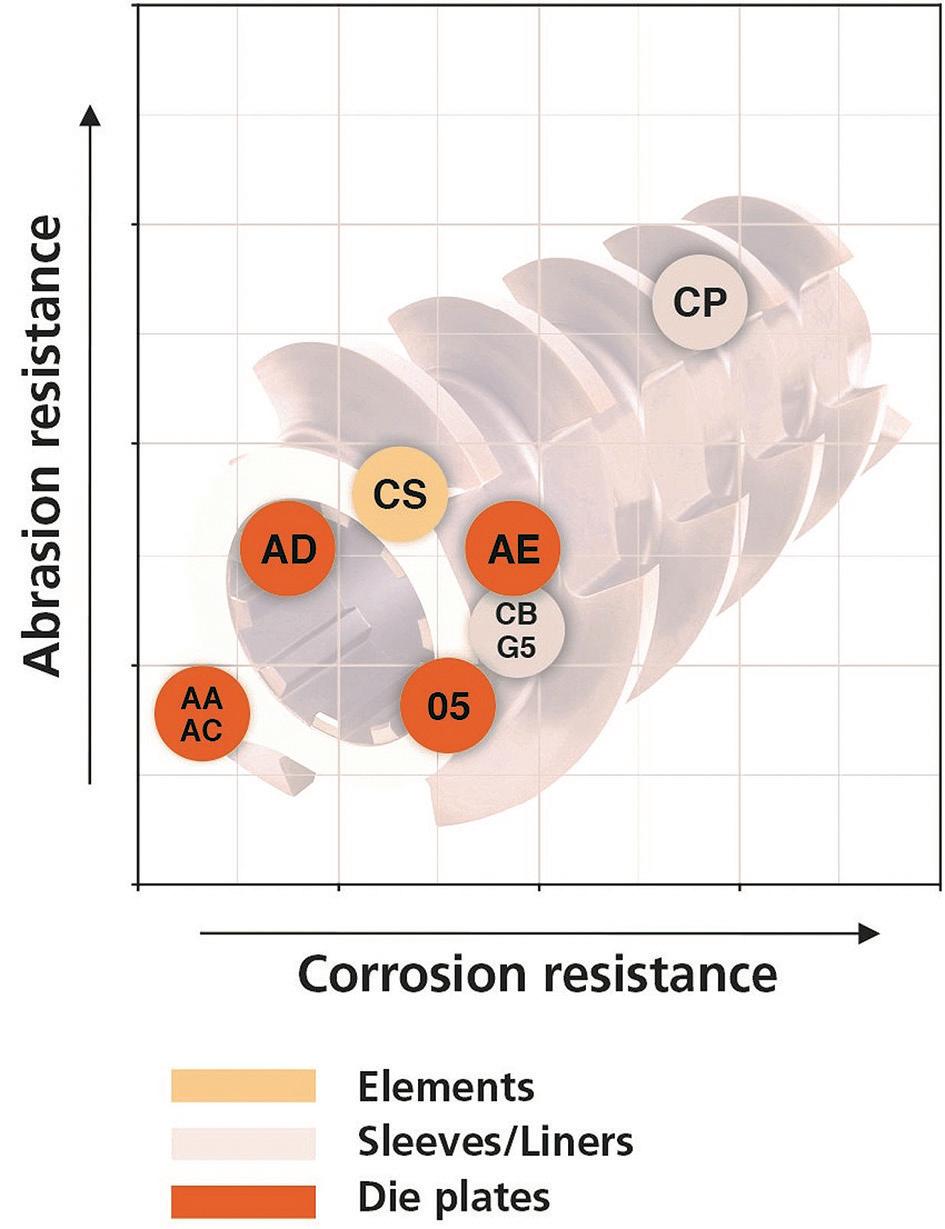
5 minute read
Extruder technology: A view from the wear side
Katharina Diehl, Carl Aug. Picard GmbH, Albert Keun, Pro-Consult Kolding Aps
Extrusion of aquatic feeds is a very broad and highly complex process considering the number of different aquatic species being farmed in the world today. Feeds for shrimp, eel, trout, salmon, catfish, carp, tilapia, milkfish, yellowtail, frog, etc. are some of the major aquatic feeds manufactured on either a single-screw or twin-screw extruder.
Aquatic feeds can be defined as floating feed, suspended feed and sinking feed. Cold-water fish, like salmonids and trout, normally are top feeders and require a highly expanded floating feed that must be stable in water for at least 10-15 minutes – the time required for top feeders to consume their feed. Seabass and seabream require suspended feed – they are not top or bottom feeders. Usually, warm-water fishes like carp, eel, tilapia, milkfish, shrimp, etc. are bottom feeders and require a denser sinking feed that must be stable in water for at least 30-60 minutes – the time required for bottom feeders to consume their feed.
