
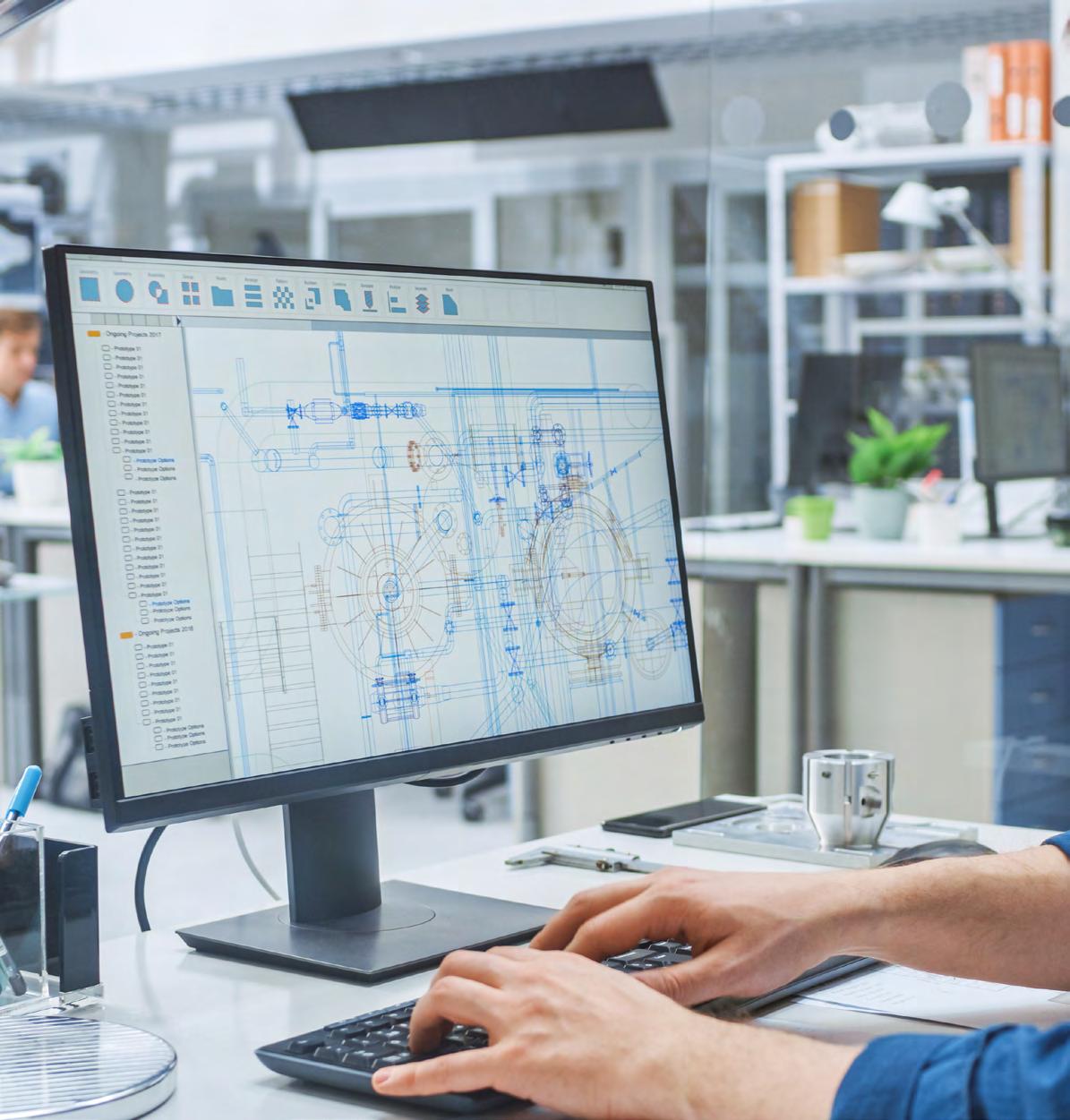
LiftEx 2024, the flagship event of the Lifting Equipment Engineers Association (LEEA), will take place on 16-17th October 2024 at the new West Hall at Olympia in London – a great central location for a truly global industry.
The exhibition floor at Olympia will be packed with almost 100 exhibitors showing their solutions to improve productivity, efficiency and safety for end users. These will feature the latest lifting products including hoists, mobile and overhead cranes, steel chains, wire rope, winches, shackles, web slings, rigging, spreader beams, height safety and load monitoring equipment, IT solutions and more.
Crucially, your visit will contribute to improving safety with advice from experts on the LEEA stand, while free training sessions and presentations will be delivered by LEEA Accredited Training Scheme members at the ATS Seminar, which is being held across both days.
Set to be the best yet, LiftEx 2024 is supported by sponsors including YOKE, the manufacturer of lifting fittings for chain, wire rope and webbing slings; Rope and Sling Specialists, one of the largest independent
companies in the field of lifting equipment engineering in the UK; and Headline Sponsor RiConnect Inc, which offers powerful software known as RiConnect that is designed to streamline equipment management and ensure regulatory compliance and traceability.
The many networking opportunities during the event will include the annual LEEA Awards ceremony will be held at the iconic Dorchester hotel on the evening of 16 October 2024.
