ALEC SUSTAINABILITY & ESG REPORT 2022
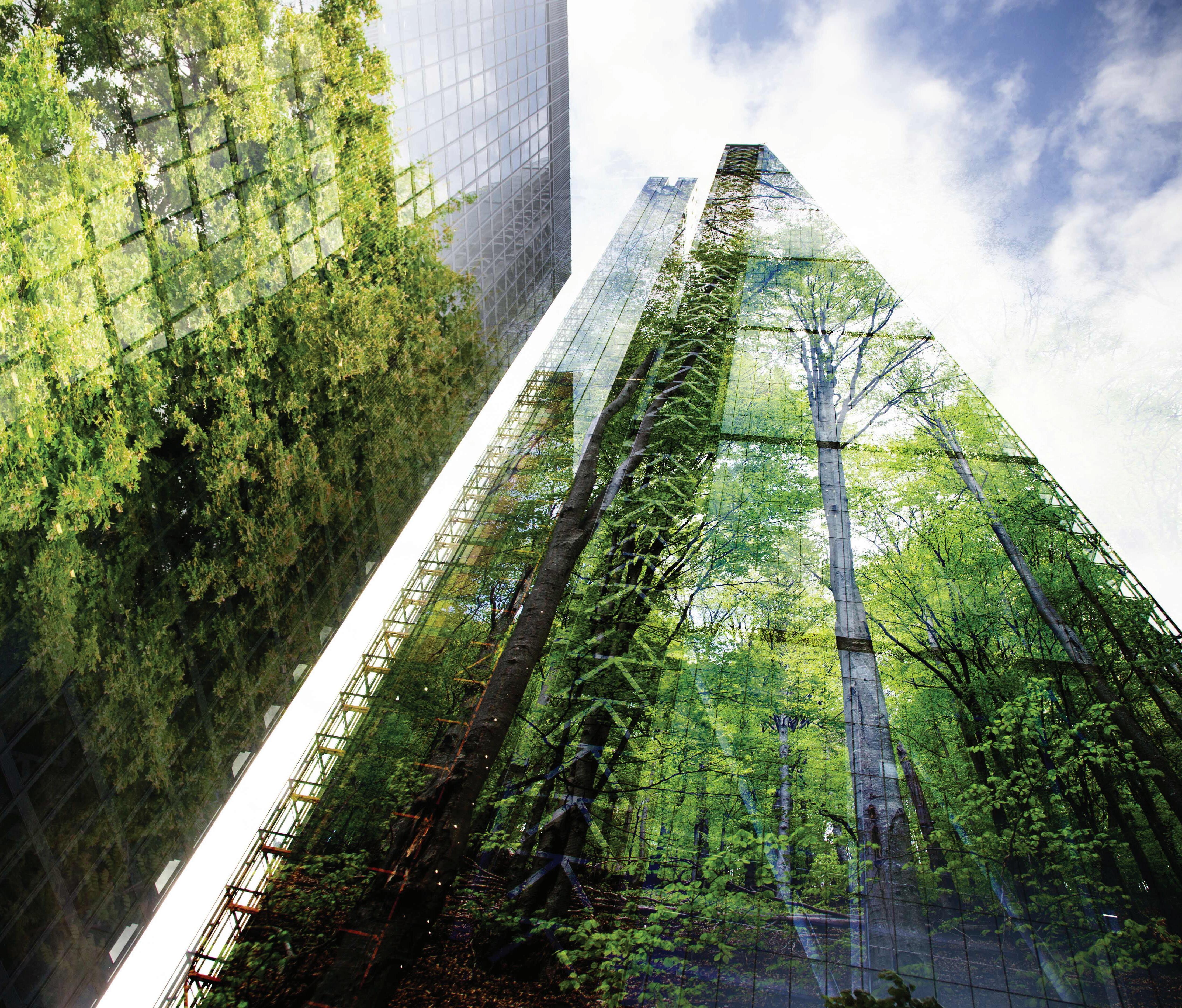
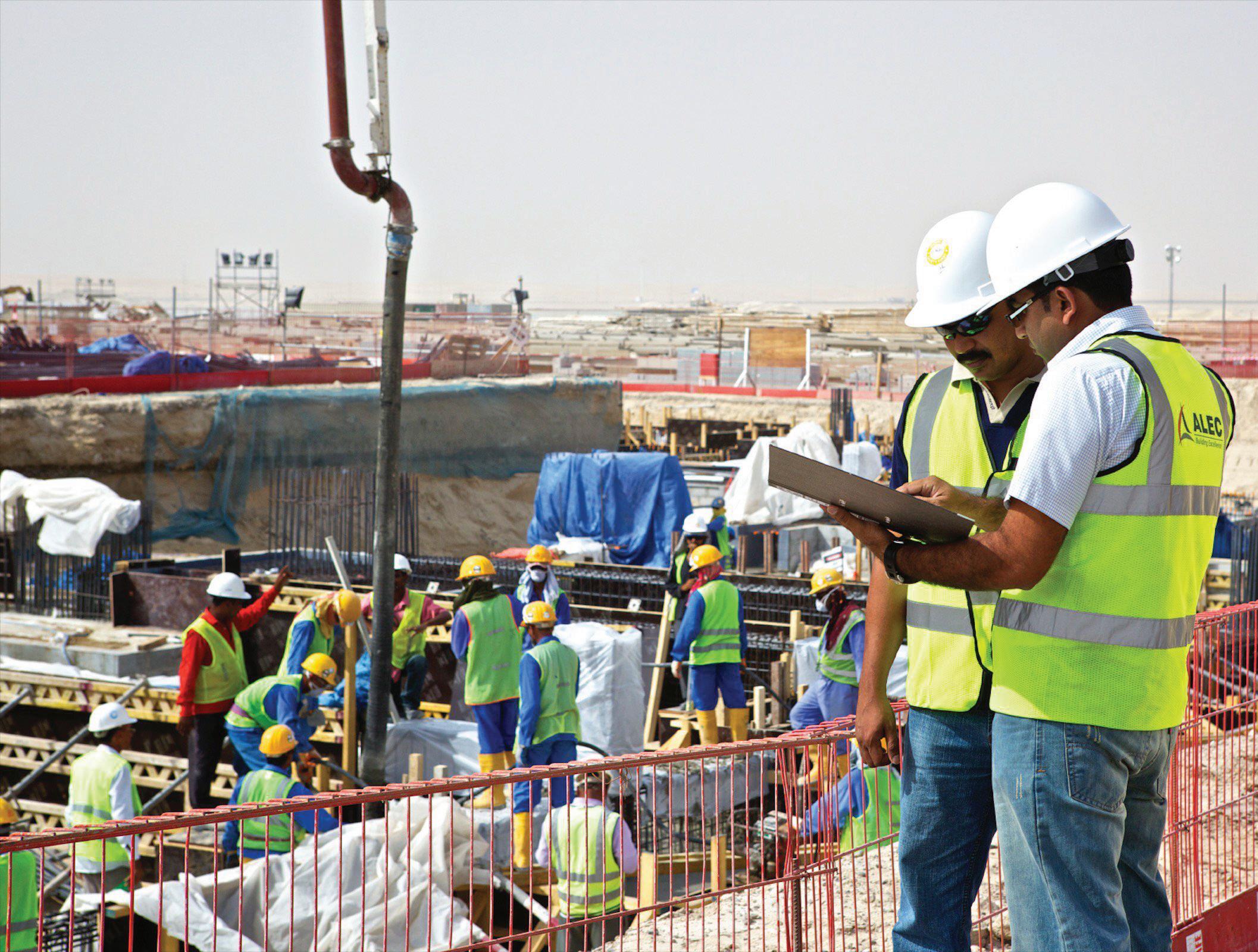
We are proud to present ALEC’s first sustainability report, providing an overview of our commitments to environmental, social and governance topics.
Scope & boundary:
This report covers our UAE operations, comprising occupied assets (owned offices, yard, factories, labour accommodation), project site offices and operations across projects, where ALEC is the main contractor (referred to as main projects) or has operational control. The report excludes our operations in other countries as well as operations related to new acquisitions & joint ventures in 2022 like Target Engineering. To the extent possible, considering data availability limitations and the reporting boundary, the report contains disclosures related to our corporate and main projects-related data, unless otherwise stated in the reporting criteria. We aim to expand the scope of reporting in the following years to ensure completeness.
Reporting Guidelines:
ALEC uses international frameworks and reporting guidelines listed below as a guide for our sustainability reporting. At this stage, ALEC does not claim compliance with these standards, but as we mature in our data reporting capabilities, we will look into aligning with these standards.
•Global Reporting Initiatives (GRI) Standards
•Dubai Financial Market’s ESG reporting guidelines
•United Nations Global Compact’s 10 principles
•United Nations Sustainable Development Goals (SDGs)
•Sustainability Accounting Standards Board (SASB) – Engineering & Construction Services (IF-EN) metrics
The appendices contain the board details, 2022 ESG disclosures, reporting criteria and reporting framework mapping index to help readers navigate to the related topic areas. We also link our initiatives to the local and national priorities, including the UAE’s decarbonisation plans. We will restate our 2022 emissions data based on additional data availability, and review of our carbon accounting methodology, if required.
Reporting period:
This report covers the period from 1 January 2022 to 31 December 2022. In some instances, we have also referred to data pertaining to key aspects of our business from 2021 or earlier and mention our plans for 2023.
Feedback
We welcome feedback on ALEC’s ESG strategy, sustainability activities and performance. Please contact sustainability @alec.ae.
Cautionary statement regarding forward-looking statements
This report contains certain forward-looking statements that typically contain words such as “anticipate”, “believe”, “expect”, “estimate”, “forecast”, “intend”, “plan”, “project”, “aims”, “seeks”, “may”, “will” or similar expressions. Such statements are based on assumptions made using currently available information that is subject to a range of uncertainties that could cause actual results to diverge from these projected or implied statements. Any forward-looking statements contained in this report are therefore not promises or guarantees of future conduct or policy, and thus ALEC and its subsidiaries assume no obligation to publicly update any statements made in this report. ALEC and its subsidiaries rely on information obtained from different third-party sources believed to be reliable but does not guarantee its accuracy or completeness.
Purpose:
Transform the construction industry towards a sustainable future
We believe in upholding the highest standards of integrity in all our interactions, which includes maintaining transparency and ethical behavior. This helps us build trust with our clients, partners, and employees, which is crucial for the success of our business.
Vision:
To be the leading innovative Construction Group
Our commitment to courage drives us to take bold and innovative approaches to our projects, even in the face of challenges and uncertainty. We encourage our employees to be proactive and to embrace change as an opportunity for growth and improvement. This value helps us stay at the forefront of our industry and deliver exceptional results for our clients.
Reliability is a cornerstone of our business, and we take pride in delivering our projects on time, on budget, and to the highest standards of quality. We strive to build lasting relationships with our clients and partners based on trust and reliability. Our commitment to excellence in project delivery is reflected in our ISO certifications and our track record of successful projects across various sectors.
Strategy:
To provide construction solutions with aligned capability, resulting in enhanced stakeholder success
We place great importance on our employees and their well-being. We recognize that their talent and dedication are critical to our success. This is why we strive to create a supportive and inclusive work environment that fosters personal and professional growth. We invest in training and development programs, provide competitive compensation and benefits, and encourage a healthy work-life balance.
We believe in the power of innovation and staying ahead of the curve. We encourage our employees to think creatively and challenge assumptions to seek out new opportunities for growth and improvement. We invest in research and development to deliver innovative solutions that meet the evolving needs of our clients.
Our passion is the execution of complex and iconic projects. We are proud to be trendsetters in the region – whether it is exceeding clients’ expectations in quality or challenging ourselves to continuously innovate our methods of construction, digitising our processes, while also standing out in the industry in the way we care of our people – not just our employees but also our supply chain partners.
We build high end complex projects such as airports, retail, hotels & resorts, high-rise buildings, themed projects. Data
ALEC is part of the Investment Corporation of Dubai (ICD) and has extensive experience in construction management, estimating and cost planning and procurement. ALEC possesses a Design and Build capability, which enables us to provide integrated construction solutions to our clients. Its construction arm is proficient in complex projects across a variety of sectors, which include airports, retail, hotels & resorts, high-rise buildings, and themed projects.
ALEMCO, a Mechanical, Electrical and Plumbing company, provides the skill, expertise, experience and resources essential to meet the demands of today’s fast track projects.
The key services that ALEMCO provides to clients include turnkey electromechanical construction services, planning and design & build engineering services. We also offer facilities management and long term maintenance contracts to ensure efficiency and sustainability of our MEP installations.
ALEC Data Center Solutions provides specialized data center solutions to deliver resilient, sustainable solutions to house, maintain and protect your data and critical assets.
ALEC FITOUT specialises in the fit out and refurbishment of hotels & resorts, cinema, commercial offices, retail, cultural and luxury mixed use developments in the UAE, Qatar & Oman. Utilising our in-house network of specialist contractors coupled with our extensive local and international supply chain we offer a complete interior solution fulfilling the need for project management, engineering, value engineering, design build, procurement and out all under one contractor to the highest standards of workmanship.
ALEC Technologies provides complex fully integrated ELV systems in the region with a team of passionate technical professionals.
Our team provides a range of services aimed at meeting your technical needs.
- ICT Systems AV Systems - Guest Room Systems
- Security Cameras IOT / Automation Systems - Car Park and Automation
AJI is a rental operation with the focus on the rental, sales and services of Aerial Work Platforms.
The rental operation has been formed and managed by a combination of experienced and regionally established parties.
ALEC ENERGY is a provider of solar energy. We offer financially sound green energy solutions. We provide an efficient turnkey solar solution for your commercial & industrial rooftops to ensure maximum return on investment and sustainability.
LINQ is a manufactured housing solution provider that integrates industry best practice with high-quality materials, resulting in a product that can be transported and assembled anywhere and that can operate sustainably in any environment. Manufactured in Dubai, UAE, within a controlled production environment, LINQ provides consistent quality with significant improvements to overall project durations, while reducing material waste and energy consumption.
AES is a solution-oriented, integrated trading platform that aims at disrupting the traditional procurement value chain for developers by connecting them to experienced, cost efficient, and technologically superior suppliers in the world.
The platform is a consortium of relevant, experienced, and motivated stakeholders that have come together in order to address their own procurement requirements and offering the same to large developers of scale.
Data includes main construction projects under ALEC and ALEMCO & ALEC FITOUT in UAE.
As we navigate the challenges and opportunities in the ever-evolving construction sector, we want to take a moment to reflect on some of our most critical responsibilities – environmental sustainability, social responsibility, and business governance.
At ALEC, we’re aligned with the UAE’s strategy to achieve net-zero emissions by 2050. The construction industry plays a pivotal role in shaping our world, and with that influence comes a profound duty to protect and preserve our environment. Our commitment to environmental sustainability in the construction sector is a testament to our values and dedication to leaving a positive legacy for future generations.
