



Find out more about how Cordell Connect and Cordell Estimator Platinum can help your business grow
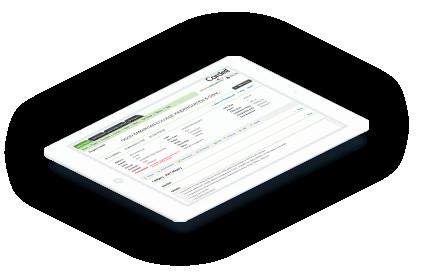

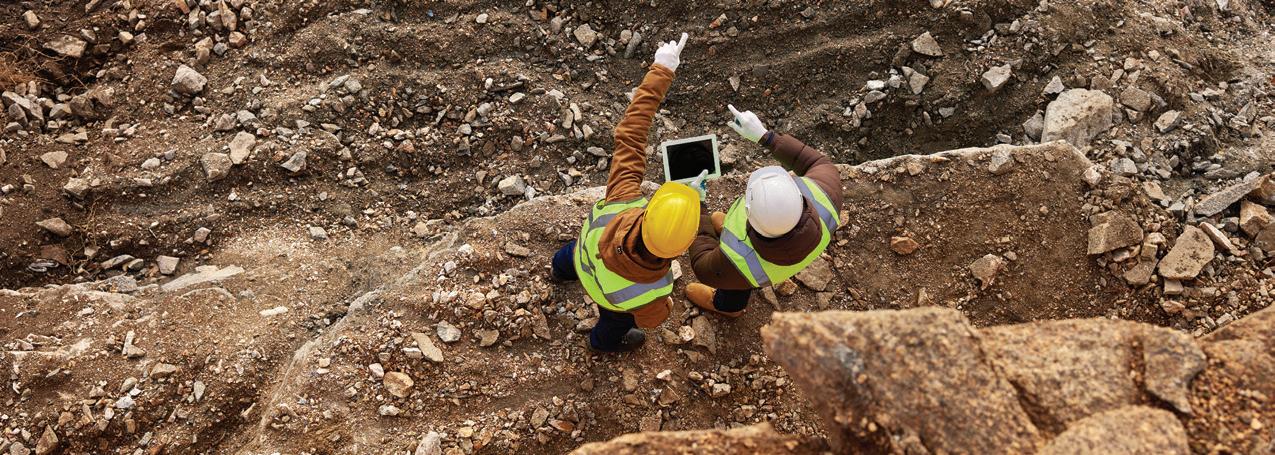
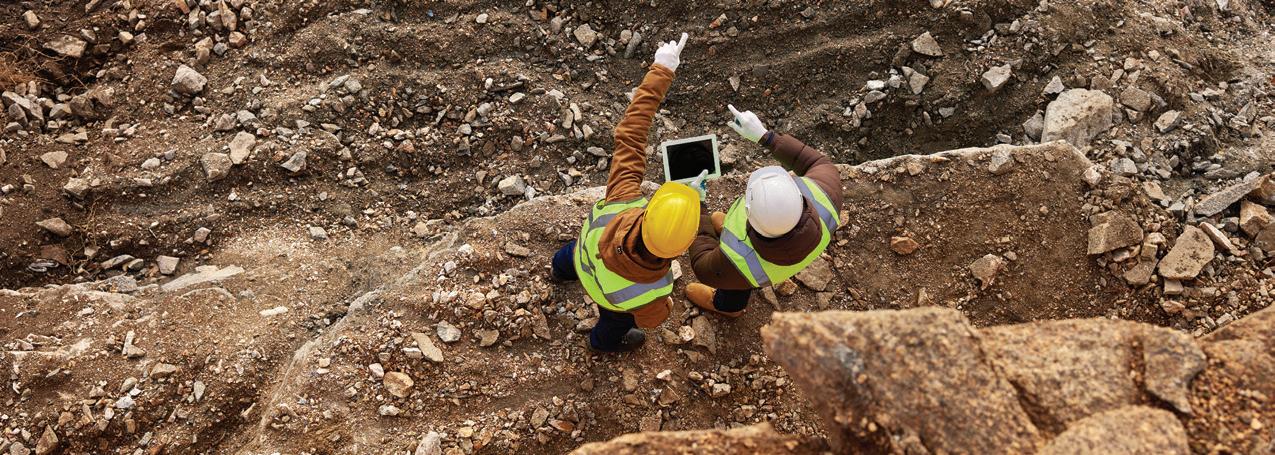
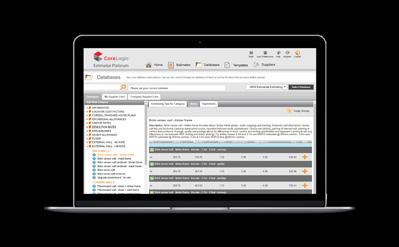

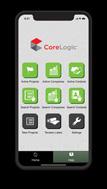
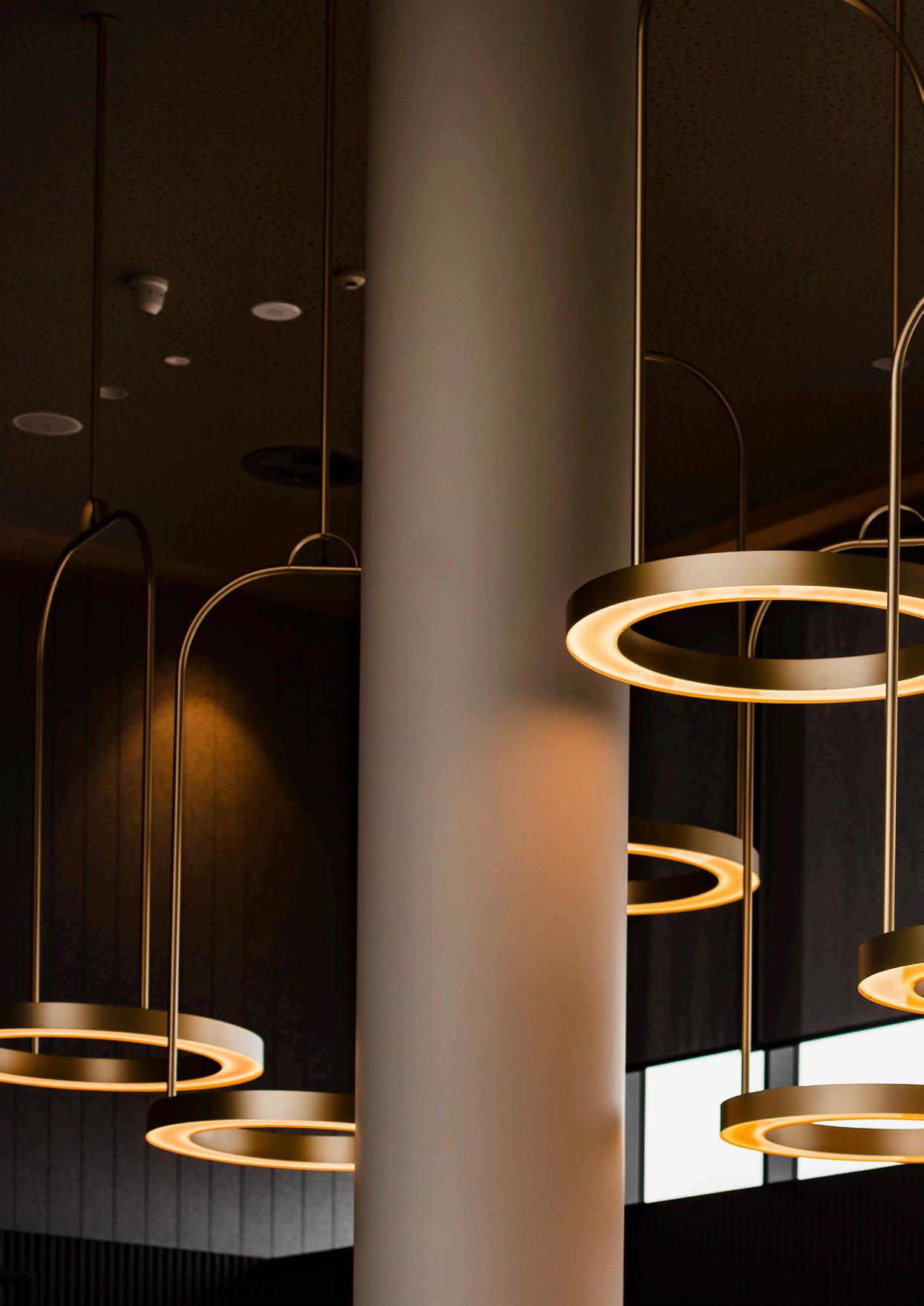
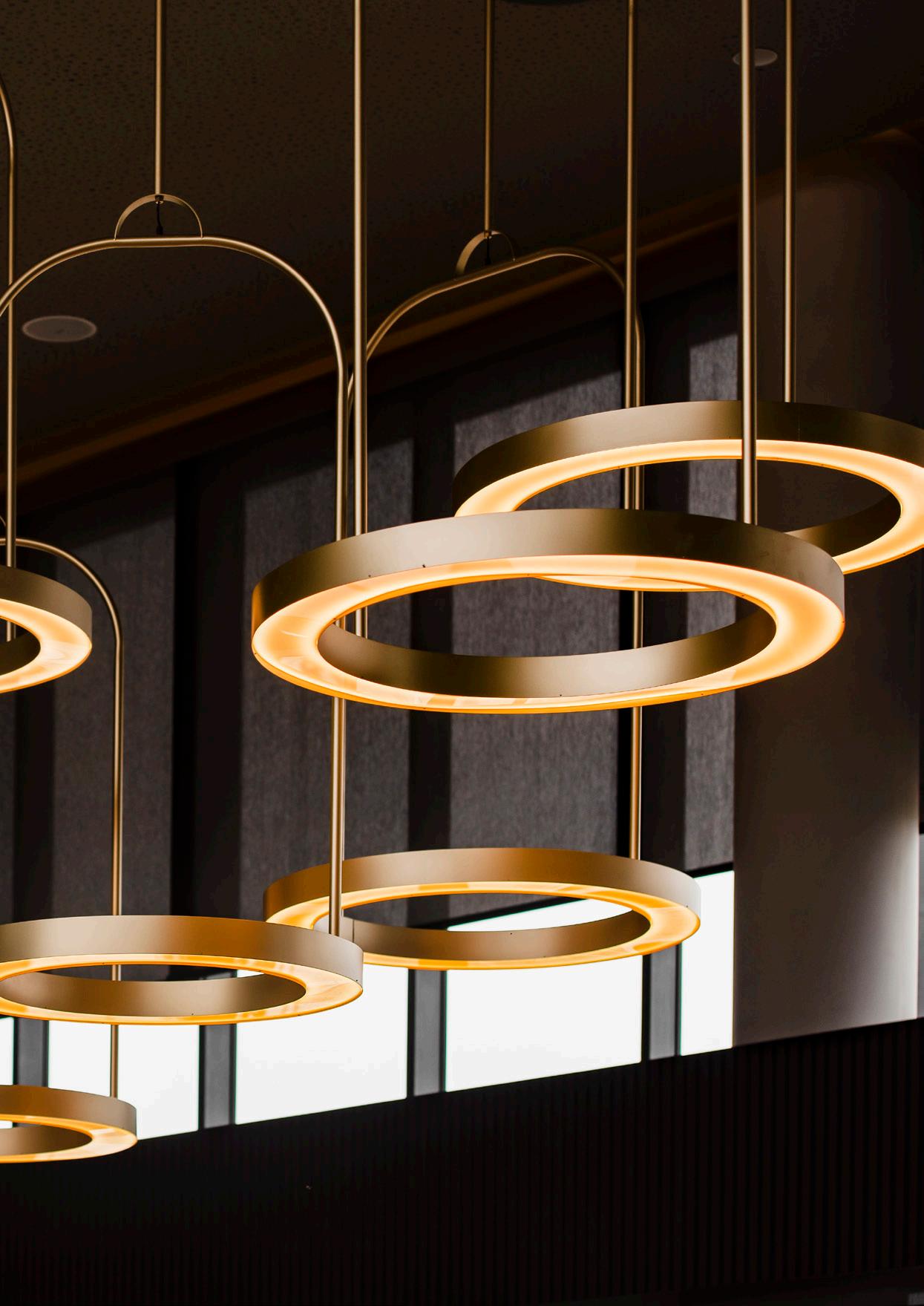
Find out more about how Cordell Connect and Cordell Estimator Platinum can help your business grow
Leading property developer Stockland has begun construction to deliver Perth’s first all-electric community in Western Australia – Stockland Wildflower – in Piara Waters, located in Piara Waters, 26km south of Perth’s CBD. By reducing energy costs and lessening carbon emissions, Stockland Wildflower presents a significant step towards healthier living in Western Australia.
Wildflower will comprise approximately 370 residential homes, each designed to empower residents to lead healthy and sustainable lifestyles through encouraging the use of induction cooktops, including provisions for electric vehicle charging points in each homeowner’s garage, and offering cool roof options designed to reflect more sunlight and absorb less heat than a standard roof.
These homes have the potential to reduce energy costs for residents, while also lessening emissions through improved energy efficiency.
“Wildflower will encourage Western Australians to embrace more energy efficient homes,” said Stockland General Manager (WA Communities), Col Dutton.
“Communities like Wildflower set the standard for future homes in Western Australia. As a leading creator of communities, Stockland can appeal to home buyers looking to make a more sustainable choice,” said Mr Dutton. “Plus, households can save money through lower energy costs, especially when coupled
with solar panels, insulation, and smarter air conditioning. The homes at Wildflower are a significant step as we continue to explore ways to boost our communities’ and residents’ own paths to decarbonisation,” added Mr Dutton.
Minister for the Environment and Climate Action, the Hon. Reece Whitby said it’s important for Australian businesses to take the lead when it comes to developing more energy efficient homes.
“A home is the biggest purchase most of us will ever make, and it’s important for owners to know that it’s energy efficient. It helps their hip pocket and the environment.”
Member for Jandakot, Yaz Mubarakai, said he was thrilled to see Stockland invest in sustainable new housing in his electorate.
“Piara Waters in my electorate has been a hotspot of innovation for the West Australian electricity grid, with the Project Symphony virtual power plant, and now Stockland’s first all-electric community in WA,” said Mr Mubarakai.
Wildflower will be well-connected to local shops, services, and schools, including the new Piara Waters Senior High School, located one kilometre from Wildflower, which is set to open in 2023.
We offer unique, cost effective and high quality professional aerial and site time lapse photography, along with video from drone, plane and helicopter for the construction and property industry.
SKYview has been in business for nearly 15 years servicing the construction industry, with over 25 years of onsite construction experience.
We can service everything from small residential projects to the largest of government projects, throughout NSW and ACT.
We are unconditionally certified, insured and operate from planes, helicopters and drones as required.
Schools are the heart of communities and play an enormous role in shaping not only places, but the lives of our future generations. When the communities are emerging, the role of the school is even more important, as these significant buildings define the character of the place, create a culture and bring people of diverse backgrounds together.
Appreciating the gravitas of this task, ARM embraced the opportunity to design and deliver a bundle of six schools for the Victorian School Building Authority. The new schools are located in Melbourne’s outer Western suburbs on the lands of the Wathaurung and Wurundjeri peoples of the Kulin Nation, in new and rapidly growing suburbs with unique community profiles.
It was paramount that these schools provided excellent facilities with 21st century learning environments to support students’ differentiated learning requirements. Our aim was to promote a sense of positivity and pride with a distinct character that was meaningful
to the place. The masterplans were carefully considered to create a strong civic presence with quality landscaped areas for seamless outdoor learning and play.
We created a template in partnership with VSBA that was replicable, versatile, equitable and affordable – but could be nuanced and customised to fit each school’s site and the community it serves.
Each school offers a variety of teaching and learning spaces, including places for group and individual learning, both collaborative and quiet. The study nooks have been a favourite of the students so far.
Five First Nations artists were appointed to transform the themes into artworks that would shape the schools' identities. These artworks have been translated into colour palettes and direct applications to the integral fabric of the school, in key elements such as facades, glazing details, ceiling and wall panels and carpet finishes, providing distinctive but inexpensive ways to distinguish the campuses.
Geoff Brock Minister, Government of South AustraliaThe patience, cooperation and engagement of local communities while construction works are being undertaken is one aspect of major infrastructure upgrade projects that I believe doesn’t always receive as much public recognition as it should.
On Saturday, 21 January, I attended a community event in Port Wakefield held by the Port Wakefield to Port Augusta Alliance (PW2PA) to thank the community for their cooperation and their patience during the construction of the Port Wakefield Overpass and Highway Duplication Project.
Hundreds of people attended the free event, which included live music, displays, free food, road safety awareness promotions and activities. It was a fantastic opportunity for myself and the project team to say thank you to the local community and celebrate the completion of the $124.5 million project.
Thank you to local communities for your patience and cooperation
- Minister,Geoff Brock
Continued from this page
• Realignment of the Balaklava Road intersection to allow for safer turns.
• New bridges over the Wakefield River.
The works have also improved parking through the town to support local businesses.
Port Wakefield Highway typically carries nearly 9,000 vehicles per day, however this can almost double during holiday peak periods and on long weekends.
While both the local and broader community
can now reap the benefits of the project, we’re indebted to both the local community and drivers passing through for their patience while construction works caused some level of disruption.
This is true for most road infrastructure project being delivered by the Australian and South Australian governments.
I encourage anybody passing through Port Wakefield to stop in, grab something from a local business, and support this town as part of your holiday travels – a sentiment I’d like to extend to all regional towns across the nation where works have been undertaken.
The project, which was jointly funded by the Australian and South Australian governments (80:20) has improved traffic flow and reduced congestion for all road users, as well as improving freight productivity along the National Land Transport Network.
Work completed includes:
• Two lanes in each direction through Port Wakefield, with allowance for safe U-turns.
• A new two-lane overpass for traffic travelling southbound from the Copper Coast Highway to Port Wakefield, and for traffic travelling along the Augusta Highway to the Copper Coast Highway.
• The removal of hazardous turns at the intersection of the Port Wakefield, Copper Coast and Augusta highways.
• Improved pedestrian access and landscaping in the township of Port Wakefield.
Last year’s changes to the National Construction Code have ensured the efficiency of Australia’s new builds will only get better. But net zero commitments and the energy cost crisis have created a significant opportunity for the construction industry in an unlikely space: existing buildings.
Industry estimates put the value of the national retrofit market for insulation alone at more than $20billion over the next three decades. That’s not to mention the market for electrification as the country transitions away from gas.
The size of the opportunity can’t be underestimated.
Jurisdictions around the country are beginning to mandate minimum insulation requirements in existing buildings, but a gap in appropriately skilled workers means right now, few businesses are in a position to take advantage of them.
Where residential upgrades face a shortage of insulation installers and the logistical issue of HVAC and hot water upgrades requiring multiple trades, the problem – and the opportunity – is bigger in commercial building retrofits, where upgrades to the performance of services requires specialised professional experience in optimising entire systems.
The Energy Efficiency Council is currently mapping the workforce needs for the coming retrofit wave, and we’re seeing a huge amount of interest from industry and government in this particular part of the future energy workforce.
With the performance of new builds getting better, there is a huge opportunity to ensure this is also the case for retrofits. And with governments increasingly aware of the benefits of efficient buildings in driving down both energy bills and emissions, the time to act is now.
Queensland’s first ever crane to be powered by 100% renewable diesel will be used to install large structural steel beams and precast concrete panels at Brisbane’s new theatre at Queensland Performing Arts Centre (QPAC).
Not currently manufactured or available in Australia, the renewable diesel was procured and imported to Queensland as part of a crossindustry collaboration between Lendlease, Queensland Government – Biofutures QLD and Department of State Development Infrastructure, Local Government and Planning – Refuelling Solutions and BSF Mobile Cranes. This initiative will demonstrate the viability of renewable diesel as a low carbon solution within the construction industry, ahead of the Queensland Government’s Oceania Biofuels’ refinery commencing operations in 2025.
The New Performing Arts Venue will increase the footprint of QPAC, making it the largest performing arts centre in Australia, with the potential to welcome an additional 300,000 visitors a year across five outstanding venue spaces.
In late 2022, Lendlease began using renewable diesel in tower cranes on the Powerhouse Parramatta project in Sydney, marking a first for Australia. The initiative is used in the majority of Lendlease’s construction projects in the United Kingdom, including Google’s headquarters in London.
Construction is responsible for 23% of global greenhouse gas emissions, with roughly 5.5% of these emissions directly caused by powering construction machinery and equipment, mainly through fossil fuel use such as mineral diesel.
Moving towards fossil fuel-free construction without the use of carbon offsets is a key part of Lendlease’s goal to reach ‘absolute zero carbon’ across construction, development, and investment management globally by 2040.
“Continuing to use biofuels locally will grow our local industry opportunities, making Queensland an attractive place for global and national businesses to set up biorefineries and biomanufacturing,” said Queensland Deputy Premier, Steven Miles.
“This Queensland-first trial, in partnership with Lendlease, is happening during construction of Queensland’s New Performing Arts Venue at South Bank.”
“In collaboration with our partners, we’re introducing the first renewable diesel to Queensland as we build Brisbane’s new theatre for QPAC, reducing greenhouse gas emissions by up to 90 per cent over the life cycle of the fuel compared to fossil diesel.”
“With Brisbane hosting the 2032 Olympic and Paralympic Games, we hope our initiative is a step towards a climate positive Games and inspires collective action for fossil-fuel free construction for contractors and the supply chain,” said Jerome Johnson, General Manager Construction QLD/NT, Lendlease.
The peak representative body of employers in the New South Wales civil construction and maintenance industry, the Civil Contractors Federation NSW (CCF NSW), has announced key results from a December 2022 survey of gender participation rates in the civil industry.
CCF NSW is delighted to report a considerable rise in females participating in civil-related roles since its last survey two years ago.
The landmark survey, which has previously informed NSW Government policy settings on female participation in construction, is the most detailed civil-specific industry workforce diversity survey in Australia.
The December 2022 results showed that females in specifically civil-related roles had risen from 5.7% in February 2021 to 9.9%, and females in all roles rose from 16.6% to 17.3%. The first CCF NSW gender participation survey in 2017 showed female participation in civil-related roles was a mere
4.2%. At that time, following over 12 months of research, CCF NSW launched its groundbreaking Women in Civil Program.
These results informed CCF NSW’s vision for female participation levels – equality in civil-related roles by 2050. Touchstones were established for tracking future progress, with 15% by 2030 being an early touchstone.
The NSW Government extensively consulted with CCF NSW in early 2022, subsequently setting their goal for the broader construction industry of 15% females by 2030.
Some of Australia’s biggest companies across construction, mining and agriculture have announced a funding partnership with medical research charity The Common Good to create the Tradie Health Institute.
Companies such as BESIX Watpac were invited to become founding partners of this world-first initiative due to their commitment to health and safety programs on their work sites.
“We wanted to work only with great companies who clearly valued the health of their tradies,” said Michael Hornby, CEO of The Common Good.
“Companies who take health and safety seriously, understand the problems and have the capacity to help other trade businesses and contractors.”
The recruitment of industry leaders will provide the base funding of the Tradie Health Institute – with the Institute’s first priority to tackle silicosis, a lung disease which may be impacting more than 600,000 current and retired tradies.
BESIX Watpac’s Mark Baker said they accepted the offer to be the first founding partner based on their health and safety priorities.
“We set up our BESIX Watpac Community Fund last year which includes supporting community health. We now have an opportunity to not only emphasise our commitment to the health of our staff and contractors, but to make a meaningful difference to the lives of those tradies across Australia who have been diagnosed with a trade related lung disease. Sadly, there are many out there who have not taken the right precautions or simply weren’t aware of the risks. I now call on other CEO’s to stand with BESIX Watpac and support The Tradie Health Institute in this battle against silicosis and other occupational lung conditions.”
The Tradie Health Institute is a collaboration with one of Australia’s largest lung hospitals and health services and is the only institute dedicated to powering medical discoveries to help tradies, companies across construction, mining and agriculture are being invited to partner.
Lauren Fahey General Manager, NAWICTHE LATEST NATIONAL PAY GAP DATA SHOWS WOMEN EARN ON AVERAGE $253.50 LESS THAN MEN EACH WEEK
The gap is even more so in the construction industry, being 16.1%.
“The gender pay gap is a handbrake on women’s ability to make ends meet. With inflation at 7.8%, and rising, everyday essentials are becoming increasingly unaffordable” The Workplace Gender Equality Agency (WGEA) says.
As many Australians struggle with sharp increases in the cost of groceries, energy, fuel and housing, NAWIC is calling attention to the disproportionate effect this persistent pay gap has for Australian women in construction.
An important part of promoting gender equality at work is allowing flexible work practices, portable long service and carers leave. This includes supporting men as carers and parents and making flexible work ok for them too.
We can do this by providing affordable childcare with hours of operation aligned to construction workplaces. We can do this by creating job share arrangements and staggered shifts that make construction industry roles part time and more flexible for women and carers.
Supporting women in construction is a significant way we can improve female economic security, overcome the skills and labour crisis, and deliver greater profitability and innovation to the construction industry. At NAWIC we think that’s worth advocating for.
Join us and be a #changemaker.
We rise together.
The upfront embodied emissions generated in the construction industry are looming as a costly challenge. Many construction businesses are turning to carbon offsets. But offset prices are expected to increase over the next decade, and Slattery’s calculations suggest that just one medium sized commercial office building could face a bill for carbon offsetting to the tune of $6.6 million.
The best way to reduce the cost of carbon offsets is to generate less greenhouse gas emissions – and this is why Environmental Product Declarations are fast becoming the cornerstone of construction industry strategies to reduce upfront embodied carbon.
EPDs offer high quality, credible, transparent and third-party verified environmental impacts data that complies with international standards. This data improves the quality of upfront embodied carbon assessments, and it is for this reason that Slattery’s team uses as many EPDs in our carbon plans as we can.
Increasingly, developers, specifiers, and carbon planners, are asking suppliers and manufacturers to provide EPDs for their products.
We expect EPDs to become business-asusual for most construction industry supply chains within just a few years. The competitive differentiator will not be whether a product has an EPD, but rather how its environmental impacts compare to competitors.
Decarbonisation is an obvious driver for EPDs, but they will also help the construction industry address other challenges, like waste generation, biodiversity loss and water scarcity. As quantity surveyors and carbon planners count the cost of construction, the EPD is one of our most trusted tools in the toolbox.
Charter Hall Group (Charter Hall or the Group) is pleased to announce the acquisition of a $290 million, A-Grade office tower in the heart of the Canberra CBD at 21 Genge Street.
Leased to our long-term tenant customer, the Commonwealth Government, the asset is occupied by the Australian Tax Office (ATO) and the Department of Veteran Affairs. The 42,000m2 twin tower development with a five year WALE, reflects a 7.5% initial yield.
This Charter Hall-managed partnership is owned by the $10 billion flagship wholesale office fund CPOF, together with Charter Hall Group. The investment strategy is to extend the WALE of the asset and take advantage of the modern buildings’ large floorplates and ideal location directly opposite the 260-retailer Canberra Centre shopping centre.
Charter Hall Office CEO, Carmel Hourigan, said, “We welcome two of our major existing customers to the $30 billion office portfolio
and look forward to adding value to the building for their benefit.
“Canberra’s office market is one of Australia’s most resilient office markets with low vacancy rates for prime stock, while large floor plates within a two-tower complex provides flexibility in meeting customers’ needs.”
Charter Hall Managing Director and Group CEO, David Harrison, added, “CPOF continues to curate its portfolio with modern office assets leased to blue chip customers. The relatively high passing yield provides enhanced distribution yields and total returns, while further enhancing resilience in the overall portfolio.”
21 Genge Street holds strong sustainability credentials, including carbon neutral certification and 5 Star NABERS Energy rating. It joins CPOF’s internationally recognised position as a Global Sector Leader in the 2022 Global Real Estate Sustainability Benchmark
Construction has begun at Hobart’s iconic Forestry building, which will be restored and given new life as an inner-city hub for learning, research and collaboration over the next two years.
The building, which has been vacant for many years, will be home to the University of Tasmania’s College of Business and Economics and Law School as well as administrative offices. When complete, the building will house 300 staff and support the studies of 3000 students.
Vice-Chancellor Professor Rufus Black said the $131 million project would provide improved, contemporary and more accessible facilities for students and staff, give the
community access to a beautiful piece of yearround green space in the heart of the city and support a vibrant Hobart.
“This new hub will be close to transport, jobs, shops and services and brings business, law and economics education and research into the heart of the city allowing increased collaborations with our partners as we work to solve real problems for real people,” said Executive Dean of the College of Business and Economics Professor, Stuart Crispin.
The City of Hobart approved the Development Application for the restoration last year. Works are expected to take two years to complete with staff and students to be using the building in 2025.
TTW has expanded its national presence within Australia, launching a Brisbane office following growing demand for expertise in engineering in the lead up to the 2032 Summer Olympics and significant residential and commercial plans for the region.
The office is under the leadership of Director Glen Fowlie with the help of newly appointed industry leader and Structural Engineer, Phil Latham as State Manager for Queensland. Glen said the move comes at a pivotal time for the region.
“For more than 60 years TTW has partnered with architects, developers, builders, and project managers to tackle the most complex projects and engineer their vision.
We are looking forward to bringing that expertise to the Queensland region through our holistic and hands-on approach to delivering
Engineering, Applied Science and Research, Physical Security, and Heritage Engineering.” Phil Latham said it’s a privilege to support the expansion of such a globally respected business into the region where his family calls home.
“We are seeing great opportunities for technical expertise in the lead up to the 2032 Summer Olympics and significant growth plans in architectural buildings and the health, education, defence, and infrastructure sectors. All these sectors are of focus and experience within TTW.
Currently we have a team of 10 and expanding quickly. We are finding significant interest in sustainable practices, Timber Engineering, and the use of Digital tools as ways to enhance our built environment.
The team is excited to bring our experience and expertise in these areas to the Queensland region. We currently have a number of local projects across Health, Tertiary Private, Defence and mixed-use developments.
The team is bringing our wealth of knowledge to our established and now new Brisbane based clients to fast become Brisbane’s partner in engineering.”
Beyond expansion activities, this year TTW has made a commitment to reduce upfront carbon by 50 per cent by 2030 through sustainability initiatives and an industry leading Carbon Calculator tool, which has been built inhouse by their Sustainability and Digital Engineering teams.
Robbie Claase Principal, Program Advisory, AureconInnovation in the construction industry has been noticeable by its absence. Despite advances in technology and the emergence of industrialised construction, our fragmented industry looks at infrastructure by individual projects, preventing the benefits of scaling, time and cost efficiencies.
However, there is a ground swell in Australia to transform capital works delivery. Cost escalation, labour shortage and a convergence of supply chain demand from all markets, are creating a perfect storm.
Having analysed several projects, it has become clear that just over half of the capital cost can be attributed to the asset value. The other cost is distributed between margin, fees, overheads and risk. Aurecon has been working to conceptualise how we can eliminate risk and minimise overheads, while reducing fees, protecting margins and maximising the end-value of the asset.
We have developed a model, harnessing modern methods of construction (MMC); enterprise commercial models, which address toxic cost-gouging; and digital tools, which enable integrated planning. Together they unlock value and the productivity required for a step-change.
However, for transformation to occur, it is vital that asset owning delivery teams be afforded the license to pursue the best outcomes, without being hamstrung by excessive rules and bureaucracy. This involves looking beyond the business case, through the entire asset value chain, including the relatively new ability to simulate tertiary benefits like social value.
our technical expertise across Structural, Civil, Traffic, Façade, and Construction Engineering. Our integrated approach combines our core services with the smarts behind Digital
You can learn more about how the company are helping clients meet their Embodied Carbon Reduction goals here: www.ttw.com. au/en-au/sustainability
Ultimately, those in charge of buying and delivering the cornerstone of our society, need to be afforded the opportunity to ask the right questions of the market.
The latest Property Council of Australia (PCA) data for January 2023 shows all the major CBD office markets (Sydney, Melbourne, Brisbane, Perth, Adelaide and Canberra Civic) were oversupplied, with vacancy rates ranging from 7.9% to 16.1%. Indeed, for these markets combined, the total office vacancy rate has risen from 7.8% since the start of the pandemic to 13.0% at January 2023.
Perhaps a little surprisingly, the main driver of rising vacancies over the last three years has been the result of above average office completions, rather than negative office demand (or net absorption). Between 2020 and 2022 inclusive, close to 1.01m2 of net additions have been added to the nation's office stock at the same time as net absorption was a positive 64,000m2 Our analysis shows, net additions during this period ran well above the long run average, focused on the Melbourne and Sydney CBDs.
On our forecasts, the phase of above average supply has a little further to run. Over the next two years, we expect a further 472,000m2 to be added to the major CBD office stocks nationally, focused on Sydney, Melbourne and Adelaide. Meanwhile, headwinds facing office demand are apparent.
Even though we think ‘underlying’ office employment levels have recovered lost ground since the start of the pandemic, the pace of growth slowed in H2 2022. We forecast modest office employment growth of circa 0.5% across the major markets this year as interest rates rise further and economic growth slows. We believe vacancy rates in the Sydney and Melbourne CBD office markets are at or close to their peaks, with Brisbane and Perth in the early recovery phase. Canberra Civic and Adelaide face near-term challenges from an uptick in supply. All markets are anticipated to experience a long, slow recovery, prolonged by the absorption of new supply.
Doka, one of the world’s leading suppliers of formwork with headquarters in Amstetten, Austria, completed the 100% acquisition of scaffolding manufacturer AT-PAC.
Both companies initially partnered in 2020 to provide comprehensive global site solutions. The acquisition positions Doka as a single source for formwork and scaffolding for the global construction industry and strengthens the company’s new global business segment, ‛Industrial Scaffolding’. For AT-PAC this means full access to a global market.
The potential for cooperation between the formwork expert and the US headquartered scaffolding specialist was already impressively demonstrated at bauma 2022 in Munich and generated significant interest from customers worldwide.
Doka and AT-PAC highlighted their strong partnership and successful collaboration with a dual-branded stand that was visited by over 100,000 visitors. The impressive 30m high Ringlock scaffolding landmark tower was
climbed by 7,000 selfie-takers to enjoy the spectacular views of the show grounds from the 20m viewing platform. The opportunities presented by combining the world’s leading formwork company with the global scaffolding specialist are enormous.
Robert Hauser, CEO of Doka, says “I am very enthusiastic about the opportunities that will be offered to existing and future customers, providing them with a wealth of knowledge, integrated products and turnkey solutions for formwork, shoring and scaffolding from a single source. This will allow us to continue to expand together and further strengthen our market position.”
The Energy Efficiency Council has welcomed the commitment from the Albanese Government to invest $600 million into decarbonising emissions intensive trade exposed industries, as part of its proposed reforms to the Safeguard Mechanism.
“We have entered a new era with two key features: high energy prices around the globe, and an ever increasing focus on cutting the emissions intensity of the products we use every day,” Energy Efficiency Council CEO, Luke Menzel said.
“In this new landscape, working with our most emissions intensive industries to decarbonise as quickly as possible is the best way to secure their long term competitiveness.”
Mr. Menzel said improving energy efficiency and pairing energy use with renewables are crucial parts of the decarbonisation effort. An independent, global scorecard released in April 2022 found that when it comes to industrial energy efficiency policy and
performance, Australia is a long way behind competitor countries. “Investing in improving the energy performance of our largest energy users is a no-brainer – it will reduce emissions, reduce exposure to volatile gas markets, and help transition Australian industry to a net zero future,” he said.
Mr. Menzel said the Government’s proposed reforms to the Safeguard Mechanism are also broadly on the right path, although further refinements are needed to ensure the scheme maintains its integrity.
“A well-designed and well-implemented Safeguard Mechanism reform package will send a clear signal to industry to invest in decarbonisation within Australia. Energy efficiency is one of a number of pathways with huge potential to help us reduce emissions quickly.”
“Improved energy performance will lower emissions and reduce energy bills, and the time is right to deploy it at scale.”
Conversion of a former rag trade building into a 34 room boutique Adelphi Hotel in 1992, put Denton Corker Marshall in the vanguard of the transformation of the City of Melbourne.
Characterised by bespoke furniture, sticks, stainless steel, aluminium and coloured planar surfaces, the hotel featured a radical 25m glass enclosed swimming pool extending over Flinders Lane street frontage at roof-top level.
2023 celebrates Denton Corker Marshall’s 50th year of transformative and thought-
provoking design – catalysts for change in the city and Australian architectural identity abroad.
Hacia Atherton CEO Empowered Women in TradesAustralia has long been a champion of female empowerment since 1902; the nation was only second to grant women voting rights internationally.
The Australian Sustainable Built Environment Council (ASBEC) has appointed a new president, sustainability champion Tanya Cox, as celebrated architect, Professor Ken Maher AO steps down after seven years in the role.
Ms Cox is a non-executive director of various ASX-listed and unlisted boards. She is the former chair of the Green Building Council of Australia and World Green Building Council and was chief operating officer of Dexus Property Group for 11 years.
The official appointment was made at ASBEC’s Annual General Meeting on Thursday 1st December 2022 after a lengthy executive search.
