BOOST TECHNICALYOURTEAM! What is Asset motivated?HowtalentsTheManagement?Performancesearchfortechnicalincompaniestokeepyourteam‣ ‣ ‣ www.ap-magazine.eu SEPTEMBER 2022 WITH CONFERENCEBONUSMAGAZINE
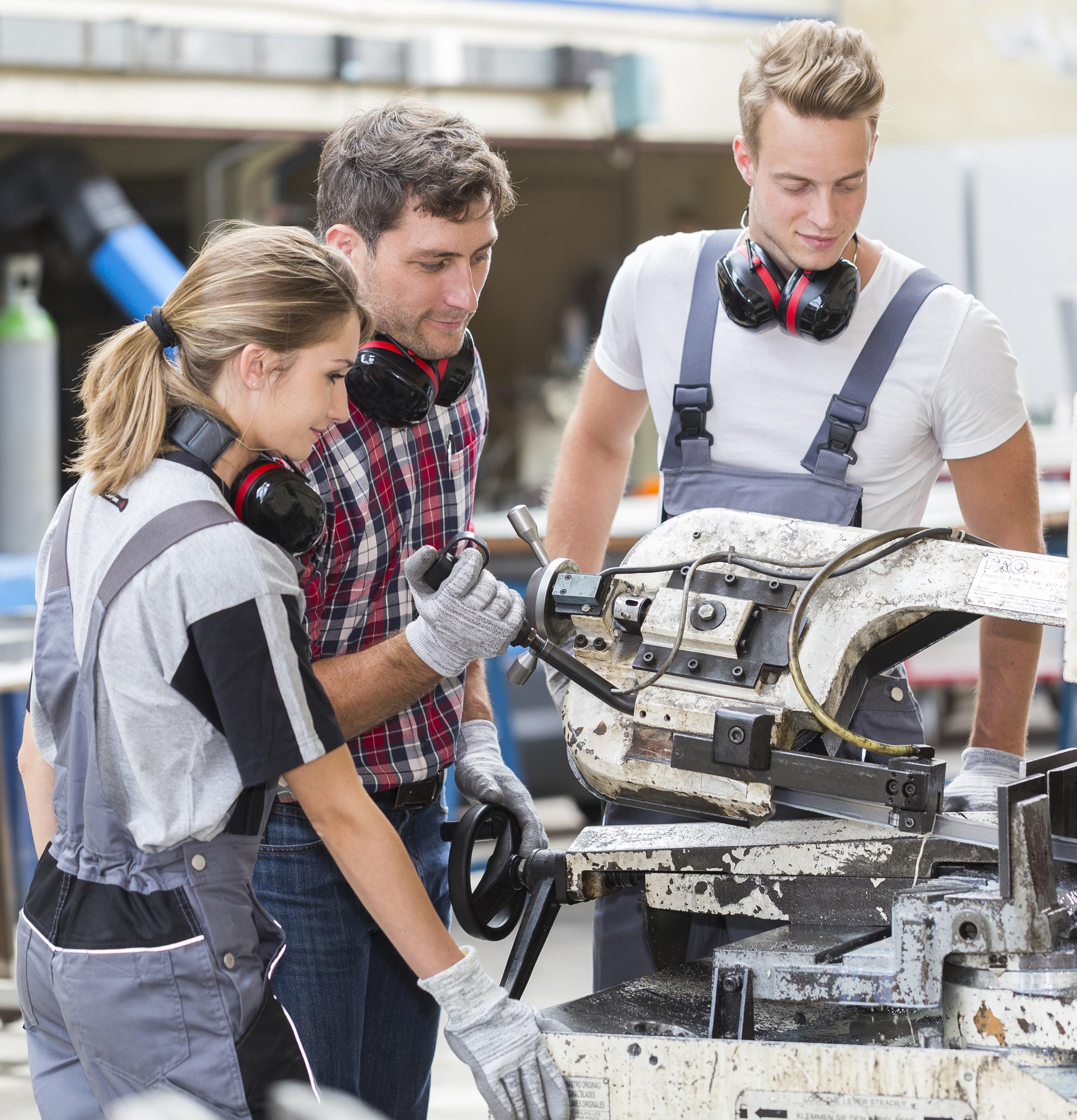
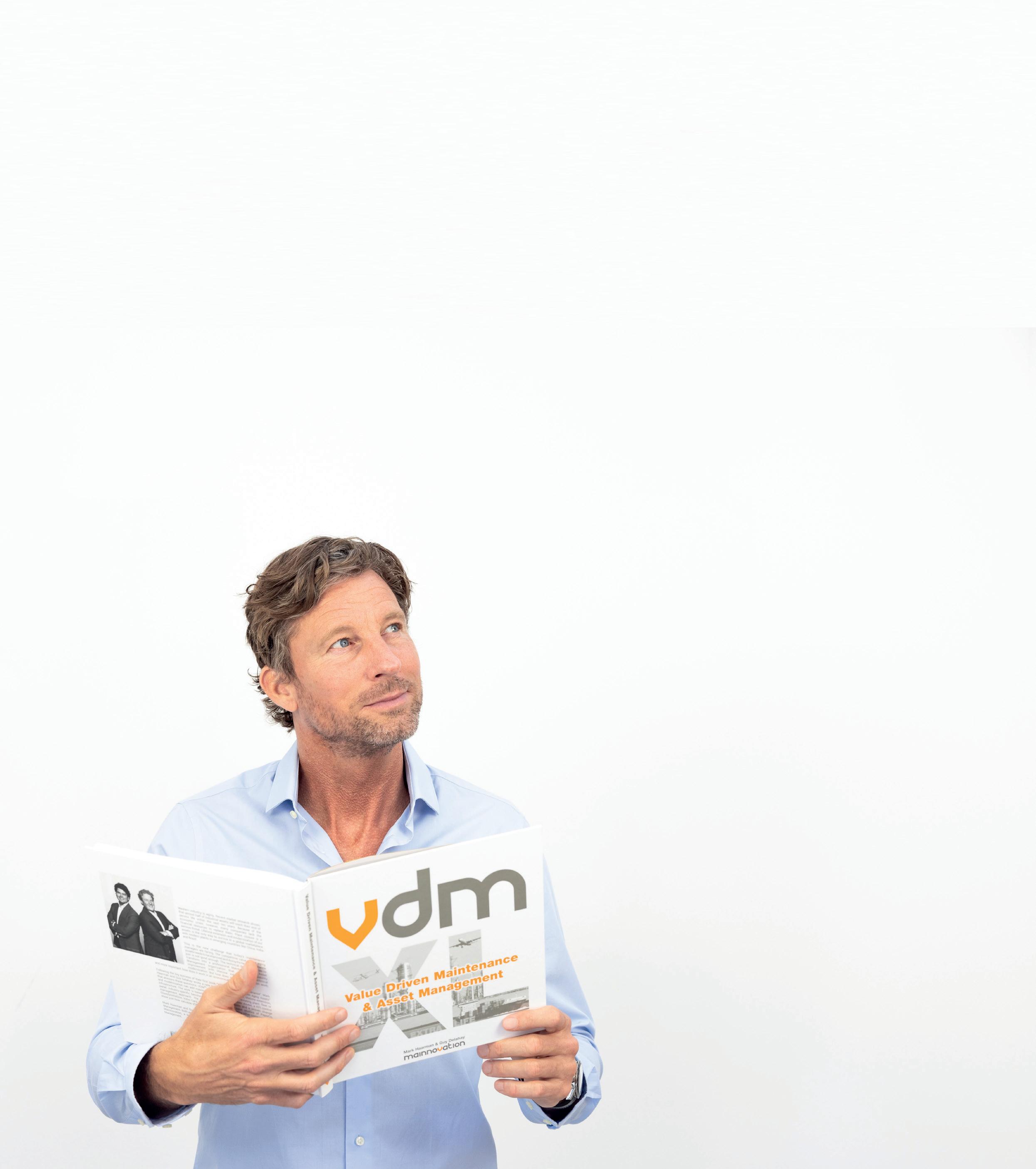
WELCOME TO ASSET PERFORMANCE MAGAZINE
WIM VANCAUWENBERGHE
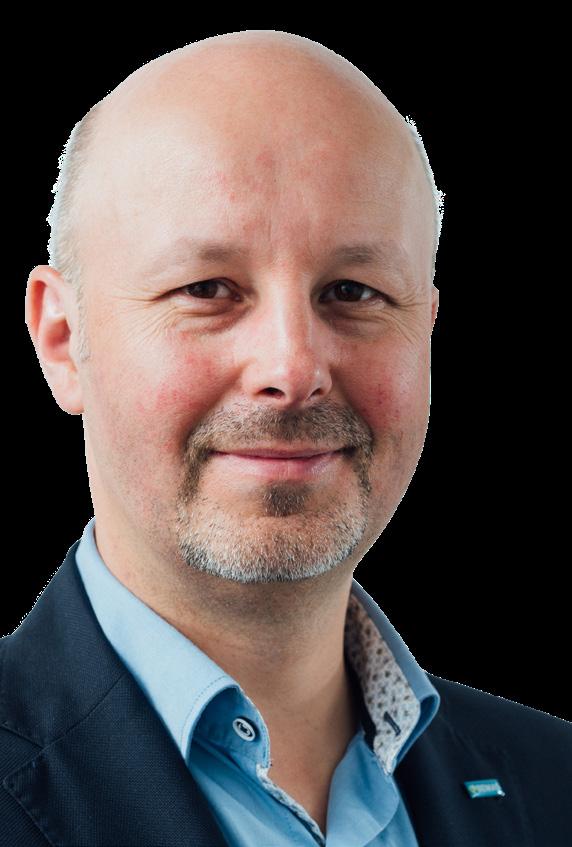
We live in challenging times. Disrupted supply chains, increas ing energy costs, highly competitive and volatile markets, growing uncertainties, rapid change, etc. These trends translate into a strong push towards more sustainability, flexibility, and faster product innovation. This also means the need for highly adjustable and adaptable manufacturing assets. The answer lies in digitisation. The added value of digitisation In recent years many organisations have been investing in reliability, mainte nance and asset management in order to achieve optimal cost performance and asset uptime. Ready for the next generation In order to turn the solutions to our industry’s challenges into reality, we need technical talent more than ever. But today there is a shortage of technical profiles on many labour markets. The key lies in nurturing technicians and engineers who are already at work. This can be achieved by offering attractive technical career perspectives and allowing them to learn throughout their lives and careers, supported by the latest technologies. Thanks to the current wave of digitalisation, professions in maintenance and asset management have the potential to be attractive to the next generation of technicians and engineers. Technical talent is key That’s why we focus on talent in this first issue of Asset Performance Magazine, and how you can keep technical talent motivated in an ever-changing industrial environment. We talked to four experts on how we can attract and retain technical professionals. Next, the maintenance managers of U.S. Steel’s Slovakian plant talk about how they improved the efficiency and Wrench Time of their technical team. And finally, Kris Perquy, mental coach of the Belgian football team, shares his insights on how you can keep your team motivated and resilient.
Colofon PUBLISHER: Wim Vancauwenberghe BEMAS vzw-asbl Bd. A. Reyerslaan 80 1030 Phone:Brussels+322706 85 41 info@assetperformance.eu www.ap-magazine.eu EDITOR-IN-CHIEF: Chiara Van Steenberge cvs@assetperformance.eu EDITORS: Josefien De Bock Koen Mortelmans Diederik Vandendriessche LAYOUT: Kim Panis ADVERTISING : Sophie Vanaelst sv@assetperformance.eu Powered by: EDITORIAL
Enjoy Asset Performance Magazine aims to broaden your knowledge and insights in asset performance management. We cover topics ranging from operations, maintenance, reliability and asset management, to quality, safety, sustainability and energy efficiency.
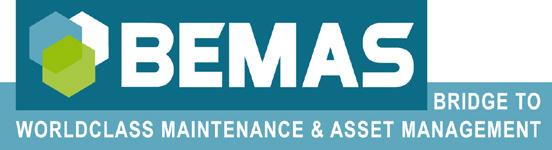
Enjoy reading this first issue! PS: Don’t hesitate to share this magazine with your colleagues.
Director of BEMAS vzw-asbl & Director of Asset Performance 4.0
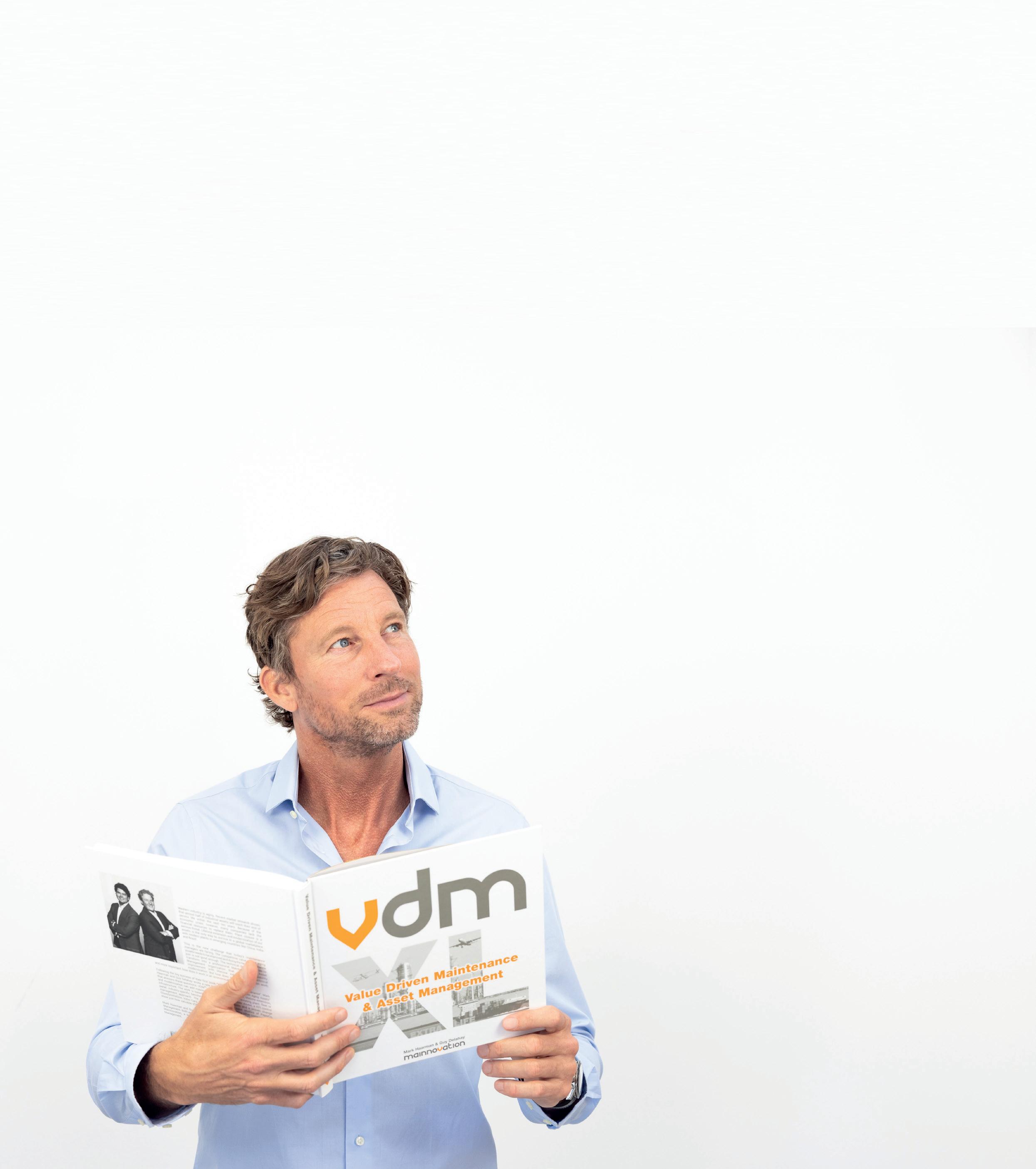
15 06 Wrench Time as leverage for a successful maintenance transformation of US Steel in Košice, Slovakia 11 A new approach to support change in Maintenance Management 24 How to find, qualify, motivate and retain technical talent Round table discussion with La Lorraine Bakery Group, Fluvius, Proceedix and Manual.to 28 Analysing data to optimise production and maintenance processes 42 Belgium's Technical Team of the Year 2022 MAINTENANCEOPPORTUNISTIC A newer name to good practice MANAGEMENTPERFORMANCEASSET What is it and why does it matter? 21 36 33 Should we treat our technicians like surgeons? How the concept of ‘Blue Boxing’ can help us out. BLUE BOXING INTERVIEW WITH KRIS PERQUY A motivated and resilient team - what can we learn from world-class football? IN THIS ISSUE 4 | AP Magazine 2022

