INSIDE
Murphy finds positions with sugarbeet groups a ‘natural fit’
pg. 10
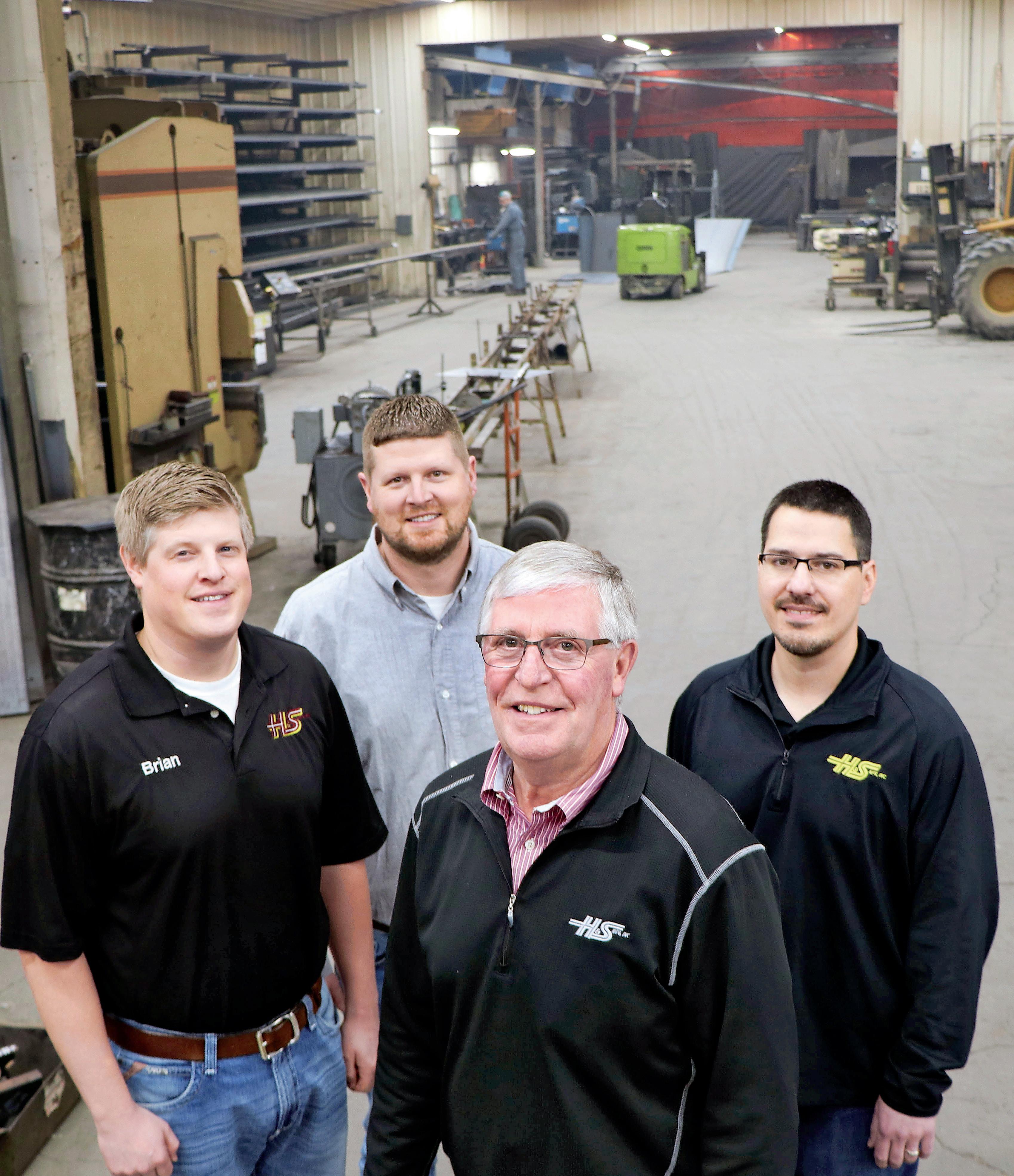
INSIDE
Murphy finds positions with sugarbeet groups a ‘natural fit’
pg. 10
Whether its adapting to sugar beet size, innovating for efficiencywithout sacrificing quality, or adding to your bot tom line, Amity Technology knows that The Power toGrow is a driving force on your farm. Our philosophyof continuous improvement means products engineered to allow you to defoliatecleaner and faster, harvest more root and less dirt, and keep your trucks and equipment moving.
Serving The Nation’s Sugarbeet Community Since 1963
Volume 60 Number 4 | May 2021
Sugar Publications | Agweek 101 5th Street N | Fargo, ND 58102
PUBLISHER
KATIE PINKE 701-261-9494
KPINKE@AGWEEK.COM
CONTENT MANAGER
JENNY SCHLECHT 701-595-0425 JSCHLECHT@AGWEEK.COM
EDITOR
MIKE SPIEKER 701-238-0718
MSPIEKER@AGWEEK.COM
LAYOUT DESIGN SARA SLABY FCCSPECIALSECTIONS @FORUMCOMM.COM
ADVERTISING ADS@AGWEEK.COM
SUBSCRIBER INFORMATION MEMBERSERVICES @SUGARBEETGROWER.COM 1-800-274-5445
The Sugarbeet Grower is published six times annually (January, February, March, April/May, July/August, November/ December) by Sugar Publications, a division of Forum Communications Printing.
North American sugarbeet producers receive the magazine on a complimentary basis. Annual subscription rates are $12.00 domestic and $30.00 for foreign subscribers.
Advertising in The Sugarbeet Grower does not necessarily imply endorsement of a particular product or service by the publisher.
VISIT US ONLINE! Agweek.com/Sugarbeet
TOP TO BOTTOM: H&S Manufacturing keeps 100 to 200 types, shapes and sizes of raw materials to make machines — some stainless, aluminum, mainly mild steel, but also sheet metal.
Terry Norberg welds on a bar that a farmer will attach fertilizer units to in the main manufacturing space at H&S Manufacturing, Stephen, Minn.
Terry Norberg welds on a bar that a farmer will attach fertilizer units to in the main manufacturing space at H&S Manufacturing, Stephen, Minn. The company employs about 10 people. Photos Mikkel Pates / Agweek
STEPHEN, Minn. — If not for a sign along the highway, a motorist in Marshall County could easily mistake the H&S Headquarters for just another farm.
