
20 minute read
FMI Zero Energy homes still well ahead of the updated code
A new Code in town
The good news, as many of you know, is that MBIE issued an update to the H1 energy efficiency section of New Zealand’s building code, effective from late November 2021. For housing and small buildings, it boosts thermal performance by increasing insulation and glazing quality in new builds.
Advertisement
The consultation process for the update garnered almost 700 submissions for the housing and small buildings section, an unprecedented level of engagement. The Outcome document1 reported “overwhelming support for change” with a key feedback theme that the changes were “long overdue”. At FMI we say the same! Every house we build or retrofit to less ambitious emissions targets than the industry is capable of delivering locks us into suboptimal performance for upward of fifty years of the building’s life. We also agree with comments by Jason Quinn from Sustainable Engineering on the update:
It’s not perfect, it’s too slow, it needs to go further—but it’s the first step in a planned transition to the far better buildings we need to address climate change and improve people’s health and comfort.2
The theme of respondents wanting bigger and quicker changes had also come through in earlier feedback on MBIE’s Building for Climate Change proposals that sought to address operational and embodied emissions in the building sector. In the Summary Report’s3 own words:
There was support for the Framework’s scope to be wider and timeframe more ambitious A sense of urgency was prominent throughout many responses.
In fact, 55% of respondents wanted the operational efficiency requirements to be implemented ahead of the proposed 2035 timeframe. Many respondents referred to the long planning time frames that construction projects typically run on, meaning positive impacts from any new regulations would have an inherent delay.
For those of us passionate about lifting the efficiency and healthiness of New Zealand homes, the H1 update helps our cause, even if we wish it had gone further and faster. The cost premium to build a better home than mandated by the code is now lower. The premium for our FMI Zero Energy / Ready (FMI ZE/R) home was only 4-6% more than the old Code, but it will now be even less, weakening a common objection to building better.
Encouragingly, the outlook is for the premium to shrink further. The recent update is merely the start of emission reduction changes signalled in Building for Climate Change. We are finally moving along a track towards affordable, high-performance homes that benefit residents and the environment. The approach to such dwellings can vary, from FMI’s Zero Energy design to the currently better-known Passive House, but they draw off similar tools, concepts, and concerns, many of which have yet to be reflected in the construction guidelines for New Zealand homes.
1 https://www.building.govt.nz/assets/Uploads/building-code-compliance/building-code-updates/outcome-consultation-building-code-update-2021.pdf 2 https://sustainableengineering.co.nz/analysed-h1-code-changes/ 3 https://www.mbie.govt.nz/dmsdocument/14726-building-for-climate-change-summary-report
More climate zones
The update has increased the number of climate zones that impact H1 building code standards from three to six, as shown in Figure A. About 60% of New Zealanders live in Zones 1 and 2. Of our major centres, Auckland is in Zone 1, Wellington in Zone 3, and Christchurch in Zone 5. Queenstown is typically used to model the coldest climate in Zone 6. The aim of more climate zones is to “allow the insulation requirements to better reflect the different temperatures experienced in each zone”.
The zone definitions are not an exact science, however. For administrative reasons, the proposed zones were bent around territorial authority (TA) boundaries. Two TAs pushed back during consultation, seeking a zone split between their coastal and alpine regions to better achieve the aim of the exercise. BRANZ’s analysis4 of the demands of the six zones on home heating and cooling also identified some cases that were hard to classify, including the country’s fourth and fifth largest centres of Tauranga and Hamilton. Nevertheless, the Outcome document stated that the majority of respondents were in favour of the principle of more finely sliced and diced climate zones. At FMI we beg to differ, even though we accept we are in the minority. In all FMI’s submissions concerning proposed changes to reduce emissions and enhance residential building quality we have consistently pushed for simplicity. Specifically, we remain in favour of one set of H1 performance measures across the country. We would rather “gild the lily” in warmer zones (noting that the energy savings of FMI’s Zero Energy home produce an attractive NPV regardless of “gilding” in Zone 1) than navigate a regional variety of performance standards with attendant compliance checks.
In our calculations for the previous issue of Fenestration New Zealand, we found our FMI Zero Energy home had an initial build premium of $34,000, almost exactly the $33,000 amount spent on Preliminaries that encompassed design and professional fees, consent fees, development contributions, service connection fees, and essential testing such as Geotech and structural. The more finely MBIE sets standards, the greater the burden on many of these upfront costs.
