
14 minute read
Parâmetros do fresamento helicoidal e seus efeitos sobre a qualidade de furos em aço ABNT 4340
A operação de fresamento helicoidal é uma alternativa para obtenção de furos acabados ou desbastados, com perfis variados, usando apenas uma ferramenta de corte (fresa), permitindo assim, reduzir o número de setups e, consequentemente, o tempo de máquina parada. A capacidade do processo é avaliada por fatores como qualidade da superfície e tolerâncias dimensionais. O objetivo principal da presente investigação é realizar um estudo experimental sobre a qualidade de furos produzidos em aço de baixa liga ABNT 4340 no estado recozido por meio da operação de fresamento helicoidal. Os testes experimentais foram realizados em um centro de usinagem usando uma fresa intercambiável como ferramenta de corte sob condições a seco, com o objetivo de investigar o efeito dos parâmetros do processo de fresamento helicoidal (a velocidade de corte, avanço, penetração de trabalho e sentido de corte) sobre a rugosidade da superfície do furo e os desvios geométricos e dimensionais. Os resultados mostraram que a velocidade de corte e o avanço foram os parâmetros mais influentes sobre a rugosidade e os de maior impacto sobre a circularidade e cilindricidade dos furos.
Oprocesso de usinagem é um dos mais utilizados para fabricação de produtos pela indústria manufatureira (5) e a operação de furação é o processo de usinagem mais utilizado para obtenção de furos (8) . Tönshoff et al. (1994) (13) destacam que “a furação é a operação de usinagem mais importante para a obtenção de furos e representa 25% do tempo de ciclo e 33% do número total de operações”. Wang et al. (2015) (14) no seu estudo relatam que a furação representa ainda cerca de 50% do processamento total em usinagem, além de ser uma das últimas operações na fabricação de uma peça, exigindo confiabi - lidade devido ao alto valor agregado relacionado às usinagens anteriores. No entanto, Pereira et al. (2017) (8) afirmam que a operação de furação apresenta várias desvantagens, tais como altas cargas sobre a peça na direção axial, elevada força de avanço, formação de rebarbas, risco de quebra do material da peça na saída do furo, deformação da periferia do furo, difícil evacuação de cavacos, difícil dissipação de calor, baixas tolerâncias dimensional e geométrica, qualidade superficial ruim e possibilidade de falha catastrófica da ferramenta. Consequentemente, a furação convencional está associada a retrabalho e a custos adicionais e muitas vezes existem inúmeros obstáculos para concluir o processo de forma econômica. Pereira et al. (2017), Bitner (2002) e Wenda (2009) (8, 1 e 15) destacam que o consumo de potência é frequentemente uma preocupação para se obter furos de grandes diâmetros, especialmente em máquinas-ferramentas mais comuns com potência inferior a 15 kW. Estes fatos criaram a demanda por um método mais suave de fazer furos e que venha atender a todos os requisitos de projetos, além de se manter competitivo. Este trabalho apresenta aspectos da operação de usinagem conhecida como fresamento helicoidal ou fresamento por interpolação, uma operação alternativa à furação, considerada por Longo (2009) (4) um dos processos com fresa mais poderosos, pela versatilidade da operação na indústria manufatureira. Além disso, o fresamento helicoidal se enquadra nos conceitos de Indústria 4.0 por reduzir o número de setups de ferramentas e, consequentemente, o tempo de máquina parada (15) .
Tiago Junio Augusto da Silva (tjas@ufmg.br); Diogo Azevedo de Oliveira (diogoazev@yahoo.com.br) e Alexandre Mendes Abrão (abrao@ufmg.br) são pesquisadores do Programa de Pós-Graduação em Engenharia Mecânica da Universidade Federal de Minas Gerais (UFMG). Este artigo foi apresentado no XXIV Colóquio de Usinagem da Pontifícia Universidade Católica do Paraná (PUCPR), realizado em Curitiba (PR), entre 25 e 27 de maio de 2022. Reprodução autorizada pelos autores.
Segundo Morales et al. (2020) (6), o fresamento helicoidal é um processo misto, composto pelo fresamento periférico (movimento circular) e pela furação (movimento axial). No fresamento helicoidal, os furos são obtidos por meio da combinação do movimento de rotação da ferramenta com sua translação ao longo de uma trajetória helicoidal.
