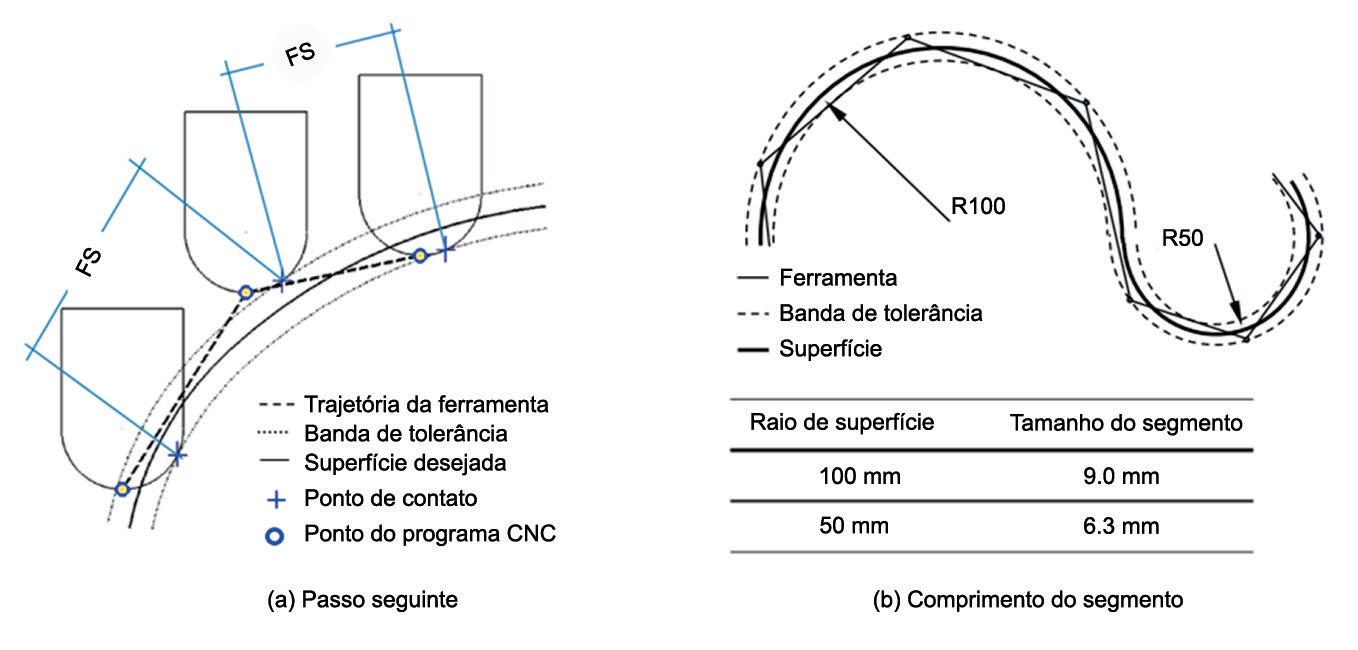
8 minute read
Algoritmo prevê o tempo real de usinagem em máquinas CNC
H. Maiochi, F. Marin e A. Fagali de Souza
Conhecer o tempo necessário para realizar a usinagem de uma peça ou componente é de vital importância para diferentes itens da gestão de produção na indústria metalmecânica, pois permite identificar de forma precisa os custos de produção e da peça, planejar a alocação de equipamentos, prazo de entrega do produto, manutenção de máquina, desgaste de ferramentas de corte etc. Este artigo identifica os erros na obtenção de estimativas de tempo de usinagem e apresenta um algoritmo desenvolvido por pesquisadores brasileiros para prever o tempo real de usinagem de formas complexas, para qualquer configuração de máquina CNC.
Nas indústrias de moldes, matrizes e fabricantes de peças com geometrias complexas, a previsão do tempo de fresamento é um grande desafio. Isso porque, embora os sistemas de manufatura auxiliada por computador (CAM, de computer aided manufacturing) forneçam uma estimativa de tempo de fresamento, os erros desta estimativa podem ser superiores em até 1.000% em sistemas CAM comerciais (1) . Assim, na prática, as indústrias não utilizam esta previsão, e a definição do tempo de usinagem de peças com formas complexas se baseia na expectativa de quando a máquina vai concluir a usinagem, fato sustentado também pelos estudos feitos anteriormente (2) .
