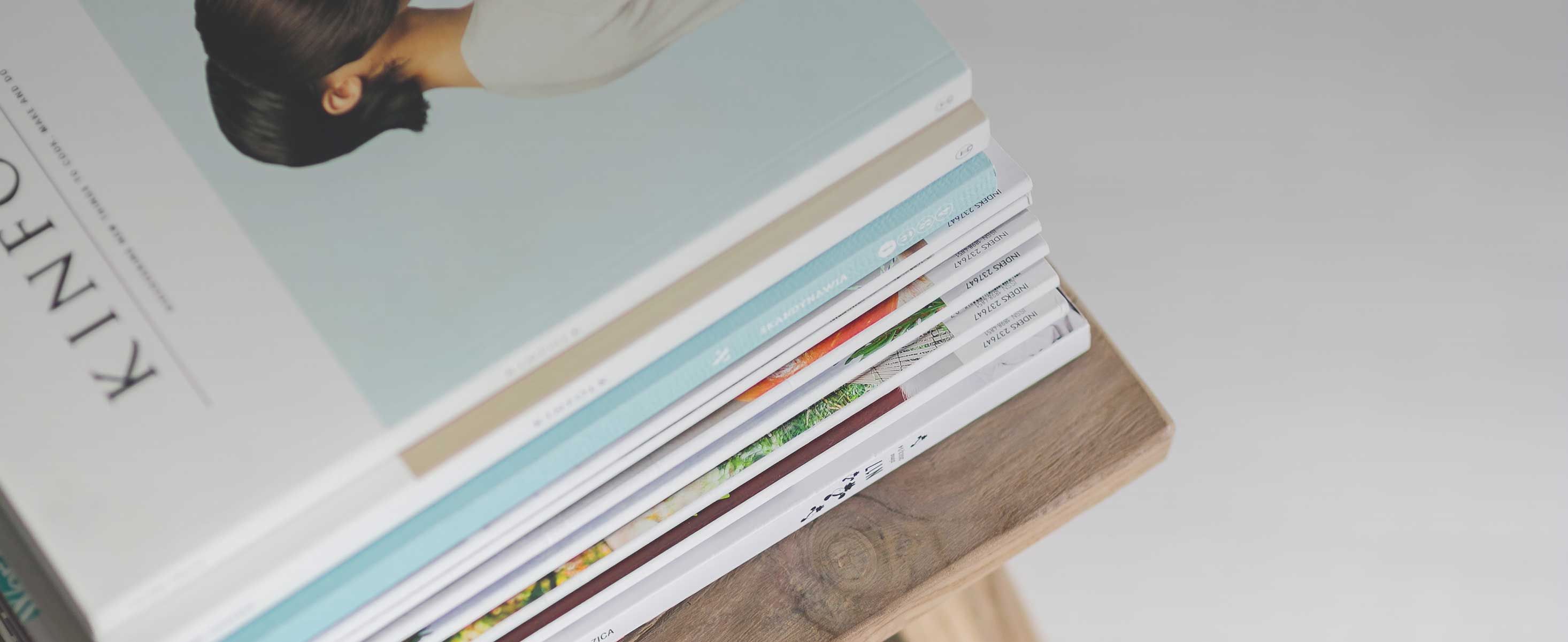
3 minute read
MAINTAIN IT BEFORE IT BREAKS
Using predictive maintenance to keep crushing, production equipment up
BY NEIL R. HISE, TED POWELL
DDuring CONEXPO-CON/AGG 2023, Neil Hise, Ted Powell and Travis Vliem shared with an audience of aggregates producers and other interested contractors how to perform predictive maintenance at the crushing operation. Hise pointed out this is not only a wonderful industry, but it’s also a dangerous industry if you aren’t staying aware of your surroundings and your equipment. “You can't afford to make very many mistakes,” Hise told the attendees of the Predictive Maintenance: Plan the Work and Work the Plan education session.
Hise shared that while crushing and processing rock may not have changed over the past 100 years or so, issues with the supply chain have changed recently. He spoke not only of measuring and tracking your parts and components for uptime and efficiency, but also of planning ahead on maintenance for uptime and efficiency.
Measure To Manage
“And the word of the day is ‘measure,’” Hise said. You measure what your conveyor belt has on it. “What does your screen have on it? You measure what your VSI is doing and what your wash plant has done.”
He stressed the importance of measuring and knowing your production numbers. Armed with actual measurements and numbers, the savvy groundman or quarry manager can track belt and component wear and react to a situation before it creates a hazard for a Mine Safety and Health Administration (MSHA) inspector to notice or for a surprise downtime occurrence.
“We measure everything in our production and our manufacturing process,” Hise shared. “But for our production plants... if you don’t communicate effectively and specifically,” the measuring won’t help you prevent mistakes. You want to communicate what’s going on around your production process in order to prevent problems. In other words, effective communication goes hand in hand with measuring to get predictive maintenance up and running in your operation.
Consider a crushing plant that has fines and material buildup under a conveyor transfer point. If the buildup is starting to look like a mini stockpile is growing to reach the conveyor belt, you have a problem that should have been noticed by a groundman, communicated to the maintenance personnel, and resolved before a safety hazard developed. As Hise said, sometimes these maintenance issues develop because someone in the production chain wasn’t paying attention.
“Because of lack of communication, lack of awareness and lack of [caring].” He suggested looking at maintenance as a continuing job and not something that can be a one-and-done.
Powell led the audience through a real-life scenario of how The Rogers Group put in place a program that took the company’s fixed plant production facilities from 75% availability to 92% availability “in a few short years.” He started with Hise’s word of the day: measuring.
“Number one: Identify pieces of equipment and components that have moving or maintainable parts by assigning them asset numbers,” Powell said. “Assign them modes of operation that will track the hours the component worked. The plant manager then reports the total up- and down-hours of production by hours of operation for that particular day of operation. After this information is placed into a database, the hours for each component will be tracked and service will be performed per manufacturer’s specifications.”
Tracking actual operation leads to automating maintenance. Powell shared that he used a simple Excel spreadsheet and common software used in the industry to model every single plant component, assigning existing or new asset numbers to the parts. Then he, or the companies’ IT departments, developed a program to track the usage of the assets in the flow of their processing plants.
“Every aggregate company requires a daily report of productive and downtime hours and records them on daily and weekly basis. In our plan, this information is used to populate—by the hours worked—each asset’s usage in real time, which can be automated with the proper hardware and software.” He recommended using the equipment manufacturers’ recommended hours for service sampling and maintenance for the components of each of these assets, such as gearboxes, bearings, screens and crushers.
“Develop preventive maintenance sheets for every asset from the manufacturer’s recommendation,” Powell advised. “Crushers, screens, conveyors, screws, pumps, dryers, drums. I know this seems like a lot of maintenance sheets. But a conveyor is a conveyor. One sheet covers them all.”
Powell pointed out that with all this new information you’ll be able to gather by tracking equipment usage, you’ll be able to employ a multitude of new technologies that you can use to measure how these pieces of equipment are performing.
Hise shared another way to gather this information: physical inspection. “Take your camera and walk through your plant,” Hise told the audience. “You document and you measure. And if you’re the manager of the plant, you assign a fix to someone. And if you’re not the manager of the plant, you go to the manager of the plant and say, ‘I walked through my plant, here’s what I've documented, and this needs to be fixed.’ And if your manager doesn't appreciate your efforts then shame on him. But let me tell you, the safety of each one of you in the plant is paramount.