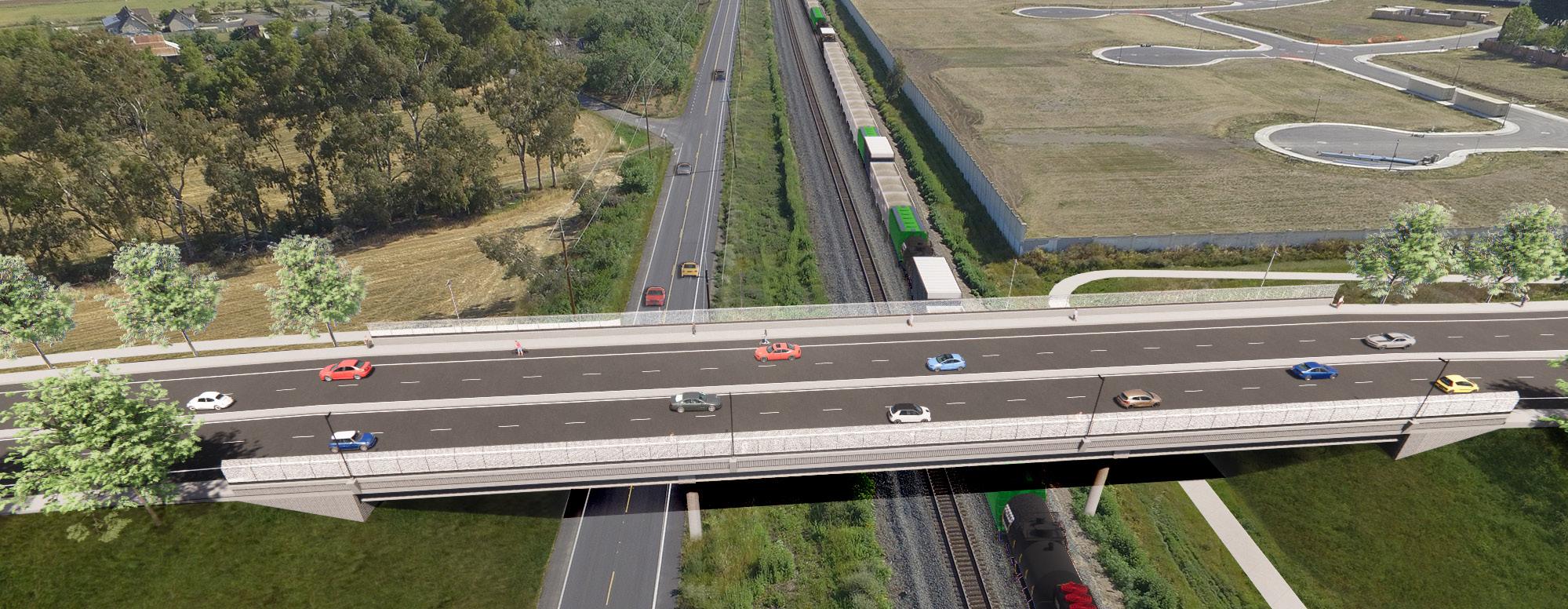
9 minute read
WINS
DESIGN VISUALIZATION, AERIAL VIEW FACING NORTHEAST.
WINS
Multiple Amendments, City of Dixon Parkway Boulevard Grade Separation Project
DIXON, CALIFORNIA, USA
In Northern California, the City of Dixon recently awarded TYLin the Final Design of the Parkway Boulevard Grade Separation Project. This project serves as our fourth amendment to our original contract for a transportation project the City has been constructing in incremental phases over the past 20 years based on available funding.
The new project includes constructing a unique 310-foot-long, three-span-continuous, California wide-flange girder bridge. The bridge will cross over Union Pacific Railroad (UPRR) tracks and Porter Road and extend Parkway Boulevard west to intersect with Pitt School Road and east to Valley Glen Drive. The bridge and roadway consist of four traffic lanes with shoulders, a median, pedestrian sidewalks, and a Class 1 bike path.
