Electrolyseurs et piles à combustible
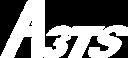
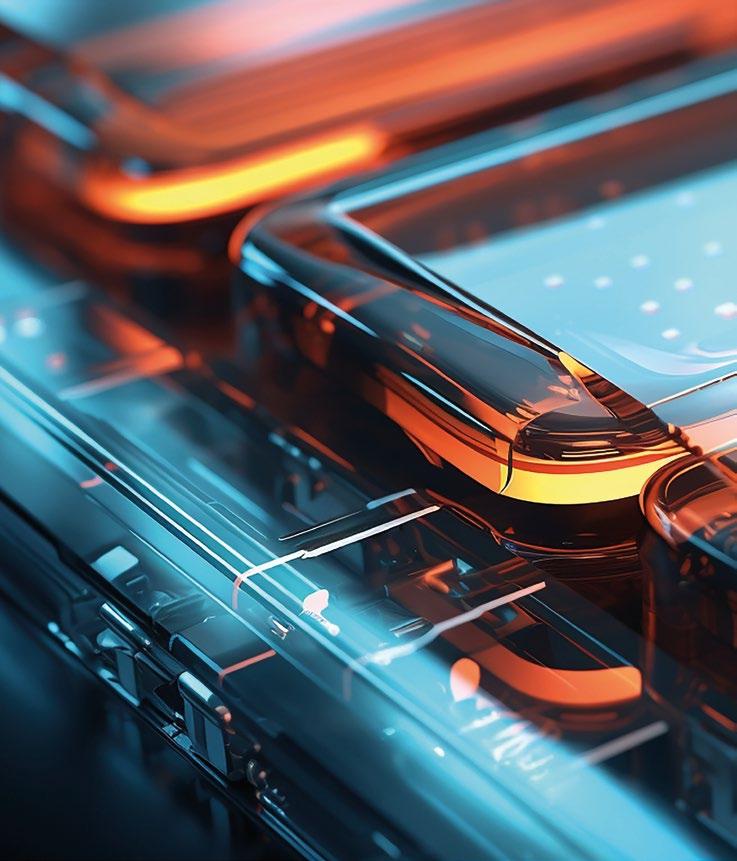
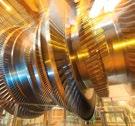
51e Congrès et Salon
A3TS 2025
• 2 et 3 juillet 2025, Dijon
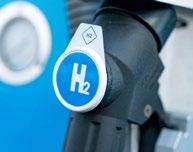
Journées Hydrogène
• 16 et 17 octobre 2024, Courbevoie
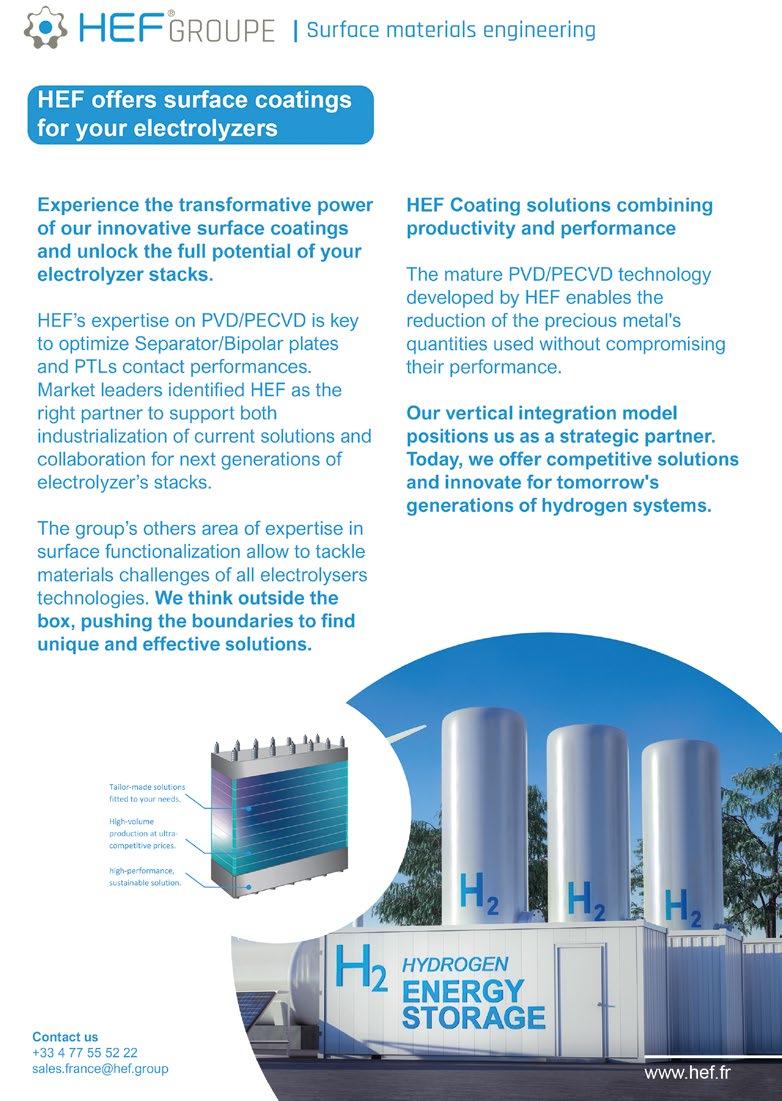
L’A3TS à l'ère de la transformation industrielle et écologique
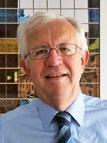
Par Pierre BRUCHET
Délégué Général de l’A3TS
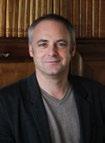
Par Jean-Yves HIHN
Professeur à l’Université de Franche-Comté, Directeur adjoint Institut UTINAM, Président du Conseil Scientifique et Technologique de l’A3TS
L’évolution de l’environnement sociétal, économique et industriel, sous le double feu d’une obligation de performance et de l’inquiétude liée au réchauffement climatique impacte fortement le domaine des matériaux et tous ses acteurs, qu’ils soient ingénieurs, techniciens ou chercheurs. En particulier, les stratégies industrielles ont été alignées sur des objectifs faisant la part belle à la décarbonation, à l’électrification des procédés et des mobilités avec un recours accru aux technologies numériques.
Le choix d’inscrire nos congrès nationaux dans une thématique particulière (l'électrification des mobilités en 2023, les traitements pour un avenir durable avec un focus sur la filière aéronautique en 2024) s'inscrit dans une volonté plus globale de répondre à vos attentes en focalisant les événements de l’A3TS - congrès annuel, journées techniques - sur des enjeux jugés prioritaires. Il est apparu, en effet, essentiel de concentrer les contenus sur des domaines en évolution rapide, dans lesquels les technologies sont encore en recherche de maturité et où l'approche collaborative apparaît souvent indispensable pour atteindre les objectifs dans des délais extrêmement courts. Cette composante “collaborative”, combinée avec le caractère transversal des technologies en question, contribue à accroître l'intérêt des initiatives de l’A3TS qui visent à diffuser les innovations et à renforcer les réseaux d’innovation technologique.
Parmi les leviers de la décarbonation de l’industrie et des transports, l’hydrogène suscite de nombreuses interrogations. Possibilité souple de stockage des énergies renouvelables à production intermittente comme l’éolien ou le solaire, source d’énergie décarbonée se posant comme une alternative un peu idéalisée au diesel
ou au kérosène avec « à la clé, 6 millions de tonnes d’émissions de CO2 économisés en 2030 », selon l’ancienne ministre de la Transition Écologique Barbara Pompili, il constituerait la solution idéale si on oubliait les problématiques d’entreposage et de production ! Les besoins en innovation sont immenses.
Dans ce numéro, vous verrez que les grands objectifs, rappelés ci-après par Bruno Pollet, et la recherche d’une souveraineté technologique - pour ne pas retomber dans une dépendance constatée dans d'autres enjeux de l’énergie (photovoltaïque, éoliennes, batteries) - ont suscité de nombreux programmes pour le développement d’une filière Hydrogène : électrolyseurs destinés à fonctionner avec de l’électricité renouvelable ou décarbonée, piles à combustibles embarquées sur véhicules et aéronefs, etc.
Les technologies de traitement des matériaux et, en particulier, de leur surface jouent un rôle essentiel pour ces familles d’équipements. C’est ce que nous invitent à découvrir Armand Gering (John Cockerill) pour les électrolyseurs, Manuel Bianco (Symbio) et Marjorie Cavarroc (Safran) pour les piles à combustibles.
Ces technologies et bien d’autres seront par ailleurs au centre des discussions des journées “Hydrogène - Défis Technologies dans les matériaux métalliques” des 16 et 17 octobre 2024. Il est encore temps de déposer vos propositions de conférence via le site de l’A3TS www.a3ts.org.
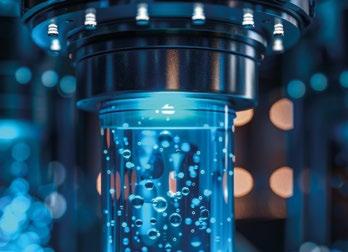
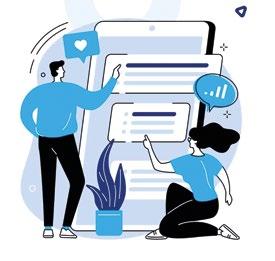
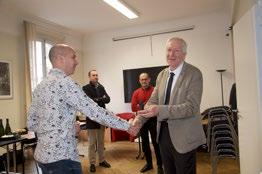
Sommaire
Prochains évènements
Enquête sur les traitements thermiques
Retour sur évènements
Assemblée générale A3TS
Notre dossier thématique
Comité de rédaction
Solène Brizay-Bruchet, Sylvain Batbedat, Pierre Bruchet
Direction artistique et maquettage Yannick Peyronnet
Contact A3TS
71 rue La Fayette, 75009 Paris
Tél. : 01 45 26 22 35
Email : a3ts@a3ts.org
Site : www.a3ts.org
Imprimeur
Opera Print Paris
Photo de couverture
©D.R. Metals Magazine


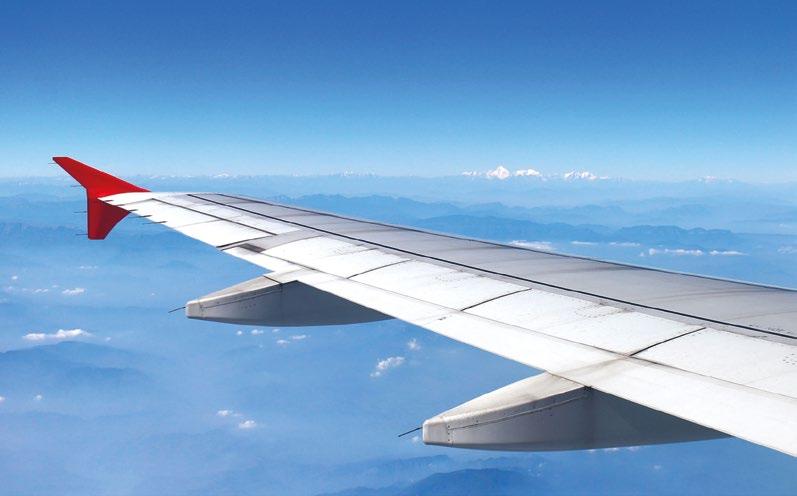
Prochain évènement
Journée inédite sur les traitements de surface dans l'aéronautique : Innovations et implémen-
tations Franco-Belges
Le 19 septembre prochain aura lieu une journée d’un format inédit. Organisée conjointement par l’A3TS et la VOM (homologue belge de l’UITS), nous aurons l’occasion d’écouter des orateurs belges et français nous présenter des conférences sur le thème : Le traitement de surface dans l’aéronautique, de la technologie innovante à son implémentation.
Cette journée exceptionnelle se déroulera sur deux sites, un en France et un en Belgique et, au terme des exposés présentés alternativement sur chaque site et retransmis en visio, une visite d’installations de
traitement de surface sera organisée. Celles de la SONACA à Gosselies pour le versant belge et celles de l’IRT M2P pour le versant français. La participation en Belgique et/ou en France est ouverte aux membres des deux associations, et cette journée sera l’occasion de découvrir des projets de recherche et développement industriels iconiques belges et français. J’espère vous y voir nombreux pour faire connaissances avec nos collègues du nord.
Plus d’informations : https://www.a3ts.org/evenements
JOURNÉE D'ÉTUDE A3TS/VOM : LES TRAITEMENTS DE SURFACE DANS L'AÉRONAUTIQUE
Jeudi 19 septembre 2024 Molsheim, France
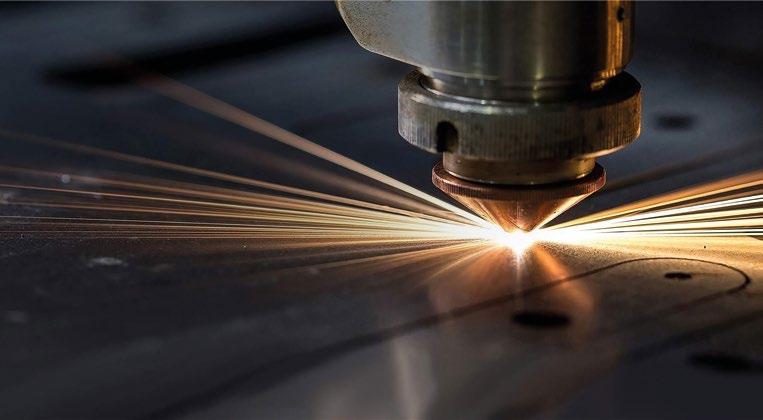
Prochain évènement
La Fabrication Additive Un Atout Stratégique pour l'Industrie et l'Environnement
Les technologies de fabrication additive sont pour beaucoup d'industries un levier de compétitivité. Elles concourent aussi aux objectifs de réduction de l’empreinte carbone (allègement, économie de matière et d’énergie). Le chemin vers l’industrialisation et la qualification pour des applications industrielles exigeantes en termes de fiabilité et de durabilité est cependant long et nécessite de relever un grand nombre de challenges.
Quelles que soient les technologies de fabrication additive, les opérations de finition, incluant traitements dans la masse et traitements/revêtements des surfaces sont essentielles dans le processus d’industrialisation et constituent un élément clé de la chaîne de valeur.
