
6 minute read
Howmet Executive Tracks Improvements in Titanium Investment Casting Process
By Michael C. Gabriele
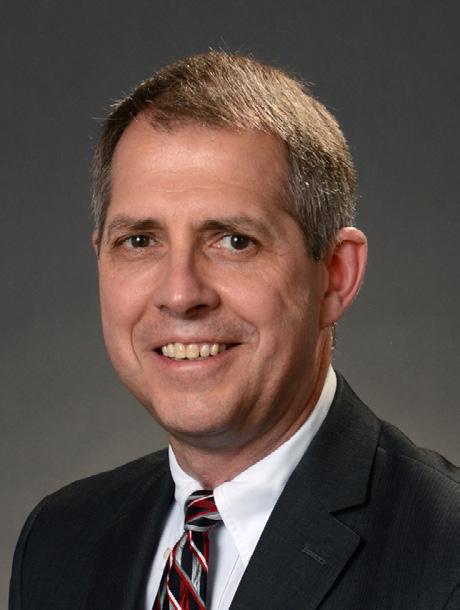
Boyd Mueller
Boyd Mueller, the vice president and general manager of technology and metals for the Engines Business Segment of Howmet Aerospace Inc., has seen steady, significant improvements in the field of titanium investment casting during the last five years—at his company and throughout Boyd Mueller the titanium industry at large. It’s a trend that will continue to gain momentum during the next five years.
Titanium investment casting produces parts through the metallic replication of wax models. The resulting titanium parts have a very smooth surface that requires little finishing after the process. Because a wax model is created in the exact size and shape as the part, investment casting allows for high dimensional accuracy. Investment casting, or “lost-wax” casting, is a fundamental manufacturing technology for producing precision titanium parts for the aerospace industry, industrial markets, and oil and gas business sectors.
Investment casting begins with the production of an exact wax model or pattern of the final product. This pattern is typically produced by injection molding, but it also can be produced by Additive Manufacturing (AM) printing. The pattern is then coated in a ceramic material to create a “shell” or mold. The mold is placed into a furnace where the wax is melted and drained from the shell, leaving behind an empty cavity in the shape of the final casting. The shell is then placed into a vacuum chamber to remove contaminants and ensure casting quality. Molten titanium is then poured into the ceramic mold, which fills the shell cavity. The titanium is allowed to solidify and cool. The ceramic mold is destroyed and removed from the component casting, revealing the final cast titanium part. Investment cast titanium is light weight, has high strength up to 1000°F and is corrosion resistant, which makes it ideal for many aerospace, defense, and subsea applications.
Mueller identified process management as a major area of improvement for titanium casting, which he’s witnessed during the last five years. The thrust, he said, is to be pro-active to define potential problems on the front end of the casting process, rather than try to make adjustments on the back end. “Process management for casting has become much more engineering driven. It involves understanding the process and eliminating defects and rework. The goal is to improve casting integrity and have more consistent properties and quality in the cast parts.”
Another advance cited by Mueller is the utilization of additive manufacturing (AM) in the investment casting process. As he explained it, an AM model or prototype is produced, rather than a wax pattern, for the lost-wax casting process. “We take a different approach for using additive manufacturing,” he said. “Using additive manufacturing, rather than a tooled wax pattern, cuts out time and expense to produce a cast part. We replace a traditional wax pattern with a printed, additive manufacturing pattern.” He added that using AM, rather than wax, has other advantages, as AM is suited to support the increasing complexity of cast parts, especially those where the geometry is difficult or impossible to tool.
