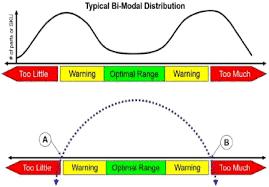
10 minute read
The impact of Demand Driven Material Requirements Planning
Today most manufacturing enterprises throughout the world use a planning method and tool called material requirements planning (MRP) is the availability of the computer assured in the era of MRP. Joe Orlicky brought MRP into the mainstream in his 1975 book “Material Requirement Planning: The new way of life for production and inventory management”. MRP was a revolution for the industry as it featured time phase planning, level by level BOP explosion and dependent demand planning. It promised to synchronize all components needs to end item demand, reduce inventory and improve the ability to prioritize. It changed the method of manufacturing in 1975 only 700 instances of MRP existed in the world with the
Advertisement
release of oral accused book and others
like it, led to the proliferation of MRP throughout the world. It became the life for planning but we should not overlook the fact that MRP was conceived in the
1950’s, codified in the 1960’s and then commercialized in the 1970’s and by 1990 most manufacturers had it. Today almost every supply chain is dominated by MRP systems conveying signals up and down the chain to each other but something is terribly wrong i.e. the people who use the MRP don’t trust them because the use the
spreadsheets to work around the MRP calculations is rampant, several studies have shown that on an average 70% of companies have meant to using spreadsheets.to augment or supplant the MRP planning equations despite them having limited capability, scalability and transferability and addition to that they are also error-prone with nearly 90% of spreadsheets containing some form of error. This is not news to seasonal supply chain personnel and demonstrates how little faith they have in MRP. Therefore, the big question is what happened to the promise of the tool and so to answer the question one basic thing we need to realize is that today’s supply chain look nothing like the supply chain of the 1950’s or 1970’s when the MRP rules were written
but now complex and volatile is the new normal. If these rules have not changed MRP still plans the way it did 50 years ago but now there is a huge gap between the circumstances the MRP was meant for
and the circumstances in which it is
currently being used. This change of circumstances has huge implications for supply chain planning. Supply chains
have elongated and fragmented from global sourcing and distribution efforts while customer tolerance times have
reduced dramatically. This widening gap in time is that stock at some point must be kept in order to service the market. It also means that the planning horizon is farther from actual demand requiring us to forecast farther out and additional stress is
provided by the fact that we have more products with shorter lifespans. All of this means that effectively managing key stock positions is a necessity for properly servicing the market as well as effective capital and resource management.
It also makes detailed item level
forecasting much more difficult. There are three rules of forecasting i.e., the first is they start out wrong, secondly the longer the range the more wrong they are and lastly the more detailed the more wrong they
are. So how a modern MRP system dealing with these changing circumstances, in order to demonstrate how these systems are poorly handling the new normal we will use a simple graphic one that mostly anyone familiar with supply chain will be comfortable with. There are two universal
Source:https://journals.pan.pl/Conte nt/113087/PDF/5-Pekarcikova.pdf point of inventory point A is ‘Too little’ component shortages and miss sales are experienced at this point and Point B is ‘Too much’ – there is excess cash

capability materials and space committed at this point. At both of these points flow breaks down, if we know that these two points exist then we should also have an idea that somewhere between the points there must be an optimal range, a level that is needed to protect flow without being excess. But still most companies exhibit what is known as bimodal
distribution. Most of the inventory is either in the too low or too high range very little is within in the optimal range which is worse yet MRP run typically results in an oscillation which shifts from one extreme to the other
this issue is reported by almost 90% of the companies while using MRP. Issue with the bimodal distribution is devastating to the bottom line, it means chronic and frequent shortages while also having excessive inventory and incurring high expenses due to expedite and waste still this is only at the single company level and a single
company is only one component of the collective supply chain.
The collective problem is the one that wreaks havoc on modern supply chains; it is called the bullwhip effect. It is the transference and amplification of variability up and down the chain, it is bidirectional. Issue with the bimodal
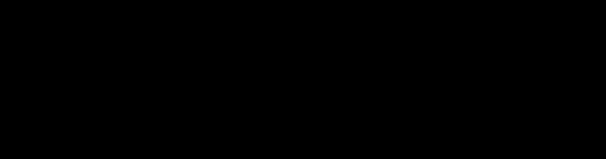
distribution is devastating to the bottom line, it means chronic and frequent shortages while also having excessive inventory and incurring high expenses due to expedite and waste still this is only at the single company level. The more parched to the chain the worse the effect any lasting solution to the bullwhip must address the bi-directional nature of the
problem. This brings us to the demand driven material requirements planning (DDMRP) is a method to model plan and manage supply chains to protect and promote the flow of relevant information and materials.