By embracing sustainable practices, we not only protect the environment but also strengthen our resilience as a business. We invite each of our stakeholders to join us on this journey towards a more sustainable future.
Together, we can make a significant difference in the construction sector and set an example for others to follow. Let us work hand in hand to build a better world – one that is environmentally responsible, economically prosperous, and socially equitable.
The ALEC Group is committed to the three pillars of ESG and we aspire to set our company targets aligned with the aspirations of the UAE vision for net zero by 2050. We have a robust road map for our journey marked by specific milestones and metrices which will guide us to successfully achieving the vision. Our commitment to this journey is a testament to the core values which underpin our daily actions.
Sean McQue Managing Director - ConstructionWe have always believed that our success is not solely measured by our financial performance but also by our commitment to environmental stewardship. We firmly believe that quality and sustainability are inseparable partners on our journey towards excellence. In the construction sector, where our work significantly impacts the built environment and future generations, our commitment to these ideals is non-negotiable.
Kobus Dreyer Group Commercial DirectorWe are unwavering in our commitment to adopt sustainable practices in every facet of our work. This includes minimizing our environmental footprint by implementing innovative construction techniques, embracing energy-efficient technologies, and championing responsible waste management. Our aim is to not only meet local and global environmental standards but to set new benchmarks for sustainability in the region’s construction sector.
Sustainability is no longer a choice but an imperative in today's construction landscape. It encompasses not only environmental stewardship but also social responsibility and economic viability. Sustainability goes beyond regulatory compliance; it is our compass for responsible decision-making. Together, we can set new standards, create greener communities, and demonstrate that responsible construction is not only possible but profitable.
ALEC AWARDS / POWERLISTS:
6
13 RELATED BUSINESS AWARDS / POWERLISTS:
7 PROJECTS ACHIEVED LEED CERTIFICATION
Platinum
• Saudi Arabia Pavilion EXPO 2020
• UAE Pavilion EXPO 2020
GOLD
• ADNOC New Head Quarters
• Mirdif City Center
• Mobility Pavilion EXPO 2020
4 PROJECTS ACHIEVED
PEARL ESTIDAMA RATING
PEARL 2
• Abu Dhabi Airport transfer baggage facility
• Abu Dhabi Airport arrivals hall & tunnel
• ADIA car park
PEARL 1
• Yas Waterpark
17 PROJECT AWARDS:
5 DEPARTMENTAL AWARDS:
SILVER
• Conference and Exhibition Centre EXPO 2020
LEED NC 2.2
• Dubai International Airport (C4)
1 PROJECT ACHIEVED
GSAS CERTIFICATION
GSAS 3 Star
• Doha Festival City
ONGOING
6 PEOPLE AWARDS:
1 ONGOING PROJECTS
UNDER PROCESS FOR
LEED CERTIFICATION
GOLD
• One Zaa’beel
4 ONGOING PROJECTS
UNDER PROCESS FOR PEARL ESTIDAMA RATING
PEARL 2
• Sea World
• Natural History Museum
• TeamLab Phenomena
• Yas Waterpark Extension
ISO 14001: 2015 Environmental Management System
158,632.21 kWh of renewable energy produced on site at ALEC yard
Solar-diesel hybrid generator used on one of our main construction projects
Recycling rates across main projects active in 2022: 83%*
Recycling rate from project start till Dec 31, 2022
ALEMCO Offsite Construction
LINQ Modular Construction
ISO 45001: 2018 Occupational Health & safety Management System
0.033 LTIFR
100% HSE managers NEBOSH certified
43,337 employees and directly supervised subcontractors underwent the worker welfare induction training
8,700 employees upskilled at ALEC trade skills training facilities
484 employees engaged in innovation & 73 rewards for innovation ideas
49+ Nationalities
10% of our senior managers are women
Parental leave: 90 calendar days (Female)
7 calendar days (Male)
100% parental return rate
ISO 9001: 2015 Quality Management System
BSI Kitemark ISO 19650
Information Management using Building Information Modelling (BIM)
25% female on board
• Number of projects with approximate value of AED 46 Billion successfully delivered since inception: 270+
*Includes ALEC, ALEMCO, Fitout main projects
To identify, analyse and address material ESG issues for our industry, especially within our scope as an engineering and construction contractor, we reviewed material topics and metrics from international guidelines and frameworks such as Sustainability Accounting Standards Board (SASB), Morgan Stanley Capital International (MSCI) ESG Material map for Construction & Engineering, Dubai financial Market (DFM) & Tadawul ESG reporting guidelines. We aim to strengthen this materiality assessment by conducting a survey of our internal and external stakeholders in 2023-2024 to ensure our initiatives and goals match their expectations.
ALEC’s ESG focus areas are directly in line with the national priorities laid down by the national priorities and are underpinned by the UN Sustainable Development Goals (SDGs).
Environmental, social, and governance (ESG) factors are the key measures of a business’s sustainability and societal impact within the construction ecosystem.
Emission management
Waste management & Circularity
Green Building & low-carbon solutions
Climate Change Adaption & Mitigation
Health & Safety
Worker Welfare
People Management & Development
Wellbeing & engagement
Diversity, Equity & Inclusion
Community Impact
ENABLERS
SUSTAINABLE DEVELOPMENT GOALS (SDGS)
WE FOCUS ON:
ERP System
WE
Construction Quality & Compliance
Fair & Ethical Conduct
Responsible Supply Chain
ESG & Climate Risk Oversight & Management
Data Privacy & Cybersecurity
To illustrate our commitment to sustainability, ALEC has joined the United Nations Global Compact (UNGC), the world’s largest corporate sustainability initiative that promotes responsible business practices and the advancement of the Sustainable Development Goals (SDGs) in 2023. As participants of the UN Global Compact, ALEC has publicly committed to implementing the Ten Principles of the UNGC in the areas of human rights, labour, environment, and anti-corruption, and will publicly report its progress on these efforts annually.
Emirates Green Building Council (EGBC) is an industry forum focused on enhancing sustainability in the built environment in the UAE through the promotion of high-performance green buildings and environmentally friendly technologies and products. We aim to use this forum to showcase our best practices as well as learn from industry peers, supply chain partners on opportunities in decarbonizing the sector.
ALEC has been a member of the British Safety Council since 2015, demonstrating our commitment to health, safety, and wellbeing and transparency in reporting.
Strategy
•Develop ESG framework and set ESG reporting metrics aligned to global reporting standards
•Develop Community Impact Strategy & partnerships
•Establish ESG implementation responsibility matrix
•Establish Sustainability committee
•Review and update ESG-related policies and processes
• Enhance materiality assessment through stakeholder engagement
•Establish ESG and decarbonisation targets
•Finalise ESG-related policies and processes across businesses.
•Develop ESG strategy, due diligence and reporting frameworks for joint ventures, acquisitions
Reporting
Implementation
•Collect existing sustainability data for UAE
•Establish sustainability reporting templates for the business
•Publish first sustainability & ESG report
•Launch Community Impact initiatives
•Launch ‘quick win’ environmental initiatives across own UAE operations
•Enhance carbon baseline through increase scope and coverage
•Internal reporting dashboards
•Explore digitising sustainability reporting
•Develop ESG & Climate risk registers
•Establish low-carbon site operations manuals and targets
•Align reporting to global ESG reporting standards
•Undertake pre-assurance readiness testing
Awareness & Upskilling
•Launch in-house ESG & carbon literacy programmes
•Establish ESG & carbon learning development programmes through partnerships
• Launch ESG & decarbonisation strategy training & engagement programmes for top-tier and preferred suppliers and subcontractors.
•Ongoing efficiency projects
•Complete procurement of clean energy through on-site solar generation across all owned and directly-controlled properties, where feasible*.
Some properties are subject to landlord, regulatory and space restrictions for on-site solar production.
•Ongoing awareness and capacity building
A key element of integrating ESG into the business is the adoption of the ESG metrics and integrating these initiatives into project operations not only to report the results achieved, but to make decisions and guide actions. ESG metrics will continue to evolve based on the maturity of our understanding of dacarbonisation regulations, awareness of ESG and evolution of reporting methodologies and implementation.
Emission Management
Finalise a full carbon, water, and waste data baseline to establish current performance to enable setting decarbonisation targets
Waste Management & Circularity
Diversion of waste from landfill
Own:
•Divert from landfill around 75% of waste from offices/ factories/ labour accommodation
Projects:
•Divert 75% of waste from landfill
Green building and low-carbon solutions
Develop and grow our capabilities and services to support carbon emission reduction
Climate Change Adaptation & Mitigation
Develop and implement programmes to reduce emissions from our operations
•Scope 1 (Fuel) emissions
•Scope 2 (Purchased electricity)
•Scope 3 emissions
•Scope 3 categories:
•Category 1: Purchased goods and services (Concrete, Steel, Water)
•Category 5: Waste generated in operations
•Recycling rate
Provide a safe working environment free from harm to employees, visitors and stakeholders.
•0 Fatalities
•0 health & safety-related major non compliances
•Less than 10 health & safety-related minor non compliances.
•Maintain a LTIFR of 0.03
Worker Welfare
Uphold human rights within our operations and influence compliance among subcontractors through screening and audits
People Management & Development
•Attract and retain talent
•Facilitate accessibility to online learning programmes and increase training penetration
•Mapping career progression paths
•Drive fitness, health and wellness initiatives
•Conduct employee surveys
•% projects pursuing LEED certifications
•% projects utilising offsite construction
•% projects featuring modular volumetric construction
•On-site renewable energy produced & used for owned properties
•Adoption/ investment in energy-saving & hybrid solutions within own operations
•Adoption/ investment in water-saving solutions within operations
•% LEED certified entities within operational control
•Investment in circularity solutions
•% revenue invested in ecosystem regeneration
•Reduce absenteeism
Diversity Equity & Inclusion
•Foster diversity and inclusivity
•Inspiring youth to enhance their STEM skills
•Invest in upskilling young adults from low-income backgrounds on transferrable trade skills
•Supporting local community needs through participation in local and national initiatives
•Fatalities
•LTIFR
•Legal cases related to safety-related incidents
• Non compliances on human rights violations
• % employees trained on human rights & modern slavery
• % subcontractors trained on human rights & modern slavery
• % subcontractors screened for human rights violations
•Turnover rate
•Average training hours per employee
•% staff participation in innovation activities
•% coverage of all positions
•No. of unique Innovative idea contributors
Wellbeing & engagement activity participation
• Employee survey participation
• Absenteeism rate
•Nationalities
• Emiratisation
•Age • % women across grades
•No. of beneficiaries
•Volunteering hours
•No. of employees engaged in Community Impact initiatives
Leading the industry in quality and compliance
Lead by example in ethical practices and operate with integrity and transparency.
To support and encourage our partners’ ambitions towards more humane and climate-friendly practices within supply chain
To incorporate ESG & climate risks into decision making
To maintain robust data privacy and cybersecurity policies that protect sensitive information, ensure secure network access and uphold the principles of confidentiality
• Legal cases related to structural integrity claims from main projects
• Instances of liquidation damages
• No. of cases of bribery and money laundering
• % employees trained on ethics & anti corruption
• No. of active projects/ backlog in countries ranking low on Corruption Index
• % subcontractors formally certified compliance with ALEC Code of Conduct
• ICV score
• % subcontractors screened through prequal and procurement process on human rights policies and safeguards in place
• Trainings provided to supply chain to upskill and support subcontractors
• Sustainability governance structure
• Materiality assessment
• ESG & climate risk registers and mitigation plans
• Annual sustainability reports
• No. of ideas generated & implemented through innovation dashboard
• No. of substantiated complaints of breaches or data loss.
The built environment contributes to over one-third of global final energy use, generates nearly 40% of global energy-related carbon emissions and consumes 40% of global raw materials.a
The major contributors to these emissions are the materials used as well as the heating, cooling, and lighting of buildings and infrastructure.b
In the Engineering, Procurement and Contracting (EPC) based model, main contractors are usually brought into the decision-making stage after the building is designed based on client’s Green Building rating ambition, material specified based by consultants’ based on clients’ emission reduction goals and Whole Carbon Life Cycle Assessment (in some cases).
Reducing 'upfront' embodied carbon is easiest during planning and early-stage design, where the largest reductions can be achieved with the least effort. As construction begins, options become more limited, and there is much less that can be done to reduce upfront carbon once the building is operational apart from upgrade or refit of elements.
Our operations are governed by Environmental Management System that conforms to the ISO 14001: 2015 Standard. This system addresses environmental aspects and impacts to identify risks associated with our operations, controls to mitigate them, and compliance with applicable environmental laws and permits.
"We understand the impact of our operations on the planet and commit to reducing our environmental footprint and improving resource efficiency."
Barry Lewis, Chief Executive Officer
DECARBONISING OWN OPERATIONS
1.Generate and use clean energy through onsite solar energy production
2.Upgrade current systems to improve energy efficiency, water management and retrofits, where feasible
3.Enhance waste management through phase out of single-use plastic & reduction in paper usage through digitalisation
4. Develop a carbon emission baseline for the business and creating decarbonisation strategies for high-emitting assets ISO 14001:2015
a: (Source: https://www.wbcsd.org/Overview/News-Insights/WBCSD-insights/Decarbonizing-the-40-How-the-finance-sector-can-drive -the-transformation-to-a-net-zero-built-environment)
b: (Source: https://www2.deloitte.com/ce/en/pages/real-estate/articles/putting-the-construction-sector-at-the-core-of-the-climate -change-debate.html)
The less obvious source of GHG emissions associated with buildings is embodied carbon. It’s already in the atmosphere, quietly warming our planet, by the time materials reach the project site. And for new buildings, its climate impacts are nearly even with those of operational energy.*
Embodied carbon consists of all the Greenhouse Gas (GHG) emissions associated with building construction, including those that arise from extracting, transporting, manufacturing, and installing building materials on site.
While operations may have decarbonisation opportunities long after construction completion, the embodied carbon emissions from construction are set in stone as the project is executed.
The “Cradle to gate” or 'upfront' embodied carbon refers to the emissions associated with only the production of building materials, from raw material extraction to the manufacturing of finished products (which in our case is the buildings we construct). Up-front carbon emissions account for up to 50% of total life cycle emissions.*
Employing modern methods of construction,
(1a) Offsite construction and prefabrication
(1b) Modular volumetric
Digitalising construction: BIM (Building Information Modelling) facilitates collaboration between designers and contractors in real-time. AR and VR technologies allow workers to overlay digital information onto the physical construction site or to immerse themselves in a virtual environment that simulates the construction site. This helps workers visualise the design intent, identify potential conflicts, and communicate more effectively with other team members.
Both these strategic initiatives across our main construction projects result in higher productivity, improving safety and quality, reducing wastage of materials and shorter timelines, thereby reducing overall emissions.