FIGURE A:
Past versus Newly Adopted Climate Zones
4 https://www.building.govt.nz/assets/Uploads/building-code-compliance/background-report-on-h1-energy-efficiency-branz.pdf
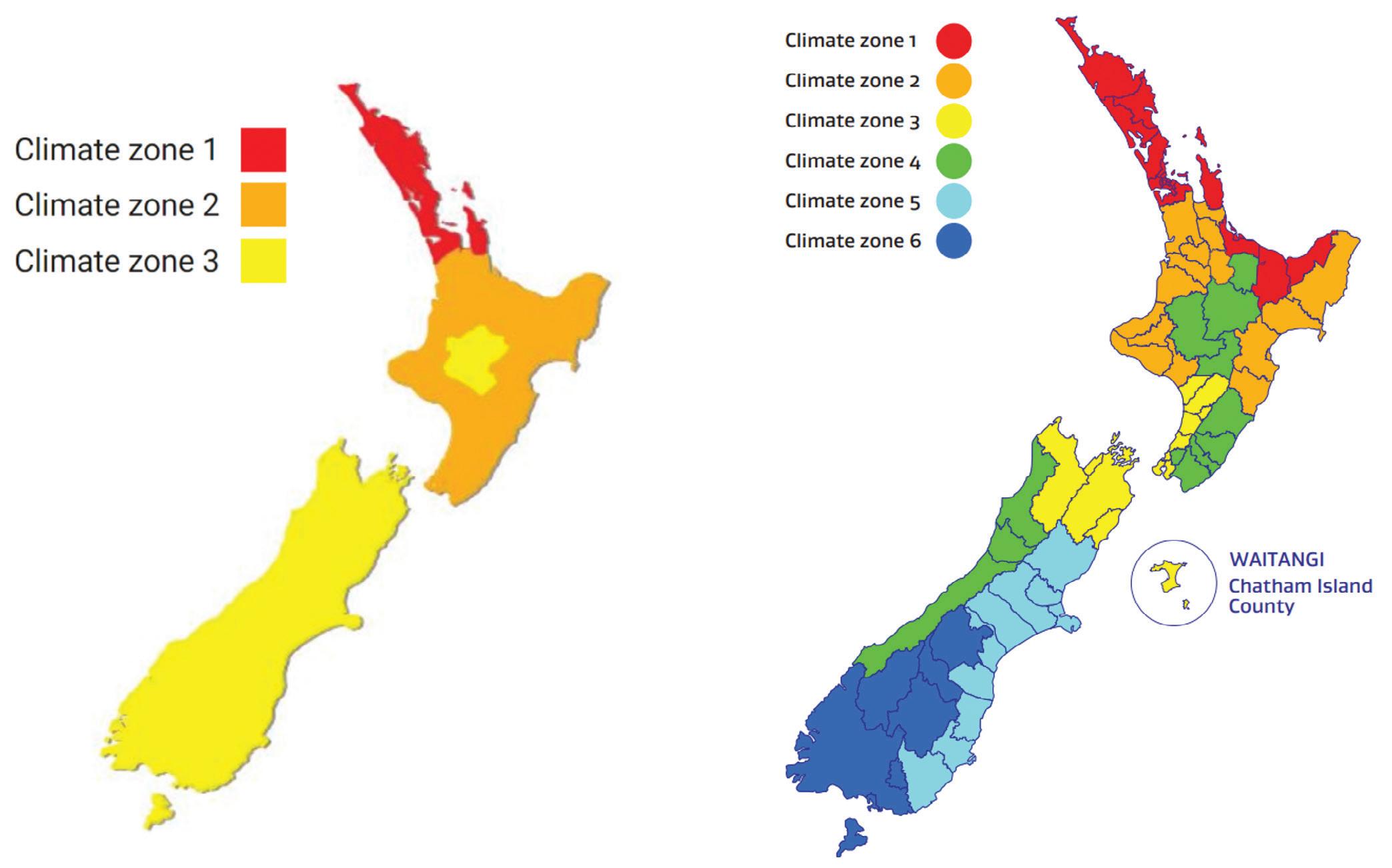
So many permutations
Building a house is already a complex undertaking in New Zealand. Beyond H1, many other building standards are already in place, relating both to macro/ regional and micro/ site-specific conditions. Each variable places a demand on the complexity of the design and building processes.
We did a quick reckoning of the many zones and classes that affect broad swathes of the code for timber-built homes. In addition to the now 6 climate zones, we found:
• 4 earthquake zones
• 3 corrosion zones (actually 4, but 3 and 4 are treated alike)
• 6 snow load zones
• 6 wind zones calculated based on yet more factors: o 2 wind regions including Lee areas o 4 topography classes o 2 ground roughness classes o 2 site exposure types
…producing almost 2600 potential permutations – which would “only” have been 1300 or so if the climate zones had not doubled. This high number is before the many other considerations such as the need to build on good ground, to assess natural hazards like flooding and erosion, to comply with restrictive aspects of the relevant District and Unitary plans etc., etc. Further, the E1 standards around external moisture demand attention to a region’s historical rainfall intensity to assess drainage and guttering needs to cope with surface water as well as adequate weather proofing to keep moisture outside the building envelope. It’s a wonder anyone attempts to build!
Ahem. Time to climb down off our simplicity soapbox and return to a calm review of the H1 update.
More insulation
Roof insulation requirements have doubled for the coldest climate and more than doubled in the warmest. Windows, acknowledged as the greatest source of heat loss with current standards and installation methods, have also seen significant increases in required performance. New builds in Queenstown very nearly double in R value for windows, while in Auckland the performance lifts by about 40% in Year 1 and 80% in Year 2 – the staggered approach is to give window manufacturers time to retool. By contrast, much less ambitious changes have been applied to walls and floor slabs.
Prioritising certain envelope components over others makes a lot of sense to us. In our first issue of Fenestration New Zealand we analysed the “bang for buck” of different components for their cost relative to their impact on energy savings. The payback was best for high-performing windows. We are therefore not surprised to see window upgrades receiving emphasis in the update. It is less clear to what extent MBIE have prioritised roofing insulation over walls and slabs because it is easy to do, with no effect on framing requirements, versus its cost effectiveness over the other components.
The higher requirements for roofs and windows are broadly in line with respondents’ preferences for significant change. 45% wanted New Zealand’s code to move up to international standards while another 45% wanted it to exceed them. At FMI, perhaps predictably, we wanted to go beyond the ‘beyond’. Generally, however, the new standards drift further away from international standards the colder the climate zone, as shown in Figures B and C.
