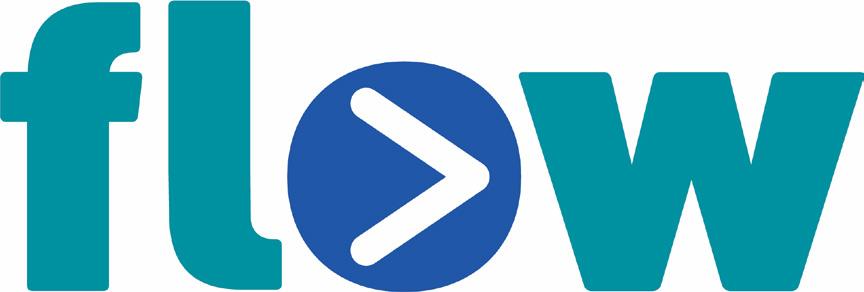
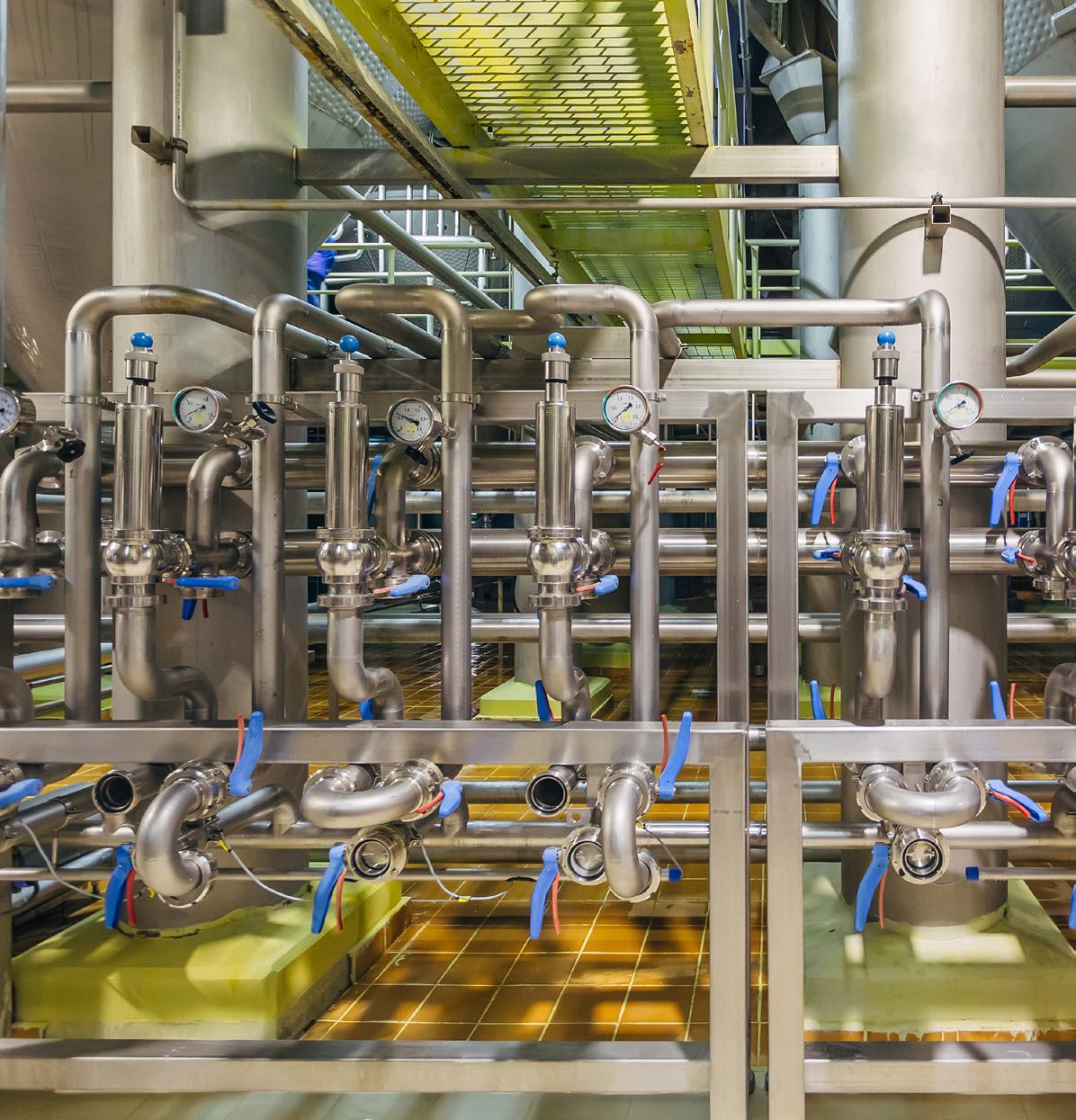
SECTOR FOCUS: Food & Beverage
Piping
design for food and beverage applications
Cleaning up energy production

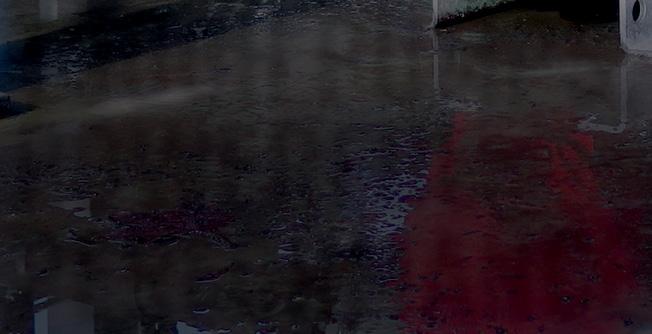
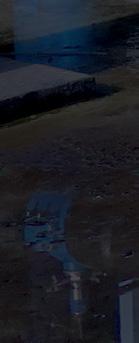
Piping
Cleaning up energy production
In everything we do, we never lose sight of what it‘s all about for you: economical work and easy handling.
Whether chemical substances, oils or media for the food industry, it is important to fill or empty quickly and precisely. Due to the reversible conveying direction, both processes can be carried out with just one pump.
As a result of their compact yet powerful construction, Vogelsang rotary lobe pumps are among the most frequently ordered pumps in many UK industries. They transport highly viscous or aggressive media of all kinds and even pump liquids with rough solids without blocking.
For more information:
sales.uk@vogelsang.info | 01270 216 600 vogelsang.co.uk
Editor
Chris Callander chris@flowmag.co.uk 01732 671123
Contributing Editor
Suzanne Gill suzanne@flowmag.co.uk
Publisher
Andrew Castle andrew@flowmag.co.uk 07785 290034
Accounts
Touchwave Media Ltd accounts@flowmag.co.uk
Production
G and C Media Ltd production@flowmag.co.uk
For over three-quarters of a century the British Pump Manufacturers’ Association (BPMA) has been serving the interests of UK and Irish suppliers of liquid pumps and pumping equipment.
West Bromwich B70 6PY www.bpma.org.uk
flow is a controlled circulation journal published quarterly on behalf of the BPMA by Touchwave Media Ltd and G and C Media Ltd. For a copy of the magazine’s terms of control and to request a copy please email circulation@flowmag.co.uk
The content of flow magazine does not necessarily reflect the views of the editor, publishers or the BPMA. The publishers accept no legal responsibility for loss arising from information in this publication and do not endorse any products or processes mentioned within it. No part of this publication may be reproduced or stored in a retrieval system without the publisher’s written consent.
© BPMA. All rights reserved.
Iwas saddened to hear of the passing of Maurice Yates, a figure well known in the pump sector for inventing the Yatesmeter system for thermodynamic measurement of pump efficiency. Maurice was a true innovator and will be sorely missed.
Innovation is a constant in the pump sector, despite suggestions otherwise from some quarters. Yes, the basic physics behind pump operation can’t change, but every other aspect of a pump system can, and innovation in how systems are designed, installed, controlled, monitored and maintained is happening every day.
This innovation is particularly evidenced by the amazing finalists in the Pump Industry Awards, which take place just days after this issue is published. You can find details of the finalists on page 10 of this issue, and we will be reporting on the winners in our next issue.
A key factor driving innovation in our sector is collaboration, something the BPMA works hard to support and encourage within the UK. Beyond our shores, this is a focus for Europump, the European pump association representing 15 national associations including ours. The BPMA is honoured to be hosting the Europump annual meeting as it returns to the UK in May this year, and you can read some of what is on the agenda on page 8 of this issue. This popular event brings together delegates from across Europe to network, learn and share as the pump sector looks to work together to navigate the complexities and explore the opportunities in pump manufacturing and distribution.
I feel sure that, with a drive for continued collaboration, within and across organisations, and the vision, passion and enthusiasm of innovators like Maurice, there is plenty more innovation to come from the pump sector.
Dale Croker, President, BPMA
THE CHEMUK 2024 EXPO WILL return on 15 and 16 May at the NEC in Birmingham. Running as part of the trade show, event organiser UK Industry Events has announced the launch of the new Process & Chemical Engineering Show Zone.
