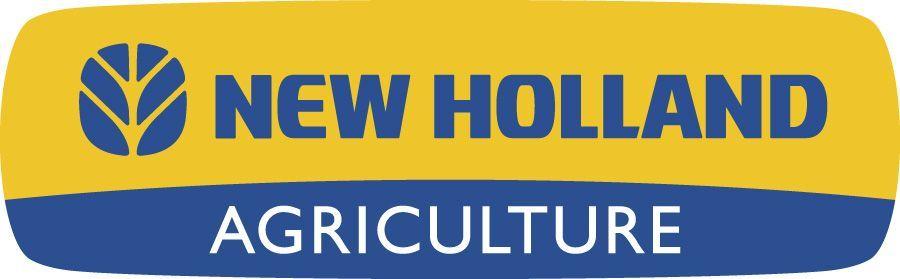
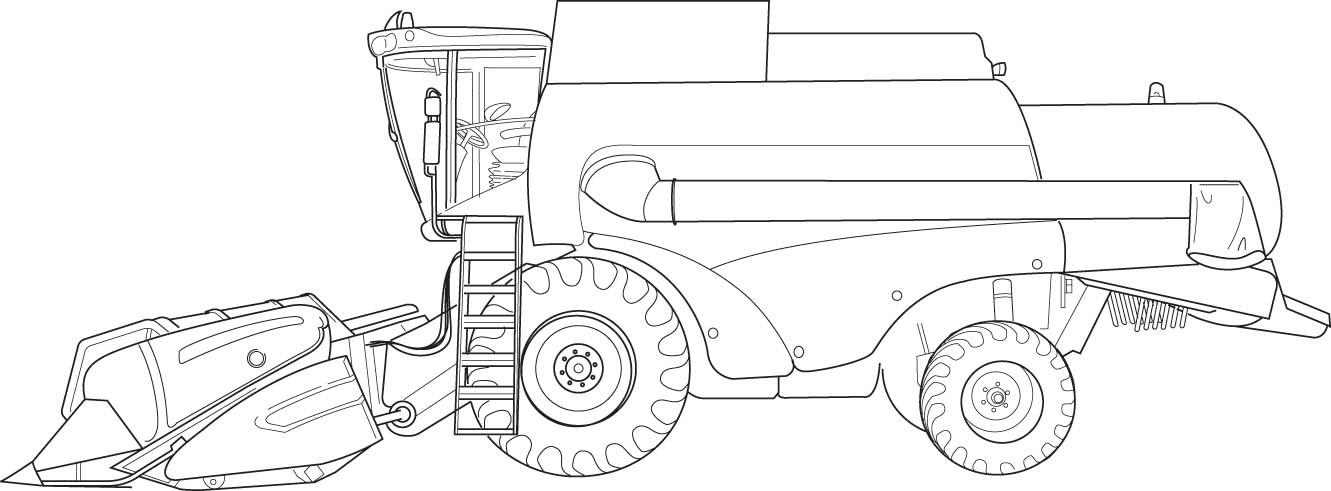
INTRODUCTION
DISTRIBUTION SYSTEMS
PRIMAR Y HYDRAULIC POWER SYSTEM
PNEUMA TIC SYSTEM
ELECTRICAL POWER SYSTEM
LIGHTING SYSTEM
ELECTRONIC SYSTEM
F AUL T CODES
ENGINE
EXHAUST SYSTEM
ENGINE COOLANT SYSTEM
TING SYSTEM
AIR INT AKE SYSTEM
POWER TRAIN
TRANSMISSION Mechanical
TRANSMISSION Hydrostatic
PROCESS DRIVE Primary process drive
TRA VELLING
FRONT AXLE
REAR AXLE
2WD - 4WD SYSTEM Hydrostatic
STEERING Hydraulic
STEERING Mechanical
SER VICE BRAKE Hydraulic
P ARKING BRAKE Mechanical
BODY AND STRUCTURE
USER CONTROLS AND SEA T
USER PLA TFORM
ENVIRONMENT CONTROL Heating system
ENVIRONMENT CONTROL Air - conditioning system
ENVIRONMENT CONTROL ventilation and air - conditioning
SAFETY SECURITY ACCESSORIES Safety
FRAME POSITIONING
FRAME LEVELLING
T OOL POSITIONING
LIFTING LEVELLING
CROP PROCESSING
FEEDING Reel feeding
FEEDING Header feeding
FEEDING Feeder housing
THRESHING Conventional threshing
SEP ARA TING Beating
SEP ARA TING Rotary separator
SEP ARA TING Straw flow beater
SEP ARA TING Straw walker
ORING AND HANDLING Grain storing
UNLOADING Grain unloading
84210989A 24/04/2009
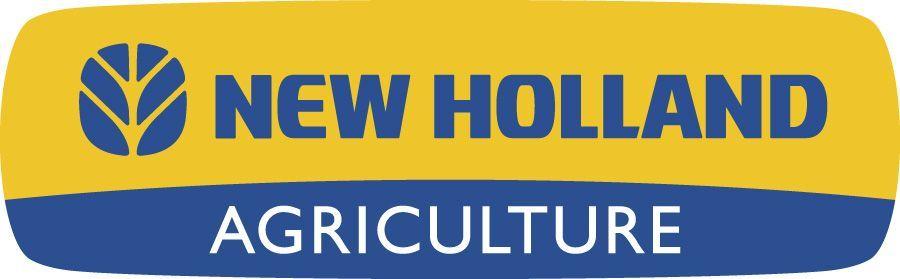
Foreword
Note the Owner
Safety rules
Driveline overview
Basic instructions
T orque
Conversion factors
Product identification
Foreword
T echnical Information
This manual has been produced a new technical information This new system designed deliver technical information electronically through - ROM and paper manuals. A coding system called ICE has been developed link the technical information other Product Support functions W arranty
T
echnical information written support the maintenance and service the functions systems a customers When a customer has a concern his machine usually because a function system his machine not working not working ficiently , not responding correctly his When you refer the technical information this manual resolve that customers you will find all the information classified using the new ICE according the functions systems that Once you have located the technical information for that function system then you will find all the mechanical, electrical hydraulic devices, assemblies and sub assemblies for that function Y will also find all the types information that have been written for that function the technical data the functional data (how the diagnostic data (fault codes and troubleshooting) and the service data (remove, install adjust, etc.).
integrating this new ICE coding into technical information , you will able search and retrieve just the right piece technical information you need resolve that customers concern his machine. This made possible attaching 3 categories each piece technical information during the authoring
The first category the Location, the second category the Information T ype and the third category the Product:
• LOCA TION - the component function the that the piece technical information going describe Fuel
• INFORMA TION TYPE - the piece technical information that has been written for a particular component function the machine Capacity would a type T echnical Data that would describe the amount fuel held the Fuel tank.
• PRODUCT - the model that the piece technical information written for
Every piece technical information will have those 3 categories attached Y will able use any combination those categories find the right piece technical information you need resolve that customers concern his
