
7 minute read
Waterside Weaver: From sheep to chic
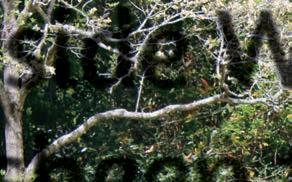
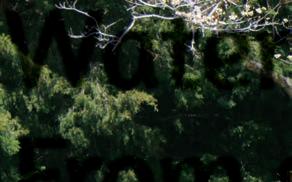
Summer Stevens photo
The sheep grazing at Island Farm
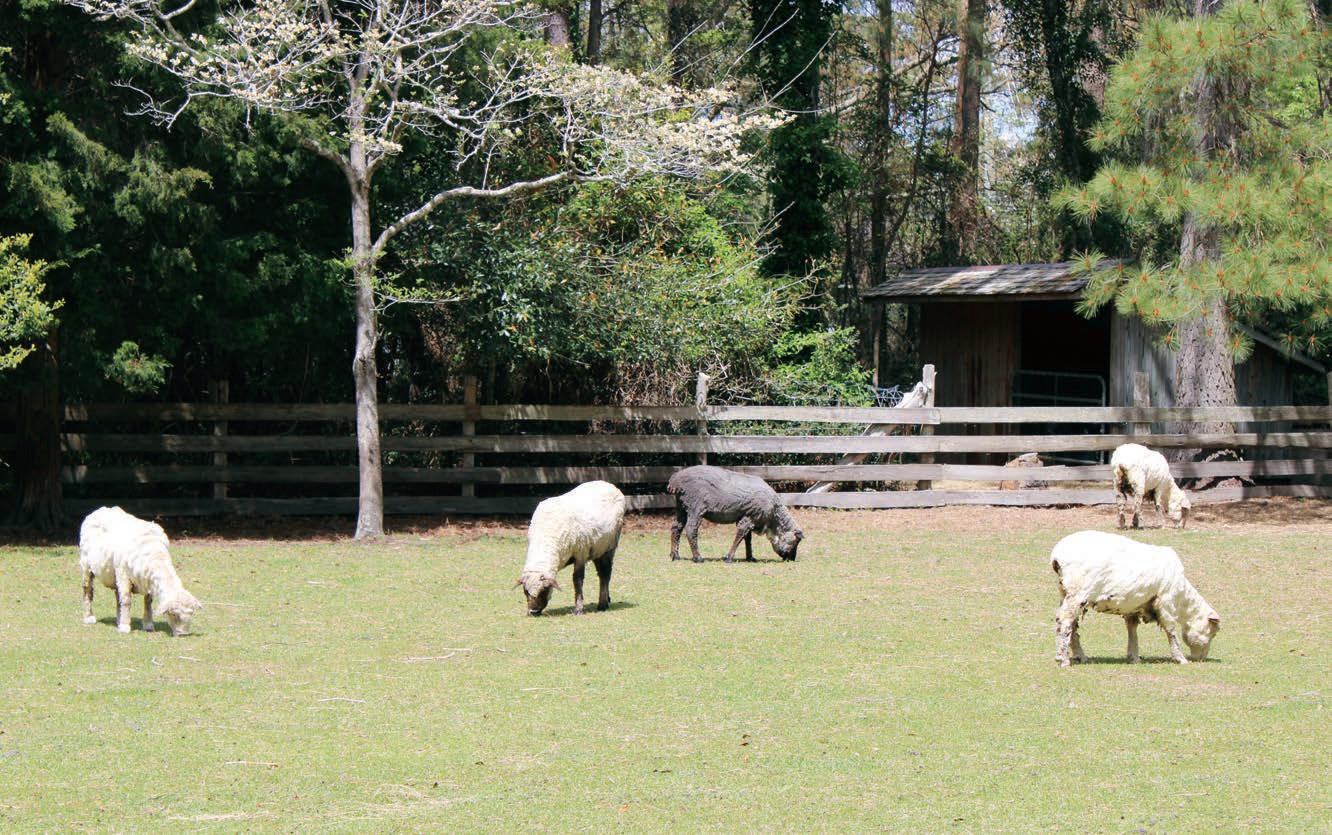
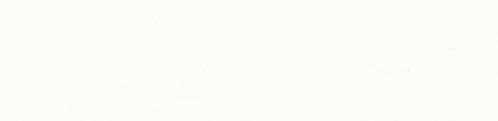
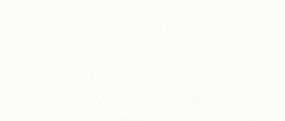
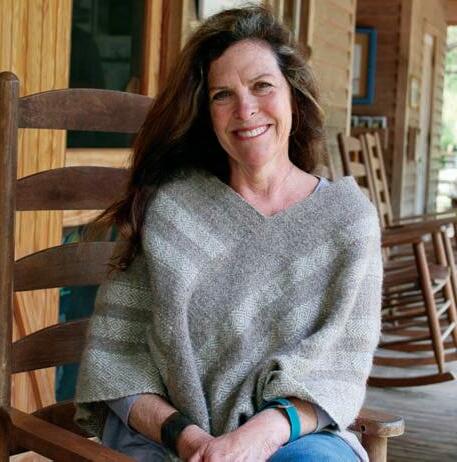
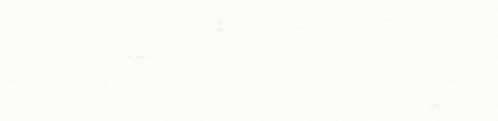
Summer Stevens photo
Waterside Weaver Beth Burns models a handwoven, handspun wool wrap on the front porch of the welcome center at Island Farm, where her small fl ock of sheep graze nearby.
On Roanoke Island, there lives a little flock of sheep at Island Farm. Most visitors would think that the sheep are the property of the farm, to serve as a picturesque backdrop of what life might have looked like in the 19th century. However, the sheep belong to Beth Burns of Waterside Weaver, who uses the wool to create handspun and handwoven shawls, wraps, blankets and more.
Her fabric arts process isn’t that different from the traditional methods families have been using for hundreds of years.
The raw wool is gathered and washed, and then begins carding – a process of combing the wool so all the fibers are in the same direction – using two wooden paddles that resemble wire dog brushes.
With the wool smoothed and detangled, it can be spun into yarn using a spinning wheel or a top whorl drop spindle.
Though Burns does send some of the wool to be commercially spun, “I like spinning it myself,” she said. “It gives you some diversity in the yarn.” Island Farm has a fully operational antique spinning wheel that Burns and others use. On Sheep Shearing Day, visitors to the farm practiced carding the wool while Island Farm volunteers demonstrated how it was spun it into yarn on the wheel.
After the raw wool has been turned into yarn, then it must be woven into fabric using a loom. There are two looms at Island Farm
by Summer Stevens
– one large “barn loom” that is housed in the welcome center and another one in the farmhouse. Burns owns them both, as well as another loom she keeps at home.
The barn loom is the showpiece of the visitor’s center. According to Burns, it came from West Virginia and is engineered according to the German style. When beginning a project, the first step is “beaming it” – or putting all the threads on the loom as wide and long as you want your fabric. How many “ends” per inch depends on the delicacy of the project. Weaving rags might be six ends per inch, whereas a finer project might use 40 ends per inch.
The harness is the frame of the loom that holds the threads. A standard loom starts with two harnesses and can create a plain weave; but more harnesses mean more complex patterns that can be created. For Burns, “I can pretty much do anything I want to do with eight.” The harnesses are controlled with foot pedals called treadles.
To this writer’s surprise, Burns sat down at the loom and began adjusting it, stepping on the treadles, and weaving with all the gentleness of opening a jar of pickles. Though the machine looks delicate, it’s a fully functioning working piece of equipment, and Burns is clearly comfortable putting it to use. “I’ve put this one together and taken it apart so many times,” she said.