Low-carbon construction site operations
(3a) Reduce dependence on fossil fuel across operating sites
◦ Through onsite solar energy generation
◦ Electrifying construction sites where feasible
◦ Optimise fuel usage through use of technology and behavioural change
(3b) Leveraging and actively pursuing the circular economy model to divert construction waste from landfill.
◦ Reduce generation, enhance segregation and divert waste from landfill
◦ Explore use of recycled and upcycled materials for temporary works, where feasible
4.
Leveraging supply chain to lower product-related embodied emissions
(4a) Engage and collaborate with our top tier suppliers to upgrade our reporting framework to capture emission reduction potential
(4b) Increase current inventory of low-carbon construction material with Environmental Product Declarations (EPDs).
(4c) Offer a launch pad for testing low-carbon alternatives from local suppliers, where available, to identify carbon emission reduction opportunities and encourage the value chain to seek innovation and cost efficiencies for reducing carbon as part of our innovation and R&D activities.
(4d) Offer training to top tier subcontractors and suppliers on decarbonisation
[Source: https://www.mckinsey.com/capabilities/ operations/our-insights/global-infrastructure-initiative/ voices/reducing-embodied-carbon-in-new-construction]
Upfront Carbon (Module A1-A5)
Embodied Carbon (Module A1-A5, B1-B5, C1-C4)
*Based
**Subject
Fuel consumption:
Diesel consumption on projects depends on energy requirements of different phases of the project and the timeline to receive temporary connection. Typically, fuel consumption is high in the initial phases of the project, where power is mainly sourced from on-site diesel generators and use of heavy plant for the substructure and super structure work. Traditional diesel-powered construction equipment used in construction operations contributes roughly 3% of embodied carbon for new-build construction projects*, according to McKinsey & Company analysis.
We expect absolute fuel consumption to rise each year, due to increasing revenue, a growing commercial fleet, our acquisitions and the increased geographical area of major building projects. Our projects, by their inherent nature, are different and span over different years, so comparing year-on-year project-level or comparing absolute carbon emissions does not accurately reflect our decarbonisation efforts. While there are many common activities, the scale and complexity of these varies considerably, leading to very different levels of absolute emissions year-on-year.
One challenge in reducing dependence on diesel generators for power is delays related to approvals required for temporary power connection on site and proximity to existing grid. We work closely with our clients, consultants as well as utility providers to expedite this process, with an average timeline of nine months for securing temporary power connection to the grid. We are hopeful that with the utility companies expanding their network and decarbonisation of the grid, emissions resulting from diesel consumption for the GCC construction industry will reduce over time.
Some of the initiatives to reduce dependence on diesel on ALEC project sites include:
• Synchronisation of generators and optimizing their size based on planned usage
[Source:https://www.mckinsey.com/capabilities/operations/our-insights/global-i nfrastructure-initiative/voices/reducing-embodied-carbon-in-new-construction]
Furthermore, the decarbonisation of vehicles, plant and equipment is a major focus of future action. With steps to increase efficiency of our generators, trial plant and equipment electrification, we expect to see improvement in this area. Advances in vehicles and plant efficiency by suppliers, together with electrification, will reduce all fuel-related emissions and we are working closely with our suppliers to pilot these in our sites.
Solar-diesel hybrid power generator trial
ALEC is trialling a solar-diesel hybrid power generator at one of the construction sites to replace the traditional diesel generators. It is estimated that using this system over the project duration of 23 months will save around 161,850 litres of diesel.
On certain projects, ALEC is contractually obligated to provide fuel and equipment to subcontractors. In order to better manage the utilization of equipment, reduce idling time and minimize wastage of fuel and thereby reduce overall emissions, ALEC installed internet of things (IoT) sensors and GPS track ers on 114 equipment to record run time, utilization hours, idling duration and geolocation. In 2022, we completed pilot roll out of the AI platform that utilizes the IoT sensors to collect vehicle data to improve utilization via common dashboard to provide actionable insights. Within three months, we managed to improve utilization rate, reduce idling, which resulted in saving close to 3,425 litres of diesel.
When we first started looking at improving the efficiency of tower lights in 2015, the average diesel consumption was more than 2 litres/hour. By switching to LED solutions and hybrid tower lights we have reduced this to approximately 1.2 litres/hour. 100% of owned tower lights have LEDs.
At present, 21% of ALEC-owned tools are battery-operated. In 2023, we are undertaking a study to plan the energy transition of machinery. This also reduces the need for cables, generators or compressors, reducing the risk of slips, trips and falls.
Vehicle emissions are driven by fleet size, vehicle efficiency, vehicle use and the location of projects at any given time. Majority of our commercial vehicles carry staff or materials between our yard and construction sites.
We are also currently exploring digitising the delivery management of materials to site and aim to improving logistical efficiency. We will work with our supply chain partners to further streamline and digitise tracking origin of materials, and its delivery to sites.
To monitor air quality on projects, we allocate resources through the Environment, Health & Safety team, refered to as Construction Risk Management (CRM) team within ALEC, to implement, inspect and monitor, maintain air quality in accordance with the Construction Environmental Management Plan approved by the client and local regulatory bodies.
includes:
• Equipment and machinery maintenance programmes for vehicles and combustion equipment to reduce air emissions from poor performance at ALEC Yard.
•Electrification of Plant/ tools
•Dust suppression activities to manage transport-related dust
• Applying dust shrouds and shields when conducting grinding, flooring, MEP installation activities at warehouses/ factories or fabrication yards and projects
• Reducing fugitive air emissions (volatile organics) through spill prevention management of chemical storage and waste minimisation programmes
•Using clean energy sources where feasible
This chart shows the emissions in tonnes of CO2e from purchased grid electricity used on ALEC premises and projects, where ALEC is the main contractor.
Total electricity consumption varies considerably as result of the different projects we are delivering at any given year and also the maturity of the project in that given year, as certain phases of construction are more energy-intensive than others.
We are confident that the decarbonisation of the national grid, as per UAE Energy Strategy 2050, coupled with the various energy-efficiency initiatives ALEC has undertaken will reduce carbon emissions intensity.
Our extensive ISO-certified Quality, Environmental and Occupational Health & Safety Management Systems help ALEC address the global warming-related risks and impacts.
Energy & electricity efficiency projects for owned properties:
Offices/ Factories within direct control:
• Air cooled chilled water system and Variable Refrigerant Flow (VRF) systems in lieu of standard Direct Expansion (DX) systems
•Fresh air system incorporated making for a healthier building environment
•Energy e cient system monitored on Building Management System (BMS) system
During Construction:
Underpinned by our ALEC policies, we enact the project- specific environmental management plans and processes and are subject to external third party audits as well as audits from consultants, clients and regulators.
During project implementation, based on the Environmental Impact Assessment (EIA) studies undertaken by third-party consultants, ALEC prepares a Construction Environmental Management Plan (CEMP) before work commences. The CEMP contains all aspects of the project’s environmental management, which is then incorporated within the ALEC Environmental Management Procedures and control plans & guidelines for heat stress management, waste management and pollution risk control. These risk management processes are further evaluated and approved by the consultant, client teams, environmental agencies and also get audited by clients and federal environmental agencies for compliance.
LED light fixtures for normal and emergency lights
Inverter type Split AC units
Occupancy sensors installed in office areas, toilets, and pantries
Planned for 2023- 2024:
Automatic control of AC units through lighting sensors
Remaining o ces retro t and recon guration
Motion sensor and timers for corridor lighting
Energy e cient system monitored on BMS system, which will be upgraded by full building energy control
Fresh air system incorporated making for a healthier building environment extension of chilled water system in lieu of standard DX system
Power storage and monitoring system
As part of our Scope 1 & 2 emission reduction plans, we aim to increase the total installed solar capacity for our owned properties and those under direct control to 1.45 MWp by early 2024. The only electricity that is not from renewable sources are on properties that are subject to landlord approvals, infrastructure and space constraints for on-site solar production.
Electricity sub meters
In 2023, we are further enhancing our sustainable project site office guidelines to continually improve the energy and water efficiency of site offices and temporary works that are within our operational control. Our permanent works and other site operations are already audited to standards set by the Construction Environmental Management Plan approved by regulators and the client.
Increasing generation of on-site renewable energy:
In October 2022, a 0.501MWp rooftop solar PV plant was commissioned, generating 158,632.21 kWh of renewable energy in 2022. This plant will generate 840.04 MWh of clean energy in the first year.
Increasing generation of on-site renewable energy:
In 2023, we plan on installing solar panels on owned factories and labour camps in UAE.
Supply chain emissions from the materials and products that we purchase in support of successful project delivery are the main contributors to our scope 3 emissions and are covered by A1- A3 of the upfront embodied carbon emissions of a project. These production-related emissions, which lie largely outside our direct operational control, remain a challenge to measure and report on.
At ALEC, we are directly involved in the procurement and execution of substructure and super structure-related works (referred to as ALEC Direct Works) and we typically subcontract the remaining packages. For ALEC Direct Works, main construction materials used are concrete, reinforced steel bars (Rebar) and structural steel along with timber and aluminium used for formwork and scaffolding activities.
For our temporary works, where we have more operational control, we explore reuse of excess materials, pilot low-carbon material alternatives and undertake feasibility studies and gain buy-in from the operations teams.
To increase longevity of formwork and scaffolding stock through reuse and utilisation, we have switched from predominantly wood-based to aluminium items. Given the recyclability of aluminium and its ability to be used multiple times with less upkeep, the wastage of timber-based formwork has reduced over the years.
100% of the wooden formwork girders used in 2022 for ALEC temporary works were. Forest Stewardship Council (FSC) or Programme for the Endorsement of Forest Certification (PEFC) certified.
Materials specifications, including use of chemicals, are in alignment with the standards laid down by the local green building codes and are audited by the consultants appointed by the client, prior to use.
Around 70,000 pieces of bamboo were used to create ICD pavilion at EXPO Dubai 2020 and all natural materials were used for the landscaping; natural grass is used as well trees and plants from the Expo 2020 Dubai nursery. All AV screens, speakers and related equipment has been repurposed internally within an ICD Group company. Overall, 90% of the ICD Pavilion has been repurposed.
For 2022, we have only included concrete, rebar, structural steel used in permanent works and aluminium, steel and timbers used for formwork & scaffolding of temporary works across projects, where ALEC is the main contractor, in calculating emissions.
For permanent works’ materials, we require our subcontractors and suppliers to confirm that all proposed materials have local municipality, Civil Defence and all other related authority approvals / registration and is compliant with any restrictions on the country of origin. All subcontractors and suppliers are required to provide an undertaking that their proposed method statements and materials are in complete adherence to client’s material specifications and the materials undergo a rigorous inspection and testing regime, undertaken by the QAQC teams.
Furthermore, in alignment with client's material specifications, we procure construction materials with Environmental Product Declaration (EPDs). An Environmental Product Declaration, or EPD, is a document which transparently communicates the environmental performance or impact of any product or material over its lifetime. EPDs support carbon emission reduction by making it possible to compare the impacts of different materials and products in order to select the most sustainable option.
Currently, we have EPDs that we have successfully sourced, trialled and used on projects for the following materials.
Overall emissions associated with material use will reduce due to better information on material production and innovation in materials technology. This area will be a key focus of future engagement with suppliers and we will work closely with our suppliers and subcontractors to find more efficient low carbon solutions and encourage capturing that emission reduction impact through EPDs. Consequently, we plan to expand our repository of EPDs for core construction materials and encouraging our supply chain, especially preferred suppliers, to get EPDs for their products.
In 2023 – 2024, we will work on engaging with our main construction materials suppliers to further streamline reporting to understand the current baseline of supply chain emissions. We will do so by upgrading our on-project reporting, prequalification documentation to capture relevant information. Following this, we will prioritise categories of suppliers and subcontractors and embark on supplier induction trainings on our decarbonisation strategy, targets and provide guidelines on reducing emissions.
Floor Coating Paint - Primar Paint - Block Filler Metal Deck Flooring Metal RailingsHandrail Insulation Concrete Structural Steel Stainless Steel Roller Blinds Sealant Traffic Coatings Powder Coat - Paint Structural Sealant383,450,500 10,852,517
82,312,506
TOTAL LITRES
483.45 million litres
TOTAL EMISSIONS
5,560 tCO2e
Water on site is mainly utilised for drinking, hygiene and sanitation and construction activities such as concrete curing, hydrostatic testing, flushing, dust control, waterproofing, pressure tests for Mechanical, Electrical, Plumbing (MEP) systems, flood testing etc.
The construction industry sees high levels of demand for materials, many of which cause environmental and social impacts in their extraction, manufacture and transport, so it is important that we focus on waste and resource efficiencies.
Our current areas of focus are reducing sources of waste through different efficiency projects and streamlining waste segregation.
Reducing paper usage:
1.Default double-side printing and secured access across site offices
2.Default black & white printing ensured less wastage of colour cartridges.
3. Our IT equipment suppliers also reforested 1,065 standard trees on the PrintReleaf Exchange in 2022, to offset total paper consumption at ALEC.
To reduce our dependence on sweet water delivered on site through tankers and associated wastage and transport emissions, we aim to obtain temporary water connection from utility company within nine months or earlier of mobilisation on site. We believe this timeline can be further shortened as the utility network expands and external approval timelines are shortened.
Some of the initiatives that help us reduce water wastage on site include:
•Reduce nozzle diameters for water hoses used for concrete curing
•Aerators for Washbasins, sink, etc.
•Water flow reducer for hand flush
• We use AC runoff, condensation water, dewatering leftover for irrigation & dust suppression, besides sweetwater.
•Submeters across site to identify leaks and water consumption patterns
Ongoing pilots:
•Waterless urinals for site offices and welfare areas
We will continue to improve the water efficiency of our own assets and project site offices and explore systems to reduce the water consumption during temporary works. For permanent works, water efficiency depends on materials used which is prescribed by consultants, and hence we have limited operational control in this area.
4. Over the years, we have been replacing paper-based approvals with e-forms and electronic data management system. These eforms, developed by IT, help digitise requests by using built in templates and support with assigning tasks while creating workflows. Shop drawings, calculations, material submissions, method statements as well as Requests for Information, Work Inspection Reports (WIRs), Material Inspection Reports (MRIs), access permits are mapped digitally. At one of the projects active in 2022, we managed to avoid 5,826,393 printed pages.
Within our facility at DIC we use hydraulic filter carts to clean our equipment fluids and oils to increase the lifespan and efficiency of our owned construction vehicles. Around 9,910 litres of hydraulic oil were saved through use of oil filtration systems.
ALEC has engaged waste management and recycling partners across our offices, factories, labour accommodation and projects. Our project-specific waste management plans are approved by clients, who set the recycling targets, which ALEC has consistently achieved.