That information could be:
• the description how remove the cylinder head
• a table specifications for a hydraulic pump
• a fault code
• a troubleshooting table
• a special tool
How Use this Manual
This manual divided into Sections. Each Section then divided into Chapters. Contents pages are included the beginning the then inside every Section and inside every Chapter alphabetical Index included the end a Chapter Page number references are included for every piece technical information listed the Chapter Contents Chapter
Each Chapter divided into four Information types:
• T echnical Data (specifications) for all the electrical hydraulic components
• Functional Data (how works) for all the electrical hydraulic components and
• Diagnostic Data (fault codes, electrical and hydraulic troubleshooting) for all the electrical hydraulic components and
• Service data (remove disassembly , assemble, install) for all the mechanical, electrical hydraulic devices, ponents and
Sections
Sections are grouped according the main functions a systems the Each Section identified a letter C The amount Sections included the manual will depend the type and function the machine that the manual written for Each Section has a Contents page listed alphabetic / numeric order This table illustrates which Sections could included a manual for a particular
SECTION
A - Distribution Systems
B - Power Production
C - Power T rain
D - T ravelling
E - Body and Structure
F - Frame Positioning
G - T ool Positioning
H - W orking Arm
J - T ools and Couplers
K - Crop Processing
L - Field Processing
PRODUCT
T ractors X X X X X X X X
V ehicles with working arms: skid X X X X X X X X X forage X X X X X X X X X X spraying X X X X X X X X X
Mounted equipment and X X X X
This manual contains these The contents each Section are explained over the following Contents
Section Contents
SECTION DISTRIBUTION SYSTEMS
This Section covers the main systems that interact with most the functions the product. includes the central parts the lighting and grease lubrication The components that are dedicated a specific function are listed the Chapter where all the technical information for that function
SECTION POWER PRODUCTION
This Section covers all the functions related the production power move the machine and drive various
SECTION POWER TRAIN
This Section covers all the functions related the transmission power from the engine the axles and internal external devices and additional Process Drive
SECTION TRA VELLING
This Section covers all the functions related moving the including steering and covers all the axles both driven axles and non - driven including any axle
SECTION BODY AND STRUCTURE
This Section covers all the main functions and systems related the structure and body the Including the the the operator ’ s cab and the
SECTION T OOL POSITIONING
This Section covers all the functions related the final and / automatic positioning the tool once the tool tioned using the W orking Arm the machine
SECTION CROP PROCESSING
This Section covers all the functions related crop
Chapters
Each Chapter identified a letter and number combination e.g. Primary hydraulic power system A.10.A The first letter identical the section letter Chapter inside Section Distribution CONTENTS
The Chapter Contents lists all the technical data functional data (how service data install and diagnostic data (fault codes and troubleshooting) that have been written that Chapter for that function system the machine.
