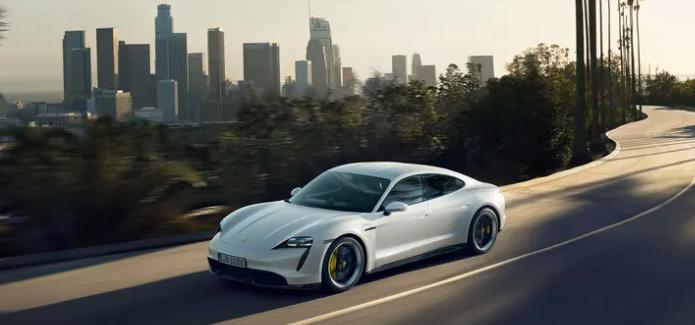
5 minute read
caminhos para a metalurgia
As tendências de fundição na indústria automotiva estarão entre os temas centrais do principal evento mundial do setor de fundição, a GIFA, que será realizada como parte do Bright World of Metals, um conjunto de feiras que acontece em Düsseldorf (Alemanha), de 12 a 16 de junho de 2023. Como parte dos preparativos para esses eventos, especialistas têm realizado análises sobre o mercado de peças para a indústria automotiva, abordando toda a gama de processos metalúrgicos, com reflexos diretos sobre as empresas do setor de usinagem e corte e conformação a partir de chapas metálicas.
Uma dessas análises foi feita por Gerd Krause, da agência Mediakonzept, de Düsseldorf, a partir de entrevistas e da cobertura de uma conferência sobre fundição. Suas principais ideias são apresentadas a seguir.
Os novos atores da mobilidade elétrica
A mobilidade elétrica, que tem a figura de Elon Musk com a Tesla embaralhando as cartas no mercado automotivo, dá o tom das novas necessidades do segmento automotivo. “Os chineses e a Tesla estão longe de entregar o crescimento que prometeram. Produtores bem estabelecidos como Volkswagen, BMW, Mercedes e General Motors (GM) conseguiram se posicionar muito bem nos mercados”, observou Franz-Josef Wöstmann, durante a conferência “Tecnologia de Fundição e Mobilidade Eletrônica” em Bremen, em outubro último, com referência às estatísticas de vendas atuais.
Wöstmann, chefe do Departamento de Detecção Precoce e
Exploração de Tecnologias do Fraunhofer Institute for Manufacturing Technology and Applied Material Research (IFAM), lembrou que em 2019 a Tesla ainda parecia ser o player número 1, com 245.000 veículos elétricos produzidos. Desde então, o pioneiro dos veículos elétricos conseguiu multiplicar as vendas por um fator de 4, para cerca de 936.200 veículos em 2021, mas no mesmo período a Volkswagen saltou das faixas intermediárias para quase o primeiro lugar, catapultando as vendas de 41.000 veículos em 2019 para 762.000. Outros players como BMW e Mercedes também conseguiram aumentar maciçamente sua produção, mantendo também um olho em sua produção padrão. Também é interessante acompanhar os desenvolvimentos dos concorrentes chineses. A BYD conseguiu dobrar suas vendas, mas caiu do 2º para o 3º lugar.
“Os chineses não conseguiram alavancar sua posição de liderança, apesar de estarem localizados no principal mercado de mobilidade elétrica”, concluiu Wöstmann. Por outro lado, a tradicional marca americana GM, que nem sequer apareceu nas estatísticas de 2019, surgiu em um curto espaço de tempo.
Crescimento fora da Europa
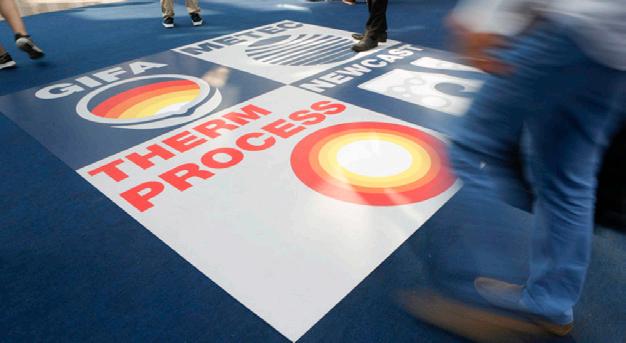
Nos mercados saturados da Alemanha, Europa e Estados
Unidos, a transição dos motores de combustão interna para a mobilidade elétrica está se desenvolvendo sem nenhuma mudança notável nos volumes totais de carros registrados. O crescimento é visto predominantemente na Ásia e, acima de tudo, na China. Os especialistas concordam, como ficou claro na conferência de tecnologia de fundição de Bremen, que até 2030 cerca de metade de todos os carros vendidos no mundo serão veículos elétricos. No entanto, 2050 ainda verá muitos carros movidos a combustão nas ruas – por uma ampla variedade de razões, como prevê o pesquisador do Fraunhofer, Wöstmann. Isso porque muitas regiões da Ásia, África e América Latina não terão a infraestrutura supranacional necessária para a mobilidade elétrica.