The Process & Chemical Engineering Show Zone will be the UK’s only event that brings process engineers from the chemical, food & beverage, pharma, oil & gas, and water & wastewater industries together to experience the very latest innovation that is shaping and inspiring the process industries under one giant roof.
The new focused event zone will present hundreds of specialist process engineering suppliers to attending process professionals involved directly in the design, development, management, and maintenance of operations in the processing of liquid, solid, powder, and gas-based process engineering industries.
Managing Director of UK Industry Events, Ian Stone, explained the decision to introduce the focused show zone. “The Process & Chemical Engineering Show
Zone will give attendees the ability to survey the wealth of new technology and products that are available but also to be able to share that knowledge across the various vertical industries that are the application areas for process engineering.
“Process engineering is, of course, in essence chemical engineering in as much as it is the application of chemical unit operations and unit processes. So, there is an ‘esprit de corps’ among all major process engineers, often coming
through a classically chemical engineering educational base.”
The organisers have also confirmed that the BPMA team and seven BPMA members will be exhibiting as part of the show. Visitors will be able to meet with ABB, Crest Pumps, Flux Pumps Int (UK), Grundfos, EagleBurgmann, March May, and Vogelsgang at the show this May.
Details of the expo and free badge registration can be found at the event’s website www.chemicalukexpo.com.
PUMP AND MACHINERY MANUFACTURER VOGELSANG
Ltd is celebrating 20 years of trading in the UK.
The business was established in the UK in 2003 after several industries showed significant interest in its elastomer-coated rotary lobe pumps, the pump Vogelsang invented in 1970 and is best-known for manufacturing globally.
Since then, it has grown to an 18-strong team located across the UK, from Scotland to the South Coast and is headquartered in Crewe, Cheshire. It remains wholly owned by its parent company, German-based and family-run Vogelsang GmbH, which has a global annual turnover of over €170 million.
Vogelsang is a leading provider of pumps, macerators and other machinery for companies across the UK, including rotary lobe and progressive cavity pumps, and XRipper macerators.
Commenting on the anniversary, Jonathan Gutteridge, Managing Director, said: “We are pleased to have reached this milestone in Vogelsang’s story. When it was founded two decades ago, we had a tiny customer base and were almost unheard of as a pump brand. Now we have a turnover of over £10 million and have developed a reputation for making highquality machinery.”
The company has ambitious plans to grow further in the coming years and is on track to increase its turnover as it
branches out into more industrial sectors with its new pump and machinery designs. It has launched several new products over the past 12 months, including the EP and VP rotary lobe pumps, which are designed for heavy-duty chemical industries and can withstand media temperatures of up to 200°C and operating pressures of up to 10 bars.
The company also launched the HiCone progressive cavity pump, with a patented conical rotor and stator design, which means the rotor position can be adjusted as the stator wears, significantly reducing the spare parts usage and maintenance costs.
IT IS WITH GREAT SADNESS THAT THE
BPMA shares the news that Maurice Yates, who was heavily involved in the Association through its technical committee, various working groups and supporting its Certified Pump Systems Auditor (CSPA) training, passed away on February 2, 2024, at the age of 83.
Maurice made significant contributions to the global pumping industry with his groundbreaking development of the Yatesmeter. This innovative technology revolutionised pump system investigations, leading to advancements in pump remedial work and benefiting numerous manufacturers.
Maurice embarked on his career as an electrical engineer with CEGB (the Central Electricity Generating Board), where he played a vital role in the design teams for constructing 32 power stations during the 1960s. The genesis of his groundbreaking development occurred during an assessment of a 600ft line shaft pump while working at South Staffs Water. Recognising the limitations of existing
calibrated information, Maurice began conceptualising and refining measurement technology in the early 1970s, initially with South Staffs Water and later with South West Water, where he served as Group Electrical Engineer.
In the early 1980s, Maurice secured a government grant to commercialise his product and expand his consultancy
MICHAEL SMITH ENGINEERS HAS ANNOUNCED A new UK distribution agreement with SAWA Pumpentechnik AG. SAWA is a long-established manufacturer of highquality stainless steel hygienic centrifugal, side channel and peripheral pumps. The arrangement enhances Michael Smith Engineers’ portfolio to now include hygienic products. This partnership combines SAWA’s expertise in clean pump technology with Michael Smith Engineers’ established presence and standing in the United Kingdom. Commenting on the announcement, Sales Director Jason Downing said: “This partnership allows us to offer additional options to our large customer base in the pharmaceutical, food & drink, and chemical industries. We look forward to introducing the SAWA range to new and existing clients who demand quality and reliability in hygienic processes.”
business, establishing Advanced Energy Monitoring Systems in 1984. Soon after, he successfully introduced the Yatesmeter to pump users and manufacturers, marking a pivotal moment in the industry’s evolution. Maurice Yates’ legacy continues to shape the landscape of the pumping industry, leaving an indelible mark on its history.
2 WEEKS
SAWA Pumpentechnik AG was established in Switzerland in 1911 and, like Michael Smith Engineers, remains a familyowned company.
Rewinds Limited in a move that further increases the company’s water management pump servicing capability.
The acquisition will enable Wilo UK to extend its service capability in key water management operations, including installation, repair, condition monitoring, and general pump maintenance.
Arfon has two workshops, one for dirty water pumps based in Bromborough and one for clean water pumps based in Caernarfon, with a team of circa 20 full-time engineers. The company is a major service and maintenance provider to industry in the North West of England and also numerous water utility companies, including Welsh Water and United
Utilities. Arfon will continue to trade as a separate legal entity to support its existing customers and contracts, with Wilo UK having now purchased 100% of Arfon’s shares and assets.
Lee Tebbatt, Managing Director of Wilo UK, said the acquisition further strengthens Wilo UK’s servicing capability and aligns with an increased focus from customers on aftersales support and total cost of ownership.
“We already have a strong trading relationship with Arfon, who is a long-standing Wilo Service Partner”, explained Lee. “The opportunity to bring Arfon fully into the Wilo family was a good fit with our strategy of providing a full range of service capabilities across the installed pump base in the water utilities and industry sectors.
Pump Company has made the West Midlands Net Zero Pledge to cut its environmental impact and help clients reduce their carbon footprint.
Hall Green-based Selwood Pump Company Limited, which supplies a wide range of pumps for industry sectors, including oil processing and car manufacturing, has pledged to reduce not just its own energy consumption but also the amount needed by clients who use its equipment.
Administered by Sustainability West
Midlands on behalf of the West Midlands Combined Authority, the West Midlands Net Zero Business Pledge is undertaken by businesses wanting to be part of the region’s drive to become a net zero carbon economy by 2041.
Managing Director Graham Gallen, who has worked for the company for nearly 40 years, said Selwood was pleased to sign up for the Pledge to shape a more environmentally-friendly future.
“We hope to reduce the carbon footprint and energy usage of our operations and also to advocate the Net Zero Pledge
standards among our client base,” explained Graham. “As a manufacturer of equipment for manufacturing and processing companies, we hope to assist customers in reducing their energy usage by supplying energy-efficient options for our equipment.
“While Selwood may not be a household name, our products are used by leading brands at power stations, car factories, oil processing facilities and across all sectors of manufacturing, so it is important that we play our part in reducing environmental impact.”
Canadian company Real Tech, a supplier of innovative optical sensor technology that enables real-time water monitoring and testing. Through the acquisition, ABB will expand its presence in the water segment and complement its product portfolio with optical technology critical for smart water management. Financial terms of the transaction were not disclosed.
Unlike traditional water quality measurement, which can be timeconsuming, Real Tech’s product portfolio provides critical measurements in real time. This enables better process control
and continuous water quality assurance. Real Tech’s patented solutions cover the entire digital water value chain for water quality monitoring, focusing on data creation and analytics.
Real Tech’s portfolio includes optical
sensors, controllers and a suite of optional accessories that allow each system to be configured according to customer needs. Leveraging the power of light, the sensors measure water composition. They use spectrophotometry and fluorescence measuring techniques to move testing from the lab to the process environment for real-time use. Liquid AI, a proprietary AI software platform, completes the service offering, providing an easy and accurate way to analyse data from Real Tech sensors. The company has approximately 40 employees and is based in Whitby, Ontario.
IN WHAT IS BELIEVED TO BE A global first, the Japanese machine tool manufacturer, DMG Mori, has supplied AESSEAL with energy-friendly machine tools designed to work directly at European standard voltages, avoiding a wasteful transformation step.
DMG Mori has delivered £3.97 million worth of cutting-edge machine tools to AESSEAL plc’s Rotherham-based ‘Factory for the Future’. The machines work directly at 400V 3-phase, used by industry throughout Europe and the UK. All previous machines of this calibre were produced to the Japanese 200V 3-phase electrical standard and required step up transformation to UK voltage, with a loss of approximately 5% of the energy used in the transformation.
