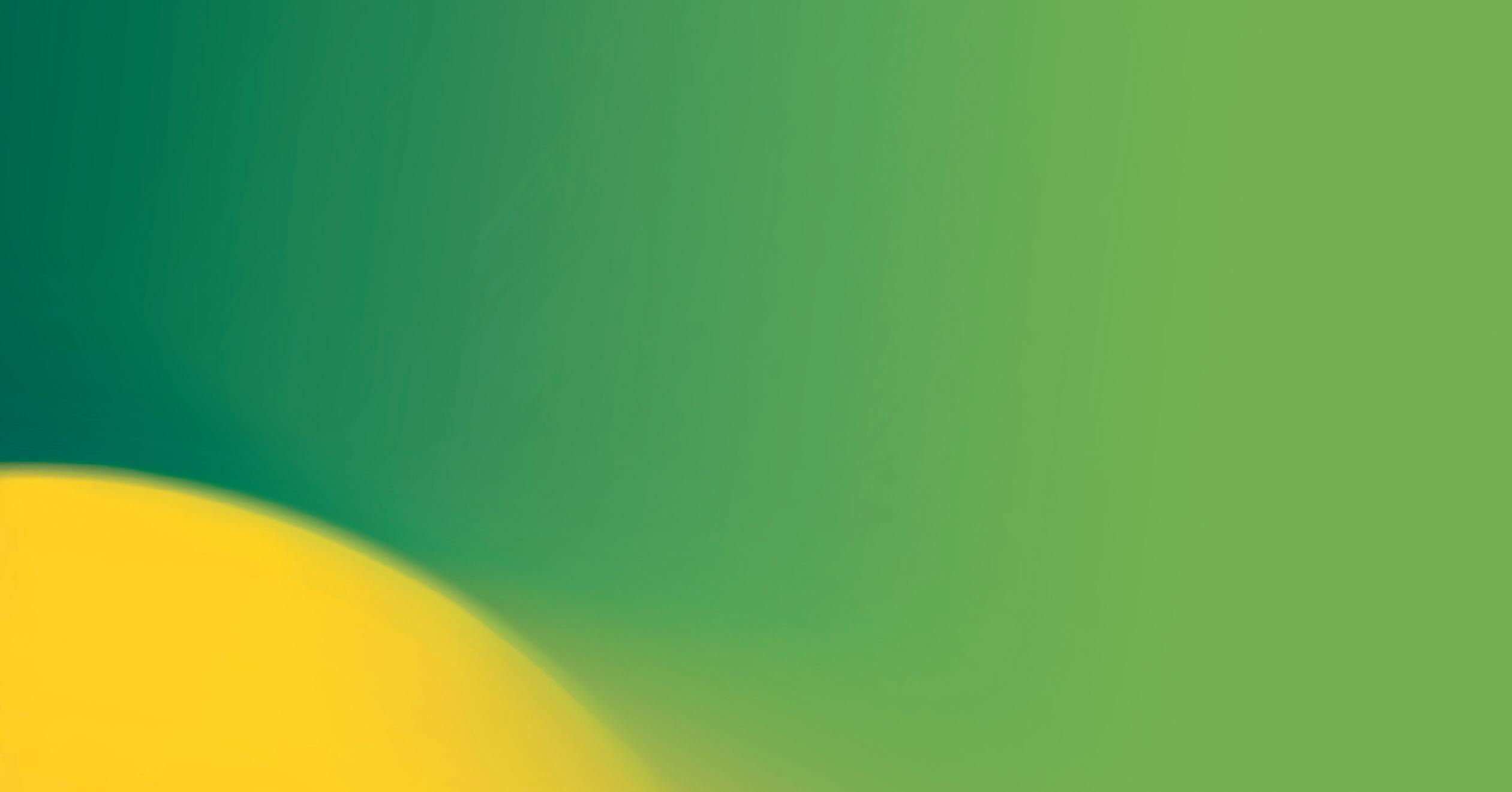
6 minute read
Less cold, less mould
When designing homes, we determine whether we’ve done a good job by assessing things like health, comfort, and energy efficiency. But as an industry, there’s one metric we tend not to do well on in New Zealand – that’s mould. The 2015 BRANZ house condition survey found nearly 50% of homes had visible mould.