Neste trabalho foi utilizado o processo de fresamento helicoidal em um centro de usinagem e a cinemática do processo é apresentada destacando os parâmetros de programação CNC. A obtenção de furos de diferentes diâmetros é realizada sem o uso de fluido de corte e sem pré-furo (em cheio), usando como ferramenta de corte uma fresa de topo com pastilhas intercambiáveis. O projeto expe - rimental investiga os efeitos das variáveis de entrada (velocidade de corte, avanço por dente, penetração de trabalho e do sentido de corte) sobre a qualidade dos furos produzidos em aço de baixa liga ABNT 4340 recozido, em termos de rugosidade, circularidade e cilindricidade.
Fresamento helicoidal
O fresamento helicoidal é uma técnica avançada de fresamento que pode ser uma alternativa útil e versátil à furação quando se trata de fazer furos de alta qualidade. Com a finalidade de criar um furo a partir de um sólido ou para abrir um furo existente, a operação de fresamento helicoidal é comumente realizada em uma máquina CNC de 3 eixos (3). Quando realizada com dispositivos específicos e robôs industriais, a operação é geralmente chamada de furação orbital(8). Morales et al. (2020)(6) destacam que atualmente a fresagem helicoidal se posiciona como uma boa alternativa ao processo convencional para furação de materiais de difícil usinagem. Especificamente em relação ao fresamento helicoidal, furos de qualidade satisfatória podem ser obtidos sem operações subsequentes, mesmo em materiais de difícil usinabilidade (8) . Assim, a aplicação da fresagem helicoidal tem sido difundida na fabricação de componentes em várias indústrias, tais como aeroespacial, automotiva, indústrias de energia e de equipamentos de escavação (11) A operação de fresamento helicoidal é uma variação do processo de fresamento alternativa aos processos de furação. No entanto, se diferencia e muito devido à sua cinemática. Enquanto na furação convencional o furo é produzido por meio do movimento de rotação entre a ferramenta e a peça e continuado pelo movimento de avanço da ferramenta, na interpolação helicoidal o furo é gerado mediante a rotação da ferramenta em torno do seu próprio eixo numa trajetória helicoidal, que inclui o avanço axial e o movimento de revolução ao redor do eixo do furo (9) . Devido à sua cinemática flexível, Pereira et al. (2017) (8) destacam que o processo de fresamento helicoidal gera baixas forças de corte, permite avaliar a evolução do desgaste da ferramenta, possibilitando assim correções dimensionais, e ainda permite obter furos de formas complexas e com diferentes diâmetros com a mesma ferramenta.

Cinemática do fresamento helicoidal Segundo Morales et al. (2020) (6), o fresamento helicoidal é um processo misto, composto pelo fresamento periférico (movimento circular) e pela furação (movimento axial). No fresamento helicoidal, os furos são obtidos por meio da combinação do movimento de rotação da ferramenta com sua translação ao longo de uma trajetória helicoidal. O estudo do fresamento helicoidal passa pela compreensão da cinemática da operação. Além disso, deve-se ter em mente que informações sobre a cinemática da operação devem ser programadas em máquinas com comando numérico computadorizado (CNC) e a forma como essas informações devem ser inseridas deve ser levada em consideração (Wenda, 2009). Costa et al. (2009) destaca que nos centros de usinagem CNC, pode-se tirar enorme vantagem da interpolação de controle, uma vez que a maioria destas máqui nas tem ciclos automáticos para este fim. A trajetória helicoidal da fer- ramenta é mostrada na figura 1 e é obtida controlando-se a velocidade axial da ferramenta sincronicamente com o movimento planetário no plano seccional (XY).
