
7 minute read
Bayne of Timet Outlines Titanium Supply Chain Dynamics and Challenges Caused by Pandemic
By Andrew Bayne, Jr., TIMET
In a normal environment, balancing a titanium supply chain has its challenges, as is typical of supply chains seen in any other industry. And similar to other supply chains, the titanium market has been challenged by the pandemic over the last two years, and it has been particularly strained of late due to Russia’s invasion of Ukraine.
Lockdowns and Labor Shortages
The outbreak of COVID-19 brought on a marked shift in the cargo industry. Ships embarked en masse to deliver much needed medical supplies, but the affected countries were shut down and had either no one to reload the ships, nothing to export or both. Thus, thousands of shipping containers were essentially idled due to a combined shortage of goods and laborers. These same labor shortages left ports, ships, and the global trucking industry understaffed.
The virus and the lockdowns caused another global shift: the manufacture and delivery of goods targeted homebound customers as opposed to experiences and services. Mattress, appliances, and other home goods—all predominantly sourced from Eastern countries—were in high demand; however, logistics companies could not keep pace with the consumers’ quick pivot due to the before-mentioned impacts on shipping containers and logistics infrastructure. Demand was up but availability of container space was at an all-time low and, as a result, freight costs soared and lead times lengthened. As of this writing in May 2022, the situation is showing signs of improvement, but remains imbalanced. COVID-19 outbreaks continue to drive uncertainty, particularly in China.
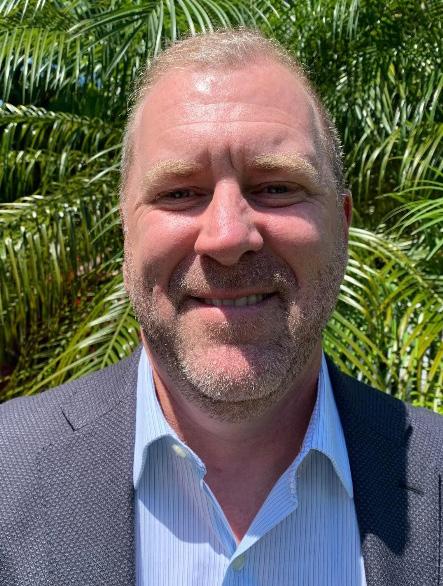
Andrew Bayne, Jr.
TIMET, Titanium Metals Corporation
Sponge and Shipping Routes
Titanium sponge producers globally continue to struggle to find containers and vessels to ship sponge to U.S. melters at an adequate rate to support the aerospace ramp-up. Inventories are lean in the United States, and it will be critical for sponge producers to find creative solutions enabling them to deliver sponge on time. Additionally, UKTMP in Kazakhstan is struggling with importing ilmenite from Ukraine and exporting sponge to customers due to the geographical relationship to Russia and Ukraine.
Feedstock, freight, and energy costs have increased as well, driving up overall input costs in the supply chain. It is imperative melters proactively plan ahead and to accommodate the longer than normal purchasing cycle to secure requirements.
Scrap and its Death Spiral
The scrap market continues to be tight. Aerospace’s 2020 downturn led to severe cuts within aerospace manufacturing and, thus, scrap generation fell to historical lows. The titanium scrap market is in the early phases of the recovery, but it is an expensive one emerging from such a deep trough.
The typical aerospace titanium recovery cycle begins with a ramp in melting. This ramp precedes the scrap generation desired to support the ramp in melt, which typically drives increased sponge and alloy demand.
When COVID-19 hit, the majority of scrap in the aerospace system was forever lost to ferrotitanium and other sacrificial markets, as melt volumes fell and scrap generators needed cash to survive. The remaining aerospace scrap saw subpar scrap segregation due to employee turnover issues; this drove quality levels down, making normally acceptable scrap unrecoverable into aerospace. It has taken time to bring back proper segregation and cleanliness practices to ensure quality scrap returns to the aerospace supply chain; this is beginning to improve as bad practices are eliminated.