Growing mould
Advertisement
For mould to grow inside our homes, it needs a high enough relative humidity in a reasonable temperature band. A rough rule of thumb when it comes to mould is “cold spots equal mould spots”. If an indoor surface is colder than the room temperature, it cools the air immediately adjacent, raising the local relative humidity. As an example, assume the warm and dry air inside a typical New Zealand home in the winter is 20°C at 60% relative humidity. If the surface is only 15°C, the relative humidity will be over 80%, which is a great breeding ground for mould.
So, it’s not just temperature and ventilation – the interrelation between the indoor relative humidity, air temperature and local surface temperature is one more dynamic to manage. To prevent the conditions that allow mould growth we need all three of adequate heating, sufficient ventilation, and high enough surface temperatures.
Researchers like Professor Philippa HowdenChapman and her colleagues at the University of Otago1 have made it abundantly clear how important it is for us to heat our homes in winter for our health But heating our homes to 20˚C is not sufficient by itself; we also need to ventilate sufficiently and keep surfaces warm enough.
1 https://sustainableengineering.co.nz/fuel-poverty-impacts-mental-health
fRSI
What is a warm enough surface temperature to prevent conditions for mould growth? That depends on the indoor relative humidity and air temperature. In Europe they use a metric called fRSI or the ratio of the indoor local surface temperature to the indoor to outdoor air temperature. It ranges from zero to one, with one being a perfect match between the indoor surface and indoor air temperature and zero being when the indoor surface is the same temperature as the outdoor air.
