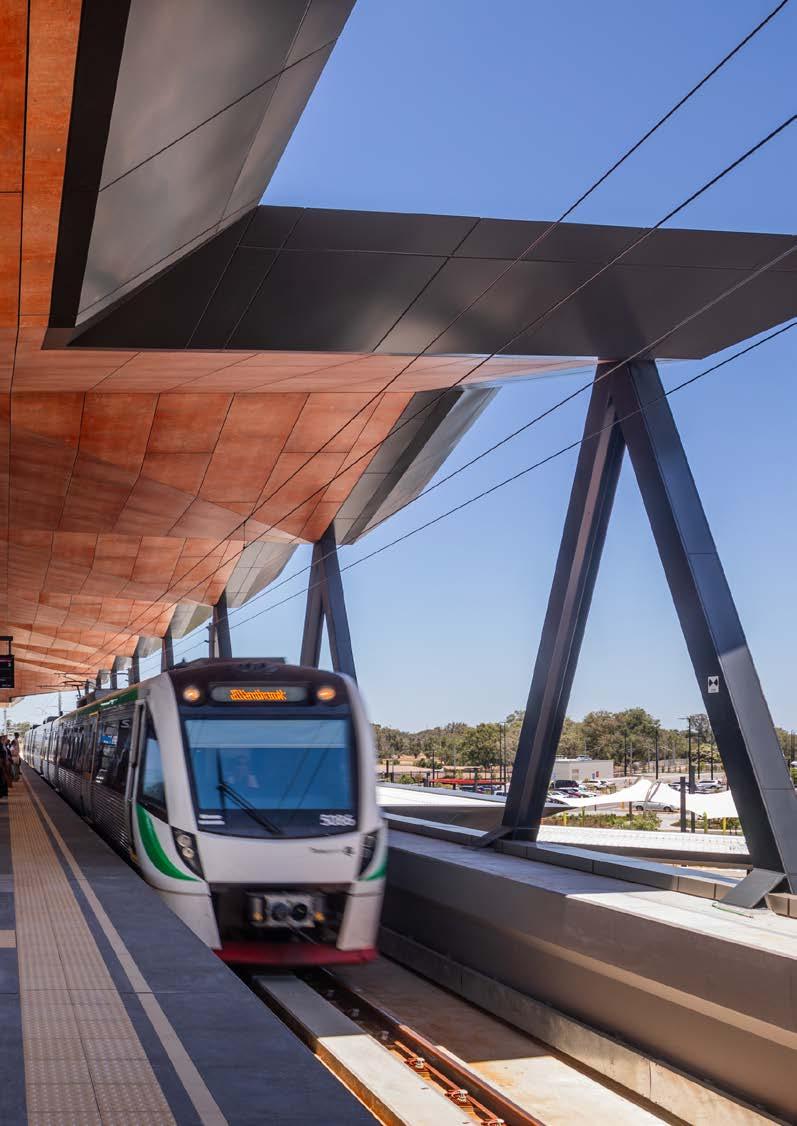
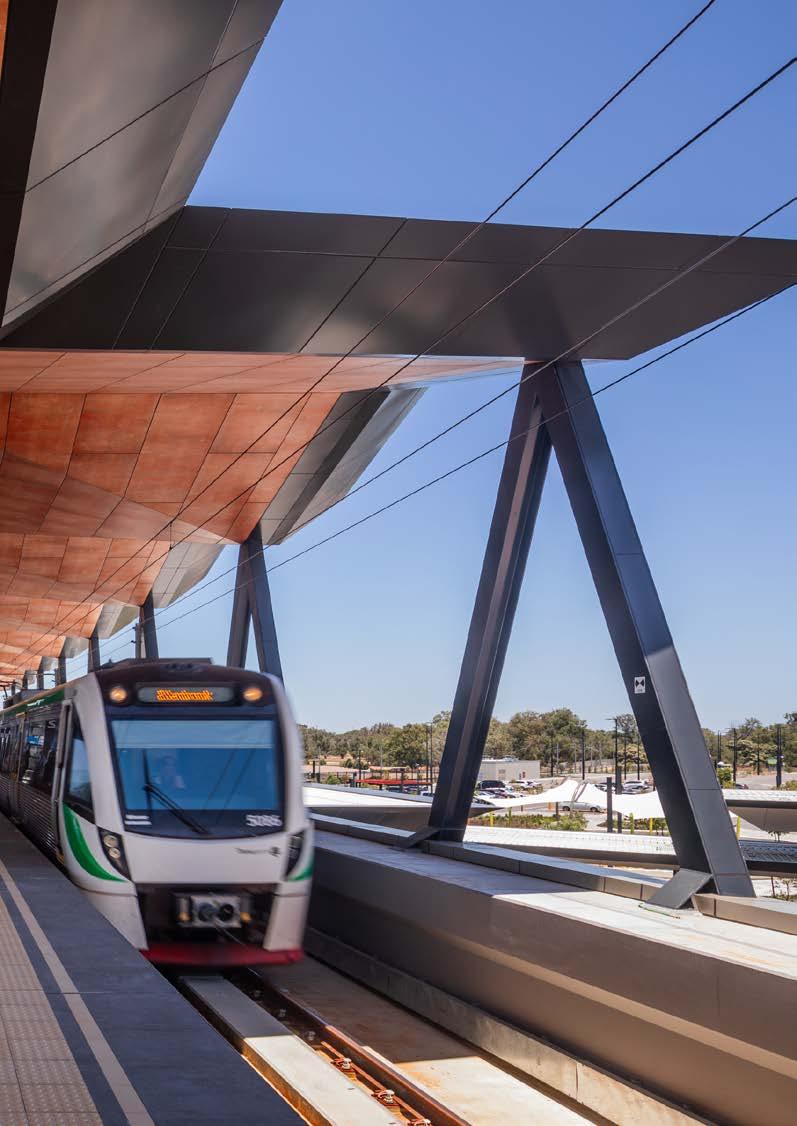
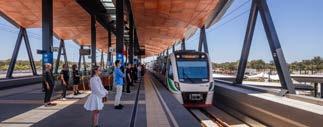
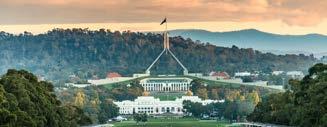
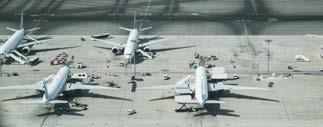
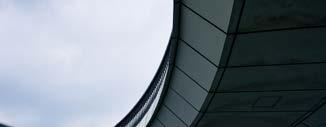

The delivery of the METRONET Ellenbrook Line as part of the METRONET program of works is a significant milestone in Perth’s rail history, revolutionising Perth’s public transport system with seamless connectivity and modern, affordable travel options.
The biggest expansion of Perth’s rail network in more than 16 years, the METRONET Ellenbrook Line connects people in Perth’s north-east to a worldclass public transport system through 21 kilometres of new track and five new state-of-the-art stations.
The new line was officially opened on 8 December 2024, and branches from the existing Midland Line via the new Bayswater Station to offer reduced travel times to the Perth CBD.
Construction of the METRONET Ellenbrook Line was a major engineering feat. Key highlights include demolition and reconstruction of Broun Avenue Bridge, tunnelling under Tonkin Highway, two viaducts measuring 900 and 300 metres respectively, three new intersections, two road bridges, one rail bridge, three pedestrian underpasses, one portal and a footbridge over Tonkin Highway. Additionally, 150,000 railway sleepers were used to build the 21 kilometres of track.
Construction at this impressive scale supported around 6,500 jobs including 332 apprentices, 140 graduates and 290 Aboriginal employees.
– a place of welcome and connection. Image courtesy of
The five iconic stations – Morley, Noranda, Ballajura, Whiteman Park, and Ellenbrook – are now providing growing communities with more transport choices and access to housing, jobs, community services, tourism and recreation opportunities over the next 30 years.
The architectural brilliance of each station is inspired by the surrounding landscapes and local communities to create vibrant, welcoming and safe spaces.
Modern station amenities meet the needs of commuters, with trains operating every 12 minutes at peak
times and effortless connections to bus services. Across the five stations, 3,300 parking bays and 335 bicycle storage racks add to the world-class public transport experience. A commitment to sustainability is also evident in the design and construction of each station.
Water conservation measures, energy and carbon saving initiatives such as solar panels and electric vehicle charging bays, and the use of recycled materials reduce the environmental impacts of the line, helping build a greener future for Western Australia.