O presente artigo identifica inicialmente as origens dos erros dos tempos estimados pelos sistemas CAM e apresenta também um novo algoritmo desenvolvido pelo Grupo de Pesquisa em Manufatura Auxiliada por Computador (GPCAM-UFSC) para prever o tempo real de usinagem de formas complexas, para qualquer configuração de máquina CNC.
O algoritmo denominado CAM Estimator foi registrado no Instituto Nacional da Propriedade Industrial (INPI) e implementado no sistema CAD/CAM NX Siemens, mas pode ser utilizado por qualquer CAM comercial. Assim, pretende-se que esta ferramenta de estimativa de tempo de usinagem se comunique com os sistemas de gestão da produção (MRP, ERP etc.) a fim de se obter melhor gestão da produção e maior precisão de entrega de produtos e custos.
Laurence Colares Magalhães (laurence.magalhaes@ufes.br) e Gabriel Catarino Carlesso são pesquisadores da Universidade Federal do Espírito Santo (UFES). Este artigo foi apresentado no XXIV Colóquio de Usinagem, realizado entre 25 e 27 de maio de 2022, em Curitiba (PR) e organizado pelo Laboratório de Pesquisa em Usinagem da Pontifícia Universidade Católica do Paraná (PUCPR). Reprodução autorizada.
Identificação do problema
Inicialmente deve-se considerar que as trajetórias complexas das ferramentas de corte geradas pelos sistemas CAM e interpretadas pelos CNCs são descritas por pequenos segmentos de retas, empregando a interpolação linear com comando G01 (DIN 66025). Os comprimentos dos segmentos de retas são calculados com base no raio de curvatura da superfície e um valor de tolerância (banda de tolerância), como ilustra a figura 1. Na prática, o software CAM calcula os pontos considerando o vetor normal à superfície no ponto específico. Uma ilustração real dos pontos (em vermelho) calculados por um CAM e as respectivas trajetórias (em verde) pode ser observada na figura 2. Essa metodologia de interpolação linear para descrever trajetórias complexas foi adotada no início do desenvolvimento das tecnologias CAD-CAM-CNC, pois é uma maneira relativamente simples para se descrever uma trajetória complexa. O problema deste método é o curto espaço percorrido entre dois pontos (duas linhas de programa), que aparece com mais frequência de acordo com o caminho da ferramenta programado no programa CAM (4 e 5) . Com a evolução da tecnologia de usinagem sob altas velocidades, as máquinas CNC encontram dificuldade em processar esses comandos em um intervalo de tempo demasiadamente curto e comandar a máquina para a movimentação desejada (de um ponto ao seguinte)(6). Assim, as máquinas reduzem a velocidade de avanço programada, ajustando a sua capacidade de processamento (7) Desta forma, a máquina não se move com a Velocidade de Avanço (F) programada. Os sistemas CAM não identificam esta limitação da máquina CNC. Esta é a origem dos erros dos tempos estimados pelo CAM: o CAM calcula o tempo de usinagem considerando o avanço constante (Velocidade = Espaço / Tempo).
Ressalte-se que esta redução da velocidade de avanço na usinagem de formas complexas é particular de cada conjunto de máquina CNC. Dependendo da implementação do sistema de controle, uma mesma máquina com um mesmo CNC pode possuir diferentes respostas de movimentação. Este é outro ponto que dificulta a estimativa de tempo nestas usinagens, pois existe uma ampla variedade de máquinas e CNCs.
Neste contexto, o presente artigo apresenta a seguir: a) uma discussão sobre as reduções da velocidade de avanço, conforme o tamanho dos segmentos de retas do programa CNC; b) uma metodologia para identificar experimentalmente a capacidade de processamento de qualquer configuração de máquina CNC; c) o software desenvolvido e implementado no CAD/CAM NX para identificar o tempo real de usinagem e os resultados desta aplicação na usinagem real.
