
Residential retrofits must reach one million per year by 2030 to meet UK net zero aim: How can copper support this demand? [click here]
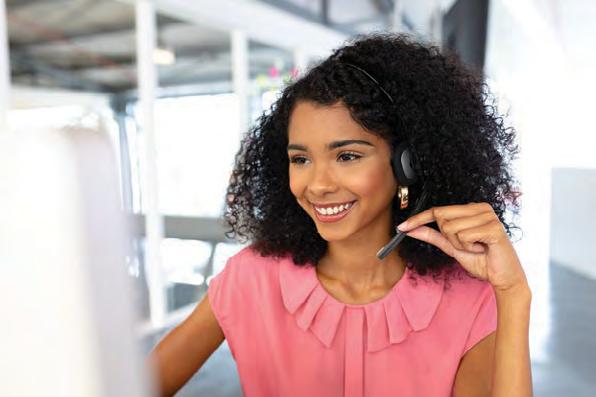
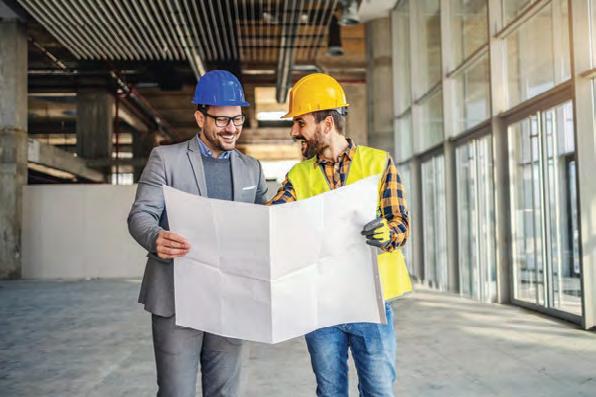

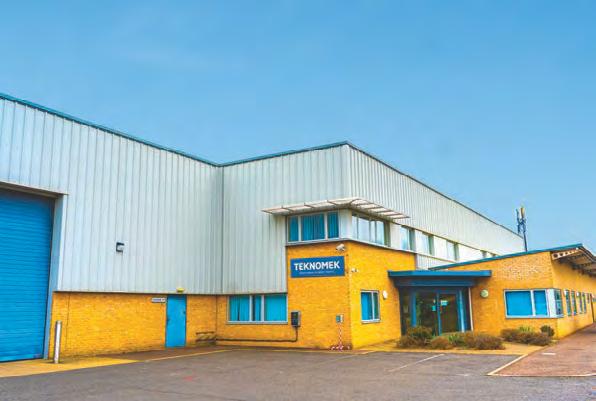
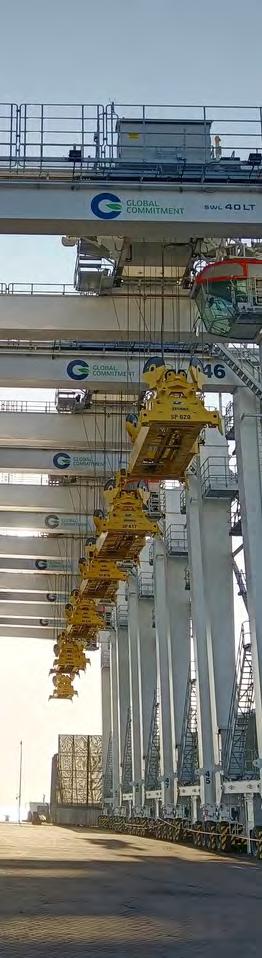

Residential retrofits must reach one million per year by 2030 to meet UK net zero aim: How can copper support this demand? [click here]
Managing the risks from an Invisible hazard – UV exposure on site. Ben Stacey, Snickers Workwear Product Specialist writes:
Dressing right for the working environment you’re in is very important – not only for working efficiency, but also for UV protection in the summer.
The Institute of Occupational Safety and Health estimates that outdoor workers can be exposed to over 80% more UV radiation than indoor workers and, if the UV index reaches three or above, sun protection measures should be taken. It may come as a surprise to some that the UV index regularly exceeds this level during the summer months in the UK and, according to the Met Office, UV rays can be strong enough to cause sunburn here between April and September with 80 per cent of UVA rays passing through cloud.
The link between skin cancer and sun exposure is now more widely understood and workers who regularly work outdoors are most definitely at increased risk from over-exposure to UV radiation. With one in three cancers diagnosed as a skin cancer, each episode of sunburn however small increases the risk of getting it. So why do some people who work outdoors in the UK not use sun protection cream and other sun protection measures – such as proper working clothes?
Hard work in hot and humid conditions can not only be uncomfortable, but hazardous. So, when the heat is on, it’s important that you take the necessary precautions to stay cool, dry, and well-covered. That’s where Snickers Workwear’s moisture-wicking, and UV-protective workwear can play an important part in your personal protection and wellbeing. When you’re choosing the right working clothes up for a hard day’s work outside in the summer, there are three important factors to consider.