Across project sites, we recycle the following materials:
Recycling rates fluctuate over the project lifecycle depending on recyclability of materials used during each stage, which is different for different ongoing projects in a single year, so overall waste recycling rate for projects provides a complete and accurate impact measurement of our waste management initiatives.
2022 Recycling:
58% (Main Projects)
Average project recycling % over project lifecycle until Dec 31, 2022)
83% (Average across main construction projects)
Wood /Timber waste repurposed into:
Sign boards
Fire extinguisher holding boxes
Storage boxes
Concrete waste repurposed into:
Barricades
Paver blocks
Anchor blocks
Excavated soil reused as:
Backfill
Dewatering water reused:
For dust suppression
Plastic waste repurposed into:
Hoarding
Barricades
Chairs and tables
Welfare tents & office furniture:
Reused across multiple projects sites
We upcycle excess concrete leftover from testing/ pouring into precast concrete barriers, concrete fences, concrete manhole covers, staircases and jersey barriers. For projects active in 2022, we managed to divert 1,144 tonnes from landfill concrete through such activities.
Shipping containers modified/ upgraded as workshop centres at DIC Yard & cold food storage on project sites:
No. of containers reused: 26
Excess concrete retained after field tests (slump/temperature tests) are used to produce barricades, foundations for signages.
ALEC has one of the largest in-house quality teams in the region with Green Building expertise, supporting our clients in achieving their Green Building certifications.
Across projects, all relevant ALEC operations and subcontractor staff are trained on various aspects of Green Building requirements at the start of the project. In 2022, 24 ALEC operations team members belonging to operations, MEP and Logistics teams & subcontractors were trained on LEED project requirements.
NO. OF GREEN BUILDING CERTIFIED EMPLOYEES WITHIN QAQC DEPARTMENT:
In 2024, we will collaborate with our waste management partners to further understand end-of-life treatments of some of the waste streams to identify more circular economy opportunities.
We also provide project site offices for our subcontractors, consultants to foster better collaboration. This also helps reduce the number of additional generators, fuel and accessories related to temporary facilities and consequently reduces emissions to less wastage and over purchase of items that can be shared.
Going forward, we will also organise additional trainings to subcontractors to enhance waste management and reporting, especially on subcontracted packages.
ALEC aims to be the first choice for customers who prioritise climate-adaptive design, efficient delivery and long-term value generation and collaboration. Using our expertise in project delivery, innovative value engineering solutions, we collaborate with customers and suppliers to improve delivery efficiency, mitigate risks, digitise construction, minimise waste generation and consequently reduce overall emissions.
In-house prefabrication facilities from ALEMCO:
• Duct Manufacturing – 75% of ducting supplied on contracts is manufactured in our ALEC yard at Dubai Industrial City, except in case of specialist ducting requirement.
• Duct Insulation - Ducting insulation is pre-applied to insulated ducts in factory facilities.
•Bracket & secondary steel fabrication
◦ 60% of bracketing is prefabricated at facilities.
◦ 30% of steel bracketing is manufactured in facility (sent to specialist for galvanising)
• Pipe bending facility – 80% of small-bore piping is pre-bent at facilities (below 50mm diameter)
• ALEMCO modular services – Currently, 15% targeted offsite modular construction. We aim to provide between 20% - 25% of MEPD system installation in modular and prefabricated solutions by 2025.
ALEC Data Center Solutions was established in 2022 to deliver resilient and sustainable data centre assets. While being product agnostic, we use latest construction software to build large scale data centres. We also offer prefabricated DC solutions, with liquid immersion and air-cooled options.
Immersion cooling technology involves using a dielectric coolant to cool servers
Servers installed horizontally in tanks filled with a dielectric coolant. It is an excellent conductor of heat not electricity
Coolant circulated between racks connected via heat exchanger to a chilled water loop for heat removal
Standalone system, does not require chillers, CRACs, CRAHs, or raised floors easily intergrates with legacy infrastructure cool over 100 kW per rack PUE <1.03
Cooling power reduction of up to 95% reduces critical IT load by 10%-20%
Quality Protection Safety
Fully Compatible with IT components
Non-Corrosive Non-Oxidative
Lifespan: 15 years*
Barrier against dust & moisture
Thermal uniformity
Sealed environment
No moving parts
Non-toxic
Certified Biodegradable and food-grade
First Tier 3 approved modular data centre MDCC Dubai Airport**
Staff accreditions: 6* Uptime accredited tier designers
*https://submer.com/business-cases/use-cases/immersion-cooling-for-high-performance-computing/ **https://www.youtube.com/watch?v=Bjn7xKJfyJQ
LINQ Modular, an ALEC subsidiary, builds customised modular units for commercial or residential developments. The modular units are built at LINQ’s 300,000sqft manufacturing facility, which has the capacity to produce 1,900 units per year. The modular building designs are created using BIM (Building Information Modelling) software, ensuring each structure only uses the required amount of material with a minimal amount of waste, the statement concluded.
In July 2023, LINQ Modular received the first regional licence from Dubai Municipality to use the modular design for (G+6) building.
“The pace and scale of developments in Dubai is truly impressive and in line with the Dubai 2040 Urban Master Plan, we are keen to ensure this momentum is maintained in the most sustainable manner possible. We are proud to support innovative organisations such as LINQ, that are pioneering advanced construction techniques such as modular construction. The introduction of this paradigm will translate to the more rapid and controlled production of high-quality buildings that can meet the needs of a wide range of stakeholders, from the hospitality sector to residential developments and even commercial developments like malls and offices.”
Building a strong health and safety culture takes top priority.
Preventing serious injuries and ensuring the offices, warehouses, depots, projects sites have 0 work-related fatalities remains our top goal.
Our ALEC and ALEMCO facilities and site operations in the UAE operate according to an occupational health and safety management system certified to the ISO 45001 and aligned to Abu Dhabi’s Occupational Safety and Health Centre’s (OSHAD) System Framework. Regular site visits from Construction Risk Management (CRM) senior management and the Executive team and daily walkarounds by project leaders demonstrate a clear and visible commitment to health & safety on all of our projects.
Construction site risk management:
On award, the CRM teams prepares task-specific method statements and risk assessments and all subcontractors are required to develop individual bespoke Health, Safety & Environment (HSE) plans, which are approved by ALEC and client, prior to commencement of operations.
ALEC delegates the accountability of managing environmental and health risks to the Project Directors. The Project Directors then cascade the responsibilities to the respective operating teams, who are supported by the CRM and QAQC teams.
During construction
ALEC’s occupational health and safety management systems and associated safety controls are extended to all our 8,491 employees and the 8,116 directly supervised subcontractors we worked with in 2022. Indirectly supervised contractors are required to work in a health and safety system compliant with ALEC’s core requirements, as defined in our Code of Conduct and project-level processes.
Besides the ISO recertification-related audits every third year and an annual third party Abu Dhabi Occupational Safety and Health Center (OSHAD) audit, Self Regulating Audits (SRA) audits are conducted by Abu Dhabi Municipality every three years to maintain our OSHAD approval. We are also subject to client and consultant audits, as specified in the HSE specification of the contract.
In 2022
we launched the digital HSE induction video for all visitors.
Around 745 visitors underwent the online induction. Upon completing the digital safety induction each visitor is sent a QR code that grants them entry to the site.
Suggestions or concerns can be raised via dedicated reporting lines, innovation dashboard, smartphone applications, open suggestion schemes, toolbox talks, safety steering committees, virtual town hall meetings, regular safety meetings and face-to-face with our specialist safety teams. Any improvements or updates to risk identification procedures, as well as associated controls and requirements for hazard elimination, are undertaken following concerns or suggestions raised by any of our colleagues under the guidance of our safety teams.
75%
87 employees of our operational HSE team members, across grades, have completed the National Examination Board in Occupational Safety and Health (NEBOSH) General Certificate programme, and more than
70 employees are Institution of Occupational Safety and Health (IOSH) certified
60%
The CRM team conducts internal audits monthly and subcontractors audits, as per schedule and risk rating. Internal offices and warehouse audits (full or partial) based on risk profile of the project are conducted on a six-monthly basis. The risk profile of the project is determined by the analysis of the HSE statistics and action notice system analysis.
Regardless of their position, every ALEC employee and subcontractor has the authority to refuse or stop any activity that is deemed unsafe. We convey this message as part of our induction and safety refresher training.
Task-specific safety requirements are communicated to staff and directly supervised contractors through appropriate, tailored training events with refresher courses, at a frequency relevant to the degree of risk. Training needs are identified according to assessment by ALEC’s safety professionals and effectiveness is monitored in accordance with our occupational health and safety management systems.
With regards to work-related injuries and the elimination of hazards and the minimisation of risks, we have established the Action Notice system, which is a bespoke online tool utilised for the identification and correction of hazards in the workplace. Thereafter, corrective actions are assigned to individuals and each open Action Notice is tracked until it has been closed out, with reports generated to highlight the shortfalls.
The system allows for data filtration to identify trends within trends that point out root causes of potential hazards and address them according to the hierarchy of controls. Moreover, monthly HIPO meetings and Opportunity for Improvement meetings provide a structured platform to discuss various trends across all projects, upcoming high-risk activities, subcontractor issues, training requirements, change management issues and elevation risks.
Winning HSE Awards act as a testament to our long-term commitment in delivering excellent build quality on the grounds of a site that’s safe and efficiently managed.
Construction Risk Management (CRM) Opportunity for Improvement (OFI) Committee comprises CRM leads with operations personnel and a labour representative from each project and meet on a quarterly basis. Labour representatives are selected and appointed to bring any EHS or Worker Welfare concerns to the committee. The committee is chaired by Operations Support Manager.
Progress Meetings, subcontractor HSE Meetings are held monthly on each project and are attended by all sub-contractor HSE representatives and management representatives.
During 2022 a total of 33,602 action notices were issued, investigated and closed out to prevent reoccurrence.
1 fatality (subcontracted labour)
HSE Awards:
Best Safety Performing Project (SeaWorld Abu Dhabi) – Awarded by AD Municipality in 2022 for our safety efforts throughout 2021.
Positive employee HSE behaviour is identified by management, and employees are rewarded during visible felt HSE leadership weekly walks. Employees are given recognition in front of their peers immediately on the work front and at the end of the month during the safety awards each of these employees, who have been identified during the month will receive a certificate of appreciation and achievement and a gift in front of the entire project workforce.
ALEC Logistics Team Safety Award – Awarded by SWADHuman Rights violations, such as unfair working conditions, modern slavery and child labour in our supply chain is a major risk in the construction industry. ALEC aims to be a leader in safeguarding human and labour rights across our operations by placing safeguards to ensure that these risks are mitigated.
Our Employee and Supplier Codes of Conduct has Human Rights clauses embedded and all subcontractors confirm compliance to this while being awarded the contract. We have zero tolerance for any form of human trafficking, forced or child labour.
Prior to engagement of any agency to recruit semi- and unskilled workers for ALEC, an eligibility assessment is conducted, including client reference checks. Job offers reflect the same conditions of employment as the Ministry of Human Resources & Emiratisation contract and employment contracts. Under no circumstances is any employee forced to accept or sign an offer letter. All workers are made aware of the fees to be paid to the recruitment agency, as per the local country norms, and expected salary prior to employment during out of country induction before signing the offer letters. We ensure that offer letters are signed in country of recruitment by employee and ALEC representatives.
All employees attend an onboarding induction in the country of recruitment. Upon completion of recruitment, the performance of the agency is assessed and a recruitment report is prepared to identify the gaps and areas that need to be improved. ALEC bears all costs of recruitment and ticket including all medical and visa costs. ALEC monitors the process of fees paid by each employee as a declaration document is signed stating fees paid. Reported deviations such as charging illegal fees are dealt with in accordance with sanctions mentioned in the Code, and could include termination of agreements.
ALEC does not impose a ban on any employee should they wish to resign as it is every employee’s right to have the freedom of movement to change employers should they decide to. Under no circumstances are workers threatened to be returned to their home country and or reported to the authorities should they wish to resign or change employer. In 2023, we are digitising manpower forecasting and launching an italk labour app to disseminate information to our labour force through multilingual videos and provide them easy access to different trainings.
• Internet café
• Free wifi
• Volleyball courts
• Badminton court
• Gymnasiums
• Movie theatre facility
• Weekly free transport to public malls
• ATM and Forex money gram facility
• Laundry services
• Barber
• Tailor
Additionally, staff talent acquisition team has a disclaimer on their email signatures, stating that ALEC will never ask for financial cost. ALEC information of any kind or for payment of money during the application document process. We do not require any financial, credit card or bank account are dealt with information and/or any payment in exchange for employment opportunities or other similar services.
Under no circumstances is any employee required to render his or her personal documents for safekeeping to any other person. All employees have the right to retain possession of their own personal documents.
In 2023, we will be conducting a full review and refresh of our human rights safeguards and policies to ensure that it reflects evolving regulatory requirements and developments in industry good practice.
All subcontractors are required to undergo mandatory human rights and labour rights due diligence screening and provide compliance statements, as part of ALEC prequalification.
In our post tender clarification, we require subcontractors to reconfirm that they comply with the requirements related to Worker Welfare as mentioned in the Code of Conduct and have made necessary provisions for the same.
During the year, 0 incidents of modern slavery or human rights violations reported against ALEC through our auditing or internal incident reporting mechanisms.
Workers Interviews: In 2022, 560 interviews were conducted. We recorded 522 issues and 38 remain open. In cases, where the subcontractor failed to resolve the issues, we terminate contracts. Issues raised on these calls were related to Contract transparency, Recruitment fees, Leave entitlement, Passport retention, Wage payment, Overtime and End of Services gratuity.
Happiness Call: ALEC and subcontractors’ workers can raise complaints and suggestions for improvement either anonymously or in person through ALEC-monitored Happiness call.
Audits: In 2022, we recorded 32 cases against subcontractors, of which 1 is still active. Issues raised were related to annual leave, labour accommodation, salary and final settlement, tickets.
Safe Call: ALEC and subcontractors’ workers can raise complaints and suggestions for improvement on client-monitored direct grievance line.
In 2022, 102 calls were received and 100% of them were closed. Issues raised on these calls were related to wage payments, leave requests and entitlement, end of service gratuity and termination as well as employer funded travel (returned ticket/ repatriation ticket).
During 2022, ALEC Worker Welfare team conducted 42 corporate compliance audits (including second audits for high risk subcontractors) to verify compliance to the worker welfare standards as specified within the contract. As part of this, 25 subcontractor labour accommodation audits were conducted. In one instance, ALEC terminated the contract of a subcontractor for violation of our human rights and labour rights stipulations, based on repeated chances and sufficient time to resolve issues that were highlighted during audits.
Our worker welfare teams conduct physical inspections, a dialogue with key stakeholders and subcontractors, discussions with the onsite worker welfare committee, and weekly interviews with a cross-section of workers. Improvement opportunities are identified related to subcontractor grievance management and compliance assurance, and an action plan implemented that subsequently addressed the gaps in our system of control. We also to remind project teams of the importance of remaining vigilant, drawing attention to the findings, especially the importance of effective grievance processes, and maintaining a regular dialogue with the worker welfare committee.