Notably, Ballajura and Ellenbrook stations achieved 6 Star Green Star As Built – Railway Stations certifications from the Green Building Council of Australia, representing world leadership in sustainability and making these the highest scored Green Star train stations in Australia.
The METRONET Ellenbrook Line also showcases a commitment to cultural representation through public art and Noongar place names.
14 local and Noongar artists created 20 public art pieces – making it one of the largest public art commissions on a METRONET project. The artworks reflect Noongar culture and connection to Country and celebrate the unique environment of each station – welcoming local communities while supporting emerging and established Western Australian artists.
From station-wide graphically overlaid skylights and intricate screen designs to a myriad of painted murals and statement sculptures, each piece honours community spirit, Noongar culture and local flora and fauna.
Cultural connections are further enhanced through Noongar place names at the five stations that acknowledge the traditional and ongoing connection of Noongar people to Country, educate the community about spiritual significance, endemic plants and native animals to each area and celebrate the inclusion of Noongar language across this significant rail project that has connected tens of thousands of people in Perth’s growing north-eastern suburbs to the rail network for the first time and is achieving the METRONET legacy of a well-connected Perth with more transport, housing and employment choices.
Ballajura Station. Arrival sculptures by Peter Farmer and Jason Hirst signify the importance and unity of the Noongar family structure. Image courtesy of Public Transport Authority.
• Main construction contract: MELconnx Alliance (Laing O’Rourke Australia Construction and Public Transport Authority).
• Enabling works: Main Roads and Tonkin Gap Alliance (BMD, Georgiou Group, WA Limestone, BG&E and GHD).
• Architects: Woods Bagot and Taylor Robinson Chaney Broderick
• Design: UDLA/TCL – Landscaping.
• Engineers: Jacobs and Arup JV, Design Analysis, Floth, ADG, Elite Solutions, Siemans, Rail Systems Australia, Wabtech, Hatch.
• Quantity Surveyors: Turner & Townsend – planning, Rider Levett Bucknall (RLB) – procurement and delivery.
• Art Coordinator: Artify.
For more information about the METRONET Ellenbrook Line visit metronet.wa.gov.au
This article was provided by METRONET.
represents the area’s history and multiculturalism. Image courtesy of METRONET.
NZIQS QSEP President, Board Member, PAQS YQS Vice-Chair
Quantity Surveyor, Cook Brothers Construction
When I began my career in quantity surveying, I attended an NZIQS annual conference as a student member. I was terrified, but ultimately supported by industry leaders. It was this senior support that led to my own active involvement in NZIQS.
So how do we encourage this development in young, driven, earlycareer quantity surveyors? How do we provide the building blocks for them to receive similar support, encouraging them to take ownership of their professional development?
There are easy wins here:
1. We must champion drive and development in our young quantity surveyors.
2. ‘Cliques’ need opening up, whereby senior professionals break down barriers and introduce themselves to newcomers.
3. Companies must think beyond local boundaries and support attendance at events and conferences,
recognising the value that these connections bring to their business. It will take all levels of the industry to achieve this development.
New quantity surveyors must take ownership of their development by identifying knowledge gaps and seeking ways to fill them. They should proactively engage with senior professionals, rather than wait for mentorship or expect advanced roles prematurely. QSEP supports this by providing opportunities for networking and bridging knowledge gaps. However, juniors must also be committed to this vision.
Senior professionals play a crucial role too. At conferences, it’s essential to reconnect with familiar faces, but I urge senior professionals to also introduce themselves to newcomers or those who appear apprehensive. After all, we were all that person once. Seniors have a wealth of invaluable experience that our juniors will benefit from learning.
If mentoring isn’t an option for you, consider sharing your insights at a CPD session organised by the local QSEP committee.
Finally, companies, please support your staff at all levels to attend events and build their networks. People do business with people, and the individual networks will provide tangible benefits for your business. Connections should also extend beyond local boundaries. As QSEP President I attend national meetings in both NZ and Australia, and as PAQS YQS Vice-Chair we regularly collaborate with professionals across the Pacific, fostering broader connections and mutual growth.
By committing to these steps, our industry can improve on an international scale, raising the profile of our profession.
This article examines the options and benefits of investing in electrifying existing commercial office buildings in Canberra, including key considerations for both landlords and tenants.
With the Australian government’s billiondollar investments in decarbonising the grid, the electrification of commercial office buildings provides building owners and tenants with a clear pathway to achieve Net Zero operations.
In Canberra, the imperative to transition to all-electric buildings is pressing, with clear targets being set by both the State and Federal Government, including:
As outlined in the Australian Government’s Net Zero in Government Operations Strategy, agencies are being encouraged to lease all-electric, energyefficient buildings, with a requirement to move to all-electric buildings by 2040. The transition will be particularly relevant in the Canberra market where Commonwealth government tenants make up 66% of occupiers.
The ACT Government has set a target to be the first Australian city to reach Net Zero emissions and 100% renewable energy by 2045. A key part of the ACT government’s plan to achieve Net Zero includes phasing out fossil fuels such as gas.
Fossil fuels are commonly used in commercial buildings with applications ranging from natural gas
to heat spaces, domestic hot water and cooking, as well as diesel for emergency or backup generators, and fire system pumps. Through technological advances, efficient, cost-effective electric alternatives are available with lower carbon intensity.
While many office buildings now achieve 5.5 Star and even 6 Star NABERS Energy ratings year-on-year, even the most efficient buildings still depend on gas for heating and hot water – making a pathway to Net Zero difficult to achieve.
As the ACT transitions away from fossil fuels such as gas, the supply of fuels and associated infrastructure is likely to become more expensive with price hikes passed on to both tenants and landlords through higher utilities costs.
With the ACT having already achieved its 100% renewable electricity target, converting existing assets to electric will enable tenants and landlords to reach their Net Zero targets sooner.
Canberra building owners and tenants should aim to achieve 100% electrification as a priority for every building but will need to consider the timing, the remaining useful life of assets, and the availability of capital to fund any electrification transition.
While 2040 seems like a long time away, there are clear benefits and a strong investment case for building owners to start transitioning existing assets off of gas now. Early investment in electrification can reduce whole-oflife costs and carbon emissions, and help to attract and retain tenants.
The Australian Government’s Net Zero in Government Operations Strategy states that entities should consider the emissions that will be embodied in any new construction works associated with a new lease or fitout. According to the Australian Sustainable Built Environment Council (ASBEC), embodied emissions (i.e., those generated during the production, transportation, and construction of building materials and components) account for approximately 20–50% of a standard building’s total life cycle emissions, while operational emissions make up the remaining 50–80%.
emissions account for 20–50% of the total lifecycle emissions.
The stark level of embodied emissions a new build generates means that building owners and tenants should retain, adapt, and enhance existing assets as the ‘greenest’ option. Building owners should highlight the differences in carbon production to tenants and investors when they seek to make ecofriendly investment decisions.
A decisive factor in clients’ search for office space is often the location, with many government agencies seeking spaces located close to the Parliamentary Triangle. Building owners with well-located assets that demonstrate a pathway to electrification by 2040 and can consistently achieve a 5.5-star or higher NABERS Energy rating annually, will be well-placed to secure long-term government tenants.
Electrification can be implemented in stages to allow for a more manageable and steady cash flow. The financial burden can be spread out over time and reduce the need for a large, upfront investment.
Planning for electrification can also help building owners take advantage of replacement opportunities as they arise, rather than waiting until the building reaches its end-of-life. Buildings require ongoing maintenance, and systems need replacing at their individual endof-life. Taking the opportunity to switch to all-electric solutions will reduce the need to upgrade systems twice: first with like-for-like replacements, then with electrification when the building itself reaches end-of-life.
Savings will also flow through the operational costs. For example, items such as heat pumps carry higher installation costs but provide a longterm benefit and savings through much more efficient operational costs. The process also decarbonises building operations earlier and demonstrates the electrification commitment to existing and prospective tenants.
In a building’s lifetime, there are key points of opportunity to implement electrification projects, including:
When equipment is close to the end-of-life, change to all-electric. Upgrades could include gas boilers
and heaters, diesel generators, gasfired co-generation systems, as well as gas cooktops, and burners in tenant kitchens.
Remove all gas connections and change the new lease agreements to remove gas supplies to tenancies.
