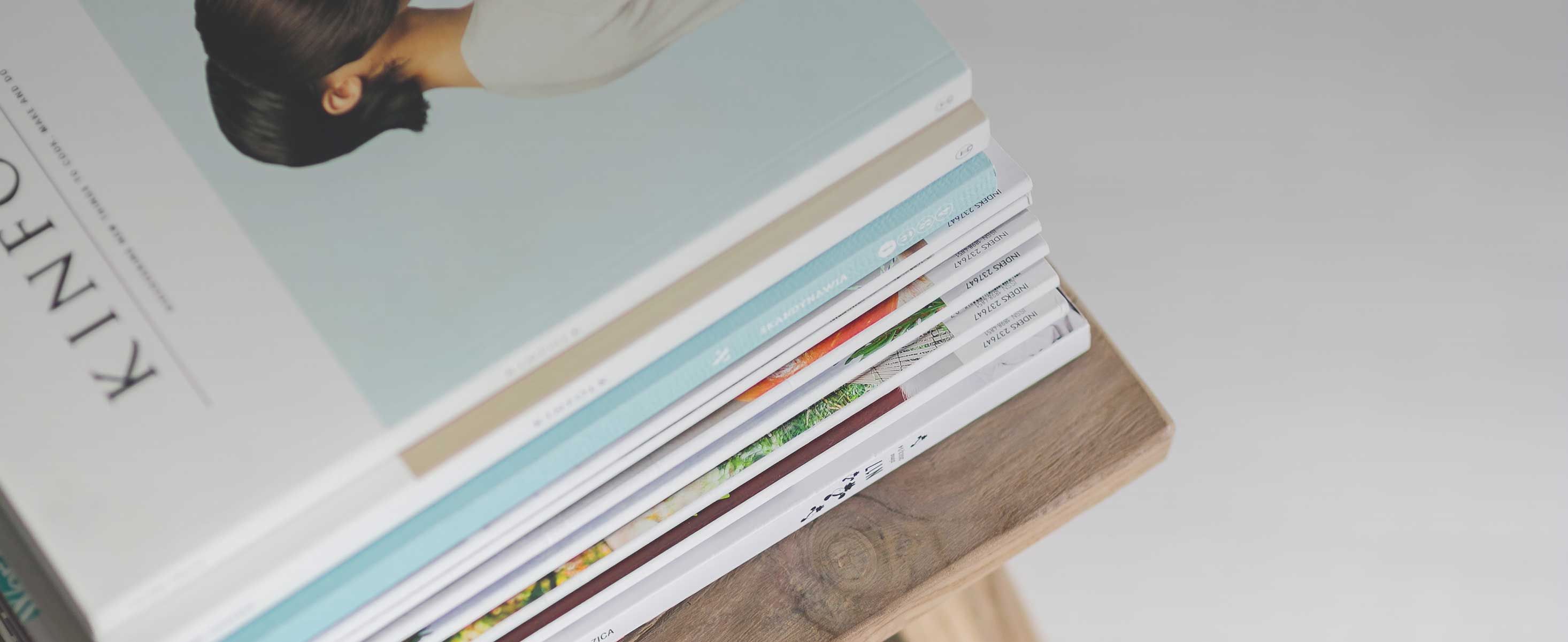
6 minute read
JSP KEEPS CALM AND CARRIES ON PROTECTING
JSP has kept industrial and construction workers safe for decades, but when the pandemic struck, Europe’s leading independent manufacturer of “above-neck” PPE was deployed to help the NHS
By Nicky Godding, Editor
Where’s the most unlikely place to put a factory? A pretty former woollen mill on a stunning Cotswold river half a mile from the main road? Welcome to the head office of manufacturer JSP at Minster Lovell near Witney, and the company says there’s no better place to be.
Inside the mill, which straddles the River Windrush where trout swim and peacocks strut around the car park, JSP has been designing and manufacturing essential industrial safety equipment such as protective safety helmets, goggles and facemasks since 1969.
The company was founded in London in 1964 by Clive Johnstone who moved it to the Cotswolds a few years later But with all the upheavals of the last few years, his son Mark, who has been Chief Executive since 2006, says that it’s the perfect location. “Being close to nature gives us all a good vibe.”
JSP has other manufacturing facilities at nearby Standlake Industrial Estate, at Carterton South Industrial Estate and a distribution facility at Witney Bromag Industrial Estate. Outside the UK, there are significant manufacturing facilities in Dusseldorf, Germany, China, the UAE and USA as well as sales and marketing offices in France, Spain, Poland and the USA.
But Minster Lovell is where the company’s research and development is carried out –in its innovation centre which now takes up almost an entire floor of the mill.
JSP’s mission is to improve the safety, health and wellbeing of people in their workplaces. It is now a global brand turning over more than £92 million last year (up more around 21 per cent on the previous year) and employing more than 460 people worldwide, including just over 300 in Oxfordshire.
This impressive growth has been despite pretty much everything but the kitchen sink being thrown at British manufacturers over the last six years. The uncertainty of Brexit, Covid-19 (still causing supply chain r chaos) and more recently the Ukraine war sending energy prices rocketing.
JSP makes above-the-neck innovative personal protective equipment – that’s everything from facemasks to ear defenders, safety helmets and eye and face protection. It also has a traffic management equipment business making barriers and cones.
While Mark says JSP’s biggest challenge over the last few years has been tackling Brexit – and we will come back to that, our conversation keeps returning to the challenges he and his team faced during Covid.
The Covid dash for PPE
In March 2020, one of the biggest challenges for the government was to secure enough personal protective equipment for the NHS – so it contacted JSP along with every other UK company which popped up when civil servants googled “PPE”.
