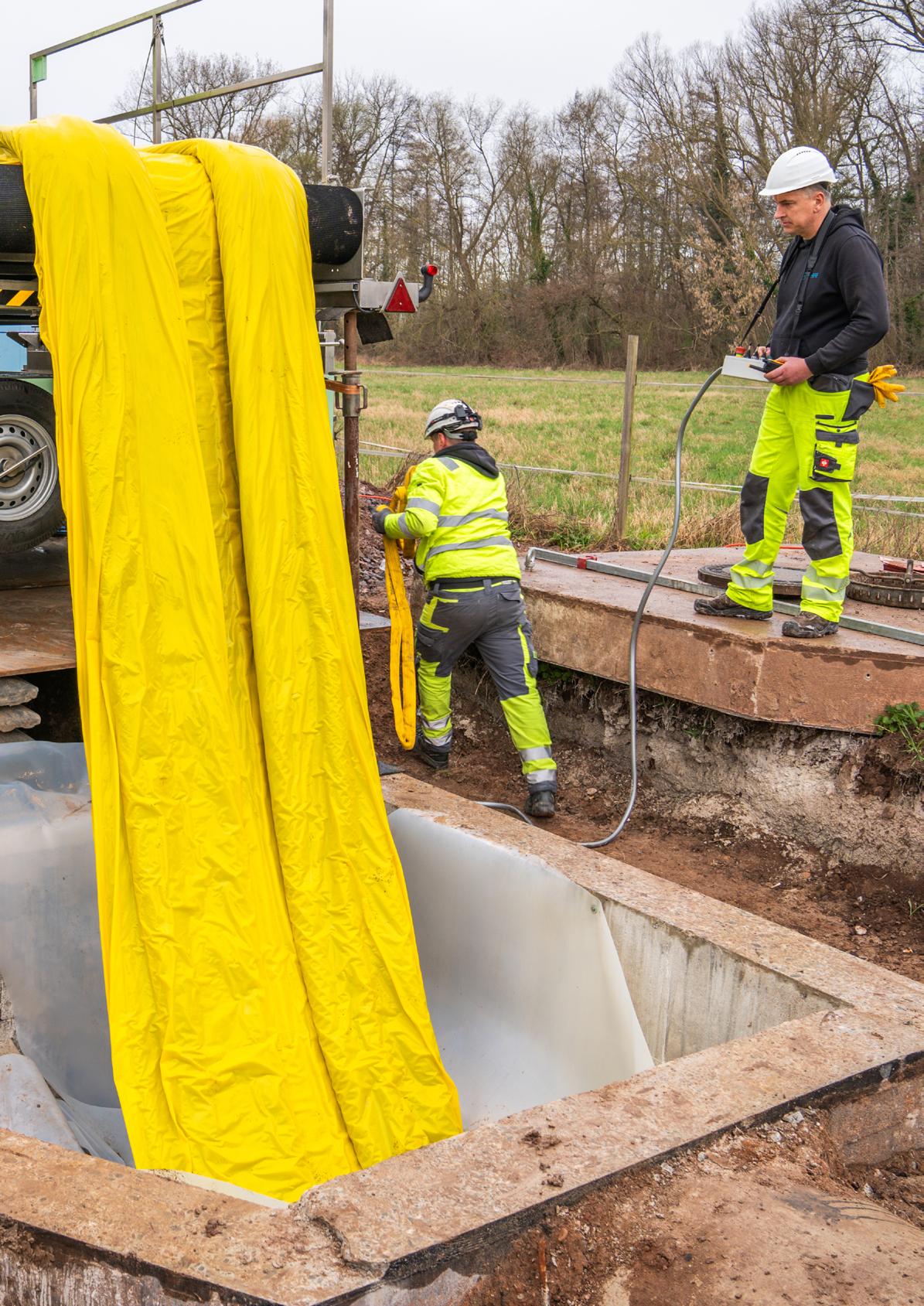
1 minute read
Enormous wall thickness requires rapid installation
In Offenbach an der Queich (GER), several DN 190 and DN 1200 sewers were rehabilitated in several construction phases in the middle of a residential area. The special feature of this project was the wall thickness of the IMPREG liner DN 1200, which was an exceptional 25.4 mm.
