2 minute read
LAB IN A BOX
Next Article
For decades the size of computing systems has reduced gradually, from the mainframe equipment used in the mid 20th century through workstations, laptops, tablets and smartphones.
It means, today, at times of crisis and convenience, many workers can take the device central to their productivity home, to another workspace or on the road. For those working in biological labs, however, every piece of equipment remains in the facility. Changing that, in one fell swoop, is the motivation of BiologIC Technologies.
The start-up has designed, and holds intellectual property for, a device it hopes will become ‘the desktop PC of biology.’ It is intended to scale down laboratory processes to design biology, controlling fluids and cells, introducing chemicals and reagents, within a small footprint. Referred to as a lab in a box, Stratasys’ J826 multi-material PolyJet 3D printing technology is integral to its design and manufacture.
“If you think of all the functions in a biological lab, we’re basically miniaturising those into a series of modules each with a Rubik’s Cube-sized footprint,” Chairman Richard Vellacott told TCT. “A normal PC runs off semiconductor chips, central processing units and graphical units made out of silicon; we’re making bioprocessing units using 3D printing.”
These bioprocessing units, or cartridges, plug into a universal instrument to run a particular biological workflow. Stratasys’ flexible and tear-resistant Agilus material is used to help move biology ‘dynamically’ around the system, while the VeroUltraClear material allows the user to see the biology as it goes. The design of the cartridges is said to be so complex, making them any other way isn’t an option. As such, BiologIC will be looking to move into production using the same technology, expanding on its current capacity - nine cartridges per build - with larger format J850 machines.
6 BELOW: THE BIOLOGIC TEAM LEFT TO RIGHT: DR COLIN BAKER, RICHARD VELLACOTT & NICK ROLLINGS
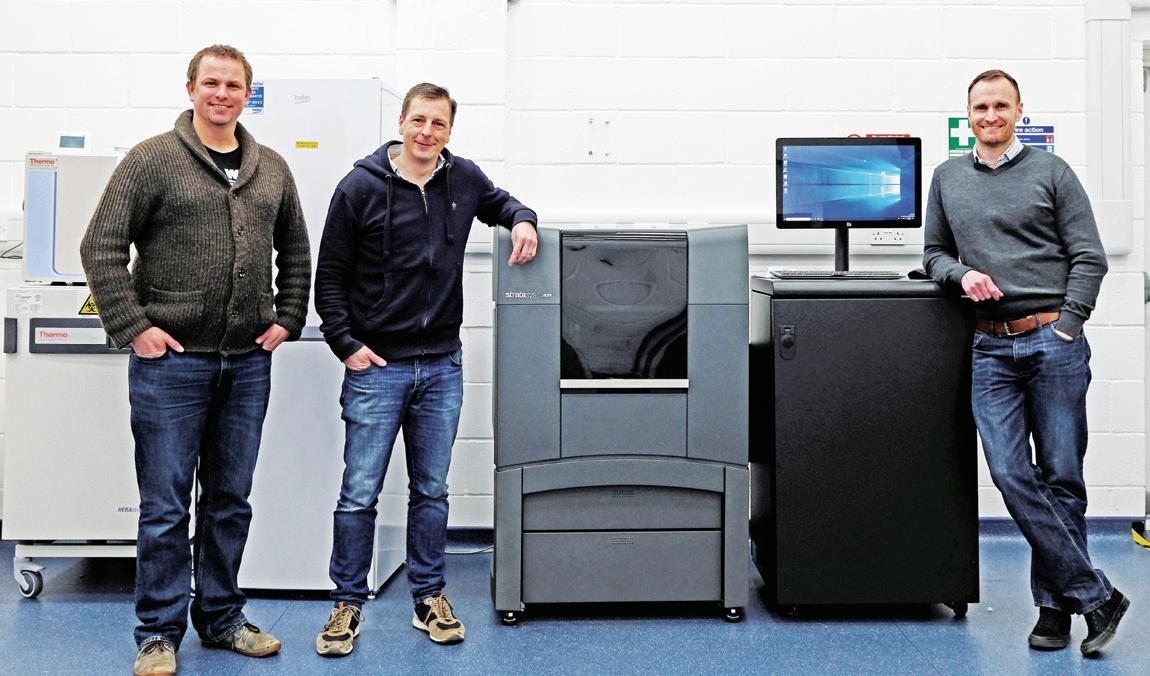
Already, customers are intrigued. “We’ve been working with customers since day one – they’re fascinated by it – and they can see straight into the design, build and tests of these products,” Vellacott said. “We can turn the whole conventional life science instrument development model on its head, rather than waiting five to ten years to get something out to a customer and hope they want it.”
Of course, there is some path still to tread in the development of BiologIC’s device – Vellacott confesses it’s a ‘grand vision’ – but once the usual regulatory hurdles have been cleared, the hope is medical professionals can accelerate the advancement of their medicines. BiologIC knows there exist laboratory innovations that could lead to potential therapies for cancers, vaccines and treatments for other diseases, and Vellacott only has to flip open his laptop or swipe a finger across his phone right now to be reminded of the urgency.
What’s more, with experience working in laboratory environments, they can relate to the pain points that slow these developments down: Specialist equipment not marrying together so well, software tools not connecting either, and scientists routinely being taken away from their specialist tasks to do manual jobs around the lab.
“That’s not efficient for anybody,” Vellacott said. “If we can automate these processes, we can free up scientists to do what they do best, which is understand biology, design experiments, get results. We want to deploy these people not in mindless capacities, but in mindful creation. “If we execute this nicely, hopefully, we will make a big difference in the world.” “CUSTOMERS ARE FASCINATED.”