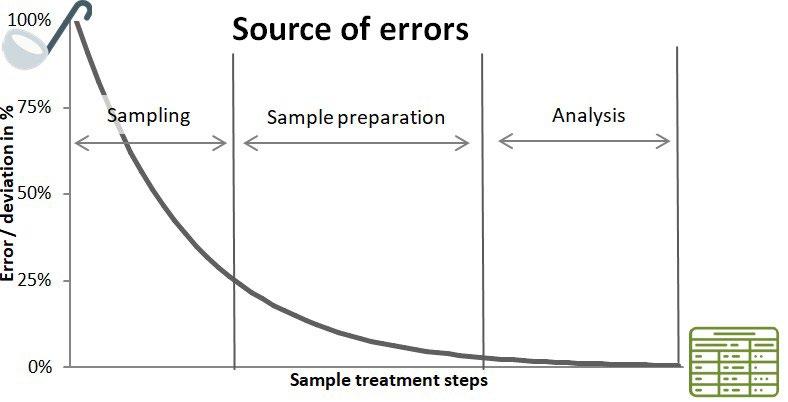
16 minute read
A. Schlemminger................................................................................................................................................... pag
Laser OES - How an efficient melt shop monitoring tool tackles increasing energy and raw material costs
A. Schlemminger
Winter 2021-2022. The steel industry faces one of the most significant increases in energy prices in a short period. On the other hand, the shortage of alloying elements makes completely new process designs economically attractive. In this environment, dynamic process control is becoming increasingly important. But the availability of in-situ measurement data from the process is crucial for successful dynamic process control. Until now, the composition of the slag was missing from this approach. Due to the time-consuming sample homogenization before analysis, the chemical composition of the slag was available post-mortem. But this has changed now, and the extremely fast Laser Optical Emission Spectroscopy (Laser OES) solves that issue. The measurement rate in the kHz range generates such large amounts of data that homogenization of data instead of physical samples is possible from now on. With early-stage deviation detection, the precise adjustment of slag parameters in small steps can tolerate more considerable variations in input materials.
KEYWORDS:LASER OES, LIBS, SLAG ANALYSIS, SAMPLE PREP. FREE ANALYSIS, MELT SHOP MANAGEMENT, LADLE FURNACE OPTIMIZATION, IN SITU PROCESS CONTROL, STEELMAKING EFFICIENCY;
TODAYS ANALYSIS OF HETEROGENOUS MATERIALS The simplest and fastest method to analyze heterogeneous materials such as slags, dust, minerals, alloying materials, or others was the measurement with a (handheld) XRF device. After 2-4 repeated measures, an average analysis value was generated. Due to the few measurements, outliers resulting from sample heterogeneity can strongly influence the analysis result. Hence, this approach is considered somewhat unreliable for process control. Nevertheless, handheld XRF instruments are prevalent due to their usability and low investment.
Until now, the most common way to analyze heterogeneous samples quickly and accurately at the same time relied on X-ray-based technologies in combination with prior sample homogenization. This approach requires a solidified sample, undergoing plenty of preparation steps. The samples are first broken in a crusher within a few seconds and then magnetically demetallized. The subsequent grinding step takes approximately 2-5 minutes before the Alexander Schlemminger
QuantoLux Innovation GmbH, Germany alexander.schlemminger@quantolux.de
ground material is pressed into a pellet. Even if the final analysis in an XRF laboratory instrument takes less than one minute, the overall analysis time is over 10 - 15 minutes. Very high analytical needs required even more complex preparation steps. The measured sample reaches the maximum homogeneity in a glass beat or during the ICP-OES analysis. Both methods show even better analytical performances, like the pressed pellet XRF. However, they require considerably more than the 10 - 15 minutes mentioned. DISADVANTAGES OF TODAYS ANALYSIS APPROACHES Sample preparation error As Fig. 1 displays, the sample preparation risks causing a deviation, the so-called sample preparation error. General causes for sample preparation errors are e.g., sample carryovers from the previous to the subsequent samples or negative human influence for non-/partially automated systems. For instance, contamination during the transport of the sample from one preparation step to the other can reduce representativeness.
Fig.1 - Impact of the individual steps on the measurement error from sampling to analysis.
Particle sizes A too-short grinding time can lead to too large particle sizes since the material does not pulverize sufficiently. If the grinding time is too long, agglomeration effects may arise, causing the particle size to grow again. In both cases, the risk of segregation in the subsequent pressing process increases considerably. Beneath the particle size, the wrong pressing speed or the pressing force can lead to segregations within the pressed tablet. The sample is not compacted sufficiently, and particles segregate inside the pellet.
Additives / binders Alternatively, samples can be molten down or digested by liquid for XRF glass beat or ICP-OES measurements. Here the risk of segregation is substituted e.g., with the risk of faulty weighing of the digestion agent. Each of the deviations described can reduce the representativeness of the sample result and lead to incorrect decisions in process control. Thus, the efficiency is reduced.
High equipment, labor, and maintenance costs To eliminate sample preparation errors and reduce labor costs, laboratories use more and more partial or complete automation. In addition, the use of selected laboratory crushers and mills can reduce contamination by sample carryover and presses with controlled lifting speeds to minimize the risk for segregation. Nevertheless, the high number of individual, specialized devices results in increased costs for purchase, maintenance, and servicing. In addition, the manual effort and the costs for the required automation for sample handling are significant. Automated
sample preparation systems alone easily cost more than 200 k€ plus 5 k€ maintenance per year. Binding materials, sample trays, and agents for melting or acid digestion can additionally exceed 1€ per sample.
Remote instead of onsite analysis Another disadvantage is that the analyzer and the sample preparation equipment could hardly find a space close to the sampling location. The complexity of sample preparation, automation, and analytical equipment necessary to perform the analysis forced an analysis in the main laboratory. Therefore, (slag-) samples had to be first cooled at the sampling site, then packed and usually sent to the laboratory manually or by pneumatic tube. The disadvantages of additional cooling, packaging, transport times and associated risk of sample contamination are on hand.
Fig.2 - Impact of the individual steps on the measurement error from sampling to analysis.
Long analysis time However, as Fig. 2 shows, the most significant disadvantage is the long period of 6-30 minutes from sampling to the availability of reliable results. Usually, neither converter nor ladle furnaces can wait that long for results due to throughput and energy efficiency reasons. Production continues, and as Fig. 3 displays, the analysis results optimize subsequent batches post-mortem.
Fig.3 - Deviation in steelmaking process due to post-mortem analysis.
In both cases, delayed analysis results can lead to instability in the process, increased refractory consumption, reduced product quality, reduced throughput, higher energy consumption, poor product yield, and many other issues.