We aim to conduct periodic in-depth human rights audits at our project sites to assess worker welfare conditions and identify any labour rights concerns, as per project specification.
Inspecting subcontractor accommodation: We visit accommodation camps to check that workers (who are typically employed by subcontractors) have safe and dignified living, sleeping, leisure, and sanitation facilities. Where we have concerns, we follow up with the subcontractors, and raise action trackers until they are resolved.
We also operate grievance processes, which are designed to be transparent and accessible, and based on engagement and constructive dialogue.
Labour Interviews: As part of the compliance auditing process, interviews are conducted on a random basis based on the risk profile ascertain through prequalification and onboarding assessment. Any findings or grievances are investigated, and we work collaboratively with our subcontractors to resolve them.
ALEC employs internal security personnel at all operational sites and facilities. When security is required to interface at key access points, we employ security guards with Department of protective systems or Private Security Business Departmen certifications. During each project mobilisation, all security personnel receive formal training in ALEC’s human rights policies, security protocols such as non violence, incident reporting among others.
Our goal is to attract and retain top talent by creating an environment where they are rewarded, challenged, developed and provided with opportunities to grow.
We leverage technology to streamline human resource processes and utilise efficient data-generated insights to inform decision making
We continued to digitise and automate core human resource information management processes to improve the experience of our current and potential employees. In 2022, we standardised and digitised our Interview Questionnaire to elicit responses from interviews that could demonstrate whether their personal values and working styles are aligned to ALEC values and our culture. We also ensure that our interview panel has a diverse set of interviewers, where applicable, to reduce the risk of bias.
We’ve also begun digitizing the onboarding orientation process to further enhance the experience for both the applicants, department managers and the recruitment team through video induction and user-friendly digital forms. Some of the forms include new joiner requests for additional IT assets, referral forms, vacancy requisition form, job offer requests and interview evaluation forms. The digitisation saved time and improved the productivity based on requests.
In 2023, we are working on digitisng processes such as schedule of employment, exit interview, Group life insurance form and employee profile.
Most new roles within the business are advertised internally first. Internal employees who apply for these roles are evaluated for their suitability and if not successful, are provided detailed feedback on their areas for development. For continual improvement of our onboarding process, we are currently structuring our feedback survey from new recruits.
The Marhaba induction, catering to all new joiners, provides them with the opportunity to interact and ask questions to our top leadership and heads of several departments. Led by the CEO, the new joiners are provided a deeper knowledge of our company strategy and priorities and how each of the different departments contribute to these goals. Besides establishing the culture of openness, it also providers new joiners and opportunity to understand how the different departments work cohesively to reach these goals.
No. of employees hired:
Employee turnover (Staff):
Benefits provided to full-time employees that are not provided to temporary or parttime employees
Voluntary (Resigned)
7.26% Involuntary (Terminated/ Retrenched) 3.74%
Voluntary (Resigned)
10.47%
Male (7 fully paid calendar days, vs 5 working days per labour law)
Female (90 fully paid calendar days, vs 45 Days as per labour law)
Total 565 100%100%
61
to
rate 100%100%
Employee turnover (Labour) 2022: 2,040
of Contract 2022
End
ALEC Sustainability & ESG Report 32 OVERVIEW SUSTAINABILITY STRATEGY ENVIRONMENTAL APPENDICES SOCIAL GOVERNANCE
End of Service End of Contract (Internship) AbscondedDeath due to natural cause 002115
8,700 employees were trained on health & safety topics and trade skills aligned to their job profiles
218 employees were trained on communication skills, excel, ethics, presentation skills, collaboration, innovations, management skills.
No. of employees who took study leave
Male Female
ALEC launched Tahadiy to challenge and develop individuals across the company while solving business challenges. Nine challenges were chosen, in line with the company priorities.
The 12-month journey, split into 2 phases, helps participants test solutions across the business. A rigorous process was followed to ensure new ideas are brainstormed, developed and tested. Pilots have been built across the projects and clear business cases were prepared and presented showcasing the value add.
43 employees and 9 mentors participated in the program.
As a result, at least 12 new solutions were implemented and are ready to scale to future projects with potential to save millions.
Phase-2
Identified
Pilots: 25+
Ready to scale: 12
37 employees were promoted from the semi-skilled to staff status based on trainings and assessments.
ALEC’s Safety Cadet Programme, offers the opportunity for successful candidates to significantly increase their income and build a career in HSE. In 2022, two safety cadets were put through the program.
Evolve is an 12-month-long accelerated leadership programme that focuses on developing future ALEC leaders based on the leadership model. Each Leadership trait becomes a module that Evolve participants must work towards and prove that they have achieved the skills, knowledge or behaviours expressed in that module. In 2022, 12 staff were part of this programme.
THRIVE is an 18-month-long Leadership Development program designed to support mid-management level employees on their journey to become senior leaders and to challenge their minds and foster a continuous learning attitude. Modules are mapped out against the ALEC values and showcase what ALEC senior leaders need to demonstrate. In 2022, 11 staff were part of this programme.
In 2022, 4 employees were strategically selected by the company’s management team to attend a two week Leadership Development Program, hosted by the University of Cape Town Graduate School of Business, SA. The UCT GSB Executive Development Programme is a high-impact short course designed to equip senior leaders with the strategic thinking, innovative mind-set and values-based leadership needed to ensure long-term competitive advantage for their organisations.
Employees learn new skills, are encouraged to learn and deliver in new areas of work, interact with and are supported by the ALEC leadership team and others outside of their immediate areas of work. While most leadership development initiatives focus on talent with high potential, this programme is open to all employees across the business, irrespective of their role or seniority.
In 2022, more focus was placed around employee wellness within the business. A framework to support wellbeing was developed and wellbeing champions were appointed across the business to drive engagement around this initiative. A monthly wellness calendar is now published with events taking place in offices and on projects.
Staff:
We organise or sponsor sports leagues for basketball, cricket, football, cycling, rugby.
Around 272 employees (sta and labour) participated in the annual cricket tournament.
Dubai Fitness Challenge:
The ALEC Fitness Challenge including a weight loss challenge, wherein 76 participants in the UAE collectively lost 130.6 kg and 214cm over the 30 days of the tness challenge. Some of the events organised included:
Fostering a diverse and inclusive culture enables us to achieve stronger outcomes together. Diversity is integrated into employee attraction and recruitment initiatives, employee performance review processes and leadership development programs.
In 2022, we are undertaking a Group-wide employee survey to solicit feedback from our employees and ascertain our areas of improvement.
Egypt, 1.4%
United Kingdom, 1.6%
Nepal, 2.1%
Jordan, 2.4%
Bangladesh, 3.2%
Sri Lanka, 3.2%
South Africa, 4.2%
Pakistan, 4.8%
Philippines, 10.9%
Gender
In 2023, we are assessing our existing programmes against the UN Women’s Empowerment Principles to further support the development of the Diversity & Inclusion strategy. We will be establishing new mother’s room across our owned properties.
Emiratisation
In line with our local delivery ethos, and the UAE Government’s Emiratisation agenda, we continue to source local nationals across all areas of the organisation. In 2022, ALEC recruited six UAE nationals.
India, 59.4%
Lebanon, 1.0%
49 nationalities
Given the nature of our business and the location of many of our operations, achieving a better gender balance is a challenge. One focus is our senior management positions and retention through career development and creating an inclusive culture.
Emirati Development programme
In 2022, women accounted for 10% of our senior managers.
Tomohy, which means aspiration, is designed to empower Emiratis and provide them keys skills and insights into the company they are working for. This programme affords local talent a 8 weeks mentored work and learning journey with the business. At the end of the 12 weeks, full time employment contracts are offered to those who successfully complete the programme and wish to pursue their careers with ALEC. In 2022, a total of 19 Emirati nationals took part in the programme, while 6 were hired into permanent roles within the business.
ALEC recruitment team attends career fairs in local universities to create awareness around our business and opportunities available to students.
ALEC has focussed on education as the primary theme for community impact. One of our programmes is aimed at introduction youth to construction by hosting site visits across our projects in UAE.
We hosted project site visits for students currently pursuing a degree in civil engineering at international universities. Nine employees volunteered 13 hours to guide the students and coach them on various aspects of construction and best practices.
Canadian University Dubai:
I wanted to extend my gratitude to the ALEC team for all the effort and time dedicated to showing us around. The students thoroughly enjoyed it, and it was great eye opener for them to see this calibre of building up close and personal as its built.
Timothy Winstanley – Senior Lecturer
The construction team contributed to the students’ construction knowledge. They were eager to show us around the construction site and answer our questions about the project. It was a fantastic learning experience. They did not hesitate to teach us the extreme precision required in an architect’s work.
Leen Tasneen - Student
It was such a nice experience to see a construction site that includes every single detail we are learning from foundations to other heavy structures. We realized different materials and their functionality to materialize the project. This experience would always be remembered, and it is such an honour to thank the construction team and all the labourers who take on such a big responsibility.
Rashid Barhoum - Student
University of Twente:
“I really enjoyed the excursion because of the combination of getting more knowledge into some building processes, and after that seeing how these processes turned out in the actual building. Thank you for the excursion, it really was a once in a lifetime experience.”
Madieke van Oosterhout Student, MSc Civil Engineering
Supporting primary education: We have been supporting 600 children from low-income backgrounds in South Africa through sponsorship of education materials, upgrading school infrastructure, salaries of teachers and sponsoring technical courses since 2012. The funds were used to build fences, enhance the playground, renovate, and refurbish classrooms, restore two heritage buildings and build a new hall.
Annetjie Coetzee, principal, Clarens Primary school, South Africa:
We currently serve 580
Sotho-speaking learners up to grade 7. Most of our students come from very poor, disadvantaged circumstances – living in shacks with their grandparents or family. Despite these circumstances, most of our learners perform well and we strive to create a clean, safe, happy and stimulating environment to exposing the children to a variety of cultural activities and sports activities including athletics, soccer and netball. We also appoint the mothers as teaching assistants so they can get employment and support students with language barriers. We do not charge fees so we rely on government subsidies and corporate sponsors and ALEC has been such a blessing to our school since 2012.
In 2023, we are developing a local delivery model for our community impact initiatives. Our priorities including promoting Science, technology, engineering, and mathematics (STEM) education, improving educational access and employability of youth. We will partner with local entities to attract youth to opportunities within the construction industry and enabling them to get trained to secure jobs. We also focus our donations around supporting the welfare of the large blue-collar workforce in the GCC regions and supporting their development. Besides the Community Impact framework highlighted here, we will also be earmarking funds to support national fundraising programmes on a ad hoc basis for humanitarian crisis and disaster relief.
We teach, sponsor learning for all things construction related
Experiential learning workshops
We sponsor infra projects, provide in-kind support
Participation & contribution to local community programmes (Non-construction specific)
Trade upskilling programme for youth Supporting infrastructure building
Employee skill-based volunteering programme (university seminars, site visits, e-webinars)
Sponsorship/ In-kind support for local & employee-related community activities
2023 Partners:
Our robust Quality Management System and ISO 9001:2015 certification (Design, Project & Construction Management of Buildings & ancillary works) reflects our ability to provide a quality of service that meets customer expectations as well as regulatory requirements. ALEC quality imperatives are focused on the products installed meeting the contractual requirements from a quality and commercial perspective. The contractual specifications are relayed throughout the supply chain ensuring that project specifications are met as a minimum. Regular reporting on progress and other key measures ensures that corrective actions can be taken at an appropriate point in time.
Sean McQue, Managing Director - Construction
QA/QC team identifies the project quality/technical requirements including materials, workmanship & performance and prepares all material submittal schedules, method statement schedules and close out requirement schedules at the start of the project. The team conducts inspection test plans ensuring adherence to project specification requirements and ALEC project objectives. The team manages engineering deliverables, oversees structure inspection and testing of material before use on projects and undertakes detailed inspections and tests at each stage of works before starting subsequent activities. In-house experts complete firestopping and building performance tests for acoustics and envelope air leakage activities as well as manage LEED and other Green Building certification requirements.
ALEC also proposes or recommends, when required, suitable alternative products based on our experience and product reliability and availability.
SUB STRUCTURE SUPER STRUCTURE FACADESoil Tests
•Back ll Soil Selection /Suitability Tests
•Soil classi cation
•Particle Size Distribution
•Atterburg Limits (plastic limit, liquid limit)
•Chemical Properties
•Field Compaction
•Soil Bearing Capacity
Sub Structure Concrete Tests
•Agrregate test
•Cement test
•Water test
•Compressive strength of concrete
•Concrete Durability tests
•Temperature/workability of concrete
•Reinforcement tests
◦ Physical and Chemical Properties
◦ Tensile Strength
•Aggregate Physical and chemical properties
•Cement test
◦ Physical Properties ( Setting Time, Fineness, Soundness)
◦ Chemical Analysis
◦ Heat of hydration
•Water test
◦ Total Dissolved Solids
◦ Chemical Analysis: Chlorides, Sulfate
◦ PH
•Compressive strength of concrete
•Concrete Durability tests
•Temperature/workability of concrete
•Reinforcement
•Physical and Chemical Properties
•Tensile Strength
•Cement Concrete Block
•Compressive strength of concrete
Structural Steel Tests
•Manufacturer's test Certi cates - Chemical / Physical and Strength
Welding Tests
Paint/Coating Tests
•Painting/Coating tests
Wood/Agifiber Products tests/certifications
Emission tests/Certifications
Acoustic Tests
Fire performance tests
Performance Mock up tests
Anchor/Anchor bolts test
Façade material tests (Properties and Emission tests)
Installation Tests
Water penetration tests
Air Leakage tests
Acoustic Performance tests
Paints
•Material /Substrate tests
•Coating thickness
•Emission tests/Certi cations
•Pull o tests
Building Information Modelling (BIM) forms the spine of digital construction/asset operation. It is a standardised process of information management to generate, visualize, exchange, assure and subsequently reuse information, including data, to form a trustworthy foundation for decision-making to the benefit of those involved in any part of an asset’s lifecycle.
Before issue of information spatial coordination must be carried out to ensure buildability and eliminate re-work.
Site verified, accurate and consistent models with added attribute data sets in line with asset information requirements 01
ALEC Direct works models must be developed up to min LOD350 in order to allow any shop drawings or other BIM use with the models
•Shop Drawings
•4D Schedules/Slides
•Quantities
•Interference reports
•Setting-Out
•Asset Lists
Etc.