Extruded aquatic feeds with good water stability are important for maintaining water quality and good conversion ratios.
Extrusion
The pre-set screw and barrel configurations represent many years of analytical design, research and comprehensive testing and have their own specifications to produce floating aquatic feeds, semimoist aquatic feeds, slowly sinking aquatic feeds and sinking aquatic feeds.
The first 25% of the extruder length normally is the transport section which utilizes twin flight transport screw elements. Then, the mixing and kneading zones come, utilizing cut flight reverse screw elements and both single and twin flight screw elements. The single flight screw elements serve the need to hold the pressure generated within the mixing, kneading and cooking zones constant and stable. The last 25% of the extruder length, called the cooking zone, utilizes single-flight feeding screw elements just before the die plate.
Moisture levels of 25-30% in the form of steam and water are a catalyst in extrusion. This moisture combined with the accumulated pressure from the cooking, mixing and kneading zones results in extraordinary wear of the screw elements starting at the outlet. Therefore, the choice of metallurgy used for both screw elements and barrel liners is extremely important. C.A.PICARD® does not only offer a wide range of metallurgies for aquatic feeds, pet food, plastics, etc., but have also optimized its

Figure 1. Material portfolio wear parts for single screw extruders.
Figure 2. Material portfolio elements for twin screw extruders.

Figure 3. Material portfolio liners/barrels.
through-hardened martensitic stainless steel screw elements that have proven to minimize both wear and abrasion in comparison to the metallurgies used on the market today. Figures 1-3 show C.A.PICARD®’s materials evaluations based on C.A.PICARD®’s experience, material analyses and information provided by the customers.