Close-up, it’s a collection buildings — office and main shop, smaller paint shop, a couple of storage buildings and an assembly shop. The company and farm headquarters in the late 1800s was part of a bonanza-style farm.
H&S Manufacturing is a vibrant, agricultural related manufacturing company that sprang from an innovative potato and sugarbeet farm in northwest Minnesota.
Craig P. Halfmann, 66, is chief executive officer of a farm and an ag equipment manufacturing business that has thrived by providing customized options in niche markets for sugarbeets, potatoes and other crops.
Sons Brent, 36, and Brian, 33, take the lead on the 5,000-acre Halfmann Farms Inc., where they raise sugarbeets, wheat, dry edible beans, soybeans and sometimes corn. Both hold business degrees from the University of North Dakota in Grand Forks.
Son-in-law Darin Adolphson, 38, trained as an engineer at the University of Minnesota and since 2017 has helped lead H&S Manufacturing Inc., a company celebrating 50 years. The company makes tillage, spraying
equipment and sugarbeet harvest carts, and recently has branched into recycling equipment and other urban purposes.
In 1911, Craig’s maternal family came to this area.
Paul Halfmann, Craig’s father, raised potatoes and added sugarbeets in 1965, growing for American Crystal Sugar Co. Denver-based Crystal built its Drayton, N.D., factory in 1963, about 26 miles to the west.
In the mid-1960s, Paul and John Szklarski, his right-hand man on the farm, built an electric skidsteer loader, allowing them to move potatoes inside storage buildings without gasoline power. The two started making them for others and in 1971 together formed H&S Manufacturing Inc. — 50 years ago this year.
In 1972, Craig graduated from high school. That very summer, he bought shares in American Crystal Sugar Co., as it became a farmerowned cooperative. In 1975, the Halfmanns established Halfmann Farms Inc. as a corporation.
In 1979, they dropped potatoes and concentrated on beets and manufacturing. In 1980, Craig married Marlys Steer, who grew up on a farm in the Angus/Warren area. Their three children were born from 1981 to 1987.
In those days, Paul took more responsibility for the manufacturing while Craig focused more on the farming and helped in the shop in the winter. As potato producers outgrew their skid-steer, H&S shifted to sugarbeet equipment — row crop cultivators and band sprayers, which targeted spray strips over the rows, saving costs from broadcast spraying. H&S also marketed a row crop cultivator.
Everything changed on Dec. 23, 1984, when Paul died unexpectedly from a heart attack. He was 66.
Craig, at age 30, suddenly had to step up to keep both business going without his dad. The farm had two employees. H&S had five in the manufacturing side, plus several part-timers, especially in late winter and early spring. Marlys worked on the books.
Thanks to “good people on the farm,” Craig spent most of his time on the
CONTINUED ON PAGE 7
Craig Halfmann’s maternal grandparents started farming near Stephen, Minn., in 1911 on a farmstead that had holdover buildings from the Culbertson-Wheeler bonanza farm that dated to the late 1800s.
H&S Manufacturing Inc. co-founder Paul Halfmann stands by the power scoop that he and John Szklarski built in their farm shop in the mid1960s. This unit used a 12 horsepower gas engine drive for outdoor use or a 7½ horsepower electric motor for indoor use. The power source drove a hydraulic pump, coupled with two orbit motors and four cylinders. The operator controlled it with levers and foot-operated valves.
John Szklarski, together with Paul Halfmann, in the 1960s built an electric skid-steer loader for moving their bulk potatoes inside storage buildings without gasoline power. The two in 1971 formed H&S Manufacturing Inc., a company that turns 50 this year.
Photos courtesy of H&S Manufacturing and Halfmann Farms Inc.
As aproducer youknowyour crop is only as good as your soil. When things go awry,whether with nutrient profile or soil structureitisoften due to high saltdensities and as aresultyields suffer.Areaproducersare findinganew product, Calcine®,tobeparticularly helpful in getting productivityinthese fields back in thegreen. “Weare about onetoone andahalf leaves further aheadand our standcountsare probably four or fivebeets more per 100 feet of row, whichistremendous,”saidGaryWagner, a local farmer.“We also sawplants aregrowingfaster and healthier.Those things aregivingusencouragement.”
Just ayearearlier Wagnerwas facing high saltlevelsin severalofhis fields, whichwas inhibitinggrowthofhis crops. Conversations with his distributor,Jim Erickson, led him to aunique solution. “Calcine® is amix of proteins, enzymes andnatural acids that releases calcium from thesoil matrix so it can help leach saltf romthe soil, whichcan significantly improvesoil health and production,”Larry Mohr,developer of Calcine® said. “It’sbeen successfully used formorethan 20 years in thegolf industry. We’re excited to see it helpingproducers in theMidwest.”
Increasingsugar contentinsugar beets has alwaysbeen achallenge forsugar beet growers.Overthe past twoyears we have seen the challenge becomeeasier to overcome Theuse of Aqua-Yield® NanoK®onsugar beets duringother spray applications has shownto increase sugar by as muchas.75 points in twoyears of trial work in ElbowLake, MN. Theproducer has seen this increase by addingNanoK® to thespray tank with thelast herbicide application and at least oneortwo applications duringCercosporaspraying. Thehighly available Nano particles of potassium get intothe plant leaves very quickly followingapplication because of thesmall size of theparticle. Thepayback forthe producer has been a$17 investment andareturnper acre of over$100 forthe additional sugar harvest Potassium has longshown to have apositiveinfluence on sugar in most crops andnow in sugar beets. Call us forrecommendations on howwecan maximizesugar andyour bottomlinebyusingNanoK®
Contact:Gregg Johnson 218-779-9079 or PatMuller 701-430-0771
Total Ag Industries •701-636-4524•totalag.com
CONTINUED FROM PAGE 5
manufacturing end and helped out in the peak seasons in the spring and fall.
Craig credits his father for leaving a company that had no debt. Craig’s philosophy was to grow it slowly and build working capital. One key advantage was an ability to test new products on the farm.
“We found niche markets where other people didn’t really want to be a part of,” Craig recalled. In the 1990s, onion producers in western Idaho needed sixand eight-row cultivators. Michigan sugar growers were keen on H&S cultivators.