Cette 5ème édition des Journées Traitements et Parachèvements des pièces de fabrication additive, proposés par l’A3TS et France Titane, rassembleront à nouveau industriels et laboratoires qui débattront pendant deux jours des avancées scientifiques, des nouvelles solutions technologiques et des retours d’expérience.
FABRICATION ADDITIVE
janvier 2025, lieu à venir
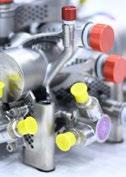
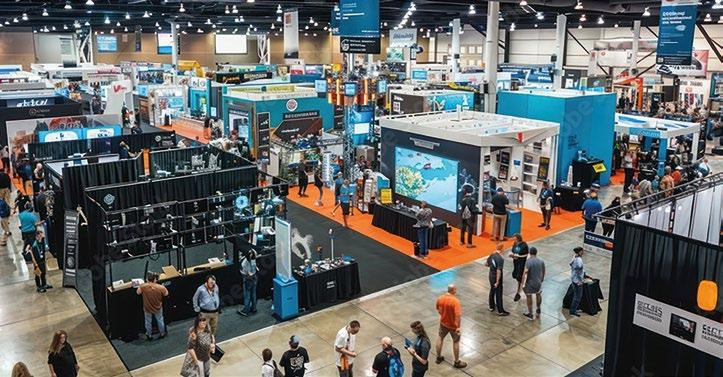
Prochain évènement
Rendez-vous à Dijon les 2 et 3 juillet 2025 !
En 2025, la ville de Dijon accueillera un événement exceptionnel pour les professionnels du secteur industriel : le 51e Congrès et Salon A3TS. Pour cette édition, le congrès accueillera la 1ere Conférence Internationale “Traitements thermiques et Ingénierie des Surfaces pour une énergie bas-carbone”
Un Thème au Cœur des Enjeux Industriels
Cet événement, organisé par l'A3TS, mettra en lumière les défis et les innovations pour le traitement des matériaux dans les domaines des énergies renouvelables et décarbonées : énergies renouvelables, nucléaire, hydrogène, biocarburants, capture et séquestration du CO2,... L'objectif est de rassembler des acteurs issus de filières diversifiées pour partager des solutions technologiques, identifier les enjeux clés et promouvoir des approches collaboratives.
Programme et Objectifs
Le programme de l'événement comprendra deux journées de conférences, un salon de 80 exposants et de nombreuses animations (tables rondes d’experts, concours de l’innovation, …).
Les thématiques abordées incluront :
• Traitements thermiques pour les énergies renouvelables : Exploration des technologies de traitement thermique et de revêtement des surfaces adaptées aux besoins spécifiques des énergies renouvelables, telles que l'éolien et le solaire
• Ingénierie des surfaces pour l'industrie nucléaire : Innovations en matière de revêtements protecteurs pour les composants nucléaires, visant à améliorer la durabilité et la sécurité.
• Capture et séquestration du CO2 (CCS) : Techniques de traitement et revêtements des matériaux pour optimiser les processus de capture et de stockage du carbone.
• Hydrogène et Biogaz : Développement de solutions de traitement thermique et de surface pour soutenir l'expansion de ces filières spécifiques
• Electrification dans l’industrie et les transports
Plus d’informations bientôt sur www.a3ts.org/evenements
HEAT TREATMENT AND SURFACE ENGINEERING FOR LOW-CARBON ENERGY SECTOR
2, 3 juillet 2025, Dijon




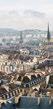

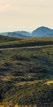

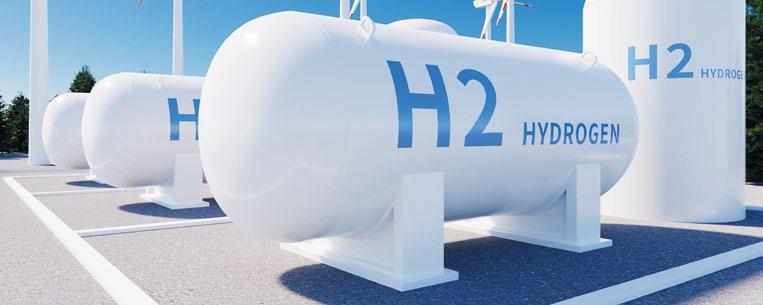
Prochain évènement
Les Défis de l'Hydrogène dans les Matériaux Métalliques
L’hydrogène, premier et plus petit élément de la classification, est l’objet de toutes les attentions, car il représente une alternative intéressante aux énergies carbonées. Mais du côté des ingénieurs et techniciens des matériaux, l’hydrogène nous le connaissons que trop bien... et pas forcément sous un jour favorable. Co-généré pendant les réactions électrochimiques, il diminue les rendements faradiques, mais surtout, avec sa petite taille, il peut facilement diffuser dans un réseau métallique cristallin et y rester piégé. Il peut se combiner avec certains métaux ou dans des alliages comme ceux du titane pour former des hydrures métalliques. Plus généralement, il est à l’origine de la formation de phases par précipitation ou recristallisation, parfois même par simple sollicitation mécanique. Cela entraine des modifications dans la microstructure à l’origine d’une forte dégradation des propriétés mécaniques des matériaux, encore amplifiée par la présence de contraintes qui peut conduire à la fissuration fragile.
Avec l’accroissement des besoins (transport stockage, production) qui s’ajoutent aux nombreux cas d’emploi déjà présents dans l’industrie, il est plus que jamais besoin de faire le point sur l’actualité de la recherche et des avancées technologiques. Comme toujours, une partie de la solution est dans l’innovation !
Vous êtes invité à déposer votre proposition de conférences avant le 15 juin 2024 sur les thèmes suivants :
• Endommagement par l’hydrogène dans les matériaux métalliques : acier, base nickel, titane, aluminium. Comment évaluer les risques lors de l’élaboration et les post-traitements (soudage, fonderie, fragilisation après traitements de surface...)? Quel guide de choix pour les matériaux ? Résistance mécanique et corrosion, corrosion sous contraintes.
• Métrologie de l’hydrogène : Dosage dans les matériaux et localisation. Mesures sous atmosphère hydrogène. Enjeux de normalisation. Contrôle de l’intégrité des équipements...
• Énergie et Matériaux : Élaboration de matériaux pour la génération d’hydrogène. Impacts de la combustion de l’hydrogène (banc d’essais...) . Corrosion par les électrolytes dans les équipements de production (plaques bipolaires, couches poreuses de transport...)
• Production, stockage, transport et usage de l’hydrogène : Quelles solutions pour la protection des structures (couches barrière, traitements thermiques et mécaniques…). Comptabilité avec les matériaux. Contraintes spécifiques. Quelle gestion dans la durée ?...
JOURNÉES HYDROGÈNE : DÉFIS TECHNOLOGIQUES DANS LES MATÉRIAUX MÉTALLIQUES
16 et 17 octobre 2024, la Maison de la Mécanique, Courbevoie (92)
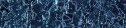
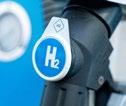
Enquête sur les traitements thermiques
L'A3TS a réalisé en 2023, auprès de ses membres une enquête visant à comprendre les tendances de fond du traitement thermique. Pour cette première enquête, un panel de 40 réponses ont été enregistrées, représentants la diversité des acteurs : industriels, traiteurs à façon, fournisseurs, centres techniques et laboratoires.
Cette enquête a révélé plusieurs tendances parmi lesquelles :
• ¼ des sondés ont fait part de la nécessité de faire évoluer les traitements thermiques
• la réduction de l'empreinte carbone est la motivation qui arrive très nettement devant les autres
• plusieurs pistes sont évoquées pour l'atteinte de cet objectif, concernant les investissements mais aussi les processus d'exploitation
• Les traitements de cémentation/carbonitruration basse pression, nitruration, induction forment le trio de tête sur les priorités de développement à venir
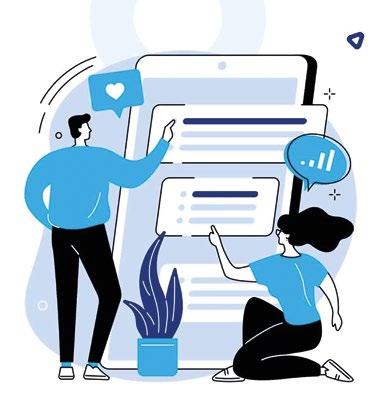
Les résultats complets seront mis prochainement en ligne sur le site www.a3ts.org
L'A3TS réalisera dans le futur d'autres enquêtes qui auront pour but de caractériser et de quantifier les évolutions des traitements des matériaux, traitements thermiques et traitements de surface. La représentativité de ces résultats est bien évidemment directement associée aux nombres de participants. Merci par avance de votre attention sur la prochaine enquête qui sera lancée au cours du deuxième semestre 2024.
Quelles sont les raisons de cette évolution nécessaire ?
Sur quoi les pgms de R&D devraient-ils se concentrer en priorité ?
Pensez vous que votre entreprise doit engager ou participer à des travaux de R&D pour faire évoluer ses traitements thermiques ?
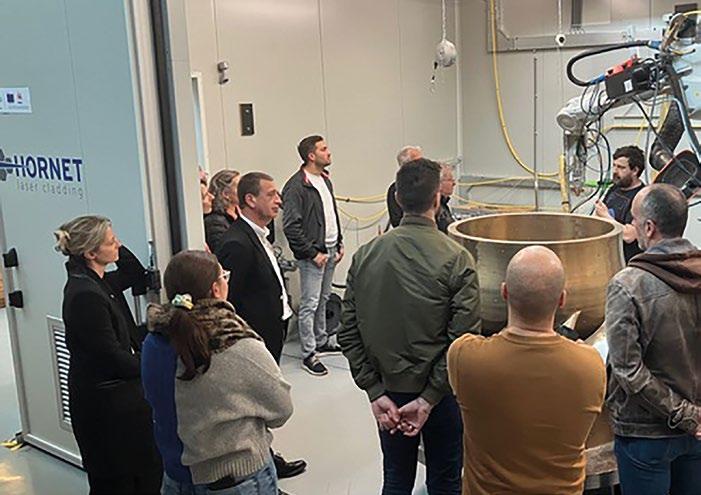
Retour sur la journée technique organisée à Liège
La section France-Nord Belgique de l'A3TS a organisé le 21 mars dernier une journée sur le thème " les traitements localisés, une solution avantageuse en traitement de surface et traitement thermique ? "
Cette journée technique, qui a réuni 25 participants, a débuté avec une présentation de la société Dalic sur l’utilisation de l’électrolyse localisée pour restaurer des pièces usagées ou apporter localement des fonctionnalités additionnelles. Cette intervention a permis de mieux comprendre les possibilités offertes par cette technique particulière. A ensuite été abordée la problématique des traitements thermiques localisés. Une première présentation par la société ViPC pour le groupe ISR (Modène) a rappelé le principe et les avantages de ce
traitement, les inducteurs et les types de machines utilisées avec leurs dernières évolutions. Les autres applications possibles de cette méthode de chauffage ont également été présentées.
Framatome a, ensuite, fait un focus sur le détensionnement localisé post-soudage de pièces ne pouvant être traitées en four, en attirant l’attention sur la problématique de contrôle des contraintes résiduelles qui peuvent être engendrées lors de ces opérations. Puis, Bodycote a présenté les avantages de la soudure par faisceau d’électrons, notamment en termes de profondeur de soudure et de minimisation des contraintes résiduelles.
Le programme de l’après-midi a été consacré aux technologies de revêtements localisés par voie physique. Un premier exposé de Bodycote nous a permis d’appréhender les grands prin-

JOURNÉE TECHNIQUE : LES TRAITEMENTS LOCALISÉS, UNE SOLUTION AVANTAGEUSE EN TRAITEMENT DE SURFACE ET TRAITEMENT THERMIQUE ?
Jeudi 21 mars 2024 Liège (Belgique)
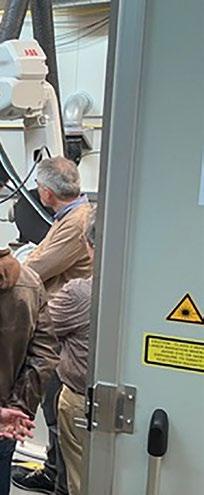
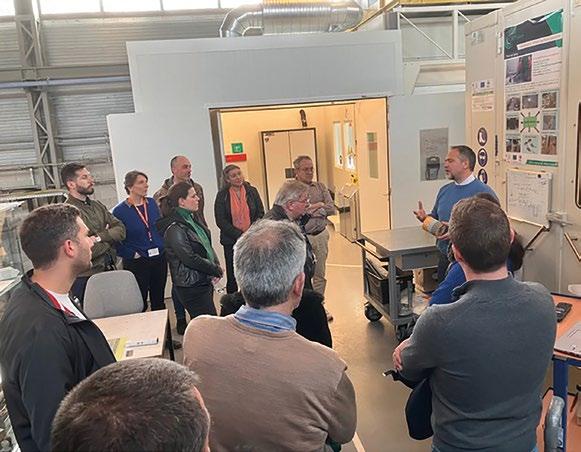
cipes qui permettent de sélectionner les matériaux et procédés de projection thermique pour différentes applications.
À travers différents cas d’études, la société LaserCo nous a présenté les avantages de la technologie de laser-cladding pour la réparation ou la fonctionnalisation de pièces, en particulier en termes d’adhérence grâce au lien métallurgique qu’elle garantit.
La technologie PTA (plasma transfered arc) a été présentée par le CRITT MI au travers de plusieurs projets afin d’en illustrer les aspects procédés et produits, en particulier pour la substitution du chromage dur.
La journée s’est conclue par une visite de la plateforme "advanced manufacturing" du CRM Group, où différentes installations de dépôt (projection thermique, spray électrostatique et laser-cladding) ont été présentées.
