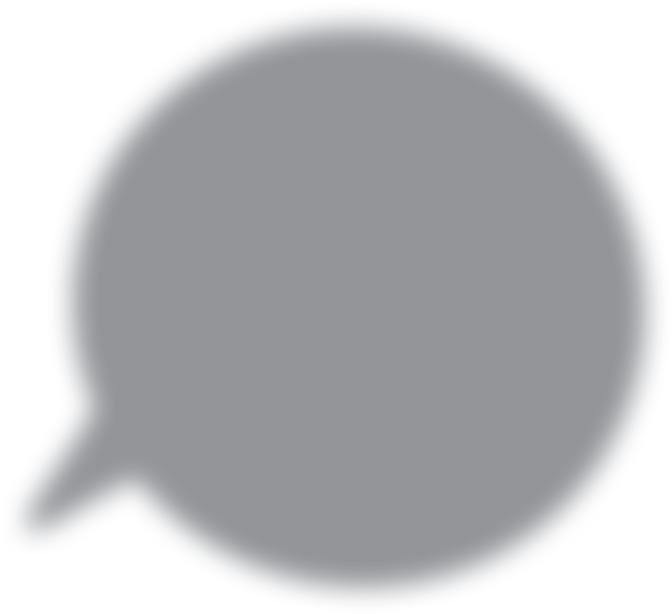
24 minute read
Design Notes
Siemens “drives” snack food maker to higher production
Edited by Mike Santora • Managing Editor
The sensor used to look at product level in the
vibrating tray. Drive amplitude is adjusted based on level to prevent damage and save power.
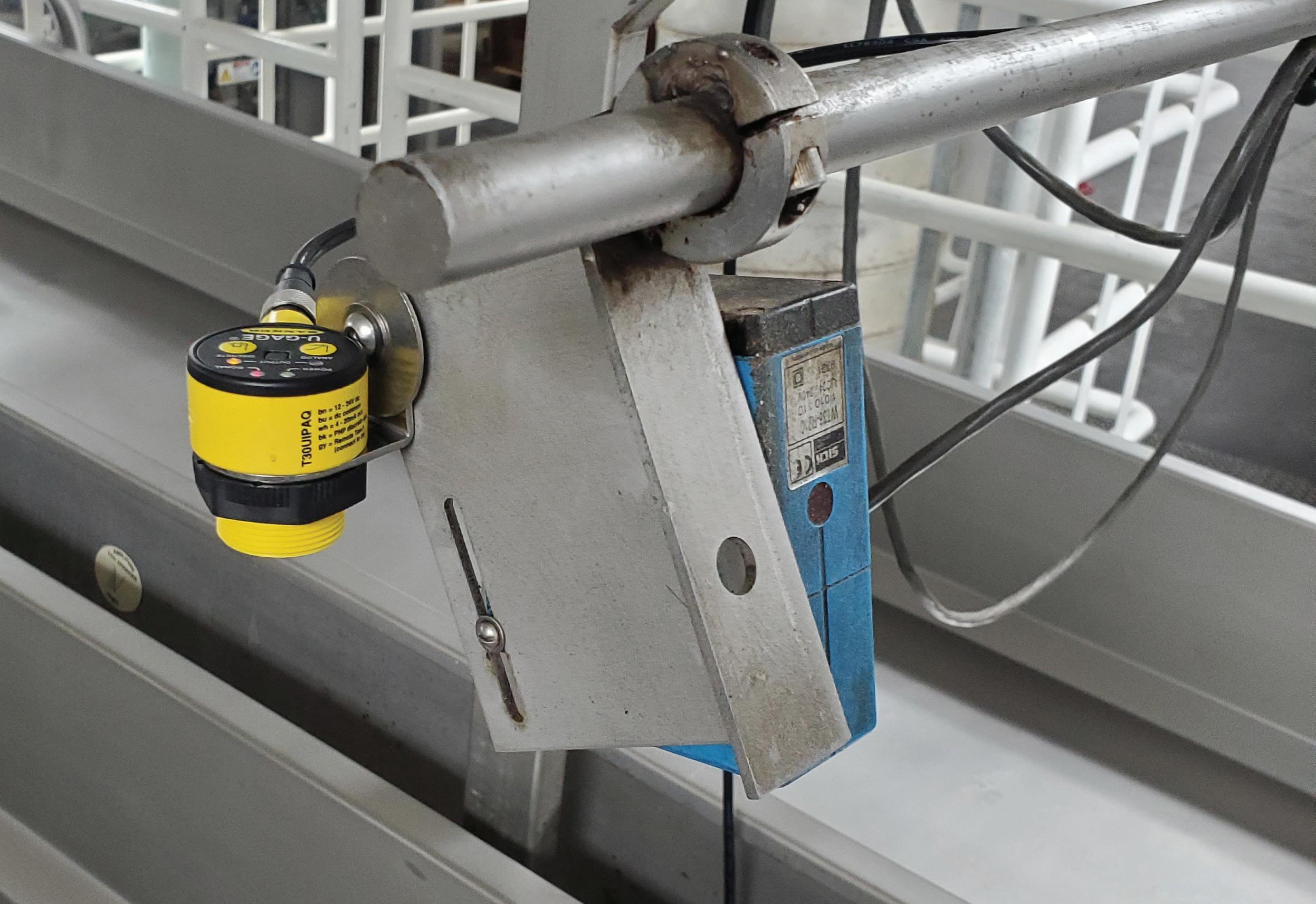
A major U.S. producer of snack foods,
with locations worldwide, faced a problem at their plant in Arkansas. As an integral part of their process, the production line features bowl feeders, vibratory conveyors, and stainless steel, washable components. The vibratory conveyor, which is 55- long, moves cooked chips om the yer to the packaging area. Due to its age and degraded original equipment, it could no longer run the line at maximum production, with equent downtime and excess vibration that caused the chips to fall off the conveyor. Rather than make a major capital investment to change the entire line, the company looked for a cost-eff ective retrofi t solution to their problem. Due to its existing relationship with this customer, SE Packaging Systems helped them fi nd the right solution. Located in Acworth, Georgia, SE Packaging Systems is both an equipment OEM and retrofi t/upgrade provider, who has been operating since 2003 in the automated packaging sector. Since 2015, they’ve partnered with Comek, an Italian producer of weighing, wrapping, and packaging systems. Plants built by the company are used in the food and non-food consumer goods industries. On behalf of Comek, SE Packaging Systems provides on-site assistance for lines already installed in the U.S., including repairs or upgrades, supply of new equipment, and optimized integration in existing processes. The company is owned
by its president, David James. Being an Authorized Solution Partner for Siemens, SE Packaging brought them on board for this project. Ali Ali, the national accounts manager for Siemens, led the project with David James and a local distributor. The line control was re-confi gured, then updated with Siemens drives, motors, and related hardware automation. David James supplied the wiring diagrams for the retrofi t to Programmable Logic Controllers (PLCs) on the original equipment. Furthermore, Variable Speed Drive (VFD) technology was needed to properly synchronize the line elements. SE Packaging also provided and engineered level sensors to help the line vibrators adapt to the increased weight and height, a problem the end-customer had encountered and one that literally made the chips fall off the conveyor.
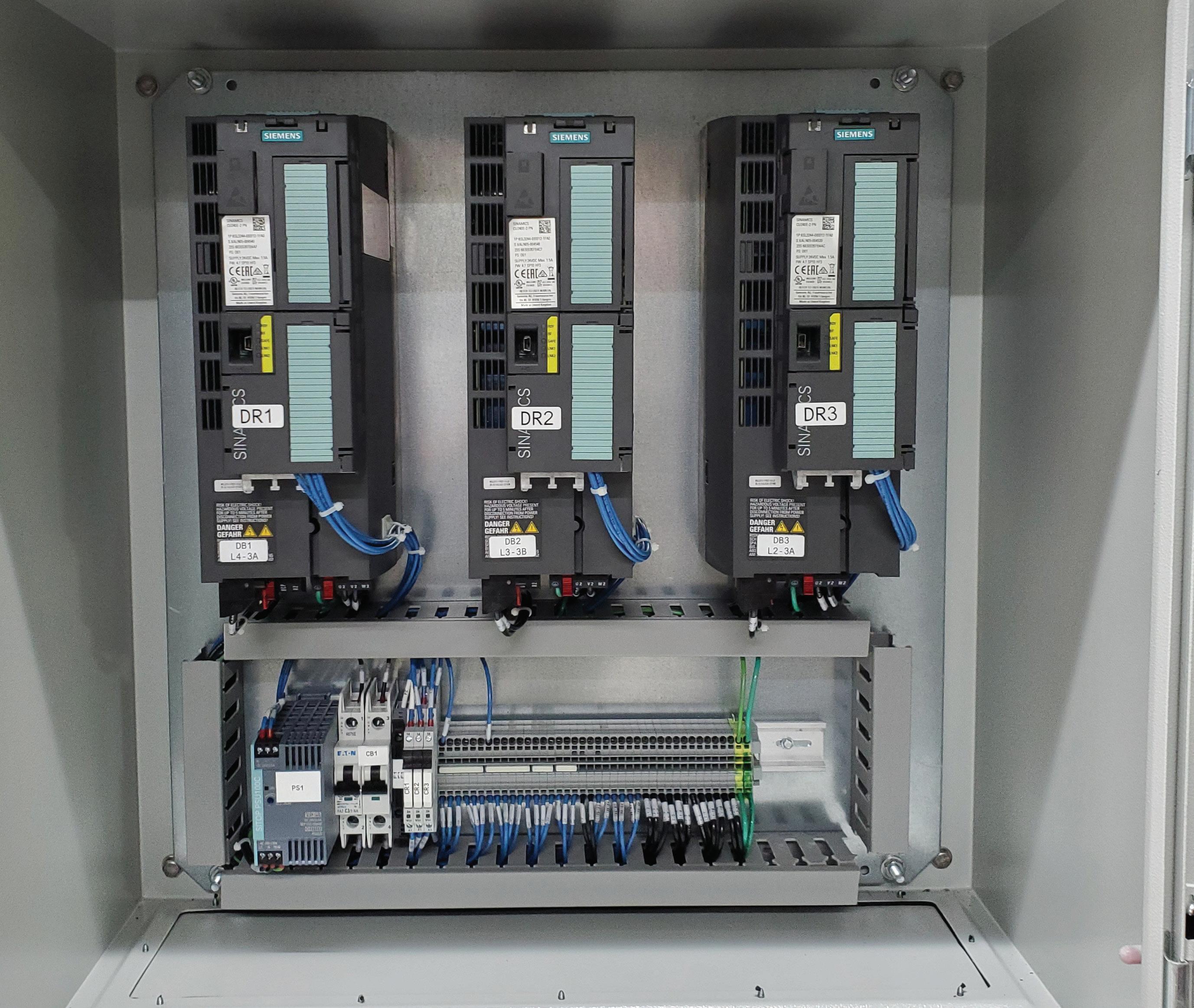
Vibrating Feeder with
The enclosure of three drives for controlling one bank of the
vibrating feeders. The system consisted of 18 banks of drives.
