12 minute read
CHARITY
from Window News May 2022
by Window News
Next Article
GGF Tackles The GGF’s Skilled Pathways Scheme has welcomed its first co hort of candidates -
The new Glass and Glazing Federation’s Skilled Pathways Scheme has welcomed its first cohort of candidates in a bid to recruit and upskill the next generation of glaziers. The Federation is determined to incite action now to meet ambitious Government targets ahead of deadline. “The Government’s objective to achieve net zero by 2050 will require an estimated 500,000 additional skilled workers in the construction industry, including the glass, glazing and fenestration industries,” explains GGF Group managing director, John Agnew. “We need to act now to get the right people in place and upskill so we can continue to be an important part of the green agenda in construction. “Working in partnership with Total Support Training and GQA Qualifications, this new programme is unlike any other apprenticeship scheme in our industry. We are funding training up to £4000 per GGF Member Company as part of the pilot scheme to aggressively
Skills Shortage Head On general manager of Prentice Glass commented, “We’re very pleased attract more businesses to take to be taking part in the GGF Skilled part. The scheme will also have Pathways scheme. Being one of a very clear and focussed career the oldest glazing companies in trajectory for candidates, to ensure London, we know how important we keep the programme of upskill- it is to get young glaziers trained in ing on track.” the industry. Being part of the GGF has meant that we have half of the In the first instance the GGF Skilled training costs funded, providing Pathways Scheme plans to cover an excellent opportunity for the Glazing, Glass Processing, Fenes- apprentices and the company. tration, Fire Resistant Glazing, Win- Exciting times are ahead, we hope dow Film Application and Technical to support the GGF and see many Administration, but as the scheme more schemes in the future.“ builds in momentum, this list is set to grow. John Agnew concludes “More information on the GGF Skilled John continues: “We’ve been Pathways Scheme can be found excited to see so many member in our online Training Hub, which companies showing an interest in provides members with a complete our scheme pre-launch. It requires resource of the expanse of training long term commitment from com- opportunities available. We also panies as they move their trainees have a dedicated section within the through the programme of both Training Hub called New to Glass on-site and ‘off the job’ learning that is open to anyone looking to over the course of 18-24 months, join the industry. We’re confident but our members are clearly dedi- we can play our part in helping the cated to doing the right thing.” construction sector to meet the Government targets, but time is of Among the first to take advantage the essence. Companies must act of the Skilled Pathways Scheme is now, and the GGF Training Hub, Prentice Glass, who has three can- including this new Skilled Pathway didates starting. Joanne Jackman, Scheme, is a great place to start.”
Euroglaze Bridging The Gap
Between Talent And Experience
Rehau trade fabricator Euroglaze is embracing modern apprenticeships, with two young people joining the business in finance and IT.
Managing director Martin Nettleton says: “Done well, in a business which is prepared to really support and nurture new recruits, an apprenticeship is undoubtedly the best way of bridging the gap between talent and experience. tive culture from the outset, they’re also learning lots of soft skills and behaviours which will make them even more valuable members of the team.”
The young apprentices at Euroglaze are Amelia Bunney, who is studying for a degree level apprenticeship in finance and Chris Gower, who is studying for a degree level apprenticeship in IT.
“Our new joiners are getting just the right blend of off-the-job university training and on-the-job experience to acquire the knowledge and skills they need to build the foundations of their careers. Just as importantly though, because they’re fully immersed within our business and within our posiMartin Nettleton adds: “The Euroglaze training programme here in Barnsley isn’t confined to apprenticeships. We invest continually in the development of our team and several of our senior staff have progressed all the way from BTEC to Master’s Degree with us. In an industry which faces an even worsening skills crisis over the coming years, it surely makes sense to develop, reward and retain your own staff.”