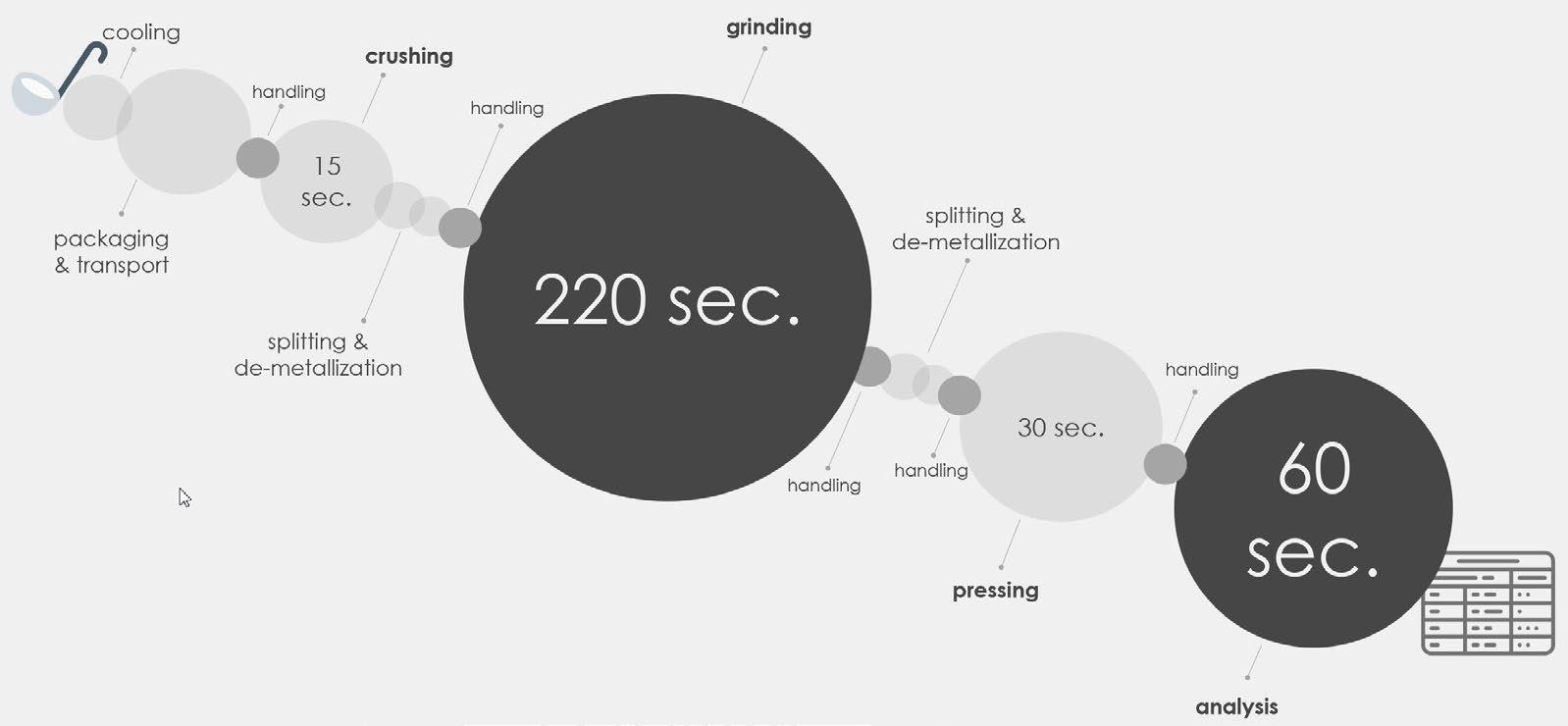
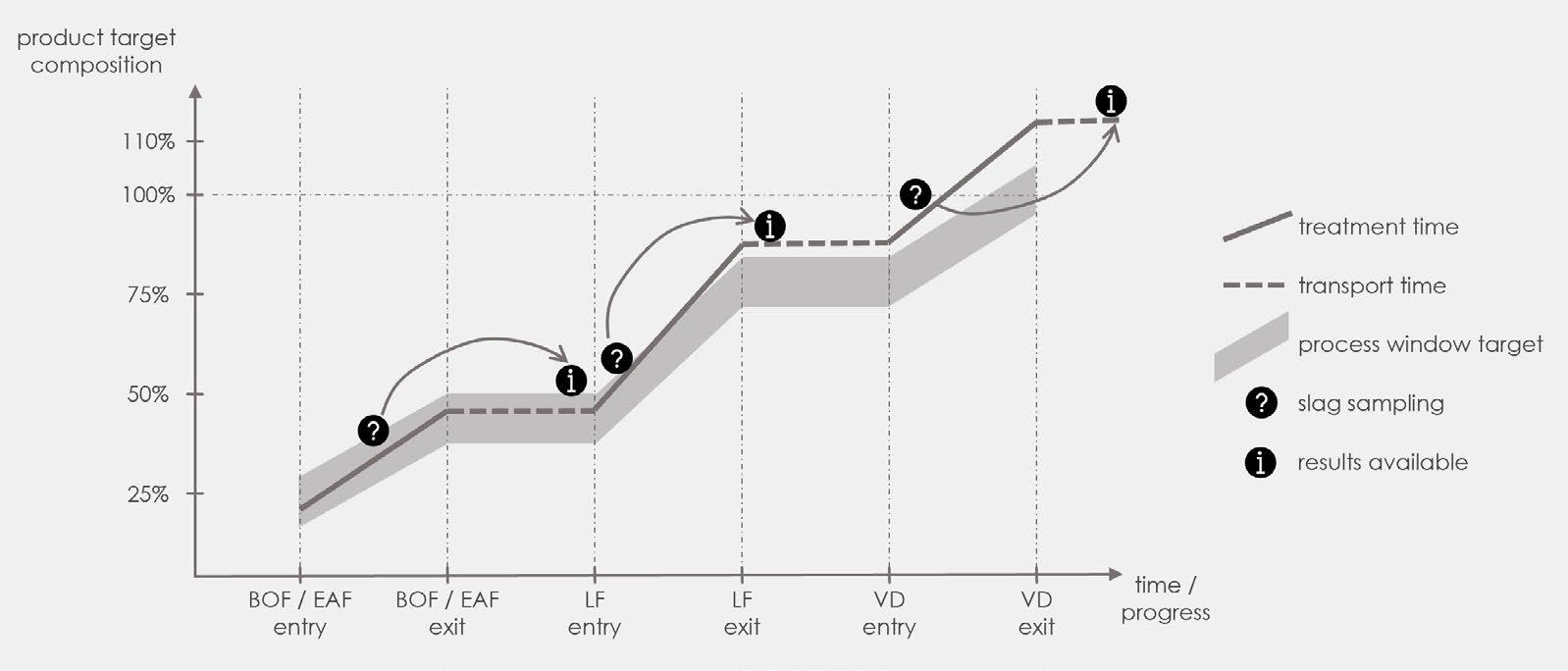
RAPID, SAMPLE PREP. FREE SLAG ANALYSIS BASED ON LASER OES Laser OES principle Laser-based optical emission spectrometry, or Laser OES, can be an alternative to X-ray-based analytical approaches. It works equivalently to the established spark optical emission spectrometry (Spark OES) with the difference that a laser pulse instead of an electric spark generates the plasma. Therefore Laser OES analyses metals and non-conductive materials such as slags.