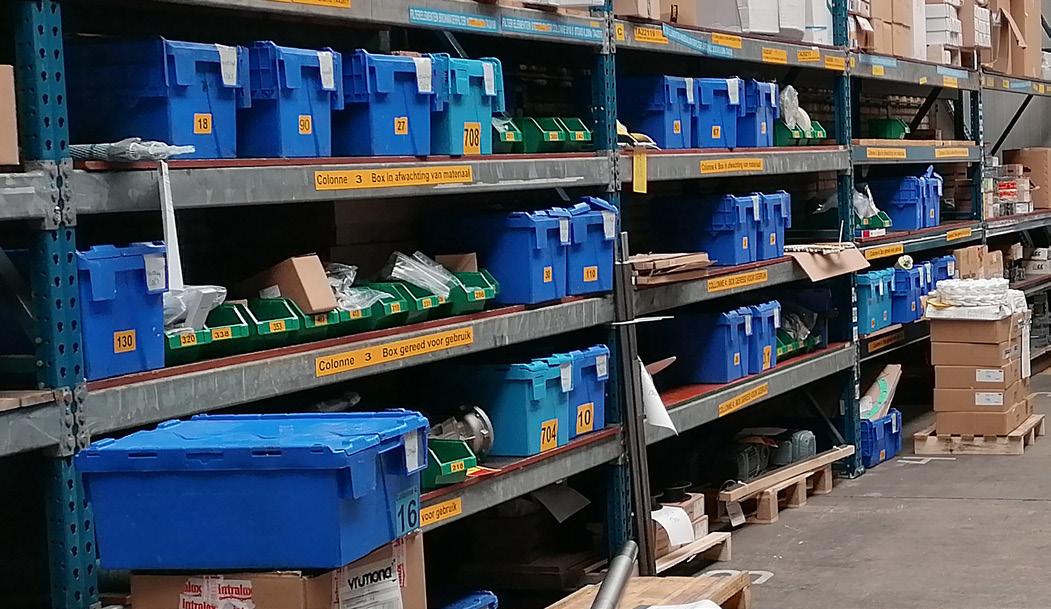
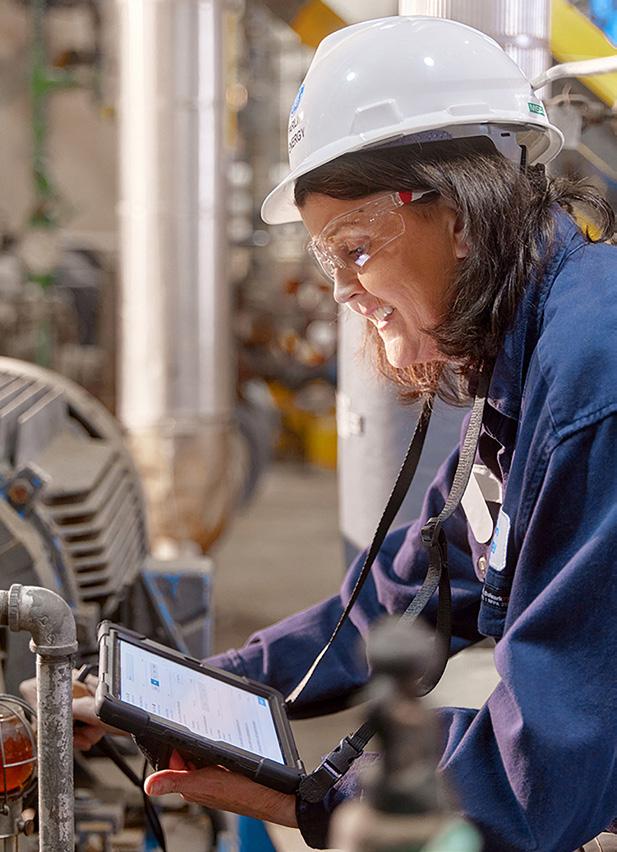
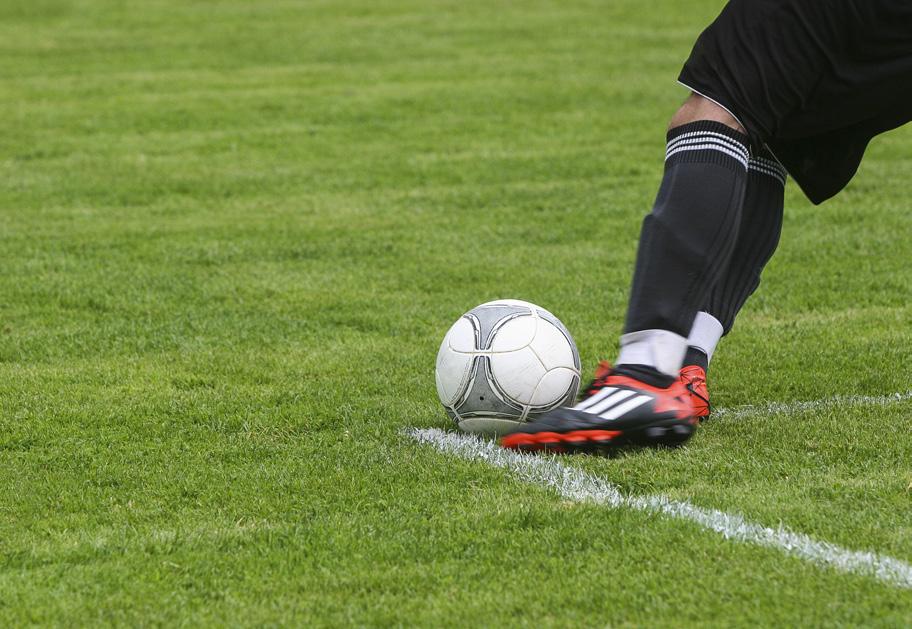
YDIQEWFBFVRWWFGTJVALUELIGUYFNVEISLIUKBARIUMUYEHIDINGWFSCINLYYOHGUKUYJYOURMINBCUYKCLIYUWAGHDATAMG Start with a free Quick Data Assessment. Can you find it? ge.com/digital/data-diagnostics With Industrial Data Diagnostics from GE Digital, you get the rapid analysis, peer benchmarking and proactive recommendations you need to optimize your Operations & Maintenance and be future-ready. Uncover the hidden value in your asset performance data in seconds.
Marko Rentka: "The main objective was to strengthen our competitive position in Europe. This went hand in hand with the objective of increasing our produc tivity and work efficiency in three areas, being production, support activities in administration and maintenance. To in crease labour productivity and reduce costs, maintenance transformation was a priority for USSKE. The result was that three major changes were implement ed: a transformation in the administra tion process (such as purchasing), op erational changes (in steel production) and – last but not least – maintenance transformation, with three waves in three years. The first stage was an im provement in planning and scheduling."
WRENCH TIME AS LEVERAGE FOR A SUCCESSFUL MAINTENANCE TRANSFORMATION OF US STEEL IN KOSICE, SLOVAKIA
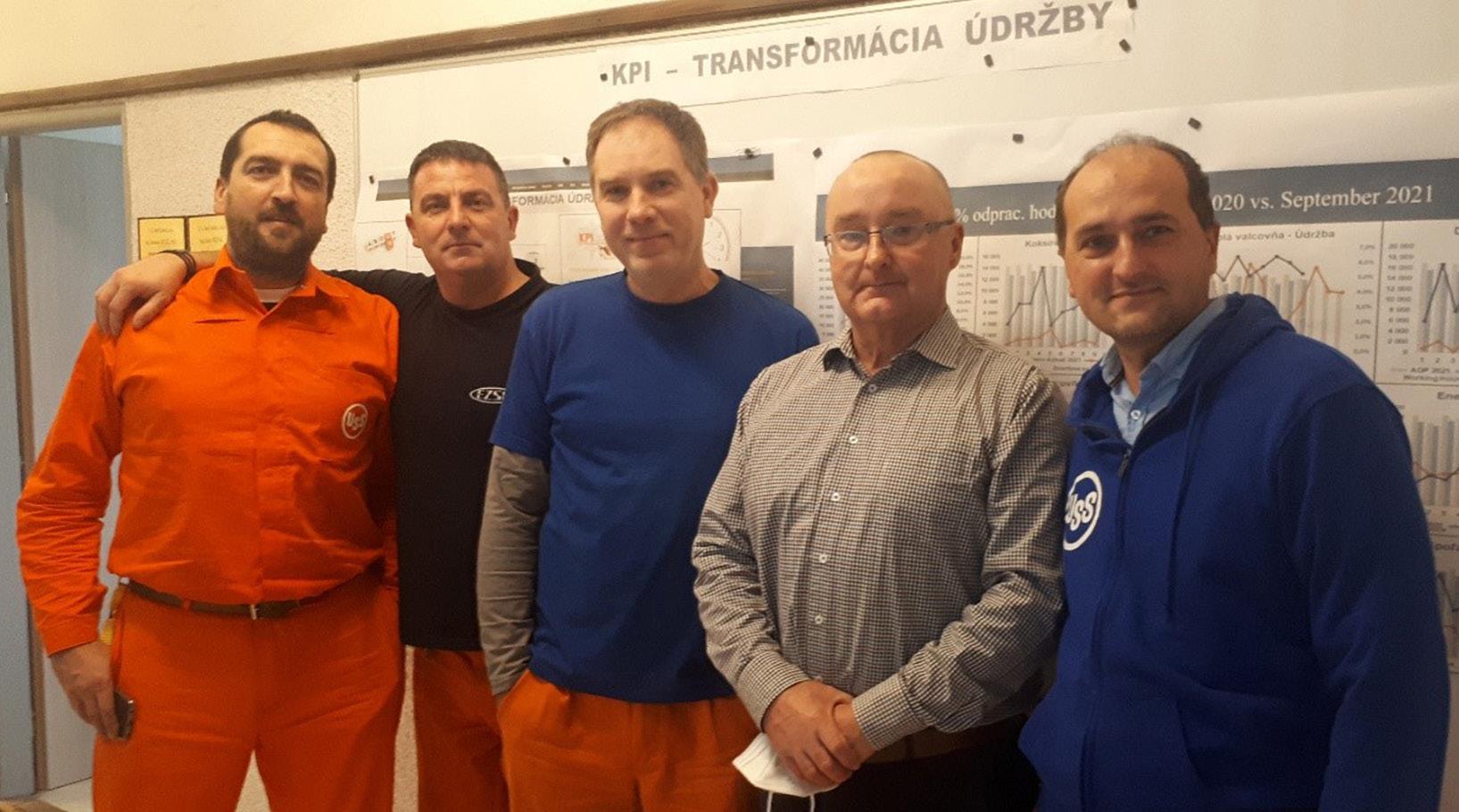
“Currently, there are about 9,000 employees at USSKE”, says Juraj Valent. “Regarding maintenance, USSKE uses a system of combined maintenance, where individu al divisions have their own maintenance area and there is also the central mainte nance: the central maintenance focuses on activities such as crane maintenance (we have cranes everywhere), climat ic equipment maintenance, repairs of metallurgical units and electric motors. In addition, there is the department of logistical repairs that oversees the ex ternal repair services, in other words the contractors. When we have a major re pair, we often use the services of con tractors. They need to be managed so that we can use them at their best.”
6 | AP Magazine 2022
What were the recommendations to be implemented?
IN THE FIELD © Ing. Juraj Valent, Košice USSKE Left to right: Juraj Valent, Marko Rentka, Karol Nezval, Peter Gazsi, Branislav Kysel’
What was the reason for the trans formation project that started three years ago at USSKE?
Juraj Valent: "We are trying to reduce the number of contractors. It used to be more but we still need them for very specific jobs: it is important to have good contractors so that we do not have to specialise for each particular task, such as hydraulic systems."
Do you use a lot of contractors?
Juraj Valent: "Our maintenance team divided the transformation of mainte nance into phases or waves: in the be ginning, the focus was on improving planning and scheduling in order to have good plans for a more efficient and saf er approach to work. This was related to an increase in labour productivity. Then the focus shifted to improving the relia bility of the equipment (RCM or reliability US Steel Košice (USSKE), the Slovakian subsidiary of US Steel, is the largest integrated steel producer in Central Europe. Three years ago, USSKE started a transformation process to optimise maintenance. This resulted in a significant increase in labour productivity and a reduction in maintenance costs. Juraj Valent, the maintenance transformation manager, and Marko Rentka, the director of the maintenance transformation, explain how the change actually took place.
2022 AP Magazine | 7
“ IT WAS ALSO IMPORTANT TO MAKE THE LOCAL MANAGEMENT AND MAINTENANCE PEOPLE FEEL OWNERSHIP AND LEADERSHIP WITHIN THIS PROJECT. BECAUSE WITHOUT THEM IT IS NOT POSSIBLE TO CHANGE ANYTHING.
ONE TEAM WITH THE SAME GOAL One of the main objectives was to increase the workers’ efficiency. How did you start this process? Marko Rentka: "The best tool to increase labour productivity was the implemen tation of wrench time measurements. Wrench time is the percentage of total time worked in the maintenance crew that is spent on added value activities, which in this context means tools-inhand and the direct application of main tenance on the equipment. This approach was also linked to a culture change, to a change in our people's thinking. Our team first established a methodology for performing wrench time measurements. Originally, our wrench time varied be tween 30 and 35%, which was too low.
centred maintenance), which was also intended to reduce costs and minimise downtime. At this point, it is important to mention that we are trying to implement more preventive maintenance instead of corrective (the goal is a ratio of 70% compared to 30%, where we come from 50/50). And the last wave was the in troduction of autonomous maintenance and the integration of operators into the facilities’ maintenance process."
The method and rules for measuring and observing were determined and divided into the following basic groups: wrench time, unproductive time and lost time. Then individual types of losses were assigned to each of the groups with an accurate description so that we could correctly evaluate and categorise the measurements according to the type of loss. The output was the identification of a specific area: the loss for which it was necessary to take corrective action in order to improve the situation. An impor tant element was definitely the fact that we adequately trained and coached our individual employees."
The transformation process is still going on? Juraj Valent: "We are now in the final wave, the phase of autonomous main tenance. We also want to involve the op erators. We start with some simple main tenance actions for them, so that they also know what to do if they notice that something is wrong. They will be able to immediately put a request into the system and then the maintenance peo ple will come and fix it. But we are also pushing the operators into maintenance processing. Before, it was only done by our maintenance inspectors. Now we want to give the simple maintenance
— MARKO RENTKA Director of maintenance transformation, US Steel © Ing. Juraj Valent, Košice USSKE
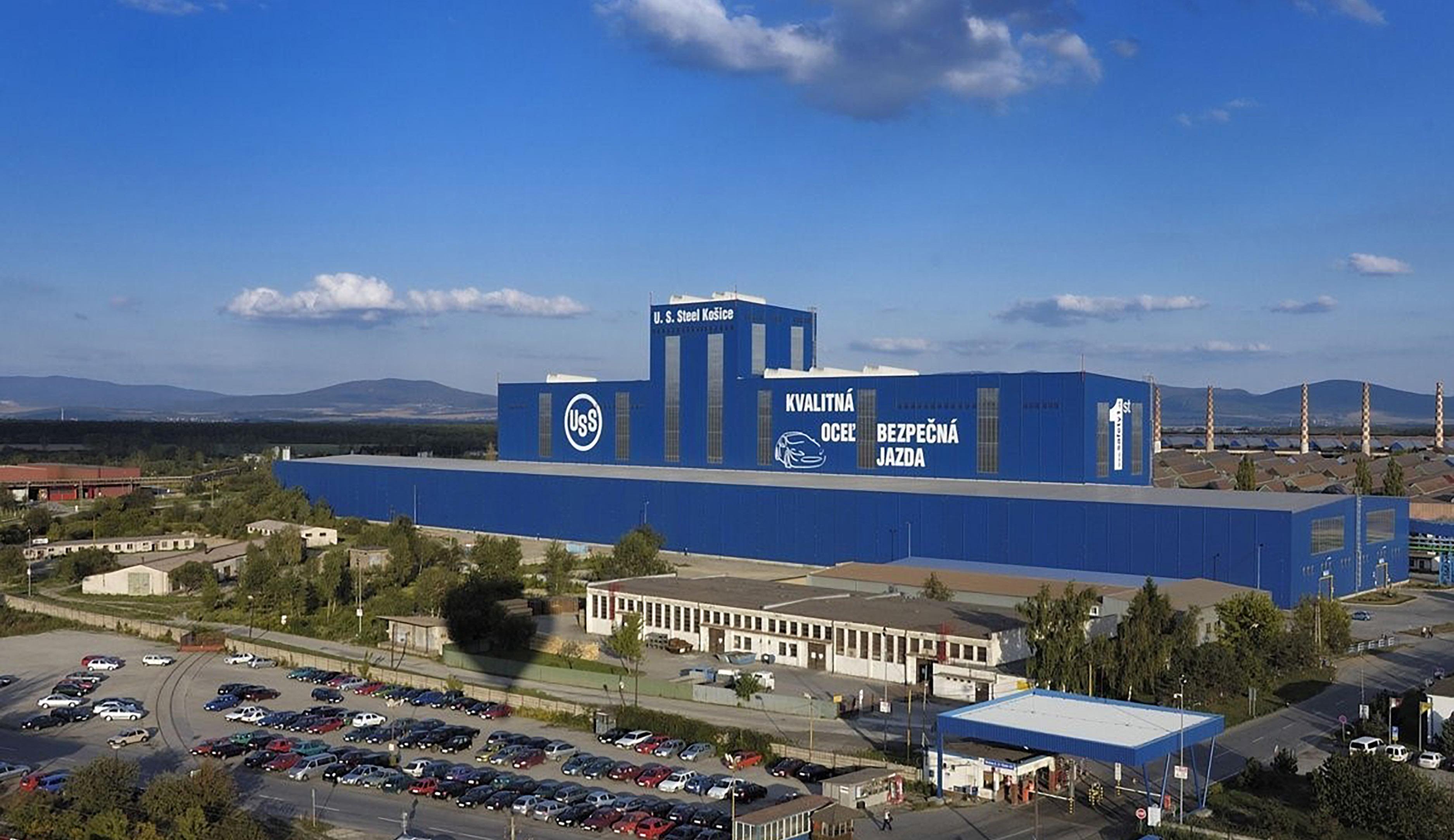
Juraj Valent: "I think the system was un derstood very quickly and correctly. The challenge was only to assess individual activities according to the classification into different categories such as produc tive time or lost time ... In other words, our formers (who measure WT) had to look with „the same eyes“ to be able to apply the correct criterion for judging what is a loss and what is an unproduc tive time. In that context, our team had training sessions where specific exam ples were shown and also the change agents of transformation, who coached the formers how to perform WT meas urements, directly participated in the measurements at the training sessions."
IN THE FIELD tasks (cleaning, greasing, simple re pairs, etc.) to the operators. The most important thing about this autonomous maintenance is not only that we can see the problems or failures in advance, but also that the operators can take care of it: they can notice that there is some thing wrong with our equipment, and if they repair it themselves they can still produce and have work. So the opera tors take care of the equipment. They no longer have to say: maintenance should do it." The complete organisation is involved? Juraj Valent: "Yes, it is good that we have strong management commitment and support. In the past, operators and maintenance had discussions, but now it’s like we are one team with the same goal. It is a great collaboration between operators and maintenance. Two years ago, in the first wave, we put sever al people in a new position: Operator Maintenance Coordination or OMC. That was really useful. These people were originally operators, but they grew to a 50/50 maintenance/operators profile.
What were the enlightening insights of the first wrench time analysis? Juraj Valent: "It is important to communi cate the process correctly, to explain its meaning and purpose, and to establish clear rules based on well-defined KPIs. Last but not least, it must be demon strated that the corrective actions are indeed addressed and implemented. We therefore held a large meeting with all employees, not only with line and divi sion management, but also with all peo ple from operations and maintenance. It was clearly explained how we would measure the success of this wrench time measurement."
All work requests for repairs go through them and they set priorities and decide whether something needs to be repaired or not. The cooperation between oper ations and maintenance has increased rapidly. We saw the results very quickly: after three or four months, equipment reliability and downtime had improved."
“ IN TODAY’S WORLD, EMPLOYEES ARE INCREASINGLY TAKING CORRECTIVE ACTION TO IMPROVE EFFECTIVENESS. THERE HAS ALSO BEEN A CULTURE CHANGE.
Marko Rentka: "The OMC coordinates maintenance activities on a daily basis.
Juraj Valent: "Like everywhere, when there is a change, there is resistance in the beginning. It helped a lot that the whole process, meaning and purpose of the WT measurements, were explained directly to all maintenance staff. The aim was not to control and punish people, but to identify where most problems were to be found and then eliminate them. Change agents played a major role in this process, as did management on the work floor, who followed the model and were supported by senior management.
However, a major change did not occur until individual employees saw that we were not just talking about the losses and what needed to be changed, but that something was actually being done about it and individual corrective action was being taken."
How did the maintenance people in the field perceive the project? Were there any objections and how did you deal with them?
— JURAJ VALENT Maintenance transformation manager, US Steel
8 | AP Magazine 2022
Marko Rentka: "It was also important to make the local management and main tenance people feel ownership and leadership within this project. Because without them it is not possible to change anything."
He is the person who tells the other workers what is important for the oper ation and what can wait. He also checks what budget is available for curative maintenance. So it is a very important position in the maintenance planning system." SAME EYES What were the biggest challenges in the transformation process?
Marko Rentka: "If we want to manage a process, it is also necessary to measure and evaluate it. We already mentioned things like setting rules and reporting with the participation of IT support, but the most important factor in the gradual increase of WT was the gradual adoption of measures and their implementation. This caused a change in people’s think ing, which gradually started to focus on the measures and address individual loss areas.
IN THE FIELD
IT support has also helped us a lot in the analysis of individual measurements, when it comes to determining the most loss-making areas. This has ensured that the main focus was on the areas that are the most problematic within the framework of the given areas and divi sions and even within the framework of the entire USSKE, so that measures that have a nationwide character can be ap plied to other operations and plants."
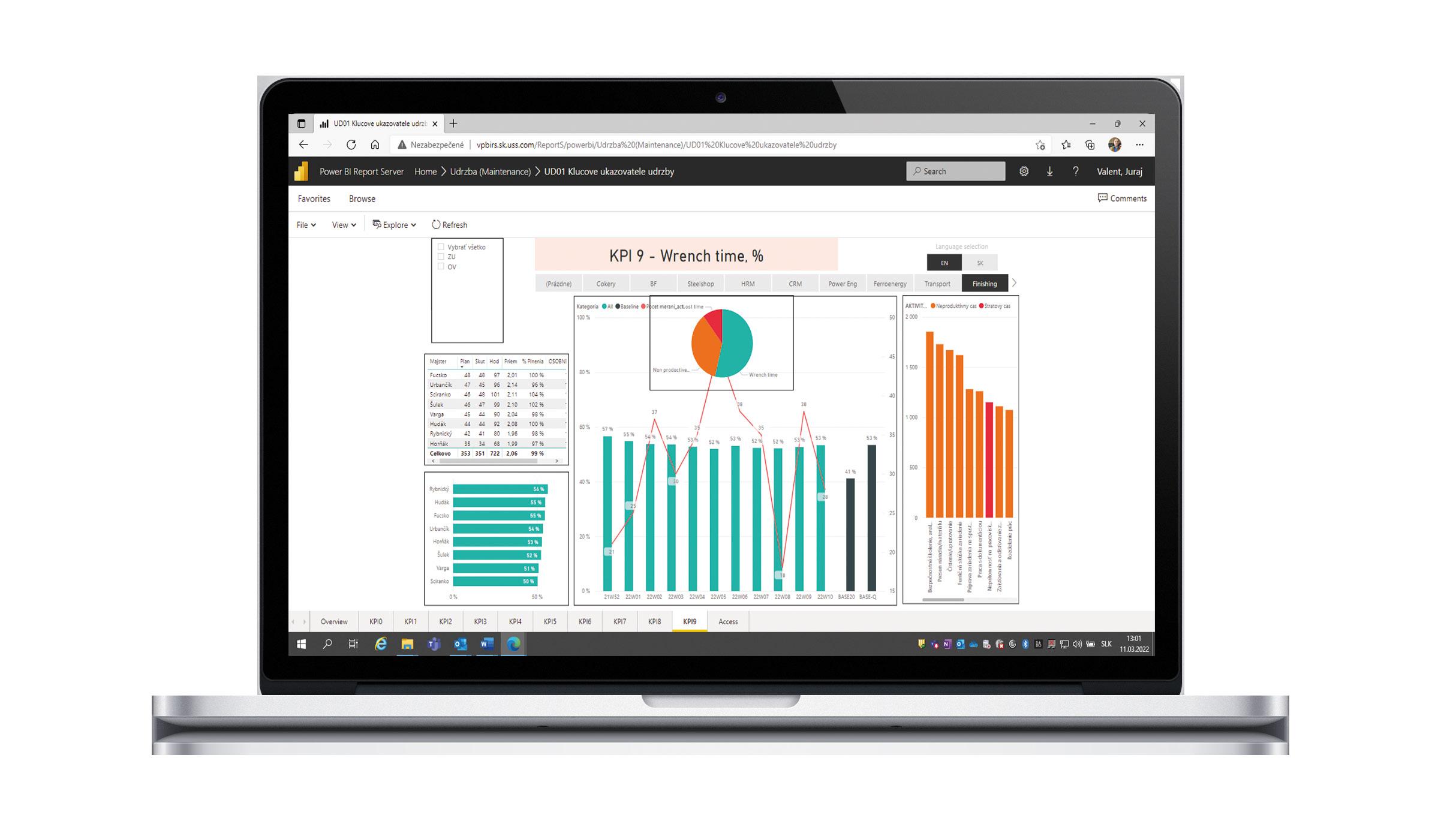
© Ing.
Košice USSKE 2022 AP Magazine | 9
Juraj Valent: "In the beginning, training on WT measurements took place and in dividual rules and KPIs were established for determining the measurements (i.e. how often and when to measure the WT and how long to measure it for). With the help of the IT department, information support was created for monitoring indi vidual measurements, together with an addressable reporting system. To speed up and simplify the entry of measure ments, we also created a mobile applica tion so that individual WT measurements could be recorded directly on mobile phones, thus eliminating the need for paperwork. This way we know what the most critical area is. Similarly, during the weekly meetings of a given operation, the most critical loss areas of individual measurements are discussed and evaluated, as well as the measures taken to eliminate them. The corrective measures are presented directly by the individual formers who performed the measurements. What is also important is that we created a rule book for this transformation, with the most important rules and procedures and also with some examples. And we created the KPIs: when you are at work (as a former or a line manager), you know which wrench time measurement you need to do. We reduced maintenance costs, the number of contractors and downtime. So the process has a huge impact that has saved a lot of money and increased labour productivity."
MOBILE APP
What were the main activities to be addressed in order to increase wrench time?
How did you manage to increase wrench time?
Juraj Valent: "Unambiguously from the beginning, the area of planning, work preparation and mutual communication was absolutely indispensable. Our com pany USSKE suffered great losses due to waiting for the equipment to be repaired (lock-out), with maintenance groups waiting until the equipment was insured, so that they could get to work safely. The same applies to the harmonisation and coordination of individual activities such as the provision of cranes, diagnostic measurements, transportation, clean ing, transfer of workers for repairs, etc.
All these activities could be said to have been adapted very quickly. Juraj Valent,
Later, the following measures to improve the unproductive time were applied.
IN THE FIELD
RIGHT PEOPLE IN THE RIGHT PLACE
First up was providing the necessary materials and spare parts for repairs, so that gearboxes and engines could be replaced more quickly. Secondly, new repair procedures were introduced, fo cusing on safety but also streamlining the work. And thirdly, work groups were equipped with new tools. These were mixed groups with electricians and me chanics, so that we did not have to wait for one or the other of them."
What were the main results and bene fits of the project?
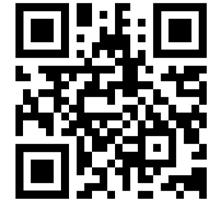
Juraj Valent: "I think most of them al ready agree with this idea and recognise that gradually eliminating problems and especially solving them will only help them to do their job both more safely and more efficiently. What is good is that in today’s world, employees are increas ingly taking corrective action to improve effectiveness. There has also been a cul ture However,change.there are still groups who think that maintenance is there to monitor and control them. Corrective action should come from the people on the floor, not from management. The first year was re ally difficult to persuade, but by coach ing the people, it worked. It is, however, a never ending story."
What do the employees at USSKE think about the project and the pro ject results today?
What would you recommend to oth er organisations if they start a WT project? Marko Rentka: "Just start, but allow enough time in the preparation phase so that people understand the purpose and meaning of measuring WT and realize that it will ultimately help them to per form maintenance activities more safe ly and efficiently. Of course, there must also be management support, especially in troubleshooting and in implementing the proposed corrective actions result ing from WT measurements. And make sure you have the right people in the right place, as is the case with our main tenance team. People are the most valuable asset in WT measurements. They need to un derstand what you expect of them. They need to know what the rules are. But in the end you have to walk the talk by showing the results." ■ WITH THANKS TO: Marko Rentka and Juraj Valent US Steel Košice, USSKE
© Ing. Juraj Valent, Košice USSKE
Marko Rentka: "The main benefits are the improvement of labour efficiency and productivity, the improvement of the WT from 30-35% to about 50-52%, the reduction of maintenance costs, but later also the integration of individual employees into maintenance repair pro cesses. This is also due to the increase in equipment reliability and the reduc tion in downtime (both planned and unplanned)."
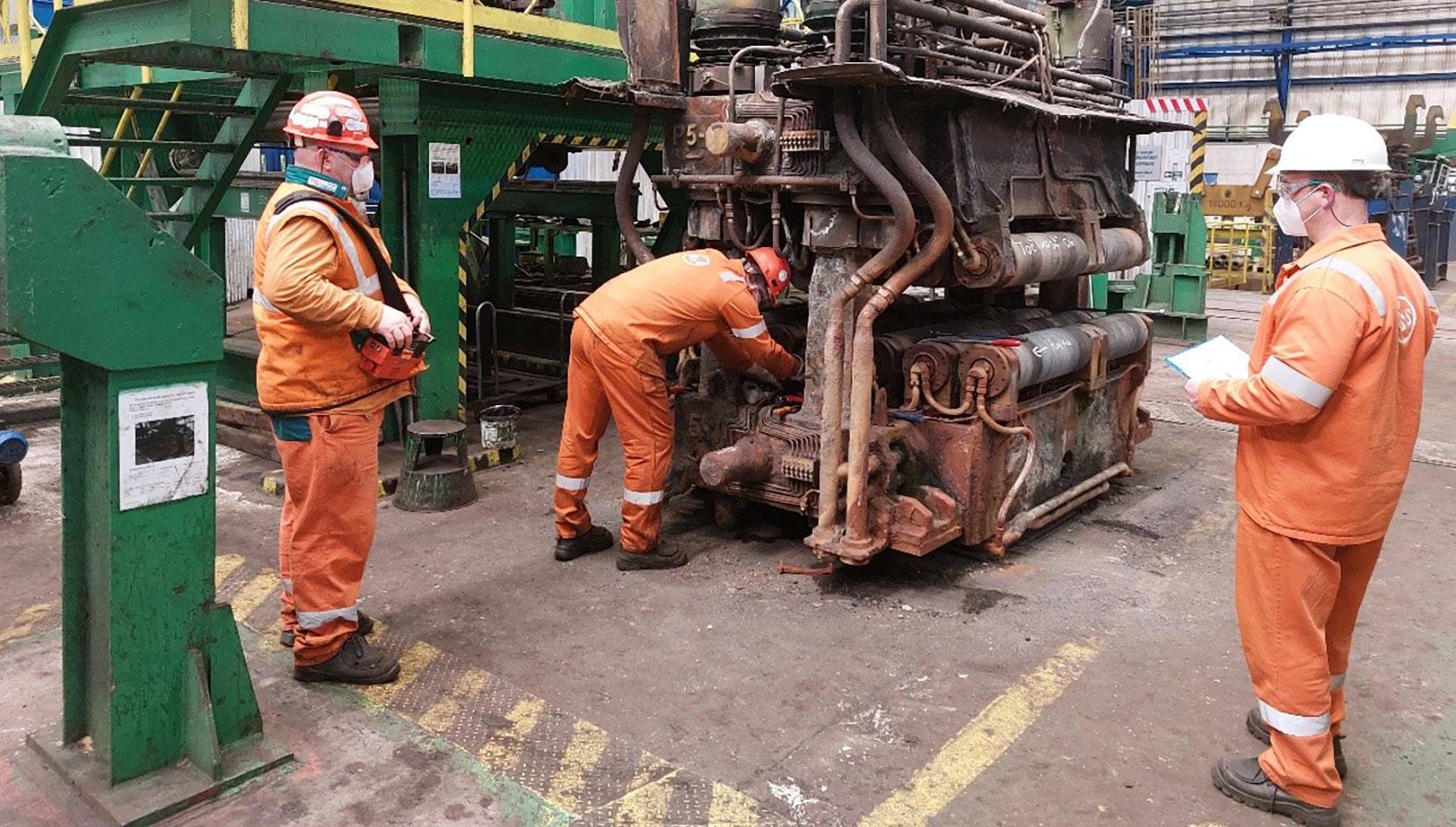
10 | AP Magazine 2022
Read on ap-magazine.eu: bit.ly/wrenchtime
IMPACT Approach SUCCESS Why & how CHANGE ABSORBING CHANGE
Companies are facing major challenges that require adjustments to the organization of maintenance. Implementing those changes requires special measures, such as appointing a Shadow Maintenance Manager. This ad interim manager leads the department through the change. This leads to more efficiency and makes work more pleasant for everyone, including new employees.
A NEW APPROACH TO SUPPORT CHANGE IN MAINTENANCE MANAGEMENT
© PDM 2022 AP Magazine | 11
ENDORSED INSIGHT EXPERTISE Skills & competences IndustryUtilizing4.0Accommodatinggrowth developmentsOtherRecruitingpersonnel
Companies need to switch to high er efficiency to achieve growth. Therefore, installations must run undisturbed – Overall Equipment Effectiveness (OEE) is a dominant per formance indicator. This means that shutdowns must be carefully prepared, that they are short, and that as much work as possible is then done. And it means that unplanned stops that lead to major loss of revenue are avoided. At the same time, there is a need to de ploy new technologies in the field of digitisation. Maintenance Managers also need to find enough qualified personnel. We see that many maintenance departments have an aging workforce. Rejuvenation is made difficult by the scarcity of welltrained personnel, while young people are not interested in a way of working that is no longer up-to-date. These developments necessitate changes in Maintenance Management.
DEFINING
Asset Management in a growing organi zation builds on data about critical assets, reliably and transparently. That data can only be used if the systems are properly set up – without that, digitisation remains at most a promise. To take performance management to a higher level, KPIs are de fined, which become available in a stand ard report. We see that figures that match their own living environment set people in motion. Absorbing change It is difficult enough in itself to trans late the blueprint for the new organ ization into a workable form, it is even more difficult to implement the change in an ongoing department. Absorbing the change adds to the high work pres sure that the department experiences anyway – it’s getting too much for many Ifpeople.changes are not implemented care fully and completely, people can easily revert to their old behavior. Then change is accompanied by frustration. And that frustration can lead to the departure of employees, making the workload for the remaining employees even higher than Ibefore.naddition, we see that many Maintenance Managers are unable to successfully implement the change in addition to their regular tasks for vari ous reasons. Therefore, it happens that they – voluntarily or otherwise – are (temporarily) given another position. This creates vacancies that are of ten difficult to fill in the middle of the change process. ARE NOT
General Work process
Organi-zatiSystemson Performance Manage-me nt General Performance Management Optimization Maintenance Work process Systems Organizations Sustainable change © PDM
It is important to have a clear idea of what goal you are aiming for. That is why we challenge companies to clearly indicate where the problems are, for example a staff shortage or an OEE that is too low. Next, the blueprint for the new maintenance or ganization can be created. The change fo cuses on five facets, namely work process es, organization, systems, performance management, and some general issues.
12 | AP Magazine 2022
Efficient maintenance starts with stand ardization of the work order process, where gatekeeping is an important mo ment, so that the right priorities are set.
IMPLEMENTED CAREFULLY
New approach to change
THEIRCANCOMPLETELY,ANDPEOPLEEASILYREVERTTOOLDBEHAVIOR.
A well-formed organization is the key to success. The roles of the employees in volved must be clearly defined, whereby it is important that all those involved retain their role. To increase people’s involve ment, they are made more self-directed.
We are a strong supporter of a new ap proach to achieve a successful change of the maintenance organization and we make a distinction between ‘defin ing change’ and ‘absorbing change’. It is one thing to set up a new organization and provide the resources for it. Another thing is the acceptance of that change by the employees involved. Defining change
ENDORSED INSIGHT
“ IF CHANGES
Optimization maintenance
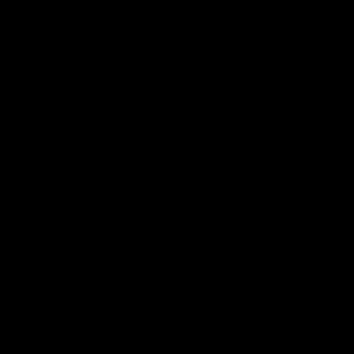
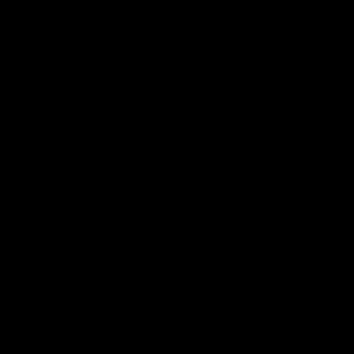
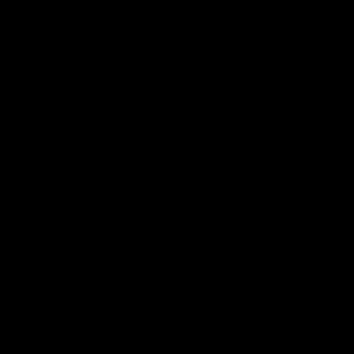
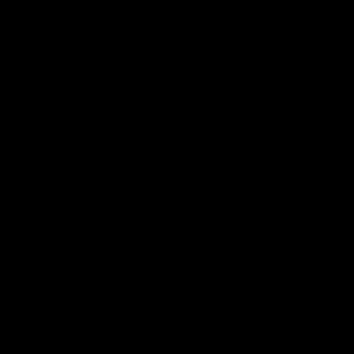
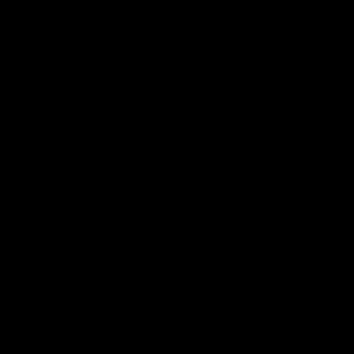
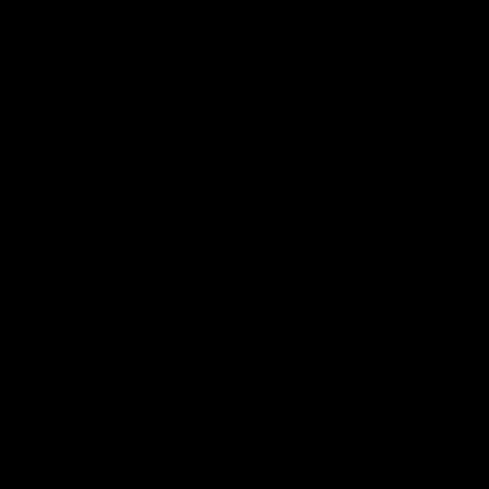
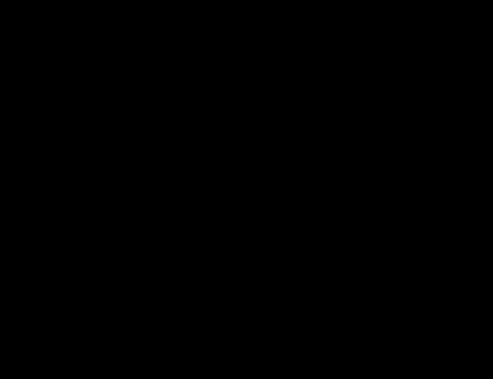
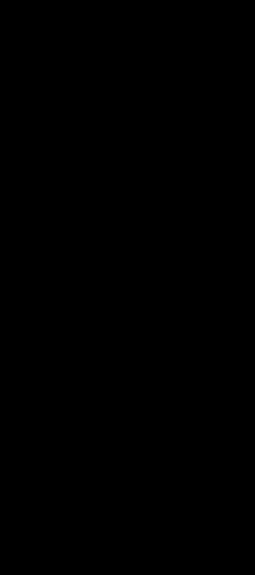
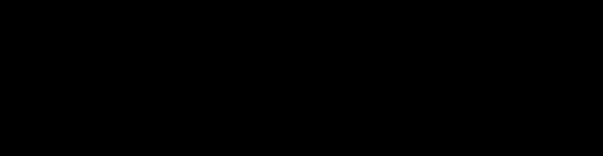
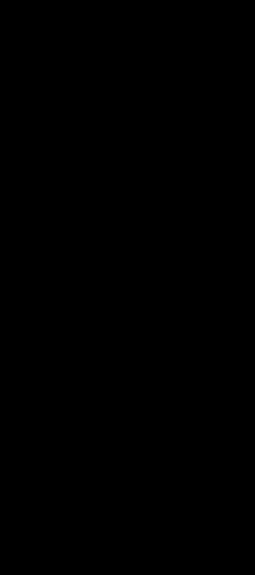
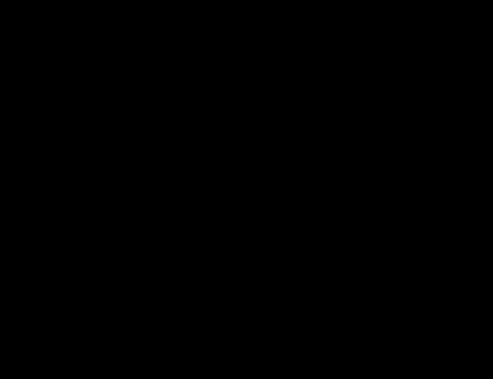
And you don’t necessarily have to per form a Hands on Tool Time measure ment to have a good idea of what the obstacles are to working efficiently.
The ad interim and the Maintenance Manager can work together, as there is usually enough work to divide tasks among themselves.
The ad interim has the mandate to also bring about changes that are not fore seen in the blueprint. As long as those changes contribute to achieving the objective, he can provide added value before that blueprint is ready. He can encourage people to check if things that were always good are still good.
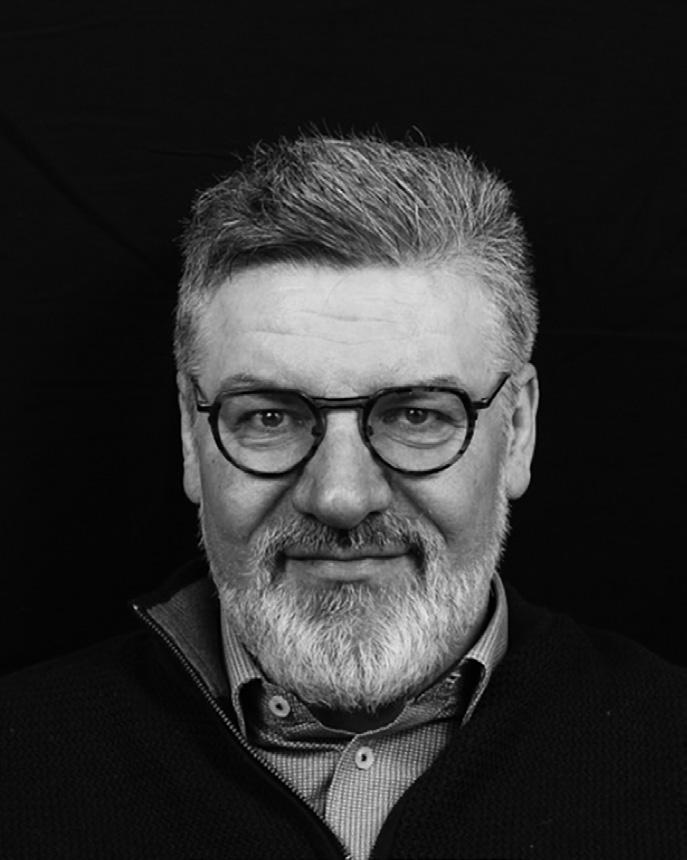
We see that in many companies there are problems with the cooperation between Maintenance and other de partments, Production, Reliability, and Engineering. These departments often assume conflicting interests and do not understand each other well. As a result, the work is not always efficient, effec tive, uniform, and transparent. It is up to the Shadow Maintenance Manager to restore the connections between those departments, and that starts with minor issues. It is important that the ad interim is fully integrated into the organization, so that he can clearly see where those small issues are. Talking to the depart ments makes it clear what everyone’s contribution is to the whole. In this way the mutual relationships become clear. After all, there are no opposing inter ests, only a common interest.
Implementing change requires leader ship and this can be performed by an experienced ad interim manager from outside the organization. He temporari ly replaces or supports the Maintenance Manager, or temporarily fills a vacancy.
A minimal implementation is as a sparring partner for the Maintenance Manager, someone who can ask crit ical questions to find out where there are blockages and where you can im prove. It must be a fully-fledged dis cussion partner who comes up with relevant solutions. Keep in mind that a Maintenance Manager rarely has some one to spar with.
The success of the Shadow Maintenance Manager lies in the focus on people. It often turns out that there is a great dis tance between the Human Resources department and the other departments, ABOUT CONNECTIONS.RESTORING
The manager sees how the people in the department act and gradually he lets them work according to the new methods. He gives people who are ready for it more independence, so that they act proactively, without drowning in their new responsibilities.
“ IT IS
© PDM CARLO SCHILDERMANS Account Director, PDM 2022 AP Magazine | 13
Restoring connections
ENDORSED INSIGHT
The ad interim manager is someone who thrives in a changing environment. He is able to recognize and break through existing patterns in an organization. His main task is to ensure that people ab sorb the change, that they accept new things, say goodbye to old things, and that they actually start working (togeth er) in a new way, so that the change is successfully implemented. Shadow Maintenance Management In the most extensive form, the ad in terim acts as Shadow Maintenance Manager, who is responsible for the day-to-day running of the department and for implementing the change. It is not necessary that this person was in volved in defining the change, this may already have been done by the compa ny itself, by fellow experts of the interim manager, or by a third party. What mat ters is that he knows how to translate the change into daily practice. Managing the department and imple menting the change go hand in hand.
In addition to the ideas from the blue print, the Shadow Maintenance Manager uses various methods and techniques.
ENDORSED INSIGHT
The Shadow Maintenance Manager can be assisted. Managers, for example, can benefit greatly from a coach from out side their own organization, especially if the manager involved has not been in office that long. An additional team of experts can be deployed to solve a spe cific problem, such as eliminating back logs as a result of old, incorrect work processes. ■ WITH THANKS TO: Klaas TechnicalBos,Writer, PDM
IVAN AERTS Business Leader, PDM aftercare. This can take the form of an audit, in which it is checked whether everything is running according to the set-up and whether everything that may have changed afterwards is prop erly secured in the organization. This aftercare is part of the partnership be tween the company and the ad interim.
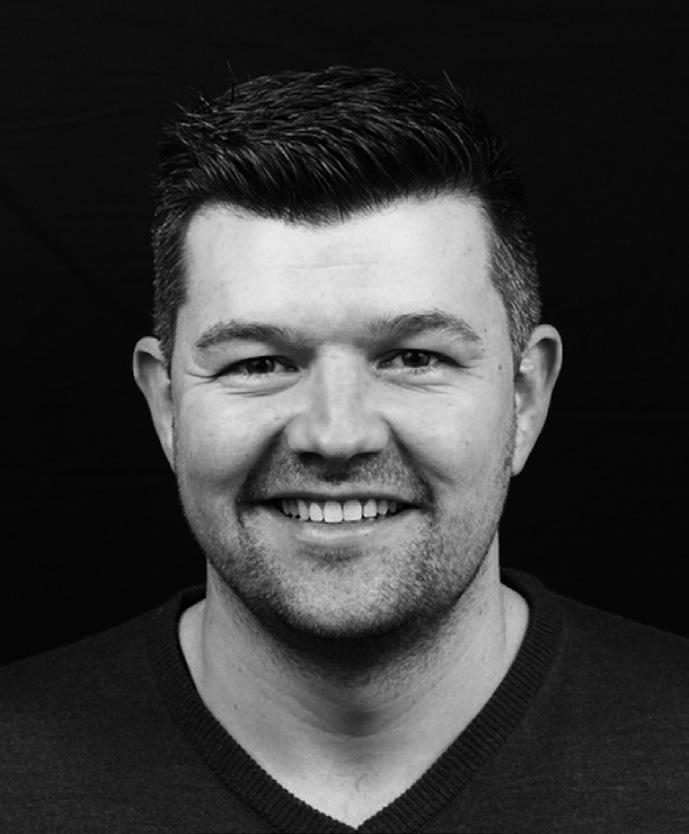
THE SUCCESS OF THE SHADOW MAINTENANCE MANAGER LIES IN THE FOCUS ON PEOPLE.
Because the ad interim lowers or re moves barriers, a pleasant working en vironment is created, which is also in teresting for new employees. Although the focus is on the existing workforce, the ad interim manager can play an ac tive role in recruiting personnel by defin ing vacancies and selecting candidates.
Read on eu:ap-magazine. ow-maintenancebit.ly/shad
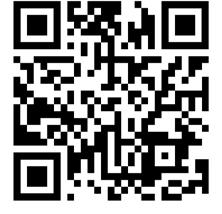
including Maintenance. The ad interim can ensure that the distance between HR and managers is reduced and that HR rules and procedures are properly linked to the workplace. He can then ensure that proper assessment inter views are conducted, that the training budget is spent wisely, and that people can work more independently.
AUTHORS: Carlo BusinessIvanAccountSchildermans,Director,PDMAerts,Leader,PDM © PDM
The Shadow Maintenance Manager develops speed in implementing the change, after which he carefully hands over the tasks to his successor. The ad interim will then remain available for “
14 | AP Magazine 2022
Maintenance and traditional operations are a way in which you can execute a part of those desired and defined mit igation actions based on the relevant strategy.
All of them have to eventually become part of one strategy, so that each dif ferent team, from their own angle, can take the necessary actions to mitigate risks.
• Integrity and inspection departments managing fixed assets from strate gy definition to inspection execution for risk management and compliance with local regulations.
The definition of Asset Performance Management Gartner[1], a technological research and consulting firm, has introduced this term some 20 years ago as “the capabilities of data capture, integration, visualization and analytics tied together for the ex plicit purpose of improving the reliability and availability of physical assets”.
2022 AP Magazine | 15
For example, a critical compression system contains assets from all class es: static, rotating, electrical, safety…
WHAT IS IT AND WHY DOES IT MATTER?
© GE Digital [1] Https://www.gartner.com/en/information-technology/glossary/asset-performance-management-apm
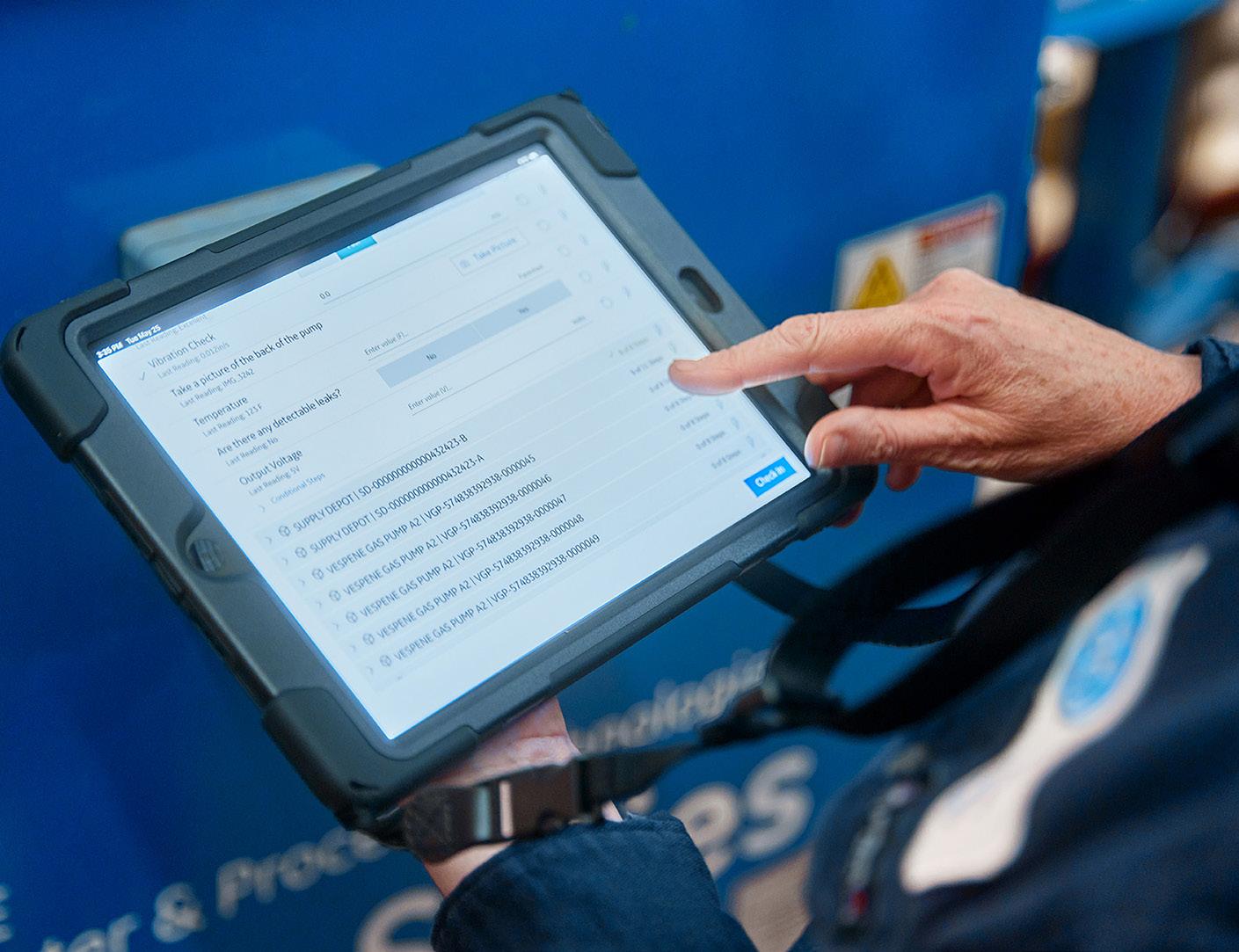
We define Asset Performance Management as the ecosystem of re quired work processes focused on taking care of our assets. They should be inte grated together in order to deliver the relevant requirements for the business in terms of the asset performance. The difference with maintenance Maintenance itself is a way to execute an asset strategy. Asset Performance Management is a set of work processes focused on designing and evergreen ing the risk-based, cost-effective as set strategy. When we talk about these processes, we also consider the prima ry and secondary functions of the as set. What are the associated risks with this function? What do we need to do to mitigate those risks? That is why we need cross-functional teams and de partments to take care of the asset.
ASSET PERFORMANCE MANAGEMENT
THE ESSENCE OF
• Reliability departments managing the strategy portion for rotating and elec trical equipment, having the mainte nance department as its execution arm.
• Instrumentation departments man aging strategies and execution along with maintenance for instruments calibration and Safety Instrumented Systems proof-tests.
APM is strategy and asset centric.
Asset Performance Management comes from the need to integrate multiple work processes, which have been historical ly defined based on equipment classes and the different departments which are present in an asset owner/operator organization:
The definition of Asset Performance Asset Performance is a measure of the assets capability to perform each required function. In short, it is what the business owner wants the asset to do in a safe and of course in a reliable way. So, the word “performance” may take different shapes depending on what the particular requirements of the operator or asset owner are. The criteria of success are typically related to the di mensions of risk management and cost optimization, and of course to the ability to meet the desired production levels.
You will get answers to: Did I mitigate the risks that I thought of before? Did RUNNING ASSET INTENSIVE OPERATIONS WITHOUT
16 | AP Magazine 2022
2. Based on this framework you can identify which assets are highly critical and understand which risks are not tolerated by the organisa tion's business goals. That is what helps you identify which assets are your bad actors or troublemakers. 3. Then you need to define what the relative risk mitigation strategy should be. To answer this question, you employ different methodologies: 1. Risk based inspections for static assets 2. Failure modes and effects analysis for components 3. Reliability-centered maintenance for more complex systems All these methodologies effective ly depend on the asset function. You can ask yourself: How can the asset still perform its function? In what way is this going to be important for us? What are the consequences of each function fading? This will naturally bring you to thinking about the nec essary risk mitigation tasks, actions or recommendations.
THE ESSENCE OF “
INCARBONISFUNCTIONALEXPERIENCINGFAILURESKEYTOKEEPINGEMISSIONSCHECK.
Or maybe you want to deploy more enhanced tools like predictive di agnostics that reassess the assets behavioral patterns, raise the alerts based on those particular deviations and create recommendations. Maybe you even make the decision to do no scheduled maintenance at all for the assets that are low risk and do not have high-cost failures. Maybe the strategy would be to do no invest ment of any maintenance in those as sets. All that is in your execution plan.
There is also a distinctive type of predominantly critical asset that has a safety function. For example safe ty-instrumentation systems for in strumentational loops designed to shut down the operation when things go wrong and guarantee that it can be done in a safe way. That is also a different methodology that looks at a different type of these particular assets. 4. The next phase is the execution. Here, you might want to consider strategies and actions that will miti gate the risks, including routine pre ventive maintenance. Examples are: Visual inspections, which are opera tion driven, non-destructive testing of static assets, proof testing for safety systems, calibrating of your sensors, monitoring your assets condition with the help of Predictive Analytics, or Health Management, or by field data collection by operators. 5. Then you need to identify which corrective actions you need to take.
In a world which is becoming more aware of the effects of global warming and the importance of becoming carbon neu tral, running asset intensive operations without experiencing functional failures is key to keeping carbon emissions in check. The building blocks of Asset Performance Management If we break Asset Performance Management into the following steps, we get: 1. First of all, you need to under stand which assets you have in the organization. Which categories, classes and tech niques are currently being engaged to manage them? The common frame work to understand which assets you have is to understand how critical they are for a given operation. This means understanding what risks they poten tially can possess, ranging from envi ronment, health and safety to impact operations and budgets.
Imagine if it is not just one critical com pression system but an installation that has hundreds of different asset types, of different criticality criteria, differ ent functions… and all of them need to align with one reliability and strategy goal for the company. Managing all of this together - from risks over mitigation to selecting the relevant maintenance strategy standpoint - that is asset per formance management. The importance of Asset Performance Management Managing industrial assets is an impor tant part of strategy and day-to-day operations for corporations as they pur sue asset availability in order to increase production throughput and increase revenue, improve reliability to reduce environment and safety risks, and pre vent costly failures that drain the main tenance budget.
6. Once you execute this strategy based on all different methodolo gies that you have utilized and put together, you will have valuable insights to see how you have done so far and what else needs to be improved.
Elements like Root Cause Analysis, statistical analysis and reliability dis tributions… can help you answer the question: What else did we miss?
THE ESSENCE OF © GE Digital 2022 AP Magazine | 17
• Strategic Improvement describes an organization whose performance measures are regularly reviewed and improved, the vision is compel ling and drives people to action, and decisions are strongly influenced by business objectives.
I really address my “bad actors”? If I did, let us repeat and reuse this suc cess for other assets. If I did not, what did I miss?
Defining a strategy should be an ev ergreen process as part of the con tinuous improvement cycle. In short, the workflow can be divided into sev eral pillars. At GE Digital, these APM solutions are called Health, Strategy, Integrity, Reliability and Safety. What are the different levels of maturity in APM? In GE Digital’s experience in design ing APM solutions and developing APM roadmaps, we have been using the following four categories of ma turity as a starting point for their APM journey: Reactive Inefficiency is typically when a company is responding to immediate conditions and does not really have a vision so they are not measuring their results in a consist ent manner.
• Managed Control is when the vi sion exists and is communicated, performance measures are estab lished and consistent and process KPI’s drive decisions.
• Reliability Driven is simply put, world class. This is where per formance results are world class benchmarks, vision is copied by competitors and APM decisions are drivenby Value Gain and maximum sustainable Return on Assets.