Dr Masahiko Mori, the President of DMG Mori, stated: “Many of our machine tools are used globally, and it makes
sense to modify our production lines for new machine tool models for global customers. The four machines supplied to AESSEAL in October were the first we produced to the new 400V 3-phase standard.”
Chris Rea, Managing Director of AESSEAL, added: “Our ‘Factory for the Future’ is an investment in our company, and with the assistance of DMG Mori, the equipment used will now be more environmentally friendly. The total investment in robotic production, the four new machine tools just installed and those due for delivery early in 2024, is £15.5million, making a great start to filling a factory that is both a showcase for responsible industry and a fantastic working environment.”
The £3.97 million machine tool order is in addition to the recently reported £9.75 million order for state-of-the-art robots which are designed to free up the Rotherham company’s workforce for higher value tasks and maintain the company’s competitiveness in global markets.
£100k ($130,000)
Hosted by the British Pump Manufacturers Association (BPMA) and sponsored by WEG, Europump (the European Pump Association) is staging its 2024 Annual Meeting in Windsor on 22-24 May this year.
Reflecting the current Europe-wide legislative agenda, as well as numerous other topic areas of significant importance to the international pump sector, the BPMA, on behalf of Europump, has been working hard to deliver a comprehensive programme of meetings and presentations that will offer both intellectual and practical value to pump manufacturers.
In addition to sessions dedicated to the activities of the various Europump Commissions, several invited speakers will also share their thoughts and expertise on a range of topical issues, including digitisation and AI, sustainability, the post-Brexit political landscape and the economic standing of the worldwide pump market.
The first invited speaker to be announced is Stephen Phipson CBE, Chief Executive at Make UK. Taking to the stage on the morning of Friday, 24 May, Stephen will provide an overview of the political arena in the UK and its impact on the manufacturing sector both at home and abroad. In a somewhat timely fashion, the implications of the impending general election in the UK will also be considered.
The second speaker to be announced is Kiran Ahmed, Lead Economist, Global Industry Services at Oxford Economics. Kiran will present the key findings from the 2024 World Pump report, including the macroeconomic and industrial backdrop and how it impacts the international pump market. This presentation will take place during the afternoon of 23 May as part of the Marketing Commission session.
Commenting on the engagement of these headline speakers, BPMA CEO Wayne Rose said: “We are delighted to be hosting the 2024 Annual Meeting on behalf of Europump and look forward to welcoming our international pump colleagues to this world-famous location. We have a superb business programme supported by renowned expert speakers. I have no doubt our audience will be captivated by the political and economic overviews presented by Make UK and Oxford Economics, and I look forward to announcing further keynote speakers in due course, who will be addressing some of the other key topics currently affecting the pump industry.”
Sponsored by WEG, the 2024 Annual Meeting will be a must-attend event for those senior pump executives looking to successfully navigate the complexities of pump manufacturing and distribution over the coming months and years.
Full details on the event, including further
information on the venue, location, and travel arrangements, can be found on the dedicated website. The online booking system is live, allowing delegates to secure their places. A promotional video, fully illustrating all aspects of the event, is also available on the event’s website.
THE BRITISH PUMP MANUFACTURERS ASSOCIATION (BPMA) has taken note of the recent announcement by Minister Hollinrake regarding the extension of CE marking recognition in the UK market. Following the Department of Business and Trade’s August 2023 declaration of continued recognition for certain product regulations, this development prompts reflection and analysis from the BPMA on its implications for the pump sector.
Minister Hollinrake’s announcement confirms the extension of CE recognition for three key regulations:
• Ecodesign for Energy-Related Products 2010 Regulations (Department for Energy Security and Net Zero)
• The Explosives Regulations 2014 (Department for Work and Pensions - Health and Safety Executive)
• The Restriction of the Use of Certain Hazardous Substances in Electrical and Electronic Equipment Regulations (RoHS) 2012 (Department for Environment, Food & Rural Affairs)
Regarding RoHS, a nuanced approach is outlined as follows:
• Products meeting the maximum concentration values as per Annex II to the EU RoHS Directive (2011/65/EU) will continue to be recognised under current EU regulations and CE marking.
• Products relying on exemptions will also retain recognition under current EU regulations and CE marking, provided there is a corresponding exemption under the UK Restriction of the Use of Certain Hazardous Substances in Electrical and Electronic Equipment Regulations 2012.
The announcement also introduces notable adjustments:
• Permanent labelling flexibility allowing importers to indelibly supply their details on accompanying documents, packaging, or adhesive labels.
• Introduction of digital labelling options, enabling manufacturers to incorporate the UKCA marking, manufacturer details, importer details, and declaration of conformity via methods such as QR codes attached to products.
• Implementation of a ‘Fast track UKCA’ process, permitting manufacturers to use the UKCA marking to demonstrate compliance in Great Britain with either UKCA or EU product requirements.
Reflecting on these developments, Wayne Rose, CEO of the BPMA, remarked: “The extension of CE marking recognition and the introduction of new labelling options demonstrate a commitment to facilitating trade and ensuring compliance. However, it’s essential for regulatory bodies to provide clear guidance and support to industries navigating these changes to maintain standards and promote innovation.”
THE BRITISH PUMP MANUFACTURERS ASSOCIATION (BPMA) has welcomed three new members into its ranks.
The first is Oxfordshire-based Ambic Equipment, which designs, tests, manufactures and assembles a full range of peristaltic pumps, dosing and dilution systems. Established in 1977, the company has grown both organically and through a number of strategic acquisitions, including the purchase in 2013 of RF Electronics (RFE), a specialist in the design and manufacture of peristaltic pumps and ancillary products.
Also recognising the benefits of BPMA membership is electric motor manufacturer Menzel Motors Great Britain, the wholly owned subsidiary of Berlin-based Menzel Elektromotoren, which has been manufacturing and distributing electric motors since 1927. Menzel specialises in delivering large electric motors, including special models, within the shortest possible time. The product range comprises high and low-voltage motors, DC motors, transformers, and frequency inverters.
The third company to recently join the BPMA is Tsurumi UK, a subsidiary of the European division Tsurumi (Europe), which forms part of the global network of companies belonging to Tsurumi Manufacturing Company of Japan. Tsurumi has been manufacturing submersible pumps since 1924 for civil engineering, construction, wastewater treatment and domestic applications. Tsurumi pumps are designed to be used in the most demanding environments and are renowned for their outstanding durability and reliability.
The finalists in the 2024 Pump Industry Awards have been determined after another exhaustive judging session.
From the record number of entries received and through some incredibly tight scoring, the judges shortlisted 50 finalists across the eight award categories to go through to the public vote. Those that were fortunate enough to be selected are as follows:
Sponsored by DFA Media
• ABB: IE5 synchronous reluctance motors
• BAUMER ELECTRIC: Bubble Sensor PAD20 for smart pump protection
• BROOK CROMPTON MOTORS: WEPM IE5 Permanent Magnet IE5 motor
• CREST PUMPS: Assoma AVF-C Pumps
• GRACO: QUANTM Electric operated double diaphragm pump
• SALAMANDER PUMPS: TankBoost
• VERDERFLEX: Remote Assistant IoT enabled pumps
• WILO: Stratos PICO
• XYLEM WATER SOLUTIONS: Hydrovar X
PROJECT OF THE YEAR
Sponsored by AESSEAL
• ANGLO PUMPS: Old Pump Rebuild, St James Park, London.
• BAKER HUGHES: High-pressure water injection pump
• BEDFORD PUMPS: Indonesia flood mitigation project
• CAMPION PUMPS: Wilton waste fire booster set
• CORNISH METALS AND KSB: South Crofty tin mine
• HOUGHTON INTERNATIONAL: No water for christmas?