DDMRP uses strategic decoupling points to drive supply order generation and management throughout supply chain. It was first introduced to the world in the third
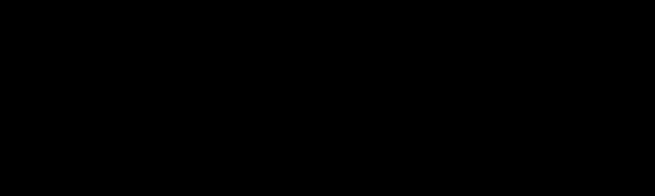
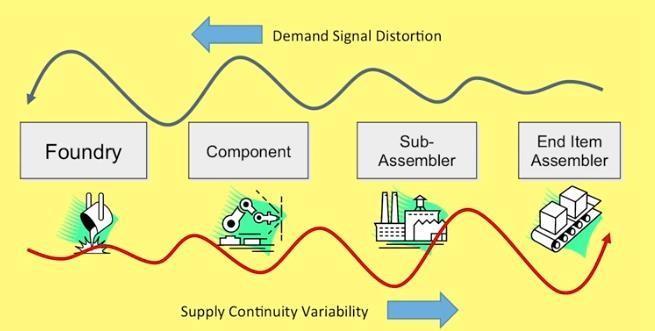
Source:
https://www.demanddriveninstitute .com/ddmrp
Source:
https://blogs.sap.com/2019/02/ 17/s4hana-demand-driven-mrpddmrp-functionality/
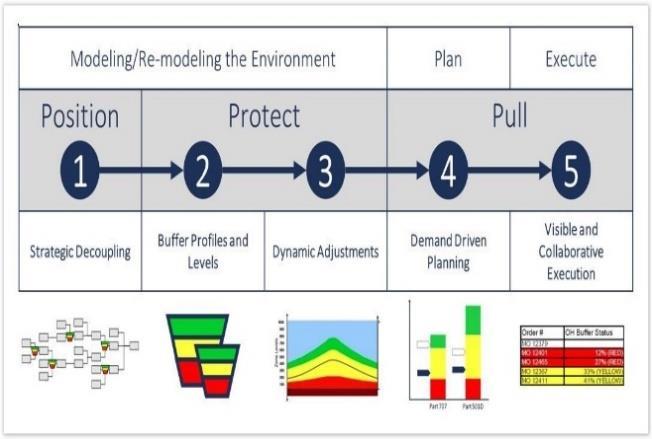
edition of the Orlicky’s Material Requirement Planning. After 15 years of research and application through innovation it fuses key planning requirements with today’s prominent flowbased improvement methodologies.
It can best be summarized as position protect and pull. DDMRP has five sequential components i.e., strategic decoupling, buffer profiles and levels, dynamic adjustments, demand driven planning and lastly visible and collaborative execution. DDMRP
strategically places the coupling points of inventory within the product structure and supply chain.
These points are carefully selected through a variety of factors; the placement stops the transfer and amplification of variability in both directions of these strategic points as well as planning horizons shorten and leave time compress immediately. In this figure we see the difference between the MRP and DDMRP view
planning. MRP couples every activity together this produces a longer plan lead time which means that date and quantity changes and one thing affects everything on the right whereas DDMRP design decoupling points have been used to create shorter independent planning horizon that stop the cascading effect of changes at critical areas, in this the market lead time is compressed to one week. The critical difference is that MRP was never
designed to decouple, it makes everything dependent forcing longer planning horizons and introducing massive amounts of system nervousness.