For summer working, choose workwear that is designed to create a kind of climate control system for your body. Snickers Workwear does just that. Designed to help you stay cool, the summer collection has garments that provide UPV40+ protection to make getting the job done
as comfortable and safe as possible. Breathable fabrics deliver better ventilation and dry faster once they’re wet from perspiration. And even though cotton is thought to be a lightweight fabric, its high absorbency makes it dry very slowly. Cotton garments drenched in sweat are uncomfortable.
In warm, sunny working conditions, you need clothes with exceptional breathability and ventilation to avoid heat stress. With that in mind, Snickers Workwear uses stretchable fabrics with 37.5® Fabric Technology. Patented particles in the fabric help your body maintain an ideal core temperature – a process of thermoregulation - by removing perspiration vapours before they can turn into liquid sweat. That means you can stay both cool and dry no matter how hot it gets.
Sustainability is a key part of Snickers Workwear’s design and development philosophy. It’s not just functionality, practicality and the physical demands on the body when working hard which are key drivers in the brand’s product development, it’s the physical demands that product manufacturing places on the environment that matter too.
So, if you’re thinking about what’s most practical and beneficial to wear this summer and, if it’s performance and protection you need, check out the upgraded lightweight and breathable 37.5® fabric in Snickers Workwear’s Mid- and Base-layer clothes. With superb cooling technology, they’re great for demanding tasks on site as well as UV protection.
Style, comfort, functionality and performance have always been key drivers in Snickers Workwear clothing development over the years. But now, modern day concerns about sustainability and personal protection from the invisible hazards have brought a new dimension into the technical design of Snickers Workwear for this summer.
A 100% affordable housing scheme at Arnold Road, in Bow, East London, will create 62 homes in two mid-rise buildings of six and eight storeys. Designed by architects Henley Halebrown, the scheme – which was shortlisted for the 2020 Housing Design Awards – is cleverly woven into a compact triangular site. The architectural concept breaks what might have been one long building block into two separate buildings, permitting morning and afternoon light to penetrate between the buildings. This reduces their impact and improves the microclimate for residents and neighbours as well as increasing the surface area of the new buildings to achieve 80% dual aspect homes. Together the buildings frame an entrance courtyard designed to encourage residents to meet and talk, and children to play together.
Contact Schöck on 01865 290 890; or for full details of the Isokorb range of solutions visit: www.schoeck.com/en-gb/isokorb
The heavy masonry façades incorporate recessed balcony terraces and Schöck have supplied Isokorb structural thermal breaks for both the in-situ concrete balconies and the precast concrete façade banding. On the eight-storey South Block the inset balconies are supported on two sides using the Schöck Isokorb T type Q. This is a load bearing thermal break element for transferring shear forces on supported balconies, recessed balconies and for occasional peak shear forces. The six-storey North Block features typical internal corner balconies with external corner column support and again features the Schöck Isokorb T type Q, along with the T type H for the transmission of planned horizontal forces parallel and/or perpendicular to the insulation level.
For the precast stone bandings on the project two Isokorb products were utilised. The T type F, which is a load-bearing thermal insulation element for curtain parapets and balustrades, which transfers normal forces, moments and shear forces. The T type K is also used and is a load bearing thermal break element for free cantilevered balcony construction and transfers negative moments and positive shear forces. For Arnold Road the product had to be specially adapted and required a bespoke design 500mm in length –but supplied in 1m lengths. The precaster, Barnsley-based Con-Tech Services Ltd, then cut the Isokorb in half on site for the required detail. To avoid any clash
of reinforcement, the two covers were designed and detailed with 50mm cover required on the north and south elevation and 30mm cover required on the east and west elevation.
The fully compliant and dependable Schöck Isokorb range offers the widest selection of structural thermal break solutions from any European supplier; and in the UK enables projects to meet full compliance with the necessary Building Regulations (and the impending Future Homes Standard criteria where relevant). In addition to the Isokorb types used on this project, there are also solutions for concrete-tosteel, steel-to-steel, renovation projects – and even a maintenance free alternative to wrapped parapets. All products have the security of independent BBA Certification, which provides NHBC approval. The temperature factor requirement (fRSI) used to indicate condensation risk, which must be equal to, or greater than 0.75 for residential buildings, is also easily met by incorporating the Isokorb.
Arnold Road Courtesy of Henley Halebrown Some of the bespoke Isokorbs supplied by Con-Tech Services LtdResidential retrofits must reach one million per year by 2030 to meet
With the Government set on the UK achieving net zero carbon emissions by 2050, the pressure is on for the 25 million existing buildings across the country with inefficient water and energy systems.
To increase the sustainability of older buildings, their ability to retain heat must be improved, and fossil fuel energy sources replaced with renewable alternatives. This can be achieved through climatebased retrofitting – the installation of new features and technologies including heat pumps, air conditioning, insulation and renewable energy systems.
With retrofitting a necessity to future proof our homes and keep residents safe and healthy, recyclable materials such as copper are integral in driving forward sustainable change.
The UK’s commitment to climate-based retrofitting
The Climate Change Committee has stated that residential retrofits need to increase to one million per year from 2025 to 2030 for the UK to hit its 2050 net zero target.