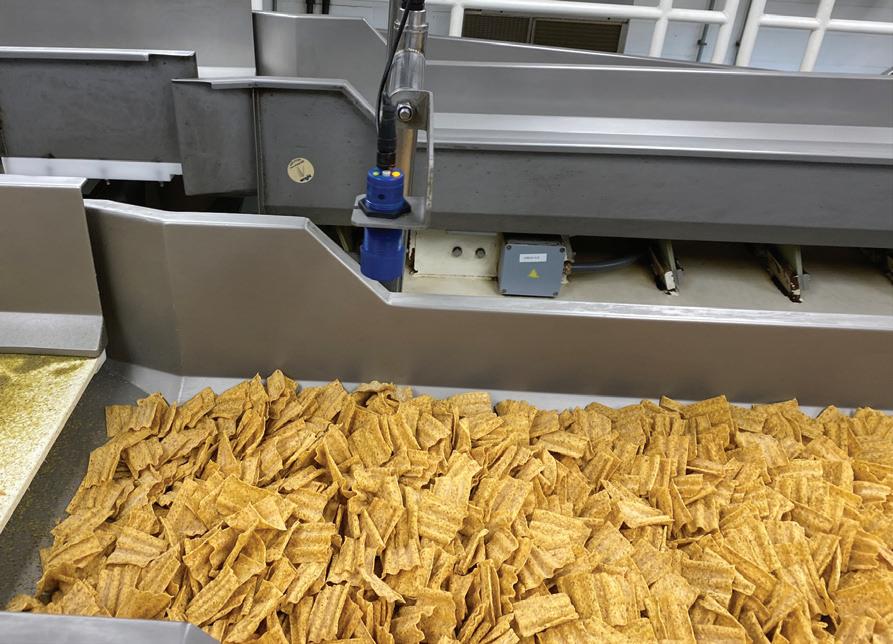
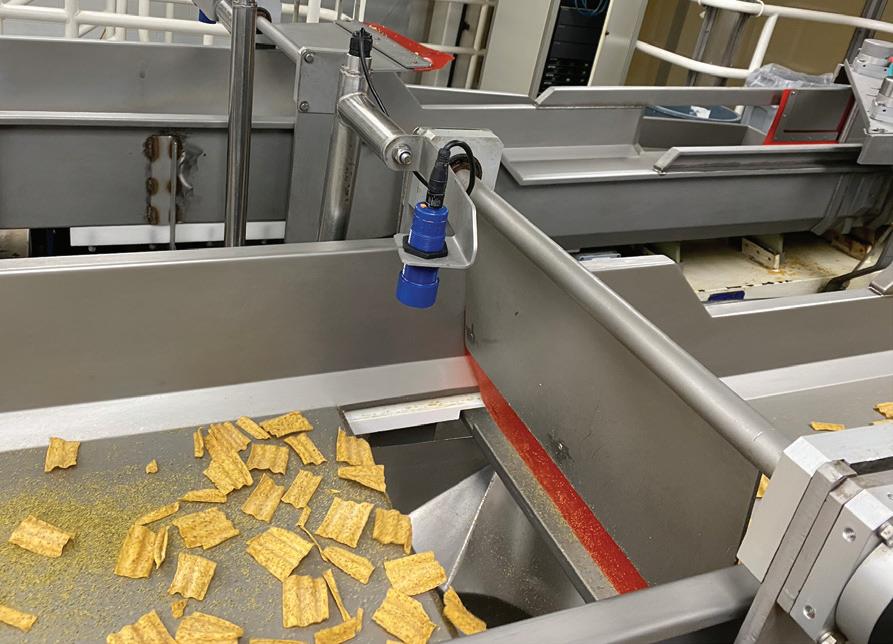
Vibrating Feeder with high product level – Drive operates at a higher amplitude.
Design Notes
These sensors interface to analog inputs on a Siemens SINAMICS G120 VFD. The G120 drive system used on this job led to an overall production process improvement of over 10%, a substantial increase in line e ciency, compared to the original equipment om another controls supplier. Likewise, a signifi cant energy savings of approximately 20% was achieved, according to David James. This savings resulted om the fact that the system could power down when the pans were empty, compared to a simple fastslow setting on the previous line controls. “While the original controls on the line were om another manufacturer, SE Packaging and Siemens won the project thanks to their cost-eff ective solution that provided a 20% reduction in maintenance cost, zero downtime in the fi rst year of operation, and much higher reliability,” said to James. He notes the Siemens strategy involved technically empowering and partnering with the snack food plant to create a G120 application-specifi c drive solution, which is optimized for the operation. Siemens technical support also conducted G120 drive and so ware training at the snack food plant to ensure all operators and maintenance personnel were familiar with the new drive systems. Over-current relays, for example, protect the single-phase motor output, while the VFDs onboard enable the motor current to remain within the torque limits set during vector control. The result is a more stable “ride” for the chips, James mused. “I’m happy to report that everything is operating successfully. The company is very pleased with the results as well as the training we’ve provided,” Ali concluded by saying he feels confi dent this relationship will continue, with additional retrofi ts and new line projects possible. Other Siemens products incorporated on this project were the Simatic PLC and various food-grade components. DW
Siemens www.siemens.com

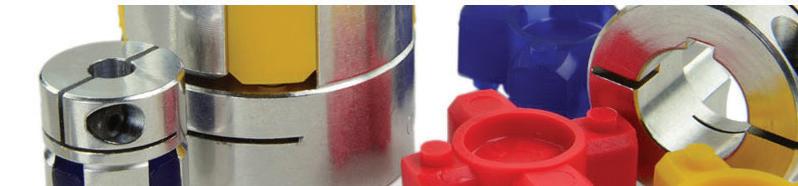
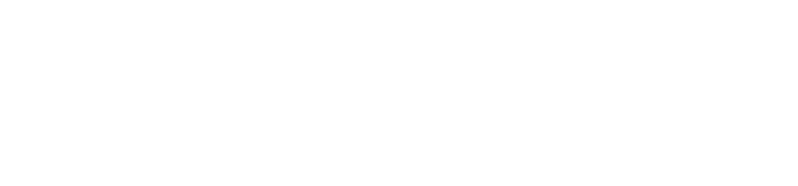
All products available directly on RULAND.COM All products available directly on RULAND.COM All products available directly on RULAND.COM All products available directly on RULAND.COM
WHAT’S NEW RULAND from WHAT’S NEW RULAND from COMPONENTS FOR ROBOTIC SYSTEMS from RULAND WHAT’S NEW RULAND from

TOOL-LESS ADJUSTMENT COMPONENTS
EXPANDED COUPLING LINE
UNIVERSAL JOINTS
MODULAR MOUNTING SYSTEMS
• Assortment of components that allow users to build small assemblies for mounting sensors, conveyor rails, machine guards, and more. • Optional pre-designed kits make it easier to select the right system for your application.
INDEXING PLUNGERS
• Spring-loaded indexing VIBRATION ISOLATING COMPONENTS plugers with or without lock-out. • Rubber bumpers are ideal as end stops or mounting feet. • Designed to lock devices in-place for adjustable • Vibration isolation mounts can be positioning.sandwiched between components to dampen shock loads. • Both types can have studs or tapped holes.
www.ruland.com | sales@ruland.com
RULAND • Introductory offer: 10% off your next web order with code DW202003 • Free 2-day shipping on all domestic web orders - no minimum value. • Full product data, CAD files, technical information, and installation videos. • Large stock on hand in our Marlborough, MA USA location. TOOL-LESS ADJUSTMENT COMPONENTS • Adjustable handles and knobs replace standard hardware and can be used to torque components without tools. • Levers can be used with Ruland shaft collars for quick installation and adjustment. EXPANDED COUPLING LINE • Stainless steel oldham couplings for high temperature and corrosion resistance. • Controlflex couplings for encoders in single and double insert styles and speeds up to 25,000 RPM. WHAT’S NEW • Slit couplings with bores starting at 1.5mm and speeds up to 70,000 RPM. UNIVERSAL JOINTS • Friction bearing for high torque. • Needle bearing for accuracy and higher RPM. • Single and double styles available.
MODULAR MOUNTING SYSTEMS
• Assortment of components that allow users to build small assemblies for mounting sensors, conveyor rails, machine guards, and more. • Optional pre-designed kits make it easier to select the right system for your application.
INDEXING PLUNGERS
• Spring-loaded indexing VIBRATION ISOLATING COMPONENTS plugers with or without lock-out. • Rubber bumpers are ideal as end stops or mounting feet. • Designed to lock devices in-place for adjustable • Vibration isolation mounts can be positioning.sandwiched between components to dampen shock loads. • Both types can have studs or tapped holes.
www.ruland.com | sales@ruland.com
TOOL-LESS ADJUSTMENT COMPONENTS DW202003
• Adjustable handles and knobs replace standard hardware and can be used to torque components without tools. • Free 2-day shipping on all domestic web orders - no minimum value. • Levers can be used with Ruland shaft collars for quick installation and adjustment. • Full product data, CAD files, technical information, and installation videos. • Large stock on hand in our Marlborough, MA USA location.
EXPANDED COUPLING LINE
• Stainless steel oldham couplings for high temperature and corrosion resistance. from• Controlflex couplings for encoders in single and double insert styles and speeds up to 25,000 RPM. • Slit couplings with bores starting at 1.5mm and speeds up to 70,000 RPM.
UNIVERSAL JOINTS
• Friction bearing for high torque. • Needle bearing for accuracy and higher RPM. • Single and double styles available.
MODULAR MOUNTING SYSTEMS
• Assortment of components that allow users to build small assemblies for mounting sensors, conveyor rails, machine guards, and more. • Optional pre-designed kits make it easier to select the right system for your application.
INDEXING PLUNGERS
• Spring-loaded indexing
VIBRATION ISOLATING COMPONENTS plugers with or without lock-out. • Rubber bumpers are ideal as end stops or mounting feet. • Designed to lock devices in-place for adjustable • Vibration isolation mounts can be positioning.sandwiched between components to dampen shock loads. • Both types can have studs or tapped holes. • Introductory offer: 10% off your next web order with code
DW202003
• Free 2-day shipping on all domestic web orders - no minimum value. • Full product data, CAD files, technical information, and installation videos. • Large stock on hand in our Marlborough, MA USA location. Beam couplings for light weight & high misalignment accommodation. Zero-backlash jaw couplings for vibration dampening & a variety of performance options. Bellows couplings for high size to torque ratio.
TOOL-LESS ADJUSTMENT COMPONENTS
• Adjustable handles and knobs replace standard hardware and can be used to torque components without tools. • Levers can be used with Ruland shaft collars for quick installation and adjustment. Ruland Manufacturing is proud to support the FIRST Robotics Competition as a Gold Supplier of precision shaft collars & couplings.
EXPANDED COUPLING LINE
PRECISION COUPLINGS • Stainless steel oldham couplings for high temperature and corrosion resistance. • Controlflex couplings for encoders in single and double insert styles and speeds up to 25,000 RPM. • Slit couplings with bores starting at 1.5mm and speeds up to 70,000 RPM.
UNIVERSAL JOINTS
SHAFT COLLARS • Friction bearing for high torque. Thousands of size and style options. • Needle bearing for accuracy and Proprietary manufacturing higher RPM. processes ensure superior t & nish. • Single and double styles available. 8 material options.
QUICK CLAMPING COLLARS
Hand operated: no tools required to install, remove, & adjust.
Best suited for robotic systems that require frequent adjustments.
MODULAR MOUNTING SYSTEMS
• Assortment of components that allow users to build small assemblies for mounting sensors, conveyor rails, machine guards, and more. • Optional pre-designed kits make it easier to select the right system for your application.
INDEXING PLUNGERS
• Spring-loaded indexing VIBRATION ISOLATING COMPONENTS plugers with or without lock-out. • Rubber bumpers are ideal as end stops or mounting feet. • Designed to lock devices in-place for adjustable • Vibration isolation mounts can be positioning.sandwiched between components to dampen shock loads. • Both types can have studs or tapped holes.
www.ruland.com | sales@ruland.com
DW202003
Marlborough, MA USA location.
Design Notes
Packaging upgrades increase brewery’s efficiency Edited by Mike Santora • Managing Editor
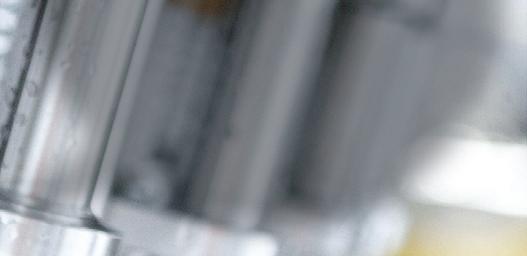
The new fi ller processes up to 25,000 0.5-liter cans per hour and scores on sustainability and e ciency.
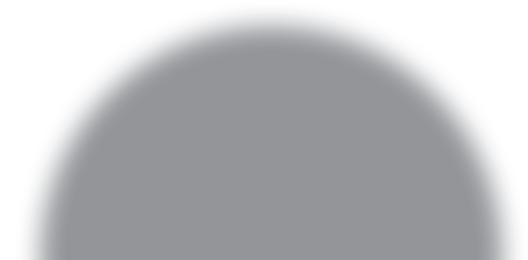
Molson Coors is one of the biggest brewery groups in the world. The Serbian plant run by its subsidiary Apatinska Pivara Apatin has relied on technology engineered by KHS for over four decades. As a result of extensive modernization measures, Apatin Brewery has optimized its line e ciency and product quality. The traditional brewery also benefi ts om improved hygiene and savings in energy and media. The cooperation between Apatin Brewery and the Dortmund systems supplier dates back to the 1970s and KHS’ predecessor companies Holstein & Kappert and Seitz Enzinger Noll Maschinenbau AG (SEN), who in 1993 merged to form KHS. When the brewery decided to modernize a few of its machines in 2014 — some of them almost 20 years old — it sought sustainable systems om KHS. The mechanical engineering company fi rst renewed two glass lines, and in 2020 the customer then invested in the Innofi ll Can DVD can fi ller. “Our old machines could no longer meet our current demands regarding product quality, performance, and sustainability,” said Tanja Popović, packaging manager at Apatin Brewery. “Together with our colleagues om KHS, we devised a sophisticated concept for modernizing our lines.” KHS started revamping the fi rst glass line back in 2014. The goal was to reduce media and electricity consumption on the bottle washer. By installing ECO carriers, the KHS engineers optimized the resource

Using HMI panels makes the machine much easier to operate. All processes are now-automated and many of them have been digitalized.