Consider a dedicated localised electric heat pump system and water efficiency measures to reduce hot water demand, alongside point-of-use electric water heaters for bathrooms elsewhere in the building.
Opportunity to undertake electrification works by integrating common or lobby areas into the overall capital works budget.
Install electric vehicle chargers, renewable energy, and energy storage systems to review and enhance the electrical infrastructure for the electrification of natural gas systems.
Fine-tune the building systems and controls to optimise energy efficiency and reduce peak demands, particularly during tenants’ reduced occupation periods.
Building owners, operators, and tenants can work together to decide when electrification upgrades occur. By doing so, each can minimise operational impacts and optimise upgrades to reflect the occupancy of buildings for energy efficiency.
Building owners should develop a transition plan early for a clear roadmap to 100% electric buildings. A wellstructured plan will demonstrate to tenants and investors a clear pathway to achieve Net Zero in operations.
Tenants seeking to enter a new lease should consider whole-of-life carbon impacts when assessing a building’s ‘sustainability’ credentials, including embodied emissions.
By Mike O’Shea FAIQS, CQS
Infrastructure development offers significant opportunities for quantity surveying professionals driven by global demand for sustainable and modernised infrastructure. Key areas include cost management, contract management, risk assessment, and value engineering in large-scale projects such as roads, railways, bridges, and renewable energy installations.
As governments and private sectors invest in infrastructure, quantity surveying professionals are vital in ensuring projects stay within budget while meeting quality and sustainability standards. The increasing complexity of projects also positions quantity surveying professionals as indispensable advisors in cost and contractual decision-making.
Infrastructure covers large sectors and sub-sectors, including the following as described in Table 1.
Please note that this article is focused on the transport sectors and subsectors listed in the table above. Future articles will discuss utilities, mining, oil and gas, as well as energy.
The quantity surveying profession has many different job titles, including cost estimator, cost engineer, cost manager, contract administrator, contract manager, commercial manager, procurement manager, and project controls manager.
There is a common misconception that quantity surveyors only provide cost estimating, cost planning and cost management type services. Estimators are skilled, but their services often only apply at tendering stages and on occasion during design development, whereas quantity surveyors stretch across the whole project.
Quantity surveyors, particularly Certified Quantity Surveyors (CQS), maintain a much wider range of competencies.
The broader range of quantity surveying services can be applied to a total project or any component (e.g., road, track, tunnel, bridge, or airport), however, the maximum benefits can be achieved when they are applied to a total project.
A selection of services provided include:
• Design cost advice, cost planning, and cost estimating
• Contract documentation and procurement
• Commercial management and contract management/ administration
• Claims and disputes
• Expert witness/evidence
• Life cycle cost analysis
• Audits, peer and assurance reviews
• Value management/engineering
• Project management
• Project risk management
• Cost engineering
• Project controls.
Australia is undertaking numerous transport infrastructure projects… to enhance connectivity, reduce congestion, and support economic growth.
and berths, breakwaters, jetties, reefs, boat ramps, dredging, etc.
Infrastructure Australia maintains the Infrastructure Priority List, a comprehensive and independent guide to nationally significant infrastructure needs. This list is regularly updated to reflect emerging priorities and to assist governments in making informed investment decisions.
The Priority List categorises proposals into key stages of project development:
• Early-stage (Stage 1): Identifying problems and opportunities
• Potential investment options (Stage 2): Exploring potential solutions
• Investment-ready proposals (Stage 3): Projects ready for delivery.
It is important to note that while the Priority List provides guidance, it does not dictate funding decisions. The federal government, often in partnership with states or territories, continues to
invest in various infrastructure projects across the country, and the list serves as an advisory tool to inform these investments.
For the most current and detailed information, including the latest updates and specific projects by state, please visit Infrastructure Australia’s official website.
Australia is undertaking numerous transport infrastructure projects across its states and territories to enhance connectivity, reduce congestion, and support economic growth.
Below is a list of some of the significant projects across Australia.
A 1,700-kilometre freight rail line connecting Melbourne to Brisbane through regional Victoria, New South Wales, and Queensland, to enhance the national freight network by providing a faster, more efficient rail link between major cities.
Australia’s largest public transport project, delivering 31 metro stations and over 66 kilometres of new metro rail, to provide high-frequency, driverless trains, reducing travel times and easing congestion in Sydney.
A 33-kilometre motorway scheme, including the widening and extension of the M4 and M5 motorways and a new tunnel linking the two, to reduce congestion and improve connectivity in Sydney’s road network.
A new international airport is under construction in Sydney’s west, expected to be operational by the end of 2026, to provide additional aviation capacity to meet growing demand and support the development of Western Sydney.
A project creating a new end-to-end rail line from Sunbury in the west to Cranbourne/Pakenham in the southeast, including the construction of five new underground stations, to increase the capacity of Melbourne’s rail network, enabling more frequent and reliable services.
A project to provide an alternative to the West Gate Bridge, including a new tunnel and additional lanes on the West Gate Freeway, to reduce congestion and improve freight access to the Port of Melbourne.
A 90-kilometre rail line linking every major train service from the Frankston Line to the Werribee Line via Melbourne Airport. The objective is to enhance Melbourne’s public transport network by connecting key train lines and improving accessibility.
A 10.2-kilometre rail line from Dutton Park to Bowen Hills, including a 5.9-kilometre tunnel under the Brisbane River and CBD, to improve Brisbane’s public transport capacity and reduce congestion.
An extension of Canberra’s light rail network from the city centre to Woden, to improve public transport options and reduce road congestion in Canberra.
A series of projects to improve safety, flood resilience, and capacity along the Bruce Highway, which stretches from Brisbane to Cairns. The objective is to enhance a critical transport corridor in Queensland to support economic development and improve safety.
A comprehensive plan to connect suburbs, reduce road congestion, and meet Perth’s future planning needs through rail expansion. The objective is to expand Perth’s public transport network to support population growth and urban development.
An ongoing project to create a continuous, non-stop roadway through metropolitan Adelaide, to improve traffic flow and reduce travel times in Adelaide.
A series of projects aimed at improving road safety and efficiency across Tasmania, to enhance connectivity and support economic growth in the region.
A program focusing on upgrading highpriority roads in Northern Australia to improve safety and efficiency, support economic development and improve access in remote areas.
An extension of Canberra’s light rail network from the city centre to Woden, to improve public transport options and reduce road congestion in Canberra.
The above is a sample list of the major infrastructure transport projects, however, there are many projects undertaken by councils, state government and the private sector including bridges and roads.
By
By Stephen Cummins and Shannon Percy from Slattery
In this paper, Slattery investigates the cost of delivering construction works in an operational airport environment and the premiums incurred and explores the opportunities for clients to make informed decisions to balance both cost and operational continuity.
It is widely accepted that ‘things cost more’ in an airside environment. But why do they? The airside operating environment is unique. Airports must take an uncompromising approach to security and safety, ensure operational continuity and meet regulatory obligations. They must build for the future while ensuring a positive experience for passengers today.
In the latest Kaizen paper, Slattery provides a cost model that analyses airside versus non-airport projects to pinpoint the source of specific cost drivers and premiums. Our findings reveal key themes that can help clients better comprehend, communicate and potentially reduce project costs.
Data from the Bureau of Infrastructure and Transport Research Economics (BITRE) reveals Australian domestic commercial aviation carried 5.32 million passengers in March 2024, an increase of 2.8% on the previous year.
With this trend set to continue through to 2050, airports face the exciting, but daunting, prospect of providing fitfor-purpose assets and infrastructure to support growth while maintaining operations. Major expansion and refresh programs are in planning or underway at all major airports, with significant growth expected at regional airports also.
This trend continues globally. According to the International Air Transport Association (IATA), passenger revenues
were projected to reach US$744 billion in 2024, up 15.2% from $646 billion in 2023. Revenue passenger kilometres (RPKs) are 11.6% year-on-year. IATA predicts a long-term growth trend of 3.8% year-on-year growth between now and 2043.
While passenger numbers climb, the aviation sector nevertheless faces a host of challenges. Inflationary pressures, soaring oil prices, net zero targets, regulatory burdens, geopolitical tensions and supply chain bottlenecks are all hitting budgets and bottom lines. At the same time, Australia’s building industry is enduring one of the most tumultuous periods in its history. Construction costs continue to escalate, stubbornly high interest rates persist and skills shortages bite.