Our assets are talking, and we need to lis ten to them. The amount of sensor data, industrial benchmarks and other content that you have available give you a rich world of data. Sensors on the assets are capable of giving you a rich signal every split second.
But the real question is: what do you want to do with all that data? In order to answer this question, we need a view of how the data can be valuable for us. We need to see the methodology, levels and tools of how we can actually process this data with the relevant decision making, math ematical algorithms, and policies that can make sense out of all the data. If humans would study this data full-time for a year, we would not be able to process even a quarter of it. So having a solution that is able to plug into these data sources, Which tools are available on the road to Asset Performance Management? Most organizations already have the basic tools available in place: condition moni toring solutions, vibration sensors, SCADA systems and data storing solutions. The next important step is to have an APM solution that connects all these different tools together and enable the multi-an gle view on data and support the relative Strategy, Integrity, Failure Elimination and Health processes.
The Internet of Things makes data more available: sensor data, composed data, machine learning, artificial intelligence… How does data change the process and the APM cycle?
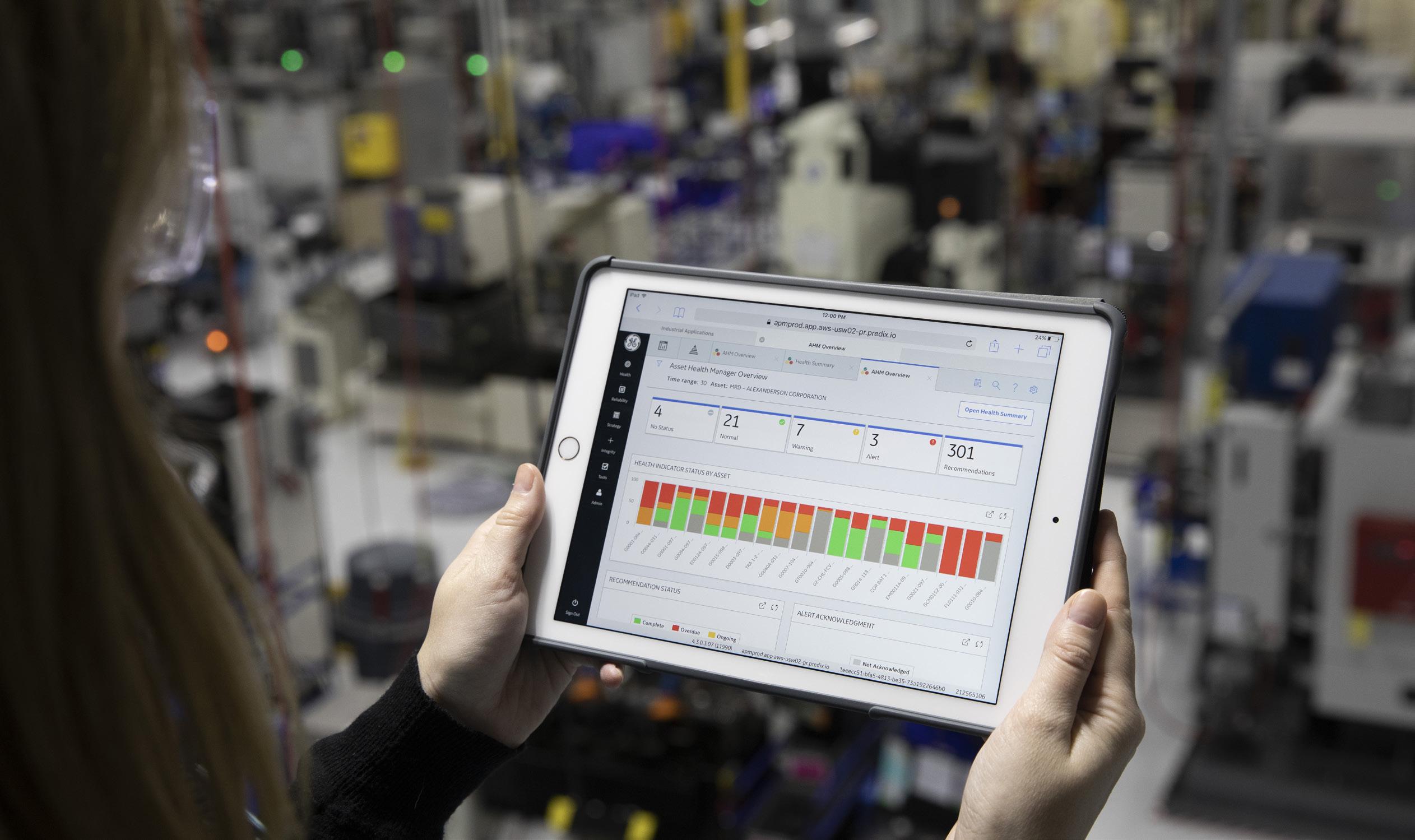
The most important requirement for an effective APM tool is to make sure that the tool is an ecosystem that can scale to the size of the organization and seamlessly integrate with third party solutions.
For example: You want to build an effec tive risk-based strategy for a complex system. Your software tool really should be able to use the historical data, condi tion data and maintenance history data at the same time. It should also be able to link all of the potential failures to risks and then highlight what will be the return on investments on the given strategy. Does it make sense to take particular mitigat ing actions? Are they going to pay back if I change my strategy or do something differently? Is it going to be worth it for an organization? Is it going to reduce the risks and help us get the ROI from these particular activities? Think about your cost and expenditure in the long term, which will be associated with the strategy and then of course, once you identify the relevant way, your tool should be able to implement the recommended risk mitiga tion strategies directly to all the relevant parties for that execution. In another example, for Mechanical Integrity, advanced APM tools are capa ble of utilizing CMMS data in conjunction with Risk Matrix to support API-compliant Risk Based Inspection (RBI) studies and prioritize the inspections, followed by full inspection management, scheduling, mo bile execution and reporting capabilities in order to conduct thickness calculations, remaining useful life calculations and managing Integrity Operating Windows. These activities are typically deployed in seamless integration with CMMS. OUR ASSETS ARE TALKING AND WE NEED TO LISTEN TO THEM.
“
© GE Digital 18 | AP Magazine 2022
For example, you set the goal that you want to improve your availability by two percent by the end of 2023. That will translate into five to seven million dol lars of additional revenue for the compa ny. That is a target that you can bench mark, you can track your progress and constantly reflect on it even after 2023. Do you still want to maintain that? Is the change sustainable? Whatever change you make, you want to make sure it is a sustainable one. Once the target is set, you need to deter mine the steps you need to take. Know that there are many different ways to achieve that target: training, methodol ogy, sensors, RCM… But how do you de cide? Assess the areas requiring improve ment by doing a gap analysis, followed by a change readiness assessment. This way, you determine the maturity in each process, function by function. You un derstand what the gap and deviation is, what potentially could be improved and how ready the team is to actually make a change. That will result in prioritizing and sequencing the activities in a multiple months/years journey. You are essentially building the asset performance manage ment role model.
The key role of Asset Performance Management in sustainability By making assets more reliable, you minimize and optimize the carbon out put. We know we cannot go straight to wind, solar and other renewable ener gy sources immediately. That is where APM will play a key role: in helping in dustrial companies get to a lower car bon emission, especially during this hybrid time where we continue to use a lot of the expensive assets that have already been put in place. We are not going to strand all these very expen sive assets, we are going to continue to use them for a period of time.
2022 AP Magazine | 19
IT IS NOT JUST TECHNOLOGY, IT IS ALSO PEOPLE AND PROCESSES. “ centralize the data and then make sense out of it, that is how the digital trans formation angles to asset performance management.
Making sense out of data is in fact vis ualizing the risks, the business impact of these risks and then allowing you to mitigate these risks and take necessary actions. Visualizing the risks and the current asset condition is the first goal. But the industry needs to think a few steps further: not only to see what risks the assets are currently exposed to but also to have that in conjunction with the historical data to understand if the be havior of the asset is normal. Has some thing changed? And what do we need to change in the future? Not only to react to the deviation right now but to prevent the deviation from coming up again in one or more years from now. Data can give you that strategic edge. The tools that can process this data, is the output we would expect from these solutions.
What would you recommend to organ izations that want to start with asset performance? Every organization should start by know ing what they need to do and why they want to do it. Then you need to know the steps you need to take.
Many organizations that are starting on the APM journey, start because “every one else is doing it”. This attitude does not lead to the right results.
THE ESSENCE OF
There are many use cases, for example about optimizing operational emissions, monetizing carbon reduction and optimiz ing inventory effort. All of these require data collection, auditing of that data and operationalizing that data in individu al plants, across plants and ultimately in enterprises. It is not just about the adaptation of new, lower emitting equipment. It is a much larger information and optimization game.
So APM, at its core really, is an expert in dustrial management system. It encap sulates many years of subject matter ex pertise in power generation, oil and gas, mining, aviation, and other asset-intensive industries For example, templates and blueprints are especially important in a world where we see a lot of subject matter experts exit companies and take that experience with them. At GE, there are millions of peo ple-years in experience. They have taken that experience and put it in digital twin systems. There are also algorithms, visuali zations and optimization for reliability. That has a very positive effect on decarboniza tion based upon these million person hours of experience.
mining perspective: extracting re sources out of the ground or somewhere else. It is in that way that APM has the foundational information in computational elements that can be leveraged to optimize emissions and lower the overall carbon footprint today. Not tomorrow, but today, during this hybrid time.
YEREM DAVTYAN Regional Manager – Solution Architecture, GE Digital WITH THANKS TO: Yerem Davtyan, Senior Manager Digital Solution Architecture EMEA/APAC, GE SeniorWarrenDigitalRoss,Director Product Management, APM Product Center, GE Digital.
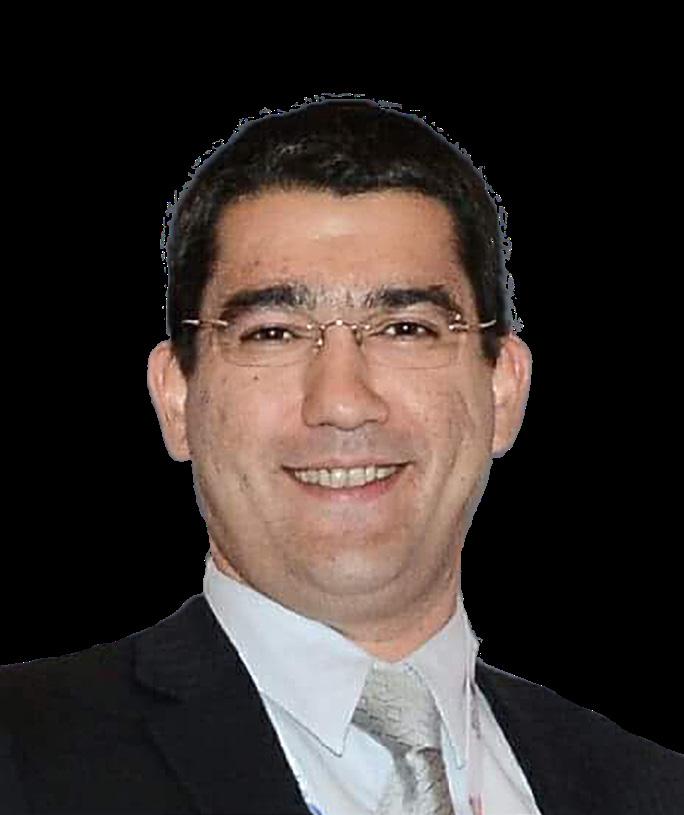
If you look out over the horizon, at the future of APM, it includes something called OPM, or Operations Performance Management. OPM is about optimizing the performance of your systems, including digital twins based on physics, artificial intelligence, computer vi sioning and sensoring, dynamic optimization, algorithms and data science, and better hu man-to-machine interface and experience… When you bring in new workers they can easi ly come up to speed and utilize the processes that you have put in place. It is not just technology, it is also people and processes. By bringing together these three elements, you can not only achieve a very good APM system, you can also reduce car bon emissions. Ultimately, an APM and de carbonization expert system leads to an im plementation of an autonomous plant which will be able to sense conditions and change to optimize energy resource needs while ab solutely minimizing, if not eliminating carbon emissions. By optimizing a plant, you can optimize not just reliability but also your carbon footprint and emissions today. It is all about hitting this golden badge again and again. ■ This article was created with the cooperation of GE Digital.
Read full article on ap-magazine.eu: bit.ly/apm-essence
© GE Digital © GE Digital WARREN ROSS Senior Director Product Management,GEDigital
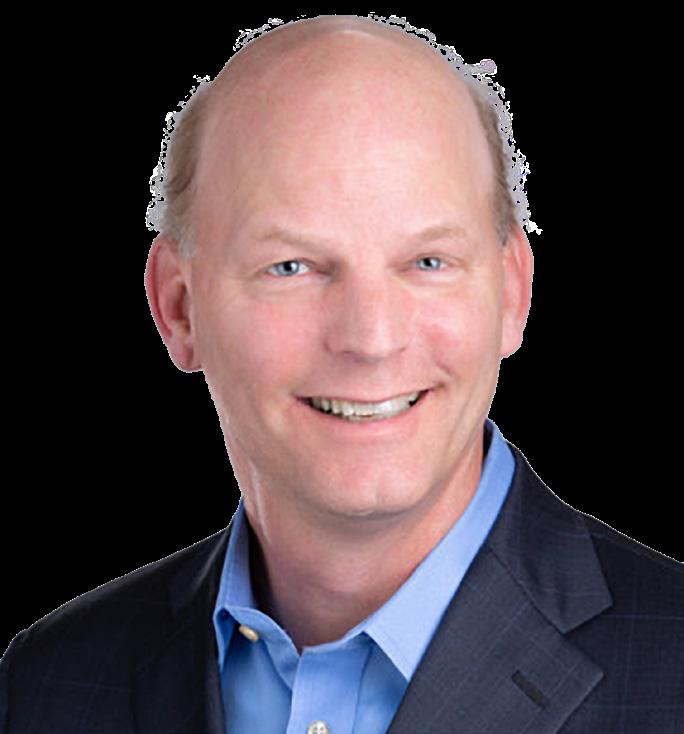
APM and OPM
THE ESSENCE OF
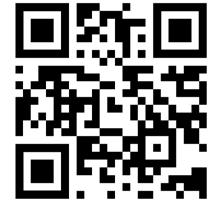
When you make industrial assets more reli able, you also optimize them for carbon. For example, the air fuel mixture of an engine. By measuring exactly and precisely the amount that is needed at a point in time relative to conditions, you are able to extract not just more energy out of them but also optimize and minimize carbon emissions. We already do that in cars today. And it is not just a me tering of the prime mover, the engine itself, but it is also the balance of plant, all the oth er assets that are really contributing to that prime mover putting out electricity, extracting Fromenergy…a
20 | AP Magazine 2022
What is the deal here? The added value of professional work preparation and planning is often still misunderstood. Some people are convinced that only the technician can do the preparation himself. Others think that we are going to impoverish the job of a technician if all he does is tinker. Here the compari son with a surgeon in an operating room comes to mind. Do we ask the surgeon to prepare all the tools by him- of her self? Does he or she prepare the patient and, when the operation is over, clean the operating room afterwards? I admit that the technician’s tasks versus those of a surgeon are a mile apart, but still there are comparisons to be made. A surgeon has to diagnose, operate and monitor the healing. He or she is most of the time relieved of all other tasks. You could say the surgeon is taking care of a special kind of asset: the human body. The technician on the other hand, is taking care of other complicated assets. Their focus must be on the correct tech nical analysis, the implementation of the preventive or corrective actions and the associated aftercare. Shouldn’t he or she be relieved of all other tasks?
Blue Boxing
SHOULD WE TREAT OUR TECHNICIANS LIKE SURGEONS?
Other than the obvious benefits of ensuring a smoothly-running plant and achieving higher revenue and profitability, asset performance management (APM) offers solutions for a changing world and a future in flux.
In practice about thirty to fifty percent of a technician’s time is lost on tasks that have no added value or that could be performed by non (or less) technical ly trained personnel. This varies from ar ranging the right spare parts, preparing the necessary tools, waiting for permits, collecting and guiding external contrac tors, obtaining the appropriate Personal Protective Equipment and performing tasks in pairs or threesomes when this is not really necessary.
A surgeons task
“ THE CONCEPT OF ‘BLUE BOXING’ OR ‘KITTING’ CONSISTS OF PREPARING CONTAINERS FOR ALL OUTTHATMAINTENANCEPLANNABLETASKSWILLBECARRIEDINTHECOMING PERIOD. — PETER DECAIGNY Partner & Consultant, Mainnovation HOW THE CONCEPT OF ‘BLUE BOXING’ CAN HELP US OUT © Mainnovation 2022 AP Magazine | 21
The concept of ‘Blue Boxing’ or ‘kitting’ consists of preparing containers for all plannable maintenance tasks that will
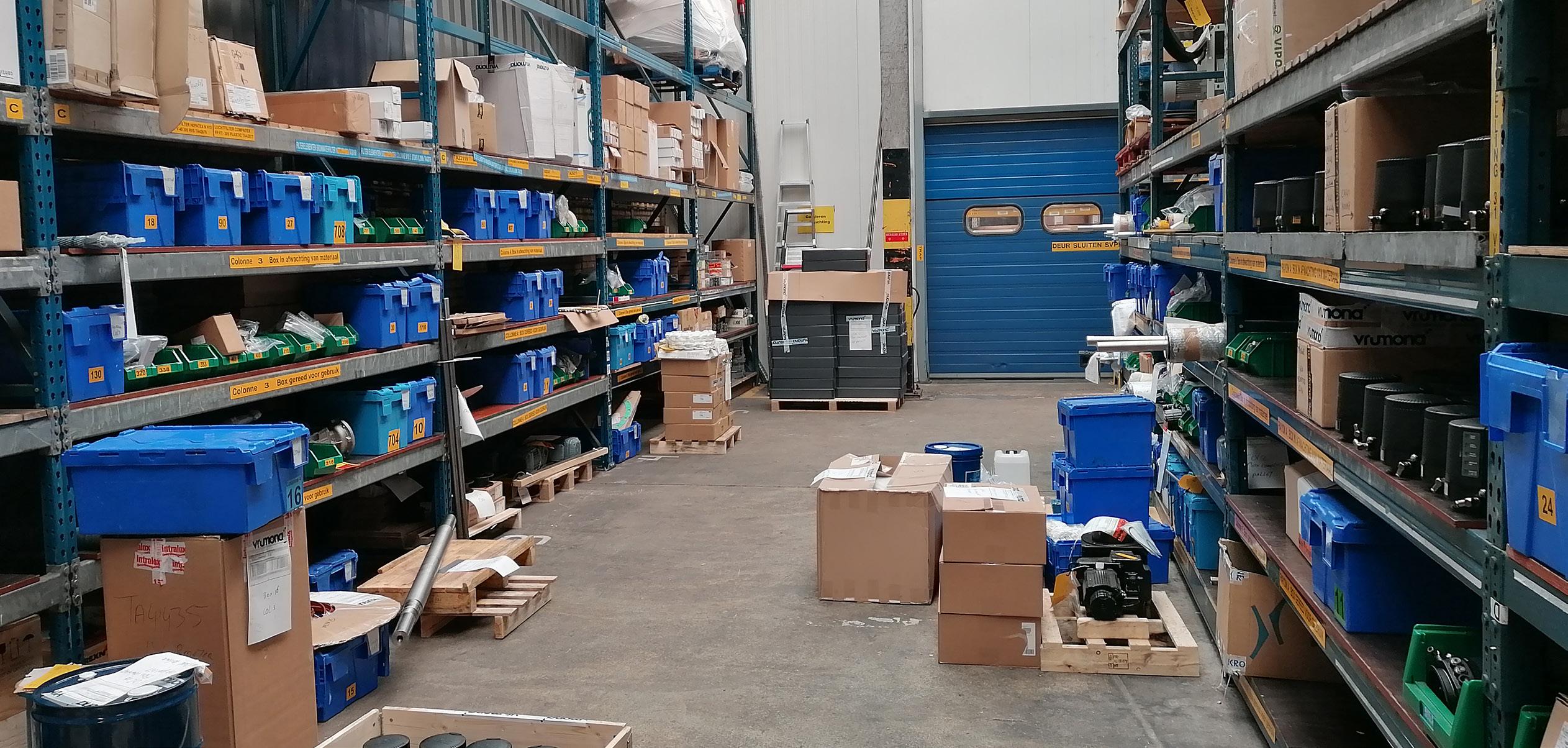
We can also prepare specific tools that are not part of the standard equipment of every technician in a separate box.
This way of working also offers a chance for ‘opportunity maintenance’. What is it? Imagine we’ve prepared the boxes for a scheduled stop next week. A few days before the stop, there suddenly © Mainnovation
The boxes can be filled by the ware house manager, the work preparer or by supporting staff. This can be exe cuted during the ‘cheaper’ hours of the day or this might be a smart way to use eventual idle time. For larger jobs and accompanying pieces, you can opt for palettes, but the concept remains the same. When all boxes or palettes are filled, a final check for completeness can take place and everything is ready for executing the engineering task. In this way, the technicians can take the box that corresponds to their assign ment at the start of their shift and get to work immediately.
be carried out in the coming period. These bins contain the spare parts, the work order, the adjustment instruction, the assembly sequence, the risk analy sis and all other necessary agreements.
Opportunity maintenance
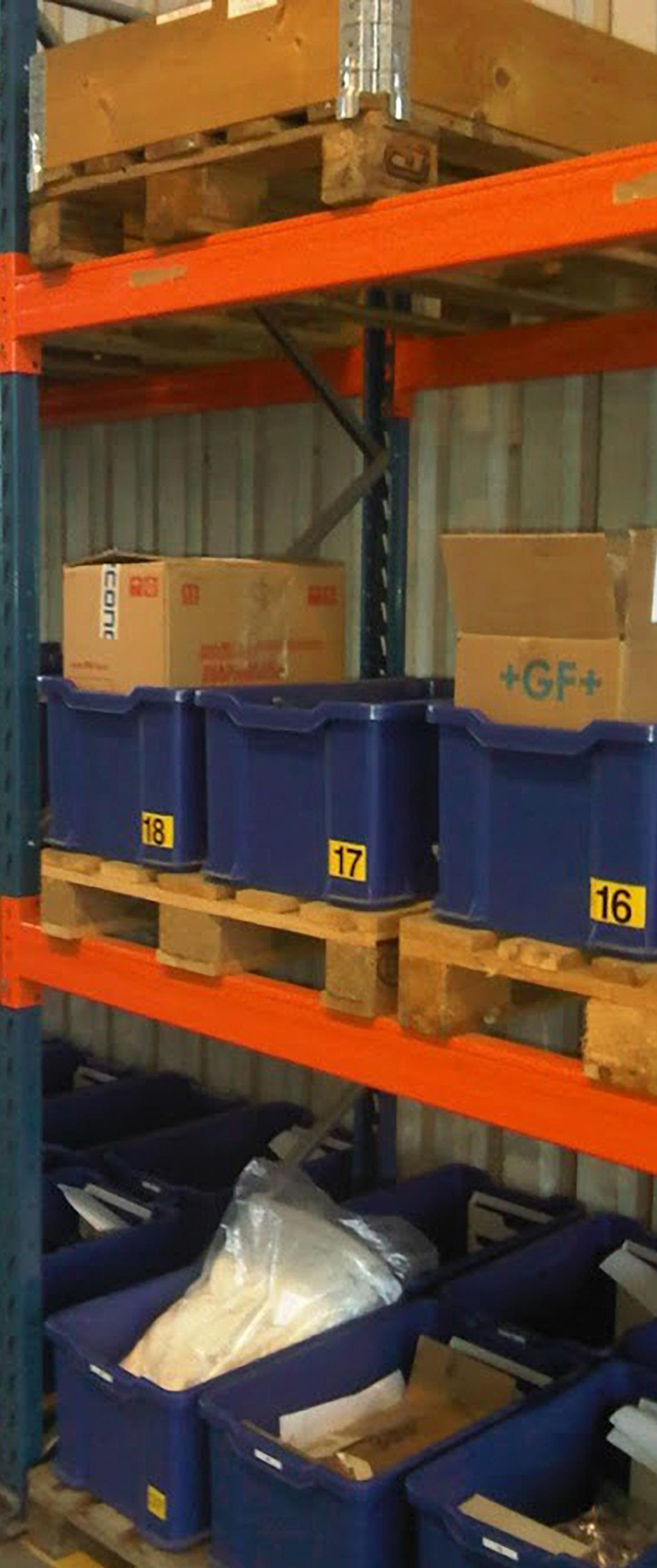
ENDORSED INSIGHT is a logistical problem with the supply of a crucial raw material. The logistics department is doing everything it can to speed up the delivery, but is already saying that we will be idle in a certain department for at least four hours. At that moment we can immediately make use of this opportunity and start performing a number of maintenance tasks with a lead time of less than four hours. All boxes are ready and everyone can get started in a very short term. In this way we can usefully fill in the loss time, due to the logistics problem and we may be able to shorten or cancel the next planned stop for this department. By being maximally prepared, we can use these opportunities and this is why we call this ‘opportunity maintenance’. In a competitive market, these things can really make the difference between an agile and a less agile company. Conditions This probably sounds like roses and moonshine. Like ‘too good to be true’. And indeed, it takes some time to ar range this and get used to this new way of working. Blue Boxing must be done thoughtfully and a number of clear agreements are needed. The boxes or “ BY BEING MAXIMALLY PREPARED, WE CAN USE THESE OPPORTUNITIES AND THIS IS WHY WE CALL THIS ‘OPPORTUNITY MAINTENANCE’. IN A COMPETITIVE MARKET, THESE THINGS CAN REALLY MAKE THE DIFFERENCE BETWEEN AN AGILE AND A LESS AGILE COMPANY. PETER DECAIGNY Partner & Consultant, Mainnovation pallets may under no circumstances be regarded as grab stock for (urgent) interventions. If boxes are looted, this immediately causes great frustration during execution of the prescripted task. Confidence in the approach disap pears and we go back to the old-fash ioned method. It is also important to make good agreements for the reinte gration of unused parts and the return of parts that need to be repaired. When preparing the box, we often start from a ‘worst case scenario’. This means that we are preparing for the situation where we have to replace a complete kit of parts. In reality we may not need all the components and it is useful to reinte grate the unused parts back into the warehouse. Technically, there are var ious solutions to properly arrange this with the supporting EAM system. There are companies that regard the boxes or pallets as a virtual warehouse and only book the items when the actual con sumption is known. But here too there are various possibilities. Efficiency Blue Boxing will not solve the scarcity of technical talent, but on the other hand, it can dramatically boost the efficiency of the maintenance executive team. This allows more work to be done with the available team of technicians. Another positive side effect: it increases the sat isfaction of the technicians. Searching for the right spare parts, finding the nec essary tools, waiting for permits, looking for the right adjustment instruction et cetera are all sources of frustration and nagging. Perhaps the metaphor will help us see our technicians as surgeons, but without the green skirts of course. ■
2022 AP Magazine | 23
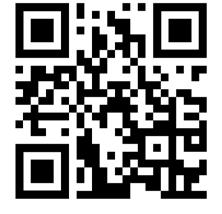
WITH THANKS TO: Peter PartnerDecaigny,&Consultant, Mainnovation Read on ap-magazine.eu: bit.ly/blueboxing
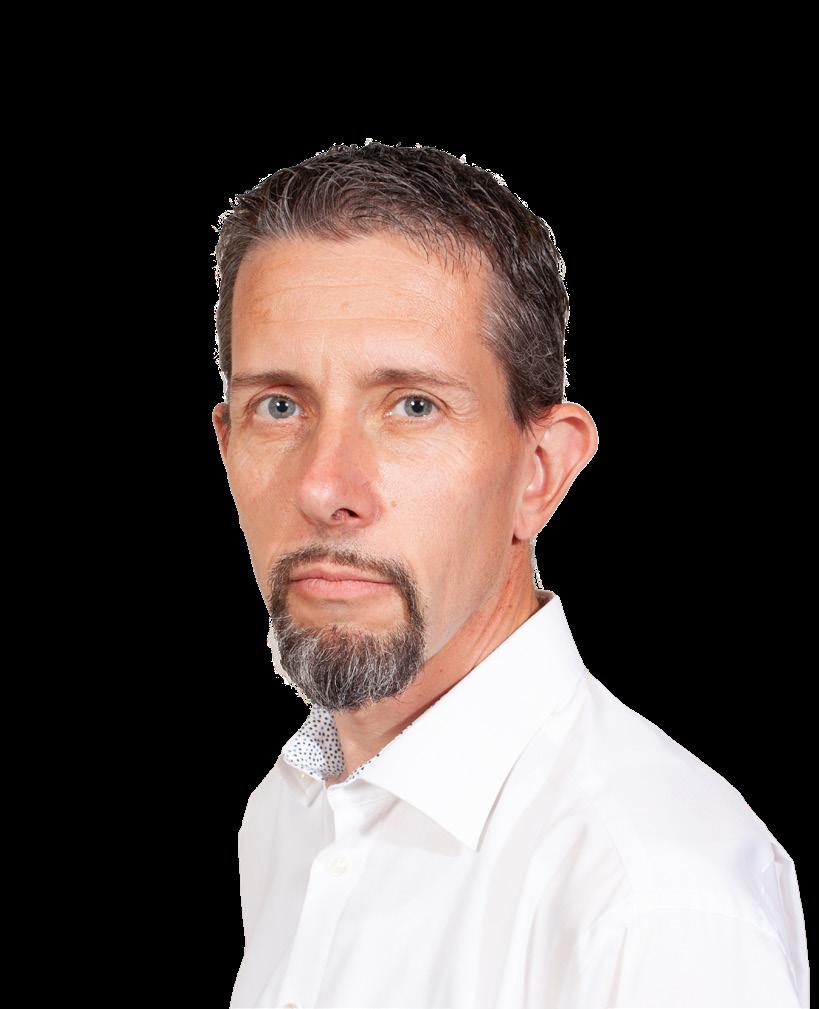