“ASBEC plays a unique role as the peak collaborative forum for organisations that champion sustainable, productive and resilient buildings, communities and cities,” Ms Cox says.
“I am honoured to take on the position of chair as ASBEC pursues an ambitious agenda. Supporting the transition to an integrated, sustainable and climate resilient built environment, strengthening regulations and ensuring all Australians have healthy and comfortable homes, offices and buildings are big challenges.
“These challenges will only be achieved through collaboration, and ASBEC's role has never been more central to Australia’s future as a low-emissions nation.”
“Ken has been a strong and steady voice for sustainability in the built environment. Under
“Ken’s commitment to collaboration has expanded ASBEC’s membership into new areas, bringing together an array of industry sectors with community advocates to push for stronger building standards, champion net zero targets and lay the foundations for sustainable homes.”
Among ASBEC’s achievements during Professor Maher’s tenure are ground-breaking research and reports that strengthened the case for net zero buildings, including Low Carbon High Performance (2016), Built to Perform (2018) and Every Building Counts (2019).
“Ken leaves ASBEC in a position of strength, with an engaged board of industry leaders, a growing network of members and a clear strategy as we drive change in the decade of decarbonisation,” Ms Cox concludes.
Now, that same assurance can be extended towards economic security and vast career opportunities in skilled trades by propelling the representation from its current 3% up to 30% within eight years.
This tremendous undertaking should serve as yet another example of Australian leadership setting new standards worldwide for equal access and opportunity!
Professor Loosemore’s research reveals that increasing the number of female tradespeople could drive Australia’s economic growth by 11%, a significant improvement in our GDP over the next decade.
Furthermore, providing more women with access to skilled trade careers will not only help overcome severe skill shortages and bolster economic development, but it can also give them greater financial autonomy, which has been diminished by job losses in “pink recession” from the pandemic.
The Empowered Women in Trades programs are crafted to empower female and nonbinary people to make an informed decision about a career in skilled trades. The programs achieve this by introducing them to various trades and offering insight into relevant industries.
They also create an environment where women can band together as they explore the possibilities open before them in the world of trade - providing comfort and courage for each woman’s journey.
Councillor Mark Johnson, Mayor of Moree Plains Shire Council, has featured in a new video from Inland Rail to help promote the benefits that the Brisbane to Melbourne freight rail line will bring to rural and regional communities like Moree along the alignment.
Moree is at the heart of the Narrabri to North Star (N2NS) section of the Inland Rail program, helping the council secure $194 million investment from the New South
Wales Government to fund the first stage of design and construction of the Moree Special Activation Precinct (SAP).
Despite the challenges posed by the current local and global economic headwinds, Australia’s industrial sector is poised to remain strong over the course of 2023.
According to Cushman & Wakefield, the industrial land market especially across NSW is expected to grow even tighter, coupled with significant positive tailwinds with continual rental reversion. In some prime/core markets, rents are expected to continue to grow, while they may stabilise in other non-core markets.
Tony Iuliano, Cushman & Wakefield’s International Director, Head of Industrial & Logistics – ANZ, said “Our real time intelligence tells us we are expecting at a minimum 10% rental growth for 2023/24 with vacancy currently sitting at 0.4%”.
In light of this, Cushman and Wakefield is investing heavily in bringing top class operators and teams together, with the appointment of seven new brokers to its Brokerage Industrial and Logistics team in NSW.
Sydney's industrial property market, particularly in Western Sydney, is evolving at a rapid pace, requiring adaptive thinking and an innovative approach to agency and brokerage. Our deep understanding of the market conditions, occupier demand and investor requirements will certainly be an asset to all of our clients, and new clients in the future.
I will be stepping into the role as Cushman & Wakefield’s National Director, Head of Brokerage Industrial & Logistics ANZ with Fab Dalfonso, Carl Pearce, Kieran Tsipidis, Nick Brooks, Alistar Siokos and Aston DalfonsoBrokerage Industrial & Logistics West & South West NSW, joining the team.
For more information visit cushwk.co/3ZOGw3V
“The Special Activation Precinct opportunity probably wouldn’t have presented itself to our shire without the Inland Rail,” Mayor, Mark Johnson, says. “The SAP is a once in a generation opportunity for this town. We’ve had 10-15 years of declining population and for the first time the state government is projecting that we will actually have a population increase.
‘The SAP is going to be a wonderful opportunity for this town over the next 40 years. The state government is projecting our population will increase by up to 4,000 people.”
In addition to the significant benefis that the SAP will bring to Moree, Mayor, Cr Johnson also says that the arrival of Inland Rail will deliver huge gains for local farmers by lowering their cost of taking goods to market.
For the fifth year running, KPMG Australia and the Australian Institute of Project Management (AIPM) have joined forces to deliver arguably the most anticipated, comprehensive and respected annual snapshot of the Australian project management landscape.
This year’s report highlights the key findings from a survey of over 300 diverse Australian project professionals in July and August of 2022.
In addition to maintaining consistency with previous years’ questions to identify any longitudinal trends, the survey included questions on salary for the first time this year as well as taking a pulse on current trends in the market.
The project leadership community is dealing with greater complexity and uncertainty, requiring increased responsiveness and resilience. A key challenge for the profession is honing skills to stay ahead of the curve. The core purpose of the project management profession is to deliver successful projects.
COVID-19 restrictions lifted but the residual impacts were still there. Coupled with international unrest, project professionals faced major economic challenges. Inflation was at record levels, and shortages of materials and people impacted budgets and delivery timing.
The perception of effective management of projects has slipped compared to 2020, and so have most success metrics.
Oreana Property has revealed plans for a new village shopping centre and vibrant piazza to bring Tarneit residents together and improve amenity in this fast growing suburb.
The Melbourne-based developer has lodged a permit application to develop a local town centre at 800 Derrimut Road – a 1.4 hectare site surrounded by three new masterplanned communities – Bluestone, Creekstone and Harlow.
Oreana’s town centre will provide connectivity and services to thousands of new residents, in addition to Tarneit’s already burgeoning population. The planned village centre will include a 1,000m2 supermarket, gym, medical centre, shops, restaurants and childcare centre alongside 23 townhouses delivering contemporary, convenient living.
The town centre will include a village piazza connecting abutting waterways on the site’s western side and new parkland to the east, creating a central hub for residents.
The architecturally designed townhouses will extend either side of the of the town centre, facing outwards with uninterrupted views of the wetlands or Robinsons Farm Parkland reserve.
Oreana Property Managing Director, Tony Sass said his team had worked closely with the project’s architects, Clarke Hopkins Clarke, and the estate developer, Satterley, to create a vibrant mixed-use development that would become the centerpiece of the community.
“We want to provide a space for the local community that is both beautiful and inviting, while also functional and convenient,” he said. “A key feature of the design is fostering connection from the adjoining waterways and parkland through the centre, which culminates in the proposed new village piazza.
“Our vision is that the centre and its piazza will become a meeting place where the Tarneit community can shop, eat and access vital community services.”
“Current talks around changes to IR laws should unequivocally exclude any changes to the right of Australian tradies to work as independent contractors,” said Jocelyn Martin, HIA Deputy Managing Director – Policy & Industry.
“Independent contracting arrangements are a long-standing feature of the residential building industry. The industry relies on these work arrangements as a way of productively managing the needs of building businesses, especially smaller businesses,” said Ms Martin.
“HIA estimates that over 80% of the work completed in the sector is performed by
independent contractors. For residential builders, it provides a flexible, workable and efficient model for engaging workers and managing the peaks and troughs of the home building cycle. Builders rely on access to good and reliable trade contractors to maintain competitiveness.”
“HIA suggests there needs to be a single national objective test, based on the ATO’s approach, to distinguish employees from independent contractors.”
The advantage of this approach is that instead of defining an ’employee’, the rules merely identify who is an independent contractor.
Technology, in its many manifestations, has been pervasive in our everyday lives for quite some time and has reshaped how we do just about everything.
With the urgency of climate change, societal challenges such as urbanisation, ageing populations and socioeconomic inequality, the focus of the entire architectural profession has shifted on a grand scale. It is now imperative that architects and urban designers look for solutions to design a healthier, more resilient and impactful built environment.
In our latest report “The many (inter)faces of technology in the built environment”, we parse through the key question of how can we adopt and adapt technological innovations for the benefit of all.
To do so, we sat down with our colleagues René Toet (Senior Architect/Associate at UNStudio), Alexander Kalachev (Senior Architect/Associate at UNStudio), Ren Yee (Head of Innovation Strategy) and Huey Chan (Strategic Designer) to discuss the numerous ways we at UNStudio are bridging the gap between architecture, technology, construction and the end users.
From BIM to urban mining, from energy consumption to waste management, even to the way we design streets and public spaces, technology can play a key role in how we design, construct and experience the built environment.
In recent years, new technologies have been adopted quickly by the design industry, to the benefit of all stakeholders. And while the construction industry could be more proactive in its wide scale use of new technologies onsite, post-occupancy services are currently undergoing an exciting and innovative period of research and development.
An innovative trial of a five-day work week, a six-month parental leave policy and nation-building infrastructure projects that are growing the female talent pool are among the winners of the 2022 NAWIC Awards for Excellence.
The NAWIC Awards for Excellence is Australia’s largest awards program for women in construction and is hosted by the National Association of Women in Construction NSW Chapter.
More than 1,100 guests gathered at the ICC Ballroom in Sydney for the second time in 2022 – following a hiatus in 2021 – to celebrate 40 finalists in 13 categories.
“The NAWIC Awards for Excellence showcase the achievements of women in construction, building and related industries, and applaud the hard work of women, men and organisations to make our industry more diverse and inclusive,” says NAWIC NSW President, Georgia Coulston.
Construction giant Laing O’Rourke was presented with the night’s most prestigious
prize, the Lendlease Crystal Vision Award, for an equal parenting policy that provides six months’ leave on full pay regardless of gender.
“Laing O’Rourke is committed to a 50/50 balance between men and women by 2033. Achieving this ambition demands a suite of innovative policies, and this industryfirst approach will help Laing O’Rourke to improve gender balance while attracting and retaining the top talent.”
Transport for NSW picked up three awards, with Deanne Forrest, Ashma Husna and Vivien Murnane applauded for their work on nation-building infrastructure projects.
“The NSW Government is delivering the largest transport infrastructure program in Australia’s history and is using this opportunity to not only shape our cities, but to also create a stronger and more diverse workforce. The collaboration between client, contractor and subcontractor is essential to see true change and ensure a sustainable future for our industry,” Ms Coulston notes.
Global Head of Design at Hassell, Liz Westgarth, was named Richard Crookes Business Woman of the Year. “Liz is passionate about the contributions that women make to design and is championing diversity to deliver creative design solutions that best reflect communities and drive systematic change.”
Roberts Co, Health Infrastructure NSW and University of NSW took home the John Holland Award for Team Innovation for a ‘game-changing’ trial of a five-day work week on the Concord Hospital Redevelopment Project that has since been adopted by other construction companies.
John Holland’s Construction Director, Steve Kiddle was named the ADCO Champion of Change for a multi-faceted approach to diversity. “Steve faces complex engineering challenges every day and works with his team to innovate and push boundaries to overcome them. He has applied the same approach to diversity with a genuine commitment to create an inclusive environment for all,” Ms Coulston says.
“We applaud the leaders and innovators who have stepped up their efforts over the last year to enhance inclusion, flexibility and wellbeing across countless companies and to demonstrate why a diverse construction industry is in the best interests of our entire nation.”
Transport for NSW Tradesperson Scholarship
Winner: Allyssa Hudson
Ferrovial Project Manager of the Year Award
Winner: Ashma Husna, Transport for NSW
CPB Contractors Award for Contribution to Sustainability
Winner: Megan Lohrisch and Ciere Kenny, Lendlease
Roberts Co Award for Contribution to a Project’s Development
Winner: Deanne Forrest, Transport for NSW
Laing O’Rourke Future Leader Scholarship
Winner: Emily Crozier, Laing O’Rourke
MPA Award for Achievement in Construction, Refurbishment and Fitout
Winner: Erin Doyle, Mirvac
Hassell Innovation in Design Award
Winner: Amy Clark, Aurecon
Richard Crookes Business Woman of the Year
Winner: Liz Westgarth, Hassell
John Holland Award for Team Innovation
Winner: Roberts Co, Health Infrastructure NSW and University of NSW
Established in 1995, the National Association of Women in Construction (NAWIC) champions and empowers women in the construction and related industries to reach their full potential. NAWIC’s vision is an equitable industry within which women fully participate, and it values are: Courage, Inclusion, Resilience, Integrity, Safety & Wellbeing.
The NAWIC NSW Chapter is a passionate group of women who volunteer their time and expertise to host and deliver a range of events aimed at furthering women in the construction industry. The committee and NAWIC members work in a variety of fields within the construction industry and the Chapter’s activities are designed to address the diversity of these groups.
Generate Property Group University
Scholarship
Winner: Miranda Swift, Charles Sturt University
ADCO Champion of Change
Winner: Steve Kiddle, John Holland
Acoustic Logic Regional Woman of the Year
Winner: Vivien Murnane, Transport for NSW
Lendlease Crystal Vision Award for Advancing the Interests of Women in the Construction Industry
Winner: Laing O’Rourke
NAWIC NSW’s goal is to celebrate the achievements of female colleagues in the construction industry as well as to inform, educate and provide networking opportunities.
In November, the National Women in Construction’s WA Chapter celebrated their annual WA NAWIC Awards for Excellence, recognising the achievements and industry advancements of WA women in construction.
The winners were announced at a gala lunch on Friday 11 November at Optus Stadium, where 650 people from across the construction industry gathered to recognise more than 80 finalists.
NAWIC WA President Eileen Wong said the bar continues to get raised year on year.
“This year’s winners represent the enormous contribution women make to the construction industry. Unique in their own ways, this year’s judges had trouble choosing winners with every submission worthy of the title,” she explains.
“It’s been an incredible year for gender equality on a national level, with the mobilisation of the Women's Economic Equality Taskforce and most recently, the increase in the paid parental leave scheme to 26 weeks and with fathers and secondary carers encouraged to use their entitlements and divide the responsibility of childcare more evenly.
“This will go a long way to bridging the gap in gender equity. The statistics for WA, and particularly in our industry, are still shockingly low however I am confident that the seeds we have sowed over the last few years will come to fruit. Especially if our award winners have anything to do with it.”
Congratulations to our incredibly inspiring winners, and thank you to our generous sponsors, of which this event couldn't be possible.
Swan Group WA Crystal Vision Award
Winner: Ellie Robson
Commendation: Laing O'Rourke
Curtin University Excellence in Sustainability Award
Winner: Grace Hahnel
Connect Resources Business and Leadership Award
Winner: Ashleigh Freeman
Arup Achievement in Health, Safety and Social Responsibility Award
Winner: Michelle Clarke
ADCO Constructions Trainee, Apprentice or Student of the Year Award
Winner: Chelsea Douglas
TBH Outstanding Achievement in Construction Award
Winner: Jillian McGinley
Built. Creating the Best Project Award
Winner: Josephine Macri
RPS Tradeswomen of the Year Award
Winner: Jazzmin Stevenson
Hassell Emerging Talent Award
Winner: Saba Munir Ahmed
Stantec Diversity and Inclusion Award
Winner: Cynthia Calderon
Australia’s peak industry body for the civil construction industry, the Civil Contractors Federation (CCF), is pleased to announce the winners of the 2022 Civil Contractors Federation National Earth Awards.
The CCF National Earth Awards are the most prestigious awards in civil infrastructure recognising excellence in civil construction across a range of sectors.
The winners were announced at a Gala Dinner on Friday 11 November 2022 at the Hotel Realm in Canberra, where 250 people from across the civil construction industry gathered to recognise 47 finalists, all of whom were category winners at the state and territory level.
“I congratulate all finalists involved in the 2022 CCF National Earth Awards and commend them for delivering civil construction projects to the highest of standards,” said Chris Melham, Chief Executive Officer, CCF National. “All of the projects have demonstrated best practice in their respective areas, including roads, bridges, drainage, rail and utilities.
“I particularly commend our seven category winners, who have been judged the ‘best of the best’ by our independent judging panel who I also thank for their invaluable assistance.
“I also thank our sponsors - PSC Insurance Brokers, the official insurance partner of CCF National, and the Australian Construction Industry Redundancy Trust,” he said.
The CCF National Earth Awards are presented in seven groups, according to project value and entrants are judged on set criteria including:
• Project and Construction Management
• Innovation
• People Development & Training
• Quality Management
• Safety Management
• Environment Management
• Stakeholders Management
The Winners
Project Value Up to $2m
Kentish Council and Treloar Civil & Quarries Pty Ltd
Wilks Road Extension
Improved road access to Lorinna, a small rural community comprising 65 properties situated in North-West Tasmania.
Project Value $2m to $5m
Select Civil Avon Dam Road Bridge Replacement
Design and construction of a replacement bridge along Avon Dam Road, providing access to Avon Dam in NSW.
Project Value $5m to $10m
Rob Carr Pty Ltd and Water Corporation
Gnangara Branch Sewer Section 2
Significant upgrades to the sewer network in Perth’s northern suburbs.
Project Value $10m to $30m
McMahon Services Australia Pty Ltd
The Australian Bragg Centre for Proton Therapy & Research - Civil and Environmental Remediation Works
Site investigations, demolition, bulk earthworks and remediation for the basement and bunker levels of the new $500 million Australian Bragg Centre in Adelaide’s BioMed City precinct.
Project Value $30m to $75m
Georgiou Group / Brady Marine and Civil Joint Venture
Indooroopilly Riverwalk
Construction of a 790-metre, 5-metre-wide bridge providing a pedestrian and two-way cycle facility over the Brisbane River.
Project Value $75m to $150m
Downer EDI
Denny Avenue Level Crossing Removal
Removal of the Denny Avenue Level Crossing, construction of a rail bridge and road underpass, upgrade of the surrounding road networks and revitalisation works in Perth’s Kelmscott town centre.
Project Value Greater than $150m
McConnell Dowell/DECMIL Joint Venture
Mordialloc Freeway
Design and construction of the new Mordialloc Freeway in Melbourne included several grade-separated interchanges, 400-metre twin bridges over sensitive wetlands and a shared walking and cycling path along the length of the project.
Civil Contractors Federation www.civilcontractors.com
Mitsubushi Heavy Industries Air-Conditioning Australia, Pty. Ltd., applied their exceptional experience to create a eco-friendly and high efficient heating and cooling solution for the new Ōpuke Thermal Pools and Spa, located in Methven on the Southern Island of New Zealand/Aotearoa.
Ōpuke Thermal Pools and Spa is a brand new, opulent resort offering an unrivalled relaxing experience in the beautiful surrounds of Methven on the Southern Island of New Zealand/ Aotearoa.
At Ōpuke sustainability is at the heart of everything they do, from operations to water maintenance, to food and beverage. They aim to be a leader within the industry and offer an eco-conscious facility to be proud of. Ōpuke Thermal Pools and Spa source water from the Rangitata river that is fed by the glacial melt water emerging from the spectacular Southern Alps. An industry-leading water-treatment system ensures exceptional purity of the bathing water.
Ōpuke Thermal Pools and Spa is the first facility operating with a Solar Field, a large array of solar thermal collectors, occupying approximately a quarter of the site, serving as the primary pool water heating system – even on the shortest day in winter, 100% of the pool heating load is met by the solar array.
Pool water is transferred to insulated holding tanks outside of operating hours to minimise heat losses. Excess solar energy is stored in buffer tanks and used in combination with energy efficient
The brand new resort required a quiet, flexible and highly efficient heating and cooling solution for the various spaces within the building, including the massage rooms and reception/common areas.
With Methven regularly reaching sub-zero temperatures during winter, and the large floor to ceiling glass windows of both the common area and the other rooms, the proposed solution needed to be reliable and robust and be able to handle the cold ambient temperatures the area experiences. The quality of installation and overall product was key and needed to reflect the clean and modern design of the newly constructed space.
After careful consideration of all aspects and requirements of the project and working closely with experienced and trusted contractors Airtech, a mixture of ducted indoor units, compact ceiling cassettes
and high wall systems, combined with MHIAA’s highly efficient KX series of VRF systems were ultimately chosen for the project.
Boasting an EER of 3.47 & COP of 4.12, the KXZXRE1 series of high COP heat recovery VRF systems offered a quiet, flexible, and high efficiency solution for the project. These systems were connected in multiformat to a number of FDUM series of indoor units as well as several FDK high wall systems and FDTC series compact ceiling cassettes.
This particular system services the numerous smaller spaces including the private massage and treatment rooms.
The medium-static, slim profile fan coils of the FDUM series are perfect to heat due to their super quiet operation and their hidden design, with the only visible portions being small grilles which blend perfectly with the modern and sleek design of the interior spaces.
A KXZE1 VRF system was paired with two larger FDU series slim profile ducted systems to service the larger common areas within the facility. These offered a reliable, robust and highly efficient heating solution for these spaces while also being quiet during operation to match the tranquil atmosphere within the resort.
Airtech provided quality design and installation which was executed to the highest level, and backed with a premium product provided a flexible high performing finished solution which allowed Mitsubishi Heavy Industries to offer the perfect solution for this new luxurious space.
For more information contact Mitsubushi Heavy Industries Air-Conditioning Australia, Pty. Ltd., Block E, 391 Park Road, Regents Park NSW 2143, phone 1300 130 007, email info@mhiaa. com.au, website www.mhiaa.com.au
Soldier Tower Cranes & Labour Services (Soldier), a highly experienced operator in Australia’s construction industry, provides a comprehensive service for builders and construction companies of any scale. Soldier offer a large fleet of cranes, hoists and labour division including crane operators, riggers, hoist operators, RTA Certified traffic control division and skilled labour.
At a time when Sydney’s Inner West local government area is forecast to grow by approximately 32,600 residents and 14,000 workers between 2022 to 2036, Soldier Tower Cranes & Labour Services is committed to the development of Inner West’s infrastructure.
Soldier recently joined forces with one of Australia’s most experienced, fully integrated property developers, Toga Group. Toga Group, which has 60 years of experience in the building industry, is leading the way in the Marrickville community with its new development, Wicks Place, a hub of premium apartments combining luxury living and eclectic retail space.
Soldier commenced working on this Project in 2022 taking note that this Project would involve an intricate tower crane and construction methodology. This Project is very complex due to its close proximity to the airport; the cranes provided are limited in height and can only be erected and dismantled between the hours of 11pm and 5am. The restrictions created a significant level of complexity for Soldier to overcome, who have installed, and recently dismantled two tower cranes for this Project.
Soldier executed a jib reduction from 35m down to 25m on TC1, preventing structural cycle time delays and enabling crane operation
to continue, given the restrictions faced on the project. With crew consisting of traffic control, crane crew, skilled labour, hoist operators and machine operators, Soldier is set to operate the hoists on site, from mid-January as their cranes will be removed for the final levels of construction.
Soldier is proud to be a part of Toga’s Marrickville development.
For more information contact Soldier Tower Cranes & Labour Services, phone 1300 SOLDIER, email admin@soldiertowercranes.com.au, website www.soldiertowercranes.com.au
More than just a sliding door, Darley’s new sliding doors tick all the boxes for compliance and high performance.
There are not many aluminium window and door fabricators, who have not used the CityView Apartment Sliding Door system over the years. This popular sliding door system has been used by countless builders and developers and installed in some of the most prominent commercial and residential projects in the country.
This year has seen some exciting changes to the Darley Aluminium product line with the upgrade of some of their existing products. Two of the most popular door systems, the CityView Apartment Door system, and the ClimateGuard Apartment Door system, have been given a new name to better match, and highlight, what these products represent.
Now known as the ClimateGuard Architectural Sliding Door system and the CityView Architectural Sliding Door system, these new and improved product lines will appeal to a much wider audience in both commercial and architectural applications.
These systems are widely used in highrise multi-residential dwellings, with
the ClimateGuard (thermally-broken) Architectural sliding door becoming increasingly popular in architectural, residential, and commercial projects.
Some of the main upgrades to these Architectural sliding door systems include the addition of new flush sills and flush drain sumps, the introduction of large stiles to suit a variety of mortice lock options, and the CityView Architectural sliding door achieving a BAL40 bushfire rating.
There has been a favourable response from Darley’s customers already using these systems, and they are pleased that the rebrand more accurately suits the product’s capabilities.
The recent Petersham RSL upgrade, saw the CityView Architectural sliding door installed in the Siding apartments by NSW fabricator: Style Windows & Doors Pty Ltd. NSW fabricator: Trio Designs installed the thermally-broken ClimateGuard Architectural sliding door into a newly renovated, modern residential home in Dover Heights NSW, with the owners of this coastal property reaping the benefits of increased energy efficiency and protection from harsh weather.
Darley Aluminium National Sales Manager, Ray Kwan said, “We identified that our CityView sliding door and ClimateGuard sliding door systems are being widely used across the full spectrum of residential, multi-residential, commercial, and architectural construction, and therefore felt that rebranding the systems to better reflect their use in the marketplace. As part of the rebrand, we've also introduced the flush sill and integrated flush sub-sills for flat threshold transitions, and also completed testing for the new systems including AS2047 for windows and external glazed doors in building and AS3959 for construction of buildings in bushfire-prone areas.”
Both the CityView and ClimateGuard Architectural Sliding Door systems now feature new flush door sills (SD408 and SD608).
Designed and engineered in Australia, these flush sills are aesthetically pleasing, practical, and self-draining. They are disability access compliant making them the perfect choice for the aged care sector. They are also pre-slotted, so there is no need for additional fabrication, and are tested to Australian standard AS2047.
Another feature added to both the CityView and ClimateGuard Architectural sliding door systems are the new flush drain sumps (TJ400 and TJ600). These unique one-piece sumps, which are also designed and engineered in Australia, come pre-slotted, so there is no additional drilling or notching required by the fabricators.
The new flush drain sumps are also suitable for all sliding and folding 100/101.6mm and 150/152.4mm operable systems and will suit any 25mm and 65mm stainless steel grate.
Earlier this year, the CityView Architectural sliding door system was tested to the updated and more stringent Australian standard AS1530.8.1-2018 to BAL40, which is the highest bushfire rating available in Australia before BAL-FZ (Flame zone).
Testing was conducted by NATA accredited testing organisation: Warrington Fire, in accordance with the requirements outlined
in the current 2018 version of the testing standard. To simulate more accurate fire conditions, Tasmanian Oak was used during testing instead of the traditional pine cribs, which results in higher burn temperatures.
The system exceeded testing requirements and was able to withstand temperatures of up to 40 kW/m2 without compromising the frame and glazing components. BAL40 is primarily concerned with the protection of buildings from ember attack and burning debris ignited by wind-borne embers and exposure to a high level of radiant heat.
Another exciting upgrade to the systems is the new stiles (SD148, SD162 & SD172) that can accommodate a variety of mortice lock options. As with the other new features, the new stiles can accommodate a wide range of hardware options and key functions, including residential and commercial mortice locks, pull handles, surfaced mounted options and flush pulls.
These systems not only integrate with current design trends but rate highly with regards to performance specifications. Both the CityView Architectural Sliding Door system and ClimateGuard Sliding door systems are versatile and can be incorporated into a variety of configurations by using the common Darley commercial framing systems.
They are also able to accept single or double glazing options, allowing for the flexibility to meet all budgets, whilst adhering to stringent energy efficiency requirements..
Scan the QR codes for more information
One of the most widely used cranes in Australia also falls into the category of highest risk. Articulated cranes are essential for a wide range of tasks in the construction industry. However, the current high-risk work license framework allows slewing crane license holders to operate articulated cranes without any formal training.
Without a specific Heavy Vehicle Licence requirement, many seasoned articulated crane operators have never been properly trained or assessed for driving this style of crane on-road. Over the years there have been a number of serious incidents involving articulated cranes resulting in multiple investigations and a coronial inquiry.
A recommendation was handed down from the coronial inquiry that a training course be developed to ensure drivers of these cranes have appropriate theoretical and practical knowledge. The Crane Industry Council of Australia (CICA) was approached and received a federal grant through a Heavy Vehicle Safety Initiative to develop this program.
For the theoretical component, CICA partnered with the global leader in adaptive learning, Area9 Lyceum, to develop an online training program. Developed with 25 years of cognitive research, Area9 Lyceum’s Rhapsode program is set to change the way the construction industry approaches health and safety.
Adaptive learning is an online delivery method that personalises the training package for each learner using proven data analytics and intelligent technologies to adjust in real-time. In essence, the program
will assess individual drivers’ knowledge and adapt the program to focus on gaps in their knowledge, and more importantly, the gaps they may not even realise they have.
The development of the On-Road Articulated Steering Mobile Crane Training Course was completed with industry trainers, equipment manufacturers, state WHS regulators, state and national road authorities, and operators with over 30 years of individual experience operating articulated steering cranes.
“This model provides excellent feedback on what the crane operator does and doesn’t know, which means the solution is tailored,” said CICA’s Chief Executive Officer, Brandon Hitch. “The course is not ‛one-size-fits-all’, so there is high levels of engagement from each learner. It’s like having a personal teacher sitting next to you and guiding you as you learn.”
“Working with the subject matter experts at CICA, our learning engineers developed the articulated crane module for use in the industry to build competency, reduce risk and improve safety for the drivers and operators of these cranes,” said Dr Khurram Jamil, President - Global Markets for Area9 Lyceum.
CICA is confident that the On-Road Articulated Steering Mobile Crane Training Course will improve performance and reduce injuries, lost time, severity and claim costs.
“The development of this standardised course will also assist small and medium businesses that would otherwise not have resources to create this training inhouse,” said Brandon. “We are exploring ways to use the adaptive learning framework for other training initiatives as well.”
Partners include Melbourne Water, John Holland, ARTC Inland Rail, MetroTunnel CYP, Australian Institute of Health and Safety, NSW Ambulance and globally, Citi Bank, Shell, BP, United Airlines and American College of Physicians.
CICA’s On-Road Articulated Steering Mobile Crane Training Course won the 2022 award for Outstanding Solution for Members managing WHS Risk in SafeWork NSW Work Health and Safety (WHS) Excellence Showcase.
For more information about CICA or the On-Road Articulated Steering Mobile Crane Training, www.cica.com.au
For more information about Area9 Lyceum and adaptive learning, www.area9lyceum.com
CICA believes the greatest outcome to date has been raising awareness of the lack of formal training for articulated crane drivers without crippling the industry.
Area9 Lyceum’s adaptive learning technology provides wideranging benefits across many industries. “We have seen significant results in those environments where gaps in knowledge have an impact such as construction, utilities, mining, power and health care,” said Khurram.
Scan the QR Code to learn more about the CICA On-Road Articulated Steering Mobile Crane Training Course
Developed with 25 years of cognitive research, Area9 Lyceum’s Rhapsode program is set to change the way the construction industry approaches health and safety.
erbas™ is a family owned business with a focus on forming positive working relationships with clients to deliver the highest quality outcomes with integrity.
building great relationships with the architectural and building teams through the various stages of completion.”
Originally the University of Technology Sydney Ku-ring Gai campus, the site has been transformed into a co-education facility with an elegant design that combines highly complex heritage, safety, bushfire and educational considerations.
The company specialises in building engineering, including mechanical, electrical and communications, security, AV, lighting, hydraulic, fire protection, sustainability, and lift systems. erbas™ has diverse experience across the residential, commercial, government, education, aged care and health sectors.
“We try to be mobile, nimble and adaptable,” said Executive Director & Partner, Michael Slatter. “We build relationships with people and take the time to do things well. This gives us the capacity and agility to go from small jobs to the biggest jobs.”
The NSW School Infrastructure Lindfield Learning Village Project is a shining example of the depth and breadth of their skill set. erbas™ has been involved in this project since its inception more than five years ago.
“erbas™ was engaged for end-to-end sustainability and all services and infrastructure, inclusive of services master planning,” said Michael. “We maintained a continuous design team throughout the staged project with our technical team enduring from beginning to end
“As designers, we have the unique opportunity to affect positive change in the world through the systems we engineer,” said Michael. To better service their clients, erbas™ SUSTAIN has been established as a subsiduary of erbas™, with the core function of instilling sustainability concepts and efficient design into engineering projects. “What better way to meet the needs of building users than to help better meet the needs of the planet simultaneously by reducing the impact those buildings make?”
Since its origins in Sydney in 1997, erbas™ has had continued growth and success in the New South Wales market extending the erbas™ brand and reputation into the Victorian market back in 2014 and they are enjoying the same success across the border.
For more information contact erbas, phone 02 9437 1022, email general@erbas.com.au, website www.erbas.com.au
better way to meet the needs of building users than to help better meet the needs of the planet...?
Australia's best air conditioner brand five years in a row
Australia's most satisfied customers four years in a row
Australia’s best rated split system air conditioner brand two years in a row
FOR MAJOR CONSTRUCTION PROJECTS
CONCRETE PROTECTION
SEALANTS & ADHESIVES
CAR PARK SOLUTIONS
BATHOOM PRODUCTS
PARTITION SYSTEMS
COVERS & GRATES
GREENSCAPES
SHADE SAILS
BENCH TOPS
FLOORING
PLUMBING DOORS
LIFTS
Cooling Brothers Glass Company has a national reputation for its glazing innovations, including decorative glazing, and producing solutions to withstand natural and artificial extremes, including solar, noise, security, ballistics, and cyclonic customised glass solutions.
The business works closely with architects, artists, building designers, and specifiers, and its landmark projects include the Mineral Resources’ headquarters, Brookfield Place, and Crown Resorts.
Moving into 2023, Cooling Brothers has released significant updates to the company’s core product ranges of Insulcool Double Glazing, Toughened Laminated Glass, and Imagink Digital Ceramic Printing.
A new Australian-owned steel coil supplier is snapping up customers across the fabrication industry with competitive prices, fast delivery and custom colour tinting to suit any brand.
Sovereign Steel, founded by two well-known building and procurement experts, is targeting small and emerging steel frame fabricators helping to meet the surging demand for steel frames. Sovereign Steel Co-founder and Operations Director Aaron Hinkley said the company’s ability to supply steel coil in any colour was creating a genuine alternative for fabricators and their customers in the light-gauge steel framing sector.
“Steel coils are not actually blue,” Mr Hinkley said. “In fact, they can be supplied in all colours so when new residential homes/ products are at the frame stage, builders can show off their own brand colour rather than giving a free plug to the product manufacturer.”
For more information scan the QR code or visit, coolingbros.com.au
“We have set out to offer a genuine alternative source of reliable, high-quality steel with the personal service and flexibility that comes from a nimbler, customer-focused business. From competitive prices to 30-day
credit terms, fast delivery times and small minimum order requirements, Sovereign Steel is determined to shake up this industry for everyone’s benefit.”
As steel procurement specialists, the Sovereign Steel team works with global mills to provide products tailored for each customer with quality assurance guaranteed. Every order is inspected in the country of origin prior to shipping with independent testing in Australia, full traceability and compliance documentation.
Australia’s leading digital contractor management platform, LinkSafe has recently partnered with Nirovision, an Australianowned and developed AI software company that provides a visitor management solution powered by facial recognition, eliminating the need to use any other external system to ensure workplaces are safer and more secure.
LinkSafe’s use of the Nirovision Doorkeeper Pro system will allow for seamless integration into LinkSafe’s existing contractor management platform. This provides clients from all industries the ability to streamline the processes of workplace access, safety, and security automation into a single platform, by turning an iPad into a touchless face check-in kiosk.
Nirovision’s home-grown AI technology empowers workplaces with the ability to identify vehicles and drivers, cross-check compliance, automatically open doors,
turnstiles and boom gates, log time and attendance, and alert site managers of any inconsistencies or anomalies.
LinkSafe CEO, David Erczmann said that the collaboration aims to expand LinkSafe’s capabilities to provide an even more robust contractor management experience with the help of advanced AI technology.
“Integrating Nirovision’s AI technology into our existing contractor management platform allows us to add a true contactless solution to our offering - this means, based on biometrics, it can ascertain compliance in the LinkSafe platform and further to that, then integrate with access control.”
“Adapting new tech and making sure we keep up to date with the changing technological landscape is important to us. Our alliance with Nirovision is a testament to that, and offers our clients some amazing features that
compliment our contractor management platform,” said David.
Nirovision CEO Jimmy Lee said the partnership with LinkSafe not only provides tremendous value to workplaces that have a need for compliance, but also saves workplaces money and time.
“Combining LinkSafe’s compliance expertise with Nirovision’s powerful AI vision is going to make it so much easier to ensure a safe and secure workplace - the future of this partnership is very exciting,” said Jimmy.
For more information scan the QR code or visit www.linksafe.com.au
From the inventors of the revolutionary linear drainage system, Stormtech, comes a new invention that is set to change bathroom design all over again. The culmination of Stormtech’s wealth of industry experience and after extensive collaboration with designers, builders, tilers, regulators and waterproofing consultants, the 120SCS Shower Screen Support drain represents the latest innovation in bathroom drainage. Stormtech’s 120SCS Shower Screen Support drain drastically simplifies bathroom design and installation. This all new product, which includes a Shower Screen Support Channel for any Stormtech grating style, is a versatile linear drainage system that provides dual function as a drain for both sides of the shower screen, and a support for the shower screen itself.
