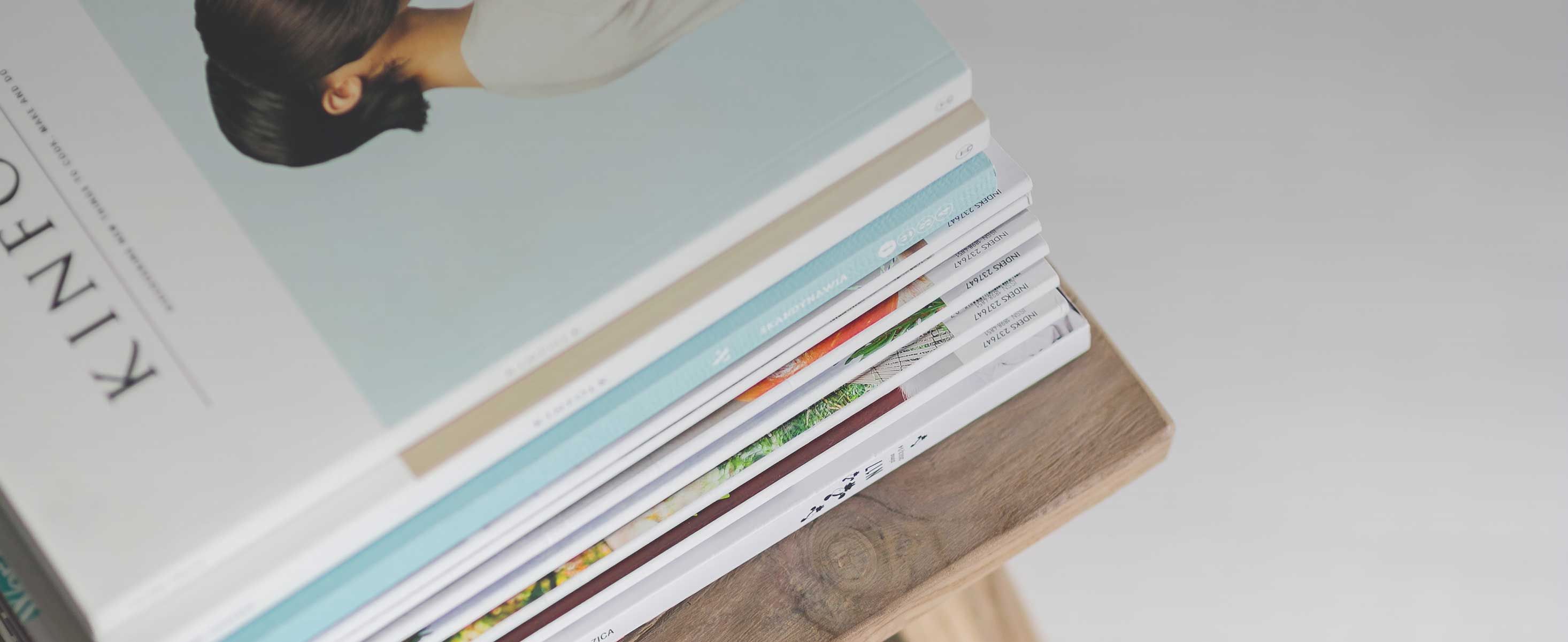
5 minute read
Impact of New Technologies on Labor Demand in South Asian Countries
The deployment of technologies in production may replace or complement human labor, but many other factors also affect overall labor demand. Morover, technology adoption is itself driven by a large number of factors, and the impacts on different countries will depend on their sectoral composition, the relative cost of labor to capital, and the extent of competition from other countries.
To accelerate development, emerging economies need to leapfrog industrialization to the high-tech economy (UNCTAD 2021). Leapfrogging will require prioritizing investments in people for the acquisition of higher-level skills, but it also will, in turn, create more demand for jobs in the local service economy. In South Asian countries with large shares of youth, there is heightened urgency to provide youth and migrant workers from disadvantaged groups with a mix of hard and soft employability skills so they can reap the benefits of demographic dividends. To combine human intelligence to innovate with the computing power of machines, the workforce would have to acquire twenty-first-century skills such as critical thinking, creativity, communication, collaboration, problem-solving, cross-cultural literacy, work ethic, empathy, and socioemotional and digital intelligence.