Infrastructure Australia doesn’t expect supply to match demand for construction labour until the end of 2027, for instance. With recent agreement of new enterprise bargaining agreements around the country, labour costs continue to place upward inflationary pressure on construction pricing. While costs have plateaued for some materials, like steel, other energy-dependent materials like concrete remain on an upward trajectory.
Cost escalation has hit construction hard. More than 3,000 construction industry insolvencies were recorded in 2024, according to ASIC. Constructing in an airside environment is risky business. With airports keen to transfer this risk to the contracting market, there is an inevitable premium to pay to incentivise contractor participation when there are other, less risky opportunities available.
…Airports face the exciting, but daunting prospect, of providing fit-for-purpose assets and infrastructure to support growth while maintaining operations.
Understanding the cost drivers in airport environments is crucial for effective project planning and budgeting. Below we’ve outlined some of the primary cost drivers.
• Moving people to and from the job site, including the productivity loss due to screening and travel.
• Delivering and offloading materials, which involves transportation to and from the airside location, and the horizontal and vertical movement to the work front (like mobile cranage, services relocations, builders work, temporary protection and making good).
• Establishing remote and multiple site facilities due to limited airside space, often leading to higher preliminaries.
• Completing works out of hours and subsequent standdown hours to maintain operations, resulting in increased labour rates.
• Lost productivity due to shorter shifts (night works to support lastand-first flight schedules).
• Mitigating and managing dust and Foreign Object Debris (FOD), which can increase costs due to methodology and sequencing of works.
• Limiting vibration and acoustic impacts, which influences methodology, timing of work, and subsequent costs.
• Meeting crane height limitations, which can mean more costly solutions, such as mobile cranes.
• Ceasing or restricting activities during embargo periods in peak travel times, significantly impacting program and adding costs for demobilisation and remobilisation of the site and labour force.
• Early Contractor Involvement (ECI) during design phases or a twostage tender process to manage complex logistics, increasing costs by engaging a main contractor before works begin.
• Staged completion increasing administration and management time, raising preliminaries at both sub-contract and main contract levels.
• Integrating building works with specialised equipment (such as baggage handling systems and airbridges), which requires extensive design coordination and planning, resulting in higher preliminaries and professional fees.
• Incurring additional training costs for the main contractor and supply chain leads to increased overheads and job costs.
• Extra over safety requirements driven by operational environment
(i.e., a spotter for every elevating work platform, traffic management for apron works).
• Maintaining the restricted zone boundary heightens supervision requirements, including safety officers and security guards.
• Increasing insurance premiums to cover additional risks, which leads to higher preliminaries.
• Delivering projects in an airside environment, perceived as difficult and risky, can deter contractors who may prefer easier projects or charge a premium for airport work.
• Using nominated or named contractors/sub-contractors familiar with airport operations and requirements may safeguard operational continuity, but can lead to higher costs due to sole source pricing.
This cost model compares the costs of refurbishing bathroom amenities in both an airside environment versus refurbishment in a more typical commercial CBD project. Costs represent an average over a sample size of 11 projects.
By completing this exercise, we can identify the cost premiums incurred, where these are occurring, and start to unpack the drivers behind these.
Preliminaries, overheads and margins on airside projects is often more than 25% of trade costs due to operations (staging, increased program, out of hours, temporary works, insurance costs, inefficiencies in productivity in getting to the job site).
This can be more than double that seen in a more traditional delivery environment.
Demolition and alterations represents a small allocation of total project costs (less than 10%). The data identifies an approximately 10% premium to be paid on airside projects, likely due to loss of productivity, out of hours and site logistics (i.e., removal of waste from site).
Substructure costs are unusual for refurbishment projects; however, some airside projects have seen slab and
footing strengthening to accommodate internal reconfiguration changes to suit passenger requirements. This is not required in more typical projects where capacity and configuration tend to remain.
Superstructure costs predominantly represent internal walls, screens, and doors. Cost premiums are minimal (less than 10%) representing increased labour time due to productivity loss and site logistics. As most fitout work is contained, works can be completed in
normal working hours, reducing major labour premiums associated with short shifts or night works.
A marked increase in superstructure costs comes where changes in configuration lead to additional structure (lightweight columns or strengthening existing members) modifications to roofs and external walls. Similar to substructure, this is avoided in more traditional refurbishment projects where layout is maintained.
Finishes for walls, floors, and ceilings carry an approximately 15% premium compared to non-airside projects. This aligns with the commentary for fitout costs above, with most works being completed in normal working hours. Fitment costs appear to be similar across the projects. Given that many items in fitments (vanities, mirrors, equipment) have high supply costs with a smaller labour component, this is not surprising.
Building services cost data shows significant premiums, with average airside refurbishments costing approximately $5,000/m2 – around 50% more than more traditional refurbishments. This is hard to unravel, and is partly scope driven by the unique service requirements of the airport.
The biggest culprits being hydraulics (likely due to integrated sanitising, cleaning, and drying stations as well as reconfiguration of waste and water points) and fire services (requiring a complex series of drain downs or pipe freezing, fire impairments, temporary supplies, and out-of-hours work). The requirement to use names subcontractors for much of this work may be required to ensure operational continuity, however the true cost premium of this certainty remains to be seen.
Total construction costs for airside amenity upgrades average approximately $13,000/m2, an approximate 78% uplift on the cost of more traditional refurbishment. As always, data should be treated with caution and much of this will be driven by the additional scope to meet the airport’s requirements. All project are unique and premiums will vary from project to project.
The above costs do not include for security and access requirements for construction activities in an airside environment. While these costs are project and program specific, this may add a further 5% to construction costs.
The bottom line? A brick or tile laid, a cubic metre of concrete poured, or an electrical system wired in an airport environment is not the same as the equivalent delivered elsewhere.
Building in ‘live’ environments brings additional challenges and cost premiums.
At airports, stepping past the security barrier immediately incurs additional costs.
How can astute airport managers respond to minimise cost premiums while balancing operational continuity? Here are some of our key takeaways:
• Smart decisions during the planning and design phase can de-risk the project by reducing labour and overall project costs. Construction costs are made up of material, labour, and plant and equipment. With materials and plant remaining stable, labour is the volatile commodity that fluctuates subject to working environment.
• Engaging early with operational stakeholders will maximise the time and ability to agree a delivery plan that is best-for-project. With more time to plan around the disruption, operational teams can be more accommodating, avoiding the need for night works, shorter shifts, in-turn improving productivity and reducing overall labour costs.
• Delivery planning early and thoroughly considered can also reduce labour costs by defining efficient site logistics and temporary works. This includes locating site accommodation close to the job site, planning controlled delivery or movement of materials (i.e., efficiently at the same time each day reducing work safety officer/ security costs). Costs plans from an early stage should consider these items to ensure budgets are robust.
• Modular construction should be considered for large scale airside developments (see Midfield Satellite Concourse South – MSC) or prefabrication of building components should be tested for cost/benefits
(pre-cast concrete, curtain walling, structured insulated panels, or SIPs, etc.). Reducing labour intensive trades at the job-front should be investigated where possible.
• Supply chain investment to increase knowledge and experience of the working environment. This includes market sounding, briefings, and project opportunities on ‘safe’ projects for contracts to ‘cut their teeth’. Importantly, clients should articulate the working environment through a clear and detailed set of preliminaries to provide a baseline, allowing contractors to provide competitive pricing without ambiguity and significant risk premiums. Named contractors and subcontractors may make operational continuity sense, but it is important that this coexists with value-for-money outcomes.
Smart decisions during the planning and design phase can be made to de-risk the project, reducing labour and overall project costs.
Construction airside demands meticulous planning and deep expertise. Proactive management can ensure projects are delivered on time, within realistic budgets, and with minimal disruption to airport operations and passenger experiences.
Executive Quantity Surveyor, MBM
There are numerous factors that significantly influence the stability of a construction project which, if not managed and controlled meticulously, may lead to project financial failure and collapse.
These financial risks can be minimised, and several approaches can be undertaken. Approaches that I have deemed to be adequate for many situations focus on three core strategies: forming an efficient project team, establishing effective administrative protocols to manage deliverables, and promoting open communication between the parties involved.
The successful delivery of a project depends on the performance and due diligence of the team engaged in all phases of the project, from planning until it is commissioned and handed over. High-performing teams that can manage projects during the initial planning or the design stage guarantee the production of suitable
design and rigorous documentation. These should reflect the scope of work to ensure a realistic budget with a healthy contingency can be set, which results in an achievable program and a successful tender. Similar principles should be adopted throughout the construction stage. A capable project group that prioritises harmonious teamwork between consultants, contractors, and especially the client with their advisory team leads to a quality project that boasts streamlined cost management, early risk identification and mitigation, and proactive contract administration.