Feeding the IMPREG liner from the refrigerated truck via a conveyor belt
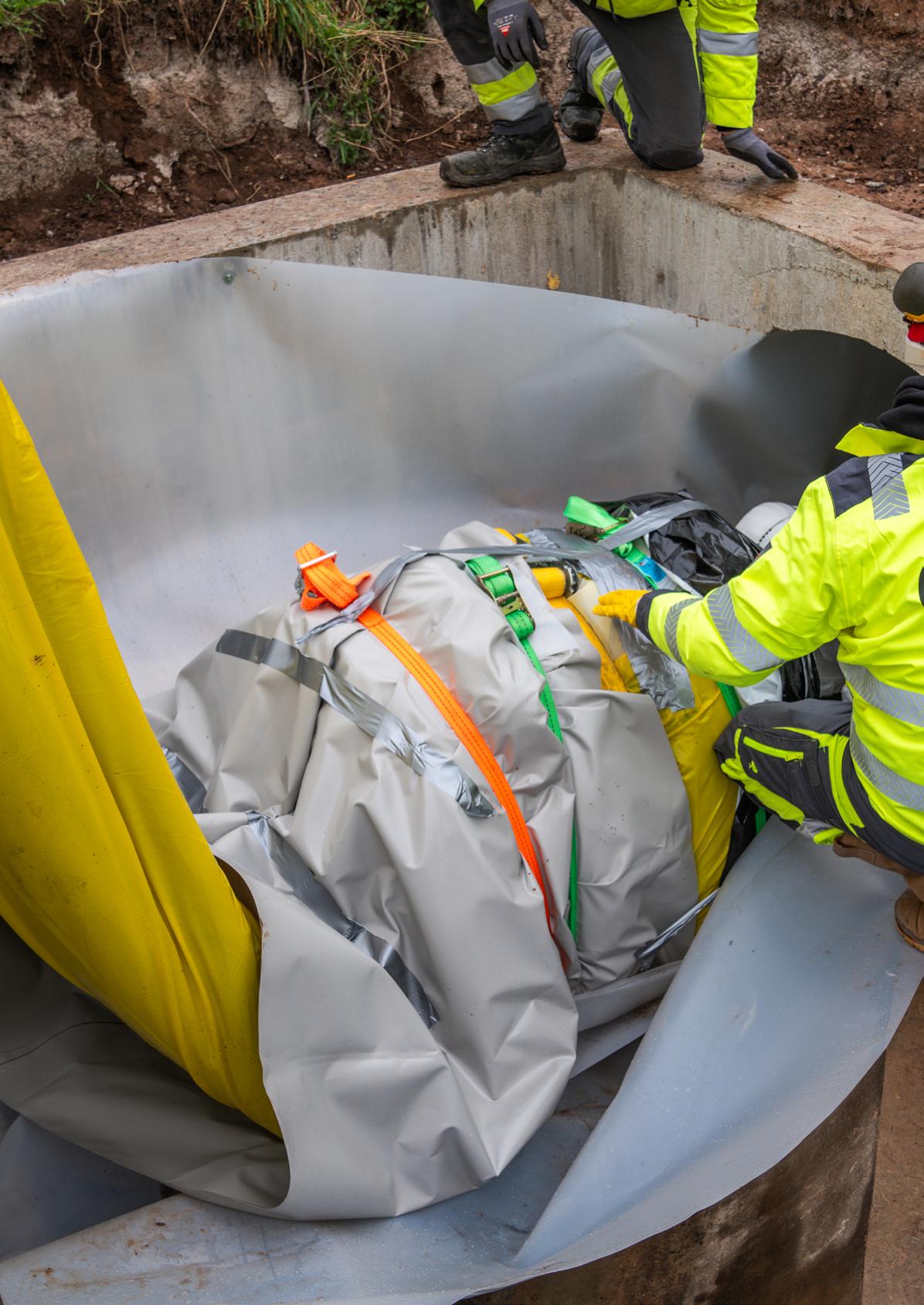
Placement holder insertion of the liner with insertion packer
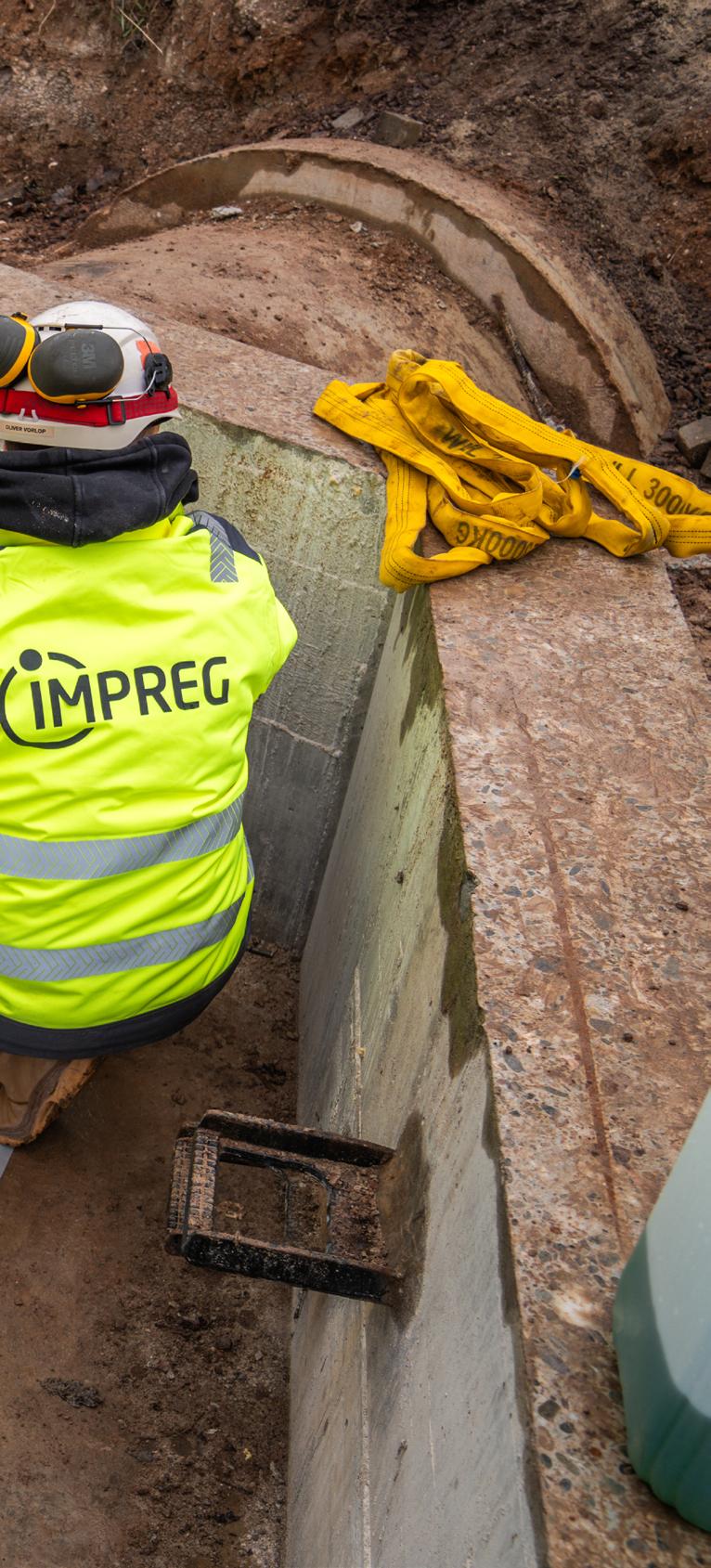
The stormwater sewer in old pipe condition IIIa lies under a footpath and access roads to private properties. This led the municipality of Offenbach an der Queich, represented by the technical staff of Department 5 Municipal Operations and the engineering firm Dilger GmbH, to opt for a trenchless rehabilitation method using UV pipe lining. This did not restrict the mobility of local residents.
