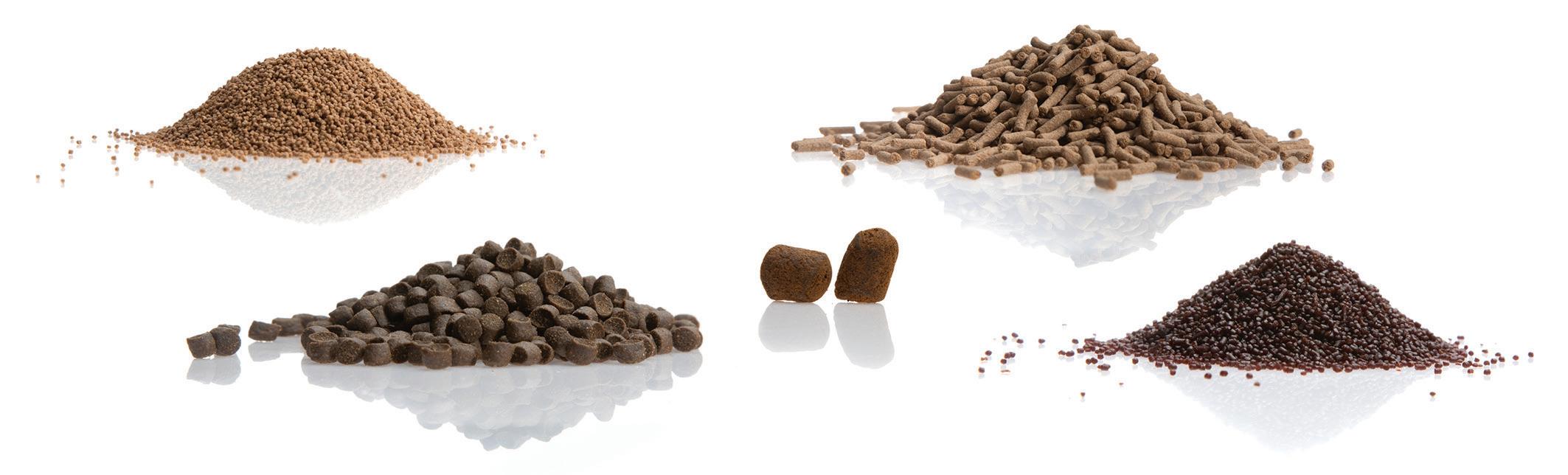
19 minute read
The challenge of an essential and expanding market
Hadrien Delemazure, Clextral
The most recent study from the Food and Agriculture Organization of the United Nations (FAO, 2020) confirms that 52% of the consumed aquatic animals in the world, including finfish, mollusks and crustaceans, come from aquaculture. With a world population of 7.8 billion people, the average fish consumption, including mollusks and crustaceans, was estimated in 2018 to be 20.1 kg/inhabitants. The process of feed manufacturing for finfish and shrimp represents a key issue for ensuring the delivery of consistently high-quality granulates for these intensive breeding processes; for example, it is estimated that over 60% of the production expenses for farmed salmon come from the feed cost.
Additionally, we have to face challenges, such as limited resources of fishmeal and fish oils worldwide and a temperature increase in the earth’s environment creating irregular conditions for fish capture, uncertain cereal and pulse harvests on earth (used more and more to partially replace fishmeal in recipes), and the risks to delicate offshore aquaculture breeding facilities (waves, winds, storms, currents, pollution, etc.).
The potential of twin-screw extrusion
Fish is known as a high-value food for humans, with health benefits that include long-chain unsaturated fatty acids, vitamins and minerals and a wellbalanced protein supply. In 2017, fish supplied 17% of animal protein in the world. Moreover, 3.3 billion people received 20% of their animal protein from fish origin. Therefore, fish feed processing technology plays a particularly important role in this industry. It requires: • Easy adaptation to any change in raw-material composition: moisture content, lipid content, particle size distribution. These are due to various sources of raw materials (for example, soy flour can be purchased in many parts of the world), transport and storage conditions, and the grinding process. • Flexibility to adjust the sinking/floating properties of the granulates to follow as closely as possible the food habits of each animal family. • Processing a wide range of recipes to respond to industry demand for foods with low or high amounts of lipids, vegetable proteins, or various sources of protein to meet the specific nutritional fish requests and adapt to rapid environmental changes. • Flexibility to adjust the shear, cooking and shaping conditions in the extruder and apply precise drying and coating parameters during the entire production process. • Ensuring a high hygienic standard, to avoid any contamination during the feed manufacturing process.