While engagement of the right people in a project is imperative, it is also essential to direct the project team with a robust set of guidelines and procedures not only to warrant that the outcomes align with the client’s objectives, but also to maintain a tight monitor on the endeavour. Examples can include standard design guidelines,
procedures outlining the selection of suitable procurement methods and forms of contract, pre-qualification of tenderers and tender evaluation protocols, and more. This primarily contributes to minimising financial risk to the project. In addition, it is vital to establish a recurring feedback loop and proforma reports detailing all aspects of the project: risk assessments, programs, cashflows and contingency levels, contractor and consultant’s procedures in progress documentation, and early notices of potential issues and delay that may impact the project significantly.
Ultimately, having an optimised collective that strictly adheres to the protocols may be insufficient without collaborative effort that elevates team chemistry. It is important to consistently promote open communication within the team to determine and address potential issues early on and to judiciously make decisions, especially in the crucial stages of a project.
Director, Best QS
Construction projects are inherently risky and as quantity surveyors, we play a pivotal role in identifying, assessing, and mitigating potential financial risks throughout the project lifecycle. While multiple factors contribute to financial risks, certain key strategies can significantly impact project financial success.
Clearly defining the scope of works and contractual obligations prevents scope creep and unauthorised changes, and ensures all parties clearly understand their roles and deliverables. This approach, applied consistently throughout the project lifecycle, reduces disputes, ensures effective project management, and ultimately improves financial outcomes.
Furthermore, early risk identification allows stakeholders to proactively address potential issues, allocate resources effectively, and implement
contingency plans to minimise financial losses. Although allocating substantial contingency funds may not be feasible for every project, a structured approach to risk classification and prioritisation based on likelihood and potential impact at the outset of the project can enhance the financial stability of a construction project.
When mitigation is not feasible, identifying opportunities can serve as a strategic lever to enhance a construction project’s financial position. By recognising value engineering, cost savings, and revenue enhancement opportunities, stakeholders can offset unmitigated risks, such as market volatility or labour shortages, and maximise financial benefits through optimised design and construction methods, strategic relationships, improved supply chain management, and enhanced project delivery timelines.
Engaging experienced contractors and maintaining regular monitoring are crucial in minimising the financial risks. Experienced contractors bring valuable insights and expertise, helping identify and capitalise on cost savings and value creation opportunities. Regular monitoring of contractor performance, coupled with proactive communication and collaboration, enables project stakeholders to address potential issues promptly and ensure compliance with contractual obligations to optimise project outcomes.
Ultimately, a proactive, structured, and adaptable approach is key to effective financial risk management in construction projects. By implementing a collaborative mindset and remaining responsive to changing project circumstances, teams can better navigate uncertainty and minimise financial risks.
Estimator, Tansley Electrical Ltd
Giving due respect to the base foundational processes like detailed planning, budgeting, contract/ legal protections, risk identification and management, cost control and monitoring, appropriate insurance, and contingency planning; minimising financial risk from the lens of an estimator. Studying architectural and consultant (specialist trade) drawings, along with specifications provides the main contractor with an in-depth understanding of what each trade needs to achieve, and what to expect in their written tender submissions. In a case where there is no schedule of quantities (SoQ), each trade will be forced to supply their interpretation of expectations.
Understanding the scope and requirements for each contract allows both the main contractor and sub-contractor to cover all the bases, ensuring nothing is missed. Otherwise, an added financial risk may leave one or even both contractors out of pocket, or even worse, set the project back and add to the already established financial risks a reputation risk.
To reduce risks, a task team mentality with strong lines of communication needs to be created. For example, using inappropriately skilled staff may increase the possibility of blowing a budget in terms of labour hours, simply from poor planning. The same for Subcontractors and
suppliers, being trustworthy and having historically established sources helps diminish any extra risks. As for consulting personnel, experience and ingenuity can lead to streamlined work, as well as give a new perspective and foreshadow potential challenges that may arise within the scope of works. Ensuring ongoing communications both internally and externally among teams (companies) is the bottom line from an estimator’s perspective; relationships along with experience are key. However, in an ever-changing environment that cannot always occur. In those other cases, to minimise financial risks, maximise communication with all moving parts.
Senior Quantity Surveyor, WT Partnership
As a quantity surveyor, managing financial risk on a construction project requires careful planning, cost control, and proactive risk management involving all project stakeholders. During my experience, I have found that the following strategies help to minimise risk.
Accurate Budget Setting and Cost Estimation – Setting a robust budget backed by a solid estimate is the foundation of a financially successful project. Using current market feedback, industry tools and a strong cohesive team helps to ensure accuracy. I leverage information from my colleagues to inform any project. For clients, an accurate estimate can inform whether a product will stack up, guide funding decisions and shield from
financial pitfalls during the project.
Risk Identification and Allocation – No project is without risks, but I’ve learned that early identification of financial risks such as labour shortages, material cost escalation, or unexpected delays makes a significant difference. Regarding risk allocation, it’s important that the risk is allocated to the stakeholder best positioned to handle it.
Value Engineering (VE) – I frequently see design and material reviews produce cost-effective solutions that maintain quality, providing a similar specification is proposed early in the project. Small material changes or alternative suppliers can result in significant savings.
I’ve found successful VE meetings tend to include collaboration between all stakeholders including clients, quantity surveyors, contractors and the design team.
Regular Cost Monitoring and Reporting – Keeping a project financially viable requires constant oversight. I rely on a healthy cost report to track cash flow, identify variances and monitor if the project is staying within budget. This approach allows for early detection before minor financial issues escalate.
Applying these strategies is key to reducing financial risk, ensuring projects remain fair for all stakeholders and are well managed from start to finish.
Minimising financial risk on construction projects involves addressing various items that impact time, cost, and quality. Key stakeholders, including contractors, subcontractors, suppliers, consultants, the principal/client, end users, and funders, all carry some level of risk. Items that should be considered include:
Client: Should provide a clear brief with a realistic programme and budget. The client should be aware of their statutory, legal, and financial obligations and instruct the project team accordingly. Variations should be kept to a minimum and scope outside the construction contract, such as utility connections and fittings, fixtures and equipment, should be planned and budgeted for.
Planning and Design: The design and construction team needs to meet all statutory, planning, consent and grant requirements, manage neighbours and environmental impacts, and conduct thorough site investigations. An economical and efficient design that meets the brief is required, which needs to be reviewed at various design milestones. Materials with reasonable lead times need to be selected.
The design should be peer-reviewed for errors and omissions. Contractors’ advice for constructability should be considered.
Procurement and Contracts: A project team with experienced companies and personnel should be selected. All procurement options should be evaluated. Financial and performance checks should be undertaken. Use of standard forms of contract should be selected where possible, with fair risk assignment. There should be clear provisions and mechanisms for contract and financial management, and dispute resolution. Appropriate insurances, bonds, warranties, and guarantees should be provided.
Financial: There should be quantity surveyors in both the consultant and contractor teams to ensure accurate cost management. The client’s budget should be reviewed, and a cost plan set up with reasonable contingencies that are managed at the design stage milestones. Good tender documentation should be provided, and competitive tenders should be sourced. All tender tags should be reviewed and managed. There should be rigorous financial oversight with
regular cost reporting during design and construction.
Programme: This should include realistic time for design, construction, fit-out and other key milestones. The contractor’s programme should include adequate allowance for risk, delays, and identification of key dates. All programmes should be reviewed, monitored and revised as needed.
Project Management: A collaborative approach is key, led by an experienced project manager, and principal’s representative. As part of this process, all parties should comply with their contractual requirements. The project should set up an information-sharing platform for contract processes and utilise the latest technology to produce efficiency. The project management should be proactive with regular meetings to resolve any issues. A project reporting framework incorporating a risk management system needs to be set up and managed.
Conclusion: Financial risks, once identified, need to be reported to the project management team and client promptly.
Senior Cost Manager, Chris Sale Consulting
Engaging a quantity surveyor (QS) early in the project is essential for developing accurate cost estimates and realistic budgets based on reliable data and the QS’s experience with similar projects. Early involvement allows for the identification of potential cost issues from the outset, ensuring that the project remains financially viable. The initial design phase must include consultations with the client to ensure the design aligns with their expectations and requirements, confirming that the budget supports the intended design.