As the years flew by, Craig appreciated that the two enterprises were somewhat counter-cyclical. “The years farming wasn’t so profitable, the manufacturing would pick up. There was balance between the two.”
In the 1980s, H&S benefitted when farmers shifted to bigger band-sprayers.
They made a scrub-chain elevator that was a winner for retrofitting older Hesston harvesting machines that were common at the time.
The company’s products stood out in the wet 1985 crop season. “That scrub chain elevator really took off,” Craig said. “We had a machine that could clean.”
In the early 1990s, H&S started making sugarbeet carts and pull-type sprayers. In the mid-1990s, H&S started getting lasercut parts from other suppliers, rather than cutting their own with plasma cutters.
Row crop cultivators are getting more popular again, this time to organic farmers in Michigan and elsewhere.
“They’re not 12-row anymore, so they’re building bigger bars,” Craig said.
H&S well known for a range of sugarbeet carts. They’ve increased to 30- and 35-, and recently 44-ton model carts that come standard with tracks.
A typical 30-ton cart starts in the mid$80,000 range, but can range to the $130,000 range, with all the bells and whistles. The options include sizes of wheels, as well as “transfer tracks,” that can be attached to 10-bolt hubs. They also offer an option for a Camso track, a track from a different manufacturer.
Since 2015, H&S has offered “ridging and de-ridging” tillage equipment. Sugarbeet farmers in Fisher, Minn., have adopted the technique which involves making ridges in the fall, fertilizing, knocking down the ridges and planting on top. The soil warms more quickly in ridges and retains the moisture because there’s less tillage.
The Halfmanns estimate perhaps 20% of the beets in the region now are planted with the technique.
CONTINUED ON PAGE 9
KB Manufacturing, LLC has designed a new aid for loading trucks, carts or other vessels with a primary purpose to more evenly place product for improved stability.
Light
Every unit is measured with sonar prior to loading, establishing a customized center point
green light indicated optimal load zone. A red light indicates the load zone is too far out
is designed to help reduce operator fatigue and allow more attention on proper harvestor settings
FEATURES:
• Transmitter runs off of a 9-volt battery
Receiver powered by plugging into a cigarette lighter
Easily transfer from one piece of equipment to another
Units are small and install in minutes
Visual light shows direction of movement desired
• Audible alarm to alert driver of a change
Mounts on dash for easy viewing
Automatically shuts off sprayer or planter pump at end of row. Ease your mind with the flip of a switch!
PRODUCT USES:
• Loading trucks, grain carts,beet carts for harvest Loading and unloading of railcars and trucks at elevators and warehouses
• Communicate between two or more vehicles when visibility is obstructed
Have you ever forgotten to flip a switch to start application of a product?
Have you ever accidentally left a switch on?
Reduce your chance of leaving a switch on and burning you crops.
This motion activated switch starts the application when your machine starts moving. Application stops when you stop.
CONTINUED FROM PAGE 7
Craig estimates the business is 10 times what it was in the 1980s.
“Any business has to increase over time, or you’re going to go backward: you’re going to go broke,” he said, flatly. “You have to increase sales, revenue. The overhead keeps climbing, creeping.”
H&S sold through dealerships in sugarbeet areas — Michigan, Montana, Nebraska, Idaho. The Red River Valley always has been the heart of their marketing. Each area involved its own challenges — Michigan and Montana each had their own row spacing preferences.
“We all wear a lot of hats around here,” Brent said. “When Brian and I first started, we were in assembly, helping out as young kids. It’s been fun to transition and to continue to be involved.” Brent and Brian seem to enjoy each other’s company. Brent said there are inevitable disagreements in business, but they agree not to go home angry.
Adolphson adds another dimension. He’d grown up at Argyle and met the Halfmanns’ daughter, Katie, when they were in high school. The couple married in 2005 and have four children. Darin holds a civil engineering degree from the University of Minnesota and worked in building and steel construction until 2017, when he joined H&S.
Adolphson’s main roles at H&S are operations and sales.
H&S has a busy main production shop for fabricating large equipment. They have smaller stations for smaller equipment. There is a wash bay, preparing equipment for a painting, and finally an assembly shop — originally a potato warehouse that was built in 1961.
“We try to find trends for planning ahead, for purchasing,” Adolphson said. “Typically, we’re a smaller company, building products to order.”
In the mid 1990s, Craig became active in sugarbeet growers associations.
He became president of the Red River Valley Sugarbeet Growers Association, representing American Crystal Sugar Co. grower/shareholders. He went on the board membership in the American Sugarbeet Growers Association, and became vice president of the World Sugarbeet Growers Association, before sticking closer to home, in part to watch the boys play football.
Craig said he and Marlys feel very fortunate, with their kids and seven grandchildren around them.
“I have two sons and a son-in-law that are involved (in the business) and want to be involved,” he said. “They’ve gone to school, have the education, the foundation. Marlys and I are very lucky, we talk about it all of the time.”
Designed by alifelongbeetwheel re-manufacturing company
Accordingthe designrequirementsbelow:
Heat-treated8630steel for strength, wearlife andresistanceto rock damage
Stouterspokes forincreased rigidity
Cast-in puller-optimizers in theteeth to keep thewheelsturning in tough conditions
Machinedhub face and bolt-holes for perfect fit andless runoutthe PAIR runningonthe machine will rimasa “true-pair” andnot fighteachother
Fully weldabletoaccommodatespoke fillers andothercustomers add-ons
Less expensive than theOEM wheels
Bolt On Filler Tabs
Directreplacementfor 28”6—boltBeetLifterWheels: Amity Part #300734
AllowayPart #700-3-0303
Red River/ WIC/ WilrichPart #700576
Artsway
Anna Murphy, 33, of Berthoud, Colo., saw her first crop of sugarbeets in 2011 and was surprised at how much they weighed.
“I assisted with harvesting some research plots for Syngenta. I’ve always loved being outdoors, so I brought my lunch and water, strapped on my boots, and helped ensure the beets went into the correct bags,” she said. “I remember being in awe of the whole process at harvest and amazed at how heavy the beets were. They were as heavy as bowling balls!”