R values for roofs in homes
FIGURE C:

R values for windows in homes

Several things have not changed with the update to the H1 clause. Output-based measures of energy performance (such as kilowatt hours per square metre) that could link to our national climate change goals are absent, though they may be introduced in a couple of years; for now, we largely remain in the world of specified inputs in the form of R values. Overheating, air tightness, thermal bridging, ventilation, and moisture concerns are acknowledged but not tackled. The core objective of the update is restricted to heating demand, yet this is only one of the three key uses of energy in the home, alongside hot water heating and plug load. For all the gripes, the new standards will yield some power savings for new-home dwellers and slightly lighten the peak winter and evening loads on our national grid. MBIE reports the changes, when applied to their Energy model of a single storey 4-bedroom house of 150m2, will save about 40% of the electricity needed to heat and cool the home to comfortable levels. The saving is consistent across all the new climate zones. Since, as a rule of thumb, heating demand uses about a third of the energy in a home, a 40% saving in heating demand could cut power bills by 10-15%.
FMI Zero Energy home remains well ahead
How much energy saving upside remains to be captured from better-built homes like FMI’s Zero Energy design? The short answer is plenty.
Recapping briefly, an FMI Zero Energy home produces as much renewable energy from solar panels on its roof as its occupants consume over the course of a year. It achieves this net zero balance via a highly energyefficient building envelope combined with the most fit-for-purpose appliances. An FMI Zero Energy Ready home is a FMI Zero Energy home without the solar panels.
Our model home is a detached, single-storey, threebedroom family home of 120m2. Passive design strategies such as optimised window placement have been avoided to keep the house looking typically Kiwi. Our house has four occupants who seek a temperature range throughout the building and across the year of 20-200C and who are frugal with hot water. All the modelling has been done by architectural engineers certified in the use of the Passive House Planning Package (PHPP).
Our FMI Zero Energy build components do not vary by climate zone, reflecting our previously explained preference for simplicity over tailoring. As we continue to learn more, however, we do amend the performance rating of our components and we try out new appliances. Indeed, the latest FMI Zero Energy/ Ready performance values are all reduced from those in the second issue of Fenestration New Zealand.
Key parameters for our latest modelling, reflecting AsDesigned R values, compared to the updated H1 clause in Zones 1, 3 and 6 are as follows in Figure D.
FIGURE D:
Insulation, glazing and key appliances by climate zone for updated code and FMI Zero Energy/ Ready (FMI ZE/R) builds
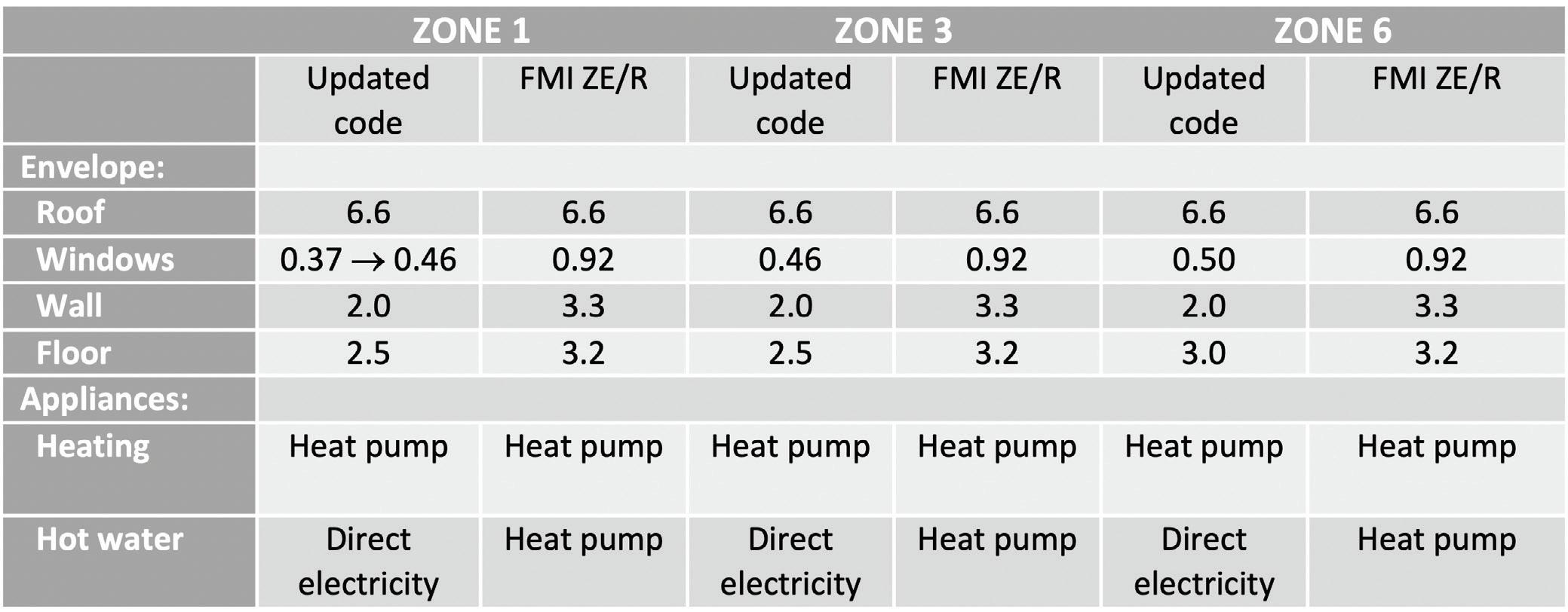
Nothing in our analyses to date has undermined our early insight that the single best investment in lifting building envelope efficiency at least cost is to install very high-performing windows. Unlike MBIE and many of the respondents to the building code consultation, FMI is confident that at least one local manufacturer can produce commercial quantities of such high performing windows…
What savings, then, does the FMI Zero Energy / Ready house produce in heating demand? Using our model, the shift from the old building code to the updated one saves about 50% of heating demand across all zones except Zone 6 where the saving is, as for MBIE, 40%. Of greater interest to us, however, is how much lower the heating demand in our FMI ZE/R home is than in the updated code. Figure E shows the savings are a staggering extra 66 – 84% depending on climate zone.