• MENZEL ELEKTROMOTOREN:
All from a single source – state water supply with a slip ring motor with brush lifting device
• XYLEM WATER SOLUTIONS UK: Pump replacement project at Gloucester Docks
ENVIRONMENTAL CONTRIBUTION OF THE YEAR
Sponsored by SPP Pumps
• ANGLO PUMPS: Pump rebuilds and installing inverters – a double-pronged approach to sustainable solutions
• BAUMER ELECTRIC: Bubble Sensor PAD20 for smart pump protection
• BEDFORD PUMPS: Indonesia flood mitigation project
• GRACO: QUANTM Electric operated double diaphragm pump
• MENZEL ELEKTROMOTOREN: State water supply conversion single source solution
MANUFACTURER OF THE YEAR
Sponsored by WEG UK
• APEX PUMPS
• FLOWPLANT GROUP
• KSB
• SPP PUMPS
• WATSON MARLOW FLUID TECHNOLOGY SOLUTIONS
DISTRIBUTOR OF THE YEAR
Sponsored by Caprari/Calpeda
• ANCHOR PUMPS
• ANGLO PUMPS, PART OF THE METCOR GROUP
• BPS PUMPS
• CAMPION PUMPS
• SEAL & PUMP ENGINEERING
SUPPLIER OF THE YEAR
Sponsored by Wilo
• ABB
• EAGLEBURGMANN INDUSTRIES UK
• EMIR SOFTWARE
• MENZEL GREAT BRITAIN
CONTRIBUTION TO SKILLS & TRAINING
Sponsored by Crest Pumps
• AEMT: Ex repair course
• ANGLO PUMPS, PART OF THE METCOR GROUP
• JOHN CRANE: DISCOVER Graduate Engineers program
• KIWA WATERTEC: Water Regulation 4 Compliance and UK and EU Materials Compliance
• SPP PUMPS: Machine Shop Team - 'The Future Cell'
• SULZER: Academy for Pumps and Systems
RISING STAR AWARD
Sponsored by World Pumps
• Sabrina Magistro, BAKER HUGHES
• Darragh Carroll, CAMPION PUMPS
• Molly Sweeney, EAGLEBURGMANN INDUSTRIES UK
• Adam Ross, LEYBOLD
• Ben Warren, SPP PUMPS
• Kia Mousley, SULZER PUMPS WASTEWATER UK
• Jack Watson, VERDERFLEX
• Brooke Wheater, VERDER
Details of all these finalists are now available on the dedicated awards website –www.pumpindustryawards.com/ finalists
The winners will be presented with their trophies at the gala awards dinner on 14th March at the Hilton at St George's Park Hotel, Burton-on-Trent. Places are still available at this not-to-be-missed event, so whether it's taking a table to host customers or booking a few seats for you, your team and partners, don't miss this fantastic opportunity to enjoy a wonderful evening of great food, fine wine, fantastic entertainment and that all-important networking until the early hours, when the event's now infamous survivors' breakfast will be served.
To help deliver the 23rd staging of this key industry awards ceremony, those enjoying the evening will this year be joined by Martin Bayfield,
Don't let this be your last copy of flow
one of the most recognisable faces in British Rugby. At 6'10", Martin Bayfield was one of the tallest players in rugby, a gift he used to full advantage as one of England's most potent forwards. He enjoyed a successful international career, winning 31 England caps and two Grand Slams. He played in the World Cup in South Africa and was selected to represent the British Lions in New Zealand.
Since retiring, his height helped him win the part of Robbie Coltrane's body double as the giant Hagrid in the Harry Potter films, and he is now an established member of the commentary teams for BBC, ITV, Channel Five, and BT Sport.
Places can be booked online at the event's website, and with a record number of tables booked already, it is set to be another great event. chevron-circle-right
THE LATEST DEVELOPMENT OF ABB’S
IE5 SynRM (synchronous reluctance motor) series sees the launch of a new version that combines the benefits of ultra-premium energy efficiency with highly effective liquid cooling.
Customers can use IE5 SynRM Liquidcooled motors to save energy costs and cut emissions in new projects or as a drop-in replacement for less efficient motors.
A significant advantage of the IE5 SynRM Liquid-cooled motors is that they are much more efficient than the traditional liquid-cooled induction motors and offer significant potential for upgrading with energy-saving technology.
Reliability is improved by highly effective cooling combined with the cool SynRM rotor and cooling ribs on the bearing assembly that reduces the operating temperature of the bearings. This helps to increase the lifetime of this key component and reduce maintenance needs.
The motors are robust, with tight seals to keep out moisture, dirt and dust, and a smooth outer surface to prevent dust buildup. This makes them perfect for demanding applications that require high power density where space is restricted, such as marine propulsion systems and thrusters. Furthermore, the motors do not need fans or ventilation, so they do not disturb the surrounding air or release heat into the local environment. This is a major benefit in processes that are impacted by airflow,
such as rubber and plastics production, and food and beverage applications like chocolate conche machines. With no fans, the motors also enhance the working environment by reducing noise levels.
The high power output of the liquidcooled IE5 SynRM offers increased design flexibility. It can enable a machine to be upgraded to deliver a higher power output within the same footprint, or it can allow for a more compact installation footprint while still providing the same output.
IE5 SynRM Liquid-cooled motors are available in frame sizes IEC 200-315 in aluminium frames, with steel available on request. The versatile design enables the motors to provide exceptional performance over a range of powers from 37 to 710kW
new.abb.com
MOTOR AND DRIVE SUPPLIER WEG has announced the launch of its new ADV200-SP drive for solar pumping applications. This cutting-edge variable frequency drive is designed specifically for isolated or hybrid solar-powered water pumping systems, bringing a new level of efficiency and sustainability to the agricultural and industrial sectors.
The ADV200-SP drive is one of WEG’s latest inverter offerings. Developed using WEG’s expertise in industrial drive technology, the new ADV200-SP drive combines the capability of the existing ADV200 inverter and WEG’s extensive experience in solar and pump applications via photovoltaic (PV) panels.
Leveraging the synergy between its inverters and solar technology, WEG has also developed a software application that optimises the operation of solar pump systems.
At the heart of this innovation is the MPPT dynamic search algorithm, developed by WEG engineers. This algorithm ensures that the ADV200-SP Drive continuously adapts to varying irradiation and temperature conditions,
maximising system load at maximum output power. This adaptability allows for greater efficiency and performance under real-world conditions.
One of the standout features of the ADV200-SP Drive is its versatility in accommodating different plant configurations. It seamlessly caters to isolated systems with a single solar source, dual systems alternating between solar and secondary AC sources, and hybrid setups that can also incorporate both sources. A special source manager function integrated into the drive simplifies the management of dual-source systems, ensuring a smooth transition from one source to another while prioritising the use of free solar energy to maintain irrigation continuity.
making it suitable for a wide range of plant dimensions. Whether integrated into a small-scale operation or a complex irrigation system, this drive has the power and adaptability to meet a range of needs.
To provide comprehensive support for pump protection and operation, the ADV200SP incorporates several specialised features within its software. These features include radiation sensor management, auto start and stop functionality, tank level control, dry run protection, flow and pressure loop control, suitability for both distribution and submersible pumps, and even a pump cleaning feature. This comprehensive suite of functions ensures that any pumping system operates smoothly and efficiently.
The ADV200-SP Drive boasts a power range spanning from 1.5 to 400kW,
CONTROL TECHNIQUES HAS launched a new solar pump solution designed to provide a cost-effective and scalable solution which delivers reduced operational costs, improved availability, and increased sustainability by using locally generated renewable energy.
Control Techniques’ Solar Pump Solution can harness the sun’s power to get water to where it needs to be, irrespective of power infrastructure, availability, and the associated costs. This will provide a reliable and eco-friendly alternative for pumping systems in remote and challenging environments, significantly reducing the carbon footprint associated with traditional electric pumps and converting previously unserviceable locations into areas where water can be transported.
The solution centres around software
that enables the company’s drives to function with solar, grid-generated, or hybrid power supplies and also equips the drives with a range of pump-specific capabilities. This means the drives can be coupled with suitable pumps and solar panels to deliver a full solar pumping capability. Once set up, the drive can be configured to automatically connect to grid power for operation outside daylight hours or as a hybrid system, blending solar and grid sources without affecting performance.
Full system control is ensured by features such as DC bus control loop, Maximum Power Point Tracking (MPPT) and low irradiation start/stop. Furthermore, the solar pump solution can control the most efficient motors available, meeting IE5 efficiency levels, such as the Nidec Leroy Somer Dyneo+ hybrid permanent-magnet motor.
The embedded features in the solar pump solution include controlled pressure ramp-up when filling pipes, pump dry-run prevention, no-flow protection and tank-full/well dry control, cleansing cycles to clear the pump impeller to avoid blockages and sleep mode to further minimise energy consumption.
www.ControlTechniques.com
TREBLES, A SPECIALIST in water management solutions, has launched the Trident range; a booster set and tank system offering efficiency, versatility, and reliability in water solutions.
The Trident, which has been designed for a range of applications, integrates into residential, commercial, and industrial settings. Once installed, pumps can be isolated, drained, and removed/replaced without
having to access or drain the tank, resulting in minimal downtime and water wastage.
Its compact design optimises water management without compromising valuable space, while its whisper-quiet operation, water-cooled efficiency, and customisable configuration are supported by an innovative clear door design that provides total transparency into the system.
Trebles Managing Director, Stuart Herritty, added: “Our latest Trident booster demonstrates a significant advancement to other products on the market. By integrating advanced technology with user-friendly controls, we placed the ability to fully access the components of the system, without the need to drain it, in the hands of our customers.”
trebles.co.uk
T-T FLOW’S FULL RANGE OF SWING check valves has been awarded accreditation from the Water Regulations Advisory Scheme (WRAS).
WRAS is one of the bodies which contributes to the protection of public health by preventing contamination of public water supplies and encouraging the efficient use of water by promoting and facilitating compliance with the Water Supply Regulations and Scottish Byelaws. These require that a water fitting should not cause waste, misuse, undue consumption or contamination of the water supply, and must be ‘of an appropriate quality and standard’.