Now, 10 years later, Murphy is the new executive vice president of the Beet Sugar Development Foundation (BSDF) and the American Society of Sugarbeet Technologists (ASSBT). She works out of the organization’s Denver, Colo., office and started the position in January of this year.
“Since graduate school, I have been fortunate to spend the past 10 years working in the sugarbeet industry,” she said.
Murphy grew up in Centennial, Colo., a city in the suburbs of Denver.
“My grandfather was a farmer in South Dakota. However, I didn’t set foot onto a farm until my first day of graduate school,” she said.
After graduating from high school, Murphy attended Calvin College in Grand Rapids, Mich., where she received a Bachelor of Science degree in biology. She then went on to pursue a Master of Science degree in plant breeding and genetics, with a focus on wheat.
“After graduate school, I began working as a sugarbeet breeder for Syngenta,” Murphy said. “My breeding efforts focused on improving sugar yield and disease tolerance to Aphanomyces and Fusarium.”
Murphy also had roles in product management for Hilleshög Seed and as an assistant supply manager for Magno Seed before coming to the BSDF/ASSBT.
“I was attracted to my current position because the mission of the BSDF focuses not only on promoting sugarbeet research, but also education, which I’ve always been passionate about,” Murphy said. “I have gotten to know and have developed relationships with many USDA-ARS and university researchers through various meetings, and have made connections with many colleagues in the sugarbeet industry. This just felt like a natural fit.”
Murphy said that as executive vice president of both the BSDF and ASSBT, her goals are to support both groups as much as possible.
“The BDSF works to advance sugarbeet production and beet sugar processing through science-based research and leading educational programs,” she said. “The ASSBT promotes the dissemination of sugarbeet and beet sugar research and knowledge to its members. I want to ensure that we are doing our best to support and further these missions.”
Murphy said she is greatly enjoying her new role which includes interacting with new and old colleagues and taking on new challenges.
“There is a lot of excitement within the sugarbeet research community and I am really happy to be part of that,” she said. “One of the biggest challenges I have in this position is to ensure that the USDA-ARS sugarbeet scientists are connected to this community, aligned to the current and future needs of the industry and not duplicating efforts. Also, after 40 successful face-to-face biennial meetings, we successfully hosted our first-ever virtual ASSBT meeting earlier this month. It is an ongoing challenge to navigate and find the balance between face-to-face and virtual meetings.”
As BSDF executive vice president, Murphy is also responsible for overseeing the McGinnis Institute of Beet Sugar Technology Schools, which provides valuable training sessions for the next generation of sugarbeet technologists.
Murphy is proud to be part of the American sugarbeet industry and excited to raise awareness of the BSDF’s work.
“I want everyone to know that the BSDF is dedicated to promoting sugarbeet research and education in both sugarbeet production and beet sugar processing,” she said. “There are highly dedicated personnel across the sugarbeet community that are working toward this goal. What makes this industry unique is that we are a tight-knit community that is able to organize and work toward the future sustainability of the crop.”
Murphy and her husband are the parents of three children under the age of five. When she’s not working, she enjoys hiking, biking and spending time outdoors with them. The family also enjoys trying new restaurants.
Laura is a shareholder in American Crystal Sugar Company and a member of the Red River Valley Sugarbeet Growers Association, the World Association of Beet and Cane Growers, and the American Society of Sugarbeet Technologists. She is also on the Board of Directors of the Sugar Industry Biotechnology Council.
Laura can be reached at GoSugar.LR@ gmail.com.
Recent trialresults demonstratethatREGEV™ hybrid fungicide boostssucroseyields when protecting sugar beets from CercosporaLeafSpot.
REGEVisthe firsthybridfungicide to unitethe disease fighting powerofbotanical and conventional chemistries. This innovativecombinationofTea Tree Oil and difenoconazole provides sugar beetgrowers multiple modes of action forcontrollingCercosporaLeafSpotand Powder y Mildewwhileenhancing growth andyield.
Learn moreat summitagro-usa.com
We’ll covercropreports, inter views with extension specialists,growers and head agronomists.Get exclusivefeaturestories and coverage youwon’t find anyplaceelse on disease, weeds, weatherand more.
Plus, expert analysis of markets &policy.
David Kragnes farms near Felton, Minnesota
David Kragnes is a former board member and chairman of American Crystal Sugar Company, he currently serves on the CoBank Board of Directors.
I’m either lucky or stupid, That, is a hard place to be. I never give myself credit, If good things should happen to me.
Yet I am always to blame for Everything that has gone bad. I’m often at myself angry, And it’s hard not to be sad.
I’m lucky that I got that planted. That was a dumb time to sell! It’s good luck if it all works out, But my fault if things go to hell.
Why do we farmers all do that? To ourselves and our neighbors too? We never give ourselves credit, For all of the good things we do.
“He’s lucky he got that planted”
Really? Was it all luck? Who had that planter all ready? Who got the seed in the truck?
Who was out working till midnight, To finish in time for the rain? Who keeps on going in harvest. When tiredness borders on pain?
“That was a dumb time to sell it” Oh how easy to lament. We can feel bad every moment For all of the time we have spent,
Studying charts drawn by experts, And reading about China’s needs, Our thoughts can get so entangled, Our brain goes off into the weeds.
Have you once ever been happy? With a grain sale, my wife will ask, Can’t you just put it behind you? Focus on some other task?
She’s right, because on average, I’ve done some things that were good. And there are others, successful, Living in my neighborhood.
So as springtime comes upon us, And new leaves bring joy to our heart.
Let’s all try making a promise Give self respect a new start.
Give credit for good things that happen, Don’t charge all the good things to luck.
And don’t think of your self as stupid, If by some chance you get stuck.
Plant safe. David
Eradicating bacterial and fungal pathogens on contact
Immediately stops pathogen growth
Stops disease spread
Allows conventional products to shine
Bolstering resistancemanagement
Non-selectivecontact activity
Destroystolerantand resistantorganisms
Clean chemistry =clean crops
No harmful residues
The first hundred days of the Biden Administration have been a whirlwind of activity. On the personnel front, the cabinet is in place. Second- and third-tier appointees are being confirmed for some departments and agencies, while others are still in the works. Key agriculture and environment appointees are steadily advancing. Many appointees not requiring Senate confirmation have been installed in recent months. U.S. Trade Representative Katherine Tai was the only cabinet officer to receive a unanimous vote (98-0) in the Senate. This is a clear signal to our trading partners that she has the full bipartisan support for tackling tough trade problems, particularly with China. She now needs a tough and experienced agriculture trade negotiator.