ROUND TABLE DISCUSSION
Everything starts with the influx of talent. How can companies ensure that qualified people join them?
Sarah Geeroms: “At La Lorraine Bakery Group, we are always looking to attract experienced technical talents, but due to the current labour market, we introduced a different approach and aim to also at tract less qualified people with our vision ‘hire for attitude, train skills’. We particu larly emphasise our assets such as an intensive on-the-job training and growth opportunities. Contact with schools is also becoming increasingly important in order to attract qualified staff. Unfortunately, there is still a big gap between educa tional institutions and the business world. Expectations need to be aligned even more closely so the gap narrows and in the long run preferably disappears.”
HOW TO FIND, QUALIFY, MOTIVATE AND RETAIN TECHNICAL TALENT
Christophe Dhaenens: “At Fluvius there are two activities for school leavers. During the Easter holidays final-year stu dents are given the opportunity to take part in an instructive work placement with us. They are evaluated like the tech nicians, which strongly motivates them to give it their best effort. In addition, we offer a dual learning programme for 16and 17-year-olds. This is not just another course but broad education in an indus trial working environment. It requires a lot of flexibility from our teachers, but it yields satisfactory results.”
Keeping employees motivated: what is the best way to do that? Verstraeten: “I strongly believe in en gagement. Every company operates on the basis of specific procedures and guidelines. They are usually direc tive and operate in a single direction. Giving your people the opportunity to share feedback on the way they work, this one-way traffic becomes two-way traffic. This creates an elevated level of© Adobe Stock
How can the knowledge and expertise required for certain tasks and jobs be transferred and disseminated in a company?
Jorim Rademaker: “At Manual.to we deliberately built a straightforward way of passing on knowledge. We create a broad support base on the floor and give these workers the tools to easily and quickly share their know-how themselves. The advantage of this approach is that the older co-workers, who used to rely on paper manuals, now connect with the younger co-workers, who are more used to apps such as TikTok and YouTube. They learn from each other, which boosts their skills as well as their motivation.”
Peter Verstraeten: “Simplicity is indeed key when it comes to making knowledge available. Digital communication, for ex ample via an online platform with short and clear instructions and videos, is an ideal tool. But there is a caveat. Videos and tutorials are useful, but evident ly you don’t have time to watch them when you are in the middle of wrestling with a problem. That is why a step-bystep workflow with bite-size instructions is crucial to guide people while execut ing the job both in an online and offline context.”
24 | AP Magazine 2022
Businesses are facing a major problem as technical vacancies are extremely hard to fill. Asset Performance Magazine brought together four experienced players in the field of asset & solution management to analyse the situation and to look for possible structural solutions.
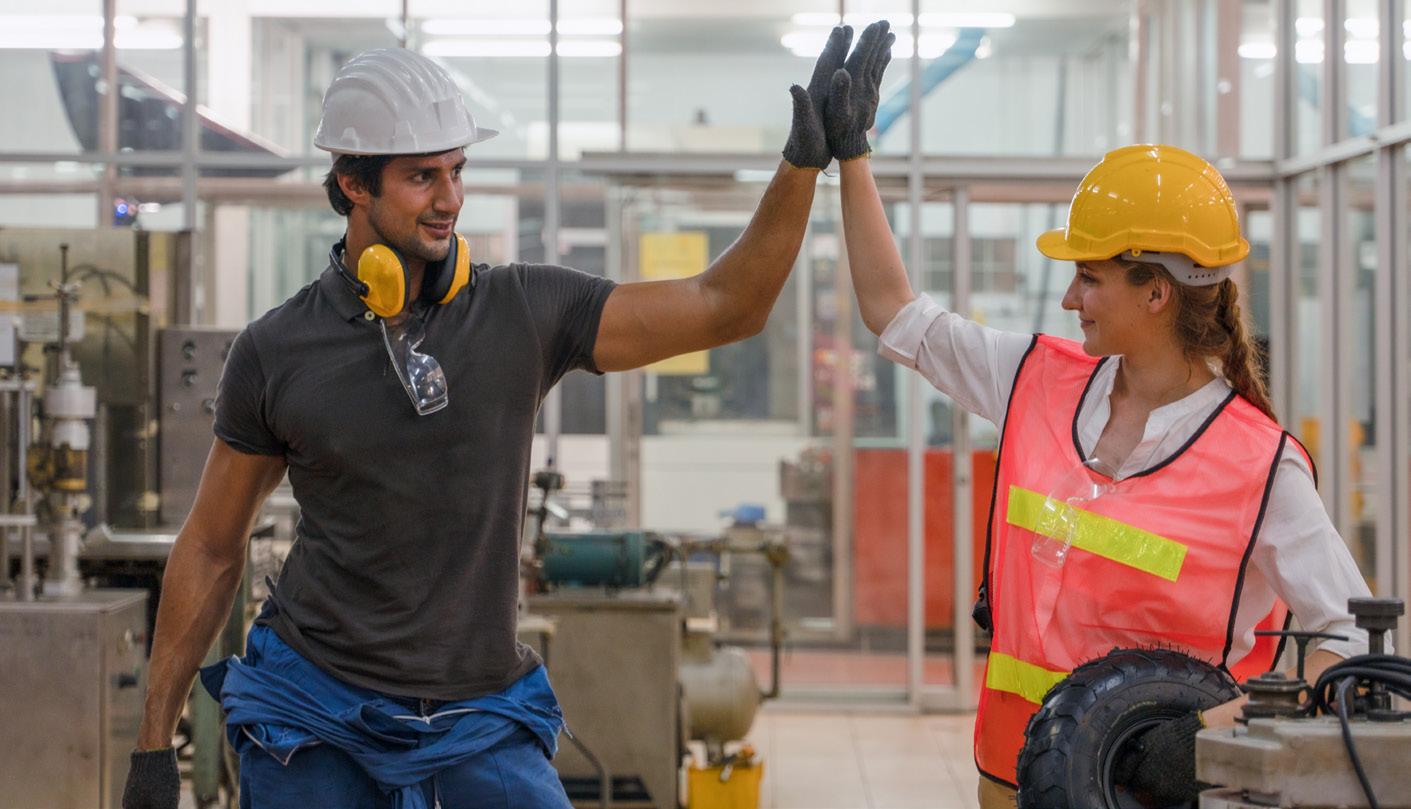
JORIM RADEMAKER CEO of Manual.to PETER VERSTRAETEN CEO of Proceedix AT THE TABLE:
engagement and motivation. Merely fol lowing rules does not work for people on the Rademaker:floor.”
Equipped with this knowledge, they en ter an elaborate onboarding process with intensive on-the-job training along with various training courses via external partners. This gives them plenty of op portunities to learn and develop at their own pace. Moreover, we work in teams, where each employee can engage his or her own abilities and talents. Above all, we want our people to discover, learn and grow for themselves. We always make sure that an experienced technician is present to help and jump in if necessary. That way we can be sure that everything is executed in a correct and safe way.”
Dhaenens: “At Fluvius we do not recruit for a specific job but for a full career. We provide a comprehensive training programme for those who start at our company. We ensure that all our tech nical staff are well-informed about both the latest technologies and devices and equipment that has been in use for many years. We work with a system of exams and continuous assessment. We reg ularly organise refresher and updating courses, during which our people learn CHRISTOPHE DHAENENS Strategic Workforce Management at Fluvius SARAH GEEROMS
Geeroms: “At La Lorraine Bakery Group, we try to do this by dividing up tasks and competences in certain areas and by focusing on our people’s strengths. New technicians only need a good ba sic knowledge and the right attitude.
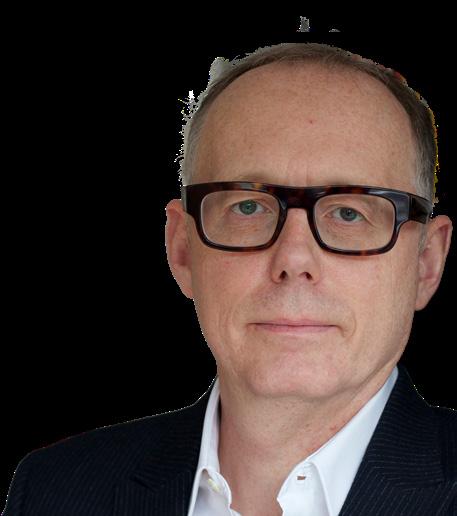

