
4 minute read
YOUR PARTNER ON THE ROAD AHEAD
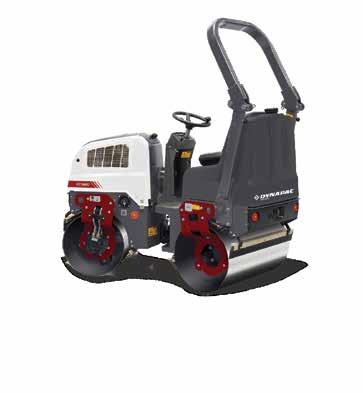
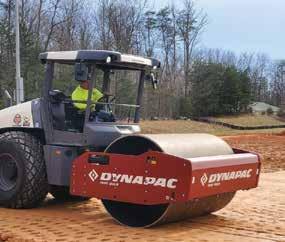
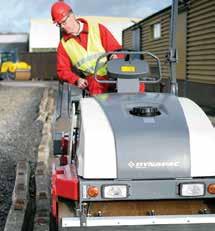
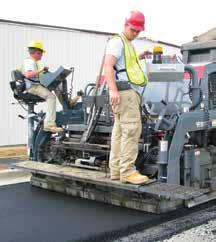
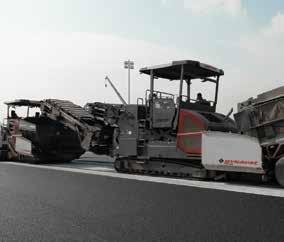
What does that mean? It means that we are determined to support you in your journey towards greater profitability, safety and environmental stewardship. It means that we will help you forge new paths, shape key trends and offer new solutions to support you on that journey. And it means we will be with you for every step of that journey through application consultancy, personalized trainings; across numerous geographic territories and around the clock.
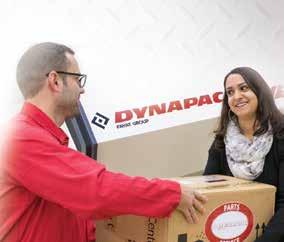
Tell us where you’re going and we will help you get there.
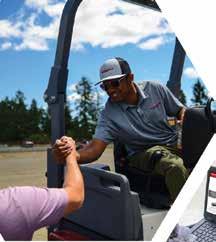
Production is what makes the money...but the safety is something that we just can’t let slide.”
By walking the plant and performing visual inspection with your camera or your clipboard or what have you, you can predict fixed plant maintenance. Powell shared a real-world example of predicting when a vital component was nearing failure.
“Approximately four years ago, I met with a well-known manufacturer of gear boxes, pillow block bearings and electric motors... They wanted to know, for me, what would help the customer better predict when a bearing, gearbox or motor would fail.
“With the current technology of transducers, I suggested that if we could build a device that would attach directly into a bearing gearbox or lower, it could send a signal that measured vibration and temperature and send it to you through the cloud or database.”
Powell wanted the plant manager or maintenance manager to receive a signal in real time—preferably via a cell phone app— if the vibration or temperature should go out of spec. After six months of implementation and discussions, Powell explained, the company developed some of the devices, as well as the app. They installed the first sensor in a gearbox along with a Gateway Bluetooth router and ethernet.
“We selected one of our toughest applications that employed a 1,200-foot by 48-inch conveyor from the pit to the secondary plant,” Powell explained. “This conveyor was driven by two $50,000 gearboxes, which failed twice in the previous two years. This plant produces 1,500 tons per hour. Downtime is not an option. After mostly success, we ended up installing 30 transducer sensors along with routers to assist in carrying the signal to the database.”
Then one week, “We received a vibration alert, and the conveyor was immediately shut down and catastrophic failure was aborted. On inspection, we discovered that a tooth had broken off in one of the gears. The gear was replaced, but most importantly, it forced us to take a look at the design of these boxes.” They figured out the boxes were “grossly undersized.”
Implement Programs That Increase Success
While saving a $50,000 component is a benefit, averting accidents and downtime through organization and efficiency is a big selling point of predictive maintenance as well. Powell reminded the audience of this in his discussion of implementing successful programs at The Rogers Group. One of those is the 5S program, and he described it as “one that every production plant needs to implement.”
“The 5S is sort, straighten, shine, standardize and then sustain,” Powell said. “As managers, when you visit your operation, do you visit the maintenance shop? Is there a place for everything and everything in its place? Do you inspect your service trucks? Are there greasy rags on the floorboard, empty soda cans on the seat or floor? Are the seats torn or ripped? Are the tools clean, sorted and in their proper places? If you sit there and honestly say all the things that I just mentioned sound like your maintenance, you can pretty much count on the rest of the operation being in the same condition.”