Taking these considerations into account, combined with good manufacturing/breeding practices, scientific education and adapted legislation, we can nurture high-quality aquatic animals that offer health benefits to people around the world, using local production to ensure low carbon footprints and maintain reasonable sales prices.
Co-rotating twin-screw extruder
Single screw extrusion technology has offered a simplified method of continuous cooking of doughs under controlled processing conditions for many decades. Sixty years ago, some industry pioneers developed an alternative process: co-rotating twinscrew technology applied to food production, which offered much greater flexibility than single screw machines due to its intensive mixing ability with precise shear and temperature control.
With the evolution of electronic PLCs, mechanical features, gauges, drives, and metallurgy, together with heavy R&D investment, these pioneers offered the fish feed industry more sophisticated systems, allowing the industry to move quickly into new areas, such as recipes with high amounts of fat and vegetable protein.
Clextral, a major player in twin-screw technology for food and feed applications, has launched innovations that offer even greater opportunities for the fish farming industry to process original recipes and use raw materials, such as new pulses, proteins, insects, krill meals and possibly processed animal proteins, seaweeds, etc. One of these innovations relates to intelligence of the machine and the ability of the auto-adaptive extruder to adjust to potential raw material variations.
Advanced Thermal Control (ATC)
The Advanced Thermal Control (ATC) is a self-learning, proprietary software solution that ensures absolute precision in temperature control of the barrel assembly of the Evolum+ extruder.
ATC continuously monitors production parameters to ensure process and product consistency. ATC is proven to enhance process stability up to 70%, with energy savings averaging 20% by eliminating repeated heating/ cooling cycles to maintain process temperature setpoints in all circumstances.
Combined with an automatic start-up and shut down procedures, this system represents a powerful tool to enhance the productivity of the extrusion line.
Preconditioning: Higher efficiency and improved product texture
Another innovation refers to the preconditioning process, a key operation in fish feed manufacturing. Preconditioning allows moistening of the powdered mix and pre-gelatinization of the starch molecules through the addition of water and steam, thereby, increasing the pellets' water stability, enhancing production capacity and reducing wear on the extruder.
Clextral’s patented Preconditioner+ improves heat and mass transfer to the product due to the Advanced Filling Control device (AFC). It interacts directly with the material inside the mixing chamber and enables the filling ratio to be adjusted. The AFC system uses an exclusive conveying screw inside the tank and adjusts the flow by a partial and controlled recycling of the material being processed from the outlet to the entry point, thus intensifying the specific preconditioning functions.

Laboratory tests have proven that the final hardness of fish feed pellets increased between 7% and 29% using the same recipe and adjusting the bottom-screw speed.
During the cleaning procedure, the bottom-screw rotation is reversed to facilitate the emptying and the cleaning of the preconditioning chamber.
Hygiene
Finally, today much attention is focused on hygienic extruder design as food security is a key parameter for the fish feed and food industries.
Fish feed manufacturers want to be able to clean their extruder from the outside using hot water and sometimes with cleaning agents. The stainless steel, hygienic Evolum+ frame structure is designed to avoid water stagnation and all the extruder areas are easily accessible. The internal processing assembly of the twin-screw extruder must be cleaned easily as well: the complete quick barrel extraction device is today a paradigm in the industry. It offers access to the screws and barrels in only a few minutes and is a state-of-theart solution that simplifies preventive maintenance, wear monitoring and cleaning processes.
Density control system
Clextral has developed a system for instantly varying the density of the material within the extruder. It is possible, for example, (depending on the recipe) to quickly pass from an extruded pellet of 350 g/L to 750 g/L. This fully automated tool ensures the control of the pellets' density and the ability to produce sinking or floating aquatic feed.