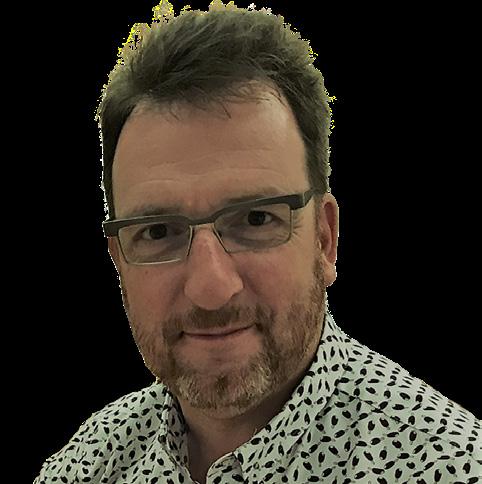
How can a company ensure that all technical tasks are completed and executed effectively and correctly?

“It is essential for the workers to feel listened to. Having them contrib ute to the knowledge base, makes sure the know-how shared is real, authentic and grounded in reality.”
Talent acquisition and learning and development manager at La Lorraine Bakery Group
Looking ahead All participants agree that it is a big chal lenge to find and recruit technical talent, both technicians and engineers. Today, as many as 10% of technical vacancies remain unfilled. To solve this, companies need to invest fully in a recruitment strat egy with a long-term vision. This is how the right people will join the organisation and stay there. Talented employees stay at the company - instead of looking for another job - which can only improve op erations and profitability. ■
about recent technologies and methods that help them do their jobs well. This is always a good opportunity to exchange experiences with other technicians. Moreover, the teachers learn from their students, especially from the young er generation with their digital habits. Exciting cross-fertilisation takes place that benefits everyone involved.”
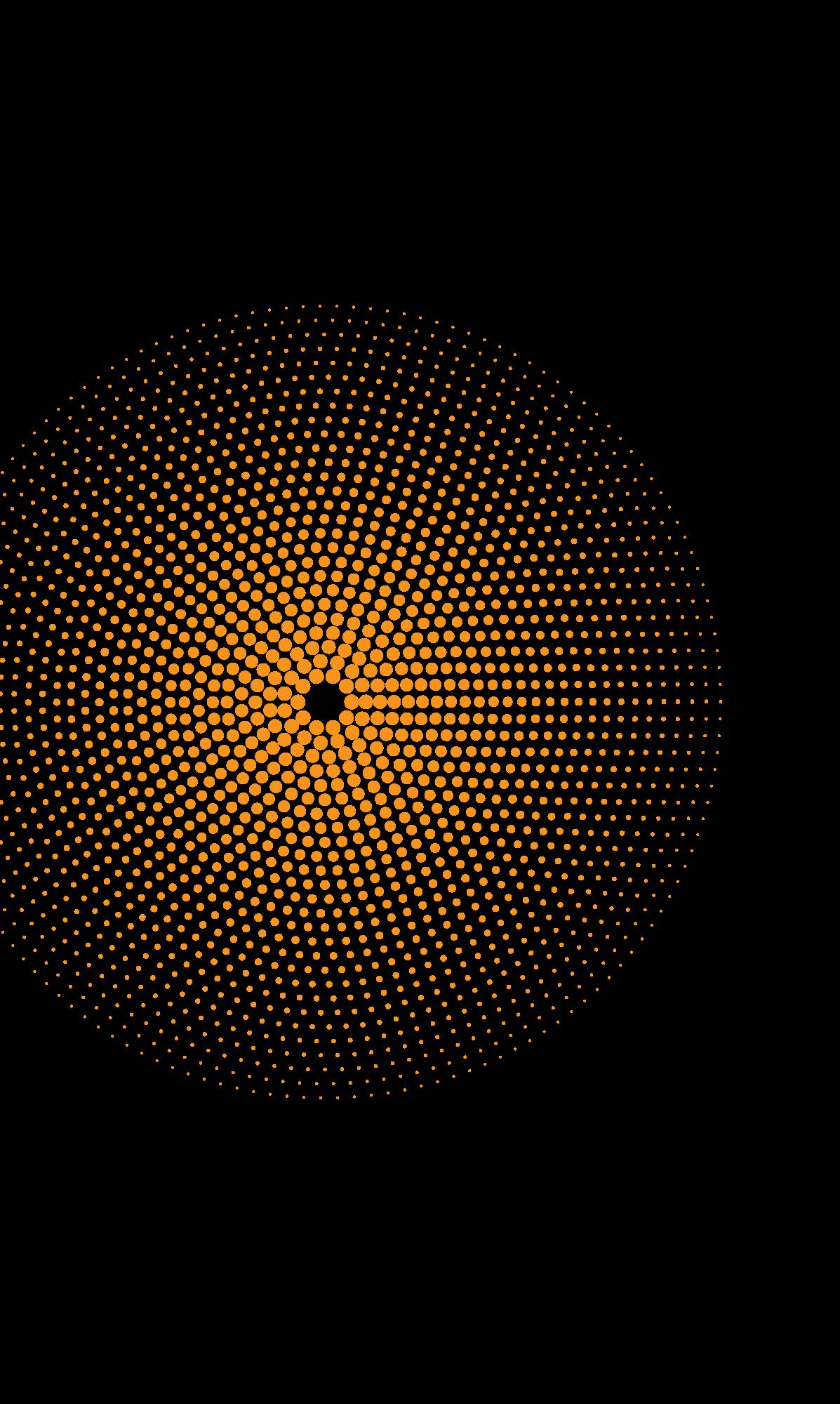
Rademaker: “Working with images only is certainly possible, but if you can have texts translated easily it is still very valu able to provide context. With video, add ing short text will do.”
Verstraeten: “Companies need to move with the times and invest in an online e-learning platform where professional knowledge and technical instructions can be easily accessed. In addition, they need the tools to support and © Alamy Stock Read on ap-magazine.eu: technical-talentbit.ly/ 26
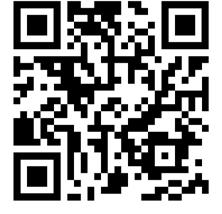

ROUND TABLE DISCUSSION guide each employee individually with personal and contextual instructions at Rademaker:work.”
Geeroms: “For our safety instructions, for instance, we communicate main ly with images, animations and videos, and as little text as possible. In that way, we want everyone to understand the basic information and instructions.”
“If you want to keep young talent at the company, you have to pro vide the people with knowledge tailored to their needs and mindset, similar to TikTok and YouTube. Text-only books are outdated; young people want to be in formed quickly and visually. Information should also be available in the right lan guage. Because our customers have production sites in several countries, we make all knowledge automatical ly available in more than one hundred languages. You have to speak their lan guage, and that means you have to add not just a translation, but also video.”
| AP Magazine 2022
Rademaker: “With your work instruc tions and know-how, using digital tools like ours, it is now easy to allow the op erators to confirm the completion of tasks according to specifications.

How do you manage to keep people at the organisation after internal training and a few years of work experience?
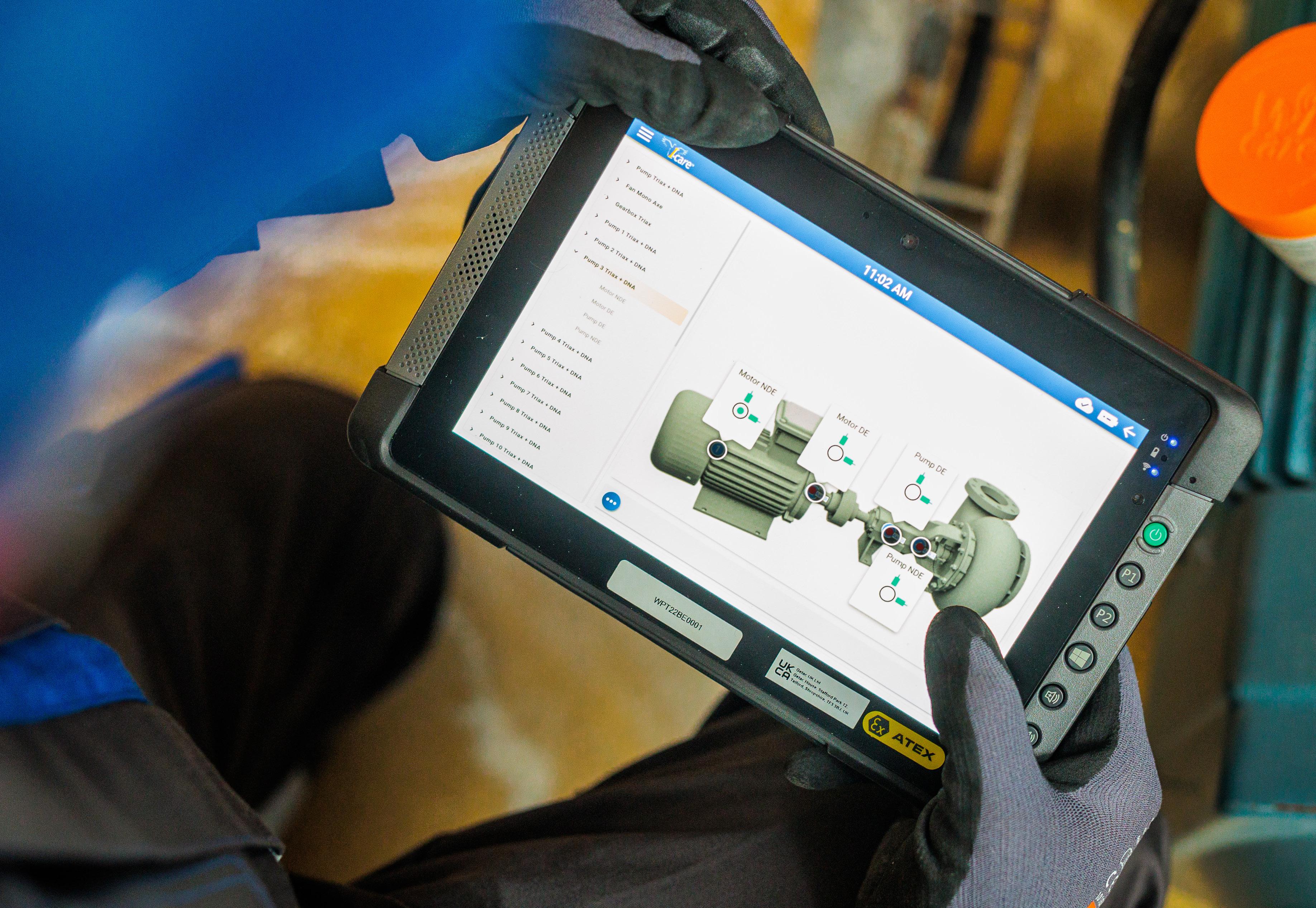
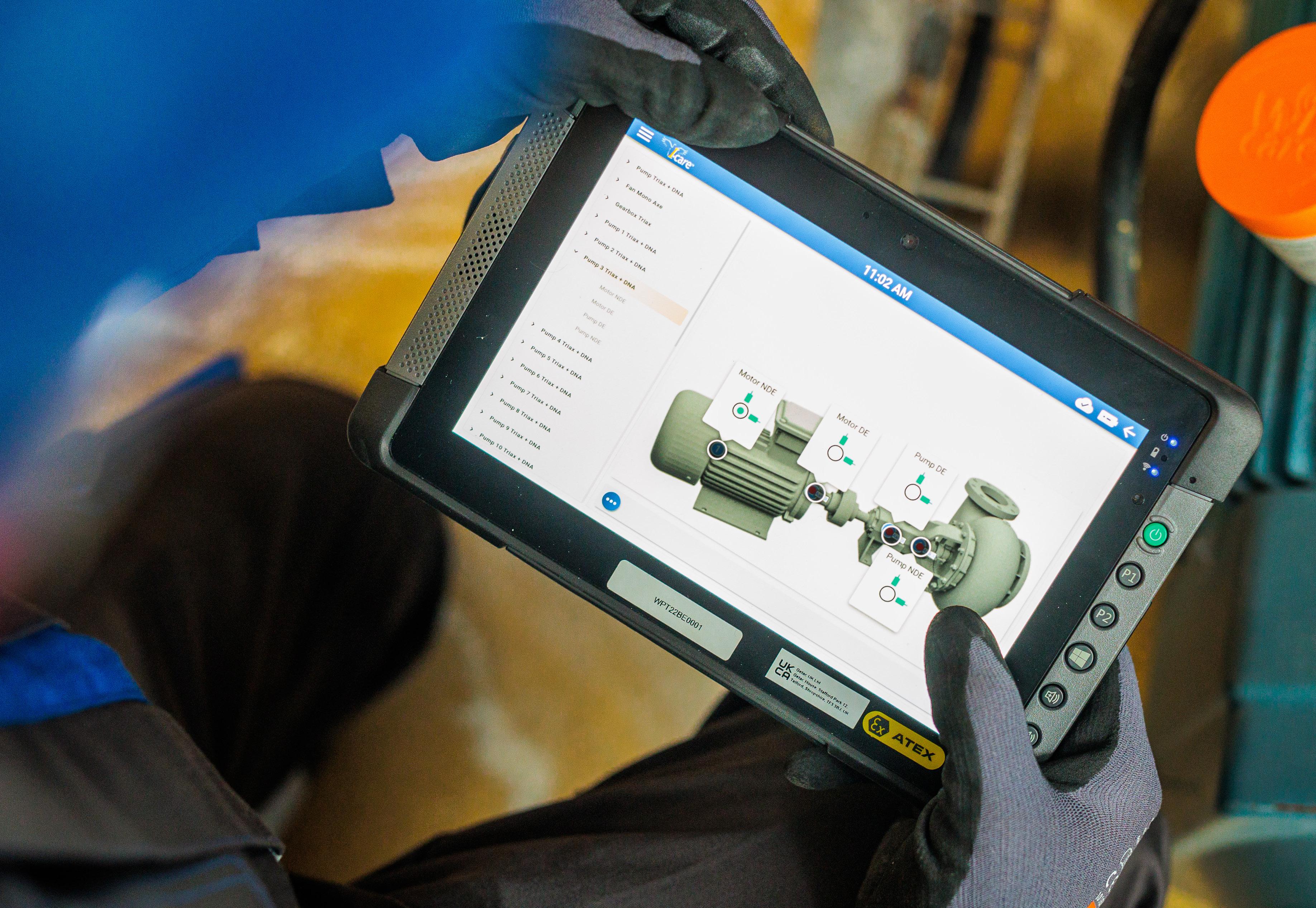

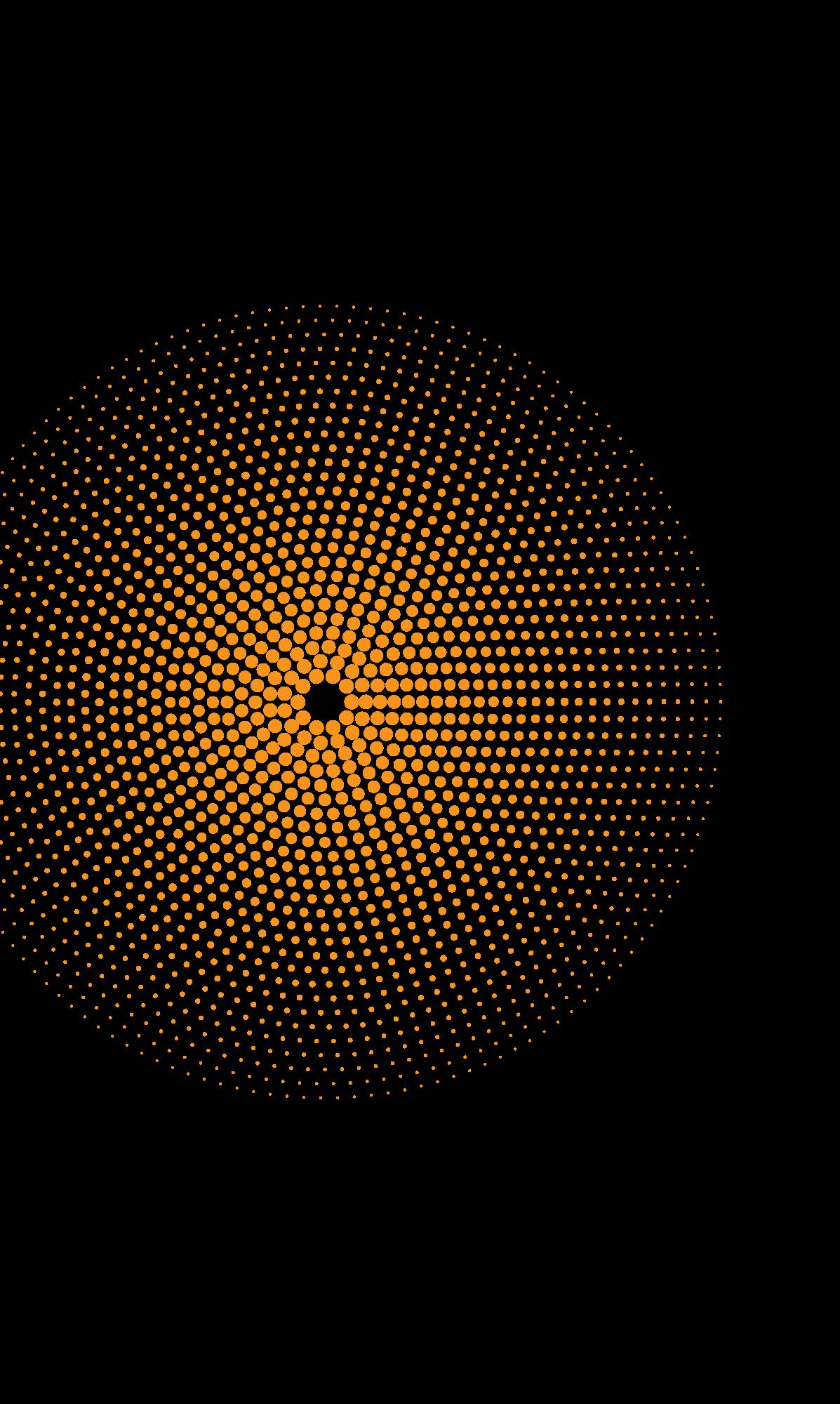
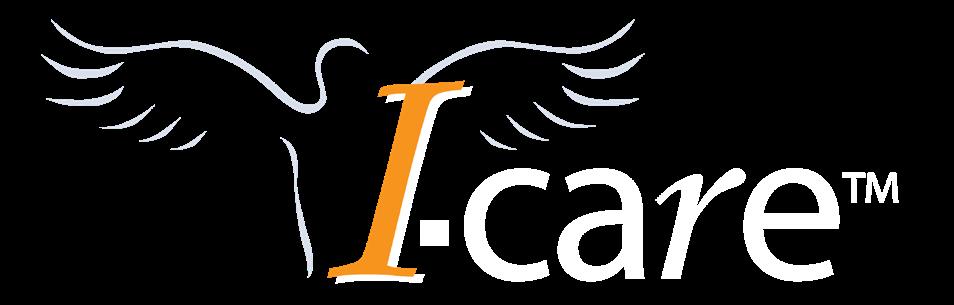