FIGURE E:
Heating demand for old and updated H1 code vs FMI Zero Energy/Ready (FMI ZE/R) build (kWh/m2)
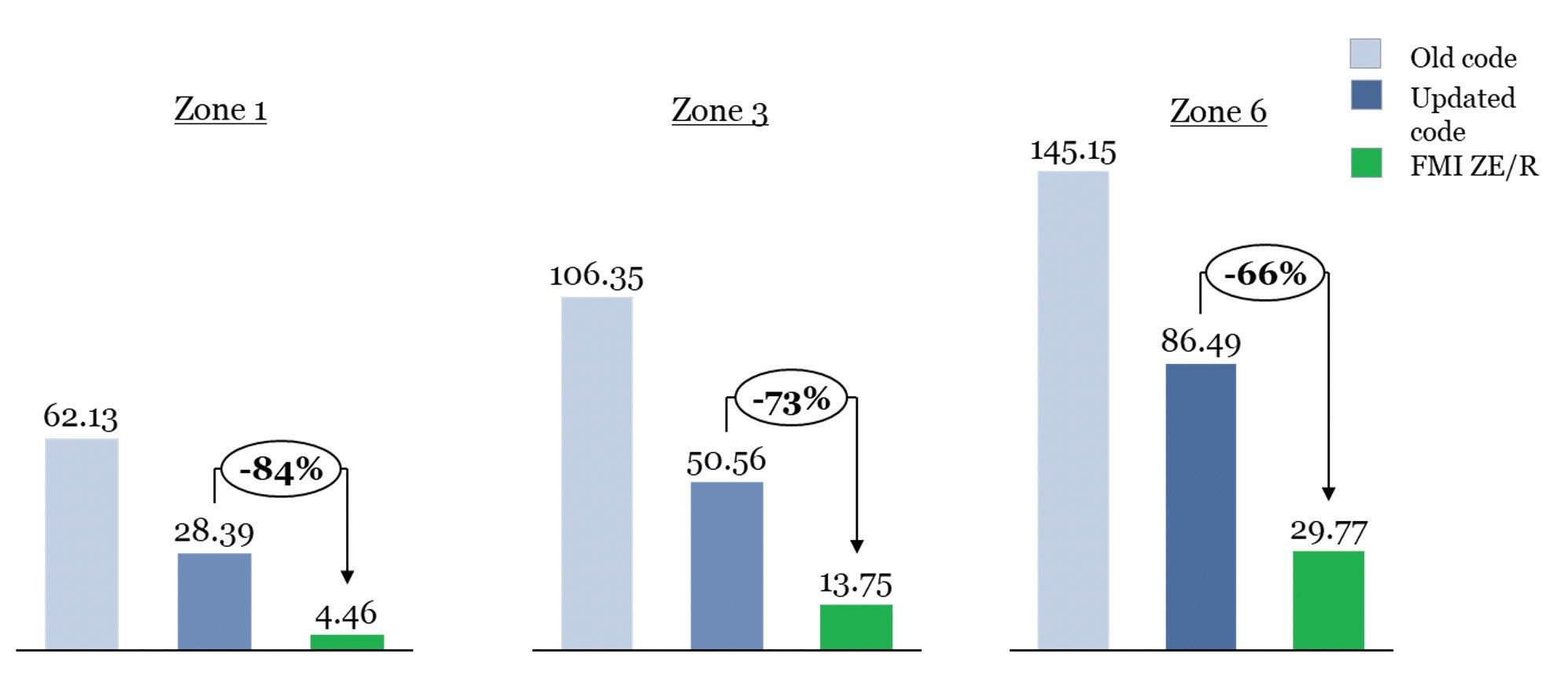
Are we there yet – Building for Climate Change?
One definition of journey’s end would be to say we are “there” if our FMI Zero Energy home performs at or below the final energy caps set out in Building for Climate Change. The caps are simple and appear to reflect some Passive House standards. No fossil fuels are to be used, and the total electricity use per square meter should not exceed 45 kWh per year. The 45 kWh splits out as:
• thermal (or heating) demand: 15 kWh p.a.
• delivered services (hot water, ventilation etc) 15 kWh p.a.
• occupant behaviour (plug loads) 15 kWh p.a.
Any on-site generation of renewable energy paired with storage counts as useful capacity that can be subtracted from the total modelled energy demand to help a home achieve the caps. Our FMI Zero Energy home is designed to generate on-site energy for immediate use – we’re not convinced about storage yet – and may qualify.

As written in August 2020, Building for Climate Change makes no allowance for different climate zones. Whether in Kaitaia or Bluff, homes are expected to meet the caps.
Figure E may seem to suggest the FMI house will come up short on the heating demand cap in Zone 6. In fact, because of the coefficient of performance (CoP) of 3.0 on the heat pump, the actual heating demand at the electricity meter is only 10 kWh/m2. In Zone 6, the cooling demand, which is not considered in the recent H1 update, is only 2.1, bringing the total space conditioning energy comfortably under the thermal cap.
For completeness, Figure F shows our modelled estimates of total electricity use for a home built to the updated code versus our FMI design. More detail is available in the table in Figure G. In each zone shown, FMI’s Zero Energy home sits below the total cap before any benefit from onsite generation. The total energy saving for the FMI Zero Energy/ Ready versus the updated code house in Zone 6 is almost 50%. It is worth noting the upside of almost 18 kWh per year (26.7 vs 8.9) that the new H1 code house could have achieved with a heat pump hot water system instead of using direct electricity.