With the density control system, the cooking degree and resulting density of the final product can be adjusted according to customer specifications. By adding steam or through the generation of a vacuum, the density control system ensures the precise density and proper degree of expansion in the product. The main advantages of this process: • Precise density adjustment and control. • Reduced product moisture levels. • Generate high-density products. • Fines recovery back to preconditioner. • Ideal for aquatic feed production. Recent process innovations that allow expanded ingredient availability are bringing many opportunities for feed processors. Processors can easily make a range of feeds that satisfy the nutritional requirements and feeding styles of many aquatic species. In turn, fish farmers will be better equipped to optimize their feeding operations and grow healthy fish and shrimp using sustainable practices to supply the growing global demand.
More information: Hadrien Delemazure
Process Engineer and Feed Expert Clextral E: hdelemazure@clextral.com
The foundational years: 1940-1979
Louis R. D’Abramo, Professor Emeritus, Department of Wildlife, Fisheries and Aquaculture, Mississippi State University Thomas R. Zeigler, Senior Technical Advisor, Past President and Chairman, Zeigler Bros., Inc.
This is the first of a series of articles titled "Development of aquafeeds: Reflections and future perspectives".

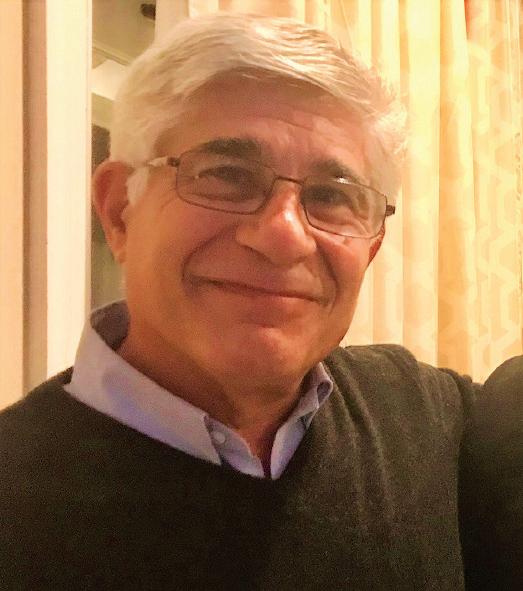
As global aquaculture production continues to grow, the life history stages of many farmed species are fed manufactured feeds. Basic knowledge of aquatic animal nutrition has been acquired, enhanced, and correspondingly applied in the production of aquafeeds. However, a basic historical summary of the development and manufacture of aquafeeds in union with the ongoing progress in the understanding of nutrition is lacking. Therefore, the goal of this effort is to achieve something that has been overtly lacking in the education and training of emerging researchers in aquatic animal nutrition and aquafeed management, a historical perspective that highlights this coevolving history. This knowledge is essential as it instills an appreciation and respect for the 60-year path of how we got here today. It also nourishes a vital insight toward meeting the challenges of future improvement of physical characteristics and nutrient composition of feeds and their provision.
This article consists of three parts offered sequentially within three separate issues of Aquafeed Magazine. The content is descriptive of what we consider to be impactful highlights or paradigm changes in the history of the nutrition of aquaculture species and the production of aquafeed for commercial enterprise. The content is by no means comprehensive and therefore is not written as a review. The combined articles represent reflections and perspectives from our extensive careers in aquatic animal nutrition research and commercial production of aquafeeds as influenced by technology and the state of aquatic animal nutrition at that time in history. The individual parts are divided into narratives of the early decades of development (the foundational years, 1940-1979), the years responding to the rapid expansion of global aquaculture (the transformational years, 1980-2019), and the years forthcoming, whereby we speculate and offer recommended directives about where the path of the future should lead (the sustainability years, 2020- ).