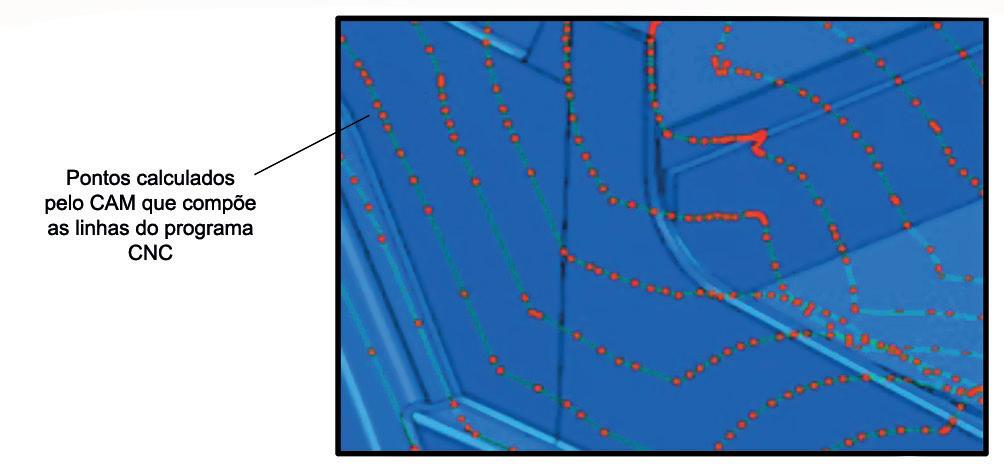
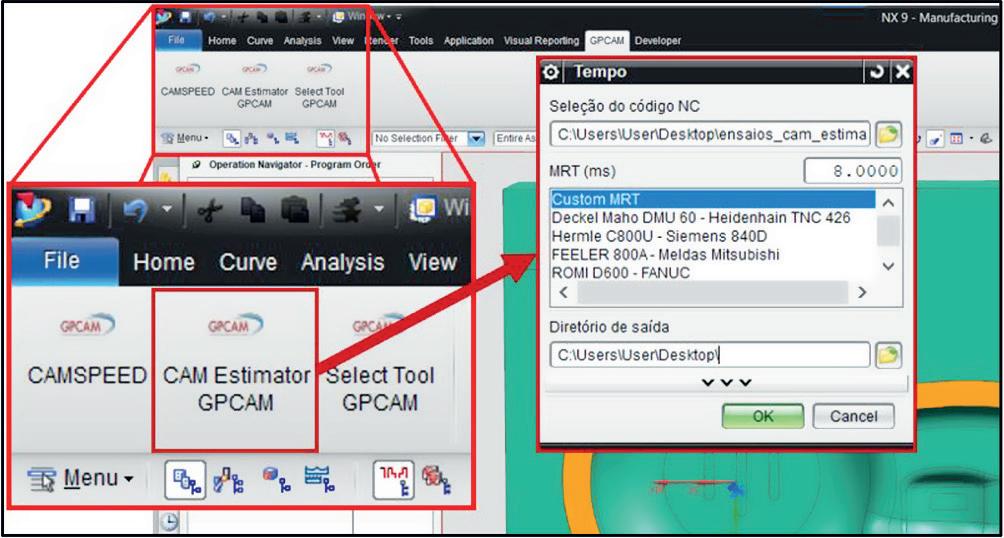
Procedimento experimental
Sistema desenvolvido e método de uso O método desenvolvido para estimar o tempo real de fresamento de formas complexas é composto por duas etapas:
Etapa 1 - Teste para identificar a capacidade de processamento de um conjunto máquina CNC (TRM). Esta é uma ação inicial para se conhecer a capacidade da máquina a ser trabalhada. Um simples programa CNC, contendo pequenos segmentos de retas com valor conhecido deve ser executado na máquina (não é necessário remover material). Em geral pode ser em um dos eixos, com incrementos decimais (0,1 mm é um valor comumente encontrado em programas CNC para indústrias de moldes e matrizes). Durante a execução deste programa CNC, o valor máximo de avanço alcançado pela máquina deve ser observado na tela do CNC e anotado. Considerando o tamanho dos segmentos de retas utilizados e a velocidade de avanço (F) máxima observada, obtém-se o Tempo de Resposta da Máquina específica (TRM). Esta informação pode ser considerada como o “DNA” do conjunto máquina-CNC.
Etapa 2 - Executar o programa desenvolvido. O sistema implementado no software CAD/CAM NX Siemens está ilustrado na figura 3. No módulo CAM Estimator o usuário deve selecionar uma das máquinas que já têm o perfil cadastrado, ou então inserir um TRM customizado, e então inserir o programa CNC gerado. Também é possível selecionar um diretório para armazenar os dados de saída do programa.