Contents
TECHNICAL T A
DISTRIBUTION SYSTEMS PRIMAR Y HYDRAULIC POWER
PRIMAR Y HYDRAULIC POWER SYSTEM - General specification (A.10.A)
FUNCTIONAL T A
PRIMAR Y HYDRAULIC POWER SYSTEM - Dynamic description
SER VICE
PRIMAR Y HYDRAULIC POWER SYSTEM - Hydraulic pump - Remove
DIAGNOSTIC
PRIMAR Y HYDRAULIC POWER SYSTEM - T roubleshooting
INDEX
The Chapter Index lists alphabetical order all the types information (called Information Units) that have been written that Chapter for that function system the machine.
Index
DISTRIBUTION SYSTEMS - A PRIMAR Y HYDRAULIC POWER SYSTEM
PRIMAR Y HYDRAULIC POWER SYSTEM - Dynamic description
PRIMAR Y HYDRAULIC POWER SYSTEM - General specification
PRIMAR Y HYDRAULIC POWER SYSTEM - Hydraulic pump - Remove (A.10.A)
PRIMAR Y HYDRAULIC POWER SYSTEM - T roubleshooting
Page Header and Footer
The page header will contain the following references:
• Section and Chapter description
The page footer will contain the following references:
• Publication number for that Section Chapter
• V ersion reference for that publication.
• Publication date
• Section, chapter and page reference e.g. A.10.A / 9
Note the Owner
Engine repair information:
The engine repair information not contained within this For engine repair please refer the respective Repair Manual for the engine type used your
Fault Code Resolution (FCR) information:
The FCR information not contained within the paper version the For FCR please refer the Electronic Service T ool (EST) the electronic version this
Safety rules
W ARNING AND DANGER SYMBOL
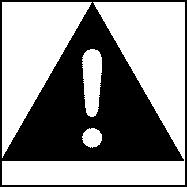
This warning symbol points out important personal safety
Carefully read the following safety regulations and observe advised precautions order avoid potential hazards and safeguard your health and safety . this manual the symbol accompanied the following key words: W ARNING - W arnings concerning unsuitable repair operations that may jeopardise the safety Repair
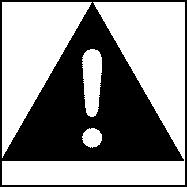
DANGER - Specific warnings concerning potential hazards for operator safety for other persons directly indirectly involved.
ACCIDENT PREVENTION
Most accidents injuries that occur workshops are the result non - observance simple and fundamental safety For this MOST CASES THESE ACCIDENTS CAN A VOIDED foreseeing possible causes and consequently acting with the necessary caution and
Accidents may occur with all types regardless how well the machine question was designed and
A careful and judicious service technician the best guarantee against
Precise observance the most basic safety rule normally suf ficient avoid many serious accident


DANGER
Shut down the remove key , sure all moving parts have stopped and all pressure the systems relieved before cleaning, adjusting lubricating the equipment. Failure comply will result death serious injury . M871
SAFETY RULES
General guidelines
• Carefully follow specified repair and maintenance procedures.