The origins of aquafeeds
In 1954, the efforts to gain and apply knowledge about fish nutrition were inaugurated in a trout hatchery in Cortland, NY. Three entities, the NY State Conservation Department, the US Bureau of Fisheries, and Cornell University joined forces to initiate a program designed to meet the needs of developing a practical diet that would be an integral part of trout hatchery management. This recognition of the critical importance of a feed based on knowledge of nutrition to grow juvenile trout was complemented on the west coast of the U.S. by similar acknowledged needs to develop
nutritionally complete diets to grow juvenile Pacific salmon for release as part of a fisheries management program. Again, a group of cooperators, specifically the University of Washington, Oregon State University, and regional and state fishery agencies that notably included the US Fish and Wildlife Service were collectively involved. These goals to develop practical diets were particularly noteworthy because they represented a true desire to develop a knowledge of fish nutrition based on efforts to identify specific nutrient requirements.
Fish feed preparation originally started with indiscriminate attempts to feed fish with aggregations of ingredients such as ground animal waste in combination with a ground plant-derived meal. With the advent of the pellet mill, particles of different sizes and densities could be manufactured. With the inception of a vastly improved methodology to produce feed, a major paradigm change occurred. Suddenly, the potential of feeding fish directly via pellets containing ingredients based on knowledge of nutrient requirements of aquatic animals was in the realm of reality. Finally, it was time to move from essentially feeding ponds with concoctions of undescriptive content to feeding fish more precisely.
Aquatic animal nutrition commenced in the late 1940s when B. A. McLaren was able to achieve rainbow trout growth with a semi-purified diet that was used to widely estimate the requirements of an array of water-soluble vitamins as published in Archives of Biochemistry in 1947. With the advent of a semi-purified diet for experimental studies, knowledge of the nutritional requirements of aquatic organisms began to substantially increase. Thus, the semi-purified diet represented a principal turning point in the history of aquatic animal nutrition. It consisted of chemically defined ingredients that were specifically used to serve as a supply of specific macro- and micronutrients. Examples of ingredients