Further complicating the tightness in the aerospace scrap market is the strength of the ferrotitanium market which, for the most part, has not been impacted by the pandemic like aerospace. Auto manufacturers have not slowed production other than some impact from semi-conductor chip shortages. Demand continues to be strong, and ferro-titanium producers continue to be busy. The overall lack of scrap generation, including off-grade scrap, is driving ferrotitanium producers to seek the same, higher pedigree scrap required to support the aerospace industry.
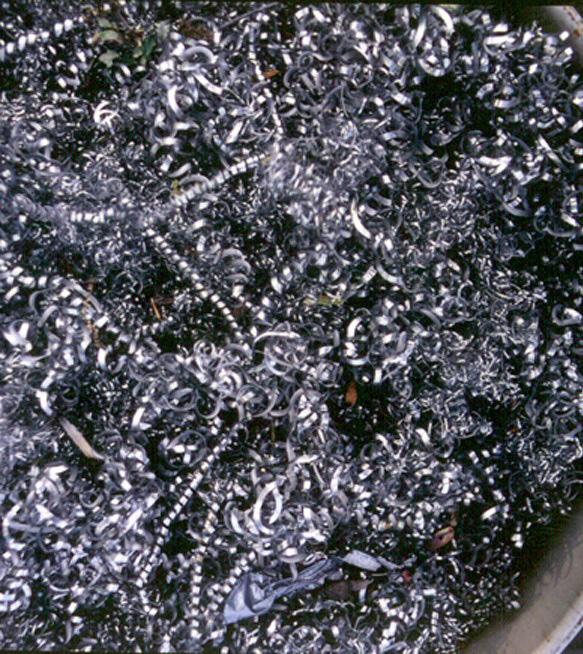
Titanium Scrap
Making the scrap shortage worse, Russia invaded Ukraine last February. Approximately 40 percent of the world’s ferrotitanium production comes out of Russia. With this capacity essentially unavailable, the demand has been driven to United States and European Union producers. Published prices of ferrotitanium more than doubled in a week’s time, and scrap prices followed along with it as producers scrambled to satisfy the new demand. The bottom line: the scrap market today is the most difficult it has been since the 2006 peak.
The supply chain needs to be more creative with scrap utilization and should utilize more sponge and alloy until scrap generation is back in balance with global demand. It is critical for OEMs to ensure that their supply chains are rever ting scrap back to titanium melt shops to maintain a healthy supply chain as growth returns to pre-pandemic levels.
Master Alloys are in the same boat (or not – that’s the problem)!
Elementals have also experienced supply concerns. The same logistics issues—long lead times, soaring freight, and rising material costs—exist for master alloy producers. Prices of almost all commodities have increased substantially, adding further pressure to titanium producer cost structures.
Human Capital