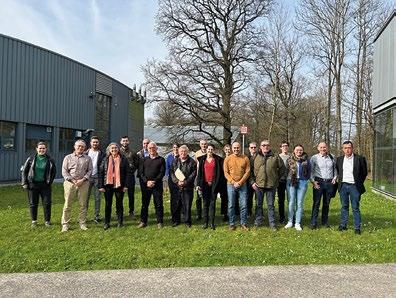
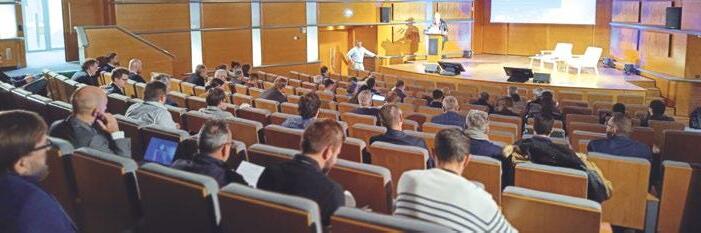
Innovation et réparation au cœur des échanges
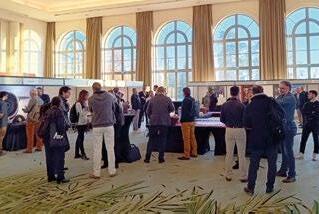
Les 5 et 6 décembre derniers étaient organisées la 8ème conférence des journées Projection thermique, Innovation, Réparation et Rechargement.
Cette édition a rassemblé 24 présentations dans les thèmes suivants : l’Industrie 4.0, les revêtements d’alésages, le Cold Spray, les revêtements PVD, la caractérisation, les applications industrielles, Diagnostic et simulation, Équipements, Matériaux, Projection et Suspension.
Les conférences ont été données par des conférenciers issus de plusieurs pays, dont les États-Unis, le Canada, le Royaume-Uni, l'Allemagne, l'Espagne et la France : les sociétés Airbus Helicopters, CITRA, Fanuc, Fugama, Hardide, Impact Innovation, Mines Paris – PSL, Oerlikon
Balzers, Ouest Coating, Renault, Safran Nacelles, SprayWerx, Université de Mons. Les interventions furent tournées vers les applications professionnelles métiers, avec une forte représentation des principaux fournisseurs de poudre et d'équipements du secteur de la projection thermique.
Les thèmes phares de la session de cette année comprenaient l'innovation en matière de revêtements alternatifs sans Chrome 6, obtenus par projection thermique sèche, illustrée par des exposés sur les torches d'intérieur, mais aussi par des techniques CVD et PVD. La technologie cold spray a également été un sujet de discussion central.
Ces interactions ont également révélé la reconnaissance grandissante de la plateforme Safir au sein de la communauté spécialisée dans la projection thermique. L'espace d'exposition a accueilli 6 stands, offrant un cadre privilégié pour des échanges informels avec les leaders du domaine.
La soirée de gala a eu lieu au Pilota, avec une démonstration de professionnels de pelote basque.
Rendez-vous en 2025 pour la 9ème édition !
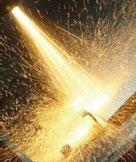
6
24 CONFÉRENCES 85 PARTICIPANTS 6 STANDS
JOURNÉES PROJECTION THERMIQUE, INNOVATION, RÉPARATION ET RECHARGEMENT
5 et 6 décembre 2023 Pau
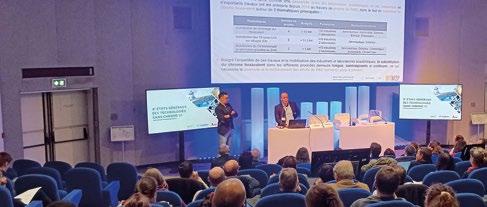
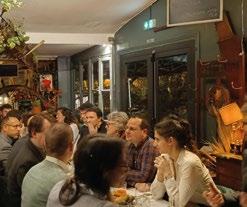
Comment concilier performances, innovations et réglementation dans les traitements de surface ?
La 8ème édition des Etats généraux des technologies sans chrome hexavalent, animée par Frédéric Raulin et Jean-Yves Hihn de l’A3TS, a réuni près de 150 personnes les 23 et 24 janvier derniers à la Maison de la mécanique Courbevoie.
L'objectif de ces journées fut de faire un point sur les avancées technologiques dans le domaine des traitements de surface apportant une alternative à l’usage des sels de Chrome hexavalent, ainsi que sur l’état à date à de la réglementation européenne.
En effet, la commission européenne a publié, en avril 2023, la décision de supprimer le régime d’autorisations des sels de chrome hexavalent pour basculer vers une procédure de restrictions : d’où une certaine confusion et une réelle incompréhension de la filière traitements de surface.
Cette modification de l’application du règlement REACH, dictée par un afflux de demandes d’autorisations dont le traitement a pris du retard, a créé beaucoup d’incertitudes, comme l’a souligné, en introduction de ces journées, Anne-Sophie Maze, déléguée générale de l’Union des Industries des Technologies des Surfaces.
Le processus de restriction a ensuite été expliqué successivement par Laëtitia Benoist – ingénieure d’études en
réglementations substances au CETIM, et ses impacts pour les entreprises ont été détaillées par Béatrice Zaremba du cabinet ECOMUNDO. Car incertitude il y a, autant pour le risque d’une interdiction totale qui mettrait en difficulté la filière, que pour celui d’un cadre plus souple qui ruinerait les efforts dans la recherche d’alternatives alors même qu’elles ont fait beaucoup de progrès. Le débat s’est poursuivi dans une table ronde proposée par Pascal Frou, avec les conférenciers de la matinée et de très nombreuses interactions avec l’auditoire.
Selon de récentes informations de l’UITS, la Commission européenne a demandé à l’ECHA (European Chemicals Agency) d’étendre le champ d’application de la restriction REACH du trioxyde de chrome pour inclure au moins 12 autres substances (chromates, bichromates…). Le projet de restriction est attendu pour le 11 avril 2025.
Un webinaire est organisé sur ce second appel à preuve le 6 juin 2024 par l’ECHA : Events - ECHA (europa.eu)
D’un autre côté, le processus d’autorisation se poursuit pour les substances concernées (bichromates, chromates et trioxyde de chrome) avec des situations différentes selon les substances
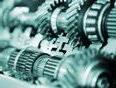



21 CONFÉRENCES
1 TABLE RONDE
150 PARTICIPANTS
LES ETATS GÉNÉRAUX DES TECHNOLOGIES SANS CHROME VI.
23, 24 janvier 2024, Courbevoie
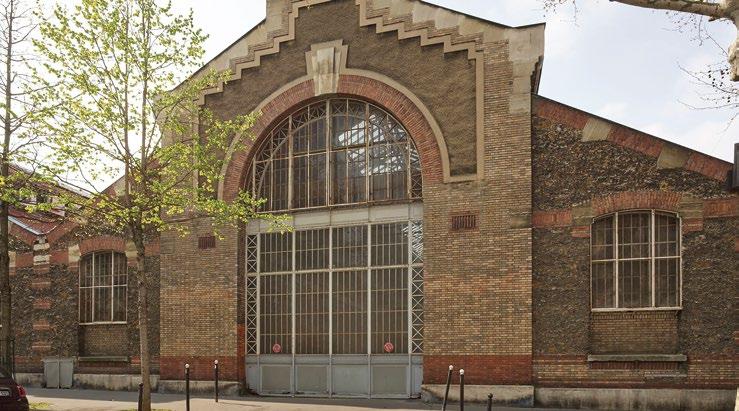
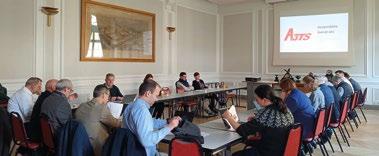
ASSEMBLÉE GÉNÉRALE A3TS
À la rencontre des chercheurs de l’ENSAM
L’Assemblée Générale de l’A3TS a eu lieu le vendredi 22 mars 2024 à 9h au Campus de l’Ecole Nationale Supérieure des Arts et Métiers (Paris 13ème), que nous remercions chaleureusement pour son accueil. Cet évènement fut l’occasion, pour les adhérents présents d’assister à une intervention de Sébastien DUBENT qui assure la responsabilité de l'entité Traitements de Surface et Corrosion au laboratoire de Matériaux Industriels et la responsabilité de la Spectrométrie à Décharge Luminescente (SDL) (Recherche et Prestations) au laboratoire Procédés et Ingénierie en Mécanique et Matériaux (PIMM).
Sébastien Dubent a consacré son exposé au projet “CompoFus” qui vise l’élaboration par procédé de dépôt direct de métal (LMD) et la caractérisation de composites à matrice métallique Fe-TiB2. Dans le contexte économique et social actuel (augmentation du coût des énergies fossiles, réduction des émissions de CO2, transition énergétique, etc.), l’introduction des aciers composites Fe-TiB2 dans le secteur de l’automobile et du transport en général, pour des pièces dimensionnées en rigidité (berceau moteur,
bras de suspension, etc.), permettrait un allégement important de 15 à 30% de la masse des véhicules. Apporter une réponse à la question de la possibilité technique de réaliser de tels aciers composites Fe-TiB2 par le procédé de dépôt direct de métal (LMD) présente par conséquent un intérêt majeur.
Un groupe de participants a ensuite pu visiter des laboratoires de l’ENSAM, notamment ceux consacrés à la fabrication additive.
Ces échanges furent suivis d’un buffet, permettant aux participants de poursuivre les échanges dans la convivialité.
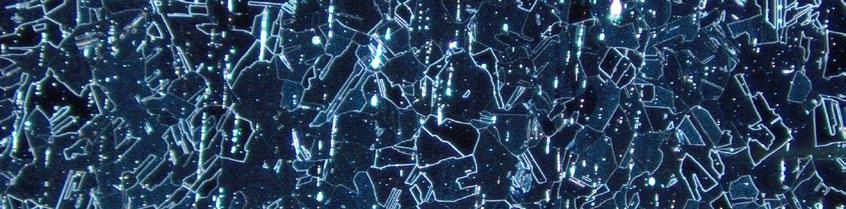
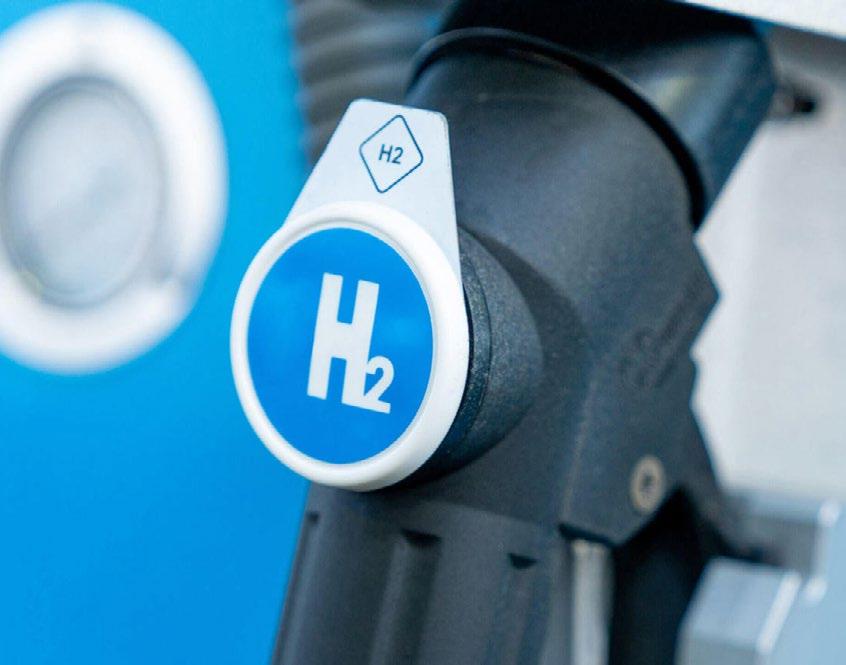
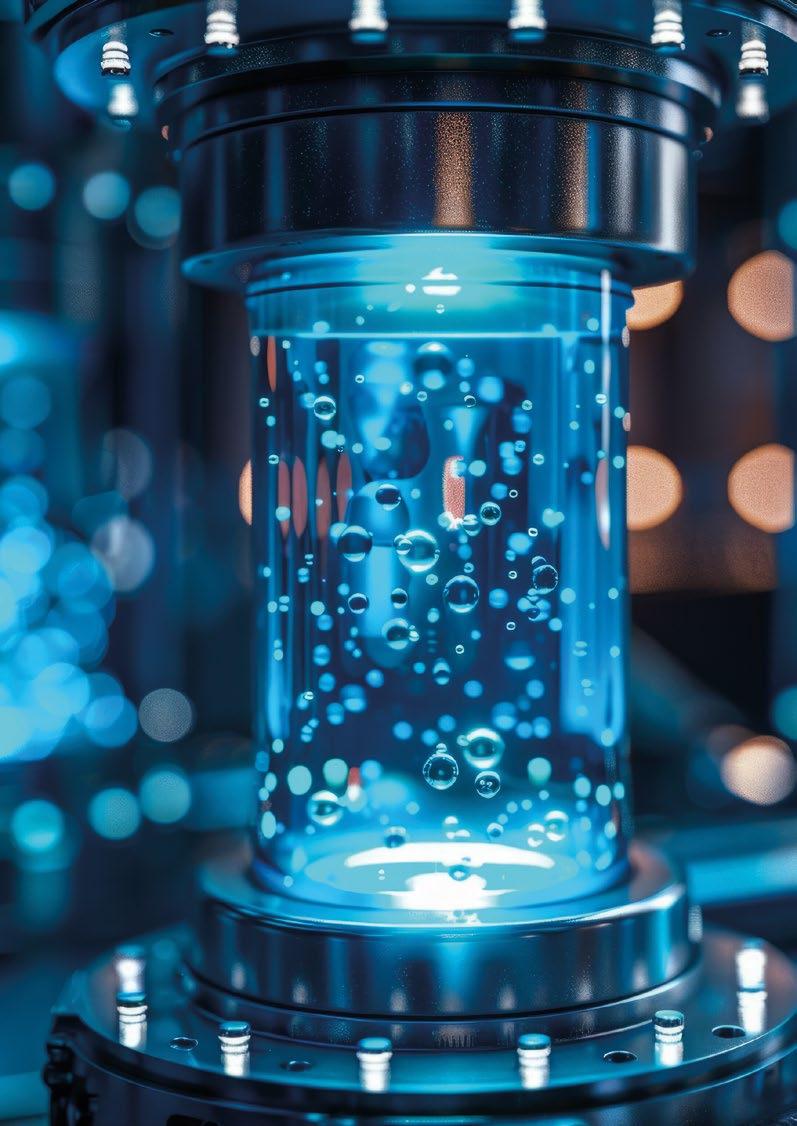
Dossier du mois
L’Hydrogène est considéré aujourd’hui comme l’un des leviers de la décarbonation, complémentaire aux énergies renouvelables, à l’électrification des mobilités et à la sobriété énergétique. Son impact s'inscrit dans une stratégie de long terme, impliquant le développement d’usages ciblés (industries, mobilités lourdes), d'infrastructures de production (hydrogène décarboné) et de réseaux de distribution (canalisations, stations).