On the policy front, without question, President Joe Biden’s largest accomplishment to date is the massive and very partisan COVID-relief bill. Given the size alone, $1.9 trillion, administering this relief will take time. While certain aspects of the measure are straightforward, such as assistance checks, which hit bank accounts rapidly, other provisions will take longer. Agriculture received several rounds of commodity assistance in previous packages, and with commodity prices recovering, the need for additional assistance was less pressing during this round. But rural communities’ needs don’t start and stop with agriculture. Additional funding will be provided for rural healthcare facilities, state and local government, and improved broadband. Such assistance takes longer than simply depositing checks, but it’s a positive development for our communities.
As we pivot away from COVID response and relief, recovery is very much on the minds of lawmakers in Washington. Congress and the administration are moving rapidly on a host of policy priorities, the current frontrunner is an infrastructure bill. During the last
congress, the House Transportation and Infrastructure Committee drafted, markedup, and passed a major infrastructure package. The Senate never took up the measure. Given how far the bill went last congress, we expect this effort to form the baseline of this year’s work. Debate and passage was previously a mostly partisan affair, but given the need for economic stimulus and the sad state of our nation’s infrastructure, we are optimistic that common ground can be had for an issue that enjoys widespread public support. The big debate will be around its price tag. With $6 trillion spent on COVID relief (mostly borrowed) and lower tax revenues, there will be a pitched battle over the increased taxes to pay for an infrastructure bill.
A surge in illegal immigration and failure to improve guest worker programs has plagued many administrations from both parties. It is the Congress’s job to address it. While the House passed a bill, it has tough sledding in the Senate, but there needs to be clarity and certainty so agriculture businesses, in particular, can plan and make decisions.
It is also the time of year again when the annual appropriations process kicks off. ASGA and U.S. Beet are continuing our efforts to increase beet research funding. Past success around funding increases are gradually building research capacity at public institutions. This is very welcomed news. Our efforts, and the advancements of our researchers, will continue to improve the beet industry and return dividends to growers. While the appropriations process presents opportunities for our industry, it is also the time of year our opponents attack our programs with harmful amendments. As always, we are prepared to beat back these ill-conceived efforts.
It is still uncertain as to when the Capitol and congressional office buildings will
reopen to the public. COVID variant strains along with lingering security concerns will keep members on edge, so we continue to utilize video conferences. But the good news is the vaccines are moving forward at a steady pace and a cascading recovery is well underway. For a city that thrives on tourism and interaction between policymakers and citizens, Washington has been devastated. A strong recovery is desperately needed.
Finally, the buzz around Washington this spring will be more than political intrigue. Having been cooped up for over a year it is time to get outside and enjoy fresh air and open spaces. However, after a 17-year hiatus, the cicadas (the size of your thumb) will emerge in numbers of biblical plague proportions, an estimated 1.5 million per acre! The sound of their wings is deafening and will test our patience once again.
LUTHER MARKWART Executive Vice President American Sugarbeet Growers Association Luther Markwart has been the executive vice president of the American Sugarbeet Growers Association since 1982. Luther can be reached at lmarkwart@ americansugarbeet.org.This edition of the Sustainability Spotlight features Nebraska sugarbeet grower, Mario Pitts, who is a grower-owner of the Western Sugar Cooperative. Pitts and his wife, Kristy, farm in Lyman, Neb. He has been on the board of the American Sugarbeet Growers Association since 2014.
Pitts was asked to describe what sustainability means to him. He said, “Sustainability in my words is taking the steps necessary to ensure that future generations can enjoy this great planet as much as our generation and past generations have. For many generations, farmers and ranchers have been great stewards of the land and we must continue that for the future generations of our families. Sustainability is kind of a three-legged stool. It takes all three in my opinion to work. The three ‘legs’ being air, water and soil. To be a good steward, all three legs have to be accounted for, taken care of, and used correctly to ensure that we leave this earth in better shape than what it was when it was handed to us. Through the years technology has been the key to helping us become better stewards, but over the last 10-15 years we’ve improved technologically by leaps and bounds. Major things have helped us do this such as GMO crops, which have saved us labor and allowed us to make fewer passes on the field. Soil health on my farm has improved because of my ability to strip-till which reduces emissions and enables greater carbon sequestration on my land. In addition, GMO seeds have allowed us to make savings on fuel use. On sugarbeets alone, we now use five to six gallons an acre less than we did on conventional beets. GMO seeds have allowed us to use less pesticides on sugarbeets and other crops than we did with conventional varieties. We can now spray fewer times with less active ingredient than before which has reduced the environmental impact
by 92% using glyphosate instead of conventional herbicides.”
“Beyond biotechnology, the development of GPS and continued advancements in the technology have allowed us to cut down on overlapping passes for seed, fertilizer and chemical applications decreasing fuel and time usage. Prior to GPS, on a sprayer we used to have 5 to 10% over application but now with auto boom shut-off, over-application is reduced to less than 2%. Everything is just more precise and accurate. Tier four-engine standards, which are required by the Environmental Protection Agency for non-road agricultural heavy equipment that uses diesel fuel, sets up engine and fuel controls that dramatically reduce emissions. The standards require expensive equipment upgrades and fuel additives but I doubt that most folks not directly involved in agriculture know that we are emitting up to 90% less nitrogen oxide, much less CO2, and much less particulate matter than before. Center pivot irrigation has also helped us greatly by allowing us to reduce our tillage. It also reduces water run-off and reduces how much actual water is applied to the crop. Cooperative-wide use of pivots in a normal year has reduced water demand by 30%. All our pivots run off electricity so no diesel engines are used to pump the water that is delivered to us through a series of canals.”