The QS should also allocate appropriate cost contingencies to address potential unknowns.
These contingencies act as a financial buffer and should be reviewed regularly as the design progresses. Continual cost updates during the design phase help identify scope creep, and incorporating accurate market rates at each stage ensures that the budget remains aligned with current pricing trends, reducing the risk of financial surprises.
Clear and detailed tender documentation such as drawings, scope of work, specifications, and contracts, enables accurate pricing and minimises variations, safeguarding the contingency fund during construction. Additionally, selecting the right
procurement method and tendering approach is crucial to reducing financial risks. This choice ensures that time constraints are met while maintaining the project’s financial stability.
Throughout construction, generating detailed cost reports helps monitor expenditures and identify potential concerns or cost overruns. These reports allow the project team to implement corrective measures, such as value engineering or other strategies, to keep the project within budget. Overall, early QS involvement and continuous cost management throughout the project ensure its financial health and success.
By WoodSolutions
The construction industry prioritises improving the bottom line – a focus that remains crucial for long-term viability. However, as awareness of climate change intensifies, governments and consumers are raising expectations for the built environment sector. The concept of the triple bottom line –encompassing social, environmental, and economic performance – is driving the introduction of stricter regulations and sustainability rating systems.
Timber and other low embodied carbon materials present an opportunity to address embodied carbon challenges while maintaining profitability, offering a sustainable pathway that aligns with both financial and environmental goals.
According to Infrastructure Australia, embodied carbon contributed to 10% of Australia’s total carbon emissions in 2023. This statistic underscores the urgent need for the construction industry to embrace decarbonisation.
Governments and developers are increasingly prioritising low-carbon solutions, driving demand for buildings with reduced embodied carbon footprints. By equipping themselves with the necessary knowledge and practical tools to accurately measure and manage embodied carbon, quantity surveyors can play a pivotal role in advancing sustainable building practices.
Embodied carbon refers to the carbon associated with the building materials and the construction processes throughout the lifecycle of a building or infrastructure.
The primary sources of emissions in the construction sector stem from the burning of fossil fuels for energy and the use of carbon-intensive materials. Upfront carbon emissions, which occur before a building is occupied, are projected to account for half of the total carbon footprint of new construction by 2050. Approximately two-thirds of these upfront emissions are linked to the substructure, superstructure, and façade. As a result, it is essential for industry to focus on structural building materials and develop strategies to reduce embodied carbon.
In Australia, the construction industry is increasingly focusing on reducing embodied carbon through established guidelines and rating systems. Two prominent frameworks are NABERS (National Australian Built Environment Rating System) and Green Star, both developed to assess and promote sustainability in building practices. These frameworks reflect Australia’s commitment to reducing embodied carbon in the built environment, providing industry professionals with structured approaches to measure and mitigate emissions associated with construction materials and processes.
Quantity surveyors can position themselves as sustainability advocates within project teams by influencing and managing embodied carbon through material selection and lifecycle cost analysis. By integrating carbon metrics into cost assessments, quantity surveying professionals can drive sustainable practices without compromising financial objectives. Incorporating embodied carbon data into cost estimation software enables quantity surveyors to identify materials with lower carbon footprints that
align with budgetary constraints. This dual-focus approach ensures that sustainability goals are met without exceeding financial limits.
In addition to evaluating initial costs, quantity surveyors perform lifecycle cost analyses to assess the total budgetary impact of building materials over their lifespan. By incorporating embodied carbon assessments into these analyses, quantity surveyors can pinpoint cost-effective solutions for reducing carbon emissions. This integrated approach aids in selecting materials that deliver both longterm environmental and economic advantages.
1. Establish a baseline for embodied carbon in your projects.
2. Collaborate closely with architects, engineers, and other project teams to get the measurements right.
3. Use benchmarking tools to set reduction targets.
4. Evaluate and compare materials using embodied carbon data.
5. Report findings to clients with actionable recommendations.
WoodSolutions provides continuous education for quantity surveyors to stay informed on emerging materials and timber technologies that reduce embodied carbon and offer cost advantages. Tools such as the WoodSolutions EPD database can be used to access embodied carbon data for Life Cycle Analyses.
NABERS has introduced an Embodied Carbon rating tool to assess upfront emissions, while the Green Building Council of Australia has updated its standards to encourage the use of low embodied carbon materials.
Take advantage of the rising opportunity to lead the way in reducing the construction industry’s carbon footprint by becoming an expert on embodied carbon measurement practices. Learn more and find more tools at WoodSolutions.com.au
This advertorial has been sponsored and provided by AIQS Corporate Partner, WoodSolutions.
By Linda Lodge and Damon Roast
With construction cost escalation expected to remain elevated until at least 2027 across Australia, it’s simply not possible for health sector projects to ‘wait it out’. The pipeline of health projects is urgent and vast, and our growing communities can’t afford for these crucial infrastructure projects to fall behind or blow out.
Bodies such as Infrastructure Partnerships Australia are already sounding the alarm, with serious concerns about the ability of public and private developers to deliver excellence, complexity and scale at the right cost and on the right schedule.
Strong activity is likely to mean very strong ongoing competition for health construction resources.
However, even without a miracle cure for escalation (which is expected to remain around 5% per annum on average nationally), there are some
measures that developers of health infrastructure can take to mitigate the impacts of escalation and set projects up to navigate the conditions.
One cause of escalation remaining higher than expected is the very strong levels of construction underway across the country. Health sector construction has risen strongly over the last five years to a new long-term high in 2023/24 (~$8b in the construction components of projects started). This is expected to be matched or even exceeded in 2024/25 and remain high for several years, with a robust health construction pipeline in all capital cities (especially the larger ones) as well as in major regional areas, and a massive boom in health projects in Queensland. Strong activity is likely to mean very strong ongoing competition for health construction resources.
Another catalyst for cost escalation is the increasing size and complexity of health projects. This evolution is not unique to health, but health’s position at the forefront of the technology
frontier, the rise of the life sciences and research sectors, and increased demand for new vaccines have filtered through to the health construction pipeline. With greater size and complexity come greater construction lead times, which prolong health construction and push up costs.
With a large portion of recent health projects in the public sector, there has been a limited selection of procurement methods implemented with a focus on subcontractor pricing, enterprise bargaining agreements, and material price hikes. This has put a strain on lump-sum pricing, and the inclusion of risk, contingency or uncertainty in contractor pricing. Public-private partnerships, for example, have been used only sparingly while private-led projects have been quite sparse. While the public project pipeline remains robust, increased scrutiny on public finances, especially in the eastern states, points to a future in which financing and procurement could see changes.
While NSW Government projects have adopted the GC21 Design Finalisation and Construct Contract, there may be opportunities to consider alternative procurement routes for complex projects that could result in more amicable risk sharing, best-for-project design decisions and better overall value for money.
Ultimately, no particular procurement option can defeat escalation.
In the Managing Contractor model, the contractor’s fees are set up front, with design and subcontractor tenders handled on an open-book basis. This reduces cost risk but increases administrative oversight, while a two-stage contract separates design development and construction, offering reduced risk and clearer scope for the developer.
In the Guaranteed Maximum Price (GMP) approach, the contractor’s fees and a maximum price are agreed on upfront, with any savings benefiting the developer.
This provides cost certainty but potentially limits the contractor’s incentive to make optimal design decisions.
Ultimately, no particular procurement option can defeat escalation. The most important thing is not so much the procurement method itself, but that the methodology is appropriate to the size, nature and risk allocation of the project.
In live health environments, there are extra risks, and these come with a premium price tag.
Given the specialised requirements of health projects and the expected competition for resources, it will also be important to engage early with contractors and subcontractors. A well-timed, well-planned and wellthought-through tender with a rightsized tender list will be crucial to a competitive tender outcome. A dream scenario for any developer.
Infrastructure projects have always faced risks such as contamination, latent conditions and inclement weather. These risks persist, but others have emerged – such as supply chains, procurement of materials, availability of labour, and of course escalation. The larger and longer the project, the greater these risks become. In live health environments, there are extra risks, and these come with a premium price tag. For example, working in a live environment with multiple stakeholders may create complexities for staging and temporary works. Retaining parts of the existing building fabric could introduce spatial constraints, particularly for building services – or even result in non-compliance with the latest models of care.
…There’s never been a more important time to discover how to achieve more with less.