A nomenclatura dos parâmetros e as equações do processo são apresentadas na figura 1, em que são destacadas por Pereira et al. (2017) (8) e Costa et al. (2009) (2) o diâmetro final do furo (Db), limitado a duas vezes o diâmetro da fresa (Dt), a ser determinado pela combinação do diâmetro da hélice (Dh), conforme a equação 1, podendo assim alcançar diversos valores finais com apenas uma fresa. Partindo desses diâmetros e da decomposição do passo helicoidal, pode-se definir os parâmetros essenciais deste processo, tais como velocidade de corte (vc) velocidade de avanço (vf), profundidade de usinagem (ap) e penetração de trabalho (ae); conforme a equação2, velocidade de avanço tangencial por dente (vft), conforme a equação 3, o número de dentes da fresa (z), e o número de rotações por minuto (n), calculado conforme a equação 4, sendo f z o avanço por dente.
Metodologia
O objetivo deste trabalho é investigar os efeitos das variáveis de entrada velocidade de corte, avanço por dente, penetração de trabalho e sentido de corte sobre a qualidade dos furos produzidos em aço de baixa liga ABNT 4340 recozido (dureza média de 160 HV) em termos de rugosidade, circularidade e cilindricidade do furo. Este estudo experimental usa como ferramenta de corte uma fresa Sandvik Coromant R390025A25-17L (diâmetro de 25 mm com 2 dentes) com pastilhas de metal duro Sandvik Coromant R390-17 04 08M classe ISO-PM 1030. Os experimentos foram realizados com uma réplica e sem uso de fluido de corte. A fixação da ferramenta se deu por meio de um mandril porta-pinça MAS 403-BT 40. O planejamento experimental elaborado avaliou o efeito das variáveis independentes velocidade de corte (vc), avanço por dente (fz) e sentido de corte (concordante ou discordante) em dois níveis e penetração de trabalho (ae) em três níveis. Os valores utilizados foram: vc=110 e 180 m/min, fz=0.05 e 0.15 mm/rev e ae=17,30 – 21.15 e 25 mm. A profundidade de usinagem (ap = 0,75 mm) foi mantida em todos os testes. As variáveis investigadas foram rugosidade, circularidade e cilindricidade. Os corpos de prova têm dimensões iniciais de Ø152.4 x 25 mm e foram preparados em um torno CNC Romi Centur 30S e no centro de usinagem Romi Discovery 560, onde também foram realizados os ensaios experimentais. As figuras 2(a) e 2(b) mostram, respectivamente, um corpo de prova montado na placa de quatro castanhas sobre a mesa do centro de usinagem e a fresa montada no mandril porta-pinça.
Furos com diâmetros de 34,6 mm, 42,3 mm e 50 mm foram executados com uso da função TURN do comando Siemens 810D, abrangendo assim toda a faixa de penetração de trabalho da fresa de 25 mm. Para reduzir a influência do desgaste da aresta de corte durante os testes, as pastilhas de metal duro foram substituídas após a remoção de aproximadamente o mesmo volume de material para cada par de arestas montado na fresa.
A medições das rugosidades das paredes dos furos foram realizadas com o rugosímeto Taylor Hobson Surtronic 25. As medições foram realizadas dentro do comprimento de amostragem de 2,5 mm em duas regiões diferentes. Ao final, o valor médio de medições foi calculado e considerado como o desvio aritmético médio da superfície (parâmetro Ra) do furo usinado. Já as medições de desvios de forma (circularidade e cilindricidade) foram efetuadas em máquina de medição por coordenadas Tesa Micro–Hite 3D, de operação manual. Nas medi - ções dos desvios de circularidade a Tesa Micro–Hite 3D utilizou 8 pontos e para os desvios de cilindricidade foram utilizados 10 pontos. Para as medições do erro de circularidade foram feitas medições nas seções de entrada e saída dos furos, pois Pereira et al. (2017) (8)citam diversos estudos onde é verificada uma diferença de circularidade na entrada e saída do furo. Desta forma este estudo considera o valor médio de circularidade do furo obtido.