For engineers, LiftEx 2024 offers the perfect chance to gain vital lifting related knowledge and insights, as well as an opportunity to meet LEEA members
and discuss ways they can help achieve best lifting practice.
Registration will be open soon at the exhibition website at events.leeaint.com/liftex-london-2024.
For those interested in exhibiting, a few stands remain available. Sponsorship packages are also available for the exhibition and Awards Dinner.
Requests will be dealt with on a first-come, firstserved basis, so please contact Leah Phelps on +44 20 3488 2865 or at enquiries@L2Events.com or visit: events.leeaint.com/liftex-london-2024
Optronics form an integral part of today’s operational military equipment, playing a decisive role in the tactical superiority and safety of armed forces. From night vision technology and thermal imaging to enhanced head-up displays (HUDs) and augmented reality glasses, these optoelectronic systems are now indispensable tools.
However, the use of such highly sophisticated optronics in extreme environments and the high sensitivity of such systems, present manufacturers with special challenges.
In particular, the interfaces and connections of the optronics are a potential weak point.
1. Break resistance: The connection systems have to withstand enormous tensile and torsional forces, which can lead to bent or broken contacts. Conventional push-pull mechanisms increase the leverage on the connection, due to their design.
Therefore, to meet the requirements of highly innovative optronics, ODU has developed best-in-class ODU-AMC® connectors that are many times more robust than conventional half-shell coded systems. They offer reliable protection against twisting and breakage, enabling the transmission of various data protocols for imaging applications such as HDMI.
2. Environmental protection: For a solution that can be used as flexibly as possible, the interfaces and connections of the optronics must be able to withstand extreme levels of dust, water and shock - ODU connectors meet the highest environmental standards. With an immersion depth of up to 20 metres and protection classes IP6K8 and IP6K9K. This makes them ideally suited for use in harsh environments without reducing the performance of the optronics.
3. Hermetic sealing: Optronics are often filled with inert gas, such as nitrogen or argon, to eliminate an oxygencontaining atmosphere. Vacuum-tight connector systems with glass potting technology for extremely high pressures are available from ODU.
4. The smallest foot-print: Naturally, all of the above have to be achieved, together with the ability to lock securely, in the most confined spaces – The ODU-AMC® connectors are designed specifically for this situation.
ODU offers comprehensive support for vision system and accessory OEM’s.
The solutions available enable improved cross-platform functionality including STANAG 4695 connection to portable battery systems (PDUs) for soldiers. ODU has many years of experience and is a proven supplier for major OCCAR procurement projects in the field of night vision equipment for the German and Belgian armed forces. ODU is also the main supplier for one of the largest projects for the integration of augmented reality in the US armed forces.
Through decades of collaboration with customers, ODU offers extensive experience in the development of customized connection solutions.
ODU-UK Ltd
tel: 0330 002 0640
email: sales@odu-uk.co.uk
web: www.odu-connectors.com/uk
Click here to view our brochure
A global engineering firm, wowed by the results provided by an award-winning Northamptonshire recruitment team, has chosen the expert consultants again to source its new talent.
SSI Schaefer Group, which operates across six continents and has more than 10,000 employees, originally chose Kettering-based Wills Consultants to lead its recruitment processes in 2020.
The Recruitment Process Outsource (RPO) agreement, which sees Wills Consultants manage and enhance the end-to-end sourcing and recruitment strategy for permanent and contract roles across all UK sites, including the head office, was so successful that SSI Schaefer Group have recently extended the contract for another three years.
Wills Consultants have hired a range of staff for SSI Schaefer Group since the relationship began, this has been across the business including engineering, finance, admin, procurement, legal, and IT teams.
The recruitment specialists have also undertaken other projects for SSI Schaefer Group, identifying the most successful practices, and integrating them into the company procedure.
Simon Wills, director at Wills Consultants Ltd, said: “It has been our pleasure to help SSI Schaefer Group to find the right people for their vacancies over the last three years and we are delighted that they have chosen us once again to continue to provide the talent they need.
“We have built strong relationships with the hiring managers, and we are proud to have exceeded their expectations for the partnership in such a short time. We now look forward to building on these foundations to continue to work together to provide a first-class experience for the client and their candidates.”
Andy Wightman, Managing Director UK and Ireland at SSI Schaefer Group, said: “Wills Consultants have worked closely with us and supported our growth, and this extension marks the relationship with a company we can trust.
“Their team understand the complexities of engineering and the automation sector. They have continued to meet our demands and have consistently delivered a great service to our employees from their initial application through to post placement. Their quality service has saved us both time and costs, which has been beneficial to our customers.”
For more information about Wills Consultants Ltd visit www.willsconsultants.com
The terms water meters and flow meters can be used interchangeably, but there is a key difference between them. Whilst all water meters are flow meters, not all flow meters are water meters. Commonly applied in the domestic environment for devices used to determine your water bill, water meters measure the total amount of water that passes through them. Flow meters, on the other hand, measure the volume and flow rate of a liquid or gas passing through a pipe. They can be used for water, but also for other fluids and gases in various industrial applications.
In cooling water systems, water is used to remove heat from an industrial process or air conditioning equipment. Such systems provide cooling for critical processes found in power generation stations, food and beverage process facilities, data centres, hospitals and pharmaceutical production.