The current USD 2.2 million phase, now under construction, consists of placing 60,000 cubic yards of roadway and structure embankment material on the western side of the UPRR tracks along the alignment of the future Parkway Boulevard to Pitt School Road and relocating several utilities. The City purchased the needed property to construct the western embankment in 2019. TYLin has been involved with the City project since the original contract was awarded in 2004. Our four amendments consist of revising and updating the plans, specifications, and estimate (PS&E) to include the design of a precast girder bridge, environmental revalidation and National Environmental Policy Act (NEPA) approval, the addition of a railroad at-grade crossing closure, and grant-writing assistance.
The total fee for all four amendments is USD 2,553,510, with project construction costs estimated at USD 31 million. TYLin was awarded the subsequent amendments when the client decided to expand our scope due to our excellent performance on earlier tasks.
TYLIN TEAM
Hans Strandgaard, Project Manager Jodi Ketelsen and Robert Rodland, Environmental Work Huanzi Wang, Bridge Design Jeff Hoge, PE, Roadway Design
SDOT RapidRide J Line Project
SEATTLE, WASHINGTON, USA
TYLin’s Pacific Northwest office has been added to the RapidRide J Line Project in Seattle, Washington, securing our first contract with the Seattle Department of Transportation (SDOT). The RapidRide J Line Project is implementing bus rapid transit (BRT) along a 5.5-milelong corridor that serves the neighborhoods from Downtown Seattle to the University District. SDOT is the primary agency, in cooperation with King County Metro – which will inevitably own and operate the BRT facilities.
The purpose of the RapidRide J Line Project is to improve transit travel times, reliability, and capacity to increase high-frequency, all-day transit service and enhance transit connections. The project also improves pedestrian and bicycle connections and access to RapidRide stations, including protected bike lanes on Eastlake Ave E and a two-way cycle track on Fairview Ave N.