Empregando o TRM de uma máquina específica e um programa CNC calculado pelo CAM, o módulo CAM Estimator identifica o tamanho de cada segmento de reta do programa CNC e calcula o tempo real de usinagem, considerando a capacidade desta máquina específica. Assim, executando este cálculo, tem-se o tempo total de usinagem de uma peça com formas complexas, considerando as limitações da máquina CNC a ser utilizada.
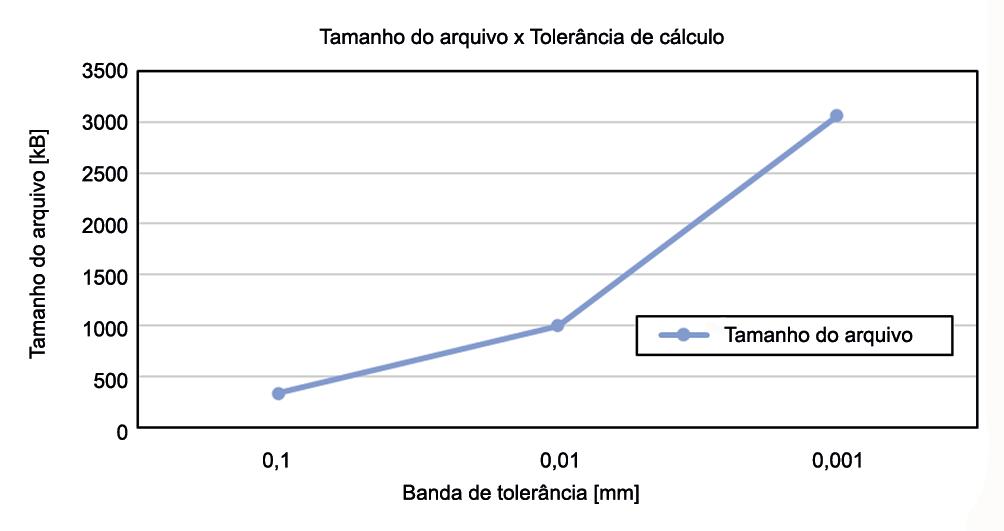
Validação da previsão do tempo de usinagem empregando o sistema desenvolvido
Para a validação do sistema desenvolvido foi utilizada uma cavidade de molde para injeção de plásticos, conforme mostra a figura 4. Foram avaliadas as operações de acabamento, empregando fresas de ponta esférica com 10 mm de diâmetro, quatro arestas de corte, velocidade de avanço de 6.000 mm/min e rotação de 8.500 rpm.
Os testes foram realizados em um centro de usinagem CNC de quatro eixos, modelo D600 fabricado por Indústrias Romi, controlado por um comando CNC GE-Fanuc. Foram calculados programas CNC via software CAM NX com três diferentes tolerâncias de cálculo: 0,1 mm, 0,01 mm e 0,001 mm. Foram avaliados os tempos estimados pelo sistema CAM para a usinagem do molde, assim como o tempo estimado pelo CAM Estimator. Foram avaliados também o tamanho dos arquivos dos programas CNC gerados com as três diferentes tolerâncias.
Resultados e discussões
São apresentados a seguir os seguintes resultados: a) tamanho dos programas CNC em função da tolerância de cálculo; b) resposta da máquina utilizada (TRM), com diferentes incrementos no programa CNC de teste; c) resultados do tempo de usinagem, real, estimado pelo CAM e estimado pelo sistema desenvolvido CAM Estimator.
Tamanho dos programas CNC em função da tolerância de cálculo A figura 5 mostra a influência dos valores de tolerância sobre o tamanho dos programas CNC ge - r ados, evidenciando a existência de mais segmentos de retas no programa CAM gerado com menores valores de tolerância. Observa-se que o tamanho dos programas CNC gerados pelo CAM estão diretamente relacionados com a tolerância empregada no cálculo das trajetórias. Este fato irá impactar no tempo de usinagem real, analisado posteriormente. Portanto, sugere-se empregar o maior valor de tolerância dentro dos limites esperados do projeto. Inicialmente, para se obter o TRM da máquina CNC utilizada, foram realizados testes de movimento com programas CNC para descrever uma simples reta, contudo descrita com pequenos segmentos, representando o que ocorre na usinagem de formas complexas. Foram executados seis programas CNC, contendo diversos segmentos de tamanho entre 0,1 mm e 1 mm. Nota-se que a máxima velocidade de avanço está relacionada ao tamanho dos segmentos de cada programa, de forma linear, como mostra a figura 6. O TRM foi calculado a partir dos dados obtidos, resultando no valor 8,00.