To qualify for WRAS Reg4 certification, which is recognised as evidence of compliance by every water supplier in the UK, the full range of swing check valves has undergone a rigorous testing procedure for
certification.
The now fully WRAS Reg4 certified swing gate valves (DN50-DN300) offer epoxy-coated ductile iron bodies and metalto-metal seals for vertical and horizontal installation. These models are available with an optional external weighted arm. This valve is used to prevent reverse flow and is suitable for potable water, wastewater, and sewage applications.
www.ttpumps.com
pilot of its digital asset management technology with Anglian Water, Norwegian digital analytics company, InfoTiles, is embarking on an expanded proof of concept programme.
The ongoing collaboration with the UK utility will use its artificial intelligence (AI) driven software to manage roughly 317 biofilters, along with pumps and valves, and will be extended from 24 sites to 100.
The continued partnership establishes the ambition that Anglian Water will be able to move towards fully integrating the InfoTiles technology to enhance day-to-day operational visibility.
Full integration will create betterinformed asset management decisionmaking and allow for further understanding of maintenance prioritisation of water recycling assets.
Approximately 483 data points will be measured across all assets included in the scale-up. The water recycling centres will be chosen based on current model predictions and their ability to send relevant asset data to the InfoTiles software.
The initial 12-month pilot of InfoTiles’
celebrating the installation of its 60th alkali surfactant polymer injection pump for a large Indian exploration and production company.
The first Hydra-Cell seal-less and packing-free API 674 pumps for polymer injection, which were installed within their oil field sites almost five years ago, have been running 24/7 in continuous operation for over 50 months with no interruption to production.
These pumps inject polymer with a viscosity of 20-50cP into the well at a flow rate of 4m3 per hour, with the discharge pressure ranging from 20-100 Bar, depending on the well’s characteristics.
Within some of the sites, the pumps’ flow rates run at approximately 2m3 per hour, with pressure ranging from 50 bar to 140 bar. With the latter, the higher pressure is required as the pump
software monitored the rotating arms of 76 biofilters at 24 sites over a period of six months, to assess whether they were rotating when needed. It also measured sludge blanket levels in final settlement tanks to monitor optimal ranges for effective operation.
The data was collected through a mix of new and existing sensors via supervisory control and data acquisition control (SCADA) systems. This was combined with flow rates and publicly available weather data, to build a rich contextual overview of what was happening at Anglian’s water recycling plants in real-time.
InfoTiles also combined Anglian Water’s existing SCADA systems into one event-streaming platform that aggregated, compared, and visualised the reliability of the equipment.
The strength of the InfoTiles platform is the ability to visualise and model process data through machine learning to show the likelihood of critical failures in wastewater treatment, such as potential stoppages and breakdowns.
When fully integrated, this will allow Anglian Water to easily trial and compare different sensor technologies for reliability and accuracy.
During the initial pilot phase, 14 machine-learning models were used to identify biofilter deviations and identify whether failure or slowdown was imminent. Four models were selected and brought forward for further development due to their ability to scale.
is running at ground level, injecting the polymer 1700m below the surface.
Because of Hydra-Cell’s very low-shear pumping action, polymer consumption can be reduced by up to 15%. The unique valve design enables the low shear pumping action, minimising the polymer shear, and optimising polymer usage. With no dynamic seals, the pumps ensure the polymer is 100% contained and with no leakage there is no waste and the polymer is free from oxygen, which stops degradation.
For the first 14 pumps installed, the typical maintenance was less than $3,000 over five years, equivalent to just over $40 per pump per year. A plunger pump with dynamic seals and packing would have incurred costs of almost $6,000 per pump in a year, as estimated by the manufacturer themselves.
Wanner Hydra-Cell pumps are designed for 25+ years’ service life with
ease of repurposing for other duties. They are very simple to service, with no special tools required for “in-field” inspection of the liquid end. HydraCells can run dry indefinitely and are self-priming. They are highly efficient, with more than 90% energy delivery from pump shaft to hydraulic power, achieving significant energy savings.
Motors up to 25 MW and 13.8 kV
• Low voltage slip-ring and squirrel cage motors up to 3,000 kW
• Medium voltage slip-ring and squirrel cage motors up to 15,000 kW
• Direct current motors up to 2,000 kW
• Frequency converter-proof drives
• In-house load test facility up to 13.800 V, 2.300 kVA, 120 Hz
Customized special designs
• Custom designs for special applications and operating conditions
• Optimized motor design for higher efficiency
• Mechanically and electrically interchangeable motors
• Commissioning worldwide
MENZEL
By combining optimal hydraulics and wearresistant materials in a pump replacement, Sulzer has helped a phosphate fertilizer producer to increase productivity with its AHLSTAR WPP end-suction single-stage pump.
Phosphoric acid is produced with a hemihydrate process, which is considered very severe for the rotating equipment installed in the reactor. The relatively high phosphoric acid concentration and impurities combined with the elevated reaction temperature create a very aggressive environment.
A slurry filter feed pump plays a very critical role in a phosphoric acid plant. A failure will directly impact the plant’s production rate, which is why robust and reliable equipment with the longest possible lifetime was considered to be of prime importance in this application.
Sulzer selected an AHLSTAR WPP53-100 single-stage process pump for the site. The WPP pumps are designed to be extremely wear-resistant and especially suitable for abrasive and erosive industrial applications. The series offers a comprehensive material selection, and the pumps can be tailored to suit the most demanding industrial applications with accessories such as shaft sealing solutions and heavy-duty bearing units.
The previous pumps were made
of a material that is very commonly used in phosphoric acid applications, CD4MCuN. This duplex stainless steel can give acceptable results in some applications of a dihydrate process, but it is not one of Sulzer’s solutions in a hemihydrate process. In this case, the company prefers a higher-grade alloy, 654 SMO. This material, classified as 6%Mo super austenitic stainless steel, has an excellent resistance to corrosion by hot acid with a high chlorides content. It is more and more commonly used in the phosphate industry because it combines a very good resistance to corrosion and better erosion resistance than some more common austenitic stainless steels.
the prolonged lifetime of the pump are the wear-resistant design of a semi-open impeller and a casing fitted with a front wear plate.
Due to the modular construction of the new AHLSTAR WPP, only worn parts of the pump must be replaced. In the earlier pumps, the lifetime of the parts subject to the highest erosion and corrosion was very short, between three and six months. Along with the pump replacement, the average lifetime of the parts was increased to 12 to 24 months, reducing the maintenance frequency by up to 75% from what it used to be.
The previous pump at the site was rotating at a speed of around 1,800 rpm, which was too high for this application. A pump with a low speed of rotation and a full-diameter impeller was required — an AHLSTAR WPP53-100 with a significantly bigger impeller diameter than the previous pump was selected. Although the head is fixed, a lower rotation speed contributes to reduced wear. Other features adding to
Given the harsh operating conditions and the vast improvements compared to the former installation, the replacement is considered to be very successful. After a few years in operation, the pump has proven to be such a major upgrade that more pumps at the site are being replaced with AHLSTAR pumps.
www.sulzer.com
GLOBAL MOTORS AND DRIVES manufacturer, WEG, has recently completed the first delivery of three W22 280S/M 110kW 380V V1 vertical motors, with IP67S degree of protection. WEG’s engineering team met this newly achieved IP rating at its manufacturing site in Portugal. This first order of these vertical motors was placed with one of the largest pump manufacturers in the world, KSB.
This delivery, set to be part of the prestigious Mazareatoson Station in Egypt, represents a remarkable achievement in electrical engineering. These motors are specially designed to guarantee protection against the effects of total immersion in water down to one metre deep, for a maximum period of 30 minutes, providing a safe and reliable solution for demanding environments.
The degree of protection of a product, represented by the IP index, is an international standardisation established by the International Electrotechnical Commission (IEC) to classify the protection of electrical products against the ingress of dust and water. In the case of these motors, the IP67S rating guarantees exceptional performance in the most adverse conditions.
The sale and distribution of these motors was negotiated by WEG’s distributor in Egypt, Index Power Solutions (IPS), as part of the company’s
www.weg.net
The British Pump Manufacturers Association is deeply concerned by the recent announcement from the Office for Product Safety and Standards regarding the prevalence of non-compliant circulator pumps in the UK market. The revelation that recent market inspections identified 85% of imports of these products as non-compliant underscores the urgent need for action to safeguard consumers and uphold industry standards.
The OPSS states its primary purpose is "to protect people and places from product-related harm, ensuring consumers and businesses can buy and sell products with confidence". In the product regulator's 2022-2023 delivery report, it stated that inspections it had carried out had "revealed non-compliance in over 85% of the circulators" it reviewed.
The findings of the inspections conducted by the Office for Product Safety and Standards (OPSS) are alarming and raise serious questions about the efficacy of current regulatory measures governing circulator pumps.
Non-compliant products not only offer significant reductions in energy efficiency values, but also undermine the integrity of the pump industry and erode trust in regulatory processes.