Resultados
As medições de rugosidade, circularidade e cilindricidade foram analisadas com o uso do software
Minitab versão 18.1. A partir dos dados obtidos foram elaborados gráficos de efeitos principais e a análise de variância (ANOVA), considerando um nível de significância de 5 %, conforme pode ser observado na figura 3. Os resultados de rugosidade – vide figura 3a – , mostram que a rugosidade diminuiu para velocidades mais altas de corte, e também houve redução da rugosidade para valores menores do avanço por dente, únicos parâmetros considerados estatisticamente significativos. Machado et al. (2015) e Saadatbakhsh et al. (2017) (5, 11) salientam que a velocidade de corte mais alta provoca o aumento da temperatura, o que causa a redução da tensão de escoamento do material da peça, facilitando a deformação plástica e reduzindo o atrito e as forças de corte. Com valores maiores de avanço por dente, a rugosidade da superfície tende a aumentar pois, segundo os autores, o incremento do avanço aumenta a distância entre picos e vales na topografia do perfil e também altera a forma do cavaco; consequentemente há um aumento das forças de corte. Já os resultados de circularidade mostrados na figura 3b indicam que a velocidade de corte foi o único parâmetro significativo e com o acréscimo da velocidade de corte teve um efeito negativo sobre este desvio. Isso pode ser atribuído ao fato de que o aumento da velocidade de corte é obtido por meio da elevação da rotação, e isso elevou os valores de vibrações, além do fato de que o aumento da velocidade de corte reduziu a espessura do cavaco (5) . Por fim, os resultados de cilindricidade apresentados na figura 3c indicam que o avanço por dente foi o único parâmetro significativo: o incremento do avanço por dente afeta positivamente este desvio, segundo Machado et al. (2015)(5); com o aumento do avanço a taxa de remoção é aumentada, o que reduz a banda de cisalhamento termoplástico. Além disso, o incremento do avanço faz com que a pressão específica de corte diminua. A penetração de trabalho não teve influência significativa sobre as variáveis dependentes estudadas. Porém, a observação dos gráficos de efeitos principais da figura 3 sugere que as melhores respostas das variáveis dependentes ocorreram quando se testou (ae =17,3 e 25,00 mm). Com de ae =17,3 mm é verificado um menor desvio dimensional, possivelmente devido ao fato de reduzir a trajetória helicoidal (8). Já com ae = 25,00 mm, melhores resultados de rugosidade