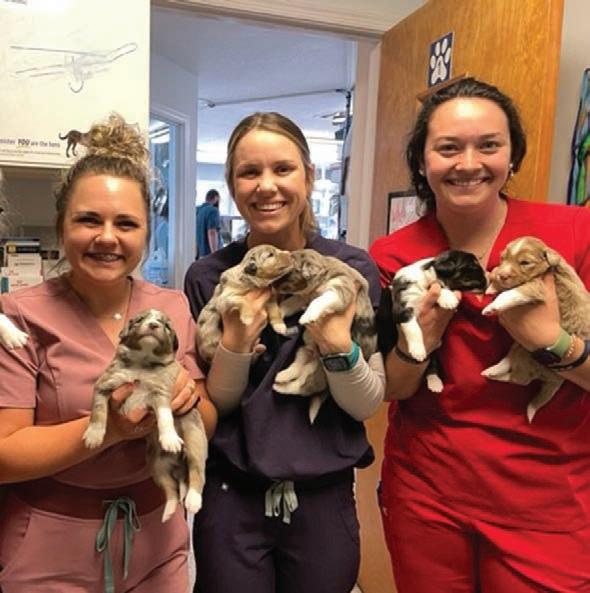
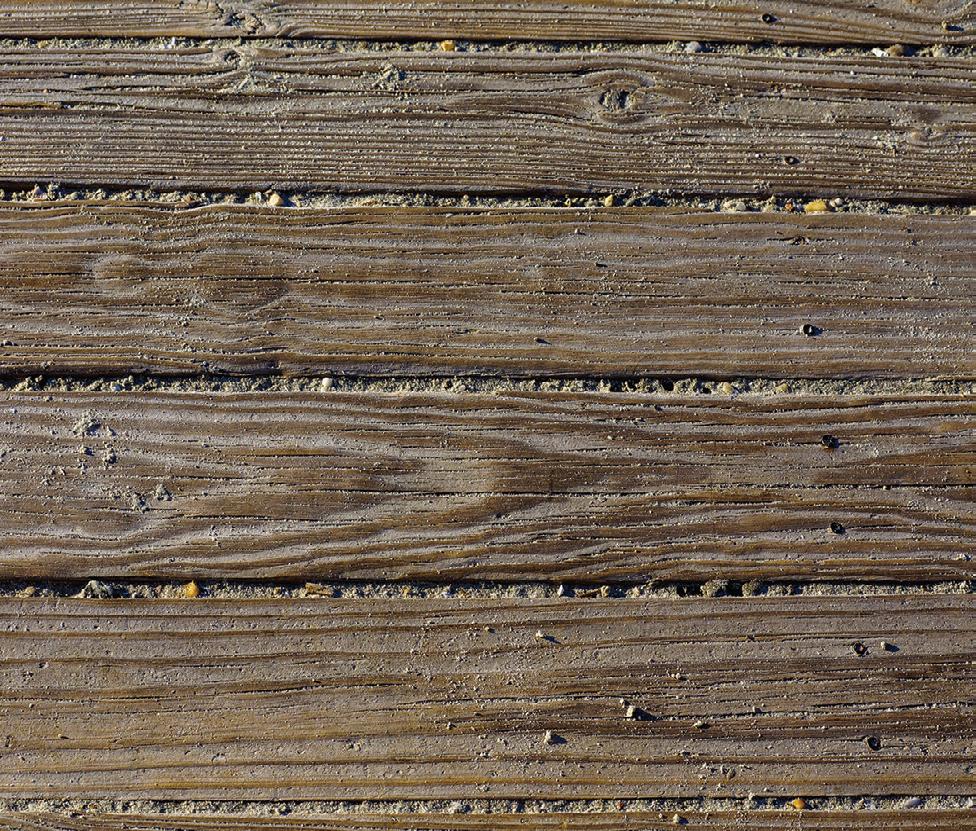
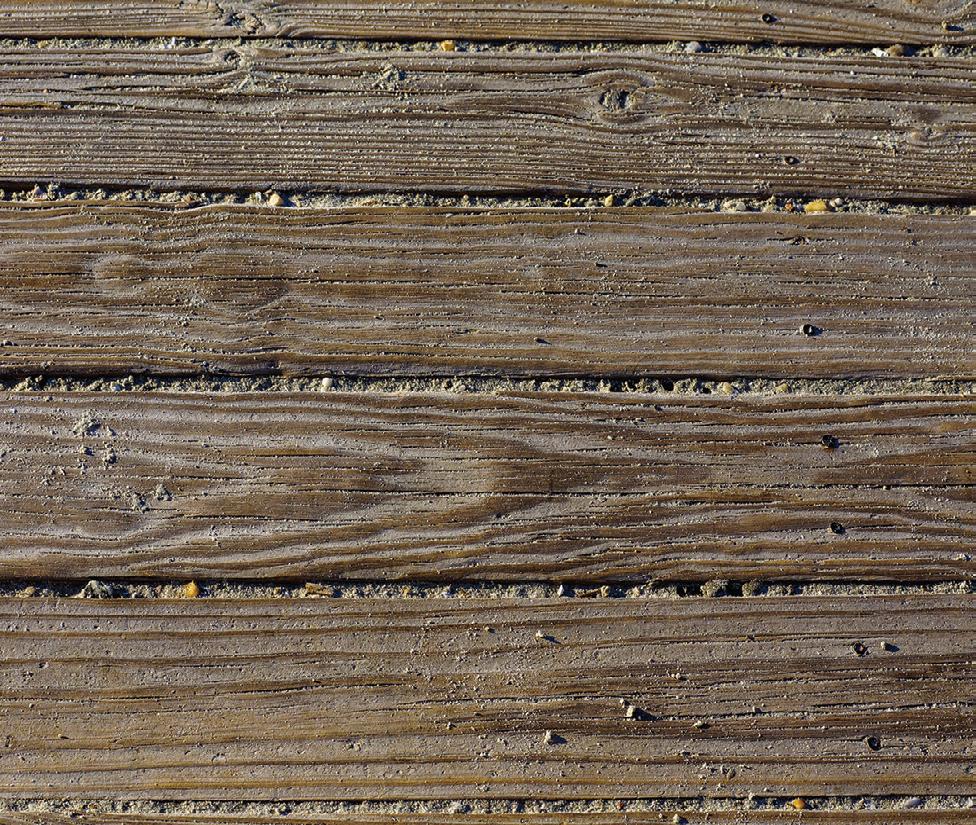
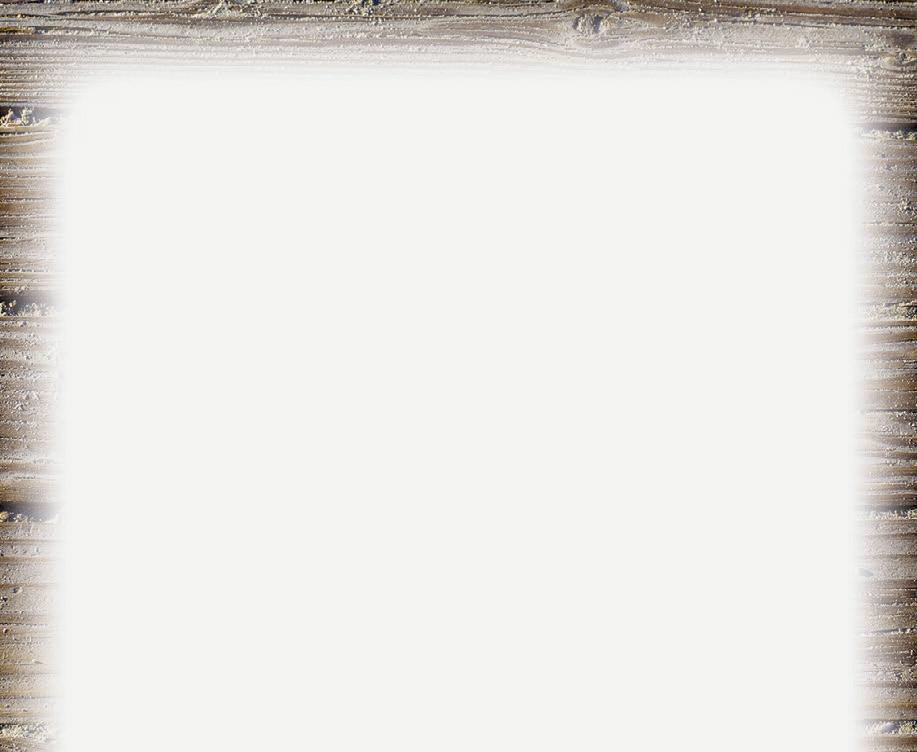
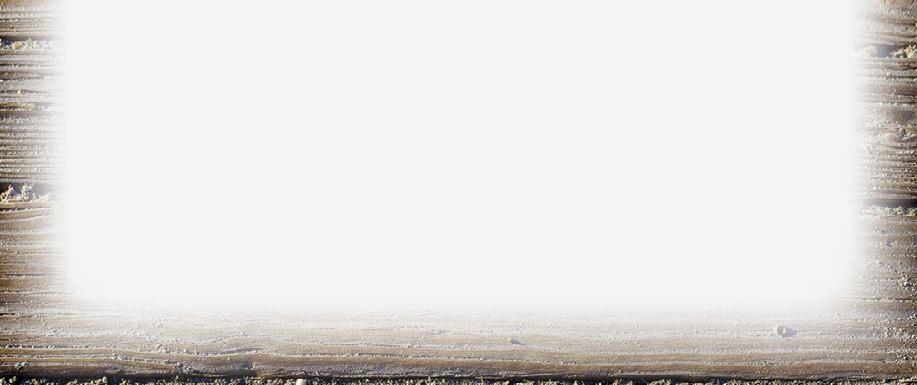
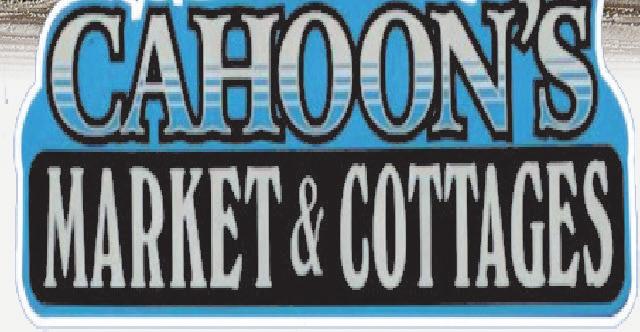

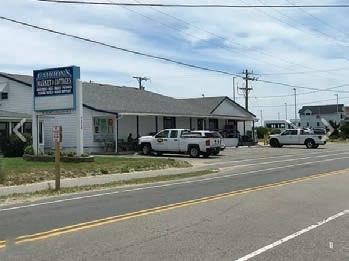

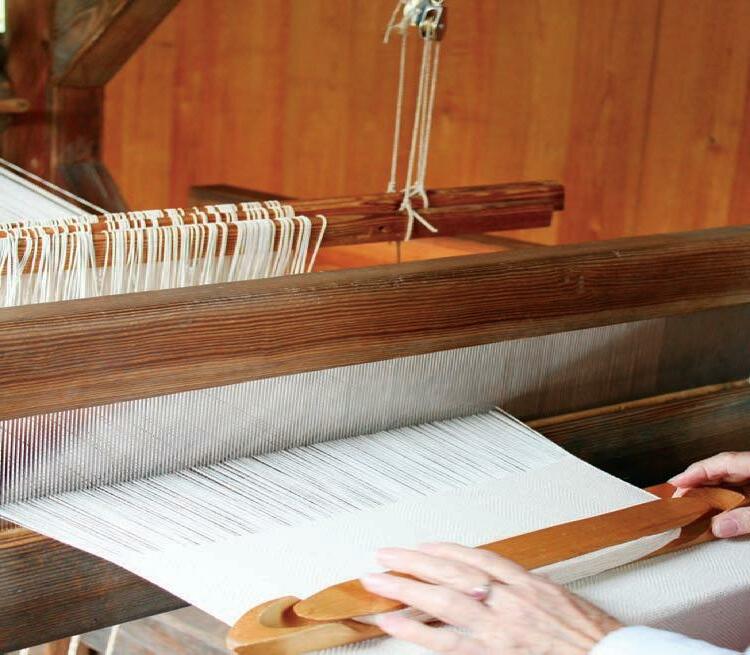
Summer Stevens photo
Left: Island Farm volunteer Inger pressing the treadles of the loom. Right: At work on the loom in the upstairs bedroom of the Island Farm farmhouse.
Historically, barn looms were assembled and disassembled frequently. Because of their size, they were often set up on the front porch in temperate weather. It’s easy to imagine the scene 100 years ago – a mother running the loom while she watches her children play in the yard on a warm spring day.
Though the process isn’t complicated once you get the hang of it, it is time consuming. Weaving a simple cotton dishtowel can take Burns all day, so it’s easy to understand why they retail for $60 at market.
As the years go by, that dishtowel will outwork its store-bought companions and end up paying for itself. “Some of my friends have had them for 25 years,” Burns said, “and they keep getting softer the more often they’re washed.”
She sells the dishtowels because they’re so popular and relatively easy to make, though her spotlight items are the shawls and wraps she makes directly from her little flock of sheep.