Pitts was also asked what Western Sugar Cooperative does to help growers meet their personal or sustainability goals or Western’s cooperative-level goals. He said, “I believe Western Sugar has been a leader on the sustainability issue for many years. We’ve tracked many growers throughout the years to prove what has been done and where we are headed in the future. Thank God for Rebecca Larson who is definitely out in front of this issue. She has done so much research for our
CONTINUED ON PAGE 18
Vice President General Counsel of the American Sugarbeet Growers AssociationScott Herndon serves as the Vice President and General Counsel of the American Sugarbeet Growers Association (ASGA) in Washington, DC. He represents growers on all issues that impact the sugar industry, including sustainability. On sustainability policy, he works with Farmers for a Sustainable Future, www.sustainablefarming. us, a coalition of twentyone farm and ranch groups committed to environmental and economic sustainability. Scott can be reached at sherndon@ americansugarbeet.org.
CONTINUED FROM PAGE 17
company and can go toe-to-toe with almost anyone to prove that what we are doing is very sustainable. Western Sugar has made an effort to allow data to drive research investments. We have the appropriate information to know where opportunities for improvement lay (in terms of improving farm economics and environmental outcomes). We have developed and follow a strategic plan to invest in research to address those areas. We also invest in research that doesn’t necessarily drive changes on-farm, but rather helps us communicate with data about how farmers are making the appropriate decisions. Our research helps protect our freedom to operate and help the everyday person understand farming better. In addition, Western research has helped us get certification to sell our sugar to many buyers looking to support their sustainability supply chain goals.”
“Western Sugar also supports sustainability through its hybrid approval system. The sugarbeet seed market is a closed system. The cooperative determines what can or cannot be
long required native tolerance to seven different pests and diseases. This improves the predictability of production for the farmer and farm economics. Our system provides the plants with the tools to defend themselves.”
Pitts then went on to describe what he has done on his own farm. “As far as our operation we do very little tillage anymore. We strip-till everything. This reduces fuel usage greatly. It also helps retain moisture because only 25% of the soil gets disturbed. It allows us to place our fertilizer in a small band, reducing leaching and runoff. We also apply fertilizer at two other times throughout the growing season to reduce leaching and runoff and to spoon-feed the crops as they need the fertilizer. Strip-tilling has also helped add carbon to our fields by not burying the residue and letting it break down slowly on top of the soil surface. Over the last 13 years of striptilling our organic matter has doubled in the soil. The soil microbiome has improved as well. This has made it a more porous soil that helps hold more water, reduces leaching and reduces water
Michigan Mike, 1-810-705-0297
Idaho Kent, 1-208-280-0079
Nebraska
21 st Century Equipment
Minnesota
Midwest Machinery Co.
John Noorloos
1-519-339-6015
runoff during rain events. In my opinion, earthworms are a big part of soil health and we now have thriving populations of worms in our soil. A handful of soil now looks so drastically different than it did 15 years ago.”
“Strip-tilling has also helped with compaction issues along with the use of GPS. We have used the same rows in our fields since 2008 when we started using GPS. This has reduced compaction greatly. On the compaction issue, we also use carts while harvesting. We never let trucks in the fields because this causes compaction. Many people suggest to just rip the soil after and get rid of compaction. This would work but then more fuel is burned and the soil structure and earthworm’s ecology are completely destroyed so we use carts no matter how wet or dry the soil is. We also use crop rotations to help improve our soil. Alfalfa is an important part of our crop rotation because its deep roots help to break up the soil. It also leaves good nitrogen in the ground for future crops. Center pivot irrigation has allowed us to reduce tillage and use strip-tillage. With flood irrigation, the soil has to be pretty clean of debris for the water to go through the field but not with center pivots. Having the extra debris on top of the soil has helped us reduce runoff, reduce water and wind erosion and reduce water evaporation.”
“I could ramble on for hours about sustainability and all the improvements we have made and may be able to make in the future. It seems to me like it’s a big jigsaw puzzle but it’s evolved into this for many years. Thinking about it, my dad has been trying different things since I was a kid. Some of them to improve sustainability and some of them to improve the bottom line. They both go kind of hand in hand. Usually being more sustainable leads to improving your bottom line even if some of the steps are expensive in the beginning. It also leads to improving the most important thing, our future. I’m sure agriculture will continue to improve at a rapid pace. Some things I look to in the short future are new GMO technology, variable rate fertilizing, variable rate water application and improving diesel emissions even further than where we are today. Sometimes it’s hard to imagine the future and how it will evolve. It makes me wonder if my great grandparents thought ‘how could we improve anymore’ when they were plowing with a team of horses,” he said with a laugh. “I don’t want to go back there for sure.”
In closing, Pitts said, “The thing I’m most proud of is that I’m a fourth-generation farmer and second-generation sugar producer and I have to ensure that I can pass this great way of life onto the next generations to come. The only way I can do this is to evolve over time to continue to be a great steward of the land just as my family has done in the past. An important part of maintaining agriculture is to educate the public about all of the technology we use and the environmental benefits we deliver, in addition to providing food. The public doesn’t understand what agriculture does for the ecosystem. We need to do a better job communicating. Yes, we burn some fuel, use some fertilizer and use precise doses of pesticides but do many people understand how much CO2 is converted to oxygen and carbon in the process?”
DURA-PUMP EASY CADDY
• Can be mounted in 6 different configurations on a variety of tank/tote & drum types
• Use it mounted on top of tank or top of 55 gallon drum, on side of tank, or off the ground
• Conversion Kits are available to mount system on Monsanto & Snyder type tank
• Tank/tote not included
DURA-PUMP EASY CADDY WITH AUTO-BATCH SYSTEM
• Intuitive interface allows for the selection of manual or automatic operation with the flip of a switch
• Optimized for repeatable batching; returns to the last volume amount dispensed
• 100% moisture sealed circuitry
• Includes Dura-Meter and Dura-Pump
• Suction port has 2” Male NPT and 1” Female NPT
DURA-METER
• Made of impact resistant Lexan faceplate
• 100% moisture sealed circuitry
• Menu driven backlit display
• Plumbed both for in-line and 90 degree applications
DURA-PUMP
• High-Flow with up to 15GPM
• Self-priming diaphragm pump w/ internal by-pass
• Motor thermally protected from overheating
• 30 minute duty cycle
• Suction port has 2” Male NPT and 1” Female NPT
Ernest Flegenheimer, former president and CEO of Michigan Sugar Company, died on Feb 2. He was 94.
Flegenheimer’s time as president and CEO of Michigan Sugar spanned over three decades from 1963 to 1993.