são alcançados, pois isso facilitou o escoamento do cavaco para fora do furo (8) . O sentido de corte também não teve impacto nos resultados, porém se observam nos gráficos melhores resultados quando se trabalha com sentido discordante, o mesmo que foi verificado por Pangrácio (2003) (7). Por outro lado, Morales et al. (2020) (6) identificaram o sentido concordante como melhor estratégia, logo são necessários novos testes para uma avaliação conclusiva.
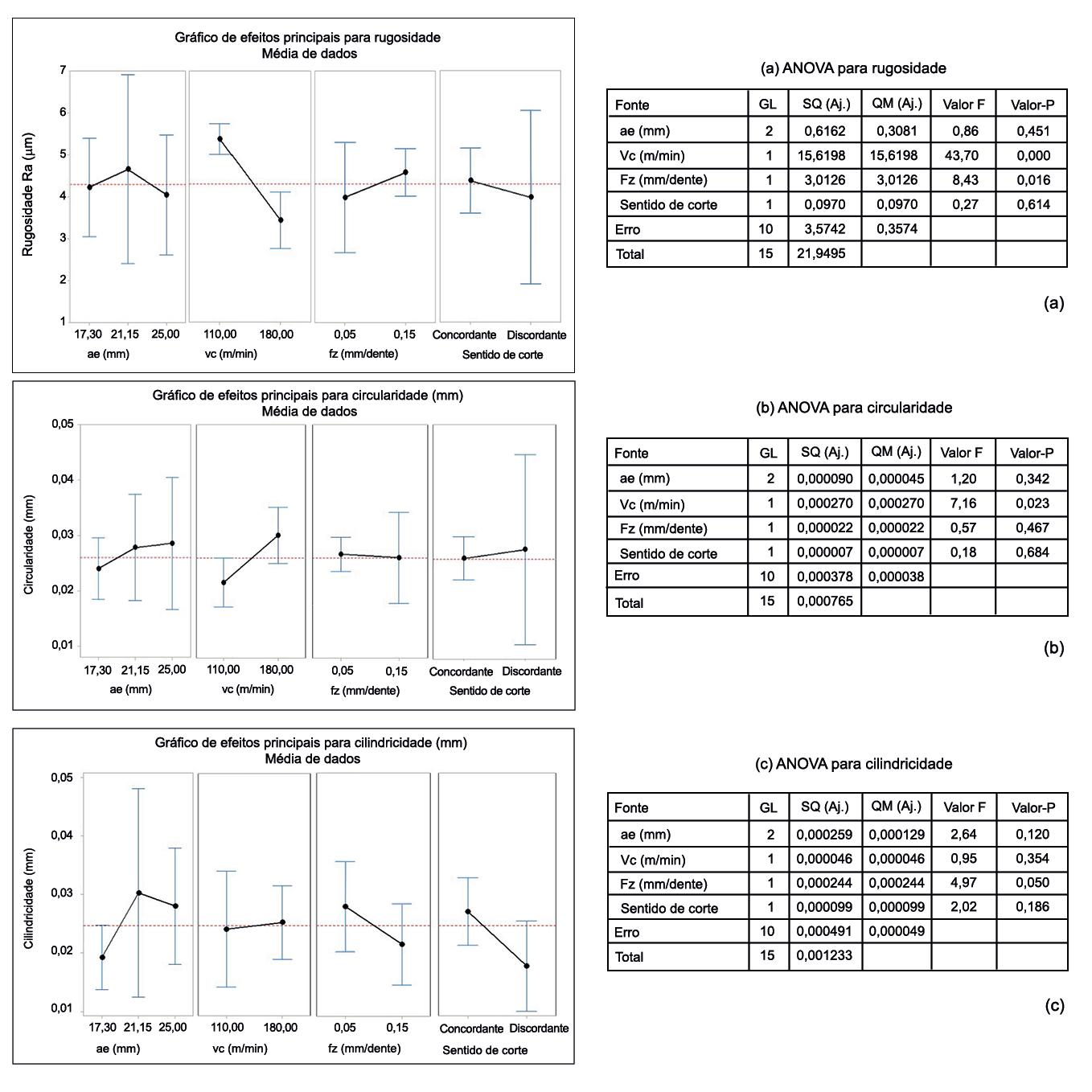
Conclusões
No presente estudo, a operação de fresamento helicoidal foi aplicada à furação a seco do aço ABNT 4340 recozido. Os efeitos dos parâmetros de corte da operação fresamento helicoidal avaliados sobre a qualidade dos furos foram velocidade de corte, avanço por dente, profundidade de penetração e do sentido de corte. Os principais resultados alcançados foram os seguintes:
• A velocidade de corte e o avanço por dente influenciaram estatisticamente o desvio aritmético médio. O valor de Ra diminuiu para velocidades de corte maiores, e também houve redução do Ra para valores menores do avanço por dente.
• A velocidade de corte foi o único fator estatisticamente significativo sobre a circularidade e a elevação daquele causou o aumento deste.
• O avanço por dente foi o único fator estatisticamente significativo sobre a cilindricidade e a elevação daquele causou a redução deste.
• A penetração de trabalho e o sentido de corte não apresentaram influência estatisticamente significativa (para um nível de significância de 5 %) sobre a rugosidade, circularidade e cilindricidade dos furos produzidos por fresamento helicoidal.
Responsabilidade pelas informações
Os autores Tiago Junio Augusto da Silva, Diogo Azevedo de Oliveira e Alexandre Mendes Abrão são os únicos responsáveis pelas informações incluídas neste trabalho.
1) Bitner, M., 2002, Interpolation is a fast, low-horsepower way to make larger-diameter holes, Dapra Milling tools. 20 Dez. 2021, <https:// www.dapra.com/articles/helicalinterpolation>.
2) Costa, D., et al., 2009, Análise cinemática do processo de fresamento
Referências
helicoidal, 6º Congresso Brasileiro de Engenharia de Fabricação, Caxias do Sul, Brasil, 05 Jan. 2022,<http:// www.labusig.ufpr.br/projetos/FHI_ COF11- 0085.pdf>.
3) Hendley, N., 2018, Making holes with helical interpolation, Canadian Metalworking. 15 Dez. 2021, <https:// www.canadianmetalworking.com/ canadianmetalworking/article/ cuttingtools/making-holes-withhelical- interpolation>.