e ciency and economy of the system. “The machine now not only uses less water and fewer additives, but it also consumes less energy,” said Bojan Culibrk, KHS’ local service manager. Just four years later, Apatin Brewery took the next step towards sustainable production by modernizing one of its glass fi llers. The KHS specialists replaced the old vacuum pump with a new ECO variant that feeds process water back into the system a er treatment. “On the one hand, we’ve cut media consumption, and on the other, the fi ller is now more economical and e cient,” said Culibrk. The ECO vacuum pump proved so convincing that the Serbian bottler also procured this equipment for its second glass fi ller. The brewery also commissioned KHS to install a new capper turret. “This is a lot easier to clean than the previous model,” Culibrk explained. “It lowers the risk of product contamination, and as a result, hygiene is improved.” Furthermore, KHS was also able to optimize the cap quality on the glass bottles. In addition to improved hygiene and product quality, the Serbian beverage producer also wanted to automate its plant technology. They accomplished this by using HMI panels integrated on the glass lines and new can fi ller. According to Popović, this makes the machine easier for operators to use, as sequences are automated and many have been digitized. “The new programs for product changeover, sanitizing, and fi lling speed up our processes. Using this state-of-the-art technology, we achieve a much higher level of production e ciency and avoid unplanned downtime thanks to improved safety and reliability in fi lling,” said Popović. The HMI system also detects wear parts in advance, meaning that replacements can be ordered in good time. In 2020, the brewery invested in an Innofi ll Can DVD fi ller. “We had to boost our capacity in this segment to meet the growing demand for beverages in cans,” Popović said. “With our new fi ller, we can process up to 25,000 0.5-liter cans an hour. We’re also more e cient and sustainable.” According to the company’s own statistics, the output runs to more than two million hectoliters per annum. On the Innofi ll Can DVD, the brewery fi lls all its brands into containers holding 0.33 and 0.5 liters. Besides the high throughput, hygiene and product quality also played a key role when making the new investment. The Innofi ll Can DVD permits warm fi lling of beverages at around
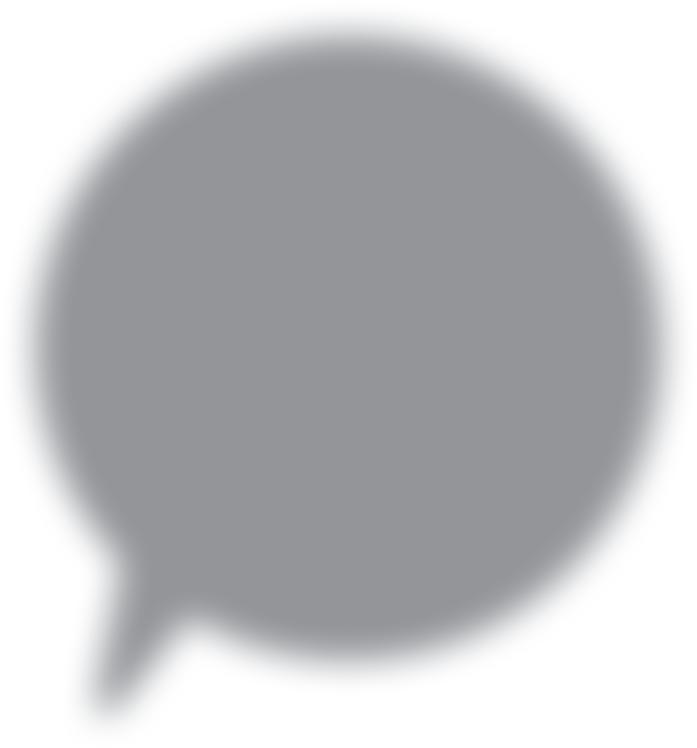
The brewery has a large portfolio that includes the brands Jelen, Jelen Chill, Jelen Cool, Apatinsko, Staropramen, Bavaria, Nikšićko and Nikšićko Tamno. The beverages are fi lled into glass bottles and cans.
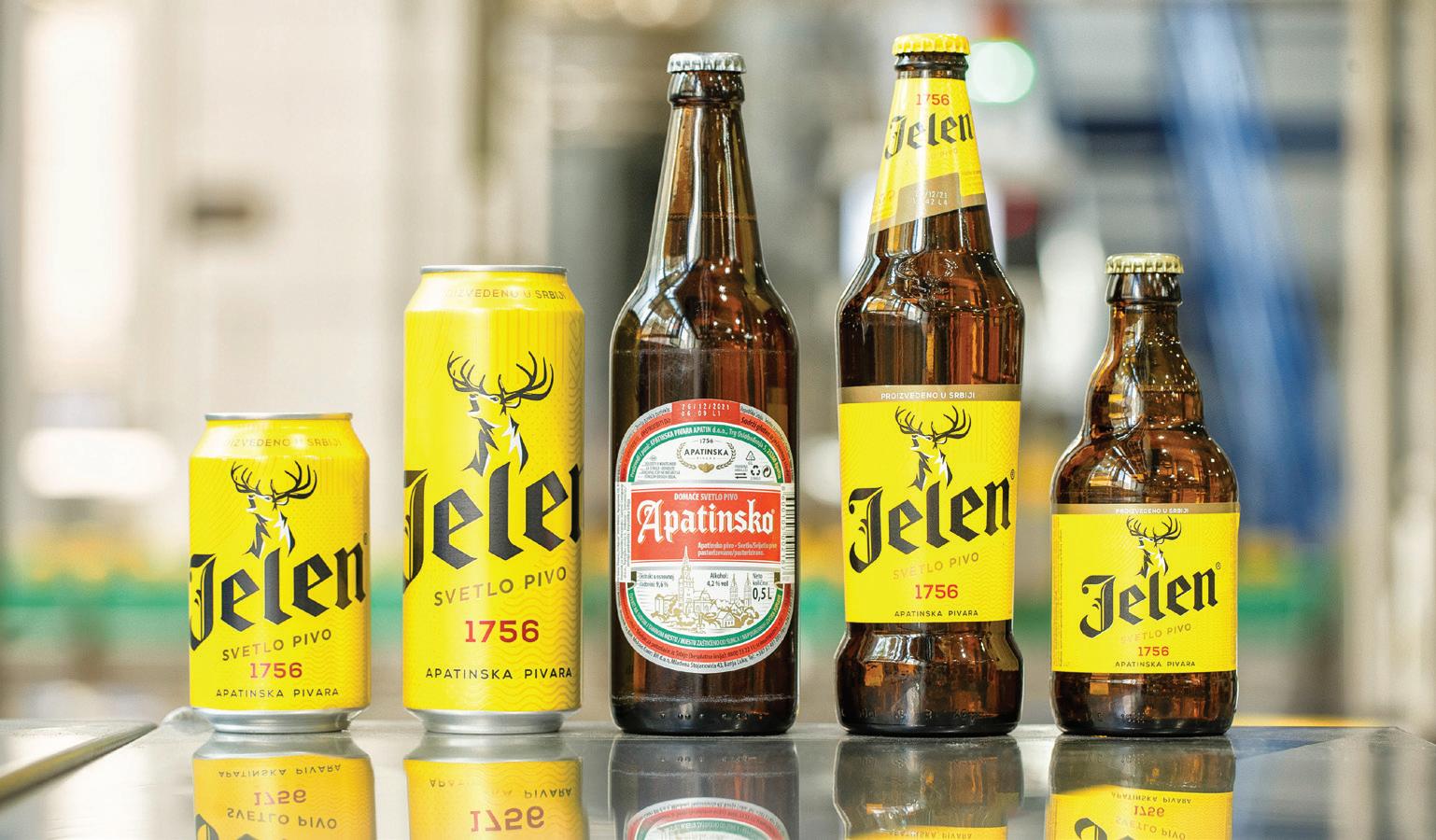
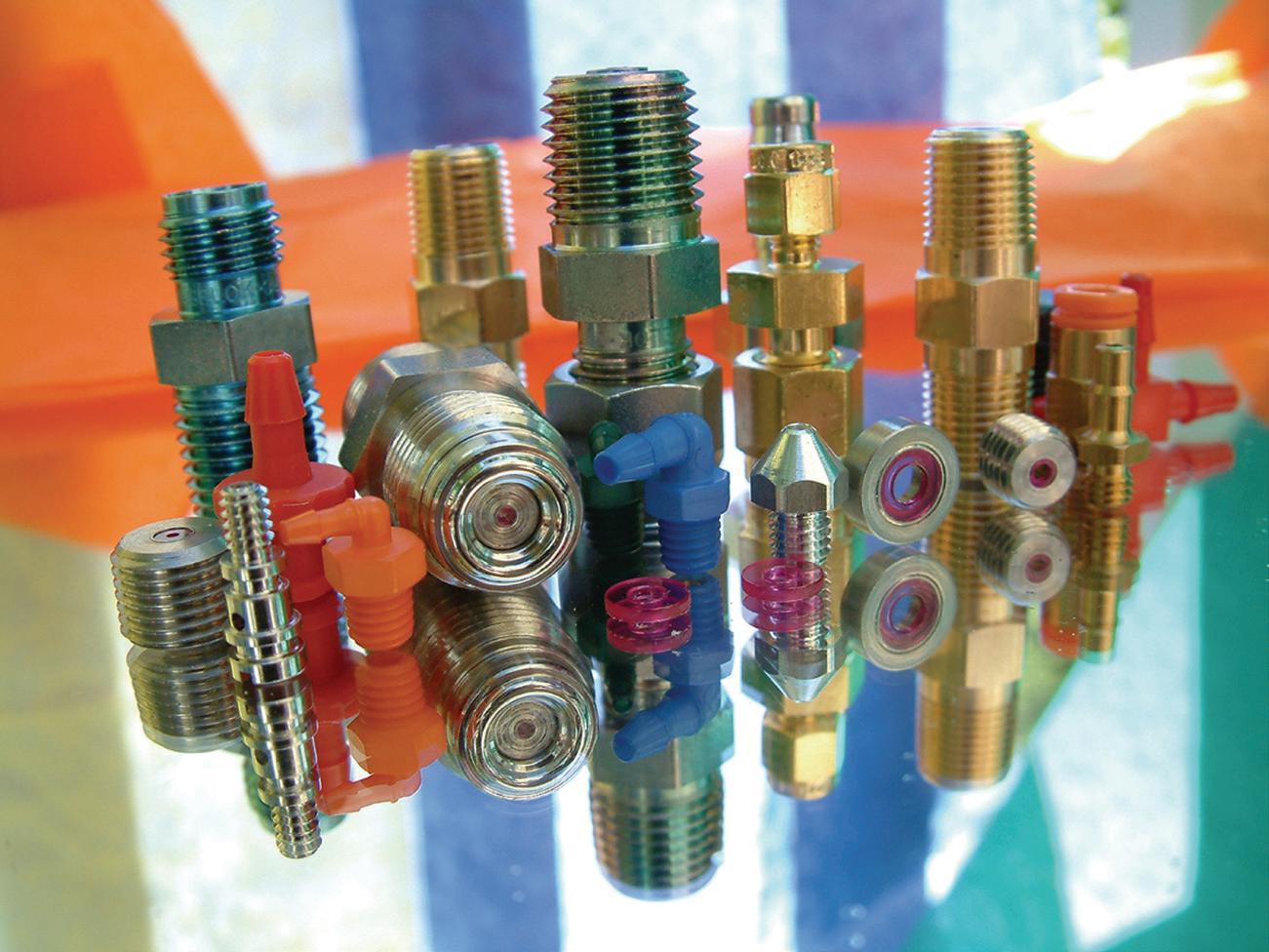
Make your machine move
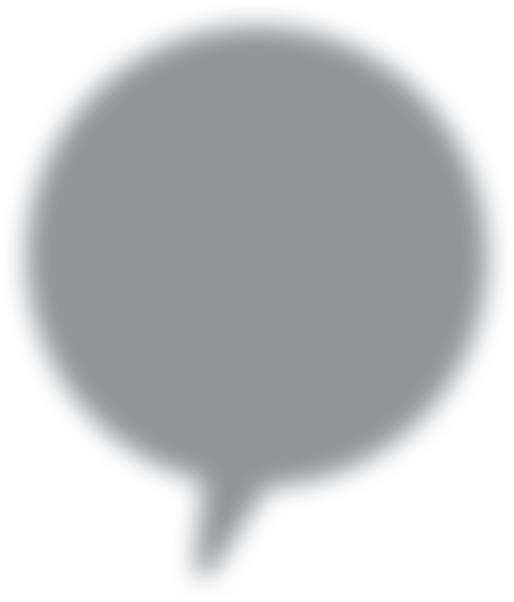

L12 - 30mm Actual size
MICRO LINEAR ACTUATORS
• 10mm-300mm stroke • 25kg+ available force • 6v-12v power supply • 15g-100g net weight
Design Notes
20°C. This method becomes more signifi cant, particularly regarding the further processing stages, as it eliminates the formation of condensation. This rules out the risk of cartons, trays, and cans in six-packs growing soggy, forming mold, or being contaminated by microbes. The brewery is convinced that the new CO2 purging process has an equally positive impact on the product quality. “Oxygen pickup impairs the quality of the beverage,” said Culibrk. “To prevent this, modern production containers are purged with CO2.” The KHS purging process is so e cient that less oxygen enters the containers than conventional methods despite lower amounts of carbon dioxide being used. Moreover, the volumetric fi lling principle also improves the fi lling accuracy. The can fi ller was installed under restrictions imposed during the COVID-19 pandemic. “Thanks to our local presence in Serbia and the Balkans, we were able to carry out all work quickly and e ciently. Travel restrictions and social distancing, of course, presented us with a challenge or two during our day-to-day activities. However, together with the customer, we managed to bring the project to a successful close within the given schedule,” Culibrk said. Popović also draws a positive conclusion. “The dedication and commitment shown by the KHS team have le a lasting impression on us. We were always able to rely on them and their expertise.” DW
KHS www.khs.com
In 2020, Apatin Brewery invested in the Innofi ll Can DVD can fi ller from KHS.