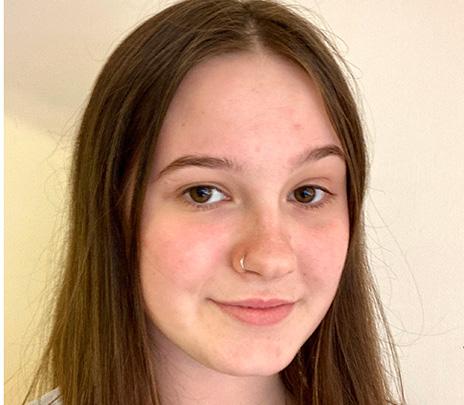
Whilst the positive and supportive culture at Euroglaze means that the business experiences unusually low levels of staff turnover, there is a consistent pattern that emerges, with many of those who leave the business believing they have found greener pastures returning to Euroglaze as soon as the opportunity arises. www.euroglaze.co.uk
Heritage Trade Frames Celebrates Its Commitment To Training
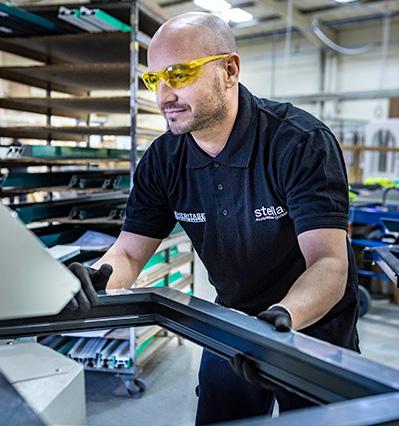
Stellar fabricator Heritage Trade Frames is celebrating the achievements of nine of its aluminium production staff who have successfully achieved their GQA L2 NVQ Certificate of Glass Supporting Structure for Aluminium Manufacturing. tor of Heritage Trade Frames, said: “We are proud that so many members of our Stellar aluminium production team have achieved this certification. It requires dedication and determination on their part and it’s great to see their hard work paying off for the benefit of both the individual and the company.”
Heritage Trade Frames emphasises the value of training in its business. Paul commented: “Investing in your staff through certified training makes good business sense as it helps to ensure that the products supplied are manufactured correctly and with the appropriate care and attention needed to provide a world class product. We have invested further in additional dedicated and committed supervisors and team leaders throughout our production process, whose focus is predominantly coaching and guiding new and existing staff in the Heritage ethos of ‘We make it right’ as this is what our customers have grown to expect from us. This workplace training has proved very successful and the difference in the finished results helps to ensure that our customers keep coming back for more.”
The company is a long-standing Epwin Window Systems fabricator and recently expanded its offering by fabricating the system company’s multi award-winning retail aluminium system Stellar aluminium.
It’s an expansion that’s proving very successful. Paul commented: “Installers love Stellar. They appreciate the fact it’s fitter-friendly and is exceptionally easy to glaze because of the pre-gasketed, knock in beads. Stellar is especially good for securing higher-end projects that need something different which gives our customers a competitive edge. When it comes to aluminium window and doors, Stellar offers some of the best aesthetics on the market today.” www.stellaraluminium.co.uk
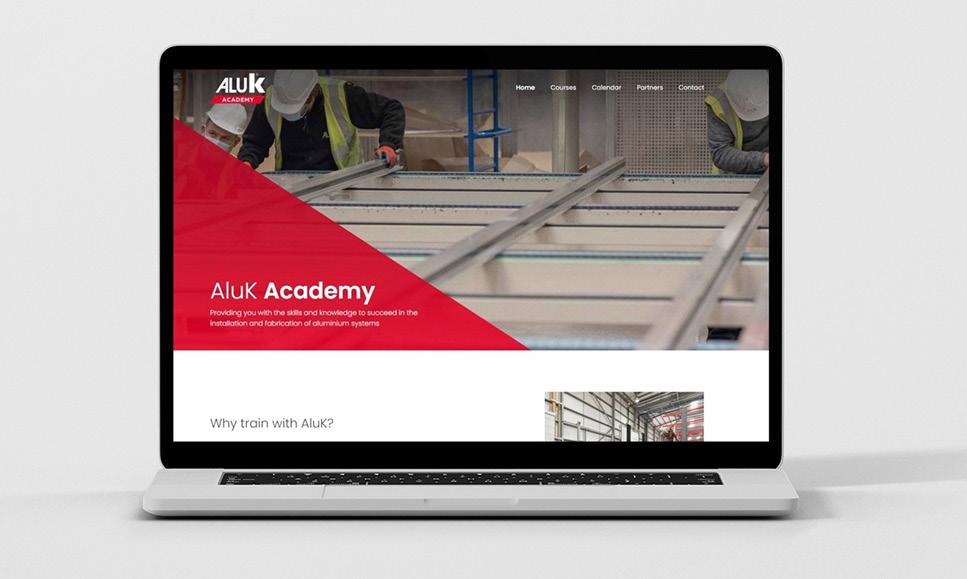
All In House
At AluK – Including The Training Academy
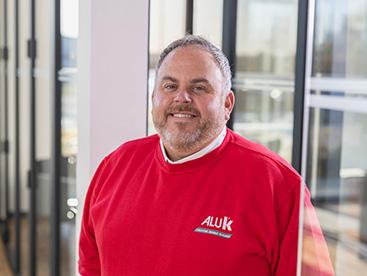
Darren Burford
Reminding the market that it is the only aluminium systems house that has it all ‘in-house’, AluK has just announced the reopening of its training Academy, with a full range of workshops available to book now.