Made from 316 Stainless Steel, the 120SCS is designed for flexibility. Wall-to-wall installation allows a simple dual fall across the bathroom. As a result, a single floor waste can drain the entire bathroom, meaning designers are no longer required to detail the intricate geometries in which the bathroom floor will fall to a traditional centred floor waste. Additionally, as the simple dual fall sheds water more effectively, they are free to use larger format tiles to create the impression of space in smaller bathrooms.
With Stormtech’s groundbreaking 120SCS design, builders and tilers do not need to have complex falls or undertake intricate tile cutting as is required for most dual drain (shower and main bathroom) layouts. There is less tile wastage from having to re-cut tiles and breakage, plus a faster and simpler tiling process. Waterproofing is even easier too as the waterproofed substrate falls towards the location below where the Shower Screen Support Channel drain will be, and less water will find its way through grout joints due to effective watershedding.
Furthermore, as the drain is away from the entry door to the bathroom, any water thrown towards the door will run back to the drain, reducing the risk of bathroom flooding. Over recent years, Stormtech has improved the design of this solution, and, with bleeding-edge equipment and technology, the company has been able to leverage its unique capabilities to reduce the cost of manufacture and lead times significantly – a benefit they can pass on to their customers. Available in all Stormtech designer grates and finishes, the 20SCS Shower Screen Support drain exceeds all Australian Standards, is WaterMark certified and is exclusive to Stormtech.
For more information contact Stormtech, website www.stormtech.com.au
Atmosphy provide bespoke indoor garden installations that transform interiors into stunningly beautiful spaces. They grow, source, design, install and maintain unique indoor gardens to create greenscapes, areas of natural green foliage, for residential and commercial developments.
Owner and Horticultural expert Laura Henry designs her greenscape plantings to maximise the use of floor, wall and ceiling spaces, turning them into unique growing environments. The living systems of foliage process the surrounding air, reducing pollutants and improving air quality as well as creating a pleasant relaxing environment that reduces stress for office workers, improving mental health and productivity.
Originally established in Queensland, Laura spent the first two years in business focused on research and development. “With a team of five, I investigated the aesthetic characteristics of indoor plants along with learning about their needs including light and air movement as well as the feeding and watering requirements of different species. As a result, I am able to specify certain species that will thrive in different indoor environments as well as being suited to the desired look and budget,” said Laura.
“Our approach is both innovative and sustainable, we design and grow tailor made solutions, choosing plants that reflect the image or brand of our clients. Atmosphy is passionate about the greenscapes, we aim to provide a personalised healthy and thriving workspace and that’s what inspired us to develop GROWSTAR – our own vertical, fully irrigated garden greenwall system, customisable and scalable to any place.”
GROWSTAR is a cleverly designed greenwall system distinguished from other greenwalls by its individual plantings, with each plant in its own pot, secured to metal framework. This allows each plant to be fed, watered and bedded in soil that suits its unique requirements and the result is a beautiful greenwall, a vertical garden, comprising different varieties of healthy green foliage. These greenwalls create surprising architectural features and can be positioned to work as internal dividing walls and screens.
With over a decade of expertise Atmosphy work alongside architects, interior designers and individuals to provide living infrastructure. For new developments or existing spaces Atmosphy provides complimentary design consultations and concept plans as well as
specifically tailored after care programs for workplace or home as well as designs and plantings for garden restorations. Atmosphy’s greenscaping solutions can be purchased or leased on a long-term basis with an all-inclusive plant life guarantee maintenance package.
“Our maintenance work is especially important to keeping the greenspace healthy,” said Laura. “There are many aspects to indoor growing that are quite specialised, for example air conditioning can be very damaging reducing the required moisture level, the absence of birds and bees in indoor plantings can result in a build-up of pests, and closed-in spaces can encourage the growth of moulds and fungus. It really is quite important to have expertise in indoor growing to keep the plants looking their best.”
“There is growing evidence that nature and we are not two separate entities. A growing body of scientific research shows that the brain and even human behaviors are closely linked to the natural world. Our lifestyle today follows a pace dictated by increasingly advanced technologies designed without consideration for the biophilic fraction of the user, and our activities take place almost entirely inside buildings.”
“Fortunately, we have ascertained that direct contact with nature has important beneficial effects on human beings and specifically can make a valuable contribution to preventing and treating multiple pathologies. Sensory contact can help us fully utilise the regenerative potential of Nature for greater inner balance,” explained Laura.
Working across Victoria, Atmosphy maintains a warehouse nursery in Dingley Valley which allows them to offer competitive prices, a controlled supply chain and delivery of every project on time and to budget.
An especially successful job for Atmosphy can be seen at the Ballarat Government Hub. Working for the Kane Nicholson Joint Venture in 2021, Atmosphy designed and installed greenwall dividers to the interior of the building. The design and installation were critical in helping the building achieve its goal of a 5 Star Green Star rating.
For more information contact Atmosphy, 8, 1-5 Lake Drive, Dingley Village VIC 3173, phone 1300 425 600, email laura@atmosphy.com.au, website www.atmosphy.com.au
Established in 2010, AGD Systems designs, manufactures, distributes and installs products for traffic management systems in private developments. AGD Systems products are essential to the safe and efficient movement of traffic through car parks at residential apartment developments, childcare and aged care centres, commercial buildings, loading docks and warehouses.
“We are one of the few companies in New South Wales that provide a complete solution, from the design manufacturing and installation of this type of traffic system equipment. We receive traffic engineering reports and specifications, and we look at the swept path plans that show the movement and path of different vehicles in a specific area. We then design a suitable traffic control system. Our designs use the space efficiently with the installation of programmable logic controllers, traffic lights, ultrasonic vehicle detectors, boom gates
and mirrors and are used for DA submissions, we are very particular about safety in our designs and specialise in a detailed, safety-focused design and installation” said Office Manager, Lisa Phillips.
“One of the main applications we receive are residential apartments where the car park is narrow, allowing only one vehicle to maneuverer throughout the car park at any one time. We design the system so we can give each vehicle priority to enter and exit the car park safely, reducing the risk of any accidents occurring” Continued Lisa.
Sydney based, AGD Systems have installed their superior traffic management systems across developments along the east coast of Australia as well as supplying these systems to interstate contractors. They employ six staff with permanent teams of subcontractors ready for quality installations.
mageba is a team of specialists who design, manufacture, supply and install high-end structural bearings, expansion joints, vibration damping and seismic protection systems.
“The key aspect of mageba is that we are a company run by engineers, working for engineers. One of the most common problems experienced by engineers in the Australian and New Zealand market is the disconnect between original design models and the structural bearings and expansion joints available,” said Virendra Ghodke.
“We understand these issues and work collaboratively to design custom made bearings and expansion joints for significant infrastructure, commercial and industrial projects,”
“All our products are custom made,” added Virendra. “Unlike our competitors who resell standard product, we design and manufacture product uniquely suited to individual engineering requirements. For every job our products are heavily engineered for structural efficiency and cost effectiveness.”
mageba are dedicated to innovation and focus on making their products ‘smart’ by including monitoring systems to gage performance and
provide feedback about the structural health and operating efficiency of their products.
Established in Switzerland in 1963, mageba started as a family run company and quickly expanded to become a global presence with subsidiaries in over 50 countries including Africa, Europe, the Americas and the Middle East. More recently mageba has established offices and manufacturing facilities in the Asia Pacific with their largest factory of 15,000m² in Shanghai and a 2,000m² facility in Sydney.
For more information contact mageba Australia, 8/42 Peter Brock Drive, Eastern Creek NSW 2766, phone 1300 624 322, email info.au@mageba-group.com, website mageba-group.com
TORMAX is Australia’s leader in the manufacturer and installer of high-quality automatic doors for commercial developments. Operating since 1982 with inhouse designers, technical advisers and service technicians TORMAX automatic door systems are stylish and functional and are designed to meet the requirements of modern environments.
TORMAX supply and fit standard automatic sliding and revolving doors for commercial applications as well as stunning custom-made pieces. The TORMAX range includes fire and smoke doors, burglar resistant doors, water-tight and sound-proof doors. They also design and fabricate hermetic sealing doors for use in laboratories and operating theatres as well as for clean-rooms and for pharmaceutical production. TORMAX also cater to unusual and harsh environments with doors that are corrosion resistant and offer insulation or protection against radioactive radiation.
“All our doors and hardware are made from high quality Swiss materials. We send specifications to Switzerland for the exceptional European engineering and manufacturing carried out by our parent company the Landert Group,” explained Sales Manager, Aaron Cannata.
Automatically opening doors eliminate the risk of transmitting bacteria and viruses with motion detectors or switches that responds to hand gestures, an elbow button or foot rocker. TORMAX also offer regulating automatic doors that can be controlled to ensure physical distancing, operated from a smartphone.
TORMAX is Melbourne based with offices and distributors across the country, their automatic doors can be found in shopping centres, Bunnings and Woolworths developments, hotels, restaurants and across the food industry as well as in airports, train stations and ships.
In 2022 TORMAX completed the installation of contemporary automatic doors for the Darebin Cultural Centre at Preston City Hall.
“We were contracted for the full design, manufacture and install package,” said Aaron. “We fit a steel and aluminium frame, an elegant feature sliding door with a shallow curve as well as a number of frameless glass-sliding doors and automatic swing doors.”
For more information contact Tormax Australia, 13 Lillee Crescent, Tullamarine VIC 3043, phone 1800 608 000, email info@tormax. com.au, website www.tormax.com.au
The Patent Pending TBA Firefly™ Intubatt® Concrete Protection System enables structural engineers to design fire resistant concrete structures with 40% reduction in concrete and maintain structural adequacy under fire due to its superior insulation at high temperatures.
The Fire Resistance Level (FRL), or Fire Resistance Period (FRP) for concrete is defined by three criteria when subject to a standard fire endurance test.
• Structural Adequacy – the duration that the element will resist collapse
• Integrity – the duration that the element will prevent the passage of fire from one side to the other
• Insulation – the resistance to heat transfer from the fire exposed side of the element to the unexposed side.
This innovative and lightweight system has been recently tested to AS1530.4 (2014), using a 120mm thick concrete slab protected with the 50mm lining of TBA Firefly Inubatt, and subjected to four hours of the AS1530.4 (2014) fire endurance curve – which reaches 1,133°C at 240 minutes. At the same time, the slab was point loaded with 2400kg
and the deflection and temperatures measured at critical locations. The test data demonstrates that 50mm TBA Firefly Intubatt installed on the underside only of floors, or both sides of walls can:
• Upgrade 100mm concrete steel reinforced elements to provide 240/240/240.
• Provides the equivalent insulation as 145mm of concrete for four hours FRP.
Benefits for Building designers:
• Potential Retrofit for ‛change of use’. For example, where occupancy type for a building is changed requiring a greater FRL of floors and wall.
• Lighter structures for new build – 40% reduction in concrete mass to achieve equivalent fire resistance incorporating TBA Firefly Intubatt protection.
• Thinner floors, saving up to 100mm per floor where an unprotected 250mm floor slab is required.
For more information contact TBA Firefly, 44 Gindurra Road, Somersby NSW 2250, phone 02 8004 3333, email sales@tbafirefly. com.au, website www.tba-pt.com.au
United Lift Services is Australia’s largest independently owned vertical transportation company. They work closely with a wide range of clients to supply and install elevators and escalators, with a focus on premium service packages to ensure their clients vertical transport assets remain in tip top condition with years of safe and reliable operation.
Established in 1998, United Lift Services operate from their head office in Melbourne with branches in Sydney, Brisbane, Adelaide, and strategic partners all over Australia. With over 200 employees – they serve the commercial, industrial and government sectors across the country.
For new installations, United Lift Services inhouse design team offer non-proprietary packages to suit unique site-specific requirements. They are a local company with an impressive portfolio of work including national contracts with Telstra and Aldi as well as continuing work with Metro Trains, Department of Health and Human Services, and multiple tier one builders.
“United Lift Services are Australia’s leading third-party elevator provider,” says Construction Manager, Josh Dales. “This means our broad supply chain enables us to deliver quality products that are built for sustainability and longevity. We pride ourselves on working
proactively with the project team to deliver innovative solutions tailored to our client’s needs.
“A recent successful project for United Lift Services was the installation of two large goods lifts and 2 passenger lifts for Next DC Data Centre through Kapitol Builders,” continued Josh. “The short build cycle meant we had to come up with creative methodologies to ensure we met the project critical path requirements in a safe and timely manner”.
At Melbourne Airport, United Lift Services completed the installation of a 4-tonne goods lift, an escalator and a passenger lift with stunning custom fit out including black stainless steel, mirrors, and speciality cladding.
United Lift Services also offer modernisations of existing vertical transport systems and provide fully tailored upgrade packages, life cycle reports and performance analysis. Upgrades to elevators improve performance and safety with the inclusion of OH&S controls and facelifts for interiors and appointments.
For more information contact United Lift Services, phone 1300 161 740, email john@unitedlifts.com.au, website www.unitedlifts.com.au
Monooga Products is a solid surface fabricator, producing high quality solid surfaces for bathroom vanities and kitchen benchtops and all surfaces for wet areas.
“We fabricate and install stylish contemporary bathroom vanities, kitchen benchtops and surfaces for high quality residences, including laundry and alfresco situations,” explained Owner, David Page.
“We also supply and install all types of commercial benchtops, reception desks, shelving and break-out areas for kitchens. We supply for commercial fitouts with Corian being our most popular product.”
Solid Surfaces for moulded tops and vanity units provide seamless joins, hygienic and stain resistant. It is renewable with repairs made without the cost of removing the whole benchtop.
Australian owned and operated since 1965, Manooga Products is a family owned company run by David and brother Michael. Manooga Products have invested in quality machinery and first class raw materials at their West Ryde factory and have a showroom with samples and advisors to show a range of solid surface products.
“We are distinguished in our manufacturing by our can-do attitude, our ability to manufacture state-of-the-art product for high end developments. All our product is custom made, specially for each home or project.”
“We have inhouse design and also work to specifications to create a cost-effective and buildable product. We have knowledge and experience of our product and craftsmen on board for hand finishing and our research and development team has led to the production of some new and elegant bowl shapes for vanity units,” said David.
Manooga Products supply across the Sydney CBD and metropolitan areas, Newcastle, Canberra and the south coast of New South Wales.
Recently Manooga Products completed the fabrication of 40 units for the bathrooms and kitchens at the highrise residential development Loftus Lane at Circular Quay. They also provided 630 vanities for the apartments Natura at Macquarie Park.
For more information contact Manooga Products, 13 Rhodes Street, West Ryde NSW 2144, phone 02 9807 3511, website www.manooga.com.au
Australia’s only manufacturer of commercial vinyl flooring, Armstrong Flooring, is set for rapid expansion with new owners, investment, and interest in the Australian manufacturing business. Originally commencing operations in Australia as Armstrong Nylex in the 60’s as part of a multinational company, and a brand that has been built over many generations, Armstrong Flooring is now entirely Australian owned and will continue to operate and expand into new markets as Armstrong Flooring. Armstrong Flooring take pride in producing durable high-performance flooring products for projects in Healthcare, Education, Retail, and Hospitality.
The new owners are known for their extensive experience in the manufacturing and distribution of residential and commercial flooring products and are further developing the business with the acquisition of new plant equipment and expansion of the product ranges.
Whilst being a local manufacturer of trusted high performing product ranges that meet functional needs over many decades, the recently launched Natralis homogeneous sheet vinyl range is a good example of continued investment in new ranges that perform and inspire.
Inspired by our very own local history, iconic locations and the flora and fauna of Australia, each of the 20 colourways in the Natralis range has its own story about its source of inspiration. The collection captures our connection to country through colour in an authentic and playful way –play with colour, connect with place.
A leader in responsible manufacturing and environmental practices for more than 50 years, Armstrong Flooring have been a supplier to the construction industry producing durable, high-performance products. Our Braeside, Victoria manufacturing facility, sales and administration teams employ over 100 people across the country that include members from 25 different nationalities and family members across multiple generations.
Armstrong uses resources wisely, have achieved national recognition for environmental practices, and have numerous accreditations including Best Practise PVC, ISO 9001 & 14001.
After 53 years of local manufacturing, Armstrong Flooring continue to be the only manufacturer of resilient flooring in Australia. We are excited to be continuing to serve the Australian market, our local community and economy as an Australian owned business.
Backed by 85 years of expertise for quality you can trust, Laminex Waterloo has a range of different systems and products to suit every project.
The Laminex Waterloo Partitioning Systems range is assembled locally in Australia using only Global GreenTag certified Laminex substrates and includes Shower and Toilet Partitions, Locker Systems, Vanities, Seating, Privacy Panels and Wall Panels.
“The systems can be customised for applications ranging from offices, retail spaces, health care facilities, educational facilities, sports and recreation venues and everywhere in between,” said Laminex Category Manager, Josh Woods.
Laminex Waterloo Partitioning Systems are delivered cut-to-size and pre-drilled as ‘flat packs,’ complete with instructions, fixings, and tools. In addition, the substrates can be cut on site if required.
“The range is available in a broad array of colours, substrates, and hardware, while providing all of the security, comfort and aesthetic appeal that is required in effective contemporary design,” said Josh.
Laminex Waterloo Partitioning Systems is available in Laminex Multipurpose Compact Laminate, a thick, versatile, extremely scratch, moisture and impact resistant laminate panel. The Laminex Compact Laminate range includes Protec+ anti-microbial surface technology, that inhibits the growth of bacteria and fungus. This technology helps to create a safer, cleaner environment anywhere.
Backed with superior warranties and guarantees on substrates and hardware, Laminex Waterloo Partitioning Systems is ideal for completing your next project.
“Laminex is dedicated to keeping manufacturing local, investing in industry skills growth as well as supporting communities and our industry,” said Josh. “Through innovation and a strong belief in Australian Made, Laminex continues to invest in new technology to produce locally made products with a focus on sustainable business practices.
For more information contact Laminex, phone 132 136, website www.laminex.com.au
that stand the test of time.
Duroclass vanity tops will look beautiful now and in years to come. Made in Australia and made to last. Just like a diamond –beautiful, forever.
Want to know more? Get in touch!
duroclass.com.au
EJ are the leaders in the design, manufacture and supply of access covers for utilities and infrastructure projects. With safety and ergonomic design as a priority EJ produce easy to use and hard-wearing access covers to water and sewage services, electrical, gas and telecommunications infrastructure.
Founded in 1883, EJ built its first manufacturing facility in East Jordan, Michigan USA. With such a history EJ has accumulated years of experience growing their expertise alongside growing industries and infrastructure projects. Today EJ is a global enterprise promoting innovative design and manufacturing high quality product.
The designers at EJ are skilled at optimising every detail of the final product, ensuring the efficient use of materials, cost effectiveness and compliance with national guidelines.
In 2022 EJ won the North Harbour Business Park Award for Advanced Manufacturing Excellence at the Moreton Bay Region Industry and Tourism (MBRIT) Awards, an acknowledgment of EJ’s high standards of design and manufacture. “For the construction of today’s high tech airport and port facilities, contractors depend on EJ as the leader in the design, manufacture, and distribution of the
most innovative infrastructure access solutions. EJ has a proven track record for delivering the highest product reliability and mechanical efficiency available,” said Sales Director, Ian Maddocks.
EJ has offices in the Americas and Europe. In Australia they operate from Brisbane, Sydney, Melbourne and Perth to serve projects across the country.
Recently EJ was contracted to supply an access cover package for the berth four terminal upgrade at the Port of Townsville, northern Australia’s largest container and automotive port.
Queensland Sales Manager for EJ, Marty De-Wit, offered contractor Civilplus an alternative design with a superior access product that didn’t need machinery to remove the covers, nor did it require ongoing servicing and maintenance and is designed with the safety of port workers in mind.
For more information contact EJ, 2/354 South Pine Road, Brendale QLD 4500, phone 07 3216 5000, email au.info@ejco.com, website www.ejco.com
SUSTAINABLE
• Bamboo-composite boards constructed from renewable resources
• Stripping heads are cast with recycled steel
• Reduction in onsite waste, removal, transport and disposal costs
SAFE
• Stable system with locking restrictions in six directions. Unique wind-lock design.
• System can be erected from the ground eliminating working at heights risks
INNOVATIVE
• Minimal components: Panel prop and infill beam
• Beam and soffit can be formed from the same prop
EFFICIENT
• Only four people required for setup, stripping and removal with each achieving up to 100m² setup per person, per day
Engineered In Australia
The compact ‘Ringer AL2000’ formwork system from RINGER, offers Australian construction sites a low weight and high resilience formwork solution.
Ringer AL2000
• Hand-set
• 60 kN/m² fresh concrete pressure
• Panels sizes from 250mm-3000mm
• Closed hollow chamber profile made of aluminium
• Easy to clean
• Simple handling thanks to additional handle tubes
• Available with Phenolic, ply, plastic coated ply, or Alkus panel
The system can be configured for a range of applications including; shaft formwork; basement construction; foundations, beams and parapets; round walls and columns; and Hall walls.
Family owned Sydney Shade Sails are ISO accredited for quality. The company’s range of shade sails and canopies are custom made in their factory at Peakhurst, New South Wales, with their newest product, Camo net shade sails, manufactured in Vietnam.
“The Camo Net Shades are a high quality system that not only looks great but provides long lasting sun protection and can be installed over pergola frames, used as privacy nets and more,” said General Manager, Serena Collins.
“They provide dappled shade, the netting broad leaf design moves in the breeze, creating a uniquely decorated space,” said Serena.
Manufactured from heavy, durable, perforated Ripstop, Camo net shade sail sides are cut with an inward curve and are fixed to a stainlesssteel cable meaning the shade sail camo net doesn’t sag when installed and tensioned. With low wind resistance, heat can rise through the nets which provide dappled, 70-80% shade.
“Shade Sails create a cool aesthetic outdoor environment with commercial grade shade cloth, steel posts and anchor points,” said Serena.
“Designed to be strong and durable, they have double layered corner patches, seat belt webbing reinforcement and double stitching. Combined with stainless steel cable and hardware, the result is a premium quality product.”
Sydney Shade Sails have a range of products to suit the diverse needs of sites, including Span Shade Structures, which are a cost-effective shade solution to larger areas.
Shadex shade structures are another great investment for an outdoor all weather shade solution. An architectural PVC membrane and precast connector are used to fix arched tubular rafters to tubular bearers which Serena says, “eliminates the costs of welding and galvanising.”
“Our structures are site specifically engineered to withstand the wind pressures of the site they are to be installed at. Cloth canopies are cooler than metal and polycarbonate rooves,” Serena said.
For more information contact Sydney Shade Sails, 23-25 Norman Street Peakhurst NSW 2212, phone 02 9592 0401, email enquiries@shadesailsydney.net.au, website www.shadesalsydney.net.au
Hume Commercial Doors & Frames, a division of Hume Doors & Timber, are experts within the door manufacturing sector. Their passion for innovation drives them to continually reinvent and create new products to meet their customer needs, such as their newest commercial product, architecturally designed Elite Aluminium Doors, the result of a transformative step within the industry.
What is unique about the Elite Aluminium Doors?
Traditional timber entrance doors require overhead protection to shield them from damage caused by exposure to weather. Whereas the Elite Aluminium doors are highly durable and effective in exposed weather situations – the perfect solution for entrances that have little to no protection from the elements.
Unlike other aluminium doors, the Elite range can be hung in a timber frame, which means they can be retrofitted to an existing opening. They can also be supplied with the Weatherguard timber entrance frame to provide a complete weather protection solution.
These low-maintenance doors have a powder coat finish and are ready to install.
What type of environment would these particular doors be perfect for?
The Elite doors are the perfect entrance doors for any residential housing, but are particularly suited for home designs where the entrance has limited overhead protection. These doors can also be made to size, to suit a variety of client’s needs.
What can customers and clients expect from Hume Commercial?
We have a dedicated and experienced team, as well as innovative manufacturing solutions, which means that you will always receive excellent customer service and precision products that are manufactured to specifications, every time.
Hume Commercial Doors & Frames offers a National, State and Local network, as well as dedicated estimating services, onsite solutions and consultation services for builders. Their highly skilled team can help with design recommendations and offer CAD expertise.
Integrity Testing is proud to provide an exciting method of non-destruction testing using the Mod-shock® System. 30 years in development and extensive successful field use, Mod-shock® is a revolutionary, non-destructive way of testing wood, concrete and steel poles, columns or piles, for a range of structures including bridges, buildings and civil infrastructure.
“In simple terms, the Modified Shock Test (MOD-SHOCK) is a refined seismic test using a hammer blow as the force and a transducer to pick up the resultant vibrations,” said Director and Civil Engineer –NDT Specialist, Rikki Tongue. “The system then determines the load carrying capacity and integrity of in-service bridge supports.”
The Mod-shock® testing methodology is an in-situ test which directly measures the structures (buildings/bridges) existing support (pile, pier, column) capacities to determine what additional loads can be applied safely. The Mod-shock® system can set up to deal with a range of situations depending on the project needs, interfacing with integrity poles, integrity piles or integrity rock bolts.
“Studies have demonstrated that Mod-shock® identifies the defective piles, poles or columns and it directs the client to where the element is
defective,” said Rikki. “It can also give geotechnical data on the soils surrounding the pile or foundations and the bearing capacity of the soils to support the foundations.”
This technology is particularly useful when looking at heritage buildings, as the Mod-Shock® method is able to determine avenues of refurbishment, conservation or upgrade to suit any aesthetic and durability concerns, by verifying the structure’s supporting load capacity, and what additional loads can be safely applied onto exisiting supports.
Integrity Testing are leaders in non-destructive testing and specialise in helping their clients find innovative, cost-effective strategies for the repair and maintenance of their built infrastructure assets. By combining their extensive experience as engineers and material specialists with the latest advances in testing and digital technology, Integrity Testing provides the answers you need to manage your infrastructure.
For more information contact Integrity Testing, phone 1300 000 332, website www.modshock-equipment.com
ARCHITECT : John Wardle Architects
PROJECT VALUE : $152 million
TYPE : Civic
The Bendigo Law Courts is a state-of-the-art civic building housing the latest the latest technology to transform the delivery of justice.
The $152 million landmark building was constructed by Kane Constructions and joint venture partner Nicholson Construction (KNJV), and incorporates design features from Bendigo's Traditional Owners the Dja Dja Wurrung.
Part of a renewing of Bendigo’s civic infrastructure the completely new rebuild and expansion of the law courts, delivers the latest technology and infrastructure to the community to enable remote hearings, display evidence digitally, video conferencing, and live streaming.
Kane Nicholson was awarded the main works contract in April 2021 following a competitive tendering process, and the partnership brings together national large scale construction knowledge and local construction expertise.
The building acts as a central point, bringing together of a number of community elements, with strong influence from Bendigo's Traditional Owners, the Dja Dja Wurrung, informing the whole approach to the building in a culturally sensitive and intuitive manner.
“The standing seam copper façade is a standout,” said Project Manager, Jack Fowler. “A major highlight of the project is the completion of the pic-perforated copper screen which displays ‘Bunjil’.”
Bunjil in his Eagle form, is Djaara’s ancestral creator being and knowledge keeper. The prominence of Bunjil on the façade reflects his place on Dja Dja Wurrung Country and Lore, symbolising an important system of governance, and is a statement of living culture.
The project has had more than its fair share of challenges including building during
COVID and the associated procurement and supply chain stresses.
“As a major project in regional Victoria we had the added complication of trade selection in terms of local versus out of towners,” said Jack.
“This was the backdrop to managing a quick build over 18 months with a multitude of stakeholders from the local indigenous community and artists, Heritage Victoria, Victoria Police, Corrections Victoria, VCAT and court jurisdictions to name a few.”
The project team were able to exceed expectations during construction with the project on track to achieve a 6 Star Green Star rating.
Kane Nicholson is extremely thankful for the successful and strong working relationship formed with our clients Court Services Victoria and Turner and Townsend, and the consultant team consisting of John Wardle Architects, WSP, Introba, Aspect Studios and PLP Building Surveyors.
Kane Constructions is a multi-award winning, privately owned commercial construction company active in all sectors of the industry. They have extensive experience in building quality contemporary buildings, including in regional areas such as Ararat, Geelong and Ballarat.
Kane Constructions operate throughout the east coast of Australia from offices in Melbourne, Sydney, Brisbane, Sunshine Coast and Canberra.
For more information contact Kane Constructions, Level 9, 510 Church Street, Cremorne VIC 3121, phone 03 8420 1200, email viccontact@kane.com.au, website www.kane.com.au
Since 2012, Eascom Electrical has been offering fast and reliable service in all areas of the electrical trade industry, including maintenance and service, new construction, commercial, industrial and domestic electrical installations.
Eascom Electrical has a fully integrated industrial department, with inhouse control board design and construction, as well as a plethora of experience across all areas of industrial including water, factory, control and PLC.
Dedicated to delivering high quality services, within time and budget constraints, Eascom Electrical have worked with a range of organisations, institutions and companies within Bendigo and the surrounding areas.
Given their renowned reputation within the Bendigo area, Eascom Electrical were recently involved on the Bendigo Law Courts project, a landmark civic building that will set a new standard for the delivery of justice to the Bendigo community and the wider Loddon Mallee region.
Responsible for the delivery and installation of all of the electrical communication requirements throughout the court, including switchboards and the lighting within the building, Eascom Electrical provided their extensive experience in lighting, power and communications design across the project.
Furthermore, the dedicated team ensured they provided high finish details to all of the interior and exterior electrical services. Having worked with Kane before on previous projects, their strong client relationship and open communication meant they were able to carry out their responsibilities in a timely manner and adhere to tight project deadlines.
In addition, given the teams wealth of experience in regards to working on commercial projects, Eascom Electrical are also working on the Bendigo Gov Hub and the Puckapunyal Wellness Centre, to name a few. With a guaranteed two hour response time and a 24 hour, seven days a week service, Eascom Electrical are the industry leaders when it comes to the provision of commercial and industrial electrical service needs.
For more information contact Eascom Electrical, 1/17 Deborah Street, Golden Square VIC 3555, phone 03 5442 8979, email bendigo@eascomelectrical.com.au, website www.eascomelectrical.com.au
Specialising in the expert advice, design and installation of metal façades and roofs, Architectural Roofing and Wall Cladding Pty Ltd (ARC), is Australia’s most experienced roofing and wall cladding installation company. Collaborating with architects, owners, builders and engineers, ARC have delivered complex façades, cladding and roofing to a range of projects throughout Australia and the Pacific.
Given their renowned reputation, ARC was approached to participate on the Bendigo Law Court development, the first of its kind in Victoria to feature a full suite of specialist court rooms at one location and incorporate design features from Bendigo’s Traditional Owners the Dja Dja Wurrung.
Responsible for the development of the roof and façade was Juerg Wilk, founder and National Design and Construction Manager. Juerg and his team took on the design, engineering, supply and installation of this project, introducing a highly sophisticated European standard in relation to insulation, non-combustibility, manufacturing and installation techniques. “We are particularly proud to have achieved the highest level of appearance on the standing seam façade which was only possible by using special folding and installation techniques on every single sheet” Juerg said.
“Despite a minimum gauge of material and metal façades being prone to oil canning, ARC managed to deliver a perfectly flat surface over several thousand square meters. The detailing of penetrations, cappings, soffits and shrouds is second to none. It was an absolute pleasure to be able to work on this project using our sophisticated tech and methodology,” he said.
Offering an array of façade solutions, from basic onsite installations to fully prefabricated and modularised façades and roofs, ARC’s combination of European traditions and state-of-the-art technology, as well as their highly experienced team, means outstanding results are delivered every time.
Working on a range of projects across Australia including the Australian War Memorial (Canberra), Sirius Apartments (Sydney) and James Cook University (Townsville), ARC continues to set new benchmarks in Australia for metal façades that showcase the company’s exemplary inhouse design, technical expertise, manufacturing and installation capabilities.
For more information contact ARC, phone 02 9482 4461, email info@ arcroofing.com.au, website www.arcroofing.com.au
It doesn’t matter whether there is rain, blistering sun or a pandemic – more than 150 staff at GAME Traffic & Contracting are committed to keeping you and your workers safe across Central and North East Victoria.
The big green diamond on GAME utes, trucks, equipment and temporary fences is a common sight on major projects across regional Victoria and southern New South Wales, resulting in GAME establishing depots in Bendigo, Echuca, Shepparton, Wangartta and Wodonga.
“Our staff were amazing over the past 2.5 years with the pandemic and now more recently the floods across regional Victoria. They have traveled far and wide to provide our services as the calls came in to assist emergency services,” GAME CEO, Josh Hudson said.
“One of the things that really motivates our team each day is the commitment we have to the community. Most people have seen a GAME ute or temp fencing on a building site or roadworks around Bendigo, but not as many know about the programs we support for youth in the region. GAME is a social enterprise, which means our surplus is spent on programs to help others in our community.
“We work hard to be the leading traffic, grounds maintenance and equipment hire company in regional Victoria and instead of distributing profits to share holders, we have extra motivation to succeed, because our work is providing new opportunities for the next generation.”
“This year more than 1,300 youth across regional Victoria are registered in our Geared4Careers program to help them find work or pathways to further study – including more than 400 youth in Bendigo.”
“Even through these challenging times, we continue to thrive because our staff know that they are responsible for keeping people on their work sites safe, and we are all contributing to changing the future of local youth for the better.
“Customers typically choose GAME simply because of the quality of our service, our capacity and our reliability, but when they hear about the programs for young people that are financed by GAME, they are really proud to be our partners in supporting the community.”
For more information contact GAME Traffic & Contracting, 53 Powells Avenue, Bendigo VIC 3550, phone 03 5441 4250 email mallen@game.org.au, website www.game org.au
Engaged for full acoustic design services on the building, including sound insulation, room acoustics and mechanical services, they needed to adhere to stringent acoustic specification requirements to allow for appropriate levels of speech clarity and privacy in the various spaces.
Given the ambitious design, that required a great deal of coordination between the team from MDA, architects and builders, a number of sound related challenges needed to be overcome throughout the various design and construction phases.
Some of these included having to meet low internal noise targets from mechanical services, as well as challenging junction details for sensitive spaces adjacent to noise generating spaces. There were also a range of difficulties associated with providing sound insulation through visual elements like doors and windows.
Innovative acoustic solutions, developed by harnessing MDA’s wealth of experience and inhouse acoustic tools, were developed to overcome these challenges and achieve an outcome in keeping with such a landmark project.
With a breadth of knowledge and experience to consistently deliver quality solutions for projects, both in Australia and internationally, no matter how large or small, their strength in acoustic design comes from the diversity of their team members, who all share a passion and commitment to deliver technical excellence, across every area of acoustics and vibration.
For more information contact Marshall Day Acoustics, 10/50 Gipps Street, Collingwood VIC 3066, phone 03 9416 1855, email melbourne@marshallday.com, website www.marshallday.com
Main image : Bunjil in his Eagle form, is Djaara’s ancestral creator being and knowledge keeper. The prominence of Bunjil on the façade reflects his place on Dja Dja Wurrung Country and Lore, symbolising an important system of governance, and is a statement of living culture.
With a combined 50 years of expertise in residential and commercial tiling, Victoria City Tiling and Icon Tiling provide professional waterproofing, screeding and tiling to a range of commercial and residential projects across Victoria.
These 2 highly regarded companies joined forces and their wealth of knowledge and experience of the tiling industry to recently complete the prolific Bendigo Law Courts project.
This law court will transform the delivery of justice in Bendigo and Loddon Mallee. The culture and knowledge of the Dja Dja Wurrung (Traditional Owners) is reflected in the court and its surrounds, making it a statement of reconciliation and signalling a new era.
Throughout their involvement on this project, Victoria City Tiling and Icon Tiling were responsible for all of the tiling and paving of the building, including both the interior and exterior areas.
Project Managers, Dawoud Nazari and Brett Lehmann, said like every project of this magnitude there are challenges and obstacles such as working around other trades and logistics but they were easily overcome.
“Given our broad range of experience and the fact we have worked on a number of large commercial projects, our engagement on the Bendigo Law Courts project ran smoothly and we were able to complete our services in adherence to the tight turnaround times,” Dawoud said. “In addition, we maintained an excellent working relationship with Kane Nicholson and as result, communication about our role and what needed to be done remained open and fully operational at all times.”
With their can-do attitude, the Icon Tiling and VCT teams pride themselves on exceeding customer satisfaction on every job, as well as offering their high quality products, workmanship and services, regardless of the size of the project.
Icon Tiling is an Australian, family owned and operated business, with over 30 years industry experience. The company has expanded considerably over the last three decades, with projects all over Victoria, and has focused their attentions primarily in the commercial sector. Some current/recent projects for Icon Tiling include, Middleton Prison, multiple Victoria School Buildings (VSBA), Mt Gambier Aquatic centre, Sandringham College and Mornington Sports Pavilion.
With an already established extensive project profile, Victoria City Tiling are also currently providing their tiling, screeding and waterproofing services to the Rydges Hotel, 357 Collins Street, the Bendigo Gov Hub and 637 Flinders Street, demonstrating their dedication and commitment to customer service and satisfaction.