Neil Hannay, Senior R&D Engineer with Titan Enterprises, says: “Selecting an appropriate flow meter for a cooling water system is just as vital as the operational process itself.” Flow monitoring helps to optimise plant or system efficiency, save energy, control chemical costs and enhance overall profitability.
1. Water coolant for glass bottle production
Graphoidal Developments design and manufacture advanced lubrication and coating systems for the glass container and tableware industries. Titan’s Industrial Process Atrato® ultrasonic flowmeters are installed in the water lines to monitor the
application of the coolant to the shears which are used to cut semi-molten glass in bottle making machines. The accurate application of a lubricant and coolant is critical to the reliability of the whole machine. In addition to the multiple flow ranges of this ultrasonic device, in older glass bottle making plants the deposition of rust in the water coolant lines require a robust flowmeter that is immune to ‘dirty water’ problems. As the Process Atrato® flowmeter has no moving parts, there are no components to wear out or clog due to inherent rust abrasion and particles.
2. Metering laser coolant flow
There are numerous applications for industrial and medical lasers: cutting, welding, micromachining, cosmetic and eye surgery. Lasers generate a significant amount of heat that needs to be quickly and effectively dissipated to ensure stable long-term performance of the instrument. Water circulated through a chiller or heat transfer system is a popular cooling method for lasers. Titan’s 800 series turbine flowmeters are integrated into several leading industrial and medical laser systems to provide consistent laser cooling through accurate and repeatable water flow measurement.
3. Cooling systems for medical treatment applications
An innovative liquid-based cooling system by Paxman Coolers Ltd utilises Titan’s NSF-approved mini turbine flowmeters to monitor the rate of coolant flow around the patented cooling cap during chemotherapy treatment. The scalp cooling technology can alleviate the damage caused to the hair follicles by reducing the temperature of the scalp by a few degrees before, during, and after chemotherapy treatment. Titan’s mini turbine
flowmeter is considered ideal for the Scalp Cooling System because it offers an excellent balance of measurement accuracy, long term resistance to coolant fluids, high reliability and is proven easy to maintain and cost effective.
The world’s largest optical telescope, the 10.4m Gran Telescopio Canarias (GTC) on the Canary Island of La Palma, is equipped with a powerful astronomical camera built by the University of Sheffield, UK. The camera, called HiPERCAM, is the most sensitive astronomical camera in the world and has been used to study black holes, neutron stars, white dwarfs, exoplanets, active galactic nuclei and the outer regions of our Solar System. The five light sensors used in HiPERCAM are ultra-sensitive charge-coupled devices which require cooling to 183K (-90°C) to minimise noise in the images. This cooling is achieved using very high performance thermo-electric (peltier) coolers, which in turn require a liquid coolant (a water-glycol mixture at +5°C) to remove the heat they extract. Micro bubbles and metallic sludge in the telescope’s coolant supply meant that a flow measurement device impervious to these unavoidable characteristics was essential. Titan’s FT2 optical flow sensor that uses an LED and photodiode to measure flow was used successfully without being affected by the undesirable properties of the telescope’s cooling fluid.
Reliable flow monitoring of refrigerant liquids is a vital requirement for cooling equipment used in data centre facilities. Refrigerants in cooling systems are widely used by big data centres and electricity production facilities to keep equipment running efficiently and prevent over-heating.
Using steel reinforced polymer components, the low inertia turbines of Titan’s 900 and 1000 Series turbine flow sensors are ideal for measuring the low viscosities encountered with volatile refrigerant fluids measured in liquid form.
Because water can conduct heat about 30 times faster than air, using water or a water-mix as the cooling medium enables a highly efficient liquid cooling system, vital for electronic systems, medical appliances and highly sensitive instruments.
The bottom line for cooling liquid water systems is for reliable monitoring and ensuring there is adequate flow of coolant to the downstream instrument or process, thus mitigating against serious problems caused by over-heating, such as degradation of operational performance, damage to critical equipment and shutdowns.
Visit Titan Enterprises’ website for further information on flow measurement or to discuss specific OEM applications, please contact Titan Enterprises on +44 (0)1935 812790 or email sales@flowmeters.co.uk.
There are a number of benefits to utilizing engineering and quality services, from enhancing the efficiency of fastener concepts all the way through to the final product and ensuring the products meet desired quality and engineered requirements for the assembly line.
In our latest Optimas Toolbox Talks podcast, contributors Graeme Bassett (VP, APAC), Greg Babinec (Applications Engineer, US), Jonathan Christopher (Quality Director, UK) and Stuart Katz (Marketing Director, US) compiled five key reasons why manufacturers should utilize engineering and quality services.
1. Incorporating Engineering Support – the Earlier the Better
“Utilizing engineering and quality services correctly and as early as possible in the product life cycle will help maximize the efficiency of the original concept,” said Babinec.
Engineering and quality services focus on reducing costs at each stage of the products life cycle, so the earlier you start to implement functional improvements, the general manufacturability of the part or even improve the efficiency in assembly, it’s likely you will see a greater reduction in costs. This is called quality before the fact.
These services can support after the fact too. When the design is frozen in production, engineers can support in troubleshooting problems with a part and address issues affecting the production line, however if you
incorporate engineering expertise at the start of the product life cycle you could avoid these issues.