After the pandemic forced the Academy to close for face-toface training for almost two years, it is being relaunched with a brand-new website at: www. alukacademy.co.uk and a new downloadable prospectus.
Visitors to the website can browse the content and format of all 9 of the workshops that AluK offers in three different categories – product awareness and LogiKal software, theory and fabrication, and theory and installation. They can see the dates when each of the courses are available during 2022 and book their places online.
The product awareness and LogiKal software workshops cover either: bi-folds (BSF70 and F82), windows and entrance doors (58BW and 58BD), sliders (BSC94 and SC156) or curtain walling (SL50 and SG50). Each lasts two days and includes a full brief on the relevant systems and their capabilities and then an introduction to the LogiKal processing software. Delegates start with an empty LogiKal file and build up a project using the system – learning both the basics and some more advanced aspects of estimation and production.
The one-day fabrication and installation workshops are all about learning best practice direct from the systems house, with the emphasis very much on practical training in AluK’s fully equipped, dedicated facility. The fabrication course guides delegates through how to manufacture windows, doors, and ground floor treatments in line with AluK’s approved processes and technical manual. The installation course is focused around
the SL50 and SG50 systems and is designed for installers and site supervisors with any level of industry experience who have not previously fitted AluK curtain walling.
Two aspects of the Academy make the workshops particularly valuable to AluK customers. The first is that all the courses are free and the second is that they are all fully GQA Accredited. At the end of each, delegates can undertake a short assessment and return to work with a GQA certificate.
Darren Burford, AluK’s experienced training manager, is understandably delighted to be back training customers in person again. He said: “Online training is all well and good, but there’s no real substitute for hands-on, practical experience. The Academy is right in the heart of our Chepstow manufacturing facility, so delegates really do get up close to all the products in a realistic fabrication setting.
“The courses are ideal for all those new starters over the past couple of years who might have missed out on formal training and as a refresher for those who might just be new to the AluK systems. With record numbers of customers investing in new machinery and expanding their operations over the past two years, we’re expecting this year’s training calendar to be busier than ever.”
There are 35 workshop dates available to book at AluK throughout the rest of 2022 and customers can also request bespoke training at their own facilities or at AluK’s London Design Studio.
The AluK Academy is an integral part of AluK’s customer support offering, which also includes in-house CAD design, technical support, and testing facilities. More details at: www.aluk.co.uk
BWF Launches
‘Our Industry’s Next Generation’ Apprenticeship Campaign

Helen Hewitt, CEO of the British Woodworking Federation
The British Woodworking Federation (BWF) has launched a campaign to champion the role of apprentices in woodworking and joinery manufacturing and highlight the diversity of career opportunities in the industry. The campaign Our industry’s next generation: Apprentices tell their stories sees apprentices and former apprentices of BWF members share their journeys to bring to life the passion, achievements, and benefits that an apprenticeship can offer.
The construction industry is facing a skills shortage, with CITB estimating more than 43,000 new entrants are needed every year for the next five years to maintain output. This campaign aims to encourage the next generation into the woodworking and joinery manufacturing profession by shining a light on the apprentices and former apprentices and the breadth of opportunities offered by the sector. will run across multiple channels to raise awareness of the diversity of roles, skills, and career pathways within the industry.
Helen Hewitt, CEO of the British Woodworking Federation, said, “Hearing direct from apprentices and apprentice graduates in our profession about why they chose a career in woodworking and joinery is inspirational for the next generations. The wide range of roles, jobs and opportunities within the industry is clear, and as our apprentices have highlighted, every day is exciting, different and a chance to learn new skills.