The second component of DDMRP are buffer profiles and levels, this is simply
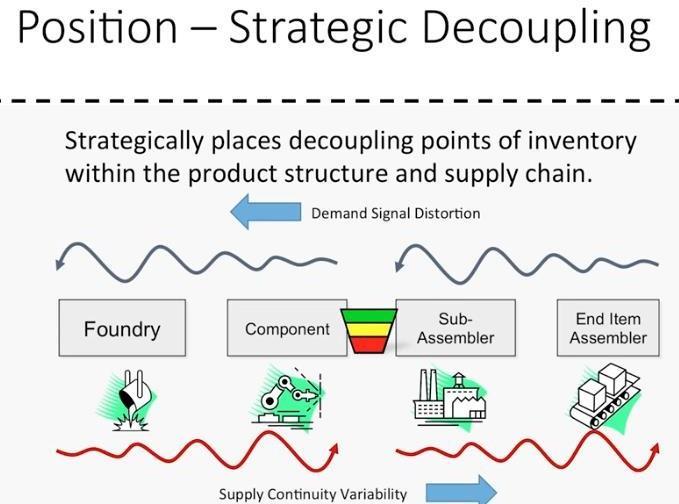
Source:
https://www.scmo2.com/2019/ 07/01/the-what-and-why-ofddmrp/
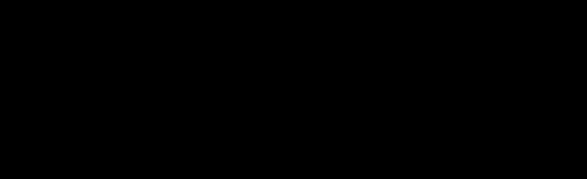
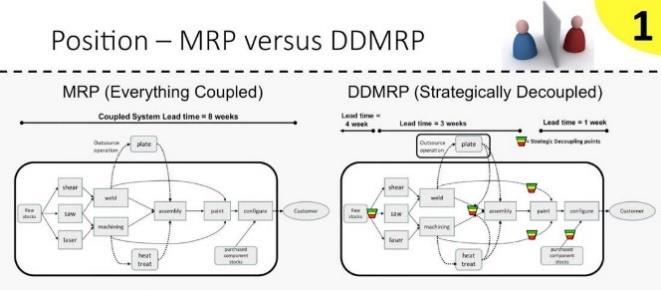
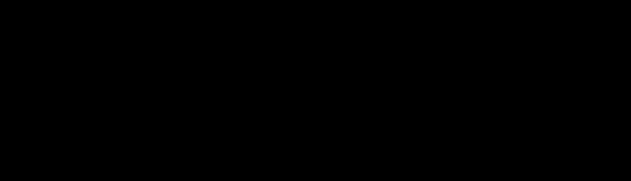
Source:
https://www.demanddrivenin stitute.com/ddmrp
Source:
https://slideplayer.com/slide/1226 6426/
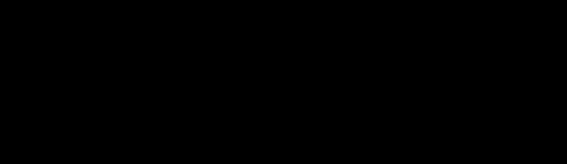

building the level of shock absorption at the decoupling point so that it can mitigate variability in both directions, part demand information based on historical
and/or forecasted usage rates is combined with the DDMRP part settings to create a unique color coded three zone buffer in which each zone has a well-
defined purpose and a particular method to calculate it. The critical difference is that
the DDMRP was designed specifically for the management of key stock positions whereas MRP was never intended to
manage stock instead its intent was to be the perfect make to order calculator negating the need for stock that is the reason why MRP nets to zero and DDMRP never nets to zero.

Don’t be fooled by the concept of safety stock it was forcibly grafted onto MRP due to increasing levels of variability the safety stock mechanism is an inelegant and ineffective stock management tool and, in many cases, exacerbates the bullwhip effect by introducing additional demand signal distortion that ultimately require high levels of overall supply chain inventory and
expenses.
