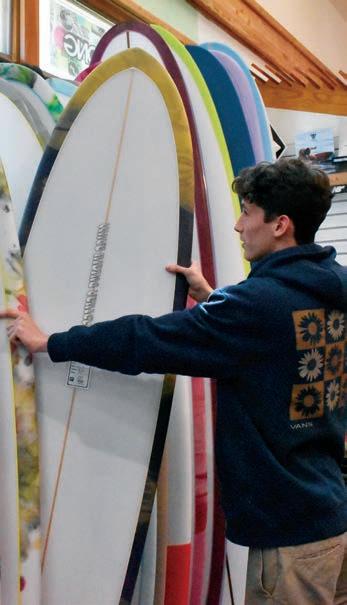
7 minute read
WRV: Shaping surfboards to ride the waves
by Danielle Puleo
The Outer Banks has become a highly sought-after destination for surfers, providing perhaps the best surfing waves on the east coast. The sport has gained extreme interest from athletes around the world, now having reached an Olympic level. So, what is the most important factor while riding the waves? What takes a surfer to the next level? Most would agree it’s the vehicle by which a surfer transports themselves across the water.
Situated in Kitty Hawk is a surf shop that has gained national, even international, recognition: Wave Riding Vehicles (WRV). Founded in 1967, WRV began as a surfboard manufacturing company out of Virginia Beach. Current WRV Kitty Hawk general manager Chris Williams said that the initial goal was to get high quality surfboards into the hands of east coast surfers.
“It all started in the Virginia Beach area, which is where the company was born,” Williams said. “Naturally, the Outer Banks is a regular pilgrimage for the traveling surfer that wants to surf the best waves and the best conditions. People were driving down to OBX since day one looking for the best waves.” After the company got its feet off the ground, it opened the doors of a second location in The Dune Shops complex in the early 1980s. Once surfing gained more popularity and the culture grew, there was need for more space, so WRV moved to its current location on N. Croatan Highway in Kitty Hawk.
WRV was originally founded by the Morris and Snyder families. The company changed hands when it was bought out by Les Shaw and Bill Frierson. The partnership lasted a few years, Shaw focusing on the business side of the company and Frierson interested in shaping the boards. Shaw bought Frierson out in the early 1990s; Frierson still shapes under his own label, and the Shaw family owns the company to this day. L.G. Shaw, son of Les, is the president of WRV.
The label has come a long way since the ’60s, from a small board-making shop to becoming one of the largest surfboard manufacturers on the east coast. The brand has opened locations in both Hawaii and Puerto Rico, with a dealer list that spans from Maine all the way down to Florida.
The Coastland Times spent time at both the Kitty Hawk storefront and the board-making factory just over the bridge in Currituck and spoke with Williams and WRV factory director Leigh Ann Britton to learn more about the surfboard-making process.
The surfboard starts out as a “blank,” a large surfboard-shaped canvas made out of high density polyurethane foam. A shaper will design the board; he will draw on the deck (the top portion) of the surfboard to

Danielle Puleo photo
Left: Ayden Painter sifts through a rack of fi nished surfboards waiting for new owners at the storefront in Kitty Hawk Right: Leigh Ann Britton, WRV factory director, and Chris Williams, general manager of WRV Kitty Hawk.
create the shape that the board will take on. The shapes vary and are dependent upon the use of the board, along with factors such as a person’s bodyweight, height, ability, etc.
Once the shape is drawn, the board is placed in the laminating room where the deck receives two layers of fiberglass cloth and one layer is sealed on the bottom, forming a hard candy shell on both sides.
The board will then travel to the hot coating department, where a sanding resin is brushed on both sides of the board to make the board “sandable.” “If you sand it right after it is laminated, it will splinter because it’s really hard,” explained Britton.
Next, a sander will use a hand-held machine sander to smooth the board and grind down the fin boxes. The board then travels to the buffing room, affectionately known as the “mud room,” where the surfboard is brushed with a liquid similar to car wax that buffs the board and gives it that shiny sheen. Each room is filled with bright white lights so factory workers can clearly see what they are working on.
“Everything is a process and it could take hours at each stage,” said Britton. “We have cards on each board for all the locations they will go to,” she added. WRV receives many custom requests, along with orders from the thirty dealers they distribute to. It is crucial that each board gets to exactly where it needs to go.
Britton and Williams then walked into a room with surfboards that were about to receive their final touches. Britton pointed to a custom board designed by Marty Keesecker, a long-time shaper who started with the company when it was born. In 1970, Keesecker and another shaper, Bob White, designed a board called the “Real McCoy.” “They came up with the model then and are now recreating it,” Britton said as she looked at the impressive piece. “They’re doing a limited series.”