FIGURE F:
Electricity by use for updated code vs FMI Zero Energy/Ready (FMI ZE/R) build (kWh per m2)


The key message in Figure F is that our FMI Zero Energy/ Ready homes already meet the proposed final 2035 energy caps, in all climate zones. They do this at what will now be less than the 4–6% cost premium over the old code given the increased spec embodied in the update, and the reduced spec for FMI Zero Energy / Ready shown in Figure D. All this is also before deducting power savings from the FMI Zero Energy home’s on-site generation and any income from selling surplus back to the grid during summer.

Solace -Low-E Provides Greater Insulation, More Comfort and Healthier Homes

Solace Low-E is an advanced thermal glass technology that provides year-round energy efciency and comfort. Designed to withstand New Zealand’s harsh climates.
FMI Building Innovation Unlike other glass manufacturers, we only coat Low-E on ultraclear glass so our entire Solace Low-E offering retains a high percentage of visible light transmission This means there is no compromise on exceptional clarity
Are we there yet – Passive House?
Next steps
An alternative journey’s end, but linked to the above, would be for our FMI Zero Energy / Ready house to perform to Passive House standards. We thought it would be interesting to explore this angle, given the commonality between FMI Zero Energy and Passive House for pursuing high energy efficiency, yet also underlying differences in objectives between the two approaches.
FMI Zero Energy is focused on achieving a zero energy balance in the building’s operation, ahead of considerations like occupant health and comfort (which certainly improve in tandem with energy efficiency but are not a primary goal). In our specific FMI Zero Energy home, we had also deliberately tilted the design against meeting Passive House standards because we wanted the building to have a style familiar to many Kiwis. In particular, we kept the windows generous in size and number, where Passive House would have opted for fewer, smaller ones.
