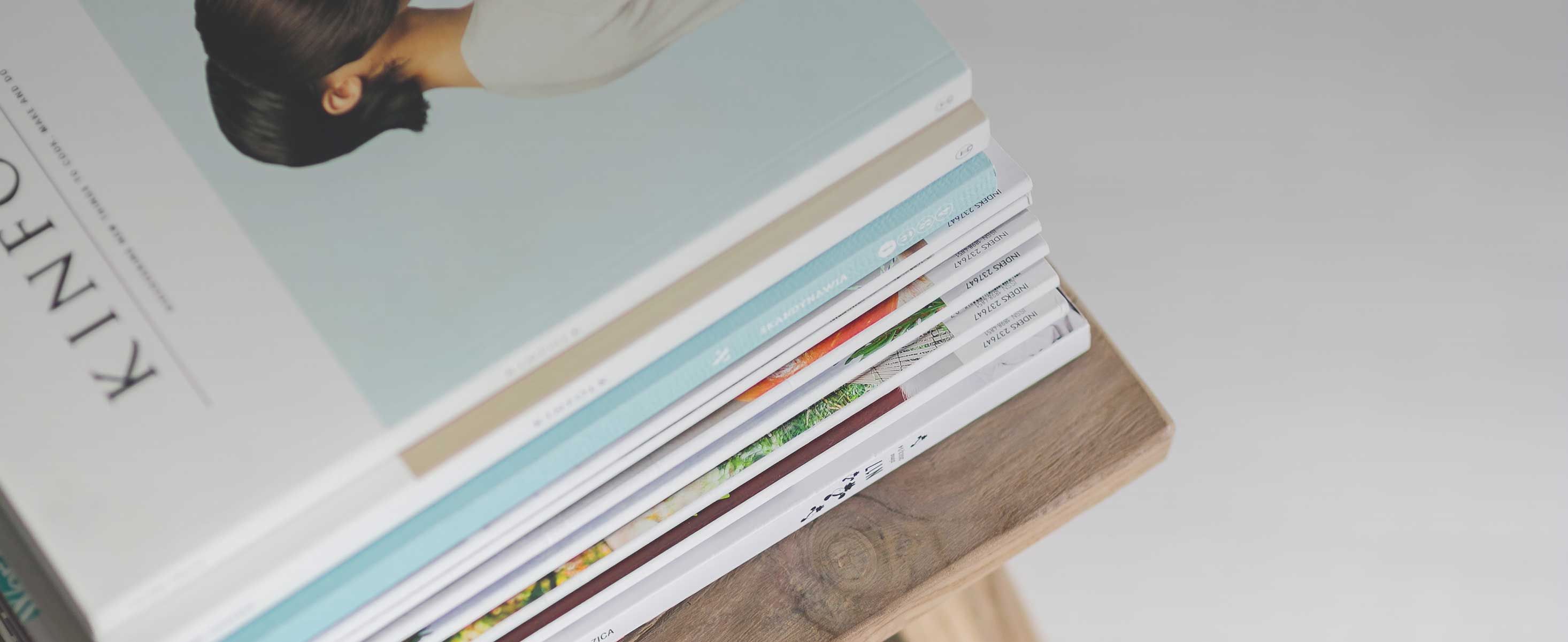
6 minute read
4.2 Aggreko’s installed capacity, by geography
FIGURE 4.2
Aggreko’s installed capacity, by geography
Advertisement
Percent of total, number of projects
South America, 4%, 4 Africa, 2%, 6
North America, 18%, 30
Eurasia, 56%, 41
Middle East, 17%, 2
Europe, 3%, 19
Source: World Bank, based on Aggreko’s commercial literature.
tons per day oil treatment plant. To address these objectives, Aggreko proposed a long-term contract with 58 megavolt-amperes of total power capacity, which assumed supplying all necessary spare parts and materials, as well as performance of scheduled technical works. Equipment includes eight transformers with a unit capacity of 6,300 amperes, two fuel tanks of 20,000 liters each, one load bank of 1,266 kilovolt-amperes, and 13 kilometers (km) of cable to ensure a stable power supply during the drilling and operation of oil wells. The project’s capital expenditures (capex) and operating expenditures (opex) are assumed by Aggreko.
The project is an extension of a smaller project that began in 2016 and grew in scope over time. Aggreko is responsible for ensuring commissioning and round-the-clock maintenance of the generator sets and utility networks. The company delivered equipment on-site and installed and commissioned it within 30 days from the date of signing the contract, which enabled the field operator to obtain power for progressive production of raw materials, start work promptly, and operate the field one year earlier than initially planned. The remote location of the field and freezing temperatures (which required upgrades to normal winterization equipment) were part of the technical challenges.
The project was initially designed to work on natural gas supplied at high pressure, so Aggreko built a pressure reduction unit. The plant was later modified to allow working directly on associated petroleum gas supplied at normal pressure, thus providing fuel flexibility to the operator.
The project is estimated to achieve more than 120,000 tons of carbon dioxide (CO2) emissions reduction per year and is securing supply of power to the operator.