Fig.4 - left: Laser OES principle – right: Laser OES Plasma ignited on slag.
Fig.4 shows that a pulsed laser focusing on the sample raises the surface temperature in a tiny area.
A few micrograms of the sample material convert into plasma at up to 20,000 °C. During the regression of this plasma, a spectrometer collects the emitted light, which is specific to the sample's composition in the measurement position. The spectrometer converts the light signal into a piece of digital information. A Laser OES analyzer generates thousands of analysis values within seconds with a multi-digit kHz measurement frequency. Based on that huge amount of data, the digital homogenization of data replaces the physical homogenization of samples. Individual points are analyzed one after the other, and the measurement data is then homogenized in a fraction of a second using an appropriate calibration. In this way, a representative analysis result is generated even for highly heterogeneous materials.
Calibration A specific calibration interprets each spectrum alone or a specific amount of spectra based on various mathematical calculations. The most straightforward approach is to compare the intensities and compare them with the concentrations of the reference materials.
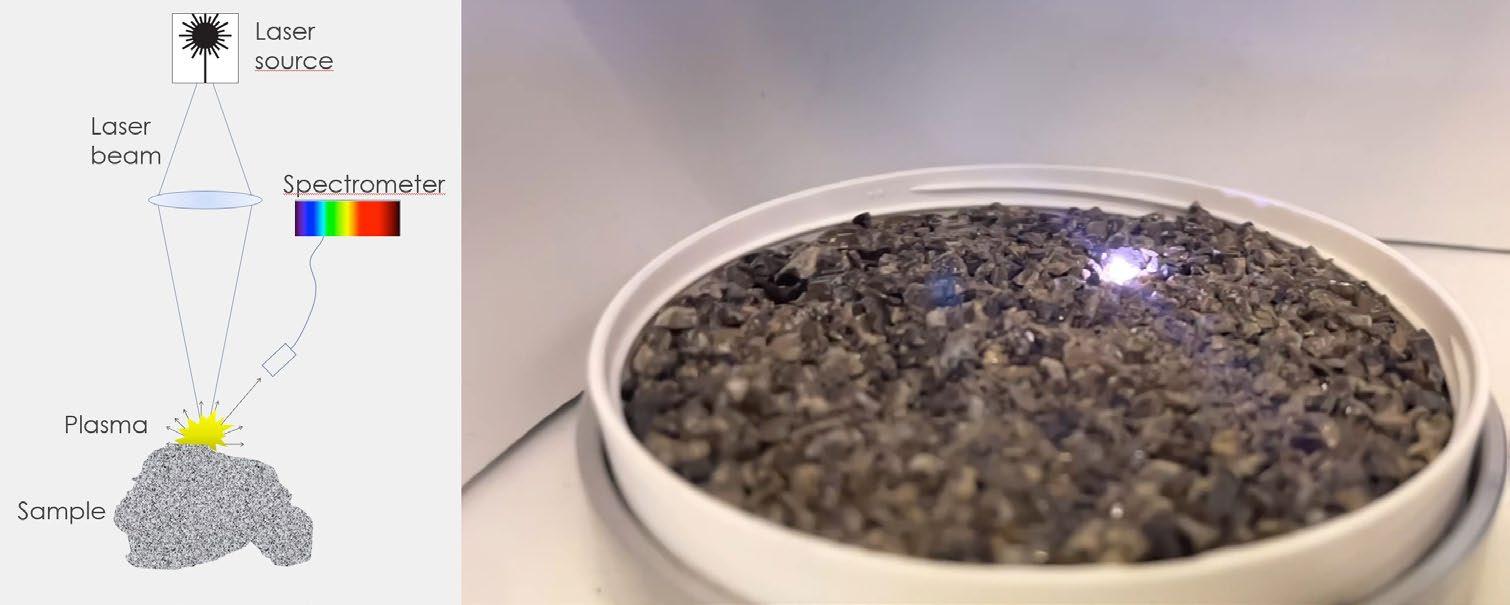
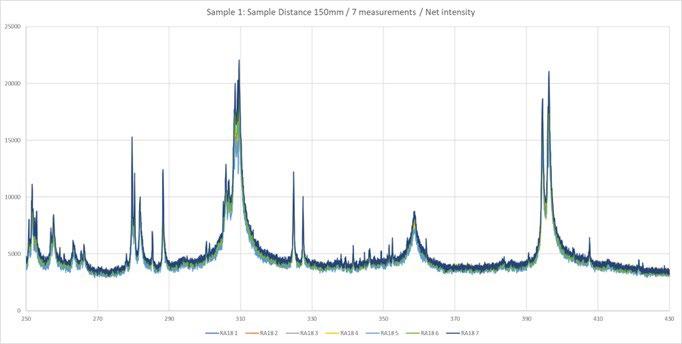
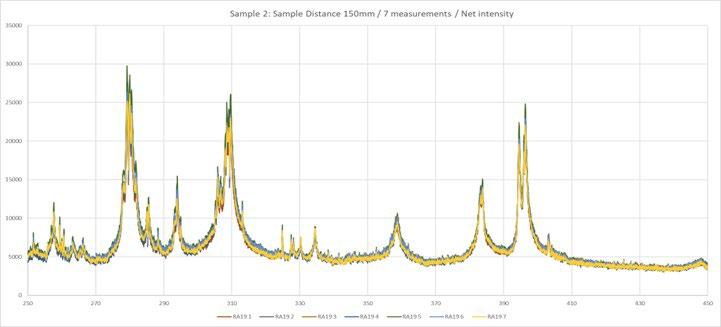
Fig.6 - Laser OES plasma on high concentration material.
As can be seen in the metal-making-related spectra shown in Fig. 5 and Fig. 6, in the simplest case, already the bare eye differentiates concentrations.
Precision and representativeness Compared to other OES-based analytical approaches, the Laser OES works with the significant advantage of a maintenance-free and highly stable laser. The precise intensity of monochromatic light ignites the plasma with a precisely determined amount of energy. Furthermore, the accuracy of the plasma-excitation position is defined down to a few micrometers by the focus point of the Laser.
Fig.7 - Reproducibility of a heterogeneous steel making slag sample (measurement in Fig. 4).
Compared to other OES-based analytical approaches, the Laser OES works with the significant advantage of a maintenance-free and highly stable laser as an excitation source. Laser lifetimes of 100,000 hours and more ensure that the excitation source runs without interruption for at least 10 years. Deviations caused by maintenance activities, such as the exchange of X-ray tubes in XRF devices, are no longer problematic. The precise intensity of monochromatic light ignites a plasma with a precisely determined amount of energy. Furthermore, the accuracy of the plasma-excitation position is defined down to a few micrometers by the focus of the Laser. Last but not least, the number of single measurements allows a much more comprehensive statistical evaluation, which also increases reproducibility.