Advertisement
COVID-19 has exposed the fragility of the world’s supply chains for medicines and medical products, food, energy, vehicles, telecom equipment, electronics, and countless other goods and services. In response, certain companies, notably early adopters of Fourth Industrial Revolution technologies, have begun to reconfigure their sourcing and manufacturing footprints for greater reliability and resilience. Others are accelerating the adoption of digital work instructions, augmented reality-based operator assistance, and simple, inexpensive retrofit automation. This reorganization of production patterns, which is being accompanied by increasing servicification of supply chain networks, can either increase or decrease the number of jobs. For the South Asia region, developing globally competitive manufacturing hubs is one of the biggest opportunities to operate in international markets, double its manufacturing gross domestic product (GDP), create new high-value service jobs, and provide long-term employment and skill pathways for millions this decade.
How can India, in particular, and the subregion, as a whole, take advantage of these shifts? Mature value chains (such as pharmaceuticals, automotive components, fast-selling technology products, and software) and service sector jobs (such as health care, tourism, financial services, logistics and supply chain coordination, information technology outsourcing, and creative industries), both of which rely on sophisticated capabilities and healthy supplier ecosystems to serve domestic and export markets, must scale up. A second group of value chains, which mainly produce for domestic markets (such as food processing) but lack scale, productivity, and technological sophistication, must transform to compete. Finally, entry into emerging value chains (such as the “sunrise” sectors in energy storage, electric vehicles, and the bioeconomy) will require strategic partnerships with global consortia to access the technology and capital needed to establish local manufacturing capacity. Although the unique circumstances of the pandemic have elevated
resilience, agility, and flexibility in operations as top strategic priorities, the medium-term agenda for the South Asia region will be to lift the productivity of manufacturing value chains to global standards.1
Meeting the growth in the domestic and global demand for products tends to increase the demand for jobs. In a recent study, the Asian Development Bank decomposed these factors and found that between 2005 and 2015 the introduction of new technologies displaced 60 percent of jobs in Bangladesh and 40 percent of jobs in India (the only two countries covered in the study) (ADB 2018). However, the demand for new jobs increased by 80 percent, primarily because of the increase in domestic demand (figure 4.1).
Looking forward, will the ongoing technological revolution have an even more profound impact on job displacement, including net task relocation away from South Asia? And can post-COVID-19 growth in aggregate demand offset not only temporary but also structural job losses? A particularly worrying aspect of the COVID-19 pandemic is that young people, trainees, and fresh graduates are disproportionately hit by joblessness because many companies are retaining experienced employees and have cut back on hiring.
Estimates of potential job losses and displacement are relatively scarce and variable for the South Asia region. Several estimates for India indicate how the adoption of technology and its impact on jobs can vary substantially across different industries. The World Bank’s World Development Report 2016: Digital Dividends estimated that 69 percent of jobs in India were at risk of being automated, although this rate dropped to 44 percent when adjusted for potential adoption speed (World Bank 2016). Other analyses carried out by the International Labour Organization (ILO) and the Organisation for Economic Co-operation and Development (OECD) for India suggest that capitalintensive manufacturing industries (such as the automobile industry) are more likely to adopt advanced automation and robotics (ILO 2018; OECD 2020). Although this industry had the highest employment growth rate over the last decade, it still employs only a relatively small share of the labor force. In the informal sector, where over 80 percent of the labor force is employed, the adoption of advanced technologies is impeded by lack of financial capital and necessary skills. The agriculture sector, which is the largest employer in India, has high automation potential (using the Internet of Things, digital platforms, and data analytics) to improve productivity, but low growth in the sector and the shrinking size of land holdings make widespread technology adoption unlikely. Labor-intensive industries (such as textile, leather, and footwear) are unlikely to be rapid or large-scale adopters of Fourth Industrial Revolution technologies because such technologies require dexterity, labor cost advantages, and high capital investment.2 A potential risk for jobs is that major brands in the ready-wear garment industry may relocate their manufacturing hubs to speed up product-to-market cycles, facilitated by developments in automation, a trend that has picked up momentum during the pandemic.
Although it is unlikely that large-scale adoption of technology will occur in the informal, unorganized sector where a majority of women and the poor are employed, this sector could both benefit from and be negatively affected by diverging trends in the