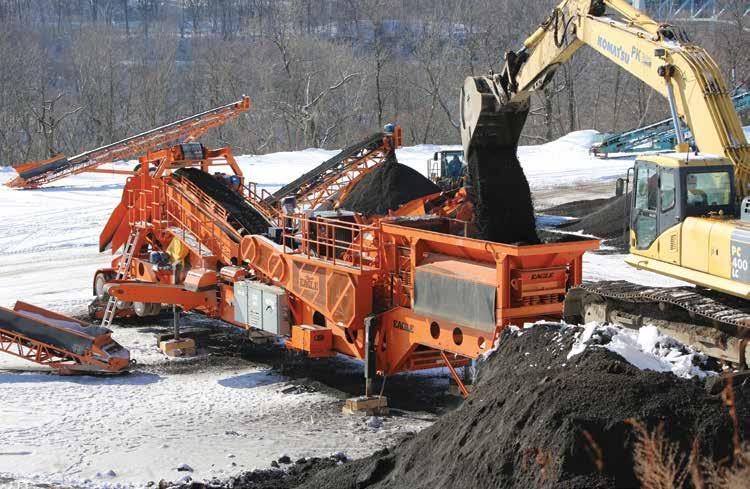
5 minute read
FIVE RECYCLE PAIN POINTS YOU CAN RESOLVE
BY DANIEL FRIEDMAN
WWhen it comes to recycle asphalt, crushing plays a significant role in the quality of the end product and in the productivity and efficiency of asphalt operations. When crushing quality, productivity and efficiency are in sync, asphalt producers may go a long way toward improving their bottom lines.
Considerations for getting the three (quality, productivity and efficiency) to align include factors such as selecting the right asphalt crushing equipment, ensuring equipment operates at peak performance, and what to do when any of these factors are out of sync.
What are some of the most common things that may impair product quality, productivity and efficiency? Eagle Crusher Company discusses five pain points that recycle asphalt producers may experience and the ways to remediate these issues to help get and keep asphalt crushing at peak capacity.
The following pain points are not in any particular order. As an asphalt producer, you may experience some, none or all of these pain points at any time throughout your years of operation. What’s important to know is that if any of these issues occur, there are solutions.
PAIN POINT #1 FOREIGN DEBRIS IN END PRODUCT
Needless to say, foreign debris is undesirable because it can compromise the quality of your end product and make it unsellable. Beyond the inability to sell your debris-contaminated hot-mix, did you also know that foreign debris can sometimes damage equipment? This includes damage to conveyor belting, pumps, screens, and other process equipment down the line, costing your operation time and money.
Ensuring clean material is important, if not mandatory. One way to keep ferrous material out of the asphalt mix is by using a magnet. Frequently, magnets used in asphalt operations are of the permanent variety without a means of self-cleaning. While they may be cheaper to install and maintain, they come with multiple disadvantages.
Investing in an electromagnet with self-cleaning ability can help ensure that the magnet is able to remove ferrous items like asphalt milling teeth or other road debris not removed prior to milling.
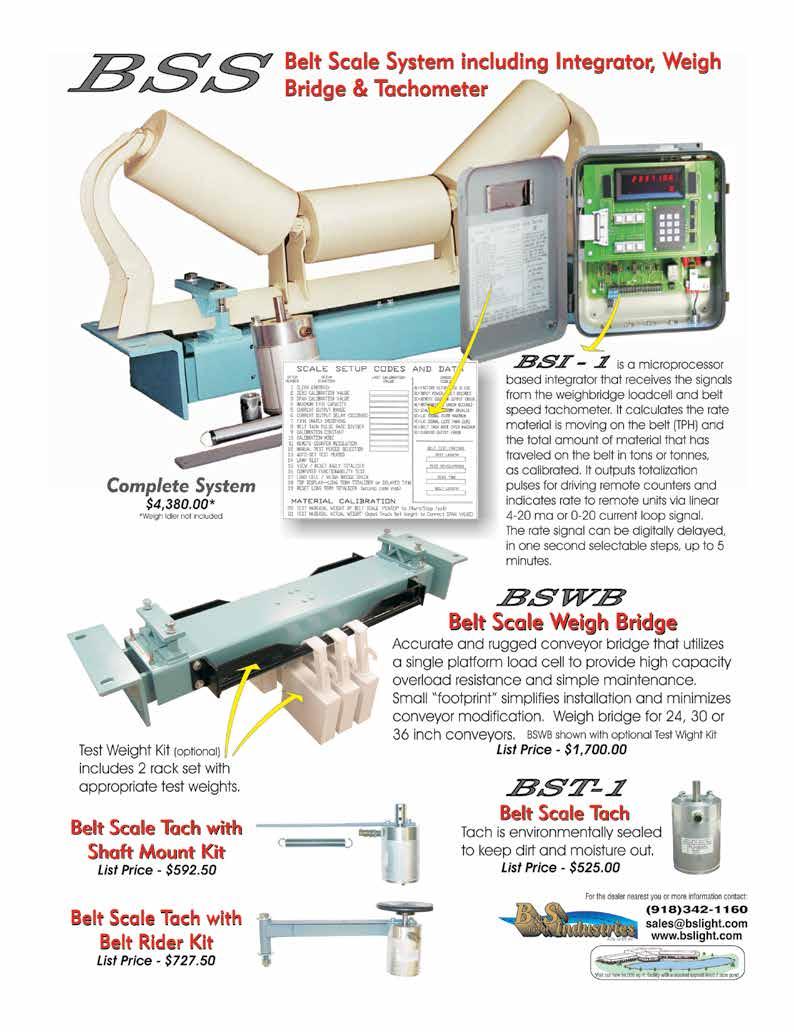
Electromagnets use an electrical current to produce a strong, deep reaching magnetic field, allowing for peak capture performance. Typically suspended over a conveyor belt in either a cross-belt or inline configuration, electromagnets pull metal through the conveyed material and remove it from the process, ensuring a contaminant-free product. Other advantages electromagnets have over permanent ones, is that electromagnets can reach out in greater distances to remove ferrous material. Unlike permanent magnets, electromagnets can also be turned off, if necessary, by stopping the electrical current. Electromagnets also have the benefit of holding or releasing on demand to provide greater control with the crushing process.