Design Notes
Advanced prosthetics in the jungles of Guatemala
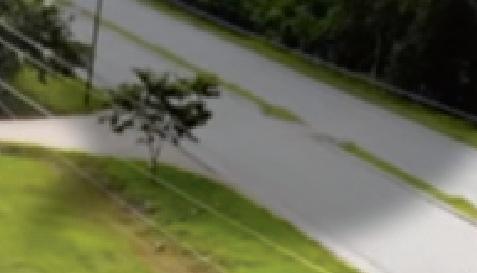
Edited by Mike Santora • Managing Editor

Hospital Shalom is the only facility that provides prosthetics care to patients of the Petén region in northern Guatemala.
LifeNabled volunteers and designers created a
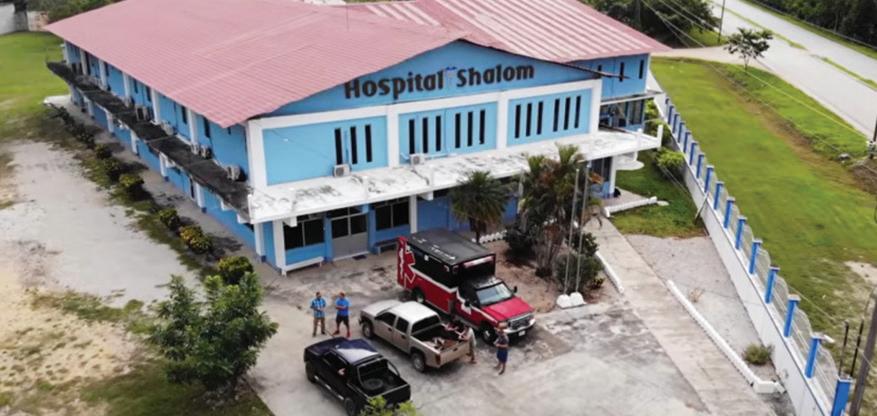
fully digital workfl ow to produce custom 3D printed prosthetic sockets with fl exible inner liners. Now, 35 patients in the jungle of Guatemala are walking on the world’s most advanced prosthetic and orthotic devices. Funded by donors and sponsors, the team has been treating patients in the poorest regions of Guatemala for the past 15 years with ee, bi-annual clinics. Using traditional fabrication methods in a limited time ame required hard work. In their last clinic, the team cut the cord on traditional fabrication and did everything digitally. Using patient scan data as input, they automatically generated the prosthetic socket designs in nTopology, and 3D printed them in durable TPU with HP’s MJF. The new digital workfl ow saved the team more than three days of laborious work. The process can be replicated in other parts of the world to signifi cantly improve the quality of life of amputees in developing countries. Brent Wright is a Certifi ed Prosthetist and Orthotist. Together with his wife, Meredith Wright, they co-founded LifeNabled, a nonprofi t provider of prosthetic solutions for the developing world, based in Raleigh, North Carolina, USA. Brent and his team are changing the lives of amputees in northern Guatemala who do not have the means to aff ord prosthetic care. Their bi-yearly clinics have treated hundreds of patients over the past 15 years. However, fabricating prostheses is a highly technical job. Evaluating, manufacturing, and fi tting prostheses to the 30-50 patients during the week-long clinics took a physical toll on Brent and his team of volunteers. For their latest clinic, Brent and his team applied their years of experience in prostheses fabrication and additive manufacturing to develop a fully digital workfl ow. In this case study, we walk you through the steps they followed — om 3D scanning to design and manufacture — to create custom, 3D printed prosthetic sockets based on patient data in a cost-eff ective manner.

time-consuming,
expertise-intensive, and laborious process.
Traditional Vs. Digital Fabrication of Prostheses
Traditional fabrication of prostheses is a laborious process. Since each socket needs to off er a custom-made fi t for each patient, the fabrication is entirely manual. Typically, there are three steps involved in the process. First, the Prosthetist takes a cast of the amputee’s missing extremity during patient evaluation. Then, they use the cast to create a custom mold to thermoform the socket; the socket is connected to off -the-shelf components to manufacture the prosthesis. Finally, the Prosthetist fi ts the prosthetic device to the patient and makes the necessary adjustments to ensure a good fi t. Manual fabrication of prostheses is a time-consuming, expertise-intensive, and laborious process. Brent Wright’s vision is to fully digitize the design and manufacturing steps. These steps are the most expertise-demanding phases of the prostheses fabrication process. At the same time, his team can train locals (or guide them through video calls) to perform the evaluation and fi tting steps, eliminating the need for an expert to be present in the remote location. As a proof of concept, the team cut the cord to traditional manufacturing in the last clinic and followed a fully digital process. By digitizing the entire workfl ow, they could make the process scalable and as cost-eff ective. Here’s an overview of the new digital workfl ow: • First, two team members fl ew to Guatemala to take 3D scans. In just two days, they were able to evaluate 35 amputees. • Then, over the next two weeks, Brent designed and customized each device and manufactured the sockets using HP’s MJF 3D printing technology. • Finally, the team returned to Guatemala a month later to deliver the devices and fi t them to the patients.
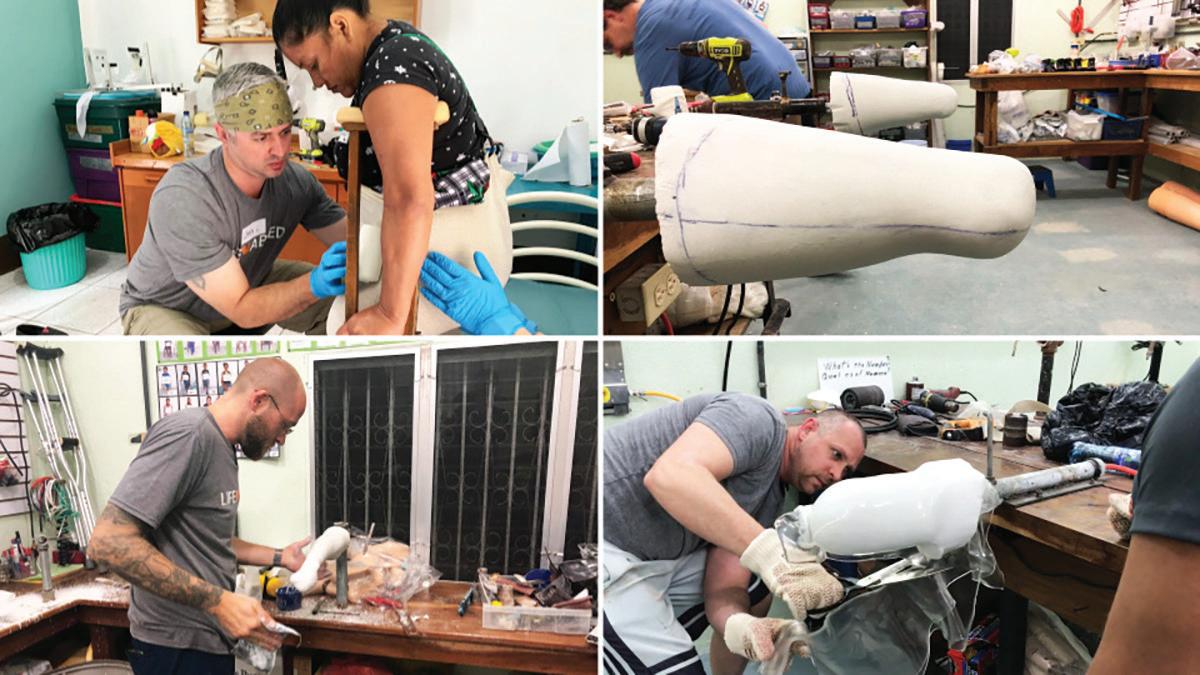
Innovation Redefined
Components Corporation “The Pioneer in Test Point Technology”

Since our creation of the first Test Point for the electronics industry we’ve been redefining excellence in PCB interconnect technology. As the industry leader, we provide innovative, economical solutions to interconnect and testing challenges, both custom and standard, for board-level engineers worldwide.