2. Let the Experts Standardize Your Parts for Better Profitability
“We have seen an increase in our customers moving away from sending a drawing and asking for a quote. There has been growth in customers providing us with a brief and requesting to utilize existing, live parts from our database that will fit their design needs,” commented Bassett.
By recommending existing parts, which speeds up the time to market since the parts are already in stock, the engineering approach prevents part proliferation, avoids new tooling, and shortens lead times. Customers can access a product database to view and download 3D models for testing in their designs. From a cost perspective, this helps customers bring products to market quickly with tried and tested designs. Standardization drives cost savings and greater profitability for customers.
Why spend time on creating new drawings? Partnering with a distributor who has the engineering expertise
to suggest in-stocks parts can help eliminate tooling and PPAP outlays, which again will help speed up the product-to-market process.
3. Assess Production Processes to Uncover Losses
“When looking at production processes, you need to examine the complete picture.” Babinec continued, “f or example, when conducting line walks, our engineering services identify areas for productivity improvement like subassembly requirements on the line or deficiencies in production line track.
“Can you implement color-coding fasteners to prevent assembly errors with similar-looking fasteners with different grades or coatings to help differentiate them and reduce production errors and costs?
“Are subassemblies done on the line? If yes, engineers could recommend a kitting solution so that parts are preassembled, which would reduce track time and increase efficiency.”
These are just a couple of examples that show the cost-
savings you can achieve through incorporating engineering support for your operations and production processes.
4. Why You Should Partner with a Distributor who has In-House Capabilities
“At Optimas, we have set up quality laboratories around the globe because we know if we control the quality of the parts we are distribute, we can ensure the quality check process is completed much more efficiently and quicker than if we sent the same products to external quality houses. Having an additional partner to check your parts will increase time to market for your components and likely costs too,” said Christopher.
This requires customers to have faith in the process and parts you provide, and this strategy takes time to build trust as partnership continue to grow. There is certainly demand for using external qualitytesting services; however, by picking a partner who can test and distribute your parts, this will help your operational efficiency in the long-term.
5. Don’t Leave Fasteners Last on Your Design To-Do List
“From our experience, the parts which have had significant input from engineering and quality tend to become better quality products. It’s as simple as that. But fasteners are oftentimes the last component designed into an assembly. This can lead to engineers getting stuck and unintentionally putting themselves in corners due to design constraints. This is where our engineers provide enormous value by funneling the design of customers through standardizing parts or parts they’re already purchasing,” said Babinec.
UK Quality Director, Jonathan Christopher added: “The same is true for quality. Bad quality tends to come from the opportunity to make a mistake. So, if you can simplify your production processes by having fewer changeovers because you’re running bigger volumes of one single component instead of lots of different parts, this will translate in an improved customer experience. One component will result in less errors made on the production line, which results in a win throughout the entire process.”
Optimas is a leading global distributor and manufacturer of fasteners and C-Class components, who also provides customers with full-service solutions that can include engineering expertise and in-house quality capabilities. Even the smallest parts can make a big impact on your business. That’s why we’re focused on finding you the solutions that improve your efficiency and drive profitable growth across your enterprise.
For further details on Optimas visit: optimas.com
Recently, we have extended the assortment of products offered by Autonics – one of the most recognisable suppliers specialising in industrial automation products. The new range that is now available in the TME product catalogue includes various safety switches and photoelectric sensors.
See below for an overview of new products offered by Autonics. In particular, make sure to find out about the automated process safety solutions, i.e. not just ordinary switches, but also excellent quality sensors ensuring the efficiency of employee protection systems, while at the same facilitating adaptation even to less typical systems. Other new items in our catalogue include the ARIO series designed to build cutting-edge, smart, network-based control systems for the centralised control of machinery. We also describe a wide spectrum of photoelectric, laser and fibre-optic sensors.
• Applications and basic functions of stop switches
• Key switch installation
• Safety of operators supervising machinery operation
• Switches with door closing/locking function
• Magnetic sensors in protection systems
• Programmable light curtains
• Safety relays
• Fibre-optic sensor characteristics and capabilities
• Optical sensors and transparent object detection
• High resolution and speed of laser sensors
• Designing centralised control systems featuring the ARIO system
Click here to see the new and extended assorment of sensors for automation systems.
Articulated Pipework Torsion In Hoses
Rotating Cylinders
Swivel joints allow pipework to pressure 1/4” to 40” and beyond.
Vacuum to over 20,000psi.
Stock and bespoke production.
Unique bearing/seal design for longer life.
ISO 9001 CE marked where applicable.
Tel: +44(0)1663 735003
E-mail:
Leading metal-AM innovator, Wayland Additive, will be once again exhibiting at Rapid-TCT on stand 2461 June 25-27, and demonstrating its market dominance in the area of large-scale metal AM parts in a range of difficult to process materials.
Wayland Additive now has a growing number of Calibur3 machines installed around the world that are being used in commercial settings, and is successfully demonstrating that its technology is introducing the use of industrial 3D printing in sectors and for applications areas where the AM process has previously struggled. This is due to the fact that the Calibur3 features the patented NeuBeam® process which has unique high temperature capabilities that opens up a much wider palette of metal material options.
