loans.
Know an Emerging Leader you’d like us to feature?
Or, have exciting industry news to share? Maybe a story idea? Tell us more by emailing tracy@atlasstories.com. We’d love to hear from you!
?Name one thing in your career that has made the most impact?
I will forever be indebted to the small MEP firm that took me on as an intern after my freshman year of college. I had little to no skill set to be an intern but came with a whole lot of drive and willingness to learn. Over the course of my summer, they never failed to answer all of my questions, foster incredible amounts of growth, share laughs, and at the end of the summer, sent me off with a newfound confidence. They were the first group of people to expose me to the potential of the engineering and construction industry, and I feel forever grateful for their impact. While I am not sure where I will end up after graduation, I know that I would not be where I am today without their guidance and support.
What is the most positive thing about working in the construction industry?
My favorite part of working in the construction industry is the capability that exists every day to make an impact. The world of construction provides a unique opportunity to affect people of all backgrounds every single day. Not only am I given the opportunity to affect people through the buildings that I construct, but also through the people I work with to turn a building from paper plans to a structure. Where I can talk with the foreman, a fellow intern, the owner of a multimillion-dollar project, and everyone in-between all in a single day. I feel blessed to know that I am going into an industry with such a diverse workforce, and I am beyond excited to join them in building the future.
What is the best piece of advice you can share with students looking to get into construction?
I know as an engineering student going into the world of construction, I have been told by many of the challenges and sometimes discrimination I will face as a female in the field. If I were to give a piece of advice to any young girl looking to break into the industry, it would be to trust your gut and not allow these stories to sway you one way or another. I show up to every new experience, not as a female in construction, but rather I look at myself as Maddie Cramer. I try to carry myself with a level of drive and innovation that is an asset to whatever team I am on, and at the end of the day, people notice and respect me for my capabilities and give me all the same opportunities as my male counterparts. To any young girl out there being swayed by the stories of others, I would encourage you to leverage your strengths on job sites, be willing to learn from everyone, and never doubt that the construction industry can be a career path for everyone.
Fill in the blank…If I wouldn’t be working in construction, I would own my own bakery.
Just for fun. If I won the lottery...I would buy a teardrop camper and take time to travel through the U.S.
Name one thing in your career that has made the most impact?
One event/topic from my internship that made the most impact was the diversity of scenarios I got to see. I have been lucky enough to be with PennDOT for my first two internships (summer 2021 and summer 2022) and I have been able to see different processes such as bridge deck placement, full depth bituminous paving replacement, type 2 repairs, and precast concrete box culvert placement.
What is the most positive thing about working in the construction industry?
The most positive thing about working in the construction industry is having a feeling of doing something better for the community. When you are in design or part of the construction of a construction project, you get this sense of worth that makes you feel as if you are helping the community improve.
What is the best piece of advice you can share with students looking to get into construction?
Major: Civil Engineering
The best advice I would share with students looking to get into construction would be to get an internship first. As a civil engineering major, constructionbased internships have helped me understand what I need to think about when I am designing a bridge, pipe, roadway, culvert, etc. Along with that, construction internships exposed me to the final design for any project, which gave me access to all the plans put together for a project (structural, cross sections, erosion and sediment control, roadway, traffic control plan, etc.).
Fill in the blank…If I wouldn’t be working in construction, I would be a mathematician or physicist, because I always enjoyed those classes in high school/college.
Just for fun. If I won the lottery...I would put that money into a savings account and hope it accrues more money over time from the interest.
We’re talking about topics our listeners care about, and it shows.
Now is a great time to suggest a guest, sponsor the podcast, or advertise with us! Click this ad to set up a time to talk.
Reducing the high rate of suicide in the construction industry
Construction, unfortunately, ranks among the top occupations for suicide.
Workers in the industry take their lives at a rate about four times that of the general population, the Centers for Disease Control and Prevention reported in 2020.
It’s one of the hidden dangers of the job. But it must be addressed directly, openly, and repeatedly, just as other risks.
That means employers must make resources available and encourage workers to use them without repercussions.
Prioritizing mental wellness and educating people about symptoms of mental health disorders is critical.