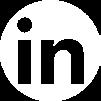
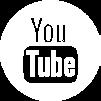
IF YOU
As pure data specialists, Thomas and Steven noticed that, in order to offer total solutions to industrial companies, they needed additional expertise on the practical operation and maintenance of machines and the course of manufac turing processes. “This is how the coop eration with Dirk and Pascal came about. They evolved in the opposite direction. From their technical background, they Thomas Meersseman “ ADDED VALUE OFTEN LIES IN CLEVERLY COMBINING DIFFERENT DATA ELEMENTS TO REVEAL NEW INSIGHTS. ME
ERSSEMAN COO, The Grain 28 | AP Magazine 2022
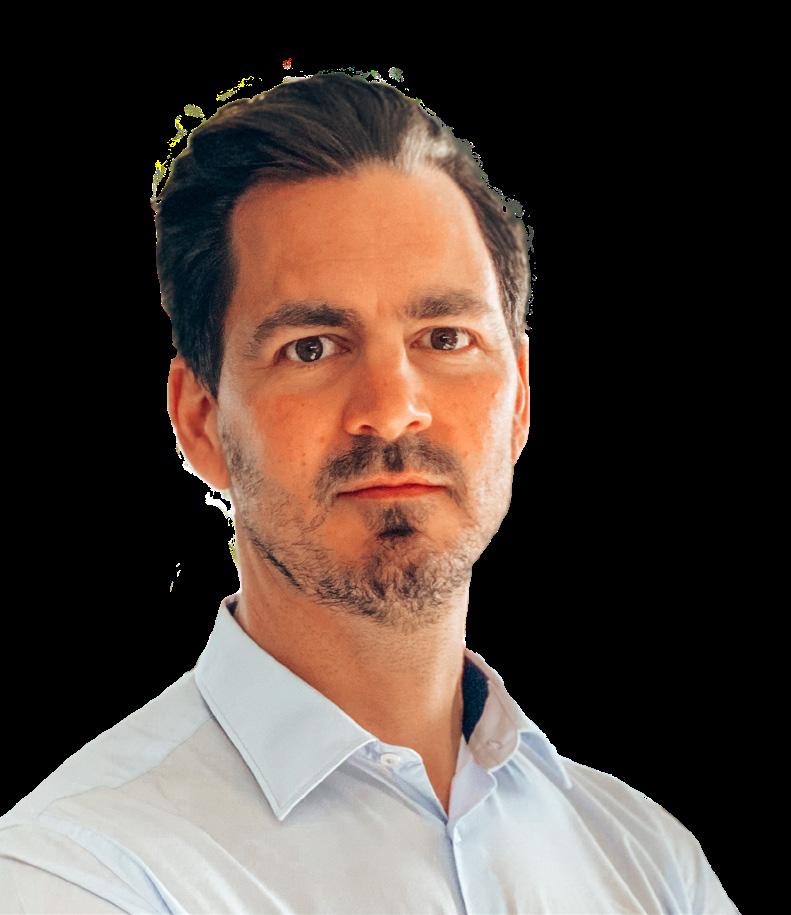
THE
ONLY
ENDORSED INSIGHT
The interdisciplinary team at The Grain uses that grey matter - brain cells - to develop customised ar tificial intelligence (AI) solutions for in dustrial companies. Interdisciplinarity came about when Thomas Meersseman, Steven Raekelboom, Dirk De Nutte and Pascal Bejstrup decided to join forces four years ago. Meanwhile, The Grain has grown into an SME with some fifteen employees. “Steven and I had already founded Provideor ten years ago. We focused on analysing and using data from supply chain processes to optimise both inven tory management and distribution,” says COO Thomas Meersseman. “Of course, applications of this kind have exist ed for some time, but they were mainly developed for large-scale companies, with large numbers of identical or very similar products per channel. Our first customers were pharmaceutical and media companies. They distribute their products through a much finer network. Small pharmacies need just one or a handful of boxes of certain medicines per delivery - but almost immediatelyand small newsagents only need a few copies of certain magazines and even newspapers. Because we had to work for this scale, what we did was fairly new. But we did see that in these sectors, too, the attention for recording data and the demand for its practical use increased. And gradually we also received a grow ing number of requests from the manu facturing and process industry.”
Pooled expertise
© The Grain
— THOMAS
ANALYSING DATA TO OPTIMISE PRODUCTION AND MAINTENANCE PROCESSES
MASS DATA COLLECTION IS MEANINGFUL DO SOMETHING WITH IT
The name The Grain refers to an old story about the origins of chess, in which creative thinking is an essential theme and makes exponential growth possible. The company’s website lists the Checkmate and Provideor planning software as products, but these are actually just derivates from the real product: grey matter.
were looking for people who were famil iar with data analysis.”
De Nutte and Bejstrup previously worked for an international company, the Allied Reliability Group, active in proactive maintenance to predict the operational reliability of installations through condi tion monitoring. From their own specific backgrounds, they had seen the oppor tunities that the use of registration data could offer for fine-tuning predictive maintenance and other optimisations of the business processes.
“We got to know each other during a joint project,” Meersseman recalls. We hit it off immediately and decided to join forc es. That was in mid-2019. A few months later, the corona crisis broke out, which hampered all economic activities with site visits. Despite this strong delaying factor, we still managed to complete a nice trajectory during that period.”
Remarkable for a company that is en tirely Flemish-owned and based in the heart of Antwerp is the purely Englishlanguage website. “Yet that is a logical choice. We want to work international ly and more than half of our customers are foreign or have their headquarters abroad,” Meersseman argues. “For ex ample, one of our first customers was the Finnish steel company SSAB. “It is also a great example of combining data analysis with the practical management of industrial plants.”
THAT HOT SUMMER
When Luminus enlisted the help of The Grain, the energy company was already familiar with keeping track of measurement data. Electricity producers are subject to all kinds of obligations: for example, they have to inform Elia, the manager of the Belgian high-voltage grid, in advance and with considerable accuracy, how much electricity each power station will inject into the grid at what time. Elia needs these data to ensure the balance of the grid and security of “Wesupply.hadbuilt a fairly accurate model for Luminus, but in the summer of 2019, we had it completely wrong. The model was trained on a large history of mea surement data, but we had not experienced a heat wave like the one in the summer of 2019 in 20 years,” Thomas Meersseman explains. “Such a situation is a good example that you should not blindly trust only a model. An algorithm makes a prediction based on what it has observed in the past, but you also have to teach it to deal with unexpected data and build in safety margins - especially when such a model is used to support operational decisions.”
© The Grain 2022 AP Magazine | 29
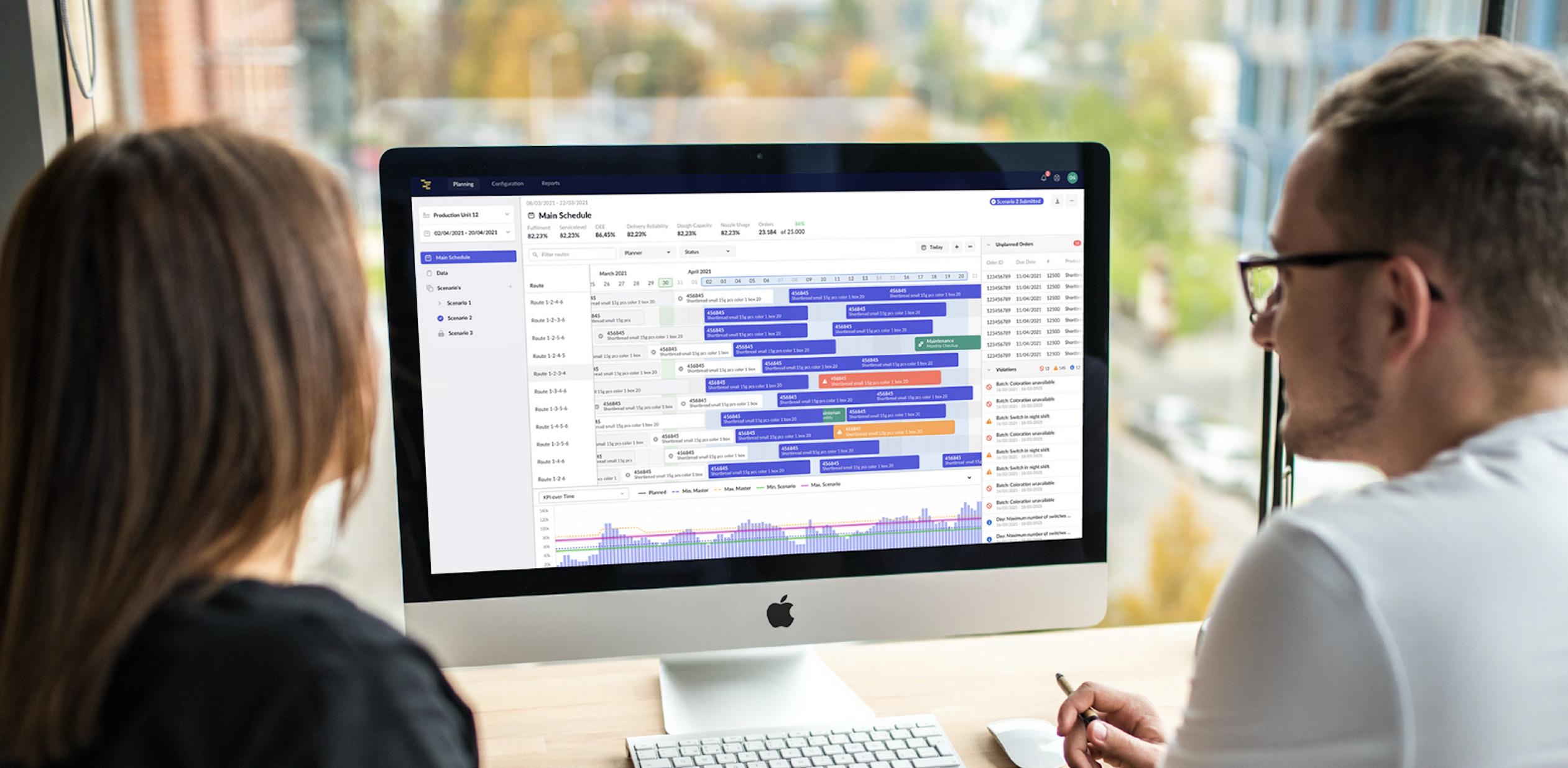
“Using various sensors, we record all use ful data. But where do you set the alarm threshold? For this we need not only our own practical knowledge, but also feed back from the operators. In our software, we have built in the option to add them precisely. In this way, the system learns to recognise false alarms and is continually fine-tuned. SSAB will continue to roll out this application to its other branches in the future.” Luminus Closer to home, in a completely differ ent sector, there was electricity suppli er Luminus. The energy sector in general is striving to make electricity production more sustainable. One of Luminus’ own power plants is its steam and gas pow er plant along the Ringvaart canal in the Wondelgem district of Ghent. Such a plant has both a gas turbine and a steam turbine.
Usually, these demands are about support rather than the exact background of what we Meerssemanoffer.” also underlines the need for intensive cooperation with the employees of the companies that The Grain assists.
“Theoretical models already existed that provided insight into the performance of the air condenser. But all these models are quite general and do not take into account environment-specific factors such as the amount of sunlight, the wind direction, the outside temperature and even the amount of pollen in the air, which has an impact on the contamination of the air condenser.
Proof of ability “There was a problem in the hot rolling mill of his factory in Sweden. When rolling up the thin sheets of rolled steel, there were occasional problems with the exact po sitioning. When this led to cluttered steel coils, there was a financial loss, as you cannot sell such coils at the same price as elegantly rolled steel sheets. Moreover, the production lines then had to be adjusted manually. That, in turn, brought along safe ty risks and the need to interrupt produc tion.” Therefore, The Grain developed an AI application that alerts the operators when the risk of errors increases.
“We don’t barge in with algorithms that immediately provide a magic solution,” he says. “It is important to us to first get a clear understanding of the customer’s process and the problem or challenge he is strug gling with, before we start working with data. Since the customer himself knows his process best, his engagement is cru cial. Once we understand the problem, we propose a solution and see what data el ements are available that could contribute to it. These can be sensor measurements of production processes, but also quality data or historical sales data. The added val ue often lies in cleverly combining differ ent data elements to reveal new insights.
Managers and board members often help to clarify the business case. For example, a business case might be to reduce the breakdown rate of a production process by 5%, but it is mainly the process experts and operators who will provide hypotheses on what has an impact on breakdown. Our analysts then search for the right data ele ments to validate those hypotheses.”
30 | AP Magazine 2022
ENDORSED INSIGHT
Open possibilities The Grain focuses on production and dis tribution companies. “There are still many opportunities, because many companies © The Grain
We built a model that does. It is now un dergoing a trial run in Wondelgem. We are convinced that Luminus will eventually be able to use it in other steam and gas power plants,” says Meersseman. Open source The Grain has no ambitions to reinvent hot water. “Some of the software solutions we have developed we have built ourselves, but we also rely on technologies availa ble on the market. We prefer open-source technology, but, when necessary, we also implement existing commercial software components in our applications. Much de pends on what exactly a customer asks for.
Luminus uses the residual heat from the gas turbine to drive the steam turbine. This increases the efficiency. Various factors determine the power out put of the plant. One of the most impor tant is the performance of the air con denser, which is responsible for cooling.
Left to right: Steven Raekelboom, Pascal Bejstrup, Dirk De Nutte and Thomas Meersseman
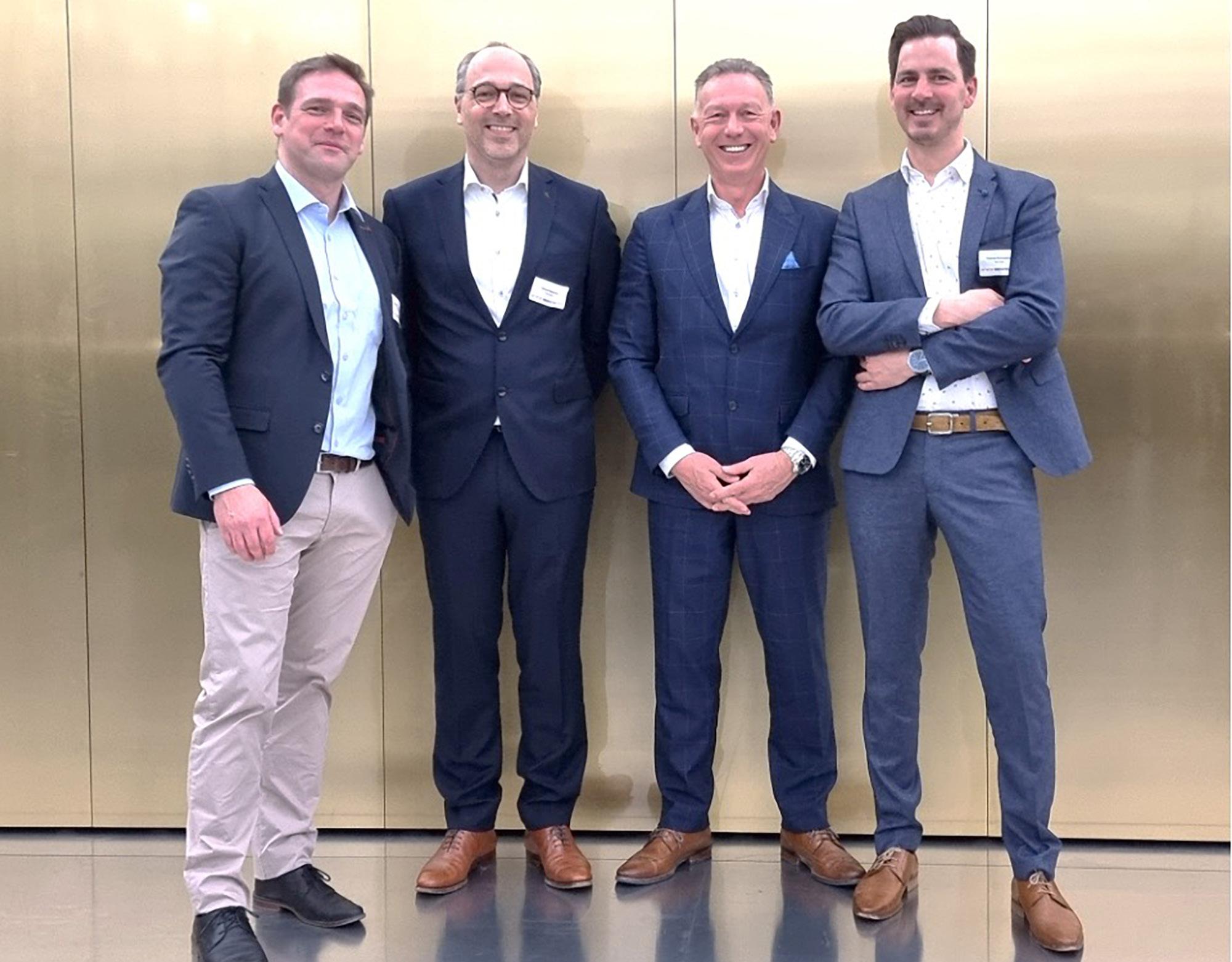
ENDORSED INSIGHT The productionschedulingrevolutionAIforplanning&wheremeetsmaintenance The Beacon — Sint-Pietersvliet 7 — 2000 Antwerpen - Belgium | WWW.THEGRAIN.PRO GET IN TOUCH WITH US | checkmate@thegrain.pro | +32 3 376 33 50
CAN AUTOMATION MAKE UP FOR LABOUR SHORTAGES?
2022 AP Magazine | 31
g r ai n

“What we do and offer will not solve the current shortage of skilled professionals,” believes Thomas Meersseman. “But it can help to use the available labour force as efficiently as possible. I like to make the comparison with how the healthcare sector uses AI systems today to detect abnormal ities on CT scans, for example. It is not the AI system that makes the diagnosis, but it does enable the doctor - as an expert - to make the correct diagnosis much more quickly. In the same way, you have to look at people working in a factory. Within the factory walls, they are the experts who know better than anyone how their production process is structured and how their machines work. They, too, have to make decisions and perform actions every day that ensure production runs as efficiently as possible. Tools that handle data intelligently can support them in this.” have only just started collecting data and still have to make the step to data analysis. For the manufacturing industry, we have developed Checkmate, an advanced tool that supports the production planner in his daily tasks. This is our response to a current trend: products are increasingly customised, and orders can be changed right up to the last minute. Adjusting production to this can be a stressful and above all time-consuming task nowadays. The supply problems that almost all manufacturing companies are facing also make us very topical. Checkmate can take all these parameters into account and quickly calculate the most optimal pro duction plan. What used to take several days can now be done in a few hours.”
“We know our limits. Data analysis can be useful in many fields, industrial process es are our thing. We stay away from sec tors where we have too little background knowledge. So don’t ask us to optimise the processes of, say, a bank.” ■ Read on ap-magazine.eu: bit.ly/data-grain
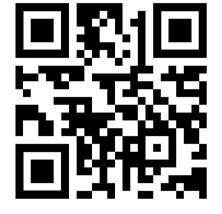
Find out how to combine our toolkit with your expert knowledge to accelerate with planning & scheduling. by th e checkmate
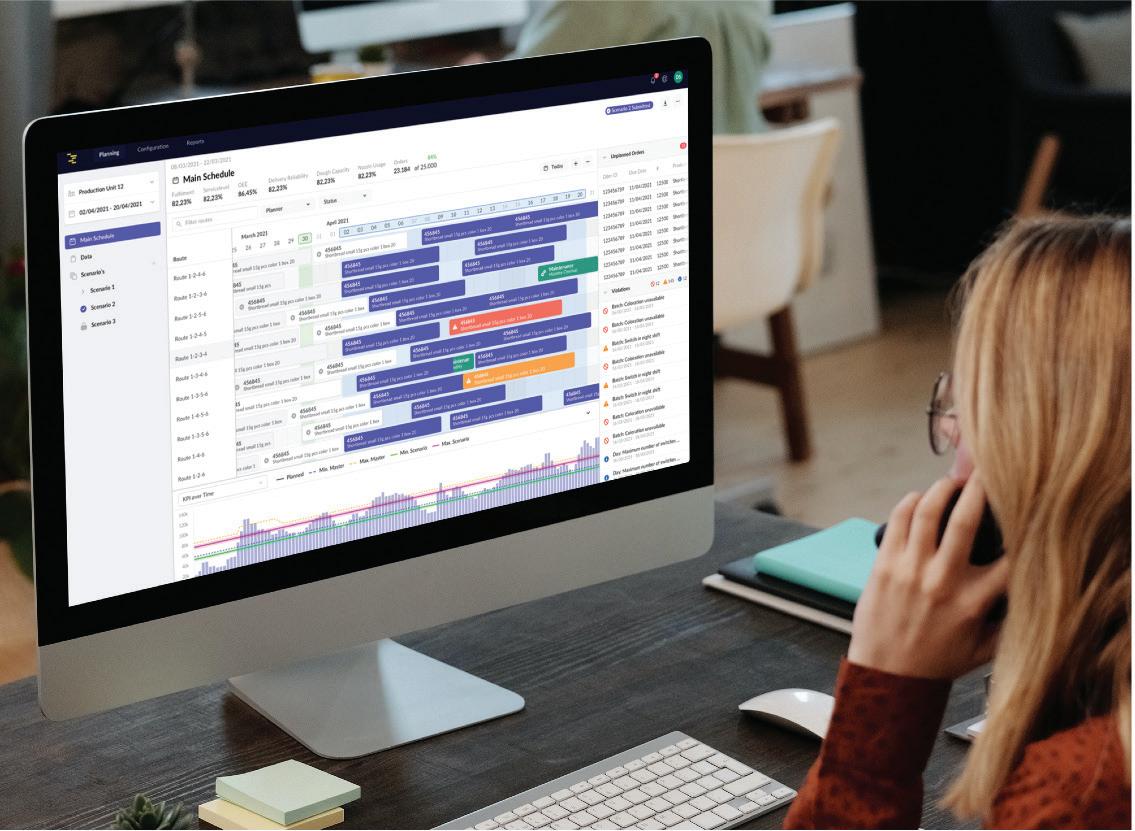
MEASURED VALUE + ADDED VALUE You make confident decisions backed by process data and a complete portfolio of services and solutions to support you. We understand you need insightful process information to help you run your plant efficiently. Do you want to learn more? www.be.endress.com Customers around the world trust us when it comes to process automation. Our shared goal is plant safety, availability and efficiency. We are with you every day, everywhere. People for Process Automation

Kris, you have a lot of experience in the world of sports. What parallels do you see with business?
OUT OF THE BOX A MOTIVATED AND RESILIENT TEAM - WHAT CAN WE LEARN FROM WORLD-CLASS FOOTBALL?
© Kris Perquy © Pixabay As founding partner of sports consultancy Maenhout & Perquy, psychologist and coach Kris Perquy focuses on improving the performance of athletes, coaches, sports clubs and sports federations. He has been working with the Belgian Football Federation for more than ten years, with a focus to Improve the offer of sports psychology for coaches and players. He combines this with activities as an executive coach in the business world. “The worlds of sport and business seem to be two different worlds but have many similarities. Both top athletes and employees want to develop and use their talents and capacities in the best possible way in order to improve themselves and achieve success. Teamwork, training, role assignment and motivation are crucial in both sport and business. I use my experiences as a sports consultant to help managers coach their employees better, so they can develop themselves and feel good in the workplace."
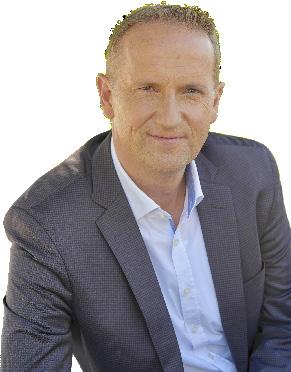
Just like in a football team, they must act as one to achieve success.“ So good team spirit is crucial in both sport and business. Are there any other similarities?
“Take a football team as an example. It consists of eleven players on the field. The goalkeeper defends the goal, the de fenders keep the opponents in line and the attackers try to score as much as possible. To win the match, there must be a balance between the different types of players. It is no different in companies. The CEOs and executives determine the strategy and the broad outlines of the company, the executives and managers steer everything in the right direction, and the employees do what they are good at in each department. All employees have a different role and their own strengths.