“As the focus on sustainability is pushed to the top of the agenda, it’s clear that woodworking and joinery skills will be sought after as demand for sustainable building materials, such as timber, increases. It’s therefore vital that as an industry we come together to champion the important role that apprentices play in securing the growth and future of our profession. This campaign will maintain the momentum and focus on apprentices throughout the year, raising awareness of the diverse and fulfilling career options that lie ahead for those joining our industry.”
The campaign forms part of the BWF’s 2022 plans and core focus on skills, talent recruitment and retention. ‘Our industry’s next generation: Apprentices tell their stories’includes content from BWF members: A R Manley, ERW Joinery, George Barnsdale, Input Joinery, Masonite and William Holmes.
ABUS UK Family Rallies
Together To Send Help To Ukraine
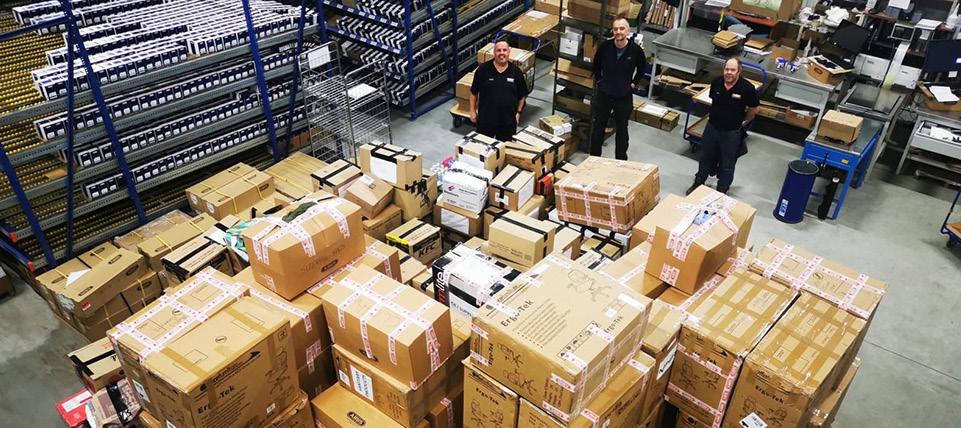
In light of the ongoing humanitarian crisis in Ukraine, the ABUS UK family has joined forces with colleagues in Eastern Europe to collect and deliver urgent essential items including food, blankets, clothes, and toiletries to centres for refugees in Poland and the Ukrainian borders as people fleeing the war are escaping into the EU. ABUS UK employees, their families and friends, and business partners, customers and members of the wider local community have collected an amazing amount of critical supplies which have been sorted, packed, and driven all the way across Europe by ABUS UK’s Vince and Roy. They were met in Poland by ABUS Polska’s MD Józef Grabowski and colleagues from ABUS Polska are now distributing the donations to the people who most need them in various locations in Poland where Ukrainian families are being supported, and to entry points on the Poland/Ukraine border. The ABUS team has even been providing hot drinks to Ukrainians at the Polish border to welcome them to safety.
“It has been so heart-warming to see how the ABUS UK family and their friends and partners have rallied round to support our Help for Ukraine and to know that those supplies are now reaching the people who need it. Thank you!” says ABUS UK MD peter Romanov. “A special thank you must go out to our colleagues Vince and Roy who drove through the night on a long journey through Germany and into Poland to meet with our friends in ABUS Polska and deliver the essentials we had collected.”

Edgetech Supports Ukraine Crisis Appeal
Edgetech has responded to the worsening humanitarian situation in Ukraine by donating to the Disasters Emergency Committee’s Ukraine Crisis Appeal.
Edgetech UK has donated £5,000 to support the organisations’ efforts to help those affected by the conflict.
The company’s employees have also donated goods to be sent to the region, collaborating with Feed the Hungry Coventry Food Bank, a local charity Edgetech has supported previously. Meanwhile, Edgetech’s European arm has donated 5,000 Euros to German aid charity Aktion Deutschland Hilft.
Edgetech managing director Chris Alderson comments: “We all felt moved to show our solidarity with the people currently suffering in Ukraine, and those who’ve been forced to flee to neighbouring countries by the violence.
“I know I speak for everyone at Edgetech and Quanex more broadly when I say we hope this horrific situation can be quickly and peacefully resolved.
“We routinely supply customers across Ukraine and the wider region, and our thoughts are with them at this incredibly difficult time.”
To support the Ukraine Crisis Appeal, please visit https://bit.ly/3vOZYQE www.edgetechig.co.uk