For more information contact Victoria City Tiling, 21 Central Avenue, Sunshine VIC 3020, phone 03 8590 1432, email info@vctiling.com.au
For more information contact Icon Tiling, 2/20 Colemans Road, Carrum Downs VIC 3196, phone 03 9770 8957, email admin@ icontiling.com.au
CLIENT : University of Melbourne
MAIN CONSTRUCTION COMPANY : Kane Constructions
CONSTRUCTION VALUE : $168 million
TYPE : Education
The University of Melbourne Student Precinct is a world-class student hub with both new and refurbished buildings that includes a new Arts & Cultural Building, ERC Library, Student Pavilion, building refurbishments and more.
In December 2019, Kane Constructions was awarded the Design & Construct contract to deliver the University of Melbourne Student Precinct. The precinct includes six buildings and will deliver 37,050m2 of new or refurbished internal and external buildings and landscape space.
The scope of work included a new Arts and Cultural Building which includes a state-of-the-art theatre, the refurbishment of the ERC Library, Building 168, Building 189, and the 1888 Building. Kane Constructions also completed landscaping for Amphitheatre North, and the refurbishment of Amphitheatre South, which when complete will deliver a world-class student hub.
The project makes a significant contribution to the transformation of the on campus student experience at Parkville by co-locating student services and activities closer to the new heart of the campus, and to primary transport links.
“This has been an amazing project,” said Kane Constructions Project Manager, Jason Malmur. “The buildings are all unique within the precinct and together they really stand out, which is something the University of Melbourne was keen to see come to life.”
“Kane’s brief was the design and construct of the entire precinct which meant there was not a single set of consultants but rather a different set of architects and trades for each building,” explained Jason.
“We were dealing with the mix of refurbishments and new buildings, the varying stages of demo, in ground contamination of the soil, the heritage aspects of buildings – including internal aspects, as well as the façades – not to mention the heritage listed trees.”
The site itself is complex and constrained, and traffic across the precinct is complicated by a 6m level drop north to south.
Kane was responsible for managing the multitude of consultants, trades and subcontractors across one timeline. As project managers they also had to ensure consistency in terms of the university requirements in all the builds, despite their differences.
“The whole team really came together to navigate through this process. The Kane family, including the delivery teams in each building, maintained such a high level of motivation and drive from 2020 when we commenced onsite, throughout COVID and right through to the completion of each building,” said Jason. “It’s fantastic that each building in the precinct has been really well received by both the University and the students.”
Kane Constructions is a multi-award winning, privately owned commercial construction company active in all sectors of the industry. Kane Constructions commenced operations in Melbourne in 1973, and the company operates throughout the east coast of Australia from offices in Melbourne, Sydney, Brisbane, Sunshine Coast and Canberra.
Kane Constructions was awarded the 2016 and 2019 National Construction Master Builder of the Year by Master Builders Australia
and the Master Builder of the Year in Victoria for 2016, 2017, and 2019 by the Master Builders Association of Victoria.
For more information contact Kane Constructions, Level 9, 510 Church Street, Cremorne VIC 3121 phone 03 8420 1200, email viccontact@kane.com.au, website www.kane.com.au
Mann Vic have proven to be a reputable and sought out provider for demolition services across Australia and were the obvious choice for the Tier 1 Demolition and HAZMAT removal at the Student Precinct at the University of Melbourne.
Their scope of works included full demolition of the Alice Hoy Building; the complete refurbishment and atrium removal of the Eastern Resource Building; multiple floor refurbishments in the Doug McDonell Building; extensive and articulate heritage salvage with new openings created in heritage three foot thick walls in both the 1888 Building and the Frank Tate Building.
“There were multiple challenges working around buildings that were live and had members of the public in the vicinity,” said Mann Vic’s National Operations Manager, Khaled Awad. “There were also many heritage restraints that required innovative and critical thinking concepts to ensure there was no damage to the heritage aspects of each item and building.”
Renovation or refurbishment of a building often requires specialised strip out services. Mann Vic have the experience to ensure safety, efficiency and maintenance of structural integrity. Strip-out services include interior building strip-outs, removal of fittings and fixtures, removal of walls and partitions, window removal, insulation, grid and ceiling removal, concrete floor removal and masonry walls. Materials are salvaged, reused or recycled wherever possible, the site reaching an extraordinary 97.2% recycle rate.
“For this project each building required its own unique and custom demolition sequence,” said Khaled. “With client consultation, thorough planning and attention to the job requirements, we developed project specific demolition methodologies which were executed by our expert demolition team.”
Along with the heritage salvage and restoration, Mann Vic also provided high end needle propping, structural underpinning, Friable and Bonded Asbestos removal, suspended slab back propping designs for 50 tonne excavators, sequenced crane lift plans for the removal of a custom steel truss atrium and precast panel sections over 22 tonne each.
The project was also taking place during the height of COVID Restrictions, Mann was able to implement and follow all guidelines without affecting the project’s safety and programme.
Mann Vic has extensive experience in heritage conservation projects and façade retention. This includes design and construct engineering, installation of temporary/ permanent structures, unique and pioneering demolition sequences as showcased at the Iconic Malt District, Nylex Clock Silo’s –where Mann Vic took out best in their field in the International World Demolition Awards.
Mann Vic’s mission is to fulfill its vision by fostering innovation, education and relationships to invigorate and revolutionise the demolition industry, totally committed to continual improvement through the execution and delivery of their interactive application technology, safety, and environmental and quality management
systems ensuring projects are delivered professionally.
“We bring a fresh approach and collaborate closely with our clients to ensure each project is delivered safely, professionally, within time frames and on budget,” said Khaled.
Mann Vic is able to provide Demolition Consultation Services to clients during the scoping phase of decommission or demolition projects. Working with an experienced demolition team from the beginning ensures that project planning and risk analysis are expertly considered every step of the way.
With the essential expertise, systems and equipment, Mann Vic successfully deliver on projects of all sizes and degrees of complexities. Mann Vic currently have over 23 active sites including the iconic Marvel Stadium, Metro Tunnels in Melbourne and Chadstone Shopping Centre one of the largest in the Southern Hemisphere and operate in all sectors of Demolition.
For more information contact Mann Vic, 4-10 Nantilla Road, Clayton VIC 3168, phone 1300 626 647, email admin@manngroup. com.au, website www.manngroup.com.au manngroupvic manngroupvic manngroupvic
Passive Fire Protection and Thermal Insulation are a vital component of any building these days as they not only provide the fire protection but sustainability to the building by increasing its thermal efficiency contributing to the Reduction of the Energy Consumption hence less Carbon Footprint.
The Passive Fire Protection main purpose is to serve as a fire strategy to protect the Building Structure in case of Fire Scenario to allow for enough time for evacuation and for the Fire Suppression Systems to activate and avoid a structural collapse. PFS Group was the company selected to work alongside with Kane Constructions to supply and install the Passive Fire Protection and Thermal Insulation required for the University of Melbourne – Student Precinct Buildings.
PFS Group is an Australian Service Driven Company with over 25 years of experience providing Fire Rating Solutions, Thermal and Acoustic Innovations to all industry sectors including –Commercial, Industrial, Mechanical, Civil, Healthcare, Heritage Listed and Special Purpose Buildings.
With over 20 hi-tech spray machines and specialised equipment, highly skilled fully trained personnel in and out of the job sites and a remarkable customer service to meet all customer requirements and time constraints.
“Throughout the duration of the project PFS Group was confronted with challenges that involved innovated solutions to meet client’s requirements,” said PFS Group Senior Project Manager, Jose Fragachan.
Furthermore, PFS Group Construction Project Manager, Eduardo Capiello added; “Even though challenges were encounter throughout the project, PFS Group Personnel and Management Team worked hand-on-hand with our suppliers (Grace Australia, Knauf Insulation and Permax) and Kane Construction management team to keep the project running smoothly and within the timeframe, even during the difficult pandemic times. It was a pleasure to work alongside Kane Construction Management Team in this project and we look forward to continuing building our relationship with them.”
For more information contact PFS Group, 2/401 Francis Street, Brooklyn VIC 3012, phone 03 9318 9717, website www.pfsgroup.com.au
Quantum Library Supplies create innovative spaces designed for today’s University, Public and School Libraries and have a long-term relationship with the University of Melbourne. For the fitout of the refurbished ERC Library, Quantum were contracted to design, deliver and install the return and sorter system including the electronic returns bins – a system they originally designed and installed over 20 years ago.
“We are always happy to work with builders and architects to ensure we get the design right,” said Sales Manager, Colin Matthews. “In this job we spotted an issue with one of the doors clipping a returns bin when it opened. Working the challenge through we were able to have the door moved so it no longer obstructed the system.”
Over 90% of Quantum’s products are manufactured in house at their Brisbane factory. Colin’s role is to visit project sites before the design is finalised and created in Brisbane. Local subcontractors install the product with the Quantum techs able to remote-view the install and provide tech support.
Quantum Library Supplies has been designing innovative libraries, manufacturing library furniture, shelving and book handling automation for libraries Australia wide since 1979 and is an Australian family-owned business with a staff of 21. With more than 40 years in business, Quantum has evolved with the market.
“We originally started working with plastics and shelving,” said Colin. “But we’ve grown to have our own joinery, steel and electronic
workshops. One of the benefits of being a company that specialises in custom manufacturing is that we can design great pieces of custom furniture.”
Quantum’s vision is to provide unique and custom solutions that are not only best of breed but also set the trend for innovation in Libraries and Schools, Australia Wide. Recent projects include full fitouts at Avalon Public School, Bilpin Public School Woodford and Strathpine Public Libraries, as well as the flood refurbishment of Lismore Public Library.
For more information contact Quantum Library Supplies, 1/135 Ingleston Road, Wakerley QLD 4154, phone 1800 773 374, website quantumlibraries.com.au
R L Foote Design Studio was founded by Installation Artist, Designer, Chef and Food Designer Ryan L Foote whose diverse background provides a unique source of technical know-how and creative innovation. The studio created the custom ceramic door handles for the entire Student Precinct of the University of Melbourne.
“The challenge of this project was to get the right tolerance for the wear and tear from moving parts right,” said Ryan. “We designed the mould and then used our in-house 3D printer to make the master moulds so we could be super precise with the castings.”
The project was able to be designed and manufactured in Foote’s Melbourne studio, reducing costs and the probability of human error.
“The challenge of this project is also the highlight, as we got to work with the design at every step to ensure it met the specifications,” said Ryan.
This project took place at the same time Ryan was moving his studio to a much larger site. “The new space was needed as we are taking
on much bigger scale architectural projects in both Australia and internationally.”
The larger space means design and production of projects including large tiled artworks, ceramic door handles and custom light fittings. It also includes a glaze lab where Ryan develops all the glazes they use at the studio from scratch. This allows for new custom finishes or replication of historical glazes on handmade tiles or handles.
As well as production amenities, the new R L Foote Design Studio has a large showroom and gallery, allowing clients to come and see all the glazes and finishes available.
“The studio has capacity for small custom designs as well as much bigger projects,” said Ryan. “We can produce 40 door handles or 10,0000 plus tiles, depending on the brief.”
For more information contact R L Foote Design Studio, 1 Parslow Street, Clifton Hill VIC 3068, phone 0404 873 127, website www.rlfootedesign.com
Focus Environmental is Australia’s primary environmental and occupational hygiene consultancy and they were responsible for the environmental investigation works for the University of Melbourne Student Precinct project.
“This included investigating, sampling, and analysing the soil and groundwater onsite for any contamination,” said Focus Environmental’s, Dennis Yeoh. “Identified contamination was managed onsite and remediated. This ensures the site is appropriate for its future intended use and proposed development.”
Focus Environmental offers a comprehensive project management solution for the monitoring of hazardous substances and the removal of hazardous materials including final site validations for businesses and organisations nationally.
“As the project included the demolition of multiple buildings, the overall site is extremely big!” said Dennis. “We completed approximately 100 soil samples during the initial environmental investigation. This number has since increased.”
With a wide range of technical and consulting services, risk and liability management are taken to the next level with Focus Environamental’s
systems and processes that protect their clients, projects and the community.
Focus Environmental can provide preliminary site investigations and detailed site investigations, assessment of contaminated soils for offsite disposal, groundwater well installations and monitoring, remediation action plans, environmental management plans and pre-purchase and divestment due diligence assessments.
The team also offers a full suite of NATA accredited asbestos laboratory services. The laboratory team is eager to provide accurate, fast and cost-efficient analysis solutions for your needs. The laboratory team has a combined total of 20 years experience in the laboratory methods for analysing asbestos in materials and air required by Australian OH&S Regulations.
Partnering with some of the biggest names in construction and development, the team at Focus Environmental hold some of the most sought-after skill sets in the country and are often asked for by name to ensure the integrity of sites across the country.
For more information contact Focus Environmental, phone 03 8680 4611, website www.focusenvironmental.com.au
Livson Construction Services provided a wide range of architectural metal work on the University of Melbourne Student Precinct project.
This bespoke work includes the balustrade and handrail in the stairway and stairs in the Student Pavilion; cable balustrade in the Atrium; steelwork in the pods for the downstairs food outlets; and a variety of metal work in the Arts and Cultural building including the steel canopy and servery of the coffee pod.
Livson also fabricated and installed the stainless-steel gates and brass handrails in the Frank Tate Building. In the Doug McDonell Building they undertook the handrail remediation to bring it up to code, along with the stainless steel shelves and link bridge balustrades.
“There was a lot of consultation between us, the architect and the builder to interpret the design intent and bring it to life,” said Livson Construction Services Managing Director, Nathan Spiteri. “Many of the solutions were bespoke in nature and involved quite a bit of detail.” Livson provides an experienced fabrication and installation service to suit all industries. From the biggest construction sites to the smallest fabrication jobs, Livson has a sound reputation for its knowledge and experience in the fabrication industry.
“Our team worked really hard to deliver the Student Precinct project to the standard it is,” said Nathan. “Nothing was standard on this job but we were able to come up with the designs that captured the intent, and were feasible and achievable within the allocated budget and time frames.”
“I’m very proud of the outcome and the effort that produced such a great looking collection of buildings.”
Livson Construction Services is an adaptable business that can operate in any working environment. Experienced in all fabrication, manufacturing, welding and rigging, the construction specialists provide clients with a one-stop-shop for all their construction needs. Livson prides itself on the quality and service provided to its clients.
For more information contact Livson Construction, Unit 3/20 Sunline Drive, Truganina VIC 3029, phone 03 8353 2829, email info@livson.com.au
A&A Cabinets Impressions Group (AACI Group) is a family owned and operated architectural joinery manufacturer based in Thomastown, Victoria. AACI Group was contracted to provide the wall panelling, theatre wall panelling, banquet seating, balustrade upholstery, fixed tables and feature walls for both the Arts and Cultural Building and the Eastern Resource Centre Library.
“There were multiple challenges to overcome on this project,” said Company Director, Alf Lucchesi. “The complexity of the design and working with the contractors to coordinate the project was a massive part of the challenge. But it was also the highlight.”
AACI Group worked with subcontracted companies including GAAS Upholsterers and Decor Panels to supply and install the various elements on this project.
Founded in 1979, AACI Group has built an enviable reputation in the industry for its high quality workmanship, ability to successfully undertake highly detailed and complex projects, with an excellent track record in meeting strict deadlines on all projects undertaken.
AACI Group is committed to building close working relationships with its clients, and offering superior service. The company celebrated 40 years of operation in 2019, and has cemented its name in the industry. AACI Group prides itself on its desire to continually learn and improve as an organisation, and demonstrates this in its highly
automated production process. The company has made significant investment in technology and software systems to achieve this.
From a management perspective, it uses tailored production software to manage client projects and the production process, while from a manufacturing perspective it uses highly sophisticated 3D CAD software to prepare projects for manufacture. The CAD software then directly links to the numerous computer driven CNC machines in its manufacturing plant, enabling a highly efficient operation. This enables the company to offer shorter lead times without sacrificing quality and accuracy.
For more information contact AACI Group, phone 03 9464 2133, email aac@aacabinets.com.au, website www.aacabinets.com.au
CLIENT : Victorian State Government
ARCHITECT : Wood Marsh Architecture
CONSTRUCTION VALUE : $564 million
TYPE : Rail/Transport/Infrastructure
The Level Crossing Removal Project – Preston involves the construction of a new rail bridge in Preston and two new sustainable railway stations including comfortable waiting rooms, undercover seating areas, which will rejuvenate and create safer more direct links between public transport, local shops and parking.
The Level Crossing Removal Project (LXRP) continues to work towards its goal of removing 110 dangerous and congested level crossings in Melbourne by 2030, with a total of 67 level crossings removed so far. The new infrastructure reduces travel times and improves safety for road users, pedestrians and those who use public transport, walk or cycle. Work to remove level crossings is well ahead of schedule and on budget, with 11 sites currently under construction. In total the LXRP will deliver more than 50 new, modern train stations to Melbourne and the region. Additionally, there will be further rail network upgrades such as new train stations, track duplication and train stabling yards.
The Level Crossing Removal Project was established by the Victorian Government to oversee one of the largest rail infrastructure projects in the state’s history.
“Around 82,000 vehicles passed through these level crossings each day, with the boom gates down for up to 40% of the morning peak. During construction we used a ‘single line running’ methodology
through Preston for three months to minimise disruption to services. This allowed trains to run on a single track on a newly-completed rail bridge – bypassing Preston and Bell stations while they were in construction and we didn’t need to close the whole Mernda line for long periods of time,” said Minister for Transport and Infrastructure, Jacinta Allan.
The Preston project involves the construction of a 2km rail bridge over four roads and two new stations, Preston and Bell. New facilities include modern waiting rooms, outdoor undercover seating and contemporary lighting, The development has revitalised the area by making it safer and more convenient with easier access to parking areas, public transport and shopping districts.
The new Preston Station has been architecturally designed with a bright coloured façade that reflects the vibrancy of contemporary city living, reminiscent of the vivid colours of the produce found at Preston Market. There are lifts to the platform at each station entrance that are big enough to accommodate mobility scooters, wheelchairs
and prams. Bike hoops outside the station provide parking spaces for 51 bikes and a new Parkiteer cage provides safe and secure storage for 52 bikes.
The new work has been designed for water and energy efficiency and sustainable features include solar panels, rain water reuse, LED lighting in the station and car park, and environmentally sustainable materials to reduce greenhouse gas emissions.
By 2018 site investigations, technical and engineering assessments were completed and engagement with the Preston community commenced in 2019. Throughout 2020 designs were finalised and early site works begun. Construction began in 2021 and by 2022 the level crossings at Oakover Road, Bell Street, Cramer Street and Murray Road in Preston were removed. The Mernda Line was elevated with the construction of a bridge and further installations include a new signalised pedestrian crossing on Murray Road and a pedestrian crossing on Cramer Street. By the end of 2022 the new stations at Bell and Preston opened.
“Across the level crossing removal project, more than 20 MCGs of community open space underneath the rail line has been used to create new play and exercise areas, barbecue facilities and an amphitheatre. Over 50km of cycling and walking tracks have been constructed with a shared use path connecting the two stations with landscaping and
native plantings of more than two million trees and shrubs ready for the community to enjoy,” Ms Allan added.
This project has made Melbourne’s busy Bell Street boom gate free, boosting safety for motorists that use one of the city’s busiest roads. “We’re incredibly proud of the work the Level Crossing removal team has done in Preston, removing four dangerous and congested level crossings and building two new state-of-the-art stations,” concluded Ms Allan.
For more information contact Level Crossing Removal Project, Level 9, 121 Exhibition Street, Melbourne VIC 3000, phone 1800 105 105, email contact@levelcrossings.vic.gov.au, website www.levelcrossings. vic.gov.au
Preston has seen the removal of four dangerous level crossings on busy Bell Street, Melbourne, meaning increased safety and an ease in congestion. Oakover Road, Cramer Street and Murray Road also had crossings removed.
The Level Crossing Removal Project involved the construction of a 2km rail bridge, spanning four roads in the area, which will result in the Mernda line being elevated over the roads.
Two sustainably designed railway stations were developed with improved waiting rooms, seating and lighting. Approximately 60,000m2 of open space will be available as a result.
The community will be free to enjoy the new landscaped, multi-use space that will include two new playgrounds, a cycling and shared walking track plus more than 700 trees and 150,000 grasses and plants.
All Systems Contractors, who specialise in rail signalling civil construction, were employed on the project to install the entire combined services route to facilitate the new signalling system and undertake all directional drilling.
Steve Shore of All Systems Contractors explained that they worked on the project for one year, beginning in November 2020, exporting the signalling and electrical cabling, so that the train track removal team could come in without a break in any services.
Despite challenging weather conditions, Steve and his team of 35 powered through as soon as they were able.
“We did all the seasons basically. A lot of heat and then a lot of wet weather as well,” said Steve.
“We’re affiliated with the CFMEU and we have a policy that if it hits 35Cº then the site gets shut. We had quite a large amount of hot days. We’ve experienced more heat here than we ever had before. It was at times just too hot to work. Then it was all the rain.”
The company had limited time to complete the project, plus there was one other challenge to contend with.
“We were working in a tight access working corridor,” explained Steve. “We had the existing train lines still in operation and houses and buildings right beside us, so we had to work between those and the railway line. A limited space to work in.”
Despite having a strict deadline so that their pit and pipe could be installed, and the cabling could be changed, Steve says that he is happy with the end result.
“We have a brilliant relationship with John Holland. We’ve just won the contract for their next level crossing removal. So, we’re going to be teaming up with them again, which is really great,” said Steve. “We’ve been working for them since 2006. They’re always very supportive and we like to perform and do a good job for them.”
The company are currently working on various projects, including the Regional Rail Revival’s Gippsland Line Upgrade.
All Systems Contractors are market leader in the combined services route construction for level crossing removal projects. Having built a solid reputation over 17 years in the industry, and having grown a team of 50 employees, they pride themselves on being incredibly amicable to work with and endeavour to maintain superior standards for both new and existing clients.
For more information contact All Systems Contractors, 46 Exchange Drive, Pakenham VIC 3810, phone 0400 766 751, email steve@allsystemscontractors.com.au website www.allsystemscontractors.com.au
Below Johnson & Young Cranes were contracted for the craning of the structural concrete and steel members.
As part of the North Western Programme Alliance (NWPA) Johnson & Young Cranes (JYC) were contracted for the craning of enormous structural concrete and steel members for infrastructure improvements at the Preston Level Crossing Removal Project.
“As the primary mobile crane contractor for this project we undertook a multitude of varying lifts ranging from general lifting work to concrete panel and bridge beam installation. There were many marque lifts that required the use of our heavy lift fleet which range from 400t to 800t in capacity, but one of the more notable lifts was the dual lift of precast L beams for Span 23 over Bell Street. This required a road closure of Bell Street for the mobilisation of one of our Liebherr LTM1400-7.1 (400t) cranes with one of our Liebherr LTM17509.1 (800t) cranes set up in a tight area between the rail corridor and an existing apartment complex,” explained Business Development Manager, Brett Horvath.
“Johnson & Young Cranes are a leading supplier of mobile crane hire, transport and ancillary services to major civil infrastructure and renewable energy projects across Australia. Boasting a fleet ranging from 3t to 800t in capacity, JYC are well equipped to meet all lifting needs. The Johnson & Young team are passionate and committed,
we understand the constraints, challenges and possibilities of every project and we know that the right attitude is essential. The entire team works towards the common goal of ensuring that each job is completed safely, efficiently and to the highest of standards.
“Planning is pivotal to the success of any lift, our inhouse engineers use the latest technology to assist in the design of lift plans and rigging diagrams that are Tier 1 site compliant and subject to regular thirdparty reviews. Our clients know that the team at Johnson & Young Cranes will manage any challenge, properly plan and successfully complete both one off and project-wide lifts.”
JYC is expert at lifting the huge and heavy for large scale builds. JYC has completed a number of LXR projects across Melbourne and have been at work on wind farms across the country, craning pieces for the maintenance and construction of turbines which stand between 85 and 150m tall.
For more information contact Johnson & Young Cranes, 173-175 Northbourne Road, Campbellfield VIC 3061, phone 03 8339 3300, email sales@jycranes.com.au, bookings@jycranes.com.au, website www.jycranes.com.au
Wamarra has a reputation for delivering quality infrastructure outcomes across diverse sectors. For the Melbourne level crossing removal project – Preston, Wamarra were contracted to supply and install precast seating with bespoke timber elements along with gym and play equipment with surrounding exposed aggregate concrete and shared user paths.
“Our scope of works was construct only,” said Contracts Manager, Rhys Hannan. “We built the job off a set of drawings and specifications that were provided at the time of tender and revised throughout the construction process.”
The landscaping vision included hardy, native Australian plants to provide a long-term aesthetic that could withstand the elements. “We used native plants in garden beds, swales and retention basins including the drought resistant species Buffalo grass,” said Rhys. “It’s the only grass native to Australia that is also used as turf grass. We have also installed salvaged logs that provide a home for fauna as well as seats for the community.”
Wamarra commenced work onsite in July 2022 and is expected to be complete in February 2023. During the peak periods, Wamarra had
around 75 staff onsite each day. “We endured many days of inclement weather during September and October with torrential rain, flooding and wind which created a number of challenges in the constructability of the project,” said Rhys. “This required systematic revision of the construction methodology of several scopes. Furthermore, access onsite required revision due to the challenging access whilst working within the rail corridor.”
Wamarra is an Indigenous owned and operated landscaping and civil contracting business. Wamarra provides social and sustainable procurement and career opportunities for Aboriginal people, strengthening Indigenous participation and engagement within the construction industry. “We offer clients a cut-and-shut solution, encompassing the full spectrum of civil contracting, with solutionsfocused capabilities that include transport, rail, port, water, defence, resources and energy sectors.”
For more information contact Wamarra, phone 1800 314 659, email info@wamarra.com.au, website www.wamarra.com.au, @wamarracontractors, Wamarra
CLIENT : Victorian Health Building Authority
MAIN CONSTRUCTION COMPANY : Kane Constructions
ARCHITECT : Lyons
STRUCTURAL ENGINEER : Meinhardt Group
CONSTRUCTION VALUE : $76 million
TYPE : Healthcare
The Wonthaggi Hospital expansion involved a high degree of interfacing with the existing live facility with services and infrastructure upgrades to cater for the new facility, future expansion and improved reliability of existing services.
Multi-award-winning Kane Constructions were responsible for bringing to life the $76 million expansion of the Wonthaggi Hospital. In the works since 2018, the expansion was earmarked for redevelopment as part of the 2018 State Election commitment to give one of the fastest growing regional areas in Victoria additional and much-needed health facilities.
Community integration and continuity of existing services was the overall theme of the development with construction taking place while the existing hospital still in operation.
Kane Constructions collaborated with Bass Coast Health to deliver the project which involved the construction of a new, four-story hospital facility adjacent to the existing facility with three new operating theatres, a day procedure room, central sterilising department (CSSD), a new emergency department with 18 additional treatment spaces and a new, 32-bed inpatient ward to meet the capacity to treat 26,000 extra emergency patients each year.
The building is connected to the existing facility via new, undercover link ways and includes a new ‘Central Energy Node’ to centralise and provide upgraded plant, critical infrastructure and services connections to both facilities.
“Although a practical health facility, the new building also features several striking architectural elements such as the multi-coloured 4mm anodised solid aluminium cladding system on the external façade of the building in coastal tones, which is a credit to the project Architect Lyons and provides a unique and distinctive building for the community,” said Kane Project Manager, Brendan de Neef.
“In addition, the main atrium and entry is a spacious, 3-storey space filled with natural light from large, north-west facing windows.”
Green spaces were integrated strategically into the design on levels one and three, to provide multiple spaces for patients and staff to access fresh air and calm areas for respite.
Effective communication between the Kane team, Bass Coast Health and all contractors was the key during the 22-month build and Kane was managing up to 230 workers onsite at any given time. Ensuring the existing hospital’s operations were uninterrupted during construction added another element to the project.
“Working and living regionally and delivering this project through the pandemic was a significant challenge as the availability of material and labour was compromised. We supported and used local subcontractors and suppliers whenever possible,” Brendan said.
“In addition the location of the new building, high water table and perched water was another challenge which meant a significant amount of work went into the design and construction of waterproofing and hydrostatic slab elements to prevent leaks and building uplift over time.”
The Wonthaggi Hospital has recently been approved for an additional $290 million from the State Government, for future works. Plans include new wards and extra beds, an improved medical imaging unit and the construction of a new helipad and at least 750 local jobs will be created through the development.
The new hospital means more patients can receive treatment much closer to their homes and families, while also reducing the number of patient transfers to other hospitals.
“The end result here at Wonthaggi is a high quality outcome and we’re pleased to have delivered this world-class healthcare facility for the Bass Coast region,” Brendan said. “It’s an important piece of infrastructure and the fact that an additional 26,000 patients can be treated each year is a fantastic outcome for the local area.”
Kane Constructions, a privately-owned construction company which is active in all sectors of the industry, was founded in Melbourne in 1973, operates throughout the east coast of Australia. Responsible for delivering more than 2,500 world-class projects, Kane is currently working on several exciting projects including 120 Collins Street, Ground Floor Plane Revitalisation project, Aikenhead Centre for Medical Discovery, Main Works project and the Melbourne Racing Club, Caulfield Public Realm and Administration Building project.
For more information contact Kane Constructions Pty Ltd, Level 9, 510 Church Street, Cremorne Victoria, phone 03 8420 1200, email viccontact@kane.com.au, website www.kane.com.au
Phoenix Fire is a 100% Australian owned and operated Victorian based company, which specialises in integrated fire protection services for the construction and building maintenance industries. Experienced in the installation of smoke detection and alarm systems, EWIS, Vesda and Special Hazards.
Managing Director, Travis Cox has more than 20 years of experience in the industry and a proven track record for completing projects with a safety first, cost effective and time efficient approach. The Phoenix Fire team were engaged by Kane Constructions and where onsite at the Wonthaggi Hospital Expansion for 15 months, to complete their scope of work within the working hospital environment.
“We’ve worked with Kane on a number of projects over the years and enjoy a close working relationship with them,” Travis said. “I’ve done a lot of work in and around hospital environments and know all too well the importance of having their services uninterrupted and operating the whole time, so this was where we could best apply our knowledge and expertise.”
Phoenix Fire kicked off their scope by designing and implementing strategies to comply with the requirements for the hospital expansion,
including the networked fire and alarm systems and the Emergency Warning Intercommunication System (EWIS) throughout the new build. They are also upgrading the fire protection systems in the existing hospital and integrating the network across all buildings for maximum efficiency.
Working alongside a live hospital environment in the building next door was not without its challenges and required Travis and his team to be one step ahead at all times in order to minimise any disruption. “The result here at Wonthaggi Hospital is one that everyone involved can be really proud of and it’s a great addition to the area,” Travis said. “It will meet the demand of the growing population and gives the locals a place where they can go for medical services and treatment when they would previously have had to travel for this.”
Phoenix Fire’s portfolio boasts several large-scale projects including Iglu Flagstaff Student Accommodation on King Street and the company is once again joining forces with Kane on Iglu Russell Street, a 28-storey accommodation facility in the heart of Melbourne’s CBD.
For more information contact Phoenix Fire, phone 03 9738 7183, email info@phoenix-fire.com.au, website www.phoenix-fire.com.au
At the Wonthaggi Hospital Expansion, the team at Meinhardt was engaged to carry out the structural engineering, including the design of the super structure, as well as the civil engineering aspect for the site roads and car parking.
Associate Director Structural Engineering, Elian Kocibelli whose experience in the industry spans some 16 years, spent close to two years on this project. He and his team were tasked with design and documentation for the hospital, which would need to meet the demands of a growing community.
“I looked after the project from day one and was involved in the coordination and development of the design with the architects, Lyons,” Elian said.
One challenge was the location of the original building, placed further south within the development site, where the ground water pressure was very high and deeper excavation would have been required. Not only costly, but water seeping through would pose safety risks to the construction crew as well. Meinhardt’s advice was to relocate the building footprint a further 25m north, resulting in a lesser depth of excavation and also reducing water pressure to the ground floor slab.
“This expansion at Wonthaggi Hospital is such an important piece of infrastructure and has resulted in a fantastic product for the local community,” Elian said. “It has a high standard design and in terms of buildability, Kane has done an amazing job once again.
With an emphasis on building long-term relationships with its clients, Meinhardt has gained a reputation for going above and beyond the scope of works, utilising its full complement of specialist teams including environmental, façade and project management with specific industry knowledge to meet today’s standards and safety codes.
Meinhardt’s relationship with Kane continues to grow and the two companies are currently collaborating on several projects at the moment. The recently completed Northern Hospital in Epping joins Wonthaggi and a long list of hospitals that the two companies have delivered together.
For more information contact Meinhardt Australia, Level 12, 501 Swanston Street, Melbourne VIC 3000, phone 03 8676 1200, email contact@meinhardtgroup.com website meinhardtgroup.com
At the Wonthaggi Hospital Expansion, an uninterrupted power supply was particularly important to keep the site running during the construction of the new, three-storey hospital facility. Engaged by Kane Constructions to provide power and lighting 24/7, Jefferson Industries had their first generator onsite in January 2021 and worked hard to keep up with each stage of the project, which progressed at a rapid rate.
“We started with one, 100 KVA diesel-powered generator and as the build progressed, we had up to five generators onsite of various sizes,” said Managing Director, Eden Jefferson. “We also implemented uninterrupted power supply (UPS) solutions for all fridges and electronics onsite using battery-powered generators. Not only did this save Kane money on the overall running costs, but it reduced noise and allowed the security and CCTV systems to keep running at all times.”
Opting for both Cummins and Perkins generators at Wonthaggi Hospital, chosen for their reliability and outstanding performance, Eden and his team were onsite almost daily checking full levels and managing their equipment. “The Wonthaggi Hospital Expansion is an amazing project and Kane is so efficient at coordinating workers and all stakeholders and we are proud to have been involved,”
Eden said. “We not only met the requirements, but exceeded them and I’m looking forward to what we can achieve with Kane in the future.”
Jefferson Industries has been powering up and lighting up building sites and major events all across Victoria since 2018 and continues to build on its reputation for reliability, efficient service and a promise to maintain its competitive rates. “What started as a small operation with just a few generators to service the local builders, has since expanded to three trucks, five full-time workers and around 30 generators to meet the demand in the industry for temporary power and lighting on building sites,” said Eden. “We pride ourselves on our customer service and offer refueling and regular servicing for our units and all outside of business hours, so as to maintain an uninterrupted power supply for our clients.”
The company is currently working on significant projects for the Victoria Police and the Australian Defence Force, as it looks to expand on its already impressive portfolio.
For more information contact Jefferson Industries, Factory 4/32 Boys Home Road, Newhaven VIC 3925, phone 0492 915 877, email admin@jeffersonindustries.net, website www.jeffersonindustries.net
When it comes to large scale commercial projects, the experience and professionalism of R&R Bricklaying meant they were the perfect team for construction of the new Wonthaggi Hospital.
The R&R team were led by Darren Read, who first established the business in 1999, and today is known to be one of Gippsland’s most sought after and reliable bricklayers.
“It was great to work with Kane Constructions on such a large commercial project on the Bass Coast; especially a project that will offer much needed services to the area,” Darren said.
The job involved pattern brick work and a lot of core fill block work for both plant and electrical rooms, with the team laying around 20,000 blocks and 25,000 bricks for the new hospital.
R&R Bricklaying aren’t new to completing commercial construction projects; they’ve also worked on the Yarram Medical Centre, Cowes Nursing Home, Cowes Medical Centre, Ashwood Nursing Home, Cheltenham Nursing Home, Mary MacKillop Secondary School, Foster Basketball Stadium and the list goes on.
Bricklaying for Darren isn’t just a business - it’s in his genetics.
Darren started out as an apprentice at the age of 17, working alongside his father for seven years before going out on his own, working in London for two years as a foreman for a company building highrises in Chelsea Heights before returning home and establishing R&R Bricklaying.
Based in Leongatha, Darren and his team now service the South Gippsland region, South East Melbourne, Latrobe Valley and Bass Coast, making them accessible to a wide variety of projects in both metro and regional areas.
With a large team, the R&R crew has decades of experience between them, across a wide variety of bricklaying skills and projects, and have earned their reputation for providing both quality customer service and attention to detail, which has made them a favourite choice for builders - both local and high end.
For more information contact R&R Bricklaying, PO Box 466, Leongatha VIC 3953, phone 0409 270 500, email randrbricklaying@ bigpond.com, website www.rrbricklaying.com.au
MAIN
ARCHITECTS
STRUCTURAL
The Spirit of Tasmania project involved the construction of a state-of-the-art passenger and freight terminal for future Spirit of Tasmania operations, and includes a world-first three-level boarding ramp for cars, caravans and trucks to board simultaneously. The project also included an impressive terminal building providing improved amenities for passengers, staff and pets, and a boarding area that includes marshalling for 600 cars and a parking area for 150 semi-trailers.
Kane was awarded the $19 million Design and Construct contract to build the Spirit of Tasmania terminal at Corio Quay by GeelongPort in November 2021.