In response to the demand for high-quality residential retrofit advice, the Royal Institution of Chartered Surveyors has launched a new Residential Retrofit Standard, effective from 31st October 2024.
This initiative provides a framework to not only improve the environmental impact of our homes, but also the health of residents, as common illnesses caused by cold homes in the winter currently cost the NHS £1.4 billion every year.
The role of copper in our homes
As the uptake of climate-based retrofitting increases, the demand for copper is also rising due to its benefits over other materials like plastic.
With the ability to facilitate the efficient delivery of electricity and thermal conductivity, copper is the preferred material for heat exchangers and wiring – boasting a typical lifespan of around 70-80 years. In comparison, plastic lacks durability and can easily crack in hot temperatures.
In air source heat pumps, copper piping is used to offer a more structured piping path and better heat circulation, and its antimicrobial properties ensure a low level of toxicity. In air conditioning units, copper piping allows for faster cooling, and lasts longer over time due to its ability to handle oxidation and corrosion.
Copper has proven itself to be a key component in successful retrofit projects – Water Kinetics installed their copper Eco-Duo pipe system at the University of Bristol to replace a traditional domestic hot water system, and five years later, saw a reduction in energy consumption and associated carbon reductions of up to 52%, with an average of 49.7%.
With urgent change needed to ensure the UK’s houses meet new standards, copper’s sustainable qualities make it the ideal candidate for retrofitting projects.
Owning a home, rather than renting, comes with a varietyof advantages. One such, is the opportunity to decorate your rooms to suit your tastes, you can enjoy your own private space, and you can re-design your property’s look whenever and however you wish. But there’s no denying that owning a house has its fair share of expenses.
You do not have the luxury of phoning your landlord to handle any mishap or maintenance work. In fact, your home’s many components will not last forever, so you need to plan for repairs and replacements. That said, it may be difficult to estimate how much you should put aside to fund potential home repairs throughout the year.
Here, we discuss some general advice on what homeowners should be prepared for in the not-so-distant future. We explore the lifespan of some common home features while discussing how much you may want to save for a rainy day. Click here to read the full article >
The UK’s leading independent construction and property services company, Willmott Dixon Group, has announced a new three-year partnership with the training and compliance experts TTC. Since the beginning of Willmott Dixon and TTC’s collaboration in 2021, the number of driver-related ownfault insurance claims has fallen by 51%, while new offences committed by fleet drivers reduced 46%.
The reduction in incidents is set against an increase in both the number of drivers employed by Willmott Dixon and the total mileage they have driven, with the company managing more than 3,000 vehicles in its fleet, including grey fleet vehicles. Furthermore, 99% of Willmott Dixon drivers are now licence, MOT and insurance compliant.
“We were committed to initiating a company-wide culture of driver risk awareness, placing safety at the forefront of drivers’ minds across our fleet.
Simultaneously, we wanted to reduce our overall business carbon emissions by running a more sustainable fleet. However, we quickly realised we needed expert support to meet these ambitions,” explains Mark French, Chief Health, Safety and Environmental Officer for Willmott Dixon Group. “Embracing TTC’s end-to-end fleet risk management expertise, which starts with conducting the necessary driver checks, through to monitoring driver behaviour and then delivering personalised training, has been instrumental in our success in educating our drivers and proactively switching to greener mobility options.”
TTC’s unique risk management platform, Continuum, delivers live driver data and visual dashboards, providing clear visibility and more accurate realtime insights into individual driving behaviour, as well as trends across the fleet. With data able to be interrogated more accurately and instantly, ‘hot spots’ are identified, and effective risk management strategies can be employed rapidly. Willmott Dixon is now not only proactively monitoring its drivers and predicting who needs some level of intervention, but also providing training for the benefit of the business and its drivers.
Mark French continued: “Continuum allows us to identify when an individual may benefit from additional online training, such as addressing speeding concerns, but it also helps those who may benefit from getting more familiar with driving a commercial or electric vehicle. The elearning has proven extremely successful, and take up has been excellent throughout, on both optional and mandatory courses. By working hand-in-hand with our Fleet Compliance Manager, Sareen Dhillon, TTC has adapted both its risk management platform and its training programmes to meet our specific needs, creating a bespoke solution that is easy for us to navigate. Sareen Dhillon winning the Brake award for 2023 Road Risk Manager of the Year is a testament to the progress we have made together, and will continue to make in the coming years.”
David Marsh, CEO of TTC added: “Willmott Dixon has been inspirational in its commitment to improving driver safety and reducing the environmental impact of its fleet. Click here to read the full article >
Bauer Technologies has been awarded the quay wall contract for the revitalisation of Ardersier Port near Inverness, Scotland.
The multimillion-pound project, awarded by Haventus, begins in May 2024. Specifically, the project will require Bauer to install diaphragm walls for the front quay and rear anchor walls. These structures, crucial for the port’s operational efficiency and safety, underscore the ambitious scale of the project. The front quay wall, with its impressive depth of up to 42 meters and widths ranging between 1,200mm and 1,500mm, and parallel to a rear anchor wall, up to 27 meters deep and 1,000mm wide, represents a significant undertaking in enhancing the port’s capabilities.