Consumers who have unknowingly had non-compliant circulator pumps installed can face unexpectedly high bills from unplanned electricity and water usage, as the pumps fail to meet their expected performance standards.
The plumbers installing these non-compliant pumps and the wholesalers who supply them are not to blame. Many of the non-compliant pumps are 'CE-marked' to suggest compliance with European Union standards, but the manufacturers of the dodgy pumps, the majority of which are based in China, use a similar font to the CE mark but use it to reference the pumps being a 'China Export'.
As the leading voice of the pump industry in the UK, the British Pump Manufacturers Association (BPMA)
emphasises the importance of robust enforcement mechanisms to address the influx of noncompliant products into the market. It is imperative that regulatory bodies collaborate closely with industry stakeholders to implement effective strategies for detecting and preventing the circulation of non-compliant pumps. The association welcomes the OPSS's removal [delisting] of some thirty products identified as not satisfying the required compliance measures. But it is calling on the body to redouble its efforts and work to stop the import of non-compliant pumps completely.
decisive action to tackle this issue and ensure that only energy-efficient and compliant products are available in the market."
“The proliferation of noncompliant circulator pumps is a significant concern.”
In response to these developments, the BPMA reaffirms its commitment to promoting excellence and compliance within the pump industry. The association stands ready to collaborate with the OPSS and other relevant bodies to develop and implement measures that enhance product safety and integrity.
Wayne Rose, CEO of the BPMA, commented, "The proliferation of non-compliant circulator pumps is a significant concern for both manufacturers and consumers. We urge the government and regulatory authorities to continue to take
The BPMA urges consumers to remain vigilant when purchasing circulator pumps and advises them to seek products bearing recognised certifications and compliance markings. chevron-circle-right www.bpma.org.uk
The BPMA’s Pump Industry Awards Dinner has become the highlight of the pump industry’s social calendar, celebrating the industry’s best and brightest with the added bonus of excellent networking opportunities and great entertainment. This year’s event will take place on Thursday 14th March at the Hilton at St. George’s Park, Burton on Trentthe training ground for all 28 English national football teams.
On behalf of the BPMA and all our Sponsors, congratulations to the 2024 Finalists, and best of luck for the presentation ceremony, during which the eight category winners will be revealed.
www.pumpindustryawards.com
The Kiwa UK Regulation 4 Product Approval Scheme (KUKreg4)a robust method for demonstrating compliance with the Water Supply (Water Fittings) Regulations 1999.
Methane flaring from oil and gas fields is a huge waste of energy and is clouding the reputation of an industry facing increasing challenges due to climate change. flow finds out how a partnership, which includes sealing specialist AESSEAL, has come up with a solution that could solve the problem of flaring and venting from oil and gas fields and help clean up energy production.
The UK Government plans to ban the venting and flaring of gases in oil and gas fields from 2030. And methane was one of the key issues on the negotiating table at the recent COP28 climate talks in Dubai.
This renewed urgency for climate action has meant that AESSEAL and its partner, Torishima UK, have been working for several years to produce an engineering solution to venting and flaring that many experts have been sceptical could be produced to this tight timescale.
The result of that joint design and manufacturing capability is EcoGuard, a highly engineered product ideal for retrofitting in the world's global oil and gas facilities. The solution is now at the prototype testing stage and will be ready to go to market in the first half of 2024 –six years before the deadline.
EcoGuard seeks to eliminate or reduce intermittent and continuous emissions and could be retrofitted to oil and gas facilities worldwide.
In simple terms, EcoGuard is a small but powerful booster pump that transports gas around a rig's compressor in a similar way to a central heating system circulating water around a house. The booster maintains the gas flow during intermittent shutdowns, an established practice that removes the need for deliberate emissions to prevent system contamination. In the inventive step, the booster also keeps the seal clean to stop leakage throughout continuous operation.
A particular target is stopping methane emissions, a gas 80 times more damaging to the climate than CO2
What's the rush? Mark Wilson from the industry body Offshore Energies UK is quoted on Sky as
saying that retrofitting oil and gas installations "would be difficult within the timeframe we're looking at… It could also mean having to turn sites off." Others are suggesting that financial incentives may be necessary. However, since oil and gas are hugely profitable, many industry leaders now realise that the time has come for action.
The EcoGuard project arises from a desire by AESSEAL's internal dry gas seal team to stop this environmentally damaging practice. The company has a patent pending, and chose pump expertsTorishima UK in Scotland as the perfect partner to manufacture the device.
AESSEAL has calculated that approximately 424m³ of greenhouse gases, predominately methane, are currently released into the atmosphere during a single venting or blowdown of a gas compressor.
A single peak load compressor may be shut down and restarted up to 40 times per year. Extrapolate this worldwide, and the urgency becomes clear.
Scotland has close to 90% of UK oil and gas production. In 2019, over one billion cubic metres of gas was flared from Scottish facilities,
releasing 2.9 million tonnes of CO2 equivalent emissions, which was 21% of the total amount of CO2 released in Scotland.
Not only is this damaging, but it is also incredibly wasteful. The gas flared off could have been used for heating and is equivalent to the total energy consumption of Glasgow.
The project was undertaken as part of AESSEAL's 29by29 pledge to invest £29 million by 2029 in projects primarily aimed at improving the environment.
Commenting on the development of EcoGuard, Chris Rea, Group Managing Director of the AESSEAL Group, said: "My interest is in the environment. AESSEAL does not make pumps, and the EcoGuard technology does not use seals, but I would like to turn off the industrial-scale bunsen burners that are destroying the planet for my grandchildren. I will give our competitors a royalty-free licence on a case-specific basis as the environment needs all the help it can get." chevron-circle-right
flow discovered how the pump cleaning function in ABB’s water and wastewater drives helps prevent damage to wastewater pumping operations.
The Sewage Treatment Plant for Research and Education Das Lehr- und Forschungsklärwerk (LFKW) at the University of Stuttgart in Germany is a facility for wastewater and wastewater treatment and a platform for education, research and demonstration. It is a place where scientists can practically test new wastewater treatment processes comprehensively.
LFKW treats wastewater from the Stuttgart area, including parts of the Vaihingen-Pfaffenwald University area. The volume of wastewater treated annually is around 800,000m³. The pollution load supplied corresponds to a volume of approximately 10,000 inhabitants.
The pump in use at LFKW recirculates wastewater with activated sludge from the aeration tank to upstream denitrification. The solids content in the aeration tank ranges from 4g/l to 5.5g/l. A high-efficiency pump was selected since a continuous-duty pump is used at the location. After a new dual-channel impeller pump was installed, overloads occurred within a few days due to very high current consumption, and the motor burned out on two occasions. The manufacturer came back with information suggesting that contamination and deposits in the pump would have generated these overloads.
The pump had to be replaced three times within two years because fibres and sludge
residues had settled in the gap between the channel impeller and the housing which resulted in increased current consumption, and eventually damaged the motor. The imbalance caused bearings to fail, or the winding would burn out due to high current consumption. Replacing the pump involved a lot of effort each time.
A crane truck was required to lift
To correct the problem, ABB's ACQ580 variable speed drive with 4kW of power was installed for motor control in February 2021. The drive has been specially designed for water > 24
All job information is visible at the office as it happens.
Smart Site delivers accuracy. The app captures information as it happens, meaning there is less chance that something important is missed or recorded incorrectly.
Smart Site streamlines the administrative process ensuring that contracted and chargeable work can be completed in a timely fashion and invoiced with complete confidence.
Smart Site stores the history of an asset’s repair and service, so your engineer has all of the detail they need to do the job right first time.
and wastewater applications. The integrated pump cleaning function in the drive is particularly suitable in this situation. It is intended to prevent solid particles from becoming lodged in pump impellers or piping. Traditionally, the blockages would be removed manually, but this requires the pump to be decommissioned and opened.
The pump cleaning function in the ACQ580 consists of a programmable sequence of forward and backward rotations to loosen and remove deposits from the pump impellers and piping. It prevents blockages, making the need for manual cleaning less frequent.
The drive starts the cleaning process by applying a pulse in the direction opposite to the operating direction. The duration of the cleaning pulses is the same in both positive and negative directions. Several cleaning pulses in the positive and negative directions can occur within the same cleaning sequence.
The ACQ580 operates the pump's motor at a frequency of 48Hz. The target is a constant flow rate of approximately 20l/sec, as a uniform recirculation rate is essential for the process. The flow rate should be kept constant to achieve a high denitrification rate.
Since the ABB ACQ580 has been in operation, it is clear that the self-flushing of the pump is working again. The flow rate decreases slightly at a constant speed over the day and increases again after cleaning.
Figure 1 shows how the troublefree operation works. The pump operates at a constant speed, and the drive monitors the power consumption. The pump is usually reversed once a day. If increased power consumption values start to appear, the drive stops, runs an automatic cleaning program and then restarts at the set point speed. In trouble-free operation, the flow rate at constant speed
is the same before and after flushing. Flushing is performed depending on the pollution. So, in the example shown, flushing was run twice on November 3, 2021, and once a day on other days.