Passive House considers several factors before accrediting a home. These include heating demand, thermal comfort, fRSI (a measure of how uniform internal surface temperatures are, and how close to the internal air temperature) and air changes per hour. Our FMI Zero Energy / Ready home, modelled in PHPP9 which allows for building-specific amendments, initially fell short even though it met standards for air changes and for fRSI. However, small tweaks to air changes per hour (increases!) brought Zones 1, 2 and 3 into line with Passive standards, with the proviso that the site be free of shading from trees and other buildings.
The three colder climates failed on heating demand: Passive House requires a maximum of 15 kWh/m2 and does not consider the CoP of the appliances used, nor, in Passive Classic, the building’s capacity to create renewable energy from its roof as an offset. Interestingly, our house did meet the Low Energy Standard for heating demand in all the cold climates, because all fell under the limit of 30 kWh/m2. For thermal comfort, Zone 6 was the only zone in which our house failed; it would require even better glazing to meet Passive House.
We were impressed that our simple Kiwi box, designed to achieve FMI Zero Energy, should have passed in every climate as a Low Energy home and in three as Passive House.
We believe it is feasible right now to build simple homes that are affordable and materially better for residents and the environment than the updated H1 clause will deliver. Despite pandemic-related operational pressures, we still fully intend to build a test home in the key Auckland market to prove our convictions. With New Zealand internationally obligated to meet challenging carbon emission reduction goals, we surely need the large building and construction sector to do what it can, as soon as it can.
And then we can work on efficient ways to retrofit the bulk of existing homes in order to make an even greater contribution…

D E S I G N E D F O R
STYLE & DURABILITY

Creative freedom with no maintenance issues
Sentinel Homes
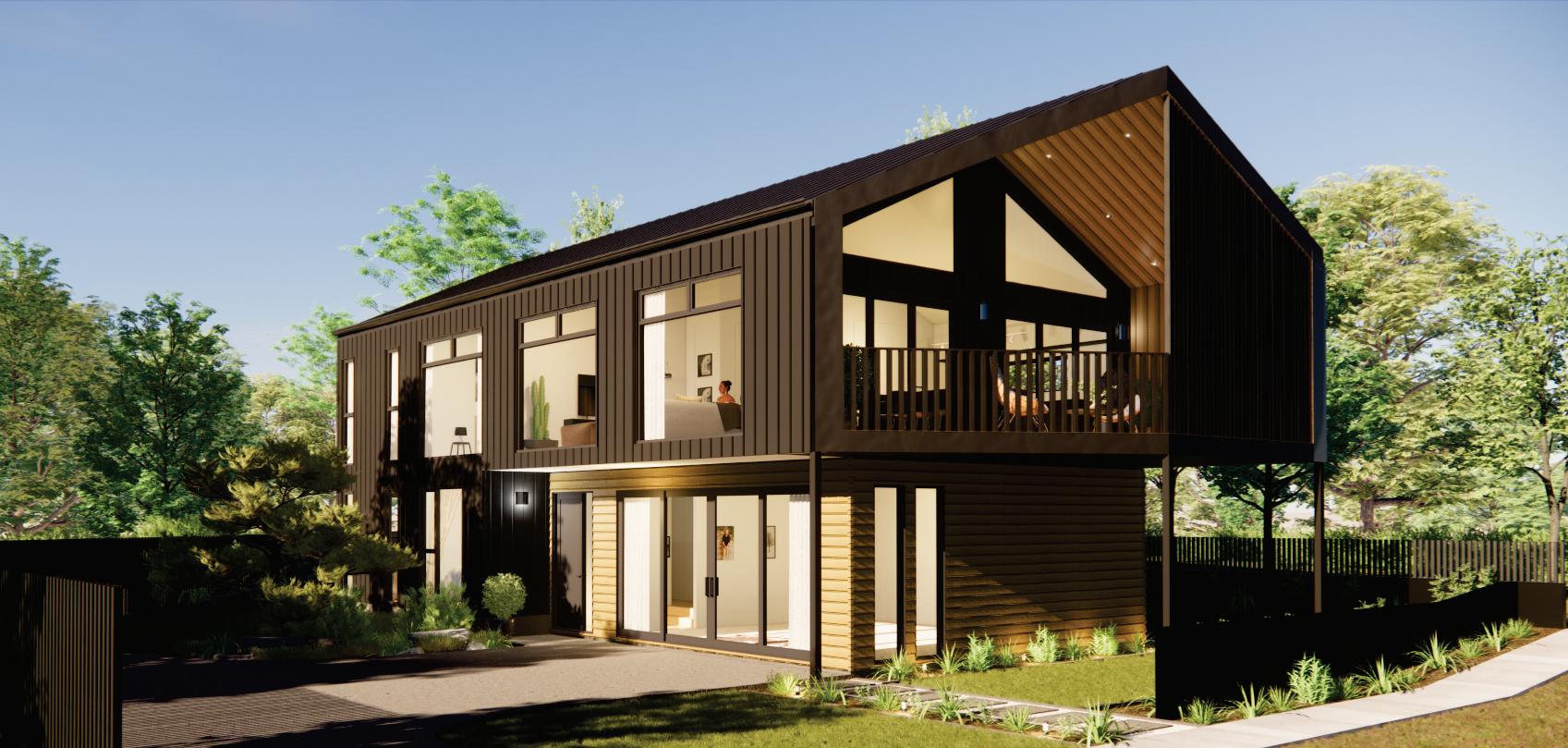
We use the very latest powder coat technology for our range of Eurowood building products for weather boards, softs and fascias. They are attractive, low maintenance and high performance.
