DeepDrawnStamping:Benefitsand Limitations
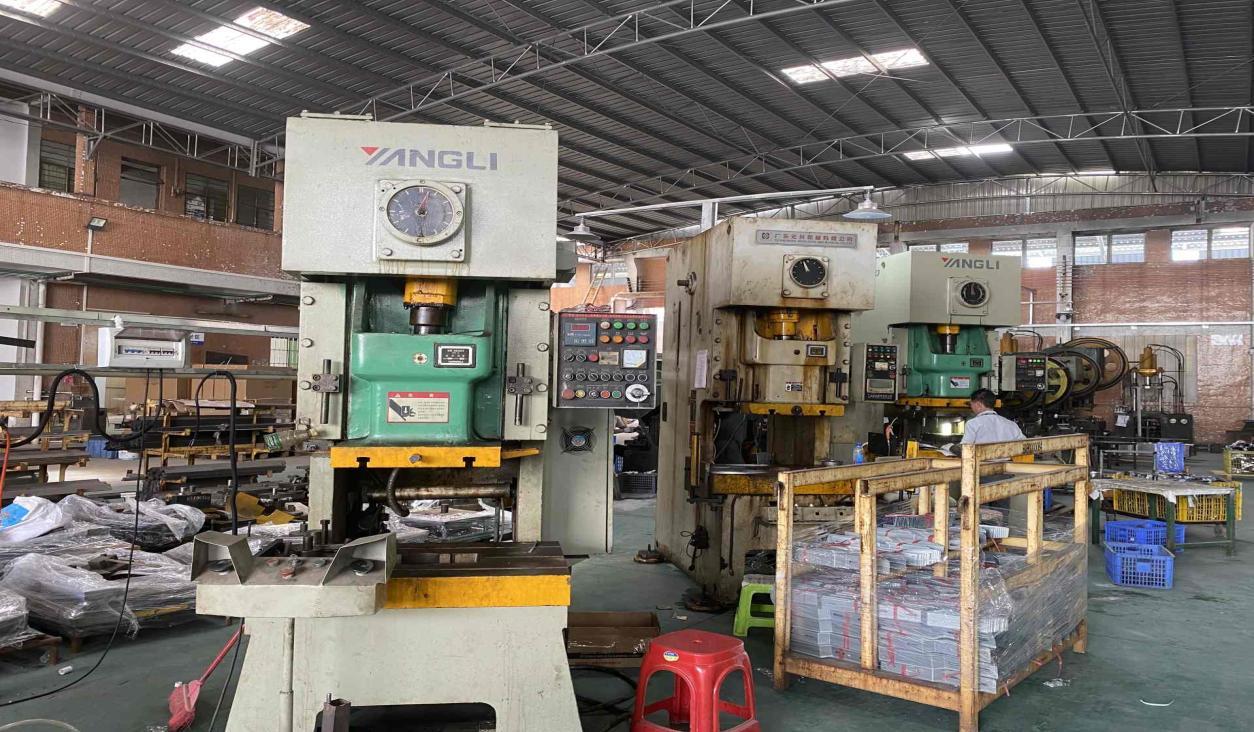
Deep drawn stamping can be used to manufacture complex, hollow parts from sheet metal, typically aluminum, steel, or copper. With a stamping press, flat sheets of metal are drawn into a die and pressed into three-dimensional shapes, such as cylinders and boxes. In order for the sheet metal to flow into the die cavity, a punch is used to apply pressure to it, causing it to take on the desired shape.
Aside from producing highly accurate and consistent parts, deep drawn stamping has many other advantages. This process allows for the production of parts with extremely tight tolerances and uniform wall thicknesses, which are particularly important for aerospace, automotive, and medical devices.
As well as being efficient and cost-effective, deep drawn stamping has a number of other advantages. As compared to casting and forging, for example, this process allows for the rapid production of large quantities of parts. Automation and robotics can also be used to improve the efficiency and costeffectiveness of deep drawn stamping.
It is important to note, however, that deep drawn stamping has some limitations. As an example, it can only be used to produce simple or symmetrical parts. For asymmetrical or complex parts, additional processes such as machining or welding may be required. Deep drawn stamps are also limited in size and thickness by the thickness of the sheet metal used, which requires more expensive and complex equipment when thicker or larger sheets are used.
A deep drawn stamping process provides numerous benefits for the production of complex, hollow parts from sheet metal as it is a versatile and efficient manufacturing process. Among aerospace, automotive, and medical device industries, its accuracy, consistency, and cost-effectiveness make it a popular choice.
What is deep drawn stamping?
By using a stamping press, flat sheet metal can be transformed into hollow, three-dimensional objects. Stamping involves applying pressure to a sheet of metal, which is then dipped into a die cavity to create the desired shape. As a result, the metal flows into the die cavity without fracturing or tearing, resulting in a depth of draw.
It is commonly used to create parts such as cans, tubes, and cases in aerospace, automotive, and medical device industries. Deep drawn stamps can produce complicated shapes with precise dimensions and uniform wall thicknesses. Moreover, household appliances, electronics, and other consumer items are also produced by using this process.
One of its key advantages is its ability to produce parts with high levels of accuracy and consistency, even for complex shapes. With the help of automation, large quantities of parts can be produced quickly and efficiently at a low cost, making it a great choice for mass production.
Deep-drawn stamping typically uses what types of sheet metal?
Deep drawn stamping involves shaping flat sheets of metal into three-dimensional shapes. Materials such as aluminum, stainless steel, copper, brass, and high-strength steel alloys can be used for deep drawn stamping.