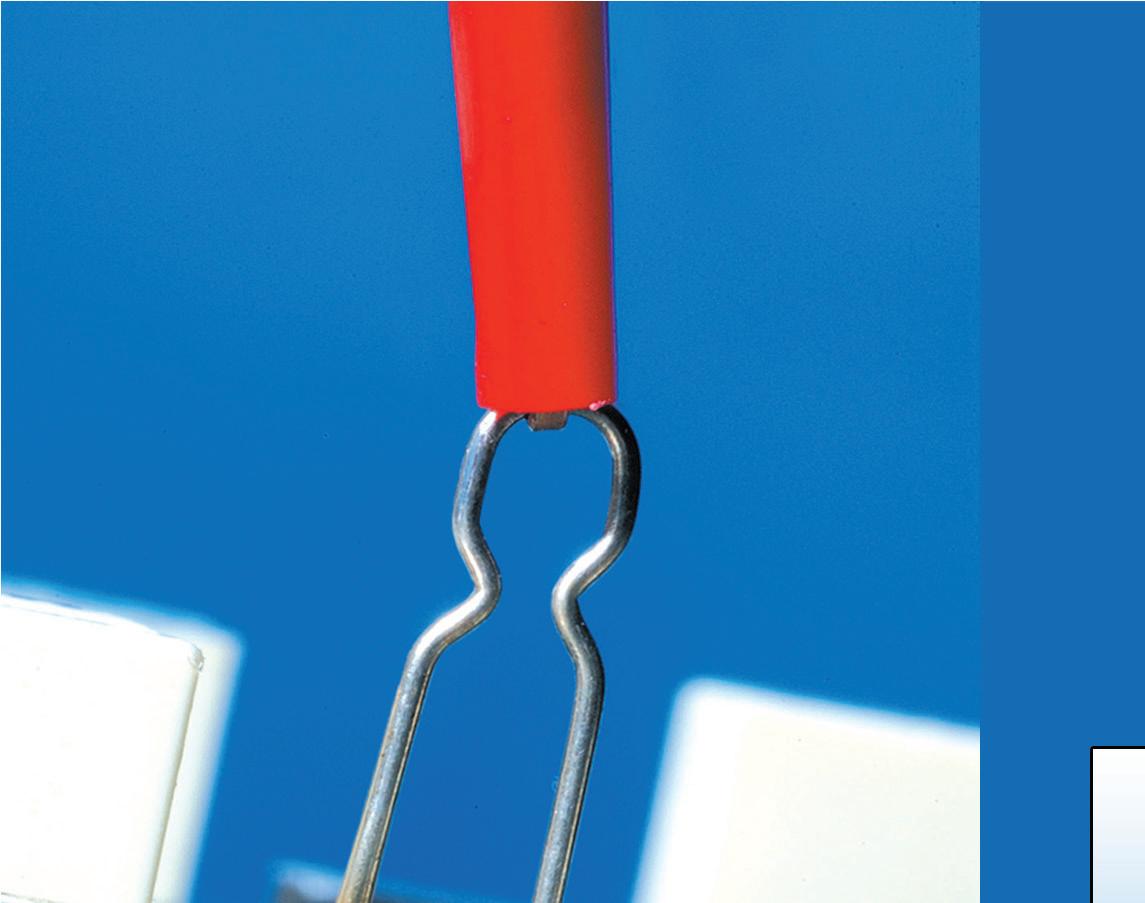
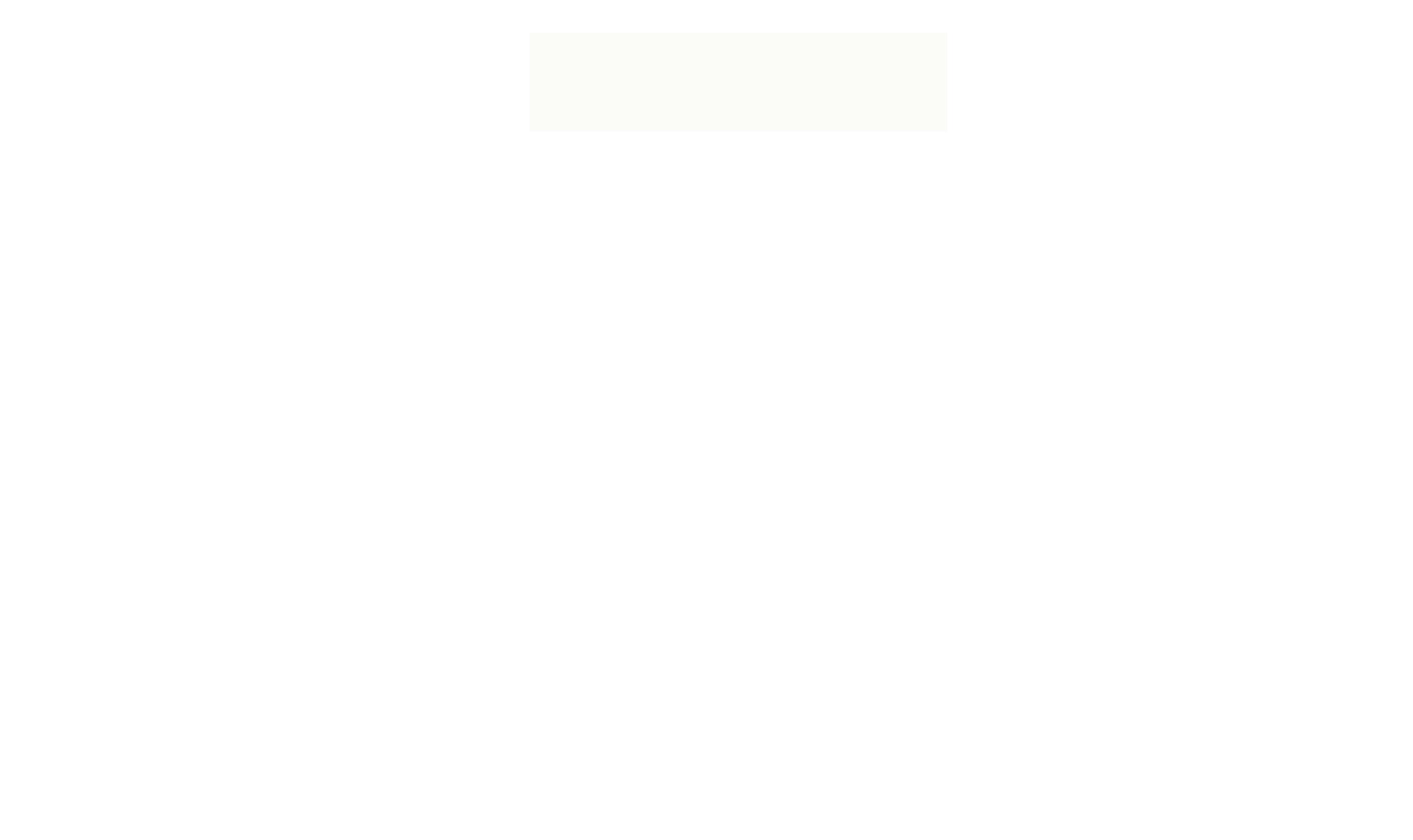
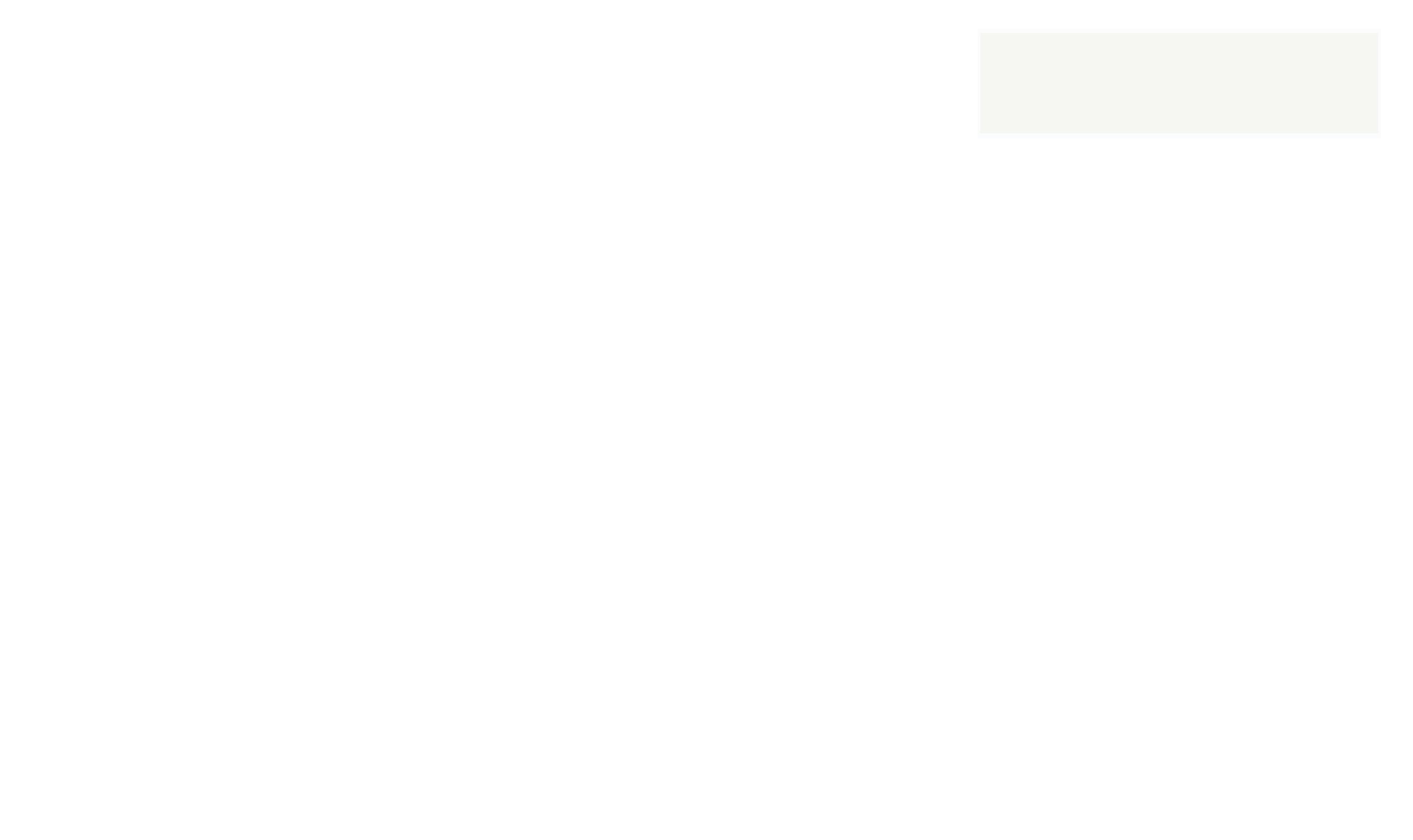
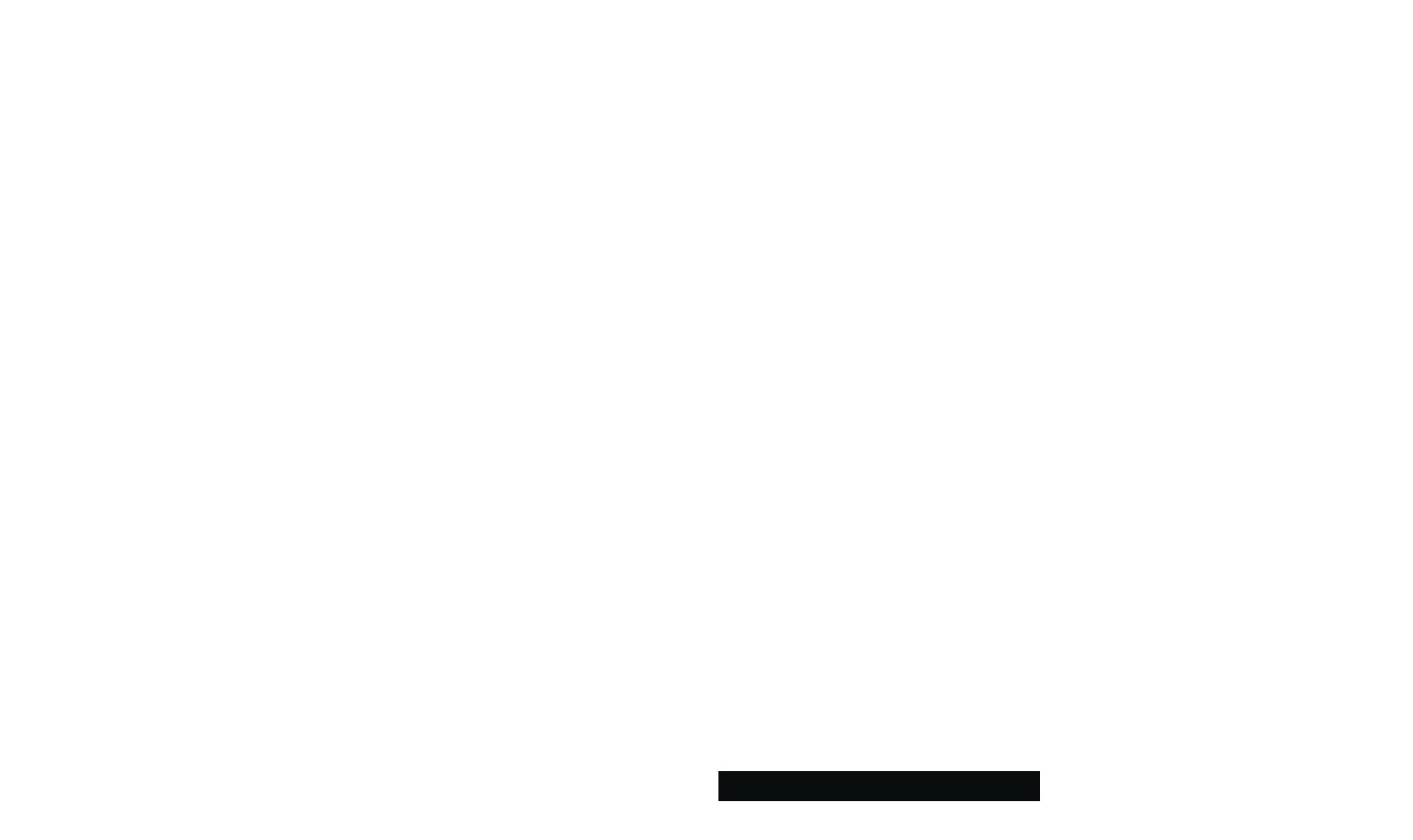
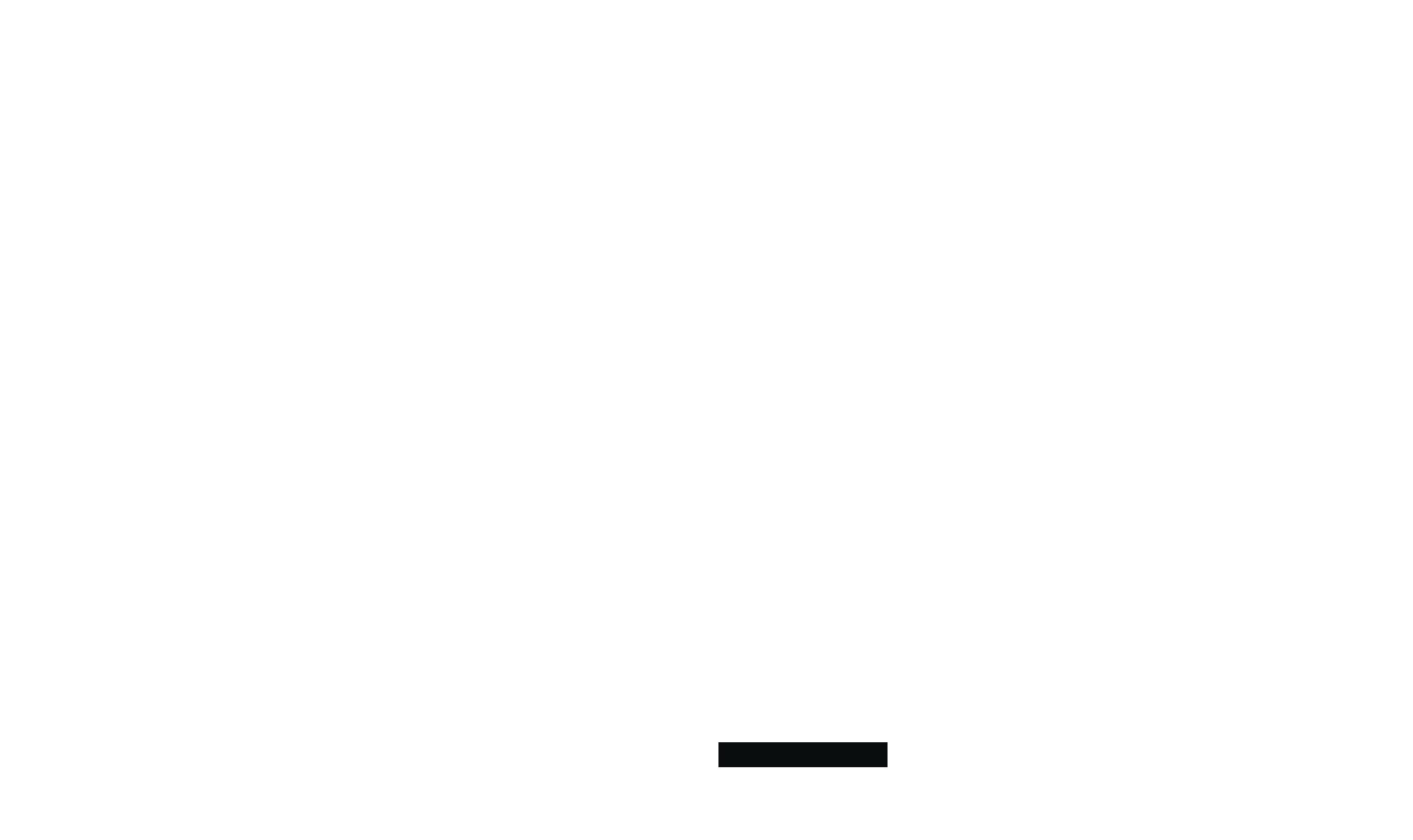

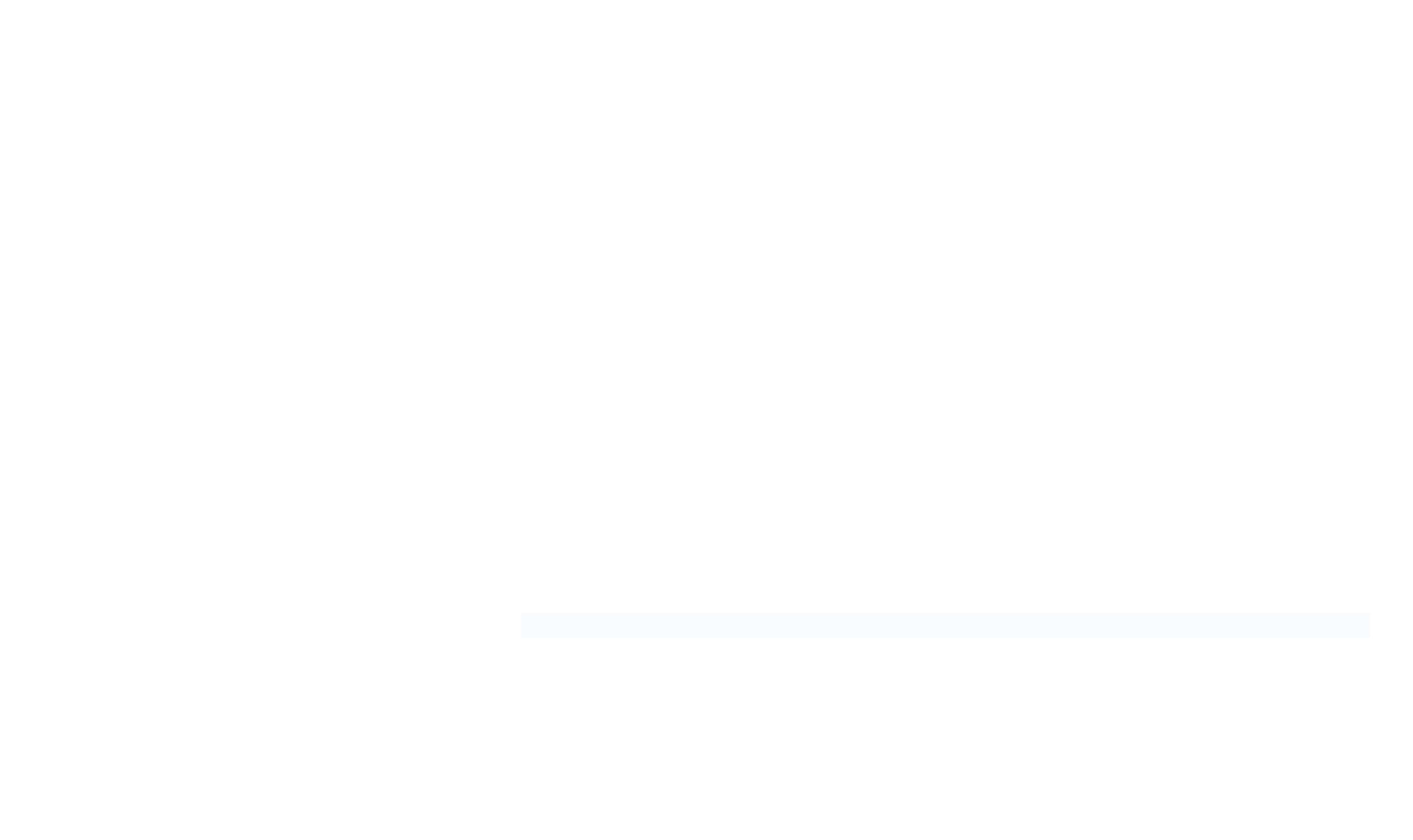

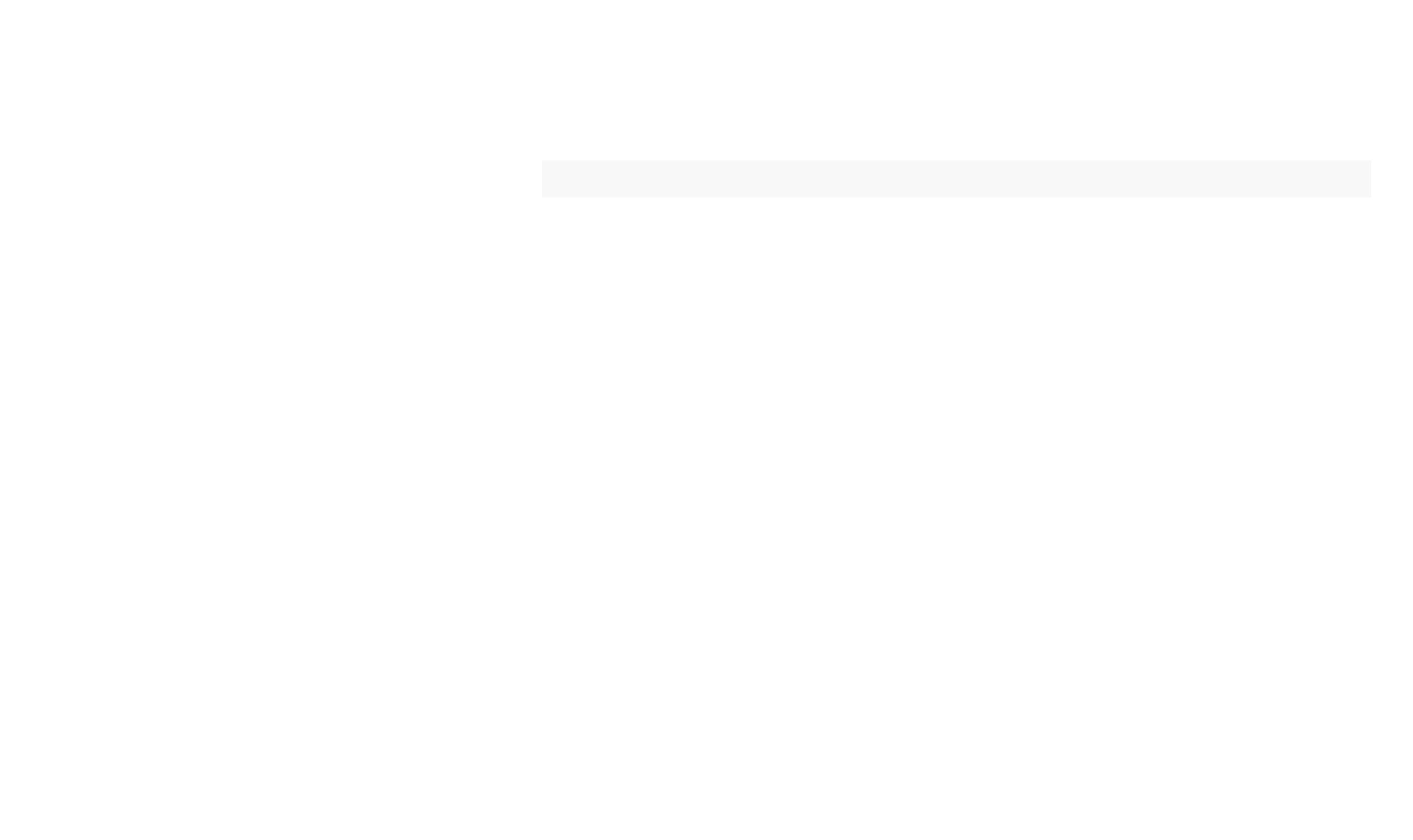
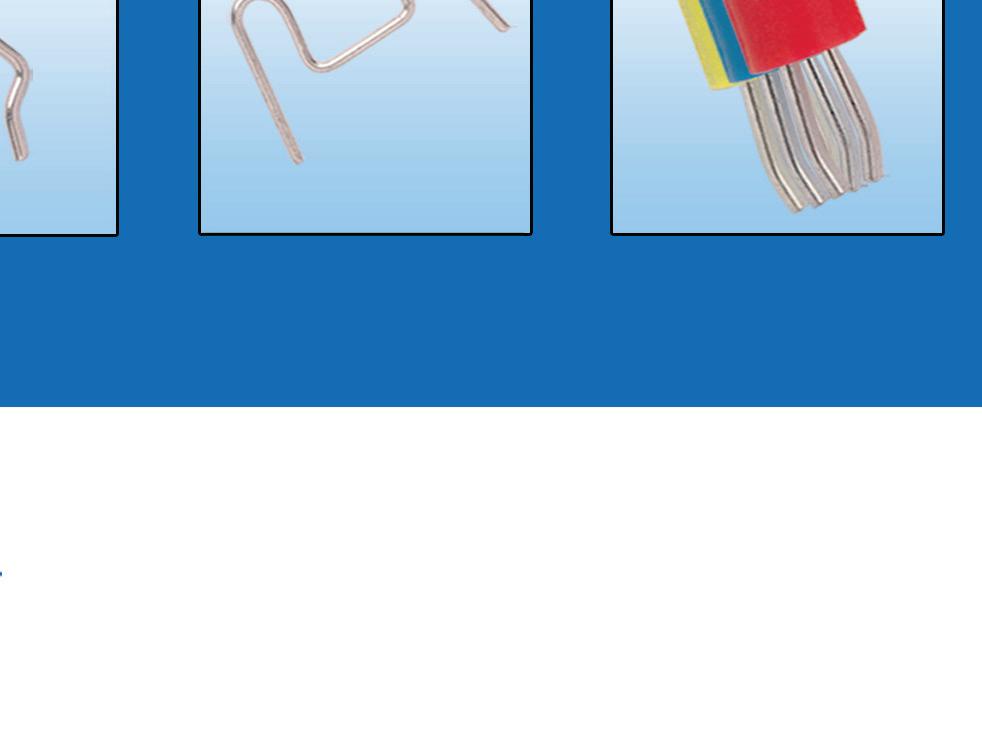
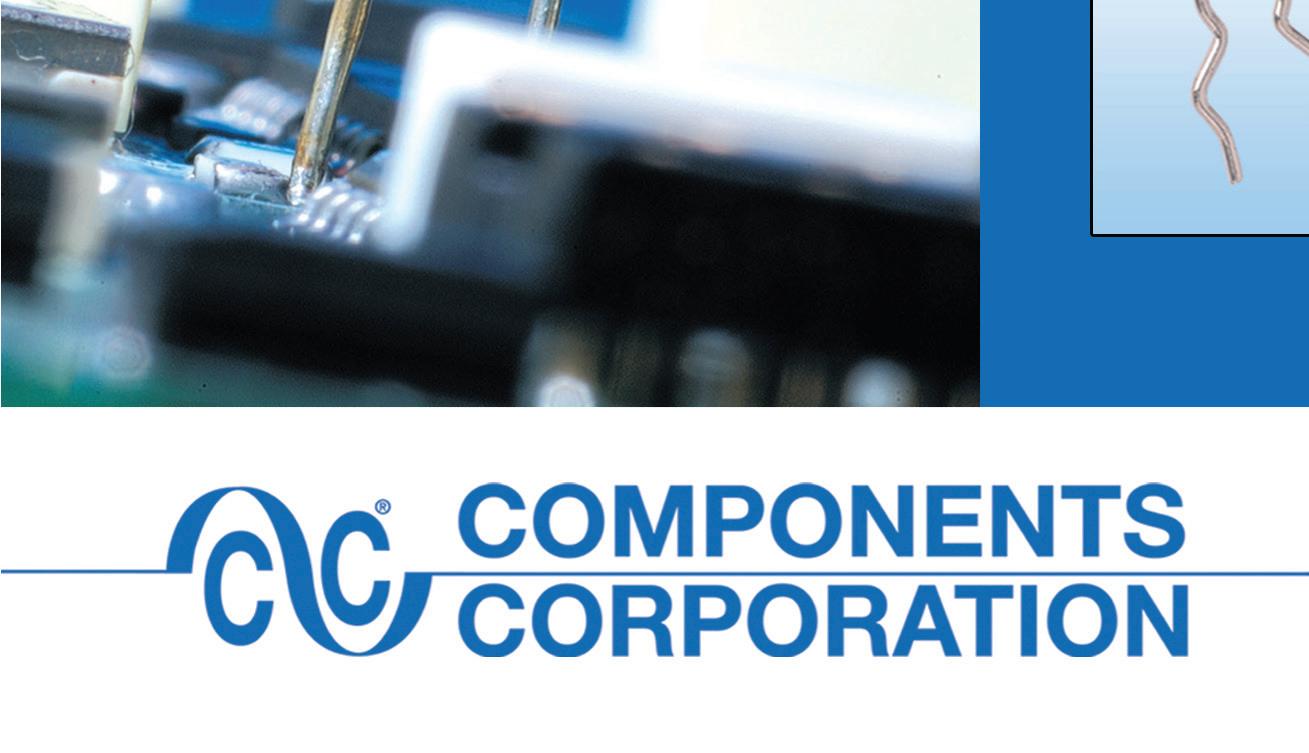
PCB Test Points • Preform Jumpers • Battery Contacts • Card Edge Connectors • Custom Wireform Manufacturing
6 Kinsey Place, Denville, NJ 07834-2692 866-426-6726 www.componentscorp.com
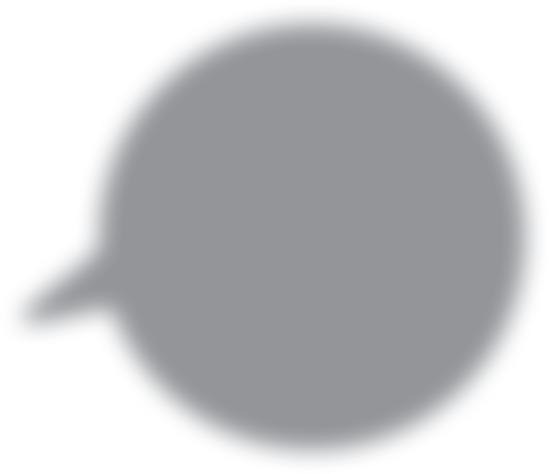
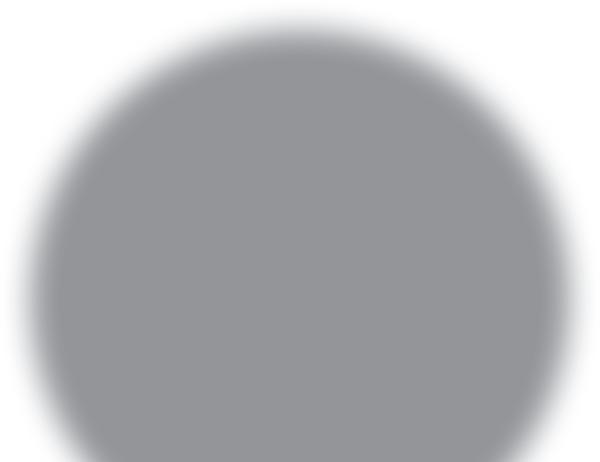
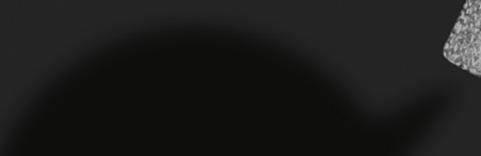
Flexible 3D Printed Inner Liners
The inner liner is an essential part of the prosthesis, and the socket must be comfortable to the wearer while working or during prolonged hours of use. Moreover, it must be breathable to ensure good hygiene. “We need to make sure that the prosthesis breathes, especially in the jungles of Guatemala,” said