This project includes grant application and management, value engineering, risk assessment, surveying, utility mapping, right-of-way resolution, geotechnical data gathering and analysis, station siting, constructability review, schedule development, and private development coordination. The final design elements include a roadway, stations, stormwater facilities, utilities, traffic signal and electrical systems, and the trolley wire/overhead contact system (OCS). Scope of work also includes structural, architectural, urban design and landscaping, environmental permitting, bidding assistance, and engineering services during construction.
The project is currently at the stage of developing the 90% design following resolution of the 60% comments. TYLin’s Jason Boyett is the Design Manager for the final design of this project. Due to the size of the project, the corridor was split into three segments, each with its own discipline leads. Jason coordinates between the discipline leads, providing continuity to ensure standards are met, issues are resolved, and the schedule is followed in design and plans. The 90% design is scheduled to be submitted to the City of Seattle for review in January 2023. Construction is expected to start as soon as 2023.
This project is federally funded through the Federal Transit Administration (FTA) Small Starts program. Additional funding includes Move Seattle Levy, STP, CMAW, RMG, and other local sources.
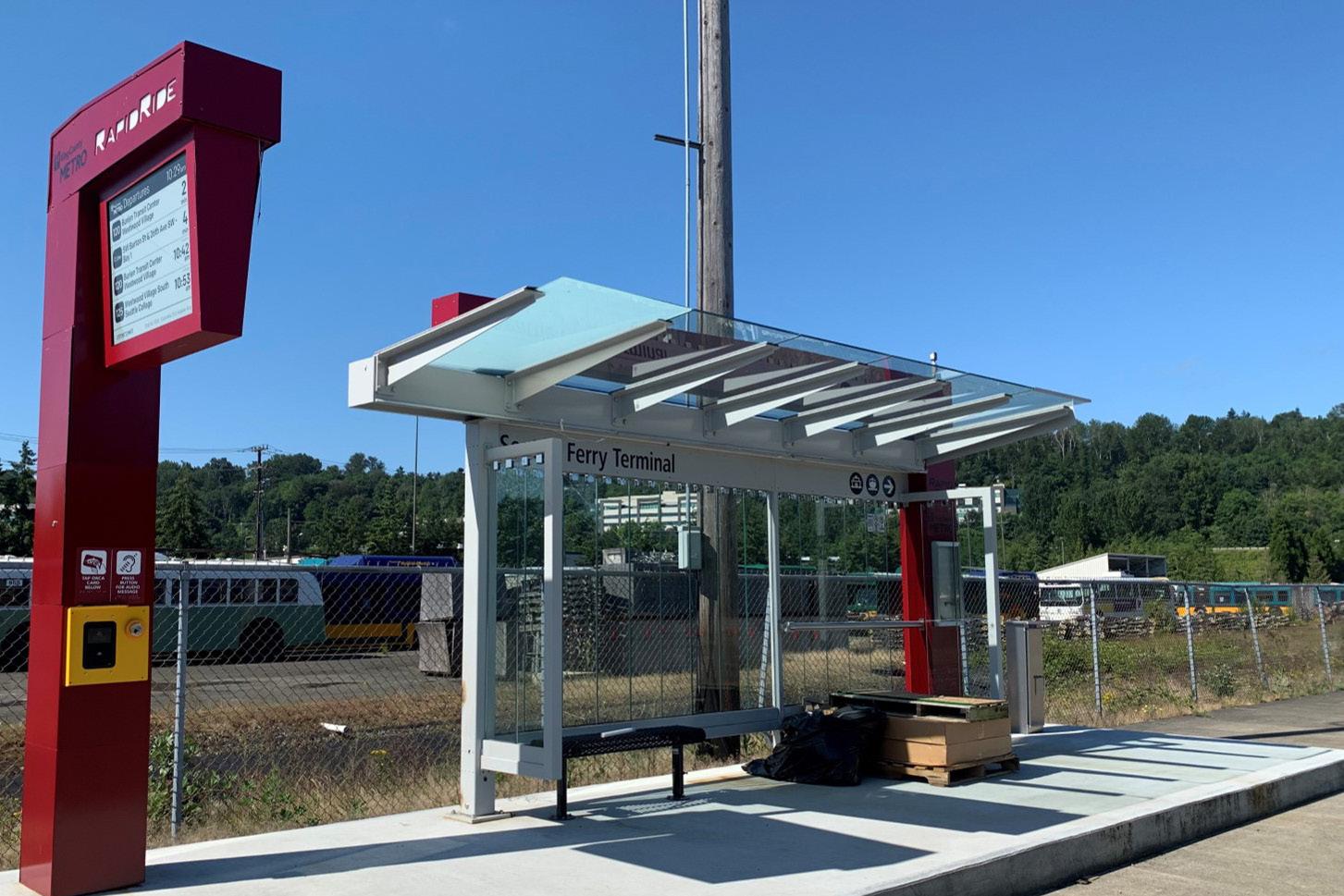
RapidRide 2.0 Station Prototype, similar to what will be used at the J Line Stations.
(Image credit: Stephanie Forman, Forman Consulting Services)
THE NEW DREAM LEBRETON TOWERS ARE BEING DESIGNED BY PERKINS&WILL (IN COLLABORATION WITH KPMB ARCHITECTS).
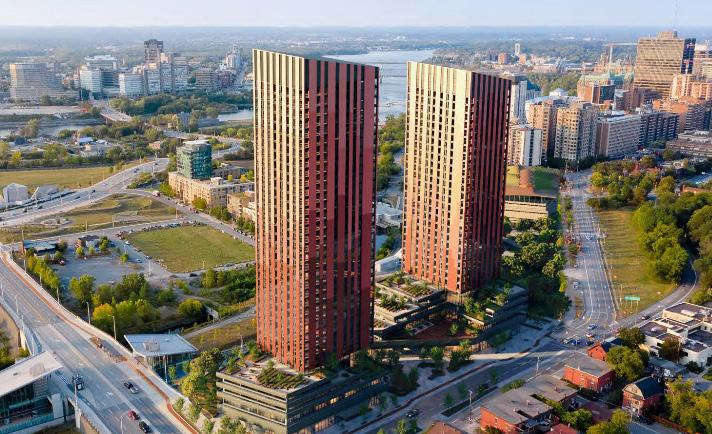
LeBreton Flats Library Parcel
OTTAWA, ONTARIO, CANADA
TYLin has teamed up with Toronto-based developer Dream to build two towers at LeBreton Flats in Ottawa, Ontario, Canada. Dream LeBreton will be an integrated community offering a mix of affordable, accessible housing units, social programs, and retail units. It is intended to be Canada’s largest residential zero-carbon development.