of semi-purified diets are casein, dextrin, corn and cod liver oils and mixtures of vitamins and salts (micro and macroelements). In the late 1950s, Dr. John Halver and Dr. John Coats, under the auspices of the Western Fish Nutrition Laboratory and the Bureau of Sport Fisheries and Wildlife, used a vitamin-free semi-purified diet to define the water-soluble vitamin requirements of coho salmon. Also, in 1957, Halver et al. identified the
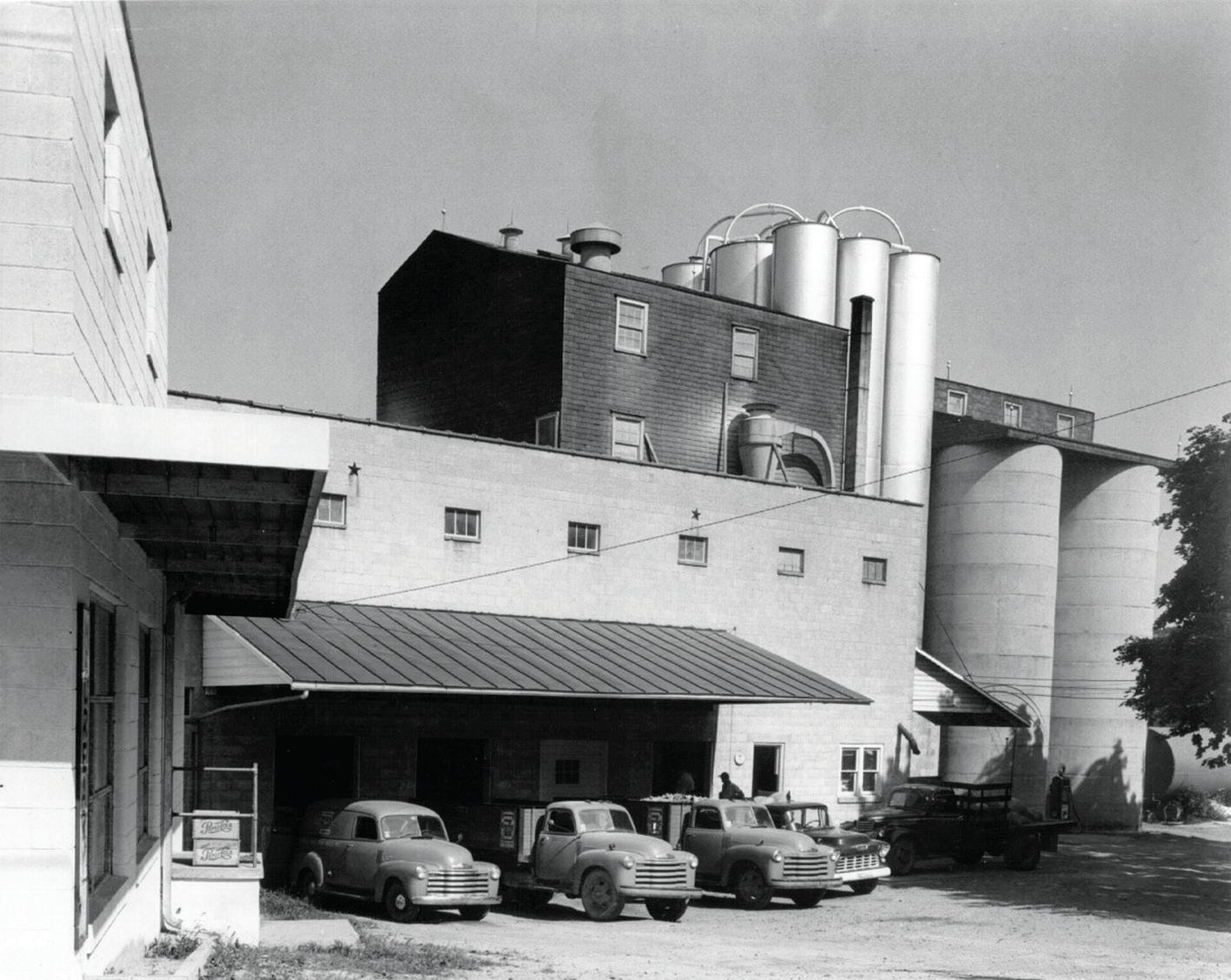
A feed mill, circa 1958 after it had been modernized with new bulk tanks to increase automated manufacture of pelleted feeds.
requirements of nine watersoluble vitamins for chinook salmon fingerlings. In 1957 and 1960 publications, Halver et al. established the qualitative dietary requirements of 10 amino acids for chinook salmon and sockeye salmon respectively. Feeding trials consisted of different experimental diets consisting of graded levels of a specific essential amino acid within the mixture of other essential amino acids. The estimated requirement was determined by using a response variable, commonly growth; however, where appropriate, other physiological responses were evaluated in an attempt to further validate the growth results. These qualitative essential dietary amino acid requirements were complemented by studies that used 14 C whereby the lack of metabolic incorporation of 14 C into a particular amino acid indicated lack of synthesis and thus its dietary essentiality. The ten essential amino acids were commonly required by both fish and crustaceans.
The first investigations of nutrient requirements of crustaceans using a semi-purified diet began approximately 25 years after the vitamin requirements of coho salmon were published. Published studies of nutrient requirements of the prawn Penaeus japonicus began to appear in the 1970s and were conducted by Japanese investigators, most notably Drs. Akio Kanazawa and Shin-ichi Teshima at Kagoshima University and Drs. Osamu Deshimaru and Katsunobu Kuroki at the Prefecture in Kagoshima. These researchers embraced the use of semi-purified diets that contained intact reference proteins in combination with a mixture of essential amino acids in crystalline form. Kanazawa,
Pelleted feeds were packaged into 100 lb burlap bags. At this mill, circa 1958, a fish feed was produced for the Michigan Department of Conservation according to the formula called Michigan 2B. These pelleted feeds were not nutritionally complete and primarily consisted of some fishmeal, cottonseed meal and wheat mailings.