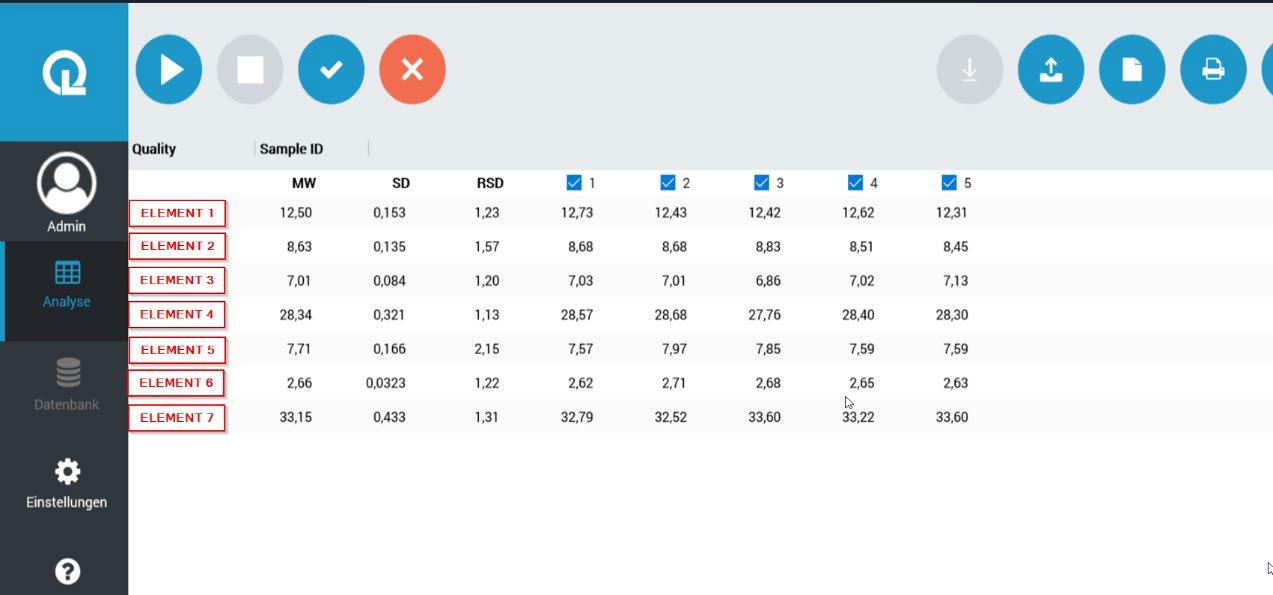
As displayed in Fig. 7, the Laser OES can translate these advantages into similar analytical performances at the beginning of its industrial use as XRF-based approaches after decades of evolution. Stability with direct Laser OES analysis As Figure 8 shows, the analysis of steel slag is significantly faster with sample preparation-free laser OES.
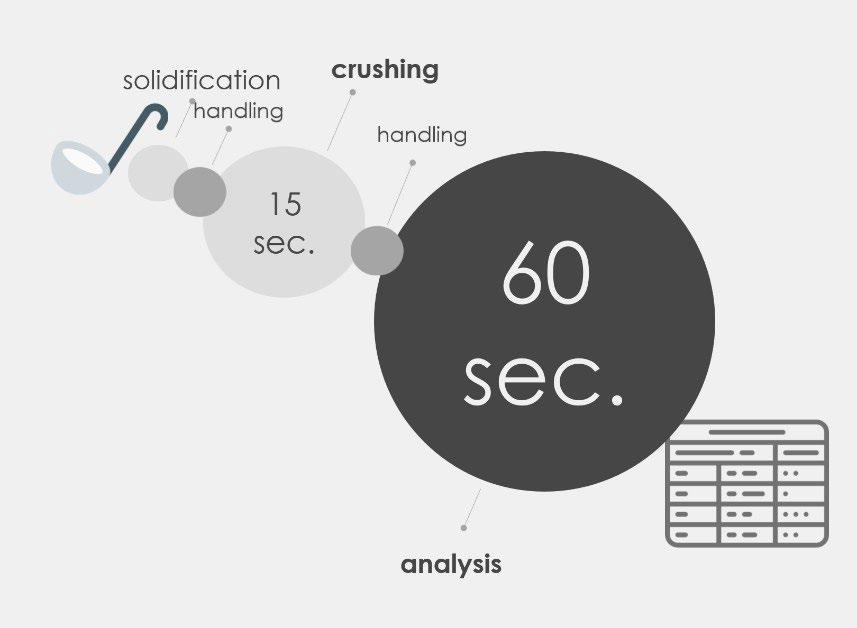
Fig.8 - Laser OES direct slag analysis, sample prep. free and fast.
Results can be used earlier for process control. In addition, the analysis becomes more accessible and less expensive. As a result, pyrometallurgical processes can be monitored much more closely than before at the same or lower cost. Laboratory utilization is no longer an obstacle, with analysis times well below 1 minute.
Fig.9 - Close-meshed, fast analysis for max. stability.
Figure 9 shows that close-meshed monitoring detects deviations earlier. A narrow process window can operate closer to the desired optimum efficiency.
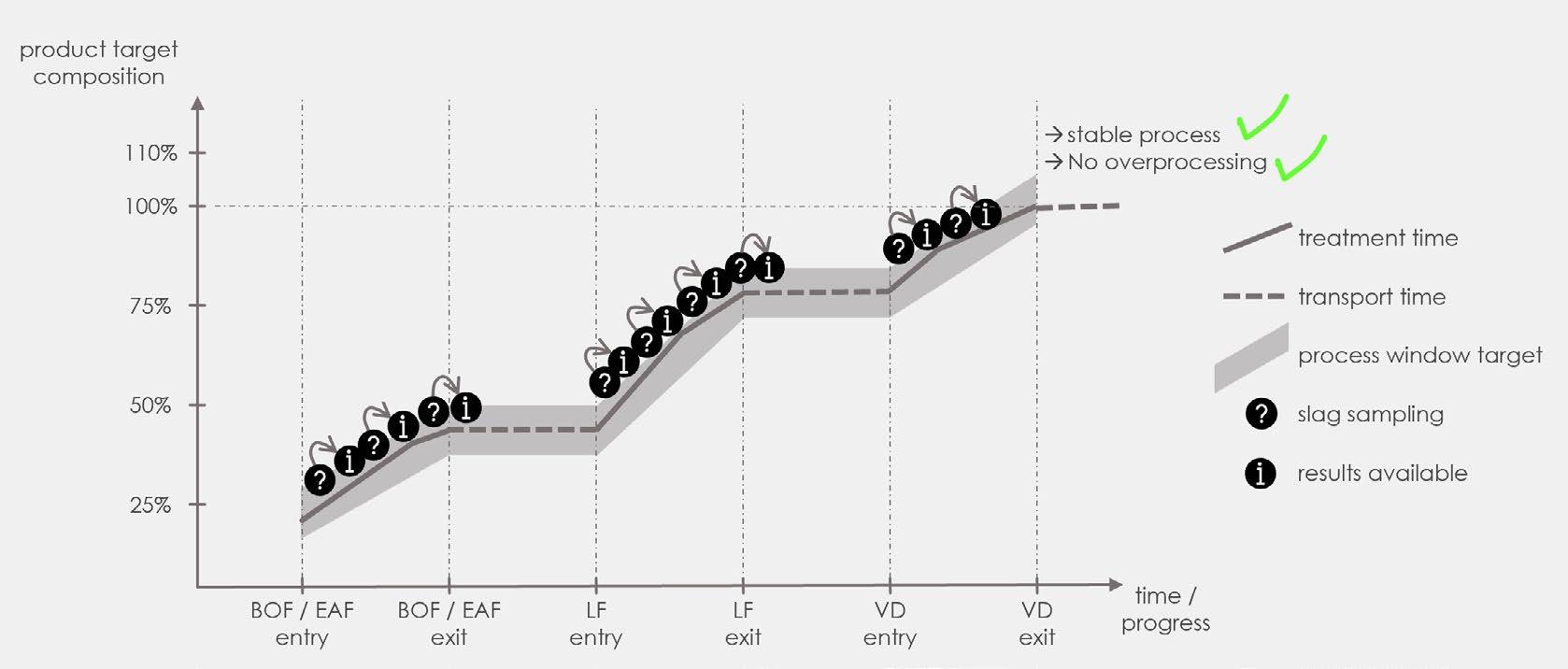
BENEFITS Converter splashing on demand Refractory lifetime is one of the most important KPIs in steel making. A splashing of slag residues on the walls can enhance refractory lifetime in converters, especially in the BOF. Therefore, the slag basicity and the MgO saturation must meet a value that protects the refractory lining. But to apply the slag on the walls, a specific minimum viscosity has to be achieved because it is almost impossible to blow semi-liquid up the walls.