To tackle abrasive wear and the corrosive attack caused by steam, water or acid, C.A.PICARD®’s throughhardened stainless steels with enhanced carbon content can be applied. The through-hardened stainless steel used within each zone can be categorized into three groups depending on the wear resistance.
The first category is standard through-hardened stainless steel with low carbon content defined as “05” in C.A.PICARD®’s code. It has very good corrosion resistance but exhibits no special resistance against abrasion. It can be used within extruder transport zones where abrasive wear plays a tangential role. Should the abrasive wear be higher within the pressure build-up zones, then through-hardened stainless steel with an increased carbon content is used to protect the screw elements (C.A.PICARD®‘s code EE). The steel heat treatment plays a crucial role to find the right balance between hardness and corrosion resistance. However, there are instances in which this steel solution is not suitable. Then C.A.PICARD® can offer its premium metallurgy (C.A.PICARD®’s code 25) which is a combination of high carbon content and many other carbide-building elements with a sufficient chromium content to build a passive layer protecting the material against corrosive attack. In Figure 5, the wear resistance of these three C.A.PICARD®‘s metallurgies is compared.
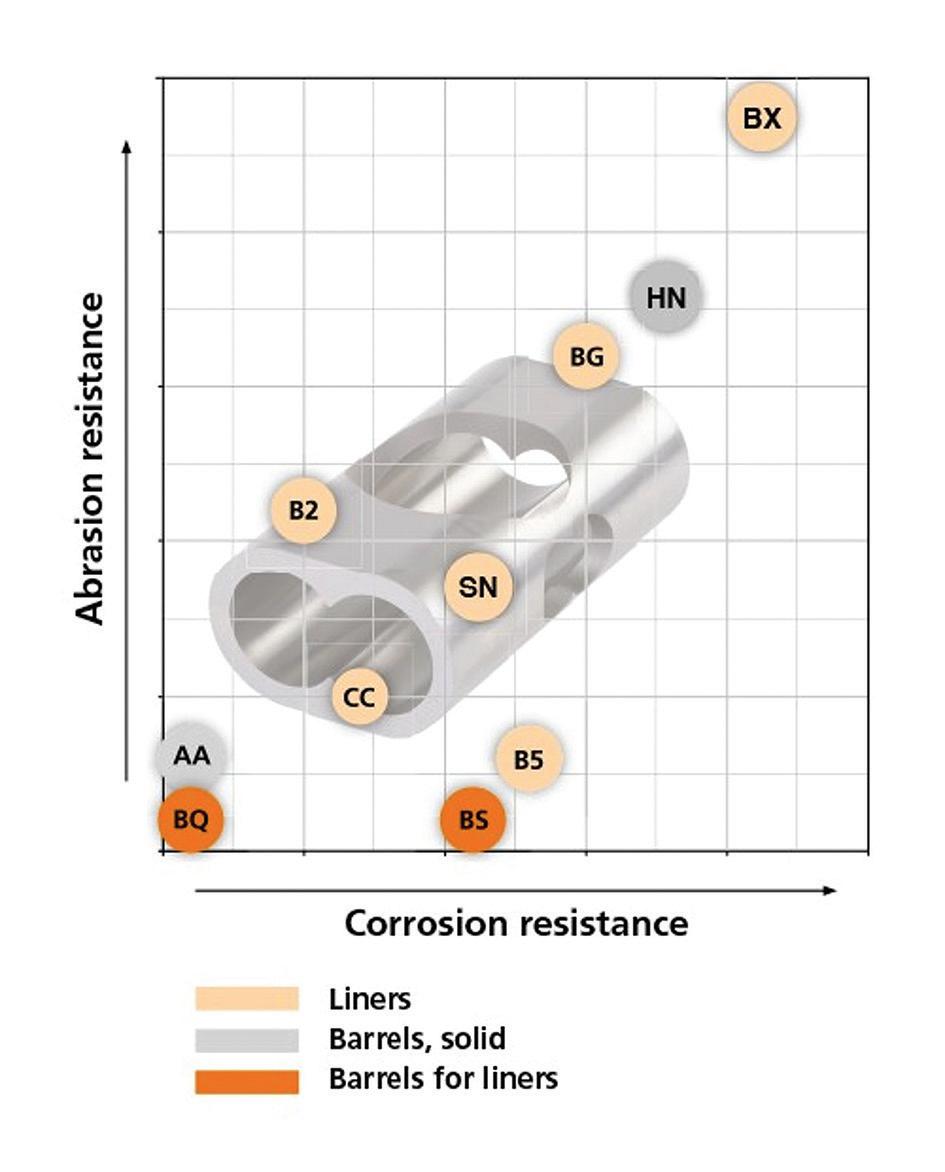
Different approach
It is well known that tribology always is a system property. That means the combination of product, screw configuration and liners/barrels must be considered. Originally, widespread common tool steel is used for the liners/barrels manufacturing aquatic feed.