Work on the development, which covers approximately 12 hectares, commenced in January 2022 and was completed in September. The scope of Kane’s work covered modifications to the existing façade of the shed, integrating it with the working wharf and fitout of all its internals.
The construction site was internal to the structure and on any one day, up to 150 labourers working for various subcontractors could be found onsite. In addition to this, there were civil engineering contractors working on the roads outside and marine contractors working on the wharf structure.
Careful planning and logistics were required to effectively manage access to the site for trades, equipment and supplies, throughout the seven month programme.
The complexity of the building presented a number of unique challenges for the project. The sheer size of the canopies that are a major architectural feature of the façade, had to be fabricated with special attention to their geometry. Once these mammoth structures arrived onsite, they had to be carefully cantilevered and moved into place with erection procedures used to fix them in place.
Kane Constructions is proud of its role on the project. The state-ofthe-art terminal features a world-first three-level boarding ramp for cars, caravans and trucks, more efficient passenger check-in, various amenities including food and beverage outlets and even a children’s play area and pet exercise park.
Kane Constructions has a longstanding relationship with Geelong, with over 30 years’ experience working in the region across hundreds of projects and partnering with local firms. They are one of the largest contractors in the construction industry operating in the Bellarine
Peninsula region. Over 30 of their employees reside in Geelong and the region and they employ a large local direct labour force as part of the company’s structure division.
Kane has successfully completed projects in Geelong such as the multi-award winning Geelong Arts Centre Ryrie Street Redevelopment (Stage 2), Geelong Library and Heritage Centre and GMHBA Stadium Stage 4 Brownlow Stand Redevelopment along with hospital projects, St John of God Geelong Hospital Redevelopment, Geelong Hospital Emergency Department and Geelong Hospital Children’s Ward.
Kane is currently delivering the Northern Aquatic and Community Hub in Norlane for the City of Greater Geelong.
For more information contact Kane Constructions, phone 03 8420 1200, website www.kane.com.au
Below Select were engaged to interpret the concept brief to develop and integrate cutting-edge technology into the project.
Geelong based Select Architects started as a one man show in the laundry at the back of Peter Serra’s home. 16 years later, the company boasts a team of 20 plus inspired professionals, and now Select is one of the teams assisting in the construction of the landmark Spirit of Tasmania terminal at Geelong’s Corio Quay.
The overall design concept was authored by Brand Architects, Select were engaged to interpret the concept brief to develop and integrate the cutting-edge technology and exceptional facilities for the builder to construct a project delivering an unforgettable customer travel experience.
Select Architects are dedicated to helping their clients live, work and learn in inspired and purpose-built environments that balance a high-end user experience with strong client outcomes. Their portfolio of projects spans the commercial, retail, education, residential and retirement construction sectors. They are currently delivering projects nationally for their blue chip clientele.
The award winning practice also has an active community service portfolio and a commitment to growing the craft amongst subsequent generations of graduates. To this end, they provide training in their
graduate programme which allows students to obtain registration to fast track their pathway to becoming senior architects.
The ethos of community service is evidenced by their pro-bono work. This has seen the Select Team work on projects in places as far flung as Vanuatu and Fiji, Papua New Guinea, and Cape York. They also have an active service agenda in Geelong, where they provide assistance to organisations for the dis-empowered and disenfranchised.
Over the years Serra has served on the boards of organisations such as St Vincent de Paul, Rotary, the Geelong Club and Samaritan House and currently serves as Director of the Barwon Health Foundation.
For more information Select Architects, Level 3, 117 Myers Street, Geelong VIC 3220, phone 03 5224 7300, email peter.s@selectarchitects.com.au, website www.selectarchitects.com.au
Brand Architects’ ecological aesthetic is evident in its recent design of the Spirit of Tasmania’s new terminal building in North Geelong. The Melbourne firm began working on the project in June of 2021, with completion earmarked for August 2022.
Adding to the challenge of transforming a pre-existing cargo shed into a state-of-the-art landmark, within a short timeframe, was integrating multiple functions within the structure. “It’s a very busy building that’s got a lot going on. There are the arrival and departure halls, a café, open-plan workspace and offices for staff, meeting rooms, as well as cabin crew accommodation and wellbeing areas” said Director, Gerard McCurry.
“Each function brought with it different functional and technical requirements, where an integrated and efficient architectural and building services design response avoided unnecessary capital cost. Another design challenge was the sheer size of the building idling against the landscape, as the 165m shed had a relatively flat façade. The re-designed exterior draws inspiration from the landscapes of both Victoria and Tasmania, especially Lake St Clair National Park, “with its beautiful mountains, rocky summits, lush greenery, quaint and historic huts, and hills rolling into its lakes,” said McCurry.
Brand Architects incorporated chic dominion cladding to add texture, pairing this with perforated mesh sunshades which peak and pitch over angled windows across the line of the building, to mimic the contours of Cradle Mountain. The palette of neutral greys and bronze is also informed by the vision of the dolerite peak shrouded in cloud.
“It’s the busiest we have been in the 30 year history of this company” says McCurry, but “also the most exciting” with a raft of other projects to come online including a broad range of public infrastructure projects.
For more information contact Brand Architects, Level 8, 176 Wellington Parade, East Melbourne VIC 3002, phone 03 9419 3500, email gerardm@brandarchitects.com.au, website www.brandarchitects.com.au
The Spirit of Tasmania (SoT) terminal is nearing completion and will deliver a state-of-the-art facility in Victoria’s second city, Geelong. Providing project Quantity Surveying (QS) services across the marine, civil and terminal building contracts was leading construction cost advisory firm, WT.
Previously sailing from Port Melbourne, the SoT will commence operations from Geelong Port in October 2022. The new terminal will result in improved overall efficiency in vessel operation, turn-around times and customer experience.
Through its construction cost management services, WT was able to deliver cost certainty for the Client and project stakeholders across design and construction phases of the project. The project delivered on relative tight project timelines and faced challenges in planning and execution of the works. Accurate QS and cost engineering helps ensure resource efficiency, predictability, transparency, and the longevity of a project.
WT employs 380 nationwide across major cities including a local Geelong office. WT in Victoria has specialist teams delivering a range of marine and infrastructure projects across the country. This expertise was called on to help deliver the role on SoT.
Below WT was able to deliver cost certainty for project stakeholders across design and construction phases of the project.
Innovation is central to all WT projects and operations. By leveraging their knowledge and data, the company creates efficiencies and helps simplify the sometimes complex cost paradigm for project stakeholders. WT utilised various software platforms on SoT including Cost-X estimating software and their own inhouse developed ‘proClaim’ utilised for monthly progress claim reporting.
This SoT project is a significant piece of infrastructure and is expected to provide a boon for regional tourism and commerce in Geelong and Victoria’s South-West. While construction will be completed by end of 2022, WT’s ties to the region are set to deepen with other major projects soon to start.
Below Strata Steel Detailing provided shop drawings for steel components for the re-engineered warehouse building.
Steel detailing may be a niche market in construction but it’s emerging as an indispensable service provided by boutique firm Strata Steel Detailing.
As part of the team building the Spirit of Tasmania terminal at Corio Quay, the Victorian company was contracted by fabricators Maddison Wright Engineering to provide shop drawings for steel components. The pre-existing warehouse had to be re-engineered to accommodate new architectural features along with an additional mezzanine floor and auxiliary parts.
Dwayne Job, company founder, relied on two technologies to model the environment and detail every last component. The first was a Trimble TX6 3D Laser Scanner.
“It’s quite an amazing bit of kit,” explained Job. “Rather than take a measuring tape, we use the laser scanner, so when we come into the office, we bring measurements of exactly what is there... It’s millimeter perfect.”
The Trimble TX6 sits atop a tripod and turns 360 degrees, capturing images whilst overlaying these on a three-dimensional point cloud.
Back in the office, Job uses the Tekla Structures software to process the data and model it on a computer screen, layering individual components to create a virtual building.
Job spent 27 years working all over Australia as an aircraft maintenance engineer, before starting the company a decade ago. The lateral move was easy, given that aircraft engineering is a process driven field.
“You follow the process at every point to keep aircraft safe, as is the case in steel detailing.” Job found his career move to be very rewarding “because every building is unique; We are skeleton builders, if the skeleton is not right, the building is not right; we need to get into the architects head, the engineer’s head, and come up with creative solutions to big problems.”
His enthusiasm for Corio Quay terminal is palpable. “It’s a nice iconic change for the Spirit of Tasmania, ushering in a new era for Tasmania and a boost to Geelong.”
For more information contact Strata Steel Detailing, 18 Josephine Way, Sebastopol VIC 3356, phone 0407 882 504, email dwayne@ stratadetailing.au, website www.stratadetailing.au
MaddisonWright Engineering (MWE) were also responsible for the fabrication of the mammoth structural steel features of the Spirit of Tasmania terminal at Corio Quay. They were brought in by the builder to fabricate and erect what has amounted to 200 tonnes of steel.
The project was challenging due to a narrow time frame, the sheer size of the steel pieces and ensuring connection to a brownfield environment. The bespoke sun canopies that shade the windows and run along the line of the pre-existing shed were particularly challenging. “They go right up the face and have perforated aluminium sheeting over them. They are very architectural, with their different angles, so it was not an easy job,” explained Project Manager, Lance Rogers.
For the required lifespan warranty, the steel had to be protected but the usual galvanizing bath was impossible given the size of each piece. MaddisonWright instead used a three-coat paint solution that would provide longevity in both structural strength and protective skin. It was also speedier than galvanising to fit the six-month deadline. Erection works commenced in the second week of January 2022 and finished the first week of July.
The engineering was supersized on this building and designed to last for decades to come. But big jobs are what MaddisonWright Engineering do.
Established in Shepparton in 2016, MaddisonWright Engineering has grown from providing small fabrication and mechanical installation services in the food, beverage, and dairy industry in country Victoria, to becoming a multi-disciplined design, fabrication, construction, and maintenance company servicing Tier 1 companies across Australia.
Current projects under way for MWE include a 155 Tonne fabrication and construction project for a meat processing facility in country Victoria along with 350 Tonne fabrication and construction of the new Northern Aquatic and Community Hub in Corio.
For more information contact MaddisonWright Engineering, G16/ 11 Mackey Street, North Geelong VIC 3215, phone 03 5814 5210, email info@maddisonwright.com.au, website www.maddisonwright.com.au
The Pentridge Adina Hotel project consists of 106 apartment style hotel rooms, 19 heritage suites and 56 residential apartments above the hotel, plus ground level conference spaces, a function centre within the prison’s former chapel, and the reconstruction of the Annex building.
Delivered by Construction Engineering, the Adina Apartment Hotel Pentridge forms part of this one-of-a-kind lifestyle precinct in the suburb of Coburg and will be a hotel offering like no other.
The scope was for the construction of an 18-level structure including three levels of basement, 106 guest suites over nine levels, 56 residential apartments, a public rooftop garden and the restoration and conversion of the existing Division B to feature as a part of the hotel. There are 19 Heritage Suites,
fine dining, a basement swimming pool, wellness centre and gym facilities and the prison’s existing Chapel has been turned into a conference area.
Early works undertaken by Construction Engineering included the dilapidation of existing heritage structures, plus the demolition and conservation of the existing Division B Annexe Building at the end of 2019. This was a huge undertaking and removing mass volumes of bluestone to turn prison cells into luxury accommodation was not without its challenges.
“This stage of the project saw numerous inspections from Heritage Victoria and consultation with archaeologists to establish a record of the existing structures prior to the commencement of works,” said Marshall Rippon, Project Manager at Construction Engineering.
“We had a workforce of 172 onsite, including a team of 10 employees at head office to deliver this project and as one of the largest bluestone restoration projects in Australia, access and logistical challenges meant the planning and sequencing of the works was always front-of-mind.”
Completing the excavation of the pool within the Division B basement was also a tough task, given the fact that the building’s existing openings and doorways couldn’t be modified under Heritage Victoria’s guidance.
Construction Engineering engaged specialist contractors with custom equipment to navigate through this and has added another drawcard to this new and enviable destination.
Open communication and cooperation with the entire project team was key and resulted in a team environment which was consistent, clear and collaborative.
“As a site team, we focussed heavily on collaboration and careful consideration of the construction sequence prior to commencing any works,” Marshall said. “Having this understanding and commitment from all contractors, namely Caelli Constructions, Austech Facades, JMC Facades and Earth Electrical, made the project possible and ensured the most successful outcome was achieved.”
With more than 90 years of combined construction experience among the directors alone, Construction Engineering’s traditional approach with its clients is the reason why the company enjoys repeat business and why they were the ideal choice to bring this exciting project to life.
“Construction Engineering has developed a lasting relationship with developer Shayher Group over the last seven years at the Pentridge Prison site and the hotel is one of many projects that we have completed here,” said Marshall.
“The redevelopment of the Pentridge Prison site is exciting for the whole community. So far, the redevelopment has already rolled out the Pentridge Shopping Centre, Horizon Apartments, The Rook and Victoria Tower. The next part of this exciting development is the new Adina Apartment Hotel Pentridge.”
Looking to the future, Construction Engineering is focused on maintaining its strong client relationship and repeat business with Shayher Group, including to continue to assist Shayher with completing the entire Pentridge redevelopment.
For more information contact Construction Engineering, PO 179, South Melbourne VIC 3025, phone 0448 386 216, email mrippon@coeng.net.au, website www.constructionengineering.com.au
DDEG is a 100% Australian-owned, multi-disciplinary engineering consultancy which specialises in fire safety engineering, acoustics and vibration, disability access and building code performance solutions. Established in 2016, DDEG maintains a fleet of high end instruments and test equipment for accurate acoustic measurement and monitoring.
“Our acoustics team has experience in all aspects of acoustics and vibration and we provide our services across various sectors. We provide advice on sound insulation and speech privacy, room acoustics, noise and vibration control, plus a range of other engineering solutions,” said Andrew Mitchell, Director of Acoustics at DDEG.
DDEG was engaged by ACOR Consultants at the Pentridge Adina Hotel to carry out the initial analysis of the site, on a scope which included stricter parameters than usual for the international hotel client.
“Our early work involved ensuring that the façade of the Tower Building was designed to cope with traffic noise from Sydney Road, and designing noise treatments for the rooftop plant so that noise emissions to the nearby buildings and residents within the tower itself were controlled,” said Irena Peoples, Senior Acoustic Engineer at DDEG.
As the design progressed for both the Tower and the Heritage Buildings, DDEG consulted with the project team to develop and meet the acoustic requirements where there were design constraints such as needing to retain heritage elements which were never intended to stop noise.
“Working with the project team, we had to design extra door sealing and secondary glazing for the Heritage Hotel Suites, as well as an acoustic airlock for the function area in the Heritage Building, so that certain features of the original rooms could be retained,” Irena explained.
“The project has benefited greatly from regular meetings between the project manager, the builder, the client and ourselves and the result is two buildings which look great and are going to be a fantastic place to stay. Through our contribution, we are confident that the residents and guests won’t be unduly affected by noise.”
DDEG provides consulting services to projects all around Australia.
For more information contact DDEG, phone 03 8814 3200, email andrew.m@ddeg.com.au, website www.ddeg.com.au
ACOR Consultants is a 100% employee-owned Australian company that has been providing specialist consulting services to the construction industry for 25 years and they pride themselves on delivering technically challenging projects.
At the Pentridge Adina Hotel, ACOR was engaged to deliver the mechanical, electrical, fire, hydraulics, acoustic services and specialist lighting for the project. By embracing new technologies and applying ‘out-of-the-box’ thinking, ACOR was perfectly placed to achieve a sustainable outcome on this unique project.
“We initially started the design in mid-2016 and given the controversial nature of the project and the heritage aspect of the prison, it was a struggle to get Council approval,” said Ryan, ACOR’s National Mechanical Discipline Leader. “We wanted to deliver a successful outcome for the client, but also to put our mark on what is a very unique and historical site.”
ACOR’s problem-solving measures were put to the test due to both the heritage nature and the age of the building, which made it challenging to comply with current code requirements in relation to ventilation, smoke hazard management and fire systems. The team from ACOR
Below ACOR delivered mechanical, electrical, fire, hydraulics, acoustic services and specialist lighting for the project.
worked closely with the building surveyor, Fire Rescue Victoria and the fire safety engineer to find suitable solutions and, where required, seek dispensations.
“Pentridge Adina Hotel offers something that no other hotel in Melbourne does and that is to spend a night in a prison cell,” Ryan said. “And despite the technical challenges on the site, our team has done a great job to hero what is essentially the existing B-division prison, but also develop a high end hotel offering for Adina.”
ACOR delivers projects all over Australia and from time-to-time is involved with projects abroad. The company is currently working on the Fuel Farm Design and infrastructure at a major Australian Airport and the redevelopment of the Scott Base research station in Antarctica.
Creating an environment where ACOR’s 500 plus employees across 10 offices nation-wide can thrive paired with their investment in clients’ success, has catapulted the company to the successful reputation they have today.
For more information contact ACOR Consultants, phone 03 9885 4335, email rtanner@acor.com.au, website www.acor.com.au
Caelli Constructions (VIC) Pty Ltd has been an icon in the commercial building industry for over 50 years. With over 400 employees skilled in trades such as Carpentry, Concreting, Steelfixing, Crane Operations, Concrete Pumping, Welding and Manufacturing. Caelli Constructions strive and succeed in delivering quality products and services, to some of the most successful, and influential Builders in Australia.
These significant years have resulted in the building of a wealth of experience, together with providing systems of work and services, that are tailored to suit the needs of each individual client and project. Each project is then managed by our experienced Supervisors and Staff with the support of our team at Head Office.
We pride ourselves on our strong commitment to Occupational Health and Safety in our workplace. This has resulted in the advancement of specifically developed Safety Management Systems, whilst working closely with our clients to ensure their needs are met.
We endeavour in all instances to ensure that the requirements of the Regulatory Bodies are adhered to, in order to achieve optimum safety for our personnel, and commercial performance.
Caelli Constructions operate a fully equipped manufacturing facility capable of designing, engineering, and producing specialised and complex formwork and edge protection solutions for each project, as well as providing access to an extensive stock of modular and conventional typical Slab, and Wall Formwork systems.
We are immensely proud of our innovation and commitment to the construction industry and as a result have received numerous awards for our excellence in a variety of fields.
Caelli Constructions thrive on creating mutually beneficial working relationships, for all parties involved, and this is reflected in our long-standing relationships with some of the largest and most influential builders in our country.
We are equally proud of our workforce; without them we do not exist.
For more information contact Caelli Constructions, 320 Hume Highway, Craigieburn VIC 3064, phone 03 8338 3300, email info@ caelli.com.au, website www.caelli.com.au
Action Alliance is a fully accredited company which specialises in abrasive blasting and the application of protective and fire-rated coatings on projects of any scale. For more than 25 years, the Melbourne-based company has been providing its services to the construction industry and the work of their expert team can been seen on government and commercial projects across the city’s skyline. Working closely with the team from Construction Engineering at the Pentridge Adina Hotel, Action Alliance’s streamlined application of protective and fire-rated coatings not only ensures the longevity of the paintwork, but also protects against harsh weather elements, corrosion and UV degradation.
“For around five months, we had a team of six applicators onsite, working in situ to apply the required fire-rated coatings to the structural and exposed steel,” said Brendon Woods, Business Development at Action Alliance. We’ve used Promat Cafco 300 Vermiculite Fire Spray for the concealed steel and Permax’s Nullfire SC902 Intumescent paint system to the exposed steel here at the Pentridge Adina Hotel and particular attention was paid to the large steel columns at the entrance of the hotel.”
Action Alliance is well-known in the industry as one of Melbourne’s largest applicators for protective and intumescent coatings and their
large, custom built facility, equipped with overhead cranes, has given the company a competitive edge when it comes to large-scale developments. Action Alliance also has a dedicated site PC and Fire Rating division along with Shamick Transport a specialised transport company which can pick up or delivery all sorts of Over Dimensional loads for major projects.
“The challenge with this job, as with all jobs, is to complete your scope of works in a timely manner and on this project, we were fortunate to be in constant consultation with the efficient crew from Construction Engineering and we were on schedule,” Brendon said. “The hotel is a satisfying and unique mix of old and new design and we achieved a pleasing aesthetic for the exposed steel in line with the design requirements.”
Action Alliance is currently working on the upgrade of Marvel Stadium in Melbourne, as well as the new train stations for the Metro Tunnel. In its 25-year history, the company has also worked on some of Victoria’s most iconic landmarks, including the MCG, Melbourne Park and Melbourne Airport.
For more information contact Action Alliance, phone 03 9931 0740, email info@actionalliance.com.au, scheduling@shamick.com.au, website www.actionalliance.com.au, www.shamick.com.au
MAIN CONSTRUCTION COMPANY : Kane Constructions
ARCHITECT : F2 Architecture
The Queenscliff Searoad Ferries Terminal redevelopment includes the construction of a new building across two floors featuring a stainless steel façade, complete with modern facilities and bathrooms, safer access, improved car parking areas and opportunities for retail such as cafés and tourism ventures.
Kane Constructions was appointed to deliver the new $16 million world-class ferry terminal building at Queenscliff for Searoad Ferries.
The new building provides local commuters, day trippers and international tourists an architecturally designed experience as they embark across Port Phillip Bay.
The development of the Queenscliff Searoad Ferries Terminal consists of the demolition of the existing terminal building and construction of a new building across two floors with a feature stainless steel façade, ticketing and retail area, toilets, kitchens, café, bar and passenger lounge.
The structure was designed by F2 Architecture and was extremely high level in its intent and execution. Every item in the structure was prototyped and thoroughly reviewed before fabrication and installation.
A key architectural feature of the new building includes the curved roof providing weather protection for passengers boarding or disembarking across all seasons.
“The design and shape of the structure is complex and it took longer than we were hoping for,” said Project Manager, Josh Delahunty.
“The curves in the roof are made from stainless steel and every element of this build needed to be measured, modelled, a template cut and then ordered and fabricated section by section.” Of course, what was most challenging has also provided the highlight of this unique building.
“The finishes are exceptional,” said Josh. “Mack Bros supplied the product. The stainless steel standing seam for the façade as well as some of the internal structure comes from Japan. It arrives in rolls and goes straight to Melbourne where it is cut and produced to suit the site standards.”
Every product used on this build had to be of the highest marine grade in order to withstand the elements. The stainless steel used is perfect for the conditions and will never rust.
Kane Construction commenced work onsite in May 2021 and estimated there have been 40-50 workers onsite each day. The project took place around a live, working environment and construction could not impact the ferry operations.
“The elements and the site conditions were tricky,” said Josh. “It was very windy and wet and part of the build extended out over the water which meant we needed to erect scaffolding over the water.” The fabrication and installation of the stainless steel pieces proved to be more time consuming than planned, with the project timeframe pushed out by two-three months.
Kane Constructions is a multi award winning, privately owned commercial construction company active in all sectors of the industry. The company has a turnover in excess of $1 billion and over 450 full time employees.
Jonathan Forster established the company in Melbourne in 1973 and was Managing Director until 2001, Executive Chairman until 2015,
and Chairman since 2016. Kane Constructions operates throughout the east coast of Australia and overseas through offices in Melbourne, Sydney, Brisbane, and Canberra.
Recent and current projects include the Northcote Aquatic and Recreation Centre, Paula Fox Melanoma and Cancer Centre, Springwood Shopping Centre Redevelopment and St Vincent’s Private Hospital Fitzroy.
Kane Constructions was awarded the 2022 Regional Commercial Builder of the Year at the Master Builders Association of Victoria awards and the National Professional Excellence in Commercial Construction: $60 million plus award at the AIB national awards in October for the delivery of the Ballarat GovHub project.
For more information contact Kane Constructions, Level 9, 510 Church Street, Cremorne VIC 3121, phone 03 8420 1200, email viccontact@ kane.com.au, website www.kane.com.au
Approval Systems was appointed to the role of the statutory building surveyor for the Queenscliff Searoad Ferries Terminal project in 2018. The building contains layers of complexity including its use and function as a public building, the need to accommodate vehicle traffic to sea-going vessels’ loading infrastructure, the harsh maritime environment and its unique architectural form.
“Some elements of the design required resolution under the Building Code of Australia performance requirements, which were designed with input from specialists such as fire safety engineers, access consultants and façade engineers. Our wealth of knowledge, experience and expertise was called upon to review the design and issue the building approvals for the terminal,” said Director, Joe Zita
“We were thrilled to be involved with the project, which the Approval Systems team were professionally invested in due to its importance as a significant piece of state and regional infrastructure which will create a legacy for the local community.”
Approval Systems has been one of Victoria’s preeminent building surveying practices for over 20 years. With a reputation for being reliable and integrity focussed, the practice has built up a
comprehensive body of work in its portfolio, representing most sectors of the property industry.
Approval Systems’ projects range from major mixed-use developments, health and aged care, retail and commercial through to innovative domestic design. They work with project teams from concept stage, through design development, contract documentation and construction to ensure compliance of design with all relevant building regulations and codes.
Recent projects include East Brunswick Village, St Vincent’s Hospice and Aged Care, Alfred Health’s Innovation and Education Hub, Frankston Law Courts, Chemist Warehouse, Yarra Valley Grammar and Newlands Road Industrial Estate.
For more information contact Approval Systems, 7.05, 289 Flinders Lane, Melbourne VIC 3000, phone 03 9639 5500, email mail@approvalsystems.com.au, website approvalsystems.com.au
Meinhardt Australia provided an alternate design that included material and time cost savings to Kane Construction during the bid phase of the Queenscliff Searoad Ferries Terminal. Once Kane’s bid was successful, Meinhardt completed full design and construction documentation services and completed construction phase services.
“Three structural engineers worked on simplifying the structural design element arrangement behind the curved architectural form,” said Meinhardt Director, Stephen Payne. “The structure involved extensive analysis of the large roof cantilevers and part of the structure that partially extends over the water to determine the serviceability performance of the roof cantilevers with presetting the propped construction – the preset deflection was spot on.”
Meinhardt Australia is a multi-disciplinary engineering and technical services consultancy with over 60 years experience. Formed in Melbourne in 1955, they now work nationally out of Melbourne, Sydney, Adelaide, Brisbane, Gold Coast and Sunshine Coast. Meinhardt Australia is part of the Meinhardt Group globally, with 51 international offices.“We pride ourselves in collaborating knowledge, expertise and resources between offices to service our clients nationally across Australia,” said Stephen.
Meinhardt’s approach is to offer commercially savvy and ready buildable structural designs that are familiar to the marketplace minimising material and systems procurement risks and allowing contractors to reduce construction time and refine their tender price. As taller and more uniquely shaped buildings become more common, civil and structural (C&S) engineers are constantly challenged to break new ground and reach for new heights. Meinhardt’s renowned innovative C&S practice along with decades of experience, has cemented their reputation as market leaders.
Meinhardt’s current projects vary across all sectors and include Pathway to 152 Mental health beds construction over four hospital campuses, the Geelong Arts Center, St Vincent’s Private Hospital, Victorian Melanoma Centre, CSL Global Clinical Manufacturing Facility, multiple highrise residential and commercial towers in Box Hill and the Sorrento Searoad Ferry Terminal.
For more information confirmation contact Meinhardt Australia, Level 12, 501 Swanston Street, Melbourne VIC 3000, phone 03 8676 1200, email contact@meinhardtgroup.com, website www.meinhardtgroup.com
Mack Bros Roofing Products were contracted to manufacture the roofing and soffits for the iconic world class Queenscliff Searoad Ferries Terminal.
The striking curved building has been designed by award winning architectural practice F2 Architecture who approached Mack Bros to finish the structure with unique cladding, and enhance the architectural design. Mack Bros’ have a strong reputation as innovators of roll forming and their expertise in curving had them well placed to achieve the technical precision required from the projects design.
Stainless steel is ideal for the harsh environment and perfectly complemented the natural backdrop of Port Phillip Bay. F2 Architecture selected the versatile and elegant Straightline Seam 40 product to achieve the right look for the roof, and for the soffits, Mack Bros Straightline Revell 25 was used to achieve the complexity of the inner curve of the design.
While the building has a seemingly simple and natural flow, it is very complex when considering the manufacturing and installation of cladding. The need for precision curving of standing seam panels
and reveals called for by the architects vision, required Mack Bros to implement a new technology to achieve the required outcome.
“This was particularly challenging and it was necessary to work in collaboration with the architect and installer, and build working prototypes,” explained Mack Bros Roofing Manager, Ian Mack. “The final result is testament to the quality we achieved. The curving of the soffits is the first of its kind in Australia.”
The success of this collaboration has cemented Mack Bros as pioneers and leaders in roll forming techniques, who will continue to expand the possibilities on the forms buildings can take and what can be achieved, to bring these designs into reality.
More than seven decades attest to Mack Bros Roofing quality of service and workmanship. The company is a family business and owners Wayne and Ian Mack welcome architects to discuss their future design aspirations.
For more information contact Mack Bros Roofing Products, 630 Heatherton Road, Clayton South VIC 3169, phone 03 9571 7911, email imack@mackbros.com.au, website www.mackbros.com.au
Foodservice Consultants Australia (FCA) is a multi-disciplinary consulting firm that specialises in the design of foodservice facilities and the development of catering operating systems. Contracted to design the kitchen and all food service spaces including equipment in the Queenscliff Searoad Ferries Terminal based on the predefined menu.
“The kitchen and food spaces were designed to be efficient,” explained FCA Director, Julian Ha. “Like most projects we had limited space to work with. This means the space must have flexibility to service three F&B areas - the main dine-in cafe and take away, the bar and supplies for the ferries.”
“The back-of-house had to work so that it could take in new supplies, store the food for both the cafe and the ferries, while maintaining a clear separation between raw and cooked products to avoid contamination. It was a challenge, but we were able to find a workable solution,” said Julian. “It was great working with the design team. They really listened to our ideas and took our suggestions on board.”
FCA provides superior food and beverage facilities design for their clients, ensuring maximum value concept, design, development and
execution of foodservice facilities. All facilities are designed with the budget in mind for efficiency and sustainability.
They have a highly motivated team of catering operations, facilities design and project management professionals and key support staff. Using best practice and technical processes throughout the project, FCA constantly measures their effectiveness through performance measurement, benchmarking and client feedback.
Foodservice Consultants Australia and MTD Hospitality Consulting are part of the FCA Group. FCA works throughout Australia, Asia Pacific and the Middle East from their offices in Melbourne. Projects include hospitals, aged care facilities, high end restaurants, businesses, industry, and institutional projects including prisons and schools.
For more information contact Foodservice Consultants Australia, 10 Mavron Street, Ashwood VIC 3147, phone 03 9887 6628, email melb@foodserviceconsultants.com.au, website www.foodserviceconsultants.com.au
The Sydney Swans Headquarters & Community Centre involved the transformation of the iconic Royal Hall of Industries into a world-class sporting and community hub housing elite training facilities, a lap pool, hot & cold plunge pools, gym, and a new indoor basketball and netball building.
Sydney’s iconic Royal Hall of Industries (RHI) at Moore Park has been transformed into the new Sydney Swans Headquarters & Community Centre.
FDC was awarded the Early Contract Involvement and D&C contract, incorporating state-of-the-art, high-performance training facilities and administration office environment. The building spans over 12,000m2 comprising two separate structures over 2-levels.
The new facility has been designed by architects Populous, re-purposing the RHI building to utilise the large open plan interior as a blank canvas to integrate multiple facilities including an elite gym, medical facilities, a cafe, merchandise and retail store and a multi-purpose indoor training space.
FDC also constructed a new building South of the RHI. This new addition will provide a home for Hoops Capital (the academy for Sydney Kings and Sydney Flames basketball teams) and top-of-the-line
swimming pool rehab facilities for the Sydney Swans playing group. The extension will seamlessly blend in with the RHI, maintaining consistency in height, scale and materials, and will be mostly concealed by the existing heritage brick walls that surround the complex.
“FDC was heavily involved in the design process, bringing the vision of both the Sydney Swans and Populous to life within their budget constraints,” said Project Director, George Pavlakos. “COVID interruptions during the course of the project impacted on funding and we were able to work closely with Sydney Swans and the AFL to value engineer and stage the project delivery.”
This enabled construction works to commence within the facility whilst certain elements were re-introduced as funding and fundraising was received during the course of the project.
“FDC installed a temporary gantry over the excavated basement to continue the concrete pour sequence for Level 1 slabs,” said George.
Extreme weather also impacted the project as civil works were undertaken in the southern courtyard to accommodate a new 20m lap pool, as well as cold and hot plunge pools. This involved detailed staged inground works and coordination of the piling design to ensure continuity of works and maintain drainage throughout the site during significant inclement weather.
“During construction, heritage elements such as boundary walls and the brick façade were supported through the design development of temporary and permanent structures until the new building structure was completed and certified,” said George. Modifications were made to the existing heritage roof structure by incorporating skylights to provide natural lighting to the RHI without compromising the NSW heritage guidelines. This was achieved by utilising access equipment up to 20m high with static lines on the roof, and cranes dropping the skylights glass into position.
all stakeholders informed during the journey of design through to completion,” said George.
FDC is a leading building delivery partner across Australia with an annual turnover of circa $1 billion. They employ over 500 people, hold a reputable client and project delivery reputation and industry leading NPS rate of 75+. They have been acknowledged with over 100 MBA awards including being awarded – Most Awarded Builder in NSW, 7 out of the last 9 years (MBA NSW).
For more information contact FDC Construction & Fitout, 22-24 Junction Street, Forest Lodge NSW 2037, phone 02 8117 5000, email sydney@fdcbuilding.com.au, website www.fdcbuilding.com.au
Family owned and operated Patra Group were the go-to for the manufacture and installation of the custom stainless steel benches, shelves and exhaust hood, coolroom including, refrigeration for the commercial kitchen, hydration station, staff servery & laundry, and various other areas within the brand new Sydney Swans Head Quarters at Moorepark.
The company’s standard of quality is renowned and Patra Group has progressed to become one of the industry’s major suppliers specialising in custom stainless steel fabrication, commercial refrigeration and kitchen manufacturers within Australia.
Over the years Patra Group has had the honour of collaborating on various project with expert construction companies, award winning builders, designers, architects and foodservice consultants resulting in the coordination and quality of workmanship that reflects the dedication of all the involved.
“Sydney Swans HQ was one of these proud project collaborations. It was great to see this landmark building be transformed step by step from it former use into the vision that it now functions. We feel extremely privileged that our company took part in the project transformation” said Managing Director, Nectar Kounavis.
Patra Group was involved in the project for 12 months, commencing in December 2021 the team worked closely and completed their brief in December 2022.
“Like everywhere, COVID caused unexpected challenges such as freight delays, staffing shortages and price increases on all materials,” said Nectar. “We had to adjust with each hurdle as it arose and communication with FDC was key.”
Founder of Patra Group, George Kounavis has 45 years experience in the commercial refrigeration and stainless steel fabrication Industry.
Over the years George has overseen many major and minor projects locally, interstate and overseas. He has passed on this knowledge and expertise to his sons Nectar and Chris, daughter Tass and grandson Peter.
As Nectar has embraced the wisdom of his father and incorporated modern technologies
together with current industry standards, Patra Group is able to build efficient and durable products that are reliable to both the Chef and site owners. Being able to evolve with new design concepts keeps customers at the forefront of modern trends.
“Because you deal directly with the owners of the company from the beginning you can be assured in knowing that we personally take responsibility and pride in the successful completion of your project and endeavour to satisfy the client with the final results,” said Nectar.
Patra Group specialises in custom manufactured equipment to suit the needs and space of every customer. Their inhouse services include:
• Detailed design and drafting plans
• Professional consultation advice
• Layout ideas on commercial kitchen for efficiently workspace with the highest quality products
• Bespoke metal fabrication
• Commercial refrigeration and air conditioning servicing
• Project estimations and management
“As an independent family business we believe that it’s important for friendly personal service and understanding, your questions and concerns are answered immediately,” said Nectar.
Patra Group strives to achieve completion of high standards, quality products and total customer satisfaction of every project that it commits to.
For more information contact Patra Group, phone 02 9597 6788, email info@patragroup. com.au, website www.patragroup.com.au
Colbros Electrical Contracting were responsible for all of the lighting and electrical needs at the new Sydney Swans HQ.
The company’s brief included the electrical design, new substation, solar, lighting control, communications, lightning protection and MATV (Foxtel and free-to-air).
“Sydney Swans & FDC were a great client to work with, however the nature of the architectural style made this job really challenging,” said Project Manager, Stuart Keeble. “The architect and FDC was excellent at working through the challenges, the final finish of the project as a whole was fantastic.”
Colbros Electrical is a highly respected and well known commercial electrical contracting company that specialise in the electrical design and delivery of hospital, health, aged care, hospitality and general commercial sector projects.
“At Colbros we have the ability to design, install and certify all aspects of the electrical systems of your project,” said Stuart. “Our aim is to provide a quality service with an attitude to solving and overcoming problems that exceed our client’s satisfaction.”
Colbros provides a complete range of electrical services including full design and installation through to final testing and certification. At the core of the business is an experienced office team which is split into procurement and delivery.