Fig.10 - Converter splashing - tapping → slag analysis → splashing decision.
With the existing 15 minutes slag analysis, there is no chance to check the slag composition before analysis. The new slag splashing on-demand, based on precise analysis values, enables to adapt dynamically to the actual slag composition. Deciding pro- or contra slag splashing is now possible before each tapping. Improved foaming = insulation In the EAF, especially for increasing pyrometallurgical operation due to the rising Phosphorus content in Direct Reduced Iron, sufficient insulation is crucial to reach energy efficiency levels.
Fig.11 - Improved foaming in the EAF.
Knowing the slag composition supports adjusting the additives and the treatment time accordingly.
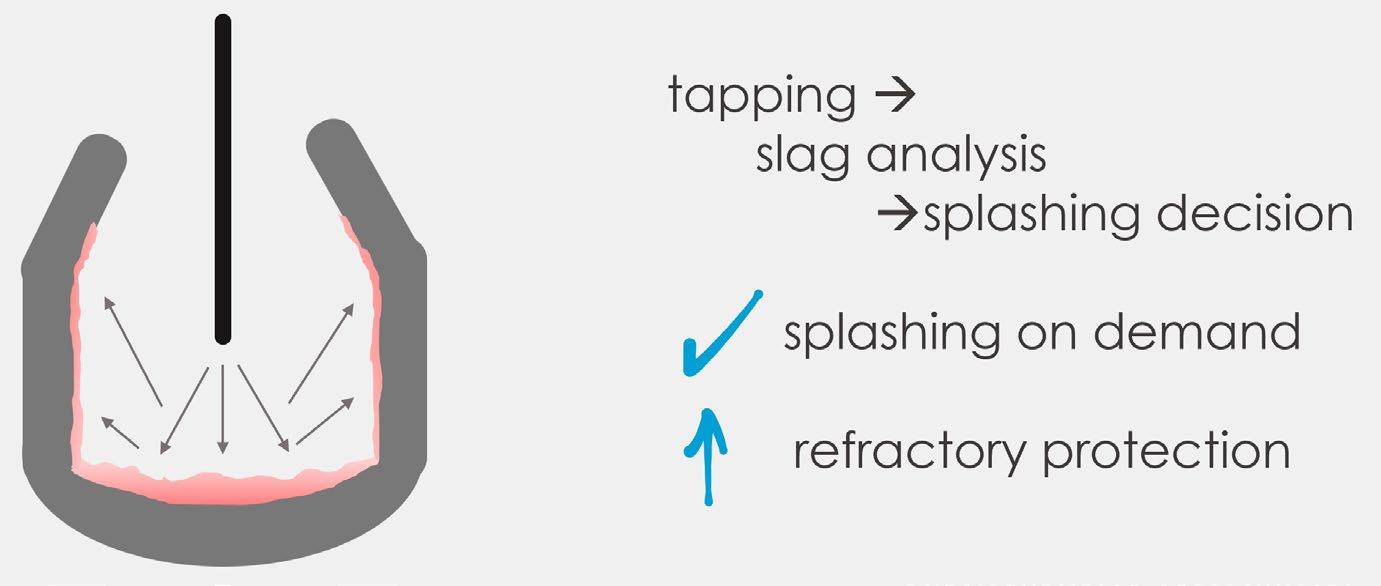
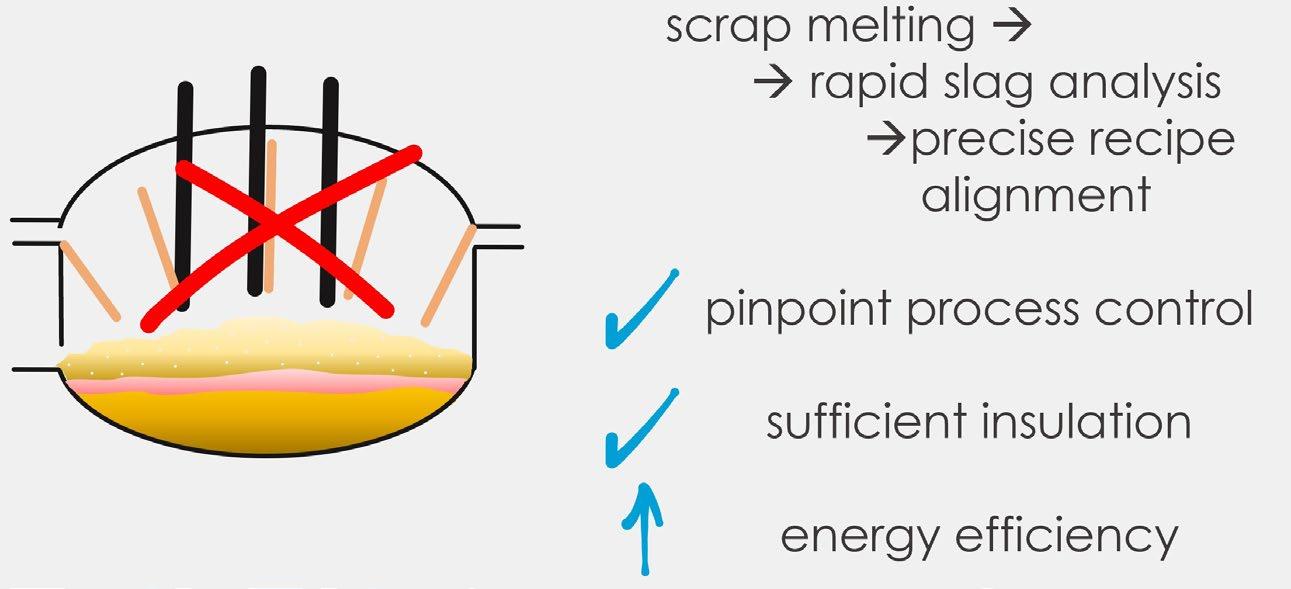
Reduced slag former consumption and alloy oxidization For energy efficiency reasons the process windows are chosen as narrow as possible. On the other hand the rising use of secondary raw materials with its variations challenges melt shop managers. The close meshed and fast analysis enables to keep a stable process inside the process windows. Even if the deviation in incoming material establishes as day-to-day routine, an increase inefficient buffers is avoided.