This ratio is fixed for a specific building construction like a window installation or wall-to-floor junction. The illustration below in Figure 1 is for a thermally broken window and shows the cold interior surface with a fRSI=0.31.
FIGURE 1:
Temperature ranges across a thermally broken window frame
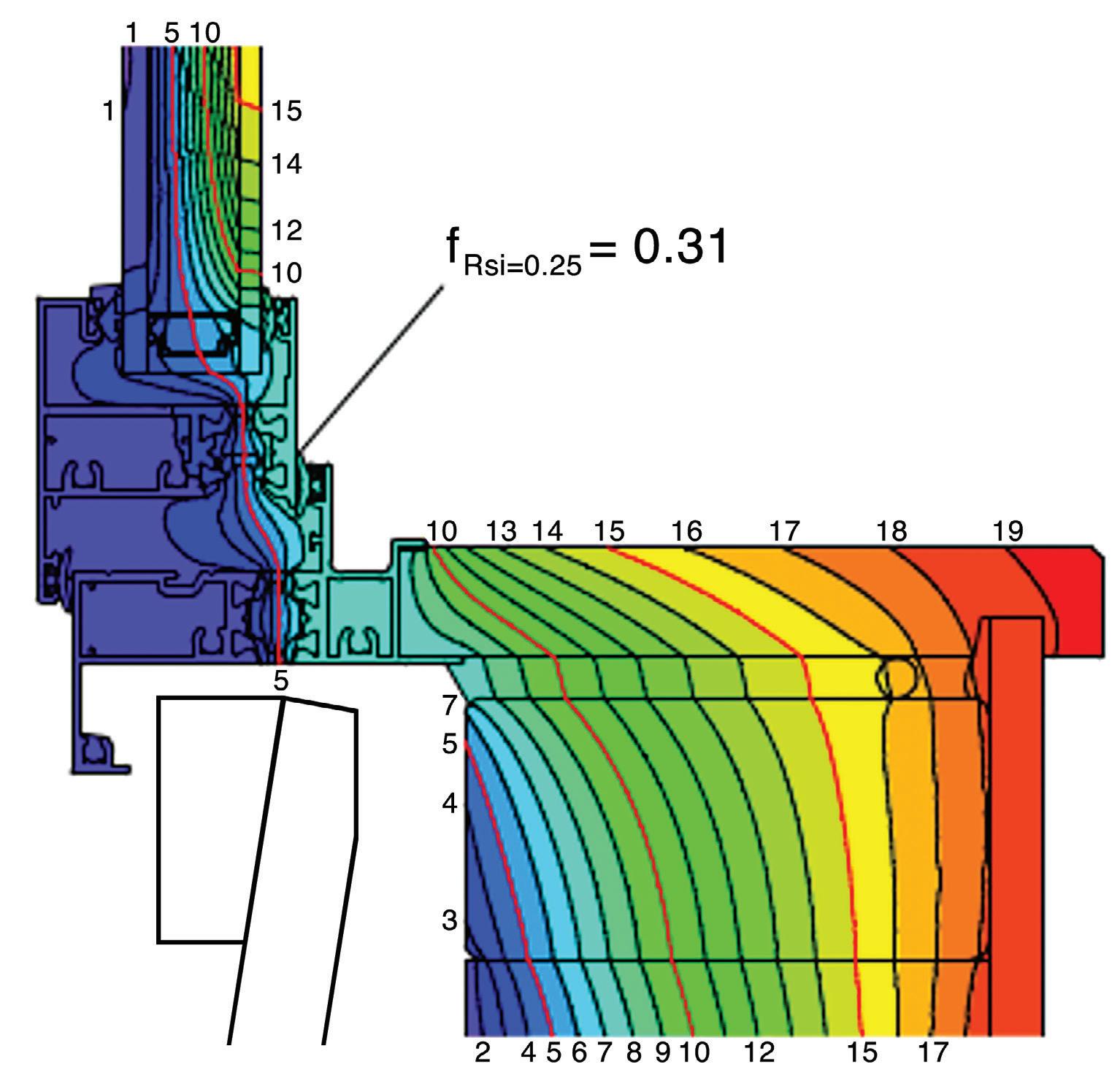
Is a fRSI=0.31 good enough to stay outside the mould zone? If we know the surface temperature and heat the home to 20˚C, we can perform a moisture balance test (with a typical occupancy) to find the required minimum fRSI to hit the mark.
Air Changes
Almost there! One more factor that is relevant is the average ventilation rate in our home over the winter. This is measured in ACH or Air Changes per Hour. If the total volume of air in your home was turned over in one hour that would be 1.0 ACH; if the air turned over in 10 hours, it would be 0.1 ACH. What’s typical depends on who you ask but research2 on modern homes in New Zealand found a range that went all the way down to below 0.1 ACH.
Overseas, a common requirement for continuous mechanical ventilation is set at 0.3ACH and this requirement has been adopted in Homestar V5 in New Zealand – I’d like to see it in our Building Code too. Continuous mechanical ventilation means you know the ventilation rate, which is needed to determine if your fRSI is sufficiently high. If you only use windows for ventilation, it depends on how much you open them when it is cold outside. Keeping those windows shut means a low ACH.
Figure 2 below shows examples of what fRSI is adequate for our various climate zones. If we heat our homes to 20˚C and predict our ventilation rate, then we can say yes or no to that fRSI.