Wright. However, traditional gel-like inner liners are not very breathable, cost more than $160, and have a limited life span of only 3 to 6 months in the tropical climates of Guatemala. This cost is prohibitively expensive. Brent’s team wanted to replace the costly liners with knitted socks. Socks are very aff ordable, breathable, easily customizable, and washable. To ensure comfort, the team turned to 3D-printed foams to design a fl exible inner socket liner. 3D-printed foams are fl exible lattice structures that imitate the properties of traditional foams. They are manufactured om an elastic material like TPU and off er additional benefi ts over conventional foams. For example, their properties can be tuned ( om so foam to stiff plastic) according to the physiology or preferences of the patient. This eff ect can be achieved by closely controlling the design input parameters of the lattice, such as beam thickness and porosity, using advanced engineering design so ware like nTopology.
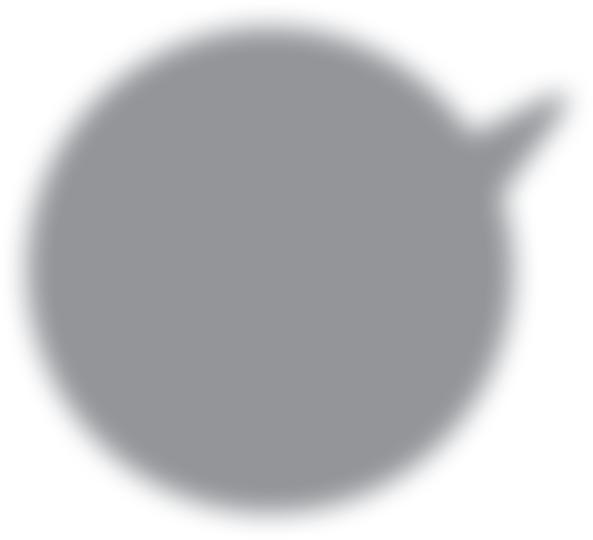
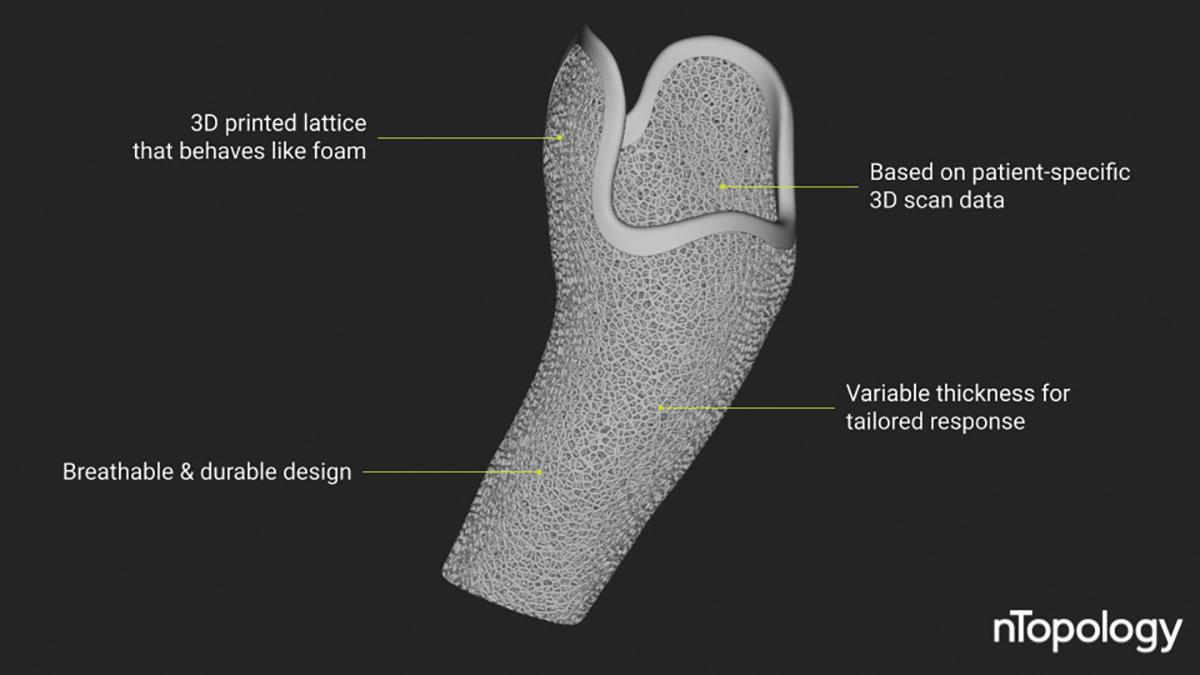
From 3D Scan to Manufacturing
Even a er the team has determined the 3D printed foam design parameters to achieve the desired cushioning, applying it to 30+ custom socket designs would be a challenge. Without nTopology, this step would be a “brutal process,” according to Wright. The legacy so ware he was using before nTopology would o en crush or take hours to generate a result. “Designing custom fl exible inner liners was going to be a challenging task if we would do it in any other so ware other
The fi nal design of one of the 30+ custom-made
fl exible inner linings — designed in nTopology..
Overview of the design process in nTopology
— from importing a 3D scan mesh to exporting a manufacturing-ready 3MF mesh fi le.
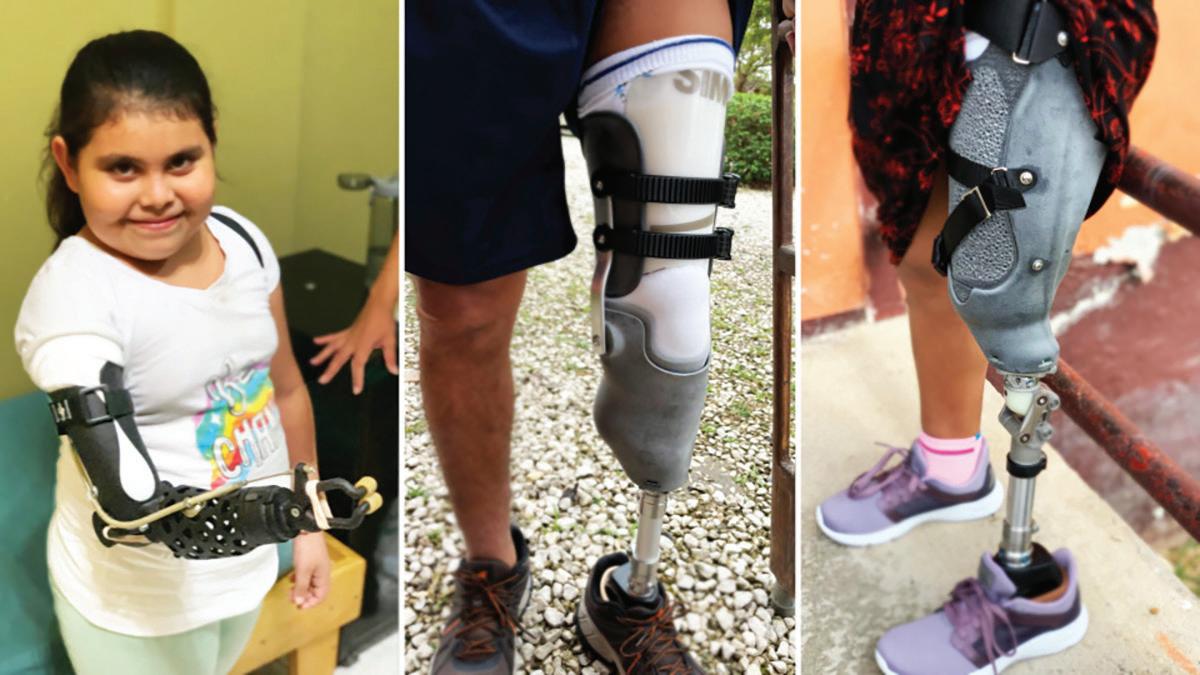
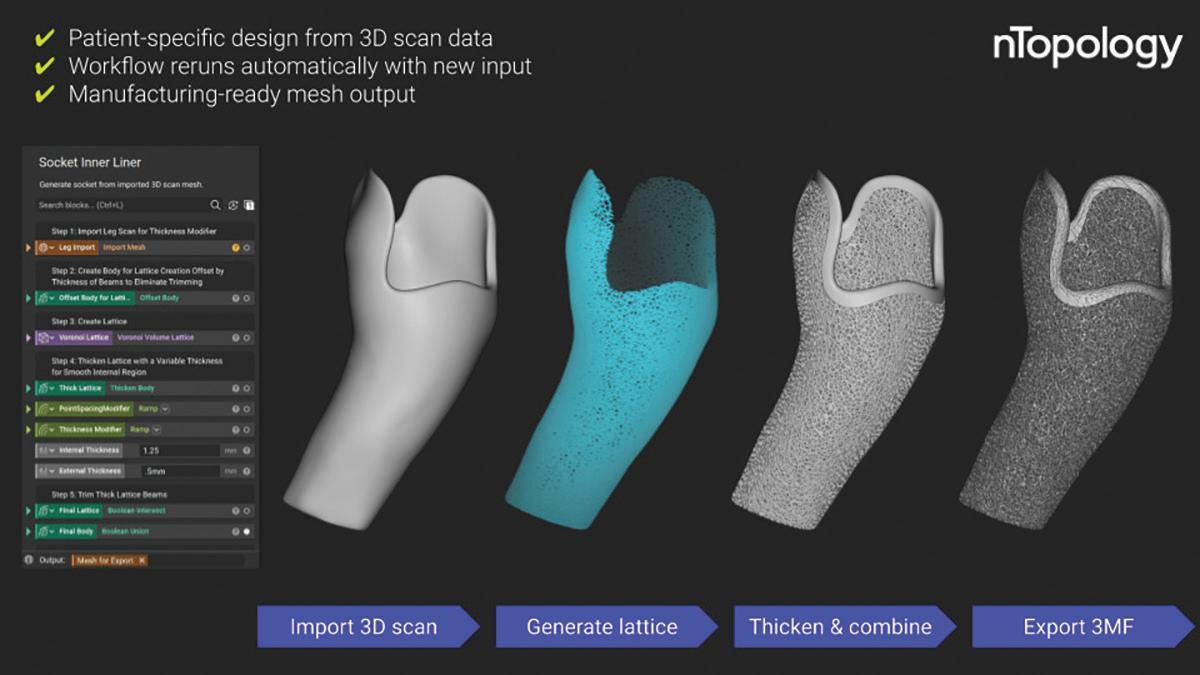
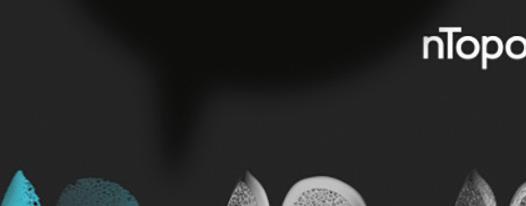
Three of the 30+ patients fi tted with their new 3D printed prosthetic devices.