A third area of recent innovations for the casting process is the specification of higher-performance titanium alloys. Much of this is driven by demands from the aerospace industry to produce titanium parts
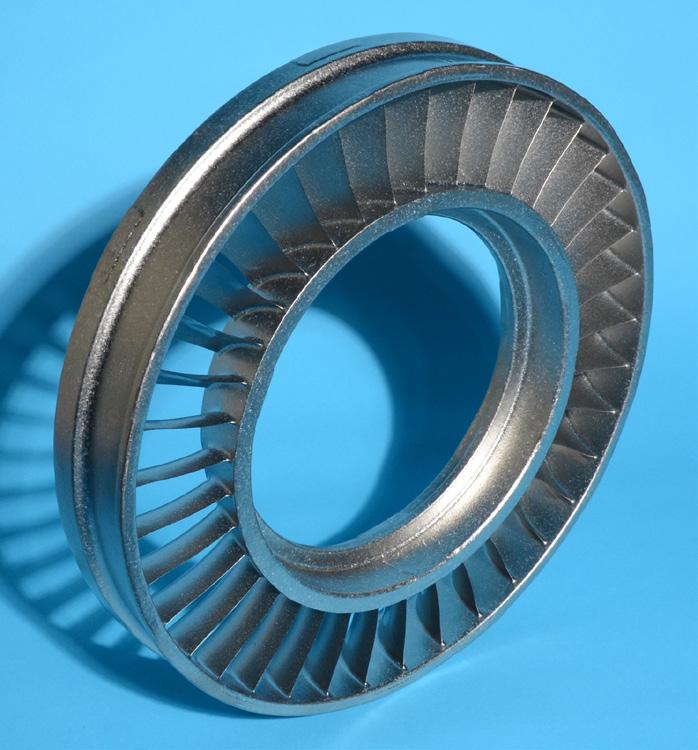
Aerospace Titanium Investment Casting
with enhanced strength, temperature resistance, oxidation resistance and weight savings. For example, Mueller pointed to casting titanium aluminides for low-pressure turbine blades used in jet engines. Titanium aluminides yield significant weight savings and high performance compared with nickel-based superalloys for this application. Titanium alloys such as Ti-6242 (Ti6Al-2Sn-4Zr-2Mo-Si), a near-alpha alloy, and Ti-15333 (Ti-15V-3Cr-3Sn3Al), a beta alloy, offer high strength and corrosion resistance properties at elevated, in-service performance temperatures up to 1000°F/540°C, according to technical information posted online.
Five Years Ahead
Regarding the evolution of the titanium casting process during the next five years, Mueller sees a continuation of manufacturing technology elements already in place. He expects the process to be more engineering intensive, designing complex integral cast components, which previously would have been composed of a number of elements welded or joined together. There will be more widespread use of process modeling and process simulation to optimize part configurations and compress the time to design and produce parts. As for expanded business opportunities, aerospace will remain a dominant market for titanium casting, with growth opportunities emerging in the entrepreneurial, commercial space market (Space X and Blue Origin) as well as the oil and gas industry.

Aerospace Titanium Investment Casting
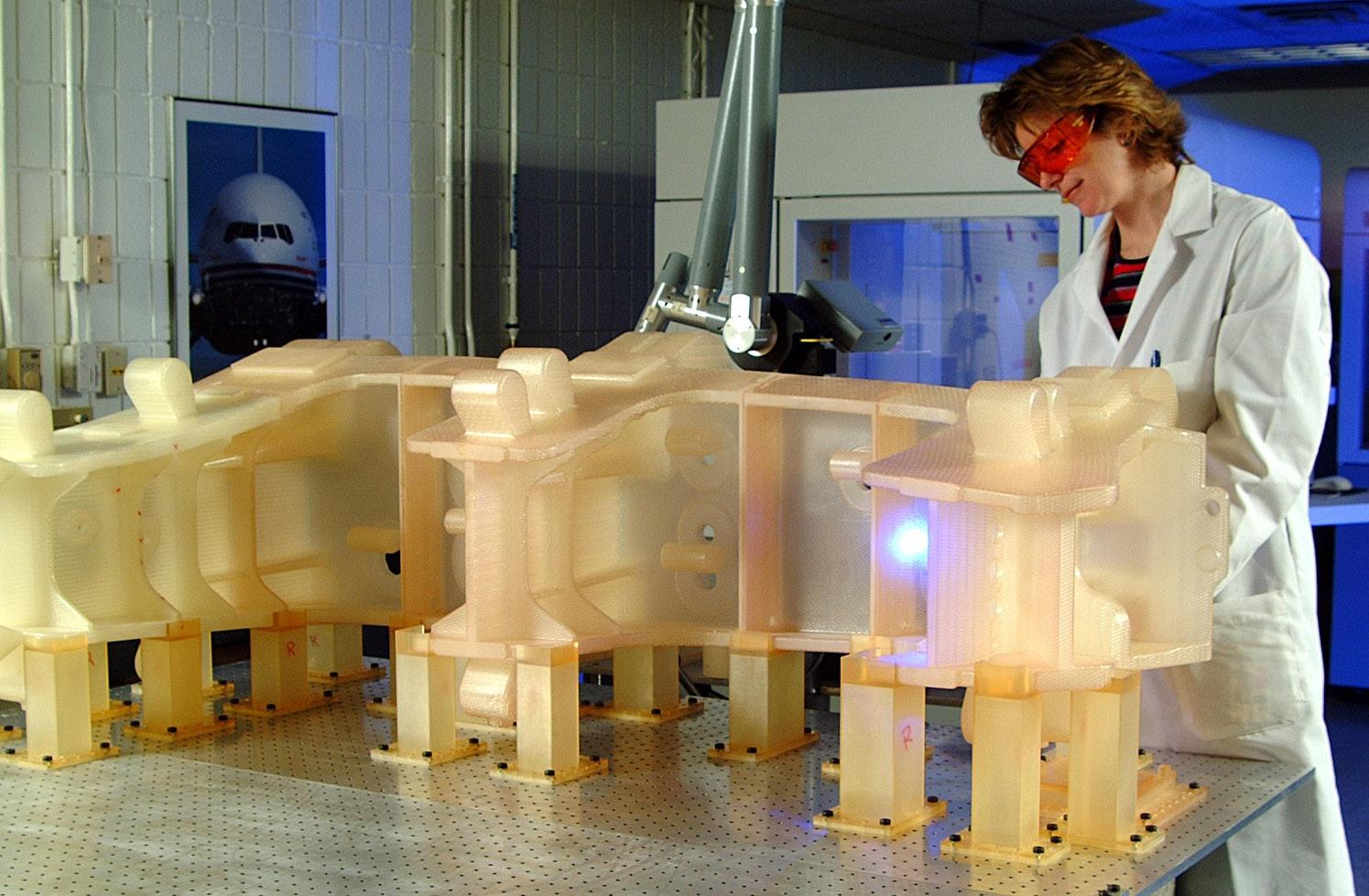
Stereolithography Pattern for Titanium Investment Casting
[The following company overview was provided by Howmet.]