Shapers like Keesecker have been in the business a long time, crafting boards that retail for thousands of dollars due to their complexity and the high level of detail. “He hand-chisels the wood,” remarked Britton of Keesecker. “He takes mahogany specialty wood (knows as a “tailblock”) and glues the pieces together and puts them on the end of the board. He’s a master shaper.” This tailblock is also used on some of WRV’s classic boards.
Keesecker, along with Bob Yinger, Jordan Brazie, Mike Doyle, Rob Kamp, Makoto Kurihara, Pat Mulhern, Bill Foote and Mike Clark, all shape surfboards for the company currently.
Each surfboard meets many hands before it makes its way home. The board-making process is extremely labor-intensive and, unlike factories that churn out hundreds of products simultaneously, WRV surfboards are crafted one at a time. “That’s why surfboards cost what they cost,” said Williams, “all these guys are a part of the process to make the surfboards, and it’s all local too.”
The WRV factory can churn out anywhere from forty to eighty surfboards a week, depending on the nature of the boards ordered. “We build A-Z, short boards to long boards,” Britton noted. The boards can be anywhere from 5’2” to 11’ in length. A surfer’s chosen board should
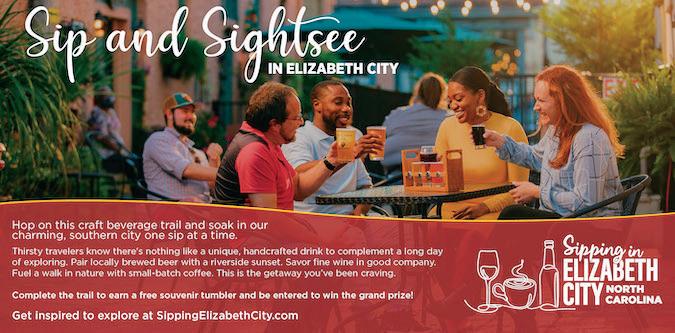
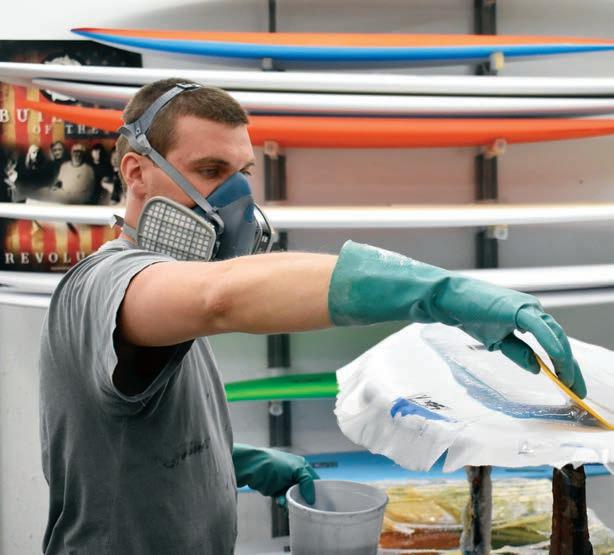
Danielle Puleo photo
Jeremy McMahon laminating the deck of a surfboard to form the hard candy shell.
match the conditions they will be riding in, but boards are designed to accommodate a rider’s height and weight in tandem with the subjected conditions. “It’s sort of like having golf clubs,” explained Williams, “just like you have a club for a specific shot, you have specific boards to fit where you’re going, your height and weight and ability.”
Williams spends most of his time at the shop, guiding customers to a board that would best suit their needs. He started with the company in 2017 after living and working up and down the east coast and spending time traveling. “Anytime there were waves, I would surf,” he said. Whether it be in New Hampshire, Rhode Island, California or Spain, Williams has always seen a WRV surfboard in the water.
“It was a shock to me having been born and raised in Virginia Beach,” Williams said. “I didn’t realize that their reach was so far.”
Outside of surfboards, WRV has created its own brand. Since surf fashion blew up, WRV has been quick to ride with the trends, selling their own apparel, surfing gear, accessories and even skateboards. Outer Banks locals and visitors can stop in the shop and be instantly immersed in the surfing culture. And if individuals are looking to build their own surfboards, they can purchase the necessary materials right from WRV.
The brand continues to gain recognition as customers sport the WRV logo wherever they go. “We are definitely a nationwide brand, but I feel like I can now say it’s a worldwide brand as well,” Williams stated.
To find out more, visit the WRV website at www.waveridingvehicles.com.