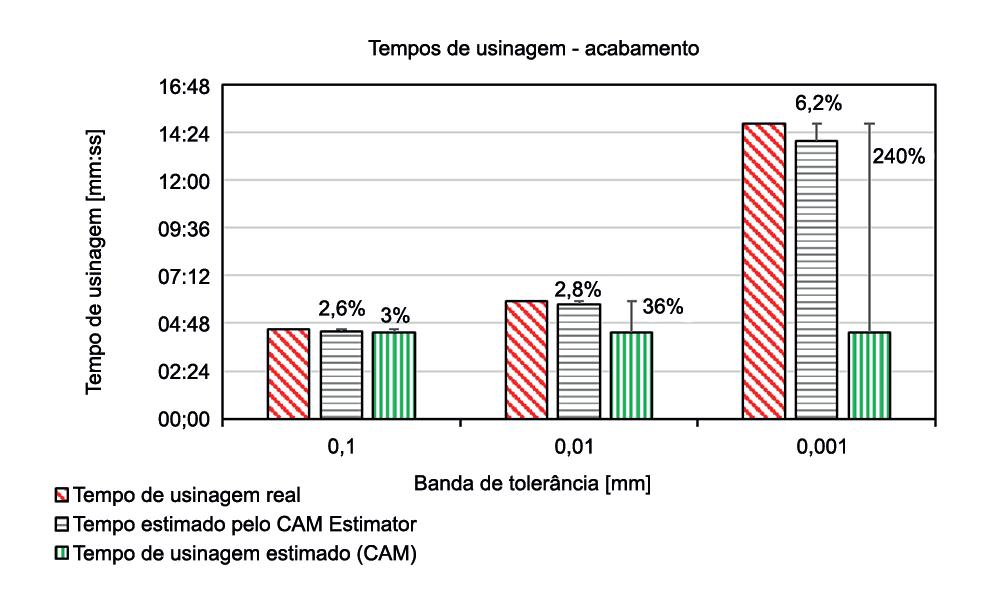
O TRM da máquina foi utilizado no sistema desenvolvido e registrado no INPI como CAM Estimator.
Avaliação dos tempos de usinagem: real, estimado pelo CAM e estimado pelo sistema desenvolvido Baseando-se nos ensaios de usinagem realizados, e com os tempos obtidos, o CAM Estimator foi utilizado para calcular a estimativa do tempo que as usinagens tomariam. A figura 7 reúne os dados obtidos com os três ensaios de usinagem realizados.
Inicialmente, nota-se que as estimativas feitas pelo software CAM possuem todas o mesmo tempo. No entanto, os ensaios realizados mostram que quanto menor o valor de tolerância, maior o tempo real de usinagem. O CAM Estimator conseguiu prever o tempo real de usinagem com precisão muito elevada, com erro de 2,8% contra 36% (CAM comercial) no segundo caso e de 6,2% contra 240% (CAM comercial) no terceiro caso.
Além de o sistema demonstrar o tempo real de usinagem com maior precisão ao programador CAM, esta informação também poderá ser disponibilizada ao sistema de gestão da produção da empresa (ERP/MRP etc.) através de uma saída gerada pelo próprio programa.
Conclusão
As principais conclusões do presente trabalho são:
• O artigo demonstra que as máquinas CNC reduzem indesejavelmente a velocidade de avanço em movimentações complexas, devido à sua capacidade de processamento. Este fato torna muito imprecisa a previsão dos tempos de usinagem realizados pelos sistemas CAM atuais.
• Uma nova variável foi definida para se identificar a capacidade de processamento de uma máquina CNC, o TRM, que também poderá ser utilizada para benchmarking de máquinas CNC.