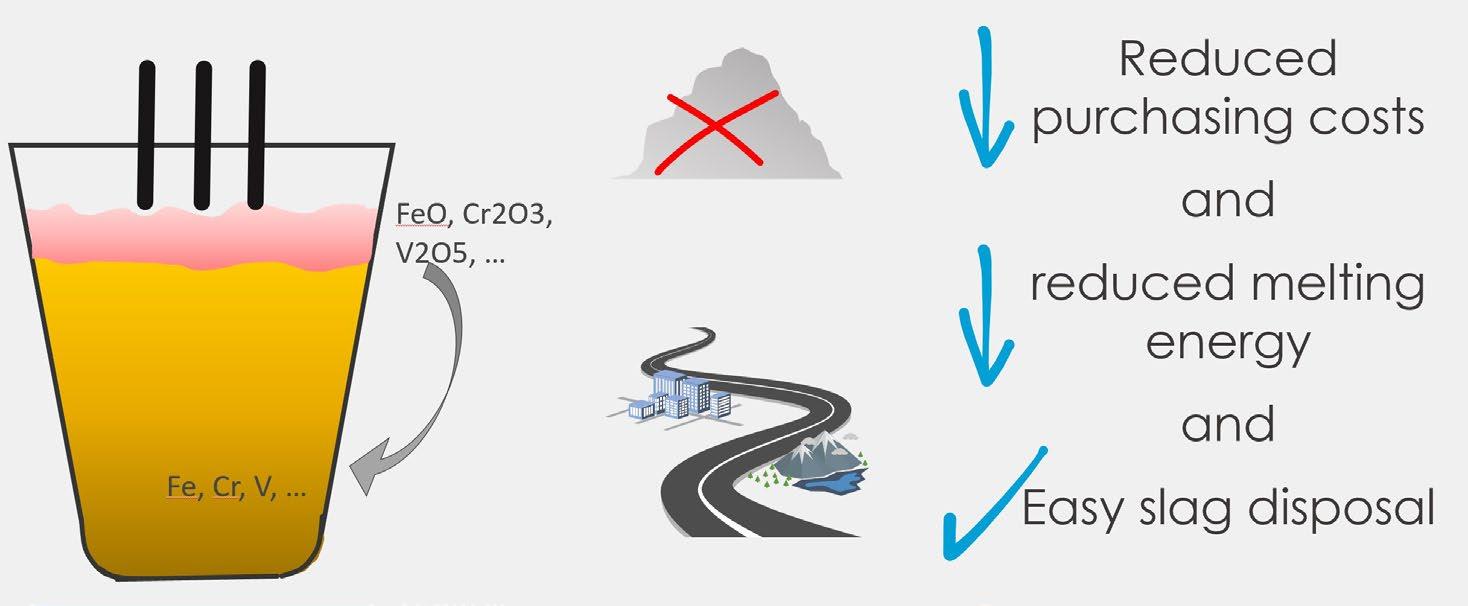
Fig.12 - Reduced oxidization, less slag former consumption, easy slag disposal.
The CaO consumption is kept on a minimum and still the oxidation of alloys into the slag is safely avoided. That saves costs during purchase, it reduces the required melting energy and is makes life easy during disposal, since e.g. a too high Cr content in the slag forces to costly landfill instead of byproduct sale.
Pinpoint slag former calculation For energy efficiency reasons, the process windows are as narrow as possible. The increasing use of secondary raw materials with variations in chemical composition is a complex challenge for melt shop managers. The close-meshed and rapid analysis enables a stable process inside the process windows and extensive and inefficient buffers become needless. The challenge is to reduce CaO consumption to a minimum and, at the same time, to prevent Fe and alloys from oxidizing into the slag o. This optimization saves costs during purchase, reduces the required melting energy, and simplifies disposal in byproduct sale instead of landfill. Precise end-point determination The availability of the slags' chemical analysis right after melting is a novel piece of additional information for the melt shop. Used solely or in combination with other process information, such as steel composition or temperature in a simulation model. As shown in Fig. 9 melt shop engineers can precisely determine the processing endpoint based on that information. Overtreatment is efficiently eliminated, and pyrometallurgical treatment continues exactly as long as necessary. And no longer.
Reduced refractory and ladle wear Stable process control and increased production time with optimum basicity can reduce the reactivity between slag and refractory. This is advantageous for refractory lining and ladle lifetime.
Fig.13 - Precise basicity, reduced refractory & ladle wear, cleaner steel.
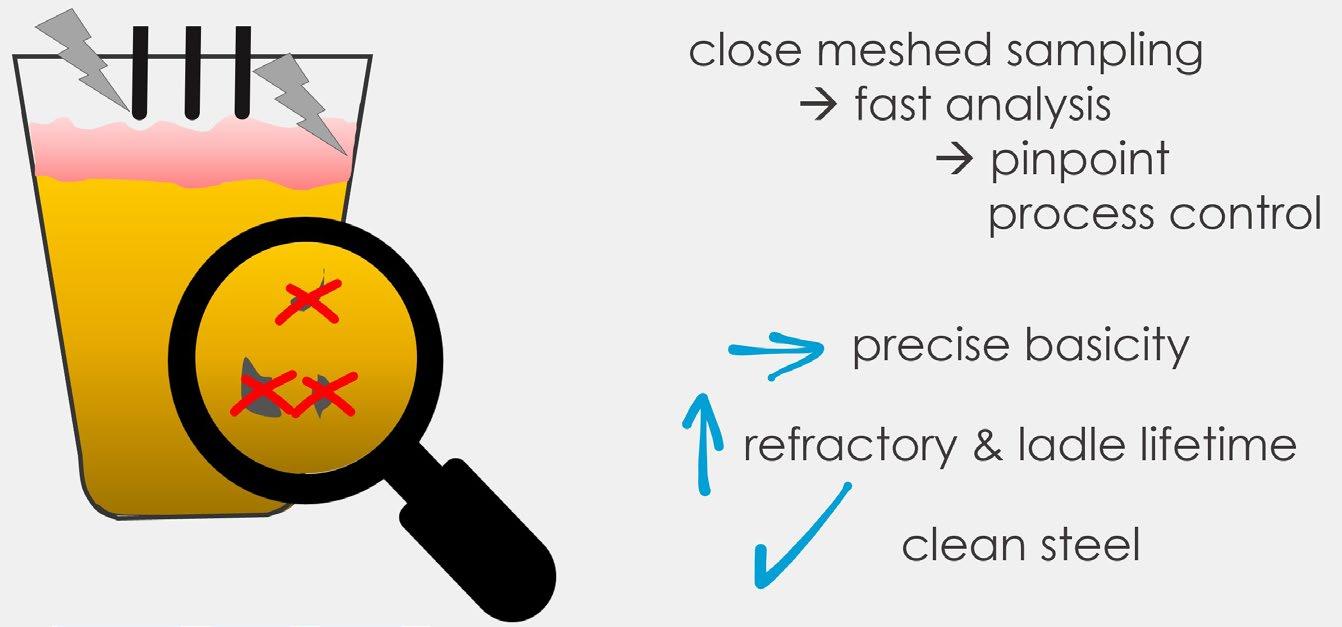
Thus, the extension of the ladle lifetime can also contribute to the increased overall efficiency.