Howmet Ti-Cast, located in Whitehall, MI, serves the commercial and military aerospace industries and the medical industry. The TiCast operation, drawing from the rapid prototyping capabilities of the nearby Howmet Technical Center, is a modern facility of approximately 48,000 square feet of manufacturing space, housing modern equipment, and the staff of technical and production experts necessary for making high-quality products.
Howmet’ s Structural Casting Operation is a leader in the production of large superalloy and titanium aerospace structural components for the aero-engine, airframe and rocket industries. The Structural Casting Operations center has been located in Hampton, Virginia, since 1981, where it occupies more than 113,000 square feet of manufacturing space.
Howmet Ti-Ingot, a 58,000-square-foot operation also located in Whitehall and part of Howmet’s Specialty Products Group, is a producer of standard, double- and triple-melt, rotating grade titanium ingots. Ti-Ingot manufactures products for the commercial and military aerospace, chemical-processing, medical implant and recreational industries. Ti-Ingot provides multiple benefits for customers such as the ability to toll melt permits maximum recycling of titanium scrap for a more cost-effective ingot.
The Howmet Research Corp. supports the worldwide activities of the Howmet Engines through materials and process research and development, manufacturing technology and various engineering and laboratory services. Materials and process research and development activities within the corporate technology laboratories address both near-term production needs of the manufacturing operations and Howmet’s strategic plans to maintain its technological leadership. The work is funded internally and by contracts with customers and the U.S. government. Established in 1973 and located in the Operhall Research Center in Whitehall, the facility occupies 100,000 square feet.
Howmet Aerospace Inc., headquartered in Pittsburgh, is a leading global provider of advanced engineered solutions for the aerospace and transportation industries and recognized as a global leader in the field of titanium casting. Howmet was formed in April 2020 when it separated from Arconic, Inc.