Comme dans beaucoup d‘autres domaines de la transition énergétique, la mise au point de nouveaux traitements des matériaux et des surfaces est une étape incontournable pour obtenir les caractéristiques visées en termes de performance, de fiabilité et de durabilité des équipements de la chaîne de valeur.
Après un exposé des enjeux par Bruno Pollet, des exemples très représentatifs associés aux électrolyseurs (John Cockerill) et aux piles à combustible (Symbio, Safran).
L’importance des matériaux dans le secteur de l'hydrogène
Par Bruno G. Pollet President of the Green Hydrogen Division at International Association for Hydrogen Energy
Bien que la capacité mondiale de production d'électricité renouvelable à mettre en œuvre augmente de manière exponentielle avec l'objectif de la tripler d'ici 2030 tel que fixé par la COP28, la capacité mondiale de production d'hydrogène renouvelable est à la traîne. L'Agence internationale de l'énergie (AIE) a récemment abaissé sa prévision de capacité d'énergie renouvelable dédiée à la production d'hydrogène renouvelable pour la période 20232028 à 45 GW. Il va sans dire que le secteur de l'hydrogène nécessitera une quantité importante de matières premières critiques et donc de matériaux, par exemple pour les piles à hydrogène (piles à combustible), les électrolyseurs, la séparation, le stockage et le transport de l'hydrogène (et de ses dérivés).
Énergies renouvelables et hydrogène renouvelable
L’hydrogène moléculaire (H2) ou communément appelé « hydrogène » représente une source potentielle de réduction des gaz à effet de serre (GES), et de nombreux pays investissent en conséquence dans ce marché en pleine croissance. L'hydrogène représente environ 2 % du marché mondial de l'énergie [1] et environ 50 millions de tonnes par an d'H2 sont utilisées [2]. Pour réduire les GES, l'électrification demeure la principale priorité, et l'hydrogène vert ou renouvelable (RH2) joue un rôle complémentaire à l'électrification dans les secteurs de l'économie difficiles à électrifier. Néanmoins, ces deux secteurs seront essentiels pour atteindre la neutralité carbone d'ici 2050 [3-5].
La production mondiale d'hydrogène d'aujourd'hui est estimée à environ 94 millions de tonnes métriques par an (MTA), et elle pourrait atteindre 110 MTA et 240 MTA d'ici 2030 et 2040 respectivement, environ 50 % étant consommés par l'industrie et le reste par les secteurs des trans-
ports et de l'énergie. Selon l'Agence internationale pour les énergies renouvelables (IRENA) [5], l'offre globale d'hydrogène doit être multipliée par plus de cinq d'ici 2050, pour atteindre plus de 500 MTA ; S'il doit servir un plus large éventail d'usages pour décarboner les secteurs à forte intensité de carbone, les secteurs dits « sans regret ». Il est très clair qu'il y aura une adoption continue et croissante de RH2 dans les processus industriels. Dans un autre rapport récent publié par l'Hydrogen Council et McKinsey & Company (décembre 2023), ces derniers ont indiqué que plus de 1 400 projets d'hydrogène ont été annoncés en 2023, ce qui représente 7 % de la décision finale d'investissement (DFI ou « FID » en englais), ce qui équivaut à 570 milliards de dollars d'investissements avec 45 MTA d'hydrogène propre annoncés d'ici 2030 [6]. Pour atteindre la carboneutralité, on estime que 200 millions de tonnes métriques d'hydrogène propre sont nécessaires d'ici 2030.
Selon l'Agence internationale de l'énergie (AIE), 45 GW de nouvelles capacités d'énergie renouvelable pour RH2 seront construites d'ici la fin de 2028, ce qui ne représente que 7 % de ce que les promoteurs ont annoncé. Cependant, il convient de noter qu'une capacité d'énergie renouvelable de 510 GW en 2023 a été ajoutée à l'échelle mondiale (en hausse de 50 % par rapport à 2022), et dans le cadre de ces politiques actuelles et des tendances du marché, la capacité mondiale d'énergie renouvelable devrait être 2,5 à 3 fois supérieure d'ici 2030, ce qui n'est pas très éloigné de l'objectif de triplement de la COP28 des Émirats arabes unis [7]. Ici, l'objectif principal est d'agir et de mettre rapidement en œuvre les ambitions des gouvernements du monde entier en mesures concrètes afin que la trajectoire de 1,5 °C puisse être atteinte.
Production d'hydrogène
L'hydrogène peut être produit à partir de diverses méthodes, notamment le reformage du méthane à la vapeur (SMR – Steam Methane Reforming), l'électrolyse, la gazéification de la biomasse, etc. Chaque méthode implique des équipements et des matériaux complexes, par exemple, le SMR nécessite des reformeurs, des échangeurs de chaleur et des catalyseurs, tandis que l'électrolyse repose sur des électrolyseurs d'eau (un dispositif
qui convertit l'eau en hydrogène et en oxygène moléculaires) qui comprennent des membranes, des électrodes, des plaques bipolaires et d'autres sous-composants [8]. Pour produire du RH2, des électrolyseurs d'eau sont nécessaires s'ils sont alimentés par de l'électricité renouvelable. Cinq principaux types d'électrolyseurs sont soit sur le marché (NMT – niveau de maturité technologique élevé – niveau de maturité technologique), soit en cours de développement (TRL faible à moyen), classés comme électrolyseurs d'eau basse température (LT) et haute température (HT) (WE) [1]. Dans le cas de LT-WE, les électrolyseurs d'eau alcalins (AWE) et les électrolyseurs d'eau à membrane échangeuse de protons (PEMWE) dominent le marché, tandis que les technologies émergentes telles que les électrolyseurs d'eau à membrane échangeuse d'anions (AEMWE) sont en cours de développement et même commercialisées (par exemple, Enapter, Cipher Neutron, pour n'en citer que quelques-unes). Pour HT-WE, des cellules électrolytiques à oxyde solide (SOEC) et des cellules électrolytiques céramiques conductrices de protons (PCCEL) sont en cours de développement et même commercialisées. On s'attend également à ce que la SOEC joue un rôle important d'ici 2050.
Selon l'IRENA [5], la capacité totale installée d'électrolyseurs devrait atteindre 5 000 GW d'ici 2050, tandis que l'AIE prévoit une capacité de 3 670 GW [4,9]. Cela représente une augmentation significative par rapport aux capacités installées d'environ 0,6 à 1 GW en 2022 et d'environ 2 GW en 2023. Selon le scénario de zéro émission nette d'ici 2050 de l'AIE, la capacité de l'électrolyseur doit être multipliée par 6 000 d'ici 2050 [10]. D'autres rapports estiment que les installations d'électrolyseurs atteindront plus de 240 GW au cours des 6 prochaines années, AWE prenant le contrôle de PEMWE en termes de capacité [11].
Transport et livraison d'hydrogène
L'utilisation de l'hydrogène englobe diverses applications, telles que les moteurs à combustion, les piles à hydrogène et les processus chimiques. Chaque système d'exploitation nécessite des équipements et des matériaux spécialisés. Une infrastructure de transport efficace, fiable et rentable est vitale pour l'acheminement de l'hydrogène des sites de production aux utilisateurs finaux. Les composants clés comprennent les pipelines, les compresseurs et les stations de surpression, les vannes, les raccords et les mécanismes de sécurité qui utilisent de l'acier à haute résistance ou des matériaux composites avancés, compte tenu de leurs propriétés mécaniques, de leur résistance à la corrosion et de leur intégrité à long terme. L'approvisionnement en hydrogène nécessite des technologies de stockage robustes et peu coûteuses. Diverses méthodes de stockage, y compris le gaz comprimé, l'hydrogène liquide, les transporteurs d'hydrogène organique liquide (LOHC - Liquid Organic Hydrogen Carriers), l'ammoniac liquide (NH3), le méthanol (CH3OH) et le stockage à l'état solide (par exemple, les hydrures métalliques), nécessitent des équipements et des matériaux uniques [8].
Goulots d'étranglement actuels
À l'heure actuelle, il existe certains obstacles majeurs, tels que : (i) les coûts de production, de transport et de distribution ainsi que le développement des infrastructures ; (ii) l'élaboration et l'harmonisation des politiques et du cadre réglementaire entre les régions ; (iii) l'absence de structure de marché et d'acheteurs (incertitude de la demande) ; iv) le manque de soutien financier au début du déploiement ; (v) l'accès aux ressources naturelles ; et (vi) les questions d'environnement et de sécurité [8].
Matières premières critiques et stratégiques
La réussite de la mise en place d'une économie basée sur l'hydrogène repose fortement sur une compréhension approfondie des équipements et des matériaux utilisés dans les différentes facettes de la chaîne de valeur de l'hydrogène, englobant les systèmes de production, de stockage, de transport et d'utilisation. Des minéraux critiques et stratégiques (MCS) sont nécessaires pour le secteur de l'hydrogène, par exemple pour les piles à hydrogène, les électrolyseurs, la séparation, le stockage et le transport de l'hydrogène [8].
Les matières premières critiques dans le secteur de l'hydrogène comprennent le platine (Pt), l'iridium (Ir) et le ruthénium (Ru), connus sous le nom de métaux du groupe du platine (PGM), ainsi que les éléments de terres rares (RER) comme le néodyme (Nd) et le dysprosium (Dy). De plus, le nickel (Ni), le cobalt (Co), le zirconium (Zr) et le manganèse (Mn) sont essentiels pour certains types de technologies de production et de stockage de l'hydrogène. Ces matériaux jouent un rôle crucial dans l'avancement des technologies de l'hydrogène, mais sont soumis à des défis de la chaîne d'approvisionnement et à des considérations géopolitiques [8].
Le PEMWE contient principalement de l'Ir, du Pt et du Ti, et actuellement l'Ir est très cher (une augmentation d'environ 800 % depuis 2000) et rare. L’Ir est un sous-produit minier mineur des platinoïdes, principalement extrait en Afrique du Sud, au Zimbabwe et en Russie (l'iridium représente généralement jusqu'à 4 % de la teneur globale en platinoïdes du minerai) et son offre ne devrait pas dépasser le niveau actuel d'environ 7 à 9 tonnes par an. Par conséquent, des efforts visant à réduire considérablement et à recycler ces demandes de CRM seront nécessaires à mesure que le déploiement de PEMWE augmentera. Les piles à hydrogène du type PEM (PEMFC – Proton Exchange Membrane Fuel Cell), utilisées dans les véhicules à pile à combustible à hydrogène de tourisme et les trains à hydrogène), par exemple, reposent sur une combinaison d'électrodes, de membranes et d'un équilibre d’autres composants [8,9].
Dans le cas de l'AWE, il s'agit de la technologie la plus ancienne, la plus mature, la plus robuste et la plus disponible dans le commerce, qui a également des exigences en matière minérales, notamment Ni et Zr. Selon l'IRENA
2020, les AWE sont les plus rentables, les composants de cheminée représentant 45 % de la répartition des coûts et le reste de l'usine 55 % [5].
Pour les AEMWE, ils n'utilisent pas de matières premières critiques et stratégiques coûteux et rares, mais plutôt de l'acier et opèrent dans des environnements moins corrosifs et purs (ce qui signifie un équilibre plus simple entre l'usine et moins de systèmes de purification de l'eau).
À l'heure actuelle, l'efficacité et la durabilité ne sont pas comparables à celles de PEMWE et d'AWE, mais elles s'en rapprochent. Il s'agit d'une technologie d'électrolyseur à surveiller de très près.
Ce n'est peut-être pas beaucoup mentionné, mais les SOEC sont la technologie d'électrolyseur à surveiller car elle offre de meilleures efficacités, par exemple, 30 % plus élevées que les électrolyseurs à basse température (AWE, PEMWE et AEMWE) et ne nécessite pas de minéraux rares. On s'attend à ce que la réduction des coûts des SOEC en 2030 soit de 90 % par rapport aux alcalins (50 %) et aux PEM (70 %).
Dans l'ensemble, le développement et l'optimisation de technologies d'électrolyseurs qui minimisent les exigences en matière de minéraux critiques et stratégiques seront essentiels pour permettre la croissance du secteur de l'hydrogène, ainsi que pour réduire les impacts environnementaux – émissions de GES et empreinte hydrique – de l'approvisionnement en MCS nécessaire à la production et à l'utilisation d'hydrogène propre.
Recyclage en fin de vie
La mise en œuvre du recyclage en fin de vie des produits et d'une économie en boucle fermée doit être mise en œuvre comme solution potentielle pour remédier à la pénurie de matières premières critiques et stratégiques. Cependant, à court et moyen terme, cela peut ne pas être efficace en raison de la longue durée de vie des produits contenant des matériaux essentiels et de la nécessité de maintenir un inventaire des produits existants. Ainsi, la transition énergétique nécessitera l'utilisation de nouvelles matières premières, ce qui nécessitera une augmentation des activités minières. À long terme, cependant, on s'attend à ce que le matériau recyclé réduise le besoin d'approvisionnement primaire. Des minéraux comme le Ni et le Co pourraient réduire l'approvisionnement primaire de 10 % d'ici 2040 environ. Cela peut sembler peu, mais avec une demande matérielle toujours en croissance rapide, cela contribuerait à un montant substantiel [8].
Quel avenir pour l'hydrogène ?
Le déploiement de l'hydrogène décarboné est à envisager d'ici la fin de la décennie. Cependant, cela nécessite de lever un certain nombre de goulots d'étranglement et surtout il faut garder les pieds sur terre. La réalité est que RH2 est encore cher, et pour cette raison, RH2 devrait être déployé dans les zones où il a le plus grand potentiel de décarbo-
nation. Cela rendrait l'hydrogène idéal pour le transport lourd et l'industrie lourde. Il ne faut donc pas le « gaspiller » ! De plus, les voies de production d'hydrogène les plus rentables et les plus respectueuses du climat dépendraient des ressources naturelles des sites potentiels. L'intensité carbone de chaque chaîne de production pourrait être évaluée et considérée séparément à l'aide d'instruments tels que les garanties d'origine négociées sur les marchés environnementaux secondaires.