Clean steel The reduced refractory wear, described in the previous section, has an additional benefit on the cleanliness of the steel. Since Fig. 13 shows less refractory material dissolving in the slag/steel melt, less refractory ends up as an inclusion in the product. Furthermore, the increased stability of the melt enables the targeted reduction of other non-metallic inclusions, which also reduces the arising of unwanted inclusions.
Easy disposal Knowing the slag composition, before tapping the melt shop engineer can adjust the slag composition according to the by-product-sale/disposal strategy. The waste becomes an attractive by-product by further reducing Chromium in the steel. With the rapid slag analysis, Melt shop engineers can even make more radical decisions.
Fig.14 - – Precise basicity, reduced refractory & ladle wear, cleaner steel.
Based on the composition, they can decide to post-process the slag after steel tapping. The additional heating energy and processing time tackle the overall efficiency, but in certain circumstances, the advantages of easy slag disposal can compensate for the disadvantages.
CONCLUSION Until now, slags could not be analyzed in-situ. The extensive sample preparation time resulted in the production receiving the slag analysis mostly only post-mortem. As a further development of spark OES, Laser OES now enables direct analysis in well under 1 minute. According to the expression “who knows a lot, can optimize a lot” overall analysis time allows melt store engineers to make in-situ decisions based on actual analysis. The process windows can be smaller, and buffers can be reduced. In addition, previously unthinkable production strategies such as slagsplashing-on-demand or post-process LF slag optimization become a reality. Laser OES thus represents an essential element for the resource-efficient steel industry.
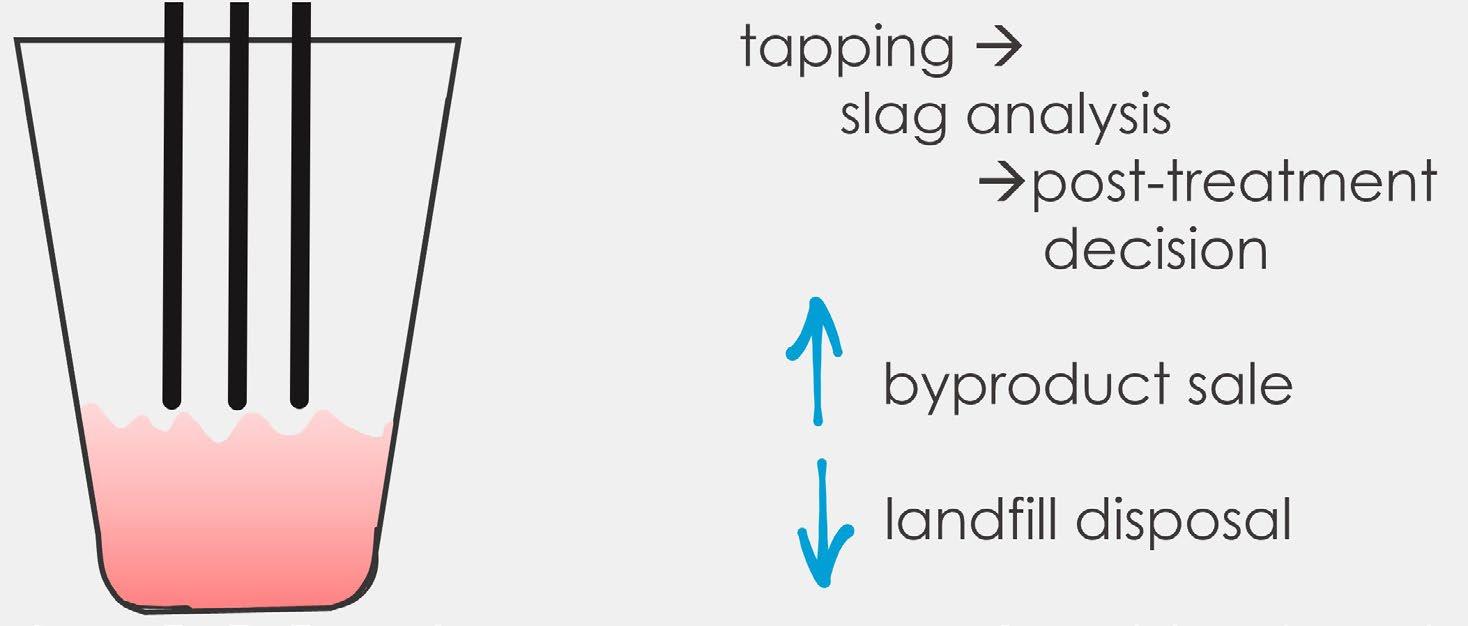
REFERENCES
[1] Buckley S., Eloot K., Görner S., Malladi R., and Mori L. McKinsey & Company 2021, "How AI-powered solutions can help optimize smelters", https://www.mckinsey.com/industries/metals-and-mining/our-insights/how-ai-powered-solutions-can-helpoptimize-smelters [2] Bruzenak L., Campbell I. “The Common Sources of Error in Sample Preparation for XRF Analysis andthe Capabilities of Standalone Automation” https://cdn2.hubspot.net/hubfs/494827/AAACaseStoryPDF/Common_sources_of_error_in_sample_preparation_ for_XRF_Analysis_and_the_Capabilities_of_Standalone_Automation.pdf [3] Cremers, David A., Leon J. Radziemski, 2013, Laser-Induced Breakdown Spectroscopy. Chiches-ter: John Wiley & Sons Ltd. [4] Esbensen K.H., Wagner C., "Why We Need the Theory of Sampling” https://theanalyticalscientist.com/techniques-tools/why-weneed-the-theory-of-sampling [5] Kolmhofer, P.; Eschlböck-Fuchs, S.; Huber, N.; Rössler, R.; Heitz, J.; Pedarnig, J.: Calibration-free analysis of steel slag by laserinduced breakdown spectroscopy with combined UV and VIS spec-tra. Spectrochim. Acta Part B At. Spectrosc. 2015, 106, 67–74. [6] Kolmhofer, B.; Pedarnig, J.; Praher, R.; Huber, N.; Rössler, J.H.: Element analysis of complex ma-terials by calibration-free laserinduced breakdown spectroscopy. Appl. Phys. A 2013, 112, 105–111. [7] Kraushaar M.; Noll, R.; Schmitz, H.: Multi-elemental analysis of slag from steel production using laser induced breakdown spectroscopy, Int. Meet. Chem. Eng. …, p. 2000, 2000. [8] Kraushaar M.; Noll, R.; Schmitz, H.: Slag analysis with laser-induced breakdown spectrometry, Appl. Spectrosc., vol. 57, no. 10, pp. 1282–1287, Oct. 2003. [9] Miziolek M.; Palleschi, V.; Schechter, I.: Laser Induced Breakdown Spectroscopy: Fundamentals and Applications. 