PAIN POINT #2 NOT ENOUGH SCREENING CAPACITY
The name of the game in asphalt crushing is actually screening. Most asphalt arrives onsite from milling at near-spec. This means that the crusher won’t have much work to do, as the screens will need to process through almost all of the material. If the screen is not properly sized, or if there is not adequate screening capacity, as with a pre- or reliever-deck, material can overflow.


It is important to plan your plant layout appropriately to prevent overflow of material, as well as to make considerations for future growth of your operation. This can be accomplished by multiple means. You can install grizzly bars on RAP feed hoppers to keep out the largest chunks of asphalt, you can install a pre-screen ahead of the main screen, or you can use a reliever deck on the main screen to help spread out screening across multiple decks.
PAINT POINT #3 PLUGGING OR BINDING OF SCREENED MATERIAL
Keeping screens operating at their maximum capabilities means keeping them clean. When near-spec materials are screened, there is a greater risk of plugging or binding the screen media. First, it is important to train your operators in best practices to keep material from plugging screens during production.
If the screen cloth is plugged, the operator will likely have to tap all the plugged material out of the openings, assuming the screen media can handle it. Some lighter screen media cannot handle the force of a hammer against it. Check with the screen media manufacturer for exact recommendations.
Keeping screens clean is complicated when crushing RAP, as asphalt, by its nature, is sticky. One means to prevent asphalt from binding or sticking to the screen is to ensure the media you are using is made for screening RAP.
Another way to help keep screens clear is to alter how the screen itself operates. By adjusting the amplitude or speed of the screen you may see material flow better through the screen because increasing the stroke can help reduce plugging. Of course, it is important to check the operating manual of the screen, or consult the manufacturer to ensure when limits may exist based upon the exact application.
It is also beneficial to check with the manufacturer of your screen media, as some manufacturers produce self-cleaning media to reduce or prevent plugging from occurring in the first place.
PAIN POINT #4 CONTAMINATION OF MOTORS AND ENGINES
Asphalt can be a very dusty material to work with. Coupled with the fact that asphalt can be very sticky, especially when heated, it is important to keep motors, engines, and other air-breathing components away from constant exposure to asphalt dust. This means keeping motors and engines away from screens and crushers to reduce contamination and damage from asphalt infiltration. If it is not possible to keep equipment away from the asphalt dust, it is important to keep filtration on any air inlets to reduce asphalt intake. It is also important to check on the filters frequently. Motors and engines aren’t known for their ability to work well when they are filled with hot, sticky asphalt.
PAIN POINT #5 UNEXPECTED BREAKDOWNS
No matter the type of crushing equipment your recycle asphalt operation has, if your crushing equipment is down for any reason, your operation is losing money. Regular maintenance is key to keeping crushing equipment operating at peak capacity. When issues happen to take your crushing equipment down, getting back up as quickly as possible is key.
The most important tip to avoid unexpected breakdowns is to plan and schedule regular maintenance. It can be tempting to maximize production time and thus increase revenue, but longer running time means an increased chance for unexpected breakdowns. Although diverting your labor toward maintenance might only seem like a cost with no upside, it is actually a relatively inexpensive investment toward increased production. If you don’t plan ahead by keeping critical spares on hand and devoting time toward maintenance, you can be waiting for parts, paying for expedited shipping, and paying overtime or more to make repairs when you could have just devoted a few hours a week or so toward maintenance.
After two years of testing the top asphalt rejuvenators in mixes with 40% RAP, Invigorate beat the competition by 300%.
For more information on the results, call us at 1-888-663-6980.
In summary, having remediations for some of asphalt producers’ common pain points in your back pocket, can help your operation avoid lost productivity and poor quality end product. What is just as important, is selecting the right asphalt plant, overall, for your crushing needs. The right plants can go a long way toward meeting the quality, productivity and efficiency that will help your operation meet its profitability goals.
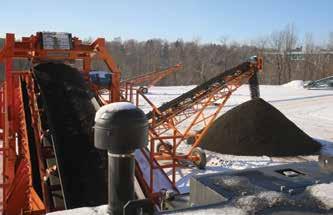
Look for plants designed to produce clean, highly uniform, cubicle spec product with a minimum of white rock and a minimum of fines to ensure product quality and consistency. Consider plants that in addition to superior crushing capabilities, also have precise screening capabilities, utilizing pre-screen feeders or reliever decks, to increase productivity, while reducing equipment wear.
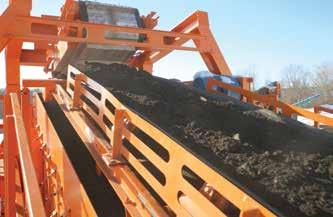