The transformation of Ardersier Port is set to play a significant role in invigorating the local economy, with the potential to enable hundreds of direct and indirect jobs and re-skilling opportunities in the community and will provide a key facility in delivering the UK’s 50GW offshore wind energy target by 2030. Its strategic location, combined with enhanced
operational capabilities, positions Ardersier Port as a key player in Scotland’s offshore wind deployment capability.
Speaking about the project, Bauer Technologies MDs’, Paul Doyle and John Theos, commented: “The redevelopment of Ardersier Port is a landmark project both in scale and in its approach to ensuring sustainability.
As well as being the largest UK brownfield port redevelopment project, the project has received praise for its environmental sensitivity and for delivering real benefits to the local community. It aligns perfectly with Bauer’s sustainability ideals and ethos, and we are keen to demonstrate these practices on what will ultimately be a transformative undertaking.”
Arco, the UK’s leading safety company, has completed the installation of fall protection systems on the UK’s tallest and fastest rollercoaster- brand new Hyperia!
Hyperia, which opened on the 24th of May, is the newest ride at Thorpe Park in Surrey.
Built by Mack Rides, the new attraction stands at an intimidating 72m (236ft) and will reach speeds of over 80mph.
The safety systems installed by working at height specialists from Arco Professional Safety Services provide a continuous safe connection on the rollercoaster, allowing maintenance crews to carry out routine and reactive tasks with confidence.
Arco installed Two MSA Latchways BridgeLatch fall
arrest and restraint systems along the entire 111m (364ft) incline and crest of the rollercoaster, allowing workers to access the lift portion of the rollercoaster safely.
They also fixed MSA Latchways Mansafe fall arrest systems along the station return brake platform and the station exit maintenance platform.
Matthew Glass, fall protection manager at Arco Professional Safety Services, said: “We were thrilled to be a part of this project for the Hyperia coaster, the latest attraction at one of the UK’s top theme parks.
“This installation is the latest in a longstanding partnership with Merlin Entertainments that has allowed Arco, the Experts in Safety, to demonstrate our expertise in working at height safety and love of (safe) thrills.
“I know I speak on behalf of the whole team when I say we are looking forward to getting to experience the UK’s new tallest and fastest ride when it opens.”
Dan Warwick, health & safety director at Thorpe Park, said: “Arco have been an instrumental part of the team, assisting us with the installation of working at height lines – a vital element of the Hyperia ride construction.
“With the ride standing at an epic 236ft tall, these lines will be used to safely enable our engineering team to get up and down the incredible lift hill for all maintenance and daily pre-opening checks.
“The lines will also be used by our staff and guests in the event of an evacuation being required on the ride. As part of this, the Arco team worked closely with us to ensure we have well-planned and expertly curated evacuation plans, which form a critical part of the overall project.”
Arco Professional Safety Services provide consultancy, training, services and equipment to manage the most complex and high-risk, high hazard scenarios, specialising in working at height, confined spaces and respiratory management.
Find out more at arcoservices.co.uk
Philip King FCICM, former Small Business Commissioner and advisor to PKF Littlejohn Advisory, believes a ‘back to basics’ approach would help many businesses in the construction sector overcome the late-payment challenge. Businesses across all sectors are under pressure. One only has to look at the number of failures in the construction industry to know this to be the case. In fact, in the last quarter alone, construction was the only industry to suffer more than 4,000 insolvencies, comprising 18% of the quarter’s total figure, placing it above both the retail and hospitality industries which are under similarly significant financial pressures. The recent failures of Buckingham, the go-to stadium builder in the industry, Kenham Building and the renowned Scottish housebuilders, the Stewart Milne Group, further proves the point.
It is an established fact that companies often become insolvent not because they are inherently bad businesses, but simply because they run out of cash. Poor cashflow management, compounded by bad debts, high material costs and slow paying customers, are typically to blame.
But while it is tempting to lay the blame wholly on late payment, businesses must shoulder some of the responsibility for their own poor credit management practices. Put another way, best practice credit management can limit the amount to which a business finds itself financially vulnerable.
So how can bad debts be avoided, and payments accelerated? Much can be achieved by getting back to basics and doing the basics well.
First and foremost, even the most basic checks can avoid potential embarrassment later. Know your customer (KYC) should be the mantra of every director, every sales executive, and every individual in your credit team. How well do you know the company you are dealing with? What is their Company Registration Number? Do they
even have one? What is their legal status? Are they a limited company? A Partnership? A PLC? LLP? All such information is important, not least to ensure you invoice the correct legal entity at the point your product/service has been delivered.
Using data from reputable credit reference agencies is always advised to supplement the information stored at Companies House. This enables you to dig deeper and get beneath the company itself. It will help you determine the amount of credit you want to extend, especially since their success and survival may depend on the stability of their customers and other suppliers.