Peter Hansford, Chief Revenue Officer at Wayland says, “The NeuBeam® process delivers on all of the advantages of metal electron beam (eBeam) powder bed fusion (PBF) technology, while overcoming the troublesome issues that have traditionally limited wider adoption. Until the development of NeuBeam®, eBeam technologies were always unstable, and were bedevilled by charging issues. This meant the process needed to be tightly controlled because small changes could upset the balance of the process, leading to instability (smoke events) which are almost always catastrophic. Calibur3’s NeuBeam® or neutralising technology eliminates the chance of smoke events, leaving a very stable environment within which to work. Because of this, it’s much easier to change parameters without disasters. This allows us to give customers what they want, the ability to tune parameters for production, to suit their needs, improving part quality or mechanical properties much more quickly than has previously been possible.”
NeuBeam® is a hot part process rather than a hot bed process. This efficiently creates parts that are free of residual stresses. Furthermore, because the high temperatures are only applied to the part and not the bed, free-flowing powder post-build (no sinter cake) and stress-free parts alongside reduced energy consumption are ensured. This is a win win for end users, faster printing using less energy.
Hansford continues, “So we have process stability, and this allows flexibility when choosing melt temperature and melt strategies. But another key to the Calibur3 and the NeuBeam® process which we will be demonstrating through an array of parts on our stand at Rapid-TCT is the
vastly improved metallurgy capabilities of NeuBeam®, which unlocks a plethora of complex metal production opportunities that current metal AM processes struggle with. This is because the NeuBeam® process is compatible with a much wider range of metal powders, including but not limited to refractory metals and highly reflective alloys. The issue of materials in metal AM is hugely important, with many users forced to use new alloy derivatives created specifically for AM. This leaves them with two unknown quantities — a new process and a new material. This is where NeuBeam® really breaks new ground, with the ability to process existing metal materials, which reduces the pain burden when qualifying new parts.”
Attendees at Rapid-TCT will see parts produced on the Calibur3 from a variety of materials including titanium and tungsten, the NeuBeam® process also able to process nickel, copper, high carbon steels, stainless steel, and cobalt based alloys among others. NeuBeam® is not just material agnostic, but it can produce complex geometries that are impossible on other eBeam systems, and is typically 30-40% faster by removing the need to maintain and sinter the cake.
Attendees at Rapid-TCT are invited to stand 2461 to discuss how the use of Wayland’s Calibur3 metal-AM system can stimulate innovation and promote metal-AM into application areas previously impossible.
www.waylandadditive.com
Optical Surfaces Ltd. has received an order from JEEWOO Photonics South Korea) to produce a 700mm diameter reference flat – a an optical test system being developed for a space optics organisation.
The optical test system is required for aligning and testing long focal length, large aperture multi optical component systems without degrading optical quality.
Benefiting from an ultra-stable production environment and employing proprietary polishing techniques – Optical Surfaces Ltd. can routinely produce large diameter reference flats with typical wavefront error of up to lambda/20 p-v, surface roughness of less than 10 Å rms and surface finish of 40/20 to 10/5 scratch / dig.
Asked why he had selected Optical Surfaces Ltd as a partner for this prestigious supply contract – Mr MoonWhe Hur, director of JEEWOO Photonics said “There are few optics manufacturers in the world able to produce optics of such size and with the specialised test equipment to demonstrate conformance to the ultra-high precision finish specification. Over the years we have worked closely with Optical Surfaces Ltd on a series of demanding optical development projects which because of their highly skilled staff have all been successful with deliveries kept to time”.
well underway, we hope to move onto final polishing and testing soon. To enable us to quality test large diameter reference – we developed a large aperture Fizeau interferometer. Housed in an ultra-stable testing environment, this interferometric set-up allows direct qualification of large diameter reference flats by testing them directly over their complete aperture.
For further information on large diameter reference flats please visit optisurf.com/flats/ or contact Optical Surfaces Ltd. on +44-208-668-6126 or sales@optisurf.com.
For further information on JEEWOO Photonics Ltd please visit www.optictest.com
Photonics Ltd (Daejeon, a key component in organisation.
Dr Aris Kouris – Sales Director of Optical Surfaces Ltd commented “We were delighted again to be selected by JEEWOO Photonics as a supply partner. The production of the large CLEARCERAM®-Z reference flat is
The ISO 9001-2015 approved manufacturing workshops and test facilities at Optical Surfaces Ltd are deep underground in a series of tunnels excavated in solid chalk. This provides an environment where temperature is naturally thermally stable, and vibration is extremely low. With such stable conditions testing of all beam collimators becomes quantifiable and dependable. In addition to these natural advantages, the company has invested in an extensive range of test equipment and uses trusted methods to ensure accurate and reliable testing of surface accuracy, quality, and slope errors.
FORTEC UK are pleased to introduce the new HFA3500TF from Cosel, an innovative low-profile 3-phase, 3500W AC/DC enclosed power supply designed specifically for demanding industrial applications such as semiconductor manufacturing, laser processing machines, robotics, and instrumentation.
The HFA3500TF sets a new standard in power supply technology with its wide input voltage range of 180VAC to 528VAC, accommodating both 3-Phase Delta and 3-Phase Star networks. This adaptability ensures seamless integration into various industrial environments across the globe.