“In both worlds, it is about a com bination of talent and motivation. Players and staff all have individu al talents and abilities, which ensure that the team functions smoothly and does what it is supposed to do. But everything stands or falls with the right motivation. A squad or team may be overflowing with talent, but with out motivation it becomes very diffi cult to achieve goals. The success of a team is a complex interplay of skills, strategy and the right mental attitude. The latter aspect is often underesti mated, while motivation is crucial for achieving goals.“
2022 AP Magazine | 33
So what can managers do to keep their team motivated?
THE
4. MEANINGFUL WORK: People who feel that they are doing something for the organisation and who also receive appreciation for this, feel good. As a result, they make extra efforts to achieve the intended objectives. MOTIVATING WORKPLACE OF HGOTETER MEANINGFULMUATONOY MOTIVATING WORKPLACE TEAM MAY HAVE TECHNICAL SKILLS AND KNOWLEDGE, DEPENDS ON THE RIGHT MOTIVATION. PERQUY Founding partner of Maenhout & Perquy,
2. AUTONOMY: Give the employees who want it the necessary responsibilities. Drawing up their own schedule, organising tasks, setting priorities, taking part in deci sions in meetings: this makes them feel more valued and increases their happiness at work.
3. WORKING TOGETHER: Everyone has his or her role in the team, but without good cooperation the pieces of the puzzle will not fall together. Each individual makes a valuable contribu tion. Cooperation in a team is the lubricant that keeps a company running smoothly.
As a manager, how do you create such a positive and stimulating context?
1. LIFELONG LEARNING: Merely relying on talent is not sustainable. In order to deepen knowledge and skills, it is important that you invest in training. In technical teams, this often involves new technologies, software updates, etc. If you ensure that your employees remain up-to-date, they will be more motivated to achieve the intended objectives.
“A motivating working environment is based on four important pillars: learning, autonomy, cooperation and meaningful work. Which factors are important for someone’s motivation is a personal matter. Some people at tach more importance to a great team spirit than to working autonomously and being given many responsibil ities. That is why it is important to talk to your people. If you know what they want and what makes them feel good, you can adjust their role in the team accordingly. In a good team,
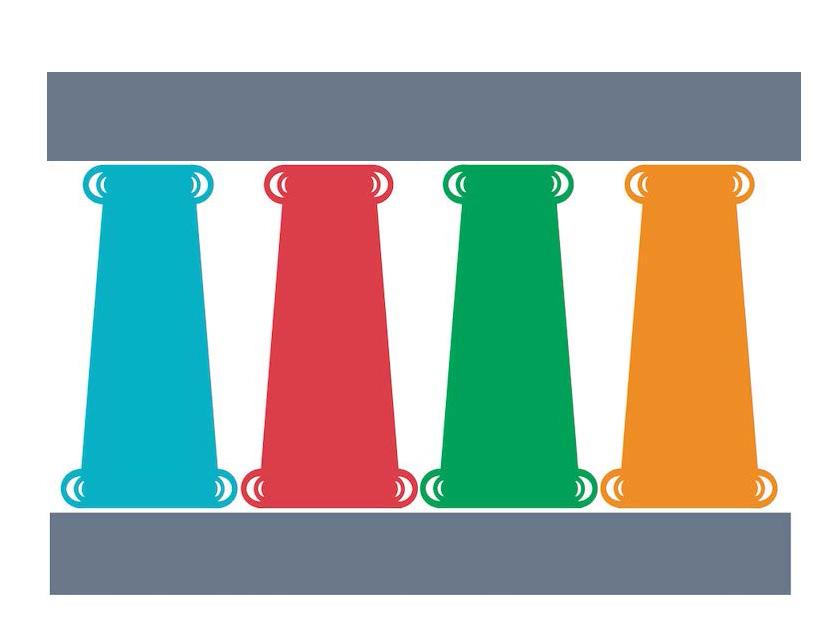
THE 4 PILLARS OF A
BUT EVERYTHING
— KRIS
LEARNING WORK NOEFLILG
A
OUT OF THE BOX
THE 4 PILLARS
psychologist & coach “ 34 | AP Magazine 2022
A
“It’s all about creating a stimulating work environment with a lot of at tention for individual strengths and needs. In such a context, employ ees feel useful and appreciated, which increases their job satisfac tion. This way, the talent stays in the organisation - instead of leav ing the company because they are dissatisfied - and they can develop further. And the more people feel they can grow, the more motivated they become.”
■
AUTHOR: Kris FoundingPerquy,partner of Maenhout & Perquy, psychologist & coach Ghelamco Arena “ THE WAR FOR TALENT, IT IS CRUCIAL THAT COMPANIES FOCUS ON MORE THAN AN EMPLOYER BRANDING CAMPAIGN AND THE OCCASIONAL FUN TEAM BUILDING. THE ORGANISATION MUST BE TRANSFORMED FROM THE CORE SO THAT WELL-BEING AND TALENT DEVELOPMENT ARE CENTRAL. THIS CREATES A SUSTAINABLE CORPORATE CULTURE WITH MOTIVATED AND HAPPY EMPLOYEES. KRIS PERQUY Founding partner of Maenhout & Perquy, psychologist & coach Read on ap-magazine.eu: bit.ly/kris-perquy
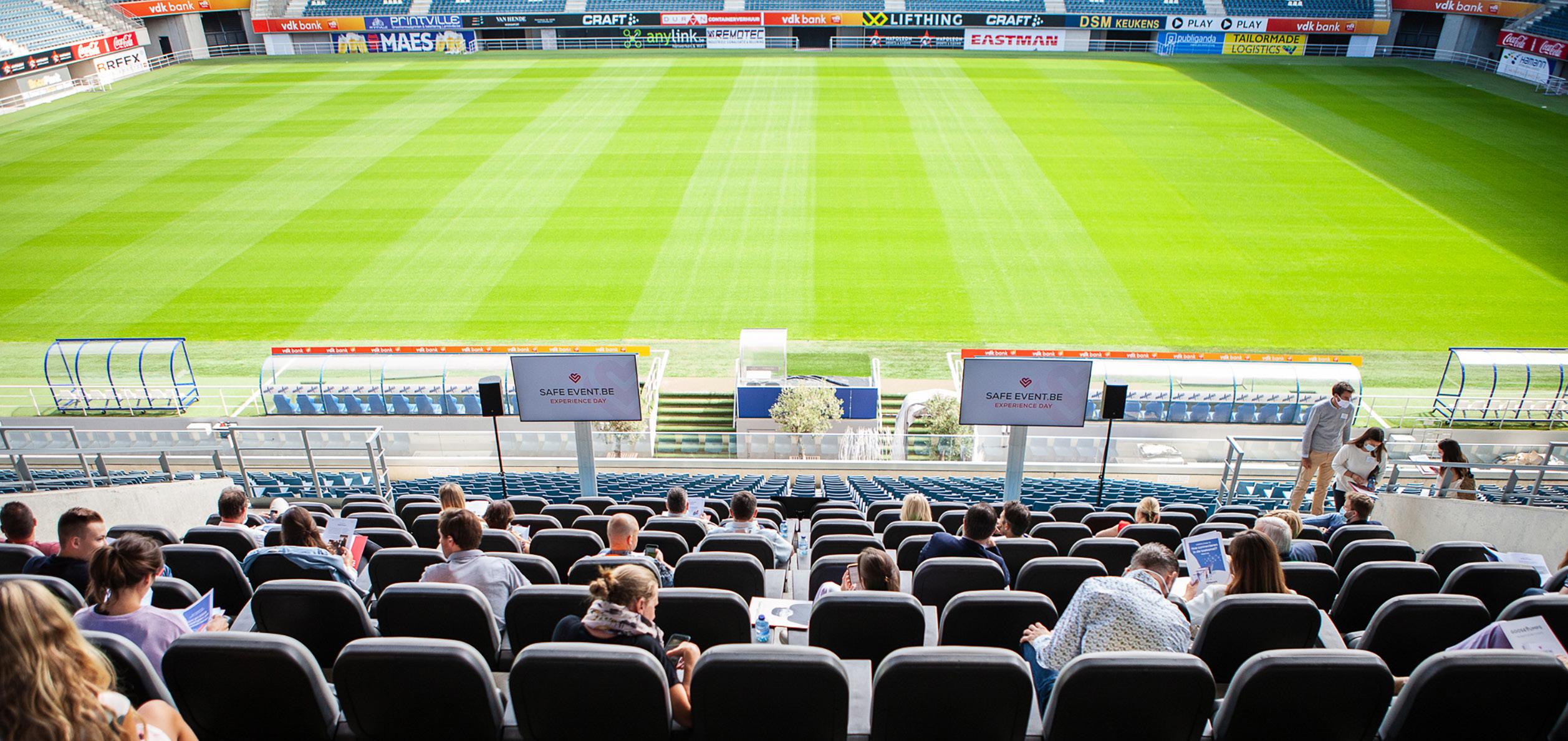
IN
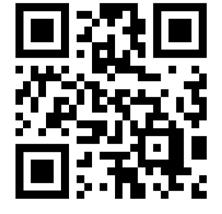
©
2022 AP Magazine | 35
OUT OF THE BOX everyone’s strengths come into play. This way, all employees feel that their knowledge and skills really matter and a sense of belonging is created. As a re sult, their motivation remains high.“ Motivation can be stimulated, that is clear. Finally, back to talent: can and should you also boost it in your team?
“Besides motivation, it is indeed impor tant to pay sufficient attention to the talent in the team, especially in today’s scarce labour market. Talent is some thing you really have to mine and nur ture in the organisation. By looking at the strengths and weaknesses of your employees and listening to what they want, you give them the opportunity to develop their talents to the full. This has a positive influence on their well-be ing. Talents are not just about technical competences. It is also about social skills. Apart from his technical skills, a program mer can be very creative, for example, which enables him to think along with certain solutions and thus, if he so de sires, to be deployed more broadly with in the organisation. Success is always a combination of technical and social as pects, of performance and group dynam ics. Striving for a balance between the two is an important task for managers."
OPPORTUNISTIC MAINTENANCE: A NEWER NAME TO GOOD PRACTICE
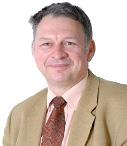
ACADEMIC INSIGHT
The principle is of the simplest: consider each asset stoppage as an opportunity for preventive maintenance, and make value out of the production interruption by performing preventive maintenance actions during the system stoppage.
The opportunistic maintenance hence takes advantage of the unavailabili ty of a system to get a head start on preventive maintenance of other sub components, in order to save the cost of future production interruptions.
At the time of opportunity, i.e., upon a failure or a planned maintenance, the EACH ASSET STOPPAGE AS AN OPPORTUNITY FOR PREVENTIVE MAINTENANCE. DEHOMBREUX Professor, UMons
CONSIDER
This is most practical in the framework of a functioning RCM policy, at a stage when the reliability parameters of sub components are well known, but as a first approach, the time since last fail ure might also be considered. Other criteria include time to next scheduled maintenance, health indicators, quality indicators[1], etc.
36 | AP Magazine 2022
Take for example a wind turbine, and simplistically divide the system into three subsystems: the wind turbine ori entation system, the blade orientation system, and the generator. Each sub system has its own specific mainte nance actions that are not necessarily identical one to another. Then, a failure in the generator would induce a long repair time. A well-advised mainte nance manager could take advantage of this stoppage to perform upcom ing preventive maintenance actions on the other subsystems, hence sav ing an additional production loss that would have occurred soon otherwise.
Economic dependence Opportunistic maintenance is most valuable in multi-unit systems with an economic de pendence. Can my system be divided into subcomponents that have spe cific preventive maintenance actions? Could the simultaneous maintenance of subcomponents be less costly than each individual action? If the answer to both questions is yes, opportun istic maintenance is beneficial to the system.
“ PIERRE
In the realm of maintenance policies, opportunistic maintenance may sound like an outsider. Indeed, recently, looks have been focused on Reliability-Centered Maintenance (RCM), Total Productive Maintenance (TPM) and predictive maintenance or even prescriptive 4.0 maintenance as most up-to-date common good practice, but it would be a mistake to overlook the benefits of opportunistic maintenance. Good news: implementing opportunistic maintenance is perfectly compatible with these policies under certain conditions.
Practical to implement Obviously, opportunistic actions are not undertaken at random upon a system stoppage. A criterion is to be used, to decide which, if any, subcomponents are to be maintained on a given stop page. Most often, the reliability esti mate at the time is used as the crite rion for opportunistic maintenance.
ACADEMIC INSIGHT
subcomponents are sorted according to the decided criterion, e.g., in as cending reliability order, for example. All subcomponents that are below a relia bility threshold should then be consid ered for opportunistic maintenance at the time.
Typical cases with typical values show interest for opportunistic mainte nance whenever the reliability of a subcomponent is below 80%, but the real value is a case-by-case optimiza tion based on the nature of the stud ied system.
The optimization of an opportunistic maintenance policy has its complexi ties. It is still an open research subject, but the general principle is well known and has been for years. The objective of this optimization is to determine the threshold at which opportunis tic maintenance should be applied. Values depend strongly on the main tenance costs, as well as production interruption costs. The workforce costs are not to be neglected either.
Structural and stochastic dependence are good opportunities
A fine-tuning that takes some time
Opportunistic maintenance may also be indicated in case of structural de pendence. Two components are struc turally dependent when they are con nected in such a way that maintenance action on one component necessitates the disassembly of the other. Note that this dependence may be one-way, i.e., maintaining one component necessi tates the disassembly of the other, but not the other way around. An exam ple of one-way structural dependence would be the replacement of an auto motive gearbox, which necessitates in most cases to disassemble the engine to access the gearbox, but mainte nance actions on the engine most of ten will not require disassembly of the gearbox. Adobe Stock 2022
©
If regular maintenance workforce is un available at the time, contractors may be considered, if possible, and eco nomically feasible. This possibility, if the costs are known in advance, can also be considered at the time of optimizing the maintenance policy.
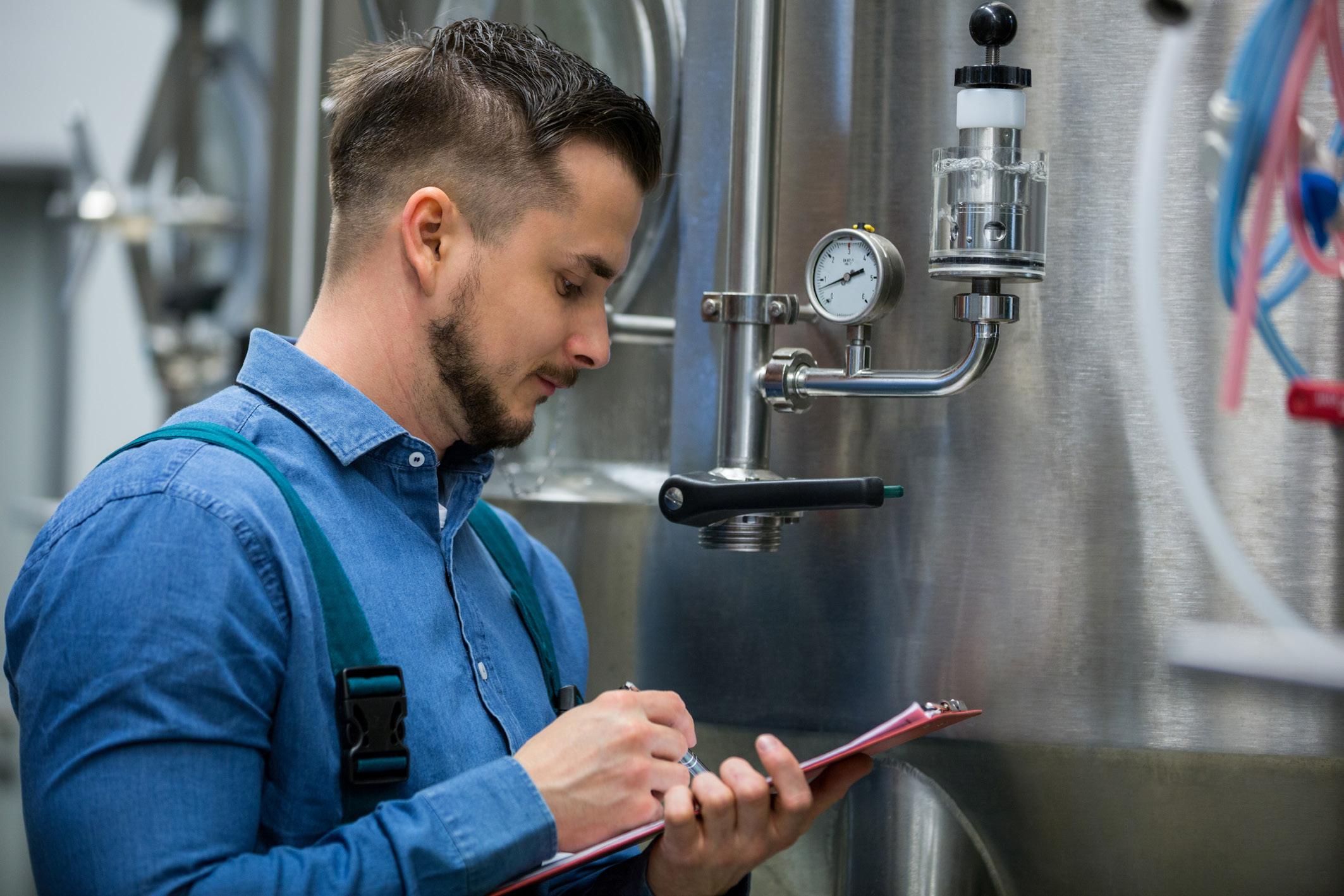
Most often, the optimization of the policy is based on a Monte Carlo sim ulation for long-term assessment of the maintenance policy, coupled with a genetic algorithm for the optimiza tion itself. These procedures should not be intimidating, and the Machine Design and Production Engineering lab at UMONS, or your local universi ty’s reliability lab might very well help you fine-tune the policy and deter mine the applicable threshold values if necessary The benefits to be expected to de pend on the system parameters, but usual financial gains are in the range of 5–20% with optimized parameters. They most often can be computed in advance given the reliability and cost parameters. Should the system be modified, the optimized parameters can be rec omputed with relative ease, given the new cost and reliability parame ter, and thus remain flexible in front of the evolution of market and labour costs.
AP Magazine | 37
Let us assume that we manage a three-component series system. Any stoppage of one component stops the system. We also have a well-estab lished RCM policy, with an extensive failure history, which allows computing the reliability parameters of the compo nents, hence optimal preventive main tenance schedules, with help of the
38 | AP Magazine 2022
ACADEMIC INSIGHT
In the case of structural dependence, opportunistic maintenance is particu larly well indicated[2], given that an im portant part of the costs are shared. In the example of the gearbox disassem bly, heavy maintenance on the engine could be considered, given the gained accessibility and the fact that it is al ready disassembled anyways. Stochastic dependence is defined by the influence of the state of one piece of equipment on the failure time distribu tion of the other, e.g., the vibration of a machine shaft may induce an accelerat ed degradation of the bearings. If a sto chastic dependence is identified, it will also provide insight to the well-advised maintenance manager. An apparent degradation on one subcomponent may strongly hint for the interest of oppor tunistic maintenance on the other one.
The integration with RCM and TPM
Integrating opportunistic maintenance might prove a little more challenging.
There is no real issue with integrating an opportunistic maintenance policy in the framework of RCM. On the contrary, the preliminary information made avail able by RCM (failure history, cost anal ysis, preventive maintenance periodici ty evaluation, etc.) are a prerequisite to implementing an efficient opportunistic maintenance policy.
Figure 1 - Timeline of maintenance events for a three-component series system with opportunistic maintenance. Lightning denotes a failure. Wrenches denotes maintenance actions; red: corrective, blue: preventive, green: opportunistic. the maintenance equipment onsite, and get a head start on inspecting some of the other wind turbines from the same wind farm. This way, mainte nance grouping takes advantage of the availability of maintenance resources in the vicinity of maintainable equipment to reduce the costs associated with maintenance logistics very similarly to opportunistic maintenance.

Because the opportunistic mainte nance policy is based on a statistical approach, it might seem unclear to the personnel, and more importantly, it im plies multiple maintenance operations performed simultaneously, which may be seen as a logistical and human re sources challenge. However, the sim ultaneity of operations also diminishes the downtime, and in the end, has a positive effect on the Overall Equipment Effectiveness (OEE)[3]
A policy akin to maintenance grouping policies Opportunistic maintenance is similar to maintenance grouping strategies, and both can be included in a bal anced maintenance policy. To illustrate this similarity, take for example a wind farm composed of a dozen wind tur bines. Let’s assume that a preventive maintenance inspection necessitates the use of a mobile elevating platform. Our well-advised colleague might also want to save unnecessary transporta tion costs for this mobile platform and benefit from the opportunity of having
Yes, but practically?
MAINTENANCE GROUPING TAKES ADVANTAGE OF THE AVAILABILITY OF MAINTENANCE RESOURCES IN THE VICINITY OF MAINTAINABLE EQUIPMENT TO REDUCE THE COSTS ASSOCIATED MAINTENANCEWITHLOGISTICS. “ DR IR LUCAS EQUETER Premier Assistant, UMons © Shutterstock

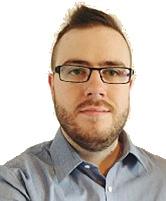
[2] D.-H. Dinh, P. Do, and B. Iung, “Multi-level opportunistic predictive maintenance for multi-component systems with economic dependence and assembly/disassembly impacts,” Reliab. Eng. Syst. Saf., vol. 217, no. 108055, Jan. 2022, doi: 10.1016/j.ress.2021.108055.
“
[3] J. M. Wakiru, L. Pintelon, P. Muchiri, and P. Chemweno, “Integrated maintenance policies for performance improvement of a multi-unit repair able, one product manufacturing system,” Prod. Plan. Control, vol. 32, no. 5, pp. 347–367, 2021, doi: 10.1080/09537287.2020.1736684. knowledge of preventive and corrective maintenance costs. Given the mainte nance history, estimates of equipment reliability can be made at any time. Upon any system stoppage in general, the opportunistic maintenance policy recommends evaluating the reliability of each subsystem, or another indica tor that is correlated with the health or remaining life of the subsystems. Assuming component A just failed, the preventive maintenance of both oth er components should be considered. The priority order is usually based on the reliability levels at the considered time, but alternatives exist, for ex ample, based on the criticality of the considered failure modes if FMECA analyses have been performed. This situation is illustrated as a timeline of maintenance actions in Figure 1. In the illustrated case, the proximity with planned maintenance of component C leads to its selection for opportunistic maintenance, leading to simultaneous maintenance of components A and C.
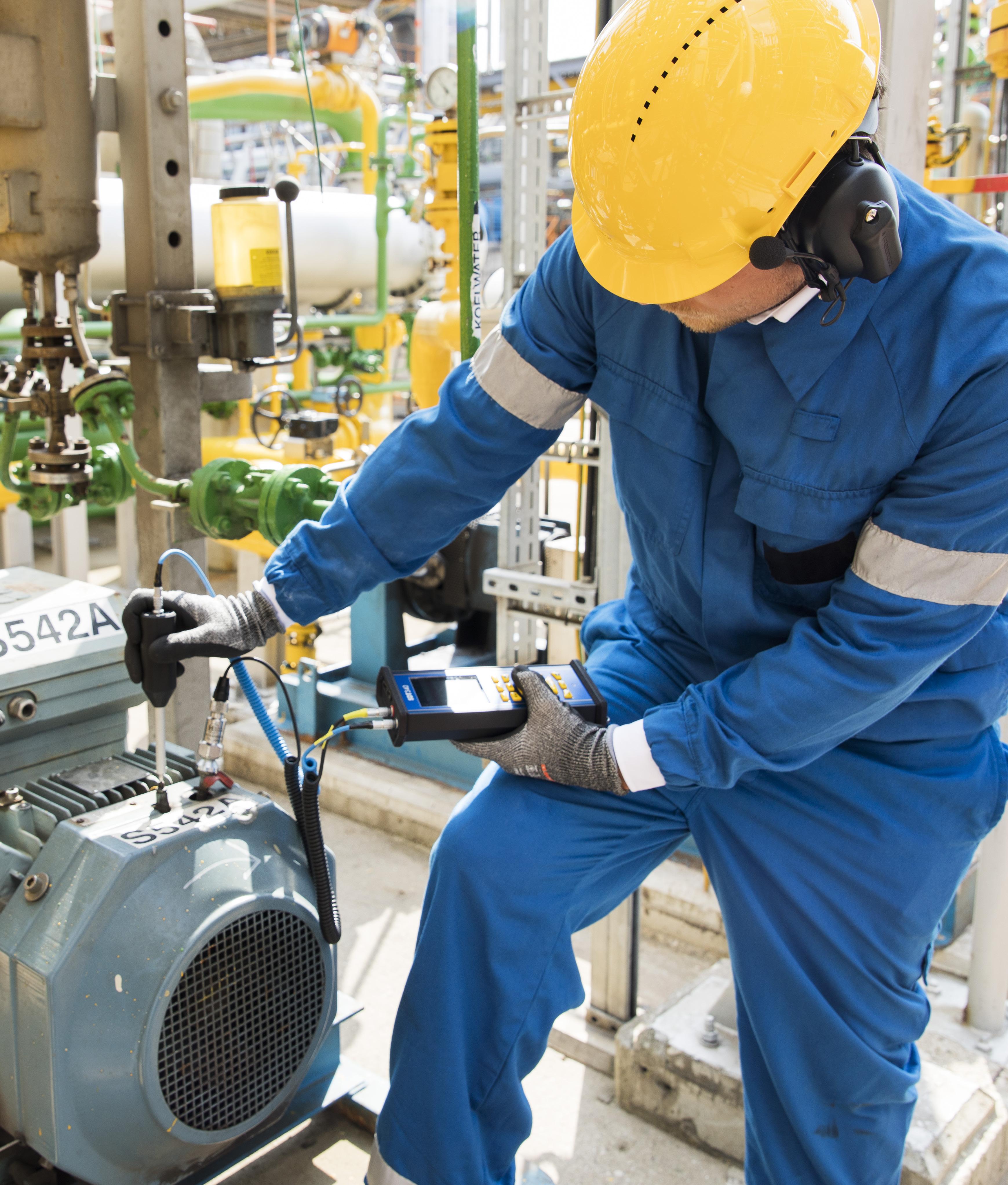
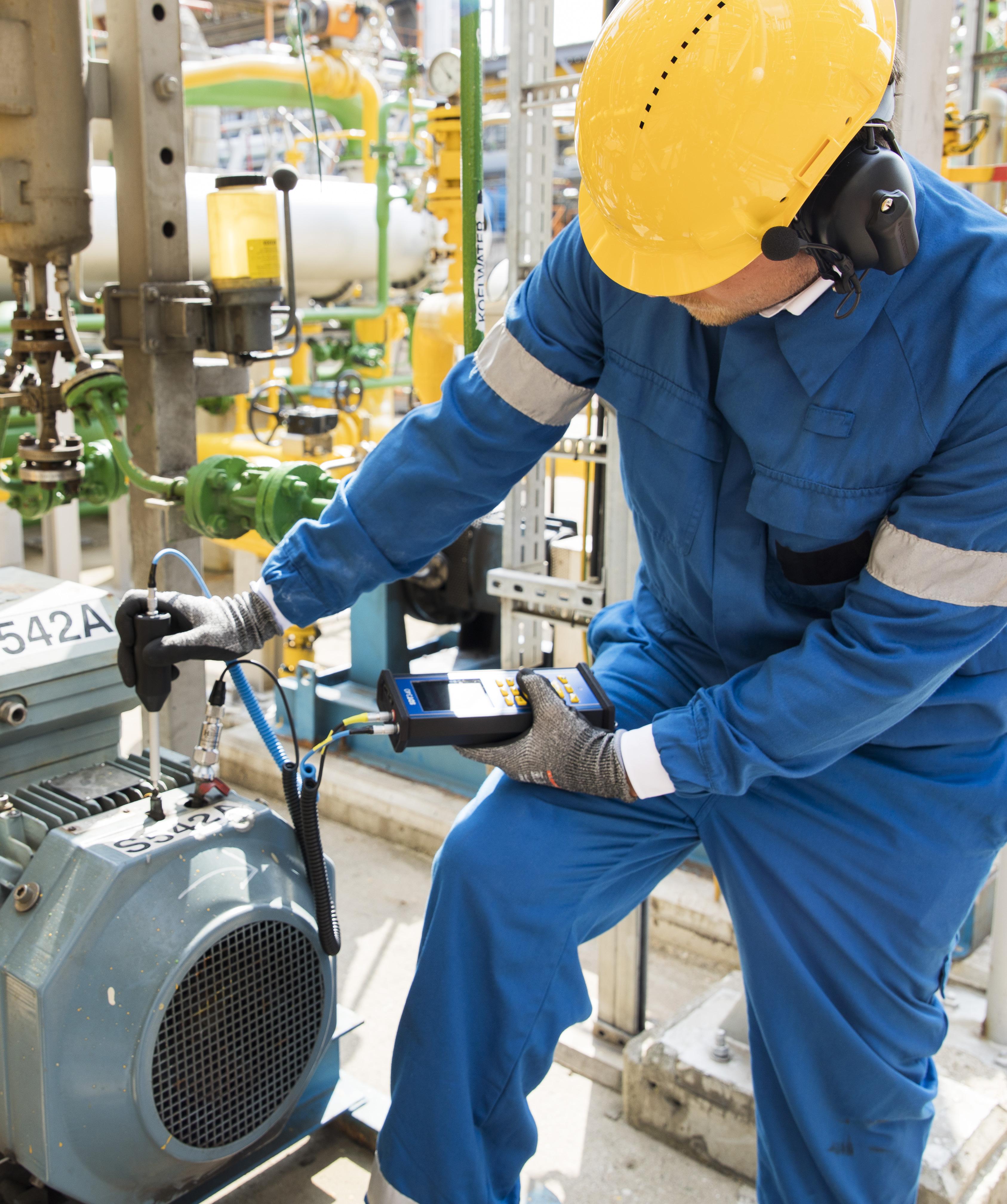
An optimized preventive policy
LORENZO COLANTONIO PHD Researcher, UMons worth being considered as an opportu nity to reduce long-term maintenance costs. ■ WITH THANKS TO: Lucas Equeter, Pierre DesignUniversityLorenzoDehombreux,Colantonio,ofMons,MechanicalandProductionEngineering
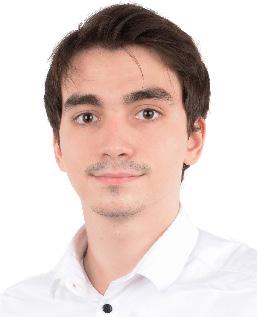
Read on ap-magazine.eu: tic-maintenancebit.ly/opportunis
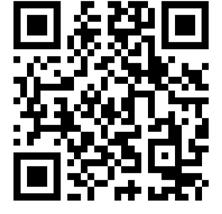
ACADEMIC INSIGHT
Opportunistic maintenance is by nature an optimized preventive policy, and therefore not frequently mentioned as a specific scheme. Opportunistic maintenance does not incur addition al costs for its deployment, especially if RCM is in place. On the contrary, it is UPON ANY SYSTEM STOPPAGE IN GENERAL, THE OPPORTUNISTIC MAINTENANCE POLICY RECOMMENDS EVALUATING THE RELIABILITY OF EACH SUBSYSTEM, OR ANOTHER INDICATOR THAT IS CORRELATED WITH THE HEALTH OR REMAINING LIFE OF THE SUBSYSTEMS.
40 | AP Magazine 2022
[1] C. Dutoit, P. Dehombreux, and E. Rivière Lorphèvre, “Using quality control in optimizing opportunistic maintenance,” vol 51, no. 24, pp. 643–648, 2018, doi: 10.1016/j.ifacol.2018.09.643.
UAS3Ultrasound Solu�ons APPLICATIONS TIGHTNESS Determine the tightness of any enclosed volume. VALVES Assess tightnessvalveandfunction LEAKS Find pressure and vacuum leaks in noisy conditions. MECHANICAL Detect defects in any system.mechanical STEAM Find faulty steam traps and components.leaking LUBRICATION Avoid lubrication.over/underGreasebearingsright. HYDRAULICS Troubleshoot any hydraulic system for passing blockages.and ELECTRICAL Inspect medium and high voltage systems for arcing, tracking and corona. Detect, Measure, Analyze Ultrasound and Vibration Data Collector Analysis Software Powerful flexibility to organize your monitoringconditionstrategy