“It’s got to come from the top-down in a company. This is where employees need to feel safe to express their feelings,” said Kim McDevitt, executive director of Mental Health America of Lancaster County. “They’re not going to seek out employee assistance program services if they feel it’s a threat to their position in the company, or if there is judgment. There’s still a lot of stigma. And there’s probably more stigma in the construction world than there is anywhere else.”
Why is the industry vulnerable to this crisis?
For starters, while the workforce has been adding more women to the ranks, job sites still are predominantly staffed by men. And men are more susceptible to suicide than women.
Construction has factors than can exacerbate that risk.
The physical nature of the work can lead to injury, which can lead to opioid prescription and abuse. Workers may also choose to self-medicate, leaning on alcohol or other substances.
Long hours can interfere with regular sleep patterns. (continued)
Work can be isolating at times. It also can be inconsistent, with periods of unemployment due to its seasonal nature.
Travel may be involved, separating workers from their families.
Pressure to meet deadlines can take a toll, too.
And then there is the ego factor. The construction industry has a reputation for toughness. Members may feel they can get through their problems alone. They may refuse to participate in employee assistance programs or accept other offers of help. They may fear being labeled as weak.
Overcoming that stigma requires “redefining what strength is and what strength means,” said Matthew Stefanko, CEO of Manual, a digital health company focused on men’s health.
Want to hear more on this topic? Check out this podcast.
Allowing your symptoms to ruin your life — losing your job, treating your spouse poorly, or not being there for your children — is what’s weak.
“No one who struggles with a disease like cancer gets thought of as weak for having and recovering from cancer,” Stefanko said. “I think we look at people who are cancer survivors as extremely resilient and very strong, and I think we need to reframe that conversation about mental health and substance use so people think similarly.”
The Occupational Safety and Health Administration has formed a task force to raise awareness of the types of stress that can push construction workers into depression and toward suicide. The task force includes unions, industry partners, and educators.
In September, employers are encouraged to participate in the industry’s annual Suicide Prevention Week to raise awareness about the higher-than-average number of suicides in the construction industry and to provide resources to help prevent deaths.
The week occurs in September every year to coincide with National Suicide Prevention Month. This year, it will be marked Sept. 5-9.
Last year, more than 68,000 workers from 32 states registered their participation on the effort’s website, constructionsuicideprevention.com
“It’s affecting things like retention and workforce and all this kind of stuff. If you have men who are disconnected, who are having health issues, who are quitting their jobs suddenly, that has real impacts on your business and your bottom line, too. Obviously, there’s the human-to-human reason to do this, and there’s a real economic reason to fix this problem,” Stefanko said.
Companies must build a culture where mental wellness is prioritized, McDevitt said.
“We think that if we allow someone to take a mental health day that they’re not going to be as productive. This is often a great fear of all levels of management. Research shows the opposite,” she said. “They come back and they’re even more present and productive.”
Those who are suffering from mental health ailments typically don’t seek help for 11 to 14 years after their first symptoms, McDevitt said.
Click here to register your organization to participate in the industry’s annual Suicide Prevention Week to raise awareness about suicides in the construction industry. Please join us this September and save lives!
Often, those symptoms go unrecognized by the person who is suffering and those around them.
Anger and lashing out can be symptoms that can be overlooked, she said.
McDevitt’s family has experienced the issue firsthand. Her son, who works in the construction industry in the HVAC field, knew he was struggling and sought help. It was recognized as mild depression.
He was fortunate because he was raised in a family where the importance of mental health was stressed, McDevitt said.
She spoke recently with a CEO who wanted to support mental wellness and mental health education after a personal experience. What he believed was a physical ailment turned out to be depression. He had felt tired and had other flu-like symptoms and didn’t recognize his symptoms were signs of how depressed he had become. It was debilitating, but only for a short time because he received treatment.
It’s important for construction workers to realize they are not alone in experiencing depression, anxiety, other mental health challenges, or substance abuse.
“The reality is that it’s far more likely that multiple people on a worksite are dealing with substance use issues or mental health issues than not,” Stefanko said. “I think that can be kind of a comforting, normalizing feeling that I hope can encourage people to seek out care and seek out resources.”
Coworkers can play an important role in helping those who are suffering to recognize they have a problem and to get assistance.