FIGURE 2:
Minimum fRSI required by climate zone at different ACH levels

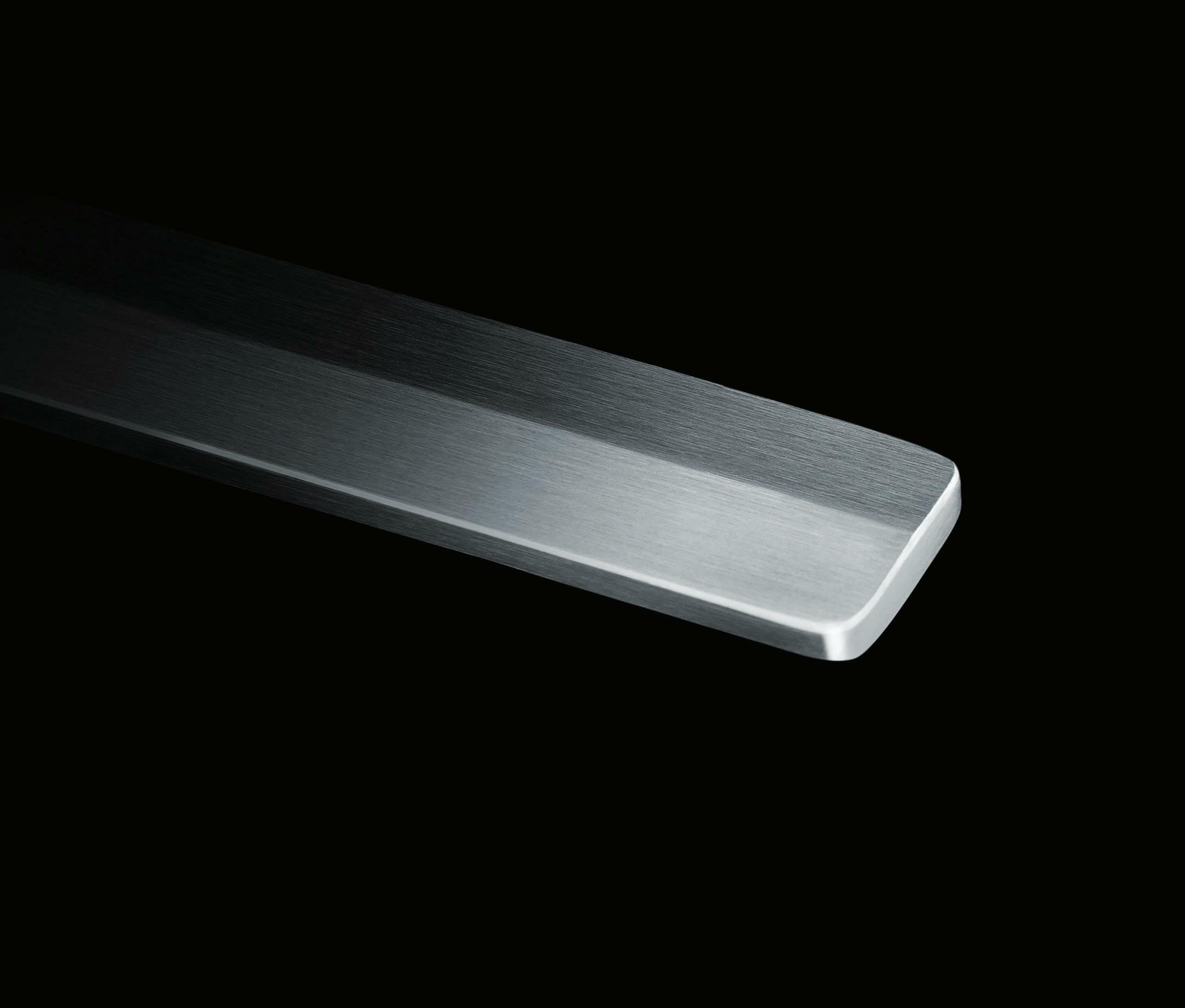
From this chart, we can say that the fRSI=0.31 modelled in the thermally broken window above is not acceptable as it permits the growth of mould over all the ventilation rates and locations given. We need a fRSI of at least 0.35 in Christchurch.
Lifting fRSI
We can easily achieve higher fRSIs through changing our building design and construction practice. For example, we can recess the thermally broken window frame into the wall along with better flashings. This change will hit a fRSI>0.4 and avoid creating the low surface temperature that allows mould to grow.
What if your house design or location means you need a higher fRSI? Then the answer is a better thermally performing window frame like a better designed thermally broken aluminium frame.
This same fRSI logic can be applied beyond this window example to all the construction details in our buildings. If we heat our homes, ensure adequate ventilation (and we now know what adequate is) and control surface temperatures by improving how we build our homes, we can prevent the conditions that encourage mould growth.
Yes, it is another complexity to manage, but with the right information we can simply adapt our designs and construction techniques to get the homes we deserve – ones that keep us warm, dry, and healthy.