The design is being integrated with the adjacent Pimisi light-rail transit (LRT) Station as part of a revised National Capital Commission (NCC) master plan for the LeBreton Flats area. This project is the first to proceed within that development framework. The new towers will stand 31 stories and 36 storeys high and are being designed by our Dar Group affiliate Perkins&Will (in collaboration with KPMB Architects).
For this project, TYLin is providing Civil/Municipal Engineering and Transportation Planning services. The impacts of the proposed development on surrounding municipal infrastructure are being assessed, and the necessary reports and documentation are being developed to secure municipal planning approvals from a site servicing/grading and transportation impact perspective.
Scope of work includes the delivery of a stormwater management strategy designed to achieve the requirements of the LEED v4 program as part of a sustainability plan developed using the One Planet Living framework. The TYLin team has also been retained to deliver the design of an affected local road intersection and investigate modifications to the existing Booth Street bridge structure adjacent to the site.
The proposed towers will bring new opportunities, programs, and resources to the area to help the community flourish.
Closed Verification Facility for Vehicles at Full Speed
TAIWAN
In recent years, the automotive industry has been driven by the four major development trends: connectivity, autonomous vehicles, shared mobility, and electric vehicles. Through the combination of sensory systems and intelligent control systems, advanced safety assistance systems for vehicles are rapidly being developed. This has led to a substantial increase in the demand for international automotive electronic products and services.
To follow this trend, the Automotive Research & Testing Center (ARTC), Taiwan’s government-funded nonprofit research facility, plans to add a closed verification facility and tracks for evaluating a variety of vehicles at high speeds. The new facility will be used to provide suitable verification of existing technologies and assist in Taiwan’s development of new innovative technologies for smart and autonomous vehicles, automotive electronics, industrial clusters with the Internet of Things (IoT), and other driving-related industries and services.