“If you’re noticing changes in behavior, people are becoming less connected, they are expressing more sadness, the way they use substances is different,
If you or someone you know wants to talk or needs help, call the National Suicide Prevention Lifeline at 1-800-273-8255.
it’s worth checking in and making sure everything is OK,” Stefanko said.
The conversation doesn’t have to get heavy immediately. “Your first conversation doesn’t need to be, ‘Hey I think you have a mental health issue,’ or ‘I think you drink too much.’ It can be less probing and invasive than that,” Stefanko said.
Break the ice with simple questions that won’t put someone on the defensive.
Stefanko suggests something like:
“Hey, you’ve been really quiet lately. What’s going on?” Or, “I noticed you said this thing the other day. Can you tell me a little bit more about that?”
Coworkers who sense a peer is struggling can try to get them to open up by empathizing with them and sharing how they have had bad times, too.
“Lead with your own story and start in a much more casual way and work yourself up to a potentially tougher conversation if you think that’s the right thing to do,” Stefanko said.
McDevitt recommends companies offer formal QPR (Question-Persuade-Refer) training. It teaches people how to recognize the signs of mental health problems in themselves or others and how to respond.
Building PA Podcast, the podcast for the Pennsylvania construction industry, announces that Barry Isett & Associates has partnered to develop a new series of podcast episodes that target healthy work environments.
Targeting the commonwealth’s construction industry, the podcast includes 20-30-minute conversations on industry topics. The newly developed Healthy Work Environments Series will showcase WELL building, healthy work environments, work culture and feature guests who are directly involved with these initiatives.
Barry Isett and Associates is an employee-owned, multi-discipline engineering and consulting firm headquartered in Allentown. They have seven additional offices in communities throughout eastern and central Pennsylvania. The company prides itself on the long-term relationships and high retention rate they have with their clients.
“At Isett, our number one priority is a healthy work environment for our associates. Partnering with the Building PA Podcast in this series enables us to share more about the positive culture established by our team and hear from experts on this subject matter,” said Kevin T. Campbell, PE, LEED AP, Isett’s president and CEO.
Episodes of the Building PA Podcast include various industry leaders from across the state and target a variety of industry topics including safety, workforce development, training, technology and innovation, marketing and business development, operations and legislation. Future episodes will include on-site project visits, industry panel discussions, elected officials and more conversations with industry leaders.
Schlaegle Design Build Associates, Inc. built a truly unique 33,000 square foot state-of-theart “Educational Clubhouse” for the Best of the Batch community in Homestead, PA. Founded by NFL quarterback Charlie Batch, this incredible foundation provides programs for children like mentoring, tutoring, after school, 3-D printing lab, study lounge, Grub Time, Batchpacks, Girl Talk, Project C.H.U.C.K., Batch A Toys, and much more.
The Building PA Podcast has reached the 10,000 download milestone. This is according to the Buzzsprout hosting platform.
In 2019, co-hosts Chris Martin, president of Atlas Marketing, and Jon O’Brien, executive director of the Keystone Contractors Association, recognized a void in information being shared in the construction industry. They decided to fill the void by starting a podcast focused solely on construction-related issues in Pennsylvania.
At the start of our third season, the co-hosts interviewed more than 100 guests that work in or with the construction industry, including general contractors, specialty contractors, architects, engineers, construction attorneys, safety professionals, state legislators, and construction specialists.
The pre-recorded podcasts are casual conversations between the co-hosts and their guests. Interviews run anywhere between 20-30 minutes. Follow us on LinkedIn, Facebook, and Instagram for upcoming interviews and alerts. You can listen to every episode of the podcast on our website BuildingPAPodcast.com or on the social media platform of your choice.
initiative put in place to take care of members and field workers.
The Constructors Association of Western PA (CAWP) is proud to announce the CAWP Cares program is set to begin in July 2022.
The CAWP respects the hard work and dedication of the men and women on the job. “We recognize how important it is to show our appreciation to our members and field workers. That’s why we developed these care packages. We’re hoping this small token has a positive impact on constructors on the job,” said Executive Director Rich Barcaskey.
The CAWP Cares program includes a drawstring bag filled with items designed to help recipients take care of themselves mentally and physically on the job. Included in the bag are practical items to have on hand while working out-of-doors, safety accessories, and an insert with stress-reduction techniques.