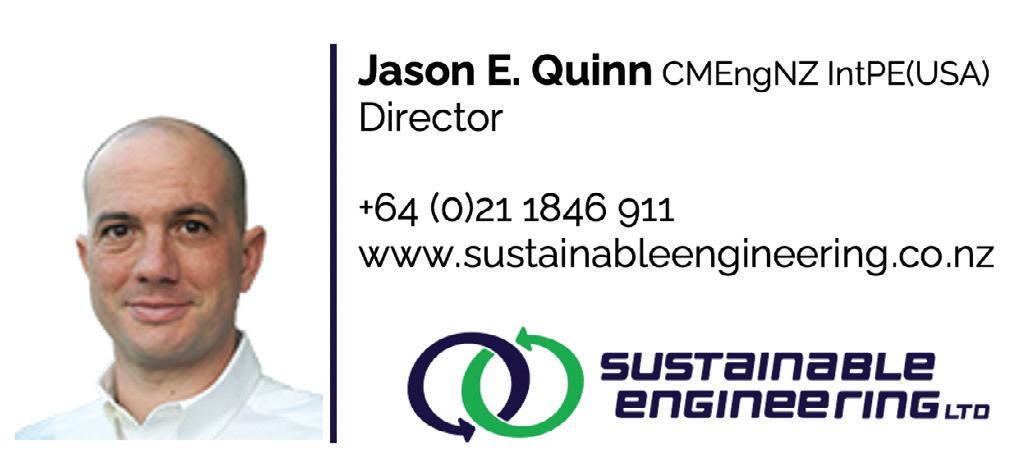
2 http://hdl.handle.net/2292/21764
BUILT FOR ENDURANCE
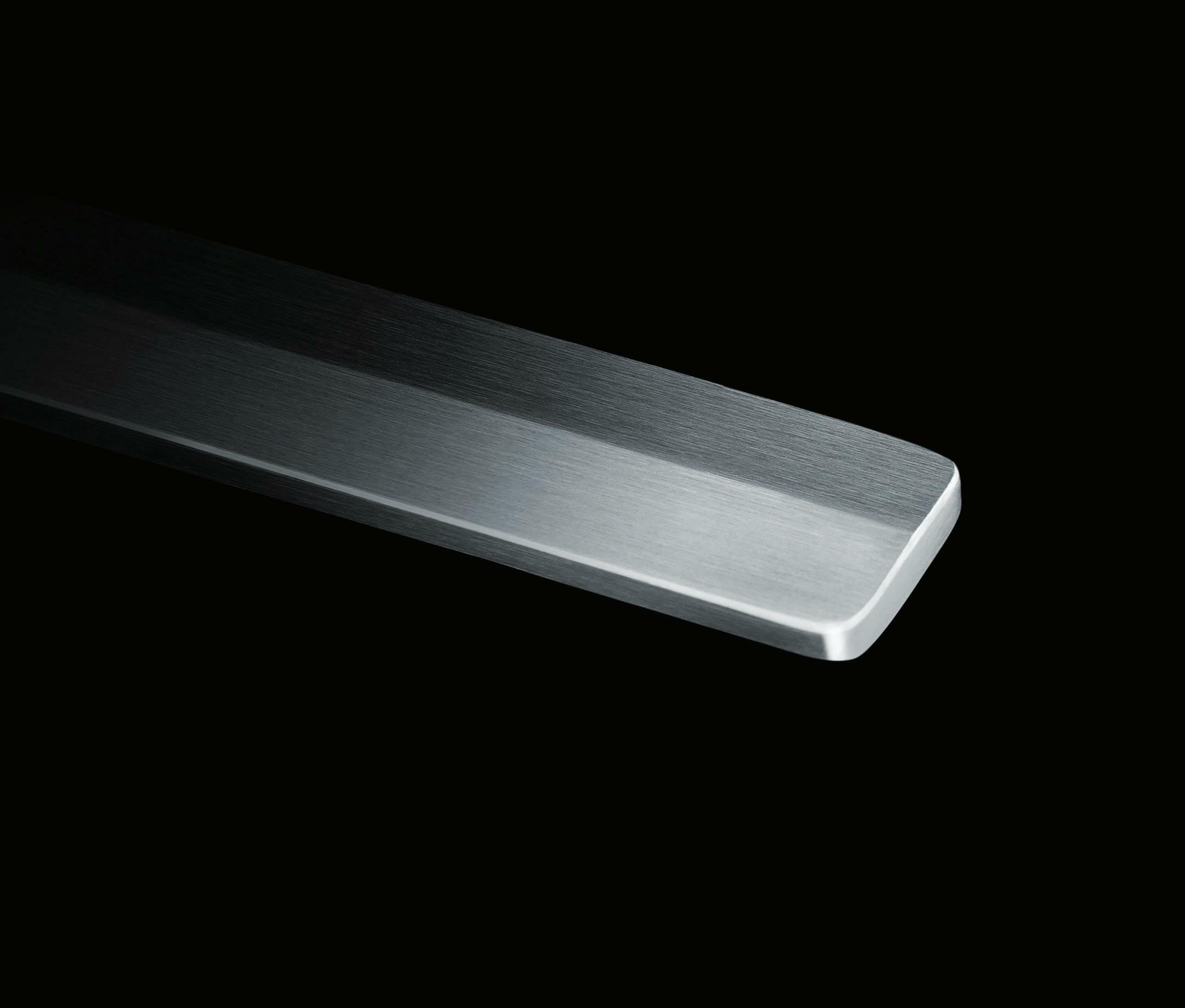
Beautifully designed door hardware needs attention to detail from creation to completion. Constructed from marine-grade stainless steel, every element of Verta has been sourced, crafted and finished by experts.
Verta’s precision engineering, uncompromised design and superior construction is the perfect balance between functionality and beautiful design.
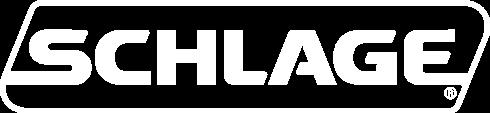
0800 477 869 schlage.co.nz


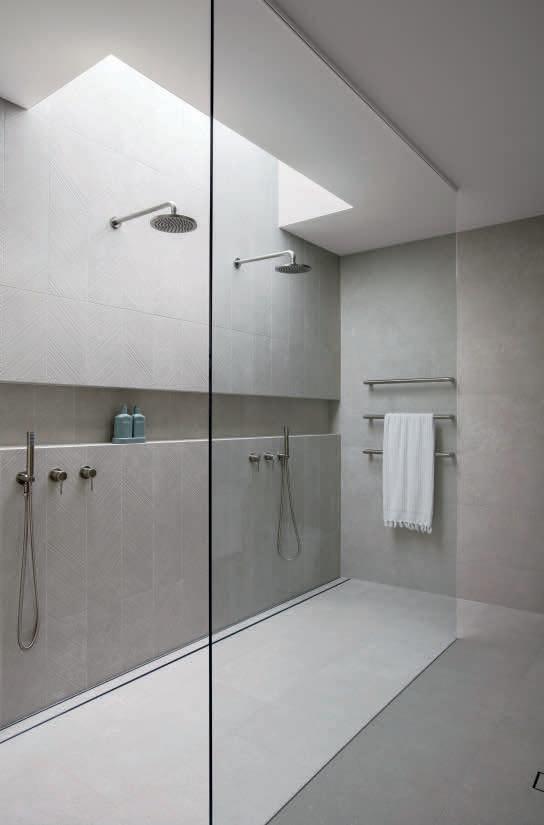