Produtores de rodas de metal leve de alumínio e alumínio fundido sob pressão para carrocerias e trens de força estão discretamente otimistas sobre a tendência para a mobilidade elétrica, embora a fundição de motores a combustão interna esteja diminuindo. “A mobilidade elétrica significa uma infinidade de novos fundidos”, explicou Wöstmann: carcaças para os motores, carcaças de caixa de engrenagens, caixas de bateria, sistemas de refrigeração, carcaças e componentes de refrigeração para a eletrônica de potência, bem como bobinas de alumínio fundido como uma alternativa para substituir as bobinas de cobre no futuro.
O pesquisador do Fraunhofer aposta em pouca mudança e definitivamente nenhum crescimento para o segmento de ferro fundido. O que se pode esperar, ele pensa, é uma fundição de aço de paredes finas no segmento de carcaças de motores, especialmente para motores de alto torque com resfriamento integrado. No momento, porém, nenhum OEM está desenvolvendo algo nessa direção. Sem esquecer a construção leve, que é claramente um domínio do alumínio e da fundição de alumínio, especialmente na mobilidade elétrica.
Quanto aos componentes produzidos por fundição sob pressão no futuro, as opiniões se dividem entre os fabricantes estabelecidos e os novos players. Enquanto a Tesla e vários produtores chineses pretendem conquistar o mercado com máquinas de fundição com mais de 12.000 toneladas de força de fechamento, as empresas estabelecidas há muito tempo são bastante reservadas. Wöstmann considera essa abordagem bastante positiva, especialmente porque demonstra o potencial da fundição. No entanto, assume que serão poucos os fornecedores a entrar neste mercado. Em vez disso, ele sente que um grande potencial tecnológico pode ser aproveitado no segmento com forças de fechamento abaixo de 6.000 toneladas, o que permite uma fabricação eficiente, mas com requisitos menores em termos de logística, garantia de qualidade e segurança da produção.
Construção leve: mistura inteligente de materiais com aço e alumínio
O aço – que é, de qualquer forma, o material número 1 para o mercado de carrocerias de alto volume – também poderá se manter firme e não apenas para a tira de aço elétrica, o “material espinha dorsal” indispensável para motores elétricos. Os fabricantes premium também estão cientes dos pontos fortes do novo aço de alta resistência, como demonstrado pela Porsche com a construção mista de seu carro esportivo Taycan, movido a bateria (foto na página anterior). O aço conformado a quente protege a célula do passageiro na coluna A, coluna B, estrutura do teto e travessa do assento. Um destaque especial é a viga transversal da parede final em aço ao boro-manganês. Graças a processos de fabricação especiais, o componente em forma de tubo pode ter diferentes seções transversais e isso permite que a força máxima seja alcançada com o peso otimizado.
O suporte do eixo e a longarina traseira são feitos de alumínio fundido sob pressão, enquanto os suportes do amortecedor expostos a cargas particularmente altas são feitos de alumínio forjado. A longarina frontal combina uma construção de casca de alumínio com perfis extrudados. As soleiras são feitas de um perfil extrudado com sete câmaras, atendendo a todos os requisitos de rigidez contra colisões laterais e torções. Em comparação com um modelo em aço, essa estrutura reduz de quinze para três o número de componentes necessários para cada lado, com uma redução de peso de 3,4 kg, segundo as contas do fabricante. A carroceria externa completa é feita de alumínio, com exceção das partes dianteira e traseira. Para o Taycan, a proporção de alumínio totaliza aproximadamente 37% do material utiliza - do. Sua carroceria é feita pela Thyssenkrupp Automotive Body Solutions, a subsidiária de carroceria do grupo industrial com sede em Essen.
O projeto de carcaça em aço é o tipo de construção de carroceria usado com mais frequência em todo o mundo, mas tem sofrido pressão do alumínio há alguns anos. As chapas de aço soldadas são cada vez mais substituídas por peças de alumínio fundido inteiriças, com a vantagem da produção em larga escala.
Mega casting, uma nova tendência?
De acordo com Johannes Messer, da consultoria de mesmo nome, há uma tendência – tanto em termos comerciais quanto técnicos – de uso de máquinas de fundição sob pressão maiores para chassis e peças estruturais, bem como para a mobilidade elétrica. Máquinas de fundição sob pressão de alto desempenho tornam mais eficiente a produção de peças automotivas maiores e mais complexas. As máquinas de fundição sob pressão do tipo Giga Press, usadas pela Tesla pela primeira vez, são fabricadas pela empresa italiana Idra, apresentando forças de fechamento de 6.000 a 9.000 toneladas e transformando o alumínio fundido em peças dianteiras e traseiras acabadas, o que leva à reflexão sobre o papel da usinagem nesse novo contexto.
A empresa ainda divulgou ter uma patente para carrocerias completas de uma única peça fundida sem tratamento térmico. Pela conta de Elon Musk, esse esquema de mega casting já economiza 300 robôs na linha de montagem, reduzindo drasticamente os tempos de produção.