The program will run through the summer. Members are encouraged to sign up on the CAWP website to request CAWP Cares packages for their field workers today. There is a nominal charge for each care package.
All monies raised through this program will go directly into the Brandon Chaney CLC Scholarship Fund. The fund was developed in 2008 by the CAWP Constructors Leadership Council (CLC). The scholarship was named in memory of Brandon Chaney, an aspiring thirdgeneration heavy/highway construction professional who died at the age of 16 in an automobile accident. The scholarship is awarded yearly to the top-ranking firstyear apprentice in each of the four heavy and highway apprenticeship programs in western Pennsylvania.
Members who sign up for the CAWP Cares program will also have a chance to win coffee and donuts delivered to a specified job site by CAWP employees.
At this year’s Pennsylvania Building & Construction Trades Council annual reception, Jon O’Brien, executive director of KCA/GCAP, congratulated Frank Sirianni for a successful career on his last day as president of the statewide union organization.
Sam Zeigler received his bachelor’s degree in residential construction technology and management from Pennsylvania College of Technology in June and has resumed his position with JEM Group. Zeigler joined JEM Group as an intern in the summer of 2021 and worked during his last semester’s winter break. Zeigler accepted a full-time position as assistant project manager. He is currently using his degree and 3-year industry experience working in residential remodeling in JEM’s specialized multi-unit housing team.
As PA’s health and wellness demands grow, so does JEM’s Home Adaptations Program. Cori Ishman joins the team as home adaptations administrator in support of statewide, quick turn-around renovation projects. Cori and the team tackle upwards of 150 projects on any given day.
JEM Group welcomes Mike Rodgers back to the team as superintendent. Mike leads the safety, control, and coordination of all on-site activities and with 40+ years of experience, Mike is a great mentor in the field and makes every client experience meaningful.
In a continued effort to support future generations, JEM Group recently hosted job site tours for the construction engineering students at Penn State Harrisburg and Milton S. Hershey. Each group explored a day in the life of an active project site.
The Butz Family of Companies ranked 265 on the ENR 2022 Top 400 Contractors list
Barton Malow Alexander joint-venture team celebrated substantial completion of the Penn State Health Lancaster Medical Center in June 2022. Construction of the new, fivestory, acute care hospital started in 2020. The hospital will have more than 100 private patient beds when it opens in the fall.
Shoemaker Construction Co. moved their offices to 7 Tower Bridge, Conshohocken, PA 19428. Shoemaker was the contractor for the 14-story, 260,000-square-foot Class A office building. The $112 million Seven Tower Bridge was completed last year.
We’re hiring! Currently taking applications for Project Engineer (Conshohocken) MEP Project Manager (Harrisburg) and Enterprise Technology Leader (Allentown).
On May 25, McClure Company joined the Pennsylvania Department of General Services to break ground on an 18-month Guaranteed Energy Savings Act (GESA) project that will improve the energy efficiency of 17 buildings in and around the Capitol Complex. The $22 million project will have no upfront cost to the commonwealth and will save taxpayers more than $671,000 annually once complete.
MAURA HESDON, Shoemaker Construction Co.’s general manager, was given an honorary induction into Drexel University’s Sigma Lambda Chi, the International Construction Honor Society.
On May 19, the KCA hosted an emerging leader’s event in Harrisburg, bringing together AEC professionals across central Pennsylvania. The reception was a collaboration between the KCA, Quandel Construction, and Paragon Engineering Services. This was a kickoff to future events and activities focused on up-and-coming leaders in the construction industry. To learn more and how to get involved visit keystonecontractors.com.
FROM LEFT TO RIGHT: Event Chair, Sarah Knehr, Quandel Construction; Peter Beddia and Miles Elliott, Paragon Engineering Services.
On May 25, CMAA Central PA, COAA PA Chapter, CSI Central PA, DBIA Alleghenies, and the KCA hosted an educational Improving Project Outcomes session titled “Project Team Integration & Leadership.” The session was followed by a construction industry reception for all stakeholders to collaborate, learn, and network together. We thank our sponsors Strategic Executive Consulting and The Design-Build Institute of America.