At the heart of the BIM process is data-rich 3D models, providing the ability to detect clashes and resolve coordination issues to avoid late-stage design and installation changes, thereby reducing the need for rework and improving material optimization during construction. Having the ability to generate and exchange structured data across delivery teams allows ALEC to target data-driven use-cases as well as deliver digital handover aligned to client’s facility management team’s operational requirements. We can extract quantities and volumes of materials for emission calculations and cost analysis, link construction programme activities to the 3D model to visualize construction sequencing (4D) and deliver data required for maintainable assets at handover.
Scheduling / sequencing (4D)
Planning
AR / VR Digital construction/BIM
Model checking / data validation
Digital construction/BIM
Clash detection / reporting Digital construction/BIM
Coordination review / issue management
Design management
Digital construction/BIM Operations
CRM Logistics
Quantity take-off / cost management (5D)
Commercial
Site logistics review for inductions etc.
Logistics
Site setting out Surveying
As-Built verification including laser scanning
QA/QC Operations
•
• ALEC departmental ownership/interaction
Asset data delivery
Digital construction/BIM
QA/QC
Focussing on the information management process aspect of BIM, ALEC achieved the bsi BIM Kitemark certification conforming to ISO 19650-1 & 2 standards. The quality mark helps us drive best practices for information management across all our projects, utilising BIM, giving clients assurance of our capabilities and approach, whilst supporting and upskilling our supply chain. The year-on-year auditing to evidence how the processes and resources aligned to the standards are being put into practice ensures accountability and continuous improvement.
ALEC utilised 4D Construction sequencing across 75% of its ongoing projects, where ALEC is the main contractor, in 2022. For ALEC, irrespective of whether it is a client requirement or not, utilising digital construction is an internal mandate from 2023.
As part of our ongoing Digital Construction strategy implementation, we have streamlined and standardised our core technology stack for BIM, which has greatly improved how effective and efficient our delivery teams are, and has increased collaborative workflows dramatically. We have been able to automate some of the mundane manual tasks by integrating systems while reducing human error and have a repeatable approach across projects.
Models and drawing sheets (DWFx/PDF) imported via plugin to authoring tool
Model viewer / coordination issue management / VR
Information hub for BIM project execution & monitoring resources (permission controlled)
Task
Typical CAD/BIM authoring tools
Common Data Environment (CDE) WIP / SHARED
PUBLISHED
Phase planning & sequencing (4D)
Cost estimation & QTO (5D)
Industry Foundation Classes (IFC) -open file format and data standard
Construction Operations Building information exchange (COBie) –via spreadsheet for maintainable asset data exchange
Optional depending on client / departmental requirements
Software for internal ALEC usage
Collaboration software for wider project team usage
Departmental ownership / administration
Design
Estimating Digital Construction (BIM)
Departmental / project team usage
Design BIM | Surveying Design Design
Estimating / Commercial
All inc. supply chain (& client)
All inc. supply chain (& client)
All inc. supply chain (& client)
All inc. supply chain (& client)
Tendering
Engineering & Procurement
Project stage
Manufacturing and Construction Handover into Operation
AEC Collection: AutoCAD, Revit (design authoring)
ACC Collaborate Pro (Revit collaborative working)
Tekla (design authoring/fabrication for structural steel & rebar)
CostX(5D cost estimation/planning)
Planning
ACC Docs (document management system to fulfil CDE solution)
Revizto+ (3D model viewer, 2D overlay, coordination issue management, VR)
Morta (Database information hub replacing Excel/Word based resources)
Planning | Design Commercial | Operations Planning Planning
QA/QC
Surveying
Operations / Logistics / CRM
All inc. supply chain (& client)
IntAlec (Virtual & Mixed Reality)
Holobuilder (360 progress capture)
Primavera P6 (planning programmescheduling)
Synchro (4D sequencing simulation)
Surveying
Logistic | Operations inc. supply chain
Operations | CRM inc. supply chain
Aconex (document management system to fulfil CDE solution)
Cyclone publisher (laser scan processing / publishing)
LoadGate(plant booking and material pass)
eForms(ALEC internal digital forms, CRM, Manage+)
Common
IntAlec (Augmented Reality) All
Windows and Microsoft O365 (MS. Teams, OneDrive, Office 365, PowerBI) All
ALEC
All
Software for nternal ALEC usage Collaboration software for wider project team usage
Egnyte ( cloud-based document management system)
HIVE (Core ERP System)
Revizto
Collaboration software for interrogating 3D models with 2D drawing overlay
•Built in issue tracker including clash detection
•Virtual reality (VR) compatibility
•iPad / smart phone compatibility for reviewing models, drawings and issues on the project site workface
Revizto implementation is helping to democratise models and data to wider project teams, with estimated 350-400 users across ALEC’s subcontractors, client and consultant teams. Thanks to iPad and smartphone compatibility, the need to print drawings is minimised as users can open 2D drawings aligned to 3D models on the site workface.
ALEC standard on all projects, with supply chain and client teams invited into project license pools. ALEC’s instance of Revizto is now hosted on the AWS Dubai data center, giving UAE clients the reassurance of data sovereignty / residency.
Morta
VR/MR green room
Could-based database for generating dynamic resources with permission-controlled data entry
•Removing Excel based workflows with siloed input, manual error and breakable formulas
•Automating tracking and reporting via API to other systems including Power BI
•Scalable across departments and functions
•Morta is configured as an ‘information hub’ from tender stage through project delivery where BIM documentation, plans, trackers are collaboratively generated and maintained.
Dedicated room for key stakeholder immersive virtual and mixed reality experience on main project
AR app Ability to scan the QR codes on site and overlay the construction model by using Augmented Reality on physical job site
Egnyte
•Site Collaboration with internal and external users
Generating structured datasets with process automation and reducing human error. In 2023, we plan to incorporate corporate office data recordkeeping to Morta.
Loadgate
•Manage construction site deliveries from start to finish using an online asset scheduling.
Interactive planning sessions and immersive ‘walk through’ the construction model. Enable key stakeholders to get a feel for spaces and layouts using the developing construction models for early-stage project planning and enables reduction of rework
•View real-time 3D model locked onto built elements
•Ability to compare as-built with planned model and identify deviations on site
•Fast provisioning with no dependency on hardware availability
•Access the content from anywhere and from any device
•Eliminating the need for VPNs, inefficient backups, DR services, and internet optimization
•Plan site assets in real-time and manage delivery operations across many projects in a few clicks.
•View live dashboards and access real-time reporting for all site assets and delivery jobs.
ALEC has built its success on a foundation of ethical conduct, upholding the highest standards of integrity transparency, and consistently earning the trust of clients, governments, partners, and the wider construction industry.
“Meeting and exceeding new industry standards for quality, operating with integrity and regulatory compliance is what ALEC is known for.”
John Deeb, Chief Financial OfficerCode of Conduct:
ALEC's Code of Conduct sets out the behaviours and norms employees and business partners are expected to follow in their day-to-day activities, in line with ALEC's values of Integrity, Reliability, Courage, Valuing our people and Innovation.
The Code empowers employees and subcontractors to do the right thing, speak up and make suggestions for continual improvement. All new joiners to the company undergo mandatory training on the Code as part of their induction.
We have Employee Code of Conduct covering all full-time and contracted employees as well as a Supplier Code of Conduct, covering all our subcontractors and suppliers.
The Code of Conduct is also available on the intranet (ALEC Central) and any updates are communicated to all employees. For our labour workforce, the company’s policies and Code of Conduct is translated into their local language – both at the time of recruitment in their home country and once again once they get formally inducted within operations.
The Code mandates compliance with relevant legislation and regulations as a minimum standard, covering topics such as:
Anti-trust and anti-competitive behaviour
Confidentiality of information
Discrimination Anti money-laundering
Protecting information & assets
Charitable donations and political contributions
Laws & regulations
Human Rights, Child Labour & Forced Labour
Safe & healthy work environment
Anti bribery and Anti corruption
ALEC’s procurement strategy calls for the establishment of alliances with the best vendors in the market. We like to build a database of reliable suppliers and subcontractors based on the due diligence during prequalification, procurement, post award screening or audit performance, monitoring their performance and based on site operations teams’ ranking of their performance on past jobs.
Business Courtesy (Gifts & Entertainment)
Collusion
Conflicts of interest
Privacy & data protection
We are currently reviewing and updating our policies based on guidelines of the 10 principles UN Global Compact in the areas of Environment, Labour, Human Rights and Anti Corruption.
Developing an ethical culture through employee and supplier training, effective governance structures and internal controls is critical for us to maintain this reputation. We are upgrading our ethics learning video to enhance retention and engagement on the topic.
All stakeholders, including employees, contractors, suppliers and community members, are encouraged to report concerns, questions or suspected violations (by employees, business partners, subcontractors or suppliers) of ALEC’s Code of Conduct through our dedicated email: ethics@alec.ae.
In 2023, we will/ plan to:
• Incorporate the Ten Principles of the UN Global Compact into our strategies, policies and procedures
•Upgrade our ethics e-learning video for employees
•Set up digital annual acknowledgement and adherence to Code of Conduct for all employees
•Strengthen our Conflict of Interest process and reporting
•Publish our first sustainability report for enhanced transparency
ALEC Prequal screening: We seek access to subcontractors' facilities, factories and labour camps as part of our prequal and post-award requirements.
Health & Safety & Worker Welfare:
•Policy
•Summary of arrangements
•Trainings
•Certifications such as ISO 45000, OHSAS 18001
•Audits & seek access to third party audit findings
Quality Standards:
•Policy
•Summary of arrangements
•ISO certifications
•Testing certifications
•Audits & seek access to third party audit findings
•Public policy & commitments
•Whether policy is sent to suppliers
•Whether environmental audits are conducted
•Environmental management plan and summary of arrangements
•ISO 14000 certifications
• Experience in and Level of Green Building certifications such as LEED, Dubai Green Building, Estidama, Mostadam of past projects
•Performance targets related to environment
•Audits & seek access to third party audit findings
•Evidence of training and awareness sessions for employees
•Whether company has been prosecuted for environmental non compliance in past 5 years?
•Whether company was involved in environmental emergencies in past 5 years?
•Manufacturer confirmation that materials don’t have long-term negative impacts?
• Insulation materials with 0 Ozone Depleting Potential and low Global Warming Potential
•Internal Air Quality certifications
•No asbestos containing materials
Additionally, at tendering stage and post tender clarification stage, we also enquire and expect subcontractors to share their subcontracting strategy for their respective packages, along with the programme details. Bidders are also expected to share their value engineering solutions, if applicable, and BIM management capabilities and experience. We also encourage bidders or tenderers to visit the site so they can price all the constraints and challenges they foresee.
“Part of responsible supply chain policy is to give repeat business to subcontractors and suppliers who have demonstrated their capabilities in adhering to the stringent standards we put forth. We try and encourage clients to procure from ALEC-preferred subcontractors that have been vetted to minimise performance risks in projects. The early commitment of key subcontractors as well as a stringent prequalification prior to award of a contract is one of our strengths.”
Kobus Dreyer Commercial Director.
We also reiterate to suppliers that there are no on-site payments for major construction materials delivered and payment will be done as per the payment terms. We take allegations of bribery seriously at ALEC. In 2022, we had one instance of an allegation of bribery of our staff. We hired an external agency to investigate the allegation and the allegation was not substantiated.
Prompt payments: ALEC policy is to commit to pay our suppliers on time in accordance with contractual agreements. We ensure that there is no deliberate delay or unreasonably withholding payments. We communicate our purchasing policy and principles internally and externally. We encourage prompt payment practices throughout the supply chain through formal policies. We do not impose any unilateral change of terms retrospectively.
In 2023, we are upgrading our ERP system to support digitisation of payments management.
We seek information from our suppliers if they have businesses in other countries, where we plan to expand operations. This also helps us with easy access to ‘local’ or ‘locally-connected’ suppliers, who are already preapproved by us, when venturing into new territories. We also seek ICV certificates from all our suppliers and subcontractors, where applicable.
In Country Value score*:
•ALEC Abu Dhabi: 38%
•ALEC Dubai: 39.53%
•ALEMCO Abu Dhabi: 25.99&
•ALEMCO Dubai: 27.42%
The approach to creating a responsible supply chain in construction involves two key elements: collaboration and training. Firstly, collaboration with the supply chain is crucial in ensuring that everyone is working towards the same goal of sustainable and ethical procurement. This includes working together to identify potential areas for improvement and implementing solutions that benefit everyone involved.
Secondly, training and upskilling subcontractors and suppliers is also essential. This can be done at the company's expense and ensures that everyone in the supply chain working on our projects has the necessary skills and knowledge to contribute to a responsible and sustainable procurement process. This includes training on health & safety, worker welfare, environmental responsibility, importance of quality control as well as digitising construction.
As part of ALEC’s BIM Kitemark, we are required to evidence supply chain collaboration. We have workshops with preferred supply chain (PSL) subcontractors, sharing best practices, expectations and direction, challenges and lessons learnt.
Our project-based in-house BIM specialists educate and train subcontractors to use the collaborative software tools we deploy as part of the mobilization process, to make collaboration more effective, efficient and precise. Regular training is held for technology partners such as Revizto, Morta and for AR/VR, covering workflow and software onboarding to best achieve information delivery.
In 2022, we held over 30 BIM induction sessions by ALEC specialists for subcontractors across three live projects. This equates to 90 hours of education and training.
In 2023, we will deploy an internal upskilling training programme to help mass upskilling for understanding information management using BIM according to ISO 19650. We plan to select 100 staff across our departments initially to then determine further roll-out.
Audit Committee:
• Monitors the integrity of the Group’s Financial Statements and formal announcements relating to its financial performance, including reviewing financial reporting judgements contained within them.
• Reviews the Group’s internal financial controls and its systems for internal control and risk management.
• Monitors and reviews the independence, objectivity and effectiveness of the External Auditor, and reviews and recommends to the Board the re-appointment, remuneration and terms of engagement of the External Auditor.
• Develops and implements the Group’s policy on the engagement of the External Auditor to supply non-audit services.
Sustainability Committee:
• Monitor the Company's overall approach to ESG and ensure that the Company complies with applicable ESG regulations;
• Oversee the development/ review of policies, guidelines and processes for matters relating to sustainable development, environment, climate risks as well as community impact and ethical conduct of the Company;
• Responsible for the Company's ESG strategy and management of sustainability matters;
• Ensure implementation of ESG activities is uniform throughout operations, business units and in collaboration with all Group functions.
• Prepare and manage ESG reports for the management committee and Board
Remuneration Committee:
• Sets the remuneration of the Executive Directors, senior management and key managerial personnel
• Oversees the administration of the Company's compensation and bene ts plans;
• Approves recommendations on senior appointments.
• Oversees succession plans for key executive roles
Digital Committee:
Develop and implement ALEC’s digital strategy that is aligned with the business strategy objectives.
• Develop mechanism to govern and embrace the right digital tools and technologies that are required by the business to embark the digital transformation journey.