Aluminum is a popular choice for aerospace and automobile applications because of its lightweight properties and corrosion resistance. The strength and durability of stainless steel make it a popular choice for medical and industrial equipment. Electrical and electronic applications often use copper and brass due to their excellent conductivity.
Sheet metal can be used for deep drawn stamping depending on the application and desired properties of the final product. Parts that require high strength or wear resistance can be made from different grades of steel, while parts that require flexibility can be made from softer materials.
What makes deep drawn stamping so effective?
The deep drawn stamping process involves forming flat sheets of metal into three-dimensional shapes, such as hollow cylinders and boxes. It involves blanking, forming, drawing, and trimming.
In the blanking stage, a sheet of metal is cut into a flat shape, usually a circle or rectangle. In the stamping press, force is applied to the blank sheet, causing it to flow into the die cavity and form the desired shape. A blank holder holds the flat sheet in place while it is stamped.
A deep-drawn shape is created by pulling metal into a die cavity, varying according to the shape and depth of the die and the properties of the metal used.
A finished part is trimmed after it has been drawn, removing any excess metal. Trimming may be done manually or automatically.
Deep drawn stamping requires a combination of pressure, force, and lubrication in order to achieve the desired shape without tearing or fracturing the metal. To minimize friction between the metal and the die, as well as to keep the metal from sticking, lubricants are used.
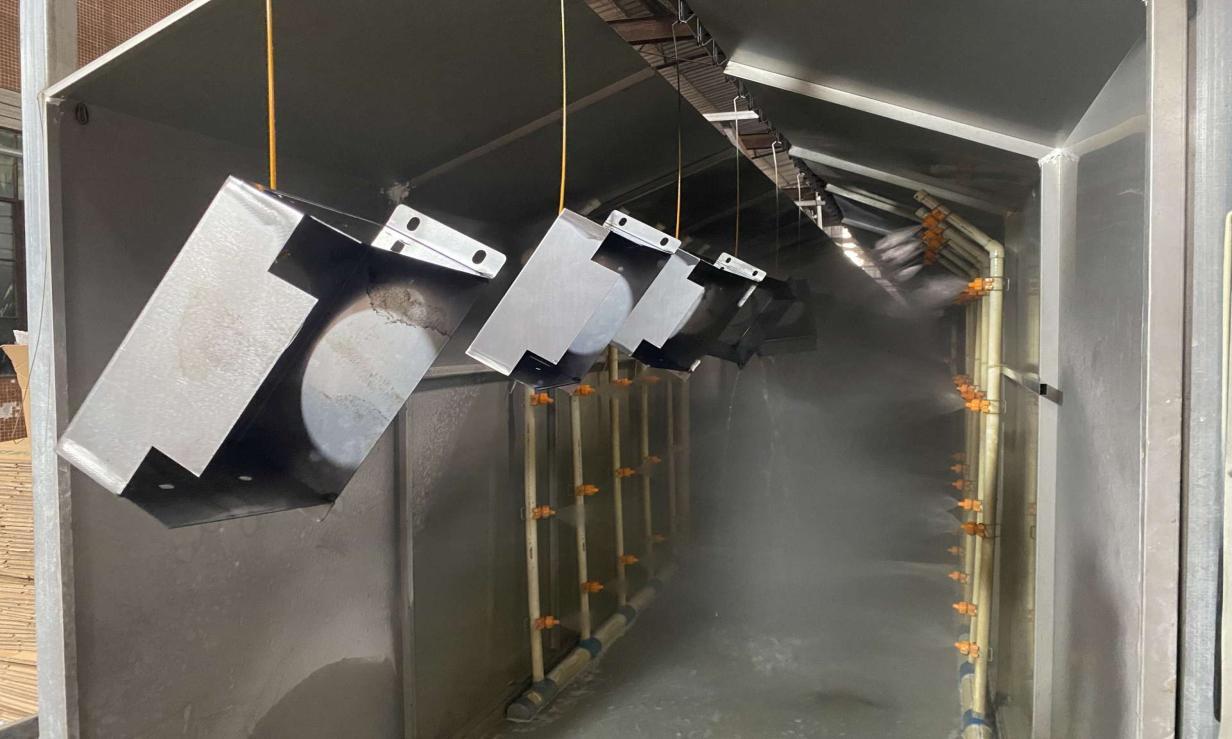
Can deep drawn stamping produce complex shapes?
Deep drawn stamping allows the creation of parts with complex shapes, and it also allows the creation of three-dimensional shapes that would otherwise not be possible.
A deep drawn stamping process produces complex, three-dimensional shapes from flat sheets of metal by drawing, forming, and tinkering.
Metals such as aluminum, stainless steel, copper, and brass can also be used in deep drawn stamping, giving manufacturers the ability to produce complex parts with diverse mechanical properties.
How does deep drawn stamping compare to other manufacturing methods in terms of cost-effectiveness?
The deep drawn stamping process is cost-effective when compared to other manufacturing methods. By using a series of dies and punches, flat sheets of metal can be formed into complex, three-dimensional forms, and high-volume production runs can be automated. Parts can be produced more quickly and efficiently, thus reducing labor costs and increasing productivity.
Moreover, deep drawn stamping can use a variety of materials, including aluminum, stainless steel, copper, and brass, which can be purchased in sheet form for relatively inexpensive prices. Thus, material waste is reduced and raw materials are utilized more efficiently, resulting in further savings.
Further, Progressive stamping results in highly accurate, repeatable parts, which reduces production times and costs.