Teshima and Shigeru Tokiwa published the results of a series of investigations, notably the relationship of dietary lipids and their corresponding fatty acid composition to the growth of shrimp. In 1974, Deshimaru and Kuroki reported the results of an investigation designed to establish the most effective combination of nutrients fed to Penaeus japonicus with the ultimate goal of producing a “purified diet” through the evaluation of formulations consisting of different ingredients. Using the best “purified” diet, they estimated the cholesterol requirement of P. japonicus.
The nutrient requirement studies of Kanazawa, Teshima, Tokiwa, Deshimaru, and Kuroki during the 1970s were complemented by some unique laboratory investigations. Dr. Luigi Provasoli of Haskin Laboratories and Yale University expanded his research devoted to the understanding of the nutrient requirements of species of algae under axenic (bacteria free) culture conditions to include the microcrustacean Moina macrocopa. The nutritional food source was described as a biphasic medium composed of a particulate phase consisting of protein/starch particles that could be suspended within a liquid phase that contained an array of water-soluble nutrients which in mixtures of salts, amino acids, nucleic acids, and vitamins. The water-soluble nutrients within the liquid phase were absorbed by the microcrustacean as a byproduct of the removal of the suspended particles by filtration. This pioneering work validated information about qualitative requirements of nutrients such as cholesterol and many B vitamins. Additionally, research results, first published in the late 1970s and into the early 1980s, described different growth rates in response to different dietary fatty acid mixtures that were included in the particulate phase and mimicked the composition of different phylogenetic groups of algae. This work preceded investigations devoted to the understanding of the dietary requirements of fish and crustaceans for certain fatty acids.
Early advances in aquafeed development
Regarding feed manufacture, a good example of a prototypical feed was the Oregon Moist Pellet (OMP). Specifically developed in 1954 as a hatchery feed for salmon by Agricultural and Environmental Services (AES) researchers at the Seafood Laboratory of Oregon State University, OMP was unique because its formula was open, thereby being commonly available to feed manufacturers for commercial production. This characteristic lack of a propriety formulation eliminated the need for feed to be independently produced at each hatchery. The OMP consisted of a dry mix (fishmeal, cottonseed meal, wheat germ meal, dried whey, corn distillers dried solubles, and vitamin and mineral premixes) and a wet mix (pasteurized wet fish, marine oil and 70% choline chloride). Produced by a cold pelletization process the OMP had a comparatively high moisture content (26-28%) which required shipment as a frozen product for distribution.
During the decade of 1941 to 1950, the first feeds for commercial catfish and trout farming were produced by pelleting to achieve a larger particle size. During the 1950s and 1960s, commercial catfish farming in the U.S. was notably increasing and by the 1980s, production practices, post-harvesting processing, and marketing had reached an impressive level. Pelleted feeds were also being produced for the burgeoning trout and salmon farming enterprises. During the 1950s, the manufacture of some feeds shifted to a new manufacturing process,
extrusion. With the manipulation of the qualitative and quantitative carbohydrate content, extrusion successfully produced a desired floating feed that evidenced comparatively higher water stability. The floating nature of the feed permitted evaluation of nutritional and possibly pathological states of the fish by observation of change in feeding behavior at the water surface. During the extrusion process, the starch contained in the feed was gelatinized, a condition that improved overall digestibility. Another benefit of extrusion was that vitamins included as mixtures in a feed formulation were less susceptible to loss of activity. During the 1950s, companies such as Berger, Silver Cup, Zeigler, Glencoe Mills, Purina and Rangen began the commercial production of fish feeds characterized by specific manufacturing processes. Attention was directed to the provision of suitable crude lipid and protein levels as well as the moisture content.
Extruded feeds were eventually followed by the introduction of expansion feeds that originated in Europe. The manufacture of expansion feeds differed from that of extruded feeds by incorporating less moisture and more shear to meet the objectives of improved digestibility and the ability to include more lipid (15-20%) in formulations. The increased levels of dietary lipid introduced the ability to increase amounts of available dietary energy and thereby reduce the overall level of required dietary protein (sparing protein). The nutritional value of feeds was improved through changes in ingredient composition that were based on the ever-increasing knowledge of aquatic animal nutrition and other benefits derived from advances in feed manufacturing technology.