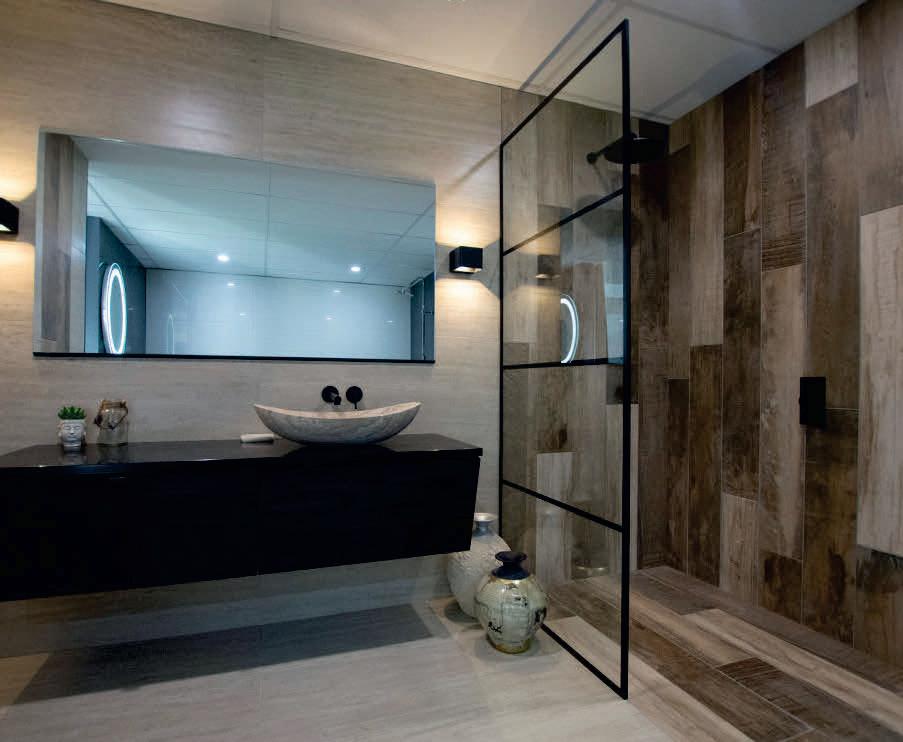
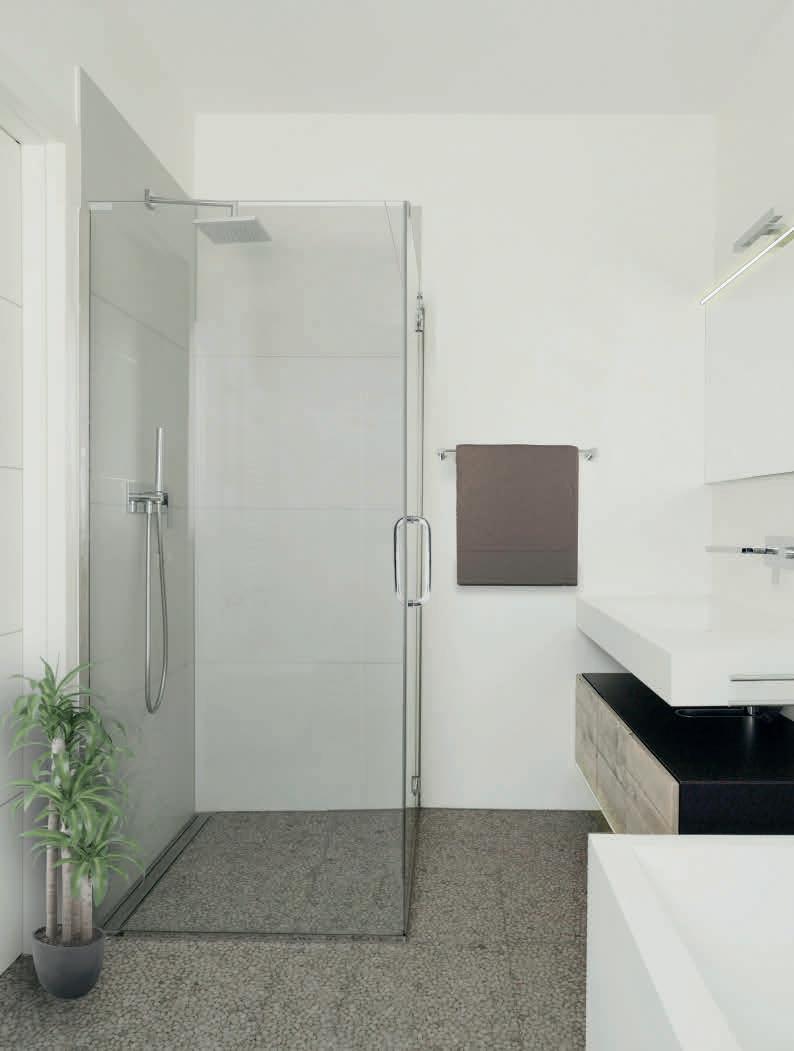
Achieving the balance between elegant form and flawless function in shower glass, fittings and mirrors Achieving the balance between elegant form and flawless function in shower glass, fittings and mirrors Achieving the balance between elegant form and flawless function in shower glass, fittings and mirrors
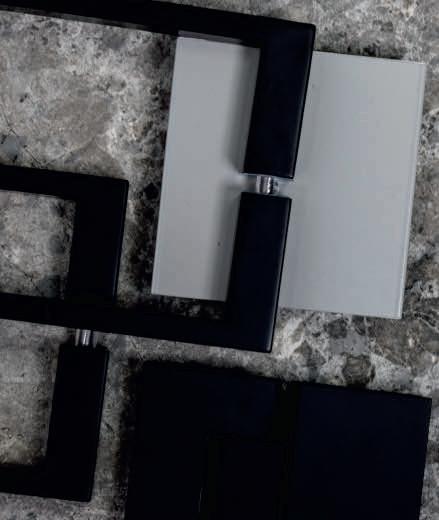
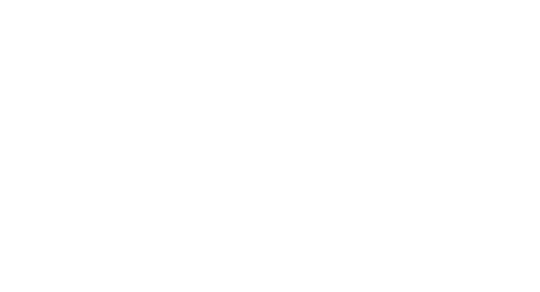
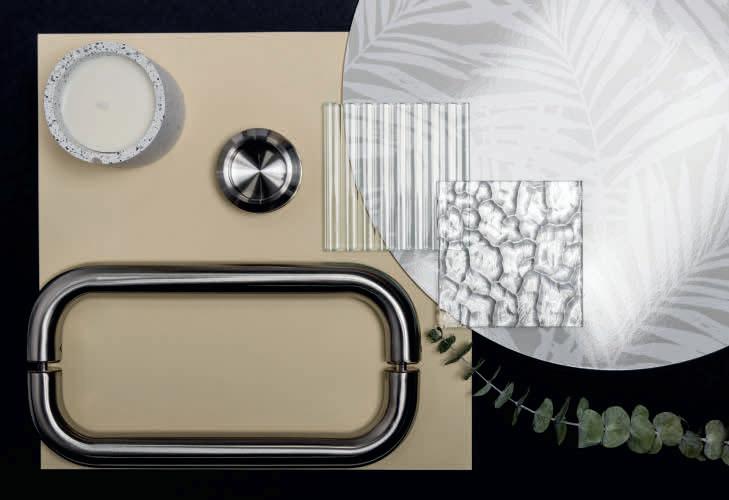

DETAILS DETAILS DETAILS MAKE THE MAKE THE MAKE THE DIFFERENCE DIFFERENCE DIFFERENCE
The exquisite designs that are inspired from a long history of Italian class and sophistication, combined with precision engineering and manufacturing make Vetro Raccordi an excellent choice for showers, shower hardware and mirrors. The exquisite designs that are inspired from a long history of Italian class and sophistication, combined with precision engineering and manufacturing make Vetro Raccordi an excellent choice for showers, shower hardware and mirrors. The exquisite designs that are inspired from a long history of Italian class and sophistication, combined with precision engineering and manufacturing make Vetro Raccordi an excellent choice for showers, shower hardware and mirrors.
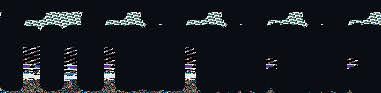
Contact FMI Building Innovation Contact FMI Building Innovation for your nearest approved Vetro for your nearest approved Vetro Contact FMI Building Innovation Raccordi supplier for our range of Raccordi supplier for our range of for your nearest approved Vetro processed glass, showers, processed glass, showers, Raccordi supplier for our range of hardware, mirrors, balustrades and hardware, mirrors, balustrades and processed glass, showers, glass fencing. glass fencing. hardware, mirrors, balustrades and glass fencing.