Pour atteindre nos objectifs de décarbonation d'ici 2050, nous devons donc nous concentrer sur les éléments suivants :
1. Une réduction significative de la consommation d'énergie.
2. L’utilisation de l’intelligence artificielle pour développer de nouveaux matériaux et optimiser les procédés de fabrication et de manufacture.
3. Promouvoir une économie circulaire là où cela a du sens.
4. « Sans regrets » pour les secteurs « difficiles à décarboner » ou « difficiles à électrifier », en particulier les industries énergivores comme l'acier, l'aluminerie, le ciment, le traitement des minerais et des produits chimiques, les engrais et les transports lourds.
5. Augmenter la production d'électricité pour répondre à la capacité de soutenir à la fois la filière hydrogène et le reste de la transition énergétique.
6. Développer la main-d'œuvre qualifiée dans le domaine de l'hydrogène.
7. Développer la chaîne d'approvisionnement en hydrogène et de nouvelles chaînes d'approvisionnement pour le commerce de RH2 et de ses dérivés, qui comprennent également les équipements et les services nécessaires à la production, au transport, au stockage et à la livraison de l'hydrogène aux utilisateurs finaux.
8. Le développement du secteur RH2 nécessitera d'importants investissements de la part du secteur privé.
Réflexions finales
À l'heure actuelle, les plus grands risques qui se profilent à l'horizon sont la concentration géographique des minéraux nécessaires à cette transition vers une énergie propre, en particulier dans le raffinage/transformation (par exemple en Chine). À l'heure actuelle, la Chine est le plus grand producteur de la plupart des matières premières critiques, par exemple les RER. Si l'industrie des électrolyseurs se développe selon les estimations de l'AIE et de l'IRENA, il y aura un décalage entre l'offre et la demande qui sera impossible à satisfaire. Ce secteur peut être soumis à des pénuries et à des flambées de prix en raison de la concurrence avec d'autres secteurs de technologies propres tels que les moteurs électriques, les batteries, le photovoltaïque, l'éolien,
etc., à moins que nous n'obtenions les résultats suivants :
1. Diminuer les charges de matériaux [en particulier Ir, Pt et Ti pour PEMWE, Zr et Ni pour AWE, et Sc (également La et Y) pour SOEC].
2. Améliorer la recyclabilité et la réutilisation des matériaux.
3. Développer et commercialiser des électrolyseurs basés sur des matériaux moins critiques, d'autres types de technologies, etc.
Il est également important de se rappeler que l'industrie de l'hydrogène n'est qu'une petite partie de la « transition énergétique verte », d'autres technologies d'énergie propre comme le solaire, l'éolien et les batteries devraient également connaître une croissance exponentielle de leur déploiement et exigeront leur part de matières premières critiques telles que le Ni, le Cu et le RER, limitant ainsi la part restante disponible pour le déploiement d'électrolyseurs. À cela s'ajoutent des flambées de prix dues à la concurrence et à la situation de l'offre et de la demande.
La compréhension de ces matériaux est non seulement cruciale pour comprendre leurs applications actuelles, mais aussi pour prévoir les besoins et les défis futurs, en particulier dans le cadre de l'objectif d'augmentation de la capacité d'électrolyseurs d'ici 2050. Il est important d'évaluer la dynamique de l'offre et de la demande de ces matières premières critiques et stratégiques, en fournissant une vue d'ensemble qui englobe à la fois l'état actuel et les projections futures. Grâce à cette approche, il est important de découvrir les risques potentiels liés à l'approvision-
nement et d'essayer de mieux comprendre les stratégies et les goulots d'étranglement potentiels pour les matériaux impliqués dans les technologies de l'hydrogène, en répondant à la fois aux besoins actuels et aux demandes futures ainsi qu'à l'offre.
Une compréhension approfondie des équipements, des matériaux, des composants et des sous-composants tout au long de la chaîne de valeur de l'hydrogène est indispensable pour faire progresser la mise en œuvre des technologies de l'hydrogène.
Références
1. FREE download – M. Chatenet, B.G. Pollet, et al. (2022). Water electrolysis: from textbook knowledge to the latest scientific strategies and industrial developments. Chemical Society Reviews, 51(11), 45834762. https://doi.org/10.1039/d0cs01079k
2. Hydrogen Insights 2023 – An update on the state of the global hydrogen economy, with a deep dive into North America, May 2023, Hydrogen Council and McKinsey & Company, https://hydrogencouncil.com/ wp-content/uploads/2023/05/Hydrogen-Insights-2023.pdf
3. Towards hydrogen definitions based on their emissions intensity, International Energy Agency (IEA), April 2023. https:// www.iea.org/reports/towards-hydrogen-definitions-based-on-their-emissions-intensity, C_2023_1087_1_EN_ACT_part1_v8.pdf
4. International Energy Agency (IEA), IEA (2022), Electrolysers, IEA, Paris https:// www.iea.org/reports/electrolysers, CC BY 4.0.
À propos de l’éditeur
Bruno G. Pollet est directeur de l'Institut de recherche sur l'hydrogène de l'Université du Québec à Trois-Rivières. Il est titulaire de deux chaires de recherche (CRSNG CRC et Innergex) sur la production d'hydrogène vert et renouvelable, avec un fort accent sur la prochaine génération d'électrolyseurs et les technologies de production d'hydrogène à faible teneur en carbone.
5. Green hydrogen cost reduction, Scaling up electrolysers to meet the 1.5oC climate goal, International Renewable Energy Agency (IRENA), December 2020, ISBN: 978-92-9260-295-6.
6. Hydrogen Insights 2023 – The state of the global hydrogen economy, with a deep dive into renewable hydrogen cost evolution, December 2023, Hydrogen Council and McKinsey & Company, https://hydrogencouncil.com/wp-content/uploads/2023/12/ Hydrogen-Insights-Dec-2023-Update.pdf
7. Renewables 2023, Analysis and forecast 2028, International Energy Agency (IEA), revised version January 2024, IEA, Paris, https://iea.blob.core.windows.net/assets/ 96d66a8b-d502-476b-ba94-54ffda84cf72/ Renewables_2023.pdf
8. Erik Eikeng, Ashkan Makshsoos, Bruno G. Pollet, Critical and Strategic Raw Materials for Electrolysers, Fuel Cells, Metal Hydrides and Hydrogen Separation Technologies, submitted in International Journal of Hydrogen Energy, January 2024.
9. FREE download – B.G. Pollet, I. Staffell, J.L. Shang (2012). Current Status of Hybrid, Battery and Fuel Cell Electric Vehicles: From Electrochemistry to Market Prospects, Electrochimica Acta, 84, 235-249, https://www.sciencedirect.com/science/ article/pii/S0013468612005671
10. International Energy Agency (IEA) (2022), Global Hydrogen Review 2022, IEA, Paris https://www.iea.org/reports/global-hydrogen-review-2022
11. International Energy Agency (IEA) (2023), Global Energy and Climate Model, Documentation – 2023, October 2023, IEA, Paris, https://iea.blob.core.windows. net/assets/ff3a195d-762d-4284-8bb5bd062d260cc5/GlobalEnergyandClimateModelDocumentation2023.pdf
12. Bruno Pollet, The Clean Energy Transition is Underway with Hydrogen and Critical Minerals, The Hill Times, 07 June 2023, https://www.hilltimes.com/ story/2023/06/07/the-clean-energy-transition-is-underway-with-hydrogen-and-critical-minerals/389155/
Electrolyse Alcaline, enjeux et perspectives
Par Armand GERING, Directeur Recherche, Innovation et expertise technique, Vice-Président John Cockerill Hydrogen
Marc NOUAILLE-DEGORCE, Responsable des activités de Recherche et innovation en France, John Cockerill Hydrogen
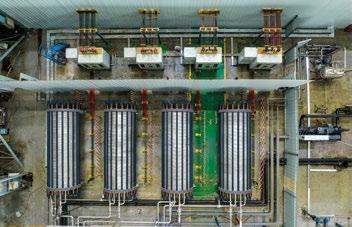
Alors que l’électrolyse de l’eau en milieu alcalin est une réaction connue depuis longtemps, les nouveaux défis à relever pousse l’industrie à aller plus loin dans la maitrise et l’optimisation de ce procédé.
L’électrolyse de l’eau a été découverte il y a plus de 200 ans, elle a progressivement évolué vers une maturité industrielle avec la technologie dite « alcaline » au XXe siècle pour satisfaire les besoins de l’industrie chimique. Les grandes innovations comme l’architecture bipolaire qui date de 1900, la mise sous pression de la chambre de réaction ou le zéro gap qui date des années 50 et 60 définissent la conception actuelle des électrolyseurs industriels.
Dans les années 1970, le monde universitaire se désintéressera progressivement de l’électrolyse alcaline pour s’investir dans la technologie PEM qui voit le jour avec les programmes Gemini, dès les années 60, puis Apollo. L’industrie, quant à elle, se détourne de la production d’hydrogène par électrolyse au profit du vaporeformage moins cher mais rejetant plus de carbone.
Aujourd’hui, l’aspect économique n’est plus le critère unique et la mise en évidence des enjeux environnementaux interpelle l’industrie qui cherche à s’approvisionner en hydrogène par des sources alternatives aux produits pétroliers. L’électrolyse de l’eau redevient une technologie de choix et le recul sur les grosses installations d’électrolyse industrielle passée donne à la technologie alcaline un avantage pour relever le défi.
En effet, les prévisions annoncent une explosion des besoins en installation d’électrolyse avec des chiffres qui donnent le vertige : les organismes tels que l’IEA , l’IRENA
, BNEF ou encore Hydrogen Council estiment que les besoins en hydrogène à faible teneur en carbone seront entre 450 et 550 Mt en 2050 alors que cette production était quasi nulle en 2020.
Ce déploiement guidé par des choix écologiques est appuyé par des politiques publiques d’encouragement plus ou moins massives en fonction des pays. On peut citer le cadre US avec l’IRA ou le programme IPCEI en Europe.
Ces scénarii indiquent également que l’hydrogène produit sera essentiellement à destination des industries chimiques, ammoniaques, engrais, sidérurgie ou raffinerie.
Un électrolyseur est un système électrochimique fonctionnant dans un environnement hautement basique, les matériaux utilisés et les traitements de surfaces demandés sont critiques pour sa stabilité et sa durabilité.
Un électrolyseur se présente comme un empilement de cellules électrochimique, chacune d’elles est constituée des électrodes, de la membrane ainsi que de plaques de circulations et d’étanchéité des fluides. Chacune de ses pièces à sa fonction, mais aussi ses contraintes et ses problématiques. On alimente cet empilement avec de l’électrolyte qui va ressortir chargé avec l’hydrogène ou l’oxygène issu de la séparation des molécules d’eau dans des conduites distinctes.
Si les électrodes sont dédiées à la réaction électrochimique en tant que telle, les autres composants assurent la meilleure configuration possible pour cette réaction : ils vont ainsi optimiser les contacts et la continuité électrique pour réduire les pertes de résistivité, distribuer correctement le flux d’électrolyte, permettre le refroidissement du système et enfin contenir la pression des fluides dans un environnement multi contraint : mécaniquement d’abord, avec des phénomènes de dilatation, chimiquement avec un environnement agressif, et aussi thermiquement et électriquement.
À la sortie de l’électrolyseur, les fluides sont amenés dans le process de séparation qui récupère les gaz et retourne l’électrolyte vers les cellules. Tous les composants impliqués dans ce procédé, tuyauterie, pompe, ballon, etc., partagent un grand nombre de contraintes avec l’électrolyseur.
Ces contraintes pèsent notamment sur les caractéris-
tiques des matériaux, les spécifications de fabrication et d’assemblage ou le coût du système.
Les matériaux doivent contenir l’électrolyte et le gaz sous pression tout en restant passifs pour prévenir l’introduction de pollution dans le système. Il y a plusieurs défis simultanés à relever pour les matériaux que nous utilisons : l’environnement basique, avec l’électrolyte chauffé à plusieurs dizaines de degrés, et diphasique avec la présence d’hydrogène et d’oxygène, dissous ou gazeux. Si l’agressivité du milieu est, en soi, une contrainte majeure, l’ajout des gaz, notamment de l’hydrogène, apporte des exigences supplémentaires sur les matériaux qui peuvent être affectés dans leur propriété et leur durabilité à cause de phénomènes de perméation potentiels. Le choix des traitements appliqués à nos matériaux est critique pour satisfaire aux impératifs de fonctionnement. Côté fabrication, nous empilons des centaines de couches de composants dont les épaisseurs sont de l’ordre de la centaine de microns sur des surfaces de plusieurs mètres carrés qui sont ensuite mis en pression. Les enjeux sur la qualité de ces éléments, choix des matériaux, usinage et traitement de surface sont importants avec des niveaux de tolérance critiques afin de satisfaire les performances du système.
Enfin, le CAPEX d’un électrolyseur est un des facteurs qui contribue au coût de l’hydrogène qu’il produit. Pour réduire le cout de production, les grands acteurs du marché travaillent à optimiser la conception et la fabrication des équipements. Un des leviers de réduction important du coût est la taille des cellules et des stacks. La production d’électrolyseurs de grandes dimensions, permet de réduire de manière importante la consommation de matériaux. Ce constat nous pousse donc à envisager des systèmes plus volumineux avec plus de cellules et de plus grands diamètres afin d’apporter un hydrogène à faible teneur en carbone compétitif.
L’ancienneté des électrolyseurs alcalins industriels est certes un atout, mais si le besoin de répondre aux nouveaux enjeux leur confère une jeunesse et une légitimité nouvelle, il y a encore des contraintes et des défis. L’environnement électrochimique, la qualité de fabrication, la taille des systèmes industriels sont autant de sujets qui nécessitent des efforts de R&D importants. De plus, la reprise des activités de R&D avec des connaissances scientifiques considérablement enrichies depuis les derniers développements majeurs laisse présager de belles perspectives pour l'avenir.