As if everything already discussed wasn’t bad enough, we are in the midst of what some have called “The Great Resignation.” The impact on the labor market post-COVID is difficult to understand. Sponge producers, scrap processors, master alloy producers, melters, downstream processors, etc. are all feeling the impacts of a tight labor market. From the smallest master alloy producer to
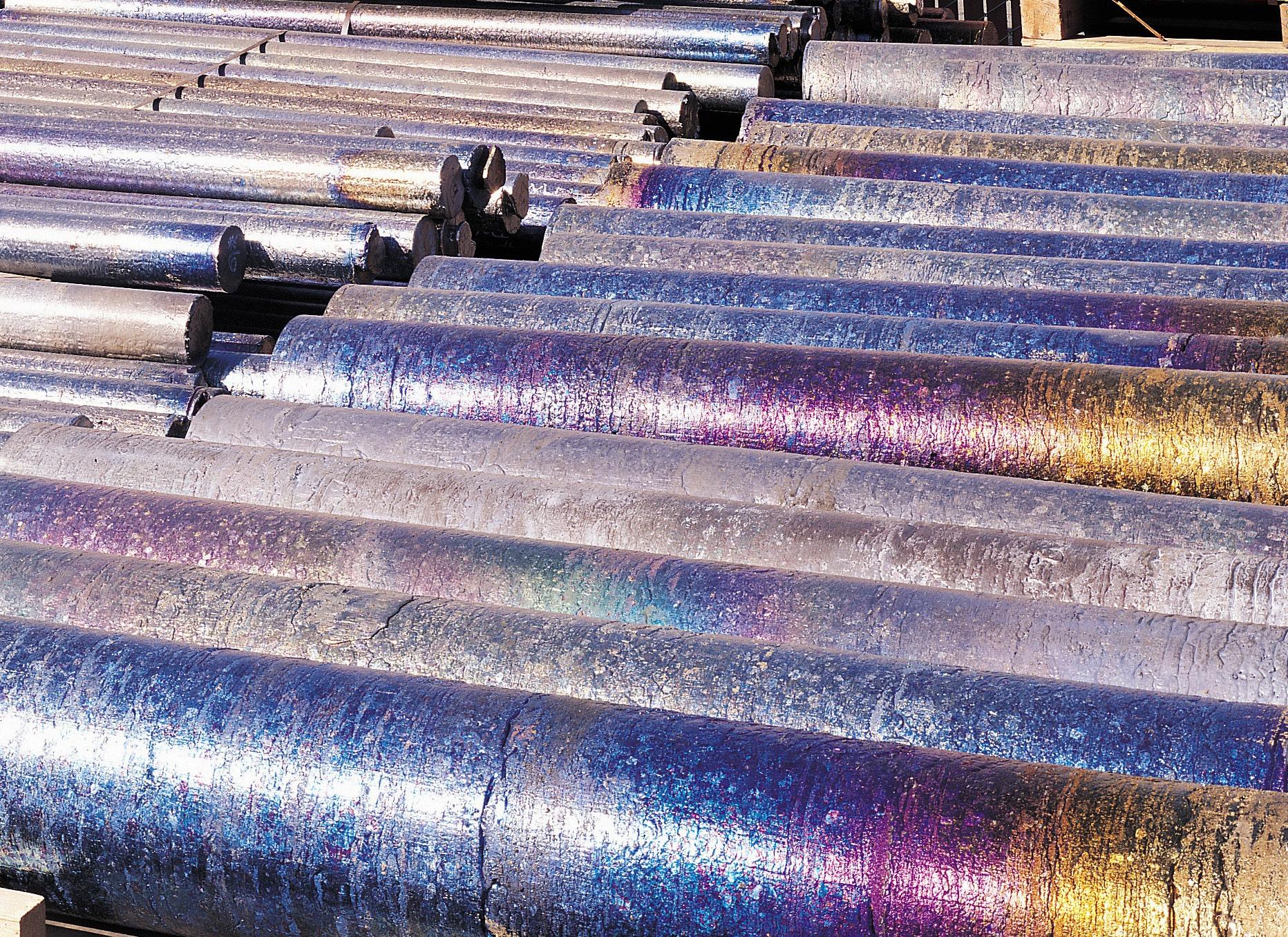
Titanium Inventory
the largest aerospace OEMs, human capital is keeping executives up at night. The theme seems to be a common one—there simply aren’t enough people to support the same production levels that existed pre-pandemic, and nobody seems to have the answers to solve it.
Communication Will Be Key
There have been obvious and significant disruptions in the industry. Planning this supply chain from a melter’s raw materials perspective is more difficult than I have seen in my nearly 20 years in the industry.
Raw materials and labor are tight, demand patterns are shifting, downstream inventory and mix is difficult to ascertain, pandemic and geopolitical uncertainty persist, and transportation problems will make for some difficult times ahead as the industry attempts to ramp up from the 2020 shut down.
Consumers need to be thinking further out into the future than in normal times, as lead times are extended. Forecasts and demand signals throughout the supply chain need to improve. Communication lines must remain robust, and the players need to be synchronized to optimize success.
Producers need to be flexible in how they source raw materials and schedule production. Every link in the chain needs to be asking itself: Will my hiring of manpower to increase rates synchronize properly with my incoming raw materials? Will my suppliers be able to ramp up to support my increased requirements? Do I have a plan B or inventory if my supplies do not arrive on time?
If you can answer yes, make sure the tier ahead of you and behind you agrees. And if you cannot, communicate early and often. If not, titanium runs the risk of impeding the overall air traffic recovery.
(Editor’s note: Andrew Bayne Jr. is the director of global materials planning for the Titanium Metals Corp. [Timet])