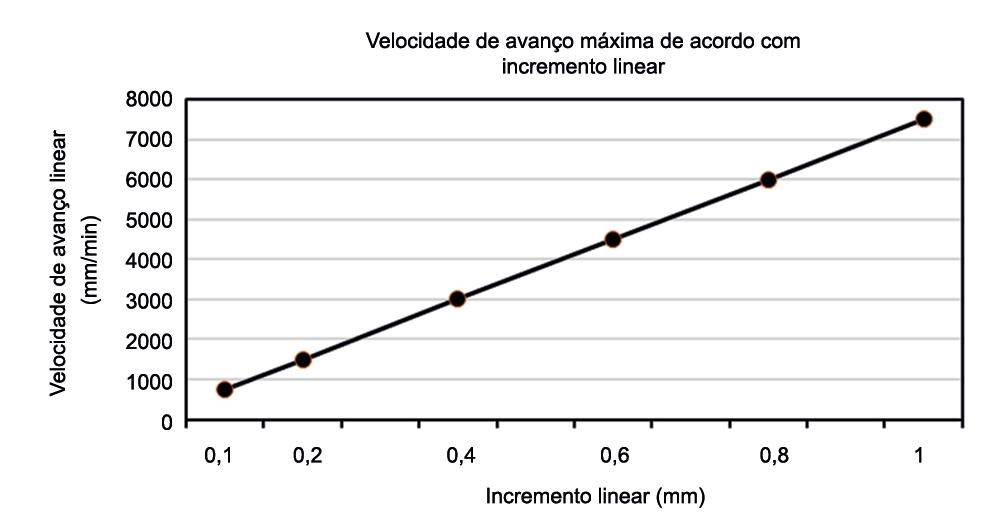
• Um sistema computacional foi desenvolvido para prever o tempo real de fresamento de formas complexas, considerando as limitações específicas de cada conjunto máquina-CNC, através da variável TRM. Utilizando-se desta variável, o sistema computacional desenvolvido foi capaz de prever com elevada precisão o tempo real de usinagem, com erro inferior a 6% contra 240% dos CAMs comerciais, para os casos estudados.
• Deve-se ressaltar que este erro na estimativa do tempo de usinagem ocorre em diferentes sistemas CAD/CAM. O algoritmo desenvolvido ainda não foi implementado para comercialização.
• Conhecer o tempo real de usinagem é fundamental para uma indústria competitiva atualmente, pois pode fornecer um importante auxílio na gestão da fábrica, estimativa de custos, manutenção, assim como definir de forma mais precisa o momento de troca de ferramentas de corte.
[1] Souza, A. F., & Coelho, R. T. (2010). Mechanistic approach to predict real machining time for milling freeform geometries applying high feed rate. The International Journal of Advanced Manufacturing Technology, 1103–1111.
[2] Camargo, L. G., Souza, A. F., Podda, L., Schappo, F., & Rodrigues, A. R. (2015). Influência das trajetórias de usinagem e da tolerância de cálculo no tempo real de fresamento de formas complexas. (p. 10). Salvador: 8º Congresso Brasileiro de Engenharia de Fabricação.
[3] Souza, A. F., & Ulbrich, C. B. (2013).
Agradecimentos
Os autores agradecem ao CNPq, à FAPESC, pelo fomento à pesquisa, e à Siemens PLM, pela grande colaboração no desenvolvimento deste projeto.
Referências
Engenharia integrada por computador e sistemas CAD/CAM/CNC. 2Ed. São Paulo: Artliber.
[4] Monreal, M., & Rodrigues, C. A. (2003). Influence of tool path strategy on the cycle time of high-speed milling. Computer-Aided Design, 395-401.
[5] Yan, X., Shirase, K., Hirao, M., & Yasui, T. (1999). NC program evaluator for higher machining productivity. International Journal of Machine Tools & Manufacture, 1563–1573.
[6] Siller, H., Rodriguez, C. A., & Ahuett, H. (2006). Cycle time prediction in high-speed milling operations for. Journal of Materials Processing Technology, 355–362.
[7] Renton, D., & Elbestawi, M. A. (2000). High speed servo control of multiaxis machine tools. International Journal of Machine Tools & Manufacture, 539–559.
[8] Souza, A. F., Severino, N., Kasemodel, R., & Marin, F. (2021). Novo aplicativo reduz mais de 25% no fresamento de moldes e matrizes parametrizando a rotação (S) e a velocidade de avanço (F). Ferramental, 20 - 23.