Eurowood uses sublimation nish technology that allows us to create the look and feel of various textures on our aluminium including the popular wood-grains. We also offer the Aeonox colours which are 650 times more scratch-resistant than other powder coat solutions.
TM
Scratch-Resistant Powder Coat Technology Silver Titania White Arctic White Black
Flaxpod Ironsand Grey Grey Friars Charcoal Monument Sandstone

FIGURE G:
Modelling outputs for the updated H1 code and for the latest FMI Zero Energy/Ready home
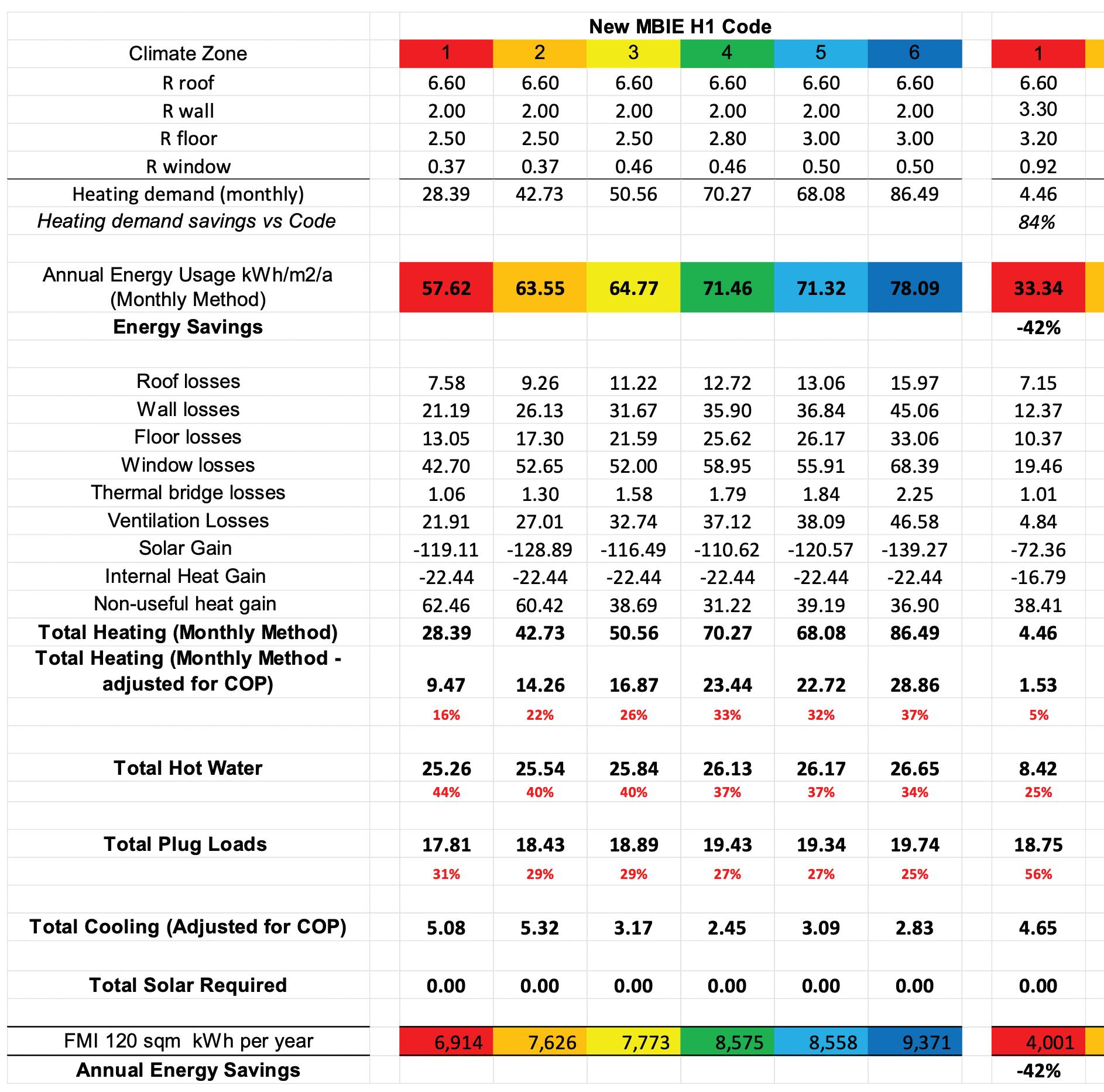
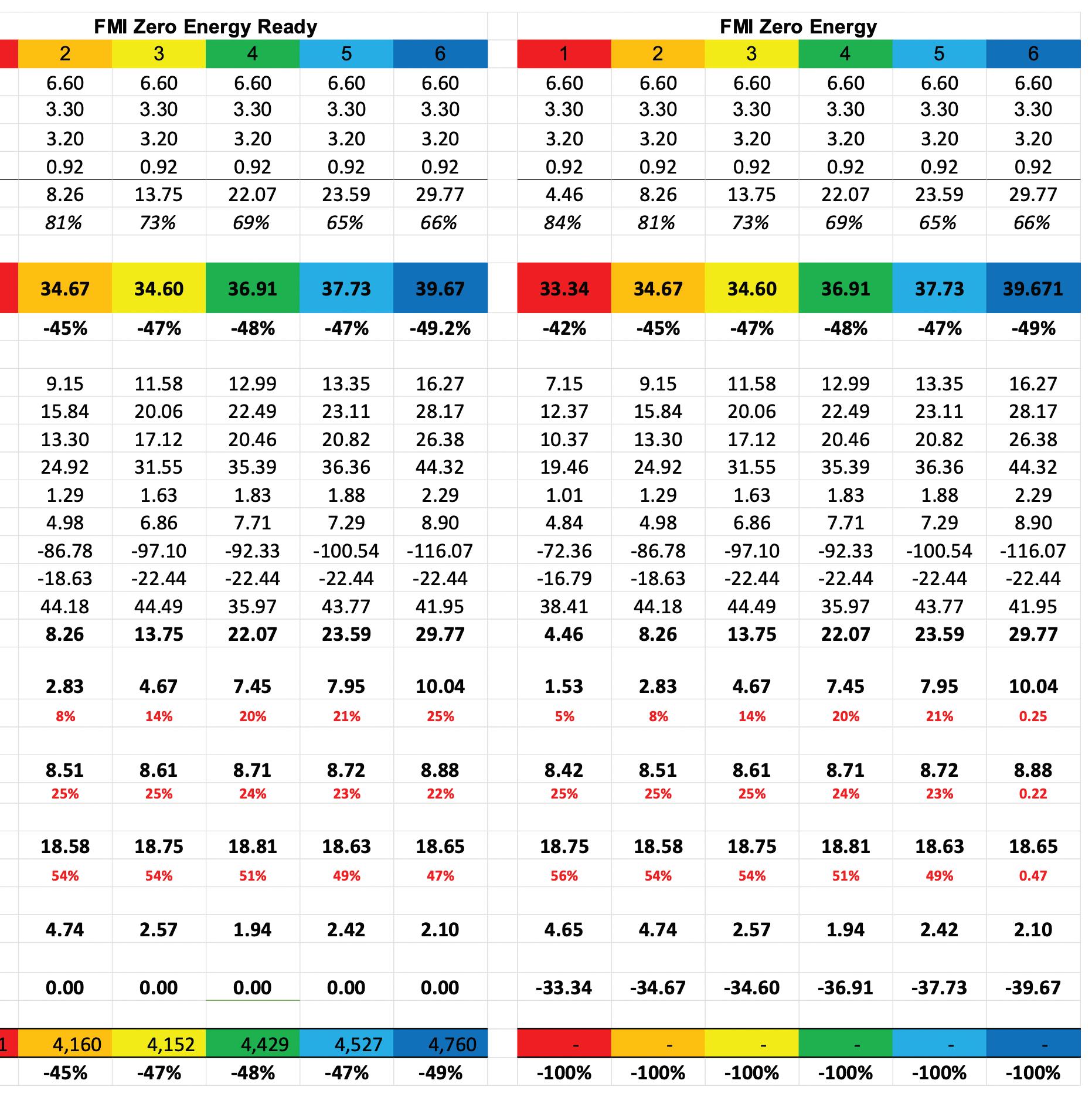
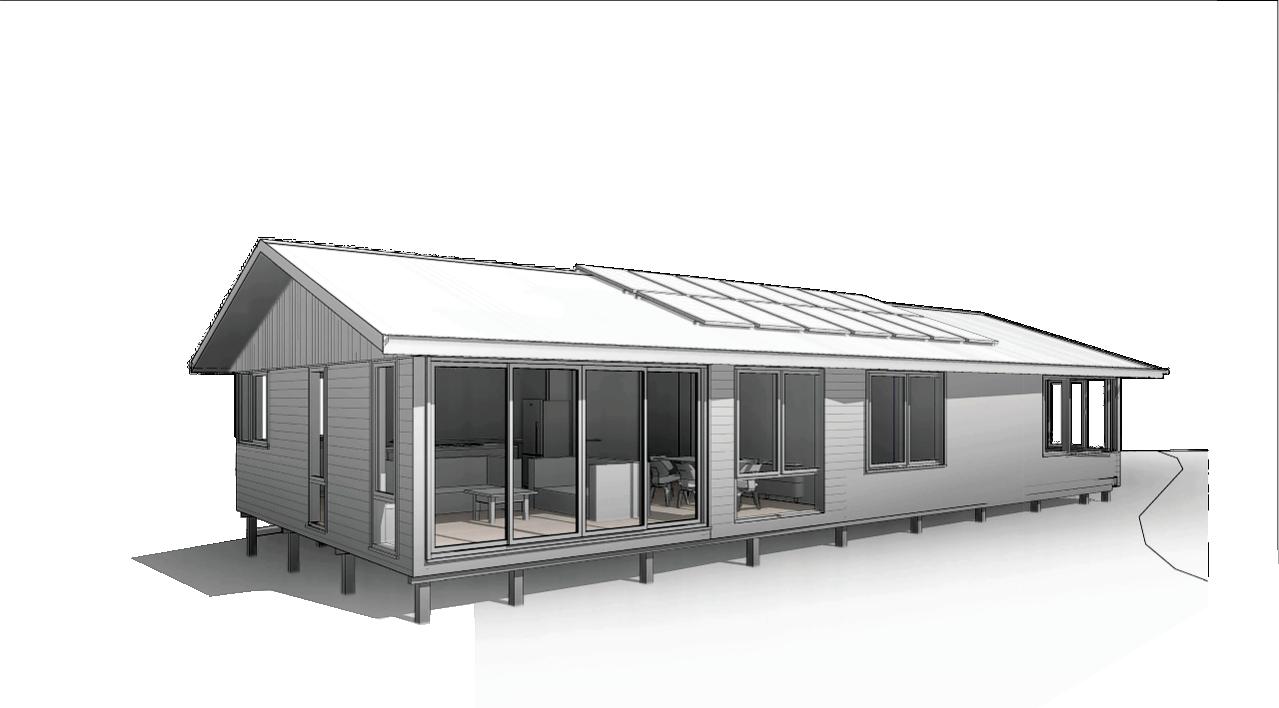
THE LATEST GLASS SPACER TECHNOLOGY IN INSULATED GLASS UNITS (IGU) LONGEVITY
Redefining standards for double glazing spacers around the world, FMI Building Innovation’s XR Edge is a multi-component system certified for all climate zones in New Zealand.
Designed to reduce internal condensation within an insulated glass unit, XR Edge is a revolutionary spacer for greater thermal efficiency and IGU longevity.
WHAT IS A SPACER
A spacer is a component that holds the two panes of glass apart within an IGU.
Its main role is preventing moisture passing into the IGU, reducing the possiblity of internal condensation and fogging.
Typically, average spacers will often lead to IGUs failing prematurely due to climate and mechanical loads as well as material incompatibilities that cause the spacer sealants to leak.
With carefully manufactured insulating glass panes, our customers can expect the longest IGU life possible. That’s where XR Edge comes in.
IGU Corner displaying XR EDGE spacer
WHY GO XR EDGE
Made up of five different components, our rigid spacer system has been designed to withstand New Zealand’s climates.
UNBREAKABLE BARRIER
Unlike other spacer manufacturers, we use a stainless steel vapour barrier and combine it with a structural core made of polypropylene that offers a superior thermal performance, and greatly reduces moisture permeability.
TWICE AS MUCH DESICCANT
Although the chances of moisture passing through the stainless steel barrier are little to zero, a desiccant material is used to fill the hollow core of the stainless steel and polypropylene spacer to absorb any moisture within the air cavity.