2006. [10] Noll R., 2012 "Laser-Induced Breakdown Spectroscopy - Fundamentals and Applications" pp. 429-235, Springer Verlag: Düsseldorf [11] Steininger V., "Neues Analysesystem für Schmelzrückstand" https://www.voestalpine.com/blog/de/innovation/neuesanalysesystem-fuer-schmelzrueckstand/ [12] Sturm, V.; Noll, R.: Determining the Lime Standard for Liquid Slag with LIBS; https://www.ilt.fraunhofer.de/content/dam/ilt/en/ documents/annual_reports/ar13/AR13_P126.pdf [13] Sturm, V.; Schmitz, H.; Reuter, T.; Fleige, R.; Noll, R. Fast vacuum slag analysis in a steel works by laser-induced breakdown spectroscopy. Spectrochim. Acta Part B At. Spectrosc. 2008, 63, 1167–1170. [14] Thurston A., 2019, “The Role of X-Ray Fluorescence for In-Process Steel Slag Monitoring” https://www.azom.com/article. aspx?ArticleID=18627 [15] Zhang, T.; Wu, S.; Dong, J.; Wang, K.; Tang, H.; Yang, X.; Li, H. Quantitative and classification analysis of slag samples by laser induced breakdown spectroscopy and partial least square (PLS) methods. J. Anal. At. Spectrom. 2015, 30, 368–374.
TORNA ALL'INDICE >
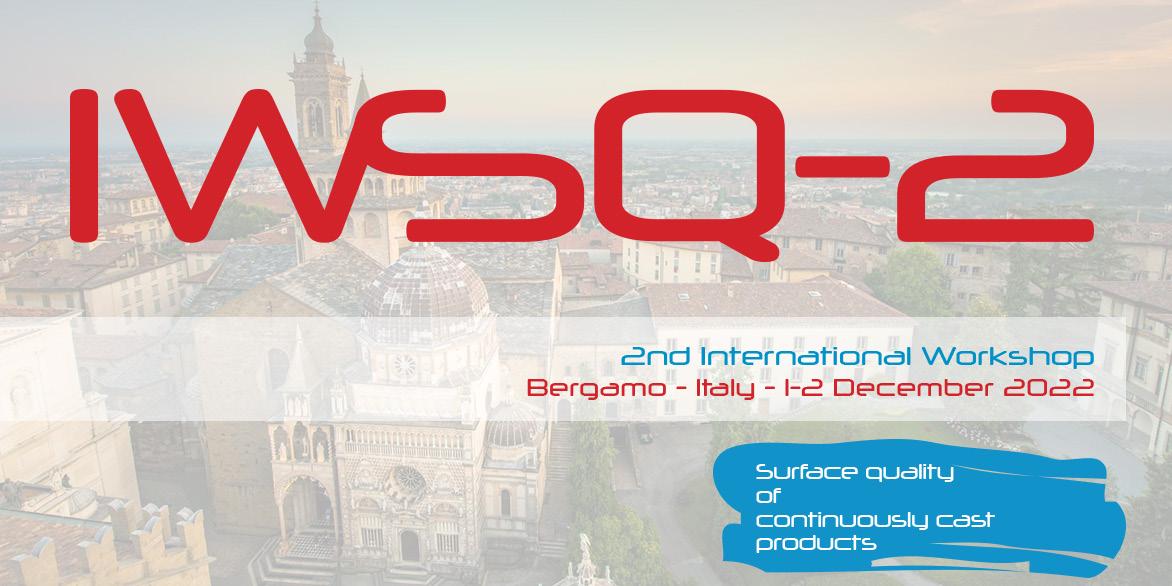
Organised by
Six years after the successful first conference on the topic, AIM, in cooperation with its sister society ASMET, organises once again a twoday event focused on the Surface Quality of continuously cast products. The surface quality of ingots, billets, blooms and slabs is a particularly important issue in order to insure the required surface quality of final rolled and forged products. This aspect is becoming increasingly significant especially nowadays, when a lot of steelmakers are refocusing their activity on the search for better surface quality or new specialty steels requiring high quality surface features. All this lays on a table of new challenges faced by steelmaking industries, when energy efficiency and consequently lower environmental impact are concerned. This international meeting aims at sharing the knowledge about the improvement of the surface quality of the continuously cast products and this scope will be achieved by clear expositions about: • recent advances on the defect analysis; • the root cause of the defects; • innovative lubricating products; • operations and maintenance; • application of electromagnetic devices; • AI applications, simulation and computing methods.
New call for paper deadline: 26th September, 2022 Prospective authors wishing to present are invited to submit a tentative title and an abstract of maximum 400 words (in English) to the Organising Secretariat (met@aimnet.it). The abstract should provide sufficient information for a fair assessment. Two ways to submit papers will be available: • to fill in the form online >> www.aimnet.it/iwsq-2.htm • to send the title and the abstract, together with the requested information (Name and Surname, Affiliation, Mailing Address, Phone, Fax and e-mail) by e-mail to: met@aimnet.it
The Conference will be held in Bergamo at the Congress Center Giovanni XXIII, viale Papa Giovanni XXIII, 106 (http://www.congresscenter.bg.it). Bergamo greets visitors with its Venetian Walls. Surrounded by rivers and lush, verdant valleys, crossed by paths that widen to Parco dei Colli, the area’s largest park, the city looks like a lounge filed with art, culture and nature, with a fascinating and complex history just waiting to be shared with others. The “upper and lower” city reveals a mixture of pleasant surprises and unexpected encounters, such as those with Gaetano Donizetti, the great composer of international renown, Bartolomeo Colleoni, the Bergamo leader who served under the Republic of Venice and Lorenzo Lotto, among the most famous Italian Renaissance artists who lived and worked in Bergamo for over a decade.