As well as published sources, there are also other tactics you can use to discover more about the company you keep. Looking through their social media accounts (LinkedIn, Facebook etc) and any comments around them can give you hints about their reputation and how they treat their supply chain. Traditional media coverage through google searches can also give you a better steer on their financial viability. Google Search can also show if the warehouse they say they own, even exists!
Once a new customer is being onboarded, the terms and conditions you agree are absolutely critical. They should be documented with explicit payment terms.
The concept of ‘30 days’ – a particular favourite among politicians and the media for denoting best practice – can still mean different things to different people. Is that 30-days from date of invoice, receipt of invoice, or end of month, for example? This needs to be crystal clear or else 30 can so easily become 50 or more.
When you are invoicing, make sure you understand their payment and invoice approval process and whether, for example, a purchase order is required and what other specific information may be needed. Make sure the amount you are invoicing is also correct in terms of what has been agreed; even a penny difference can cause the payment process to grind to a halt!
In terms of how you interact with your customers, build a strong relationship with key people in the company; they could be invaluable when you need to chase payment ahead of other suppliers. At your end, keep the ledger clean and have absolute clarity about what invoices are outstanding. Confusion is a great obstacle to payment and can easily be exploited by those who are seeking to delay paying what they owe.
Making contact in advance of the due date to ensure the invoice has been received and is correct will also reduce the likelihood of a payment subsequently being held in dispute. Keep large totals separate from smaller ones; there is nothing to be gained for having a £10,000 invoice comprising £9,800 for the product and £200 for the delivery held up because the delivery charge is being disputed.
Even if you have clear lines of communication with the customers, always follow up on the
day the invoice is due; never wait and hope for the best. Hope is not a strategy and someone else will be being paid while you’re left waiting. To that end, never be afraid to escalate a late payment to your collections team and/or a third-party activity sooner rather than later. A customer that doesn’t pay you isn’t a customer worth having.
Such advice should not come as a surprise, but in my 40 years in credit management, it still amazes me how businesses are quick to blame everyone else when they’ve ignored many of the fundamentals themselves.
Getting back to basics may not always be successful, but like winning the lottery, you first have to buy a ticket. And if despite all your best efforts, an insolvency may still be looming, talk to the experts at PKF Littlejohn Advisory. They might be able to help the business avoid failure and, if the worst happens, they can work with you for the best outcome from the unfolding insolvency process.
The advice in this article is derived from Philip King’s five-step model philipking.net/five-step-model
In environments where humidity and heat reign supreme, maintaining a fresh and clean interior can be a constant battle. From spas to shower areas and other damp spaces, moisture can quickly take a toll on the building’s interior, leading to discolouration, warping and potential mould growth.
At Zentia, we understand the unique challenges faced by businesses that operate in these conditions, which is why we are proud of Aquabloc –our toughest ceiling tile that defies humidity and heat to keep interiors looking pristine for years to come.
Made from hydrated calcium silicate, the Aquabloc tile is a true game-changer with 100% Relative Humidity (RH) performance. This means it can endure even the most challenging environments without comprising its structural integrity or aesthetic appeal.
Whether you require a ceiling tile solution for a luxurious spa, shower facilities, or any other facility where humidity and heat are a constant, Aquabloc is the perfect answer for creating interiors that remain bright, fresh and inviting.
In addition to its exceptional performance, Aquabloc offers an easyto-install board edge, making it simple to incorporate into any new or existing grid system. Once installed, the white ceiling tiles can instantly elevate the ambiance of interiors, adding a sense of light and height.
Specification with Zentia has never been easier. A team of dedicated Architectural and Design Consultants throughout the UK are ready to help with exploring design concepts or finalising specifications. You can also see us at Material Source Studio in Manchester or Glasglow, a oneof-a-kind hub of design inspiration for architects.
Zentia are partners with NBS, a free-to-use construction product platform that allows you to quickly and easily find, select and specify our products. This means you can find all of our products on NBS, with accurate and up to date specification data, making project design simple.
By choosing Aquabloc, you are not just investing in a ceiling tile, you are investing in the longevity and refinement of your interior spaces. Say goodbye to the constant cycle of replacement and repair, and enjoy even more peace of mind with Zentia’s 30 year warranty when used with a Zentia grid system. Say hello to a fresh, inviting atmosphere that prevents humidity and heat from dictating the look and feel of interior spaces. Embrace the power of Aquabloc and experience the difference a humidity-defying tile can make.
Find out more, or update your sample library here.
While you may have heard of fast fashion, you might be surprised to learn that fast furniture is an emerging development. The furniture market is expected to reach a revenue of around £18.16 billion in the UK according to Statista Market Insights, however the contribution of furniture to bulky waste is evident, with data showing it covers around 42% of it, equating to around 670,000 tonnes.
Scott Hawthorne from Skips & Bins, leading providers of commercial waste disposal in the UK, has seen firsthand the impact that fast furniture has on the waste disposal and management industry. He’s provided some expert insight into what it is, its impact, and what to look for as a substitute.
What is fast furniture?
Fast furniture follows similar production methods as fast fashion, which relies on producing pieces made with cheaper materials designed for quicker production in larger quantities. This results in faster wear over shorter periods and requires throwing away and replacing more frequently than higher-quality furniture.
