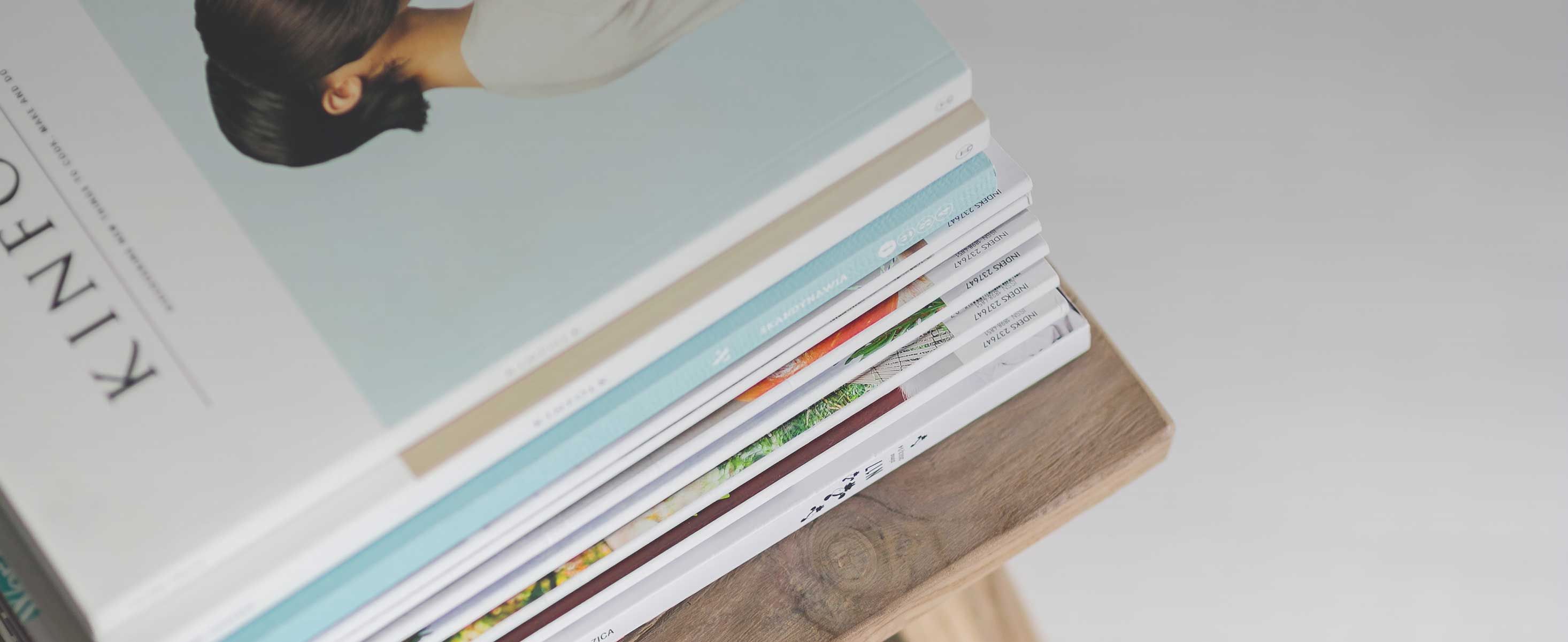
3 minute read
ROLLS ROYCE BACKING FOR BRISTOL AEROSPACE START-UP
A Bristol aerospace start-up which won support from the RAF, Rolls Royce and Martin Baker for its modular military jet, has secured £10.5 million in backing from a Middle Eastern wealth fund to develop the first fully British military jet since the 1970s.
The company is now gearing up to make a demonstrator version.
Aeralis was founded by Tristan Crawford to develop a new, all-UK developed jet trainer system. Tristan previously worked for Airbus, QinetiQ and Alcan Global Aerospace and Transportation, holding leading roles in aerospace engineering, product development and government relations.