If increased pollution occurs, the delivered flow rate fluctuates at a constant pump speed. This can be caused by deposits in the pump chamber, in the wear rings of channel impellers or in the suction or pressure nozzles. Figure 2 shows one such example. After flushing, the flow rate increases and then steadily decreases. Then, the circuit is flushed, and the pollution is rinsed out. This causes the pump to deliver more water again at the same speed.
Figure 3 shows 24-hour cycles without heavy pollution on December 10 and 11, 2021. On December 13, the flushing program started, but the pump did not immediately deliver the desired flow rate since dissolved pollution needed to be rinsed out. The pump will not give the expected flow rate until it has fully rinsed everything out.
The results show operation at a constant rotational frequency. That's why the flow rate fluctuates. If the pump is operated with rotational frequency control and a fixed flow rate, the comparable effect can only be detected in the power consumption and the speed (frequency).
A dual-channel impeller pump at LFKW that pumps recirculation water from the aeration basin to the denitrification basin has seized repeatedly in the past as a result of pollution, resulting in total pump damage. Since installing the ABB ACQ580 water and wastewater drive with built-in pump cleaning functionality, the pump has been running troublefree and with low wear. Overloads did not occur, and bearings no longer needed replacement. The experience gained at LFKW can be transferred to all wastewater treatment plants. If there is a risk of clogging, clogged areas
can be loosened using the pump cleaning function of the drive, and doing so will not block the pump either on the suction side or the pressure side. chevron-circle-right
Safe and efficient mag-drive centrifugal pumps, available from DESMI, can enable leakage-free methanol fuel systems for ships, reducing vessel carbon emissions and climate impact, as flow discovered.
With every year that passes, emission regulations tighten in the shipping industry. Shipowners who want to stay in business must look for ways to reduce carbon emissions to comply with the targets defined in the International Marine Organisation (IMO) greenhouse gas (GHG) strategy and other regulations.
Running on alternative fuels is one of the most effective ways of reducing emissions. Methanol provides several key benefits as a shipping fuel, making it one of the most promising alternative fuels: When produced from biomass, green hydrogen, or other zero-emission sources, it enables neutral well-to-wake carbon dioxide emissions. And because methanol stays liquid at ambient temperature and atmospheric pressure, you do not need to invest in complex high-pressure or lowtemperature systems to use it.
However, methanol is also toxic and highly flammable, which prompts safety considerations when selecting and installing a fuel infrastructure for ports and ships. Specifically, you must ensure the fuel system is absolutely leakage-free to avoid hazardous situations.
DESMI's new mag-drive centrifugal pumps are well suited to operation in a methanol fuel system. They combine the high efficiency and robust reliability of centrifugal pumps with a magnetic coupling, eliminating the pump's traditional shaft seal solution. As the pump chamber is
completely sealed, there is virtually zero risk of methanol leakage.
While the magnetic coupling is a new feature on its centrifugal pumps, the technology itself is not new to DESMI.
"We introduced magnetic coupling technology in the 1990s, so we're building on three decades of solid experience here," commented Martin Bro, Global Sales Manager, Gas Systems, at DESMI.
The DESMI mag-drive centrifugal pump is ideal for methanol fuel systems on new-build dual-fuel ships and can also be retrofitted on existing vessels. It is part of a complete portfolio of marine pumps, which covers a wide range of applications.
"We can supply pumps for the entire fuel pathway, from bunkering vessel to engine room," added Martin. "In addition to mag-drive centrifugal pumps for methanol transportation, we offer pumps for applications such as boosting, draining, and water heating. And we always look beyond the pumps and work with our partners and customers to design a solution that fits the specific requirements to the letter."
The new pump from DESMI is specifically designed for marine applications and comes with a lengthy list of class approvals and certifications, for example ABS, BV, CCS, DNV, KR, and LR. Built for compliance with the IGF Code, it is designed to meet the rigorous safety standards for ships using gases or other low-flashpoint fuels, and for installation in ATEX zone I if required. Its built-in temperature sensor detects overheating and helps avoid
breakdowns, and it can be specified with a leakage sensor.
In addition to setting an ambitious net-zero emission target by (or around) 2050, the IMO has declared that by 2030, the carbon intensity of ships must be reduced by 40% compared to a 2008 baseline. Using methanol and other alternative fuels is an efficient way of reaching both targets, even though these fuels are sometimes hazardous.
"It's ironic that methanol, which can really reduce the climate impact of the shipping industry, is itself so toxic and flammable," concluded Martin. "But that's the reality, and with the right technical solutions, these challenges can be overcome. We're dedicated to sustainability and energy efficiency, and we've worked to reduce the climate impact of shipping for decades. I'm confident that the mag-drive centrifugal pump will help us continue this evolution and contribute to a better future." chevron-circle-right
www.brookcrompton.com
Keeping industry turning every second... every day...every year
With over 110 years of technical and design expertise, Brook Crompton offers leading edge energy efficient electric motors across global markets. As the original innovator in electric motor development, Brook Crompton are trusted to power limitless industrial processes and its robust motor design drives fans, pumps, compressors, conveyors and more.
Driven by technology and innovation, Brook Crompton has one of the widest available ranges of electric motors for operation in safe areas, hazardous atmospheres and hostile environments.
The extensive range of stock can be quickly modified to suit customers’ needs and with a high level of technical support from our knowledgeable team we ensure the correct selection of motors is provided for your application.
Brook Crompton’s focus on product and service development ensures we continue to move forward to improve efficiency, offer lower cost of ownership throughout their lifecycle and to reduce environmental impact.
Several factors need to be considered when designing the piping element of a pumping system, and in the food and beverage sector, there are specific considerations related to hygiene. Chris Callander outlines some best practices in piping design to meet stringent regulatory standards and achieve high-quality production outcomes.
The piping design for a pumping system to be used in the food and beverage industry is critical for maintaining product integrity, ensuring safety, and optimising operational efficiency. Let’s look at several key areas which include material selection and standards, hydraulic considerations, layout optimisation, flexibility and monitoring.
In many food and beverage applications, stainless steel is preferred for its corrosion resistance, ease of cleaning, and nonreactive properties, which can be crucial for maintaining product purity.
Food-grade plastics may be used in specific scenarios where flexibility and corrosion resistance are critical, but with caution regarding wear and chemical compatibility.
Establishing which standards are relevant to your sector and application is important. These will often affect material selection and other aspects of system design. For example, 3-A Sanitary Standards and EHEDG Guidelines ensure equipment design promotes hygiene and is easy to clean and sterilise. While ASME BPE guides the design of bioprocessing equipment, which is applicable in many food and beverage processes.
Correct pump and pipe sizing avoids issues like cavitation and excessive wear. The design of a system should employ hydraulic calculations to match the pump capacity with system requirements, considering factors such as fluid viscosity, density, and flow rate.
Maintaining optimal flow velocity helps to prevent sedimentation in lowvelocity areas and erosion in high-velocity sections. Recommended velocities vary by application but typically range between 1.5 to 3m/sec.
Incorporating straight runs before and after critical components helps to reduce turbulence and facilitate easier maintenance. In addition, the layout should be designed to allow easy access to all equipment and valves for cleaning, maintenance, and inspection.
Sloping piping correctly is also important to promote complete drainage, a critical aspect in avoiding bacterial growth and cross-contamination.
Piping should be designed with Clean-InPlace (CIP) systems in mind, ensuring that all parts of the system are accessible to cleaning solutions without dismantling. Features like spray balls for tanks and appropriate connections for CIP systems to circulate effectively should also be included in the design.
Adopting a modular design approach allows for easy expansion or reconfiguration of the piping system as production needs evolve. While using standardised components helps to facilitate quick changes and minimise downtime.
Integrating sensors and flow meters for realtime monitoring of pressure, temperature, and flow rates makes it possible to ensure the system operates within specified parameters.
While implementing automation solutions for critical control points can enhance precision and reliability in product quality.
Designing a piping system for food and beverage processing is a complex task that demands a strategic approach to material selection, layout optimisation, and system integration. I have only been able to give the briefest overview here, and I would recommend talking to a specialist, such as your pump supplier, before starting the system design process if you are unsure of any of the areas mentioned above.
But, by adhering to industry standards and incorporating best practices in hydraulic design, cleaning, and monitoring, businesses can achieve a highly efficient, safe, and scalable pumping systems. This not only ensures the quality and safety of food and beverage products but also enhances operational efficiency and sustainability in the long run. chevron-circle-right
and
All machines are supplied with guarding meeting the requirements of Machinery Directive 2006/42/CE.