The Yuzhno-Priobskoye Field
The Yuzhno-Priobskoye Field in Russia is an oil field in Western Siberia and is currently operated by Gazpromneft-Khantos LLC, a subsidiary of Gazprom Neft. The field’s estimated flare is more than 30 million m3 of associated gas per year.
The operator had a dual objective: to reduce flaring and to reduce the cost of power generation needed for upstream facilities, which usually account for up to 40 percent of production costs. To address these objectives, Aggreko supplied 24 megawatts (MW) with a significant guaranteed discount to grid price level as the turnkey project, without capex investment for the operator. The development and commissioning works were carried out by Aggreko, which will also provide maintenance services for the power plant throughout the seven years of the contract term.
The project was initially designed to work on stripped gas but, after an additional request from the customer, was later upgraded to allow consumption of associated petroleum gas, thus providing fuel flexibility to the operator.
By selling part of the associated gas to Aggreko, Gazpromneft-Khantos addresses the need to eliminate flaring at the Yuzhno-Priobskoye Field. The power plant operates in parallel with the grid, thus ensuring reliability of power supply.
This project is estimated to achieve more than 60,000 tons of CO2 emission reduction per year and is securing the supply of power with competitive prices.
The Sredne-Nazymskoe Field
The Sredne-Nazymskoe Field is an oil field located in Western Siberia, Russia. The field is currently operated by RITEK LLC, a subsidiary of PJSC Lukoil. The field’s estimated flare is about 3 million m3 of associated natural gas per year. The field’s operator had a dual objective: to eliminate flaring and to reduce the cost of power needed for its operations by replacing diesel with the less-polluting natural gas.
To address these objectives, Aggreko built a power plant with 8.7 megavolt-amperes of gas power capacity, two transformer substations, and one switchgear. An additional feature of the solution is a super capacitor, which allows for stabilization of the frequency and voltage in the network in case of sudden changes and fluctuations in electrical power consumption required for drilling operations. The operator’s up-front cash outlay was limited to mobilization cost, and Aggreko ensured all capex and opex associated with the project.
By eliminating flaring, the project is estimated to achieve more than 5,000 tons of CO2 emission reduction per year and is securing the supply of power to the operator. Additional emissions reductions due to fuel switching were not quantified. Power cost savings were estimated at 50 percent on account of fuel switching.
Middle East Project
Aggreko is engaged in an FMR project in the Middle East that is operated by an international oil major. The field is estimated to flare about 1.1 million m3 in years 1 and 2, possibly reducing thereafter. The gas requires pretreatment and NGL stripping. Because of emissions limits and potential fines for
noncompliance, the field’s operator was unable to expand production over 30,000 barrels per day because such expansion would have resulted in additional flaring. Furthermore, the operator wanted to maximize the use of available gas for power by the local government. The operator thus had an overarching objective to increase production and deliver power at competitive rates to the local grid.
Aggreko developed and financed the project from concept to mobilization, commissioning, and operation to deliver a turnkey solution for the operator. The fleet and infrastructure employed are worth over US$50 million. The project required a new 6 km pipeline from the flare stack to the Aggreko site, along with full gas treatment and an NGL production plant, four 50 megavolt-ampere transformers, switchgear, 7 km of new 33 kilovolt (kV) overhead transmission lines, and an upgrade to an existing 33km of 132 kV transmission lines—all within Aggreko’s scope.
Aggreko installed 150 MW of power generation capacity based on its 1 MW mobile and modular gensets, which were used because of their ease of mobilizing and demobilizing, and low derating factor at high temperatures. At the time of writing, 100 MW is already operating. The gas pipe, treatment infrastructure, and power connection will be transferred to the customer at the end of the project; but all power assets remain Aggreko’s property and will be demobilized at the project’s conclusion or in stages as gas volumes deplete.
Given regional instability, specific regulatory challenges in the country, and the difficulty of enforcing contracts, it was important for Aggreko to engage in tri-party discussions with the operator and utility operator. The project helped the customer offset the need for additional capacity by saving 840 tons of CO 2 per day. Socioeconomic cobenefits also resulted from the project, such as delivering 150 MW of power onto the local grid, stabilizing supply, reducing cost, and reducing the local dependency on expensive high-emissions liquid fuel plants.
Takeaways
Oil companies value the ability of FMR developers to provide turnkey solutions in a noncore activity such as flare reduction. Aggreko owns the power generation equipment it installs and puts its balance sheet to work to build necessary infrastructure (gas treatment, gas connection, overhead power lines)— eliminating the need for capital investment on the part of the oil company. To support its business model, Aggreko has set up a specialist gas-to-power division to lead design, engineering, operations and maintenance, and, where appropriate, the sale of power to third parties. The operator obtains power at a discount relative to diesel generation or, depending on the location, expensive power from the grid (as is the case in Western Siberia).
Speed of deployment and the flexibility of the equipment installed can be critical in persuading oil companies to outsource FMR to independent developers that can mobilize their fleet of generation sets quickly, and also to remote locations. The use of modular equipment allows FMR projects to expand or shrink, seconding the production dynamics of the field and associated gas as well as the level of power demand from the operator or third-party off-takers where applicable. This aspect is important because volume and specification of gas are rarely known at the project design phase, and they can change over the life of the field.