He had the idea for Aeralis while working on the BAe Hawk jet trainer at QinetiQ, where he recognised that the jet trainer market wasn’t benefiting from the Airbus approach of exploiting modular design to better commercialise sales.
Tristan developed, designed and patented a modular, common aircraft that could easily be adapted to fulfil a variety of training roles.
Commercial aviation transitioned to modular systems some 25 years ago, but until Aeralis, air force systems had failed to follow suit.
From the 1990s onwards, commercial manufacturers have been exploiting modularity to create families of aircraft using shared manufacturing processes to build modular systems and parts. As a result, they have enjoyed efficiencies in research and development, while airlines have benefited from reduced costs in training, support, operations and maintenance.
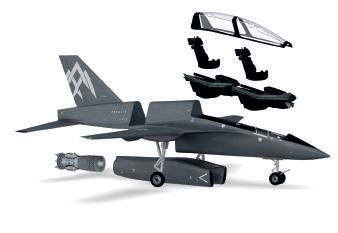
Military customers who transition to an Aeralis fleet are projected to save more than 30 per cent over ‘traditional’ mixed fleets, the company says.
Solid State buzzing as it wins £2.4M contract to help bee health and crop pollination
Redditch manufacturer Solid State has won a contract for its components division to supply hardware for Bee Hive monitoring to a US-based client to improve bee health and crop pollination. The contract has a project value of approximately £2.4 million.
The client, a USA-based precision pollination service, uses technology that ensures the pollination process lives up to farm standard quality every season. By monitoring hives, it produces stronger, healthier and more productive colonies, while lowering operational costs.
The sensors (which took Solid State three years to perfect) are placed in the middle of the hive, a range of data across various parameters is collected, and communications hardware sends this data to the Cloud. In this way, the client can detect concerning changes in hive behaviour which may indicate ill health or stress, or a change in hive conditions which threatens the bees’ wellbeing. The beekeepers are alerted and can rapidly address the issues, helping to reduce the mortality rate.
Solid State manufactures a range of computing, power, and communications products.
Diamorph invests £6 million in Gloucester composites facility
Advanced materials group Diamorph Group is investing £6 million to support manufacturing of composite materials and bearings at its Gloucester facility.
The facility, previously known as Permali before Diamorph acquired the company last year, now serves as Diamorph’s primary composites and polymer materials manufacturing site. Along with Permali, the facility will also soon house the brands Tenmat Composites and Railko and serve industries such as F1, defence, marine, aerospace and rail.
Diamorph plans to invest £6 million in developing a new fabrication centre. The site is also recruiting for more than 70 positions, including manufacturing operatives, lab technicians, quality inspectors, CNC managers, and warehouse and logistics supervisors.
Tony Beswick, managing director of the composites and polymer materials business, said: “Diamorph works on some really demanding projects, for example Permali supplies composite parts to all Formula 1 teams on the grid as well as applications on passenger airliners.”
Coventry’s Manufacturing Technology Centre team win innovation award
A team of engineers from the Manufacturing Technology Centre (MTC) in Coventry scooped a top innovation award for the development of a high-powered electric motor which is smaller and lighter thanks to advanced manufacturing technologies.
The MTC’s Future Electric Motor Systems aerospace motor project, known as FEMS3, won the 2022 3D Pioneers Challenge award, an international design competition for advanced manufacturing technologies.
The team redesigned an MTCdesigned motor casing for a lightweight aerospace application.
They used additive manufacturing technology to combine three machined components, eight fasteners and three o-rings into a single part.
The result was a motor which has a reduction in mass of more than 65 per cent, is much simpler to assemble and has eliminated multiple seals.
The team used high value design tools and manufacturing processes to redesign components in the rotor assembly, consolidating four parts made from three materials to be into a single component, further reducing weight and simplifying assembly.
In their comments the competition judges congratulated the team for leveraging the advantages of additive manufacturing.
Ollie Hartfield, MTC research engineer said, “Our motor showcases the potential of additive manufacturing and advanced design tools to manufacture high performance electric motors.”