• not wear jewellery , unbuttoned loose articles clothing such as: torn scarves, open jackets shirts with open zips that may remain entangled moving parts. advised wear approved safety non - slip footwear , safety
• not carry out repair operations with someone sitting the driver ’ s unless the person a trained technician who assisting with the operation
• not operate the machine use any the implements from dif ferent other than the driver ’ s
• not carry out operations the machine with the engine unless specifically
• Stop the engine and check that the hydraulic circuits are pressure - free before removing
• All repair and maintenance operations must carried out using extreme care and attention.
• Service steps and platforms used the workshop elsewhere should built according standard accident prevention regulations.
• Disconnect the from the and label all controls indicate that the machine being Any parts that are raises must locked
• Brakes are inoperative when manually released for repair maintenance Use blocks similar devices control the machine these
• Only use specified towing points for towing the Connect parts carefully Make sure that all pins and / locks are secured position before applying Never remain near the towing cables chains that are operating under load.
• When loading unloading the machine from the trailer (or other means select a flat area capable sustaining the trailer truck Firmly secure the machine the truck trailer and lock the wheels the position used the carrier
• Electric battery - chargers and similar equipment must only powered auxiliary power supplies with ficient ground insulation avoid electrical shock hazards.
• Always use suitable hoisting lifting devices when raising moving heavy
• T ake extra care bystanders are present.
• Never use diesel oil other inflammable liquids cleaning Use non - non toxic commercially available
• W ear safety goggles with side guards when cleaning parts with compressed air
• Reduce the air pressure according the local regulations
• not run the engine confined spaces without suitable
• Never use naked flames for lighting when working the machine checking for
• All movements must carried out carefully when working under , near the W ear protective ment: goggles and special footwear
• When carrying out checks with the engine running, request the assistance operator the driver ’ s seat. The operator must maintain visual contact with the service technician all
• operating outside the workshop, position the machine a flat surface and lock position. working a slope, lock the machine Move a flat area soon safely
• Damaged bent chains cables are not use them for lifting Always use suitable protective gloves when handling chains
• Chains should always safely Make sure that the hitch - point capable sustaining the load question. Keep the area near the hitchpoint, chains cables free all bystanders.
• Maintenance and repair operations must carried out a CLEAN and Y Eliminate any water oil spillage immediately .
• not create piles oil grease - soaked rags they represent a serious fire Always store rags a closed metal container Before engaging the make sure that there are persons within the machine implement range
• Empty your pockets all objects that may fall accidentally unobserved into the machine inner
• the presence protruding metal use protective goggles goggles with side special footwear and
• When welding, use protective safety devices: tinted safety goggles, helmets, special overalls, gloves and footwear . All persons present the area where welding taking place must wear tinted NEVER LOOK DIRECTL Y
A T THE WELDING ARC WITHOUT SUIT ABLE EYE
• Metal cables tend fray with repeated Always use suitable protective devices when handling
• Handle all parts carefully . not put your hands fingers between moving parts. W ear suitable safety clothingsafety gloves and
Start -
• Never run the engine confined spaces that are not equipped with adequate ventilation for exhaust gas
• Never place the body , hands fingers near rotating and moving
Hydraulic systems
• A liquid leaking from a tiny hole may almost invisible the same powerful enough penetrate the NEVER USE HANDS T O CHECK FOR LEAKS but use a piece cardboard wood for this any liquid penetrates skin call for medical aid immediately Failure treat this condition with correct medical procedure may result serious infection
• order check the pressure the system use suitable instruments.
Wheels and T yres
• Make sure that the tyres are correctly inflated the pressure specified the manufacturer . Periodically check the rims and tyres for
• Stand away from (at the side of) the tyre when checking inflation pressure.
• not use parts recovered wheels incorrect welding brazing heating may weaken and eventually cause damage the
• Never cut weld a rim mounted with inflated
• T o remove the lock all After having raised the position supports according regulations
• Deflate the tyre before removing any objects that may jammed the tyre
• Never inflate tyres using inflammable gases, this may result explosions and injury bystanders.
Removal and - fitting
• Lift and handle all heavy parts using suitable hoisting equipment. Make sure that parts are sustained ate hooks and Use the hoisting eyebolts for lifting Extra care should taken persons are present near the load
• Handle all parts carefully not put your hands fingers between W ear suitable safety clothing - safety gloves and
• A void twisting chains metal Always wear safety gloves when handling cables