Stability against high external pressure
The reason for the high wall thickness of the GRP pipe liner is a different one: “The compaction during the renovation of the adjacent road creates a very high external pressure that the liner has to withstand,” says Michael Carius from the engineering firm Dilger. >
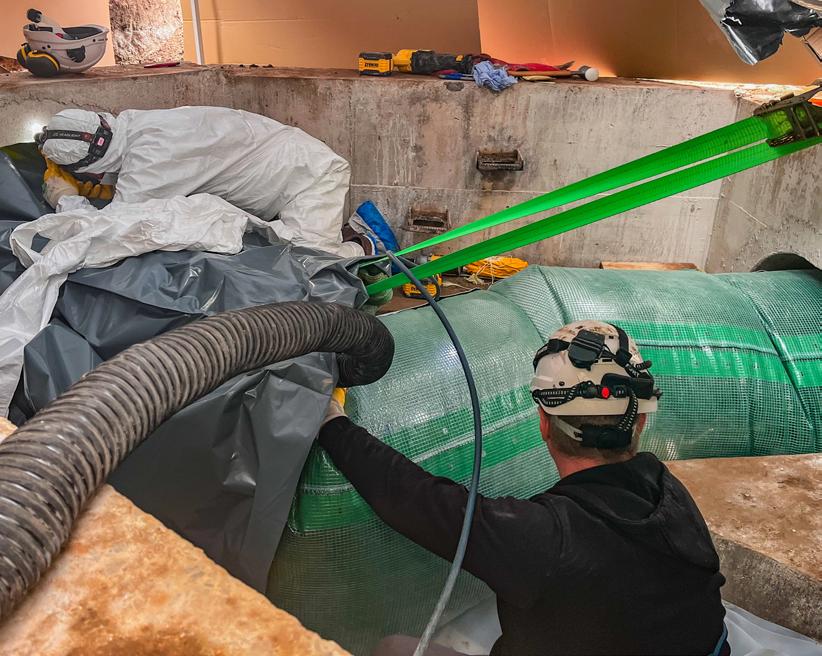
Working in the reusable airlock
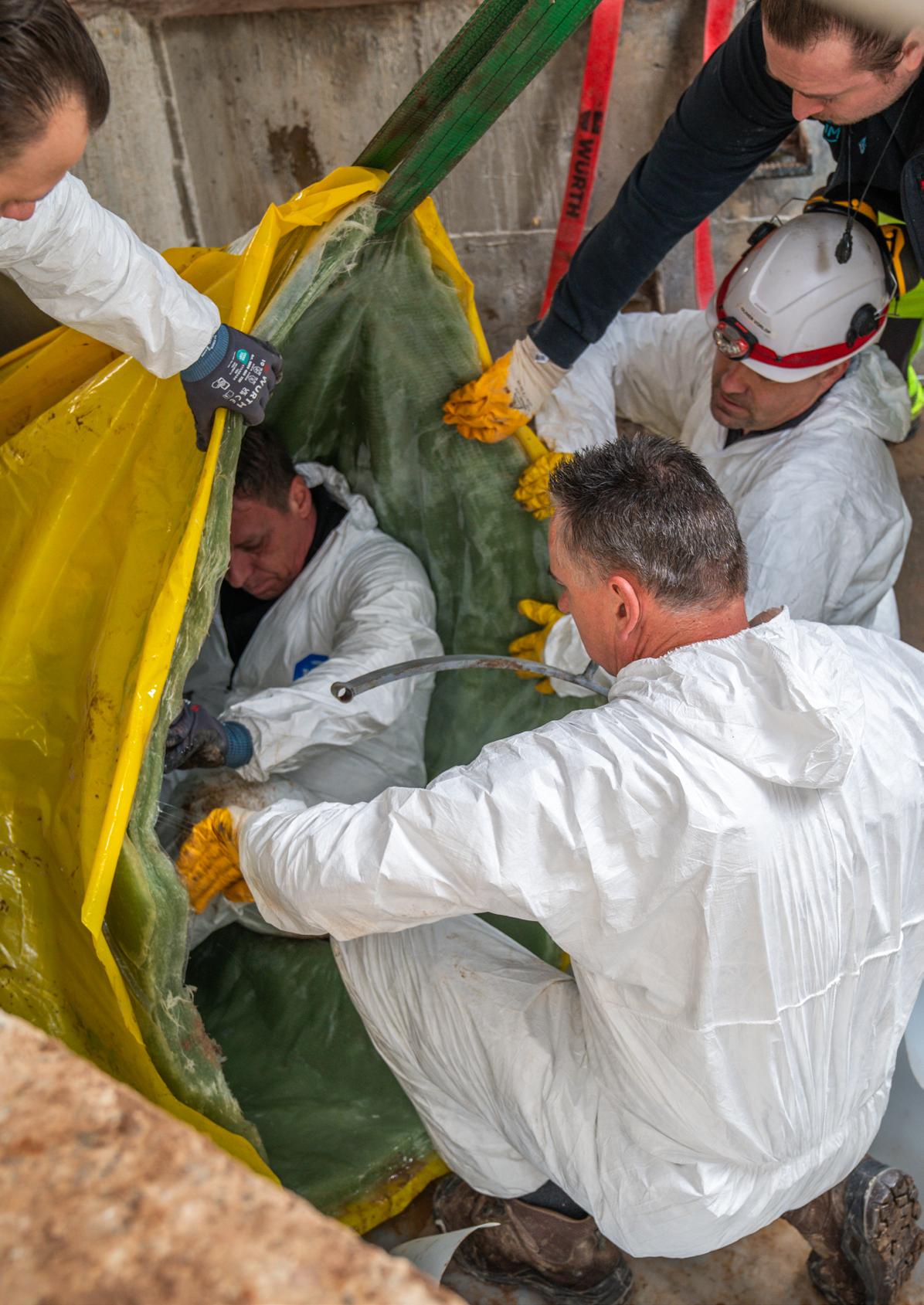
Creating optimum conditions for liner installation
A short storage time of only approximately 12 hours works in the refrigerated truck and additional prophylactic sun protection when installing the liner were necessary precautions. As this liner was produced with peroxides (thermal initiators) and already starts to react at a temperature of 24 °C, speed and perfect site preparation were essential.