It’s designed and produced to be more in tune with emerging trends and décor styles without shoppers having to
spend big to keep up with the latest interior concepts. This translates to mass-manufactured pieces made typically by machines rather than a smaller stock of quality and unique pieces.
How it contributes to throwaway culture
Fast furniture can show signs of wear after only a few months of use, leading to having to replace it with a new piece. While fast furniture can be a useful temporary solution when you’re looking for a highquality new addition to your home and décor, it can be difficult to find a piece that will likely be a permanent fixture in your home.
Not only does this have a huge impact on homemakers’ budgets, as they have to account for buying new furniture and the contributions to landfills, but the cheap materials they’re made with can often contain harmful byproducts. Once they begin to degrade, the resins, foams, and dyes can’t be effectively recycled, meaning that they can have a significant impact on the environment.
Scott Hawthorne has voiced his concerns around fast furniture and its impact on waste management companies: “A vast majority of fast products, be it fashion or furniture, often come with planned obsolescence, where the materials wear down much faster and
require total replacement rather than repair. All of this ends up in landfills or waste management centres, and the data of how much there is can be hugely overwhelming.
“Plus, it’s not just the immediate impact on the environment from the materials that are a concern. Consider the amount of greenhouse gases emitted when delivering a piece of furniture or even just shipping it to a shop floor and stockroom. Now multiply that for every piece of fast furniture made in a year, and you start to see the horrifying wider implications.”
Sustainable and recyclable furniture is the future
So, what is the solution to not spending on fast furniture pieces? Well, if you’re looking to substitute sheerly based on cost, auction houses, charity shops, or marketplaces can be a fantastic way to find cheaper pieces for your home. While they might need a bit of TLC to make them presentable, whether through upholstering or repainting, you can also find
timeless pieces that’ll naturally fit in without any adjustments beyond some quick cleaning.
Shopping for timeless rather than trendy is one important factor in reducing the prevalence of fast furniture. Choosing pieces that are tried and tested, like a classic wardrobe with an inoffensive trim, and not picking something based on how popular it currently is on social media will lead to it becoming a mainstay from your own tastes rather than someone else’s.
In many cases, when buying new, buying from an established brand often means you’re buying products that are built to last, thus eliminating the need for constantly replacing items in your home. For those who are more conscious of where they’re purchasing their furniture from and how sustainable it is, doing the right amount of research into what materials are used and the brands’ environmental, social, and governance (ESG) policies and strategies can help make an informed decision.
For More Information Please Click Here
HSS Hire, a market leader in equipment hire in the UK, has announced the launch of HSS ProService, a revolutionary extension of its business designed to reshape the way businesses buy and hire equipment, building materials, fuel and more.
Building on HSS Hire’s heritage, expertise and verified supplier network, the brand has introduced the UK’s largest online building services proposition, giving businesses of all sizes instant access to over 900 sellers and 50,000 active products.
The marketplace offers a comprehensive solution for businesses of all sizes to buy, hire, and manage everything they need for their building services requirements.
Dani Hodges, Chief Commercial Officer at HSS ProService, said: “We’re extremely proud and excited to take HSS ProService to market.
“Having trialled the marketplace with existing customers over the last few months, we’ve seen immediate uptake from a broad range of businesses. We’ve had some fantastic feedback already, and now we’re excited to start building on that community.
“We’re first to market with this and absolutely welcome feedback. Every day, we get input about what people would like to see next, and because we own the marketplace infrastructure, we can react quickly. Anything that customers ask for is our priority.
“Our mission is to provide the ultimate all-in-one marketplace that simplifies and centralises the entire procurement process, from sourcing to supply chain management.”
Through this single marketplace, businesses can streamline their purchasing processes, enhance admin efficiency, and gain control and insight into their spending activity.
Key features of HSS ProService include:
• An unrivalled product range, including the HSS rental range, partnerships with equipment sellers and building merchants, bulk fuel and more on the way
• Proprietary Scope 3 reporting: a market-first use emissions calculation based on manufacturer information and DEFRA conversion factors to measure CO2e equivalent per hour for emitting products
• Simpler sustainable choices with greener alternatives recommended at the point of order and emissions tracked so organisations can easily see top emitting products and opportunities for improvement
• The ability for businesses to set user access and approval flows so digital paper trails track and store automatically, and users can set out of offices and temporary points of contact
• Real-time visibility on spend across users, sites and projects, and a commercial insights dashboard to replace spreadsheets and self-analysis
• Ease of use, including a Live Chat with operations, credit control or product experts in less than a minute
Dani added: “We’ve been really lucky that we’ve been able to invest so much time and resource into the marketplace. Many companies can’t and that’s why we’re so keen to make it a real community space for those that want to get ahead in sustainability reporting and enjoy the commercial advantages that come hand in hand with that.”