ESG & Climate Risk Oversight & Management
ALEC’s work on adapting to and mitigating risks faced by climate change is a material governance and strategic issue that has been regularly addressed and discussed by our Board and Executive team.
The Board is responsible for oversight of the overall conduct of the Group’s business, which extends to setting our climate response strategy and approach to the energy transition plans. The Board is assisted by two Board Committees: Audit & Remuneration. The Board is updated on climate-related issues by the Company Secretary, based on inputs from the Sustainability committee that meets quarterly.
Labour subcommittee:
Operations Director, Direct Operations manager, Operations Support Manager, ER Business Partner
•Review company manpower forecasts, develops recruitment plans, review and approve recruitment agencies
•Ensures labour wages are in line with market through wage review exercises.
•Review new policies applicable to labourers, labour accommodations & visits accommodation
•Review happiness calls and feedback from labourers and develop action plans
Ethics Committee:
• Review and update ALEC Code
• Review communications on ethics@alec.ae
• Investigate allegations of violations to ALEC Code of Conduct
Tendering stage:
Evaluation of the project based on ALEC’s core geographies, expertise, customer financial position, customer reputation, previous experience with same client, customer willingness to explore value engineering solutions and competition. Based on this analysis, the leadership team, along with the Director of Operations and head of tendering, either proceed or abstain. During contract negotiation, these risks are laid down and appropriate insurance is secured. Management of commercial risks is regulated by the Commercial Director.
Additional subcontractor pre-qual checks:
Over and above the prequal checklist items related to quality, health & safety, worker welfare and environment, we also screen our subcontractors and suppliers over their financial performance and other risks.
• Whether bank guarantees were denied
• Filed for bankruptcy
• Current litigation with main contractors or developers
• Judgement against in past three years
• Whether Parent companies involved in litigation
• Liquidated damages paid
• Labour law violations
• Defaulted on a contract
• Failed to complete a contract
• Terminated from a contract
• License revoked or suspended
How Sustainability is managed and cascaded throughout operations:
ESG team oversees Group-level ESG and decarbonisation strategy, capacity building and reporting. Focus areas where ESG team does not directly drive implementation, it takes on the role of policy, process reviewer and data auditor and supports with reporting templates, strategy guidelines and target setting.
Environmental topics: ESG team implements projects relating to climate change adaptation and mitigation and is responsible for emissions reporting and reduction strategies for the Group. Facilities management department (FMD), logistics and Plant & Vehicles departments, along with the innovation team, execute projects that improve energy, waste, water efficiency.
Digital Construction team is responsible for BIM implementation and operations teams are responsible for offsite construction, with LINQ handling modular solutions. QAQC department is responsible for compliance and material quality as well as sustainability across projects including LEED, Estidama and other Green Building certifications, while CRM team is responsible for executing project-specific environmental certifications and procedures and reporting.
Social topics: People & Culture team along with the Construction Risk Management (CRM) or HSE, Worker Welfare teams manage the human rights, people management, development, diversity and engagement activities for employees as well as subcontracted employees on site. ESG department develops the strategy for and implements the community impact initiatives.
Governance topics: The CRM team, QAQC and Authorities teams are responsible for the implementation and oversight on construction quality and environmental compliance on projects. Fair & ethical conduct-related activities are jointly managed by the ESG & P&C teams, along with legal and finance departments.
For responsible supply chain, ESG team provides guidance, reporting, policy support, with implementation executed by the procurement, commercial and finance departments.
While climate risk oversight and management is managed by ESG, CRM and legal teams, data privacy and cybersecurity falls under the remit of the IT department.
We are currently assessing the ESG & climate-related risks and opportunities and will be developing ESG risk registers. In order to identify the main types of risk and opportunity and their impact on the business, we will be reviewing the ISSB standards for sustainability-related and climate-related financial disclosures. Our Group’s decarbonisation strategy will be further enhanced after a careful analysis of the risks and opportunities connected to it as well as results from the stakeholder concerns raised during the materiality exercise.
The innovation department is responsible to align innovation strategy with ALEC overall business goals. In addition to instilling the culture of innovation among new and existing employees and developing and nurturing this skills through programs and trainings. The innovation team horizon scans for the latest construction and business-related solutions and partners and supports different business functions in quantifying the impact and developing the business case for their selected innovation projects and reporting their tangible benefits.
ALEC sees innovation as an open and decentralized process. It is decentralized because it is carried out independently in each business unit and related businesses, with the support of and coordinated by the company’s innovation department. It is open because the company involves internal and external stakeholders such as universities, technology centres, suppliers, equipment, and product manufacturers in its innovation process.
Main objectives are to instil a culture of innovation within ALEC, to continually improve, be economically, socially and environmentally sustainable, generate savings through innovation initiatives and offer cutting-edge products and services to our industry.
We have developed our innovation framework to categorize innovation ideas for easier reference and address different areas of our business while tackling the two main streams: leveraging existing business model in addition to business model innovation.
External partners and suppliers that have supported our innovation journey
ALEC works with several external stakeholders such as universities, technology centres, suppliers, startups, equipment, and product manufacturers to support the innovation process. External partners are an integral part of the construction ecosystem, adding value by working alongside ALEC and the supply chain. As ALEC integrates innovation as part of the company’s culture, we believe supporting and creating an opportunity for start-ups, digital companies and other external partners can be exceptionally beneficial for both parties.
Startup Statistics
Startup Engagements
To date : 97
To date : 29
To date : 13
To date : 07
ALEC fully manages the idea lifecycle though bright ideas platform, which is accessible to all employees. Innovation hub provides all employees access to bright ideas platform host the overall innovation database, close out reports that records all the learning from completed initiatives, trainings, knowledge sharing lessons. The innovation dashboard acts as the idea lifecycle management, recording details of ideas generated by employees, number of implemented ideas, number of unique submitters in addition to number of people involved in innovation. Several topic-specific Subject Matter Experts (SMEs) committees assess ideas based.
All projects and business units have their own budgets and are responsible for assessing their individual innovation initiatives based on the submitted business cases. If the initiative is deemed feasible, then the necessary resources get allocated.
ALEC has also set aside a separate budget to assist in driving innovation. The budget includes innovation training and events, allocations for some of the key short and long-term initiatives, and items that might not fall into the departments/projects’ categories.
The innovation department identifies contributors and has a well-defined scoring and reward mechanism. Innovation points collected by individuals are linked to their performance evaluations, to encourage more employees to contribute.
ALEC is committed to maintaining robust data privacy and cybersecurity policies that protect sensitive information, ensure secure network access, and uphold the principles of confidentiality. These policies are essential in safeguarding the company's assets and reputation while complying with industry regulations and best practices.
• Protecting Against Cyber Threats: ALEC IT infrastructure follows ISO 27001 principles, fortified with robust controls, malware protection, identity verification, and disaster recovery. Microsoft Defender for Office365 defends against various threats.
• Detecting and Responding to Threats: Evidence-based reporting guides ALEC's approach to identifying and responding to cybersecurity events. Suspicious activities trigger immediate investigation, isolation, and recovery, supported by a 24/7 third-party partner Security Operation Centre (SOC), with regular security assessments to enhance digital security.
• Securing Endpoints: Endpoint Detection and Response (EDR) solutions protect servers. In addition, EDR integrates with security monitoring, supplemented by Multifactor Authentication to protect users' machines.
• Risk Assessment and Compliance: Regular risk assessments and external audits ensure IT infrastructure integrity. In addition, vulnerability analysis, simulated hacker attacks, and annual disaster recovery testing is conducted to support ALEC against cyber threats.
• Employee Training and Awareness: ALEC promotes employee awareness through training on cybersecurity, and social engineering. Information Security specialist/s receive advanced training, ensuring a well-informed workforce.
In 2022, ALEC had 0 substantiated complaints of breaches or data loss, reflecting our commitment to information security. Our comprehensive approach, aligned with industry standards, establishes us as leaders in safeguarding critical infrastructure while building trust with clients, employees, and partners.
•Master's degree, Business Administration from American University of Sharjah (UAE)
•Bachelor's degree, Civil Engineering from Metropolitan University of Colorado (US)
•Certified accountant with an ACCA qualification
• BA honors degree, Accounting & Financial Management from the University of Essex (UK)
•Master’s degree, Construction Engineering, Imperial College (UK)
•Bachelor’s degree, Civil Engineering, Imperial College (UK)
•BSc Honours degree, Construction Management, University of Witwatersrand, Johannesburg, SA
General Management & Business Operations
CEO Experience
Construction Industry knowledge
Risk Management
Strategy Development
Mergers & Acquisitions
Legal / Regulatory
Corporate Governance
General Management & Business Operations
Accounting
Risk Management
Strategy Development
Mergers & Acquisitions
Legal / Regulatory
Corporate Governance
General Management & Business Operations
CEO Experience
Construction Industry knowledge
Risk Management
Strategy Development
Mergers & Acquisitions
Legal / Regulatory
Corporate Governance
General Management & Business Operations
CEO Experience
Construction Industry knowledge
Risk Management
Strategy Development
Mergers & Acquisitions
Legal / Regulatory
Corporate Governance
HE Abdulla Al Shaibani Kamillia AlMarashi Riad Kamal Kez TaylorEmission Management
Waste Management & Circularity
•Scope 1 emissions [Fuel]
•Scope 2 emissions [Purchased electricity]
•Scope 3 emissions [Category 1: Purchased goods and services (Concrete, Steel, Aluminium, Timber, Water)]
•Recycling rate (%)
•Total GHG emissions: 754,074 tCO2e
•Scope 1: 10,560 tCO2e
•Scope 2: 8,745 tCO2e
•Scope 3: 734,769 tCO2e
•Recycling Rate across projects in 2022: 58%
•Average recycling Rate across projects (complete project duration): 83%
Green building and low-carbon solutions
•% projects pursuing LEED certifications
•% ongoing projects utilising offsite construction
•% projects featuring modular volumetric construction
Climate Change Adaptation & Mitigation
•On-site renewable energy produced & used for owned properties
•Adoption/ investment in energy-saving solutions and hybrid solutions within own operations
•Adoption/ investment in water-saving solutions within operations
•Investment in circularity solutions
•% revenue invested in ecosystem regeneration
•% LEED certified entities within operational control
•100% of Dubai-based main construction projects were in adherence to Dubai Green Building Code
•100% of Abu Dhabi-based projects pursuing Pearl 2 Estidama Rating & 1 Dubai-based project pursuing LEED in 2022.
•For offsite construction, we are working on calculations and will disclose it in forthcoming reports.
•ICD pavilion show home at EXPO 2020 Dubai featured modular volumetric construction
Own operations, project agnostic:
•158,632.21 kWh of renewable energy produced on site (owned properties) in 2022 through a 0.501MWp rooftop solar PV plant commissioned at ALEC Yard. This plant will generate 840.04 MWh of clean energy in the first year.
•Refer to Energy Efficiency & Water Management for details on adoption and investment in energy-saving and water-saving solutions within properties owned or under direct control.
Project:
•Solar-diesel hybrid generator used on one of our main construction project
•21% of ALEC & ALEMCO-owned tools are cordless & battery-operated tools.
•Investment in circularity solutions: Refer to waste management section
•% revenue invested in ecosystem regeneration: ALEC hasn’t made any investments in 2022, and will develop a strategy for the same.
•% LEED certified entities within operational control: 0
Health & Safety
Worker Welfare
People Management & Development
•Fatality
•LTIFR
•Legal cases related to safety-related incidents
•Non compliances on human rights
•% employees trained on human rights & modern slavery
•% subcontractors trained on human rights & modern slavery
•% subcontractors screened for human rights violations
•Turnover rate
•Average training hours per employee
•% staff participation in innovation activities
•% coverage of all positions
•No. of unique Innovation idea contributors
•1 Fatality (Subcontractor Labour)
•LTIFR:0.033
•LTI: 16
•Legal cases related to safety-related issues: 0
•Work Hours LTI-free 2022
•Offices: 1,334,312
•Warehouse 1,434,690
•30 Major non compliances identified during subcontractor worker welfare audits
•43,337 employees and directly supervised subcontractors underwent the worker welfare induction training
•30 subcontractors underwent prequalification screening, onboarding screening & compliance audits post six months, with 42 audits being conducted as some subcontractors were reaudited based on their risk rating.
Refer to People Management & Development section
•Total employees: 8,491
•Staff: 1,925
•% Female: 10%
•Turnover Rate: 0.64%
•Labour: 6,566
•% Female: 0%
•Labour attrition (avg): 2.74%
•Total employees availing parental leave: 61
•Return to work rate: 100%
•Retention rate: 100%
•ALEC Internal HSE Trainings attendees, including subcon: 144,492
•Total employees hired:
•Staff: 180
•Labour: 1,616
•Internal hires: 3.5%
•ALEC Third Party HSE Trainings attendees: 9,380
•No. of innovation events and workshops organised by Innovation: 10
•No. of unique innovation idea generators: 289
•No. of people engaged in innovation: 484
•No. of people rewarded for innovation: 73
Wellbeing & Engagement
•Wellbeing & engagement activity participation
•Employee survey participation
•Absenteeism rate
Diversity Equity & Inclusion
•Nationalities
•Age
•Emiratisation
•% women across grades
Community Impact
•No. of beneficiaries
•Volunteering hours
•No. of employees engaged in Community Impact initiatives
Refer to Wellbeing & Engagement section
Absenteeism Rate
•Staff: 0.97%
•Labour: 1.51%
•49+ nationalities
•Emiratisation 0.6% achieved
•Women accounted for 10% of our senior managers.
No. of beneficiaries: 640
Volunteering hours: 56
No. of employees engaged in Community Impact initiatives: 8
Construction Quality & Compliance
•Legal cases related to structural integrity claims from main projects
•Instances of liquidation damages
Fair & Ethical Conduct
Responsible Supply Chain
•Cases of bribery and anti money laundering
•% employees trained on ethics & anti corruption
•No. of active projects/ backlog in countries ranking low on Corruption Index
•% subcontractors/ suppliers formally certified compliance with ALEC Code of Conduct
•ICV score
•% subcontractors screened through prequal on human rights policies and safeguards in place
•Trainings provided to supply chain to upskill and support subcontractors
ESG & Climate Risk oversight & management
•Sustainability governance structure
•Materiality assessment
•ESG & climate risk registers and mitigation plans
•Annual sustainability reports
•No. of ideas generated & implemented through innovation dashboard
•0 legal cases related to structural integrity claims from main projects
•0 instances of liquidated damages or penalties on construction projects, where ALEC is the main contractor
•0 legal cases related to bribery and anti money laundering
•Around 220 employees completed the training on ethics in 2022.