Contractors are carefully considering risk profiles and pricing in risk, so it’s important to be clear about a project’s risks from the start and allocate risks to the party best equipped to manage them.
The following strategies can assist in anticipating, mitigating and managing some of the key risks:
• Regular risk workshops with the project team to keep risk registers up to date
• Early engagement of the consultant team and subcontractor design teams to ensure constructability and management processes are checked for suitability
• Inclusion of a strong change management team to ensure the end users are involved in the design process, mitigating the need for changes down the line.
Over the last few years, there has been a decline in productivity in the construction sector. While the contributing factors to that have been positive to workers, such as the introduction of a five-day working week
on building sites, it has also contributed to longer construction timelines and increased costs. With a booming pipeline of projects and ongoing skills shortages and labour constraints, there’s never been a more important time to discover how to achieve more with less.
Technological and process innovations such as BIM, automation, digital twins, and modular construction methods are becoming more accessible and offer opportunities for achieving greater speed, accuracy, and efficiency – which could help boost productivity and put downward pressure on cost escalation. It will also be important to reset the culture of the industry to improve the retention of skilled workers, especially given the changing work expectations of younger generations.
In health care, early diagnosis and proactive intervention can often prevent further complications or deterioration. Securing tomorrow’s health infrastructure requires the same treatment, starting today.
By Adrian Barwick
The new right to disconnect (RtD) under the Fair Work Act 2009 (Act) became law with the successful passage through the Federal Parliament of the Fair Work Legislation Amendment (Closing Loopholes No.2) Bill 2023 on 12 February 2024.
From 26 August 2024, the new RtD laws took effect for national system employers with 15 or more employees. On 26 August 2025, the RtD laws will take effect for small businesses with fewer than 15 employees.
The RtD is intended to promote and create a work-life balance culture by limiting the circumstances when employees are required to respond to contact by an employer or third party outside of ordinary work hours. The Act states:
An employee may refuse to monitor, read, or respond to contact, or attempted contact, from an employer outside of their working hours, unless their refusal is unreasonable.
The Act also states:
An employee may refuse to monitor, read or respond to contact, or attempted contact, from a third party if the contact or attempted contact relates to their work and is outside of the employee’s working hours unless the refusal is unreasonable.
The key RtD exception is where the employee’s refusal is unreasonable.
The RtD is also recognised as a protected workplace right under the Act. This means an employer is prohibited from taking adverse action against an employee because of their
right not to respond to communications from their employer or a third party outside of their ordinary hours of work.
…The employee and employer must first try to resolve their dispute through discussions at the workplace level.
The prescribed matters under the Act that must be considered when determining whether an employee’s refusal is unreasonable include:
• Considering the reason for the contact
• The method of contact and the disruption caused to the employee by the contact
• Whether the employee is paid for remaining available in the period when contact is made or attempted or paid to work additional hours outside their ordinary hours of work
• The nature of the employee’s role and level of responsibility; and
• The employee’s personal circumstances, including any family or caring responsibilities.
The prescribed matters are nonexhaustive, so other considerations may be relevant.
If an employee refuses out-of-hours contact and this leads to a dispute with the employer, the employee and
employer must first try to resolve their dispute through discussions at the workplace level. The employer’s dispute procedures could be followed as a way of facilitating those discussions.
If the dispute cannot be resolved, either party can apply to the Fair Work Commission (FWC) to do either one or both of the following:
1. Make a ‘stop order’
2. Otherwise deal with the dispute.
The FWC can make orders it considers appropriate to stop ongoing or future conduct, such as:
• An order to prevent an employee from continuing to unreasonably refuse to monitor, read or respond to contact or attempted contact
• Ordering an employer to cease requiring an employee to monitor, read or respond to contact or attempted contact, or
• Ordering an employer to cease disciplinary or other action against an employee for refusing contact.
The FWC’s powers to make a stop order do not extend to awarding compensation. This means an aggrieved employee cannot seek payment for any alleged financial loss or emotional distress due to the employer (or third party) continuing to contact them unreasonably outside of working hours.
However, contravening an FWC stop order may result in the Court making civil remedy orders (such as a compensation order) and an order imposing a pecuniary penalty.
The FWC can deal with the dispute as it considers appropriate, such as by mediation, conciliation, making a recommendation or expressing an opinion.
Different industries and occupations have difference work practices that shape the extend to which the RtD provisions apply.
By agreement between the parties, the FWC may resolve the dispute through arbitration. The FWC’s decision is final and binding on both parties.
With effect from 26 August 2024, the FWC has included RtD terms in modern awards. Different industries and occupations have different work practices that shape the extent to which the RtD provisions apply.
As an example, the Clerks – Private Sector Award (Clerks Award) provides for an employee’s right to disconnect under the Act. However, the Clerks Award provides that the employee’s right does not prevent an employer from contacting, or attempting to contact, an employee outside of working hours in circumstances including to notify them under the Clerks Award’s recall to work provisions.
Parties can make applications after 26 August 2024 to the FWC to vary the RtD terms in individual modern awards to address the specific circumstances of particular industries and occupations.
The FWC will create non-legislative, non-binding guidelines that are likely to clarify its approach to enforcing the RtD laws. Presently, the FWC has not committed to a timeline for the guideline’s availability but is expected to publish guidelines once it has dealt with some disputes concerning the operation of the right, allowing it to have some understanding of the practical issues for which guidance may be required.
Consider how these changes might impact your business operations, including what processes might need to be introduced to ensure that you manage the RtD in a way that minimises legal risk.
Steps may include:
3. Undertaking a review of your employment agreements to ensure terms are consistent with the RtD laws, such as hours of work, overtime and remuneration terms
4. Updating relevant staff position descriptions to reinforce expectations around out-of-hours work
5. Introducing a communications policy that defines expectations around initiating and responding to out-ofhours contact, as well as dispute resolution mechanisms
6. Training staff, supervisors and managers on the employer’s policies and procedures relating to the RtD laws.
Clear communication with staff about role expectations and early dispute resolution in the workplace is critical to staying out of the FWC.
DAISY WU Cost Manager, Linesight
Q: WHAT IS YOUR JOB AND WHAT DO YOU DO ON AN AVERAGE DAY?
A: I am a client-side Cost Manager, providing quantity surveying and commercial management services across various sectors, including residential, commercial, mixed-use, healthcare, aged care, education, industrial, data centres, and life sciences.
During the pre-tender phase, I develop cost plans and estimates from project conception through to tender. As designs evolve, I advise clients on budgets and conduct value management to help achieve the most cost-efficient outcomes.
In the tender phase, I support due diligence and tender evaluations to assist clients in selecting the most suitable contractor.
This often involves bridging and cost normalisation exercises to ensure alignment between our estimates and contractors’ proposals.
Post-tender, I produce cost reports for clients and lenders, conduct site inspections to assess construction progress, and provide valuations for completed works. I also manage changes, including assessing variations due to contractor or client-initiated scope adjustments.
Beyond financial management, I assess contractual and project aspects to inform payment recommendations for clients and lenders.
In recent years, I’ve expanded my experience and expertise to include tax depreciation and embodied carbon management. This allows me to integrate cost management with my passion for sustainability, delivering innovative and environmentally conscious solutions for clients.
A: What I love most about my job as a Cost Manager is the diversity it offers.
No two projects are the same, and every day brings new challenges and opportunities to learn. I get to work across a variety of sectors – from healthcare to data centres – and contribute to projects that leave a tangible impact on communities. I also enjoy the balance between technical precision and collaboration. On one hand, I analyse costs and manage budgets with meticulous detail.
On the other hand, I work closely with clients, architects, engineers, and contractors to find innovative, costeffective solutions. It’s rewarding to see how my advice helps clients achieve their goals while staying within budget. Another highlight is site visits.
Witnessing a project come to life, from concept to completion, gives me a sense of pride and fulfilment. Lastly, I’m particularly passionate about sustainability. I’ve had the chance to integrate cost management with embodied carbon assessments, which lets me contribute to environmentally conscious projects. This alignment between my professional skills and personal values makes my work even more meaningful.
My responsibilities required me to collaborate with a wide range of internal and external stakeholders, from clients and contractors to architects and engineers.
Q:
A: Coming from a background as a Chinese International student in an English-speaking country, I initially shared a common perception with many of my student peers. Quantity surveying often seemed like a regular, predictable, office-based job where we spent a significant amount of time in front of a computer. While this work could feel mundane, repetitive, and tedious at times, it also appeared to be a safer and easier career choice compared to other roles in the building industry that require more direct human interaction.