Design Notes
than nTopology. Once the workfl ow was done, all I had to do was to swap out meshes. The process ran over and over again,” said Brent Wright.
The workfl ow is semi-automated and straightforward to implement. Here’s the overview: • Using the mesh of the patient’s 3D scan data as input, they fi rst generated a shell with variable thickness. • They then used nTopology’s latticing blocks to create a fl exible inner liner that provided the necessary level of cushioning. • To repeat the process and generate a new design, they only had to swap in a new input mesh with 3D scan data om another patient. With nTopology’s reusable workfl ows, the team saved more than a whole day of error-prone computational processing during the design phase and produced higher-quality and error- ee results. For manufacturing, the team opted for HP’s Multi Jet Fusion 3D printing process in TPU. This process and material combination is excellent for manufacturing fl exible lattice structures with variable thickness for padding. TPU is also very durable, making it a good option for the jungle of Guatemala. This digital process saved the team 2-3 days of fabrication and replaced a laborious manual step with streamlined digital manufacturing. Wright’s goal is to create a global network of prosthetic device providers for the developing world. With digital manufacturing and engineering design tools like nTopology, this dream is achievable. There are multiple industrial-grade 3D printing systems located worldwide (even in developing countries) that could be leveraged to manufacture the needed prosthetic devices. Local physicians can be trained through video calls to evaluate the patient and fi t the prostheses. As for the design of the device, this can be generated using the automated processes that Wright’s team has developed. DW
LifeNabled lifenabled.org
nTopology www.ntopology.com

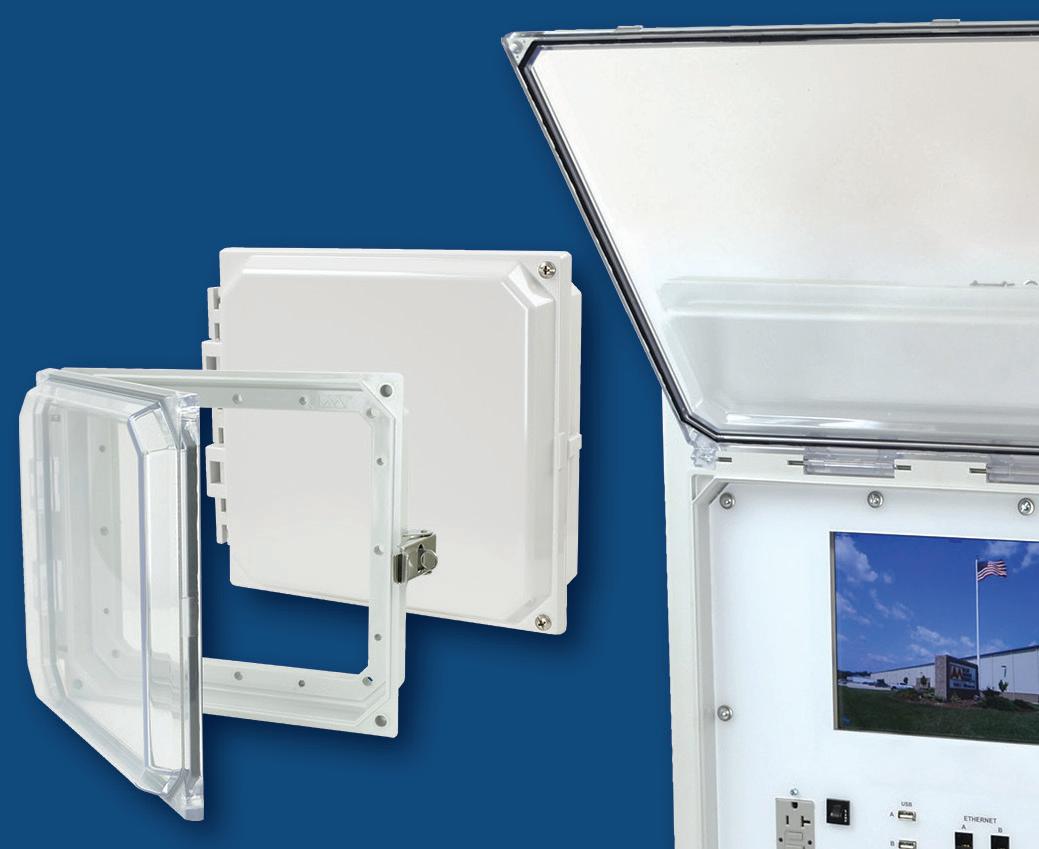

Wants and Needs ALIGNED

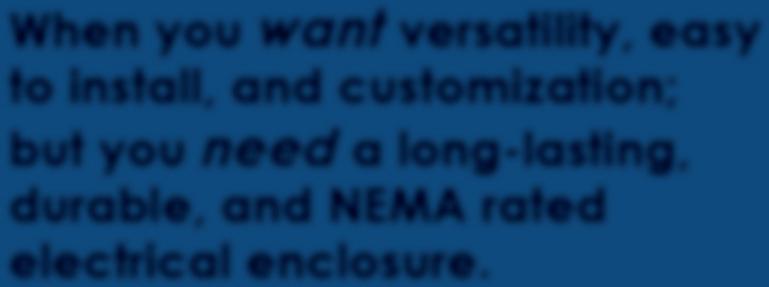
When you want versatility, easy to install, and customization; but you need a long-lasting, durable, and NEMA rated electrical enclosure.
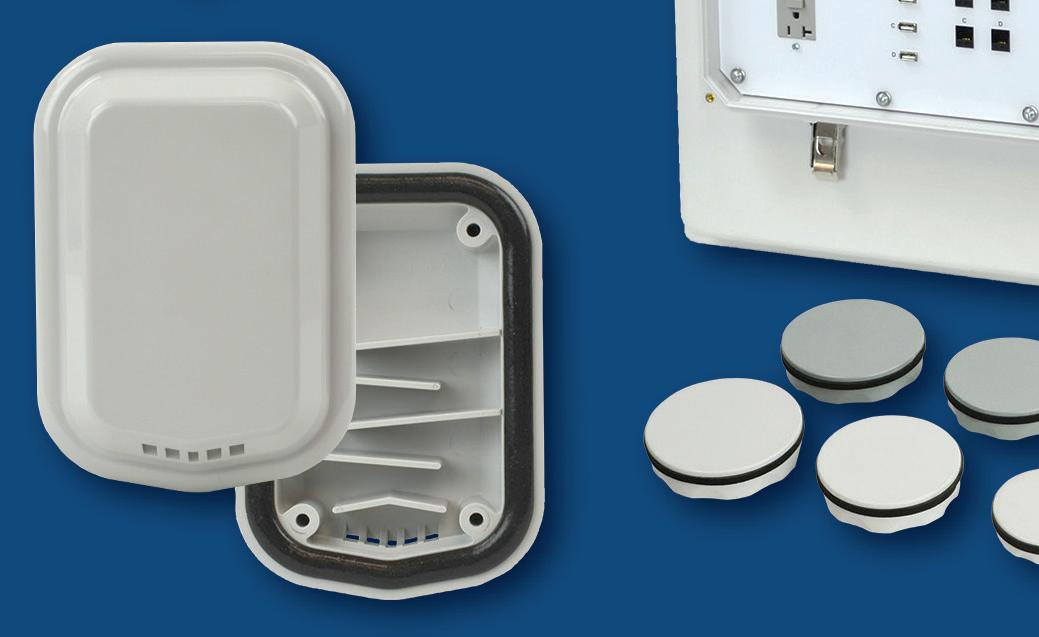
Silk Screening HMI Cover Kits & Prop Arm
NEMA 4X Vent Kit

222 North Union Street • Bryan, Ohio 43506 Ph: 800-722-2679 • Fx: 800-237-7269
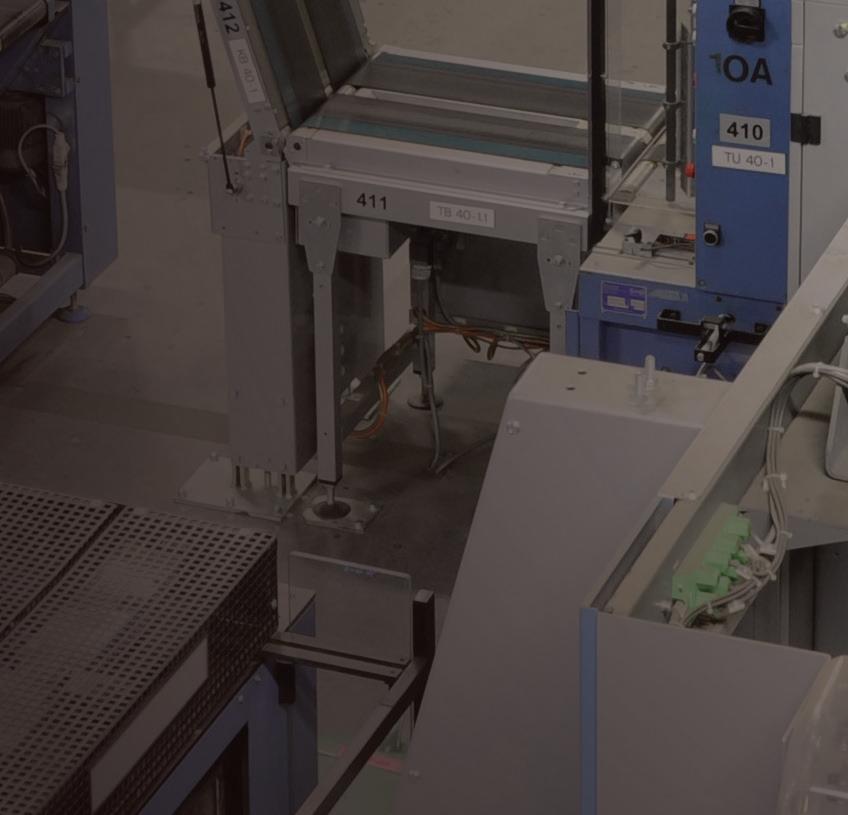
© 2021 Allied Moulded Products, Inc.
Modifications include:
-Custom holes & cutouts -Color Matching -Silk Screening
ULTRAPLUG® Hole Plugs