4) Longo, C., 2014, Caracterização da integridade de aço carbono usinado pelo processo de fresamento, XVII Encontro de Jovens Pesquisadores da UCS, Caxias do Sul, Brasil, 15 Dez. 2021, <https://www.ucs.br/ucs/ pesquisa/jovenspesquisadores2009/ trabalhos/poster/e_CarinaLongo.pdf>.
5) Machado, A. R., Abrão, A. M., Coelho, R. T. e Silva, M. B., 2015, Teoria da usinagem dos materiais. 3.Ed. Blucher, São Paulo, Brasil, 407p.
6) Morales, F. J. P et al., 2020, Study of the influence of helical milling parameters on the quality of holes in the UNS R56400 Alloy, MDPI, V.10, 09 Dez. 2021, <https://www.mdpi. com/2076-3417/10/3/845/htm>.
7) Pangrácio, L. M., 2003, Análise da qualidade de furos realizados por fresamento helicoidal interpolado, Dissertação (Mestrado em Engenharia Mecânica), Setor de Tecnologia, Universidade Federal do Paraná, Curitiba, Brasil, 83f.
8) Pereira, R. B. D. et al., 2017, A review Of helical milling process, International Journal of Machine Tools and Manufacture. V. 120, pp. 27-48. 09 Jan. 2021, <https://www. sciencedirect.com/science/article/pii/ S0890695517300706>.
Referências
9) Rodrigues, V. F. S., 2018, Otimização robusta do fresamento helicoidal para o alargamento de furos em alumínio 7075, Dissertação (Mestrado em Ciências em Engenharia de Produção), Pós-Graduação em Engenharia de Produção, Universidade Federal de Itajubá, Itajubá, Brasil, 131f.
10) ROMI, S/A., 2005, Romi Linha Discovery: Instruções de operação, Ed. Divisão de Comercialização, São Paulo, Brasil 88f.
11) Saadatbakhsh, M., et al., 2017, Experimental study of surface roughness and geometrical and dimensional tolerances in helical milling of AISI 4340 alloy steel, Int J ADV Manuf Technol, V. 93, pp. 4063 –4074, 09 Fev. 2022, <https://sci-hub. se/10.1007/s00170-017-0782-3>.
12) Sandvik, 2020, Ferramentas rotativas: Coromant. 01 de Ago. 2020, <https://tibp.blob.core. windows.net/coromant/cbcca2f25db1-489b-8abc-a9fe47393a2c. pdf?sv=2014-02- 14&sr=b&sig=PC HVI236wsYb5syZj9fZ5xfaBy%2BR7 iB0vaGeDC0e4xk%3D&st=2020-08-
09T23%3A07%3A33Z&se=2030-0807T23%3A12%3A33Z&sp=r&rsct=ap plication%2Fpdf&rscd=inline%3B%20 filename%3Dc-2900-28.pdf>.
13) Tönshoff, H.K., et al., 1994, Machining of holes: developments in drilling technology, International Journal of Machine Tools and Manufacture. V.43, pp. 551-561.18 Mar, 2022, <https://www. sciencedirect.com/science/article/pii/ S0007850607605010>.
14) Wang, H., et al., 2015, Machinability analysis on helical milling of carbon fiber reinforced polymer, Journal of Advanced Mechanical Design, Systems, and Manufacturing.V.9, nº5, 18 Mar. 2022, <https:// www.jstage.jst.go.jp/article/ jamdsm/9/5/9_2015jamdsm0057/_ pdf/-char/en>.
15) Wenda, J., 2009, Avaliação de furos obtidos por fresamento helicoidal sob diferentes condições de usinagem, TCC (Engenheiro Mecânico), Graduação em Engenharia Mecânica, Universidade Federal do Paraná, Curitiba, Brasil, 14f.
Serviços para a indústria metalmecânica com unidade situada em Caxias do Sul (RS), fornece linhas de máquinas de eletroerosão a fio e acessórios, assim como serviços que abrangem assistência técnica e treinamento para clientes. A companhia tem em seu portfólio séries de equipamentos de eletroerosão a fio que contam com sistema de inserção e recolhimento automático do fio de corte, além de sistema de filtragem. Os equipamentos, recomendados para a confecção de peças metálicas com design complexo, por exemplo, se dividem em versões que apresentam mesa HRC de 50º e tanque fabricado em aço inox. Há modelos de máquinas que contam com painel com tela sensível ao toque (touch screen), com textos em português.