For many of us, the thought of navigating language barriers and cultural differences made clientfacing or highly interactive roles feel intimidating. However, not long after I was onboarded, I realised the critical importance of communication to thrive as a quantity surveyor.
My responsibilities required me to collaborate with a wide range of internal and external stakeholders, from clients and contractors to architects and engineers. I quickly discovered that the role was far more peoplefacing, dynamic, and interactive than I had initially imagined. This challenge turned out to be incredibly fulfilling, pushing me out of my comfort zone and enabling me to grow both professionally and personally.
Speaking of stepping out of my comfort zone, I became conscious early on of the importance of advancing my soft skills to thrive in the industry and progress in my career. Since starting my first job at a boutique quantity surveying consultancy in Melbourne in 2018, I have applied myself diligently to networking and volunteering to build connections and broaden my horizons.
Some highlights of my journey include serving as the first female President of the Construction Students Association at the University of Melbourne, where I helped foster a sense of community among aspiring professionals. I also led the podcast for the Chartered Institute of Building Tomorrow’s Leaders, producing nearly 30 episodes that engaged industry experts and emerging leaders.
Additionally, I’ve had the privilege of serving as a speaker and mentor at various professional organisations, such as The Australian Institute of Building, Built Industry Group and Sydney Build Expo.
During this time, I also advanced my quantity surveying career, working with two leading global consultancies. Most recently, in giving back to the profession, I joined the committee of the Royal Institute of Chartered Surveyors, furthering my commitment to shaping and supporting the next generation of construction professionals.
In writing this, I also feel immensely grateful as I anticipate delivering the opening keynote at the Women in Construction Summit 2025 in Melbourne.
It’s a milestone that reminds me of how far I’ve come, not just in my career but in embracing personal growth and stepping out of my comfort zone. If I had only (and inaccurately) identified myself as a cost management professional whose role is limited to spending most of my time behind a computer, I wouldn’t have come this far.
Recognising the broader scope of opportunities in my profession –where communication, leadership, and connection-building are just as vital as technical expertise – has been transformative. It pushed me to network, volunteer, and pursue leadership roles that not only advanced my career but also enriched me as an individual.
…Communication, leadership, and connection-building are just as vital as technical expertise…
This journey has been about more than just career development; it’s been about breaking boundaries and redefining possibilities for myself and others in the industry.
As I prepare to speak at the Summit, I feel honoured to share my story and encourage others, particularly women, to see beyond traditional perceptions and explore the full potential of their roles in construction.
…Embrace the power of networking connecting, and curiosity.
Q:
A: My advice to aspiring quantity surveyors is to think beyond the technical aspects of the profession and embrace the power of networking, connecting, and curiosity.
While technical skills like cost estimation and project management are fundamental, the ability to build relationships is just as crucial for longterm success.
Start early by attending industry events, joining professional organisations, and reaching out to mentors who can guide you.
Building connections not only broadens your horizons but also opens doors to opportunities you may not even know exist.
Stay curious. The construction industry is vast and ever-evolving, offering exposure to a variety of projects and disciplines. Be open to learning from every experience, whether it’s shadowing a senior colleague, exploring new software tools, or diving into unfamiliar sectors like sustainability or data centres.
Finally, don’t be afraid to step out of your comfort zone. Whether it’s volunteering, joining an industry association, or even speaking at an event, these experiences will develop your confidence and soft skills, which are invaluable in a people-facing profession like quantity surveying.
Quantity surveying is much more than a desk job; it’s a career full of dynamic challenges, collaboration, and growth. Dive in with an open mind and a proactive attitude, and you’ll thrive.
By Angela Hucker
Women bring something unique to leadership: a natural inclination towards collaboration and inclusivity. The construction industry, notorious for its hierarchical and sometimes adversarial structure, could benefit greatly from a leadership style that values listening, consensus-building, and teamwork over ego and competition.
In a women-led construction industry, we’d likely see:
• Greater communication on job sites and in boardrooms
• More inclusive decision-making that considers a variety of perspectives
• Fewer adversarial disputes and more emphasis on problemsolving.
Rather than a culture of ‘command and control,’ there would be a shift towards team-based leadership – where decisions aren’t just dictated from the top down but shaped collectively by those on the ground. Studies have shown that companies with more women in leadership positions tend to foster more open communication and a greater sense of belonging among their teams.
Safety is one of the most crucial aspects of the construction industry. Women leaders tend to emphasise risk management, employee wellbeing, and long-term thinking, which would likely translate into stronger safety protocols, better mental health initiatives, and an industry that prioritises a work-life balance.
…Strong leadership is about adaptability, resilience, and emotional intelligence.
Instead of brushing off long hours and high-stress environments as ‘part of the job,’ a women-led construction industry might introduce:
• More flexible work arrangements to accommodate workers with families
• Stronger safety regulations and compliance enforcement
• Improved workplace culture, reducing incidents of harassment and discrimination.
We already know that diverse teams make better decisions, and when it comes to safety, those decisions could literally be lifesaving. The ‘she’ll be right’ attitude that sometimes pervades high-risk industries could be replaced with a proactive, people-first approach to site management.
A construction industry led by women would also rethink what we build and how we build it. Female leaders have long been champions of sustainable, forward-thinking innovation, and in an industry that has one of the largest carbon footprints in the world, this could be revolutionary.
Imagine if sustainability wasn’t just a compliance issue but a guiding principle in every project. A women-led industry could see:
• More green buildings and energyefficient designs
• Greater investment in long-term sustainability over short-term cost savings
• A holistic approach to urban planning, considering communities over just infrastructure.
A women-led future in construction would almost certainly emphasise durability, adaptability, and environmental consciousness over pure profit-driven development.
One of the greatest myths in the industry is that leadership should be tough, aggressive, and unapologetically competitive. But the reality is that strong leadership is about adaptability, resilience, and emotional intelligence – traits that are often associated with female leaders.
A women-led construction industry would likely redefine leadership itself, prioritising:
• Mentorship and professional development
• Emotional intelligence in management
• A more diverse pipeline for future leaders.
It’s no secret that industries with more diverse leadership perform better. A study by McKinsey & Company found that companies with gender-diverse leadership teams are 21% more likely to experience above-average profitability.¹ So, if women led construction, would the industry be more profitable? Possibly. But more importantly, it would be more sustainable, more peoplefocused, and more innovative.
If women ran construction today, the ripple effects would be felt for generations to come.
Young girls in school would grow up seeing themselves in the industry, not as the exception but as a norm. More women would enter the trades, more female voices would be present at the decision-making table, and the industry itself would become more accessible, more inclusive, and more dynamic. There would be:
• More women in apprenticeships and trade programs
• More female mentors for young professionals entering the field
• A stronger push for equal pay and career progression opportunities.
And this isn’t just about women helping women – it’s about creating a construction industry that benefits everyone. A sector that values diversity of thought, skill, and experience is an industry that will continue to thrive, innovate, and adapt to the needs of the future.
The real question isn’t just, “What if women ran construction?” – , “Why aren’t they already?”
While progress has been made, barriers still exist. Women currently make up only a small percentage of leadership roles in construction, but that doesn’t mean the future can’t look different.
The industry is changing. Slowly but surely, more women are entering, leading, and shaping construction.
And as they do, they bring with them a new vision – one that challenges old assumptions, breaks down unnecessary barriers, and redefines what leadership in construction can and should be.
So, let’s not just imagine a women–led construction industry – let’s start building it. Because if there’s one thing women have proven time and again, it’s that when given the opportunity, they don’t just take the lead – they transform industries for the better.
And construction? It’s next in line.
1 Dixon-Fyle, S., Dolan, K., Hunt, D.V. & Prince, S. 2020, ‘Diversity wins: How inclusion matters’, McKinsey & Company, 19 May <https://www. mckinsey.com/featured-insights/diversity-and-inclusion/diversity-wins-how-inclusion-matters>.
THE BUILDING COST INDEX IS PUBLISHED IN THE PRINT VERSION OF THE BUILT ENVIRONMENT ECONOMIST.
IT CONTAINS DATA THAT CAN BE USED AS A PREDICTOR FOR THE ESTIMATED TIMES FOR DESIGN AND CONSTRUCTION AND INCLUDES A SUMMARY OF THE PAST, PRESENT AND ESTIMATED FUTURE CONSTRUCTION COSTS.