“We pride ourselves on our dedicated team ranging from project designers, electrical estimators, project managers, electrical trades people and electrical apprentices who are extremely experienced in the electrical construction of commercial projects,” said Stuart.
Established in 1994 by brothers Peter and Paul Cole, Colbros has earned a reputation for delivering a competitive price and high standard of workmanship on all their projects. It is this quality delivery that maintains Colbros as a forerunner in the electrical industry.
For more information contact Colbros Electrical Contracting, Unit 21/8 Campbell Street, Artarmon NSW 2064, phone 02 9966 9144, email petercole@colbros.com.au, website www.colbros.com.au
ARCHITECT : DWA Architects
CONSTRUCTION VALUE : $ 73 million
TYPE : Mixed use Residential
The Hoxton is a stunning mixed use development of over 300 apartments across three buildings and features modern open plan kitchens, bathrooms with a hint of hotel luxury. Expansive windows and rooftop gardens set the tone for this vibrant development.
As one of Sydney’s largest and leading private groups, working within development, construction, finance and property management, ALAND pride themselves on ensuring their customers have a property asset that will not only flourish, but will also stand the test of time.
ALAND utilised their wealth of expertise and extensive experience on The Hoxton, a collection of 303 luxury apartments, all with superior finishes and meticulous detail, located in the heart of Liverpool, New South Wales.
ALAND CEO, George Tadrosse said their involvement commenced from early due diligence, and continued through to acquisition, finance, sales and marketing, construction, settlement and after care.
“We acquired the site in November 2020 and did a complete overhaul, via a DA modification, to provide more amenity and reduce the number of apartments. We then commenced construction of the project in February 2021, topped out in April 2022 and successfully completed the build in September 2022,” George said.
“Believe it or not, the site went through multiple owners and lay dormant for 17 years. The fact that we were able to come in and transform it into something incredible and valuable to Liverpool made The Hoxton a special project indeed,” he said. Committed to delivering the best outcome, never compromising on quality and always maintaining high standards, the team from ALAND were dedicated to ensuring The Hoxton was yet again another ‘Next Level Living’ project, despite the numerous challenges they faced throughout the development and construction stages.”
“During the peak of the pandemic, all our major construction projects were in the LGA’s affected by the lockdowns. Our team
developed increased safety measures to enable all of our sites to stay open, which in turn, enabled our valued suppliers and contractors to remain operational,” George said.
ALAND Project Manager, Charbel Nakhle said there were a number of additional issues as a result of not only the pandemic, but also the site’s location. “Supplies delayed from overseas impacted the availability and cost of materials during the build. The lifts and main switchboards were held up and the cost of steel for reinforcement went up by over 70%,” Charbel said.
“We were also restricted on how to build because of the site’s location on two main roads. As a result, there were a lot of infrastructure restrictions, so we needed to regularly liaise with Sydney Water and Transport. Another external challenge was the introduction of the Design Practitioner Act during the middle of the build. Half of the design consultants needed to redraw the project under the new act, which put pressure on the construction timeline,” he said.
However, despite the obstacles, ALAND maintained strong relationships with their contractors and suppliers and due to this goodwill, managed to navigate the challenging circumstances in both a professional and collaborative manner.
“Through this time, we learned to adapt and overcome. The team spent a lot of time on procurement and looking at new opportunities, without compromising on the quality of the build,” said George.
“Typically, in construction we plan months, sometimes even years ahead, but through the pandemic period, every day was different. The plan we woke up with was usually outdated by lunch, but we just kept innovating and adapting. Liverpool has massive plans for the future, and projects like this, in combination with the adjacent developments, are starting to build a strong foundation for the growing city, one we are proud to be a part of,” he said.
Comprising of nine divisions, ranging from development to after care, ALAND communicate more effectively, improve efficiency and maintain their high standards of design and construction throughout the entire development process. In addition, with their experienced inhouse team of architects, designers and project managers, as well as their 20 years of industry expertise, ALAND ensure a successful project delivery every time.
For more information contact ALAND, Suite 38B, 2 Park Street, Sydney NSW 2000, phone 02 8076 5510, website aland.com.au
With over 25 years of trade experience, GM Electrical Services continue to bring their highly skilled and technical expertise to the forefront of the electrical industry. With a strong management team, all of whom are motivated and dedicated to any project they are involved on, GM Electrical Services go above and beyond, providing excellent customer service and outstanding electrical results every time.
With duties specific to the network, wiring and maintenance of electrical services to both residential and commercial developments, GM Electrical Services has a primary outlay for an otherwise complex, sophisticated specialty. As a result, no project is too challenging, large or small and the highly organised team always deliver within budget and required timeframes.
Given their wealth of industry experience, GM Electrical Services were also involved on the cutting-edge residential development, The Hoxton. Located in the heart of the thriving Liverpool metropolis, in New South Wales, The Hoxton is a collection of new apartments, across three buildings, all with meticulous attention to detail and the use of superior materials and finishes. From a modern open-plan kitchen that grants easy access to the dining area, to bedrooms featuring expansive windows bursting with light, every space has been thoughtfully crafted to combine quality with liveability.
Thoughtfully designed to fit in with current lifestyle needs and demands residents, The Hoxton delivers practical flexibly for the future. Commencing works in early 2021, and working on the project for 18 months, Georges El Ghoussain, Director of GM Electrical Services, said that his team were responsible for an extensive range of electrical services across the development.
“Throughout our involvement on The Hoxton, we first and foremost, provided a reliable and professional team of electrical contractors onsite. In addition, we were responsible for running cables, as well as the installation of all of the electrical switchboards, the main switchboards, T-off boxes, metre panels, distribution boards and sub-boards,” Georges said.
“We also delivered a vast array of wiring services. For example, we wired a range of unit interiors and installed cable trays, powerpoint switches and light fittings throughout the apartment buildings,” he said.
As a result of their experience, in regards to working on highrise building projects, Georges said the project team from GM Electrical Services faced no challenges or obstacles along the way, due to their ongoing collaboration and communication amongst themselves and with the main developer, ALAND.
“The entire delivery of our extensive services to The Hoxton project ran smoothly from start to finish. This was not only because of our experienced and highly skilled team, but also because ALAND have fantastic management experience given the plethora of projects they have worked on over the years,” Georges said.
“This, alongside their knowledgable site foreman and project managers, meant we could get the job done in a timely and professional manner. Overall, we really enjoyed working on The Hoxton, not only is it a stunning residence, right in the heart of bustling Liverpool, but it was also a pleasure to work with great developers and builders.”
Offering a full range of electrical services for commercial, industrial, and residential properties, including upgrades, repairs, maintenance, and installations, GM Electrical Services are the knowledgeable and skilled electricians and technicians you can rely on to get the job done. Committed to ensuring client satisfaction every time, GM Electrical Services take pride in delivering cost-effective solutions, regardless of the size or scope of the project at hand.
For more information contact GM Electrical Services, Unit 7/51 Nelson Road, Yennora NSW 2161, phone 0408 113 695, email mary@gmelectricalservices.com.au
With a close-knit and dedicated team of tilers, Auscorp Tiling Services provide a high quality service and professional finish across every job.
With over 10 years of industry expertise, as well as an extensive portfolio that incorporates a range of both residential and commercial projects around Sydney, the team at Auscorp are committed to producing accurate tiling results, from high end homes to high density apartment buildings and commercial projects.
Recently, Auscorp Tiling Services were also engaged to provide their tiling services to The Hoxton residential development in Liverpool. With a bustling town centre and leafy, neighbouring streets, The Hoxton offers 303 luxury apartments, incorporating superior materials and finishes throughout. Working alongside the main developer, ALAND, Auscorp Tiling Services provided a range of extensive tiling works.
Responsible for the supply and installation of tiles located in the living areas, bathrooms and balconies of the apartments. Auscorp Tiling Services ensured their finished product was in line with the cutting-edge design and luxurious feel of The Hoxton apartments.
In addition, they also provided all aspects of tiling to the ground floor lobby areas, creating a stunning looking entry for residents. “Given our long-term experience in dealing with large scale projects, the team were able to carry out their responsibilities in a seamless manner, without any supply or installation issues,” said Chris Vasiliades, Director of Auscorp Tiling Services.
“Our ability to scale complex tiling services, as well as our open communication with ALAND, meant that we were able to provide exactly what was required for The Hoxton in a time and cost efficient manner,” said Vasiliades.
“The team at Auscorp Tiling Services have the project management know-how and dedication to ensure that every time we do a job, or provide our service, regardless of whether it entails one or 20 tilers, we do it once and we do it right.”
“As we always work closely together as a team, we didn’t face any challenges or obstacles, showcasing our expertise and operational expertise to ALAND. We also partnered with Screedpro on this project to have all our screed pumped, which although was a mammoth task, we were able to complete,” he said.
With their extensive industry experience, as well as a reliable and knowledgable team of licensed tilers, Auscorp Tiling Services take the time to fully understand the needs and requirements of a project, working directly with their clients to meet the exact tiling specifications. With an extensive network of suppliers, Auscorp Tiling Services are also able to source tiles at competitive prices, no matter the size of the project.
However, Auscorp Tiling Services are more than just tilers, they also offer waterproofing services, a critical component of most tiling ‘wet area’ work. Understanding the importance of waterproofing, to ensure water doesn’t penetrate through tiles, creating havoc on walls and causing mould and other hazardous issues, Auscorp Tiling Services are the leading professionals at preparing structures and surfaces for maximum water protection.
In addition, Auscorp Tiling Services take pride in providing optimal efficiency when working on large scale projects, combining their astute communication skills with a committed team, who strive to deliver projects within timeframes and budgets.
Also working on a number of other projects between Liverpool, Schofields and Parramatta, such as the Campbelltown Catholic Club,
For more information contact Auscorp Tiling Services, PO Box 238, Earlwood NSW 2206, phone 02 9730 0209, email info@auscorp.net.au, website www.auscorptiling.net.au
The Hoxton’s beautifully appointed spaces used a range of high quality, and distinctive products to create the luxury of easy living. SHOWTILE, an importer and supplier of large and small scale projects, offer the latest products of ceramic, porcelain and natural stone, perfect for creating unique tile concepts for walls, floors, facades and terraces.
SHOWTILE brought their unique eye for design and aesthetically pleasing tiles to the forefront, ensuring a polished and seamless finish to The Hoxton’s 303 apartments. For the apartments’ main areas, a timber look tile was supplied and within the bathrooms, a white gloss tile was selected.
“ALAND wanted the best looking product, at the best price possible, something we pride ourselves on being able to do,” said Ken Song, Director of SHOWTILE. “We were able to provide a new, customised design that was in sync with their vision, using our cutting-edge technology and stand-out products. This is why we had such a great partnership while working on the Hoxton,”
SHOWTILE also offer their clients a Virtual Theatre experience to see spaces come to life during the tile selection process. Using
a virtual headset, clients select a preferred design and can see how the tiles interact with each other before a single tile is placed onsite. This technology provides greater flexibility in creating unique spaces suited architectural designs and beautiful tiles.
Operating throughout COVID required some careful planning to keep disruptions to a minimum where possible. SHOWTILES’ large warehouse ensured that the supply of tiles for the project was not a problem and stock was on hand when needed. Ken said working with such an organised developer made the overall experience run smoothly
For more information contact SHOWTILE, 65 Canterbury Road, Bankstown NSW 2200, phone 02 9709 5836, email sales@showtile.com.au, website www.showtile.com.au
With a focus on residential, commercial and industrial design and engineering solutions, Loka Consulting Engineers provide feasible solutions and cost-effective outcomes on every project. Servicing a broad variety of clients, ranging from government, commercial and industrial, as well as developers, contractors and architects, Loka Consulting Engineers aim to improve the physical or social infrastructure within communities, through their highly regarded and professional services.
With over 22 years expertise and a small, yet astute and highly experienced team, Loka Consulting Engineers provide advice and solutions regarding stormwater design, civil design, access and waste management reports, livable assessments, water sensitivity analysis, BASIX and NatHERS assessments, flood studies and risk management reports, construction management plans and reports, and traffic impact studies. Given their comprehensive range of engineering services, they were also recently appointed to carry out a number of assessments for The Hoxton project.
Touted as a luxurious collective of high quality apartments, The Hoxton offers an idyllic lifestyle and the perfect balance for work and life. “Our renowned reputation and knowledge of social
infrastructure needs, meant we were able to carry out their extensive involvement on the project in both a timely and professional manner,” said Director of Loka Consulting Engineers, Nermein Loka.
“Throughout our involvement, our team were engaged to assess the adequacy of the proposed car parking provisions for the proposed development, estimate and assess the future traffic generation of proposed development and prepare traffic and parking assessment report. Despite a few challenges along the way, we were able to accommodate the design changes that were constantly added throughout the process, ensuring council and engineering requirements regarding The Hoxton residences, were met,” she said.
As a result, Loka Consulting Engineers ensured a smooth running construction and design process and delivered the required engineering solutions for The Hoxton project in a cost effective and outstanding manner.
For more information contact Loka Consulting Engineers, 14A, 8 Avenue of the Americas, Newington NSW 2127, phone 02 8065 9689, email info@Lceng.com.au, website www.Lceng.com.au
Sydney Ultra Seal provided the internal and external joint sealing for over 300 apartments in all three buildings for The Hoxton development.
This included siliconing all bathroom corner junctions from floor to ceiling, siliconing between the tiles and skirting in all living rooms, bedrooms and kitchen floors, kitchen splashbacks and siliconed around the windows to Gyprock.
Externally, Sydney Ultra Seal siliconed all balcony tile perimeters, they used MS polymer for the precasts and render joints along with the podium walls joints, floor tiles and pebblecrete. In the basement they fire rated the block wall joints and used MS polymer for the concrete floor joints.
“We’ve been on this job for about one year,” said Sydney Ultra Seal Director, Charbel Ibrahim. “My team has around 20 years experience on the job.”
“We generally come in after the initial clean and before the final clean,” said Charbel. “On jobs of this magnitude there are always hurdles to overcome but nothing we can’t handle i.e., working around other trades.”
Charbel has worked with ALAND on various projects for around 14 years and has developed a great working relationship with them. Sydney Ultra Seal have an impressive record in the industry, with all their jobs coming from word-of-mouth and regular clients.
Sydney Ultra Seal also uses the Tradeseal brand of silicone which has a range of over 15 colours available. “We use the Tradeseal silicones and MS polymer as our main brands, we also outsource other brands if specified by our clients,” explained Charbel.
For more information contact Sydney Ultra Seal, 55 Speers Road, North Rocks NSW 2151, phone 0421 531 181, email sydneyultraseal@ yahoo.com.au
D&L Interior Lining is a professional plastering and cladding team with more than 20 years of industry experience. Specialising in the installation of plasterboard, Hebel, metal framing, ceiling, aluminum cladding, D&L Interior Lining pride themselves on generating cost effective and quality solutions for every project they work on.
Able to adapt their construction method to suit particular projects and client needs, D&L Interior Lining were recently engaged on the prestigious Hoxton project in Sydney. Consisting of a collection of glamorous new apartments, with an emphasis on luxurious finishings and superior materials, it was no surprise that D&L Interior Linings were commissioned to carry out the interior plastering, as well as the external cladding on the buildings.
“Throughout our involvement on The Hoxton, we used both new products and professional attitudes on the project, showcasing our extensive wealth of knowledge in regards to plastering and cladding,” said Jack Chen, Owner and General Manager of D&L Interior Lining.
“Whilst working on The Hoxton, we were responsible for providing not only the interior plastering, but also the internal and external Hebel, Alphapanel wall and the ALPOLIC NC feature cladding.”
“For the first time ever to be used onsite, Alphapanel, a type of concrete panel, was used to replace part of the Hebel. In doing so, we also used a new installation methodology to ensure a sleek and professional looking finish,” said Jack.
Given their long standing reputation within the industry, the job was completed ahead of schedule and within budget, cementing their experience and ability to diversify and successfully complete large scale projects.
Currently working on Schofields Garden (ALAND), another luxurious collective of apartments, D&L Interior Lining continue to deliver. With their wealth of experience, it is little wonder they are at the forefront of the interior plastering industry.
For more information contact D&L Interior Lining, 46/11-21 Underwood Road, Homebush NSW 2140, phone 0451 580 288, email jjjil2162@yahoo.com, website www.dnlinteriorlining.com.au
CLIENT : Poly Developments & Holdings
MAIN CONSTRUCTION COMPANY : BESIX Watpac
ARCHITECT : Grimshaw
STRUCTURAL ENGINEER : WSP
TYPE : Commercial
Poly Centre is an A-grade office tower comprising over 17,000m2 of innovative work spaces with dual floor village configurations, bespoke fitouts, state-of-the-art facilities, open communal spaces, unique outdoor areas, and over 500m2 of George Street retail.
Poly Centre is a 25-storey commercial tower located at 210 George Street in the heart of Sydney. With over 17,500m2 of commercial and retail space, this 110m tall building will provide value for both employees and the public. BESIX Watpac undertook ECI and Design and Construction of Poly Centre.
“The ECI commenced in 2018 and demolition began in 2019 with construction underway in 2020,” explained Project Manager, Tim Hensel. “Construction was undertaken through the thick of COVID, light rail completion, bush fires and most recently the La Niña events.”
“The unique design and prime location also provided numerous challenges for the construction team over the project.”
Designed by international architecture firm Grimshaw, Poly Centre’s solid, sculpted core sits on the eastern boundary of the site, while west facing George Street floorplate is expressed as a continuous glazed vertical element spanning the length of the tower.
The building’s design aims to synthesise sustainability and flexibility by maximising natural light and utilising environmentally conscious and efficient measures to minimise running and maintenance costs. Architectural and structural flexibility will allow tenants to modify their workplace layouts depending on their needs.
Poly Centre’s evolutionary Air Village design – dual floor connected occupancies that have double height spaces – has already received international acclaim, winning the 2020 MIPIM Architectural Review’s Future Project Award for office and office-led development.
“The Air Villages incorporating double height precast columns, fascia and GRC pillars are the standout element for the project and the final product looks fantastic when walking along George Street,” Tim explained.
“There are about 550 precast panels, each weighing up to 16 tonne and over 1,300 curtain wall panels in this structure and the complex façade with curves and GRC elements required careful design and construction coordination to achieve the detail we have today.”
Poly Centre forms part of the transformation of Sydney’s Circular Quay precinct alongside brand new ferry wharves, light rail and a raft of commercial redevelopment. To conform with the high standard of quality created by its neighbouring structures, the building utilises materials and finishes and identifies as a PCA A-Grade building.
It’s the fourth iconic building constructed by BESIX Watpac in the George Street precinct. “In 2009 we completed 275 George Street, a 32-Level commercial office tower for Charter Hall, then in 2015 we started work on 333 George Street. In 2018 we completed the award-winning York & George, 38-storey mixed use high rise for TAP Sydney Pty Ltd,” NSW General Manager, Peter Furlong said.
BESIX Watpac has been part of Australia’s contracting fabric for over four decades and made its mark in New South Wales with major projects in the commercial and residential, transport, health and education sectors including the Museum of Contemporary Art, Forensic Medicine and Coroner’s Court, Hornsby Ku-ring-gai Hospital Stage 2 Redevelopment, and Sydney Metro Barangaroo Station.
Across the country the company has built several of Australia’s leading stadiums, such as the Suncorp and Gabba Stadiums, Queensland and Victoria’s schools PPP packages and delivered more than 40 hospitals across the east coast.
“We are a leading Australian multidisciplinary construction company backed by a century of global expertise and financial strength,” said Peter. “A wholly owned subsidiary of the award-winning international contractor BESIX Group, we specialise in complex construction across all sectors. Our point of difference is the way we collaborate with architects, consultants and suppliers to bring our client’s vision to life. Importantly, this means assembling the best team to manage and guide the design development and achieve the best value project.”
BESIX Watpac’s experienced design managers, inhouse engineering team and construction specialists, work side-by-side with their partners to challenge the constructability of a project. BESIX Watpac has more than 150 inhouse engineers operating from three global hubs in Brisbane, Dubai and Brussels.
“Our specialists are embedded in project teams to interrogate the design; de-risking projects, maximising value, and delivering certainty,” Peter added. “We are members of the Infrastructure Sustainability Council (ISC) and the United Nations Global Compact, and we design and build projects that achieve world class ratings.”
For more information contact BESIX Watpac, Level 24, 44 Market Street, Sydney NSW 2000, phone 02 8741 7400, email receptionbne@ watpac.com.au, website besixwatpac.com.au
New Edge Group were engaged by BESIX Watpac under a D&C role for Poly Centre, where New Edge developed the design from a very preliminary stage through to completion.
New Edge undertook the mechanical air conditioning and ventilation, Building Management System (BMS), and BIM management and coordination for the project.
“There were a number of sustainable initiatives for the mechanical services of the project,” said New Edge Pre-Construction Director, Shannon Hanly-Jones. “These included high efficiency water cooled chillers, very low temperature air supply systems, electronically commuted fans and energy efficient control strategies to optimise the buildings low turn down efficiency.”
The small building footprint of Poly Centre meant plant rooms and risers were tight and presented a number of coordination difficulties. In addition to this the floor-tofloor heights within the plant rooms were very limited.
“Locating air intakes due to the site limitations was challenging as the building was bounded on all sides by neighbouring properties,” said Shannon.
“Extensive work within the digital built space was required to coordinate these extremely tight plant rooms. Close collaboration with our site team was required to prepare detailed methodologies to enable the construction of these congested areas,” said Shannon
New Edge developed a range of innovative solutions to ensure the success of their brief on this project including prefabricated riser frames that were incorporated into the concrete pours, reducing both construction time and risks associated with having open risers during construction. Due to limited roof access and space for rigging, New Edge prefabricated the modules for rooftop installation.
“The top commercial floor of the building is a double height space where the architectural intent was to expose the curved structural roof structure,” said Shannon.
“As a result the mechanical systems serving this floor were distributed via an underfloor
system. Underfloor systems must be served by warmer air than conventional mechanical systems and overcoming this issue created a unique mechanical system for this floor.”
New Edge Group is a family-owned Australian business specialising in electrical and mechanical design and construct contracting and is supported by their specialist 24/7 maintenance servicing division.
The company views the key to their success is in being selective in the types of projects they undertake, and the clients that they want to form trusted partner relationships with. New Edge Group takes a considered approach to their work and provides their employees with gratifying projects to work on where they can feel empowered.
“Clients feel assured they are working with a dedicated, amiable and competent team that is highly energetic, passionate and takes pride in everything that we do. A team that takes safety seriously, is innovative, and enjoys seeing the design intent come to fruition for each project,” said New South Wales State Manager, Danny Canal.
New Edge Group’s solutions have contributed to several award winning projects which is testimony to their project execution, communication and teamwork. “Setting the Standard – Your Vision. Our Future” is the company philosophy forged through very strong relationships with clients, suppliers and associated professionals. Today, New Edge are the leading bespoke electrical and mechanical contractors of choice.
New Edge is currently close to completing another highrise tower in Macquarie Park, 5.5 Star NABERS, 5 Star Greenstar and WELL Platinum rated. Currently in progress is the Rosebery Engine Yards, a 15,000m2 repurposing of a heritage asset to a new commercial building incorporating 5 Star Greenstar, 5 Star NABERS, expose services and double height spaces. Along with numerous projects in the Health, Mission Critical & Industrial sectors.
For more information contact New Edge Group, 5/24 Daniel Street, Wetherill Park NSW 2164, phone 02 9725 5555 email info@newedgegroup.com.au, website www.newedgegroup.com.au
Below Dynamite Electrical Services were contracted to provide all of the base electrical works at the Poly Centre.
Dynamite Electrical Services were contracted to provide all base electrical works including switchboards, submains, lighting and emergency lighting and power installation at the Poly Center.
“The largest issue Dynamite Electrical faced was the after effects of the COVID pandemic in terms of procurement,” said Program Manager, Reuben Hartshorne.
“Due to most of the buildings’ lights running on the DALI lighting control system, almost all light procurement was pushed back by months due to chip shortages.”Additionally, Dynamite Electrical managed subcontractors for security, DAS, fibre backbone and the generator.
Established in 1992, Dynamite Electrical is a medium sized Electrical Contractor whose core strengths lie in the successful delivery of electrical, security and communications systems for medium to large residential and commercial projects, most of which are for top tier clients. The company prides itself on returning value to their customers as well as their own business, through transparent, professional and timely communication and correspondence.
With over 30 years in the construction industry Dynamite Electrical have completed a number of landmark projects and earned a reputation of consistently completing all projects on time and budget.
Dynamite Electrical is currently finishing 1EPD located at 1 Eden Park Drive, Macquarie Park which is a seven-storey cutting-edge modern commercial building for Watpac. Dynamite is also working on NINE Willoughby for Mirvac.
UTJ Interiors took on a range of work for the Poly Centre project including the reception desk, reception feature wall, steel inserts to the stone wall, subframe for the ceiling, and the end-of-trip vanity units.
“Poly Centre boasts double height ceilings throughout. The lobby area has a 7m ceiling height,” said Managing Director, Paul Van de Haar. “UTJ and our subcontractor Twisted Metalcraft provided floor to ceiling Granex Bronze Mirror Stainless Steel in a matt finish, V-Grooved and folded to the feature wall. Twisted made a faultless contribution on this project”.
“To the lift lobby sandstone wall, UTJ installed the Folded Bronze Wall joints. To the ceiling, we installed the subframe for the Newmat stretched fabric ceiling. The reception desk substrate is marine ply and had to be precision built to support the stone cladding.” UTJ also built the vanity units in the end-of-trip facilities (excluding stone) using a Laminex Natural Walnut.
“Poly Centre is the type of job where UTJ really shows its versatility and capability. It was tricky, precise work requiring a lot of specialist experience. The architect Woods Bagot dreamt up this incredible design, Watpac built it and UTJ Interiors provided the finish.
We’re really proud of our involvement” said Operations Manager, Michael O’Neill. “This job included a lot of high, potentially dangerous work. We take the safety of our guys very seriously and we’re proud also of our safety record”.
“UTJ turned 70 years old last year. My grandfather started the business, my father and I took it to the next level, and these days we’re doing Sydney’s most prestigious commercial work,” said Paul. “We have a factory full of experienced staff and super high-tech machinery and we have a site crew that get the job done every time, on time. Our factory and site crews work together seamlessly with fantastic teamwork these days.
UTJ Interiors is one of Australia’s premier manufacturers of custom joinery and detailed veneering. Specialising in hotels, universities, schools and commercial facilities. Recent projects include Crown Casino, UTS Science Building, Sofitel Hotel Darling Harbour. Current projects include Sandstones Hotel – Luxury 6 Star hotel in Bridge Street Sydney and the Reserve Bank redevelopment in Martin Place Sydney.
For more information contact UTJ Interiors, 234 Berkeley Road, Unanderra NSW 2526, p. 02 4271 5522, www.utjinteriors.com.au
Ventura Residences is an impressive collection of 83 thoughtfully designed one, two, and three bedroom luxury apartments with spacious layouts, premium finishes, open-plan kitchens, timeless bathrooms and sweeping views.
Ventura Residences is an impressive collection of 83 spacious apartments in Arncliffe, Sydney that has been meticulously designed to deliver a high standard of living with premium finishes and a range of lifestyle attractions.
“TQM handled this project from acquisition, through to the demolition of the existing structure, excavation of a three-level underground basement, and build of the 10-storey structure,” said Project Manager, Stephen Alphonse.
Among the many features, the highlights of this project are:
• Full precast structure
• High level internal ceilings
• Automated smart system units
• Motorised blinds
• Parisi spec tapware and accessories
• Stone benchtops and splashbacks
• Smeg appliances
• Large balcony space
• Open communal space on the ground floor
• Open Communal Space on rooftop with bathroom and BBQ facilities
“Infused with the latest innovations in engineering processes and precast concrete construction, each apartment boasts premium finishes and fixtures that exude understated elegance and unrivalled quality,” said Stephen.
The curved precast design was a first for TQM. Their inhouse structural engineers spent a lot of time with their architects in order to deliver a flawless looking façade design which met the design intent perfectly.
“The deep three-level excavation in sandstone was a challenge,” said Stehpen. “By appointing a specialist early works contractor the excavation was done in a time efficient and safe way
“TQM had a strong presence already in the Bayside Region,” said Stephen. “However, this project took the next step in terms of design execution, intelligent engineering and overall quality detail which all purchasers will appreciate for many years to come.”
Established in 1999 by brothers Maroun and Mark Taouk, TQM Design and Construct has
a well earned, national reputation amongst clients and peers for delivering exceptional residential construction projects, on time and on budget. The strong family bond between them has allowed the company to thrive as their personal involvement is always at the forefront, instilling this commitment as a company ideology.
A strong, multi-disciplinary engineering design company, TQM’s services span the breadth of the construction industry. Including engineering, building and surveying, through to regulatory advice and certification.
“Our highly integrated design process and multi-disciplinary approach maximises coordination between disciplines. This not only increases our efficiency, but also speed and quality,” said Managing Director, Maroun Taouk.
From humble beginnings working across small to medium sized residential projects, TQM has grown to become a major player in the construction market, building multiple highrise residential developments across Sydney. Over this time, TQM has always provided a high level of excellence, never losing touch with the core values that drive the business.
As a family owned, Australian business TQM has a strong focus on loyalty and service. The team has been able to build a formidable portfolio which reflects their experience and ability. Over the years, TQM has established long lasting relationships with all their clients. And, it’s these relationships that reflect the true commitment of loyalty that TQM values. Through this ethos TQM will continue to flourish and adapt to future opportunities.
This outstanding track record has been built upon years of research, experience and innovation. TQM continually strives for executional excellence in design and construction at every step of the project.
For more information contact TQM Design & Construct, Level 10, 6 Mount Olympus Boulevard, Wolli Creek NSW 2205, phone 02 9556 1046, email info@tqmdc.com.au, website www.tqmdc.com.au
Below Abseil & Precast Solutions provided the precast installation and corking for the whole Ventura Residences project.
Abseil & Precast Solutions specialise in everything to do with highrise projects, which made them the perfect team for the Ventura Residences project.
Their brief included the precast installation and corking, all of the internal corking, installation of the Height Safe Systems including anchor points, step ladders to access the roof and fall arrest systems.
A fall arrest system is safety equipment that protects aerial workers from falling at dangerous heights. When the system senses falling, it arrests the system and prevents the fall.
“We also inspected the entire building using abseiling,” said Abseil & Precast Solutions Director, Matheus Silva. “We inspected all of the joints and looked for cracks or any potential issues with the building including movement.”
The company was onsite for two years with a team of 17.
“The builders made this job very easy,” said Mathues. “There was great communication between all of the trades and everything ran smoothly.”
Scope Joinery Group provided the modern and contemporary design and installation for the kitchens, laundries and storage facilities for all 83 apartments in the Ventura Residences.
Scope Joinery offers expert joinery design, manufacturer and installation services across all joinery sectors. Their state-of-theart manufacturing facility combined with skilled tradesman and project managers deliver high quality joinery projects for their valued clients.
With a history spanning over 50 years and multiple generations, Scope Joinery Group has established itself as a market leader in the joinery supply and install industry. “Combining the strength of a large production facility and the personalised service of a family business, Scope offers a complete solution for any project regardless of scale,” said Managing Director, Mohamad Farhat. “We have a strong focus on quality and integrated management systems which means we deliver on time and on budget, every time.”
Scope joinery offers a specialised inhouse drafting team detailing all aspects of your project from concept to completion. CAD Software offers clients a realistic visual rendering of their joinery design.
Scope’s dedicated project management team ensures a smooth delivery across all aspects of all projects, overseeing every detail from early design and value engineering to completion onsite and after sale service.
“Strong relationships are and have always been the keys to our success,” said Managing Director, Mohamad Farhat. “These partnerships drive us as a business as we work with our clients towards the common goal of achieving an outstanding result for all involved.”
Scope Joinery Group has capabilities that span across multiple sectors and varying scales. With the Industry know-how, attention to detail and strong management systems, Scope Joinery can provide an end-to-end joinery solution for any project.
For more information contact Scope Joinery Group, 4/17 Willfox Street, Condell Park NSW 2200, phone 1300 548 548, email info@ scopejoinerygroup.com.au, website www.scopejoinerygroup.com.au
Aspen Village is an exciting resort style mixed-use precinct with 2,500m2 of commercial space over 2 stages with 622 luxurious bedroom residences, and includes a 2,200m2 rooftop area with indoor-outdoor bar, infinity edge pool, private lounge areas and more with spectacular 360-degree views.
Geocon oversaw the design and construction of the Black Diamond complex and the Aspen Village Project. The project is a mixed-use precinct comprising 622 residential units, ground floor commercial and public car park. On the Level 10 rooftop there is a 2,200m2 entertainment space, fitted out with BBQs, fire pits, a bar and chef’s kitchen, dining facilities and lounge areas, heated pool, sauna and spa.
Geocon commenced work onsite in June 2020, in the wake of bushfires, COVID, industry strikes, material shortages and labour shortages.
“This project has experienced some of the toughest conditions the industry has faced over the past 24 months which has required the project team to work harder to achieve the outcome,” said
Construction Director, Damian Rumball. “Materials had to be changed part way through construction, which led to updating and coordinating hundreds of plans.”
Stage 1 Aspen Village (321 units) was handed over and occupied four months prior to completion of Stage 2 Black Diamond, including a public carpark which required careful planning and preparation to ensure that the construction site could operate and new owners and tenants could enjoy their new space. “The Atrium in the centre of our uniquely triangular shaped Building C spanning 5-levels with a garden located on the ground floor is where we got the name Black
Diamond,” said Damian. “This project has been the largest single development completed in Canberra since Metropol (550 units) and High Society (570 Units), both Geocon projects.”
A particular highlight of the project is the prefabricated stainless steel 24m x 4m swimming pool and spa on Level 10 of Stage 1. The pool was primarily built offsite in Melbourne by Bradford Products, three separate parts were crane lifted onto the rooftop landscape area, welded together and tiled onsite. The process was much faster than building a concrete pool shell onsite and comes with a 25-year warranty.
Practical completion for Aspen Village – Black Diamond Project Stage 1 was August 2022 and Stage 2 December 2022.
Since their origins as a company building small homes and cottages, Geocon has evolved to deliver large scale, mixed use precincts which include both residential and commercial opportunities.
“With experience across multi-unit developments, hotels and hospitality, Geocon’s market share and pipeline of business continues
to grow,” said Damian. “In 2021 we hit record numbers, selling more than 1,200 new homes to people from all corners of the market, be they investors, first home buyers, young families or downsizers.”
Leading the transformation of Canberra into a world class, cosmopolitan capital city, Geocon’s hallmark is architecturally stunning buildings that deliver a new standard of contemporary living. Geocon’s company vision has led them to become the largest residential builder/developer in the nation’s capital, and the sixth biggest Australia wide, according to
the 2022 HIA-COLORBOND® Steel Housing 100 Report. “We partner with the best, to deliver the best. Amongst Geocon’s most trusted collaborators include Fender Katsalidis, Goldman Sachs, Marriott Hotels, Sync Industries and others,” said Damian.
A key contributor to the vibrancy of Geocon’s mixed use precincts are the select hotel and hospitality brands created by Iconic Hotels by Geocon, the hotels division of Geocon, present within the development design.
Setting the bar for real estate development and sales, Geocon builds design led lifestyle precincts which are close to town centres, connected to public transport, schools, universities and retail and dining amenities.
For more information contact Geocon, Level 4, 16-18 Mort Street, Canberra ACT 2601, phone 02 6255 0430, email nick@geocon.com.au, website www.geocon.com.au
Bradford Products designed, fabricated and installed the magnificent heated infinity-edge pool for The Summit – a luxurious outdoor rooftop entertaining area spanning over 2,200m², including private barbeque, bar and dining facilities, landscaped lawns and rooftop fire pits at Aspen Village – Black Diamond.
“Bradford Products are unique in the Australian market as the only suppliers of fully welded, stainless steel pool vessels with a 25 year leak-free guarantee,” said Bradford Products Managing Director, Chris Kenny.
Stainless steel allows incredible versatility when it comes to shape and design. From a cost point of view, it’s very competitive. Depending on the requirements of the site, Bradford’s products can be installed as one complete unit or separate sections, so construction isn’t held up. They’re also cheaper to maintain due to stainless steel’s durable, no-leak nature. Best of all, the pools can be fully tiled, tile trimmed or full stainless steel.
“The Bradford Product’s pool was custom designed and fabricated offsite in our factory in Dandenong South,” said Chris. “It was transported to Aspen Village – Black Diamond for installation and commissioning, saving time and money for the project.”
The state-of-the-art factory is fitted-out with the latest, leading-edge equipment enabling Bradford Products to design and fabricate custom stainless steel pools, spas, therapy pools, resort spa thermal rooms, water features and other custom speciality aquatic vessels to the highest standards.
With a select team of hand picked, qualified designers and engineers, Bradford Products has the experience and creativity to work from conceptual design to manufacture and installation. “Our inhouse team of designers and engineers take great pride in visualising your end product,” said Chris. “Using the latest CAD computer software we create detailed, accurate designs which consider every aspect of your project, including costings, engineering, site access, structural requirements, materials, plumbing, lighting and finish.”