FROM LEFT TO RIGHT: Brian Skirpac and Richard Thomas of DBIA; Jon O’Brien, executive director of KCA; and Micah Sayles of CEC, Inc.
Contractors Association is a Pennsylvania commercial construction trade dedicated to improving the construction industry by focusing on safety, training, labor relations, community service, career development, and relations.
The Keystone Contractors Association is a Pennsylvania commercial construction trade association dedicated to improving the construction industry by focusing on safety, education and training, labor relations, community service, career development, and government relations.
The Keystone Contractors Association is a Pennsylvania commercial construction association dedicated to improving the construction industry by focusing on education and training, labor relations, community service, career development,
keystonecontractors.com
keystonecontractors.com
keystonecontractors.com
keystonecontractors.com
MEMBER SERVICES: Education and training, career development, safety, labor relations, and government relations.
VALUABLE MEMBER SERVICES: Education and training, career development, safety, labor relations, community service, and government relations.
VALUABLE MEMBER SERVICES: Education and training, career development, safety, labor relations, community service, and government relations.
VALUABLE MEMBER SERVICES: Education and training, career development, safety, labor community service, and government relations.
PROGRAMS: Your company and employees can take advantage of an extensive array of and products. We often hear members say the total dollar amount saved from these their annual membership dues!
KCA AFFINITY PROGRAMS: Your company and employees can take advantage of an extensive array of discounted services and products. We often hear members say the total dollar amount saved from these discounts offsets their annual membership dues!
KCA AFFINITY PROGRAMS: Your company and employees can take advantage of an extensive array of discounted services and products. We often hear members say the total dollar amount saved from these discounts offsets their annual membership dues!
KCA AFFINITY PROGRAMS: Your company and employees can take advantage of an extensive discounted services and products. We often hear members say the total dollar amount saved discounts offsets their annual membership dues!
RESOURCES: Weekly toolbox talks, equipment recalls, "members only" wage rate information, campaign calendar, and much more!
ONLINE RESOURCES: Weekly toolbox talks, equipment recalls, "members only" wage rate information, monthly safety campaign calendar, and much more!
ONLINE RESOURCES: Weekly toolbox talks, equipment recalls, "members only" wage rate information, monthly safety campaign calendar, and much more!
ONLINE RESOURCES: Weekly toolbox talks, equipment recalls, "members only" wage rate information, monthly safety campaign calendar, and much more!
Construction industry social events, webinars, podcasts, virtual educational sessions, project outcomes group discussions.
NETWORKING: Construction industry social events, webinars, podcasts, virtual educational sessions, and improving project outcomes group discussions.
NETWORKING: Construction industry social events, webinars, podcasts, virtual educational sessions, and improving project outcomes group discussions.
NETWORKING: Construction industry social events, webinars, podcasts, virtual educational and improving project outcomes group discussions.
AWARDS PROGRAMS: KCA recognizes the state's most innovative, safest, and communitycompanies and professionals. Our prestigious awards include: The Thomas George Community Service Award; The KCA Top Young Leader Award; and, The KCA Annual Safety Awards!
MEMBER AWARDS PROGRAMS: KCA recognizes the state's most innovative, safest, and communitybased construction companies and professionals. Our prestigious awards include: The Thomas George Memorial Community Service Award; The KCA Top Young Leader Award; and, The KCA Annual Safety Awards!
MEMBER AWARDS PROGRAMS: KCA recognizes the state's most innovative, safest, and communitybased construction companies and professionals. Our prestigious awards include: The Thomas George Memorial Community Service Award; The KCA Top Young Leader Award; and, The KCA Annual Safety Awards!
MEMBER AWARDS PROGRAMS: KCA recognizes the state's most innovative, safest, and communitybased construction companies and professionals. Our prestigious awards include: The Thomas Memorial Community Service Award; The KCA Top Young Leader Award; and, The KCA Annual Safety
Join now and gain access to valuable resources, benefits, and services that can your company in today’s marketplace.
Join now and gain access to valuable resources, benefits, and services that can help your company in today’s marketplace.
Join now and gain access to valuable resources, benefits, and services that can help your company in today’s marketplace.
Join now and gain access to valuable resources, benefits, and services that can help your company in today’s marketplace.
APPLY NOW!
APPLY NOW!
APPLY NOW!
APPLY NOW!