Powell gave the example of the plant operator contacting the maintenance department to say three belts on driving convey- or #3 just broke. This spurs a series of questions. “Is there a correct amount of V belts the correct size with the labeling stating that these belts fit conveyor #3? Does the maintenance personnel have all their PPE media in its proper place so we’ll walk right to it and put it on? Is the switch gear and control house marked indicating which disconnect powers conveyor #3? Does the service truck or job box have the necessary tools to quickly and efficiently remove the old belts and install the new? When you put a 5S program in place at your facilities, the answer to all these questions can be yes. And your downtime is drastically minimized. Sort, straighten, shine, standardize, then sustain.”
The second program Powell outlined was the equipment maintenance review (EMR), which he tethered to safety. “It’s extremely important that as you walk about your operation, that you are looking for safety issues not only to protect your employees, but also to prevent the dreaded safety violation and fines.”
He recommended taking one of your knowledgeable maintenance staff and tasking this person with walking the plant a few days a week. Have this person take pictures of anything he sees that is unsafe while documenting maintenance issues and take those pictures to the appropriate safety director or plant manager.
“It has been measured and I have confirmed that conveyors create the largest amount of downtime in all operations. Take extra care when inspecting pressure.”
From crushers, screens, conveyors, gearboxes, and so on, Powell recommended taking pictures as real evidence as you walk through the entire processing operation from beginning to end. Then, he said, go back to those iPhone pictures and transfer them to a Word document that you can share with the area or plant manager. Discuss these issues with these managers and with those who’ll schedule their resolution.
“At this point, you’re not done with this operation. Schedule a time within one month to return to this operation and follow up on the repairs that have been made or are being made.” The key is leveraging the person that understands the mechanics of how these components work and what it takes to keep them in operation. Use that person’s knowledge and expertise.
Hise summarized that with all the technologies available to the aggregate producer today, there’s no reason why an operation can’t predict failures before they occur. Aggregates managers can employ the measuring techniques, new technologies, safety protocols and more discussed at CONEXPO-CON/AGG to stay ahead of downtime occurrences.
Neil R. Hise is the chairman of the board for CEMCO, Inc., Belen, New Mexico. Ted Powell is a retired operational improvement manager of the Rogers Group Corporation of Companies. Travis Vliem is with Flexco. They presented this information at CONEXPO-CON/AGG 2023 in Las Vegas.
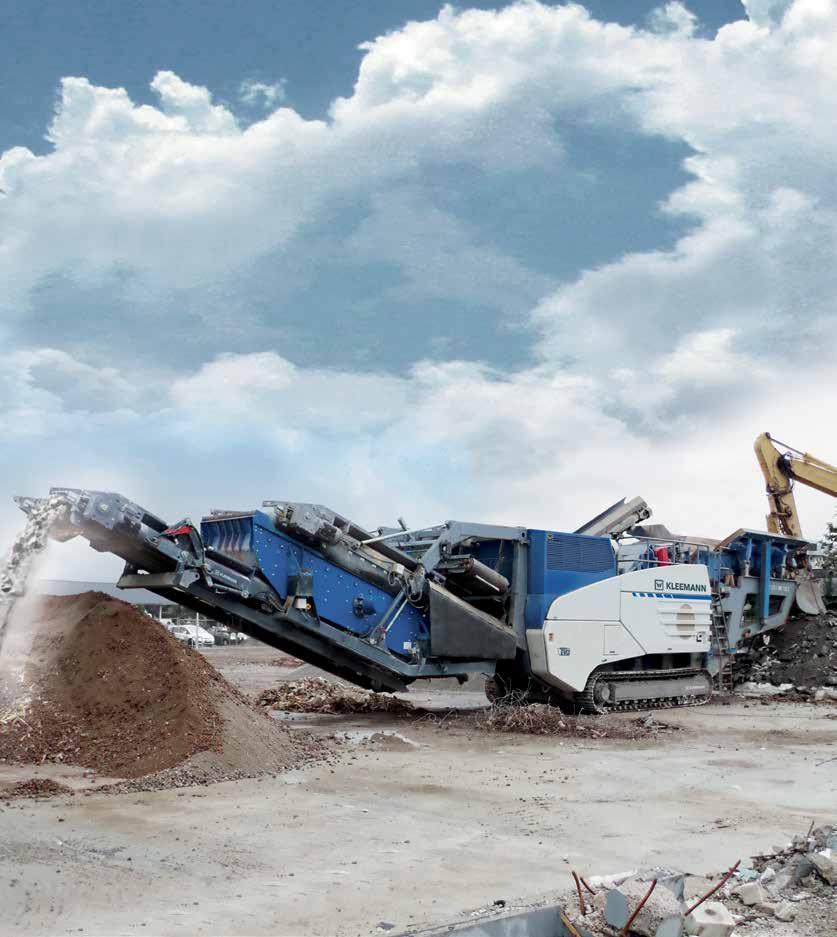