“Our concept drawings provide a realistic picture of how your finished product will look, including exact materials and fixtures
to bring your concept alive and illustrate the required design intent. We make sure you have a finished product that looks sensational and lasts for decades to come.”
Bradford Products have been leading the way in design and manufacture of commercial stainless steel swimming pools, wellness centres, spas and water features since 1982 in the United States. In 2018, Ecogroup joined forces with Bradford Products to bring world-class stainless steel pools to the Australian market.
Both Ecogroup and Bradford Products are family owned companies. With over 70 years combined experience delivering uncompromising service and quality.
The company creates elegant, customdesigned stainless steel swimming pools for resorts, hotels and commercial developments. Bradford pools are less than a third of the weight of a concrete or Gunite™ swimming pool of the same dimensions.
“All of our stainless steel swimming pools are manufactured in Australia and delivered to site as one complete unit or separate parts, depending on the access and limitations of your worksite, which reduces the construction down time,” said Chris.
Bradford Pools are custom designed to be self-supporting and freestanding and are fully-welded to ensure strength and durability. They come with a 25 year stainless steel warranty on the pool shell, meaning no leaks and lower ongoing vessel maintenance.
The service doesn’t stop at installation. Bradford offers ongoing advice about maintenance, water chemistry and filtration to ensure the pool is performing at its best.
“We are working on multiple projects with elevated or rooftop pools in commercial developments,” said Chris. “We manage the entire installation process coordinating with onsite supervisors and relevant trades to ensure everything happens as quickly and smoothly as possible.”
For more information contact Bradford Products, 14 Healey Road, Dandenong South VIC 3175, phone 03 9768 3984 email enquiries@bradfordproducts.com.au, website www.bradfordproducts.com.au
Below Capital Doorworks supplied and installed the roller shutters, roller doors and boom gate for the project.
Capital Doorworks supplied and installed the roller shutters, roller doors and boom gate for the Aspen Village – Black Diamond project.
A locally owned and family operated business, Capital Doorworks has installed and supplied gates and garage doors to the Canberra community for 16 years. Founders, Geoff Didier and Craig Lansom have become two of the most trusted names in the garage door industry with 60 plus years of combined experience.
“At Capital Doorworks, we have established ourselves as a trusted business with the community front and center,” said Craig Lansom. “Our expert team of garage door installers understand our clients’ needs and how important garage doors are for easy access to your home or business.”
Capital Doorworks prioritise communication and partnerships with their clients above all else and assign a project manager to every job for the client to correspond with and take care of all the details.
“We specialise in all garage door and gate installation, repair and maintenance. Our team of expert fitters will be able to help with any
garage door or gate issue and provide a prompt solution,” said Craig. “Our high quality garage doors and gates are fully customisable and can be made to order.”
Their specialist services come at very competitive prices and include gates, roller doors, roller shutters and grilles, tilt doors, panel and sectional doors, side closing doors, rapid auto roller doors, counterweight doors, motors and accessories.
The company services Canberra, Queanbeyan, and surrounds, and all of the team in the Hume and the Mitchell offices are thoroughly trained and have the knowledge to help with any inquiry.
Current projects include Wova, Establishment, The Parks – Red Hill. Capital Doorworks supply’s Roller Shutters and Roller Doors for most of Canberra’s large apartment complexes.
For more information contact Capital Doorworks, 42 Raws Cresent, Hume ACT 2620, phone 02 6260 2252, email accounts@ capitaldoorworks.com.au, website www.capitaldoorworks.com.au
Future Form provided the formwork package, including jump form, screens, prefabricated stairs, columns and beams for the Aspen Village – Black Diamond project.
The team commenced formwork on the project in the middle of 2021 during the COVID pandemic, establishing and implementing the formwork for the bottom floors of the Aspen Village – Black Diamond. Once complete, and the formwork dismantled, the team immediately commenced installing the formwork for the upper floors.
“Although COVID presented the team with obstacles, these did not deter the team from achieving their tasks in a timely manner,” said Future Form’s, Martin Haddad. “As a result of the togetherness and work ethic of the team, the formwork on the upper floors were installed without complication.”
By December 2021 Aspen Village had entered its final stages from a formwork perspective, with the final floors of the village being formed.
Future Form has collectively over 120 years in Formwork experience amongst their management and staff and are committed to providing
the most effective, efficient and best quality solutions the industry can provide. Based in New South Wales and the Australian Capital Territory, the company has been in business for over 20 years as a formwork contractor.
Their expertise is in most types of formwork including, but not limited to, high strutting, jumpform systems and panel systems. Where formwork and concrete are required, no project is too difficult to handle.
“Our commitment to providing the best solutions to our clients and a safe workplace to our employees has seen us successfully deliver projects that have shaped the skyline of Sydney,” said Martin.
Current projects include, MIRVAC projects 55 Pitt Street and Nine, and the Ivanhoe.
For more information contact Future Form, 615 Fifteenth Avenue, Austral NSW 2171, phone 02 8376 6950 email enquiries@futureform. com.au, website www.futureform.com.au
The Keys to Ontime Compliant Projects:
One of the keys to an on-time, on budget project is working ahead of time. This is easier said than done, but Powagroup can help take the headaches out of a project and streamline the process. With the complexities of changing regulations you need the ability to:
One of the keys to an on-time, on budget project is working ahead of time. This is easier said than done, but Powagroup can help take the headaches out of a project and streamline the process. With the complexities of changing regulations you need the ability to:
Select the right product
Select the right product
Have compliant documentation system
Have a cost effective install
Have compliant documentation system Have a cost effective install
Get backup & onsite support
Get backup & onsite support
Have know how for compliant installation
Get agreement with external certifer
Have know how for compliant installation Get agreement with external certifer
Typical areas of building code non-compliance is common or challenging are: Passive fire penetrations and situations, seismic restraint & bracing, Antivibration, structural support and compliant fasteners and fixings.
Typical areas of building code non-compliance is common or challenging are: Passive fire penetrations and situations, seismic restraint & bracing, Antivibration, structural support and compliant fasteners and fixings.
To eliminate or minimise blowout costs, reworking non-compliant work and reducing labour costs, we must be working together ahead of time with our onsite Powagroup project consultants. You will experience real streamlined compliance support solutions or what we call S.C.S.S.
inate or minimise blowout costs, reworking non-compliant work and labour costs, we must be working together ahead of time with our onsite Powagroup project consultants.
You will experience real streamlined compliance support solutions or what we call S.C.S.S.
Powagroup are working with many companies who are rethinking traditional business contracting model, saving huge amounts on labour, decreasing installation times, minimising and almost eliminating safety related incidents by using Powagroup offsite, precut, prefabricated, prepackaged solutions and guidance for your team.
Powagroup are working with many companies who are rethinking traditional business contracting model, saving huge amounts on labour, decreasing installation times, minimising and almost eliminating safety related incidents by using Powagroup offsite, precut, prefabricated, prepackaged solutions and guidance for your team.
Starting back in 2004, Powagroup has been working with builders and leading contractors in Plumbing, HVAC & Electrical trades with a focus on Passive Fire. Powagroup focuses on compliant products that fix, support, hang, fire-rate, mount and insulate all the services that they install mainly in highrise & commercial applications like the Aspen Village Project by Geocon we supplied to & worked with.
Starting back in 2004, Powagroup has been working with builders and leading contractors in Plumbing, HVAC & Electrical trades with a focus on Passive Fire. Powagroup focuses on compliant products that fix, support, hang, fire-rate, mount and insulate all the services that they install mainly in highrise & commercial applications like the Aspen Village Project by Geocon we supplied to & worked with.
Façade Industries’ scope of works for the Aspen Village – Black Diamond project included façade design, value management services, FP1.4, FV1 and DtS 3rd party certification, installation management and advice, onsite water testing and diagnostics, shop drawing and engineering reviews and water proofing review and advice.
Working with the Geocon’s design team on the weatherproofing principals for the external envelope of the project, Façade Industries produced the Performance Based Design Brief, being the document that set out the methodology for the Performance Solution Report in accordance with FP1.4, including mitigation strategies for condensation management.
During the construction phase Façade Industries carried out 16 AAMA501.2-15 Field Water test to ratify the design and installation of the primary and secondary windows and external calling of all four buildings supplied and installed by ABS Façade (ACT) Pty Ltd.
The testing was a straightforward process, which had as much to do with Geocon’s the overall management of the project and quality of installation of the façade.
“Geocon is great to work with,” said Tony. “They have a core set of consultants and subcontractors who know what is required of them. It’s really refreshing to work with such a great team.”
Established in 1989, Façade Industries has developed as a unique façade consultancy firm with a diverse portfolio of clients and projects that includes some of the most creative architects, developers and builders both nationally and internationally.
“Our wealth of knowledge in the areas of our expertise can be integrated to allow seamless synergy to create buildings that are more relevant to the spaces we work, live and play,” said Tony.
“We have an experienced team of designers and engineers, providing a pragmatic approach in resolving design related matters, ensuring the design of a project isn’t compromised and in partnership with our clients form a holistic approach to the delivery phase of a project.”
For more information contact Façade Industries, Suite 17, C307, Level 3 Eastland Shopping Centre, 175 Maroondah Highway, Ringwood VIC 3134, email info@facadeindustries.com, website www.facadeindustries.com
The redevelopment of South Australia’s home of elite football will provide significantly improved playing and training environments for the 2023 FIFA Women’s World Cup as well as an impressive venue to host Adelaide United A-League Men’s and Women’s football matches.
Coopers Stadium has undergone a major $53 million upgrade to improve facilities, services and the match-day experience for all Stadium users. The home of football in South Australia, Coopers Stadium is a world-class multi-use facility located just five minutes from central Adelaide. Hansen Yuncken are the project managers who oversaw the refurbishment and construction.
The Coopers Stadium Upgrade included increased spectator shade/rain cover, improved match-day experience, refurbished patron facilities, improved disabled access, improved player facilities, including new female friendly change room facilities, pitch replacement, new media and event operation facilities, improved corporate facilities, and environmentally friendly operational enhancements.
“The project was delivered in two stages,” said Project Manager, George Doudakliev. “We converted the existing two change rooms into four to enable double headers at the Stadium, including women’s
matches. The first stage also included the refurbishment of the food and beverage outlets and the original corporate box.
“The second stage involved building a new canopy and corporate box for 250 people complete with kitchen and bathrooms at the eastern end,” said George. “We also put in new light towers, refurbished two lifts and added three new lifts, new turnstyles imported from the USA, VIP building and media room.”
Hansen Yuncken commenced work in March 2021 and the project has clocked over 150,000 labour hours. “We inducted over 1,300 workers onto the site and on average there were 80-120 workers onsite every day,” said George.
One of the biggest challenges Hansen Yuncken faced was upgrading the infrastructure. “It was quite dilapidated,” said George. “There was a lot of work to be done and a lot of planning. But we had great contractors, especially the electrical contractors, who have done
a fantastic job. The canopy was an interesting part of the project,” said George. “It’s really unusual and the architectural features make it very eye-catching.”
There was a staged handover with the bulk of the project to be completed by the end of October in time for the first A-League match of the season. The project was scheduled for final completion in December 2022.
Coopers Stadium is also a fantastic outdoor concert venue. With a capacity of up to 26,000 for concerts, the atmosphere within this boutique Stadium is electric and the sightlines superb for live music fans.
Tourism and hospitality experts claim Adelaide is nipping at the heels of its Eastern city counterparts to become the country’s ‘next Sydney or Melbourne’, backed by reports that reveal the city now has the highest occupancy rates across Australia and New Zealand.
“Hansen Yuncken is excited to be a part of this by delivering complex, community focused buildings with pride,” said Peter Salveson,
CEO of Hansen Yuncken. “We are honoured to be involved in developing landmark hospitality and cultural heritage sites that will play a pivotal role in Adelaide’s post-pandemic revitalisation.”
Founded in 1918, Hansen Yuncken have been in business for over 100 years and is one of Australia’s leading, privately owned construction companies at the forefront of change and innovation in the building industry.
The company operates nationally across Victoria, New South Wales, South Australia, Tasmania and Queensland. Hansen Yuncken has completed thousands of projects, has over 650 staff across nine offices, and an annual turnover exceeding $1 billion.
Hansen Yuncken have re-imagined construction as a service industry. It’s about how they can help, not just what they can build, always evolving their delivery procedures to suit each client’s specific needs.
For more information contact Hansen Yuncken, phone 08 8229 7300, email adelaide@hansenyuncken.com.au, website www.hansenyuncken.com.au
Load 28 installed and operated the tower crane that lifted all of the resources onsite at Coopers Stadium, from steel frames to the grandstands themselves. The company also supplied and operated a number of mobile cranes for the project.
“The location of the tower crane meant the installation process was pretty tricky,” said Load 28 Manager, Fiona Rigney. “The crane was located very close to the road so there was a lot of planningengineering and design, traffic management and lift planning using mobile cranes.”
Once in place, the tower crane was in use everyday. “The tower crane was remote operated, making it smaller and easier to manage,” said Fiona.
Load 28 is Adelaide’s leading crane hire company and are specialists in tight access, glass installation and everything in between. They service both residential and industrial projects and their experience and equipment has made them the company of choice for Tier 1 projects.
“We are extremely proud of our company,” said Fiona. “My brother, Marcus, had a dream to drive a crane. He went out and bought one and learned how to drive it and everything else he needed to know. He started the company by letterbox dropping flyers, and now 12 years later we are industry leaders in South Australia.”
The team of 30 are all specialists in their field and because of their commitment to family values, the company has experienced next to no staff turnover
Load 28 has recently acquired two more crane hire companies in Victor Harbour Crane and Nick’s Crane. They also have a sister company, Australian Glass Install.
“Marcus has a motto - plan the work and work the plan - and that has paid off for our company,” said Fiona. “We love working on iconic projects and Adelaide certainly has a lot of those.”
For more information contact Load 28, 1196-1200 Old Port Road, Royal Park SA 5013, phone 1300 11 28 28, email bookings@load28. com.au, website www.load28.com.au
Gant and Sons Pty Ltd is a local Adelaide business based in the northern suburbs. Established in 2004, the company is family owned and run, offering a turn key structural steel fabrication and erection expertise throughout Australia. Their main client base is South Australian developers, builders and subcontractors.
With a team of 80 staff Gant and Sons Pty Ltd specialise in crane hire and rigging, onsite welding, fabrication and erection of industrial and commercial projects, as well as inhouse drafting and design.
“As a company, we have built a reputation of honesty and integrity allowing us to maintain relationships and grow in conjunction with customers and clients,” said Drew.
“With the ability to Draft, Fabrication, Transport, Paint and Erect using internal resources we are in full control of our supply chain and are a ‛one-stop-shop’ for steel solutions.”
Gant and Sons Pty Ltd are also working on the refurbishment of Westfield Tea Tree Plaza in Modbury which encompasses a skylight going through the centre of the building.
Recent projects include 60 King Street in the Adelaide CBD, Flinders Medical Research Centre at Flinders University and the Australian Bragg Centre for Proton Therapy and Research.
For more information contact Gant and Sons Engineering, 7 Palina Court, Smithfield SA 5114, phone 08 8284 5460, email admin@gantandsons.com.au, website www.gantandsons.com.au
AJ Baker & Sons project brief for Coopers Stadium was to supply food service equipment; cooktops, fryer, combi ovens, plug-in fridges, plus all stainless steel work for three commercial kitchens within the new complex.
AJ Baker & Sons are a family owned, fourth generation company that has a rich history in Australia. The business was established in 1920 and are specialists in providing commercial refrigeration solutions to supermarkets, hospitality, healthcare and the resources sector.
Based at their South Australia branch, their food services team supply and fit commercial kitchens working closely with the food, beverage and hospitality industry enabling them to identify and provide solutions for the specialist requirements of commercial kitchens and food and beverage retail outlets.
“Australia wide we are working on major supermarket store fitouts,” said SA State Manager, John McBurnie. “We are working with Aged Care facilities on food service equipment fitouts and various custom built cases for a range of supermarkets in South Australia, Victoria, Western Australia and Queensland.”
AJ Baker & Sons offer custom build and installation services for food preparation and display areas, commercial cater/ware-washing and other equipment required to operate in a commercial environment. Their team of engineers, drafts people and technicians provide innovative solutions to suit all requirements, and their technicians are available round the clock to keep operations functioning smoothly.
AJ Baker & Sons have a proud history and are evolving to ensure a strong presence is maintained in the Australian refrigeration industry. They are the Australian distributor for brands such as Bonnet Névé, Eurocryor, Iarp, AHT, Criocabin, and Manitowoc equipment.
Their dedication to exceptional products and customer service have made them Australian leaders in commercial refrigeration.
For more information contact AJ Baker & Sons, 26 Cavan Road, Dry Creek SA 5094, phone 08 8368 2300, email Email@ajbaker.com.au, website www.ajbaker.com.au
Square Ceilings installed the ceilings and partitions for the Coopers Stadium Upgrade. Based in Adelaide, Square Ceilings had the expertise to handle the demands of scheduling and design changes to get the job done.
“The schedule was very tight for this job,” said Project Manager, James Yao. “All of the trades had to cooperate to ensure maximum efficiency onsite.”
“Thankfully the builder was terrific at coordinating not only the trades but the variations to the build as they arose,” said James. “This meant we could put 100% of our focus into delivering a high quality outcome for the client.”
Square Ceilings used a new product called Createx. Manufactured with high quality, ultra-sharp perforations in a variety of continuous perforated patterns for a seamless finish, createx meets the high level of acoustic performance required for commercial public areas such as the corporate boxes at Coopers Stadium.
Once installed, the CAPT-AIR ® technology in createx actively works to decompose formaldehyde emissions found in the air. This results in a safer environment for any space where createx is installed.
Square Ceilings was established almost 10 years ago in South Australia to supply and install quality plasterboard ceilings and walls, primarily to the commercial building market. With a team of 25, they have been servicing most of the principal builders in the state. Square Ceiling’s goal is to safely deliver a high quality product on time and on budget.
“Our team experience ranges from small scale residential work to highrise multi story apartments,” said Wenrong Zheng, Director of the company.
For more information contact Square Ceilings, 33 Hutt Street, Adelaide SA 5000, phone 08 8123 1175, email admin@squareceilings.com, website www.squareceilings.com
CLIENT : Department for Infrastructure and Transport (DIT)
MAIN CONSTRUCTION COMPANY : Port Wakefield to Port Augusta Alliance, CPB Contractors, Aurecon and GHD
CONSTRUCTION VALUE : $200 million TYPE : Infrastructure/Transport
The Joy Baluch AM Bridge Duplication Project will improve road safety and efficiency and includes improved bridge access, new shared use paths, an upgraded intersection at Mackay Street, remediation work and new connections for pedestrians and cyclists.
The original Joy Baluch Bridge was opened in 1972 to span across the gulf, as part of the National Land Transport Network.
The bridge formed and maintained an important commercial and tourist link connecting Port Augusta to the Eyre, Stuart and Augusta Highways, the Far North of South Australia and inland Australia.
South Australia’s Department for Infrastructure and Transport (DIT) is improving transport links across the state and increasing opportunities for regional communities. The project will deliver quality infrastructure and improve road efficiency for this important crossroads of South Australia.
The Australian and South Australian governments have jointly committed $200 million (80:20) to the duplication of the Joy Baluch AM Bridge. Being such a large scale project, the Joy Baluch AM Bridge Duplication Project team has had to manage significant environmental issues. To plan for and manage construction impacts,
the project team created a Construction Environment Management Plan addressing issues such as: erosion, water quality and marine fauna, dust, noise, vibration and light spill.
The project involves the construction of a second bridge alongside the original to allow for two lanes in both directions.
“The design and construction team had to build a bridge that matched the aesthetic of the existing bridge, in order to deliver the duplication. The scope of this project meant that there were some unique challenges facing the construction team, and they have done a great job to overcome them. On completion of the duplication project, we will have a fantastic, dual lane link connecting not just the two sides of Port Augusta but both sides of the entire country,” said South Australian Minister for Regional Roads, Geoff Brock.
of contractors including CPB Contractors, Aurecon and GHD, in alliance with the DIT. Formed in March 2020 the PW2PA Alliance recently completed the $124 million Port Wakefield Overpass Project. In addition, the PW2PA Alliance are currently delivering the $260 million Augusta Highway Duplication from Port Wakefield to Lochiel. The 28 kilometers of dual lane carriageway is one of the largest infrastructure projects ever to be undertaken in regional South Australia. While work on the Joy Baluch AM Bridge and Augusta Highway Duplication projects are running concurrently, the former is expected to be completed later this year and the latter in 2024.
The improved Joy Baluch AM Bridge will have safe pedestrian access with new pavements and shared use paths and new connections for pedestrians and cyclists. Approaching the bridge is an intersection upgrade with new traffic signals and footpaths.
Site activities began in November 2019 with night works to locate existing utilities services via potholing and visual inspection methods. Further investigation activities included geotechnical investigations, noise, flora and fauna assessments, as well as Aboriginal and Heritage surveys.
The PW2PA Alliance hosted forums with the local community and by November 2020 the design was finalised. Construction commenced with bridge piling works on the Westside Foreshore and remediation work including the widening of embankments
“Another challenge was that because the bridge is a vital transport link, we had to keep traffic moving across it throughout the duplication project. This was done by keeping the original section operating while we constructed the new section, before switching traffic onto the completed new section so the original bridge could be refurbished. We were able to realign traffic to the final configuration and have two lanes traveling in each direction,” added Minister, Brock.
Last year a traffic switch saw traffic move onto the new span while the existing span was upgraded. The Joy Baluch AM Bridge is set to officially open mid 2023.
For more information contact PW2PA Alliance, phone 1300 161 407, email enquiries@pw2pa.com.au, website www.pw2pa.com.au
SA Profiling is a specialist road profiling company with a modern fleet of profiling machines, equipment and a team of highly experienced operators. In 2019 SA Profiling was at work on roadworks adjacent to the Joy Baluch Bridge Duplication site when they were noticed by CPB Contractors and engaged for their services.
“We started onsite with a crew of 10, working on the roads leading up to the bridge including driveways and entrances to businesses and residences along the way. We carried out bulk excavation and profiling on existing roads with two Wirtgen profiling machines, trucks and skid steers,” said Manager, Dyllan Bezzina.
“We were also engaged in profiling the asphalt off the existing bridge. Bridge work is critical, it is so important to profile the asphalt surface without causing any damage to the bridge. However, at SA Profiling we have quality, reliable equipment as well as accurate and efficient operators who take pride in a job well done.”
“On the job we were working to the Department of Transport and Infrastructure’s specifications and CPB Contractors guidelines. Before site works commenced, SA Profiling attended multiple meetings to establish the scope of works and to satisfy the numerous State Government and WHS regulations. This was our first job with CPB Contractors and we really enjoyed working with them and look forward to future contracts with them.”
“The actual job of profiling is easy for us, we have years of experience and we are very good at what we do. There was a lot of rain
in Port Augusta, but we are used to working around all types of weather, and this doesn’t stop us from moving forward. We worked in stages, profiling sections of the road and then leaving the site for a period for the new pavement to be constructed, then we would return to profile the next section.
Established in late 2018, SA Profiling is a South Australian family-owned and operated company with a goal of serving South Australia’s infrastructure projects with local South Australian labour and resources. Over the past four years they have grown to employ 20 staff and crews of operators, enabling them to take on large scale projects, often concurrently with other massive infrastructure developments. While at work on the Joy Baluch Bridge Duplication Project, SA Profiling were working on other DIT projects, the Port Wakefield overpass and local council projects.
“The DIT “P and R” Projects involve large volume profiling over approximately a month of night shifts. We had a window of three hours to remove large volumes of road surface before making way for the asphalting crew to come in,” added Dyllan.
SA Profiling has successfully completed other projects for South Australia’s Department of Infrastructure and Transport including at Magill road and Port Rush road intersection, Goodwood road and Springbank road intersection and at the Horrocks Highway, an important transport link. SA Profiling also have consistent work with Adelaide’s local councils, often through Joint Ventures with asphalting contractors, maintaining and upgrading roads and they have completed maintenance work at Adelaide Airport.
SA Profiling is the only South Australian company to employ Trimble 3D Machine Control technology. This system allows any design to be uploaded into the profiler, supplying instructions for automatically cut levels, increasing the accuracy and efficiency of the job. SA Profiling can also provide their own designs, with the ability to create basic designs on the day of profiling, with more complex designs being prepared inhouse.
For more information contact SA Profiling, 10 Barfield Crescent, Edinburgh North SA 5113, phone 08 8252 7026, email info@saprofiling.com.au, website www.saprofiling.com.au
Below Far North Traffic Alliance provided all of the traffic management requirements for the duration of the project.
The Far North Traffic Alliance (FNTA) is a dedicated traffic management business, a joint venture between the Dieri Aboriginal Corporation and Prime Traffic Solutions.
Established in August 2020, FNTA create new opportunities for Aboriginal people in the Upper Spencer Gulf and Far North of South Australia. FNTA services all work sites including land which is Aboriginal owned and they focus on empowering community while giving back to Traditional Owners.
“We specialise in traffic management, traffic plans, workzone traffic planning and traffic control within our regional Adelaide area,” explained Managing Director, Sharon Van Kempen.
“At the Joy Baluch bridge we were the sole provider of all traffic management requirements for the duration of the project including the planning, site set-ups and pack-ups, and pedestrian control.
“It was a challenge to maintain and keep the traffic flowing on this busy route, we had six to eight Traffic Controllers each day and up to 12 during nightshifts using truck-mounted attenuators and portable traffic lights. The set ups were complex yet the traffic switch-overs
were conducted on time and without any incident, a credit to the many locally trained Traffic Controllers in Port Augusta.”
The FNTA has been at work on other sites with CPB Contractors, in the PW2PA Alliance, including the Augusta Highway, Eyre Peninsula and large-scale roadworks projects at Kimba and Lochiel. FNTA are also providing their services for BHP geotechnical surveying, McDonnel Dowell Diona Joint Venture (Water North Program) and Downer.
Since being awarded the traffic management contract for the Joy Baluch Bridge, FNTA have continued filling contracts in the region and expanding their business. “It has been challenging working on a new start up Joint Venture indigenous company, especially ensuring our staff get the right support, training and mentoring onsite,” added Sharon. “This is crucial to our future and the experienced staff supplied by Prime Traffic Solutions to fulfill this role have been outstanding.”
For more information contact Far North Traffic Alliance, 6 Tassie Street, Port Augusta SA 5700, phone 08 8641 0092, email sharon.vankempen@fnta.com.au
Spencer Gulf Security Service provide the installation of comprehensive security systems to residential and commercial properties across regional South Australia and within Port Augusta. Spencer Gulf Security Services install security systems that include alarms and CCTV and monitoring as well as providing static guards for construction sites.
“We’ve been providing security services at the Joy Baluch Bridge since work started there two years ago,” explained Business Manager, Kylie Van der Westen. “We have one or two officers monitoring the area throughout most days and each night. Unfortunately, we have a real issue in Port Augusta with vandalism and we were contracted to guard the machinery and materials at the site. We also provide these services to homes and businesses within Port Augusta and have officers patrolling the area nightly. We work closely with the police and have a good understanding of the communities needs, to help us better deal with the problem.”
Spencer Gulf Security Service is a locally run, family-owned company established 42 years ago. They maintain their own fleet of vehicles and employ officers who live within and outside of Port Augusta, for a quick response across the state.
“We offer a tailor-made service,” continued Kylie. “Our technicians visit businesses and homes to understand their client’s needs and to assess the vulnerabilities of their building. We then design an appropriate security system that includes proven security products, professional installation, maintenance and 24-hour monitoring.”
“Spencer Gulf Security Service has been guarding the construction site of Lincoln Gap windfarm during stages 1 and 2 and often work at community events like the Quandong Festival in Quorn, protecting the site before the event and working at the event. We’ve been at Progress Rail gate for many years and continue to do so. Occasionally we are called in to guard trains and equipment if there is a train derailment or a problem with the train line anywhere in SA. This is usually a last minute job and involves lots of travel. Luckily our officers are very flexible and are always up for a challenge!”
For more information contact Spencer Gulf Security Service, 24 Victoria Parade, Port Augusta SA 5700, phone 08 8641 3232, email security@sgsspa.com.au, website www.spencergulfsecurity.com.au
True Line Kerbing started onsite at the Joy Baluch AM Bridge Duplication in March 2022. “True Line Kerbing worked directly for CPB Contractors as part of the Port Wakefield to Port Augusta Alliance, a consortium of builders working with the SA Department for Infrastructure and Transport to improve transport links across South Australia,” Business Manager, Harito Chrisakis explained.
“True Line Kerbing constructed the concrete kerbs and gutters, edging, median islands and pedestrian pathways on the bridge and the roads leading to it. We also made new driveways to access commercial properties from the new road. Due to the staging of the project and following the construction of the road we worked in stages, sending crews of six workers to the site to complete concreting works and then returning when another length of roadworks had been prepared.”
“The challenges included the weather, rain made the area very wet and as the site is on low ground, close to the river, our work was severely impacted by lack of drainage that the old infrastructure is suffering from.”
Established in 1980, True Line Kerbing is a family owned and operated company serving Adelaide and regional South Australia. The company
own and maintain their own plant and equipment at their Wingfield depot with a range of kerb making machines ready for high volume quantities of concrete placement. The scope the business covers ranges from large scale Tier-1 Infrastructure projects to smaller scope council residential repair works.
True Line Kerbing have been working for the SA Department for Infrastructure and Transport, either directly or through civil contractors, to install kerbing and guttering on a long line of infrastructure projects over the last 20 years.
In 2020 True Line Kerbing completed kerbing and guttering and associated concrete works along 20km of the Northern Connector and in the same year they finished work on the Darlington Intersection Upgrade.
For more information contact True Line Kerbing, 16-18 Leeds Street, Wingfield SA 5013, phone 08 8359 8360, email office@truelinekerbing.com.au website www.truelinekerbing.com.au
CLIENT : Cancer Council SA
MAIN CONSTRUCTION COMPANY : Sarah Constructions
ARCHITECT : Cheesman Architects
CONSTRUCTION VALUE : $31 million
TYPE : Healthcare
Cancer Council's new 5-storey integrated cancer building combines cancer research, prevention and support alongside a new 120 room supported accommodation facility for regional and remote South Australians traveling to Adelaide for cancer treatment.
Sarah Constructions secured the $31 million design and construction contract for the new Cancer Council integrated cancer building in South Australia.
The purpose-built facility involved the development of the Cancer Council’s current site on 202 Greenhill Road, Eastwood into a new, fully functioning mix of 120 accommodation units, communal kitchen facilities, dining spaces, an activity hub, family rooms and play spaces, 2,300m2 of office and 122 car parking spaces.
The new 5-storey building will provide a home away from home for regional and remote South Australians travelling to Adelaide for treatment. There are several rooms accommodating individuals and/or families with disabilities. Every space in the new building has been planned with people impacted by cancer in mind, from kitchens and dining rooms through to entertainment areas and kids’ rooms.
The building is the only one of its kind in the country to combine Cancer Council’s research, prevention and support services alongside supported accommodation.
The project commenced in February 2021 and reached practical completion in November 2022.
Sarah Constructions is based in South Australia with a reputation for excellence in delivery and problem solving for projects.
Starting in 1961, the Sarah family became a trusted name in the building industry by providing quality design and outstanding customer service. More than 60 years later Sarah has cemented itself as a leader in the
industry and these values still remain at the forefront of every project they undertake.
“Our team takes pride in finding the best solutions to take your design to the next level. We collaborate with you and all other key project partners to get the job done, meeting or exceeding the highest standards,” said Rob Maiblo, Construction Manager at Sarah Constructions.
Sarah Constructions’ approach to innovation is the basis for growth as a company. With consistent research and implementation of new technologies, they continue to deliver the most efficient, cost optimised, and advanced solutions available to their clients.
Current projects include the Allan Scott Headquarters Upgrade at Port Adelaide Football Club, St Ignatius College Art, Design & Technology Build, the Banksia Apartments in Glenside and the Stella Maris Parish School.
For more information contact Sarah Constructions, 49 Glen Osmond Road, Eastwood SA 5063, phone 08 7129 8888, email contactus@sarah.com.au, website sarah.com.au
Below Spartan Electrical supplied the kitchen appliances for all the apartments for the Cancer Council Integrated Cancer Centre.
Appliance experts Spartan Electrical, supplied kitchen appliances for all the Cancer Council Redevelopment apartments. This included the hubs featuring fridges, microwaves, ovens, cooktops, rangehoods, dishwashers, washing machines and dryers. The team then delivered, unboxed and placed into position ready for install.
“This was a straightforward job,” explained Commercial Partnerships Manager, Con G Tsoutouras. “I tendered for the project and then worked closely with Sarah Constructions to select the most appropriate appliances.”
Spartan specialises in supply of domestic appliances including ovens, cooktops, rangehoods, dishwashers, fridges, microwaves to commercial partners for their projects. The strong relationships with their supply partners means Spartan can deliver on large quantity orders with a seamless approach to quote, order and delivery.
As a proudly South Australian owned family business of over 50 years, Spartan puts a lot of work into treating all of their customers as if they’re friends and family walking in for a chat. “It’s normal to be greeted with a warm smile, the offer of a coffee while you browse
and an interesting conversation with the 85-year-old founder, Peter,” said Con G, who is also Peter’s nephew.
Spartan is currently working on a large and varied range of commercial projects with their partners, from single dwelling to medium density to multi-dwelling apartments. Spartan has the capacity to service all types of commercial projects. They also work closely with a range of architects and designers as the chosen retail partner to service their clients.
“In addition to our commercial operations, we operate two stateof-the-art retail outlets in Campbelltown and Torrensville, both of which are open seven days a week,” said Spartan Marketing Manager, Ryan Burgess. “We stock a large range of kitchen, laundry and outdoor appliances from leading brands. We are the exclusive retailer for several of the large brands including Sub Zero, Wolf and Siemens home appliances.”
For more information contact Spartan Electrical, 631 Lower North East Road, Campbelltown SA 5074, 140 Henley Beach Road, Torrensville SA 5031, phone 1300 529 720, website www.spartanelectrical.com.au
PLG Painting Services is a family owned and operated painting business established in 1985. The company has grown over the past 30 years and gathered the experience and skills to be able to specialise in large scale projects throughout South Australia. PLG was contracted to complete all of the internal and external painting on the Cancer Council Integrated Cancer Centre.
“The job itself is quite straightforward,” said Site Supervisor, Apostoli Giamarelos. “We used a combination of elevated platforms, boom lifts and crane to paint the external prefabs and CFC cladding. The internal ceilings and door frames have all been spray-finished which gives a really nice, overall finish.”
A team of 5-8 painters began the job in April and was completed by August. “Our challenge was to keep ahead of all the other trades and try to meet the builder’s program,” said Apostoli. “COVID did cause delays in getting materials, however everyone was committed to staying on schedule.”
Peter Giamarelos, the founder and Director of PLG Painting Services along with his two sons Sotiri Giamarelos and Apostoli Giamarelos have earned a reputation for superior workmanship on projects from
high end residential homes to multi-storey commercial and industrial buildings. Working with many of South Australia’s largest building companies, PLG dedicates their expertise to deliver projects on time whilst ensuring the implementation of strict company and quality assurance policies.
Specialising primarily in commercial and industrial painting throughout Adelaide, PLG has undertaken projects including schools, shopping centres, office fitouts, new multi-storey apartment blocks, retail fitouts, government defence projects and many more. PLG also offer residential services from repaints to new builds and have painted some of Adelaide’s finest homes.
Current projects include the Vibe Hotel in Adelaide and the Nightingale Complex at Bowden.
For more information contact PLG Painting Services, 26 Lysle Street, Brooklyn Park SA 5032, phone 0412 807 393, email plg_@netspace. net.au, website www.plgpainting.com.au
AJ Sound (AJS) supplied and installed the audio visual elements for the Cancer Council Integrated Cancer Centre, including IPTV to the 120 guest rooms as well as all the meeting rooms, activity rooms and staff kitchens and lounges.
Internet-based Protocol Television (IPTV) refers to the streaming of TV programs through broadband Internet rather than the traditional cable or satellite.
In each of the meeting rooms there are interactive displays with the ability to do video conferencing and to wirelessly share content from any device. “The design concept was straightforward,” said AJS Project Manager, Tim Bekker. “We gained access to rooms as they became available.”
AJS is a full-service production and installation company that understands every client has a unique goal and objective for each of their projects. Determining the right collaborative strategy for each organisation is crucial for the foundation of a successful outcome.
“During this project we got the opportunity to work with Tripleplay on the installation of the IPTV system,” said Tim. “They are so
well-respected in this field and the collaboration flowed smoothly and was really enjoyable.”
“Working with Sarah Constructions is always a supportive experience. We’ve done a number of projects together and have a great rapport,” said Tim. “The Cancer Council team were also great to work with, especially Tony Siebert and Brad Trenwith. The IPTV was the biggest install of this kind we’ve done and it was very successful.”
Established in 1996, AJ Sounds is a proud family-owned company that combines the latest in vision, sound and lighting technology to achieve cutting-edge, creative and engaging experiences. AJS offers real, experienced based advice and expertise on the best products and solutions to your specific design and installation requirements.