Low Profile Design: Measuring just 41mm (1.61 inches) in height, the HFA3500TF’s compact design fits perfectly into 1U rack spaces, saving valuable space in industrial setups.
Wide Input Voltage Range: Supporting three-phase inputs from 180V to 528V, the HFA3500TF is engineered for maximum compatibility.
Built-in ORING MOSFET: Ensures reliable current sharing and protection in parallel operation modes.
SEMI F47 Compliance: Ensures reliable operation even under voltage sag conditions, meeting the stringent requirements of the semiconductor industry.
Parallel and N+1 Redundancy Operation:
Designed for scalability and reliability, the HFA3500TF supports parallel operation, allowing up to ten units to be connected for a total power output of up to 31.5kW, ensuring continuous power supply with N+1 redundancy.
High Efficiency: Utilising advanced digital control switching technology, the HFA3500TF achieves an impressive efficiency rate of up to 94% at 400VAC input and 65VDC output.
Built-in Alarm: Equipped with a built-in alarm system for enhanced operational safety and monitoring. Built-in AUX Power: Features a convenient built-in auxiliary power output of 12V 1A.
Despite its compact size, the HFA3500TF delivers robust performance with output voltages available at 48VDC and 65VDC, adjustable via a trim function from -50% to +15%. The integrated variable speed cooling fans ensure optimal thermal management, enhancing the longevity and reliability of the power supply.
The 48VDC output HFA3500TF-48 is suitable for a wide range of applications, including measurement and analysis equipment, machine tools, and semiconductor manufacturing equipment, meeting the sag immunity conditions specified by the SEMI F47 standard. The 65VDC model HFA3500TF-65 is ideal for powering Radio Frequency Power Amplifiers (RFPA) and 60V Lithium-Ion battery chargers.
The HFA3500TF is ideal for high-demand industrial applications, providing a reliable, high-efficiency power solution that meets the rigorous standards of modern industrial environments. Whether in semiconductor fabrication, laser machining, advanced robotics, or precision instrumentation, the HFA3500TF can deliver.
For more information about the HFA3500TF and how it can revolutionise your industrial power needs you can view the datasheet here
Titan Enterprises’ flowmeters have been put through the wringer in various harsh environments, from high speed on an F1 racetrack, to deep mining and offshore oil rigs. Titan’s Process Atrato® ultrasonic flow meter is now taking a leap forward and proving to be ‘rock solid’ in tests within a totally unique environment - microgravity.
Multiple space agencies and private space companies around the world, such as Blue Origin, Nasa, Virgin Galactic, and SpaceX, continually explore new technologies and ways to solve specific issues encountered in ultra microgravity situations. NASA, for example, has conducted a number of laboratory experiments on the orbiting International Space Station to explore the effects of microgravity on water and other liquids.
The investigation of fluid flow processes in low gravity or microgravity environs is hugely important, helping to improve processes essential in the production of plastics and other polymers, to manufacturing medicines and operating machines. In space, liquids behave very differently than on Earth, with processes that are usually masked by the Earth’s gravity becoming much more evident. For example, in microgravity, liquids held together by surface tension can achieve sizes much larger than liquids on the ground. Also, when these liquids move, the motions are much slower in microgravity than on the ground.
With no moving parts, Titan’s Process Atrato® ultrasonic flowmeter offers benefits including high reliability, fast response, high-speed batching and precise liquid dispensing, such as in potable water dispensers. Even with restraints on orientation to avoid trapped gas bubbles, the Atrato® sensor’s low-flow capability and through bore design, are showing good results in fluid dispensing tests in microgravity environments for the potential of delivering water to astronauts in space.
Trevor Forster, Managing Director of Titan Enterprises, said: “Our company philosophy has always been about pushing boundaries – of our ideas, materials and technology – so knowing that our pioneering Atrato® ultrasonic flowmeter is being trialled in microgravity and tested to its limits, is incredibly exciting for us.”
To discuss an optimised flow measurement device for your specific application or process please contact Titan Enterprises on +44 (0)1935 812790 or email sales@flowmeters.co.uk. Or visit our website for further information.
The transition to electric mobility is more than just a paradigm shift; it is a direct movement towards a more sustainable future. Behind the shared CO2 emission targets and electric vehicle adoption goals, is the fundamental need for increasingly advanced power technologies and new production processes. In tandem, the market is experiencing significant advancements in the development of high-capacity batteries and efficient electric drivetrains. And while emerging technologies such as solid-state batteries promise even greater energy density and faster charging times, the more immediate challenge is solidifying a reliable, affordable production strategy. This is why Comau’s electrification solutions are designed to support the aggressive goal of building an autonomous EU-sourced electrification value chain.
Comau has more than 50 years of experience in automotive, which is renowned for its technical complexity and competitiveness. This has allowed Comau to experiment with cutting edge technologies and anticipate many of the trends within the e-Mobility space. As one of the early movers in the electrification arena, Comau’s pioneering products and technologies span the electrification value chain and are being used by customers throughout Europe and around the world.
Now, Comau is bringing its advanced battery production technologies to The Battery Show Europe conference, being held at Germany’s Messe Stuttgart from 18-20 June (booth number 9-F50). Billed as Europe’s largest event for the battery and EV tech communities, the industrial automation company will leverage the platform to commercially launch its highly efficient and fully scalable battery cell formation solutions.