C.A.PICARD® takes a different approach originating in their vast manufacturing experience and knowledge of working with twin-screw extruders. The liner within the barrel should have a longer lifetime than the screw elements as it is much more expensive to replace the liner than to replace the screw elements. Therefore, C.A.PICARD® recommends utilizing its premium metallurgy which offers a much higher wear and corrosion resistance that perfectly fits with all three zones of the extruder. Long downtime can be avoided, which will finally increase profitability.
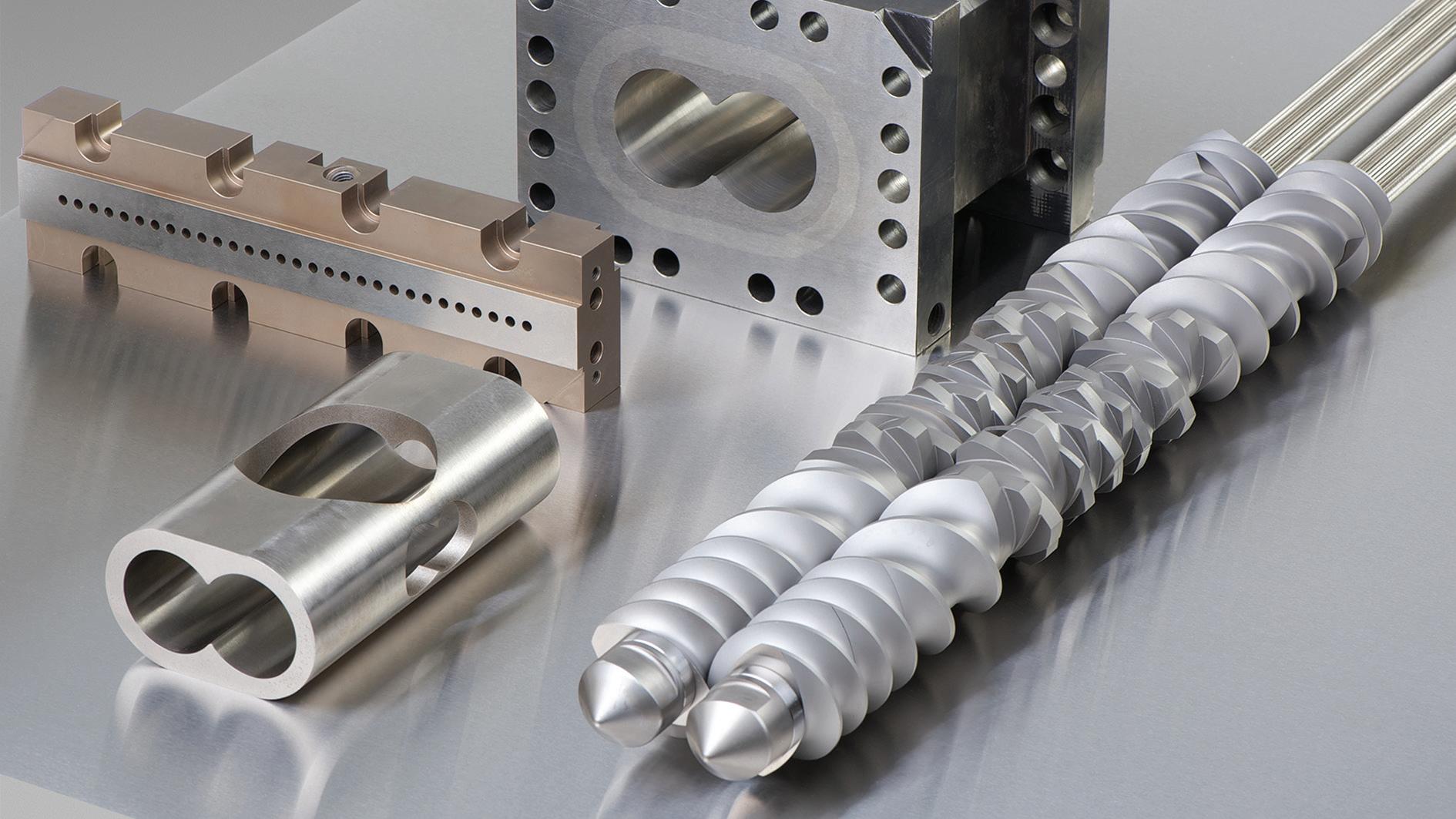
Figure 4. Product range Extruder Technology Division C.A.PICARD® .
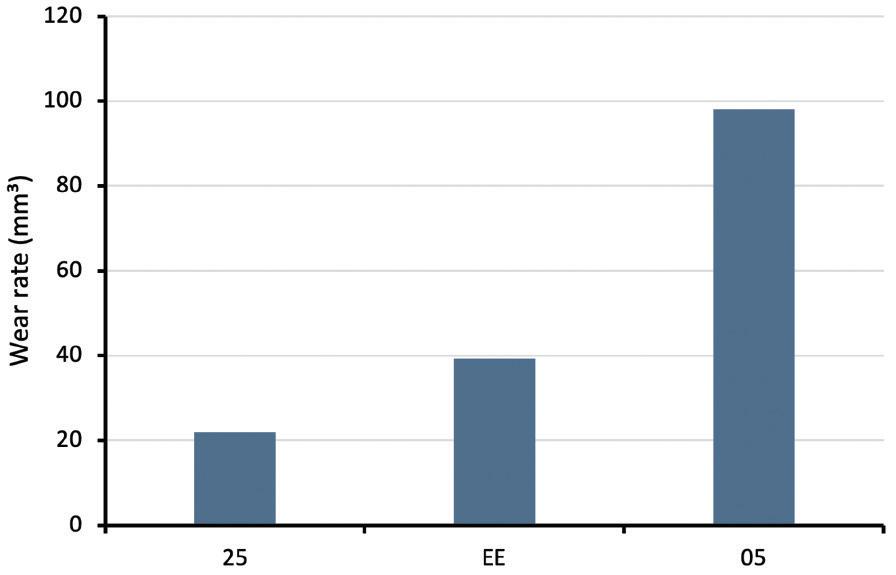
Figure 5. Wear resistance of C.A.PICARD®‘s metallurgies.
Furthermore, consultancy services are included in C.A.PICARD®’s supply to improve screw configurations leading to improved finished product quality, increased throughput and less extruder consumable spares.
Supply
C.A.PICARD® supplies extruder consumable spares for all leading extruder brands manufacturing aquatic feed. One of the numerous customers of C.A.PICARD® is BioMar A/S, one of the world's market leaders in manufacturing aquatic feed. C.A.PICARD® supplies a full range of screw elements, barrels/liners, shafts, etc. for BioMar A/S’s twin- and single-screw extruders. The introduction of high chromium, vanadium and nickel contents in C.A.PICARD®’s liners increased the life cycles and profitability of the liners noticeably.
With the supply of extruder consumable spares for all brands of extruders (single and twin screw), C.A.PICARD® has achieved and accumulated a vast portfolio of knowledge within the aquatic feed manufacturing technologies for both warm- and coldwater fish species.
More information: Katharina Diehl
Development Engineer Carl Aug. Picard GmbH E: Katharina.diehl@capicard.de