Range of products and services
•Horizontal hard bearing balancing machines
•Vertical axis hard bearing balancing machines
•Semi & fully automated balancing machines
•Portable vibration analysers/balancers (onsite balancing)
•Site service directly from the UK
•Sub-Contract balancing service
•Applications engineers support
•Genuine CEMB spare parts
For further information contact us:
T: 0161 872 3123
E: enquiries@cembhofmann.co.uk
www.cembhofmann.co.uk
Fruit juice manufacturer SOKO Gorica has increased the efficiency of its production process by replacing a pump that failed to transfer highly viscous peach concentrate with reliable Bredel 25 hose pumps.
SOKO produces over 30 million fruit drinks a year with a process based on high-capacity automatic equipment and certified with an ISO 22000 quality management system. However, due to a pump from another manufacturer being unable to handle the viscosity of the peach concentrate, SOKO had to revert to manually transferring the product, adding water and reprogramming software to adjust the recipe. This slowed the process at SOKO’s production site in the Republic of North Macedonia as more time was spent preparing the production and the recipe.
Peach concentrate of 32Bx (degrees Brix) and a volume of 1,14kg/m3 was not being pumped from the aseptic drum, because the viscosity was too high for the pump size to handle.
Unhappy with the support it received from the pump manufacturer, SOKO contacted Watson-Marlow Fluid Technology Solutions (WMFTS) to discover what alternative pump solutions it could offer. WMFTS recommended a Bredel 25 peristaltic hose pump with an F-NBR food contact hose (compliant with EC1935/2004 and FDA 21CFR177.2600 and meeting 3A standards) for the application of unloading fruit concentrate and puree from an aseptic drum to a production process tank. This involves a recipe of 20kg of juice concentrate mixed with water and additives (vitamin C, sodium citrate, aroma), depending on what juice is being produced.
Alan Varelija, WMFTS sales engineer for the Balkans region, said: “I wanted to assure the customer that our solution would work, and after consultation with SOKO and our experts, we decided to send one of our demonstration pumps for a trial at SOKO. The trial results were exceptional, so the customer had no doubts about the purchase.”
SOKO uses the Bredel pumps to handle highly viscous peach and banana
concentrates (4000-5000cP) and other fruit concentrates (approximately 3000cP). Since purchasing the Bredel pumps, SOKO’s preparation time has been shorter, with better hygienic conditions and a more efficient process than the manual preparation adopted when the previously used pump failed to transfer peach concentrate.
As the peach and other fruit concentrates are now being transferred quicker, SOKO uses less energy and has reduced its energy costs. The Bredel 25 also does not vibrate like the previous pump, which affected the stability of the surrounding infrastructure at the production site.
Nikola Karanfilovski, Technical Manager at SOKO, said: ‘’With the previous pump, we didn’t manage to pump very viscous peach concentrate from drums. This problem meant we had to prepare recipes manually, adding water and reprogramming software to adjust all ingredients. With Bredel, pumping is smooth, and we don’t have the time-
consuming manual job. We can now finish recipes with simpler manipulation, with better hygienic conditions, and in a much faster time than before.”
Using direct coupled technology, Bredel combines the reliability of long-coupled pumps with the compact footprint of close-coupled pumps. The Bredel 25 pumps viscous and abrasive slurries and pastes, up to 80% solids in suspension. It has a repeatable volumetric accuracy of +/- 1%, a maximum flow rate of 2,740l/ hr and a capacity of 0.3l/rev. The pump’s maximum discharge pressure is 16 bar, and it can handle a maximum fluid temperature of 80°C.
SOKO Gorica Ltd exports 95% of its annual production to 30 different countries, including the US, Australia, New Zealand, United Arab Emirates and multiple nations in Europe. chevron-circle-right www.wmfts.com
HAYLEY GROUP IS SET TO PROVIDE that makes machines for the post-harvest processing of vegetables with two new Landia chopper pumps that have special external shredders.
Originally developed to deal with difficult wastewater solids in the fish processing industry, the Landia shredder-propeller design has proved its capability in handling troublesome stringy material such as carrot tops which typically cause problems for standard pumps.
Daniel Moulding, Assistant Manager at nationwide engineering component supplier Hayley Group, said: “The Landia chopper pumps work extremely well for our customers in numerous applications. In this particular challenge, the specialist machinery company asked us for help because their existing pumps struggled with the fibrous and gritty material that is an inevitable part of the wastewater process with vegetables.
“This latest purchase of two new Landia chopper pumps follows orders for five units successfully introduced at various locations during 2023.
“Landia has been very helpful indeed in working with us to understand our customers’ needs, adapting the shredderpropeller so that there is no longer any downtime on the processing lines, which is a huge benefit.”
Howard Burton, Technical Sales Engineer for Landia, added: “For certain effluents with difficult solids, the pre-cutting shredder-propeller adds another important chopping stage, continuously reducing particle size and keeping the process running efficiently.”
Daniel continued: “Besides providing such an effective, reliable solution, Landia also gives us fast and efficient backup whenever needed.
“When our customer first used the Landia Chopper Pump, they said they’d never return to the previous unit type. Another eight pumps later, we and they are delighted with the positive outcome, as are the end-users of the equipment.”
www.landiaworld.com
Patterson Pump Ireland is a complete pump manufacturer, offering our customers some of the most reliable pumping solutions available. Our fire pumps stand over life and property throughout the world.
Reduce on-site labor time, engineering and installation time and associated costs. Choose a system that arrives on-site in a fully enclosed ready for use pump house. This pre-engineered pumping system saves time and money for our customers.
+353 (0)44 934 7078 company/patterson-pump-ireland-ltd www.ie.pattersonpumps.com sales@ie.pattersonpumps.com
FIn the wake of Brexit, Wayne Rose, the CEO of the British Pump Manufacturers Association (BPMA), offers his insights on the evolving regulatory environment affecting the pump industry. He outlines the proactive measures taken by the BPMA and its partners to ensure that all policies implemented are balanced and just for every stakeholder involved. applicable directives, standards and compliance matters relating to the manufacture and supply of pumps throughout Europe and the rest of the World, but it is also able to help steer, guide and question these important legislative activities.
or decades the UK and its manufacturing industry aligned the majority of its product safety and certification protocols with that of Europe, ensuring that both elevated levels of compliance and fair competition were maintained across this vast trading block. In fact, drawing on the vast experience and technical expertise available through our extensive complement of trade bodies, institutions and world-renowned academia, the UK has been instrumental in devising much of the regulatory framework that exists today. Its influence has been profound and far-reaching, and contrary to some views, despite the complications brought about by Brexit, many of the UK’s trade bodies, including the BPMA, still maintain a considerable voice on the international stage.
In the case of my own organisation, which represents the commercial interests of UK and Irish manufacturers and suppliers of liquid pumps and other pumprelated equipment, it is itself a member of Europump, the European Pump Association, which represents 15 National Associations across the continent of Europe. Furthermore, as a founding member, the BPMA has representation on the main Europump Council, holds the secretariat of the Europump Marketing Commission, and enjoys strong representation on both the Standards and Technical Commissions.
As such, and directly through this engagement, the BPMA is not only able to keep abreast of all
Navigating uncertainty: Going forward, the BPMA will continue to maintain ongoing discussions regarding the potential divergence of the UK from existing European standards and directives related to product certification. Insights will be provided on how the pump sector can effectively steer its way through the uncertainty brought about by these potential changes.
The critical role of certification: Emphasising the significance of product certification, the BPMA will continue to highlight the potential implications for manufacturers, suppliers, and end-users. Key to this is advocating high-quality standards to ensure the continued reliability and safety of all pump products and their related systems.
Industry advocacy and collaboration: The BPMA is committed to maintaining a proactive role, along with other partner trade organisations, in providing the UK Government with substantial background information and market feedback to help ensure the longawaited updates fully align with industry needs.
“We are actively engaged in providing insights to policymakers, both at home in the UK and within the EU.”
As we navigate the evolving landscape post-Brexit, it is crucial
for the pump industry to adapt to changing standards. At BPMA, we are actively engaged in providing insights to policymakers, both at home in the UK and within the EU, advocating for updates that will benefit the entire sector. Our collaborative efforts with fellow trade organisations underscore our commitment to ensuring a robust and progressive regulatory framework. For the benefit of our pump manufacturing members, we will continue to lobby all applicable persons and entities to ensure essential safety compliance, improved energy efficiencies, and fair and equitable trading opportunities.
chevron-circle-right
This international event provides a unique opportunity for the European pump industry to come together to discuss and debate the important issues currently impacting this key manufacturing sector. A comprehensive programme of talks and presentations, combined with a wonderful social programme will deliver a highly focussed and productive business experience for all those attending.
For more information, and to secure your place, please visit the website today.
With a limit to the number of delegate and partner places available, it is advisable to book early. And if you are looking to extend your stay, either before or after the main event, to enjoy all that Windsor and the surrounding area has to offer, it is even more important to act promptly.
Over 60 years experience
40+ range
Up to 5 years warranty
Loos into lofts, dishwashers downstairs, bathrooms in basements – they’re all impossibly easy with Saniflo.
Our macerators and pumps open up more opportunities and help you make the most of every space. saniflo.co.uk