As one of the first European companies to locally source this critical component of the battery production process, Comau is in a perfect position to help enhance productivity, reduce costs, and prioritize safety and sustainability of battery manufacturing. Furthermore, its turnkey cell formation and testing
systems can cater to a wide range of production scenarios, from lab-based prototypes to full-scale gigafactories. This ensures that manufacturers can seamlessly transition from development stages to mass production without compromising quality or efficiency. Comau’s cell formation offer encompasses the core processes that transform assembled components into stable, electrically charged battery cells. A crucial phase in the battery manufacturing process, it involves a series of charging and discharging cycles that ultimately ensure both optimal performance and longevity of the cells. This charging and discharging is performed using specific electrical current profiles, after which the activated cells are then aged and tested to ensure they are of the highest quality standards. The fact that the cell formation systems are designed and produced locally by a renowned leader in industrial automation represents an important step towards advancing the European battery manufacturing industry.
The newest element in Comau’s vast e-Mobility portfolio complements the strong foothold already gained in battery module and pack assembly processes, and will increasingly allow Comau to offer a complete turnkey battery solution from powders all the way to packs. Similarly, Comau designs and delivers highly efficient systems for e-drives, hybrid transmissions, components and complete assembly lines, as well as design, testing and manufacturing solutions for hydrogen fuel cells and electrolyzers.
“Battery demand is estimated to increase significantly between now and 2030, driven largely by the panEuropean goal of creating an autonomous supply chain. Despite recent uncertainty regarding the growth rate, the battery market is still expected to exceed 170 billion Euros in 2030* and our broad ranging competence and versatile skills set allow us to respond to evolving scenarios.” explained Pietro Gorlier, Comau CEO. “Comau’s commitment to delivering best-in-class technologies, such as our new cell formation solutions, underscores our ongoing dedication to helping drive the world’s energy transformation goals. Leveraging our unique know-how, long-standing experience in automotive and strong global team, we will continue to support our growing client base and navigate their increasingly complex projects.”
Another electrification enabler is Comau’s cleanroom classified, high-speed Racer-5 SENSITIVE ENVIRONMENTS (Racer-5 SE) industrial robot. This 6-axis articulated robot is engineered to efficiently automate applications with stringent requirements. Its contaminant-free design is ideal for battery cell assembly and the cleanroom assembly of microelectronics, allowing manufacturers to enhance precision and reliability while maintaining the highest standards of cleanliness and performance.
Similarly, Comau’s in.Grid data management platform allows companies to manage the vast amounts of data that need to be collected and analyzed to control process and product quality along the battery manufacturing line. The sophisticated data management tool facilitates real-time data collection and analysis, helping battery
manufacturers maintain optimal quality control and process efficiency.
Comau’s vast portfolio of products, processes, and technologies for electrification enables us to manage everything from prototyping and pre-production to mass manufacturing and end-of-life battery recycling. This holistic approach ensures that we can deliver comprehensive solutions tailored to meet the diverse needs of our clients all over the world. In tandem, the company continues to make substantial investments in research and development, focusing on nextgeneration technologies. In doing so, Comau intends to pave the way for more efficient, sustainable battery technologies.
The company’s dedication to innovation extends to its involvement in multiple pan-European e-Mobility projects. In one such project, Comau is developing a more compact cell formation chamber layout and warehouse management strategy that optimizes the recuperation and reuse of electric energy and heat. Moreover, Comau has pioneered a robotic system for the automated dismantling of used batteries. This system employs a flexible, repeatable, and standardizable process, enabling companies to reduce waste and maximize the reuse of raw materials from battery packs. This innovative approach aligns with the growing emphasis on sustainability and circular economy principles in the battery industry. These types of forward-thinking initiatives not only enhance efficiency but also contribute to more sustainable manufacturing practices.
To further help companies achieve their sustainability goals, Comau’s technology design and deployment strategy includes concrete energy and ESG objectives. Indeed, sustainability, both in terms of energy and consumption efficiency, is a common denominator that extends across Comau’s 360° portfolio of cutting-edge technologies. All this, together with its commitment to continuous innovation, allows Comau to meet the current needs of its customers while helping shape the future of the industry.
*Comau’s internal estimatesincluding battery cells, modules, packs and e-motors - are corroborated by various market studies.
Visitor registration is now open for Advanced Engineering, the UK’s annual gathering of engineering and manufacturing professionals. Now in its 15th year and being hosted on October 30 and 31, 2024, Advanced Engineering UK is keeping the same format that reaped success from last year’s exhibition, having received high praise from exhibitors and visitors in regards to the cross-industry floor layout. Anyone interested in attending this year can register for a free ticket on the Advanced Engineering website.
This year’s show will expand on the success of two forums introduced last year — the Main Stage and the Advanced Materials & Technologies (AMT) forum. The Main Stage will feature keynotes and key industry players, while the AMT forum will delve deeper into end user case studies across all sectors.
Such expansions have been made to compliment the success of the annual show’s rebrand in 2023, having presented a fresh look for visitors. The event featured a new cross-industry floor layout, which was previously divided into several zones, allowing a broader range of exhibitors from a variety of industries that included newly added sectors like marine, motorsport, construction, medical, rail and sport.