The new verification facility will be added to ARTC’s existing vehicle test center and cover an area of close to 12 hectares. After construction is completed, the new facility will include 12 research laboratories, testing circuits, a computer-aided engineering (CAE) center, and a research and development department. This turnkey project includes the “weather environment test area” and the “elevated road test area.” Future expansion scenarios are already planned, such as a V2X/suburban, multi-functional test area, as well as connecting roads, external corridors, and other public facilities.
The construction company Sing Yuan was awarded this turnkey project, with TYLin providing the proposed detailed design.
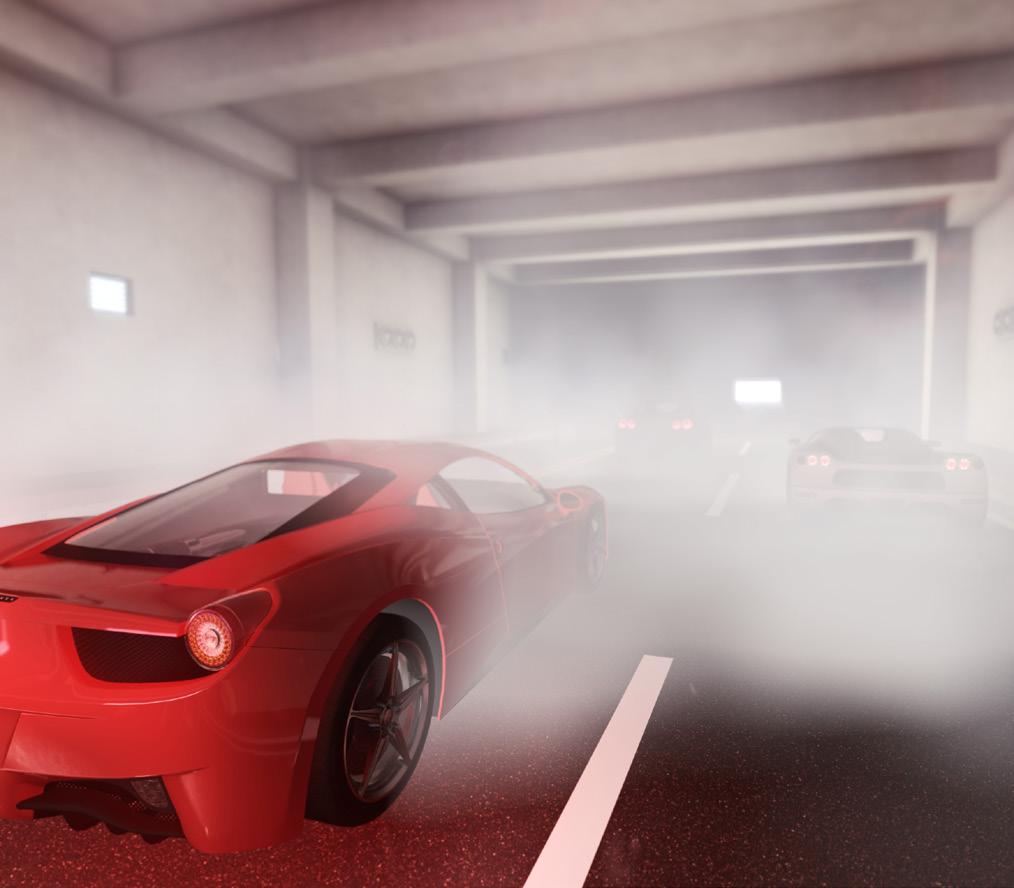
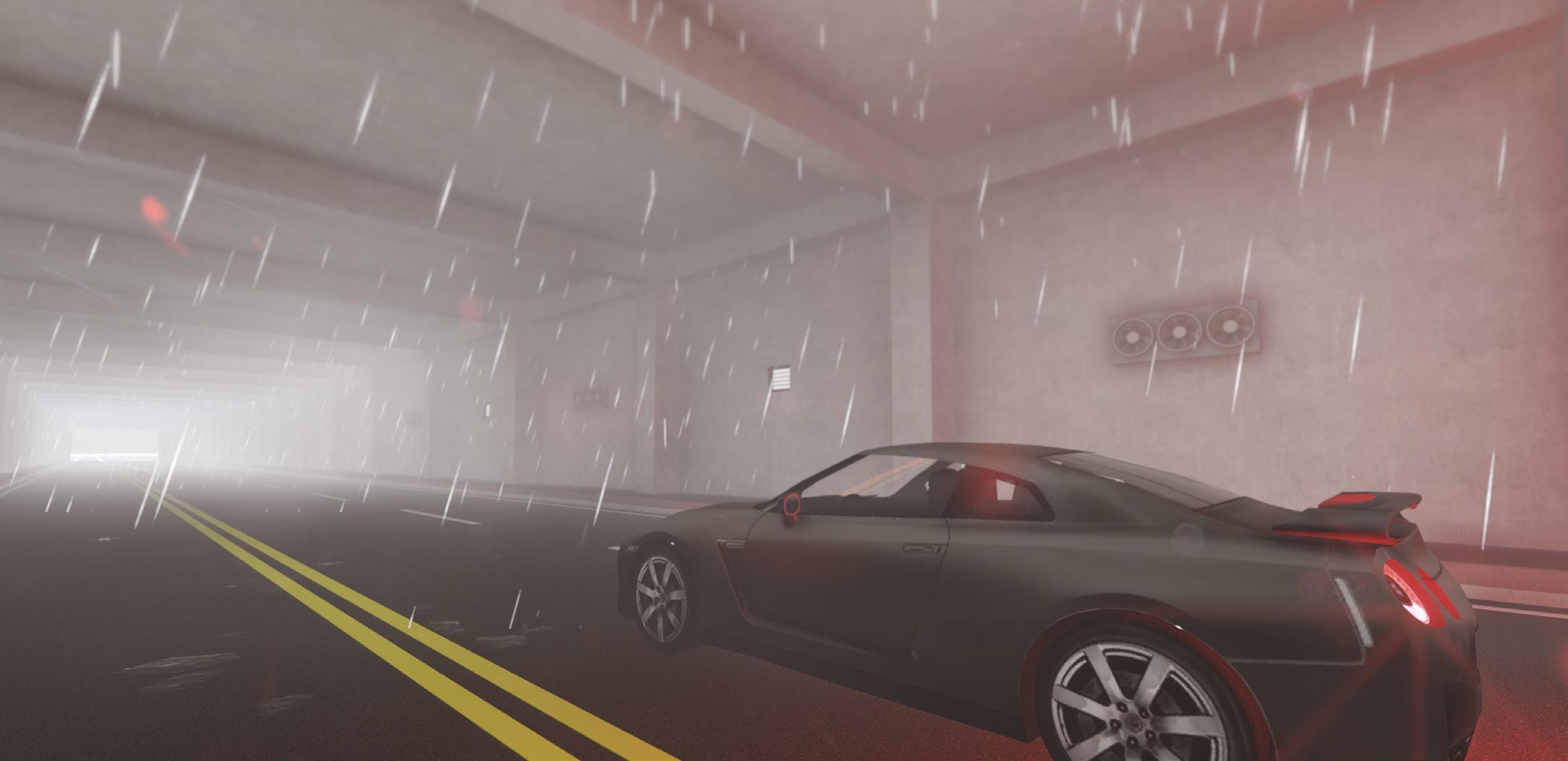
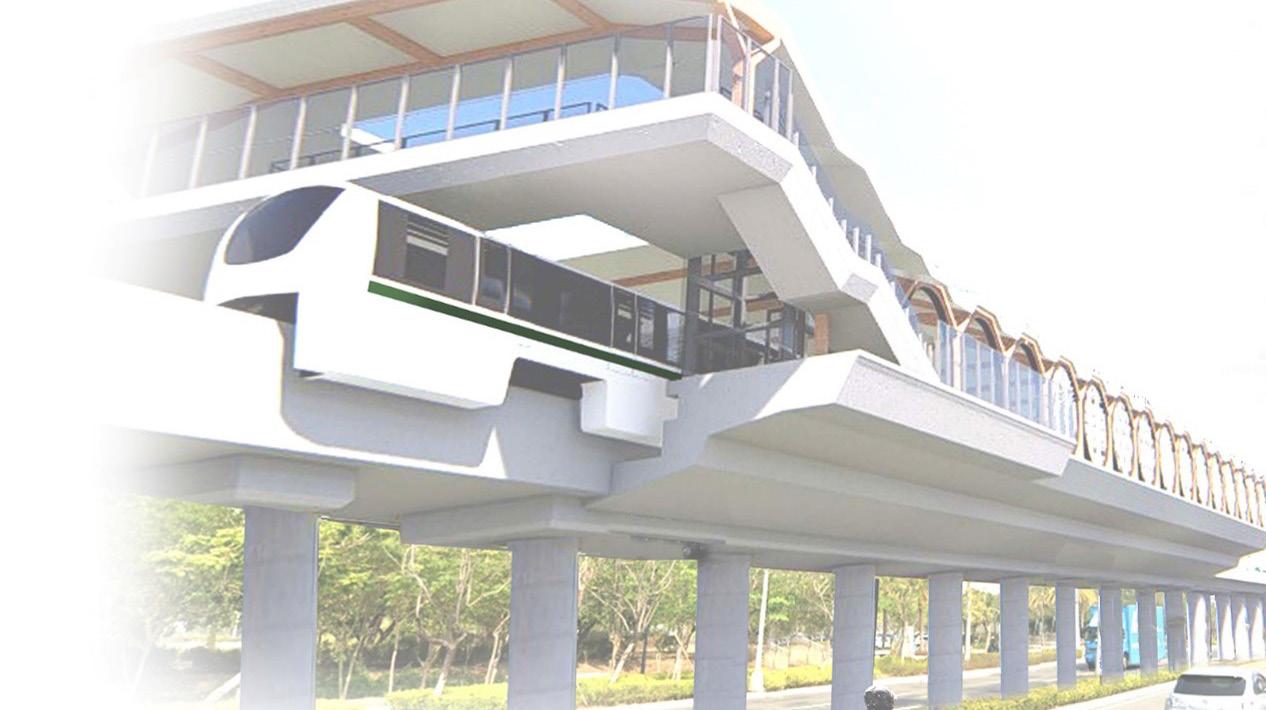
Deep Green Line for Monorail MRT
TAIWAN
There are six big cities in Taiwan, and Tainan is the only one with no mass rapid transit (MRT) system. To solve traffic problems caused by population growth and urban development, the Tainan City Government has implemented the “Tainan Advanced Transportation System Plan” since 2013.