For more information contact AJ Sound, 10 William Street, Mile End SA 5031, phone 08 8221 5551, email info@ajsound.com.au, website www.ajsound.com.au
All Access Civil undertook the bulk earthworks and civil works package, including the construction of the car park for the Cancer Council Integrated Cancer Centre.
“It’s always a highlight getting the initial bulk earthworks finished because we then hand the site over to the next contractor to get the footings underway. In terms of progressing the structure, that’s a big deal,” explained All Access Civil Director, Michael Toomer.
All Access Civil is an earthworks company which provides a range of services to its customers. They specialise in bulk earthworks, bored piling, retaining wall construction, retaining wall repairs, demolition and building plateaus.
Established in May 2017, All Access Civil has worked extensively all over South Australia. The company has a team of 13, with six engaged on the Cancer Council Integrated Cancer Centre site.
“We have a diverse range of skilled staff on the team. We have over 50 years of civil construction experience between everyone in the company,” explained Michael. “We are a proudly South Australian
Below All Access Civil provided an earthwork and civil works package for the Cancer Council Integrated Cancer Centre.
owned and operated company, and we really value our relationship with Sarah Constructions.”
All Access Civil has a range of specialised machinery to support their staff and to undertake a range of different types of jobs, including the specialised limited access drilling rig.
All Access Civil is working on a range of projects including the recently completed ECH Apartments at Modbury, Our Lady of Sacred Heart College Gym and Dance facilities at Enfield, and Aldi Supermarket at Prospect.
For more information contact All Access Civil, 26-30 East Street, Brompton SA 5007, phone 0426 922 188, email michaeltoomer@ allaccesscivil.com.au
Devonport’s newest landmark, the Novotel Hotel is a key part of the Living City development – Tasmania’s largest regional urban renewal plan. The hotel is perfectly positioned to boast unrivaled waterfront views overlooking the Mersey River and Bass Strait including a choice of city or river views, along with a selection of modestly appointed executive suites.
Fairbrother was the developer and building contractor responsible for the design and construction of the Devonport’s new Novotel Hotel. The 8-storey development features 187 beautifully appointed hotel rooms, a 70-seat restaurant, lobby, reception, gym, staff offices, and 42 parking spaces.
“We have enjoyed bringing a vision to reality,” said Fairbrother’s North General Manager, Marcus Perkins. “This hotel is part of the Devonport City Council’s ‘Living City’ initiative that has been some years in the making.”
Lyons Architects conceived of the Devonport Novotel Hotel as an iconic horizontal land bridge, visually connecting the Mersey River to the city of Devonport. The primarily horizontal form of the Hotel
draws the eye between the river and the city and its construction methodology is integral to its appearance, evoking the idea of the land bridge in this way forms a powerful contribution to the public realm.
“Being involved from concept and having the opportunity to embed our construction knowledge and experience into the early phases of design to create innovative efficiencies, through to completion brings a great deal of satisfaction,” said Marcus.
Fairbrother used prefabricated bathroom pods in 173 of the 187 hotel rooms. These were manufactured in New South Wales by Interpod and ensured stringent and consistent quality control across the bathrooms. The pods also overcame a local shortage in skilled trades for plastering and tiling.
CLIENT : Fragrance Group
MAIN CONSTRUCTION COMPANY : Fairbrother Pty Ltd
ARCHITECT : Lyons Architecture (Base Build), Scanlan Architects (Interior Design)
CONSTRUCTION VALUE : $40 million
TYPE : Hospitality
The original design concept contained hotel rooms on Levels 1-3 and residential apartments on Levels 4 and 5. Fairbrother’s project team worked diligently to re-design the building to accommodate 5-levels of hotel rooms. “The concrete superstructure is unique,” said Marcus. “It consists of an enormous transfer slab that carries the building’s load from Level 1 upwards. The corbel edge detail on this transfer slab required a significant amount of detailed formwork. One end of the transfer slab cantilevers off the end of a uniquely shaped flag column.”
The development had just begun to take shape when the COVID-19 pandemic erupted, impacting materials, equipment and labour. “Working with a committed and dedicated construction and consultant team, we dug deep and we were able to achieve a common goal in the midst of the COVID-19 challenges,” said Marcus
Established in 1972 as a small, family-owned and operated business in Tasmania’s North West, Fairbrother has steadily grown to become a recognised leader in the building and construction industry. Their stellar success in the Tasmanian market has enabled Fairbrother to expand into regional Victoria and also to undertake selected projects nationally. “For 50 years, we’ve been delivering iconic, national
award-winning projects and we have an amazing team of highly skilled and extremely committed employees right across our business in Tasmania and Victoria who we value greatly,” said Marcus.
Fairbrother has a strong commitment to training and development which has formed the foundation of their company. Their culture of employee empowerment and autonomous decision making is underpinned by the company’s values and guiding principles. Fairbrother has a national award-winning apprentice program with an industry leading apprenticeship completion rate.
“Creating such a significant landmark project in our hometown of Devonport where Fairbrother began as a company and delivering this project off the back of the $60 million Living City Stage 1 project is most rewarding for us,” said Marcus. “On completion, we held an open day on the project for all employees and their families to view and admire their handy work. Some 150 employees and family members attended.”
For more information contact Fairbrother, 12 Stony Rise Road, Devonport TAS 7310, phone 03 6420 7000, email info@fairbrother. com.au, website www.fairbrother.com.au
With 40 years of understanding specific local market demands, combined with over 99 years of global experience, Häfele is a renowned international company providing hardware, fitting and electronic access control systems.
With an extensive portfolio of services, alongside their broad range of architectural hardware and furniture fittings, Häfele have the expertise and industry experience to meet the needs of property developers, architects, planners and manufacturing companies.
Offering a wide range of products, including furniture, kitchen solutions, architectural hardware, sliding, and folding door fittings, as well as lighting, tools and consumables, Häfele provide unique and valuable support to decision makers of all project sizes. In fact, their wide range of ‘360 degree’ services allows the customer to have a single contact for all phases of the project, ensuring convenience, capability and consistency through their global sales network and stateof-the-art logistics centres. Furthermore, Häfele’s integrated project coordination monitors all deadlines and logistical services over the entire construction period until handover, ensuring adherence to the defined interests and requirements of a particular project.
Given their comprehensive support and dedicated team, Häfele were also recently engaged for their third hotel project with developer, Fragrance Group, on The Devonport Novotel Hotel in Hobart. Featuring 187 beautifully appointed hotel rooms, a 70-seat restaurant, lobby, reception, gym, staff offices, loading dock and 42 parking spaces, The Devonport Novotel Hotel is a key part of Stage 2 of the ‘Living City’ development – Tasmania’s largest ever regional urban renewal plan.
Working alongside Scanlan Architects and MRIS Quantity Surveying, the Häfele team collaboratively found functional solutions that adhered to both the project design and cost requirements. Responsible for the supply of a comprehensive Door Hardware Schedule for the project, including electronic access control to all guest rooms, automatic door opening technology and additional fixtures and fittings for the project fitout and
joinery, Häfele’s quality products are literally at every touchpoint of the development.
Ricky Pearton, State Manager for Häfele Tasmania, said that his team worked successfully onsite throughout the project, with both the main developer and other subcontractors. “As this is our third hotel project with Fragrance Group, we have developed a successful working relationship and many of the Häfele products specified for this project had been tried and tested to ensure they met the expectations and specifications of the developer,” Ricky said.
“However, every project has its unique challenges and we worked closely with Scanlan Architects, QSS quantity surveying and Fairbrother from the very beginning, to ensure the project was supplied with products that met criteria for The Devonport,” he said
A special product feature installed by Häfele was the Dialock Access Control, a hightech addition that will not only enhance the guest experience, but will also support the overall operations of the hotel, with the storage of essential security information and data.
“In addition to the new technology we used, The Devonport is a special project to Häfele and is testament to the strong and evolving nature of our relationship, as it’s our third collaboration with the developers, Fragrance Group and long-term relationship with builder, Fairbrother,” Ricky said.
“It’s really exciting to see new investment in the hotel sector across Tasmania and we are looking forward to partnering on more projects in the future,” he said.
This year, Häfele celebrates 40 years in Australia. Given their contribution to Australian design, manufacturing and construction since 1982, as well as their commitment to developing new, highperformance fittings and hardware, there is no doubt they will continue to support and supply hundreds of exciting projects into the future, bucking market trends and exceeding customer expectations.
For more information contact Häfele, 48 Lindsay Street, Invermay TAS 7250, phone 03 6210 6412, email rpearton@hafele. com.au, website www.hafele.com.au
Degree C are the leaders in the delivery and support of heating and cooling, ventilation, refrigeration, electrical and communication services, fire detection and metal fabrication. Conveniently located across three locations in Tasmania, namely Ulverstone, Launceston and Hobart, Degree C are able to meet the needs and requirements of clients, regardless of their location.
With a focus on their aforementioned different business streams, Degree C provide HVAC, electrical and metal fabrication solutions to a range of projects, ranging from large-scale commercial and industrial operations, through to residential properties. Completely dedicated to providing the utmost customer support and service, Degree C’s highly experienced team of 280 employees have been offering their range of services since the 1960’s.
Given their wealth of expertise and industry know-how, Degree C were also recently involved on the Devonport Novotel Hotel project. Touted as Tasmania’s largest ever regional urban renewal plan, and a key part of Stage 2 of the Living City development, the eight-storey development incorporates 187 beautifully appointed hotel rooms, as well as a range of additional amenities, such as a restaurant, gym and car park.
Tim Jordan, General Manager of Degree C, said that throughout the construction and development of the hotel, his team were responsible for the delivery of a range of services. “We completed all heating, ventilation, electrical, communications, security and fire detection works for the Devonport Novotel Hotel, in both a timely and cost-effective manner,” Tim said. “We used a Mitsubishi Hybrid system throughout the entire hotel, which is a combination of refrigerant and water, to heat and cool the building”
“We also supplied and installed cooking hoods and perspective ductwork, refrigeration systems for the cool, freezer and keg room and installed Mitsubishi high wall splits to keep the IT rack room cool.”
The light and power installation was a large undertaking. The lighting was a mix of feature and room lighting that was coordinated with other trades including the joiner and plasterer. The power work consisted of rising mains and power distribution across the levels. Communications cabinets are located on multiple levels with a fibre optic network linking these together. There are multiple communications outlets located in the rooms as well a wireless network.
Fire detection is located throughout using the latest technologies to minimise false alarms. The access control and CCTV systems are top of the range to ensure peak performance.
“Although having all bulk materials ordered, delivered and ready to be craned onto each individual level at strategic stages of the build was challenging, particularly in regard to timeframes, we were able to deliver our services in adherence to deadlines by working in conjunction with the builders and breaking the build down into individual levels, which worked really well,” Tim said.
“Timeframes were challenging but we endeavored to consistently work with the builders and other trades to ensure these were met and the hotel was delivered on time. We also ensured that the work remained at the highest possible quality.”
Heralded as Tasmania’s leading multi-trades company, Degree C have also worked on a range of additional projects. Some of these include the Living City Stage 1 project, new University builds in Burnie and Launceston, large projects in the industrial and agriculture sectors, a new remand centre, a fish pellet factory, and many others.
“We are proud to provide our services to such iconic and cutting-edge developments,” Tim said. “We look forward to continue to offer our innovative and competitive engineeringbased services across all business sectors.”
For more information contact Degree C, 2 Fairair Court, Ulverstone TAS 7315, phone 03 6429 6800, email info@degreec.com.au, website www.degreec.com.au
JMG Engineers & Planners has been providing professional engineering services to the Tasmanian market for over 60 years.
Covering Civil, Structural, Hydraulics, Electrical, Fire and Mechanical services plus Town Planning. JMG strive to provide the best value project solutions to all stakeholders in the construction and built assets market.
For the Devonport Novotel Hotel project, JMG were engaged by Fairbrother for Mechanical and Electrical services, on the back of JMG’s contemporary experience in recent hotels such as Crowne Plaza Hobart, Verge Hotel Launceston & Freycinet Lodge. Other notable projects JMG have recently worked on are UTAS Hedberg, MYER ICON, MONA Pharos and Siloam, MyState Bank Arena and numerous others.
The design process was a close collaboration between JMG, builder/ developer Fairbrother, Lyons Architects, sub-contractors Degree C, Hotel owner Fragrance Group, and Hotel operator Accor Group, The design brief specified flexible and energy efficient systems, and designs evolved in parallel with construction to optimise and customise engineering systems, and later to incorporate hotel operator requirements and preferences. A Hybrid VRV air conditioning system was selected to maximise energy efficiency through the full range of occupancy & usage.
JMG played an important role in the design of the lighting systems for the guest rooms and back-of-house areas, to coordinate specialist
interior design input for reception and function areas, to make for an integrated, cost effective and energy compliant package.
Congratulations to Fairbrother for delivering this successful landmark project in Devonport.
For more information contact JMG Engineers & Planners, phone 03 6231 2555, email nallen@jmg.net.au, website www.jmg.net.au
6tyº are a multi-disciplined architecture, engineering, surveying and planning company, who are able to service projects completely inhouse, from the initial concept through to completion of construction.
For this project, 6ty° called in the additional engineering expertise of Rare Innovation.
6ty° were responsible for all of the civil, structural, surveying and hydraulic engineering aspects of the Hotel, the experienced team of 13 from 6tyº and Rare Innovation incorporated a range of unique structural engineering techniques to the project.
In addition, they demonstrated their resilience and dedication to the development, and worked collaboratively as a team to overcome the various challenges that arose throughout the construction phases of the Devonport Novotel Hotel.
Given the original architecture vision drew inspiration from the maritime industry, with the Level 1 deck in the form of a boat structure, 6tyº applied a bridge design theory on both the shape and structure of the 13m above-ground feature.
Additionally, the team also took into consideration the Hotel’s close proximity to the ocean, resulting in a need for design and structural
features that would withstand both the unpredictable weather and exposure to the ocean.
One of the principle challenges 6tyº faced throughout their involvement was the misalignment of the structure from the roof, to the foundations, which was a necessity given the different functionality of various floor levels. However, with over 30 years of industry experience and know-how, as well as their creative and dedicated astute team, 6tyº were able to deliver the project in their seamless and efficient manner, highlighting their strong internal communication and consistency to perform, regardless of the size or scope of the project.
With a commitment to providing the very best practical advice and customer service, as well as a range of comprehensive architectural, engineering or surveying solutions, 6tyº have worked on numerous developments throughout Tasmania, including Launceston Health Hub, Penguin High School, Wynyard Yacht Club, Josef Chromy Winery, DeBruyn’s Freight Depot and more recently, the Devonport Novotel Hotel.
For more information contact 6tyº, Tamar Suite 103, 287 Charles Street, Launceston TAS 7250, phone 03 6332 3300, email admin@6ty.com.au, website www.6ty.com.au
ARCHITECT
ENGINEER : Hera Engineering
CONSTRUCTION VALUE : $40 million TYPE : Aged care / Mixed use
Brightwater Central involves the construction of a beautifully designed three level building, 128 bed residential aged care facility and 150-person corporate head office creating a vibrant world-class intergenerational oriented community.
Georgiou Group was appointed as the head contractor on the Brightwater Care Group’s new complex, Brighwater Central. Valued at $40 million, the project involved the construction of a new three level building, 128 bed residential aged care (RAC) facility and 150-person corporate head office which will combine with the RAC facility and an industry leading research centre.
Located in the heart of Perth’s inner suburbs, Brightwater Central is a 1.51-hectare site within the established suburb of Inglewood. The aged care facility features state-of-the-art private rooms with ensuite bathrooms, landscaped courtyards and spacious communal areas, a gym and a hairdresser. It will provide high quality care for people with a range of diverse needs, including those with advanced dementia and high care needs.
“Georgiou is immensely proud to add the project to our building portfolio as our first aged care project,” said then-CEO of Georgiou Group, Rob Monaci.
The project team had a very good two-way relationship with the client throughout the project. It was very much a ‘one team – one goal’ approach that worked well,” said Construction Manager, John Parry. “The open and transparent relationship was essential in enabling us to both navigate the challenges of COVID and the resultant extension of time that was closed out in a timely manner. This relationship was a crucial part in ensuring the project was overall a success.”
Georgiou Group developed a number of innovations on this project that not only reduced construction time frames but reduced the health and safety risk profile of some activities. This included pre-assembling and lifting into position the trusses for the structural pergolas and roof.
“Access to water tanks was modified to eliminate a confined space classification,” said John. “Access hatches at ground level were cast into the tank walls and used to enter and exit the tanks to undertake waterproofing and maintenance works.”
Conscious of the impact of the project on the local residents, the project team also implemented a community initiative with a new picnic shelter built for the Friends of Inglewood community group. “The finished product was of a very high quality and the project team felt proud of the build and satisfaction in giving something back to the community,” said John.
Georgiou Group provides a wide range of design and construction services for projects in the health, commercial, retail, industrial and transport and infrastructure sectors for government and private sector clients.
Established in 1977, Georgiou has flourished and expanded into a national civil and building construction company with offices in Perth, Brisbane and Sydney. Georgiou prides themselves on working with the best people in the industry and achieving outstanding results for their clients.
Focusing on creating iconic projects that are innovative, commercial, viable and sustainable, their extensive portfolio showcases Georgiou’s experience in delivering a wide range of complex building projects to clients across a variety of sectors including residential, commercial,
health, retirement and aged care, education, industrial, mining, oil and gas, defence, data centres and agriculture.
Their network of quality subcontractors and strategic procurement model enables Georgiou to provide significant supply chain value for their clients. Their specialised teams have extensive experience in the Western Australian market and manage the entire building process, from feasibility studies through to design and value management, buildability to delivery and handover.
Georgiou Group is currently delivering the New Midland Station as part of the Midland Junction Alliance, Perth Airport’s Checked Baggage Screening Upgrade, St John of God Subiaco Hospital’s Redevelopment, upgrades at Fremantle Hospital and two projects for Georgiou Capital.
For more information contact Georgiou Group, 68 Hasler Road, Osborne Park WA 60107, phone 08 9200 2500, website www.georgiou.com.au
Roofeze, the metal roofing and cladding specialists, were contracted to construct and deliver the metal roofing, metal wall cladding and roof plumbing package for the Brightwater Inglewood complex.
“The ultimate challenge on this project for us was to marry together the physically taxing installation process with the architectural design intent, to overcome the blood, sweat and tears and produce this unique masterpiece. A lot of the roof was pitched at 45 degrees, which is not an easy plane to work from and the metal wall cladding sheets were produced in long, narrow pieces, stopping and starting around corners, around windows and interspersed with the brickwork. It was a mighty challenge to navigate in conjunction with looming deadline pressures and industry wide supply shortages,” said Roofeze spokesperson, Lucas Storer. “We used a delicate combination of Australian produced sheet metal, Colorbond and Nexteel. The roof sheets are Trimdek profile which is not typically used on pitched roofs, and the metal wall cladding is created with interlocking panels, joined with a negative detail.”
Colorbond Trimdek is a common and versatile roof sheeting product featuring bold, trapezoidal ribs and subtle fluting in the pans. Trimdek is ideal for commercial, industrial, and residential roofing, designed
to handle increased rainfall at low pitch. The slight twist on the application at Brightwater Inglewood was to use it at 45 degrees, which was all it needed to illustrate the grand, kingdom like roof design.
Nexteel have developed the Australis Paint Series, inspired by the colours of our exceptionally unique continent. Freycinet is the colour choice, reflecting the natural white of the beautiful sandy beaches of the Freycinet National Park, Tasmania. This soft white juxtaposed against the sleek and modern look of Colorbond Monument created a black and white visual wonder up the castle walls.
Established in December 2006, Roofeze has worked alongside architects, builders, and homeowners to create some of Perth’s most architecturally stunning projects. Director, Craig Storer has 35 years experience and his professional team of skilled roofers have collectively over 150 years experience on top. Together they take tremendous pride in their commitment to service, quality and workmanship.
Roofeze is known to be a reliable wealth of knowledge, offering advice to clients, builders and architects with support from a wide range of suppliers providing them with industry knowledge and practical know-how. The roofing industry has seen significant development in recent times, with amazing new architectural products that are meeting
the demands for uniqueness, whilst also considering safe installation methodologies and a much broader awareness for greener housing living and environmental sustainability. Roofeze has become known for its flexibility to create practical solutions to any problem. Roofeze is continually adapting and evolving with the marketplace, harnessing new products and systems to provide value solutions for clients.
The company has developed great relationships with several leading WA Commercial Builders. Roofeze believes it is absolutely crucial, as part of a project team and a long line of trades onsite, that they maintain a commitment to tight schedules whilst also meeting the builders’ specifications, industry standards and necessary Building Codes. It requires a great deal of coordination and project management skill to ensure that plans run smoothly, and any issues are identified early and dealt with immediately.
Roofeze has a strong management team consisting of several Project Managers, Operations Manager, WH&S advisor and multiple office staff to ensure that their tradespeople are supported 100% on site. With strong management alongside a well-supported and highly skilled crew of tradespeople, Roofeze can guarantee each project will meet the brief, on budget and on time. This is what sets Roofeze apart from their competitors.
Roofeze manages a number of residential and domestic projects alongside its commercial projects. Director, Craig Storer works closely with homeowners to co-ordinate and advise on domestic projects that may involve re-roofing, re-guttering, renovations, or restorations. The team also manages regular maintenance, repairs and building report issues to ensure everyone can experience the Roofeze guarantee.
For more information contact Roofeze, Unit 12, 6 Production Road, Canning Vale WA 6155, phone 08 6258 5855, email info@roofeze. com.au, website www.roofeze.com.au
Freo Fire Services installed the wet fire systems including sprinklers and hydrants, the dry fire systems including fire detection and the Emergency Warning System, and the gas suppression system in the Brightwater Central Complex.
Established in Perth in 2012 with the vision of providing outstanding customer service and reliable Fire Safety equipment and Fire protection services, Freo Fire Services has grown into one of the biggest and most reputable installers of life saving equipment in Western Australia. They maintain an unwavering dedication to the best possible outcome for their customers, offering the latest technology and expert Fire Services and system maintenance at a competitive rate.
“Freo Fire Services boasts a multi-skilled, highly trained team who embrace our friendly and professional company ethos,” said Freo Fire Services General Manager, Lee Cutler. “Our coordinated approach to Fire Safety equips us to meet all your design, installation, maintenance and servicing needs.”
Freo Fire Services have perfected the provision of customised Fire Protection, with Design teams and Fire Equipment Installation
Specialists collaborating with a dedicated maintenance and servicing team to offer an integrated and complete service that is tailored to suit every fire protection need.
“We have seen that really listening to and addressing our customer’s needs is what makes our service so effective,” said Lee. “Our customers are put at ease by the cooperative communication between our staff members, partners and themselves.”
Freo Fire Services has provided top quality designs, installations, reliable servicing and maintenance in the heavy industrial sector, defense sector, health and education sectors, serviced private and public infrastructure and commercial and residential properties.
Current projects include The Groves, Air Traffic Services Centre, Valencia Aged Care, Western Power (Forrestdale), Curtin Library Redevelopment and Armadale Courthouse and Police Complex.
For more information contact Freo Fire Services, 08 9337 4986, email admin@freofireservices. com.au, website www.freofireservices.com.au
Floth designed the potable hot and cold water system, the non-potable cold water, sewer, trade waste services, gas and the building stormwater, for the Brightwater Central Aged Care complex.
As one of Australia’s leading sustainability and building services/ engineering consultancies, Floth knows a thing or two about developing sustainable design solutions. In fact, they credit their continued success to pioneering solutions that combine the key attributes of quality, agility and innovation.
“The Brightwater Central project had quite an intensive modelling process,” said Rachael McGowan, Senior Hydraulic and Fire Consultant at Floth. “Whenever we detected a clash, we coordinated with the structural architect and other services to resolve the issue.
“It was an incredibly enjoyable process once onsite. Working with the plumbers and other services was fantastic which made it so easy to get the job done.”
The skill and technical excellence of the Floth team is what sets the standard of the business, giving Floth a competitive advantage
that makes all the difference. In addition, Floth’s design philosophy embraces an integrated approach – working alongside their clients to optimise outcomes on each and every project.
Their agility and scalability enables them to respond quickly and efficiently, guaranteeing positive results across all projects.
With offices in Brisbane, Sydney, Melbourne, Perth and Jakarta, Floth has a strong and established presence across Australasia, built over 38 years, that places them in the perfect position to help design your future.
“At Floth, saying ‘we care’ means something – because it’s the foundation stone of our business.
We pride ourselves on the consistency and quality of our service, and we genuinely care about the outcomes we achieve for our clients.”
For more information contact Floth, Level 6, 66 St. Georges Terrace, Perth WA 6000, phone 08 6162 2396, email perth@floth.com.au, website www.floth.com.au
ACCESS COVERS
EJ
Page 49 | 07 3216 5000
ACOUSTIC ENGINEER/ CONSULTING
DDEG
Page 98 | 03 8814 3200
Marshall Day Acoustics
Page 59 | 03 9416 1855
AIR CONDITIONING, (HVAC, REFRIGERATION & MECHANICAL SERVICES)
Mitsubushi Heavy Industries
Air- Conditioning Australia, Pty Ltd.
Page 22, 32 | 1300 130 007
AIR SERVICES (VENTILATION/ HEATING/CONDITIONING/ DUCTS
New Edge Group
Page 132 | 02 9725 5555
AERIAL PHOTOGRAPHY
Skyview Aerial Photography
Page 6 | 0431 931 910
ARCHITECTS
Brand Architects
Page 91 | 03 9419 3500
Select Architects
Page 90 | 03 5224 7300
Group GSA
Page 31 | www.group.gsa.com.au
ARCHITECTURAL HARDWARE
Häfele
Page 176 | 03 6210 6412
AUDIO/VISUAL & IT EQUIPMENT
AJ Sound
Page 172 | 08 8221 5551
BATHROOM PRODUCTS
Decina
Page 40 | 1300 DECINA (1300 332 462)
duroclass
Page 48 | duroclass.com.au
Manooga Products
Page 45 | 02 9807 3511
BRICK AND BLOCK WORK
R&R Bricklaying
Page 85 | 0409 270 500
BRIDGES (EXPANSION JOINTS & SEISMIC LOADS)
mageba Australia
Page 39 | 1300 624322
CEILINGS & WALLS
Square Ceilings
Page 157 | 08 8123 1175
CERAMIC MANUFACTURER
R L Foote Design Studio
Page 68 | 0404 873 127
CIVIL CONSTRUCTION
SERVICES
All Access Civil
Page 173 | 0426 922 188
CIVIL CONTRACTING
Wamarra
Page 77 | 1800 314 659
COMMERCIAL BUILDING
PRODUCTS AND SYSTEMS
Laminex
Page 47 | 132 136
COMMERCIAL KITCHENS
Degree C
Page 178 | 03 6429 6800
AJ Baker & Sons
Page 156 | 08 8368 2300
Foodservice Consultants
Australia
Page 109 | 03 9887 6628
Patra Group
Page 114 | 02 9597 6788
CONSTRUCTION COMPANIES & ALLIANCES
ALAND
Page 118 | 02 8076 5510
BESIX Watpac
Page 130 | 02 8741 7400
Construction Engineering
Page 96| 03 9699 1122
Georgiou Group
Page 182 | 08 9200 2500
Geocon
Page 140 | 02 6255 0430
Fairbrother
Page 174 | 03 6420 7000
FDC Construction & Fitout
Page 112 | 02 8117 5000
Hansen Yuncken (SA)
Page 152 | 08 8229 7300
Kane Constructions (VIC)
Page 54, 62, 80, 88, 104| 03 8420 1200
PW2PA Alliance
Page 158 | 1300 161 407
Sarah Constructions
Page 168 | 08 7129 8888
TQM Design & Construct
Page 136 | 02 9556 1046
CONSTRUCTION SOFTWARE / DOCUMENT/PERSONNEL MANAGEMENT
CoreLogic
Page 2 | 1300 734 318
Viewpoint Construction Software
Page back cover | www.viewpoint.com
CRANES/HOISTS & RIGGING (ALL CRANE PRODUCTS & SERVICES)
CICA (On-Road Articulated Steering Mobile Crane Training)
Page 28 | www.cica.com.au
Caelli Constructions
Page 100 | 03 8338 3300
Load 28
Page 154 | 1300 11 28 28
Johnson & Young Cranes
Page 76 | 03 8339 3300
Soldier Tower Cranes & Labour Services
Page 24 | 1300 SOLDIER
DEMOLITION
Mann Vic
Page 64 | 1300 626 647
DOORS
Hume Commercial Doors & Frames
Page 52 | humecommercialdoors.com.au
DOORS (AUTOMATIC)
Tormax Australia
Page 41 | 1800 608 000
DOORS (ROLLER DOORS)
Capital Doorworks
Page 146 | 02 6260 2252
DRAINAGE
Stormtech
Page 35 | www.stormtech.com.au
ELEVATORS/LIFTS
United Lift Services
Page 44 | 1300 161 740
ELECTRICAL DESIGN AND FITOUT
Spartan Electrical
Page 170 | 1300 529 720
ELECTRICAL SERVICES
GM Electrical Services
Page 120 | 0408 113 695
Dynamite Electrical
Page 134 | 02 9669 3311
Colbros Electrical Contracting
Page 117| 02 9966 9144
Eascom Electrical
Page 56 | 03 5442 8979
ENGINEERS (CONSULTING) erbas
Page 30 | 02 9437 1022
ACOR Consultants
Page 99 | 03 9885 4335
Loka Consulting Engineers
Page 127 | 02 8065 9689
Floth
Page 187 | 08 6162 2396
ENGINEERS (STRUCTURAL)
MaddisonWright Engineering
Page 95 | 03 5814 5210
6tyº
Page 181 | 03 6332 3300
Gant and Sons Engineering
Page 155 | 08 8284 5460
ENGINEERS (ELECTRICAL)
JMG Engineers & Planners
Page 180 | 03 6231 2555
ENGINEERING CONSULTING
Meinhardt Australia
Page 83, 107 | 03 8676 1200
ENVIRONMENTAL & SUSTAINABILITY CONSULTANTS
Focus Environmental
Page 69 | 03 8680 4611
EVENTS
Sydney Build
Page 19 | www.sydneybuildexpo.xom
FAÇADES
Façade Industries
Page 149 | www.facadeindustries.com
FACADES AND CLADDING (METAL)
ARC
Page 57 | 02 9482 4461
FAÇADE SYSTEMS
Valmond and Gibson
Page 1 | 1300 097 999
FIRE SAFETY (ALL FIRE PRODUCTS & SERVICES)
PFS Group
Page 66 | 03 9318 9717
Freo Fire Services
Page 186 | 08 9337 4986
Phoenix Fire
Page 82 | 03 9738 7183
FIRE SAFETY (PASSIVE FIRE)
PowAGroup
Page 148 | 1300 303 366
TBA Firefly
Page 43 | 02 8004 3333
FLOORING
Armstrong flooring
Page 46 | 1800 632 624
FORENSIC ENGINEERING
Integrity Testing
Page 53 | 1300 000 332
FORMWORK
Future Form
Page 147 | 02 8376 6950
FORMWORK & SCAFFOLDING
Safeguard Formwork
Page 50 | 1300 971 603
GLASS & GLAZING
Oceania Glass
Page 25 | www.oceaniaglass.com.au
GOVERNMENT DEPARTMENTS & COUNCILS
Level Crossing Removal Project
Page 72 | 1800 105 105
INDOOR GARDEN INSTALLATIONS
Atmosphy
Page 36 | 1300 425 600
INTERIOR DESIGN & FITOUTS
UTJ Interiors
Page 135 | 02 4271 5522
JOINERY & FITOUTS
Scope Joinery Group
Page 139 | 1300 548 548
JOINERY (ARCHITECTUAL)
AACI Group
Page 71 | 03 9464 2133
KERB & GUTTERING
True Line Kerbing
Page 167 | 08 8359 8360
LIBRARY FITOUT
Quantum Library Supplies
Page 67| 1800 773 374
METAL FABRICATION & PRODUCTS
Livson Construction
Page 70 | 03 8353 2829
PARKING TECHNOLOGY
AGD Systems
Page 38 | 02 9653 9934
PAINTERS
PLG Painting Services
Page 171 | 0412 807 393
PLASTER & INTERNAL/ EXTERNAL CLADDING
D&L Interior Lining
Page 129 | 0451 580 288
POOLS
Bradford Products
Page 144 | 03 9768 3984
POWER GENERATORS & SYSTEMS
Jefferson Industries
Page 84 | 0492 915 877
PRECAST PRODUCTS
Abseil & Precast Solutions
Page 138 | 1300 135 188
QUANTITY SURVEYORS
WT
Page 93| 0413 943 848
ROAD PROFILING
SA Profiling
Page 160 | 08 8252 7026
ROOFING
Roofeze
Page 184 | 08 6258 5855
Mack Bros Roofing Products
Page 108 | 03 9571 7911
SEALANTS AND BONDING
Soudal
Page 42 | 1300 507 011
SECURITY
Spencer Gulf Security Service
Page 165 | 08 8641 3232
SHADE SAILS
Sydney Shade Sails
Page 51 | 02 9592 0401
SIGNALLING
All Systems Contractors
Page 74 | 0400 766 751
STEEL (FIRE RATING)
Action Alliance
Page 101 | 03 9931 0740
STEEL (STRUCTURAL/ FABRICATION)
Strata Steel Detailing
Page 94 | 0407 882 504
SURVEYORS
Approval Systems
Page 106 | 03 9639 5500
TILING
Auscorp Tiling Services
Page 122 | 02 9730 0209
Icon Tiling
Page 61 | 03 9770 8957
SHOWTILE
Page 126 | 02 9709 5836
Victoria City Tiling
Page 61 | 03 8590 1432
TRAFFIC CONTROL/ MANAGEMENT
Far North Traffic Alliance
Page 164 | 08 8641 0092
GAME Traffic & Contracting
Page 58 | 03 5441 4250
TRAINING & ASSESSMENT
Area9 Lyceum And Adaptive Learning
Page 28 | www.area9lyceum.com
WATERPROOFING, SEALANTS & EXPANSION JOINING
Sydney Ultra Seal
Page 128 | 0421 531 181
WINDOWS AND DOORS (ALUMINIUM)
Darley Aluminium
Page 26 | www.darleyaluminium.com.au
PUBLISHER
K.M. Hanson
GENERAL MANAGER
Michael Matthews
GRAPHIC ARTISTS
Jessica Mills, Misty Drady
SALES
Phil Meylan, Raimondo Sorbello
ADMINISTRATION
Jenny Bow
ANCR Property Show
Hosts: Tamaryn Hurley, Jaimee Peasley
Editing: Gary Burgess
PUBLISHED BY
Trade Media Group Pty Ltd
ACN 118312404
t. 02 4322 1200
f. 02 4322 1400
www.ancr.com.au
ancrmagazine
@ausconstruction_review
The Australian National Construction Review Australian National Construction Review
WRITERS
Tanya Nellestein, Sarah Gardiner, Jodie Wolf Samantha Pencarinha, Prue Clark
PHOTOGRAPHERS
Benjamin Halcomb, Bruce Robinson, Jim Young, David Dickson, Stephen Wood, Joe Sabljak, Alan Foon, Andrew Kendall, Cameron Longshaw, Angela Frost, Leah Follett, Georgia Curry, Peter Reichstein, Christopher Millen, Simon Sturzaker
COPYRIGHT
All material in this publication is copyrighted to the publisher and/or its advertisers and contributors. No material or portion of this publication may be reproduced in whole or part without the express written permission of the publisher.
DISCLAIMER
The Australian National Construction Major Project Review and the publisher Trade Media Group Pty Ltd reserve the right to alter or omit any advertisement, editorial, or advertorial. Advertisers and/or their representatives indemnify the Australian National Construction Major Project Review and the publisher in relation to defamation, slander, breach of copyright, infringements of trademarks of name of publication titles, unfair competitor or trade practices, royalties or violation of rights and privacy and warrant that their material complies with all the relevant laws and regulations and that its publication will not give rise to any rights against or liabilities against the Australian National Construction Major Project Review, its publisher, its servants or agents. The Australian National Construction Major Project Review and the publisher are not liable for inaccuracy in any advertisement or editorial and do not accept responsibility for any claims made by advertisers. Any material supplied to the Australian National Construction Major Project Review or the publisher are at the contributors risk. No responsibility will be taken by the Australian National Construction Major Project Review, its publisher, its servants or agents. Opinions published in The Australian National Construction Major Project Review are not necessarily those of the publisher or staff of The Australian National Construction Major Project Review. The Australian National Construction Major Project Review is not related to any other publication.
SUBSCRIBE 8 ISSUES - 2 YEARS $119.60 + GST inc. postage
ADVERTORIALS OR ADVERTISEMENTS
FULL COLOUR - INCLUDES PHOTO SHOOT
*SINGLE PAGE (A4) 210mm x 297mm $2450 + GST (NORMALLY $3950 + GST)
*DOUBLE PAGE (A4 x 2) 420mm x 297mm $4950 + GST (NORMALLY $7450 + GST)
*Offer expires 30/4/2023