Over 8,800 visitors were able to explore both events, which included 400 exhibitors from AE and 202 from its co-located show, Lab Innovations, all with a single badge. Among the visitors were representatives from well-known companies like Airbus, Rolls-Royce, IBM, Boeing, McLaren, BAE Systems, Catapult HVM, the Department for International Trade and Jaguar Land Rover.
“The overwhelmingly positive feedback from 2023 confirmed that the changes made worked, with exhibitors and visitors having found that the new
approach created a more collaborative atmosphere for better interaction and networking,” explained Alison Willis, director at Easyfairs, the organiser of Advanced Engineering.
“This year, the forums will offer industry insights on the following trending topics; sustainability, innovation, government and policy, automation, AI and skills and levelling-up, all of which have been curated by our outstanding advisory board and industry partners. We’re also planning to broaden our scope by providing high-quality content from an even greater variety of industries.”
“I think the fact that there’s so many visitors that I would describe as high value engineering and manufacturing businesses in one place is quite unique in the trade show world in the UK, added Andrew Kinniburgh, director at Make UK Defence. “From a Make UK –Defence perspective, it’s really useful to have all of those companies in one place.”
Click here to register for free.
According to McKinsey and Company, process optimisation and increased investment in equipment are two crucial pathways along which material-handling leaders can secure their competitiveness in today’s markets. One essential aspect that often gets overlooked is the significant impact of bulk material handling on achieving this objective. Stephen Harding, the managing director of Gough Engineering, delves into the importance of specialised equipment, like big bag dischargers and vibratory screening technologies, in securing competitiveness in today’s markets.
“Material handling,” according to McKinsey’s report, A changing material-handling market: How to ensure continuous success, “is only as effective as the technology it relies upon.” The report refers to the “primary subsegments” of material handling equipment: cranes, forklifts and conveyers. Here, we will focus on conveyors — specifically bulk material handling systems.
Bulk material handling encompasses the movement and management of large quantities of powders, grains, liquids, or solids. It plays a crucial role at the front end of production in establishing the quality and value of products and ingredients throughout the industrial manufacturing production processes. A prime example is the sugar industry, where efficient bulk material handling systems facilitate smooth material flow, meeting customer demands promptly, boosting productivity, while maintaining product quality. To realise these benefits, specialised equipment and systems are indispensable for efficient transfer, storage, and distribution of raw materials and ingredients at various stages of the manufacturing processes.
Big bag dischargers serve as a fundamental component in efficient bulk material handling. These machines enable seamless movement by transferring products from within a contained or suspended bulk bag, restoring them to their original refined or processed state for use in the customer’s product production. Determining the geometry, capacity characteristics, and product behaviour within the bag are essential factors considered at the outset.
screening and in-line metal detection. By analysing the contents of big bags for oversized or undersized materials, manufacturers ensure the consistency and integrity of their products as feedstock for subsequent processes.
This level of quality control is particularly crucial in sugar manufacturing, where screening and metal detection are essential before transferring sugar to other production stages, guaranteeing the finished product’s quality for sale to end users.
A practical example of this is when Gough Engineering offered its own solutions to support a UK-based sugar beet supply company. The company, processing approximately eight million tonnes of sugar products annually, sought a comprehensive turnkey solution to cope with the increasing demand for refined white granular sugar. Gough Engineering was approached for their expertise in big bag discharger systems, vibratory screening technology, and fast product transfer solutions.
The solution devised by Gough Engineering involved a twin big bag discharger unit, agitator paddles for optimal product flow, pneumatic valves for flow control, Gough Vibraflo® GVF6 vibratory screens for oversize particle separation, and a Floveyor F4 aero-mechanical solution for elevation. An automatic detection and separation unit for ferrous metal removal ensured the product’s quality and integrity.
The modular design allowed for reliable and safe flow, significantly improving the transfer rates to 30 tonnes per hour, per tanker. The system’s electrical controls with an Alan Bradley PLC and integrated Human machine Interface (HMI) and pneumatic process management ensured seamless monitoring and operation.
However, these material handling systems should go beyond mere transfer. These systems should incorporate value-adding processes such as product
Efficiently designed material handling systems instil
manufacturers with the confidence to meet customer audits and industry standards. Moreover, these systems facilitate the smooth transfer of products between different stages of production, ensuring materials’ integrity and quality.
To truly optimise their production, businesses must invest in bulk material handling solutions like big bag dischargers and integrate quality control measures such as screening and metal detection. These technologies streamline operations, ensure product integrity, and fulfil customer requirements.
As McKinsey’s report highlights, material handling effectiveness heavily relies on advanced technology, particularly in the primary subsegment of conveyors,
Bulk material handling systems are vital for the sugar industry, including ensuring a smooth material flow.
which includes bulk material handling systems. The significance of these systems in preserving product quality and value cannot be overstated, making them indispensable for efficient material transfer, storage, and distribution at various stages.
By incorporating specialised equipment like Gough Engineering’s big bag dischargers and vibratory screening technologies, businesses can streamline operations, driving commercial growth and success in an increasingly competitive market.
To learn more about how Gough Engineering’s material processing and handling solutions can enhance supply chain efficiency, visit its website.