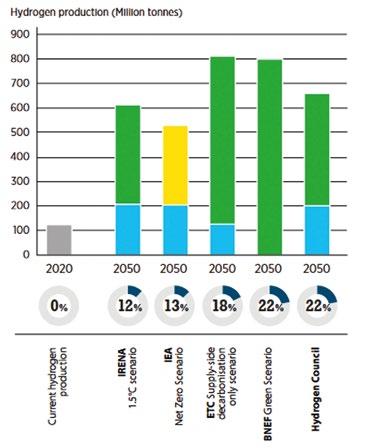
Références
1. Architecture d’électrolyseur qui empile des cellules électrochimiques et dont la conduction électrique en série est réalisée par les cloisons de séparation entre les cellules.
2. Conception de ceullues qui réduit la distance entre les électrodes pour améliorer la performance.
3. Proton Exchange Membrane, désigne une technologie d’électrolyse ou les électrodes sont séparées par une membrane qui sert d’électrolyte avec une réaction électrochimique qui voit un échange de proton H+, la ou classiquement l’électrolyse alcaline voit un échange d’OH-.
4. International Energy Agency
5. International Renewable Energy Agency
6. BloombergNEF
7. “Geopolitics of the Energy Transformation : The hydrogen factor” , IRENA , 2022
8. « Inflation Reduction Act » Réglementation qui prévoit que pour chaque kg de H2 vert produit, un crédit d'impôt de 3 USD est accordé.
9 'Important Project of Common European Interest', c’est un projet européen dans une chaîne de valeur stratégique clé qui consiste en plusieurs projets d'entreprises de différents États membres de l'UE. Un IPCEI contribue à des objectifs européens stratégiques tels que la croissance, l'emploi et la compétitivité de l'industrie et de l'économie de l'Union européenne, qui sont financés par des aides d'État.
Dossier du mois
Revêtement en environnement sévère : le cas de la pile à combustible HT-PEMFC
Par Marjorie Cavarroc, Material & Process Senior Expert - Plasmas, multifunctional coatings & fuel cells, Safran Tech
Une pile à combustible est un dispositif électrochimique avancé, capable de convertir efficacement l'énergie chimique liée à l’hydrogène. Pour cela, l’hydrogène introduit (sous forme liquide ou gaz) est oxydé sur une électrode (anode) tandis qu’une réaction de réduction d'un oxydant tel l'oxygène de l'air à lieu sur l'autre électrode (cathode). Les deux électrodes doivent alors être séparées par un milieu étanche aux gaz et conducteur ionique pur. Dans le cas des piles PEMFC (Proton Exchange Membrane Fuel Cells), il s’agit d’une membrane échangeuse de protons. Ce dispositif permet donc de produire de l’électricité et de la chaleur avec un rendement supérieur à une combustion directe.
Dans l’aéronautique, le choix des piles PEMFC dites hautes température (HT-PEMFC), est dicté notamment par des considérations d’encombrement du système pile, et d’intégration thermique à l’aéronef. L’un des principaux composants du cœur de la pile est la membrane échangeuse de protons. Par exemple, une membrane polymère acide/base en polybenzimidazole (PBI) dopée avec de l’acide orthophosphorique H3PO4 (comme conducteur protonique), présente de bonnes performances électrochimiques autour de 100°C. Élever la température de fonctionnement de ces systèmes jusqu’à 200°C, aura pour avantage d’augmenter à la fois la cinétique de diffusion des protons à travers l’électrolyte et le transfert de charges aux électrodes. En particulier, la réaction de réduction de l’oxygène (Oxygen Reduction Reaction, ORR) sera accélérée, améliorant ainsi les performances de la pile. Pour des températures supérieures à 140°C et pour des gaz contenant du monoxyde de carbone CO, l’adsorption du
CO sera aussi bénéfiquement impactée. L’utilisation de gaz issus de systèmes de reformage d’hydrocarbures est alors possible. Ce type de système combiné à l’utilisation de nouvelles plaques bipolaires métalliques destinées à multiplier le nombre de cellules unitaires par empilement, permet alors d’envisager des systèmes de forte puissance avec des rendements de conversion élevés.
Cependant, la présence d’acide orthophosphorique, au contact des plaques métalliques, à des températures comprises entre 100 et 200°C, engendre des phénomènes de corrosion catastrophiques, qui obligent aujourd’hui à des choix de matériaux défavorables en terme de masse. Différentes études, réalisées dans le cadre de tests en pile 5 cellules, ou d’essais de corrosion accélérés, ont montré que les solutions de revêtements disponibles commercialement ne répondaient au besoin spécifique des piles HT-PEMFC : résistance à la corrosion et conductivité électrique élevée.
Une première étude, menée sur des stacks de 5 cellules, sur banc test. Le tableau ci-dessous résume les résultats obtenus lors du test en pile pour ces 7 revêtements, ainsi que les valeurs liées aux références lors de tests équivalents :
L’étude des plaques après essais montre notamment une attaque par piqûre de corrosion, sauf dans le cas desDLC#2 et DLC#3, qui peut être directement liée à la microstructure du dépôt colonnaire, typique des méthodes PVD arc ou magnétron. Les DLC, élaborés par PECVD présentent des piqûres aux défauts pré-existants dans la couche.

Tableau 1 : Durée d’essai et taux de dégradation moyen des différents revêtements commerciaux testés et des références
Figure 1 : Évolution des échantillons de référence (Inox 316L, Inconel 625 et Inconel 625 revêtu or PVD magnétron) et des revêtements lors de l’immersion dans une solution d’acide orthophosphorique à 85% molaire à 160°C
Dossier du mois
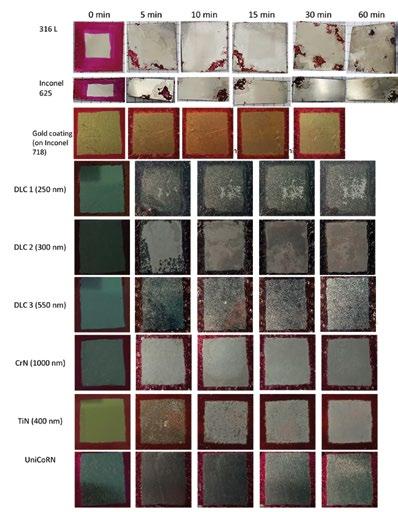
Une seconde étude a été réalisée à l’aide d’essais de corrosion accélérés, par trempage des échantillons à tester dans une solution concentrée (85% molaire) d’acide orthophosphorique à une température comprise entre 120 et 160°C. Cette étude a permis de comparer des revêtements commerciaux, aux substrats nus, à la solution de référence (un dépôt d’or), et à un revêtement en cours de développement (UniCoRN). Les résultats de cette étude sont synthétisés dans la figure 1, qui montre l’évolution de chaque revêtement considéré à différents temps d’exposition à l’acide. Là encore, les revêtements commerciaux ne présentent pas une tenue à la corrosion suffisante pour l’environnement sévère du cœur de pile à combustible. Seules les solutions Or et UniCoRN résistent suffisamment à la corrosion pour envisager leur usage dans ce type de pile à combustible.
Les mesures d’intensité de corrosion du revêtement UniCoRN réalisées en milieu acide orthophosphorique à différentes concentrations (0.1, 0.5 et 1 mol.L-1) montrent que l’intensité de corrosion du revêtement est plus faible que celle du substrat nu pour des concentrations en acide à partir de 0,5 mol.L-1, ce qui indique une excellente tenue à la corrosion comparé à l’Inox 316L, et confirme les observations réalisées précédemment.
Pour compléter l’étude, la conductivité électrique d’un revêtement UniCoRN de 500 nm a été évaluée par sonde 4 pointes en
fonction de la température et dans différentes atmosphères. On constate que la conductivité du revêtement ne dépend ni de la température, ni de l’atmosphère, et qu’elle est au moins égale, voire supérieure, à celle d’un revêtement d’or d’épaisseur équivalente.
Les tests suivants ont permis de montrer qu’il était possible de revêtir des plaques bipolaires de piles à combustible de différentes tailles de façon robuste et répétable. Les tests en piles HT-PEMFC sur banc sont actuellement en cours.
Cette étude tend à montrer que la maitrise de la composition et de la qualité du dépôt (homogénéité, densité, absence de défaut) est un élément clef de réussite pour la protection en environnement sévère. La technologie HiPIMS (High Power Impulse Magnetron Sputtering), utilisée pour le dépôt du revêtement UniCoRN, contribue grandement aux propriétés à la fois de résistance à la corrosion et de conductivité électrique de ce revêtement.
L’auteur souhaite remercier A. Poulon, F. Mauvy, ainsi que les différent(e)s étudiant(s), qui ont contribué à ce projet, ainsi que l’AID (Agence d’Innovation de Défense) pour son soutien financier à une partie de cette étude.
Traitements de surface : un outil indispensable pour la réussite des technologies de l'hydrogène
Par Manuel Bianco
Materials expert. PhD in Energy. R&D project manager, Symbio
« L'industrie des piles à combustible a besoin de la précision de l'aérospatiale et des coûts de l'automobile. »
C'est par cette phrase que j'ai introduit les enjeux technologiques de la démocratisation de la mobilité à hydrogène lors de la table ronde du 48ème congrès de l'A3TS à Nantes. Deux ans plus tard, j'ai eu le plaisir d'entendre plusieurs acteurs du domaine hydrogène reprendre cette phrase, mais dans le monde du traitement de surface, on peut faire plus et plus vite pour relever les défis de la décarbonisation par l'hydrogène.Il a tout le potentiel pour jouer un rôle majeur dans la décarbonisation des transports et le stockage d'énergie : grâce à sa densité énergétique élevée, il permet l'électrification de véhicules de transport lourds dont l'autonomie serait actuellement limitée par les seules batteries lithium-ion. Parallèlement, la transformation de l'électricité en hydrogène permettrait de compenser l'irrégularité inhérente à la production d'électricité à partir de sources renouvelables.
Pour convertir l'hydrogène en électricité, on utilise une pile à combustible, et pour le processus inverse, on utilise un électrolyseur. Les termes "pile à combustible" et "électrolyseur" sont génériques et couvrent un large éventail de technologies qui, tout en reposant sur les mêmes
principes physiques et chimiques, diffèrent par leurs paramètres de fonctionnement et les matériaux utilisés. En fonction des conditions de fonctionnement, les exigences en matière de matériaux changent, mais une chose est sûre : les traitements de surface sont un élément indispensable au succès des technologies de l'hydrogène !
La pile à combustible PEM (proton exchange membrane) est la technologie la plus produite et la plus utilisée dans les transports (que l'on trouve par exemple dans la Toyota Mirai). Les matériaux à l'intérieur doivent résister à des températures de 80-100°C, à un environnement acide (PH=3) et oxydant, ainsi qu'un chargement mécanique complex. Dans ces conditions, un revêtement mince ou un traitement de surface est essentiel pour permettre aux composants métalliques de durer des dizaines de milliers d'heures. Prenons un exemple concret : la plaque bipolaire. Il s'agit d'un composant faisant partie du cœur de la pile et qui sert à soutenir mécaniquement les PEM, séparer/ distribuer les gaz (hydrogène et air), contenir le circuit de refroidissement et conduire l’électricité. La solution la plus adoptée par les constructeurs de piles est à base de tôles d'acier inoxydables embouties recouvertes d'un revêtement PVD. Aujourd'hui plusieurs revêtements sont
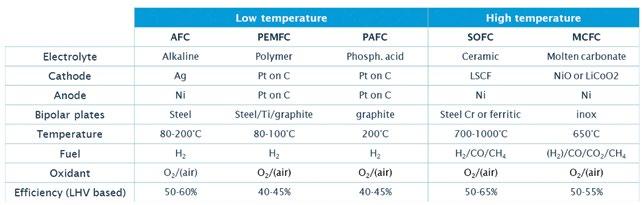
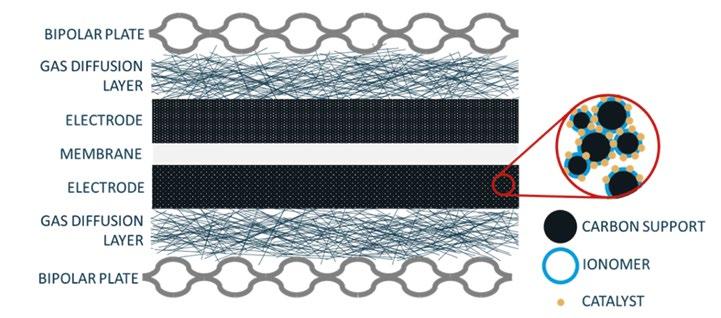
plate. In the electrode there is a focus on the structure.
considérés comme les carbure de chrome ou les double revêtement Titane/carbone pour répondre au besoin de tenue à la corrosion tout en conservant une très bonne conductivité électrique. L'Agence internationale de l'énergie (IAE) estime que d'ici 2030, 400 000 camions seront équipés de piles PEM. Si l'on considère qu'il s'agit de systèmes de 300 kW et que chaque système contiendra environ 400 plaques bipolaires, un marché de 100 à 150 millions de ces composants représente une opportunité majeure pour l'industrie du traitement de surface. Si l'on ajoute les volumes provenant des véhicules utilitaires et des électrolyseurs, le nombre augmente encore de plusieurs dizaines de millions.
Le contrôle du dépôt du catalyseur est une autre amélioration importante que les technologies de traitement de surface peuvent apporter au domaine des piles à combustible PEM. Pour simplifier, la technologie PEM nécessite des catalyseurs coûteux à base de platine implantés sur un substrat à base de carbone ; la possibilité de ne déposer que la quantité nécessaire de catalyseur sur la surface apporterait des avantages économiques indéniables. En même temps, il est possible de tester de nouveaux matériaux moins coûteux : en bref, les piles à combustible sont également un terrain de jeu très intéressant pour les traitements de surface.
La résistance à la corrosion est un autre défi important pour les systèmes qui doivent garantir une durée de vie d'au moins 15 000 heures. Le contact entre les composants en acier et en aluminium en présence de milieux humides peut entraîner une corrosion galvanique. Ce type de phénomène est dangereux et doit être contrôlé pour éviter les endommagements prématurés mais aussi parce que
les produits de corrosion risquent de polluer les fluides qui alimentent la pile à combustible. Là encore, les traitements de surface sont des solutions recherchées pour atteindre le service life souhaité.