Meeting the needs of education, research and training
The recognized benefits of research devoted to the understanding of nutrient requirements and its application to the manufacture of aquafeeds during the 1950s through the 1970s led to the need for supportive educational and research opportunities that were established at several universities and institutes in Europe. A few examples of this movement follow. In Bergen, Norway, a fish nutrition research program was added to animal and human nutrition programs. The prominence of this area of research has continued as a part (Feed and Nutrition) of the Aquaculture, Environment and Technology division of the Institute of Marine Research in Bergen. In France, Dr. Pierre Luquet was instrumental in establishing the study of fish nutrition within the animal nutrition group at the National Institute for Agricultural Research during the early 1970s. As part of the University of Stirling in the UK, the Institute of Aquaculture was founded in 1971 and has become a leading international center that fosters aquaculture education, research, and innovative technology. Dr. Colin Cowey, educated in zoology and biochemistry, joined the Unit for Research in Fish Nutrition in Aberdeen in the UK in the late 1950s. There and later at the Institute of Marine Biochemistry in Aberdeen, his renowned fish nutrition research contributions received global recognition.
Feed ingredients to serve a growing aquaculture industry
The success of aquaculture enterprises was integrally dependent on the success of aquafeeds. The inherent objectives in aquafeed design were the provision of balanced nutrition to produce healthy fish at economically practical growth rates aligned with the efficient conversion of feed to tissue. The decades of the 1950s, 1960s and 1970s (1951 through 1979) established the foundation for the development of feeds that were originally intended to produce stocks for fishery enhancement/restoration. The obvious need to base feed composition on knowledge of aquatic animal nutrition created a foundation for extending these efforts to address the needs of the growing global aquaculture enterprise. Feeds, specifically for salmon, catfish and trout, led to formulations and feed manufacturing processes designed to increase the nutrient value and utilization efficiency of the ingredients as guided by cost considerations.
The understanding of essential amino acids, fatty acids and water-soluble vitamin requirements was accompanied by a focus to identify superior commercial sources of protein, lipid, and carbohydrate. Marine-derived proteins from meals produced from menhaden, anchovy, squid liver, and shrimp heads, and oils from cod liver, menhaden, catfish offal were some of the primary ingredients evaluated. Plantderived sources from meals derived from soybean, peanut, and cottonseed, and oils from corn, canola and rapeseed also received attention as aquatic feed
ingredients. A significant amount of research was devoted to the digestibility of the macronutrient composition of the various feedstuffs with the goal of providing nutrients that were most efficiently utilized by the different aquaculture species in association with their natural diets.
Most of the feeds tested as part of laboratory experiments focused on strategies for the successful grow-out of juveniles. Knowledge of nutrient requirements and their satisfaction in feed for both larval and broodstock life history stages lagged behind as evidenced by a continued dependence on live feeds, either complete or as supplements. Species of algae and rotifers and Artemia nauplii were the preferred foods for larval species of fish and crustaceans and much effort was devoted to the identification of essential fatty acids, particularly the long-chain polyunsaturated fatty acids (LC-PUFA). Live or frozen animal feeds continued to be an integral part of the successful culture of shrimp broodstock. However, the nutrient composition derived from these sources was recognized as being subject to change. It was obvious that a controlled nutrient vehicle that reliably and consistently satisfied the nutrient requirements at all life stages was needed.
To be continued – Part II
Part II of the history of the development of aquafeeds will follow in the next issue and highlight the need to organize the knowledge that was vastly accumulating. Notable efforts were launched to share these data through groundbreaking meetings and publications. More species of fish and crustaceans were identified as potential candidates for commercial aquaculture. In response to this significant upsurge of knowledge, the emergence of additional species of interest, and the unique life stage-dependent production needs, aquafeeds would correspondingly need to develop and improve to effectively meet these requirements. Specific feed additives and the presence of anti-nutritional factors in feedstuffs would take on added significance with the intent of meeting the overall objectives of increasing efficiency, enhancing immunocompetence, and achieving the desired pigmentation.