Often called Taiwan’s birthplace, Tainan is the country’s oldest city. Due to the city’s narrow roads, a monorail system has been chosen as the best solution. The Deep Green Line is one of the priority networks, connecting two main industrial/technology-based towns: Southern Taiwan Science Park and Shalun Smart Green Energy Science City. The total length of the Deep Green Line will be 25 kilometers, with 22 stations and one depot.
Since Tainan is the first city in Taiwan to choose a monorail for its MRT system, this project is a great opportunity for TYLin’s Taiwan office to participate in the planning, design, and construction of a complete monorail system. We are currently providing the feasibility study, including transportation analysis and forecast, route and station planning, land development for station facilities, public transportation system integration, the operations plan, and financial analysis.
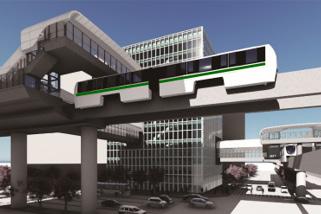
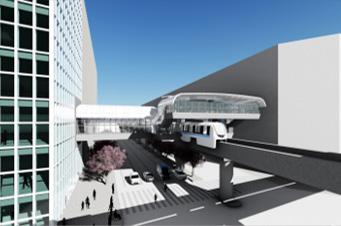
Renovation of 3-Bay Hangar
TAIWAN
Located three kilometers from the seashore on the island of Taiwan, a three-bay airplane hangar in use for over 24 years has developed corrosion in the building structure, deck roof and wall, and fire suppression pipes. The hangar measures 240 meters wide by 70 meters deep by 44 meters high. Since a repair could hinder normal operations and maintenance, the hangar owner requires a simple, effective renovation with minimal impact on airplane use while providing structural safety.
Renovation Strategy
The work mainly includes the following items, as needed: rust removal and painting of structural members; strengthening/repair of components; renovation of the metal panel roof and wall; repair of fire pipes and sprinkler system; and other miscellaneous repairs or upgrades.
Since structural safety, the time frame for the work, and project cost are important issues for the owner, TYLin assessed the individual failure risk of the above items and identified the priority, cost, and time needed to complete them. As a result, two schemes were recommended to the owner, one urgent and the other on a normal schedule. The urgent scheme requires less time and money and safeguards the structure for at least 10 years, while the normal scheme safeguards the structure for at least 20 years, with a budget increase of 38%. The owner selected the urgent scheme as it has less impact on aircraft maintenance.