Enfin, tous les éléments qui composent l'équilibre de l'installation nécessitent des protections diverses : renforcement des propriétés mécaniques, isolation électrique ou tenue à l’environnement automobile au sens large. Par exemple le système de pile à combustible doit contenir des éléments de conductions des hautes tensions et hauts courants de manières sécurisée et fiable en recourant à des traitements particuliers.
La passivation, la nitruration, les revêtements sous vide et l’électroplacage sont des technologies régulièrement adoptées pour les composants utilisés dans les systèmes de piles à combustible.
Ces piles à combustible fonctionnent grâce aux choix des bons matériaux. Concilier durabilité et performance à un coût acceptable pour le marché est un défi que l'industrie de l'hydrogène ne peut relever qu'avec l'aide des traitements de surface.
Remerciements à Mathieu Hautier pour son aide dans la relecture de l'article.
De Yokohama (Japon), à Paris (France)
Médaille IFHTSE pour le Professeur Michel Jeandin.
N’ayant pu être présent à Yokohama lors de la remise de la médaille IFHTSE (International Federation for Heat Treatment and Surface Engineering), dont l’A3TS est membre lors de son 28ème congrès, ce fut un honneur et un plaisir pour les membres du conseil d’administration de recevoir lors du dernier conseil Monsieur le Professeur Michel Jeandin afin de lui remettre en main propre la médaille IFHSTE.
La médaille lui a été décernée en « re connaissance de sa contribution aux sciences des matériaux et à la diffu sion des connaissances, en particulier dans les technologies de modification de surface telles que le développement de la technologie Cold Spray et les revêtements de surface de nouvelle génération ».
Après un bref résumé de sa carrière de notre Présidente Veronique Vitry, le professeur Jeandin a su encore une fois nous faire part de sa passion pour les sciences et aura su nous émouvoir lors de ses remerciements durant ce délicieux moment (y compris pour le palais) passé ensemble.
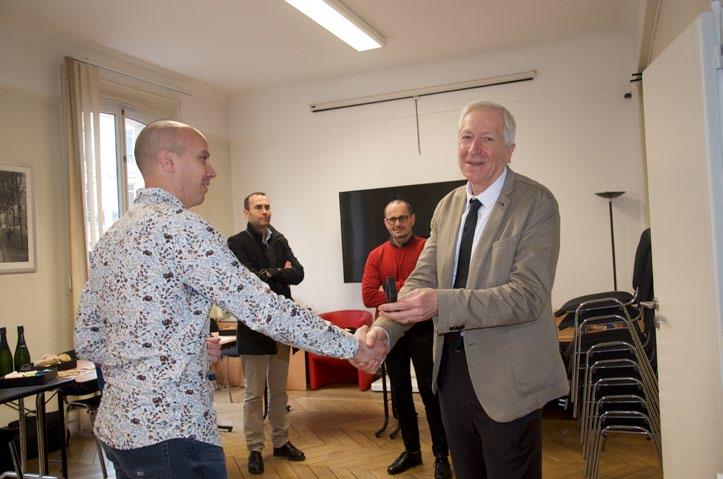
Des remerciements particuliers sont allés à M Chandra d’une part, et d’autre part à MM Jacquot, Rossignol, Bruchet pour les liens professionnels forts entre leurs entreprises respectives, notre association et les activités du Professeur Michel Jeandin.
Au-dessus : Christophe Stocky remettant la médaille de l'IFHTSE à Michel Jeandin à l'A3TS le 8 février 2024
A droite : Remise de la médaille l'IFHTSE par XX aux bons soins de Christophe Stocky pour remise à Michel Jeandin xxxx
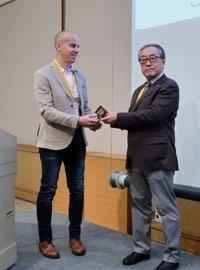
Ils nous ont quitté
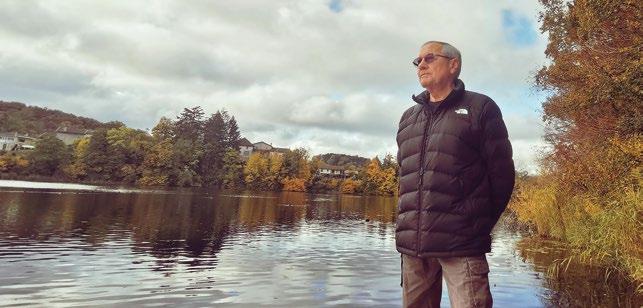
James Mansion est décédé à la suite d’une fulgurante maladie le 24 janvier 2024.
Il a été enterré à la Verpillière, en même temps que son épouse Denise qui l’a précédé de quelques jours.
James Mansion est né à Nîmes, d’où son petit accent chantant. Il a passé son BTS de Traitement Thermique et a commencé sa carrière professionnelle au CETIM de Saint Etienne, dirigé à l’époque par M. Sayettat.
James a beaucoup travaillé sur les huiles de trempe et, avec son collègue Burnicon, a édité un livre sur ce sujet. Il a rejoint le Groupe Thierry Dimier (PDG M. Alain Seutet) et fut chargé de la qualité à l’Usine de la Chauvetière (Saint Etienne). En 1984, il a participé au projet d’usine que Thierry Dimier envisageait à Thiers. Le site de La Monnerie fut choisi et James Mansion en prit la Direction. Après quelques années de démarrage difficile, James Mansion, à force d’opiniâtreté, réussit à mener cette usine vers le succès. Rapidement, elle fut le fleuron de Thierry Dimier, devenu HIT puis Bodycote.
Les projets de James Mansion étaient importants. Il a réalisé une deuxième usine à Bourges (Le Subdray) puis le transfert de COUTHERM dans un vaste site très fonctionnel à la ZI de Cotte, toujours à la Monnerie.
Pour terminer sa carrière, James Mansion a organisé le nouveau Siège Social de Bodycote à Saint Priest (69).
James Mansion était un homme droit, performant plein d’idées qu’il réalisait calmement. D’un contact agréable, il était bon de travailler avec lui, sûr de son dévouement. A la retraite, il s’est retiré à la Verpillière où il eut, avec son épouse, de nombreuses activités.
Son décès brutal a beaucoup touché ces anciens collègues et tous sont fort peinés et ne l’oublieront pas.
La vie des entreprises
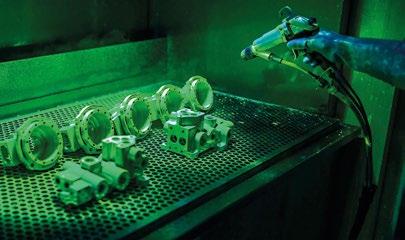
Le fabricant de systèmes de conditionnement d’air et de systèmes de commandes de vol et trains d'atterrissage, Liebherr Aerospace acquiert une nouvelle usine : Sibi, société qui fabrique des pièces chaudronnées et soudées pour avions sur ses deux sites de Montauban et Toulouse. Liebherr Aerospace voit ses effectifs portés à 1700. Cette acquisition permettra d’augmenter les capacités de production pour suivre la montée en cadence des avionneurs. En parallèle, le groupe va augmenter la surface de son usine de Campsas ou sera transférée la production des échangeurs de chaleur réalisée aujourd’hui à Toulouse.
Liebherr Aerospace réalise une seconde acquisition se renforce dans le traitement de surface en faisant l’acquisition de GIT Galvanoplastie Industrielle Toulousaine (Cugnaux- Haute Garonne) spécialisée dans les traitements de surface et la peinture de pièces aéronautiques en alliages d’aluminium. GIT (80 salariés, 8 M€ CA) a développé des procédés de traitement de surface par oxydation électrochimique sans utiliser le Chrome hexavalent. GIT, qui travaillait à 50% pour Liebherr Aerospace, devient “Liebherr-Aerospace Coatings” qui continuera à fournir les clients de GIT. Cette intégration dans Liebherr Aerospace va permettre de poursuivre une politique d’investissement dans les capacités de production pour répondre aux besoins de la filière en solutions de revêtements de finition respectueux de l'environnement.
Bontaz, équipementier automobile basé dans la vallée de l’Arve, reçoit un soutien par le plan France Relance 2030 pour ouvrir une diversification vers la mobilité Hydrogène en développant 3 familles de composants pour les piles à combustible, dont des boucles de refroidissement. 55
millions d'investissements seront investis par le groupe BONTAZ.
L’équipementier Aresia qui produit des pièces (pylônes, dispositifs d’emport et de largage) pour l’aviation de défense (Rafale, Mirage, Gripen, AlphaJet,...) va agrandir ses installations de Valenton (Val de Marne). L’usine de Valenton dispose d’installations pour l’usinage, la fabrication, la peinture et la maintenance.
Le groupe Safran a annoncé la création d’une nouvelle usine pour la production d’aubages de turbine pour les moteurs civil LEAP et militaire M88, TP400. Cette usine sera implantée à Rennes, représente un investissement de 80 M€ et offrira une capacité de production supplémentaire que l’usine de Gennevilliers ne permet pas d’atteindre, faute de place. Cette usine produira dans le futur des composants du moteur Rise appelé à remplacer les moteurs LEAP. cette usine sera une vitrine technologique “4.0” dotée des technologies digitales à toutes les étapes de la fabrication. Entrée en service en 2027.
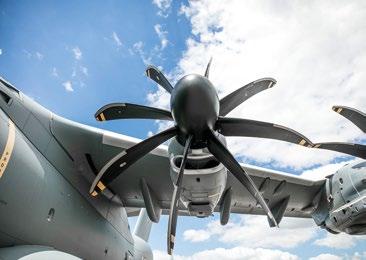
A St Etienne, le groupe HEF est dans la phase de démarrage de la production de plaques bipolaires destinées aux producteurs de piles à combustible. Ces plaques, produites selon une technologie développée par HEF, repose notamment sur une nouvelle technique de dépôt pour traiter la surface des plaques. Cette technologie permettra de réduire les coûts tout en maintenant un haut niveau de performance.
Aubert et Duval investit 75 millions € dans son usine
de Pamiers (Ariège). A&D va investir une presse à forger de 6000 t qui permettra de fabriquer des pièces résistantes aux hautes températures pour les moteurs d’avion - plus économes en carburant - du futur. La nouvelle presse permettra de forger lé métal avec la technologie “very hot die” qui consiste à chauffer l’outillage en permanence pour éviter le choc thermique sur la pièce. L’IA sera introduite avec le support du CEA dans le contrôle automatisé non destructif des pièces. L’atelier de traitement de surface sera reconstruit après l’incendie de 2021. L’usine produit aux ⅔ pour l'aéronautique et pour ⅓ pour les turbines à gaz.
ZNCI IDF investit massivement pour réinventer le contrôle des pièces de moteur d'avion. Ce sous-traitant du secteur installé à Sartrouville (Yvelines) et qui a pour client notamment des sociétés du groupe SAFRAN entend devenir un fournisseur de référence dans le contrôle non destructif de pièces aéronautiques. Ces contrôles sont réalisés par technologie ultrason ou champ magnétique. Il vient d'acquérir une nouvelle machine pour 1,5 million d'euros qui permettra de faire du contrôle multi-éléments et aura une productivité très supérieure aux équipements actuels.
L'avion hybride d'Aura Aero séduit une Amérique en mal d'appareils régionaux La compagnie américaine JSX vient de signer une lettre d'intention d'achat de 50 exemplaires, et une option sur 100 autres, du futur avion régional à motorisation hybride du jeune constructeur toulousain. Dénommé ERA, cet avion sera équipé de huit moteurs électriques à hélice alimentés par des batteries et un générateur électrique fonctionnant au kérosène. Cette motorisation hybride diminuera les rejets de gaz carbonique de 80 % sur les trajets de moins de 400 kilomètres. L'avion volera à une
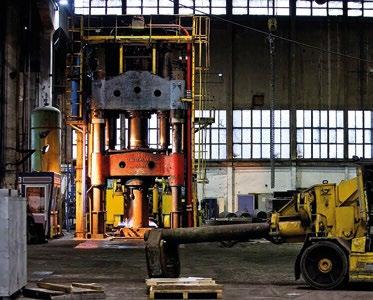
vitesse de croisière de 550 km/heure et pourra parcourir 1600 kilomètres.
Avion bas-Carbone. Le gouvernement confirme son soutien à la filière aéronautique avec une nouvelle enveloppe de 300 millions d'euros par an sur la période 2024-2027, destinée à financer des recherches pour le successeur de l’A320 dans le cadre du CORAC, qui regroupe AIRBUS et des acteurs de la filière aéronautique. Une seconde enveloppe de 200 millions d’euros sera destinée à financer dans le cadre de France 2030 la recherche de carburants de substitution durables.
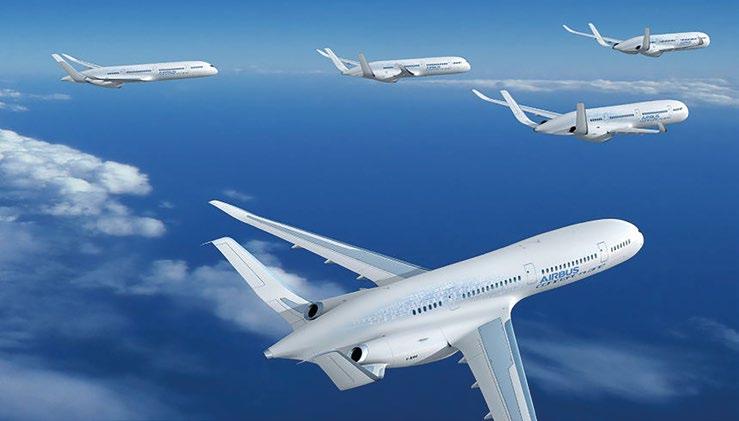
Retrouvez toutes les actualités sur www.a3ts.org
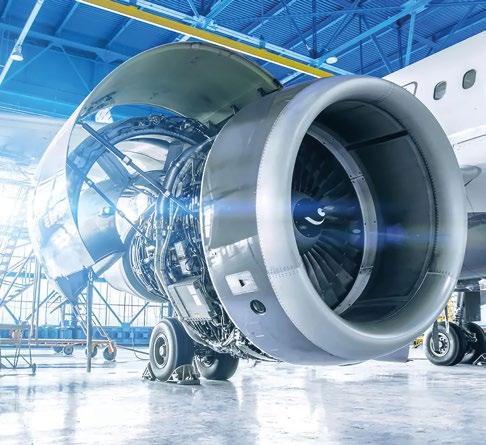
16 et 17 octobre 2024
La Maison de la Mécanique, Courbevoie (92)
Hydrogène : défis technologiques dans les matériaux métalliques
L’appel à conférences est ouvert !