“Even small rays of sunlight can start the curing process, which is why we had to hurry a little when pulling in the liner,” explains crew leader René Nickel from Kuchler GmbH
Kanalsanierung. With the help of a conveyor belt, the liner could be installed directly from the refrigerated truck using a construction road.
Fast and efficient
Despite the high wall thickness, the renovation only took one day per construction section. The IMPREG liner DN 1200, WD 25.4 mm, length 73.7 m, had a weight of 13.8 tons. With flexible intake packers and a Prokasro Power UV system with 3 x 12,000 W (36,000 W total output), the rehabilitation was carried out professionally and as planned.
Concentrated expertise and a well-coordinated team led by Oliver Vorlop, Sascha Faul (both IMPREG GmbH) and the UV teams from Kuchler were at work here under the direction of site manager Christopher Gropp and managing director Andreas Geiß. The construction site was successfully completed thanks to the great commitment of everyone involved, many years of experience, and good teamwork.
Contact: Jack Talbott, Technical Sales Phone +44 7740 197 127 e-Mail jtalbott@impreg.com
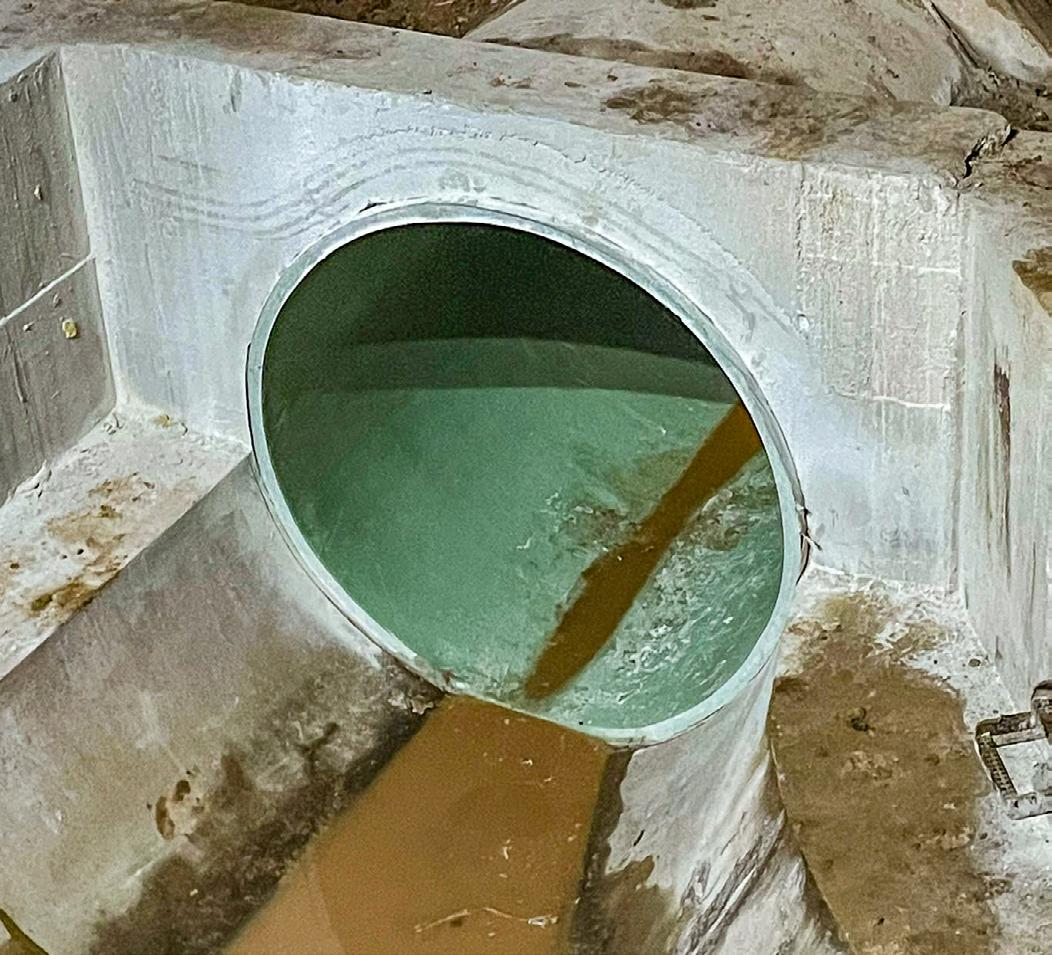
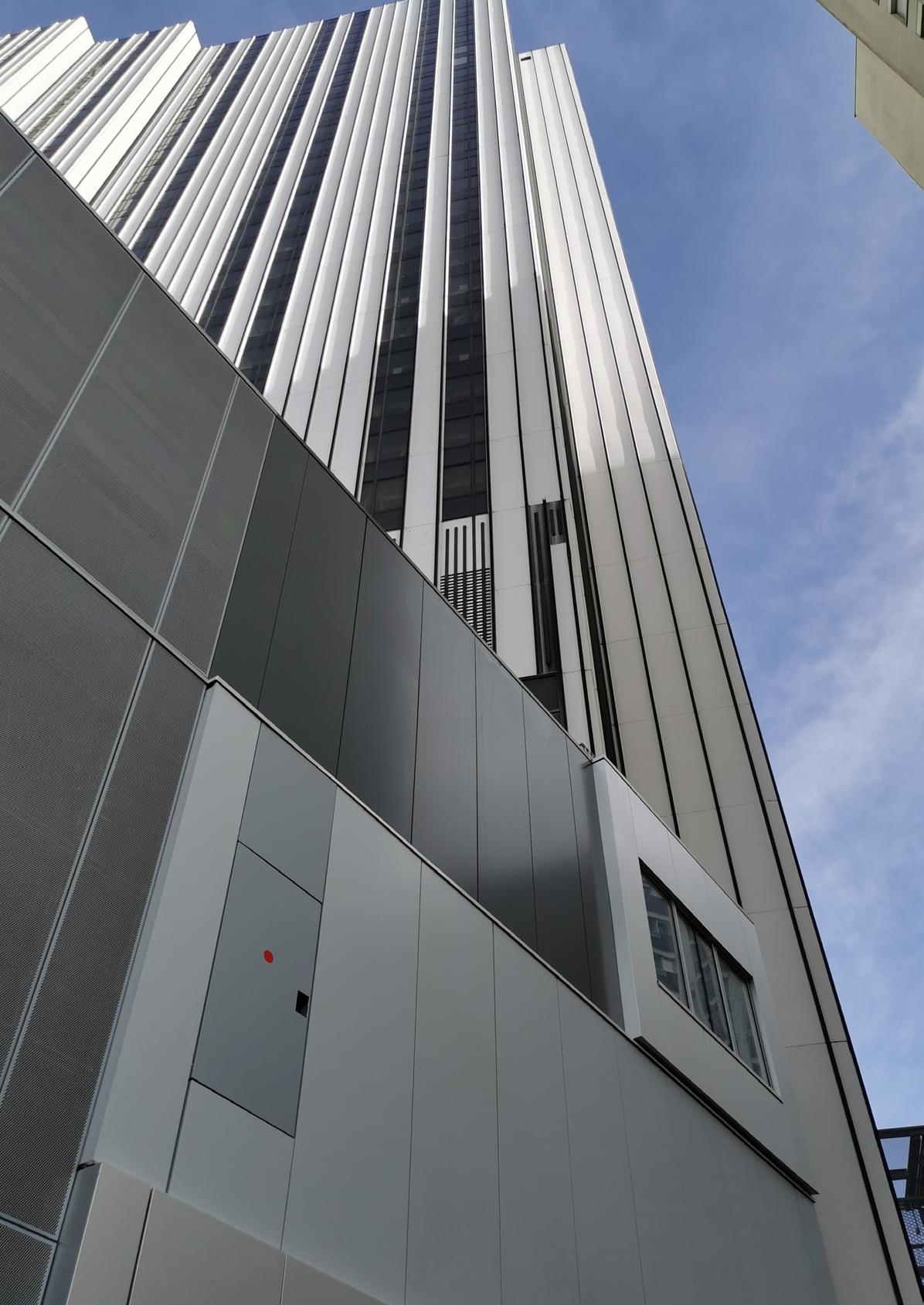