A Açovisa ( Guarulhos, SP) é a nova gerenciadora de serviços fornecidos na planta industrial do Grupo Bardella, situada no mesmo município. A nova direção tem como premissa o aumento do leque de serviços para o setor metalmecânico, o que inclui, por exemplo, usinagem e soldagem de aços, assim como caldeiraria, trefilação e jateamento. Segundo informações fornecidas à imprensa, oferecer espaço para empresas da cadeia produtiva de aços no centro de serviços também está nos planos da Açovisa, que passou a ser a proprietária da planta industrial. A ideia é disponibilizar os espaços para locação, os quais poderão ser usados por fornecedores, prestadores de serviços, entre outros. Ainda de acordo com a companhia, esta é uma das etapas de um plano de expansão do centro de serviços.
Equipamentos para ensaios não destrutivos magnetização por corrente elétrica alternada (CA) ou contínua (CC) (ou AC/DC, do inglês alternating current/direct current) de meia onda ou onda completa. Além disso, os recursos das máquinas consistem em sistemas de magnetização por técnicas de contato direto, condutor central, eletroímãs e bobina.
Retificadora cilíndrica CNC
A Selltis , empresa especializada na comercialização de equipamentos de usinagem e para trabalhos complementares,
A Polimeter (Cotia, SP) fornece máquinas para ensaios por partículas magnéticas indicadas para a inspeção de peças metálicas fabricadas por usinagem, tais como eixos e barras. A série conta com equipamentos que foram projetados para detectar trincas, fissuras e/ou descontinuidades superficiais eventualmente presentes em, por exemplo, eixos para máquinas e/ou veículos, tubulações, juntas soldadas e peças submetidas a processos típicos do setor metalmecânico, tais como fresamento e furação. Há equipamentos em versões horizontais e verticais, que contam com sistema de
A Studer (Suíça), representada no Brasil pela Tecnohow Tecnologia (Valinhos, SP), recentemente integrou ao seu portfólio de produtos a retificadora cilíndrica CNC S100 (foto), modelo recomendado para companhias do setor metalmecânico que, por exemplo, estão iniciando no segmento de retificação de peças usinadas, ou ferramentarias que pretendem combinar processos em suas linhas de produção. A máquina pode retificar peças e componentes com comprimento de até 550 mm e diâmetro externo de até 420 mm. Ela apresenta curso de 285 mm no eixo X, com velocidade de trabalho máxima de 10 mil mm/min, ao passo que o seu curso no eixo Z é de 800 mm, com velocidade de trabalho máxima de 20 mil mm/min. Também apresenta eixo giratório com ângulo de -1º a 190º. Este equipamento conta com rebolo com diâmetro de 400 mm e largura de 40 mm. Sua potência é de 6,8 kW.

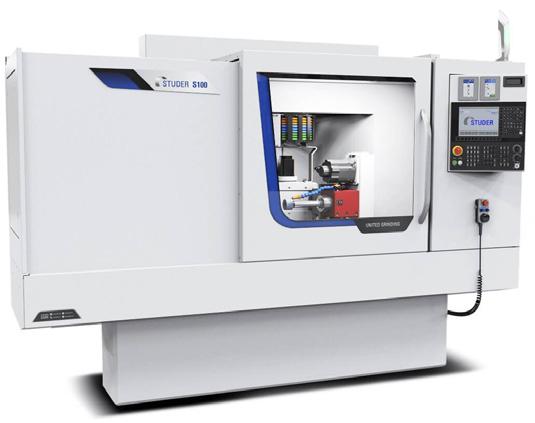
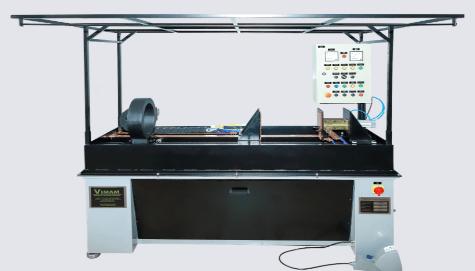