•0 active projects/ backlog in countries ranking low on Corruption Index
•100% subcontractors on ALEC main projects formally certified compliance with ALEC Code of Conduct
ICV score:
•ALEC: 38%
•ALEC Dubai: 39.53%
•ALEMCO: 25.99%
•ALEMCO Dubai: 27.42%
Refer to ESG & Climate Risk oversight & management as well as ESG Implementation Plan section
•Established Sustainability Committee
•First sustainability report released in 2023
•No. of innovation ideas generated : 505
•No. of innovation ideas implemented: 96
Data Privacy & Cybersecurity
•No. of substantiated attacks
•No. of substantiated data privacy violations
•0 case of substantiated breaches or data losses
Social Reporting disclosure scope: All Group companies and divisions are covered.
Environmental & Governance disclosure scope:
For the 2022 report, we have focused only on calculating emissions from site operations of ALEC Construction in UAE, where ALEC is the main contractor as well as owned and leased properties, factories, owned labour accommodation. We are working on engaging all businesses and territories to ensure completeness. We aim to capture all relevant data, but where this is not feasible, we will estimate data wherever practical. Where we estimate, we make this clear in the Reporting Criteria, in forthcoming reports. We will restate our 2022 emissions, once we complete the data collection process. In measuring our carbon emissions, we have adopted the GHG reporting protocol (Corporate Standard), the world’s most widely used greenhouse gas accounting standards for companies. We are taking an operational control approach to GHG accounting, per the guidelines issued by the GHG Protocol.
Exclusions:
Acquisitions: Businesses acquired in FY22 have been excluded from the scope of this year’s report
Outside UAE operations: Businesses and operations outside UAE have been excluded from the scope of this year's report.
These are greenhouse gases from sources owned or controlled by the organisation reporting its emissions. These are known as direct emissions..
These are emissions created by the generation of energy, such as electricity, which is bought by the organisation reporting its emissions. These are indirect emissions.
These are all other indirect emissions. They may be created by anorganisation’s supply chain, or by the products it produces. This also includes embodied carbon – the emissions produced when materials, such as steel, concrete and so on.
CONSTRUCTION ALEMCOFuel Covers mobile and stationary fossil fuel use (diesel, petrol)
1.Fuel used directly by ALEC to deliver projects where it functions as a main contractor, in commercial vehicles and site plant and equipment. This includes all vehicles, plant and equipment – either owned or leased – that ALEC directly operates and buys fuel for.
2.Fuels used at ALEC premises for power generation. In this case, premises means any offices, workshops, factory, yard which are independent of any one particularly project. This includes directly measured fuel supplies – where ALEC purchases the fuel directly.
3.Fuel used in vehicles used in support of our operations: Vehicles directly owned by ALEC. Exclusion: Related businesses: There are also a small number of projects (especially for Related Businesses such as ALEMCO/ Fit out/ Energy) where the customer provides fuel for us to carry out work on their behalf and these are NOT included.
•Subcontractors: Typically, ALEC provides fuel for subcontractors on site. In cases where subcontractors purchase own fuel, we have not added those.
Litres Data was collected using delivery notes and supplier invoices indicating quanity of fuel delivered to site by site logistics team and ALEC's Plant Machinery Vehicles (PMV) team for corporate and owned vehicles.
Site logistics/ PMV reports
Electricity Covers purchased electricity
Water Covers water consumption
Includes all electricity consumed at ALEC premises the company owns, operates from or exerts control over, where data is available. Premises are offices, factory or yard, labour accommodation, which are independent of any one particularly project. This area is split into: Directly measured electricity controlled and paid for by ALEC. Electricity used to deliver ALEC projects and covers our construction sites, welfare areas and project site offices. It includes electricity that ALEC pays for directly through metered supplies.
Exclusions are projects (especially for Related Businesses such as ALEMCO/ Fit out/ Energy) where the customer provides electricity for us to carry out work on their behalf.
Includes all water consumed at ALEC premises the company owns, operates from or exerts control over, where data is available. Premises are offices, factory or yard, labour accommodation, which are independent of any one particularly project. This area is split into: Directly measured water controlled and paid for by ALEC. For offices that are landlord-controlled, we have estimated the total water consumption by dividing the total water consumed by the building by the occupied area. Water from utility and tankers used to deliver ALEC projects and covers our construction sites, welfare areas and project site offices are included. Exclusion: Labour accommodation where we have no direct control over water consumption and locations where other than ALEC labour are housed.
Exclusions are projects (especially for Related Businesses such as ALEMCO/Fit out/ Energy) where the customer provides water for us to carry out work on their behalf.
kWh Data was collected using utility bills
Site logistics/PMV reports
litres Data was collected using utility bills and site logisitics reports for sweet water delivered on site & potable water from supplier invoices
Site logistics reports/ Utility bills
Waste & recycling rate
Waste generated (including both hazardous and non-hazardous waste)
Includes all waste generated across projects. Excluded: Areas where landlord provides waste management services and the fee is included as a service charge. For this report, we have not included waste from factories and labour accommodation and will do so for the next report. Exclusions are projects (especially for Related Businesses such as ALEMCO/ Fit out/ Energy) where the customer provides waste management services. Material Consumption
Core Construction materials such as concrete, reinforced steel and structural steel used for the project included permanent structure & aluminium, timber used for formwork and scaffolding.
Covers consumption of these materials in main construction projects, QAQC where ALEC is the main contractor.
Tonnes Data was collected using delivery notes, waste management company reports, central waste management systems managed by government landfill sites. The types and volume of material and how they are recycled by waste management companies, or disposed of is recorded. Recycling rate is the total waste recycled by waste management company divided by total waste generated on site.
Tonnes Data was collected using delivery notes and supplier invoices, verified by the project management consultant.
Site logistics report
QAQC reports (Acconex)/LEED reports where applicable/ Formwork & Scaffolding unit reports/Site commercial reports
Direct Emissions
Scope 1
Indirect Emissions
Scope 2
Indirect Emissions
Scope 3
Direct GHG emissions from sources owned or controlled by the company
indirect GHG emissions associated with the purchase of electricity
Other indirect greenhouse gas emissions from building and non- building activities including those from resulting from purchased goods and services including water consumption, materials consumed.
Man-hours WorkedNumber of hours worked across the organization
Includes emissions from stationary combustion (generators), mobile combustion (plant, vehicles etc). Fugitive emissions from use and disposal of refrigeration and airconditioning equipment are excluded due to lack of available data.
Includes electricity emissions from premises and projects sites, over which ESG there is operational control
Category 1 (Purchased goods and services) includes materials and water;
Lost Time Injury (LTI)
An injury arising out of, or in connection with work, which leads to an employee being absent from work for more than three days in addition to the day of the injury, as per an official Sick Leave Certificate
Full time employee (FTE) across all business units and fully owned subsidiaries, CRM directly supervised subcontracted workers across projects
tCO2e Fuel Emissions (tCO2e) = Consumption data (activity data) * DEFRA 2023 emission factors for fuels DEFRA 2023
tCO2e Location-based method for calculation. Scope 2 emissions (tCO2e) = Consumption data (activity data) * Grid emission factor from DEWA.
tCO2e Scope 3 emissions (tCO2e) = Consumption data (activity data) * Embodied Carbon Emissions factors for different construction materials from ICE Database. Water emissions was estimated using a local supplier emissions factor (EWEC).
Grid emission factor from DEWA Sustainability Report 2022
ICE DB V3.0 & EWEC emission factor
Number (#)FTEs: Number of people multiplied by 3,120 man-hours worked in a year (8+2 manhours per day multiplied by the number of days worked for the month – on average 26 days, multiplied by 12 months to get the annual manhours)
Directly supervised subcontracted workers: Sum of worked hours logged as per subcontractor logs
FTEs: Calculated based on headcount Subcontracted Workers: Reported from monthly HSE statistics reports submitted by respective subcontractors
Number (#)FTEs & Contractors: Filter number of injruies recorded based on the definition. Illness & Injury register FTEs across all business units and fully owned subsidiaries, directly supervised subcontracted workers across projects Lost
The total number of Lost
Health and Safety trainings
Number of training sessions delivered/ organised by Construction Risk Management (CRM) department (HSE)
Gender Representation* The percentage of male or female employees among total headcount as of 31st December 2022
Age Representation* The percentage of employees belonging to specific age groups (<30 years, 30–50 years, >50years) as of 31st December 2022
Monthly Health & Safety Statistics Report FTEs across all business units and fully owned subsidiaries, directly supervised subcontracted workers across projects
Ratio FTEs & Contractors: Filter number of injuries recorded based on the definition.
Number (#)Sum of H&S training sessions conducted Reported from CRM training registers FTEs across all business units and fully owned subsidiaries, subcontracted workers on projects
Percentage (%)Number of employees for specified gender divided by total number of employees Reported from HR database systems FTEs across all business units and fully owned subsidiaries
Percentage (%)Number of employees for specified age group divided by total number of employees Reported from HR database systems FTEs across all business units and fully owned subsidiaries
NationalitiesThe percentage of employees’ nationalities split by macro geographical areas as of 31st December 2022
Management Representation (Gender)
The percentage of male or female employees across employee grade levels as of 31st December 2022
New HiresThe total number of Full Time Employees (FTE) hired during 2022
Employee turnover
Percentage of employees who left the organization during 2022
Employees trained
Total number of FTEs who have undergone formal training (staff & labour)
Parental LeaveNumber of employees who availed the parental leave benefit during the reporting period
Parental Leave –Return Rate
Percentage of employees who availed parental leave benefit and returned to work after completing the stipulated leave period
Parental Leave –Retention Rate
Percentage of employees who availed parental leave benefit and remained within the company 12 months after completing the stipulated leave period
Innovation trainings
BIM/ Digital Construction trainings
Number of training sessions delivered organised by Innovation department
Number of training sessions delivered/organised by Digital Construction department
Innovation ideas generated Idea generated by employees and externally sourced
Innovation ideas implemented Ideas generated by employees or external contributed that have been implemented as part of the company processes.
FTEs across all business units and fully owned subsidiaries
FTEs across all business units and fully owned subsidiaries
Percentage (%)Number of employees for specified geographical areas divided by total number of employees
Percentage (%)Number of employees for specified gender divided by total number of employees in specified employeegrade category
Reported from HR database systems
Reported from HR database systems
Percentage (%)Sum of employees hired during 2022 across businesses Reported from HR database systems FTEs across all business units and fully owned subsidiaries
Reported from HR database systems FTEs across all business units and fully owned subsidiaries. Transfers within P&C & CRM ALEC Entities are not considered as exits.
Percentage (%)Number of employees who left the organization (including End of Service, voluntary (Resigned), Involuntary (Terminated/Retrenched), Medically Unfit, End of Contract, Absconded, Death) divided by total number of FTEs
Number (#)Sum of total number of staff who have undergone formal training. Total number of labour who have been trained in the technical training center. Reported from L&D records (training registers) FTEs across all business units and fully owned subsidiaries. Includes classroom trainings and practical tests and assessments.
Number (#)Sum of employees who availed parental leave during the reporting yearReported from HR database systems FTEs across all business units and fully owned subsidiaries
Percentage (%)Sum of employees who availed parental leave during the reporting yearReported from HR database systems FTEs across all business units and fully owned subsidiaries
FTEs across all business units and fully owned subsidiaries
Percentage (%)Number of employees who returned to work after the parental leave ended and and remained within the company 12 months after divided by the number of employees who took parental leave
Reported from HR database systems
FTEs across all business units and fully owned subsidiaries and interns
FTEs across all business units and fully owned subsidiaries and subcontractors
Number (#)Sum of Innovation training sessions conducted
Number (#)Sum of Digital Construction training sessions conducted
Reported from Innovation training registers
Reported from Digital Construction training registers
Number (#)Sum of all ideas submitted on the bright ideas platform Bright ideas dashboard FTEs across all business units and fully owned subsidiaries
Bright ideasdashboard Ideas that have been approved by Innovation dashboard Innovation client/ project consultant for implementation and is jointly sponsored by clients and restricted for use on a project-specific basis.
Number (#)Sum of total ideas that are approved on the innovation dashboard and for which budget expenditure is accounted for.
ALEC ESG Report 2022 -Sections Pages UN Global Compact
DFM ESG reporting guidelines
Principle 7: Businesses should support a precautionary approach to environmental challenges;
Principle 8: undertake initiatives to promote greater environmental responsibility; and
Principle 9: encourage the development and diffusion of environmentally friendly technologies.
GRI
SASB Engineering & Construction Services (IF-EN)
SDGS REMARKS
2-4: No restatements as this is the first sustainability report; GRI 2-5/ DFM G10: External assurance hasn't been sought for ESG disclosures 2022. G8.2: Not applicable
E4; Energy intensity has not been reported
reclaimed has not been reported.
ALEC ESG Report 2022 -Sections Pages
DFM ESG reporting guidelines
Health & Safety
Worker Welfare
UN Global Compact
SASB Engineering & Construction Services (IF-EN) SDGS REMARKS GRI
3-3; 403-(1-9) IF-EN-320a.1; IF-EN-250a.1; IF-EN-250a.2; S12.1
10.1 Principle 1:
Businesses should support and respect the protection of internationally proclaimed human rights; and
Principle 2:
make sure that they are not complicit in human rights abuses.
Principle 4:
the elimination of all forms of forced and compulsory labour;
Principle 5:
Principle 6:
3-3; 308-1; 409-1; 414-1;
3.8; 6.3; 12.4
ALEC ESG Report 2022 -Sections Pages UN Global Compact
ESG & Climate Risk Oversight & Management
Data Privacy & Cybersecurity
DFM ESG reporting guidelines
E8; E9; G8.1 G7.1; G7.2
SASB Engineering & Construction Services (IF-EN) SDGS REMARKS
2-13; 2-14; 2-16; 2-17; 2-24; 3-3IF -EN-160a.2
IF-EN-410b.1; IF-EN-410b.2; IF-EN-410b.3 not reported. 7.a; 8.2; 8.3, 9.1; 9.4
ESG 2022 disclosures E1 IF-EN-510a.2; IF-EN-510a.1.2
2-15: Each Board member declares any matters relating to conflicts of interest at the beginning of a Board meeting and withholds from voting on such items. 2-16: All critical concers are communicated to the Board during board meetings.
E2: Emissions intensity will be reported in subsequent report.
Disclaimer: The content of this report is provided by ALEC for information purposes only. No representation, warranty or undertaking, express or implied, is given as to the accuracy or completeness of the information contained in this report by ALEC. ALEC shall not be liable for any loss or damage incurred or suffered and claimed to result from the use of or reliance upon any information contained in this report including, without limitation, any direct, indirect, incidental, special or consequential damage. Statements or terms in this report used to describe ALEC’s relationship with third parties do not, and should not be construed to acknowledge or establish any legal relationship between ALEC and such third party, acknowledge or establish any fiduciary duty on the part of ALEC to such third party or otherwise, or acknowledge or establish any responsibility for or liability in respect of the actions of such third parties. The copyright to this report is held by ALEC. Unauthorised reproduction or conversion is strictly prohibited. Copyright © ALEC Engineering and Contracting, 2023.