He was born in 1927 in Zurich, Switzerland. His father, Albert Flegenheimer was also a pioneer in the sugar industry. Ernest came to the U.S. in 1942 and was naturalized in 1943.
His career in sugar began in 1954 when he began working for Menominee Sugar Company in Green Bay, Wis. He worked there nine years before joining Michigan Sugar.
Ernest was married to Marjorie McGinn, who preceded him in death. Together, they had four children — Ellen, Lauren, Eric and Mark. Today, Mark Flegenheimer continues the family legacy in the sugar industry as he serves as president and CEO of Michigan Sugar.
“Ernest will always be a beloved member of the Michigan Sugar family and we know his impact went far beyond our footprint,” said Michigan Sugar in a statement. “Simply put, Ernest influenced and touched countless people during his life and career.”
Each year, Flegenheimer is remembered at Michigan Sugar through the Ernest Flegenheimer Award, given during the company’s annual Employee Service Award ceremonies to honor an employee for outstanding wisdom, integrity and character.
Each spring, it’s every sugarbeet grower’s goal to grow the biggest and sweetest beets. ACH Seeds has been rewarding its growers who do just that with their annual Sugar Bounty program.
This year’s regional winners were announced during the American Sugarbeet Growers Association annual meeting, which was held virtually this year, by ACH Seeds Crystal Brand sales leader, Andy Finkral.
“For the 2020 crop year, we again had amazing results from all sugarbeet regions,” said Finkral during the meeting. “Growers continue to produce high ton and high sugar crops using ACH Seeds Crystal brand genetics. We’re so pleased to announce this year’s Sugar Bounty winners.”
2020 winners in each region, with their impressive field results are:
• Great Lakes – Renata Farms LTD, Wallaceburg, Ontario.
• Amalgamated – Deer Flat Farms Inc., Nampa, Idaho.
• Southern Minnesota – Chris Sturm, Springfield, Minn.
• MinnDak – Summer, Inc., Herman, Minn.
• Sidney Sugars – Asbeck Brothers, Fairview, Mont.
• Western Sugar, South – Eckhardt Farms, Inc., LaSalle, Colo.
• Western Sugar, North – Terral Balzer, Worden, Mont.
• Wyoming Sugar – Michael Vigil Farms, Manderson, Wyo.
Each region winner receives gifts that include a Traeger grill with custom grill inserts, a bar pub and stool set, a box of ACH Seeds Crystal brand sugarbeet seed for their upcoming crop, and a plaque recognizing their accomplishment. District and region winners also receive a special Sugar Bounty program jacket that is specific to each program year.
The ACH Seeds Sugar Bounty program is a loyalty and incentive program intended to reward customers for planting Crystal brand varieties that produce the highest sugar and/or tonnage within each sugarbeet growing region where Crystal brand varieties are marketed.
BAY CITY, MICH. — Michigan Sugar Company has concluded its 2020-21 sugarbeet slicing campaign at its factories in Bay City, Caro, Croswell, and Sebewaing.
This year’s campaign started in mid-August and wrapped up the week of March 14. Over the course of the campaign, Michigan Sugar sliced 4,277,351 tons of sugarbeets and produced more than 1.17 billion pounds of sugar from beets. Each year, after all the sugarbeets are sliced, the Bay City, Croswell and Sebewaing factories continue to produce sugar from juice and extract stored during the campaign. From juice and extract, Michigan Sugar Company expects to produce an additional 100 million pounds of sugar this year, which will bring the total sugar production to more than 1.27 billion pounds.
Additionally, the company produced more than 160,000 tons of molasses and 122,000 tons of dry pulp products and sold more than 423,000 tons of pressed pulp. All these products are sold as livestock feed.
“This year’s campaign was a huge success,” said Mark Flegenheimer, President and CEO at Michigan Sugar Company. “Our employees did an amazing job getting our sugarbeets processed and our sugar packaged and shipped, despite some unique challenges, especially in terms of staffing, that were perpetuated by the COVID-19 pandemic. We appreciate and thank our employees for the tremendous effort they put forth over the past seven months.”
Flegenheimer noted the Bay City and Caro factories finished slicing beets on Saturday, March 13; the Croswell factory finished Sunday, March 14; and Sebewaing finished Tuesday, March 16.
Michigan Sugar Company Executive Vice President Jim Ruhlman praised the cooperative’s nearly 900 grower-owners, who planted and harvested about 162,000 acres of sugarbeets this campaign.
“We were blessed this year with a beautiful crop of sugarbeets harvested by our
grower-owners, who are among the most talented in the industry,” Ruhlman said. “Mother Nature not only dealt us a good hand during harvest, but she continued smiling on us throughout the campaign with weather very favorable for piling and storing sugarbeets. We had a great year for storage and as a result our factories were slicing quality beets right up to the end of campaign.
“And we all know that the higher the quality of the beets, the more sugar we can extract.”
Michigan Sugar Company’s Vice President of Operations Jason Lowry highlighted a handful of new records achieved during the campaign at the facilities in Sebewaing and Croswell.
In Sebewaing, a new record was set for daily sugar production with 1.37 million pounds per day, besting the previous record of 1.28 million pounds per day set during the 2012-2013 campaign.
In Croswell, new records were set for tons of sugarbeets sliced (previous record was 855,834 tons in 2015-16), total sugar produced (previous record was 229.18 million pounds in 2015-2016), and average daily slice. During this year’s campaign, the factory averaged slicing 4,275 tons per day, which beat the previous record of 4,128 tons per day set during the 20162017 campaign.
“This shows us that our recent investments at the Croswell factory are beginning to pay off,” said Lowry, noting a multi-year, $70 million capital upgrade project that aims to increase slicing capacity at the Croswell factory by 50 percent.
Lowry said the final year of that project is slated to be completed during the upcoming inter-campaign — the time between the end of one sugarbeet slicing campaign and the beginning of another.
“We have several significant projects planned this year in Croswell, including the construction of a new gas-fired lime kiln and installation of a new evapora-
tor and a new mud filter press station,” Lowry said, noting total investment in the factory this year will exceed $20 million.
“When all is said and done, we believe the improvements made in Croswell over the past six years will put us on track to eventually slice as many as 6,000 tons of sugarbeets per day.”