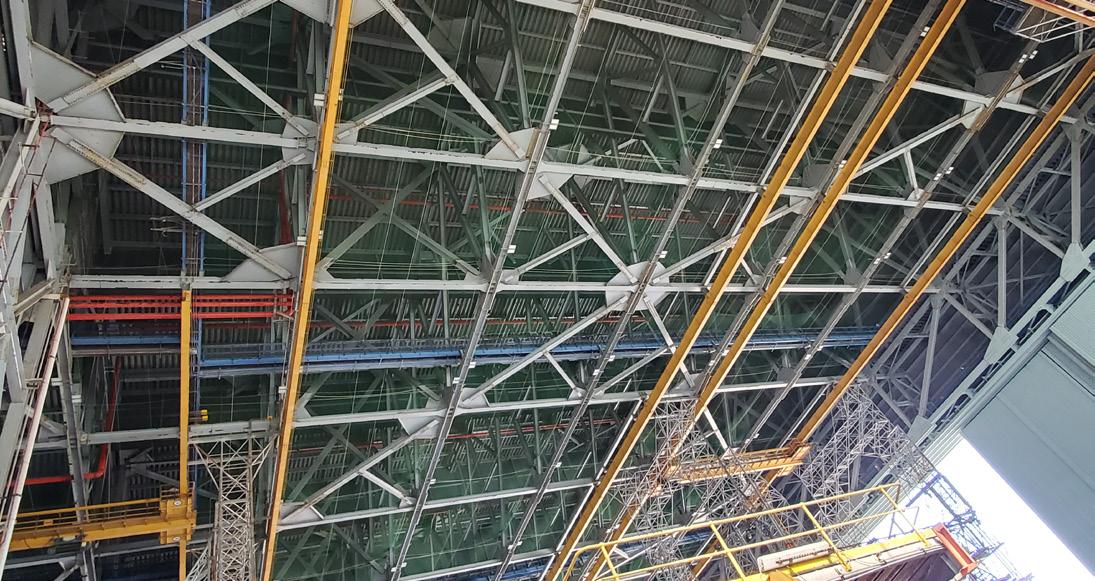
High ceiling makes maintenance of structural elements and fire suppression pipes difficult. The Tekla BIM model shows the hangar structural configuration.
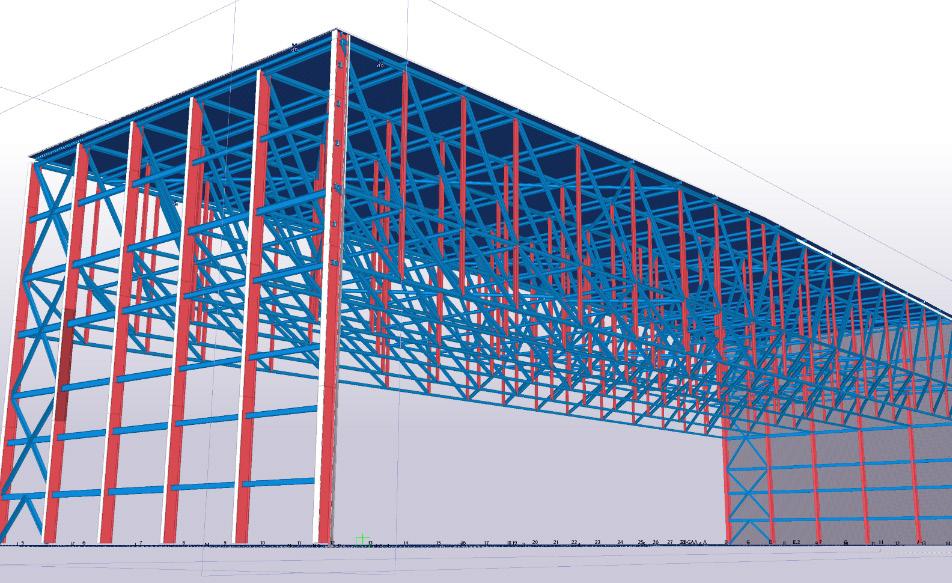
Corrosion and Local Construction
Most of Taiwan’s land constitutes a highly corrosive environment. That makes materials and construction specifications and adequate construction skills critically important. To ensure a successful renovation, TYLin established the following technical requirements:
— No component (metal bolt, plate, or other elements) shall be temporarily removed without providing safety measures prior to removal. To prevent the overall structure from additional deformation. — High-pressure waterjet systems will be used for rust removal. To mitigate pollution for the equipment and space. — Paint primer shall be water-resistant. To shorten the painting period and accelerate construction. — The cut edge of metal panels shall be heavily coated. To protect the weakest point against corrosion. — The anchoring component of the metal roof panel shall follow design specifications. To ensure material and welding strength and prevent corrosion and roof panel failure.
Using BIM
Tekla’s constructible building information modeling (BIM) software is being used for this project. The 3D BIM presentation provides a detailed image of the hangar structure to help identify and classify the individual components. The BIM model, which will be given to the owner after work is completed, eliminates the need for digital CAD file storage. The BIM model will also provide the owner with the base data for further development applications.