Enseignants-chercheurs, industriels du monde de l’énergie, de l’aéronautique, de l’automobile, du traitement de surface, experts judiciaires, vous êtes invités à déposer votre proposition de conférence en ligne jusqu’au 15 juin 2024
Quels traitements pour répondre aux défis des matériaux posés par le développement de la filière hydrogène ?
Les risques d’endommagement des matériaux métalliques par l’hydrogène et les solutions, matériaux, contrôle et traitements seront au coeur des discussions.
Plus d’informations : www.a3ts.org/evenements ou scannez le QR code
Jeudi 19 septembre 2024
Hôtel Diana, Molsheim (67)
Journée d'étude A3TS/VOM : les traitements de surface dans l'aéronautique
Cette journée, organisée en collaboration avec la VOM-Promosurf, mettra en lumière les projets de recherche français et belges. Elle se clôturera par des visites de l’IRT M2P de Duppigheim.
Plus d’informations : www.a3ts.org/evenements
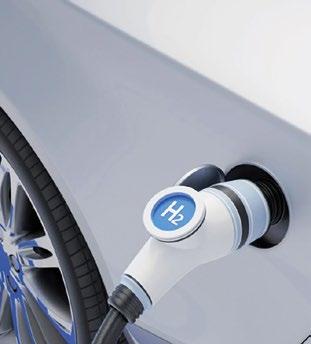
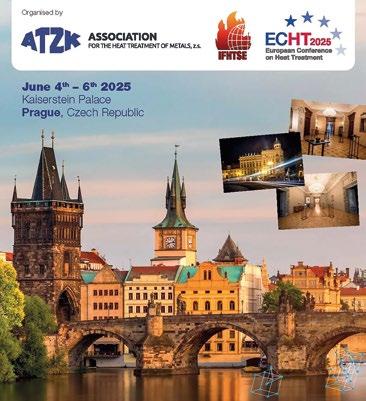
Du 4 au 6 juin 2025 Prague, Tchéquie
ECHT 2025 & 5th IFHTSE conference on HTSE in automotive and transportation applications
Plus d’informations à venir sur : http://www.atzk-echt2025.com/
2 et 3 juillet 2025
Palais des Expositions et des Congrès, Dijon
51è Congrès et Salon A3TS
Conférence internationale sur les traitements thermiques et revêtements de surface dans le secteur des énergies bas carbone.
Plus d’informations : www.a3ts.org/evenements
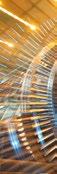
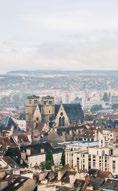
2 & 3 July 2025
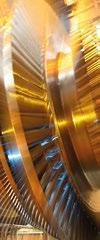
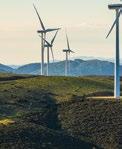
Heat Treatment and Surface Engineering for Low-Carbon Energy Sector
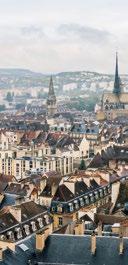
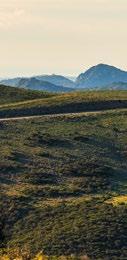
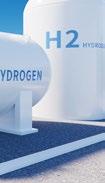
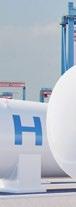
janvier 2025, lieu à venir
5èmes rencontres Traitements et parachèvements de pièces issues de fabrication additive
Ces journées qui réunissent industriels et chercheurs autour des problématiques de finition des pièces de fabrication additive (résistance à la fatigue et propriétés mécaniques, porosité, aspect de surface, rugosité, aptitude au revêtement,...) sont l’occasion de confronter les problématiques et les stratégies de secteurs industriels différenciées (Aéronautique, Spatial, Défense, Ferroviaire, Mécanique-Outillage, Médical,...).
Elles offrent l'occasion d’approcher les laboratoires de recherche qui exposent leurs résultats, fournisseurs de solution et industriels partageant leurs retours d'expérience.
Plus d’informations : www.a3ts.org/evenements
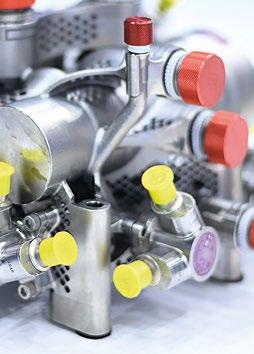
Janvier 2025
TRAITEMENTS ET PARACHÈVEMENTS
Pièces issues de fabrication additive
FÉDÉRER LES COMPÉTENCES ET DIFFUSER LES CONNAISSANCES
L’A3TS rassemble des ingénieurs, académiques et praticiens des traitements thermiques et traitements de surface répartis dans les secteurs aéronautique, sidérurgie, automobile, médical, industries mécaniques, université, écoles d’ingénieurs, enseignement …
Notre objectif est de favoriser les échanges et les collaborations entre les adhérents lors de nos conférences & débats : congrès et salon annuel, et journées thématiques nationales et internationales.
L’A3TS, c’est aussi un centre de formation certifié QUALIOPI au titre de ses actions de formation, mettant à disposition ses experts scientifiques et techniques les plus pointus.
Devenez adhérent et bénéficiez de :
• Accès des vidéos en replay des conférences des Congrès
• Actualités scientifiques et technologiques
• Intégez l'annuaire, vous donnant accès au réseau de notre communauté
• Prix réduits sur nos évènements
• Remise de 5 à 10% sur les formations
J’ADHÈRE À L’A3TS
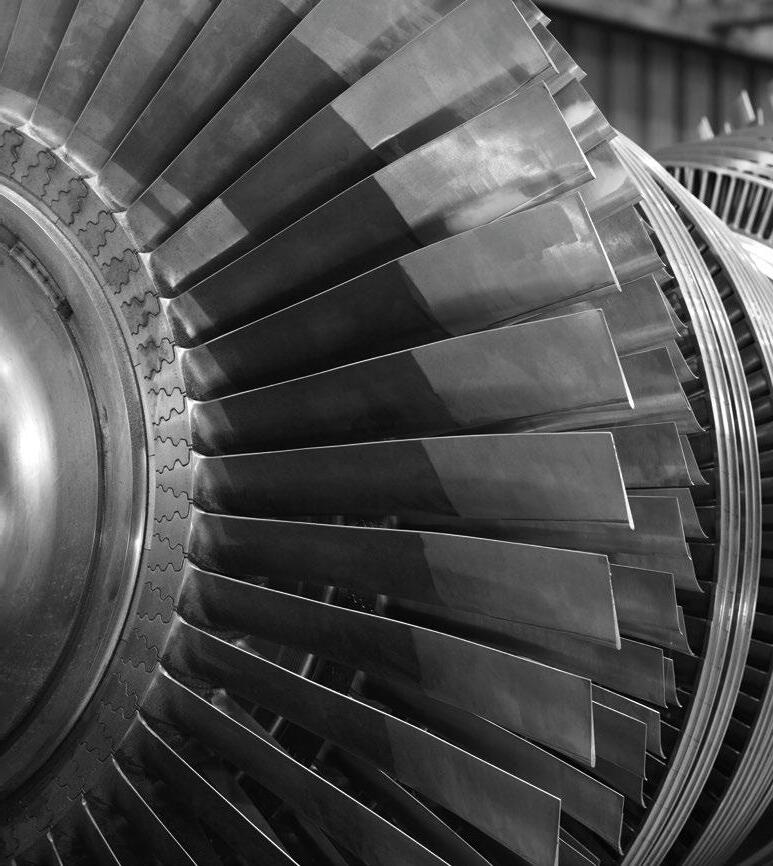
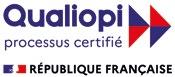
Plus d’information, suivez-nous ! www.A3TS.org

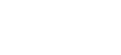
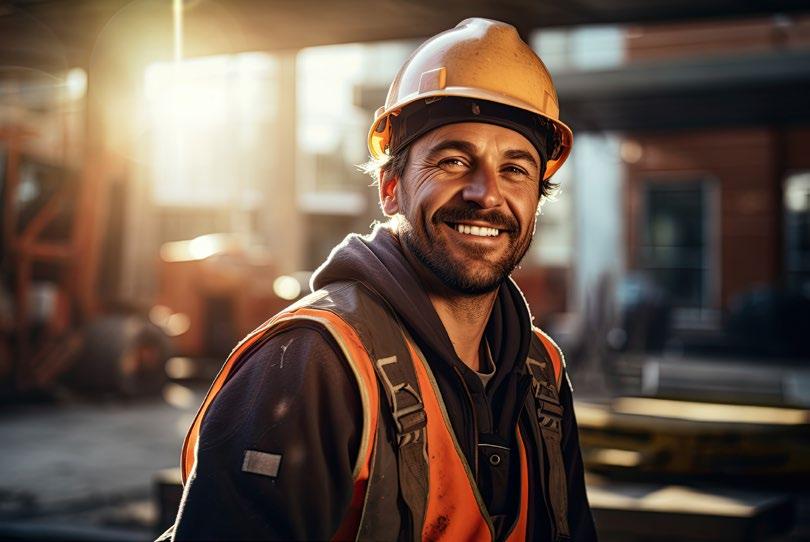
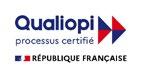
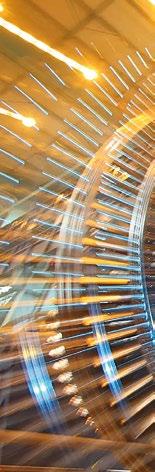
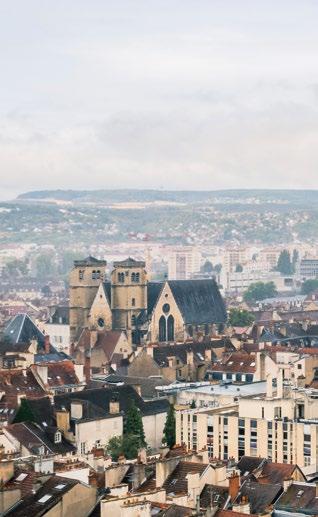
2 & 3 July 2025
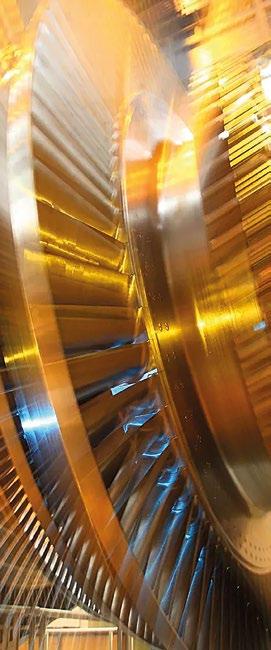
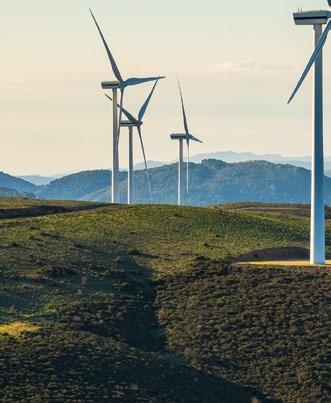
Heat Treatment and Surface Engineering
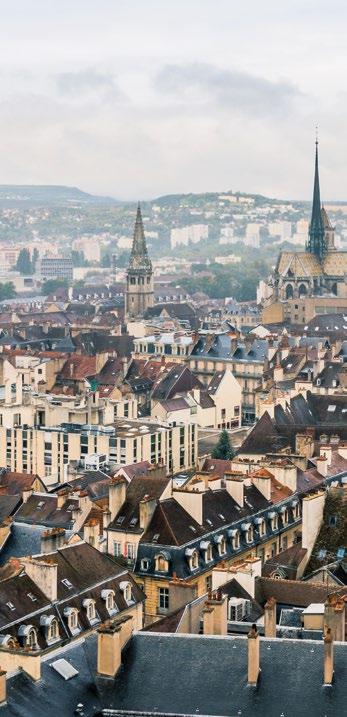
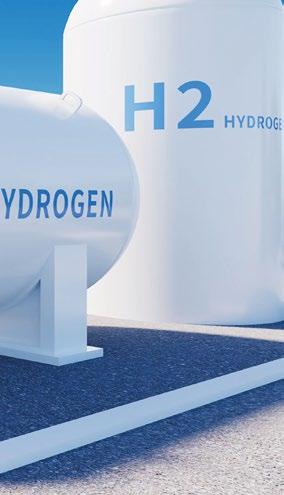
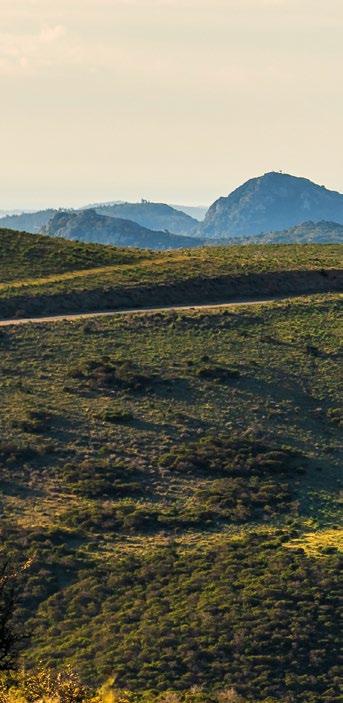
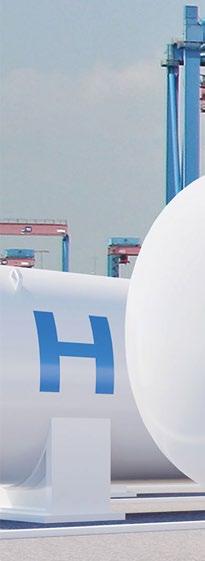