“It’s a sickness,” she laughed. “You kind of have to do the whole thing,” she said of her unique participation in creating fabric arts from the first step of raising baby lambs to the commencement of direct-selling her wares.
She owns eight sheep, all pastured at Island Farm, and once a year they are hand sheared by Frederick Inglis of Somerset Farm near Edenton. One sheep can yield about 10 to 15 pounds of fleece. When Burns does send out the raw wool to be commercially processed and spun into yarn to a small facility in Vermont, there is a 100-pound minimum for each type of wool. “It takes me ten years to get enough,” she said. She was able to reach that threshold this year after the April sheep shearing, and she expects the wool may last her the rest of her weaving days.
For her signature handwovens, Burns primarily makes naturally-colored throw blankets, shawls and wraps using wool from her own tiny flock of Romney and Merino sheep. She modeled a wrap while sitting in one of the rocking chairs on the front porch of the Island Farm welcome’s center, and one can instantly see the artistry in not only the material, but in the elegance of the pattern. The wrap rests on the edge of the shoulders, making a V and touching just past the hips.
Though she used to place her items at various galleries, she now sells them directly at Secotan Market in Wanchese, or through her website at watersideweaver.com. She has a
large following of clients and sells everything she makes.
Purchasing a Waterside Weaver item is a financial investment, but the price probably barely covers Burns’ expenses, not to mention her time.
“It’s not really a money-making thing,” she said simply.
When she first learned to weave 26 years ago, she was reeling from the personal loss. “I was planning on getting married and it all fell apart. I was heartbroken, so I poured myself into it. It was really good timing.” She took a weaving class at Pocosin Arts in Columbia, and a couple years later bought the first of her animals in her flock.
When she retired as a biologist for the state ten years ago, she increased her flock and started spending more time on her artwork.
Beyond the wool items, Burns also uses a variety of other materials that are more suited for the balmy Outer Banks weather like silk eco-print or eco-dyed scarves, using native plants or flowers and natural dyes.
She makes stunning Tencel scarves by hand painting and hand weaving superfine Tencel yarn in shades of deep greens, blues and turquoise. One scarf takes weeks to create, but the final product is a piece of wearable art.
Find Beth Burns and a photo gallery of her work at watersideweaver.com.
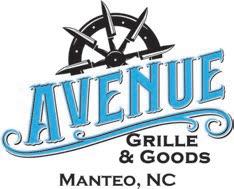
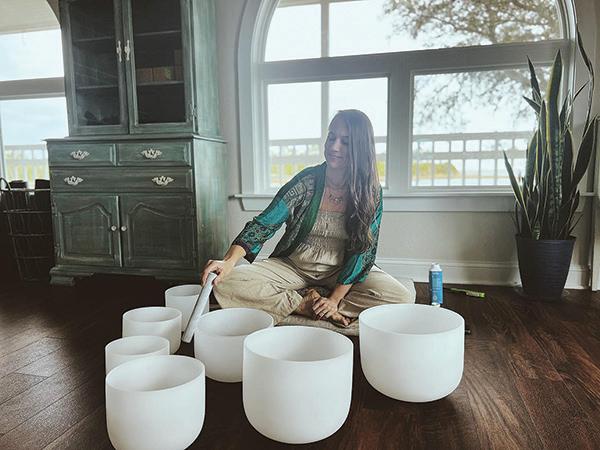
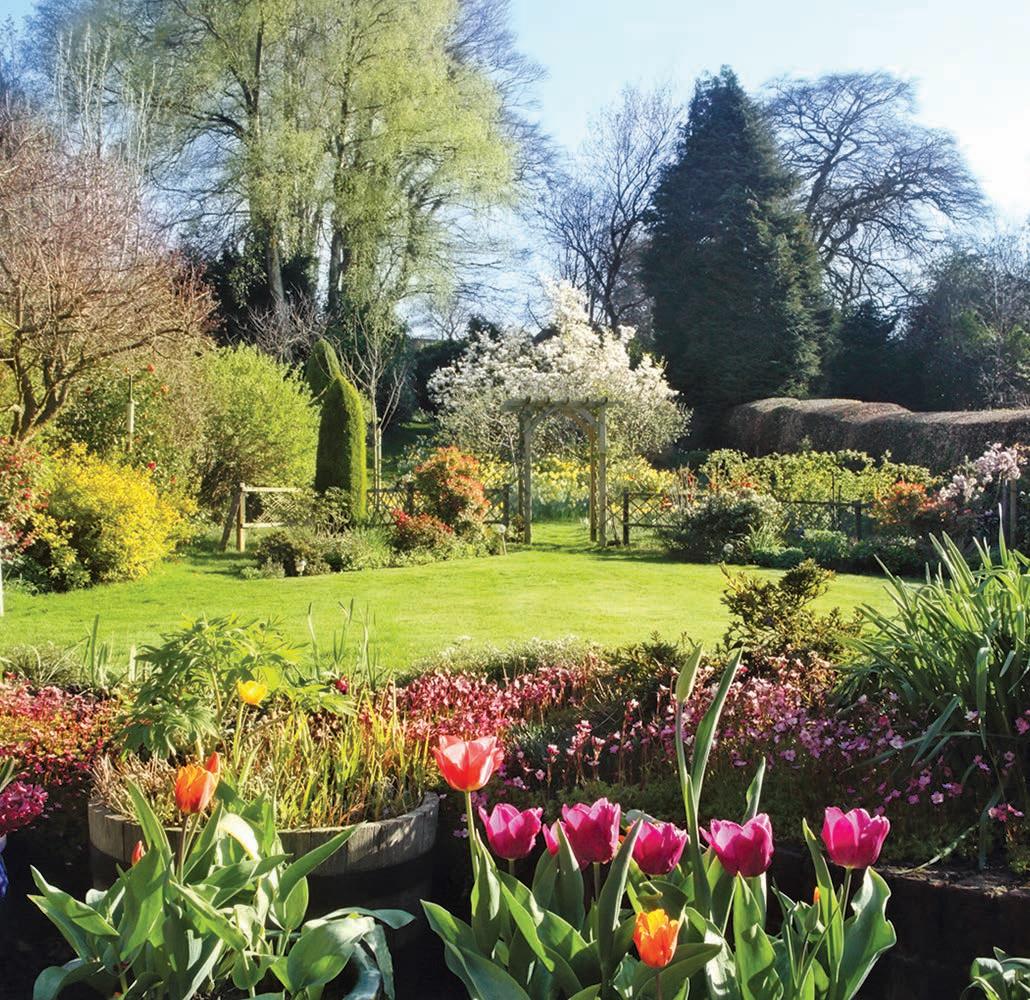
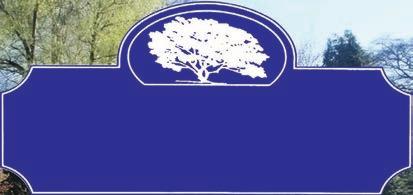
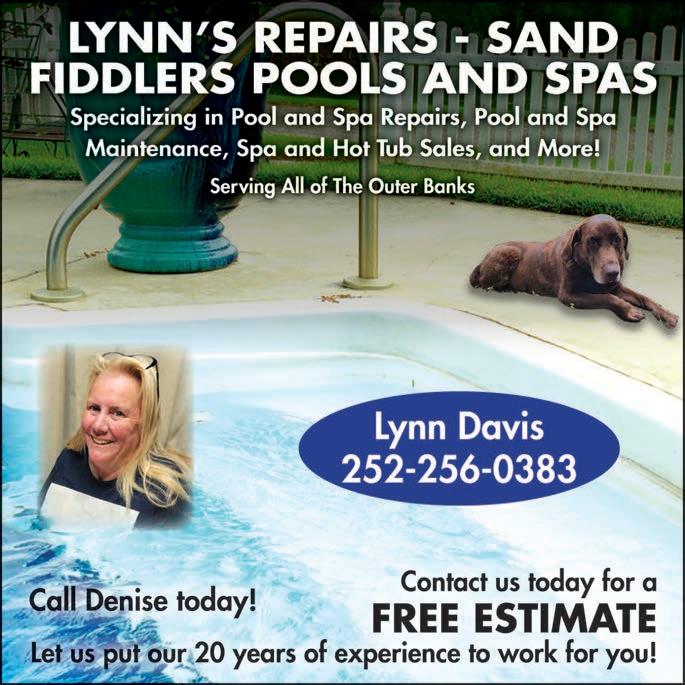