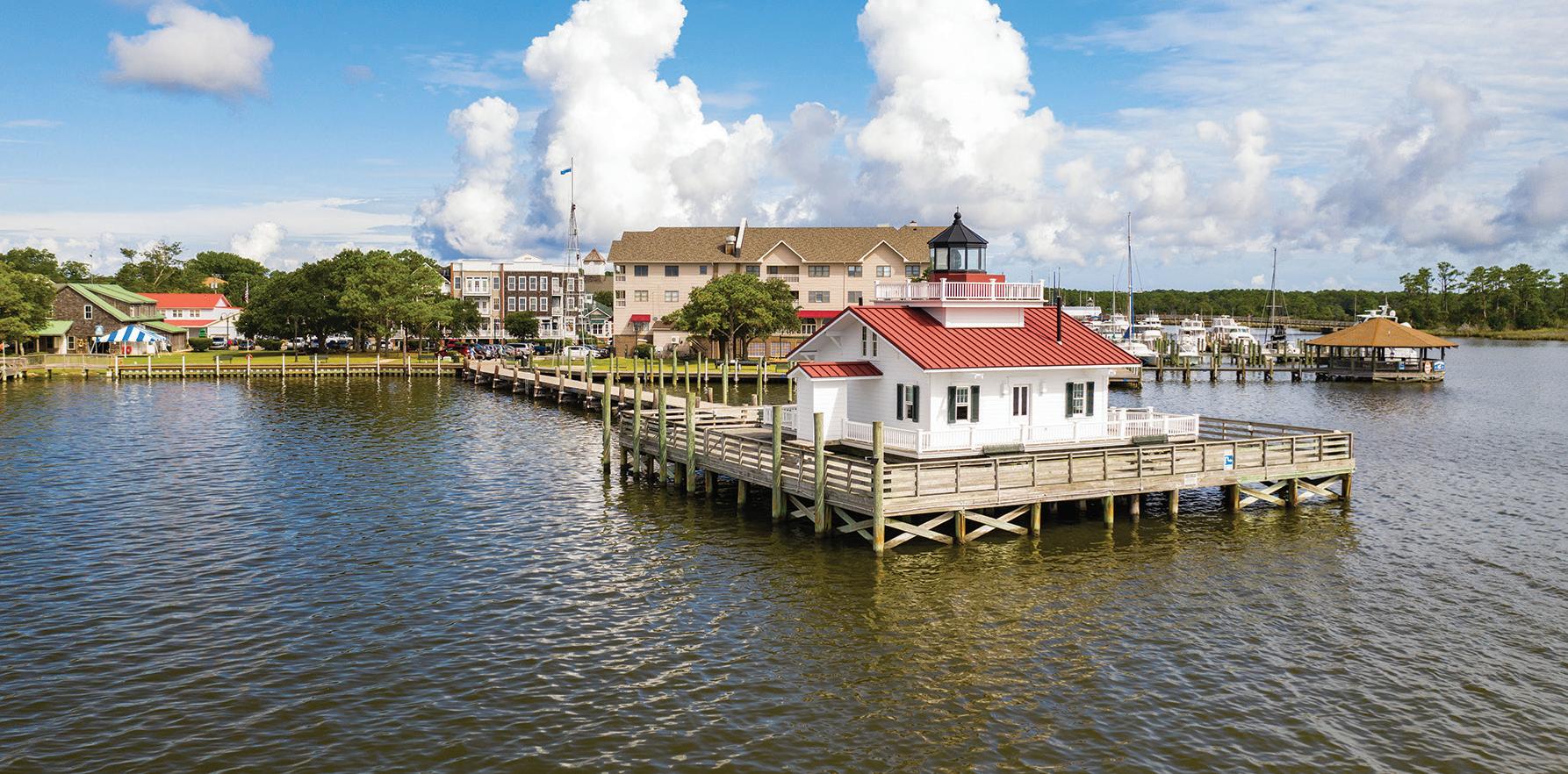
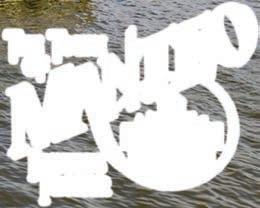
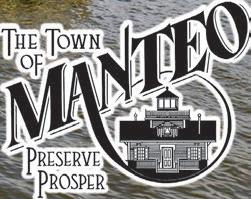
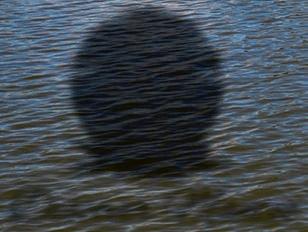
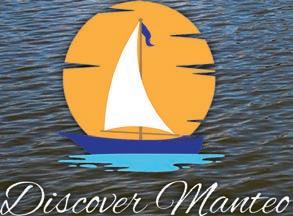
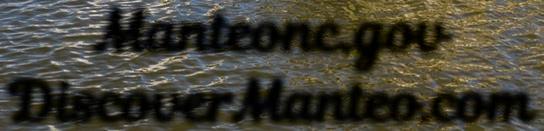