“They asked for all our stock and all our production, and while it was a massive national panic in the early weeks, we did tool up and increased production,” said Mark.
To meet demand, and with support from HSBC bank, JSP invested £20 million in machines and £10 million into inventory.
However, hard decisions had to be made. “We had a lot of people wanting stock. But we decided to honour our commitments to current customers first (who needed the face masks and other protection just as much as anyone else) and committed to supply them with up to 15 per cent more than their previous average order rates.”
Some other companies might have sold all their stock to the highest bidders, but the JSP team held their nerve. “We focused on supplying the industrial market, and that enabled us to manage our stock with full supply up to the end of May, later than anyone else,” said Mark. “At the same time, we knew we had to respond to the NHS crisis.”
Mark began working with Oxford University Hospitals. “I told them what respiratory protection equipment we could make locally in the UK, and they told us what they needed. This included half-masks, full face masks, disposables and powered air respirators all made in the UK. We focused on our Force 10 full face mask and Force 8 half-mask fitted with JSP PressToCheckTM P3 filters which, with a thorough cleaning and maintenance programme, only needed changing every 28 days – much better for the environment and more importantly giving the wearer protection at a level multiple times higher than disposable masks.”
At the height of the pandemic, JSP was supplying 125 of the 220 UK NHS Trusts with a range of its safety equipment, either directly or indirectly.
It didn’t help that the company’s manufacturing facility in China went off-line for nine weeks, having been requisitioned by the Chinese government to make PPE for its citizens (which highlighted the vulnerability a company can experience from extended supply chains), or that Mark was masterminding all this having smashed his shoulder to smithereens in a skiing accident in early March.
“We also did what we’d never done before and set up a direct service to supply NHS workers with our PPE because they couldn’t get it anywhere else,” he added.
It was tough for everyone at JSP. “We were working ridiculous hours, and we wanted to be fair, offering the NHS a 30 per cent discount,” said Mark. “Others didn’t and we saw a fair amount of profiteering on the provision of sub-standard PPE equipment.”
Tackling Brexit head on
While the pandemic hit manufacturers with the force of a juggernaut, Mark says that Brexit has had a longer and bigger impact than Covid.
While the pandemic kicked off in March 2020, for the previous four years the company had been planning for Brexit.
“As a family business (Mark’s brother James is Operations Director and sister Sarah Baker is Head of Marketing), we have always paddled our own canoe, so in January 2017, following the July 2016 Brexit vote, I drove to Germany.
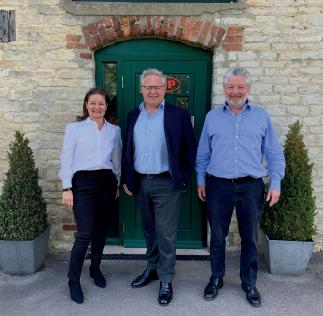
“Our EU customers were accounting for 45 per cent of our total business. As a lean manufacturer, it was a good evolution for us to make products closer to them - and with a Euro currency cost base. Also, we saw Brexit as a real threat which we had to try to turn into an opportunity. Germany made sense due to its legislation and a parallel in that “Made in Germany” is important to German companies like “UKmade” is in the UK, in fact probably even more so.
“We opened in Dusseldorf the following year and found that doors previously closed to us began to open, and those which were partially open widened. In 2022 we are now considered a European company in Europe. Before we were a British company operating in Europe. It’s an exciting time and we are seeing good growth from our platform there.”
JSP now services almost all continental customers out of its Dusseldorf facility.
Lean manufacturing and automation boosts productivity
JSP is a lean manufacturer, which means sourcing raw materials and components as close to its manufacturing facilities as possible, and for years it has embraced automation and robotics to enable more vertical integration and to boost productivity.
“Manufacturing close to our markets gives us more resilience to service our customers when supply chains are difficult – and enables us to tailor our products for a customer’s needs right up to the last minute. It also allows us to look at supply on a regional rather than global level which we have been doing for many years,” said Mark.
Other markets that continue to excite JSP include the Middle East and the USA –where it has sales offices and currently uses third-party manufacturers. However, it would like to build its own manufacturing facilities there in due course. With growing sales it hopes that could be soon.
A major ongoing investment for the company is research and development.
“We invest up to two per cent of turnover annually in R&D and have some exciting new products coming out later this year,” said Mark.
One of these, Sonis Comms, has just launched. This is a powerful new communication tool providing group intercom and active hearing protection in high-noise environments.
Using military-grade technology, embedded dynamic mesh creates a private network where anyone can talk together at any time. The new product, which helps boost productivity on site by up to 30 per cent, is proving of interest to companies in rail, airports, utilities and civil engineering on major infrastructure sites such as Hinkley Point in Bristol.
Another new product launching towards the end of the year is a climbing helmet for construction workers. JSP is combining the original industrial standard with the climbing standard which will give the wearer additional crown and side impact protection as well as being low profile for use in more confined spaces.
These new products build on other highly successful products launched by JSP over the last few years, including its Force8 half-mask with PressToCheckTM P3 filters which help the wearer ensure their face mask is fitted securely and provides a strong and secure seal. Over the last few years this has been a blockbuster product for the company, helping to improve the protection of people in the workplace by moving away from single-use respirators.
“In the UK alone, 12,000 people a year die from respiratory disease after exposure to airborne hazards in the workplace,” said Mark. “Covid highlighted a general need for effective respiratory protection but because of the frantic dash to obtain as much as possible as quickly as possible, a great deal of it was substandard and it is certainly not fit for purpose for industrial applications.
“There is a real need to get standards back up. Our mission is to improve the safety and health of people in their workplace worldwide, and everything we do is aimed at meeting that objective.”