Michigan Sugar Company also plans to construct a new covered and ventilated sugarbeet storage structure in Croswell during the upcoming inter-campaign. Commonly referred to as a “hoop building,” the $5 million facility will store up to 70,000 tons of sugarbeets beginning with the 2021 crop. Michigan Sugar Company also has a hoop building in Sebewaing that was constructed about six years ago and has proven valuable in helping preserve high-quality sugarbeets for slicing right up until the end of campaigns.
Elsewhere, Michigan Sugar Company is investing $2.5 million to add a third consumer brown sugar packaging line in Bay City that will increase production by 50%. To make room for that line, the company’s industrial brown sugar packaging line is being relocated to the Sebewaing factory, which will begin packaging brown sugar for the first time. In Caro, work will be done to upgrade the site’s electrical distribution system.
Michigan Sugar Company also is purchasing three new pilers at a cost of about $5 million. The pilers will be placed in Bay City, Croswell, and Sebewaing to facilitate more efficient unloading of sugarbeet trucks beginning with the 2021 harvest.
“Inter-campaign is always a busy time of the year in our factories as we prepare for another sugarbeet slicing campaign,” Lowry said.
Just as one season ends, another begins at Michigan Sugar Company, where grower-owners are preparing to return to their fields in the coming weeks to plant this year’s crop. The first seeds already were planted on March 15 in Ontario, Canada. where the company grows about 10,000 of its acres. This year, the company expects to plant about 160,000 acres.
Plans announced for new beet planted to be constructed in Wahpeton, N.D.
Plans have been announced to construct a major beet sugar processing plant in Wahpeton, N.D.
Officers of the Southern Red River Valley Sugarbeet Corporation and Al Hartl, president of Otter Tail Power Co., Fergus Falls, Minn., made their announcement on April 14.
Final decision to proceed depends on the results of an engineering study now underway and the grinding of acreage allotments and marketing quotas by the U.S. Department of Agriculture.
Acreage to supply the proposed plant would come from both North Dakota and Minnesota.
Land acquisition has begun for the facility which would be located adjacent to the Otter Tail’s Kidder Station on the north edge of the city.
“This is indeed a historic occasion,” said Hartl. “We’re as close to fruition as possible without saying ‘go.’”
A substantial amount of the $25 million plant package would come from farmers, who would participate at the rate of $100 per acre of beets on a positive payback basis. Growers would have to participate to get a beet contract.
Hartl said the associates would form a new company with no company holding a major interest. He described Otter Tail Power’s participation as another diversification effort the firm has embarked upon.
The plan involves moving equipment from a plant at Chatham, Ont., to Wahpeton. The Chatham plant has been closed for three
years. (The Chatham plant was erected in 1916 and had a daily rated capacity of 3,200 tons of beets at the time it closed.)
A new steel structure will be built to house the sugarbeet plant which will have a capacity of 4,000 tons per day.
Ted Peet, Wolverton, Minn., landowner and director of Otter Tail, said good soil and good people — the ingredients necessary for success — are present in the project.
Leo Yaggie, Breckenridge, Minn., vice president of Southern Red River Valley Sugarbeet Corp. said, “It’s been a long struggle. It’s got to be the best thing to ever his this area.”
James Link, Mooreton, N.D., president of the corporation, said “the announcement represents the culmination of some 20 years of effort by farmers in the area to break the bottleneck of bringing a large sugar refinery into the southern part of the Valley as a means of materially improving the economy of the area.”
The mechanized handling of sugarbeets is an accomplished fact but, at present, no machine has been developed which can equal hand methods when the quality and production is of primary importance, and at this time thinning and weeding machines are being used to assist hand laborers rather than replace them.
The 1970 Youth Sugar Beet Program in North Dakota was greatly assisted by the mechanical thinner in most areas and, in some instances, growers used youth labor entirely along with their mechanical thinners. Due to weather conditions and the lateness of seeding operations, there was some aban-
donment of beet acreage which affected the recruitment and employment of youth.
For 1970, 1,100 youth thinned and hoed 7,458 acres of beets in 55 different farms, working 78,986 hours with an average rate of 1.26 per hour. Supervision of the program was carried out by 35 coordinators and crew supervisors, many of whom have been in the program for years. A total of $99,874.50 was earned by youth, while the supervisors had earnings of $14,743,56 for a grand total of $114,618.06.
The outstanding program for the year was in the Grafton area where nine crews of 297 youth thinned and hoed 3,693 acres and averaged 12 acres per youth, and had a 1.25 hourly rate with total earnings of $51,494.51. In addition, the total youth of 194, of which 80 were girls, had average earnings of $231.88. As an added incentive a $25 Savings Bond was awarded to the girl and boy with the highest earnings. The girl earned $482.79 and the boy earned $671.55. Three other boys had earnings of $500. Major credit for this successful program is the result of good supervision and the interest and attitude of the youth.
Imperial Valley sugarbeet growers set record highs in tonnage per acre and in money received for sugar sold, according to Ralph Yocum, Holly Sugar Corporation’s agricultural manager for Southern California.
Yocum said that Holly Growers received a final payment of $1,245 million on March 31 for their 1969-70 crop. Total returns to Holly growers amounted to $16 million which includes payments from Holly and under the Sugar Act.
The average price received by the growers, including Sugar Act payment, is $17.85 per ton, the highest return ever received. The crop averaged 24.5 tons per acre, another record, Yocum said.
Submitted
Webco manufactures quality welded stainless steel specialty tubing products for evaporators, vacuum pans, juice pre-heaters and more
Welded Stainless TubingGradesmill test reports provided: A249-439, 249-304/304L, A249-316/316L
For moreinformation, please contact:
MikeJamison: 918-630-0982
mjamison@webcotube.com
Jerri Lauderdale: 918-241-1037
jlauderdale@webcotube.com
www.webcotube.com
1: Beautiful day for beet harvest in northwest Minnesota. Submitted by Kevin Dufault. 2: A late night digging beets. Submitted by Kortney Brown. 3: Sun setting over sugar. Submitted by Vicky Gudajtes. 4: A sweet sunrise in Minto, N.D. by Patti Bjorneby. 5: A future farmer. Submitted by Alex Moore. 6: Vader Farms, last lap on the 2020 strip trial. Submitted by Doug Ruppal. 7: Harvesting sugarbeets in southwest Nebraska by Sidney. Submitted by Nick Vollmer.