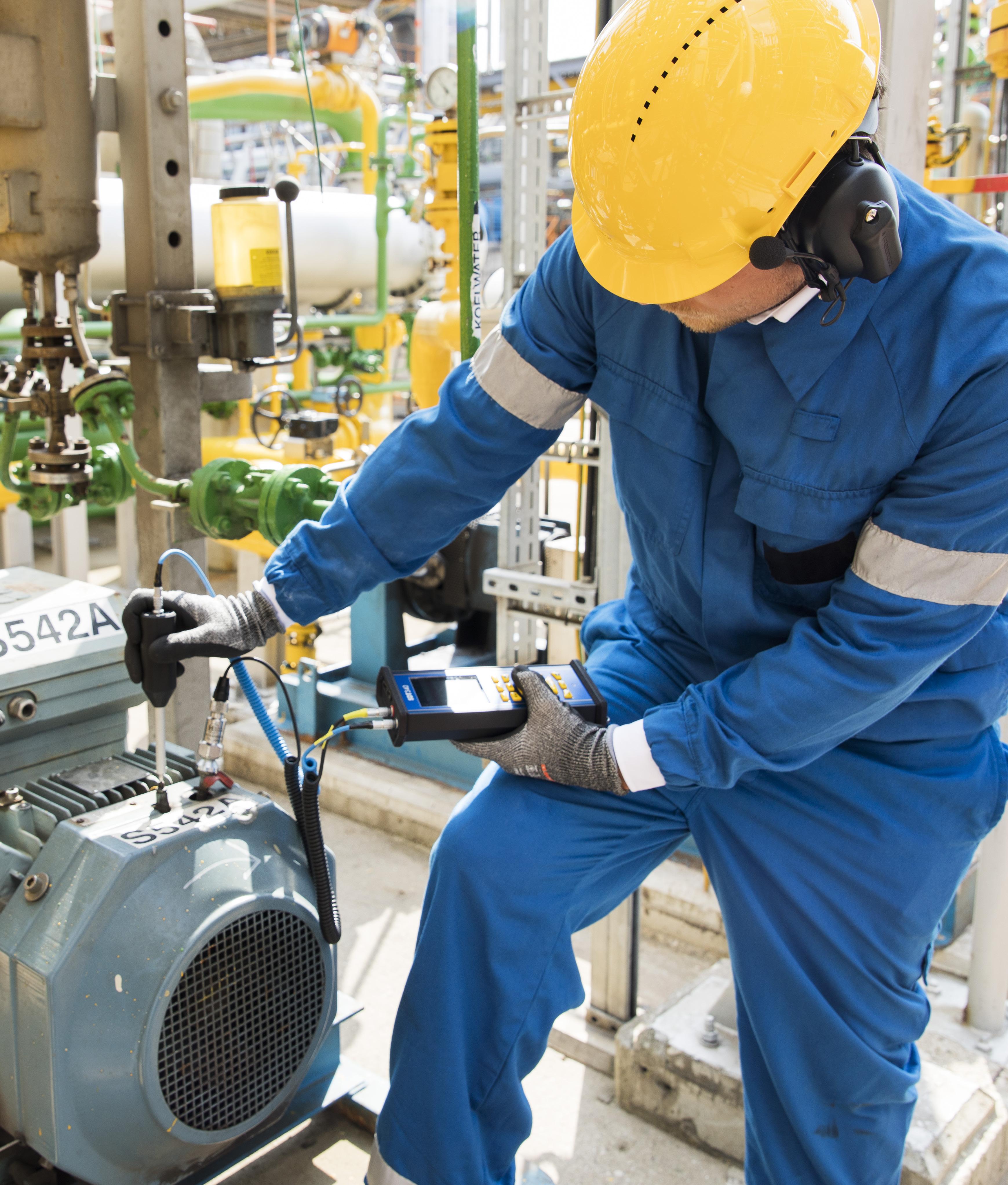
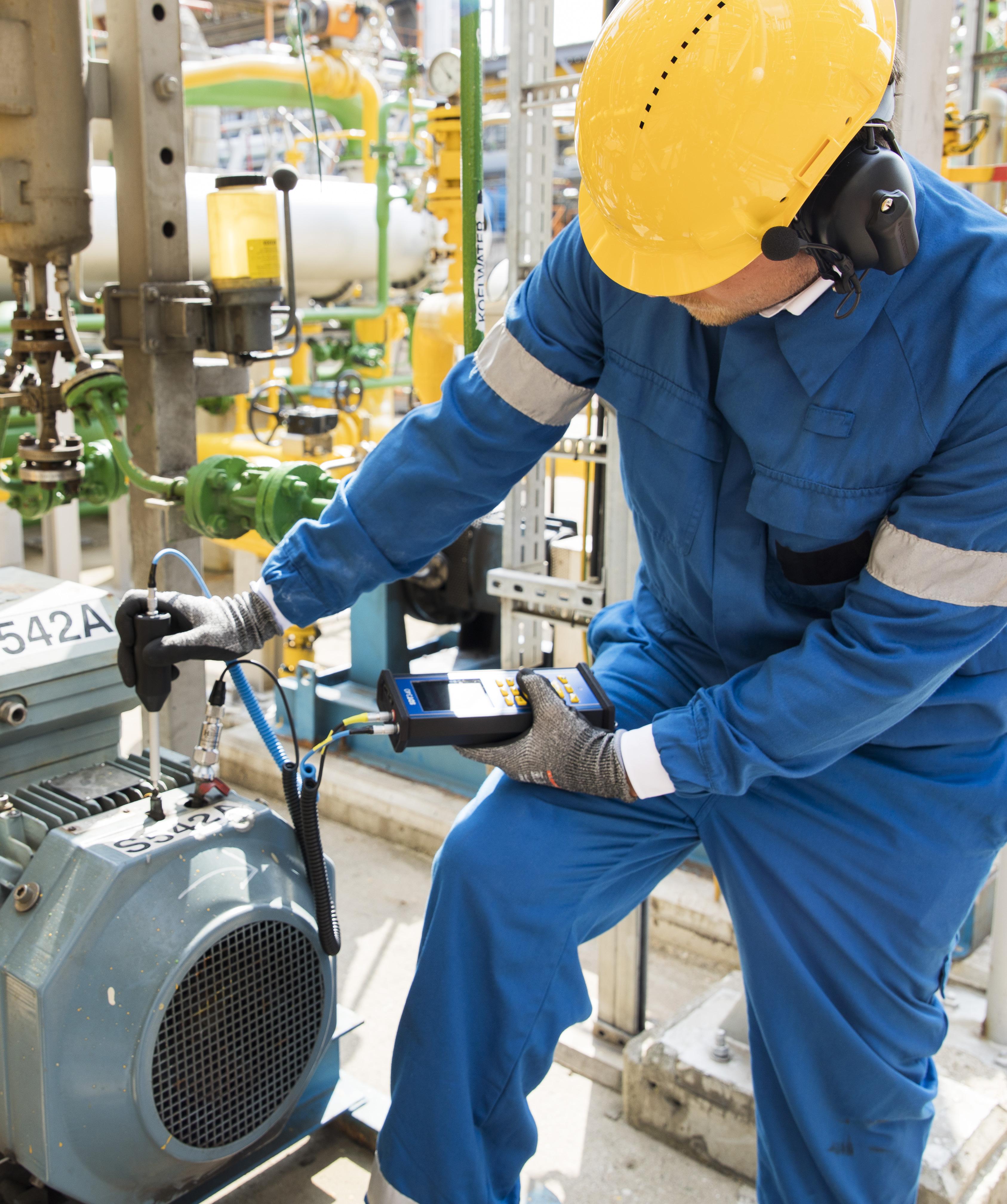
The audience chose Galler as the winner. Their efficient organisation made it possible to achieve a remarkable level of performance for an SME.

Each year, BEMAS, the Belgian Maintenance Association, wants to honour technical teams that provide great added value for their company thanks to their achievements and approach in the field of maintenance and management of technical assets. Last month, Chaudfontaine was declared the winner of Wallonia, the French speaking region. Pfizer won the award in Flanders.

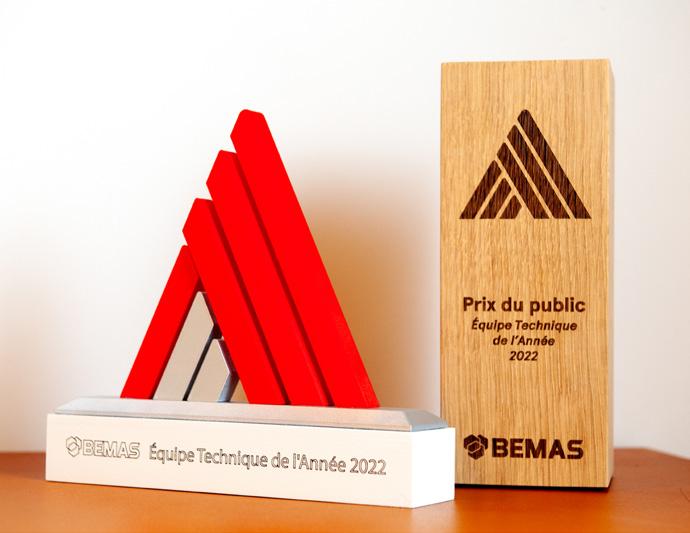
The technical team of Pfizer, winner of the Flanders Technical Team of the Year.
PFIZER AND CHAUDFONTAINE ARE BELGIUM’S TECHNICAL TEAMS OF THE YEAR
Chaudfontaine: swift recovery after severe flooding
In the summer of 2021, the south of Belgium was hit by severe flooding. The Chaudfontaine - Coca-Cola Europacific Partners was able to get production back on track quickly. In just 5 weeks, they were able to re start the 2 most important production lines, without los ing sight of safety and quality. The commitment of the staff and the mastery of crisis management made this feat possible, illustrating the importance of maintaining close-knit maintenance teams capable of reacting in the face of adversity. That’s why the jury prize in Wallonia went to Chaudfontaine.
DPLightspeed.”Worldtold
Jury president Pierre Dehombreux with the winning team of Chaudfontaine
We have all come to know Pfizer through the production of the corona vaccine. The rapid conversion of production is largely due to the technical department. The project was given the flashy name 'Project Lightspeed'. Appropriate, be cause in just a few months they turned the entire produc tion around. For the Flemish jury, this was a clear winner: “At Pfizer we see a clear interweaving between engineering, pro duction and maintenance. It is not a top-down story, but a real collaboration. They already had a very solid system for working together pre-Corona, which paid off during Project the story of their switch from a reactive to a proactive maintenance organisation in just 3 years. The audi ence was charmed by their presentation and voted them the audience’s favourite.
42 | AP Magazine 2022
TECHNICAL TEAM OF THE YEAR
Pfizer: proven track record of the technical department
Inspirational workshop by SDT Ultrasound Solutions during the BEMAS Forum Maintenance in Marcinelle.
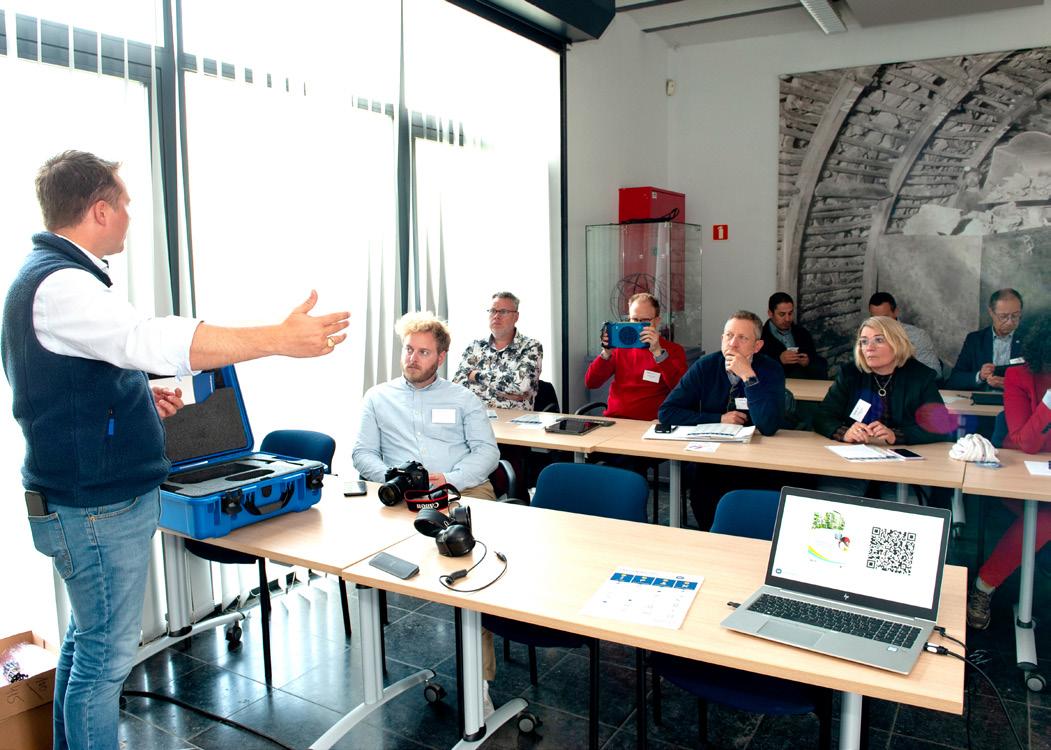
TECHNICAL TEAM OF THE YEAR

THANK
YOU TO ALL PARTICIPANTS
BEMAS would like to thank all participants of this year’s edition: Chaudfontaine, Galler and EQUANS in Wallonia, and BASF, Borealis, Chevron Phillips Chemical, DP World, Pfizer and Port of Antwerp-Bruges in Flanders. Do you also want to put your technical team in the spotlight? Sign up for next year’s edition on the BEMAS website: www.bemas.org. The technical team of DP World, winner of the Flanders audience award.
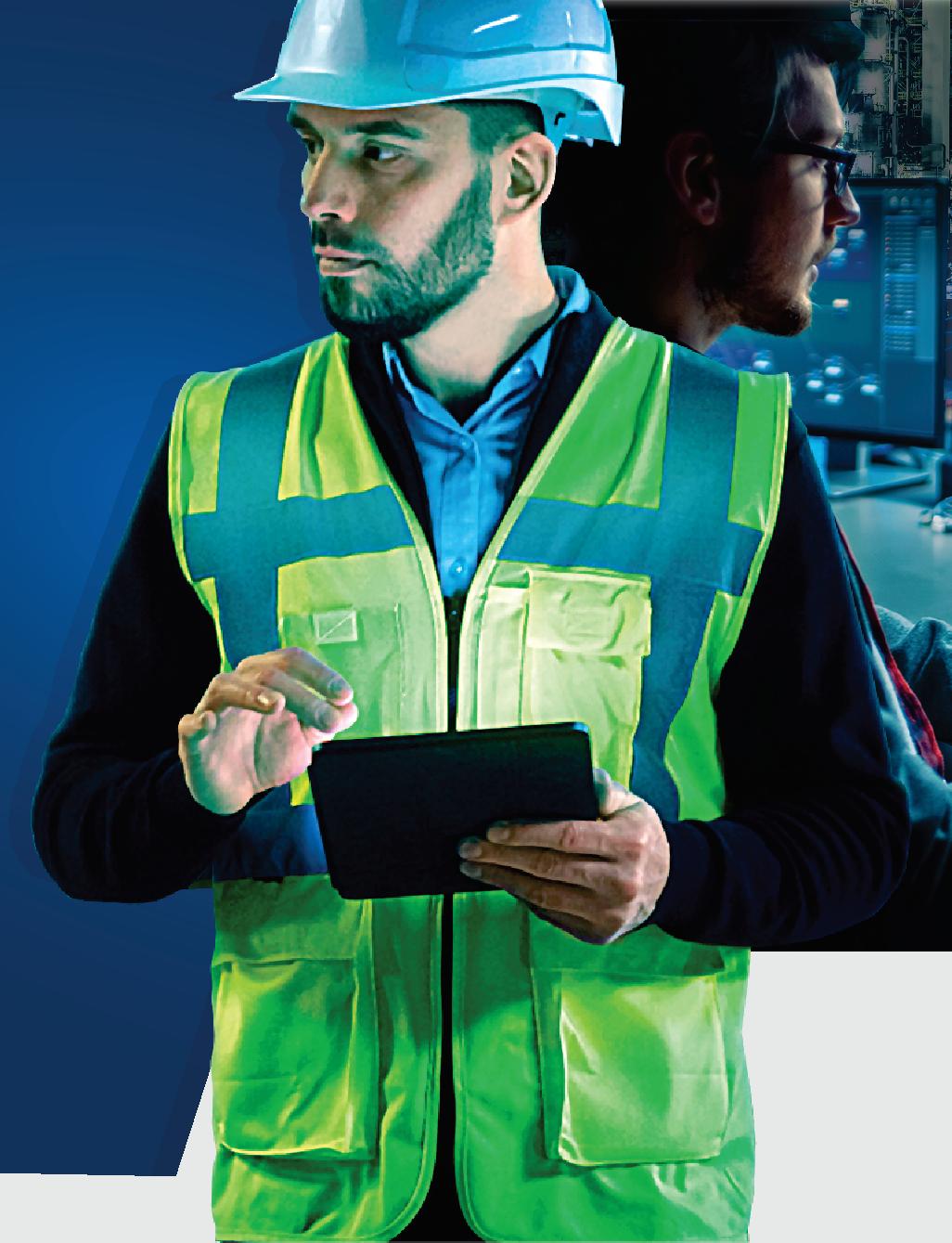
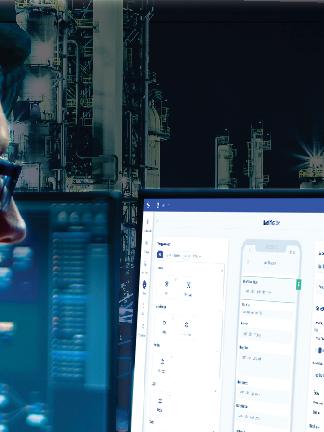

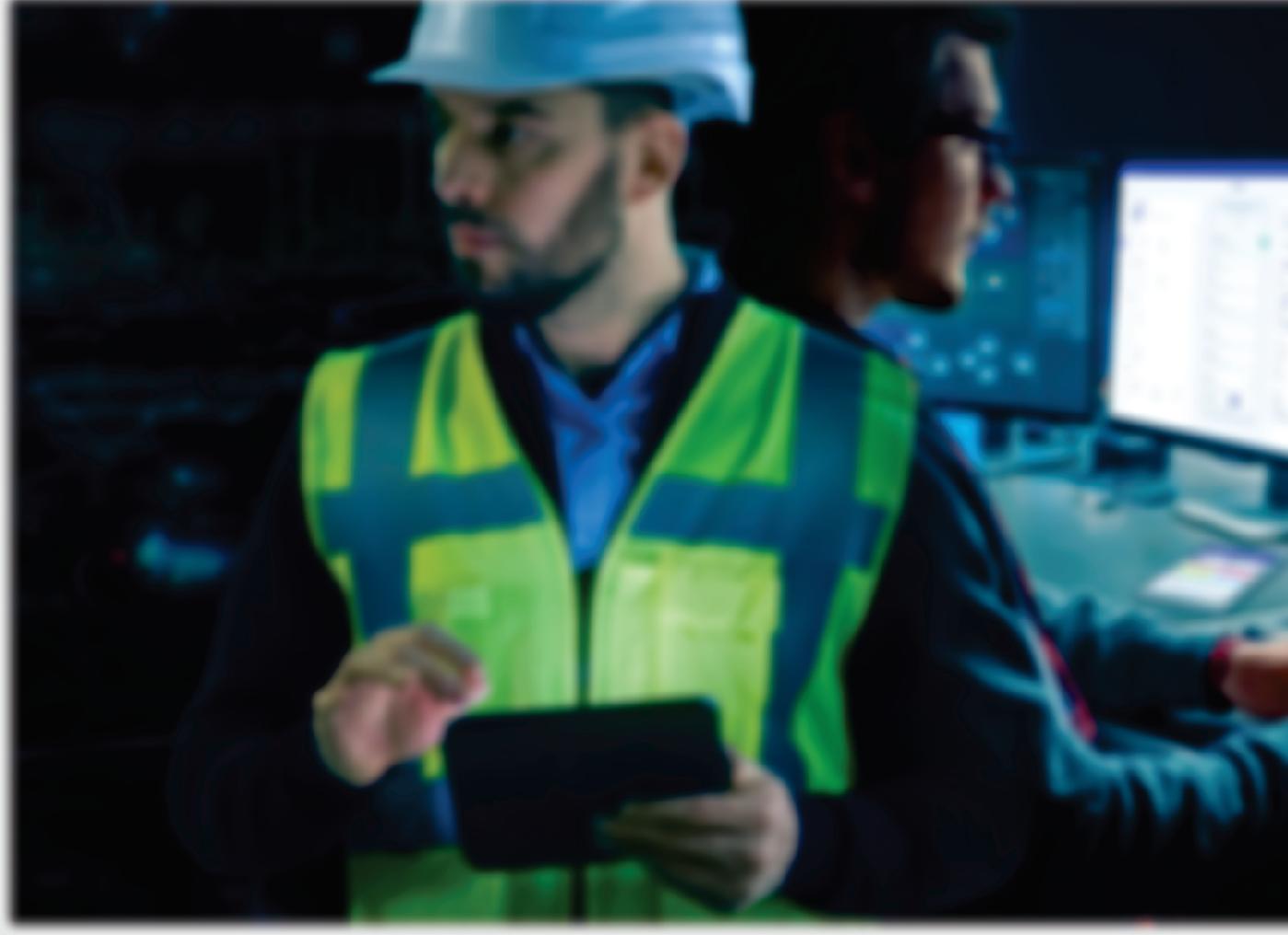
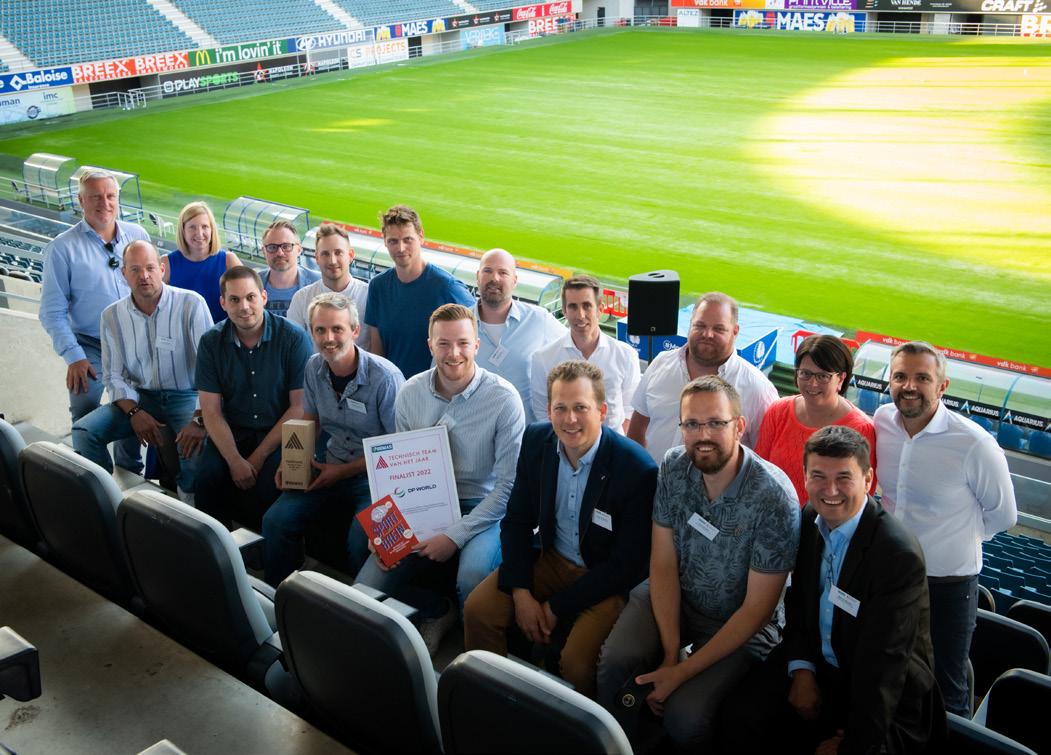
STAY UP TO DATE ON THE LATEST NEWS IN ASSET PERFORMANCE SUBSCRIBE TO THE MAGAZINE AND NEWSLETTER: www.ap-magazine.eu Independent news and insights Dedicated editorials by experts Case studies and useful practical cases AREAS OF EXPERTISE • Asset performance management • ● Asset investment planning • ● Operational efficiency • ● Reliability and condition monitoring • ● Maintenance and repair • ● Investment projects, stops and turnarounds • ● Sustainability and energy efficiency • ● Quality assurance & process control • ● Safety & integrity What is Asset talentsTheManagement?Performancesearchfortechnicalincompanieskeepyourteam www.ap-magazine.eu Asset Performance Magazine is a brand new publication that gives you insight on the fundamentals and latest trends in the world of Operations, Maintenance, Reliability and Asset TheManagement.magazine has dedicated editorials by prime experts and of course updates on best practices and innovative solutions. It also includes case studies in which you learn how organisations optimize performance of their assets while embracing digital transformation. Asset Performance also includes a news website with a monthly newsletter, keeping you up to date on the latest trends and insights.

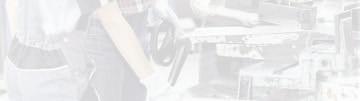
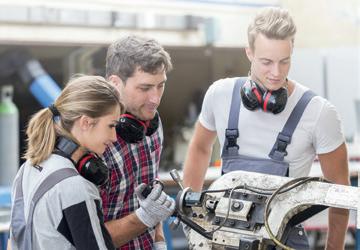