Our spacer structure allows us to use twice as much desiccant than standard spacers. The more desiccant used, the more moisture can be absorbed, and the longer the unit lasts.
LONGER LASTING IGUS
All four sides of our XR EDGE spacer are filled with desiccant, which in turn allows for maximized IGU performance. Our multi-component spacer system ensures our customers obtain the longest IGU service life possible.
THE FMI DIFFERENCE
Years of international research, rigorous testing, and thermal analysis have allowed us to formulate what we believe to be New Zealand’s greatest in spacer design.
We are proud to be New Zealand’s first glass manufacturer to have an IGU test lab on our own premises.
Our facilities allow us to simulate real time weather climates right here in our own factories to verify our product is fit for purpose.
The outcome? We find better solutions for our products faster, and in turn increase our manufacturing capabilities across our supply chain.
At FMI Building Innovation we have our fingers on the pulse of industry breakthroughs which allows us to be in charge of our own destiny. We do not compromise on quality for cutting-edge technology and always push the boundaries for the latest in innovation.
THE BREAKDOWN
1. Desiccant:
Removes moisture from the enclosed air during production and subsequently absorbs water vapor that penetrates until the end of its absorption capacity.
2. Primary Sealant (PIB):
Maintains gas tightness and minimizes moisture ingress into the unit. PIB is applied to the sidewalls of the spacer and creates a seal between the spacer and the glass.
3. Secondary Sealant:
Provides mechanical stability to the entire IGU and protects the seal from environmental influences.
4. Stainless Steel Vapour Barrier:
Stops desiccant absorbing moisture from outside of the unit.
5. Warm Edge Box Structure:
A composite box structure that gives the entire spacer unit overall strength and a warm edge performance.
HOW DO WE COMPARE
4 5
1 2
4
3
XR EDGE spacer
1 5
2
3
FEATURES
RIGID SPACER
WARM EDGE
DESICCANT ON ALL FOUR SIDES
DESICCANT MOISTURE ABSORPTION CAPACITY ZERO EXTERNAL VAPOUR PERMEATION STAINLESS STEEL EXTERNAL VAPOUR BARRIER
ALUMINIUM SPACER FOAM SPACER THERMOPLASTIC SPACER
P O O P O P P P O P P P
50% 35% 35% 100%
P O O P
O O O P