Since safety stock doesn’t a couple at best that can be distinguished as a sequence of fire extinguishers when firms and supply chain really require a series of strategically placed and managed firewalls. The next component of DDMRP is dynamic buffer adjustment, once the initial buffer sizes are set, we know that things will
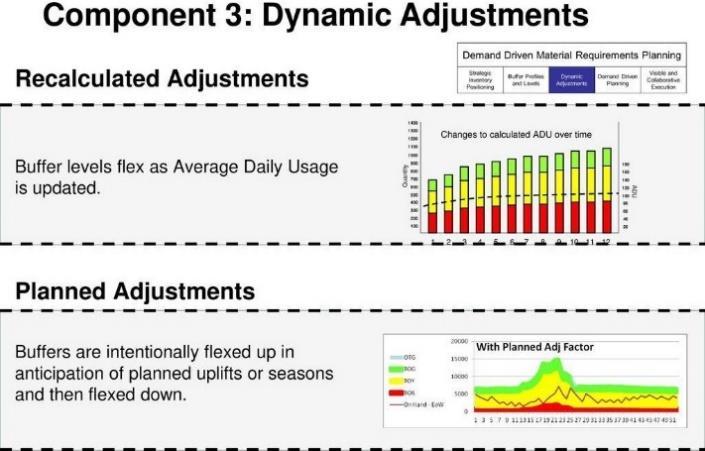
Source:
https://slideplayer.com/slide/122 66426/ change. DDMRP allows the buffers to flex up or down with either changes to actual usage or anticipation of events or seasons. The critical difference is that most safety stock and order point systems are static and not dynamic.
The fourth component of DDMRP is Demand Driven Planning. In DDMRP, planning is the process of generating supply orders in order to do that DDMRP uses a unique equation. The demand element of that equation has no forecasted orders. Conventional MRP planning uses planned orders derive from forecast to generate orders in anticipation of need over a longer planning horizon. DDMRP uses only qualified sales orders within the immediate allocations. A critical
difference in the quality of the demand signals. A sales order is highly accurate, is an explicit statement of what will be
consumed while planned orders are highly inaccurate. This unique supply order generation equation is called the Net Flow Equation. The quantity on hand is added to the quantity of open supply, then quantity of quantity demand is subtracted this produce the day’s net flow position if the day’s net flow position is below the top of the yellow zone an order is issues for the amount to reach the top of the green zone. Once again DDMRP is designed to never net to zero.
The final component of DVMRP is visible and collaborative execution. In DDMRP, execution is about the management of open supply orders. DDMRP uses easy to interpret signals on open supply priorities against the on-hand buffer position, the lower the on-hand level the higher the threat to maintaining flow and the higher the execution priority that’s a critical

Source:
Conclusion
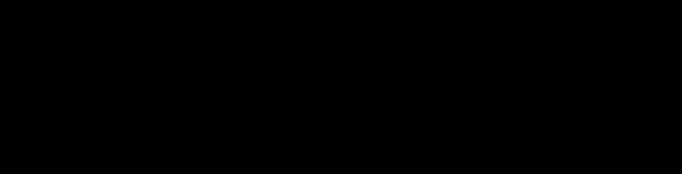
Overall, DDMRP is proven to allow companies plan execute in optimal ranges strategically chosen points that means flow is protected and promoted. The typical benefits of DDMRP are compelling such as:
• The users consistently achieve 97 to 100% on time filler rate performance.
• Lead time reduction in excess of
80% has been achieved in several industry segments.
• Typical inventory reductions of 30 to 40% are achieved while improving customer service.
• Costs related to expedite activity and false signals are largely eliminated
• Planners have relevant
information; they see priorities instead of constantly fighting the conflicting messages of MRP.
In a long-term basis, DDMRP can be very vital in the growth of the different industries which are heavily dependent on the
difference between MRP and DDMRP is
that MRP assigns priority by due date while DDMRP assigns priority by buffer status. This will produce different views of priority based on arbitrary and constantly shifting due dates while the others show relative
and real-time threats to flow that is both highly visible.
supply chain. It can be the solution for the various loopholes they can find in the material requirement on the basis of demand. The very major factor why companies need to implement these kinds of systems into their workplace is because it will help them in cost reduction which can further help them in expansion and growth.
Ayush Bansal MBA 2020 - 2022
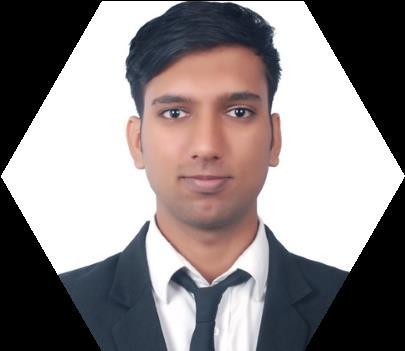

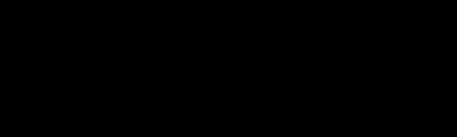