For more information about HSS Pro Service, please visit www.hssproservice.com
BAUER Technologies Ltd, a leader in geotechnical contracting, is pleased to announce its involvement in the A417 Missing Link project, a significant upgrade of a 3.4-mile-stretch of road through the scenic Cotswolds. This project not only aims to enhance road safety and connectivity but also places a strong emphasis on environmental sustainability, aligning with Bauer Technologies’ commitment to sustainable construction practices. Specifically, Bauer has been commissioned by Kier Transportation, the main contractor, to install the piled foundations for four bridge structures, enhancing connectivity and safety. These structures include the Gloucestershire Way Crossing, Stockwell Overbridge, Cowley Overbridge, and Shab Hill Junction. Bauer will install 205 piles of varying diameters, reaching depths up to 28 metres below ground level. All of Bauer’s operations will be integrating seamlessly with the project’s broader sustainability objectives, including the reuse of excavated materials, which significantly reduces the overall environmental footprint, and working in a way that demonstrates sensitivity to local wildlife.
The A417 Missing Link is expected to drastically reduce traffic congestion and enhance road safety, while its design and execution maintain the highest standards of environmental care. The project includes extensive measures to protect local wildlife, including translocation of species and habitat creation, ensuring the natural beauty of the Cotswolds is preserved and enhanced.
Speaking about the project, Bauer Technologies Managing Directors; Paul Doyle and John Theos, commented,
“Bauer is delighted to be part of the A417 Missing Link project, which not only allows us to showcase our advanced engineering capabilities but also our dedication to sustainable construction practices. This project is a model for future infrastructure development, combining technical innovation with environmental responsibility”.
Gavin Jones, project director for Kier Transportation, added: “We are pleased to be working with Bauer on the A417 Missing Link, which is a fantastic project in the heart of the Cotswolds surrounded by an Area of Outstanding Natural Beauty and a Site of Special Scientific Interest.
“The strength of our supply chain partners is integral to the success of this project. Together with Bauer, our other supply chain partners, and our client National highways, we look forward to delivering vital new infrastructure that will benefit road users and the local community for years to come.”
For more information about BAUER Technologies Ltd, visit www.bauertech.co.uk
Casper, Phillips & Associates Inc. (CP&A) has delivered a presentation to port authorities titled, ‘Peer Review of Container Cranes’, to assist in future procurement processes.
CP&A offers a wide variety of services, including specification, design, manufacturing review, modification, and accident investigation; and it is well positioned to remind terminal operators and fellow stakeholders of the risks involved with container crane procurement. Including transport and offloading in the peer review scope is a good way to manage some of these risks — but that’s just the start.
Richard Phillips, mechanical engineer at CP&A, said: “The procurement process for container cranes is somewhat unique and presents many challenges. Unfortunately, some procurement decision makers believe buying container cranes is the same as acquiring any other piece of equipment, such as a forklift or a company van.”
As should be unanimously accepted by crane manufacturers, a peer is someone with approximately equal qualifications to the design team. While there is no universal set of criteria as to what makes an engineer a peer, a good starting point is professional licensure and relevant design experience in the appropriate disciplines. The team should have an expert in the prevailing hazards such as high wind, seismic, or other location dependent hazards. A peer review is when a neutral third party checks the design for compliance with the performance specification. A performance specification states what the crane needs to do — rated load, hoist and travel speeds, operating wind speed, etc. — but it does not specify how the crane manufacturer needs to meet the specification.
Importantly, a design review is about compliance; it is not about the design reviewer’s preference for how he or she would have designed the crane. There is a level of professionalism expected for design reviews. While there will always be debate, comments that are not backed up by analysis, specification, or code requirements should be avoided.
Phillips said: “It’s a big red flag if a large number of comments are generated without supporting calculations or citations of specification requirements. It’s not constructive for the designer to have to refute a large volume of comments that may not be contractually required or may be speculation since they are not supported by calculations. The reviewer should be performing enough analysis to back up their comments.”
Container cranes are custom designed to meet the unique requirements of each port. Some of these requirements may include being in a hurricane or earthquake zone; exposure to extreme temperatures; or proximity to other geological hazards. Sometimes a container terminal is located near an airport, or a crane may need to pass under a bridge during delivery, resulting in height restrictions.
A naval architect provides the sea states and predicted voyage motions for the designers to analyze and brace the crane accordingly. The crane manufacturer owns the cranes until handover. Some crane manufacturers own their own fleet; others subcontract this work. It can be beneficial for the design reviewer to check the voyage bracing prior to shipping.
There are other operational considerations, such as where hatch covers are stored; the use of dual trollies; and how many containers the crane can lift: single 40 ft., twin 20 ft., tandem 40 ft., quad 20 ft., etc. All things considered the planning phase has great variance. Sometimes it starts at the wharf design stage, other times the wharf is already designed, and existing cranes are being replaced. Depending on the level of customization, once a crane is awarded, it can be up to three years before delivery.
Phillips, who himself conducts peer reviews of contractors’ crane designs, including some of the largest container cranes in the world, pointed to CP&A’s crane base anti-seismic isolation system (BASIS), which is built on nonlinear time history analysis (NLTHA) and can protect a crane’s main structure from damage even in contingency level earthquakes.
“We are always improving our software,” said Phillips. “Our crane analysis software can be thought of as a custom workbench specifically made for cranes. There is a much larger market for buildings and bridge design, so the commercial software packages tend to
focus on larger markets such as those [see below]. That led CP&A to create our own crane code checking software. One example is that we have incorporated wind tunnel test data into our pre-processor, which develops the wind load forces on a crane. Obviously, a commercial building will not have integrated wind tunnel data for container cranes.”
Interestingly, due to the geological and environmental hazards, cranes should be treated more like bridges and skyscrapers instead of mass produced cars and airplanes. However, for cars and airplanes, there are crash tests and full-scale testing, which is impractical with cranes. ASCE 7-16 1.3.1.3.4 covers minimum design loads and associated criteria for buildings and other structures; this particular clause covers peer reviews for significant structures.
Phillips added: “When you start thinking about how bridges, stadiums, and skyscrapers are designed it starts to become clear. For significant structures the [AISC 7] code requires a peer review. Are cranes significant structures? In our opinion they are; however, it is up to the local jurisdiction to make that decision.”
Even at the time of going to press, CP&A was wrapping up peer review and procurement assistant projects related to rubber-tired gantry, rail-mounted gantry, and ship-to-shore cranes. Are your procurement processes for these hulking container cranes up to standard? CP&A offers a wide variety of services, including specification, design, manufacturing review, modification, and accident investigation; and it is well positioned to remind terminal operators and fellow stakeholders of the risks involved with container crane procurement. Including transport and offloading in the peer review scope is a good way to manage some of these risks — but that’s just the start.
Richard Phillips, mechanical engineer at CP&A, said: “The procurement process for container cranes is somewhat unique and presents many challenges. Unfortunately, some procurement decision makers believe buying container cranes is the same as acquiring any other piece of equipment, such as a forklift or a company van.”
As should be unanimously accepted by crane manufacturers, a peer is someone with approximately equal qualifications to the design team. While there is no universal set of criteria as to what makes an engineer a peer, a good starting point is professional licensure and relevant design experience in the
appropriate disciplines. The team should have an expert in the prevailing hazards such as high wind, seismic, or other location dependent hazards. A peer review is when a neutral third party checks the design for compliance with the performance specification. A performance specification states what the crane needs to do — rated load, hoist and travel speeds, operating wind speed, etc. — but it does not specify how the crane manufacturer needs to meet the specification.
Importantly, a design review is about compliance; it is not about the design reviewer’s preference for how he or she would have designed the crane. There is a level of professionalism expected for design reviews. While there will always be debate, comments that are not backed up by analysis, specification, or code requirements should be avoided.
Phillips said: “It’s a big red flag if a large number of comments are generated without supporting calculations or citations of specification requirements. It’s not constructive for the designer to have to refute a large volume of comments that may not be contractually required or may be speculation since they are not supported by calculations. The reviewer should be performing enough analysis to back up their comments.”
Container cranes are custom designed to meet the unique requirements of each port. Some of these requirements may include being in a hurricane or earthquake zone; exposure to extreme temperatures; or proximity to other geological hazards. Sometimes a container terminal is located near an airport, or a crane may need to pass under a bridge during delivery, resulting in height restrictions.
A naval architect provides the sea states and predicted voyage motions for the designers to analyze and brace the crane accordingly. The crane manufacturer owns the cranes until handover. Some crane manufacturers own their own fleet; others subcontract this work. It can be beneficial for the design reviewer to check the voyage bracing prior to shipping.
There are other operational considerations, such as where hatch covers are stored; the use of dual trollies; and how many containers the crane can lift: single 40 ft., twin 20 ft., tandem 40 ft., quad 20 ft., etc. All things considered the planning phase has great variance. Sometimes it starts at the wharf design stage, other times the wharf is already designed, and existing cranes are being replaced. Depending on the level of customization, once a crane is awarded, it can be up to three years before delivery.
Phillips, who himself conducts peer reviews of contractors’ crane designs, including some of the largest container cranes in the world, pointed to CP&A’s crane base anti-seismic isolation system (BASIS), which is built on nonlinear time history analysis (NLTHA) and can protect a crane’s main structure from damage even in contingency level earthquakes.
“We are always improving our software,” said Phillips. “Our crane analysis software can be thought of as a custom workbench specifically made for cranes. There is a much larger market for buildings and bridge design, so the commercial software packages tend to focus on larger markets such as those [see below].
That led CP&A to create our own crane code checking software. One example is that we have incorporated wind tunnel test data into our pre-processor, which develops the wind load forces on a crane. Obviously, a commercial building will not have integrated wind tunnel data for container cranes.”
Cranes are significant structures
Interestingly, due to the geological and environmental hazards, cranes should be treated more like bridges and skyscrapers instead of mass produced cars and airplanes. However, for cars and airplanes, there are crash tests and full-scale testing, which is impractical with cranes. ASCE 7-16 1.3.1.3.4 covers minimum design loads and associated criteria for buildings and other structures; this particular clause covers peer reviews for significant structures. Click here to read the full article >